反应-再生系统及工艺设计
催化裂化装置反应再生及分馏系统工艺设计方案
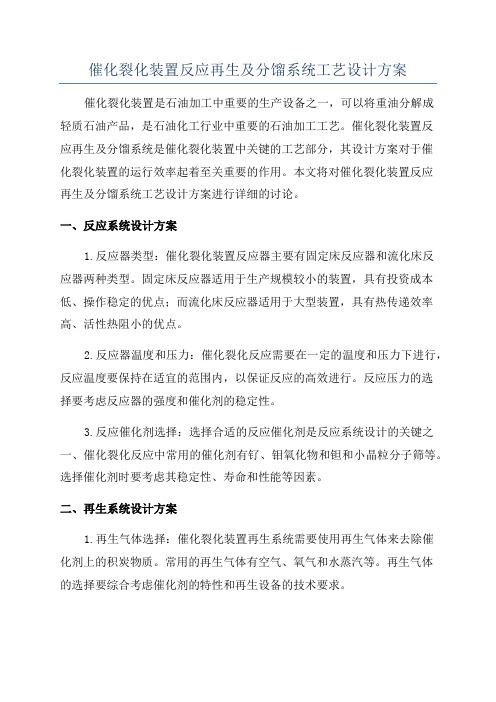
催化裂化装置反应再生及分馏系统工艺设计方案催化裂化装置是石油加工中重要的生产设备之一,可以将重油分解成轻质石油产品,是石油化工行业中重要的石油加工工艺。
催化裂化装置反应再生及分馏系统是催化裂化装置中关键的工艺部分,其设计方案对于催化裂化装置的运行效率起着至关重要的作用。
本文将对催化裂化装置反应再生及分馏系统工艺设计方案进行详细的讨论。
一、反应系统设计方案1.反应器类型:催化裂化装置反应器主要有固定床反应器和流化床反应器两种类型。
固定床反应器适用于生产规模较小的装置,具有投资成本低、操作稳定的优点;而流化床反应器适用于大型装置,具有热传递效率高、活性热阻小的优点。
2.反应器温度和压力:催化裂化反应需要在一定的温度和压力下进行,反应温度要保持在适宜的范围内,以保证反应的高效进行。
反应压力的选择要考虑反应器的强度和催化剂的稳定性。
3.反应催化剂选择:选择合适的反应催化剂是反应系统设计的关键之一、催化裂化反应中常用的催化剂有钌、钼氧化物和钽和小晶粒分子筛等。
选择催化剂时要考虑其稳定性、寿命和性能等因素。
二、再生系统设计方案1.再生气体选择:催化裂化装置再生系统需要使用再生气体来去除催化剂上的积炭物质。
常用的再生气体有空气、氧气和水蒸汽等。
再生气体的选择要综合考虑催化剂的特性和再生设备的技术要求。
2.再生温度和压力:再生温度对催化剂的再生效果有重要影响,要选择合适的再生温度,以保证催化剂的活性能得到有效的恢复。
再生压力的选择要考虑再生设备的设计和操作要求。
3.再生设备选择:再生设备主要有再生炉和再生器两种类型。
再生炉适用于小型装置,具有结构简单、操作方便的优点;再生器适用于大型装置,具有稳定的再生效果和高效的催化剂循环的优点。
三、分馏系统设计方案1.分馏塔类型:催化裂化装置的分馏塔主要有常压塔和减压塔两种类型。
常压塔适用于生产重质油品,具有生产成本低、操作稳定的优点;减压塔适用于生产轻质油品,具有产品质量好、产品收率高的优点。
反应——再生系统工艺计算

第七节反应—再生系统工艺计算目录一、再生器物料平衡和热平衡计算------------------------------------------21.燃烧计算-------------------------------------------------------------------3 2.再生器热平衡-------------------------------------------------------------6 3.再生器物料平衡----------------------------------------------------------8 4.附注------------------------------------------------------------------------10二、提升管反应器的设计-----------------------------------------------------121、基础数据--------------------------------------------------------------------122、提升管直径和长度计算--------------------------------------------------13三、再生器的工艺计算--------------------------------------------------------20四、旋风分离器系统的压力平衡--------------------------------------------24五、旋风分离器工艺计算-----------------------------------------------------26六、两器压力平衡------------------------------------------------------------33七、催化剂循环量的几种计算方法-----------------------------------------38反应—再生系统工艺计算这一章的主要目的是通过几个具体的例子掌握反应—再生系统工艺计算的基本方法。
石油化工催化裂化装置工艺流程图.docx
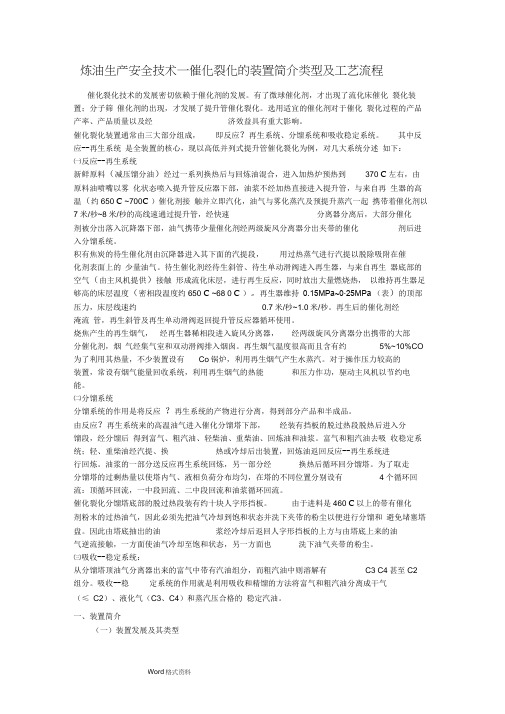
炼油生产安全技术一催化裂化的装置简介类型及工艺流程催化裂化技术的发展密切依赖于催化剂的发展。
有了微球催化剂,才出现了流化床催化裂化装置;分子筛催化剂的出现,才发展了提升管催化裂化。
选用适宜的催化剂对于催化裂化过程的产品产率、产品质量以及经济效益具有重大影响。
催化裂化装置通常由三大部分组成,即反应?再生系统、分馏系统和吸收稳定系统。
其中反应--再生系统是全装置的核心,现以高低并列式提升管催化裂化为例,对几大系统分述如下:㈠反应--再生系统新鲜原料(减压馏分油)经过一系列换热后与回炼油混合,进入加热炉预热到370 C左右,由原料油喷嘴以雾化状态喷入提升管反应器下部,油浆不经加热直接进入提升管,与来自再生器的高温(约650 C ~700C )催化剂接触并立即汽化,油气与雾化蒸汽及预提升蒸汽一起携带着催化剂以7米/秒~8米/秒的高线速通过提升管,经快速分离器分离后,大部分催化剂被分出落入沉降器下部,油气携带少量催化剂经两级旋风分离器分出夹带的催化剂后进入分馏系统。
积有焦炭的待生催化剂由沉降器进入其下面的汽提段,用过热蒸气进行汽提以脱除吸附在催化剂表面上的少量油气。
待生催化剂经待生斜管、待生单动滑阀进入再生器,与来自再生器底部的空气(由主风机提供)接触形成流化床层,进行再生反应,同时放出大量燃烧热,以维持再生器足够高的床层温度(密相段温度约650 C ~68 0 C )。
再生器维持0.15MPa~0∙25MPa (表)的顶部压力,床层线速约0.7米/秒~1.0米/秒。
再生后的催化剂经淹流管,再生斜管及再生单动滑阀返回提升管反应器循环使用。
烧焦产生的再生烟气,经再生器稀相段进入旋风分离器,经两级旋风分离器分出携带的大部分催化剂,烟气经集气室和双动滑阀排入烟囱。
再生烟气温度很高而且含有约5%~10%CO 为了利用其热量,不少装置设有Co锅炉,利用再生烟气产生水蒸汽。
对于操作压力较高的装置,常设有烟气能量回收系统,利用再生烟气的热能和压力作功,驱动主风机以节约电能。
再生器反应器讲义讲解

1.烧焦段
上述各反应对除焦是必要的,但对催化 剂容易造成损害。它导致催化剂表面温度 上升,而高温则极大地增加了催化剂永久 性损害的危险。所以烧焦要控制好,这是 通过控制燃烧过程的氧含量来完成的。 氧含量过高造成温度过高,但氧含量过低 则燃烧不足。正常操作时,氧含量保持在 0.6~1.0摩尔%之间,这是使烧焦速度达到 最快,烧焦温度相对最低的最佳范围。
谢谢
催化剂入口
第一反应器原料入口 第一反应器流出物出口
催化剂 转移管 反应器原料 入口 反应物流出口
出物出口
第一反应器 第二反应器原料入口 第二反应器原料出口
二反应器流出物出口
中心管
第二反应器 最后反应器原料入口 最后反应器流出物出口 扇形筒
催化剂出口
零部件
2、扇形筒
一般由壁厚3mm的不锈钢板制成,外 表面上开有很长的长条孔,各开孔的圆角 处都不准有尖锐的棱角,制造要求精度很 高,每个扇形筒都紧贴在反应器壁上,采 用膨胀圈固定,但固定的紧密度很严格, 即要使扇形筒不能移动,保证其不会变形; 又要考虑在操作状态下扇形筒的热膨胀需 要的间隙;
3.干燥段
催化剂在进入铂重整反应器之前越干燥,那么它 的总体性能越好。高温和干燥时间长及足够的干 燥气体流速,有利于本步骤完成。足够的干燥气 体流速,能确保气体分布良好,热量充足;
4.冷却段
冷却区有两大作用:冷却去下游待处理的催
化剂,预热部分去干燥区的空气。 冷却的催化剂降低了下游催化剂输送设备的 材质方面的要求。 预热的干燥空气降低了空气加热器负荷,这 样可节约公用工程开支。
催化剂连续再生必须经历五个工艺过程, 既催化剂的烧焦﹑氧氯化﹑干燥﹑冷却﹑ 还原。其中四个过程是在再生器中完成的, 还原是在再生器外完成的。因此再生器的 结构要按能够完成四个工艺过程来设计, 必须满足催化剂连续再生工艺的要求。
150万吨年渣油催化裂化反应再生系统工艺设计

150万吨年渣油催化裂化反应再生系统工艺设计摘要在本设计中,使用大庆常压渣油作为原料,采纳汽油生产方案,进行渣油催化裂化反再系统的工艺设计。
催化裂化装置由反应再生系统,分馏系统,吸取稳固系统和能量回收系统组成。
本设计要紧针对反应再生系统进行设计运算。
由于渣油催化裂化的焦炭产率高,对再生器的烧焦能力要求较高,故本设计选用烧焦罐式再生器以实现高效完全再生。
在本设计中,基于设计的原料性质,参考国内同类装置的数据采纳高低并列式再生系统,提升过反应器和烧焦罐高温完全再生系统。
反应部分:反应器为原料油和催化剂充分接触提供必要的空间,本设计采纳提升管、汽提段、沉降器同轴布置,以减少生焦,提高轻质油收率。
再生部分:再生器的作用是烧焦,烧掉催化剂上的积炭,使催化剂上的活性得以复原。
本设计采纳带有预混合管的高效烧焦罐式再生器,可使催化剂含碳量降到0.1%以下,充分发挥了催化剂的选择性,延长了催化剂的寿命。
关键词:催化裂化,提升管,再生器,催化剂TECHNOLOGCIAL DESIGN FOR REACTION AND REGENERATION SYSTEM OF 150wt/a RFCCAbstractReaction and regeneration system technology of a 270wt/a RFCC processing DAQING atmospheric residue feedstock has been designed and calculated in this layout.The catalytic cracking unit is made up from reaction and regeneration system fractionation system,absorption and stabilization system and energy recover system. This layout is derected against reaction and regeneration system to compute.A high efficient and complete coke burning regenerator having high burning capacity was adopted because much coke was produced during RFCC process.In the design,Referring to the dates of feed and the same type reactors,I design a high-low parallel FCC reactor-regenerator system-riser reactor and coke container high temperature complete reactor-regenerator system. The part of reaction: the reactor develops sufficient room for feed oil and catalytic contacting completely. This kind of design is to reduce coke promote recall ratio of light oil. The part of regenerator system: the regenerator can burn up remaining carbon about catalytic to recover activity of CAT. General speaking,my design can reduce the ratio of carbon in CAT to 0.1%,so it makes full use of choice of CAT,extends the life of the catalyst.Keywords:catalytic cracking,riser,regenerator,catalyst名目1 文献综述 (1)1.1催化裂化工艺产生的背景及意义 (1)1.1.1国外催化裂化 (1)1.1.2国内催化裂化 (2)1.2催化裂化技术的现状及进展 (2)1.2.1国外催化裂化技术的现状及进展 (3)1.2.2我国催化裂化技术的现状及进展 (5)1.3重油催化裂化 (7)1.3.1重油催化裂化的原料 (8)1.3.2重油催化裂化的产品 (8)1.3.3重油催化裂化装置特点 (8)1.4催化裂化装置研究进展 (11)1.4.1催化裂化再生装置形式 (11)1.4.2催化裂化反应装置形式 (15)1.4.3催化裂化反应—再生两器排布方式 (19)1.4.4提升管末端快速分离器 (21)1.4.5进料雾化喷嘴 (24)1.4.6空气分布器 (26)1.4.7结语 (29)2 设计说明 (30)2.1 加工方案的确定及装置形式的选择 (30)2.1.1 加工方案 (30)2.1.2 装置形式的选择 (30)2.2 流程说明 (30)2.2.1 反应再生系统 (30)2.2.2 分馏系统 (32)2.2.3 吸取稳固系统 (34)2.3 要紧操作条件 (35)2.3.1 再生温度 (35)2.3.2 再生压力 (36)2.3.3 再生烟气中过剩氧含量 (36)2.3.4 反应温度 (36)2.3.5 反应压力 (37)2.3.6 焦中氢碳比(H/C) (37)2.3.7 反应时刻 (38)2.3.8 烟气中CO与CO2比值(CO/CO2) (38)2.3.9 原料的预热温度 (38)2.3.10 再生剂含碳量(定碳) (39)2.4 装置设备的特点 (39)2.5 能量回收 (40)2.6 环境爱护 (41)3 设计运算 (42)3.1 基础数据 (42)3.2 再生部分运算 (43)3.2.1 燃烧运算 (43)3.2.2 反应系统热平稳运算 (48)3.2.3 再生系统热平稳运算 (53)3.2.4 取热器的设计 (56)3.2.5 催化剂外循环管设计运算 (58)3.2.6 再生器结构尺寸运算 (59)3.2.7 催化剂输送管线 (64)3.2.8 旋风分离器的设计运算 (67)3.2.9 主风分布板的设计运算 (72)3.2.10 辅助燃烧室的设计运算 (73)3.2.11 能量回收的运算 (76)3.3 反应器部分运算 (78)3.3.1 提升管反应器的设计运算 (78)3.3.2 预提升管尺寸运算 (86)3.3.3 沉降器和汽提段尺寸运算 (86)3.3.4 旋风分离器的选型与核算 (91)3.4两器压力平稳运算 (93)4 工艺设计运算结果汇总 (98)4.1 反再系统要紧操作参数运算结果汇总 (98)4.2 反应系统物料平稳 (103)4.3 反应系统水平稳 (105)4.4再生器物料平稳 (106)4.5 再生器水平稳 (106)4.7 再生系统热平稳 (107)4.8 再生器外取热器设计结果汇总 (108)4.9 再生催化剂线路 (109)4.10 待生催化剂路线 (109)4.11 反再系统要紧操作条件 (110)致谢 (111)参考文献 (112)130万吨/年渣油催化裂化反再系统工艺设计1 文献综述1.1催化裂化工艺产生的背景及意义一样原油经常减压蒸馏后可得到10~40%的汽油,煤油及柴油等轻质油品,其余的是重质馏分和残渣油。
MTO工艺流程
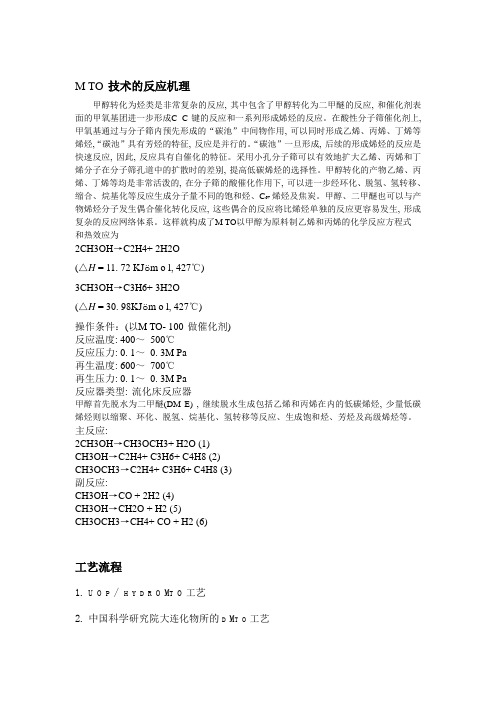
M TO 技术的反应机理甲醇转化为烃类是非常复杂的反应, 其中包含了甲醇转化为二甲醚的反应, 和催化剂表面的甲氧基团进一步形成C- C 键的反应和一系列形成烯烃的反应。
在酸性分子筛催化剂上, 甲氧基通过与分子筛内预先形成的“碳池”中间物作用, 可以同时形成乙烯、丙烯、丁烯等烯烃,“碳池”具有芳烃的特征, 反应是并行的。
“碳池”一旦形成, 后续的形成烯烃的反应是快速反应, 因此, 反应具有自催化的特征。
采用小孔分子筛可以有效地扩大乙烯、丙烯和丁烯分子在分子筛孔道中的扩散时的差别, 提高低碳烯烃的选择性。
甲醇转化的产物乙烯、丙烯、丁烯等均是非常活泼的, 在分子筛的酸催化作用下, 可以进一步经环化、脱氢、氢转移、缩合、烷基化等反应生成分子量不同的饱和烃、C6+ 烯烃及焦炭。
甲醇、二甲醚也可以与产物烯烃分子发生偶合催化转化反应, 这些偶合的反应将比烯烃单独的反应更容易发生, 形成复杂的反应网络体系。
这样就构成了M TO以甲醇为原料制乙烯和丙烯的化学反应方程式和热效应为2CH3OH→C2H4+ 2H2O(△H = 11. 72 KJöm o l, 427℃)3CH3OH→C3H6+ 3H2O(△H = 30. 98KJöm o l, 427℃)操作条件:(以M TO- 100 做催化剂)反应温度: 400~500℃反应压力: 0. 1~0. 3M Pa再生温度: 600~700℃再生压力: 0. 1~0. 3M Pa反应器类型: 流化床反应器甲醇首先脱水为二甲醚(DM E) , 继续脱水生成包括乙烯和丙烯在内的低碳烯烃, 少量低碳烯烃则以缩聚、环化、脱氢、烷基化、氢转移等反应、生成饱和烃、芳烃及高级烯烃等。
主反应:2CH3OH→CH3OCH3+ H2O (1)CH3OH→C2H4+ C3H6+ C4H8 (2)CH3OCH3→C2H4+ C3H6+ C4H8 (3)副反应:CH3OH→CO + 2H2 (4)CH3OH→CH2O + H2 (5)CH3OCH3→CH4+ CO + H2 (6)工艺流程1.U O P / H Y D R O M T O 工艺2.中国科学研究院大连化物所的D M T O 工艺3.E x x o n M o b i l M T O 工艺4.中国石化上海石油化工研究院( S R I P T) 的S 一M T O 工艺(详见参考文献甲醇制低碳烯烃工艺技术新进展)主要两个工艺:U O P / H Y D R O M T O 工艺;中国科学研究院大连化物所的D M T O 工艺1.1 UOP/Hrdro 的MTO 技术UOP 公司在S A P O - 3 4 分子筛的基础上开发出了M T O - 1 0 0 甲醇转化制烯烃专用催化剂。
催化裂化的装置简介及工艺流程
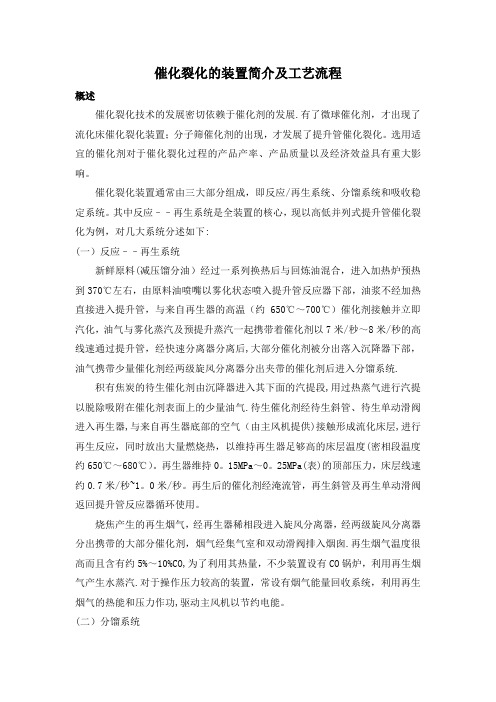
催化裂化的装置简介及工艺流程概述催化裂化技术的发展密切依赖于催化剂的发展.有了微球催化剂,才出现了流化床催化裂化装置;分子筛催化剂的出现,才发展了提升管催化裂化。
选用适宜的催化剂对于催化裂化过程的产品产率、产品质量以及经济效益具有重大影响。
催化裂化装置通常由三大部分组成,即反应/再生系统、分馏系统和吸收稳定系统。
其中反应––再生系统是全装置的核心,现以高低并列式提升管催化裂化为例,对几大系统分述如下:(一)反应––再生系统新鲜原料(减压馏分油)经过一系列换热后与回炼油混合,进入加热炉预热到370℃左右,由原料油喷嘴以雾化状态喷入提升管反应器下部,油浆不经加热直接进入提升管,与来自再生器的高温(约650℃~700℃)催化剂接触并立即汽化,油气与雾化蒸汽及预提升蒸汽一起携带着催化剂以7米/秒~8米/秒的高线速通过提升管,经快速分离器分离后,大部分催化剂被分出落入沉降器下部,油气携带少量催化剂经两级旋风分离器分出夹带的催化剂后进入分馏系统.积有焦炭的待生催化剂由沉降器进入其下面的汽提段,用过热蒸气进行汽提以脱除吸附在催化剂表面上的少量油气.待生催化剂经待生斜管、待生单动滑阀进入再生器,与来自再生器底部的空气(由主风机提供)接触形成流化床层,进行再生反应,同时放出大量燃烧热,以维持再生器足够高的床层温度(密相段温度约650℃~680℃)。
再生器维持0。
15MPa~0。
25MPa(表)的顶部压力,床层线速约0.7米/秒~1。
0米/秒。
再生后的催化剂经淹流管,再生斜管及再生单动滑阀返回提升管反应器循环使用。
烧焦产生的再生烟气,经再生器稀相段进入旋风分离器,经两级旋风分离器分出携带的大部分催化剂,烟气经集气室和双动滑阀排入烟囱.再生烟气温度很高而且含有约5%~10%CO,为了利用其热量,不少装置设有CO锅炉,利用再生烟气产生水蒸汽.对于操作压力较高的装置,常设有烟气能量回收系统,利用再生烟气的热能和压力作功,驱动主风机以节约电能。
催化裂化工艺流程及主要设备
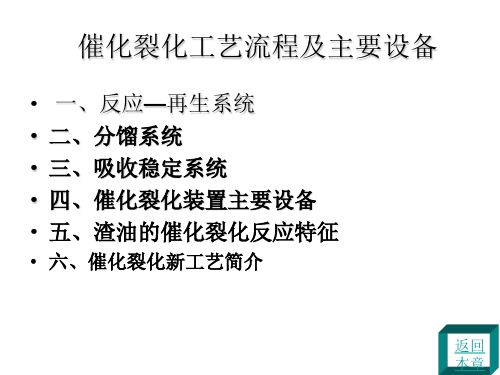
➢分布器可分为板式(蝶形)和管式(平面树枝或环形)两种
重催再生器需设取热设备: a.内取热式 b.外取热式
主要要求有:
①再生剂的含炭量较低,一般要求低于0.2%,甚
至低于0.05%;
②有较高的烧碳强度,当以再生器内的有效藏量
为基准时,烧碳强度一般为100~250kg/(t.h);
③催化剂减活及磨损较少; ④易于操作,能耗及投资少; ⑤能满足环保要求
①对于全混床反应器,第一段出口的半再生剂的含碳量 高于再生剂的含碳量,从而提高了烧碳速率;
②在第二段再生时可以用新鲜空气和更高的温度,提高 了烧碳速率;
③第二段内的水气分压可以很低,减轻了催化剂的水热 老化;且第二段的催化剂藏量比单段再生器的催化剂藏量低, 停留时间较短。因此,第二段可采用较高的再生温度。
从流化域来看,单段再生和两
段再生都属于鼓泡床和湍流床 的范畴,传递阻力和返混对烧 碳速率都有重要的影响。
你知道吗?
如果把气速提高到1. 2m/s
以上,而且气体和催化剂向 上同向流动,就会过渡到快 速床区域。
烧焦罐再生(亦称高效再生)就是 循环流化床的一种方式
二密床高度4~6m. 烟气流速 0.1~0.25m/s
稀相管高度8~15m.
烧焦罐再生 烟气流速7~10m/s
循环管是烧焦罐再生器的独有设备, 它的作用是把热催化剂从二密相返回 烧焦罐,提高烧焦罐底部温度和烧焦 罐密度,以提高烧焦速度并增加烧焦 能力。早期的烧焦罐装置循环比为 I~I.5,循环管直径与再生剂管直径相 当;近年设计的烧焦罐装置循环比为 1.5~2,循环管直径明显大于再生管 直径。
100~125mm厚的隔热耐磨衬里。 ➢ 伸到汽提段、沉降器内的部分只设耐磨衬里。 ➢ 提升管的上端出口处设有气-固快速分离机构,用于使催化剂与油气
催化裂化工艺介绍

1.0催化裂化催化裂化是原料油在酸性催化剂存在下,500℃左右、1× 105~3× 105Pa 在下发生裂解,生成轻质油、气体和焦炭的过程。
催化裂化是现代化炼油厂用来改质重质瓦斯油和渣油的核心技术,是炼厂获取经济效益的重要手段。
催化裂化的石油炼制工艺目的:1)提高原油加工深度,得到更多数量的轻质油产品;2)增加品种,提高产品质量。
催化裂化是炼油工业中最重要的一种二次加工工艺,是重油轻质化和改质的重要手段之一,已成为当今石油炼制的核心工艺之一。
1.1催化裂化的发展概况催化裂化的发展经历了四个阶段:固定床、移动床、流化床和提升管。
见下图:流化床在全世界催化裂化装置的总加工能力中,提升管催化裂化已占绝大多数。
移动床提升管(并列式)1.2催化裂化的原料和产品1.2.1原料催化裂化的原料围广泛,可分为馏分油和渣油两大类。
馏分油主要是直馏减压馏分油(VGO),馏程350-500℃,也包括少量的二次加工重馏分油如焦化蜡油等,以此种原料进行催化裂化称为馏分油催化裂化。
渣油主要是减压渣油、脱沥青的减压渣油、加氢处理重油等。
渣油都是以一定的比例掺入到减压馏分油中进行加工,其掺入的比例主要受制于原料的金属含量和残炭值。
对于一些金属含量低的石蜡基原有也可以直接用常压重油为原料。
当减压馏分油中掺入渣油使通称为RFCC。
以此种原料进行催化裂化称为重油催化裂化。
1.2.2产品催化裂化的产品包括气体、液体和焦炭。
1、气体在一般工业条件下,气体产率约为10%-20%,其中含干气和液化气。
2、液体产物1)汽油,汽油产率约为30%-60%;这类汽油安定性较好。
2)柴油,柴油产率约为0-40%;因含较多芳烃,所有十六烷值较低,由重油催化裂化得到的柴油的十六烷值更低,这类柴油需经加氢处理。
3)重柴油(回炼油),可以返回到反应器,已提高轻质油收率,不回炼时就以重柴油产品出装置,也可作为商品燃料油的调和组分。
4)油浆,油浆产率约为5%-10%,从催化裂化分馏塔底得到的渣油,含少量催化剂细粉,可以送回反应器回炼以回收催化剂。
反应再生系统方案

催化裂化:反应再生,分馏,吸收稳定 催化再生和烟气轮动力
操作条件:
反映再生器压力 反映温度和反应时间
原料预热温度 剂油比 回炼比 外甩油浆 烧焦温度(烧焦罐,第二密相)
烧焦罐出口氧含量 烧焦罐线速度 催化剂
烟气能量回收系统工艺设计
主要设备装配图:反应器 再生器 取热器 第三级旋风分离器
废热锅炉
反映再生系统设备选着:
1反映系统形式(同轴,高低并列)
2反映器系统:1提升管反应器 2气固分离系统:沉淀器,快速分离器,旋风分离器
3再生器系统:1高效烧焦罐 2稀相再生管 3第二密相床 4气固分离系统:沉淀器,快速分离 器,旋风分离器 5主风分布管 6辅助燃烧室 7主风机(空气压缩机)
取热系统:外取系统
烟气能量回收系统:烟气轮机(烟机) 第三级旋风分离器 废热锅炉
催化剂循环系统:待生斜管及待生滑阀 待生斜管及再生滑阀 双动滑举阀
产物分离和化学原理:参考《石油炼制工程》 《石油炼制工艺学》 《石油化工工程设计基础》
设备工艺设计 反应器工艺设计
甲醇制烯烃工艺流程简述
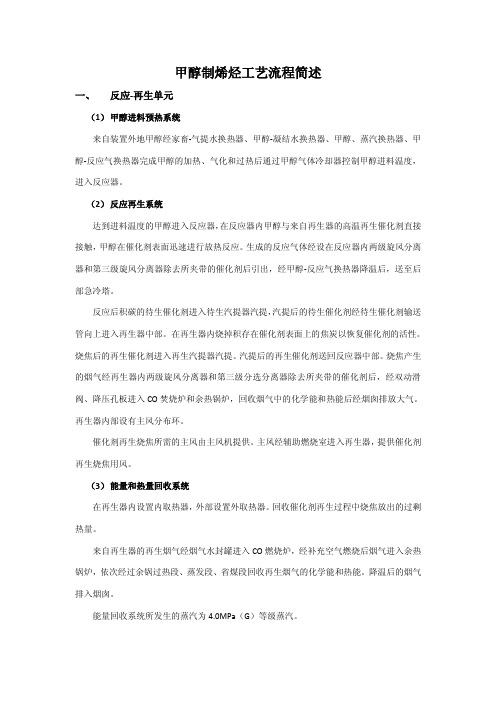
甲醇制烯烃工艺流程简述一、反应-再生单元(1)甲醇进料预热系统来自装置外地甲醇经家畜-气提水换热器、甲醇-凝结水换热器、甲醇、蒸汽换热器、甲醇-反应气换热器完成甲醇的加热、气化和过热后通过甲醇气体冷却器控制甲醇进料温度,进入反应器。
(2)反应再生系统达到进料温度的甲醇进入反应器,在反应器内甲醇与来自再生器的高温再生催化剂直接接触,甲醇在催化剂表面迅速进行放热反应。
生成的反应气体经设在反应器内两级旋风分离器和第三级旋风分离器除去所夹带的催化剂后引出,经甲醇-反应气换热器降温后,送至后部急冷塔。
反应后积碳的待生催化剂进入待生汽提器汽提,汽提后的待生催化剂经待生催化剂输送管向上进入再生器中部。
在再生器内烧掉积存在催化剂表面上的焦炭以恢复催化剂的活性。
烧焦后的再生催化剂进入再生汽提器汽提。
汽提后的再生催化剂送回反应器中部。
烧焦产生的烟气经再生器内两级旋风分离器和第三级分选分离器除去所夹带的催化剂后,经双动滑阀、降压孔板进入CO焚烧炉和余热锅炉,回收烟气中的化学能和热能后经烟囱排放大气。
再生器内部设有主风分布环。
催化剂再生烧焦所需的主风由主风机提供。
主风经辅助燃烧室进入再生器,提供催化剂再生烧焦用风。
(3)能量和热量回收系统在再生器内设置内取热器,外部设置外取热器。
回收催化剂再生过程中烧焦放出的过剩热量。
来自再生器的再生烟气经烟气水封罐进入CO燃烧炉,经补充空气燃烧后烟气进入余热锅炉,依次经过余锅过热段、蒸发段、省煤段回收再生烟气的化学能和热能。
降温后的烟气排入烟囱。
能量回收系统所发生的蒸汽为4.0MPa(G)等级蒸汽。
(4)急冷、水洗系统来自反应器富含乙烯、丙烯的反应器经降温后一起送入急冷塔,自上而下经人字型挡板与急冷塔顶冷却水逆流接触,冷却水自急冷塔塔底抽出,经急冷塔底泵升压,进入急冷塔底泵出口过滤器,过滤除去急冷水中携带的催化剂,过滤后的急冷水分成两路,一路送至烯烃分离单元作为低温热源,经换热后返回的急冷水再经急冷水干式空冷器冷却后,一部分急冷水作为急冷剂返回急冷塔,另一部分送至装置外(正常不开)。
年加工50万吨重油催化裂化反应再生系统工艺设计_毕业设计

年加工50×104吨重油催化裂化反应-再生系统工艺设计前言催化裂化是一项重要的炼油工艺。
其加工能力位于各种转化工艺前茅,其技术复杂程度位居各类炼油工艺首位,但因其投资省,效益好,因而在炼油工业中占有举足轻重的地位,其主要原因和中国原油的性质密切相关,大多书中国原油350℃以前的馏出量只有26%~28%,常压渣油产率70%以上,同时,大多数中国原油都属于石蜡基原油,其常压渣油的沥青质含量低,低硫、低重金属(特别是钒)含量适合于采用催化裂化加工方法,而不需要经加氢处理等费用较高的预处理。
近年来,我过汽车工业飞速发展,2003年全国生产汽车444万辆(其中轿车201万辆),截止2003底.全国汽车保有量达到2420辆。
专家预测2020年汽车保有量将超过1亿辆(此外还有1亿辆摩托车)。
在调整车型结构提高燃油经济性的前提下,汽油需求量超过7400万吨、柴油需求量将超过1亿吨。
我过约80%的商品汽油和30%的商品柴油来自催化裂化,使催化裂化成为我国应输燃料最重要的生产装置。
从以上两个方面可见,催化裂化在实际生产中有很重要的意义,研究其工艺很有价值。
在原油价格居高不下,炼化企业的效益日益恶化的背景下,使用劣质原料来获得优质质,是炼厂的必然选择。
因此,要不断开发催化裂化新技术、新工艺,以增加产品收率、提高产品质量,这也是炼化企业在21世纪可持续发展的重大战略措施。
第一节设计原则1 工程设计采用国内开发的先进可靠的工艺技术,成熟可靠的新设备、新材料等,以达到装置技术先进,经济合理。
2 除少量关键仪表及特殊设备需引进外,其它设备及仪表立足国内。
3 尽量采用―清洁工艺‖减少环境污染。
严格遵循环保、安全、卫生有关法规,确保装置的安全生产。
4 充分吸收国内生产装置长期实践积累的有利于长周期运转,降低能耗以及简化操作等方面的经验,确保装置投产后高水平,安、稳、长、满、优生产。
第二节装置概况1 装置规模设计公称能力为50 × 104t/a。
1.1Mt每年独山子炼厂催化裂化装置工艺设计.

1.1Mt/a独山子炼厂催化裂化装置工艺设计摘要:根据独山子石化常压渣油催化裂化反应性质数据及相关数据对催化裂化装置进行了工艺设计,本设计主要内容是反应—再生系统。
首先确定独山子石化1.1Mt/a 常压渣油催化裂化装置的加工方案为多产汽油方案,反应—再生系统的烧焦形式为烧焦罐完全燃烧形式,并对反应系统和再生系统分别进行了物料衡算和热量衡算,根据计算的结果设计了反应—再生系统的主要主要设备(反应器,再生器,沉降器,旋风分离器等)的工艺尺寸,其次还对反应—再生系统进行了压力平衡计算,并计算滑阀直径。
关键词:催化裂化;反应—再生;催化剂目录1 绪论 (1)1.1 设计依据 (1)1.2 设计原则 (1)1.3 装置的特点 (1)1.4 催化裂化的国内外发展概况和趋势 (1)1.5 工艺流程说明 (2)2 反应系统的计算 (4)2.1 原料及产品性质计算 (4)2.1.1 基础数据 (4)2.1.2 原料及产品性质 (4)2.2 提升管工艺计算 (5)2.2.1 基础数据 (5)2.2.2 提升管直径和长度的计算 (5)2.2.3 预提升段尺寸的确定 (12)2.3 沉降器的工艺设计计算 (13)2.3.1 沉降器的结构 (13)2.3.2 旋风分离器的设计计算 (14)2.4 反应沉降器的工艺计算结果汇总 (17)3 再生系统的计算 (18)3.1 再生器的燃烧计算 (18)3.1.1焦炭中的碳与氢的量 (18)3.1.2 燃烧产物量和空气用量 (18)3.1.3 烧焦耗风指标 (20)3.1.4 烟风比 (20)3.1.5 燃烧结果汇总 (20)3.2 再生器的热平衡计算 (21)3.2.1 再生器各处吹扫及松动蒸汽 (21)3.2.2 供热——烧焦放出的热量 (21)3.2.3 出再生器热 (21)3.2.4 外取热器取出热量 (22)3.2.5 再生器热平衡汇总 (23)3.3 再生器的物料平衡 (23)3.4 再生器藏量及烧焦强度计算 (23)3.4.1 再生器藏量的计算 (23)3.4.2 再生器烧焦强度计算 (25)3.5 再生器的工艺尺寸设计 (25)3.5.1 主要部件直径的计算 (25)3.5.2 高度的计算 (26)3.5.3 内部附件设备的设计计算 (27)3.5.4 旋风分离器的设计计算 (28)3.6 主风机选型 (31)3.7 再生器计算结果汇总 (32)4 两器压力平衡 (34)4.1 再生线路压力平衡 (35)4.1.1 推动力 (35)4.1.2 阻力 (35)4.2 待生线路压力平衡 (35)4.2.1 推动力 (35)4.2.2 阻力 (35)4.3 滑阀的设计计算 (36)4.3.1 再生滑阀 (36)4.3.2 待生滑阀 (36)5 毕业设计总结 (37)参考文献 (38)致谢 (39)1 绪论1.1 设计依据(1)西安石油大学职业技术学院下发的毕业设计任务书。
【设计】催化裂化装置设计

【关键字】设计广东石油化工学院石油化工生产技术专业课程设计题目:150万吨/催化裂化装置反应—再生系统工艺设计目录摘要 (I)第一章前言 (3)1.1催化裂化的目的及意义 (3)1.2催化裂化技术发展 (4)1.3设计内容 (4)第二章工艺叙述 (5)2.1分馏系统 (6)2.2分馏系统 (6)2.3吸收—稳定系统 (6)第三章设计原始数据 (7)3.1开工时 (7)3.2处理量 (7)3.3原始数据及再生-反应及分馏操作条件 (9)第四章反应-再生系统工艺计算 (11)4.1再生系统 (11)燃烧计算 (11)热量平衡 (12)热流量入方 (12)热流量出方 (13)4.2反应器 (16)物料衡算 (16)18 .各进料温度 (18)热量出方 (19)提升管工艺计算 (21)21 21旋风分离器工艺计算 (24) (24) (25)二级入口截面积 (25)2525第五章分馏塔能量平衡计算 (27)第六章计算结果汇总 (29)结束语 (30)参考文献 (31)致谢 (32)第一章前言1.1催化裂化的目的及意义我国原油偏重,轻质油品含量低,为增加汽油、柴油、乙烯用裂解原料等轻质油品产量。
我国炼油工业走深度加工的道路,形成了以催化裂化(FCC)为主体,延迟焦化、加氢裂化等配套的工艺路线。
2001年底全国有147套催化裂化装置,总加工能力超过100.0Mt/a ,比1991年增加58.4 Mt/a,增长137.16%,可以说是世界上催化裂化能力增长最迅速的国家。
催化裂化是重要的重质油轻质化过程之一,在汽油和柴油等轻质油品的生产占有很重要的地位。
催化裂化过程在炼油工业,以至国民经济中只有重要的地位。
在我国,由于多数原油偏重,而H/C 相对较高且金属含量相对较低,催化裂化过程,尤其是重油催化过程的地位显得更为重要。
随着工业、农业、交通运输业以及国防工业等部门的迅速发展,对轻质油品的需求量日益增多,对质量的要求也越来越高。
石油化工催化裂化装置工艺流程图

炼油生产安全技术—催化裂化的装置简介类型及工艺流程催化裂化技术的发展密切依赖于催化剂的发展。
有了微球催化剂,才出现了流化床催化裂化装置;分子筛催化剂的出现,才发展了提升管催化裂化。
选用适宜的催化剂对于催化裂化过程的产品产率、产品质量以及经济效益具有重大影响。
催化裂化装置通常由三大部分组成,即反应¾再生系统、分馏系统和吸收稳定系统。
其中反应––再生系统是全装置的核心,现以高低并列式提升管催化裂化为例,对几大系统分述如下:㈠反应––再生系统新鲜原料(减压馏分油)经过一系列换热后与回炼油混合,进入加热炉预热到370℃左右,由原料油喷嘴以雾化状态喷入提升管反应器下部,油浆不经加热直接进入提升管,与来自再生器的高温(约650℃~700℃)催化剂接触并立即汽化,油气与雾化蒸汽及预提升蒸汽一起携带着催化剂以7米/秒~8米/秒的高线速通过提升管,经快速分离器分离后,大部分催化剂被分出落入沉降器下部,油气携带少量催化剂经两级旋风分离器分出夹带的催化剂后进入分馏系统。
积有焦炭的待生催化剂由沉降器进入其下面的汽提段,用过热蒸气进行汽提以脱除吸附在催化剂表面上的少量油气。
待生催化剂经待生斜管、待生单动滑阀进入再生器,与来自再生器底部的空气(由主风机提供)接触形成流化床层,进行再生反应,同时放出大量燃烧热,以维持再生器足够高的床层温度(密相段温度约650℃~68 0℃)。
再生器维持0.15MPa~0.25MPa (表)的顶部压力,床层线速约0.7米/秒~1.0米/秒。
再生后的催化剂经淹流管,再生斜管及再生单动滑阀返回提升管反应器循环使用。
烧焦产生的再生烟气,经再生器稀相段进入旋风分离器,经两级旋风分离器分出携带的大部分催化剂,烟气经集气室和双动滑阀排入烟囱。
再生烟气温度很高而且含有约5%~10% CO,为了利用其热量,不少装置设有CO 锅炉,利用再生烟气产生水蒸汽。
对于操作压力较高的装置,常设有烟气能量回收系统,利用再生烟气的热能和压力作功,驱动主风机以节约电能。
225万吨年新疆渣油催化裂化反-再系统工艺设计
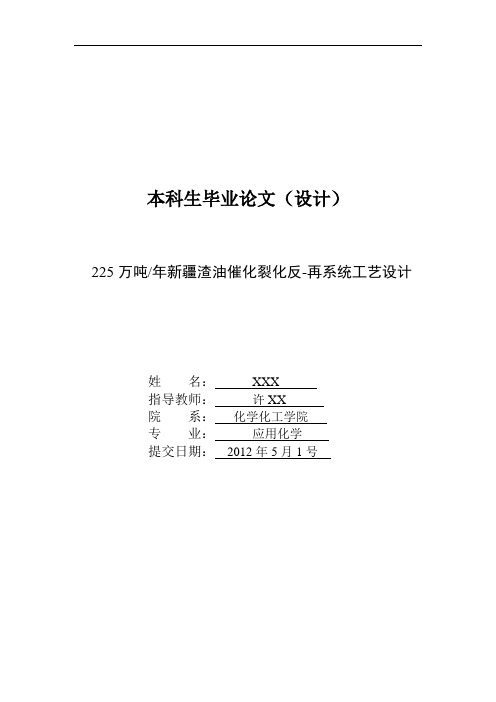
本科生毕业论文(设计)225万吨/年新疆渣油催化裂化反-再系统工艺设计姓名:XXX指导教师:许XX院系:化学化工学院专业:应用化学提交日期:2012年5月1号目录中文摘要 (3)英文摘要 (4)引言 (5)1总论 (5)1.1概述 (5)1.2新疆渣油的特点及催化裂化所需要解决的问题 (5)1.3催化裂化的发展现状以及发展趋势 (6)1.4设计地区的选择 (6)1.5 设计任务书 (6)2生产方案的确定以及生产流程说明 (7)2.1方案的确定依据 (7)2.2装置形式及特点 (7)2.3装置设计特点 (8)3生产流程简述 (9)3.1流程说明 (9)3.1.1反应-再生系统 (9)3.1.2分馏部分 (9)3.1.3吸收稳定部分 (10)3.2主要操作条件的选择依据 (10)3.2.1反应温度 (10)3.2.2反应压力 (11)3.2.3再生温度 (11)3.2.4再生压力 (11)3.2.5再生烟气氧含量 (11)3.2.6再剂碳含量 (12)3.2.7原料预热温度 (12)3.2.8反应时间 (12)3.2.9焦中H/C比 (13)3.2.10 CO/CO2 比 (13)3.2.11剂油比 (13)4工艺计算 (13)4.1基础数据 (13)4.2物料衡算 (15)4.2.1再生器物料衡算 (15)4.2.2反应器物料衡算 (17)4.3热量衡算 (20)4.3.1反应器热量衡算 (20)4.3.2再生器热量衡算 (23)5主要设备工艺计算和设备选型 (25)5.1提升管反应器 (25)5.1.1几个参数的确定 (25)5.1.2原料预热温度 (26)5.1.3提升管尺寸的计算 (26)5.2提升管长度的确定 (29)6环境保护与安全措施 (30)6.1污水处理 (30)6.2废气排放 (31)6.3废渣排放 (32)6.4安全措施防护 (32)7设计体会及收获 (33)参考文献 (35)致谢 (36)225万吨/年新疆渣油催化裂化反-再系统工艺设计江亚峰指导老师:许修强(黄山学院化工学院,黄山,安徽245041)摘要:本设计主要针对根据新疆渣油的性质特点确定选用同轴式催化裂化装置进行工艺设计,本设计采用两段再生过程,在提升管下段增加预提升段及下流式外取热器,该过程可以提高原料、催化剂、水以及能量的可循环利用率,提高效率。
11-1催化裂化反应再生系统设计

再生器系统
高效烧焦罐 稀相再生管 第二密相床 气固分离系统:沉降器、快速分离器 、旋风分离器 主风分布管 辅助燃烧室 主风机(空气压缩机)
取热系统
外取热器
烟气能量回收系统
烟气轮机(烟机) 第三级旋风分离器 废热锅炉
催化剂循环系统
待生斜管及待生滑阀 待生斜管及再生滑阀 双动滑举阀
反应器再生器外型设计
外型设计说明 两器立面图
操作条件确定
反应器再生器压力 反应温度和反应时间 原料预热温度 剂油比 回炼比 外甩油浆 烧焦温度(烧焦罐、第二密相) 烧焦罐出口氧含量 烧焦罐线速度 催化剂的含碳量
ห้องสมุดไป่ตู้
工艺流程图
装置工艺流程草图 装置工艺物料流程图 反应再生系统带控制点工艺流程图
三、设备工艺设计
反应器工艺设计 再生器工艺设计 取热器工艺设计 烟气能量回收系统工艺设计 主要设备装配图
1、渣油金属<10PPM残炭<5%。这类加工难度较少,过剩热 量可用降低进料温度,多取油浆来解决,利用低转化率操作 来减少剂油接触时间。用钝化剂可减少焦炭产率。 2、渣油金属10~30PPM,残炭5~10%。这类加工难度较大,过 剩热量采用在再生器内或再生器外设取热措施除掉。 3、渣油金属>30PPM,残炭>10%。此类难加工,需预处理。
反应器 再生器 取热器 第三级旋风分离器 废热锅炉
四、车间布置设计 车间布置设计概述 车间布置图 五、“三废”处理 六、设计计算结果汇总
化工07-3班37人(7人1组,分5组) 化工07-4班28人(7人1组,分4组) 共65人
• • • 装置工艺流程草图 装置工艺物料流程图 反应再生系统带控制点工艺流程图
三、设备工艺设计
重整反应-再生框架平面布置及管道设计

号 还 原 器 电加 热 器 再 生 电加
、 、
核 心 部 分 其平 面 布 置是 否 合 理 管道 设 计 是 否 满 足工 艺要求 就成 为 最重 要 的问 题
。
热器 空 气 电 加 热 器 粉 尘 收集 器 空 气 干 燥 器 等 号 还原 气 电加 热 器 和
。
这里 介 绍 采用
一
号 还 原 气 电加 热 器 因与
、 ,
。
反应
一
再 生 框架 下 地 面布 置 的重
、
整 注 硫罐 再 生 注 氯罐 重 整 注 水 罐 预 加 氢 注 硫 泵 重整 注 硫泵 重 整 注氯 泵 重 整 注水 泵 重 整 开 工 注 氯泵 再 生 注 氯泵 根据 放火 规 范 应 与重 整 进 料 应
,
以上 避免
,
,
建 议 重 整 第 四 反 应 器 下 切 线 距地 面 高
以上
。
由于 结 构梁 较 高 时 影 响 人 员 的通 过 性 个 别 嘴 子 或 阀门离 平 台 较 高 时 可 增 设 板 凳 来 操 作
,
。
重 整 进料换 热器如采
,
布置
的技 术 应 注 意 热 端混 合 同侧
,
电加 热器 时 应 充 分 考 虑 电加 热 器 抽 芯 的 距 离 要 求 避免 与 框 架 结 构 梁 及 斜 撑 碰 撞
,
反应
器 顶 部 需根 据 检 修拆 除 还 原段 时 抽 出 的 中 心 管 和 扇形 筒 的 长度及 重量 设 置 吊梁 和 电动 葫 芦
、 、
。
再
生风机 再生 空 冷 器风 机 除尘 风机 和 提 升风 机 需 在风机 顶 部 设 置检 修 梁 及 电动 葫芦
- 1、下载文档前请自行甄别文档内容的完整性,平台不提供额外的编辑、内容补充、找答案等附加服务。
- 2、"仅部分预览"的文档,不可在线预览部分如存在完整性等问题,可反馈申请退款(可完整预览的文档不适用该条件!)。
- 3、如文档侵犯您的权益,请联系客服反馈,我们会尽快为您处理(人工客服工作时间:9:00-18:30)。
主要技术要求:
再生剂含碳低(一般要求低于0.2%, 甚至要求达到0.05%~0.01%)。 较高的烧焦强度:100~250kg/t.h。 100~250kg/t.h 催化剂减活与磨损条件比较缓和。 易于操作,能耗和投资少。 能满足环境要求。
三种再生组合类型—— 单段再生、两段再生、快速再生
单段再生
反应-再生系统的热平衡
470~530 ℃, 吸热反应 反 应 器 600~750℃ 强放热反应 再生器
高温的再 生催化剂
冷的待生 催化剂
再生取热技术:
多余热量用于发电,发生蒸汽,可供本 车间与相邻车间使用。 内取热技术 外取热技术:
下行式取热器(图9第六节 反应-再生系统
1、学习了解反应-再生系统的流程、设 备及操作方式。 2、学习了解提升管反应器基本结构与工 艺特点,设计指标。 3、学习了解再生器基本类型、结构与工 艺特点,设计指标。 学习方法:课堂介绍提纲携领,主要内 容以自学为主。
一、提升管反应器
直径:由进料量决定。线速度:
入口处:4~7m/s;出口处:12~18m/s。 ;
常规再生 CO2/CO(体积比) 1—1.3 . 燃碳强度kg/t.h 80-100 再生剂 含碳量% 0.15—0.20 0.10—0.20 0.05—0.10 助燃剂再生 3—200 80—120 高温再生 200—300 100--120
两段再生
两器再生 (不取热) 两器再生 (带取热) 两器逆流 再生
第七节 再-反系统的工艺计算
设计计算的主要内容: 再生器的物料平衡,决定空气流率与烟 气流率。 再生器烧焦计算,决定催化剂藏量。 再生器热平衡,决定催化剂循环量。 反应器物料平衡、热平衡,决定原料预 热温度,结合再生器热平衡决定燃烧油 量或取热设施。
设计计算的主要内容(续):
再生器设备工艺计算:包括壳体、旋风 分离器、分布管(板)、淹流管、辅助 燃烧室、滑阀、稀相喷水等。 反应器设备工艺计算,包括气提段和进 料喷嘴的设计计算。 两器压力平衡,包括催化剂输送管路。 其它细节,如松动点的布置、限流孔板 的设计等。
稀相区:要求气速不能太高。
对于堆积密度较小的:0.6 ~0.7m/s; ; 对于堆积密度较大的:0.8 ~0.9m/s
从密相区至一级旋风分离器入口之间的空间 高度应大于TDH(分离空间高度)。 再生器内装有两级串联的旋风分离器。回收 固体颗粒的回收率为99.9%。 下部装有空气分布器:使空气沿整个床层均 匀分布。有碟形与分布管形两种。
单器再生
CO2/CO(体积比) 1.5—200 2—2.5 2—150 3--5 燃碳强度kg/t.h 150--200 80—120 80--120 60--80 再生剂 含碳量% 0.05-0.10 0.03-0.05 0.03-0.10 0.03-0.05
快速床再生
前置烧焦罐 CO2/CO(体积比) 50—200 燃碳强度kg/t.h 150--320 再生剂 含碳量% 0.05—0.20 后置烧焦罐 3—200 200—250 0.05—0.20 烧焦罐-湍流床 串联 50--200 200--350 0.05—0.10
二、再生器
国内最大的直径达16.8米。上段稀相段, 下部为密相段。 密相段的有效藏量:由烧碳负荷及烧碳 强度决定。
有效藏量——是指处于烧碳环境中的藏量。
密相区的直径:由空塔气速决定:
采用较低气速时为:0.8 ~1.0m/s 采用较高气速时为: 1.0~1.5m/s
密相区的床层高度一般为:5~7米。
高度:由反应时间确定:2~4s;
高温再生,汽-柴方案时:2s。并采用中止反应技 术或混合温度控制技术。
上端出口设有气-固快速分离设备。 下部对进料的雾化有较高的要求,尤其是重油 FCC。要迅速汽化、较高汽化率与催化剂均匀 接触。 沉降器下段的汽提作用:减少油气损失,减小 再生的烧焦负荷。
再生器——烧去焦碳恢复活性