第六节 催化裂化反应-再生系统
最新万吨年催化裂化反应—再生系统计算
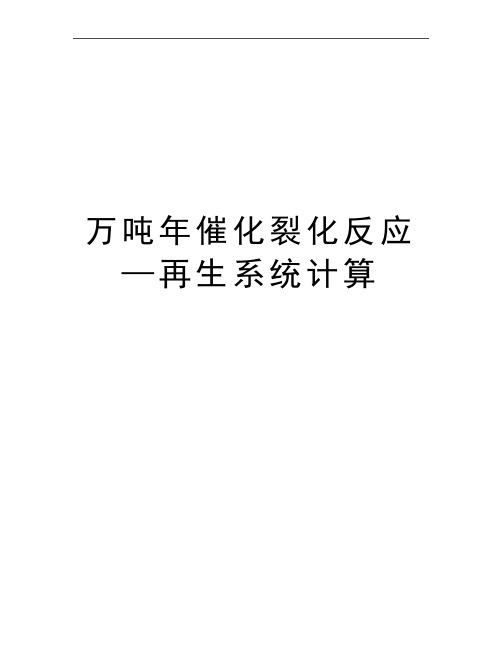
万吨年催化裂化反应—再生系统计算摘要催化裂化装置主要由反应—再生系统、分馏系统、吸收稳定系统和能量回收系统构成,其中反应—再生系统是其重要组成部分,是装置的核心。
设计中以大庆原油的混合蜡油与减压渣油作为原料,采用汽油方案,对装置处理量为250万吨/年(年开工8000小时)的催化裂化反应—再生系统进行了一系列计算。
根据所用原料掺油量低,混合后残炭值较低,其硫含量和金属含量都较小且由产品分布和回炼比较小,抗金属污染能力强,催化剂的烧焦和流化性能较好及在此催化剂作用下,汽油辛烷值较高这些特点,故采用汽油方案。
设计中,采用了高低并列式且带有外循环管的烧焦罐技术,并对烧焦罐式再生器和提升管反应器进行了工艺计算,其中再生器的烧焦量达32500㎏/h,烧焦罐温度为680℃,稀相管温度为720℃,由于烟气中CO含量为0,则采用高效完全再生。
在烧焦罐中,烧焦时间为1.8s,罐中平均密度为100㎏/m3,烧焦效果良好。
在提升管反应器设计中,反应温度为505℃,直径为1.62 m,管长为29 m,反应时间为3s,沉降器直径为2 m,催化剂在两器中循环,以减少催化剂的损失,提高气—固的分离效果,在反应器和再生器中分别装有旋风分离器,旋风分离器的料腿上装有翼阀,在提升管和稀相管出口处采用T型快分器。
由设计计算部分可知,所需产品产率基本可以实现。
关键词:催化裂化,反应器,再生器,提升管,烧焦罐,完全再生AbstractThe catalytic cracker constitutes reaction-regeneration system、fraction system、 absorption-stabilization system and power-recovery system. The most important and core part of the unit is reaction-regeneration system. The DaQing Crude wax oil and vacuumdistillation residue are taken as feedstock. This paper is a series of processing calculation mainly about reaction-regeneration system. With gasoline scheme, capacity is designed to be 150 Mt/a under the condition of 8000 hours’ operating time.After being mixed the contents of blending residuum, sulphur and metal as well as the carbon residue in feedstock are low. As the even distribution of product, superior properties of resisting metal pollution and the catalyst’s coke burning and fluidization as well as the higher octane number of gasoline with the function of this catalyst, the gasoline scheme are taken.In the design, technology of coke-burning drum with outsider-circulation tube is applied. The drum is of high-low parallel style. The processing calculation is about reproducer of coke-burning drum style and riser, coke-burning capacity is 32500㎏/h, the temperatures of coke-burning drum and dilute phase riser are respectively 680℃and 720℃. Accounting that there is no carbon monoxide in off-gase. The high efficient regeneration is applied. In the coke-burning drum, the scorching time is 1.8s and its average density is 100 ㎏/m3, thus the effect of coke-burning is good. The temperature of riser is 505℃. Its diameter is 1.62m and the length is 29m. While its reaction time is 3s and the diameter of settling vessel is 2m. Catalysts circulate in the drum and reactor. In order to reduce the loss of catalyst and improve the effect of gas-solid separation, cyclones are equipped in both reactor and reproducer. There is trickle vavle on the dipleg of the latter, whilethe T-rapid separation unit is fitted in the exit of riser and dilute phase riser. From the date, the unit can substantially reach the required yield. Keywords: Catalystic cracking, Reactor, Reproducer, Riser, Coke-burning drum毕业设计(论文)原创性声明和使用授权说明原创性声明本人郑重承诺:所呈交的毕业设计(论文),是我个人在指导教师的指导下进行的研究工作及取得的成果。
催化裂化反再系统培训 资料
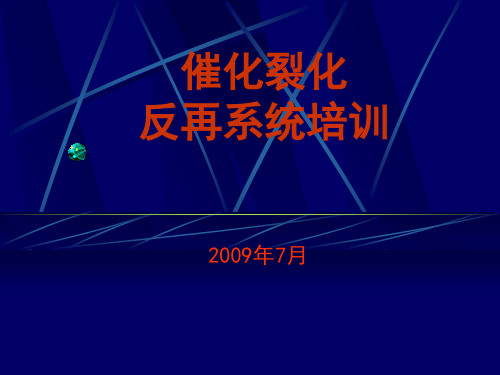
反应特点
1、各类烃之间的竞争吸附和对反应的阻滞作用 从以上分析看出,吸附能力强的烃分子将首先占据催化剂 活性中心进行反应。 但若吸附能力强,反应能力却差,则会阻碍其它烃分子反 应。 在一定反应条件下,各种烃类在催化剂上的吸附能力和反 应能力有很大差别 吸附能力:
稠环芳烃>稠环环烷烃>烯烃>单烷基侧链单芳>环烷烃>烷烃
催化裂化再生过程
催化裂化催化剂
催化剂:能够改变化学反应速度而本身 不发生化学反应的物质 催化剂能有选择性地促进某些反应 催化剂不仅对装置的生产能力、产品产 率及质量好坏、经济效益起主要影响, 而且对操作条件、工艺过程和设备型式 的选择有重要影响。
裂化催化剂的失活与再生
催化剂的失活 :在反应过程中,裂化催化剂的活性和选择性不断 下降的现象称为催化剂的失活。失活原因主要有:高温或高温与 水蒸气的作用;裂化反应生焦;毒物的毒害。
反应沉降器在提升管反应器的上部,沉 降器分为两部分,上部为沉降段,下部 为汽提段。 沉降段内设有四组单级旋分器,顶部为 集气室。提升管反应器出来的反应油气 和催化剂进入反应沉降器进行催化剂和 油气的自由沉降分离,没有沉降下来的 催化剂随油气进入设在沉降器顶部的旋 风分离器进行继续进行分离,分离后油 气经集气室去分馏单元。
催化裂化反应
催化裂化进料
烃类在催化剂 表面发生反应
循环使用 烧焦 催化剂恢复活性 再生 催化剂活性下降 分解 缩合 气体和轻油 沉积在催化剂上
催化裂化特征
催化裂化反应类型
(1)裂化反应 催化裂化的主要反应是裂化反应,反应速度快。各
类烃的裂化反应规律:
烷烃:分子中间C-C键断裂,分子越大,越易断裂;碳 数相同的链状烃中,异构比正构易反应 烯烃:与烷烃类似,速度比烷烃高得多 环烷烃:断侧链和开环
催化裂化装置反应再生系统工艺流程
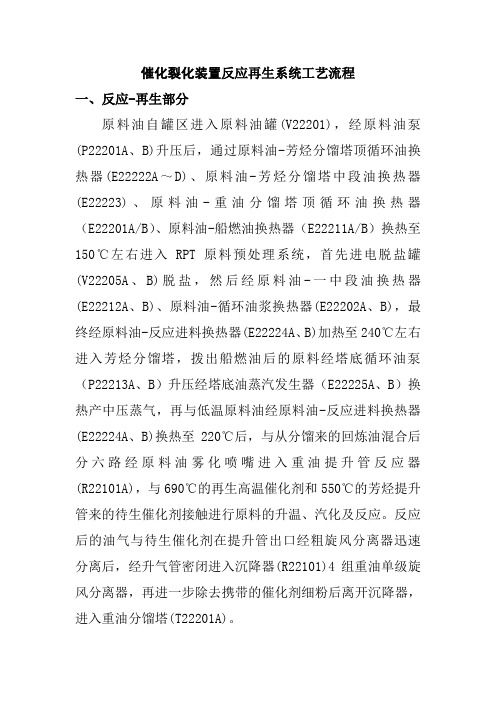
催化裂化装置反应再生系统工艺流程一、反应-再生部分原料油自罐区进入原料油罐(V22201),经原料油泵(P22201A、B)升压后,通过原料油-芳烃分馏塔顶循环油换热器(E22222A~D)、原料油-芳烃分馏塔中段油换热器(E22223)、原料油-重油分馏塔顶循环油换热器(E22201A/B)、原料油-船燃油换热器(E22211A/B)换热至150℃左右进入RPT原料预处理系统,首先进电脱盐罐(V22205A、B)脱盐,然后经原料油-一中段油换热器(E22212A、B)、原料油-循环油浆换热器(E22202A、B),最终经原料油-反应进料换热器(E22224A、B)加热至240℃左右进入芳烃分馏塔,拨出船燃油后的原料经塔底循环油泵(P22213A、B)升压经塔底油蒸汽发生器(E22225A、B)换热产中压蒸气,再与低温原料油经原料油-反应进料换热器(E22224A、B)换热至220℃后,与从分馏来的回炼油混合后分六路经原料油雾化喷嘴进入重油提升管反应器(R22101A),与690℃的再生高温催化剂和550℃的芳烃提升管来的待生催化剂接触进行原料的升温、汽化及反应。
反应后的油气与待生催化剂在提升管出口经粗旋风分离器迅速分离后,经升气管密闭进入沉降器(R22101)4组重油单级旋风分离器,再进一步除去携带的催化剂细粉后离开沉降器,进入重油分馏塔(T22201A)。
重油分馏塔分馏后的塔顶油气经冷凝冷却后进入油气分离器(V22203A),分离出的粗轻燃油分四路经雾化喷嘴进入芳烃提升管反应器(R22101B),与690℃催化剂接触进行原料的升温、汽化及反应。
反应后的油气与待生催化剂在提升管出口经粗旋风分离器迅速分离后,经升气管密闭进入沉降器内轻燃油单级旋风分离器,再进一步除去携带的催化剂细粉后离开沉降器,进入芳烃分馏塔(T22201B)。
油气分离出来的待生催化剂与重油部分的待生催化剂一起进入反应沉降器的汽提段。
催化裂化

再生器的主要作用是烧去催化剂上因反应而生成的积炭, 使催化剂的活性得以恢复。再生用空气由主风机供给,空气通 过再生器下面的辅助燃烧室及分布管进人流化床层。 催化剂(称再生催化剂)落人淹流管,经再生斜管送回反应器 循环使用。再生烟气经旋风分离器分离出夹带的催化剂后,经双 动滑阀排人大气。 再生烟气的温度很高,不少催化裂化装置设有烟气能量回收 系统,利用烟气的热能和压力能(当设能量回收系统时,再生器的 操作压力应较高些)做功,驱动主风机以节约电能,甚至可对外输 出剩余电力。对一些不完全再生的装置,再生烟气中含有5%-10% (体积分数)的CO,可以设CO锅炉使CO完全燃烧以回收能量。
工艺流程概述
包括:反应-再生系统、分馏系统、吸收-稳定系 统、再生烟气的能量回收系统和液化气、汽油的 脱硫精制等 1.反应—再生系统
高低并列式提升管催化裂化装置的工艺流程
470~510 ℃
3 ~4s
650~700 ℃
300~380 ℃
新鲜原料油经换热后与回炼油浆混合,经加热 炉加热后至催化裂化提升管反应器下部的喷嘴,原 料油由蒸气雾化并喷入提升管内,在其中与来自再 生器的高温催化剂接触,随即汽化并进行反应。
进入分馏塔的油气含有相当大量的不凝气和惰性气
体,它们会影响塔顶冷凝冷却器的效果 提高富气压缩机的入口压力以降低气压机的功率损
耗
3.吸收—稳定系统
主要由吸收塔、解吸塔、再吸收塔及稳定塔组成。
第六节催化裂化反应再生系统资料
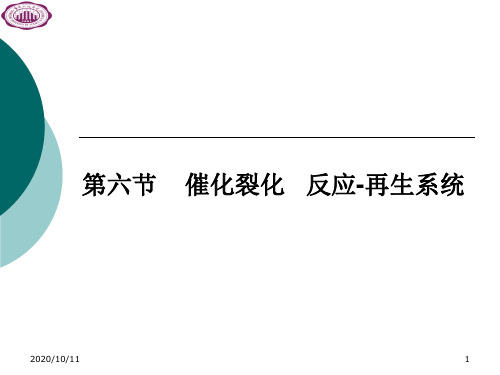
2020/10/11
19
c.快速床(循环流化床)再生 ➢气相转化成连续相,催化剂颗粒变为分散相,从而强化 了烧碳过程 ➢随着气速的提高,返混程度减小,中、上部接近于平推 流,也有利于烧碳强度的提高 ➢在快速流化床区域,必须有较大的固体循环量才能保持 较高的床层密度 ➢催化裂化装置的烧焦罐再生就是属于循环流化床的一种 再生方式
➢再生温度对烧碳反应速率的影响十分显著,提高再生温 度是提高烧碳速率的有效手段,在单段再生时,密相创层 的温度一般不超过730℃
➢工业上一般采用的空气线速为0.6~0.7m/s ➢工业装置采用的再生器压力在0.25~0.4MPa(绝)之间 ➢单段再生的主要问题是再生温度的提高受到限制和密相 床层的有效催化剂含炭量低
9
分段反应
➢不同的馏分需要不同的反应条件,理想选择是不同的 馏分在不同的场所和条件下进行反应 ➢两段提升管(Ⅰ型)催化裂化:
★第一段提升管只进新鲜原料,段间抽出柴油出装置 ★第二段提升管单独进循环油,显著改善产品分布 ★第二段提升管底部回炼汽油,降低汽油烯烃含量 ➢分段进料避免了新鲜原料和油浆的相互干扰
2020/10/11
18
b.两段再生 ➢两段再生是把烧碳过程分为两个阶段进行 ➢与单段相比,两段再生的主要优点是:
①对于全混床反应器,第一段出口的半再生剂的含碳量 高于再生剂的含碳量,从而提高了烧碳速率;
②在第二段再生时可以用新鲜空气和更高的温度,提高 了烧碳速率;
③第二段内的水气分压可以很低,减轻了催化剂的水热 老化;且第二段的催化剂藏量比单段再生器的催化剂藏量低, 停留时间较短。因此,第二段可采用较高的再生温度。
2020/10/11
20
2020/10/11
21
重油催化裂化的反应—再生系统

重油催化裂化的反应—再生系统
崔璀
【期刊名称】《《石油化工设备技术》》
【年(卷),期】1991(012)001
【摘要】镇海石化总厂炼油厂催化裂化装置原设计为120×10~4t/a 蜡油催化裂化。
为解决重油出路,提高轻油收率,于1985年从美国 S&W 公司引进重油催化技术,对原装置进行改造。
从1987年开始,利用每年的停工检修时间分期进行施工,全部改造工程于1990年6月完成,投运试车一次成功,产品质量和收率均达到了设计要求。
一、反应—再生系统改造简介1.进料喷嘴提升管/沉降器为原有设备,为适应重油催化的需要作了部分改动。
【总页数】5页(P54-58)
【作者】崔璀
【作者单位】
【正文语种】中文
【中图分类】TE626.25
【相关文献】
1.重油催化裂化装置再生系统的技术改造 [J], 焦伟州;赵振辉;刘耀宇
2.MPC 在重油催化裂化反应-再生系统控制中的应用 [J], 郭锦标;房(韦华);高维进;魏国志
3.重油催化裂化反应-再生系统的热平衡控制研究 [J], 霍彦斌;温杰
4.重油催化裂化反应-再生系统的热平衡控制 [J], 康明艳;李钒;伍丽娜
5.重油催化裂化反应-再生系统的热平衡控制 [J], 康明艳;李钒;伍丽娜;孙津清因版权原因,仅展示原文概要,查看原文内容请购买。
催化裂化再生系统

1再生动力学1.1催化剂上的焦炭1)焦炭的化学组成催化剂上的焦炭来源于四个方面:⑴在酸性中心上由催化裂化反应生成的焦炭;⑵由原料中高沸点、高碱性化合物在催化剂表面吸附,经过缩合反应生成的焦炭;⑶因汽提段汽提不完全而残留在催化剂上的重质烃类,是一种富氢焦炭;⑷由于镍、钒等重金属沉积在催化剂表面上造成催化剂中毒,促使脱氢和缩合反应的加剧,而产生的次生焦炭;或者是由于催化剂的活性中心被堵塞和中和,所导致的过度热裂化反应所生成的焦炭。
上述四种来源的焦炭通常被分别称为催化焦、附加焦(也称为原料焦)、剂油比焦(也称为可汽提焦)和污染焦。
实际上,这四种来源的焦炭在催化剂上是无法辩认的。
所谓“焦炭”并不是具有严格的固定组成和结构的物质。
它不是纯碳,一般主要由碳和氢组成,是高度缩合的碳氢化合物,但碳和氢的比例受多种因素的影响,有相当大的变化范围。
影响H/C的因素主要有:催化剂、原料、反应温度、反应时间及汽提条件等。
对一定的催化剂和原料,影响焦炭H/C的主要因素是反应温度和反应时间(或结焦量)。
普遍认为,反应温度越高,焦炭的H/C越小,即焦炭中氢含量越低。
反应时间加长也有同样的影响。
在硅酸铝催化剂上用多种单体烃和轻瓦斯油进行催化裂化反应试验,结果表明所得焦炭的H/C不相同,而在0.4~0.9之间变化。
除碳和氢外,焦炭中还可能含有硫、氮、氧等杂原子,这主要决定于原料的杂原子化合物的含量。
应该指出,焦炭的化学组成,是焦炭的一个重要性质,尤其是C/H,对再生器的操作,特别是对装置的热平衡具有重要意义。
但很遗憾,焦炭的C/H很难测定准确,主要是氢含量很难测准,因为一般用燃烧法测定生成的水量,而水量难以测准,而且在燃烧过程中催化剂结构本身也可能放出一部分水,因而造成实验误差。
在生产装置上,一般还是以测定烟气中CO、CO2和O2的组成,利用焦炭在空气中燃烧时的元素平衡等计算焦炭中的C/H比。
2)焦炭的结构前面谈到焦炭的化学组成是不均匀的,而焦炭的结构与其组成密切相关,可以想象,焦炭的结构也是不均匀的,实际研究结果也证明了这一点,而且结构问题比组成更为复杂。
第六节 催化裂化反应-再生系统概述

2018/11/5
21
催化裂化主要设备
1、预提升段 2、裂化反应段 3、汽提段
2018/11/5
22
催化裂化主要设备
预提升段:加速催化剂,使催化剂形成活塞流向
上流动,使催化剂上的重金属钝化,有利于油雾
的快速混合,一般为3-6m。
裂化反应段:提供裂化反应的场所。
中止反应技术(MTC)
2018/11/5 11
两段与单段实验室结果对比:
轻油收率可提高 2-3 个百分点 原料转化深度提高 5 个百分点
汽油烯烃含量下降12-13个百分点
液收率提高2.5个百分点以上 干气产率大幅度降低 可显著提高柴汽比
2018/11/5
12
两段与单段工业试验结果对比:
轻油收率提高4个百分点以上
第六节
催化裂化 反应-再生系统
2018/11/5
1
催化裂化装置一般有四部分构成:反应-再生系统,分
馏系统,吸收-稳定系统和能量回收系统
装置形式主要有高低并列式、同轴式等
2018/11/5
2
一:提升管反应器
提升管反应器主要有提升管、沉降器、汽提段、旋分 器、待生斜管等部分组成
2018/11/5
2018/11/5
6
两段提升管 FCC技术的思想及特点
两段FCC技术的基本思想:
★提高催化裂化催化剂的有效活性和选择性,从而改
善目的产品分布;
★分段反应,提高调整生产方案的灵活性
因此,两段提升管FCC技术打破原来的提升管反应器型 式和反-再系统流程: ★两段提升管反应器取代单一反应器 ★构成拥有两路循环的反应-再生系统
催化裂化反应-再生系统的失效模式、效应和危害度分析

械造 故问
了 分 析, 并 建 立 了 催 化 裂 化 故 障 树 分 析 模 型 ( FTA),本文针对催化裂化反应-再生系统建立了 FMECA 方法,为催化裂化装置的可靠性分析和长 周期安全运行提供理论指导。该方法可以推广应用
于同类炼油厂催化裂化装置的可靠性分析及风险性 评价,具有显著的经济效益和工程应用价值。
应 反 焦 壁 正常 环
质量含量;
应
上
裂解
量 (4)选择合格的反应条件和温度。
产
器 生 膨 露 液 体 液 (l)更换材料,选超低碳钢或双向不锈钢;
油 胀 点 漏 出 体 (2)制造成型后应进行稳定化热处理;
节
影响
气 裂 腐 反 应 漏 (3)保证反应温度在露点以上;
开 蚀 进 行 出 (4)避免液相设计时防止膨胀节受剪力。
事件
编号 x13 x14 x15 x16 x17 x18 x19 x20 x21 x22 x23
相对概率重要度 IC
1. 902505 > 10 - 2 3. 261519 > 10 - 2 2. 717905 > 10 - 2 6. 802927 > 10 - 1 6. 522725 > 10 - 3 3. 261519 > 10 - 2 3. 261519 > 10 - 2 6. 522725 > 10 - 3 6. 522725 > 10 - 3 5. 436083 > 10 - 2 5. 435593 > 10 - 3
利用 FMECA 很容易分析各层次之间的因果关 系,而 FTA 很容易考虑人为因素、环境因素或多 种因素相互组合对顶事件的影响。在可靠性分析 时,FMECA 可以与 FTA 分析方法结合使用,综合 使用的基本原理是根据系统的功能要求和故障定 义,首先选择一个或多个系统中不希望发生的事件
简述催化裂化反应再生系统流程

简述催化裂化反应再生系统流程下载温馨提示:该文档是我店铺精心编制而成,希望大家下载以后,能够帮助大家解决实际的问题。
文档下载后可定制随意修改,请根据实际需要进行相应的调整和使用,谢谢!并且,本店铺为大家提供各种各样类型的实用资料,如教育随笔、日记赏析、句子摘抄、古诗大全、经典美文、话题作文、工作总结、词语解析、文案摘录、其他资料等等,如想了解不同资料格式和写法,敬请关注!Download tips: This document is carefully compiled by theeditor. I hope that after you download them,they can help yousolve practical problems. The document can be customized andmodified after downloading,please adjust and use it according toactual needs, thank you!In addition, our shop provides you with various types ofpractical materials,such as educational essays, diaryappreciation,sentence excerpts,ancient poems,classic articles,topic composition,work summary,word parsing,copy excerpts,other materials and so on,want to know different data formats andwriting methods,please pay attention!催化裂化反应再生系统是石油炼制过程中的重要环节,其主要作用是将重质油转化为轻质油和气体产品。
第六讲 催化裂化
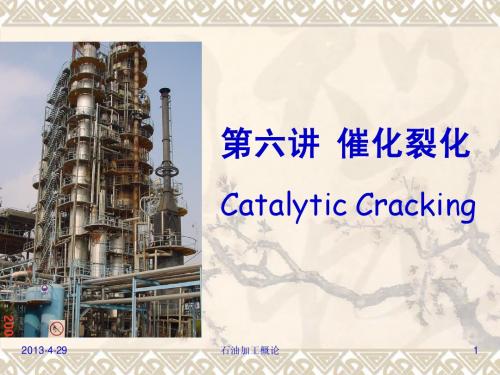
一、单体烃的催化裂化反应
1.各类单体烃的裂化反应 .
(1). 烷 烃 烷烃主要发生分解反应,例如 : 烷烃主要发生分解反应,
C16H34
C8H16 + C8H18
生成小分子的烷烃和烯烃, 生成小分子的烷烃和烯烃 , 生成的烷烃还可以进一步 分解成更小的分子。 分解成更小的分子。
2012-1-5
石油加工概论
11
三、催化裂化工艺流程概述
包括:反应-再生系统、分馏系统、吸收-稳定系 包括:反应-再生系统、分馏系统、吸收再生烟气的能量回收系统和液化气、 统、再生烟气的能量回收系统和液化气、 汽油的脱硫精制等 1.反应—再生系统 反应— 高低并列式提升管催化裂化装置的工艺流程 高低并列式提升管催化裂化装置的工艺流程
2012-1-5
石油加工概论
24
高低并列式
反应器位置较高,两器压力不同, 反应器位置较高,两器压力不同,一般再生器比反应器 02~ Pa。 的压力高 0.02~0.04 M Pa。 催化剂在两器中循环,用斜管输送,并由滑阀调节。 催化剂在两器中循环,用斜管输送,并由滑阀调节。滑 阀的材质要满足耐磨要求。 阀的材质要满足耐磨要求。
2012-1-5 石油加工概论 2
重质油加工技术
2012-1-5
石油加工概论33一、Fra bibliotek化裂化的原料和产品
催化裂化是目前石油炼制工业中最重要的二次加工过程, 催化裂化是目前石油炼制工业中最重要的二次加工过程, 二次加工过程 重油轻质化的核心工艺 是提高原油加工深度、 也是重油轻质化 也是重油轻质化的核心工艺 ,是提高原油加工深度、 增加轻质油收率的重要手段。 我国约 80% 的汽油和 增加轻质油收率的重要手段 。 我国 约 1/3 的柴油均来自该工艺,总加工能力约 1.4 亿吨 年 的柴油均来自该工艺 均来自该工艺, 亿吨/年 催化裂化原料:重质馏分油(减压馏分油 催化裂化原料:重质馏分油(减压馏分油VGO 、焦化馏 分油CGO(通常须经加氢精制))、常压重油、减压渣 (通常须经加氢精制) 常压重油、 分油 掺一部分馏分油) 脱沥青的减压渣油、 油 ( 掺一部分馏分油 ) 、 脱沥青的减压渣油 、 加氢处理 重油等 重油等
催化裂化反应再生系统的建模与优化
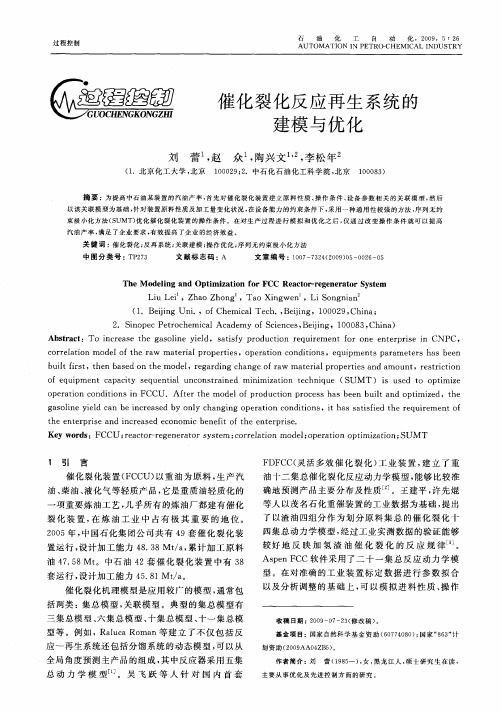
石
油
化
工
自
动
化 ,2 0 ,5:2 09 6
AUT0M AT1 0N N I PETR0一 CHEM I CAL NDUSTRY I
催 化 裂 化 反 应 再 生 系统 的 建 模 与优 化
刘 蕾 赵 , 众 陶兴 文 李 松 年 , 一,
108) 0 0 3 (.北 京 化 工 大学 , 京 1 北 1 0 2 ;.中石 化 石 油 化 工 科 学 院 , 京 0 0 92 北
o q i me t c p ct e u n i l u c n t a n d mi i ia i n t c n q e ( UM T ) i s d t p i z f e u p n a a iy s q e t n o s r i e n m z t e h i u a o S s u e o o tmie
b i is ,t e a e nt em o e , e a dn h n eo a ma e il r p r isa da u t e tito u l f t h n b s do h d l r g r ig c a g f w t r o e t n mo n ,r srcin t r r ap e
Li i u Le ,Zha on , Ta n o Zh g o Xi gw e n ,LiSo ni n ng a
( .Be ig Un.,o e c lTe h B in 1 in i j fCh mia c ., ej g,1 0 2 Chn ; i 0 0 9, ia 2 io e e r c e c lAc d myo ce c s Bej g 0 0 3 Ch n ) .S n p cP to h mia a e fS in e , i n ,1 0 8 , ia i
石油催化裂化—反再系统工艺流程介绍

类型:单段再生
两段再生
快速流化床再生
2、再生器
催化剂堆积密度 较小 较大
稀相区气速 0.6 - 0.7 m/S 0.8 - 0.9 m/s
5-7m
稀相区 密相区
两级串联 旋风分离器
分离效率 99.99%
2、再生器
(分 碟布 形板 )式
目的:使烧焦空气进入床层时沿截面分布均匀
空气分布器
( 平 面 分树 布枝 管形 式和 环 形 )
3、取热器
3、取热器
内
外
取
取
热
热
4、主风机
作用:
➢ 提供烧焦所需的氧气; ➢ 保证再生器、烧焦罐内的
催化剂处于流化状态
课程小结
反
再
提升管反应器
系
统
再生器
典 型
取热器
设
主风机
备
提升管 快速分离器 旋风分离器
沉降器 汽提段
• 含催化剂颗粒的气体 • 由切线方向进入筒体 • 形成高速旋转的外涡流
• 颗粒被甩向器壁 • 落入灰斗 • 返回密相床层
• 气体受中心低压区吸引 • 形成向上内涡流 • 通过升气管排出
4.沉降器
沉降器:
利用重力的差别使流体(气体或液体)中的固体颗粒沉降的设备。
➢ 将气溶胶或悬浮液导入器内,经一定时间的静置或极慢的 流动,然后将沉降物导出器外。
课程:石油炼制运行与操控
知识点:反再系ห้องสมุดไป่ตู้典型设备
催化裂化
反应-再生系统 分馏系统 吸收-稳定系统
反再系统典型设备
1、提升管反应器
提升管反应器
提
快 速
旋 风
沉
汽
升
第六节 催化裂化反应-再生系统
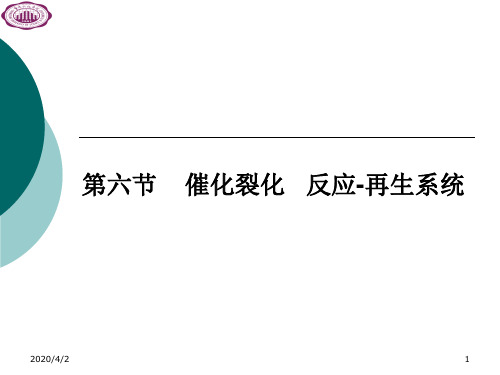
6
两段提升管 FCC技术的思想及特点
➢两段FCC技术的基本思想: ★提高催化裂化催化剂的有效活性和选择性,从而改 善目的产品分布; ★分段反应,提高调整生产方案的灵活性
➢因此,两段提升管FCC技术打破原来的提升管反应器型 式和反-再系统流程:
★两段提升管反应器取代单一反应器 ★构成拥有两路循环的反应-再生系统
2020/4/2
19
c.快速床(循环流化床)再生 ➢气相转化成连续相,催化剂颗粒变为分散相,从而强化 了烧碳过程 ➢随着气速的提高,返混程度减小,中、上部接近于平推 流,也有利于烧碳强度的提高 ➢在快速流化床区域,必须有较大的固体循环量才能保持 较高的床层密度 ➢催化裂化装置的烧焦罐再生就是属于循环流化床的一种 再生方式
2020/4/2
10
短反应时间
两段技术,采用分段反应,两段反应时间之和比常规 催化反应时间还短(2秒以内)
大剂油比
受热平衡控制,常规催化的剂油比难以提高,两段催 化采用两路催化剂循环,从设备角度提高剂油比可不受限 制;第一段的低转化率和汽油回炼改质可以突破原有热平 衡的限制,在较高的剂油比(催化剂/催化原料)下实现 新的热平衡
2020/4/2
7
两段提升管反应器示意图
2020/4/2
8
催化剂接力 ➢原料在第一段提升管经过短反应时间后,及时 将催化剂与油气分开;需要继续反应的中间物料 在第二段提升管与另一路再生催化剂接触反应 ➢催化剂两路循环,整体活性及选择性提高 ➢催化反应比例增大,热反应得到有效抑制
2020/4/2
9
快速床循环流化床再生?气相转化成连续相催化剂颗粒变为分散相从而强化了烧碳过程气相转化成连续相催化剂颗粒变为分散相从而强化了烧碳过程?随着气速的提高返混程度减小中上部接近于平推流也有利于烧碳强度的提高随着气速的提高返混程度减小中上部接近于平推流也有利于烧碳强度的提高?在快速流化床区域必须有较大的固体循环量才能保持较高的床层密度在快速流化床区域必须有较大的固体循环量才能保持较高的床层密度?催化裂化装置的烧焦罐再生就是属于循环流化床的一种再生方式催化裂化装置的烧焦罐再生就是属于循环流化床的一种再生方式201771221201771222催化裂化主要设备1预提升段2裂化反应段3汽提段201771223催化裂化主要设备?预提升段
7催化裂化

31
(2)空速和反应时间
催化剂藏量:在流化床催化裂化反应装置中,催化 剂不断地在反应器和再生器之间循环。但是在任何 时间,两器内部各自保持有一定的催化剂量。两器 内经常维持的催化剂量称为藏量。
催化剂循环量:单位时间进入反应器的催化剂量, 也就是离开反应器的催化剂量。
空速:是指每小时进入反应器的总进料量与器内的 催化剂藏量之比。单位:h-1
24
(4)较小的正碳离子与烯烃、烷烃、环烷烃之间 的氢转移反应; (5)正碳离子和烯烃接合在一起生成大分子的正 碳离子(叠合反应); (6)各种反应最后都由正碳离子放出质子(H+)还给 催化剂而变成烯烃,反应终止。
25
三、 催化裂化反应的特点
1、烃类催化裂化是气—固非均相反应,各类烃之间 的竞争吸附对反应有阻滞作用。
重质石油馏分
中间馏分 缩合产物
汽油
气体 焦炭
各产品产率与转化率的关系 二次反应 回炼油、回炼操作
28
四、重油(渣油)催化裂化反应的特点
焦炭产率较高、轻质油收率较低 多环芳烃、稠环芳烃难裂化 沥青质基本转化为焦炭 胶质易生成焦炭 渣油可先进行溶剂脱沥青 气-液-固三相反应 雾化、汽化等状况对结果影响大 大分子先在载体上反应再进入分子筛微孔内反应
2
第一节 概述
一、催化裂化在炼油工业中的作用
催化裂化是使重质馏分油或重油、渣油在催化剂 存在下,在温度为460~530℃和压力为0.1~0.3MPa 条件下, 经过以裂解为主的一系列化学反应, 转化 成气体、汽油、柴油以及焦炭等的过程。
3
对轻质油的需求量大,质量要求高 原油常减压蒸馏轻质油10~40%,MON40~60 我国车用汽油中催化裂化汽油占80%以上,催 化汽油RON可达~90 催化裂化是重质油轻质的主要手段 2001年底,中国的实际原油加工能力为280Mt/a, 催化裂化加工能力约为100 Mt/a,催化裂化占 原油加工能力之比为35.7%。 催化裂化是提高炼厂经济效益的重要加工过程
催化裂化反应再生系统流程

催化裂化反应再生系统流程
1. 新鲜原料油经换热后与回炼油浆混合,经加热炉加热至180-320℃后至催化裂化提升管反应器下部的喷嘴。
2. 原料油由蒸气雾化并喷入提升管内,在其中与来自再生器的高温催化剂(600-750℃)接触,随即汽化并进行反应。
3. 油气在提升管内的停留时间很短,一般只有几秒钟。
反应产物经旋风分离器分离出夹带的催化剂后离开沉降器去分馏塔。
4. 积有焦炭的催化剂(称待生催化剂)由沉降器落入下面的汽提段。
汽提段内装有多层人字形挡板并在底部通入过热水蒸气,待生催化剂上吸附的油气和颗粒之间的空间内的油气被水蒸气置换出而返回上部。
5. 经汽提后的待生催化剂通过待生斜管进人再生器。
再生器的主要作用是烧去催化剂上因反应而生成的积炭,使催化剂的活性得以恢复。
6. 再生后的催化剂(称再生催化剂)落人淹流管,经再生斜管送回反应器循环使用。
再生烟气经旋风分离器分离出夹带的催化剂后,经双动滑阀排人大气。
催化裂化装置反应再生部分控制系统设计
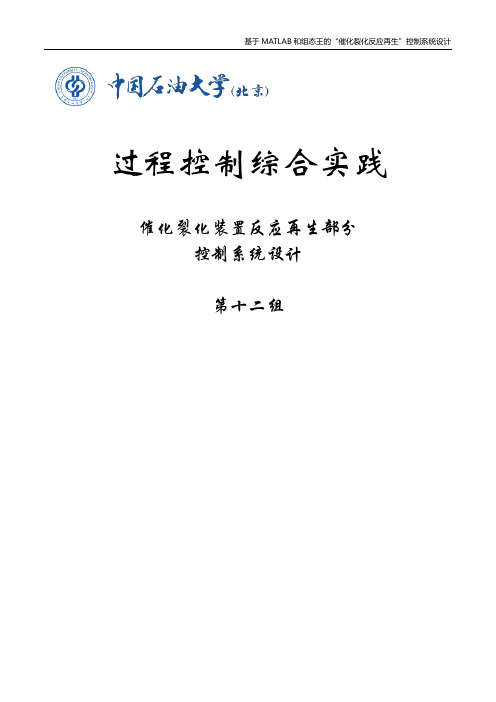
过程控制综合实践催化裂化装置反应再生部分控制系统设计第十二组目录第一章系统分析 (1)一、工艺流程 (1)二、控制需求分析 (2)三、对象特性分析 (2)1.控制系统特点 (2)2.控制系统扰动 (2)3.控制难点 (2)第二章控制系统详细的设计 (3)一、系统变量设置 (3)二、控制回路设计 (3)三、安全联锁报警设计 (4)四、I/O表 (5)第三章设备选型与图纸绘制 (6)一、控制器选型 (6)二、调节阀选型 (6)三、测量变送装置选型 (7)四、PLC接线图 (7)1.CPU224接线端子图 (7)2.EM235接线端子图 (8)3.控制柜接线图 (8)4.控制柜柜门设计图 (9)五、系统图纸绘制 (9)1.P&ID图图纸规格 (9)2.P&ID图的内容 (9)3.P&ID图中设备 (10)4.P&ID图中管道 (10)5.P&ID图代号和图例 (10)6.其它 (10)第四章MATLAB仿真研究 (11)一、基于MATLAB的控制对象仿真 (11)1.参考模型FCC——Linear (11)2.对象特性的阶跃响应测试 (12)二、数字控制器的设计 (12)三、控制参数对控制性能的影响及参数整定 (13)1.PID的三个调整参数对控制系统的影响 (13)2.参数整定结果 (14)第五章MATLAB与组态王的DDE连接 (17)一、动态数据交换 (17)二、组态王DDE功能 (17)三、MATLAB与组态王建立连接 (17)第六章组态王监控软件的详细设计 (20)一、组态王监控软件的界面设计 (20)二、监控软件功能设计 (20)1.工艺流程画面 (20)2.总体实时监控画面 (21)3.各个回路独立监控画面 (21)4.数据报表画面 (22)5.报警画面及报警查询画面 (23)6.总控制室画面 (23)7.标签画面 (23)三、设计过程 (23)1.建立组态王新工程 (23)2.创建组态画面 (24)3.定义I/O设备 (24)4.构造数据库 (24)5.建立动画连接 (24)6.运行和调试 (24)第七章实验结果及分析 (25)一、系统使用流程 (25)二、实际运行效果 (25)1.阶跃响应实时曲线 (26)2.性能指标整理 (26)3.鲁棒性实验 (27)三、控制系统性能分析 (28)1.控制方案优点 (28)2.控制方案缺点 (28)3.模型改进 (29)第八章感受和建议 (30)一、设计感受 (30)二、遇到的一些问题 (30)第一章系统分析催化裂化(Fluid Catalytic Cracking)是原油二次加工的核心工艺。
催化裂化的装置简介及工艺流程

催化裂化的装置简介及工艺流程概述催化裂化技术的发展密切依赖于催化剂的发展。
有了微球催化剂,才出现了流化床催化裂化装置;分子筛催化剂的出现,才发展了提升管催化裂化。
选用适宜的催化剂对于催化裂化过程的产品产率、产品质量以及经济效益具有重大影响。
催化裂化装置通常由三大部分组成,即反应/再生系统、分馏系统和吸收稳定系统。
其中反应––再生系统是全装置的核心,现以高低并列式提升管催化裂化为例,对几大系统分述如下:(一)反应––再生系统新鲜原料(减压馏分油)经过一系列换热后与回炼油混合,进入加热炉预热到370℃左右,由原料油喷嘴以雾化状态喷入提升管反应器下部,油浆不经加热直接进入提升管,与来自再生器的高温(约650℃~700℃)催化剂接触并立即汽化,油气与雾化蒸汽及预提升蒸汽一起携带着催化剂以7米/秒~8米/秒的高线速通过提升管,经快速分离器分离后,大部分催化剂被分出落入沉降器下部,油气携带少量催化剂经两级旋风分离器分出夹带的催化剂后进入分馏系统。
积有焦炭的待生催化剂由沉降器进入其下面的汽提段,用过热蒸气进行汽提以脱除吸附在催化剂表面上的少量油气。
待生催化剂经待生斜管、待生单动滑阀进入再生器,与来自再生器底部的空气(由主风机提供)接触形成流化床层,进行再生反应,同时放出大量燃烧热,以维持再生器足够高的床层温度(密相段温度约650℃~680℃)。
再生器维持0.15MPa~0.25MPa(表)的顶部压力,床层线速约0.7米/秒~1.0米/秒。
再生后的催化剂经淹流管,再生斜管及再生单动滑阀返回提升管反应器循环使用。
烧焦产生的再生烟气,经再生器稀相段进入旋风分离器,经两级旋风分离器分出携带的大部分催化剂,烟气经集气室和双动滑阀排入烟囱。
再生烟气温度很高而且含有约5%~10%CO,为了利用其热量,不少装置设有CO锅炉,利用再生烟气产生水蒸汽。
对于操作压力较高的装置,常设有烟气能量回收系统,利用再生烟气的热能和压力作功,驱动主风机以节约电能。
催化裂化装置反应再生系统认知

• (十二)反应深度的控制
• 反应深度是一个综合参数,直接影响产品分布。深度变化对轻油收率,生焦量 等起关键作用,可以说它对整个催化装置的经济效益起决定性作用。一般反应 温度:反应温度高,反应深度大。剂油比:剂油比大,反应深度大。再生催化 剂定碳低,催化剂活性高,再生剂温度高,反应深度大。
• (八)氧分压
• 烧焦速度与再生烟气中氧分压成正比,氧分压是再生压力与烟气中氧的分子浓 度的乘积。提高再生压力,或提高主风量增加烟气中氧的分子浓度,都会提高 氧分压。
• 烟气中氧分压对烧焦速度的影响相当明显,氧分压由1%上升到 2%,烧焦速度 上升18%,对于二段完全再生装置, 因二次燃烧的可能性大大降低,为获得 高烧焦速度,进入烟道的再生烟气中的氧含量一般控制在2~5%。
• (九)催化剂性质 • 催化裂化催化剂属于固体强酸催化剂,主要由分子筛、担体、粘结剂构成,主
要成份氧化铝、氧化硅及稀土、磷等改性元素组成。
• ①平衡剂活性 • ②再生剂含碳量 • ③催化剂的重金属污染
• (十)原料性质
• 原料油性质是所有操作条件中最重要的条件,选择催化剂牌号, 制定生产方 案,选择操作条件,都应首先了解原料油性质。生产中我们要求原料性质相对 稳定,同时加工几种性质不同的原料时,要在原料罐或管道中调合均匀再进提 升管反应器,并要求分析单位预先评价。原料带水会造成装置操作波动,严重 时甚至会造成事故。理想的催化裂化原料是H/C比高,CA、残炭低,密度小 (K值大),含水少。
- 1、下载文档前请自行甄别文档内容的完整性,平台不提供额外的编辑、内容补充、找答案等附加服务。
- 2、"仅部分预览"的文档,不可在线预览部分如存在完整性等问题,可反馈申请退款(可完整预览的文档不适用该条件!)。
- 3、如文档侵犯您的权益,请联系客服反馈,我们会尽快为您处理(人工客服工作时间:9:00-18:30)。
老化;且第二段的催化剂藏量比单段再生器的催化剂藏量低,
停留时间较短。因此,第二段可采用较高的再生温度。
2013-8-29 19
c.快速床(循环流化床)再生 气相转化成连续相,催化剂颗粒变为分散相,从而强化
了烧碳过程
随着气速的提高,返混程度减小,中、上部接近于平推
流,也有利于烧碳强度的提高
在快速流化床区域,必须有较大的固体循环量才能保持 较高的床层密度 催化裂化装置的烧焦罐再生就是属于循环流化床的一种 再生方式
T字形的构件,现在用得比较多的是初级旋风分离器
2013-8-29
4
提升管下部进料段的油剂接触状况对重油催化裂化的反应
有重要影响。减小原料油的雾化粒径,可增大传热面积,
从而提高了原料的气化率,且可以改善产品产率的分布
沉降器下面的汽提段的作用是用水蒸气脱出催化剂上吸附
的油气及置换催化剂颗粒之间的油气。汽提段的效率与水
柴油产率提高3.5个百分点以上
液收率提高2.5个百分点以上
干气产率大幅度降低
显著提高了柴汽比
可采取灵活多样的操作方式
2013-8-29
13
二:再生器
主要作用是烧去结焦剂上的焦炭以恢复其活性,同时
也提供裂化反应所需的热量
2013-8-29
14
主要要求有: ①再生剂的含炭量较低,一般要求低于0.2%,甚至低 于0.05%; ②有较高的烧碳强度,当以再生器内的有效藏量为基 准时,烧碳强度一般为100~250kg/(t.h); ③催化剂减活及磨损较少;
2013-8-29
23
催化裂化主要设备
汽提段:用水蒸气脱除催化剂上吸附的油气及 置换催化剂颗粒之间的油气,以免其被催化剂
夹带至再生器,增加再生器的烧焦负荷。
2013-8-29
24
催化裂化主要设备
2013-8-29
25
2013-8-29 10
短反应时间
两段技术,采用分段反应,两段反应时间之和比常规
催化平衡控制,常规催化的剂油比难以提高,两段催
化采用两路催化剂循环,从设备角度提高剂油比可不受限
制;第一段的低转化率和汽油回炼改质可以突破原有热平
衡的限制,在较高的剂油比(催化剂/催化原料)下实现 新的热平衡
3
提升管反应器的直径是由进料量来决定的。工业上一般
采用的气速是入口处为4~7m/s,出口8~18m/s
提升管的高度由反应时间来决定,工业上反应时间多采
用2~4s
提升管的上端出口处设有气-固快速分离机构,用于使
催化剂与油气快速分离以及抑制反应的继续进行
快速分离机构的形式有多种多样,比较简单的有伞帽形、
④易于操作,能耗及投资少;
⑤能满足环保要求
2013-8-29 15
工业上再生器的主要形式可分为三类:单段再生、两段再
生、快速床再生
分布器可分为板式(蝶形)和管式(平面树枝或环形)两种
2013-8-29
16
重催再生器需设取热设备:
a.内取热式
b.外取热式
2013-8-29
17
工业上常用再生器的形式大体上可以分为三类:
2013-8-29
6
两段提升管 FCC技术的思想及特点
两段FCC技术的基本思想:
★提高催化裂化催化剂的有效活性和选择性,从而改
善目的产品分布;
★分段反应,提高调整生产方案的灵活性
因此,两段提升管FCC技术打破原来的提升管反应器型 式和反-再系统流程: ★两段提升管反应器取代单一反应器 ★构成拥有两路循环的反应-再生系统
9
分段反应
不同的馏分需要不同的反应条件,理想选择是不同的
馏分在不同的场所和条件下进行反应
两段提升管(Ⅰ型)催化裂化: ★第一段提升管只进新鲜原料,段间抽出柴油出装置 ★第二段提升管单独进循环油,显著改善产品分布 ★第二段提升管底部回炼汽油,降低汽油烯烃含量 分段进料避免了新鲜原料和油浆的相互干扰
2013-8-29 20
2013-8-29
21
催化裂化主要设备
1、预提升段 2、裂化反应段 3、汽提段
2013-8-29
22
催化裂化主要设备
预提升段:加速催化剂,使催化剂形成活塞流向
上流动,使催化剂上的重金属钝化,有利于油雾
的快速混合,一般为3-6m。
裂化反应段:提供裂化反应的场所。
中止反应技术(MTC)
蒸气用量、催化剂在汽提段的停留时间、汽提段的温度及
压力、以及催化剂的表面结构有关
重油催化裂化则用4~
汽提汽用量一般为 2~3kg/1000kgCat
2013-8-29 5
5kgH2O/1000kgCat
两段提升管催化裂化技术
目前提升管反应器的固有弊端: 提升管过长恶化产品分布 新鲜原料与循环油浆竞争催化 中心 难于实现大剂油比操作
2013-8-29 11
两段与单段实验室结果对比:
轻油收率可提高 2-3 个百分点 原料转化深度提高 5 个百分点
汽油烯烃含量下降12-13个百分点
液收率提高2.5个百分点以上 干气产率大幅度降低 可显著提高柴汽比
2013-8-29
12
两段与单段工业试验结果对比:
轻油收率提高4个百分点以上
第六节
催化裂化 反应-再生系统
2013-8-29
1
催化裂化装置一般有四部分构成:反应-再生系统,分
馏系统,吸收-稳定系统和能量回收系统
装置形式主要有高低并列式、同轴式等
2013-8-29
2
一:提升管反应器
提升管反应器主要有提升管、沉降器、汽提段、旋分 器、待生斜管等部分组成
2013-8-29
2013-8-29 18
b.两段再生
两段再生是把烧碳过程分为两个阶段进行
与单段相比,两段再生的主要优点是:
①对于全混床反应器,第一段出口的半再生剂的含碳量
高于再生剂的含碳量,从而提高了烧碳速率; ②在第二段再生时可以用新鲜空气和更高的温度,提高 了烧碳速率; ③第二段内的水气分压可以很低,减轻了催化剂的水热
2013-8-29 7
两段提升管反应器示意图
2013-8-29 8
催化剂接力
原料在第一段提升管经过短反应时间后,及时 将催化剂与油气分开;需要继续反应的中间物料 在第二段提升管与另一路再生催化剂接触反应 催化剂两路循环,整体活性及选择性提高
催化反应比例增大,热反应得到有效抑制
2013-8-29
a.单段再生
再生温度对烧碳反应速率的影响十分显著,提高再生温
度是提高烧碳速率的有效手段,在单段再生时,密相创层
的温度一般不超过730℃
工业上一般采用的空气线速为0.6~0.7m/s
工业装置采用的再生器压力在0.25~0.4MPa(绝)之间
单段再生的主要问题是再生温度的提高受到限制和密相
床层的有效催化剂含炭量低