电线押出技术合集
电线生产过程之押出常见问题点及对策
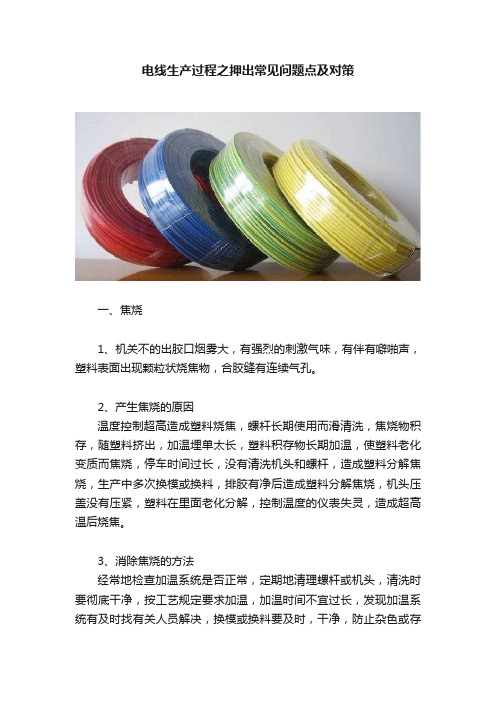
电线生产过程之押出常见问题点及对策一、焦烧1、机关不的出胶口烟雾大,有强烈的刺激气味,有伴有噼啪声,塑料表面出现颗粒状烧焦物,合胶缝有连续气孔。
2、产生焦烧的原因温度控制超高造成塑料烧焦,螺杆长期使用而滑清洗,焦烧物积存,随塑料挤出,加温埋单太长,塑料积存物长期加温,使塑料老化变质而焦烧,停车时间过长,没有清洗机头和螺杆,造成塑料分解焦烧,生产中多次换模或换料,排胶有净后造成塑料分解焦烧,机头压盖没有压紧,塑料在里面老化分解,控制温度的仪表失灵,造成超高温后烧焦。
3、消除焦烧的方法经常地检查加温系统是否正常,定期地清理螺杆或机头,清洗时要彻底干净,按工艺规定要求加温,加温时间不宜过长,发现加温系统有及时找有关人员解决,换模或换料要及时,干净,防止杂色或存胶焦烧,调整好模具后要把模具盖压紧,防止进胶,发现焦烧应立即清洗机头和螺杆。
二、塑化不良1、塑化不良的现象塑料层表面有蛤蟆皮现象,塑料表面发乌,关有微小裂绞或没有塑化好的小颗粒。
塑料的合胶缝合提不好,有一条明显的痕迹。
2、塑料不良产生的原因温度控制提过低或控制得不合适,塑料中有难塑化的树脂颗粒,操作方法当,螺杆和牵引速度太快,塑料没有完全达到塑化,造粒时塑料混合不均匀或塑料本身存在质量问题。
3、消除塑化不良的方法按工艺规定控制好温度,发现温度低要适当地把温调高,适当地控制螺杆和牵引速度,使塑料加温和塑化的时间增长,以提高塑料塑化的效果,利用螺杆冷却水,加强塑料的塑化和致密性,选配模具时,模套适当配小些,加强出胶口的压力。
三、表面质量1、塑料层表面质量缺陷及产生的原因1.1塑料材质不良,有较难塑化的树脂在没有完全塑化时被挤出,造成塑料层表面有小晶点和小颗粒,分布在塑料层表面四周。
1.2加料时混入杂物,造成塑料层表面有杂质疙瘩。
1.3模套承线径表面不光滑或有缺口,或因温度控制过高,有塑料中分解物堆积在模口处,造成塑料表面有痕迹。
1.4线芯或缆芯太重,放线张紧力小,且冷却不好时,易造成塑料层起皱。
电线押出机设备操作资料

中心的调整及注意事项
一、在清洗好机头之后。安装注意内外模不得碰撞,利用对角螺角螺丝 进行适当调整,使内模肉眼看上去 位于外模中心,完成初步调整,四 边螺丝不宜旋得太紧。
二、依据标准书,量好间隔。之后,进入实料调试阶段,由于内模为固
定的,只是移动圆柱套管的位置来调整,根据料出方位一般可分以下几
种状态,及调整过程。
押出的温度设定是以材料取得良好效率为目的,能得到均一的熬炼。 取得最佳特性的挤压出来的绝缘体来决定的。机身的温度在头部的前位 要高一些是通常的做法。而中央部高温的情况也不少,为了使材料部分 容易取得良好的状态。不要加热从机身的后方到中央到前方,其温度逐 渐从5~20℃加高是普通的做法。
温度设定应注意:1、如果挤压的温度过高的话,材料会产生热分 解,产品的特性变坏。2、如果挤压温度过低的话,不能得到满足的外观 产品,表面出现开裂。
输送用
汽车 船舶
放线架的安装及注意事项
用于安装芯线的架子叫做放线架,也称为送线架。 一、首先,将芯线套上线轴,将其固定,螺母末端系上少许导线,避 免运转中脱位,线头要朝于上方。套上两端之滚动轴承。
二、将其推上架轨,再将两端滚轴承,用以螺母锁定。 三、芯轴圆盘那边,套上刹车皮带⑦。
初装完毕,进入调试张力阶段。 芯线通过滚动轴棒,通向上方导轮,见图绕法。 芯线在运转中分别会出现以下几种状况:
E-1 E E-2
转为偏上型
⑥偏上,左型: (同理)
F-1 F F-2 ⑦偏左,下型: (同理)
G G-1 G-2 ⑦偏右,下型: (同理)
H H-1 H-2 注意事项:
1.每次必须将各部清洗干净,并加油润滑。 2.对于以上状态,偏于哪一方,必须先旋松哪一方。避免用力
电线押出教育

押出基本知识1、押出机原理:A、利用螺杆转动对胶料进行剪切并使胶料由进料口向机头方向流动;B、押出机的进料区对胶料进行预热,并将原料不断向前输送,同时在此过程中排除料中水份;C、压缩区主要将进料区推送过来的原料进一步加温使胶料完全胶化并将进行充分混炼,使胶料成份充实;D、计量区主要将压缩区之原料进一步混炼,使胶料更加均匀,以保证胶料以恒定的体积和压力向前推送;E、多孔板主要将料流由旋转改为直线流动,并支撑滤网得以过滤胶料中未熔之胶粒和杂质,同时以此增加押出内压,从而达到胶料在机筒的滞留时间完成充分熔化;F、料流通过机头分流,并径由模具押出所需形状;2、押出机因用料不同而设定不同温度,以下是各类押出料加工温度:A、PP、PE料一般押出各段温度在150℃-230℃之间;B、PVC芯线料一般押出各段温度在130℃-190℃之间;C、PVC外被料一般押出各段温度在120℃-160℃之间;D、PU料一般押出各段温度在150℃-220℃之间;3、押出线材时,内、外模怎样选用?A、内模选用原则:a、押出内模视铜线或芯线总外径决定(总外径=条数×1.15×单条外径);b、芯线内模押出以总外径+0.1mm为宜;c、PVC外层内模以总外径+0.4mm-0.6mm为宜(依芯线集合效果而定,芯线较圆则内模较小,芯线不圆或加棉纸则用较大内模);B、外模选用原则:a、PP、PE料为完成外径+0.4mm,PVC料为完成外径+0.05mm为宜;b、PVC外被押出时外模选用为完成外径+0.3-0.5mm;备注:PVC外被押出时外模选用受芯线结构及完成外径的影响较大;4、线材偏芯怎样调整?A、原因是锁模套松动造成偏芯;B、线材调偏芯是机头锁模套以调整外模而进行的,在调整中应以松少紧多为原则;5、绞线过预热的目的是什幺?为增加胶料与铜丝间的附着力,以增强芯线抗摇摆性能。
6、火花机有什幺作用?怎样设定火花拔机?火花机报警应如何处理?A、火花机作用是为检测生产中芯线出现的绝缘不良(如绝缘厚度不够或露铜丝)B、生产时火花机应设定在3kv;C、报警应即时调整机台解决此不良,并将不良报废7、过滤网的目的是什幺?A、1、过滤未熔胶料或杂质;2、调节押出机之压力;B、防止螺杆中胶料烤焦或硬化;过滤网通常放两张,800目在内、100目在外;8、为什幺天车的张力不可过紧或过松?A、太紧会拉伤芯线,太松会乱线暴及生产;B、张力调整以手感线有蹦紧感为准。
芯线押出教材

芯线押出教材芯线押出教材内容1.芯线押出生产线,及押出机构成2.各芯线料基本特性及作业参数设定3.操作程序及注意事项………………………………共六页一.芯线押出生产线,及押出机的构成教学内容:1.目前芯线押出机及产能介绍:目前PDG 电线厂芯线押出机有16台,其中有10台是注条芯线押出机,它的表示法通常以螺杆直径或螺缸内径尺寸表示。
例如直径为50MM 者,称为50MM 芯线押出机。
电线厂芯线押出机高纬50MM 产能为:500M/Min,有8台。
三丰50MM 产能为:600M/Min 有7台。
伟达隆45MMTeFlon 未量产。
1.芯线押出生产线如图所示:导体利用送线轴供给生产在线,经预热后通过押出机的机头及眼模,而行绝缘押出,经一小段空冷后进入水槽冷却。
然后以火花试验机检查押出层有无针孔与杂质,并检查外径及偏心等。
线缆速度控制则利用引取装置以一定速度引取,最后利用卷取机卷到线轴上。
2.押出机构成因素:a. 加料斗(HOPPER):贮存一定量原料,以供入押出机押出用。
b. 螺缸(BARREL):内藏螺杆的圆筒。
c. 螺缸加热器(BARREL HEATER):设在螺缸外围的加执带,用以加热熔融材料.d. 加热区(HEATING ZONE):各加热带加热螺缸的区域,变称加热段,通常分为 3~4区.e. 滤纲组(SCREEN PACK):过滤杂质及增加反压,使材料混练良好所用的组合 滤纲,通常采用不锈钢纲.f. 蜂巢板(BREAKER PLATE):设在螺缸前端的孔板,用来支持滤纲,并衔接螺缸送預抽真押冷火花引卷与机头,及改变材料的流动方向.g. 螺杆(SCREW):螺杆通常分三部分,各部分的主要功用如下: Ⅰ、供料段(FEED SECTICN):由供料口进入的材料,在这部分被推进,而向螺缸前端移动,粒状材料堆容积约为熔融态容积的两倍,为使材料能够不断的向前传送,此段长度约要为螺杆全长的四分之一以上。
电线押出工艺流程

电线押出工艺流程一、电线押出工艺概述电线押出是一种生产电线和电缆的重要工艺方法,主要是将金属材料通过模具,通过连续的挤压和拉伸过程,使其成为所需直径和形状的线材。
押出工艺广泛应用于铜线、铝线、合金线等材料的生产,是生产高精度、高品质电线和电缆的关键工艺环节。
二、电线押出工艺流程电线押出工艺主要包括原料准备、预处理、押出成形、冷却、拉伸、绕线等环节。
下面详细介绍每个环节的工艺流程。
2.1 原料准备电线押出的原料主要包括铜、铝等金属材料。
在进行押出工艺之前,首先需要对原料进行准备工作。
1) 选择高质量的原料。
原料的质量直接关系到押出成品的品质,因此需要选择纯度高、质量稳定的金属原料。
2) 对原料进行配比。
根据生产要求和产品规格,需要对原料进行合理的配比,确保押出成品符合要求的化学成分和机械性能。
2.2 预处理预处理主要是对原料进行清洁和加热处理,以提高原料的可塑性和押出成形的质量。
1) 清洁处理。
将原料进行洗涤和去除表面污物,以确保表面光洁,不影响押出成形的质量。
2) 加热处理。
将原料进行加热处理,使其达到一定的温度,提高原料的可塑性,有利于进行押出成形。
2.3 押出成形押出成形是整个电线押出工艺的核心环节,通过对原料进行连续的挤压和拉伸,使其成为所需直径和形状的线材。
1) 挤压过程。
将预处理好的原料送入押出机中,通过挤压头将原料进行挤压,使其成为所需直径的线材。
2) 拉伸过程。
经过挤压的原料,在通过一系列的拉伸模具,使其得到所需的光洁度和机械性能。
2.4 冷却冷却是将通过押出成形的线材进行快速冷却,使其达到所需的机械性能和组织结构。
1) 水淬冷却。
将押出成形的线材送入水槽中进行水淬冷却,快速降温。
2) 空气冷却。
将冷却好的线材通过空气冷却设备进行晾晒,使其完全冷却。
2.5 拉伸拉伸是将冷却好的线材进行一定的拉伸,以提高其机械性能和强度。
1) 设定拉伸参数。
根据产品规格和要求,设定拉伸机的拉伸参数,包括拉伸速度、拉伸力等。
电线押出训练

高手之成績
2)對于 1.2.1 中的 2)項
A:將螺桿.螺缸的溫度降低,并減少濾網數或換用較粗的濾網 B:清理螺缸和機頭 C:膠料桶加上蓋 D:避免異物混入 E:降低押出及引取速度 F:選用新型螺桿. 1.3 老化前的抗張力低: 1.3.1 原因: 材料溫度不當,即機械作用力不好. 1.3.2 工藝上解決辦法: A:增加對導體的預熱 B:增加網目 C:注意螺桿的冷卻 D:增加機頭和螺缸的溫度 E:選用新型螺桿 1.4 熱彎曲試驗.耐熱試驗.焊錫試驗及低溫彎曲試驗不合格: 1.4.1 產生原因: 主要是在絕緣或外被押出後的冷卻過程中,無法緩和外模附近因材料流 動而形成的內部壓力,或擠管式眼模使用了較大的引落比,具體分析如下: A:芯線未預熱或預熱不夠 B:第一段水槽未加溫 C:外模流道不暢 D:為了保持外徑的穩定而使用了較大的管狀眼模而造成引落比過大. 1.4.2 易產生此類不良的線種: 絕緣層較薄的線 1.4.3 工藝上解決辦法: A:芯線(導體)預熱 30~150 ℃
只賣力,不動腦的人技術永遠不會得到提高
第五部分 押出生產技術
B:將外模內表面重新刨光 C:改善眼模的流道 D:減小引落比,不能超出 5~8%的面積比. 2.氣泡: 2.1 外被或絕緣表面的氣泡 2.1.1 產生的原因: A:空氣經干燥料斗混入螺桿,這種情況多發生在融熔段過于靠前的螺桿. B:螺桿的背壓設計太小. C:超出押出機押出能力. 2.1.2 工藝上解決辦法: A:增加網目或將蜂巢板的孔改細 B:外模的廊段加長 C:調節螺桿的冷卻水溫 D:提高螺缸溫度 E:押出前將 PVC 預熱 F:降低押出機的引取速度 G:較厚結構的線采用大規格押出機 H:換用 L/D>20/1 的螺桿 I:換用融熔段較淺的螺桿 2.2 氣泡發生在絕緣體或外被表面的下部,較嚴重者,產生粗皮或粒狀表面. 2.2.1 產生原因: 材料中含有水份 2.2.2 產生此類不良現象的線種: 多數線的共同現象 2.2.3 工藝上改進的方法: A:利用干燥料斗對膠料進行干燥 B:膠料保存在干燥的環境里 C:完全去除濕氣法:將有濕氣的材料先押出後,再粉碎或切粒,然後進行正式 生產. 2.3 絕緣或外被體周圍不規則的氣泡生成的粗面. 2.3.1 形成原因: 由于材料溫度過高,同時由于眼模的流道過于復雜,致使 PVC 分解而產生 HCL 氣體. 2.3.2 工藝上的改進方法: A:降低螺缸和機頭的溫度,減少過濾網的張數,或改用較粗濾網. B:降低押出和引取的速度 C:重新選用螺桿. 其它的改善方法如下:
电线押出常见问题及对策
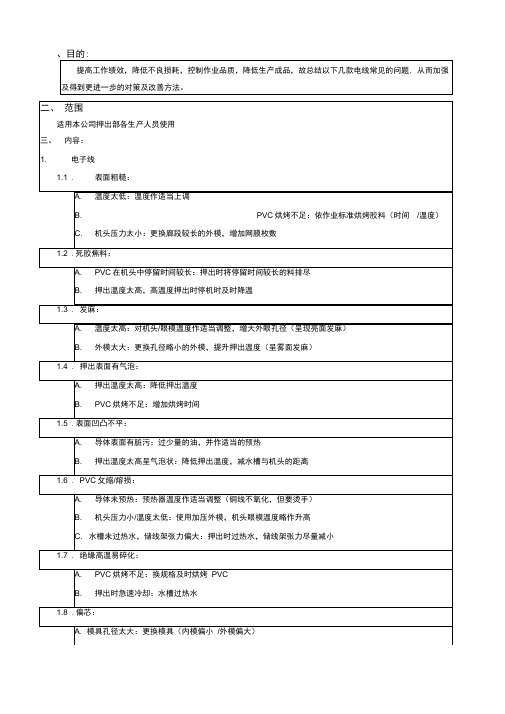
、目的:
注意内模的选择不可太小(用半成品穿过眼模能轻松滑动为宜)
C过粉太少造成脱皮不良,生产中因滑石粉潮湿和过粉太少都会造成脱皮困难,生产前及时将滑石粉烘
B.两芯过粉线外被偏扁,线径偏小:调大线径至正常大小
2. 7印字不全、模糊、拖墨不清晰:
A:字印不全:有可能是压轮未压紧、印字轮高度偏高、调试未调好,必须进行调正确保质量
B. 印字模糊:字外围有印影,有可能是字轮过深,要更换字轮。
字糊有印影一般是线表面或油墨盒内有水造
成,解决的方法应调正好气压,使线上的水吹干净。
经常的更换盒中的油墨,调配适中。
C. 印字拖墨不清晰:线材表面拖墨主要是刮片(刮油墨刀片)有缺口刮不干净字轮上油墨而造成拖墨这种情
况,可换刮刀片,加大压紧力,刮干净油墨,解决拖墨问题。
2.8裁线尺寸错误有误或超出公差范围
A.使用正确尺子度量
B 细核对订单尺寸及桌面定位尺寸是否一致,定位长度治具是否固定好。
C. 首裁第一条尺寸需再次测量确认0K,方可开裁。
D. 裁线不能拉得太紧,也不能一次手握太多,以免裁出线材公差太大,长短不一,
E. 手握需裁线线材应往铡刀里侧铡下,以免铡下刀锋不利而拉出导体铜丝。
电线押出基本原理

電線押出基本原理一、押出機構造二、螺桿的形式三、押出能量計算四、押出量的簡單計算法五、螺桿型式的決定六、馬達容量決定七、加熱、冷卻裝置八、溫度測定與控制九、機頭十、眼模十一、依線徑(押出量) 選定機台十二、如何選用眼模及眼模調整十三、押出溫度十四、抽真空的效果十五、冷卻的效果十六、常用塑膠押出(PVC、PP、十七、發泡塑膠的押出電線押出基本原理介紹一.押出機的構造:此處所討論的押出機,係指可將配料好的膠粒(PVC.PP.PE---),使其熔融可塑化的設備,稱可塑化押出機,而所使用的螺桿只有一支,所以又稱為單螺桿可塑化押出機(Single Screw Plasticize Extruder).如圖二所示.1-1.單螺桿押出機的構成,如圖2所示.最重要的部分為內藏螺桿的螺缸.塑化流程為,加料斗加入固形原料→經螺缸內熔融可塑化後→由末端眼模成形押出,螺缸末端設有蜂巢板,用以支持濾網并作為螺缸與機頭的接續部分密封用.1-2.螺缸的加熱冷卻通常都用電熱及風扇為主.部分場合設有夾層而採用油熱或蒸汽加熱,螺桿轉數由幾十轉至幾百轉,係由馬達經減速齒輪而轉動亦有採用DC馬達或變速馬達.二.螺桿的形式PP用螺桿為例,(如圖3所示).其螺旋從根部直通到前端,這種螺桿稱為螺旋螺桿(Full-Flight Screw),以螺缸內徑65mm為代表值,稱65mm螺桿及65mm押出機.a.螺距與螺缸內徑相同為65mm.b.螺旋廊寬為內徑的1/10即6.5mm.c.螺桿外徑略小於螺缸,其外徑約小於螺缸的1/250~1/100.d.加料斗側的部分有一段溝深相同,稱為供料部.(Feed Section)圖3中供料部溝深9.8mm,長度為390mm.相當於螺缸內徑的6倍,亦即為6D.e.螺桿中間部分,溝深漸淺部分稱為壓縮部(Compression Section),長度845mm,相當於13D.f.在螺桿末端亦有溝深相同部分,稱為計量部.(Metering Section),其溝深為2.8mm,長455mm相當於7D.供料.壓縮.計量三部份合計長度為螺桿有效長度(L),其長度為1690mm.亦即26D.g.通常螺桿以供料部6D.壓縮部13D.計量部7D來表示為主,螺桿有效用L/D來表示,即為26D.h.溝深是以螺缸內徑到溝底距離.如圖3.供料部的溝底為45.4mm(65-9.8*2)i.螺桿末端計量部的溝深比供料部溝深淺.兩者間有一段溝深變化的壓縮部,螺桿供給的原料在壓縮部接受壓縮作用.其壓縮程度的大小,稱為壓縮比.(Compression Ratio)CR=〔Hf(D-Hf)〕/〔Hm(D-Hm)〕CR: 壓縮比Hf: 供料部溝深mmHm:計量部溝深mmD: 螺桿內徑mm例圖3中CR=〔9.8(65-9.8)〕/〔2.8(65-2.8)〕=3.11因此,圖3螺桿的表示方法為:Φ65mm. L/D 26 CR 3.11.供料部6D.壓縮部13D,計量部7D.計量部溝深2.8mm.三.能量計算3-1押出機的尺寸用螺缸直徑作代表,原因為:a.由螺缸的直徑,可約略決定押出量.b.押出量決定後,所需動力便可決定.c.從螺缸的直徑,幾乎可決定押出機的個部尺寸.d.從圖4所示,例如65mm押出機,最大押出量80kg/m,所需動力為22kw(不同材料動力不同).e.螺桿有效長與螺缸內徑比L/D約22~26D取L/D=24螺桿有效長度為65*24=1.56M四.押出量的簡單計算法Q={0.9πD〔Hm(D-Hm)〕*60*N}/106*ρ(KG/hr)D: 螺缸內徑Hm;計量部溝深mmN: 螺桿回轉數rpmρ: 原料比重注1:實際押出量約為計量值得40%五.螺桿形式的決定a.L/D較長的螺桿混練較好,可用於低溫押出.b.供料部需有6~7D才能確保供料穩定均勻.c.混練段最主要在計量部,計量段長對混練有益約需7~10D.d.壓縮部長對粒間空氣的排除有較佳效果,Nylon FEP需要短及急壓的壓縮部.六.馬達容量決定a.依經驗數據所需動力為押出量0.20~0.25kwh/kg,若押出量為75kg/hr,則動力為75*(0.2~0.25)=15~18.75KW.考慮損耗則為15~18.75/0.8=18.75~23.44KW.b.深溝比淺槽螺桿,長比短螺桿需較大動力.c.粘度高樹脂需較高動力.七.加熱冷卻裝置a.押出機加熱區分佈:「加熱部6 D」「壓縮部13 D 」「計量部7 D 」C1 C2 C3 C4 C5120℃180℃230℃230℃210℃圖5 加熱區的分配與溫度設定C1.C2供料部間距可大,且可以不加冷卻裝置.C3~C5需較精確溫度,固間距亦小,且須裝冷卻裝置.b.加熱裝置有帶型,鑄鋁,鑄黃銅加熱器等.特殊情況亦有用誘導電流加熱裝置.c.冷卻裝置有冷風扇,夾層水冷,油加熱冷卻等.d.通常Φ65mm以下用帶型加熱器+冷風扇組合,Φ65mm以上若重視加熱能力則用鑄鋁加熱器,300℃以上則採用鑄黃銅加熱器.e.夾層水冷是在須要強制冷卻及精確溫度的場合.八.溫度測定與控制a.押出溫度左右成品的良莠,溫度控制與計測則為重點.b.溫度計測以熱電偶感溫棒為主.c.控制一般以ON/OFF為主,近來被比例式所代換,比例式為快達到設定溫度時電流會自動變小而加熱程度自動變弱直至溫度到達時切斷,可得較精準溫度控制.九.機頭押出機頭一般皆與機頭縱向成直角,乃螺缸到眼模熔融材料的流動通路如圖6所示.a.螺缸到機投頸部要盡量短,否則流動會受阻.b.機頭內容積要盡量小,避免回流及停滯.c.流道要直且平滑,避免島形或急大急小.d.如圖7,為使圓周方向有均等流動速度,流路由普通型改為2分割或4分割.十.眼模電線押出眼模分為加壓型(Pressure Type)與套管型(Tubing Type)兩種.a.圖8加壓眼模押出場合:熔融材料在加壓下押出到導體上,材料與導體密著性好,表面良好,一般絕緣及厚層外被押出常使用.b.圖9套管眼模押出場合,熔融材料呈管狀押出,押出後引落而包在芯線上.必要時(較大引落如Nylon FEP)絕緣與導體間可用真空抽吸,使絕緣緊密避免氣泡發生.套管眼模優點為絕緣厚度較均一,密著力較小,細導體剝皮時較不易斷。
电缆押出工艺

芯押制程常识芯押制程常用绝缘材料1. PP(6331)化学名称聚丙稀,PP介电常数较大,耐电压强度好,燃烧时不易滴落且略有臭味,PP质量比PE轻.2. PE(3366,0105,7100,3485)化学名称聚乙稀,其中3366是高密度PE,而0105和7100为低密度PE,3485为发泡PE,发泡PE 传输信号比较好,最为典型的是应用在显示器的RGB线.PE有优异的电氯特性,耐磨性,耐溶性,耐低温劣化,耐溶性等.在电线电缆绝缘器被覆中使用最为广泛.燃烧时易滴落但无臭味.3. PVC(PVC,SR,1792)化学名称聚氯乙稀SR属半硬质材料,大多用于电源线系列,如USB红,黑两根电源线.1792属中被线所用,比较硬.二. 芯押制程常用导体1. 芯押制程所用导体按信号要求分为裸铜线和镀锡铜线.裸铜线导电性能好.价格比镀锡铜便宜,易氧化.三. 芯押制程各种胶料温度设定1. PE:190℃~240℃(3366,0105),180℃~230℃(7100)2. PP:190℃~240℃3. PEF:160℃~180℃视所需电容量和发泡度而定4. PVC:150℃~180℃5. SR:150℃~180℃四. 芯押模具选择1. 依照其导体绞合外径N*1.155*d的公式选择内模,一般比导体绞合外径大0.2~0.5mm,视其所用导体定论,如:7/0.195 OD:0.58,选用0.6内模,19/0.06 OD:0.3选用0.35内模.2. 外模选择一般依照芯线OD和其所用材质选择.A. PE绝缘比OD大0.02~0.03mm.B. PP绝缘比OD大0.01~0.02mm.PP和PE外模选择一般等于或接近芯线OD,最多偏差0.05mm.C. PVC外模选择一般与OD相等或小一点.D. PEF外模比芯线OD小0.35mm左右.依公式A=(1-K)B2+4C2A.外模B.发泡线ODC.铜线OD K.发泡度3. 内外模选择一般依制程卡为标准,若有问题与实际情况选择.4. 外模有凸7和凸3二种,内模有长形和短形二种,按照押出形式有管状和充实,芯押一般充实.五. 芯押常用计算公式1. 选择内模公式:N*1.55*d.2. ×100%偏心率计算公式: 最大厚度-最小厚度最大厚度+最小厚度3. ×100%伸长率计算公式: 拉伸后长度-2.5(取样长度)2.5六. 芯押开发泡线的电容量控制1. 发泡的作用:增强内部信号,减少外界干扰.2. 电容与温度,线径成反比,温度越高,电容小.线径小,电容大.温度越高,其发泡度也越高.3. 前段水槽也可调节电容,水槽向眼模靠近芯线,冷却成型快,则电容增加,离眼模距离远,相对冷却成型慢点,则电容减少.七. 芯押检查和管控点1. 开机前对材料和数据确认.2. A.开机中时常对路径检查,必须顺畅.B.机器的运转状况检查,必须正常.C.仪器工作性能检查(火花机,电容检测)D.张力检查,需平稳,不能过大也不能过小.3. 自主(首件)检查:检查各项规定内容,特别落实及时检查.对导体素线径,芯线OD,最小厚度,芯线颜色,芯线外观,排线,火花电压,电容量,拉断力,伸长率,附着力,偏心率等进行严格检查.八. 芯押常见问题的引起因素1. 偏心A. 模具选用不当.B. 胶料胶化不够.C. 换料或换模具时,未清理干净.D. 机器工作时胶料押出不均,速度快时易偏心.E. 有杂物和杂质等.F. 温度设定不恰当.G. 路径不顺畅.H. 内外模间距调整不当.2. 伸长,拉断,附着力达不到要求.A. 预热机温度设定不当.B. 押出机胶料温度设定不当.3. 色差.A. 配色不当.比例不均.B. 未拌均匀.C. 色母用错.D. 换色时未换好,机头里还有余料.九. 芯线抗张及伸长要求.1. SR-PVC:抗张力>3000PSI,伸长>100%.2. PE:抗张>1400PSI,伸长>300%.3. PP:抗张>3000PSI,伸长>150%.4. PVC:抗张>1500PSI,伸长>100%.十. 押出机头拆装步骤65+30A)1. 用扳手拆卸外眼套,单动开启押出机,取出外眼.2. 用顶丝顶出内眼.3. 用圆形板手松导料阀外环套.4. 用拔帽拔导料管.5. 用圆形扳手松导料阀内环套.6. 用顶丝顶出导料阀套组件.7. 用尖嘴钳取出导料阀组件.注意事项:拆装时一定要用专用工具,特别装机时敲内眼线其它组件时一定要用胶棒,以免损坏内眼和其它组件.。
芯线押出教材

芯线押出教材内容1.芯线押出生产线,及押出机构成2.各芯线料基本特性及作业参数设定3.操作程序及注意事项………………………………共六页一.芯线押出生产线,及押出机的构成教学内容:1.目前芯线押出机及产能介绍:目前PDG电线厂芯线押出机有16台,其中有10台是注条芯线押出机,它的表示法通常以螺杆直径或螺缸内径尺寸表示。
例如直径为50MM者,称为50MM芯线押出机。
电线厂芯线押出机高纬50MM产能为:500M/Min,有8台。
三丰50MM产能为:600M/Min有7台。
伟达隆45MMTeFlon未量产。
1.芯线押出生产线如图所示:押出导体利用送线轴供给生产在线,经预热后通过押出机的机头及眼模,而行绝缘押出,经一小段空冷后进入水槽冷却。
然后以火花试验机检查押出层有无针孔与杂质,并检查外径及偏心等。
线缆速度控制则利用引取装置以一定速度引取,最后利用卷取机卷到线轴上。
2.押出机构成因素:a.加料斗(HOPPER):贮存一定量原料,以供入押出机押出用。
b.螺缸(BARREL):内藏螺杆的圆筒。
c.螺缸加热器(BARREL HEATER):设在螺缸外围的加执带,用以加热熔融材料.d.加热区(HEATING ZONE):各加热带加热螺缸的区域,变称加热段,通常分为3~4区.e.滤纲组(SCREEN PACK):过滤杂质及增加反压,使材料混练良好所用的组合滤纲,通常采用不锈钢纲.f.蜂巢板(BREAKER PLATE):设在螺缸前端的孔板,用来支持滤纲,并衔接螺缸与机头,及改变材料的流动方向.g. 螺杆(SCREW):螺杆通常分三部分,各部分的主要功用如下:Ⅰ、供料段(FEED SECTICN):由供料口进入的材料,在这部分被推进,而向螺缸前端移动,粒状材料堆容积约为熔融态容积的两倍,为使材料能够不断的向前传送,此段长度约要为螺杆全长的四分之一以上。
Ⅱ、移转段(COMPRESSION SECTION):也称为压缩段,乃螺沟由深到浅的部分,材料在这部分逐渐溶融态,堆容积减小,为补偿其变量,故螺沟渐浅以得到压缩作用。
【技术研讨】线缆材料发泡PE、PVC、PP押出技术简介

【技术研讨】线缆材料发泡PE、PVC、PP押出技术简介发泡PE押出1.发泡的目的:一般材料发泡的目的在于使制品轻量化,并加强制品隔热性,及降低材料成本,而线缆用材料发泡的目的则在于降低材料的介质常数.2.发泡PE用螺杆:L/D约20-28,并有较长的供料段,压缩比约2.0-2.53.发泡PE眼模计算:当完成外径及导体外径决定时,外眼尺寸便可利用以下公式求出来:眼模孔径=√Dcw2+Dw2(2为膨胀比,一般薄层押出膨胀比约为2,厚层押出的时候膨胀比约为4 )低发泡薄层押出的场合,眼模设计入口角60-90°,出口角9-15°,设1-2MM廊长,这样可得到良好的押出表面,4.押出条件对发泡PE的影响1)押出温度的影响在低温时押出气泡很少,如上图A所示.温度上升则气泡分布逐渐均匀,发泡度逐渐提高, 在达到某个温度时,发泡度最高,并得到及细微的气泡构造如上图B所示.温度再上升则气泡粗大化,并且有气泡破裂现象,形成不均匀的气泡构造,如上图C所示.此项最适当的温度条件,视材料别而异,除利用实验来决定外,无其它良策.2)螺杆回转数的影响螺杆回转数对发泡状态亦有相当影响性,回转数增加的时候,发泡度也逐渐增加,气泡构造更加细微,直到达到某限度为止.超越此限度后,效果反而下降,故如何决定适当的螺杆回转数,及为重要5.发泡PE押出必须注意以下各点,才能使变异减为最低1)选用品质稳定的材料.2)材料供入定量化.3)保持一定押出稳度.4)保持螺杆回转数不变.5)维持一定的导体预热.6)维持一定的线速pvc押出1)PVC性能及用途PVC比重约1.4,耐水,耐盐酸,耐燃,及绝缘性能良好,由于PVC介电特性较差,故一般用于600V以下PVC电缆,通信局内电缆,及电缆的被覆.PVC在65-85°C软化,120-150°C完全熔融,190°C以上就会分解,故其加工温度范围约为150-180°C2)PVC用螺杆:PVC用螺杆普通为较深沟设计,压缩比约2.0-2.5.为使混练良好,L/D比取较大值3)PVC用眼模可采用加压型与管型任何一种,完全视线缆结构而定.为使材料流动顺畅,入口角约30-45°,廊长约为外径的0.5-1倍,视押出机与线缆类别而作适当的调整.4)PVC温度的设定:押出温度视所用PVC聚合度及配方而异,普通PVC押出的时候其温度设定如下:一段:100-120 二段:120-140三段:140-160 机经:160-170机头:170-175 眼模: 180-185作业时可视押出线表面情况,作适当的温度修正5)半硬质PVC 押出注意事项线缆用PVC材料大部分为软质,由于可塑剂含量较多,故流动性良好,押出温度也比较低,押出作业极易进行.由于可塑剂含量多电气特性较差,故用途不同的时候某些线缆必须使用半硬质PVC达成目的.半硬质PVC 由于可塑剂含量少,流动性差,故押出作业较困难,必须注意以下几点。
电线押出工艺流程

电线押出工艺流程The wire extrusion process is a crucial technique in the manufacturing of electrical wires. 电线押出工艺是电线制造中至关重要的技术。
This process involves shaping a metal wire by forcing it through a die to create a specific cross-sectional shape. 这个过程涉及通过将金属导线推动通过模孔来塑造金属导线以形成特定的横截面形状。
One of the initial steps in the wire extrusion process is the selection of the appropriate material for the wire. 电线押出工艺的初始步骤之一是选择适当的金属材料用于导线。
The material chosen should have good conductivity, flexibility, and durability to ensure the wire's performance. 选择的材料应具有良好的导电性、柔韧性和耐久性,以确保导线的性能。
Copper and aluminum are commonly used materials due to their excellent electrical properties. 由于其出色的电气性能,铜和铝是常用的材料。
During the extrusion process, the wire material is heated to a specific temperature to make it malleable. 在押出过程中,导线材料会被加热至特定温度使其具有可塑性。
电线押出工艺流程

电线押出工艺流程电线押出工艺流程是电线制造过程中的关键环节,它涉及到多个步骤和精细操作,以确保最终产品的质量和性能。
下面将详细介绍电线押出工艺流程的主要步骤和注意事项。
电线押出工艺流程的第一步是准备阶段。
在这个阶段,工作人员需要确保所有原材料,如导体、绝缘材料、护套材料等,都符合质量要求,并已按照生产需求准备好。
此外,还需检查生产设备,如押出机、牵引机、切割机等,确保其处于良好状态,能够正常运行。
接下来是导体加工阶段。
导体是电线的核心部分,其质量直接影响电线的导电性能。
在这一阶段,工作人员需要将导体按照规定的规格进行加工,包括切割、绞线、退火等步骤,以形成符合要求的导体线芯。
然后是绝缘层押出阶段。
绝缘层是保护导体并防止电击的关键部分。
在押出机上,工作人员将绝缘材料加热至熔融状态,并通过模具将其押附在导体线芯上。
这一过程需要精确控制温度、压力和速度等参数,以确保绝缘层的厚度和均匀性符合要求。
完成绝缘层押出后,进入护套层押出阶段。
护套层是电线的外层保护,具有防水、防晒、耐磨等作用。
与绝缘层押出类似,工作人员需要在押出机上将护套材料加热并押附在绝缘层外。
同样,这一过程也需要精确控制各项参数,以确保护套层的质量。
在押出过程中,还需要进行冷却和固化处理。
冷却可以使押出的电线快速定型,而固化则能确保电线结构稳定,不易变形。
通常,冷却和固化是通过冷却水槽或固化炉来实现的。
最后,电线经过牵引机进行长度控制和张力调整,然后通过切割机切割成规定长度。
最后,进行质量检验和包装,确保每卷电线都符合相关标准和客户要求。
在电线押出工艺流程中,还需注意以下几点:一是要确保生产环境的清洁和安全,避免灰尘和杂物对电线质量的影响;二是要定期对生产设备进行维护和保养,确保其性能稳定;三是要加强员工培训和技能提升,提高生产效率和质量水平。
综上所述,电线押出工艺流程是一个复杂而精细的过程,涉及多个步骤和参数控制。
只有严格遵循工艺流程和操作规范,才能生产出高质量、性能稳定的电线产品。
电线押出技术合集

.专业整理 .塑料和导体塑料电现电缆要适应各样不同需要,就应拥有宽泛的优秀而稳固的使用性能。
塑料电线电缆的使用性能和寿命,决定于产品构造的先进性、塑料采纳的合理性以及工艺的完美性。
从塑料电现电缆技术的发展来看,合理而正确的使用资料是重点的要素。
为了制造性能优秀而稳固的塑料电线电缆,在导电线芯和半成品缆芯知足规定的技术要求的前提下,主假如对绝缘和护套用塑料提出了较高的要求。
绝缘塑料的基本要求是拥有优秀的电绝缘性能,同时依据产品用途和使用条件分别提出对机械性能、耐高温性、物理-化学性能及工艺性能的要求。
对护套塑料的基本要求是耐受各样环境要素作用的老化性能,在知足这个条件下分别提出一些特别要乞降协助要求。
第一节塑料塑料是高分子合成资猜中凡是性能上拥有可塑性变化的资料的总称。
塑料可分为热塑性塑料和热固性塑料两大类,电线电缆制造中所用的塑料都是热塑性塑料。
电线电缆常用的热塑性塑料有聚氯乙烯、聚乙烯、交联聚乙烯、泡沫聚乙烯、氟塑料、聚酰胺、聚丙烯和聚酯塑料等。
塑料是以合成树脂为基本成份,再增添各样配合剂,经捏合、切粒等工艺而塑制成必定形状的资料。
为了知足加工、储存和使用的要求,合成树脂内一般都要增添各样配合剂,依据增添配合剂所起的作用不同,塑料的增添剂大概有以下几种:防老剂(它包含抗氧剂、稳固剂、紫外线汲取剂、光障蔽剂等,这几种资料在塑猜中所起的作用不同但又相互联系,同一种资料可起几种作用,所以统称为防老剂。
);增塑剂;交联剂;润滑剂;填补剂;着色剂;发泡剂;防霉剂;驱避剂;阻燃剂;耐电压稳固剂;抑烟剂等。
各样塑料既拥有塑料共有的特征,又拥有各不相同的各自独具的某些特征。
各样塑料共有的特征有:比重小、机械性能较高、电绝缘性能优秀并且化学稳固性好、耐水、耐油、加工成型方便,原料根源丰富。
为了适应日趋增添的电线电缆技术发展的需要,塑料将精益求精配方和性能,提升其耐热性和电压等级,提高资料的耐寒、耐大气老化性能、耐火阻燃性能,延长电线电缆使用寿命,同时,还将不断开发新式塑料并合理用于电线电缆上。
电线押出技术
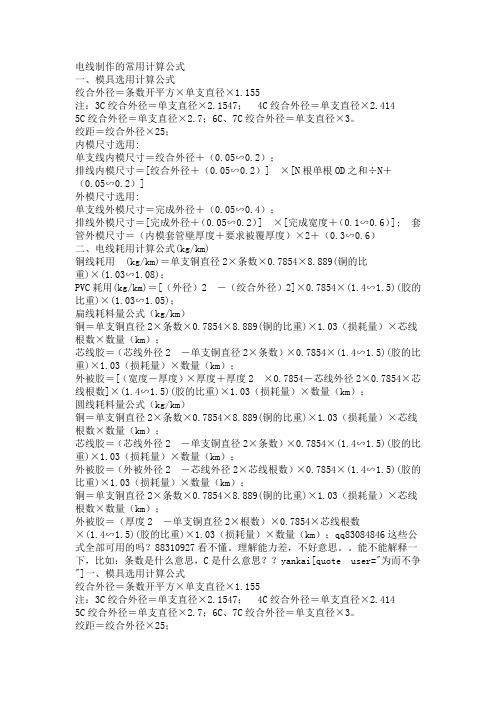
电线制作的常用计算公式一、模具选用计算公式绞合外径=条数开平方×单支直径×1.155注:3C绞合外径=单支直径×2.1547;4C绞合外径=单支直径×2.4145C绞合外径=单支直径×2.7;6C、7C绞合外径=单支直径×3。
绞距=绞合外径×25;内模尺寸选用:单支线内模尺寸=绞合外径+(0.05∽0.2);排线内模尺寸=[绞合外径+(0.05∽0.2)] ×[N根单根OD之和÷N+(0.05∽0.2)]外模尺寸选用:单支线外模尺寸=完成外径+(0.05∽0.4);排线外模尺寸=[完成外径+(0.05∽0.2)] ×[完成宽度+(0.1∽0.6)]; 套管外模尺寸=(内模套管壁厚度+要求被覆厚度)×2+(0.3∽0.6)二、电线耗用计算公式(kg/km)铜线耗用(kg/km)=单支铜直径2×条数×0.7854×8.889(铜的比重)×(1.03∽1.08);PVC耗用(kg/km)=[(外径)2 -(绞合外径)2]×0.7854×(1.4∽1.5)(胶的比重)×(1.03∽1.05);扁线耗料量公式(kg/km)铜=单支铜直径2×条数×0.7854×8.889(铜的比重)×1.03(损耗量)×芯线根数×数量(km);芯线胶=(芯线外径2 -单支铜直径2×条数)×0.7854×(1.4∽1.5)(胶的比重)×1.03(损耗量)×数量(km);外被胶=[(宽度-厚度)×厚度+厚度2 ×0.7854-芯线外径2×0.7854×芯线根数]×(1.4∽1.5)(胶的比重)×1.03(损耗量)×数量(km);圆线耗料量公式(kg/km)铜=单支铜直径2×条数×0.7854×8.889(铜的比重)×1.03(损耗量)×芯线根数×数量(km);芯线胶=(芯线外径2 -单支铜直径2×条数)×0.7854×(1.4∽1.5)(胶的比重)×1.03(损耗量)×数量(km);外被胶=(外被外径2 -芯线外径2×芯线根数)×0.7854×(1.4∽1.5)(胶的比重)×1.03(损耗量)×数量(km);铜=单支铜直径2×条数×0.7854×8.889(铜的比重)×1.03(损耗量)×芯线根数×数量(km);外被胶=(厚度2 -单支铜直径2×根数)×0.7854×芯线根数×(1.4∽1.5)(胶的比重)×1.03(损耗量)×数量(km);qq83084846这些公式全部可用的吗?88310927看不懂。
【技术研讨】电线押出的常见问题及解决方法

【技术研讨】电线押出的常见问题及解决方法一.电子线1.表面粗糙:A.温度太低:温度作适当上调B. PVC烘烤不足:依作业标准烘烤胶料(时间/温度)C.机头压力太小:更换廊段较长的外模,增加网膜枚数2.死胶焦料:A.PVC在机头中停留时间较长:押出时将停留时间较长的料排尽B.押出温度太高,高温度押出时停机时及时降温3.发麻:A.温度太高:对机头/眼模温度作适当调整,增大外眼孔径(呈现亮面发麻)B.外模太大:更换孔径略小的外模,提升押出温度(呈雾面发麻)4.押出表面有气泡:A.押出温度太高:降低押出温度B. PVC烘烤不足:增加烘烤时间5.表面凹凸不平:A.导体表面有脏污:过少量的油,并作适当的预热B.押出温度太高呈气泡状:降低押出温度,减水槽与机头的距离6. PVC收缩/熔损:A.导体未预热:预热器温度作适当调整(铜线不氧化,但要烫手)B.机头压力小/温度太低:使用加压外模,机头眼模温度略作升高C.水槽未过热水,储线架张力偏大:押出时过热水,储线架张力尽量减小7.绝缘高温易碎化:A. PVC烘烤不足:换规格及时烘烤PVCB.押出时急速冷却:水槽过热水8.偏芯:A.模具孔径太大:更换模具(内模偏小/外模偏大)B.模具未装正:重新将模具装正C.内外模距离不当:以先近后远的原则调整内外模的距离9.其它A.跳股引起的外观不良:内外模更换为孔径稍大的B.PVC混炼不足引起外眼有积渣:升高押出温度,减小外模孔径和内外眼的距离C.刮伤:外模引起的刮伤,更换外眼内外眼模中间堵铜丝:折模清理内外模水槽导轮储线架刮伤:将线材放致导轮,储线架合适的位置,有破损时及时更换。
二.外被线1.外观显示成品纹路缠绕纹:A压大太大(内外模距离离太远):生产中内外模距离2M/M左右。
外模太小:生产中外模宜选用比OD大0.1-0.3M/M的外模纹编织纹:A外模太小:太小的眼模因压力大造成外观不良,生产中宜选用孔径稍大的外模(具体孔径尺寸依实际生产中更换为准).B内外模距太远:生产中因内外模距离离太远造成压力偏大从而导致显编织纹/生产中尽量押空一点.编织线一般要求好脱皮,故无特殊要求时一般采用半空管押出.针对需要充实型押出的编织线机头压力太大和太小时都会造成押出外观不良.生产中针对实际情况对内外模距离及外模孔径进行调整,来解决外观问题.2.过粉线,铝箔线的外观不良滑石粉的好坏直接影响线材的外观,故滑石粉在使用前一定要烘烤干燥.这样滑石粉才能均匀分布在经线材上,生产中半成品一定要从毛刷中间穿过,避免因过粉太多导致外观不良,外模太小和内外模太近都会导致押出外观不良,生产时要特别注意.铝箔线的外观调试同编织线.3.外被脱皮不良以及芯线粘连(1) 生产中押出机头压力太大时会造成脱皮不良,押出时尽量通过增大外模孔径的方法避免压力过大.其次水槽距离机头应越近越好.水量应最大为宜,做到急速冷却.(2) 隔离不良造成脱皮不良,缠绕偏移,编织松散等倒造成外被附在芯线上造成脱皮不良,生产中要注意内模的选择不可太小(用半成品穿过眼模能轻松滑动为宜)(3) 过粉太少造成脱皮不良,生产中因滑石粉潮湿和过粉太少都会造成脱皮困难,生产前及时将滑石粉烘烤干燥.押出中及时添加滑石粉,加速时对模具的距离进行调整(减小)(4) 芯线粘连:芯线粘连一般是因为胶皮熔点太低押外被时高温熔融粘在一起,生产中第一段水槽要放最大的水,做到急速冷却,必要时绞合时离型剂或过粉.押外被时也可采用先过离型剂再过粉.(5) 部份客户要求线材剥高力,在实际操作中根据客户要求对押出条件进行调整即可.4.表面外观异常(1) 粗糙:A. 外模太大,生产中因外模太大或造成外观粗糙,此时需要更换孔径稍小的外模B. PVC潮湿,开机前依作业标准提前干燥滑石粉C. PVC混炼不良,增加网膜,提升加出温度,选用加压外模可解决(2) 条纹:A. 亮条纹,第一/二段温度偏高造成押出表面有亮条纹,降一/二段温度B. 雾条纹,第三/四段温度偏高造成押出表面有雾条纹,降第三/四段温度(3) 边亮边雾:机头/眼模温度偏高以及机头/眼模加热不均匀造成押出外表一边亮一边雾.此类现象发生时及时降低机头,眼模温度,更换滤网(片数减少)外模选用稍小的无廊段外模可改善.(4) 发麻:A. 机头/眼模温度偏高,对温度进行适当下调.B. PVC潮湿,开机前及时干燥PVC5.偏芯(1) 内模太大:外被押出时为使外观良好一般选用孔径稍大的内模,但内模太大容易出现间断性偏芯或高速押出时偏芯,生产过程中尽量避免内模太大(2) 调模螺丝未锁紧,中心调整OK后及时将四颗调模螺丝销紧后再正常开机(3) 其它方面,机头漏料,导管内有杂物也会造成偏芯生产中根据实际情况进行调整,针对偏芯,认真落实自主检查可杜绝批量不良产生.三.其它不良的控制1.D大小不均:人为控制不当,注意加减速的异常,放线架张力收线张力,测量工具异常等.2.印字不良依印字不良情形及对策进行调整3.刮伤:眼模刮伤及时更换眼模因过线导轮和储线架等刮伤及时调整可解决外眼有积渣也会造成刮伤,从根本上应更换材料,其次可以通过提升押出温度,更换孔径略小的外模(无廊段)可解决外眼因积渣造成刮伤之问题.塑料焦烧塑料焦烧是塑料挤出过程中常见的质量缺陷,其注意表现为:温度显示超高;机头模口有大量烟雾、强烈刺激味,严重时有爆裂声;挤出塑料层有焦粒;合胶缝处有连续气泡;产生的注主要原因有:1)、温度控制超高达到塑料热降解温度;2)螺杆长期未清洗,积存的焦烧物随熔融塑料挤出;3)加温或停机时间过长,使机筒内塑料长期受热而分解;4)控温仪表失控或失准,造成高温分解;5)挤出机冷却系统未打开,造成物料剪切摩擦过热。
线材行业押出安全技术操作规程样板

一、押出机手操作时注意事项1.开机时料常会有受潮的情形,一定要在开机前在烘料桶上烘干,烘干温度一般PVC为50℃~70℃之间、PE料约50℃~70℃、HDPE料约80℃~100℃、发泡料约80℃~100℃之间、PU约70℃~85℃、PBT料120℃~140℃之间.开机漏料中如有发现一点外被有气孔就是料受潮.2.一般CL2料或80℃料其耐燃剂加重常会开机时发现外观麻麻,押出时尽量将押出机内段温度降低,让耐燃剂不致于螺缸内段中起化学作用,而于机头与眼模段加高温度让料胶化而不会麻麻的情形.3.为了减少杂质,押出机每周必须将螺杆取出,进行清洁和保养,遇到特殊情况时,如:更换不同规格物料,不仅要把料桶清洁干净,此时必须将螺杆取出,同机头一起进行全面清洁,避免不同物质混入。
于漏料完毕之后,需尽快将蜂巢板装上之前必须要预热才不会有胶粒不良情形与温度不足引起死料.4.开机之后需注意料的押出,引取机的稳定性好不好,料押出之后常常会发生眼模有料屎时,有可能机头本身压力不足,必要时将模具换小增加压力.5.机头电热片要机头紧密加温才会快带平均.6.感温棒须确实的锁进去,严禁将感温线夹在电热片上.7.发现外观有分流线时,将押出速度降低或将机头温度升高,如还有此一情形,尽可能将眼模套加长让料胶化时间多一点.8.发现外被押出有拖痕立刻停机,将外模取下用砂布修整或换外模..9.押出装上模具前,一定要将内模管往后退,避免装内外模时伤到模具.10.装好模具时可用气枪将外模吹出,看其内外模廊段距离是否符合设计卡上要作的线的条件.11.装上外模时,严禁用坚硬材质如板手或铁棒将外模敲进外模套内,会使外模壁变形,内流道改变.12.线材放线架需时常注意放线是否平稳,不稳时会影响押出外观,OD不稳或凹凸情形.13.押出机机头严禁有风扇直吹,会造成亮雾不均或有死料产生.14.印字机印字刮片座角度的调整最理想角度是刮片座与印字轮成30度角.15.油墨使用浓度需适中,不可太浓,会有印字拖痕,太淡会有散形或印字模糊不清.16.引取机一般都可以调整,较小的线用高速档,较大的线用低速档,押出时才比较好控制.17.储线架的使用张力不可太强会影响线的特性.18.收线张力不可太强,排线距离依实际线的外径来调整卷取,排线一定要好.避免轴子与外被磨擦造成不良.19.押出时过滤网需注意是否将蜂巢板全部盖上,避免有杂料流入模具之内,造成破皮或外观起颗粒的情形,押出一段时间尽可能将网膜换过,避免有破网的情形,影响质量.20.押出机机头的水平需调正,才不会影响押出时的偏心度.21.外被押出时校正完毕后,正式生产时需作记号确认是否有偏心的情形.22.押出机控制箱上的各段温度控制要常注意,如发现故障要马上修理,而电流表上的电流要作记号才能看出电热片是否故障.23.线材押出时首件检验必须落实,导体材质、亮雾度、押出方式、印字内容、偏心度、外径是否符合制造标准书要求.24.线上的冷却水槽要保持干净,水源保持清洁,不可在水槽里清洗任何物品,每天保持至少清洗一次,以免脏污附在线的表面。
- 1、下载文档前请自行甄别文档内容的完整性,平台不提供额外的编辑、内容补充、找答案等附加服务。
- 2、"仅部分预览"的文档,不可在线预览部分如存在完整性等问题,可反馈申请退款(可完整预览的文档不适用该条件!)。
- 3、如文档侵犯您的权益,请联系客服反馈,我们会尽快为您处理(人工客服工作时间:9:00-18:30)。
塑料和导体塑料电现电缆要适应各种不同需要,就应具有广泛的优异而稳定的使用性能。
塑料电线电缆的使用性能和寿命,决定于产品结构的先进性、塑料选用的合理性以及工艺的完善性。
从塑料电现电缆技术的发展来看,合理而正确的使用材料是关键的因素。
为了制造性能优异而稳定的塑料电线电缆,在导电线芯和半成品缆芯满足规定的技术要求的前提下,主要是对绝缘和护套用塑料提出了较高的要求。
绝缘塑料的基本要求是具有优异的电绝缘性能,同时根据产品用途和使用条件分别提出对机械性能、耐高温性、物理-化学性能及工艺性能的要求。
对护套塑料的基本要求是耐受各种环境因素作用的老化性能,在满足这个条件下分别提出一些特殊要求和辅助要求。
第一节塑料塑料是高分子合成材料中凡是性能上具有可塑性变化的材料的总称。
塑料可分为热塑性塑料和热固性塑料两大类,电线电缆制造中所用的塑料都是热塑性塑料。
电线电缆常用的热塑性塑料有聚氯乙烯、聚乙烯、交联聚乙烯、泡沫聚乙烯、氟塑料、聚酰胺、聚丙烯和聚酯塑料等。
塑料是以合成树脂为基本成份,再添加各种配合剂,经捏合、切粒等工艺而塑制成一定形状的材料。
为了满足加工、贮存和使用的要求,合成树脂内一般都要添加各种配合剂,根据添加配合剂所起的作用不同,塑料的添加剂大致有以下几种:防老剂(它包括抗氧剂、稳定剂、紫外线吸收剂、光屏蔽剂等,这几种材料在塑料中所起的作用不同但又相互联系,同一种材料可起几种作用,所以统称为防老剂。
);增塑剂;交联剂;润滑剂;填充剂;着色剂;发泡剂;防霉剂;驱避剂;阻燃剂;耐电压稳定剂;抑烟剂等。
各种塑料既具有塑料共有的特性,又具有各不相同的各自独具的某些特性。
各种塑料共有的特性有:比重小、机械性能较高、电绝缘性能优异并且化学稳定性好、耐水、耐油、加工成型方便,原料来源丰富。
为了适应日益增长的电线电缆技术发展的需要,塑料将不断改进配方和性能,提高其耐热性和电压等级,提高材料的耐寒、耐大气老化性能、耐火阻燃性能,延长电线电缆使用寿命,同时,还将不断开发新型塑料并合理用于电线电缆上。
一、塑料基本性能的含义1.体积电阻系数塑料在电场的作用下有泄漏电流通过,泄漏电流通过塑料时的阻力称为体积电阻。
电流通过每1cm3塑料的电阻即为体积电阻系数ρv,单位为欧姆米,单位符号为Ω.m。
体积电阻系数越高,绝缘性能越好。
2.击穿场强当塑料上施加的电压达到某一极限时,塑料丧失绝缘性能被击穿,击穿瞬间所施加的电压值称为塑料的击穿电压,击穿电压与塑料厚度之比称为击穿场强E单位符号为kV/mm。
3.介电常数它是表示塑料极性大小的指标。
介电常数ε越小,塑料在电场作用下的极化强度越小,其介质损耗也越小。
4.介质损耗角正切在交变电场作用下,塑料中所消耗的级量称为介质损耗。
它常以介质损耗角的正切值tgδ来表示。
介质损耗角正切tgδ越小,说明介质损耗也越小,塑料的电绝缘性能越好。
在高频、高压下使用时,要求塑料的tgδ值不大于千分之几或万分之几;低压和一般的绝缘时,塑料的tgδ值则不大于百分之几。
5.耐电晕性在高电压情况下,由于绝缘表面放电而引起电晕,当其袭击绝缘体时,因离子撞击、电子袭击、臭氧袭击和局部热的作用,导致高聚物裂解,使其电绝缘性能和物理机械性能产生恶化。
塑料抵抗电晕作用而保持其使用性能的能力,称为耐电晕性。
6.抗拉强度和延伸率在材料拉力试验机上对塑料试样施加静态拉伸载荷并以一定速度拉伸直至试样断裂。
此时试样单位截面上所承受的拉力称为该塑料的抗拉强度。
试样拉断时长度增加的百分比称为该塑料的延伸率。
7.密度在一定温度下(通常指20o C),单位体积塑料试样的质量,称为塑料的密度。
8.耐热变形性塑料在受热条件下,仍能保持良好的物理机械性能的最高温度,即为该塑料的耐热变形性能。
通常以塑料在等速升温时,在一定负荷下使其变形达到规定值时的温度来表示。
9.熔融指数在一定温度荷压力下,熔融树脂在10分钟内从一定孔穴中被压出的克数,称为熔融指数,以MI表示,单位为g/min。
10.耐寒性在低温下,塑料仍能保持一定的物理机械性能的能力,称为塑料的耐寒性。
它常用以下的耐寒温度来表示。
(1)低温脆化温度:即为塑料在低温下,受特定的冲击负荷时,50%的试样出现损坏时的温度。
(2)低温对折温度:即为塑料试样在弯折180o时出现将要破裂而未破裂时的温度。
(3)低温冲击压缩温度:即为塑料试样在低温下,以一定能量和速度的冲锤对其进行冲击压缩,使之破裂率达50%时的温度。
11.耐燃性能耐燃性能是指塑料抵抗火焰燃烧的能力。
通常塑料接触火焰后均会燃烧,移去火焰后,延燃情况随塑料品种不同而不同,因此耐燃性能亦有差别。
12.耐热老化性能塑料在加工和使用过程中,由于变热导致塑料性能变劣,这种现象称为热老化。
塑料抵抗热老化的能力称为耐热老化性。
采用在高温下,进行加速热老化试验,测定塑料性能(机械性能或电气性能)在老化后的保留率,来衡量塑料的耐热老化性。
13.耐气候性塑料在大气条件下使用,受日晒、雨淋、风吹、大气污染等严酷的自然条件作用,塑料性能变劣称为大气老化。
塑料抵抗大气老化的能力称塑料的耐气候性。
14.耐油性能及耐溶剂性能塑料与矿物油或各类溶剂接触时,抵御油或溶剂的能力称为塑料的耐油性能或耐溶剂性能。
可用试样浸入油或溶剂中,在一定温度下经一定时间后,测定其吸油或溶剂的吸收率、体积变化率或抗拉强度、延伸率的保留率来衡量。
15.耐水性及耐湿性塑料在浸水或潮湿条件下,抵御水或潮湿气体渗入的能力,称为塑料的耐水性或耐湿性。
塑料吸水或吸湿后,会引起绝缘电阻、击穿场强下降,介质损耗增大,且使塑料的外观、重量、机械性能等都有变化。
所以要求塑料应具有良好的耐水性和耐湿性。
对于电线电缆用塑料,主要考虑的是,在浸水或吸湿后,应保证塑料的电绝缘性能符合使用要求。
塑料的吸水量,可用单位面积的吸水量、吸水率或吸水重量来表示。
塑料的透湿性,则以透湿系数和透汽量来表示。
16.耐环境应力开裂性一些结晶型塑料,由于加工过程中内应力的存在和使用时接触化学药品,致使在贮存和使用中出现开裂,称为环境应力开裂。
塑料抵御环境应力开裂的能力称为耐环境应力开裂性能。
可用表面刻有槽痕的塑料弯曲试样,置入表面活性剂中,观察在规定时间内出现开裂的试样数量及所占比例来衡量。
二、聚氯乙烯(PVC)聚氯乙烯塑料是以聚氯乙烯树脂为基础,加入各种配合剂混合而成的。
其机械性能优越、耐化学腐蚀、不延燃、耐气候性好、电绝缘性能好、容易加工、成本低,因此是电线电缆绝缘和护套用的好材料。
1.聚氯乙烯树脂聚氯乙烯树脂是由氯乙烯聚合而成的线型热塑性高分子化合物,其分子结构如下:H H H H H H…… C C C C C C ……Cl H Cl H Cl Hn从该分子结构看,聚氯乙烯具有以碳链为主链,呈线型,含有C Cl极性键。
聚氯乙烯树脂具有下列基本特性:(1)是热塑性的高分子材料,可塑性和柔软性较好。
(2)由于C Cl极性键的存在,树脂具有较大德极性,因此介电常数ε和介质损耗角的正切值较大,在低频情况下,有较高的耐电强度。
另外由于极性键的存在,分子间的作用力较大,机械强度较高。
(3)分子结构中含有氯原子,树脂具有不延燃和较好的耐化学腐蚀性及耐气候性。
氯原子能破坏分子的晶体结构,树脂的耐热性较低,耐寒性较差,加入适量的配合剂,就能改善树脂的性能。
2.聚氯乙烯树脂的种类聚乙烯的聚合方法有:悬浮聚合、浮液聚合、本体聚合和溶液聚合四种。
聚氯乙烯树脂的制造目前主要采用悬浮聚合方法,电线电缆就是采用悬浮法聚氯乙烯树脂。
聚氯乙烯悬浮聚合过程中所用树脂的结构形状有:疏松型树脂(XS型)和紧密型树脂(XJ型)。
疏松型树脂质地疏松,吸油性大,易于塑化,加工操作控制方便,晶点少,因此电线电缆用的树脂是疏松型。
树脂的特性如下:3.聚氯乙烯的主要性能1)电绝缘性能:聚氯乙烯树脂是一种极性较大的电介质,电绝缘性能较好,但比较非极性材料(如聚乙烯、聚丙烯)稍差。
树脂的体积电阻率大于1015Ω·cm;树脂在25o C和50H z频率下的介电常数ε为3.4~3.6,当温度和频率变化时,介电常数也随之明显的变化;聚氯乙烯的介质损耗正切tgδ为0.006~0.2。
树脂的击穿场强不受极性影响,在室温和工频条件下的击穿场强比较高。
但聚氯乙烯的介质损耗较大,因而不适用于高压和高频场合,通常用在15kV以下的低压和中压电线电缆的绝缘材料。
2)老化稳定性:从分子结构上看,氯原子都与碳原子相连,应具有较高的耐老化稳定性。
但在生产过程中,由于温度的直接影响和机械力的作用,易放出氯化氢,在氧的作用下,产生降解或交联,导致材料变色发脆,物理机械性能显著下降,电绝缘性能恶化,因此聚氯乙烯老化。
为改善它的老化性,必须添加一定的稳定剂。
3)热机械性能:聚氯乙烯树脂为无定型聚合物,在不同温度下具有三种物理状态,即玻璃态、高弹态、粘流态。
聚氯乙烯树脂的玻璃化温度为80o C左右,粘流温度160o C左右。
在常温下处于玻璃状态,这很难满足电线电缆使用要求。
为此,必须将聚氯乙烯进行改性,使其在室温下具有较高的弹性,同时又兼有较高的耐热性和耐零性。
加入适量的增塑剂能够调节玻璃化温度,以增加塑性,达到柔软性,提高机械性能。
4.电线电缆用聚氯乙烯塑料聚氯乙烯塑料是多组份塑料,根据不同的使用条,改变配合剂的品种和用量,能够制得不同品种的电线电缆用聚氯乙烯塑料。
聚氯乙烯电缆塑料按其在电线电缆上用途不同,可分为绝缘级电缆料和护层级电缆料。
(1)绝缘用聚氯乙烯塑料根据电线电缆的使用要求和特性,绝缘用聚氯乙烯塑料的类型、性能、要求及主要用途如下表所示。
绝缘用PVC塑料分类及性能各类聚氯乙烯绝缘料的技术要求见下表。
绝缘用PVC塑料的技术要求(2)护套用聚氯乙烯塑料聚氯乙烯塑料护层具有较好的耐腐蚀性,足够的机械性能,一定的耐大气性能,柔软、耐振、重量轻、加工及敷设方便。
根据电线电缆的使用条件,研究制成了不同类型聚氯乙烯护套料,其性能要求及应用范围见下表。
护套用PVC塑料的分类及性能(3)半导电聚氯乙烯塑料半导电聚氯乙烯塑料可作为屏蔽材料来使用,例如可作为10kV聚氯乙烯电缆的屏蔽层。
半导电塑料用作高压电缆的屏蔽料时,由于半导电料直接与绝缘料接触,会发生相互迁移,因而尽量选用与绝缘料相同的增塑剂或电性好、迁移小的增塑剂。
否则在使用过程中会影响绝缘料的电绝缘性能。
(4)环保型防白蚁、防鼠电缆护套料白蚁和老鼠对电缆造成破坏,轻则中断供电,重则酿成重大事故,使电力和通信部门受到损害。
以往采用在电缆护套料内加入有毒添加剂(如氯丹、七氯、狄氏剂、艾氏剂等)的办法,杀灭白蚁、老鼠,以保护电缆安全运行。
但这些有毒添加剂对环境和人身会造成污染和危害。
目前,多使用在护套料中加入环烷酸铅或环烷酸酮做添加剂,制成改型的防白蚁护套料。