钢铁厂除尘灰及其他废弃物的再利用技术
钢铁冶炼废弃物处理的新技术
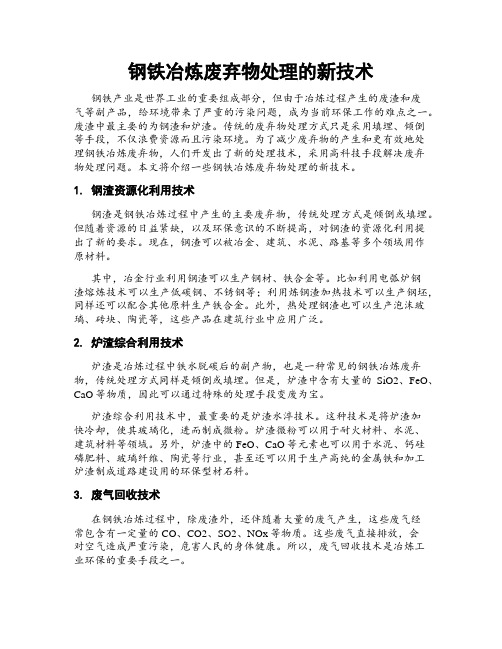
钢铁冶炼废弃物处理的新技术钢铁产业是世界工业的重要组成部分,但由于冶炼过程产生的废渣和废气等副产品,给环境带来了严重的污染问题,成为当前环保工作的难点之一。
废渣中最主要的为钢渣和炉渣。
传统的废弃物处理方式只是采用填埋、倾倒等手段,不仅浪费资源而且污染环境。
为了减少废弃物的产生和更有效地处理钢铁冶炼废弃物,人们开发出了新的处理技术,采用高科技手段解决废弃物处理问题。
本文将介绍一些钢铁冶炼废弃物处理的新技术。
1. 钢渣资源化利用技术钢渣是钢铁冶炼过程中产生的主要废弃物,传统处理方式是倾倒或填埋。
但随着资源的日益紧缺,以及环保意识的不断提高,对钢渣的资源化利用提出了新的要求。
现在,钢渣可以被冶金、建筑、水泥、路基等多个领域用作原材料。
其中,冶金行业利用钢渣可以生产钢材、铁合金等。
比如利用电弧炉钢渣熔炼技术可以生产低碳钢、不锈钢等;利用炼钢渣加热技术可以生产钢坯,同样还可以配合其他原料生产铁合金。
此外,热处理钢渣也可以生产泡沫玻璃、砖块、陶瓷等,这些产品在建筑行业中应用广泛。
2. 炉渣综合利用技术炉渣是冶炼过程中铁水脱碳后的副产物,也是一种常见的钢铁冶炼废弃物,传统处理方式同样是倾倒或填埋。
但是,炉渣中含有大量的SiO2、FeO、CaO等物质,因此可以通过特殊的处理手段变废为宝。
炉渣综合利用技术中,最重要的是炉渣水淬技术。
这种技术是将炉渣加快冷却,使其玻璃化,进而制成微粉。
炉渣微粉可以用于耐火材料、水泥、建筑材料等领域。
另外,炉渣中的FeO、CaO等元素也可以用于水泥、钙硅磷肥料、玻璃纤维、陶瓷等行业,甚至还可以用于生产高纯的金属铁和加工炉渣制成道路建设用的环保型材石料。
3. 废气回收技术在钢铁冶炼过程中,除废渣外,还伴随着大量的废气产生,这些废气经常包含有一定量的CO、CO2、SO2、NOx等物质。
这些废气直接排放,会对空气造成严重污染,危害人民的身体健康。
所以,废气回收技术是冶炼工业环保的重要手段之一。
钢铁冶炼过程中产生的废弃钢渣循环再利用

钢铁冶炼过程中产生的废弃钢渣循环再利用近年来,随着可持续发展战略的进一步实施和落实,钢铁工业作为基础原料供应产业和社会能源消耗大户不得不进行整改。
具体整改方式是在未来工业中需要从国家长远经济利益出发,以节能环保为核心开展,但是由于我国钢铁工业起步晚、起点低,没有发达国家钢铁工业生产中廉价资源及环境容量,这就要求在钢铁生产中要在不损害环境的基础上,以最小的代价换取最大经济效益。
基于这种要求,以废弃钢渣为主的废弃材料循环利用逐渐被人们重视,成为工作重点。
1 废弃钢渣现状废弃钢渣是钢铁工业生产、加工和冶炼中所出现的一种废弃物,它伴随我国经济发展、钢铁工业进步而不断增长。
与国外发达国家的钢铁工业生产加工技术相比较,我国的钢铁生产技术还有待提高,对废弃钢渣再利用技术非常落后,目前每生产一吨钢材大约会产生0.2 吨的废弃钢渣。
这些钢渣在堆放和排除中一方面占据了大量的生产车间和工区,另外也造成很大的环境污染。
因此,为了更好的解决钢铁工业生产中存在的这方面问题,国内各大钢铁生产企业和单位都投入大量的人力物力研究废弃钢渣的再次循环利用新技术,也取得了一定的成绩。
目前我们常见的废弃钢渣循环利用技术主要包含了:废弃钢渣回收金属技术、废弃钢渣污水处理技术、废弃钢渣磷回收技术等;同时也有不少化工产业对这些物质采用了回收处理技术。
2 传统钢铁工业加工中废弃钢渣处理技术2.1 废弃钢渣制造水泥铁质校核材料经过长期工作实践我们发现,全国各地钢铁工业生产中大多都能是将废弃钢渣直接应用到建筑业,是以水泥胶和材料的主要原材料,这种材料在水泥制造材料中能直接替代传统的铁成分,起到校核铁的作用。
2.2 废弃钢渣制造农业化工材料在一些化工生产中,废弃钢渣被广泛的使用,一方面废弃钢渣经过高温加热之后能够直接添加到烧结矿中,另外即便会出现一定的问题对整个化工产品的质量影响也并不是很大,可以说它的应用很大程度上保证了化工农产品的稳定性。
因此,这种技术的应用可谓是对我国农业、化工业的发展起到一定的积极推动作用。
钢铁厂废弃物处理与资源化利用规定

信息公开
钢铁厂应将废弃物处理与资源化 利用情况向社会公开,接受公众
监督。
05
钢铁厂废弃物处理与资源化利用 经济效益分析
经济效益评估方法与指标体系建立
评估方法
采用成本效益分析、投资回报率、净现值等评估方法,对钢铁厂废弃物处理与资 源化利用项目进行经济效益评估。
指标体系
建立包括投资成本、运行成本、资源回收量、销售收入、利润等在内的指标体系 ,全面衡量项目的经济效益。
设备要求
安全要求
采用先进的设备,提高资源化利用效 率。
在资源化利用过程中,应确保设备和 设施的安全运行,防止事故发生。
设施要求
建设完善的资源化利用设施,包括废 弃物储存设施、加工处理设施等。
04
钢铁厂废弃物处理与资源化利用 监管措施
监管机构与职责分工
环保部门
负责制定钢铁厂废弃物处理与资源化 利用相关政策和标准,并监督实施。
目的
为了规范钢铁厂废弃物的处理和资源化利用,提高资源利用效率,减少环境污 染,促进可持续发展。
背景
随着钢铁工业的快速发展,钢铁厂废弃物产生量不断增加,对环境造成了严重 污染。为了解决这一问题,需要制定相应的规定,规范废弃物的处理和资源化 利用。
汇报范围
钢铁厂废弃物处理与资源化利用规定适用于所有钢铁企业。 本规定涉及的废弃物包括废渣、废气、废水等。
THANKS
感谢观看
钢铁厂废弃物处理与资源化利用规 定
汇报人:XXX 2023-12-14
目录
• 引言 • 钢铁厂废弃物处理规定 • 钢铁厂废弃物资源化利用规定 • 钢铁厂废弃物处理与资源化利用监管
措施
目录
• 钢铁厂废弃物处理与资源化利用经济 效益分析
探析钢铁企业尘泥资源再生利用-钢铁工业论文-工业论文
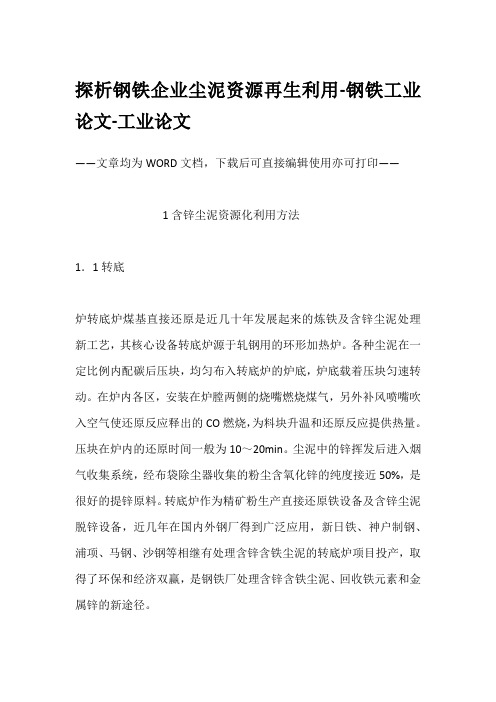
探析钢铁企业尘泥资源再生利用-钢铁工业论文-工业论文——文章均为WORD文档,下载后可直接编辑使用亦可打印——1含锌尘泥资源化利用方法1.1转底炉转底炉煤基直接还原是近几十年发展起来的炼铁及含锌尘泥处理新工艺,其核心设备转底炉源于轧钢用的环形加热炉。
各种尘泥在一定比例内配碳后压块,均匀布入转底炉的炉底,炉底载着压块匀速转动。
在炉内各区,安装在炉膛两侧的烧嘴燃烧煤气,另外补风喷嘴吹入空气使还原反应释出的CO燃烧,为料块升温和还原反应提供热量。
压块在炉内的还原时间一般为10~20min。
尘泥中的锌挥发后进入烟气收集系统,经布袋除尘器收集的粉尘含氧化锌的纯度接近50%,是很好的提锌原料。
转底炉作为精矿粉生产直接还原铁设备及含锌尘泥脱锌设备,近几年在国内外钢厂得到广泛应用,新日铁、神户制钢、浦项、马钢、沙钢等相继有处理含锌含铁尘泥的转底炉项目投产,取得了环保和经济双赢,是钢铁厂处理含锌含铁尘泥、回收铁元素和金属锌的新途径。
1.2竖炉德国蒂森钢铁集团采用竖炉工艺处理含锌含铁尘泥取得了良好的经济和环保效益;中国太钢集团也已投产了采用含锌尘泥为原料的竖炉生产铁水工艺。
竖炉的冶炼过程类似于小型高炉,竖炉原料为含碳六角形尘泥压块、铸造焦、废钢。
除尘污泥的含锌量为16%,必须将污泥回用竖炉,使锌富集到30%以上外销。
国内淘汰的小高炉可以用来处理含锌含铁尘泥,但在环保、尘泥的运输成本和锌的有效回收利用等方面有所欠缺。
由于竖炉本身的特点,竖炉原料需至少添加约20%的废钢,直接提升了竖炉的经济效益,这在一定程度上使竖炉充当了废钢的熔化炉,日本JFE在2008年建造的竖炉就专门作为废钢的熔化炉。
1.3转底炉和竖炉工艺的比较两种工艺都有本身的优缺点。
转底炉现阶段对于处理钢铁厂含铁尘泥能取得一定效果,但对处理高锌尘泥仍然存在产品残留锌含量,不能满足大高炉入炉要求的缺陷。
竖炉产品铁水可直接进入炼钢系统使用,不必考虑产品含锌量的问题,但是存在含锌粉尘等在竖炉炉膛内挥发,对炉衬耐火材料进行附着,造成耐火材料使用寿命降低;竖炉生产的铁水含硫率超过炼钢厂的入炉标准;含锌尘泥的锌元素不能有效回收利用等问题。
钢铁行业废弃物综合利用技术综述
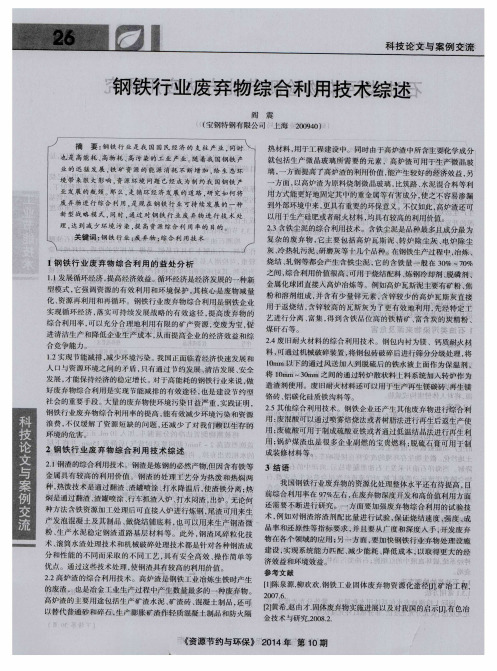
品率和还原性 等指标要求 , 并且 要从广度 和深 度人手 , 开发废 弃
物在各个领域 的应用 ; 另一方 面 , 要 加快钢铁行业弃 物处理 没施
2钢铁 行 业废 弃物 综合 利用 技术 综述
成装修材料等。
2 . 1 钢渣 的综合利用技术 。钢渣是炼钢 的必然产物, 但因含有铁等 3结 语 金属具有较 高的利 价值 。钢 渣的处 理] - 艺分 为热泼 和热焖 两 我 国钢铁行业废弃物 的资源化处理整体水平还有待提高 , 目 种, 热 泼技 术是通过翻渣 、 潘罐喷涂 、 打水 降温后 , 使渣铁分 离 ; 热 前综合利用率在 9 7 %左右 , 在废弁物深度开发和高价值利 用方 面
金属化球 团直接人高炉冶炼等 。 并 含有少量锌 元素 , 含锌较少 的高炉瓦斯灰直 接
用 于返烧 结 , 含锌较 高的 瓦斯 灰为 了更有效 地利用 , 先经特定 工 实现循 环经济 , 落实可持续 发展 战略的有效 途径 , 提高废 弃物 的 艺进行分 离 、 富集 . 得 到含铁品位高 的铁 精矿 、 富含炭 的炭精粉 、 综合利』 } i 率, 可 以允分合理地 利用有 限的矿产资源 , 变 废为宝 , 促 煤 矸 石 等 。
2 _ 4 废 旧耐火材料的综合利月 J 技术。钢包内衬为镁 、钙质 耐火 材 料, 可通过机械破碎装置 , 将 钢包 砖破 碎后进行筛分分级处理 , 将 l O mm以下的通过风送加入 到脱 硫后的铁水液上面作 为保温剂 , 将 1 0 mm一 3 0 am之 间的通 过转炉散状料上料系统加 入转 炉作为 r
炼钢除尘灰资源化利用
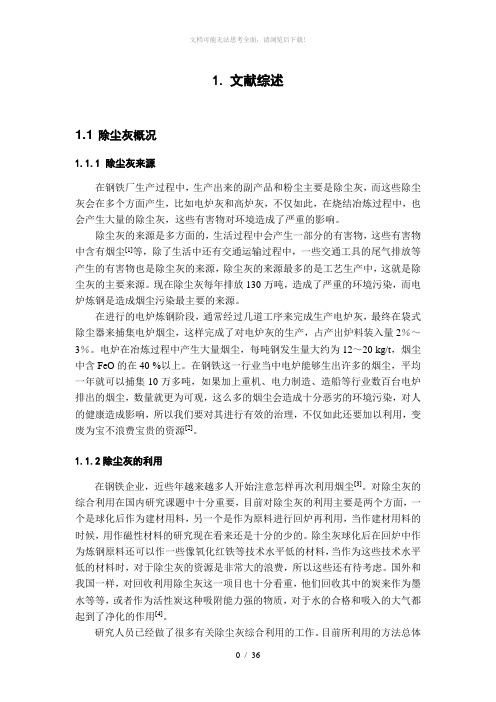
1.文献综述1.1 除尘灰概况1.1.1 除尘灰来源在钢铁厂生产过程中,生产出来的副产品和粉尘主要是除尘灰,而这些除尘灰会在多个方面产生,比如电炉灰和高炉灰,不仅如此,在烧结冶炼过程中,也会产生大量的除尘灰,这些有害物对环境造成了严重的影响。
除尘灰的来源是多方面的,生活过程中会产生一部分的有害物,这些有害物中含有烟尘[1]等,除了生活中还有交通运输过程中,一些交通工具的尾气排放等产生的有害物也是除尘灰的来源,除尘灰的来源最多的是工艺生产中,这就是除尘灰的主要来源。
现在除尘灰每年排放130万吨,造成了严重的环境污染,而电炉炼钢是造成烟尘污染最主要的来源。
在进行的电炉炼钢阶段,通常经过几道工序来完成生产电炉灰,最终在袋式除尘器来捕集电炉烟尘,这样完成了对电炉灰的生产,占产出炉料装入量2%~3%。
电炉在冶炼过程中产生大量烟尘,每吨钢发生量大约为12~20 kg/t,烟尘中含FeO的在40 %以上。
在钢铁这一行业当中电炉能够生出许多的烟尘,平均一年就可以捕集10万多吨,如果加上重机、电力制造、造船等行业数百台电炉排出的烟尘,数量就更为可观,这么多的烟尘会造成十分恶劣的环境污染,对人的健康造成影响,所以我们要对其进行有效的治理,不仅如此还要加以利用,变废为宝不浪费宝贵的资源[2]。
1.1.2除尘灰的利用在钢铁企业,近些年越来越多人开始注意怎样再次利用烟尘[3]。
对除尘灰的综合利用在国内研究课题中十分重要,目前对除尘灰的利用主要是两个方面,一个是球化后作为建材用料,另一个是作为原料进行回炉再利用,当作建材用料的时候,用作磁性材料的研究现在看来还是十分的少的。
除尘灰球化后在回炉中作为炼钢原料还可以作一些像氧化红铁等技术水平低的材料,当作为这些技术水平低的材料时,对于除尘灰的资源是非常大的浪费,所以这些还有待考虑。
国外和我国一样,对回收利用除尘灰这一项目也十分看重,他们回收其中的炭来作为墨水等等,或者作为活性炭这种吸附能力强的物质,对于水的合格和吸入的大气都起到了净化的作用[4]。
钢铁冶炼废弃物资源化利用技术
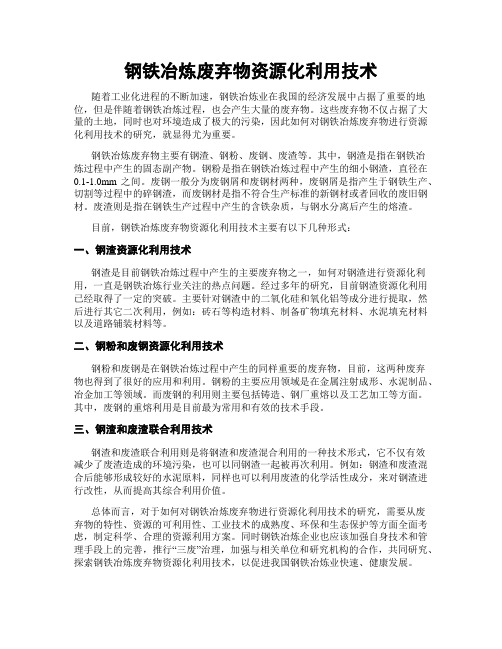
钢铁冶炼废弃物资源化利用技术随着工业化进程的不断加速,钢铁冶炼业在我国的经济发展中占据了重要的地位,但是伴随着钢铁冶炼过程,也会产生大量的废弃物。
这些废弃物不仅占据了大量的土地,同时也对环境造成了极大的污染,因此如何对钢铁冶炼废弃物进行资源化利用技术的研究,就显得尤为重要。
钢铁冶炼废弃物主要有钢渣、钢粉、废钢、废渣等。
其中,钢渣是指在钢铁冶炼过程中产生的固态副产物。
钢粉是指在钢铁冶炼过程中产生的细小钢渣,直径在0.1-1.0mm之间。
废钢一般分为废钢屑和废钢材两种,废钢屑是指产生于钢铁生产、切割等过程中的碎钢渣,而废钢材是指不符合生产标准的新钢材或者回收的废旧钢材。
废渣则是指在钢铁生产过程中产生的含铁杂质,与钢水分离后产生的熔渣。
目前,钢铁冶炼废弃物资源化利用技术主要有以下几种形式:一、钢渣资源化利用技术钢渣是目前钢铁冶炼过程中产生的主要废弃物之一,如何对钢渣进行资源化利用,一直是钢铁冶炼行业关注的热点问题。
经过多年的研究,目前钢渣资源化利用已经取得了一定的突破。
主要针对钢渣中的二氧化硅和氧化铝等成分进行提取,然后进行其它二次利用,例如:砖石等构造材料、制备矿物填充材料、水泥填充材料以及道路铺装材料等。
二、钢粉和废钢资源化利用技术钢粉和废钢是在钢铁冶炼过程中产生的同样重要的废弃物,目前,这两种废弃物也得到了很好的应用和利用。
钢粉的主要应用领域是在金属注射成形、水泥制品、冶金加工等领域。
而废钢的利用则主要包括铸造、钢厂重熔以及工艺加工等方面。
其中,废钢的重熔利用是目前最为常用和有效的技术手段。
三、钢渣和废渣联合利用技术钢渣和废渣联合利用则是将钢渣和废渣混合利用的一种技术形式,它不仅有效减少了废渣造成的环境污染,也可以同钢渣一起被再次利用。
例如:钢渣和废渣混合后能够形成较好的水泥原料,同样也可以利用废渣的化学活性成分,来对钢渣进行改性,从而提高其综合利用价值。
总体而言,对于如何对钢铁冶炼废弃物进行资源化利用技术的研究,需要从废弃物的特性、资源的可利用性、工业技术的成熟度、环保和生态保护等方面全面考虑,制定科学、合理的资源利用方案。
钢铁冶炼除尘灰作为冶炼原料的技术研究
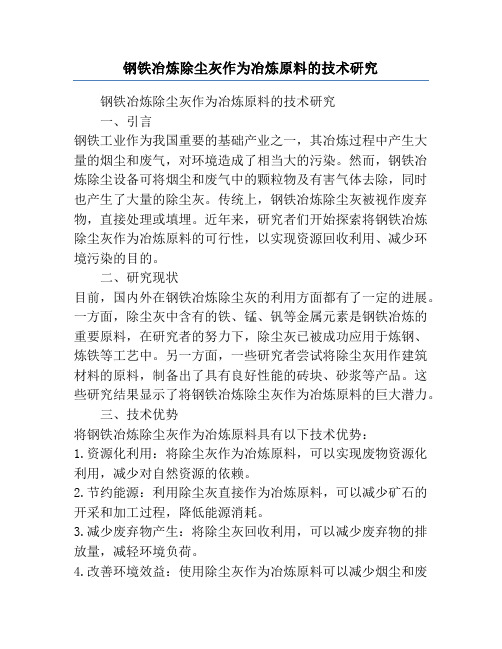
钢铁冶炼除尘灰作为冶炼原料的技术研究钢铁冶炼除尘灰作为冶炼原料的技术研究一、引言钢铁工业作为我国重要的基础产业之一,其冶炼过程中产生大量的烟尘和废气,对环境造成了相当大的污染。
然而,钢铁冶炼除尘设备可将烟尘和废气中的颗粒物及有害气体去除,同时也产生了大量的除尘灰。
传统上,钢铁冶炼除尘灰被视作废弃物,直接处理或填埋。
近年来,研究者们开始探索将钢铁冶炼除尘灰作为冶炼原料的可行性,以实现资源回收利用、减少环境污染的目的。
二、研究现状目前,国内外在钢铁冶炼除尘灰的利用方面都有了一定的进展。
一方面,除尘灰中含有的铁、锰、钒等金属元素是钢铁冶炼的重要原料,在研究者的努力下,除尘灰已被成功应用于炼钢、炼铁等工艺中。
另一方面,一些研究者尝试将除尘灰用作建筑材料的原料,制备出了具有良好性能的砖块、砂浆等产品。
这些研究结果显示了将钢铁冶炼除尘灰作为冶炼原料的巨大潜力。
三、技术优势将钢铁冶炼除尘灰作为冶炼原料具有以下技术优势:1.资源化利用:将除尘灰作为冶炼原料,可以实现废物资源化利用,减少对自然资源的依赖。
2.节约能源:利用除尘灰直接作为冶炼原料,可以减少矿石的开采和加工过程,降低能源消耗。
3.减少废弃物产生:将除尘灰回收利用,可以减少废弃物的排放量,减轻环境负荷。
4.改善环境效益:使用除尘灰作为冶炼原料可以减少烟尘和废气中有害物质的排放,改善环境质量。
四、存在问题与挑战在将钢铁冶炼除尘灰作为冶炼原料的过程中,仍然存在一些问题和挑战:1.除尘灰成分复杂。
除尘灰中含有多种元素和化合物,其成分复杂,影响了利用效果。
2.除尘灰中有害元素含量高。
除尘灰中含有一定量的重金属元素和有害气体,直接用于冶炼可能带来环境和健康的风险。
3.技术成熟度有限。
钢铁冶炼除尘灰作为冶炼原料的技术还处于初级阶段,还需要进一步的优化和改进。
五、未来发展方向为了解决以上问题并实现钢铁冶炼除尘灰作为冶炼原料的可持续利用,我们可以从以下几个方面进行研究:1.深入分析除尘灰成分。
钢厂废料循环利用方案

钢厂废料循环利用方案随着经济的快速发展,钢材的使用量也日益增加,而钢铁生产过程中产生的废料也越来越多。
废料的处理和利用已经成为一个重要的环保议题。
为了实现钢厂废料的循环利用,需要采取以下方案。
首先,要加强钢厂内部废料的分类和回收。
钢铁生产产生的废料种类繁多,如钢渣、废钢屑等。
钢厂可以通过建立科学的废物分类体系,将不同类型的废料进行分类回收。
例如,可以在钢铁生产过程中采用先进的技术将废料进行粉碎和分离,使其更易于回收利用。
同时,在废料处理过程中,要注重资源的综合利用,将其中可以再利用的物质进行回收,减少浪费。
其次,要与社会和企业合作,寻求废料的外部回收渠道。
除了内部回收,钢厂还可以积极开展废料的外部回收工作。
可以与废品回收企业合作,将废料卖给他们进行二次利用。
同时,还可以与其他行业合作,将废料作为原材料供给他们使用。
例如,废钢屑可以用来制造钢材等。
这样既可以减少废料的排放,又可以为钢厂带来额外的收益。
再次,要加强废料的再利用研究和开发。
钢厂可以投入资金和人力资源,加强对废料再利用的研究和开发。
在现有技术的基础上,不断创新,提高废料的再利用率。
例如,可以开发新的高效回收技术,将废料转化为新的有价值的材料。
同时,还可以开展废料的能源回收利用研究,将废料进行燃烧,产生能源。
这样既可以减少废料的排放,又可以节约能源,促进可持续发展。
最后,要加强宣传和教育,提高社会对废料循环利用的重视程度。
钢厂可以利用多种宣传渠道,如媒体、社交网络等,向公众普及废料循环利用的重要性。
同时,还可以加强与学校、社区等机构合作,开展废料循环利用的教育活动。
通过提高公众的环保意识,推动废料循环利用工作的开展。
综上所述,钢厂废料循环利用是一项重要的工作,需要采取多种措施来实现。
只有通过全面深入的工作,才能实现废料的高效回收和利用,推动可持续发展。
钢厂除尘灰环保处理方案
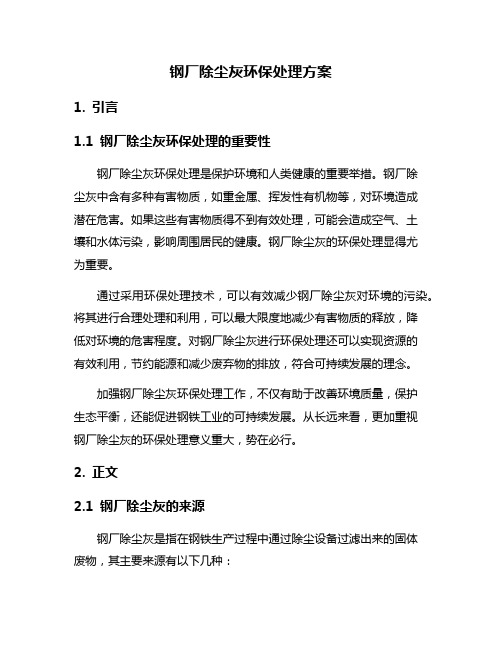
钢厂除尘灰环保处理方案1. 引言1.1 钢厂除尘灰环保处理的重要性钢厂除尘灰环保处理是保护环境和人类健康的重要举措。
钢厂除尘灰中含有多种有害物质,如重金属、挥发性有机物等,对环境造成潜在危害。
如果这些有害物质得不到有效处理,可能会造成空气、土壤和水体污染,影响周围居民的健康。
钢厂除尘灰的环保处理显得尤为重要。
通过采用环保处理技术,可以有效减少钢厂除尘灰对环境的污染。
将其进行合理处理和利用,可以最大限度地减少有害物质的释放,降低对环境的危害程度。
对钢厂除尘灰进行环保处理还可以实现资源的有效利用,节约能源和减少废弃物的排放,符合可持续发展的理念。
加强钢厂除尘灰环保处理工作,不仅有助于改善环境质量,保护生态平衡,还能促进钢铁工业的可持续发展。
从长远来看,更加重视钢厂除尘灰的环保处理意义重大,势在必行。
2. 正文2.1 钢厂除尘灰的来源钢厂除尘灰是指在钢铁生产过程中通过除尘设备过滤出来的固体废物,其主要来源有以下几种:1. 高炉炼铁工艺:高炉炼铁是钢铁生产的重要工艺之一,其中产生大量的烟尘和废气。
在高炉炼铁过程中,炉内的矿石在高温下被还原变质,生成的炉渣和废气在除尘设备中被捕集,形成除尘灰。
2. 钢厂熔炼过程:钢铁生产的另一种重要工艺是熔炼,通过电弧炉或转炉等设备熔化金属原料,去除不纯物质。
在这个过程中产生的炉渣和燃烧废气中的固体颗粒被除尘设备捕集形成除尘灰。
3. 炼钢过程中的粉尘:炼钢过程中,金属原料经过多次冶炼、合金等处理,产生大量的粉尘和烟尘。
这些粉尘在除尘设备中收集,形成除尘灰。
4. 加工工艺中的废料:在钢铁加工中会产生很多废料,比如修磨、切削、焊接等过程中产生的废渣和烟尘,均会被除尘设备捕集形成除尘灰。
2.2 钢厂除尘灰的成分分析钢厂除尘灰的成分分析是非常重要的,因为了解其具体成分可以为环保处理提供有效的参考。
钢厂除尘灰主要由氧化铁、氧化钙、氧化铝等成分组成。
氧化铁是主要成分之一,占据了除尘灰的大部分比重。
钢铁厂尘泥的回收利用
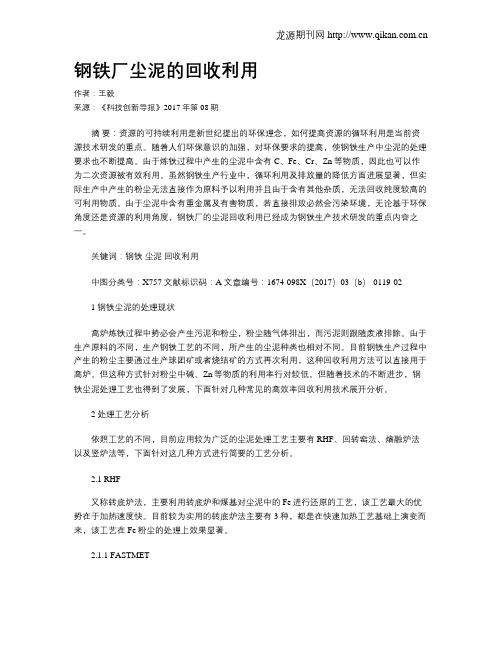
钢铁厂尘泥的回收利用作者:王毅来源:《科技创新导报》2017年第08期摘要:资源的可持续利用是新世纪提出的环保理念,如何提高资源的循环利用是当前资源技术研发的重点。
随着人们环保意识的加强,对环保要求的提高,使钢铁生产中尘泥的处理要求也不断提高。
由于炼铁过程中产生的尘泥中含有C、Fe、Cr、Zn等物质,因此也可以作为二次资源被有效利用。
虽然钢铁生产行业中,循环利用及排放量的降低方面进展显著,但实际生产中产生的粉尘无法直接作为原料予以利用并且由于含有其他杂质,无法回收纯度较高的可利用物质。
由于尘泥中含有重金属及有害物质,若直接排放必然会污染环境,无论基于环保角度还是资源的利用角度,钢铁厂的尘泥回收利用已经成为钢铁生产技术研发的重点内容之一。
关键词:钢铁尘泥回收利用中图分类号:X757 文献标识码:A 文章编号:1674-098X(2017)03(b)-0119-021 钢铁尘泥的处理现状高炉炼铁过程中势必会产生污泥和粉尘,粉尘随气体排出,而污泥则跟随废液排除。
由于生产原料的不同,生产钢铁工艺的不同,所产生的尘泥种类也相对不同。
目前钢铁生产过程中产生的粉尘主要通过生产球团矿或者烧结矿的方式再次利用,这种回收利用方法可以直接用于高炉。
但这种方式针对粉尘中碱、Zn等物质的利用率行对较低。
但随着技术的不断进步,钢铁尘泥处理工艺也得到了发展,下面针对几种常见的高效率回收利用技术展开分析。
2 处理工艺分析依照工艺的不同,目前应用较为广泛的尘泥处理工艺主要有RHF、回转窑法、熔融炉法以及竖炉法等,下面针对这几种方式进行简要的工艺分析。
2.1 RHF又称转底炉法,主要利用转底炉和煤基对尘泥中的Fe进行还原的工艺,该工艺最大的优势在于加热速度快。
目前较为实用的转底炉法主要有3种,都是在快速加热工艺基础上演变而来,该工艺在Fe粉尘的处理上效果显著。
2.1.1 FASTMET该方法主要将Fe3O2和粉煤充分混合预制成团块并铺设在RHF炉床上,再并对其加热至1 350 ℃,达到加热还原的效果,6~12 min后,可以得到还原铁。
炼钢除尘灰资源化利用

1.文献综述1.1 除尘灰概况1.1.1 除尘灰来源在钢铁厂生产过程中,生产出来的副产品和粉尘主要是除尘灰,而这些除尘灰会在多个方面产生,比如电炉灰和高炉灰,不仅如此,在烧结冶炼过程中,也会产生大量的除尘灰,这些有害物对环境造成了严重的影响。
除尘灰的来源是多方面的,生活过程中会产生一部分的有害物,这些有害物中含有烟尘[1]等,除了生活中还有交通运输过程中,一些交通工具的尾气排放等产生的有害物也是除尘灰的来源,除尘灰的来源最多的是工艺生产中,这就是除尘灰的主要来源。
现在除尘灰每年排放130万吨,造成了严重的环境污染,而电炉炼钢是造成烟尘污染最主要的来源。
在进行的电炉炼钢阶段,通常经过几道工序来完成生产电炉灰,最终在袋式除尘器来捕集电炉烟尘,这样完成了对电炉灰的生产,占产出炉料装入量2%~3%。
电炉在冶炼过程中产生大量烟尘,每吨钢发生量大约为12~20 kg/t,烟尘中含FeO的在40 %以上。
在钢铁这一行业当中电炉能够生出许多的烟尘,平均一年就可以捕集10万多吨,如果加上重机、电力制造、造船等行业数百台电炉排出的烟尘,数量就更为可观,这么多的烟尘会造成十分恶劣的环境污染,对人的健康造成影响,所以我们要对其进行有效的治理,不仅如此还要加以利用,变废为宝不浪费宝贵的资源[2]。
1.1.2除尘灰的利用在钢铁企业,近些年越来越多人开始注意怎样再次利用烟尘[3]。
对除尘灰的综合利用在国内研究课题中十分重要,目前对除尘灰的利用主要是两个方面,一个是球化后作为建材用料,另一个是作为原料进行回炉再利用,当作建材用料的时候,用作磁性材料的研究现在看来还是十分的少的。
除尘灰球化后在回炉中作为炼钢原料还可以作一些像氧化红铁等技术水平低的材料,当作为这些技术水平低的材料时,对于除尘灰的资源是非常大的浪费,所以这些还有待考虑。
国外和我国一样,对回收利用除尘灰这一项目也十分看重,他们回收其中的炭来作为墨水等等,或者作为活性炭这种吸附能力强的物质,对于水的合格和吸入的大气都起到了净化的作用[4]。
钢铁生产中的环保技术和废弃物处理

钢铁生产中的环保技术和废弃物处理随着我国经济的快速发展和城市化进程的加速,对钢铁产品的需求增加,也推动了钢铁生产的快速发展。
然而,传统的钢铁生产模式中,废气、废水、固体废物等环境问题日益凸显。
为了解决这些环境问题,钢铁企业在生产过程中逐步引入环保技术,并进行废弃物处理,以达到可持续发展的目标。
一、钢铁生产中的环保技术1. 脱硫技术:钢铁生产过程中,喷吹脱硫技术是目前最主流的方法,其原理是通过喷射石灰石或石灰乳到高温炉内形成CaCO3和CaO,从而实现炉内二氧化硫的反应,最终达到脱硫的目的。
喷吹脱硫的最大优点在于可以降低二氧化硫排放,且操作相对简单,已经广泛应用于钢铁企业的脱硫过程中。
2. 脱硝技术:脱硝技术主要是针对高温炉内NOX(氮氧化物)排放问题,其原理是通过低温催化、选择性催化等技术方式降低高温炉内NOX的排放。
其中低温催化技术是一种比较成熟的技术,其核心就是“还原-氧化”反应,可以有效降低NOX的排放,目前已经广泛应用在钢铁企业中。
3. 脱除颗粒物技术:钢铁生产过程中,颗粒物是一种常见的污染物,也是造成大气污染的重要源头。
目前,通过高压喷雾、静电除尘、湿式电除尘等技术手段可以有效地去除颗粒物,减少钢铁生产过程中的颗粒物排放。
二、钢铁生产废弃物的处理1. 污泥处理:钢铁生产过程中会产生大量火力锅炉废渣、储存池底泥和渣坑底泥等,这些废弃物中含有大量有机物、磷、氮等污染物,这些物质经长期暴露会对水、土壤、空气等环境形成严重的环境污染。
钢铁企业可以通过高温焚烧、微波辅助烘干等方式对这些污泥进行处理,将有害物质转化为无害物质,达到环保要求。
2. 炉渣处理:钢铁生产过程中会产生大量的炉渣,其中粗炉渣、精炼渣、脱硫渣等不同种类的渣可以进行不同的处理方式。
例如,对于粗炉渣,可以通过细碎、分级、选别等方式处理,将其转化为可用的脆性炉料;对于精炼渣,则可以通过针对性的化学处理来回收银、钴、钼等有价值的金属元素。
钢铁厂的三废治理与再利用
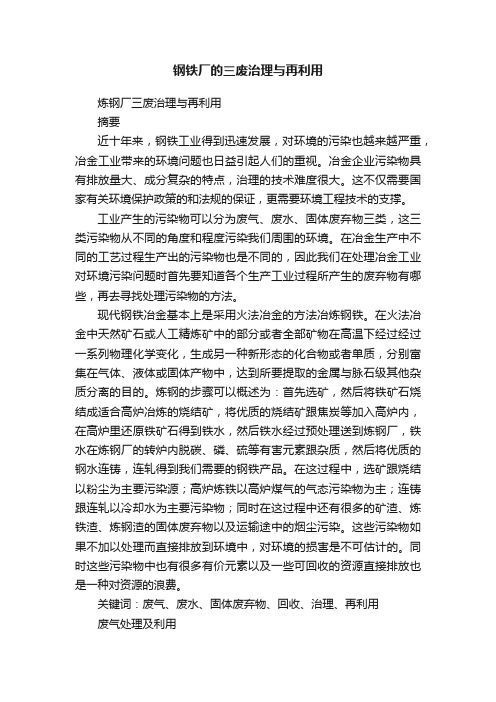
钢铁厂的三废治理与再利用炼钢厂三废治理与再利用摘要近十年来,钢铁工业得到迅速发展,对环境的污染也越来越严重,冶金工业带来的环境问题也日益引起人们的重视。
冶金企业污染物具有排放量大、成分复杂的特点,治理的技术难度很大。
这不仅需要国家有关环境保护政策的和法规的保证,更需要环境工程技术的支撑。
工业产生的污染物可以分为废气、废水、固体废弃物三类,这三类污染物从不同的角度和程度污染我们周围的环境。
在冶金生产中不同的工艺过程生产出的污染物也是不同的,因此我们在处理冶金工业对环境污染问题时首先要知道各个生产工业过程所产生的废弃物有哪些,再去寻找处理污染物的方法。
现代钢铁冶金基本上是采用火法冶金的方法冶炼钢铁。
在火法冶金中天然矿石或人工精炼矿中的部分或者全部矿物在高温下经过经过一系列物理化学变化,生成另一种新形态的化合物或者单质,分别富集在气体、液体或固体产物中,达到所要提取的金属与脉石级其他杂质分离的目的。
炼钢的步骤可以概述为:首先选矿,然后将铁矿石烧结成适合高炉冶炼的烧结矿,将优质的烧结矿跟焦炭等加入高炉内,在高炉里还原铁矿石得到铁水,然后铁水经过预处理送到炼钢厂,铁水在炼钢厂的转炉内脱碳、磷、硫等有害元素跟杂质,然后将优质的钢水连铸,连轧得到我们需要的钢铁产品。
在这过程中,选矿跟烧结以粉尘为主要污染源;高炉炼铁以高炉煤气的气态污染物为主;连铸跟连轧以冷却水为主要污染物;同时在这过程中还有很多的矿渣、炼铁渣、炼钢渣的固体废弃物以及运输途中的烟尘污染。
这些污染物如果不加以处理而直接排放到环境中,对环境的损害是不可估计的。
同时这些污染物中也有很多有价元素以及一些可回收的资源直接排放也是一种对资源的浪费。
关键词:废气、废水、固体废弃物、回收、治理、再利用废气处理及利用钢铁工业废气主要来源于:①原料、燃料的运输、装卸及加工等过程产生大量的含尘废气;②钢铁厂的各种窑炉再生产的过程中将产生大量的含尘及有害汽体的废气;③生产工艺过程化学反应排放的废气,如冶炼、烧焦、化工产品和钢材酸洗过程中产生的废气。
炼钢除尘灰的处理方法

炼钢除尘灰的处理方法
钢铁生产中,炼钢除尘灰是一种普遍存在的废料,主要由氧化铁、氧化钙、氧化镁、氧化铝等物质组成,含有高度的活性和毒性。
炼钢除尘灰的处理是一个极其重要的环节,合理的处理能够减少对环境的污染并且使其得到有效的利用。
首先,炼钢除尘灰可以直接用来制作水泥和混凝土,这主要是因为除尘灰的成分中含有大量的硅酸盐、铝酸盐、氧化钙等成分,正是这些成分为制造水泥和混凝土提供了重要的原料。
此外,炼钢除尘灰还可以用于剃刀刃磨料、磨料、钼、锆等金属的提取等方面。
其次,炼钢除尘灰可以经过热处理后再利用。
热处理后的除尘灰含有更高活性的氧化钙,并且热处理可以促进除尘灰的水化反应,提高水泥和混凝土的强度。
另外,除尘灰处理后的热稳定性和耐火性能也有所增加,可以用于制作耐火料、隔热材料和高温隔热材料等。
最后,炼钢除尘灰还可以用作施肥剂。
除尘灰中的钙、镁等元素对提高土壤的肥力很有帮助,可以与有机肥料混合施用于农田中,提高农田土壤的肥力,增加土地的产量。
总之,炼钢除尘灰的处理方法多样,可以循环利用,有效减少对环境的污染。
在处理炼钢除尘灰时,应根据其成分特点,结合具体情况采取相应的处理方式,实现资源的合理利用和环境的友好保护。
钢厂除尘灰环保处理方案

钢厂除尘灰环保处理方案全文共四篇示例,供读者参考第一篇示例:钢厂是重要的工业生产基地之一,但在生产过程中会产生大量的粉尘和灰尘污染。
这些粉尘和灰尘不仅污染了环境,还对周边居民的健康造成了威胁。
钢厂除尘灰环保处理方案变得尤为重要。
钢厂除尘灰主要来源于炼钢过程中的烟尘以及炉灰、废渣等固体废物。
这些废物中含有大量的有害物质,如重金属、硫化物、氮化物等,对环境和人体健康造成极大危害。
对钢厂除尘灰进行有效的处理和处理成为了当务之急。
钢厂除尘灰环保处理方案主要包括以下几个方面:1. 建立完善的除尘设备。
钢厂可以通过安装先进的除尘设备,如电除尘器、脉冲布袋除尘器等,有效地捕集和净化排放的烟尘和灰尘。
这样不仅可以降低环境污染,还可以减少废物的产生量。
2. 采用有效的干湿处理工艺。
钢厂可以通过干法或湿法处理除尘灰,将废物中的有害物质有效地去除或固化。
干法处理主要通过热解、焙烧等方式将固体废物处理成无害的物质,湿法处理则是通过溶解、过滤等方式将固体废物转化为可回收的资源或安全的处理物。
3. 推广资源化利用技术。
钢厂可以通过技术创新和设备更新,将除尘灰转化为有用的资源。
可以将除尘灰作为砖料原料,通过砖料化处理技术生产砖瓦等建筑材料;也可以将除尘灰作为填料加入混凝土中,提高混凝土的强度和耐久性。
4. 加强监管和管理。
钢厂需要建立完善的环保管理机制,加强对除尘灰处理过程的监督和检查,确保按照相关法律法规和标准进行处理。
要积极推动企业技术创新,不断完善环保设施和工艺,减少环境污染和资源浪费。
第二篇示例:钢厂是一个重要的工业生产单位,但在生产过程中会产生大量的除尘灰,如果不进行处理,会给环境造成严重的污染。
钢厂除尘灰的环保处理方案显得尤为重要。
在这篇文章中,我们将分享一些钢厂除尘灰环保处理方案。
一、污染源分析钢厂是一个产生大量工业废气和废渣的行业,其中除尘灰就是重要的污染源之一。
在钢厂的炼铁、炼钢和轧钢等工艺过程中,炉烟中含有大量尘粒和有害物质,这些尘粒和有害物质在高温状态下很容易聚集成颗粒状的除尘灰。
钢铁工业烟尘减排与回收利用技术指南
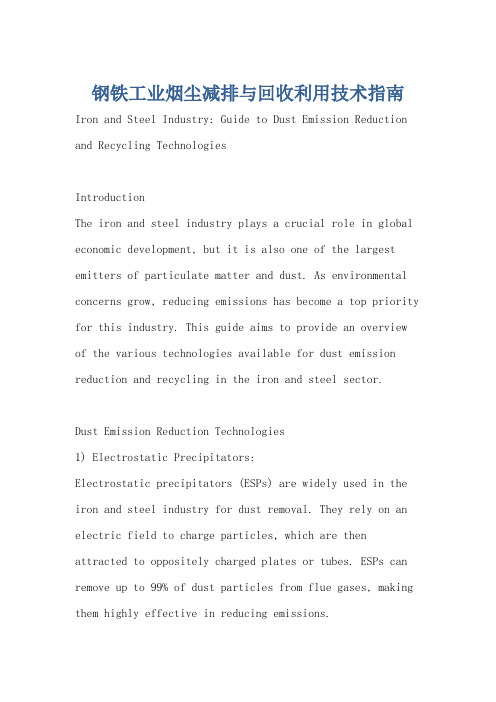
钢铁工业烟尘减排与回收利用技术指南Iron and Steel Industry: Guide to Dust Emission Reduction and Recycling TechnologiesIntroductionThe iron and steel industry plays a crucial role in global economic development, but it is also one of the largest emitters of particulate matter and dust. As environmental concerns grow, reducing emissions has become a top priority for this industry. This guide aims to provide an overview of the various technologies available for dust emission reduction and recycling in the iron and steel sector.Dust Emission Reduction Technologies1) Electrostatic Precipitators:Electrostatic precipitators (ESPs) are widely used in the iron and steel industry for dust removal. They rely on an electric field to charge particles, which are thenattracted to oppositely charged plates or tubes. ESPs can remove up to 99% of dust particles from flue gases, making them highly effective in reducing emissions.2) Bag Filters:Bag filters use fabric bags to capture dust particles from flue gases. These bags act as filters, allowing clean air to pass through while trapping particles inside. Bagfilters have a high collection efficiency and are commonly used in combination with other technologies like ESPs for further emission reduction.3) Wet Scrubbers:Wet scrubbers are another popular technology for controlling particulate emissions in the iron and steel industry. These scrubbers use water or other liquid solutions to capture dust particles by direct contact or absorption. Wet scrubbers can effectively remove both particulate matter and certain chemical pollutants.Dust Recycling Technologies1) Solid Waste Recovery:Solid waste generated in the iron and steel industry consists of various materials that can be recycled or reused. For example, blast furnace slag can be processedinto cement, aggregate, or mineral wool production. Similarly, baghouse dust can be transformed into raw materials for cement kilns or even recovered as valuable metals.2) Dust Briquetting:Dust briquetting is a technique that converts fine iron and steel dust into briquettes, which can be used as feedstockin electric arc furnaces or other iron-making processes. This approach not only reduces waste but also conserves energy by replacing conventional raw materials.ConclusionThe iron and steel industry must address the challenge of reducing dust emissions while remaining economically viable. By implementing effective emission reduction technologies like electrostatic precipitators, bag filters, and wet scrubbers, as well as adopting dust recycling methods such as solid waste recovery and dust briquetting, the industry can achieve significant environmental improvements. These measures will not only help reduce air pollution but also promote sustainable resource utilization within the sector.翻译:引言钢铁工业在全球经济发展中起着至关重要的作用,但也是颗粒物和烟尘排放量最大的行业之一。
- 1、下载文档前请自行甄别文档内容的完整性,平台不提供额外的编辑、内容补充、找答案等附加服务。
- 2、"仅部分预览"的文档,不可在线预览部分如存在完整性等问题,可反馈申请退款(可完整预览的文档不适用该条件!)。
- 3、如文档侵犯您的权益,请联系客服反馈,我们会尽快为您处理(人工客服工作时间:9:00-18:30)。
钢铁厂除尘灰及其他废弃物的再利用技术来源: 中国环保信息网切记!信息来至互联网,仅供参考2010-04-15 访问:274次随着环境立法的要求越来越严,对钢铁企业环境适应性的要求也不断提高。
因此,一些降低能源消耗、减少废弃物排放及废弃物回收再利用的技术方法在钢厂得到大力推广。
近几年开发的一些钢厂废弃物回收、回用技术都已得到成功应用。
这些技术可以实现诸如降低废弃物排放、节约废弃物处置费用、回收利用部分含fe、zn产品的作用。
废弃物主要来源于除尘器的细粉尘和各种生产过程中产生的尘泥。
废弃物的回收利用过程中要求实现无尘处理,经常采用粘结成形、造球、压块、制砖等工艺方法。
上述工艺处理方法的一个共同生产工序是废弃物的混合即混料过程。
混料系统必须同时能够进行混料、加湿、混匀、紧密、预成球、反应、冷却等过程。
采用逆流强力混合机可以实现上述功能。
混合原料中常含有一些难处理的回收料,如坚硬的(烧结矿、焦炭)、腐蚀性的(含氯化物材料)、易产生火花的(含fe粉材料)、易发生反应的(生石灰)或粘性大、易结成团的回收料。
1、除尘灰造球近年来,锌的回收在钢厂越来越重要。
随着表面热浸镀钢材使用量的增多,回收到钢厂重熔的锌量也大量增加。
含锌废弃物的处理有两种方法:一种是仅对外观进行处理;另一种是将回收的锌加工成氧化物。
在奥地利林茨奥钢联钢厂,从转炉出来的含尘废气经冷却器和下步的电除尘进行除尘。
从冷却器出来的粗粉尘以及从电除尘出来的低锌细粉尘在回转窑中进行加热,并在一条连续生产线上压制成团块,压制团块再直接返回到转炉中进行再利用。
从电除尘出来的富含锌的粉尘则被送到另一条生产线——造球系统。
由于这种粉尘铁含量及生石灰含量高,且工作温度达到150℃时,易产生火花,因此,为防止铁发生反应,系统采用氮气进行保护。
为了消除熟石灰的反应焓及其他热源,混合机同时也作为蒸汽冷却器使用。
在混合机和圆盘造球机之间安装有改进的圆盘给料机作为反应器。
由于混合机是批量间歇式非连续生产,而造球机是连续生产,圆盘给料机即可以作为间歇式生产和连续生产之间的缓冲装置,也可为熟石灰的完全反应提供充足的时间。
虽然粉尘很难溶于水,但混合过程却需要大量的水。
加水量由工艺控制系统根据检测数据自动计算出来,基本由以下几部分组成:cao熟化用水量(化学计量)、消耗反应热用水、热粉尘冷却用水、消耗高温混合机机械能用水、粉尘造球需要加湿的用水。
水的蒸发作用使混合机、反应器、造球机内产生大量的含尘蒸汽,这些蒸汽在净化器中被净化后循环使用,从净化器出来的污水又被送入混合机中使用,这些水在完全封闭的系统内循环,不会向外部排放,而且整个工艺所用的水都是加入到净化器中的新水。
由于含石灰的粉尘加湿后很粘,混合机上一般配有自动清除装置。
从造球机出来的湿球在带式干燥机上进行干燥,以利于储存。
造好的球机械强度高,在潮湿的环境中也能保持良好的稳定性,且适于长距离运输。
2、waelz回转窑工艺1992年bus公司在德国弗莱堡市saxonia工业区原钢铁厂的厂址上建起了一座现代化的生态环保型锌回收工厂。
该厂用回转窑将含锌的工业废弃物转换成生态环保和环境友好的氧化物。
在锌车间再将氧化物转换成锌。
waelz回转窑工艺可处理的原料有炼钢车间除尘灰、污泥、废球团,湿焦炭,干焦炭(石油焦、无烟煤焦),烟气脱硫石膏(湿的),碾碎的干石膏、生石灰、熟石灰等。
炼钢车间的粉尘通常采用专用料罐车进行运输,然后储存在大容积的料仓中。
为提高原料性能,1997年又安装了一套混合造球系统,使炉子产量提高约20%。
根据废弃物含锌量的不同选用不同的还原剂或粘结剂,然后进行混合、均匀、加湿。
该造球系统主要设备是批量间歇式生产的强力混合机及连续生产的圆筒造球机。
1号waelz回转窑轻微倾斜,长43m,直径3.6m,每分钟约旋转一次。
加热气体与混合料(球团)运行方向相反,混合料缓慢通过炉子的同时被加热、烘干。
金属氧化物在1200℃的反应区被还原,在此温度锌和镉被蒸发。
工艺通风会使金属重新氧化,它们和废气一起进入气体洗涤系统,在扁管冷却器和过滤器处分离出金属氧化物,并输送到料仓进行中间储存。
从waelz回转窑出来的炉渣可以用来填埋或修路。
waelz窑炉工艺专利(sdhl)利用了回转窑内铁氧化物的反应热,极大地降低了能源(气体和焦炭)消耗,氧化物产量也提高近30%,这一工艺不产生废水,与没用铁氧化物反应热的普通工艺相比,co2排放量减少40%。
第一座炉子生产很成功,于是在2002年又投建了2号长50m的waelz回转窑。
这次生产采用烧结工艺,产量明显提高,因而没有再安装造球圆筒。
该生产线可以实现连续生产。
混合烧结工艺采用了爱立许(eirch)改进型强力混合机。
混料塔设计采取提高产量的设计结构,可以为产量提高后的回转窑提供足够的原料,因此,2004年安装了爱立许混合系统,将粉尘和污泥用焦炭、粘结剂进行混合粘结成团块。
与高校及研究所的合作研究证明,含铁废弃物可以通过带式烧结机进行回收。
这可以降低废弃物处置成本、回收循环使用材料中的铁,但是会使烧结料的渗透性变差,烧结机排放气体中的含尘量提高。
为避免上述情况发生,进行了粉尘烧结的试验研究。
1997年hkm(蒂森克虏伯曼内斯曼)公司建设了回收粉尘的烧结中试生产线,试验结果非常满意,因此试验持续了很多年,直到2001年才转成工业化生产。
利用不同类型的混合机进行大量试验,研究了粉尘粘结团块的性能以及炼钢车间大型生产不同系统的适应性,对比了爱立许逆流强力混合机和带有头部切割机的单轴管式混合机,实践证明爱立许混合机使用性能表现良好。
2002年hkm公司新生产线投入使用,可处理的原料包括高炉炉顶煤气粉尘(细而湿)、除尘室粉尘(粗大而坚硬)、烧结厂冷却过程粉尘(破碎、筛分过程)、铸造车间粉尘(干而细)、粘结剂(石灰、水泥等)、水。
这些材料自动进行储存、运输、配料、称重、送入配料混合机。
将混合机混合好的粘结团块倒进箱式喂料器,然后再连续加到烧结机台车上。
经过较长一段时间的生产,回收系统的设备配件及粘结系统得到优化,生产结果更加可控。
粉尘团块提高了烧结混合料的透气性,使烧结产量得以提高,降低了烧结系统排放气体中的粉尘含量。
除尘室中的含铜微粒加入到粉尘团块中,降低了废气中的铜含量及其对形成二恶英的催化作用。
3、primus 工艺在primus 工艺中试生产成功后,首座工业化生产线于2003年建成投产。
primus 工艺的主要设备是多膛炉及电炉,电炉将预还原铁转变成生铁。
另外该厂还装有废气检测装置以保证其最小排放量。
primus 工艺利用铁矿粉生产海绵铁(dri)和铁水,是一种生态环保型新工艺,也可把它看成微型高炉。
再利用钢铁生产中废弃物的目的是重新获得铁、锌及其他有价金属。
新工艺采用多膛炉技术进行直接还原,适合采用低级煤。
该工厂设计回收卢森堡钢铁公司的所有废弃物,包括电炉粉尘和轧钢车间的含油尘泥,高炉及其他炼钢车间的粉尘及尘泥也能处理。
在混合机内,不同的废弃物和粘结剂分别进行混合、称重和处理。
根据测量混合机内已混匀原料的湿度,在混合过程中可直接对基料进行不同含水量的补偿。
混合的下道工序是造球,混合料在造球圆筒中造球,时间较长,然后进行烘干。
多膛炉是一套工艺简单、流程短、生产可靠的设备,由几个炉床竖着一个摞在另一个的上面排列组成。
在每一层都有混料臂在工作,混料臂由一个冷却的旋转柱状轴带动。
原料和煤一起被装进去,煤从炉子的顶部流到底部。
混料臂驱使它们运动,在一层由外向里运动,在其下一层又从中心向外运动,空气从炉子的侧面进去然后从顶部出来。
废弃物在炉内被烘干、还原,整个过程要经过以下几个步骤:先在100℃左右被烘干,在400℃左右除油,在1100℃左右被还原。
在料床上还原气氛占主流,气流是氧化性的。
这会使锌在气流中被重新氧化,而在废气清洁器中被分离出来,所以又叫做primus氧化。
从炉底出炉的海绵铁被连续装入primus熔化炉——特制的三段式电弧炉,连续生产出铁水和渣,这种渣与高炉渣相比,不易发生反应,可用于铺路。
4、oxycup工艺2004年夏天,蒂森克虏伯钢铁公司(tks)在德国杜伊斯堡建设的oxycup工艺生产线投入使用。
tks拥有三个烧结厂,四座高炉和两个炼钢厂。
利用这项技术该厂可以回收利用所有这些厂的废弃物,并使含铁产品得到回收。
整个工程由德国某公司负责设计施工,并提供核心设备——竖炉。
在tks决定建设新工厂之前,已经与一些公司合作,利用改进的冲天炉成功进行了多年的中试试验。
这一工艺是将含铁和碳的废弃物制成砖块,这些砖块在炉内被还原成dri然后再被熔化成生铁。
该工艺也可以处理不能在普通生产线上回收的含锌粉尘。
能处理的原料包括烧结机粉尘、高炉污泥、转炉粉尘、轧机污泥、焦炭渣。
这些废弃物经准备车间冷却、输送、分类后,送入特定的强力混合机内进行混合,并加入粘结剂混合成混凝土的样子,然后被送到110mm六边形的型砖生产线上,生产出铺路石用砖。
含铁50%的原料制成的砖经过大约三天硬化后,可以直接进行熔化,也可以储存以后再用。
对于废弃物的统一处置和所制砖块的稳定性来说,原料准备中的混合工序最重要。
不同种类的污泥需要进行分解破碎后与细粉尘均匀混合,经过大范围的多次系列试验后,tks公司决定采用爱立许逆流强力混合机,该混合机不仅可以破碎污泥,还可以准确控制粘结剂和水分的分布范围和量。
这两个性能是制砖过程中的先决条件,可以保证在制砖的压制过程中优化喂料,并使制成的砖具有合适的硬度。
由于回收废弃物颗粒细小、反应面积大、温度高,炉子内的反应速度非常快。
由于所有的砖块都是一种尺寸,竖炉内比高炉内有很多有利的空洞。
当砖块下行时被还原成dri,然后进入熔化区,铁渣分离连续流出。
废弃物中的锌被蒸发与废气一起从炉顶出来,在过滤器处收集起的富锌泥渣可以再回收锌。
oxycup工艺的通用性、适应性强,可处理的废弃物原料范围广泛,它的原料准备车间能根据制砖生产线的设计和布置灵活提供原料,还可以进行连续处理。
5、结论通过对欧洲一些钢铁厂废弃物回收利用生产线的介绍发现,他们不是将废物堆积而是将其回收利用。
烧结厂、高炉、铸造车间、炼钢厂和电弧炉的粉尘和污泥,加上粘结剂(有时还有还原剂),通过处理,其中的有用物质可以在高温下重新回收。
这些废弃物中的大多数难以处理,具有很高的机械、化学和物理性能。
原料准备工序总是被低估,其实它在很大程度上决定着生产工艺的成功与否。
原料准备最核心的工作是原料的混合。
逆流强力混合机在所有工艺中的应用证明,它可以达到极好地混合效果,能够保证中间产品(混合料)的稳定性以及其他所需要的性能。
爱立许混合机具有耐磨、自清洁功能,适应性强,因此,可以处理与普通原料性能极为不同的各种性能的废弃物。