伴生气轻烃回收工艺技术
油田伴生气的回收工艺方案
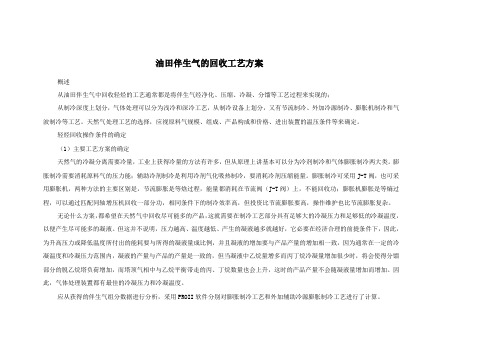
油田伴生气的回收工艺方案概述从油田伴生气中回收轻烃的工艺通常都是将伴生气经净化、压缩、冷凝、分馏等工艺过程来实现的;从制冷深度上划分,气体处理可以分为浅冷和深冷工艺,从制冷设备上划分,又有节流制冷、外加冷源制冷、膨胀机制冷和气波制冷等工艺。
天然气处理工艺的选择,应视原料气规模、组成、产品构成和价格、进出装置的温压条件等来确定。
轻烃回收操作条件的确定(1)主要工艺方案的确定天然气的冷凝分离需要冷量,工业上获得冷量的方法有许多,但从原理上讲基本可以分为冷剂制冷和气体膨胀制冷两大类。
膨胀制冷需要消耗原料气的压力能;辅助冷剂制冷是利用冷剂气化吸热制冷,要消耗冷剂压缩能量。
膨胀制冷可采用J-T阀,也可采用膨胀机,两种方法的主要区别是,节流膨胀是等焓过程,能量都消耗在节流阀(J-T阀)上,不能回收功;膨胀机膨胀是等熵过程,可以通过匹配同轴增压机回收一部分功,相同条件下的制冷效率高,但投资比节流膨胀要高,操作维护也比节流膨胀复杂。
无论什么方案,都希望在天然气中回收尽可能多的产品,这就需要在制冷工艺部分具有足够大的冷凝压力和足够低的冷凝温度,以便产生尽可能多的凝液。
但这并不说明,压力越高、温度越低、产生的凝液越多就越好,它必要在经济合理的前提条件下,因此,为升高压力或降低温度所付出的能耗要与所得的凝液量成比例,并且凝液的增加要与产品产量的增加相一致,因为通常在一定的冷凝温度和冷凝压力范围内,凝液的产量与产品的产量是一致的,但当凝液中乙烷量增多而丙丁烷冷凝量增加很少时,将会使得分馏部分的脱乙烷塔负荷增加,而塔顶气相中与乙烷平衡带走的丙、丁烷数量也会上升,这时的产品产量不会随凝液量增加而增加。
因此,气体处理装置都有最佳的冷凝压力和冷凝温度。
应从获得的伴生气组分数据进行分析,采用PROII软件分别对膨胀制冷工艺和外加辅助冷源膨胀制冷工艺进行了计算。
对于较富的伴生气而言,单纯采用膨胀制冷工艺,采取提高天然气压力,利用膨胀机膨胀制冷、分离。
小气量低压气轻烃回收工艺方案

低压伴生气轻烃回收工艺方案在油田开发过程中, 油田伴生气和油罐挥发气都是关键资源, 因气量小, 地点分散, 气体集输困难, 没有得到合理利用。
小流量、低压伴生气中回收轻烃,对于降低油气损耗, 取得较高经济效益和良好社会效益, 都含相关键现实意义。
从轻烃回收工艺来看, 关键有油吸收法、低温分离法、压缩法、吸附法、复合回收法等。
在气量较大, 含烃量高时低温分离法与其它轻烃回收方法相比, 含有投资少、操作费用低、效率高等优点。
现在广泛采取回收方法是低温分离法或低温分离法与其它方法组合——复合回收法。
天然气(含伴生气) 经过以上某一个或多个方法, 把其中丙烷以上重组分从气体中分离出来而得到混合液烃。
对于少许低压气回收, 我企业依据多年实践, 采取我企业专利技术, 提出了合理工艺回收方案。
1 基础数据气体处理量:原料气压力:气体温度:原料气组成:工艺要求技术指标: 从原油伴生气回收混合轻烃。
产品收率≥90%2 轻烃回收方案因为原料气气压低, 无压力能可利用, 所以, 对原料气实施增压。
对于小流量、低压气轻烃回收工艺技术路线可概括为:原料气增压→脱水→节流, 膨胀, 冷凝→产品(混烃, 干气)。
实践证实混烃液化率伴随压力升高、温度降低而增加。
一样若压力太低, 要想使丙烷达成较高液化率, 需要很低冷凝温度(- 50℃以下) ,将使步骤复杂化, 增加投资。
对于小流量、低压气轻烃回收路径, 通常单纯采取节流膨胀制冷法, 液烃回收率很低, 达不到工艺要求。
我企业消化吸收中国外优异技术和设备, 推出涡流管节流膨胀制冷工艺, 使得工艺简化, 投资节省, 混烃回收率高。
产品收率≥90%。
3 轻烃回收工艺标准步骤经过工艺方案和操作参数优选后, 确定轻烃回收工艺标准步骤图: 原料气经二级压缩(25-30MPa)→脱水→涡流管膨胀制冷→节流膨胀制冷(0℃)→混烃分离,该工艺步骤含有以下特点:(1) 采取涡流管膨胀制冷+ 节流膨胀复合制冷方案, 提升了轻烃回收率。
油田伴生气回收工艺技术

和湿法脱硫。采用固体吸附剂或吸收剂来脱除硫化氢或有机硫的
• 再生温度:120℃
伴生气综合利用项目部
轻烃及回收工艺技术
制冷系统及其作用 在轻烃回收的冷凝分离法中,获得需
要的低温是关键。因此采用适宜的制冷方
法,为工艺装置提供必需的冷量是油气田 轻烃回收技术的一个重要方面。工业上制
冷方法一般分为相变制冷和气体膨胀制冷
两类。
图3-1 压缩蒸汽冷 冻机
伴生气综合利用项目部
接触,从而吸收脱除气体中的水蒸气。
固体吸附有分子筛脱水工艺,吸收法有乙二醇脱水工艺。
伴生气综合利用项目部
轻烃及回收工艺技术
分子筛脱水工艺 分子筛(又称合成沸石)是一种硅铝酸盐多微孔晶体,它是 由SiO2和Al2O3四面体组成的框架结构。 分子筛脱水是利用干燥剂表面张力使气体的水分子被干燥剂 内孔吸附而从天然气中除去的方法。
轻烃及回收工艺技术
冷凝分离流程图
轻烃及回收工艺技术
轻烃回收技术的发展
国内外近 20 多年已建成的轻烃回收装置大多采用低温分离法,
该方法的发展推动和促进了轻烃回收工艺的进步。但总体来说能耗高、 收率低仍然是制约轻烃回收工艺发展的重要因素。近年来对轻烃回收
工艺的研究也主要是围绕这两方面开展,同时开发利用了一些新技术
伴生气综合利用项目部
轻烃及回收工艺技术
涡流管技术--工作原理
常温状态的气体进入喷嘴膨胀以后以很高的速度切线方向进入涡 旋室,形成自由涡流,经过动能的交换并分离成温度不相同的两部分, 中心部分的气流动能降低经孔板流出,即冷气流;边缘部分的气流动 能增大成为热气流从另一端经控制阀流出,冷气流的温度可达(- 50~-10)℃,热气流的温度可达(100~130)℃。
伴生气轻烃回收液化气工艺设计

伴生气轻烃回收液化气工艺设计引言伴生气轻烃回收液化气工艺设计是一种对伴生气中的轻烃进行回收利用的技术。
伴生气是指在石油、化工等生产过程中产生的含有各种轻烃物质的气体。
传统上,伴生气中的轻烃往往被视为废气,大量的轻烃被直接排放到大气中,不仅造成了能源的浪费,还对环境造成了污染。
通过伴生气轻烃回收液化气工艺设计,可以将这些轻烃回收利用,并转化为液化气,实现能源的有效利用和环境的净化。
工艺步骤伴生气轻烃回收液化气工艺设计包括以下几个步骤:1. 原料准备在进行伴生气轻烃回收液化气工艺设计之前,需要先准备好所需的原料。
原料主要包括伴生气和液化气。
伴生气是从生产过程中获取的含有轻烃物质的气体,而液化气则可以通过石油气或天然气等途径获得。
2. 气体分离在伴生气中,常见的轻烃有丙烷、丁烷等。
在进行气体分离时,可以利用不同轻烃的沸点差异实现。
一种常见的气体分离方法是通过冷却和压缩来将伴生气中的轻烃物质分离出来。
这一步骤可以使用分离塔等设备来完成。
3. 液化处理在分离出轻烃物质后,需要将其进行液化处理。
液化处理是将轻烃物质转化为液体状态的过程。
这可以通过降低温度或增加压力来实现。
常见的液化处理方法包括冷凝和压缩。
4. 气体再生在液化处理后,得到的液化气可以作为能源使用。
但是,为了实现循环利用,还需要对剩余的气体进行再生。
再生是指将剩余的气体经过各种化学反应或物理处理后,使其重新变为伴生气中的轻烃物质。
这一步骤可以采用吸附、脱附等方法。
5. 产品分离在再生后,可以得到纯度较高的轻烃物质。
这些物质可以经过进一步处理和分离,得到所需的液化气产品。
这一步骤可以使用分离设备来实现。
设计要点在进行伴生气轻烃回收液化气工艺设计时,需要考虑以下几个要点:1. 能源消耗在工艺设计中,需要考虑能源的消耗情况。
为了减少能源的浪费,可以通过优化设备结构、改进工艺流程等方式来实现。
2. 环境影响伴生气轻烃回收液化气工艺设计涉及到大量的气体处理和转化过程。
油田伴生气轻烃回收浅冷工艺的对比研究

6CHEMICAL ENGINEERING DESIGN化工设计2020,30(2)油田伴生气轻7回收浅冷工艺的对比研究武娜#薛慧北京石油化工工程有限公司西安分公司西安710075扌商要为降低油气损失、提高油气田收益、提高产品在储存和运输过程中的安全性,对轻7回收工艺进行对比研究。
本文以油田伴生气小规模处理气量为研究基础,采用模拟软件进行计算并结合经济性分析研究两种常用的改进浅冷轻7回收工艺流程。
关键词油田伴生气轻7回收浅冷工艺经济性分析轻7回收的方法一般有三种:吸附法、油吸收法和低温分离法,前两种方法具有局限性[I]O 其中,吸附法因吸附剂吸附容量及运行成本较高等问题未得到很好的解决,一直尚未在世界范围内得到广泛使用[2],一般只适用于小气量且重7含量不高的天然气;而油吸收法虽然可以明显提升轻7组分的回收率,但是存在工艺复杂、经济成本偏高的问题;低温分离回收工艺应用较为广泛和成熟,但是存在能耗较大、效益不理想的问题,所以轻7回收技术也在不断地发展和创新,人们的关注度也在不断提高。
低温分离法根据冷凝温度的不同,分为浅冷、中冷和深冷工艺。
浅冷工艺常用氨或丙烷制冷,C3收率一般仅为50%-65%中冷或深冷工艺需要混合冷剂、透平膨胀制冷或冷剂和膨胀机联合制冷来实现,通常用在回收乙烷或丙烷收率要求高的工况。
油气田井场布置分散且地处偏远,油田伴生气气量、气大、分、用、经济利用价值低的特点,大多被直接排放或燃烧,这既浪费宝贵资源,又污染环境,因地制宜地建立小型撬装轻7回收站,合理地开发利用这部分天然气资源,可以变资源为产能。
处理合格的天然气可站内发电自用或压缩成CNG外输、回收的液体作为混7或液化石油气和轻油外运,极大增强了油气田零散井口气资源的经济效益和环保效益。
在工艺方案确定前,要结合气质组分、市场情况、现场情况以及投资等给出合适的工艺路线及选择建议。
经过对延长油田三大油区的各增压站和联合站调研发现,各站的伴生气产量多数小于10N104 Nm3/d o对于气量小于1.0x104Nm3/d的伴生气,一般作为站内自用气(自发电或作为燃料气);气量在1.0x104-10.0x104Nm3/d采用小型撬装轻7回收装置。
某油田伴生气轻烃回收工艺流程优化的探讨
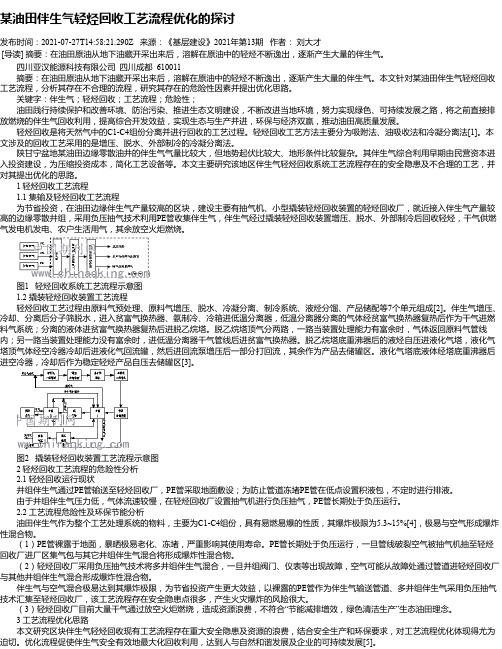
某油田伴生气轻烃回收工艺流程优化的探讨发布时间:2021-07-27T14:58:21.290Z 来源:《基层建设》2021年第13期作者:刘大才[导读] 摘要:在油田原油从地下油藏开采出来后,溶解在原油中的轻烃不断逸出,逐渐产生大量的伴生气。
四川亚汉能源科技有限公司四川成都 610011摘要:在油田原油从地下油藏开采出来后,溶解在原油中的轻烃不断逸出,逐渐产生大量的伴生气。
本文针对某油田伴生气轻烃回收工艺流程,分析其存在不合理的流程,研究其存在的危险性因素并提出优化思路。
关键字:伴生气;轻烃回收;工艺流程;危险性;油田践行持续保护和改善环境、防治污染、推进生态文明建设,不断改进当地环境,努力实现绿色、可持续发展之路,将之前直接排放燃烧的伴生气回收利用,提高综合开发效益,实现生态与生产并进,环保与经济双赢,推动油田高质量发展。
轻烃回收是将天然气中的C1-C4组份分离并进行回收的工艺过程。
轻烃回收工艺方法主要分为吸附法、油吸收法和冷凝分离法[1]。
本文涉及的回收工艺采用的是增压、脱水、外部制冷的冷凝分离法。
陕甘宁盆地某油田边缘零散油井的伴生气气量比较大,但地势起伏比较大、地形条件比较复杂。
其伴生气综合利用早期由民营资本进入投资建设,为压缩投资成本,简化工艺设备等。
本文主要研究该地区伴生气轻烃回收系统工艺流程存在的安全隐患及不合理的工艺,并对其提出优化的思路。
1 轻烃回收工艺流程1.1 集输及轻烃回收工艺流程为节省投资,在油田边缘伴生气产量较高的区块,建设主要有抽气机、小型撬装轻烃回收装置的轻烃回收厂,就近接入伴生气产量较高的边缘零散井组,采用负压抽气技术利用PE管收集伴生气,伴生气经过撬装轻烃回收装置增压、脱水、外部制冷后回收轻烃,干气供燃气发电机发电、农户生活用气,其余放空火炬燃烧。
图1 轻烃回收系统工艺流程示意图1.2 撬装轻烃回收装置工艺流程轻烃回收工艺过程由原料气预处理、原料气增压、脱水、冷凝分离、制冷系统、液烃分馏、产品储配等7个单元组成[2]。
伴生气轻烃回收的工艺分析
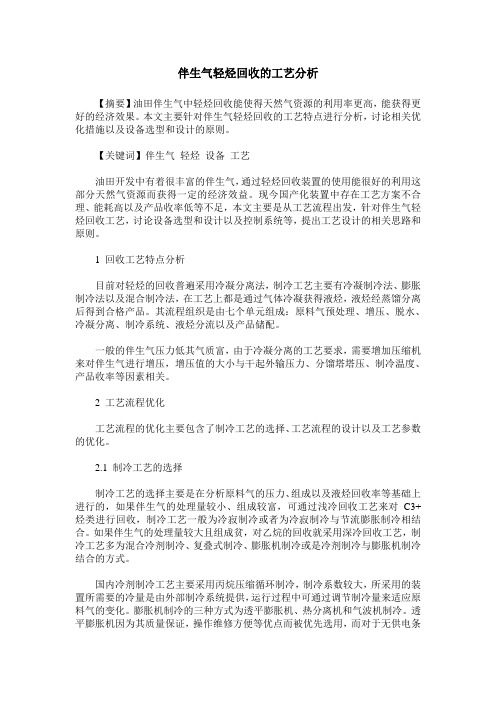
伴生气轻烃回收的工艺分析【摘要】油田伴生气中轻烃回收能使得天然气资源的利用率更高,能获得更好的经济效果。
本文主要针对伴生气轻烃回收的工艺特点进行分析,讨论相关优化措施以及设备选型和设计的原则。
【关键词】伴生气轻烃设备工艺油田开发中有着很丰富的伴生气,通过轻烃回收装置的使用能很好的利用这部分天然气资源而获得一定的经济效益。
现今国产化装置中存在工艺方案不合理、能耗高以及产品收率低等不足,本文主要是从工艺流程出发,针对伴生气轻烃回收工艺,讨论设备选型和设计以及控制系统等,提出工艺设计的相关思路和原则。
1 回收工艺特点分析目前对轻烃的回收普遍采用冷凝分离法,制冷工艺主要有冷凝制冷法、膨胀制冷法以及混合制冷法,在工艺上都是通过气体冷凝获得液烃,液烃经蒸馏分离后得到合格产品。
其流程组织是由七个单元组成:原料气预处理、增压、脱水、冷凝分离、制冷系统、液烃分流以及产品储配。
一般的伴生气压力低其气质富,由于冷凝分离的工艺要求,需要增加压缩机来对伴生气进行增压,增压值的大小与干起外输压力、分馏塔塔压、制冷温度、产品收率等因素相关。
2 工艺流程优化工艺流程的优化主要包含了制冷工艺的选择、工艺流程的设计以及工艺参数的优化。
2.1 制冷工艺的选择制冷工艺的选择主要是在分析原料气的压力、组成以及液烃回收率等基础上进行的,如果伴生气的处理量较小、组成较富,可通过浅冷回收工艺来对C3+烃类进行回收,制冷工艺一般为冷寂制冷或者为冷寂制冷与节流膨胀制冷相结合。
如果伴生气的处理量较大且组成贫,对乙烷的回收就采用深冷回收工艺,制冷工艺多为混合冷剂制冷、复叠式制冷、膨胀机制冷或是冷剂制冷与膨胀机制冷结合的方式。
国内冷剂制冷工艺主要采用丙烷压缩循环制冷,制冷系数较大,所采用的装置所需要的冷量是由外部制冷系统提供,运行过程中可通过调节制冷量来适应原料气的变化。
膨胀机制冷的三种方式为透平膨胀机、热分离机和气波机制冷。
透平膨胀机因为其质量保证,操作维修方便等优点而被优先选用,而对于无供电条件的地区则有限采用热分离机或气波机制冷。
石油伴生气回收与利用操作技术与设备
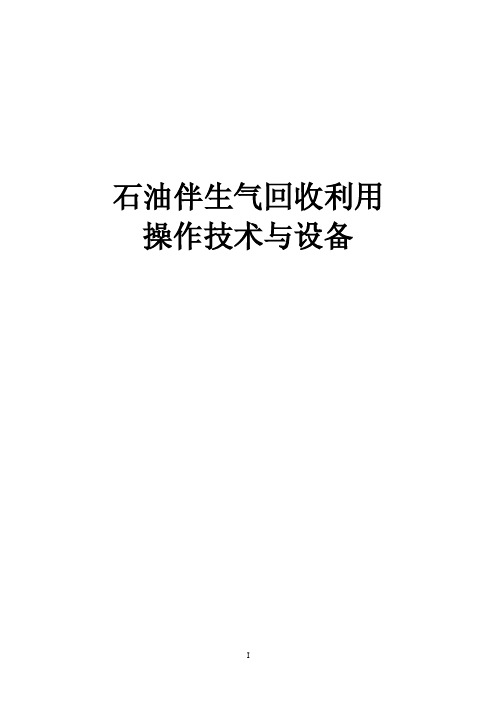
石油伴生气回收利用操作技术与设备目录绪论 (1)0.1轻烃回收及产品 (1)0.1.1轻烃生产工艺原理 (1)0.1.2产品及质量标准 (2)0.2轻烃回收产品的用途 (3)1 原油稳定系统 (4)1.1原油稳定系统的作用 (4)1.2原油稳定系统的原理及方法 (5)1.2.1 原油稳定的原理 (5)1.2.2原油稳定的方法 (5)1.3原油稳定系统的工艺流程 (6)1.4原油稳定系统的主要设备 (7)1.4.1原油稳定塔简介 (7)1.4.2加热炉系统 (7)2 压缩系统 (8)2.1概述 (8)2.1.1 气体压缩的作用 (8)2.1.2压送机械的分类 (8)2.2往复式压缩机 (9)2.2.1压缩机的基本结构 (10)2.2.2往复式压缩机的工作原理 (10)2.2.3 往复式压缩机压缩气体的三个过程 (12)2.2.4 压缩机的生产能力及影响因素 (13)2.2.5 多级压缩 (15)2.2.6 往复式压缩机的分类及型号 (16)3 冷冻系统 (18)3.1冷冻系统的目的及作用 (18)3.2压缩蒸汽冷冻机 (18)3.2.1 压缩蒸汽冷冻机的工作过程 (18)3.2.2 压缩蒸汽冷冻系统的主要设备 (19)3.2.3多级压缩蒸汽冷冻机 (21)3.3冷冻剂的选择 (24)3.3.1冷冻剂 (24)3.3.2载冷体 (25)4 脱水系统 (26)4.1脱水的原因 (26)4.2脱水的方法 (26)4.2.1吸附脱水的定义 (27)4.2.2物理吸附和化学吸附 (27)4.2.3吸附过程 (28)4.2.4脱水吸附剂的选择 (28)4.3分子筛脱水 (30)4.3.1分子筛特性 (30)4.3.2分子筛作为干燥剂的优点 (31)4.3.3使用分子筛时应注意的问题 (32)4.3.4分子筛的再生 (32)5 脱硫系统 (33)5.1概述 (33)5.1.1天然气中的酸性组分 (33)5.1.2酸性组分的危害 (33)5.1.3脱硫的必要性 (33)5.2脱硫的方法与分类 (33)5.2.1分子筛法脱硫 (34)5.2.2活性炭法脱硫 (34)5.2.3氧化铁法脱硫 (35)5.3湿法脱硫方法分类与选择 (35)5.3.1湿法脱硫方法分类 (35)5.3.2脱硫方法的选择 (37)5.4醇胺脱硫的化学反应 (39)5.4.1醇胺与H 2S 、CO 2的化学反应 (39)5.4.2 醇胺溶剂性质比较 (40)6 分馏系统 (42)6.1 蒸馏 (42)6.1.1蒸馏的基本概念 (42)6.1.2 理想二元溶液的汽液平衡关系 (42)6.1.3 ()T x y -图和y x -图 (43)6.2 精馏原理 (45)6.2.1简单蒸馏的原理 (46)6.2.2精馏原理 (47)6.2.3连续精馏流程 (48)6.3多组分的精馏 (49)6.3.1关键组分 (49)6.3.2物料的分配方法 (49)6.4 精馏设备 (50)6.4.1板式塔的基本结构 (50)6.4.2填料塔 (51)6.5精馏过程中几种典型的异常现象 (56)7 冷却水及污水处理系统 (57)7.1 冷却水及污水处理系统的目的及作用 (57)7.2液体输送机械 (57)7.2.1离心泵 (57)7.2.2其它类型泵 (65)7.2.3各类泵的比较 (67)7.3换热器 (68)7.3.1传热概述 (68)7.3.3换热器 (72)7.4化工生产中常用阀门 (80)7.4.1 球阀 (80)7.4.2 闸阀 (82)7.4.3旋塞阀 (83)7.4.4截止阀 (85)7.4. 5安全阀 (86)绪论由天然气中回收天然气凝液称为轻烃回收。
低温分离法在油田伴生气轻烃回收中的运用

低温分离法在油田伴生气轻烃回收中的运用在石油伴生气轻烃中因为内部各种气体沸点和冷凝点的不同,因此将原料的温度降低到一定的范围能够实现各种气体的分离,然后通过再加工形成合格有效的产品,该工艺被称为低温分离法。
下文将对于该技术在实际生产中的应用进行详细论述。
标签:低温分离;油田半生气;回收运用引言下文将详细论述某原油工厂伴生气轻烃工艺的改造案例,全面分析低温分离法在新时代背景下的实际应用需求以及应用效果,通过列举的实际案例并结合自身的经验,对未来该工艺的生产管理以及参数控制提出了一些建议,希望能够提高其他工厂的经济收益。
一、伴生气轻烃回收技术简介在传统工业生产中轻烃回收方法主要分为又吸收,吸附,低温分离等一些新型的技术工艺。
当前最为有效的方法为吸附和低温分离的回收方式,并且低温分离在很多的轻烃回收工作中应用范围最为广泛。
低温分离法作为当前回收系统中的主流生产工艺,具有投资设备经费少,运行结构简单,轻烃回收率很高的特点,但是该工艺的实施往往需要原材料降低反应温度,因此在实际生产应用的过程中往往会出现意外的事故和麻烦。
低温分离法根据制冷方式的不同可以被分为冷剂制冷,膨胀剂制冷,热分离制冷以及混合制冷等多种方式,下面将以实际的生产案例介绍低温分离法的具体应用效果[1]。
二、低温分离系统在轻烃回收工艺中的应用该生产体系于2019年下半年正式施工建立,在同年年底完成,并且投入使用和运行。
该工厂整体的占地面积为45亩,并且使用混合制冷的工作方式,在中央位置配备一套DHX的冷气伴生气处理装置,该机器装置的在工作的时候能够处理轻烃的数量为25吨。
该工程在运行过程中所使用的基本原材料全部来源于采油12厂板桥作业工作区,这些原料在一定工序的操作环境中转变为石油气以及轻烃等燃料,产生的副产品燃气同时被输送到其他的工作地点供加热使用[2]。
该工程自从投入运行以来,总共设置了6个管理岗位,以及下属的四个运行岗位,为了能够保证整个系统的连续运行,设置四班三道的工作模式。
油田伴生气的回收工艺方案
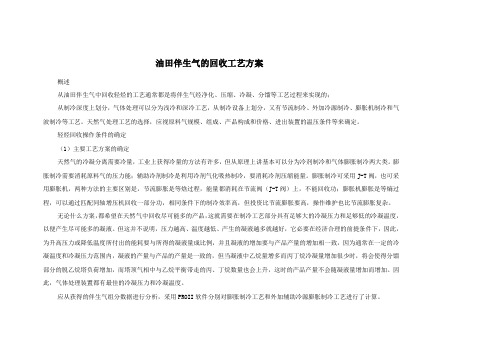
油田伴生气的回收工艺方案概述从油田伴生气中回收轻烃的工艺通常都是将伴生气经净化、压缩、冷凝、分馏等工艺过程来实现的;从制冷深度上划分,气体处理可以分为浅冷和深冷工艺,从制冷设备上划分,又有节流制冷、外加冷源制冷、膨胀机制冷和气波制冷等工艺。
天然气处理工艺的选择,应视原料气规模、组成、产品构成和价格、进出装置的温压条件等来确定。
轻烃回收操作条件的确定(1)主要工艺方案的确定天然气的冷凝分离需要冷量,工业上获得冷量的方法有许多,但从原理上讲基本可以分为冷剂制冷和气体膨胀制冷两大类。
膨胀制冷需要消耗原料气的压力能;辅助冷剂制冷是利用冷剂气化吸热制冷,要消耗冷剂压缩能量。
膨胀制冷可采用J-T阀,也可采用膨胀机,两种方法的主要区别是,节流膨胀是等焓过程,能量都消耗在节流阀(J-T阀)上,不能回收功;膨胀机膨胀是等熵过程,可以通过匹配同轴增压机回收一部分功,相同条件下的制冷效率高,但投资比节流膨胀要高,操作维护也比节流膨胀复杂。
无论什么方案,都希望在天然气中回收尽可能多的产品,这就需要在制冷工艺部分具有足够大的冷凝压力和足够低的冷凝温度,以便产生尽可能多的凝液。
但这并不说明,压力越高、温度越低、产生的凝液越多就越好,它必要在经济合理的前提条件下,因此,为升高压力或降低温度所付出的能耗要与所得的凝液量成比例,并且凝液的增加要与产品产量的增加相一致,因为通常在一定的冷凝温度和冷凝压力范围内,凝液的产量与产品的产量是一致的,但当凝液中乙烷量增多而丙丁烷冷凝量增加很少时,将会使得分馏部分的脱乙烷塔负荷增加,而塔顶气相中与乙烷平衡带走的丙、丁烷数量也会上升,这时的产品产量不会随凝液量增加而增加。
因此,气体处理装置都有最佳的冷凝压力和冷凝温度。
应从获得的伴生气组分数据进行分析,采用PROII软件分别对膨胀制冷工艺和外加辅助冷源膨胀制冷工艺进行了计算。
对于较富的伴生气而言,单纯采用膨胀制冷工艺,采取提高天然气压力,利用膨胀机膨胀制冷、分离。
油田伴生气轻烃回收综合利用技术

经过气体预处理系统后,提取 $%& 的工艺流程归结为以下 几种方 法:! 利 用 透 平 膨 胀 机 进 行 低 温 分 离;" 运 用 56789 :;6<=6> 效应进行液化 处 理,即 5 4 : 膨 胀 阀 制 冷;# 丙 烷 制 冷;$油吸收法。
(") 透平膨胀机厂。该流程多用于深冷厂( 低于 4 ,?-), 它利用透平膨胀机使气体降压制冷,将进料气中不易挥发的组 分液化。透平系 统 通 常 回 收 率 较 高, 尤 其 对 乙 烷 的 回 收 较 好。 它需要高的进口压力,多用于小的处理单元,但其费用较高, 需要低温不锈钢材料,对水的露点要求低。其典型回收率为: -* @ +,) ,-A @ B?) ,-/. !"??) 。
目前,气体处理厂多采用深冷装置,虽然相比制冷装置其 费用较高,但该装置可以回收大量 $%& 液体,并且操作简单, 便于运输,采用制冷装置对于富气是较经济的;贫油吸收装置 既昂贵,又难于操作,现在已经很少采用。
A# 轻烃回收装置的应用前景
轻烃回收装置可以组装成撬,在油田或井口附近使用,一 旦油井采集完毕,可以方便地被运输到另一个井地进行工作。 我国大多数油田都发现了伴生气资源,有些大油井已经采用了 伴生气轻烃回收技术,因地域限制一些分散的小油田每年烧掉 的伴生气约 "? 亿 <A ,这相当于一百万吨石油,随着内陆油田 的进一步开发,越来越多的伴生气被浪费掉,因此,轻烃回收 装置的开发和设计有广泛的应用前景。通过不断的努力,要力 争使我国在轻烃回收工艺上达到国际先进水平,尽快实现我国 油田产能建设和油气综合利用的新局面。
步加工,作为纯组分或天然气混合液( $%&) 或液化石油气 ( &’%) 销售。我国典型的石油伴生气中含有 $%& 的体积百分
伴生气轻烃回收工艺技术
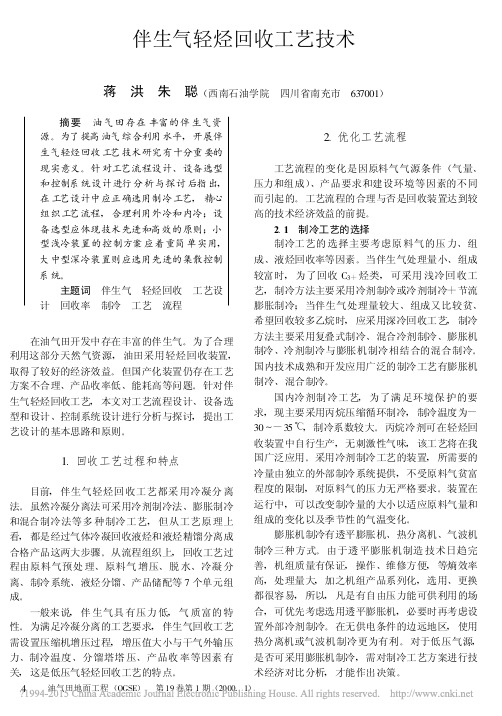
伴生气轻烃回收工艺技术蒋 洪 朱 聪(西南石油学院 四川省南充市 637001) 摘要 油气田存在丰富的伴生气资源。
为了提高油气综合利用水平,开展伴生气轻烃回收工艺技术研究有十分重要的现实意义。
针对工艺流程设计、设备选型和控制系统设计进行分析与探讨后指出,在工艺设计中应正确选用制冷工艺,精心组织工艺流程,合理利用外冷和内冷;设备选型应体现技术先进和高效的原则;小型浅冷装置的控制方案应着重简单实用,大中型深冷装置则应选用先进的集散控制系统。
主题词 伴生气 轻烃回收 工艺设 计 回收率 制冷 工艺 流程 在油气田开发中存在丰富的伴生气。
为了合理利用这部分天然气资源,油田采用轻烃回收装置,取得了较好的经济效益。
但国产化装置仍存在工艺方案不合理、产品收率低、能耗高等问题。
针对伴生气轻烃回收工艺,本文对工艺流程设计、设备选型和设计、控制系统设计进行分析与探讨,提出工艺设计的基本思路和原则。
1.回收工艺过程和特点目前,伴生气轻烃回收工艺都采用冷凝分离法。
虽然冷凝分离法可采用冷剂制冷法、膨胀制冷和混合制冷法等多种制冷工艺,但从工艺原理上看,都是经过气体冷凝回收液烃和液烃精馏分离成合格产品这两大步骤。
从流程组织上,回收工艺过程由原料气预处理、原料气增压、脱水、冷凝分离、制冷系统、液烃分馏、产品储配等7个单元组成。
一般来说,伴生气具有压力低,气质富的特性。
为满足冷凝分离的工艺要求,伴生气回收工艺需设置压缩机增压过程,增压值大小与干气外输压力、制冷温度、分馏塔塔压、产品收率等因素有关,这是低压气轻烃回收工艺的特点。
2.优化工艺流程工艺流程的变化是因原料气气源条件(气量、压力和组成)、产品要求和建设环境等因素的不同而引起的。
工艺流程的合理与否是回收装置达到较高的技术经济效益的前提。
2.1 制冷工艺的选择制冷工艺的选择主要考虑原料气的压力、组成、液烃回收率等因素。
当伴生气处理量小、组成较富时,为了回收C3+烃类,可采用浅冷回收工艺,制冷方法主要采用冷剂制冷或冷剂制冷+节流膨胀制冷;当伴生气处理量较大、组成又比较贫、希望回收较多乙烷时,应采用深冷回收工艺,制冷方法主要采用复叠式制冷、混合冷剂制冷、膨胀机制冷、冷剂制冷与膨胀机制冷相结合的混合制冷。
油田伴生气轻烃回收工艺发展及应用研究
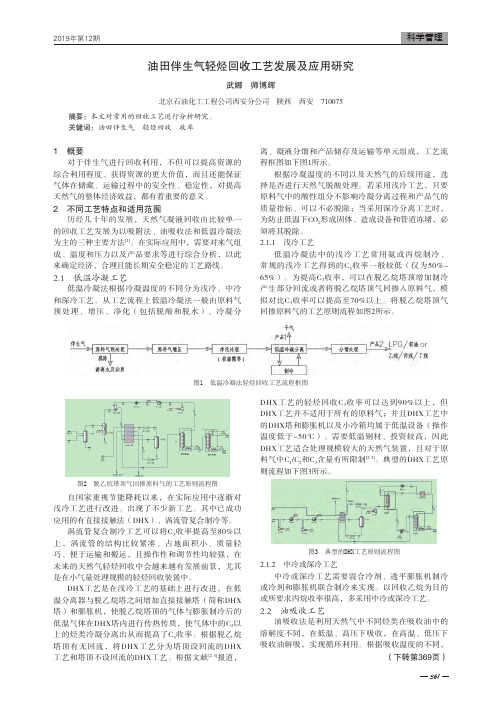
1 概要对于伴生气进行回收利用,不但可以提高资源的综合利用程度、获得资源的更大价值,而且还能保证气体在储藏、运输过程中的安全性、稳定性,对提高天然气的整体经济效益,都有着重要的意义。
2 不同工艺特点和适用范围历经几十年的发展,天然气凝液回收由比较单一的回收工艺发展为以吸附法、油吸收法和低温冷凝法为主的三种主要方法[1]。
在实际应用中,需要对来气组成、温度和压力以及产品要求等进行综合分析,以此来确定经济、合理且能长期安全稳定的工艺路线。
2.1 低温冷凝工艺低温冷凝法根据冷凝温度的不同分为浅冷、中冷和深冷工艺。
从工艺流程上低温冷凝法一般由原料气预处理、增压、净化(包括脱酸和脱水)、冷凝分离、凝液分馏和产品储存及运输等单元组成,工艺流程框图如下图1所示。
根据冷凝温度的不同以及天然气的后续用途,选择是否进行天然气脱酸处理。
若采用浅冷工艺,只要原料气中的酸性组分不影响冷凝分离过程和产品气的质量指标、可以不必脱除;当采用深冷分离工艺时,为防止低温下CO 2形成固体、造成设备和管道冻堵,必须将其脱除。
2.1.1 浅冷工艺低温冷凝法中的浅冷工艺常用氨或丙烷制冷、常规的浅冷工艺得到的C 3收率一般较低(仅为50%-65%)。
为提高C 3收率,可以在脱乙烷塔顶增加制冷产生部分回流或者将脱乙烷塔顶气回掺入原料气,模拟对比C 3收率可以提高至70%以上。
将脱乙烷塔顶气回掺原料气的工艺原则流程如图2所示。
油田伴生气轻烃回收工艺发展及应用研究武娜 师博辉北京石油化工工程公司西安分公司 陕西 西安 710075摘要:本文对常用的回收工艺进行分析研究。
关键词:油田伴生气 轻烃回收 收率图1 低温冷凝法轻烃回收工艺流程框图图2 脱乙烷塔顶气回掺原料气的工艺原则流程图自国家重视节能降耗以来,在实际应用中逐渐对浅冷工艺进行改进、出现了不少新工艺。
其中已成功应用的有直接接触法(DHX)、涡流管复合制冷等。
涡流管复合制冷工艺可以将C 3收率提高至80%以上,涡流管的结构比较紧凑、占地面积小、质量轻巧、便于运输和搬运,且操作性和调节性均较强,在未来的天然气轻烃回收中会越来越有发展前景,尤其是在小气量处理规模的轻烃回收装置中。
伴生气轻烃回收的工艺与优化措施研究
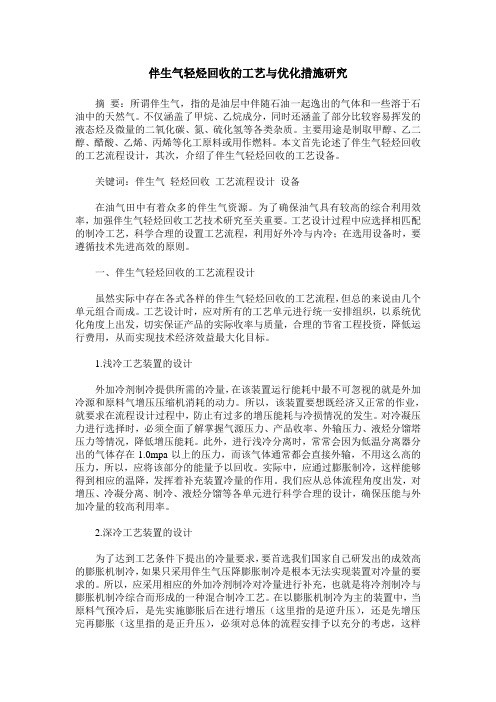
伴生气轻烃回收的工艺与优化措施研究摘要:所谓伴生气,指的是油层中伴随石油一起逸出的气体和一些溶于石油中的天然气。
不仅涵盖了甲烷、乙烷成分,同时还涵盖了部分比较容易挥发的液态烃及微量的二氧化碳、氮、硫化氢等各类杂质。
主要用途是制取甲醇、乙二醇、醋酸、乙烯、丙烯等化工原料或用作燃料。
本文首先论述了伴生气轻烃回收的工艺流程设计,其次,介绍了伴生气轻烃回收的工艺设备。
关键词:伴生气轻烃回收工艺流程设计设备在油气田中有着众多的伴生气资源。
为了确保油气具有较高的综合利用效率,加强伴生气轻烃回收工艺技术研究至关重要。
工艺设计过程中应选择相匹配的制冷工艺,科学合理的设置工艺流程,利用好外冷与内冷;在选用设备时,要遵循技术先进高效的原则。
一、伴生气轻烃回收的工艺流程设计虽然实际中存在各式各样的伴生气轻烃回收的工艺流程,但总的来说由几个单元组合而成。
工艺设计时,应对所有的工艺单元进行统一安排组织,以系统优化角度上出发,切实保证产品的实际收率与质量,合理的节省工程投资,降低运行费用,从而实现技术经济效益最大化目标。
1.浅冷工艺装置的设计外加冷剂制冷提供所需的冷量,在该装置运行能耗中最不可忽视的就是外加冷源和原料气增压压缩机消耗的动力。
所以,该装置要想既经济又正常的作业,就要求在流程设计过程中,防止有过多的增压能耗与冷损情况的发生。
对冷凝压力进行选择时,必须全面了解掌握气源压力、产品收率、外输压力、液烃分馏塔压力等情况,降低增压能耗。
此外,进行浅冷分离时,常常会因为低温分离器分出的气体存在1.0mpa以上的压力,而该气体通常都会直接外输,不用这么高的压力,所以,应将该部分的能量予以回收。
实际中,应通过膨胀制冷,这样能够得到相应的温降,发挥着补充装置冷量的作用。
我们应从总体流程角度出发,对增压、冷凝分离、制冷、液烃分馏等各单元进行科学合理的设计,确保压能与外加冷量的较高利用率。
2.深冷工艺装置的设计为了达到工艺条件下提出的冷量要求,要首选我们国家自己研发出的成效高的膨胀机制冷,如果只采用伴生气压降膨胀制冷是根本无法实现装置对冷量的要求的。
油田伴生气轻烃回收过程中低温分离法的使用
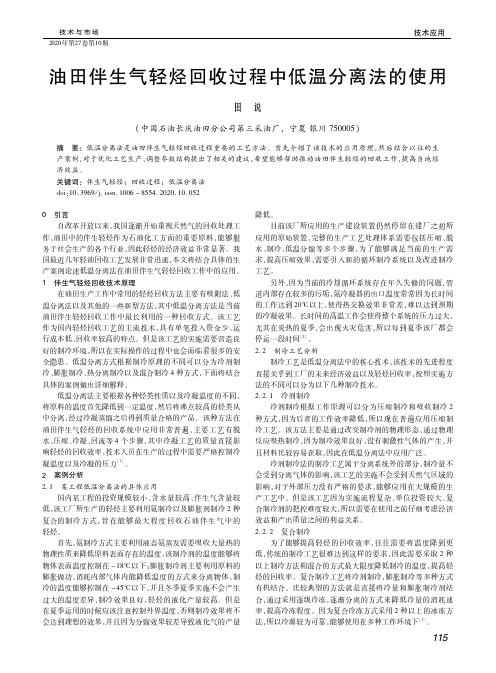
技术与市场技术应用2020年第27卷第10期油田伴生气轻烃回收过程中低温分离法的使用田 说(中国石油长庆油田分公司第三采油厂,宁夏银川750005)摘 要:低温分离法是油田伴生气轻烃回收过程重要的工艺方法。
首先介绍了该技术的应用原理,然后结合以往的生产案例,对于优化工艺生产、调整参数结构提出了相关的建议,希望能够帮助推动油田伴生轻烃的回收工作,提高当地经济效益。
关键词:伴生气轻烃;回收过程;低温分离法doi:10.3969/j.issn.1006-8554.2020.10.052 引言自改革开放以来,我国逐渐开始重视天然气的回收处理工作,油田中的伴生轻烃作为石油化工方面的重要原料,能够服务于社会生产的各个行业,因此轻烃的经济效益非常显著。
我国最近几年轻油回收工艺发展非常迅速,本文将结合具体的生产案例论述低温分离法在油田伴生气轻烃回收工作中的应用。
伴生气轻烃回收技术原理在油田生产工作中常用的轻烃回收方法主要有吸附法、低温分离法以及其他的一些新型方法,其中低温分离方法是当前油田伴生轻烃回收工作中最长利用的一种回收方式。
该工艺作为国内轻烃回收工艺的主流技术,具有单笔投入资金少、运行成本低、回收率较高的特点。
但是该工艺的实施需要营造良好的制冷环境,所以在实际操作的过程中也会面临着很多的安全隐患。
低温分离方式根据制冷原理的不同可以分为冷剂制冷、膨胀制冷、热分离制冷以及混合制冷4种方式,下面将结合具体的案例做出详细解释。
低温分离法主要根据各种烃类性质以及冷凝温度的不同,将原料的温度首先降低到一定温度,然后将沸点较高的烃类从中分离,经过冷凝蒸馏之后得到质量合格的产品。
该种方法在油田伴生气轻烃的回收系统中应用非常普遍,主要工艺有脱水、压缩、冷凝、回流等4个步骤,其中冷凝工艺的质量直接影响轻烃的回收效率,技术人员在生产的过程中需要严格控制冷凝温度以及冷凝的压力[1]。
案例分析2 1 某工程低温分离法的具体应用国内某工程的投资规模较小、含水量较高、伴生气含量较低,该工厂所生产的轻烃主要利用氨制冷以及膨胀剂制冷2种复合的制冷方式,旨在能够最大程度回收石油伴生气中的轻烃。
- 1、下载文档前请自行甄别文档内容的完整性,平台不提供额外的编辑、内容补充、找答案等附加服务。
- 2、"仅部分预览"的文档,不可在线预览部分如存在完整性等问题,可反馈申请退款(可完整预览的文档不适用该条件!)。
- 3、如文档侵犯您的权益,请联系客服反馈,我们会尽快为您处理(人工客服工作时间:9:00-18:30)。
伴生气轻烃回收工艺技术
摘要
油气田存在丰富的伴生气资源。
为了提高油气综合利用水平,开展伴
生气轻烃回收工艺技术研究有十分重要的现实意义。
针对工艺流程设计、设备选型和控制系统设计进行分析与探讨后指出,在工艺设计中应正确选用制冷工艺,精心组织工艺流程,合理利用外冷和内冷;设备选型应体现技术先进和高效的原则;小型浅冷装置的控制方案应着重简单实用,大中型深冷装置则应选用先进的集散控制系统。
主题词伴生气轻烃回收工艺设计回收率制冷工艺流程
在油气田开发中存在丰富的伴生气。
为了合理利用这部分天然气资源,油田采用轻烃回收装置,取得了较好的经济效益。
但国产化装置仍存在工艺方案不合理、产品收率低、能耗高等问题。
针对伴生气轻烃回收工艺,本文对工艺流程设计、设备选型和设计、控制系统设计进行分析与探讨,提出工艺设计的基本思路和原则。
回收工艺过程和特点
目前,伴生气轻烃回收工艺都采用冷凝分离法。
虽然冷凝分离法可采用冷剂制冷法、膨胀制冷和混合制冷法等多种制冷工艺,但从工艺原理上看,都是经过气体冷凝回收液烃和液烃精馏分离成合格产品这两大步骤。
从流程组织上,回收工艺过程由原料气预处理、原料气增压、脱水、冷凝分离、制冷系统、液烃分馏、产品储配等几个单元组成。
一般来说,伴生气具有压力低,气质富的特性。
为满足冷凝分离的工艺要求,伴生气回收工艺需设置压缩机增压过程,增压值大小与干气外输压力、制冷温度、分馏塔塔压、产品收率等因素有关,这是低压气轻烃回收工艺的特点。
优化工艺流程
工艺流程的变化是因原料气气源条件(气量、压力和组成)、产品要求和建设环境等因素的不同而引起的。
工艺流程的合理与否是回收装置达到较高的技术经济效益的前提。
制冷工艺的选择
制冷工艺的选择主要考虑原料气的压力、组成、液烃回收率等因素。
当伴生气处理量小、组成较富时,为了回收烃类,可采用浅冷回收工艺,制冷方法主要采用冷剂制冷或冷剂制冷+节流膨胀制冷;当伴生气处理量较大、组成又比较贫、
希望回收较多乙烷时,应采用深冷回收工艺,制冷方法主要采用复叠式制冷、混合冷剂制冷、膨胀机制冷、冷剂制冷与膨胀机制冷相结合的混合制冷。
国内技术成熟和开发应用广泛的制冷工艺有膨胀机制冷、混合制冷。
国内冷剂制冷工艺,为了满足环境保护的要求,现主要采用丙烷压缩循环制冷,制冷温度为-40 C,制冷系数较大。
丙烷冷剂可在轻烃回收装置中自行生产,无刺激性气味,该工艺将在我国广泛应用。
采用冷剂制冷工艺的装置,所需要的冷量由独立的外部制冷系统提供,不受原料气贫富程度的限制,对原料气的压力无严格要求。
装置在运行中,可以改变制冷量的大小以适应原料气量和组成的变化以及季节性的气温变化。
膨胀机制冷有透平膨胀机、热分离机、气波机制冷三种方式。
由于透平膨胀机制造技术日趋完善,机组质量有保证,操作、维修方便,等熵效率高,处理量大,加之机组产品系列化,选用、更换都很容易,所以,凡是有自由压力能可供利用的场合,可优先考虑选用透平膨胀机,必要时再考虑设置外部冷剂制冷。
在无供电条件的边远地区,使用热分离机或气波机制冷更为有利。
对于低压气源,是否可采用膨胀机制冷,需对制冷工艺方案进行技术经济对比分析,才能作出决策。
工艺流程的设计
从伴生气中回收轻烃的工艺流程尽管种类较多,但基本上由几个单元组成。
在工艺设计中,必须统一组织各工艺单元,从系统优化的观点出发,力求有较高的产品收率和产品质量,达到节约工程投资和运行成本,获得较高的技术经济效益的目的。
对于浅冷工艺装置,所需冷量由外加冷剂制冷提供,外加冷源和原料气增压压缩机消耗的动力是浅冷装置运行能耗的主要部分。
因此,为了能使装置经济合理地运行,在组织流程时,尽可能减少增压能耗和冷损。
在确定冷凝压力时,应综合考虑气源压力、外输压力、液烃分馏塔压力和产品收率等因素,使增压能耗最小。
与此同时,在浅冷分离中,由于低温分离器分出的气体具有一定的压力(一般在1.0mpa以上),而这部分气体大多直接外输,并不需要这样高的压力,因而应该考虑回收这部分能量。
利用膨胀制冷,可以获得一定的温降,以补充装置冷量。
要从整个流程来综合设计增压、冷凝分离、制冷、液烃分馏等单元,有效利用压能和外加冷量。
对于深冷工艺装置,为满足工艺条件的冷量要求,首先应立足于国内成熟的膨胀机制冷,仅靠伴生气压降膨胀制冷,满足不了装置对冷量的要求。
为此,需要设置外加冷剂制冷以补充冷量,即采用冷剂制冷与膨胀机制冷相结合的混合制冷工艺。
对于采用膨胀机制冷的装置,原料气预冷后是先膨胀后增压(逆升压)还是先增压后膨胀(正升压),应从整个流程的安排考虑,以便使其达到比较合适的膨胀比,取得尽可能低的制冷温度和尽可能高的收率。
在工艺流程设计中,应积极采用和开发新工艺、新技术,以达到节能降耗、提高液烃收率的目的。
如采用气体过冷工艺、液体过冷工艺、直接换热工艺、混合冷剂制冷工艺等。
工艺参数的优化
合理的工艺参数既是满足一定工艺要求的保证,也是使装置能在经济合理的工况下运行的前提。
当油田伴生气的组成一定时,对于浅冷工艺装置,主要是确定冷凝温度和压力。
冷凝压力的确定首先应考虑气体外输的压力要求。
当冷凝下
来的液烃需要靠本身压力输到液烃分馏单元时,冷凝压力还应满足液烃分馏操作的压力要求。
如果气体外输压力高于液烃分馏操作压力,则应按外输压力确定冷凝压力,反之则按液烃分馏操作的压力来确定冷凝压力。
当采用膨胀机制冷时,冷凝压力也应为达到一定的膨胀比创造条件。
对于以回收烃类为目的装置,当冷凝压力初步选定后,在确定冷凝温度时,既要保证较高的冷凝率,又不能使的冷凝率过高。
在压力一定时,这个温度主要与气体组成有关。
伴生气中含量较多时,此温度较高,反之则较低。
若冷
凝温度降低,虽然的冷凝率有所增加,但因的冷凝率增加更快,不仅要耗费更多的冷量来冷凝,而且还必须耗费热量将其从凝析液中脱除出来,这在经济上是不合理的。
在工艺设计中,从整个工艺流程出发,综合考虑各单元的能量利用,从而确定合理的冷凝温度和压力。
以回收烃类为目的浅冷装置,一般情况下的收率是比较合适的,深冷装置的回收率一般认为比较合适,但应进行工艺计算、方案对比,确定最佳产品收率。
若确定适宜的冷凝温度介于,采用丙烷冷剂压缩循环制冷提供工艺所需的冷量;若冷凝温度低于,为了达到较为经济的轻烃回收率,可适当提高冷凝压力或可采用膨胀制冷达到要求的低温。
主要设备选型和设计
工艺流程是由各种工艺设备组合而成,流程能否实现工艺设计的目的,关键问题之一是设备选型和设计是否合理。
设备选型和设计中应遵循轻便、高效、技术先进、工作可靠等原则。
在装置中,如果气—液分离器存在设计计算和内部结构不够合理等问题,气相中会携带出液滴,就得不到与计算结果相同的凝液量,液烃回收率就降低了。
常规的重力分离器,分离效果并不是很好,为了改进分离效果,我公司致力于这方面的研究工作,研制了多种高效分离器,可在回收装置中选用,以提高气—液分离效果。
压缩机、制冷机、膨胀机设计选型时,要与制造厂家充分协商研究,给厂家提供详细、准确的工艺要求和相关参数,正确选型,以保证机组供货质量。
选型时应以国产机组为主,必要时可引进国外设备。
对于伴生气轻烃回收装置,压缩机和冷剂制冷机组是装置能耗的主要部分,选型时,压缩机的功率和制冷机的制冷量要估算准确,以减少能耗。
板翅式换热器具有体积小、换热面积大、对介质的适应性强、换热温差小等优点。
但板翅式换热器还没有形成标准系列。
设计选型时,设计人员给生产厂家提供各股流的工艺参数、热负荷以及工艺要求,由厂家进行详细设计和生产,以保证换热器的质量。
冷换设备和冷剂蒸发器都可用板翅式,重量轻、换热效率高,有利于橇装设计。
目前,国产轻烃回收装置中,分馏塔(脱乙烷塔、脱丙烷塔、脱丁烷塔)多数采用填料塔,少数采用浮阀板式塔。
近年来,我公司根据已投产的几十套设备的经验,已研制成功新型高效填料、高效分布器与再分布器,为填料塔在轻烃回收装置中广泛应用创造了良好条件。
加热炉的设计和选型应力求炉体结构简单、造价低、占地面积小、热效率高,满足连续和平稳生产运行的工艺要求,便于实现橇装化。
国内主要采用圆筒式加热炉和火筒式加热炉。
结语
一般来说,伴生气具有压力低,气质富的特性,为满足冷凝分离工艺要求,需设置压缩机增压过程,增压值大小与干气外输压力、制冷温度、分馏塔塔压、产品收率等因素有关。
应精心组织工艺流程,正确选用制冷工艺,合理利用外冷和内冷,通过工艺计算、参数研究,对多种工艺方案进行技术和经济对比分析,达到提高液烃回收率、节约投资的目的。
设备选型和设计应体现技术先进和高效的原则。
小型浅冷装置控制系统应简单实用,大中型深冷装置应优化控制设计方案,选用先进的集散控制系统。
青岛汇森能源设备有限公司。