DTS,GD&T图纸审查标准
汽车开发中尺寸工程的实际应用及未来展望
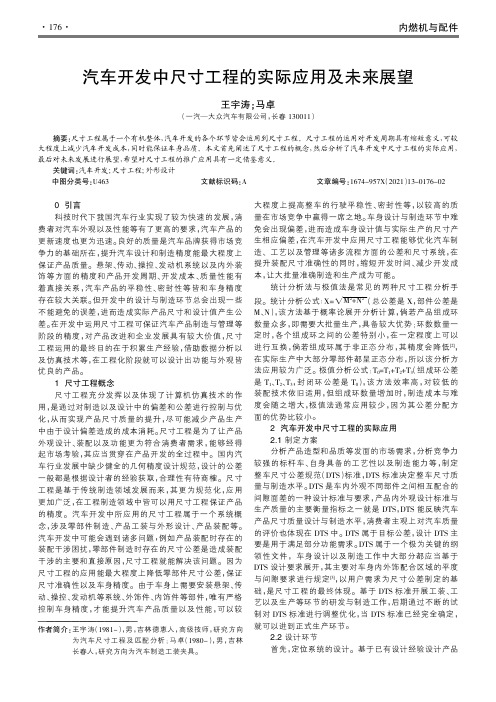
· 176 ·
内燃机与配件
汽车开发中尺寸工程的实际应用及未来展望
王宇涛曰马卓
(一汽—大众汽车有限公司,长春 130011)
摘要院尺寸工程属于一个有机整体,汽车开发的各个环节皆会运用到尺寸工程。尺寸工程的运用对开发周期具有缩短意义,可较
大程度上减少汽车开发成本,同时能保证车身品质。本文首先阐述了尺寸工程的概念,然后分析了汽车开发中尺寸工程的实际应用,
最后对未来发展进行展望,希望对尺寸工程的推广应用具有一定借鉴意义。
关键词院汽车开发;尺寸工程;外形设计
中图分类号院U463
文献标识码院A
ቤተ መጻሕፍቲ ባይዱ
车身部DTS培训课件
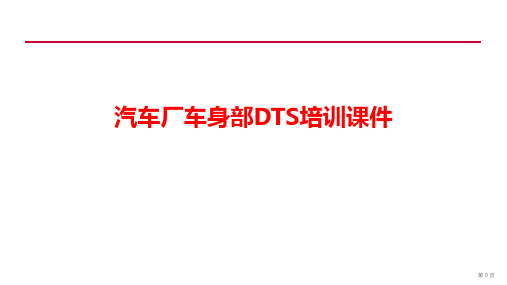
• 前大灯到引擎盖的DTS标准。包 括了上下及左右方向的间隙、间 隙的平行度;前后方向的平整度、 平整度的平行度。如果设计上平 整度非零的话还要定义出哪个零 件低。
第5页
1.1 尺寸十步法
2、尺寸技术规范(DTS) • 仪表板上本体到前门内饰板的 DTS标准。包括左右方向的间隙、 前后方向的平整度、左右间隙的 一致性、上下方向的直线度。
一、尺寸工程的工作流程概述
GD&T
测点图
第 12 页
1.1 尺寸十步法
6、测量系统 定义:在生产过程中具体使用什么设备,如何对零件、总 成、整车进行测量。包括在线和离线两种用方式。 不同的测量设备能提供不同的测量输出,但需要的成本和 时间都不同。在制造规划中,这是用非常重要的环节。 常用用的测量设备:三坐标测量机+测量用支架、检具、 白光扫描、激光扫描、游标卡尺、塞尺等等。
第9页
1.1 尺寸十步法
3、尺寸偏差分析
输入 • 造型 • 基准定位策略 • 制造工艺 • 制造能力
一、尺寸工程的工作流程概述
尺寸 偏差分析
输出 • ±3σ(99.73%) • 设计目标的理 论超差概率 (< 5%) • 影响因素的权 重
第 10 页
1.1 尺寸十步法
一、尺寸工程的工作流程概述
4、工程图纸/基准定位策略 尺寸工程前期开发阶段的最后一步工作,以输出为主。 包括了基准定位策略和工程图纸。
9、尺寸验证 定义:在小批量的匹配验证以及大批量的尺寸数据管理的基础上,大批量地验证零件及DTS的实现状态。
第 16 页
1.1 尺寸十步法
一、尺寸工程的工作流程概述
10、稳定性控制/经验总结 定义:在投产阶段完成所有尺寸验证以后,项目开始进入稳定生产阶段。持续提升制造稳定性,并继 续优化尺寸波动,使其更趋向于设计名义值。同时为新项目的开发做好经验总结。
汽车尺寸工程(5星培训材料)
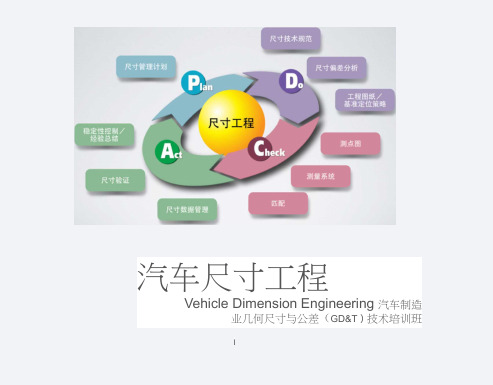
ALIGNMENT)
•平行度(PARALLEL)、一致性 (
CONSISTENCY)、 •车身外饰、空调电子内饰
13
丫 —J
汽车制造业几何尺寸与公差(GD&T)技术培训班
1.1尺寸十步法
3、尺寸偏差分析
目标
发布
白车身 图纸要求
DTS Door to Fender Gap +/- O.xx
9
网絡系统运行 11/5/2012 12/1/2012
5'
57
8
9 10 11 12
I
L_______________I I_________________________
9
汽车制造业几何尺寸与公差(GD&T)技术培训班
1.1尺寸十步法
2、尺寸技术规范(DTS)
-定义:在整车层面上定义了能代表客户呼声的尺寸要
2
汽车制造业几何尺寸与公差(GD&T)技术培训班
课程目录
3.尺寸技术规范(DTS)的实现 3.1. DTS实现方案综述 3.2. 基准定位策略的开发方法 3.3. 尺寸偏差分析简介 3.4. 尺寸与制造工艺的同步开发 3.5. 尺寸与结构设计的同步开发 3.6. 尺寸与制造能力的同步 3.7. DTS风险评估
以及整车的尺寸表现,以整车匹配达到设计标 准为目的。
7
汽车制造业几何尺寸与公差(GD&T)技术培训班
1.1尺寸十步法
匹配
©
尺寸数据管理
8
汽车制造业几何尺寸与公差(GD&T)技术培训班
1.1尺寸十步法
"出赢E網関識关工
汽车尺寸工程学习培训资料
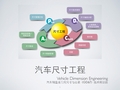
汽⻋车制造业几几何尺寸寸与公差(GD&T)技术培训班
1.1 尺寸寸十十步法
尺寸寸技术规范 尺寸寸管理计划 尺寸寸偏差分析
工工程图纸/ 基准定位策略
稳定性控制/ 经验总结
尺寸寸工工程
测点图
尺寸寸验证 匹配
8
测量系统
尺寸寸数据管理
汽⻋车制造业几几何尺寸寸与公差(GD&T)技术培训班
1.1 尺寸寸十十步法
15
汽⻋车制造业几几何尺寸寸与公差(GD&T)技术培训班
1.1 尺寸寸十十步法
3、尺寸寸偏差分析 输入入
• • • •
输出
• •
尺寸寸 偏差分析
造型 基准定位策略 制造工工艺 制造能力力
±3σ(99.73%) 设计⺫目目标的理 论超差概率
(< 5%)
•
影响因素的权 重
16
汽⻋车制造业几几何尺寸寸与公差(GD&T)技术培训班
1.1 尺寸寸十十步法
2、尺寸寸技术规范(DTS) • 仪表板木木纹条到⻔门内饰板木木纹条的DTS标准。包括左右 方方向的间隙、前后方方向的平整度、左右间隙的一一致性、 上下方方向的直线度。
12
汽⻋车制造业几几何尺寸寸与公差(GD&T)技术培训班
1.1 尺寸寸十十步法
2、尺寸寸技术规范(DTS) • 几几个关键词: • 客户呼声:源自自(a)标杆⻋车的配合状态; (b)市场调查 (c)损益函数 • 间隙(GAP)、平整度(FLUSH)、直线度 (ALIGNMENT) • 平行行度(PARALLEL)、一一致性 (CONSISTENCY)、 • ⻋车身身外饰、空调电子子内饰
1.1 尺寸寸十十步法
• 尺寸寸工工程的定义: - 整⻋车设计的一一部分,致力力于获得最佳的⻋车身身内外饰外 观配合。 - 以尺寸寸技术规范(DTS)为贯穿始终的主线。 - 前期开发阶段(第1到4步)以提出标准为主,包括外 观配合要求以及零件图纸要求,辅以基准定义、偏差 分析、⻛风险评估等工工具。以达到设计合理性为⺫目目的。 - 后期试制阶段(第5到10步)以测量控制为手手段,评 估零件以及整⻋车的尺寸寸表现,以整⻋车匹配达到设计标 准为⺫目目的。
尺寸匹配专业术语
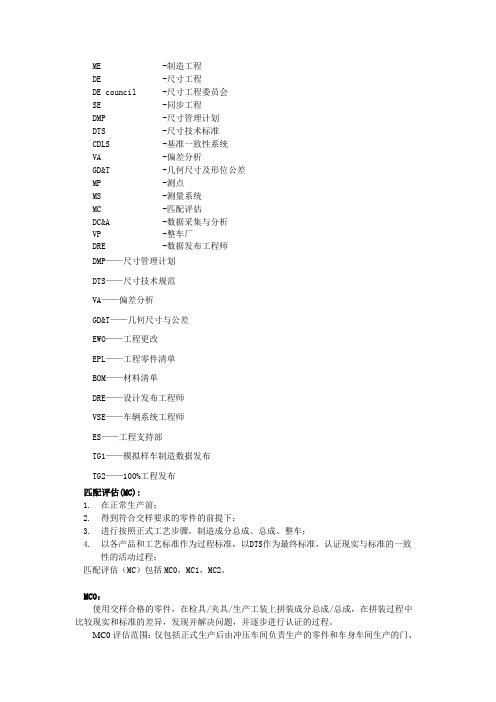
ME -制造工程DE -尺寸工程DE council -尺寸工程委员会SE -同步工程DMP -尺寸管理计划DTS -尺寸技术标准CDLS -基准一致性系统VA -偏差分析GD&T -几何尺寸及形位公差MP -测点MS -测量系统MC -匹配评估DC&A -数据采集与分析VP -整车厂DRE -数据发布工程师DMP——尺寸管理计划DTS——尺寸技术规范VA——偏差分析GD&T——几何尺寸与公差EWO——工程更改EPL——工程零件清单BOM——材料清单DRE——设计发布工程师VSE——车辆系统工程师ES——工程支持部TG1——模拟样车制造数据发布TG2——100%工程发布匹配评估(MC):1.在正常生产前;2.得到符合交样要求的零件的前提下;3.进行按照正式工艺步骤,制造成分总成、总成、整车;4.以各产品和工艺标准作为过程标准,以DTS作为最终标准,认证现实与标准的一致性的活动过程;匹配评估(MC)包括MC0,MC1,MC2。
MC0:使用交样合格的零件,在检具/夹具/生产工装上拼装成分总成/总成,在拼装过程中比较现实和标准的差异,发现并解决问题,并逐步进行认证的过程。
MC0评估范围:仅包括正式生产后由冲压车间负责生产的零件和车身车间生产的门、盖等总成,及门盖相关的中小冲零件;MC1:使用交样合格的零件,在检具/夹具/生产工装上拼装成分总成/总成/整车,在每步的拼装过程中比较现实和标准的差异,发现并解决问题,逐步进行认证的过程。
* MC1评估范围:所有白车身零件/总成,车身车间生产的门、盖等总成,及直接或间接影响DTS的内、外饰零件/总成,包括部分地盘和电器零件。
MC2:使用交样合格的零件,在生产工装上拼装成分总成/总成/整车,在每步的拼装过程中比较现实和标准的差异,发现并解决问题,逐步进行认证的过程。
同时需要验证MC1活动中发现问题的更改结果。
* MC2评估范围:所有白车身零件/总成,车身车间生产的门、盖等总成,及直接或间接影响DTS的内、外饰零件/总成,包括部分地盘和电器零件。
尺寸工程在汽车设计过程中的应用
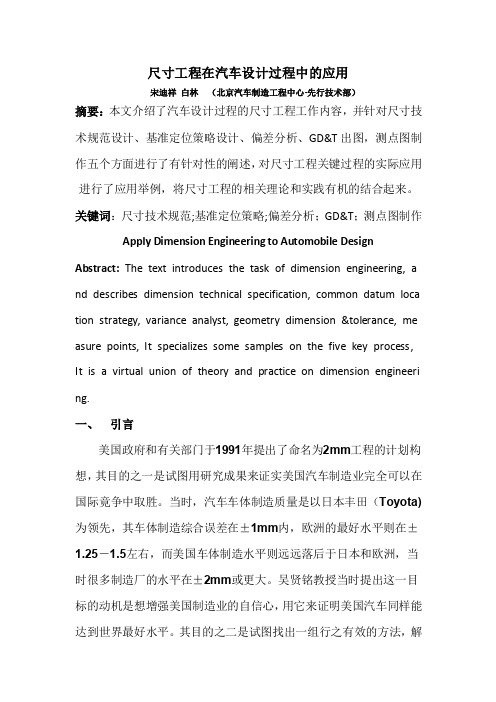
图6 后轮罩定位孔所在控制方向的转化 3.3、偏差分析
在产品结构确定后,建立了定位基准,要对零件大的总成或整车 控制要求进行公差初步设计,传统的偏差有1D尺寸链分析,通过尺寸 链图解进行测算,后续又有2D尺寸链计算,由于整车的结构设计比较 复杂,传统的计算方法已经很难满足需求,通过3D尺寸的公差分析, 确保公差实施的可行性,同时又能够满足产品的功能要求和客户的视 觉美感。产品设计部门希望制造的结果越精细越好,而制造部门的希 望是公差放的越宽松越好,所以两者必须找到一个平衡点,以确保产 品功能的最终合理实现。
Байду номын сангаас
图11 某主机厂基础通用公差表 通用公差表,是单件制作GD&T图纸的重要依据,根据它及相关工艺 知识对焊接总成的公差进行合理设计。
图12 某车型大地板总成GD&T局部图
如图所示大地板的总成的轮廓度公差带是2.0,对其进行验算,地板 的翻边轮廓度公差为1.0,门槛加强版的配合面轮廓度公差为1.0,定 位孔偏离公差为0.3,焊接后变形轮廓度公差0.4,对总公差带进行验 算采用RSS算法:总公差带=SQRT(12+12+0.32+0.42)=1.5,所以给定的公 差带2.0可以满足工艺要求,同时该处在配合处不能向外突出太多, 所以公差带不是对称的,最多允许突出0.5,以确保最终白车身总成 的合格。 3.5、测点图制作
尺寸工程介绍

Sum of Remaining 12 Contributors
15
DM- Dimensional Management
柔性零件偏差分析(EVAS)
• 在三维偏差分析(3-DCS)的基础上融入了有限元的原理来建立数学 模型,充分考虑零件变形,用以分析最终的DTS配合公差。同时还就 焊接工装及检具的夹紧顺序进行分析和改进。 优点:在融入了有限元的原理后,所建立的数学模型与实际零件的状 态最符合,考虑因素最全面。 缺点:建模时间最长,工作量最大。
尺寸项目经理
设计工程师 造型工程师 制造工程师
尺寸工程师
*CBOB:Competitive Best of Best
9
DM- Dimensional Management
尺寸技术规范(DTS)
• • • • DTS图示文件,以图片表达DTS的位置以及具体的要求。 DTS汇总表,以列表的形式来表达DTS,便于统计以及状态跟 踪。 典型断面 统一基准定位策略
质量评估报告
测量设备准备 车身及内外饰零件 在线质量认证 及Launch支持
建立偏差分析模型验算
工艺工程部
生产尺寸数据监控 及数据分析和发布
质量保证部
生成GD&T图纸
不断改进
采购部/供应商
11
DM- Dimensional Management
偏差分析
“输入” • 尺寸管理计划 • 尺寸技术规范 (DTS) –统一基准 定位策略 –估算公差 –工艺及生 产能力 –造型 “输出”
7
DM- Dimensional Management
尺寸管理计划
• 是一种项目管理工具,用以在车辆开发过程中跟踪关键的尺寸工作及 其交付物。 “输入” • 尺寸管理计划 模版
上海通用术语

AHE:外观颜色匹配工程师APQP:产品质量先期策划DRE:设计发布工程师DTS:尺寸技术准备ETR:工程试装要求EWO:工程更改FE:功能评估GCA:全球顾客评审GD&T:主要尺寸相关的零件、总成和整车的形位公差图纸,几何尺寸及公差图纸。
GMGlobalAAR---GM全球外观认可报告GP4:生产件批准状况通知-MC0/1基准必须与PTRTE:试验工程师TVE:(动力总成)总认证工程师VPM:整车性能经理IV:工程认可(需要提供零件尺寸报告、材料试验报告、总成性能报告等所有试验报告)MC1/2:尺寸匹配(提交尺寸报告,合格率80%/90%)PVV:产品验证,小批量制造(尺寸报告,零件必须通过GP12)NS:非销售车制造(零件必须通过GP12-100%检验)S:销售车制造(零件通过PPAP人认可,零件必须通过GP12-100%检验)SORP:量产开始(具体数量根据订单,一般IV80套,MC10套,PVV几套到几十套不等。
)AQC:AttributeQualityCharacteristic属性质量特性ASQE:AdvancedSupplierQualityEngineer先期供应商质量工程师BIW:uallythebaremetalshellofthebodyincludingdoorsanddecklidpriortopaintandtrim.白车身BOM:BillofMaterials材料清单BOP:BillofProcess过程清单BrownfieldSite:Anexpansionofanexistingfacility.扩建场地CMM:CoordinateMeasuringMachine三坐标测试仪Cpk:CapabilityIndexforastabileprocess过程能力指数CTC:ComponentTimingChart(DREdocument)零部件时间表(DRE文件)CTS:ComponentTechnicalSpecifications零部件技术规范CVER:ConceptVehicleEngineeringRelease概念车工程发布DC:DesignComplete设计完成Defectoutflowdetection:AphraseusedintheSupplierQualityStatementofRequirementsthatreferstoin-processorsu bsequentinspectionusedtodetectdefectsinparts.缺陷检测DFM/DFA:DesignforManufacturability/DesignforAssembly可制造性/可装配性设计DFMEA:DesignFailureModesandEffectsAnalysis.Itisusedtoidentifythepotentialfailuremodesofapart,associated withthedesign,andestablishaprioritysystemfordesignimprovements.设计失效模式和后果分析DPV:Defectspervehicle每辆车缺陷数DR:DocumentationRequiredDR特性DRE:DesignReleaseEngineer设计释放工程师DV:DesignValidation设计验证E&APSP:Engineering&AdvancePurchasingSourcingProcess.工程&先期采购定点程序EP:E-Procurement电子采购流程)LAAM:(GeneralMotors)LatinAmerican,Africa&MeddleEast(通用汽车)拉丁美洲、非洲及中东LCR:LeanCapacityRate.ItistheGMdailycapacityrequirement.正常生产能力MCR:MaximumCapacityRate.ItistheGMmaximumcapacityrequirement.最大生产能力MOP:MakeorPurchase制造/采购MPC:MaterialProductionControl物料生产控制MPCE:MaterialProductionControlEurope欧洲物料生产控制MRD:MaterialRequiredDate;datematerialmustbedeliveredinordertoallowabuildeventtobegin.物料需求日期MSA:MeasurementSystemsAnalysis测量系统分析MVBns:ManufacturingValidationBuildnon-saleable非销售车制造验证MVBs:ManufacturingValidationBuildsaleable销售车制造验证NBH:NewBusinessHold停止新业务OEM:OriginalEquipmentManufacturer主机客户PAD:ProductionAssemblyDocuments生产装配文件PC&L:ProductionControl&Logistics生产控制&物流PDT:ProductDevelopmentTeam产品开发小组PFMEA:ProcessFailureModesandEffectsAnalysis.Itisusedtoidentifypotentialfailuremodesassociatedwiththema nufacturingandassemblyprocess.过程失效模式和后果分析PPAP:ProductionPartApprovalProcess生产件批准程序Ppk:Performanceindexforastableprocess过程能力指数PPM:1)ProgramPurchasingManager,2)PartsperMillion(rejectsandreturnstosuppliers)1)项目经理2)每百万件的产品缺陷数PPV:Product&ProcessValidation产品及过程验证PQC:ProductQualityCharacteristic产品质量特性SSTS:Sub-systemTechnicalSpecifications子系统技术规范Sub-Assembly/Sub-System:Anassemblyofsub-componentsdeliveredtotheSGMmainproductionlineforinstallationtothevehicleasasingleunit.Subcontractor:Thesupplierofasub-componenttoaComplexSystem/Subassemblysupplier(Tier2,3,etc).分供方SVE:Sub-SystemValidationEngineer子系统验证工程师SVER:StructureVehicleEngineeringRelease.结构车工程发布TeamFeasibilityCommitment:AnAIAGAPQPformthatisprovidedwiththeRequestforQuotation.Itisthesupplier’sconcernswiththefeasibilityofmanufacturingthepartasspecified.小组可行性承诺TKO:ToolingKick-Off模具启动会议UG:UnigraphicsUG工程绘图造型系统VLE:VehicleLineExecutive车辆平台负责人VTC:ValidationTestingComplete验证试验完成WO:EngineeringWorkOrder工程工作指令。
上海通用术语
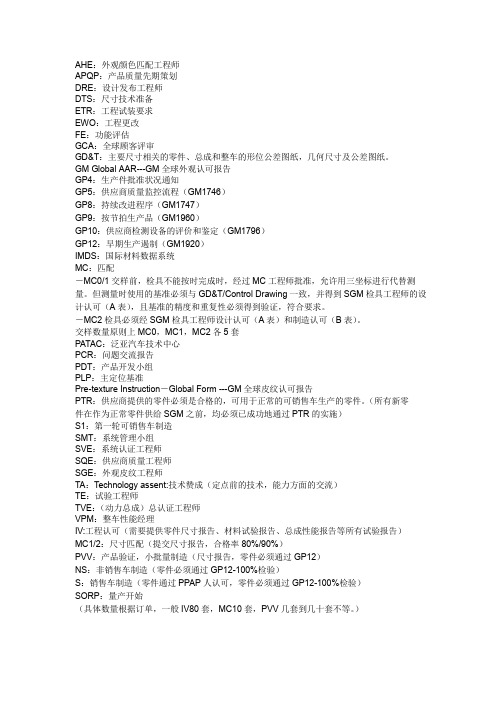
AHE:外观颜色匹配工程师APQP:产品质量先期策划DRE:设计发布工程师DTS:尺寸技术准备ETR:工程试装要求EWO:工程更改FE:功能评估GCA:全球顾客评审GD&T:主要尺寸相关的零件、总成和整车的形位公差图纸,几何尺寸及公差图纸。
GM Global AAR---GM全球外观认可报告GP4:生产件批准状况通知GP5:供应商质量监控流程(GM1746)GP8:持续改进程序(GM1747)GP9:按节拍生产品(GM1960)GP10:供应商检测设备的评价和鉴定(GM1796)GP12:早期生产遏制(GM1920)IMDS:国际材料数据系统MC:匹配-MC0/1交样前,检具不能按时完成时,经过MC工程师批准,允许用三坐标进行代替测量。
但测量时使用的基准必须与GD&T/Control Drawing一致,并得到SGM检具工程师的设计认可(A表),且基准的精度和重复性必须得到验证,符合要求。
-MC2检具必须经SGM检具工程师设计认可(A表)和制造认可(B表)。
交样数量原则上MC0,MC1,MC2各5套PATAC:泛亚汽车技术中心PCR:问题交流报告PDT:产品开发小组PLP:主定位基准Pre-texture Instruction-Global Form---GM全球皮纹认可报告PTR:供应商提供的零件必须是合格的,可用于正常的可销售车生产的零件。
(所有新零件在作为正常零件供给SGM之前,均必须已成功地通过PTR的实施)S1:第一轮可销售车制造SMT:系统管理小组SVE:系统认证工程师SQE:供应商质量工程师SGE:外观皮纹工程师TA:T echnology assent:技术赞成(定点前的技术,能力方面的交流)TE:试验工程师TVE:(动力总成)总认证工程师VPM:整车性能经理IV:工程认可(需要提供零件尺寸报告、材料试验报告、总成性能报告等所有试验报告)MC1/2:尺寸匹配(提交尺寸报告,合格率80%/90%)PVV:产品验证,小批量制造(尺寸报告,零件必须通过GP12)NS:非销售车制造(零件必须通过GP12-100%检验)S:销售车制造(零件通过PPAP人认可,零件必须通过GP12-100%检验)SORP:量产开始(具体数量根据订单,一般IV80套,MC10套,PVV几套到几十套不等。
GD&T基础培训

GD&T 基础培训GD&T OverviewYFJC Plastic TeamMay. 2010培训目的Target一:了解GD&T图纸的作用和基本构成二:了解用来定义形位公差的术语和基本符号三:了解基准的基本含义四:理解独立原则与最大实体原则2五:充分理解经常使用的面轮廓度和位置度六:了解尺寸和形位公差的基本检测要求目录content一:GD&T概念及背景Overview二:GD&T的标注介绍Symbols三:基准Datum四:公差带Tolerance Zone3--面轮廓度Surface Profile--位置度Position五:公差原则Principles--最大实体MMC--独立原则RFS六:案例和练习Example & practice一:GD&T及背景OverviewGD&T是Geometric Dimensioning and Tolerancing的缩写,即几何要素公差,我们常称为“形状与位置公差”。
标准中包含有尺寸标注方法(属我国技术制图标准)和几何公差(属我国形状和位置公差标准)两大部分。
本次培训将重点地对“形状和位置(几何)公差”部分结合我们的产品要求进行基础性介绍和讲解。
4目前,各大OEM标准(GM)和我国的形位公差标准都等效采用了国际ISO标准,所以绝大多数的内容是相同和互通的,除非特别需要,不再分别展开介绍。
一:GD&T及背景OverviewGD&T图纸的意义1.设计思路(定位方式与DTS要求)的表达和传递。
2.检具设计的依据。
3.零件重要特征的粗略定义。
5二:GD&T的标注介绍SymbolsGD&T中的名词定义Definitions•尺寸Dimension带有测量单位的数值,用以规定一个零件的尺寸和/或形位特性和/或要素的位置•要素Feature指零件上的特征,如:点、线、面、孔、槽、突起等, 形位公差研究的对象。
尺寸工程概述讲解

设计完成的时候,我们想知道:水箱横梁安装是否会出现安装不上的问 题?如果干涉,将通过改进什么来消除?怎么办?
通过尺寸链计算,得出公差并和1.25mm的调整量比较。要加大孔径、 或者改变设计结构、焊装顺序等。
左侧图表为尺寸链的计算: 上面显示尺寸链各组成环的详细信息,从图中可以得出 ± 3σ=
± 0.87
VSA软件中各尺寸链主要组成环的公差列表:
输入信息
装配界面
模型界面
装配界面为整个侧围总成的特性,可显示夹具信息,装配操作,数据信息,数据特性(GD&T) 模型界面可将特性可视化,图中可以看出侧围外板的定位系统,定位特性(包括板件和夹具公差及矢量方向)
目
录
一、尺寸工程概述
二、尺寸工程工作流程
三、减小累积公差的方法
四、奇瑞公司尺寸工程的现状
五、尺寸仿真软件VisVSA工作原理和应用情况介绍
一:尺寸工程概述
1、什么是尺寸工程?
◆尺寸工程是完善设计和装配制造阶段的工程化过程。 ◆尺寸工程是通过控制制造偏差和优化设计来提高产品尺寸质量和减低产品生产成本的一种手段。 ◆从产品研发早期介入一直到量产,通过执行一套完整、系统、严谨、科学、操作性强的工作流程,达到降低研发成本,缩短 开发周期,完成产品设定目标,提高产品竞争力的目的。 ◆尺寸工程确保产品的:a、功能(舒适性、安全性、密封性);b、装配;c、外观设计要求。 ◆尺寸工程应该贯穿整个产品开发周期,尤其是产品设计前期的工作尤为重要。
2、减小尺寸链中每环的公差 ◆ 提高冲压件的精度; ◆ 提高夹具的精度; ◆ 提高附件的精度。
通用术语

AHE:外观颜色匹配工程师 APQP:产品质量先期策划 DRE:设计发布工程师 DTS:尺寸技术准备 ETR:工程试装要求 EWO:工程更改 FE:功能评估GCA:全球顾客评审GD&T:主要尺寸相关的零件、总成和整车的形位公差图纸,几何尺寸及公差图纸。
GM Global AAR---GM全球外观认可报告 GP4:生产件批准状况通知GP5:供应商质量监控流程(GM1746) GP8:持续改进程序(GM1747) GP9:按节拍生产品(GM1960)GP10:供应商检测设备的评价和鉴定(GM1796) GP12:早期生产遏制(GM1920)IMDS:国际材料数据系统 MC:匹配-MC0/1交样前,检具不能按时完成时,经过MC工程师批准,允许用三坐标进行代替测量。
但测量时使用的基准必须与GD&T/Control Drawing一致,并得到SGM检具工程师的设计认可(A表),且基准的精度和重复性必须得到验证,符合要求。
-MC2检具必须经SGM检具工程师设计认可(A表)和制造认可(B表)。
交样数量原则上MC0,MC1,MC2各5套 PATAC:泛亚汽车技术中心 PCR:问题交流报告 PDT:产品开发小组 PLP:主定位基准Pre-texture Instruction-Global Form ---GM全球皮纹认可报告PTR:供应商提供的零件必须是合格的,可用于正常的可销售车生产的零件。
(所有新零件在作为正常零件供给SGM之前,均必须已成功地通过PTR的实施) S1:第一轮可销售车制造 SMT:系统管理小组 SVE:系统认证工程师 SQE:供应商质量工程师 S GE:外观皮纹工程师TA:Technology assent:技术赞成(定点前的技术,能力方面的交流) TE:试验工程师TVE:(动力总成)总认证工程师 VPM:整车性能经理IV:工程认可(需要提供零件尺寸报告、材料试验报告、总成性能报告等所有试验报告) MC1/2:尺寸匹配(提交尺寸报告,合格率80%/90%)PVV:产品验证,小批量制造(尺寸报告,零件必须通过GP12) NS:非销售车制造(零件必须通过GP12-100%检验)S:销售车制造(零件通过PPAP人认可,零件必须通过GP12-100%检验) SORP:量产开始(具体数量根据订单,一般IV80套,MC10套,PVV几套到几十套不等。
通用术语

ASQE: Advanced Supplier Quality Engineer 先期供应商质量工程师
GD&T: Geometric Dimensioning & Tolerancing 几何尺寸与公差
SGM: Shanghai General Motors 上海通用汽车
GMAP: General Motors Asian Pacific 通用汽车亚太
PSA: Potential Supplier Assessment, a subset of the Quality System Assessment (QSA) 潜在供应商评审
PV: Product Validation 产品验证 QSA: Quality System A: General Motors Europe 通用汽车欧洲
GMNA: General Motors North American 通用汽车北美
GP: General Procedure
MCR: Maximum Capacity Rate. It is the GM ma ximum capacity requirement. 最大生产 能力
APQP:产品质量先期策划 DRE:设计发布工程师 DTS:尺寸技术准备 EWO:工程更改 GD&T:主要尺寸相关的零件、总成和整车的形位公差 图纸,几何尺寸及公差图纸。 GP4 :生产件批准状况通知 GP5 :供应商质量监控流程( GM1746 ) GP8 :持续改进程序( GM1747 )
AAR: Appearance Approval Repo rt 外观批准报告
Sub-Assembly / SubSystem: An assembly of subcomponents delivered to the SGM main production line for installation to the vehi cle as a single unit.
通用英文缩写解释

通用英文缩写解释AH:外观颜色匹配工程师APQP:产品质量先期策划DRE:设计发布工程师DTS:尺寸技术准备ETR:工程试装要求EWO:工程更改FE:功能评估GCA:全球顾客评审GD&T:主要尺寸相关的零件、总成和整车的形位公差图纸,几何尺寸及公差图纸。
GM Global AAR---GM全球外观认可报告GP4:生产件批准状况通知GP5:供应商质量监控流程(GM1746)GP8:持续改进程序(GM1747)GP9:按节拍生产品(GM1960)GP10:供应商检测设备的评价和鉴定(GM1796)GP12:早期生产遏制(GM1920)IMDS:国际材料数据系统MC:匹配-MC0/1交样前,检具不能按时完成时,经过MC工程师批准,允许用三坐标进行代替测量。
但测量时使用的基准必须与GD&T/Control Drawing一致,并得到SGM检具工程师的设计认可(A表),且基准的精度和重复性必须得到验证,符合要求。
-MC2检具必须经SGM检具工程师设计认可(A表)和制造认可(B表)。
交样数量原则上MC0,MC1,MC2各5套PATAC:泛亚汽车技术中心PCR:问题交流报告PDT:产品开发小组PLP:主定位基准Pre-texture Instruction-Global Form ---GM 全球皮纹认可报告PTR:供应商提供的零件必须是合格的,可用于正常的可销售车生产的零件。
(所有新零件在作为正常零件供给SGM之前,均必须已成功地通过PTR的实施)S1:第一轮可销售车制造SMT:系统管理小组SVE:系统认证工程师SQE:供应商质量工程师SGE:外观皮纹工程师TA:Technology assent:技术赞成(定点前的技术,能力方面的交流)TE:试验工程师TVE:(动力总成)总认证工程师VPM:整车性能经理IV:工程认可(需要提供零件尺寸报告、材料试验报告、总成性能报告等所有试验报告)MC1/2:尺寸匹配(提交尺寸报告,合格率80%/90%)PVV:产品验证,小批量制造(尺寸报告,零件必须通过GP12)NS:非销售车制造(零件必须通过GP12-100%检验)S:销售车制造(零件通过PPAP人认可,零件必须通过GP12-100%检验)SORP:量产开始(具体数量根据订单,一般IV80套,MC10套,PVV几套到几十套不等。
基于尺寸工程的产品质量控制
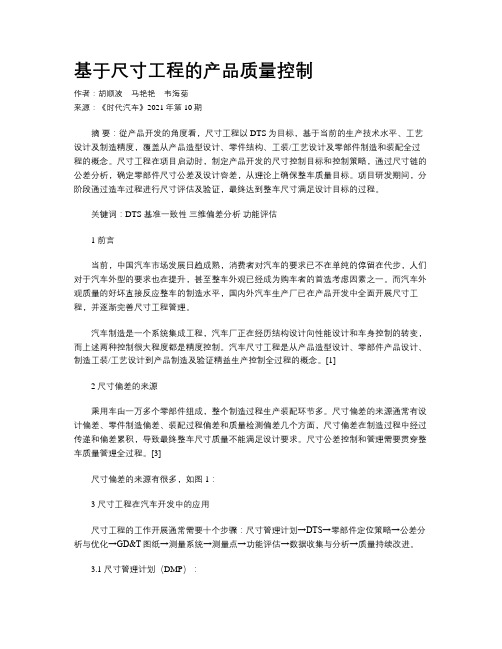
基于尺寸工程的产品质量控制作者:胡顺波马艳艳韦海菊来源:《时代汽车》2021年第10期摘要:從产品开发的角度看,尺寸工程以DTS为目标,基于当前的生产技术水平、工艺设计及制造精度,覆盖从产品造型设计、零件结构、工装/工艺设计及零部件制造和装配全过程的概念。
尺寸工程在项目启动时,制定产品开发的尺寸控制目标和控制策略,通过尺寸链的公差分析,确定零部件尺寸公差及设计容差,从理论上确保整车质量目标。
项目研发期间,分阶段通过造车过程进行尺寸评估及验证,最终达到整车尺寸满足设计目标的过程。
关键词:DTS 基准一致性三维偏差分析功能评估1 前言当前,中国汽车市场发展日趋成熟,消费者对汽车的要求已不在单纯的停留在代步,人们对于汽车外型的要求也在提升,甚至整车外观已经成为购车者的首选考虑因素之一。
而汽车外观质量的好坏直接反应整车的制造水平,国内外汽车生产厂已在产品开发中全面开展尺寸工程,并逐渐完善尺寸工程管理。
汽车制造是一个系统集成工程,汽车厂正在经历结构设计向性能设计和车身控制的转变,而上述两种控制很大程度都是精度控制。
汽车尺寸工程是从产品造型设计、零部件产品设计、制造工装/工艺设计到产品制造及验证精益生产控制全过程的概念。
[1]2 尺寸偏差的来源乘用车由一万多个零部件组成,整个制造过程生产装配环节多。
尺寸偏差的来源通常有设计偏差、零件制造偏差、装配过程偏差和质量检测偏差几个方面,尺寸偏差在制造过程中经过传递和偏差累积,导致最终整车尺寸质量不能满足设计要求。
尺寸公差控制和管理需要贯穿整车质量管理全过程。
[3]尺寸偏差的来源有很多,如图1:3 尺寸工程在汽车开发中的应用尺寸工程的工作开展通常需要十个步骤:尺寸管理计划→DTS→零部件定位策略→公差分析与优化→GD&T图纸→测量系统→测量点→功能评估→数据收集与分析→质量持续改进。
3.1 尺寸管理计划(DMP):在项目立项初期,需要定义该项目的尺寸目标,尺寸工程的交付物内容以及各项交付物的开发完成计划。
- 1、下载文档前请自行甄别文档内容的完整性,平台不提供额外的编辑、内容补充、找答案等附加服务。
- 2、"仅部分预览"的文档,不可在线预览部分如存在完整性等问题,可反馈申请退款(可完整预览的文档不适用该条件!)。
- 3、如文档侵犯您的权益,请联系客服反馈,我们会尽快为您处理(人工客服工作时间:9:00-18:30)。
面差B设计为 0(-0.5~0)
2. 外观品质基准审查标准
编号 QS-BIW-004
简图
主题
漏风、漏雨、漏光品质要求
说明 前后门窗框部位面差设置应考虑漏 风、漏雨、漏光功能品质要求,如果 窗框部位面差比侧围高的话,整车上 会因密封胶条的弹力影响,面差更加 突出,出现漏风、漏雨、漏光现象, 从而影响整车功能品质。故前后门窗 框面差设计要比侧围低,公差控制在2~0范围内(以侧围为基准)。如左图 前门窗框与侧围面差。 具体要求应与设计公司探讨
y
Y
X
3. 零部件品质基准审查标准
3-2测量点审查
编号
QS-CP-001
简图
主题
测量点位置要求
说明 为使检具设计时合理设置关键检测点, 应提供相应依据,测量部位包含:定位 点、孔位、点焊装配面、CO2焊接面、涂 胶、包边面、关键型面等
3. 零部件品质基准审查标准
编号 QS-CP-002 简图 主题 测量点形式 说明 测量点尽量均布,考虑设置在汽车坐标 线位置,测量点不易过多,以保证测量 的难度,如图,标注部位没有装配要 求,故不需要设置测量点
a L
3. 零部件品质基准审查标准
编号 QS-LC-004 简图 主题 定位孔的形式(有过孔) 说明 d1:定位孔直径d2:间隙孔的直径L<30mm, d2= d1+3(如果是三层板的情况,d2= d1 +3,d3= d2+1)L≥30mm,d2= d1+5
d1
A
L
d2
A
3. 零部件品质基准审查标准
2. 外观品质基准审查标准
外观品质基准 外观品质基准:反应了整车的品质目标要求,及车身间隙面差的设计。
编号
QS-BIW-001 简图
主题
标杆对比 说明 根据标杆车拆解数据,结合我公司工 艺水平,尽量考虑车身外观间隙、面 差设计值与标杆车保持一致,避免公 差加严,以保证工艺上实现的可能性
2. 外观品质基准审查标准
P0 P1-11 P12 P12 P12-16 P17 P18-20 P21 P22 P22-30 P31-45
3-3-1. GD&T审查标准
3-3-2. 特殊公差审查标准 3-3-3. 一般公差审查标准
1. 前言
目前我公司开发车型未对产品输入-车身品质基准进行工艺性分析及验证,品 质基准分外观品质基准(DTS)、零部件品质基准(GD&T)两种,内容包含定位点、
编号 QS-BIW-002
简图
主题
文件与数模一致性
说明 通过车身外观间隙、面差设计值与数 模实际尺寸对比,确保文件与数模一 致性,否则在车身调试过程中,检查 基准书中间隙面差值以品质基准书为 根据编制,导致测量结果误判,造成 模具、夹具按照错误的检测结果进行 更改,从而影响车身品质,调试周期 延长
2. 外观品质基准审查标准
编号 QS-BIW-003
简图
主题
风噪品质要求
说明 车门面差设置应考虑风噪功能品质要 求,因汽车向前高速行驶时,如果前 门比翼子板、后门比前门、侧围后部 比后门面差高的话,会产生风噪现象, 影响整车功能品质。故车门间隙面差 设计时,前门比翼子板、后门比前门、 侧围后部比后门面差要低,公差控制 在-0.5~0范围内(分别以前门、后门、 侧围为基准)。如左图翼子板与前门 面差。 具体要求应与设计公司探讨
编号
QS-GD&T-001
简图
主题
形位公差要求(GD&T)
说明 零件本身、零件与零件相互配合关系要 设定形位公差,包含:直线度、平面 度、线轮廓度、面轮廓度、圆柱度、倾 斜度、垂直度、平行度、位置度、同轴 度、对称度、圆跳动、全跳动等
3. 零部件品质基准审查标准
编号 QS-GD&T-002 简图 主题 特殊公差要求 说明 零部件品质基准书中,影响焊接装配的 搭接部位,影响全车尺寸(长、宽、 高)的相关搭接部位要设定特殊公差 例1:为防止前纵梁翻边反弹导致水箱架 总成安装不到位,进而影响车身长度, 给前纵梁翻边0.5mm的负公差
3. 零部件品质基准审查标准
编号 QS-CP-003 简图 主题 测量点一致性要求 说明 同一零件从单件到总成,要保证测量点 的一致性,避免测量误差,如车门内 板、车门总成、侧围总成相互配合部位 的检测点只有一致,才能通过分析找到 问题真因,从而解决问题
3. 零部件品质基准审查标准
3-3公差设定审查
简图
主题
其他要求-面差方向
说明 以外观面作为基准,朝外为正,朝内 为负
2. 外观品质基准审查标准
编号 QS-BIW-011
简图
A +
主题
其他要求-测量基准
说明 基体作为基准,安装在基体上的装配 件作为被测量对象。例如车身外观件 以白车身本体为基准,外观安装件作 为被测量对象先安装件作为基准,后 安装件作为被测量对象。例如前后门 以后门为基准,前门作为被测量对象 固定件作为基准,可调整件作为被测 量对象。例如前翼子板与前车门,前 车门作为基准,前翼子板作为被测量 对象
前围上部总成
0。5
下前围板总成
3. 零部件品质基准审查标准
编号 QS-GD&T-004 简图 主题 特殊公差要求 说明 零部件品质基准书中,影响焊接装配的 搭接部位,影响全车尺寸(长、宽、 高)的相关搭接部位要设定特殊公差 例3:为防止因地板翻边反弹导致侧围拼 装不到位,进而影响车身宽度,给地板 翻边1.0mm的负公差
简图
主题
特殊公差要求
说明 零部件品质基准书中,影响焊接装配的 搭接部位,影响全车尺寸(长、宽、 高)的相关搭接部位要设定特殊公差 例7:为了保证车身宽度,给侧围门槛 0.5mm正公差
编号 QS-BIW-007
简图
主题
机盖与翼子板外观品质要求
说明 机盖与翼子板面差设置应考虑外观品 质要求和调试难易程度,面差设计上 给0.5 mm的段差,公差控制在±0.5范 围内(以翼子板为基准)。如左图 具体要求应与设计公司探讨
面差B设计为-0. 5(±0.5)
2. 外观品质基准审查标准
编号 QS-BIW-008
2. 外观品质基准审查标准
编号 QS-BIW-006
简图
主题
车身与保险杠外观品质要求
说明 前保险杠与翼子板,后保险杠与侧围 面差设置应考虑外观品质要求和调试 难易程度,公差控制在-0.5~0范围内 (分别以翼子板、侧围为基准)。如 左图 具体要求应与设计公司探讨
面差B设计为 0(-0.5~0)
2. 外观品质基准审查标准
测量点、公差要求,如果这些要求设置不合理,会使模具、夹具、检具开发没有统一
的依据,导致车身不稳定、调试周期延长、开发成本增加。举例说明:定位方面:车 身定位点如果设定不合理,导致零部件到总成没有统一的制作和检验标准,造成车身 质量不稳定,调试周期会延长;测量点方面:如果产品不指定测量点要求,检具设计 就会失去依据,过多的测量点造成成本增加,测量点不一致,会无法找到问题真因, 车身品质提升困难;公差方面:世界上没有理想的零部件,每个零部件都存在偏差, 车身零部件更是如此,在车身质量控制过程中,要进行检查,那么合理的公差就是判
0。5
水箱架总成 0。5
前防撞梁
前纵梁
3. 零部件品质基准审查标准
编号 QS-GD&T-003 简图 主题 特殊公差要求 说明 零部件品质基准书中,影响焊接装配的 搭接部位,影响全车尺寸(长、宽、 高)的相关搭接部位要设定特殊公差 例2:为防止因下前围板翻边反弹导致前 围上部安装不到位,进而影响车身高 度,给前围板翻边0.5mm的负公差
DTS、GD&T图纸审查标准
工程院SE技术部 田学强 2011.03.30
每天进步一点点
◈ 目录
1. 前言 2. 外观品质基准审查标准 3. 零部件品质基准审查标准 3-1. 定位点(RPS)审查标准 3-1-1. 定位孔审查标准 3-1-2. 定位面审查标准 3-2. 测量点审查 3-3. 公差设定审查
编号 QS-LC-005 简图 主题 定位孔和钣金件间隙要求 说明 如果不能在钣金件上为定位孔设立出一 个间隙孔,按照以下方式审核: a:钣金件和定位孔之间距离 d:定位孔直径 一般:a≥4+1/2*D*tan(30°) 特殊:a≥4+1/2*D*tan(45°)
A
a
d
A
3. 零部件品质基准审查标准
断车身是否合格的标准和依据,公差设定如果不合理,要求太松将无法满足车身品质
要求,要求太严会增加制造成本,进而延长产品开发周期。 基于以上原因,结合以往车型开发经验,特制作本审查标准,用于产品设计阶段, 对产品设计输入进行有效的工艺性审查并提出ECR,以保证过程开发顺利进行。 本标准适用于工程院对DTS、GD&T的审查。
3. 零部件品质基准审查标准
编号 QS-GD&T-006
简图
主题
特殊公差要求
说明 零部件品质基准书中,影响焊接装配的 搭接部位,影响全车尺寸(长、宽、 高)的相关搭接部位要设定特殊公差 例5:为防止因车门自重(包括门芯板、 玻璃等)导致车门下沉,进而影响车门 间隙,在车门安装时给车门铰链安装孔 及关联过孔设定0.5mm负公差
简图
主题
一般公差要求
说明 除以上特殊要求(面差)外,一般间 隙面差公差控制在±1.0范围内
2. 外观品质基准审查标准
编号 QS-BIW-009
简图
主题
其他要求-间隙平行度
说明 为了保证车身装配的对称性,对间隙 设置增加平行度要求,公差控制在±1. 0范围内
2. 外观品质基准审查标准
编号 QS-BIW-010
编号 QS-LC-006 简图 主题 定位面要求 说明