钒铁的生产
氮化钒铁生产工艺

氮化钒铁生产工艺
氮化钒铁是一种重要的合金材料,广泛应用于钢铁、航空航天、电子
等领域。
其生产工艺主要包括原料配比、炉型选择、炉温控制等方面。
下面将详细介绍氮化钒铁的生产工艺。
一、原料配比
氮化钒铁的主要原料是钒铁和氨气。
钒铁的品质对氮化钒铁的生产质
量有着重要的影响。
一般来说,钒铁的钒含量越高,氮化钒铁的氮含
量就越高。
同时,钒铁的硫含量也会影响氮化钒铁的质量,硫含量过
高会导致氮化钒铁的氮含量下降。
因此,在原料配比时,需要根据生
产要求选择合适的钒铁品质,并控制硫含量在一定范围内。
二、炉型选择
氮化钒铁的生产炉型主要有电炉和高炉两种。
电炉生产氮化钒铁的优
点是生产周期短,能够快速调整生产工艺,适应市场需求的变化。
而
高炉生产氮化钒铁的优点是生产成本低,能够大规模生产,适合长期
稳定的生产。
因此,在选择炉型时,需要根据生产需求和市场情况进
行综合考虑。
三、炉温控制
炉温控制是氮化钒铁生产中的关键环节。
炉温过高会导致氮化钒铁的氮含量下降,炉温过低则会导致氮化钒铁的产量下降。
因此,在生产过程中,需要根据原料配比和炉型选择合适的炉温,并进行精确的控制。
同时,还需要根据生产情况和市场需求进行调整,以保证生产质量和产量的稳定。
综上所述,氮化钒铁的生产工艺主要包括原料配比、炉型选择和炉温控制等方面。
在生产过程中,需要根据生产要求和市场需求进行综合考虑,以保证生产质量和产量的稳定。
钒铁冶炼工艺流程
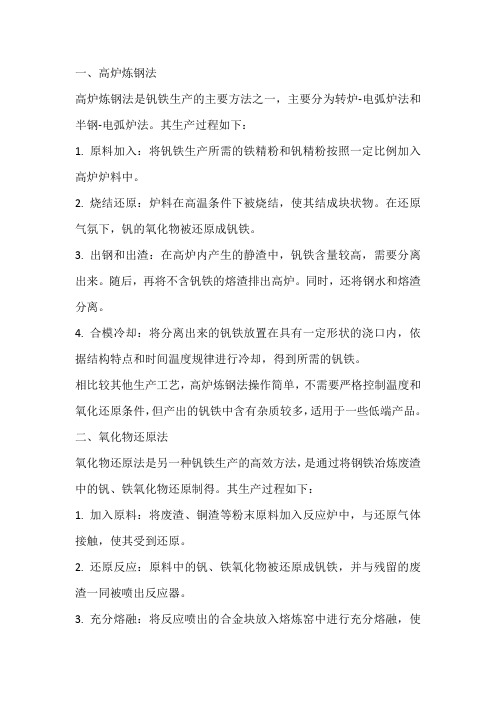
一、高炉炼钢法
高炉炼钢法是钒铁生产的主要方法之一,主要分为转炉-电弧炉法和半钢-电弧炉法。
其生产过程如下:
1. 原料加入:将钒铁生产所需的铁精粉和钒精粉按照一定比例加入高炉炉料中。
2. 烧结还原:炉料在高温条件下被烧结,使其结成块状物。
在还原气氛下,钒的氧化物被还原成钒铁。
3. 出钢和出渣:在高炉内产生的静渣中,钒铁含量较高,需要分离出来。
随后,再将不含钒铁的熔渣排出高炉。
同时,还将钢水和熔渣分离。
4. 合模冷却:将分离出来的钒铁放置在具有一定形状的浇口内,依据结构特点和时间温度规律进行冷却,得到所需的钒铁。
相比较其他生产工艺,高炉炼钢法操作简单,不需要严格控制温度和氧化还原条件,但产出的钒铁中含有杂质较多,适用于一些低端产品。
二、氧化物还原法
氧化物还原法是另一种钒铁生产的高效方法,是通过将钢铁冶炼废渣中的钒、铁氧化物还原制得。
其生产过程如下:
1. 加入原料:将废渣、铜渣等粉末原料加入反应炉中,与还原气体接触,使其受到还原。
2. 还原反应:原料中的钒、铁氧化物被还原成钒铁,并与残留的废渣一同被喷出反应器。
3. 充分熔融:将反应喷出的合金块放入熔炼窑中进行充分熔融,使
其混合均匀。
4. 浇注冷却:将熔化的钒铁灌入特制结型器中,并冷却定型。
相比较高炉炼钢法,氧化物还原法产出的钒铁纯度高、含有杂质少,适用于高端产品。
总结:钒铁的生产工艺包括高炉炼钢法和氧化物还原法,前者操作简单但产出的钒铁含有杂质较多,后者产出的钒铁纯度高,但操作复杂。
选择工艺需要根据需求来定。
钒的选矿方法和步骤

钒的选矿方法和步骤:钒铁生产的主要原料是钒钛磁铁矿,经选矿富集后,通过高炉炼出含钒生铁,在雾化炉或转炉吹炼过程中提取钒渣。
钒渣经粉碎后配加钠盐(纯碱、食盐或无水芒硝)进行氧化钠化焙烧,使钒成为可溶的偏钒酸钠(NaVO3),浸取净化后加硫酸铵沉淀出多钒酸铵[(NH4)2V6O16],再经脱氨熔化,铸成片状五氧化二钒。
要求成分为V2O597~99%,P<0.05%,S<0.05%,Na2O+K2O <1.5%。
此外也从含钒铁精矿或含钒炭质页岩直接通过化学处理提取五氧化二钒。
电硅热法片状五氧化二钒用75%硅铁和少量铝作还原剂,在碱性电弧炉中,经还原、精炼两个阶段炼得合格产品。
还原期将一炉的全部还原剂与占总量60~70%的片状五氧化二钒装入电炉,在高氧化钙炉渣下,进行硅热还原。
当渣中V2O5小于0.35%时,放出炉渣(称为贫渣,可弃去或作建筑材料用),转入精炼期。
此时,再加入片状五氧化二钒和石灰,以脱除合金液中过剩的硅、铝等,俟合金成分达到要求,即可出渣出铁合金。
精炼后期放出的炉渣称为富渣(含V2O5达8~12%),在下一炉开始加料时,返回利用。
合金液一般铸成圆柱形锭,经冷却、脱模、破碎和清渣后即为成品。
此法一般用于含钒40~60%的钒铁冶炼。
钒的回收率可达98%。
炼制每吨钒铁耗电1600千瓦?时左右。
铝热法用铝作还原剂,在碱性炉衬的炉筒中,采用下部点火法冶炼。
先把小部分混合炉料装入反应器中,即行点火。
反应开始后再陆续投加其余炉料。
通常用于冶炼高钒铁(含钒60~80%),回收率较电硅热法略低,约90~95%钒和钻常呈铁的类质同像分别赋存于钛磁铁矿和黄铁矿中。
此类矿石的选矿,一般是先用弱磁选分出钒铁精矿,再用重选、强磁选、浮选、电选联合方法从尾矿中回收钛铁矿和用浮选回收黄铁矿。
钒铁精矿所含的钛是选矿无法除去的,可以在冶炼中分离。
为了满足高钛渣炼铁必需的渣量,过分提高钒铁精矿的铁品位,有时是不合理的。
从磁选尾矿中回收钛的流程,首先要保证得到优质钛精矿。
钒铁冶炼原理

钒铁冶炼原理一、引言钒铁是一种重要的合金材料,广泛应用于钢铁制造、航空航天、电子等领域。
钒铁冶炼是将含有钒的矿石经过多道工序处理,最终得到纯度较高的钒铁合金的过程。
本文将详细介绍钒铁冶炼原理。
二、钒铁冶炼工艺流程1. 矿石选矿首先需要对含有钒的矿石进行选矿,去除其中不需要的杂质,得到较为纯净的原料。
2. 熔炼还原将选好的原料放入高温高压环境中进行还原反应,使得其中的氧化物被还原为金属元素。
此时产生了大量气体和灰渣,需要通过特殊设备进行处理。
3. 分离提纯经过还原反应后得到了含有钒和其他金属元素的合金液体,需要通过分离和提纯来得到纯度更高的钒铁合金。
通常采用多级分离和提纯工艺,包括重力分离、浮选分离、溶剂萃取等方法。
4. 铸造成型最后将得到的钒铁合金液体倒入模具中进行铸造成型,得到所需形状和尺寸的钒铁合金块。
三、钒铁冶炼原理1. 矿石还原反应钒铁冶炼的核心是还原反应。
在高温高压环境下,氧化性较强的矿物质会和还原剂(如焦炭、木炭等)发生反应,将其中的氧化物还原为金属元素。
以钒钛磁铁矿为例,其主要反应方程式为:FeTiO3 + 2C → Fe + TiC + 2CO此时产生了大量气体和灰渣,需要通过特殊设备进行处理。
2. 分离提纯经过还原反应后得到了含有钒和其他金属元素的合金液体。
此时需要通过分离和提纯来得到纯度更高的钒铁合金。
通常采用多级分离和提纯工艺,包括重力分离、浮选分离、溶剂萃取等方法。
3. 铸造成型最后将得到的钒铁合金液体倒入模具中进行铸造成型,得到所需形状和尺寸的钒铁合金块。
四、钒铁冶炼工艺的优缺点1. 优点(1)钒铁合金具有良好的耐腐蚀性、韧性和强度,广泛应用于钢铁制造、航空航天、电子等领域。
(2)钒铁冶炼工艺简单,成本较低。
(3)钒铁冶炼过程中产生的气体和灰渣可以得到有效处理,减少了对环境的污染。
2. 缺点(1)钒铁冶炼需要大量能源和原料,对环境造成了一定影响。
(2)分离提纯过程中需要采用多种化学药剂,可能对环境造成污染。
钒铁精矿直接提钒

钒铁精矿直接提钒钒铁精矿钠盐焙烧制取五氧化二钒的钒提取方法。
又称铁精矿水法提钒。
钒钛磁铁精矿经磨矿、磁选所得含钒铁精矿通常含V2O5O.5%~2%和全铁5O%~65%,可不经高炉炼铁和铁水吹钒渣而直接进行钠盐焙烧和水浸出提钒,提钒后的铁精矿再用作炼铁原料。
原理经细磨的钒铁精矿和钠化剂(碱、芒硝或元明粉Na2SO4)制成粒或造成球,在焙烧炉内进行氧化钠化焙烧,钒铁精矿中的钒便被氧化生成V2O5:用水浸出焙烧产物过程中,NaVO3进入溶液与大部分不溶产物分离,然后再从经净化处理过的含钒溶液中沉淀出钒的化合物。
工艺根据钠化焙烧所用的主体设备,钒铁精矿直接提钒又分为竖炉钠化焙烧、流态化床钠化焙烧、回转窑钠化焙烧和链算机回转窑钠化焙烧四种方法。
竖炉钠化焙烧提钒芬兰劳塔鲁基(Rautaruukki)钢铁公司所属的奥坦梅基(Otan mäki)钒厂和木斯特瓦拉(Mustavaara)钒厂均采用钒铁精矿加钠盐造球,竖炉钠化焙烧的提钒方法。
奥坦梅基钒厂所用的原料成分(质量分数ω/%)为:全Fe68.4,TiO23.2,V2O51.125,SiO2O.4,CaOO.O6,MgOO.24,A12O3O.5。
钒铁精矿磨至-O.O38mm粒级占85%,加入占料量2.2%~2.3%的芒硝(Na2SO4)或1.6%~1.8%Na2CO3,用混料圆筒(直径2.7m,长9m,倾角7。
)造球机制成直径13~16mm的球粒,入直径3~3.3m、高15m圆形竖炉中进行钠化焙烧。
焙烧产物在2O个浸出罐中浸出。
浸出罐用钢板焊成,外部保温,罐径2.5m、高12.5m、容积6Om3,可装钠化球8Ot。
浸出后的钠化球送高炉炼铁。
浸出液含钒2O~25g/L,在6个1Om3沉淀罐中加硫酸和硫酸铵在363K温度下沉淀出V2O5。
沉钒后尾液含钒O.O8g/L,经进一步处理后排放。
竖炉作业率9O%,热耗为每吨球团18~2OL重油,蒸汽消耗为每吨V2O56OOL,电耗为每吨V2O533OOkw•h,产品五氧化二钒纯度为99.5%,钒收率78%。
钒铁的生产方法简介课件

contents
目录
• 钒铁简介 • 钒铁的生产方法 • 不同生产方法的比较 • 钒铁生产的发展趋势 • 结论
01
钒铁简 介
钒铁的性质
密度大
01
硬度高
02
热稳定性好
03
钒铁的应用
01
02
钢铁添加剂
化学工业
03 其他领域
钒铁的生产意义
满足市场需求
随着钢铁和化学工业的发展,市场对钒铁的需求量不断增加,因 此生产钒铁对于满足市场需求具有重要意义。
金属铁的方法。
在碳热还原法中,铁矿石和碳在 高温下反应,生成金属铁和一氧
化碳气体。
碳热还原法具有工艺成熟、能耗 低、原料来源广泛等优点,但需 要控制一氧化碳排放和粉尘污染。
03
不同生产方法的比较
生产效率的比较
熔融还原法
直接还原法
碳热还原法
能源消耗的比 较
01
熔融还原法
熔融还原法的能源消耗较高,需 要大量的热量来维持冶炼过程的 进行。
金属还原法
金属热还原法是一种利用金属或 其化合物与铁矿石进行高温还原
反应的方法。
在金属热还原法中,选用一种金 属或其化合物作为还原剂,与铁 矿石在高温下反应,生成金属铁
和相应的氧化物。
金属热还原法具有工艺简单、产 品纯度高、能耗低等优点,但需 要大量的金属或化合物作为还原
剂。
碳热还原法
碳热还原法是一种利用碳作为还 原剂,将铁矿石在高温下还原成
降低能源消耗的途径
节能技术应用 余热回收利用 能耗管理
环境保护的措施
废弃物处理 清洁生产 资源循环利用
05
结论
钒铁生产的意义和价值
钒铁的生产方法简介

(2)炉料分配 电硅热法冶炼钒铁有两个过程:还原过程和精炼过程。 还原过程可分为二阶段(三期冶炼法)和三个阶段(四期冶炼
法)。对三期和四期冶炼各阶段炉料分配见表。
炉料
V2O5 硅铁 铝块 石灰 钢屑
表 三期冶炼各期炉料分配/%
本次课内容回顾提要
第四章 钒材料
第十六节 钒铁的生产方法简介 第十七节 硅热法冶炼钒铁的基本原理 第十八节 硅热法冶炼钒铁的生产工艺与设备 第十九节 铝热法冶炼钒铁的基本原理 第二十节 铝热法生产钒铁的工艺流程与设备 第二十一节 碳还原法简介 第二十二节 钒渣直接冶炼钒铁简介 第二十三节 钒铁的质量标准 第二十四节 钒铝合金生产简介 第二十五节 钒铝合金生产原理 第二十六节 钒铝合金生产工艺
2)含钒量高 补加钢屑量=
需降V(%)炉中合金量 降后合金含钒数
(2)合金含硅不正常
由于配料不准及反应不正常造成。
1)硅低
补加硅铁量=
需增Si%炉中合金量 硅铁Si%增后合金含硅
2)硅高
降S量 i %炉中合金 3量 64
• 补加V2O5=
140 V2O5纯度 %
补加石灰量=
降S量 i %炉中合金6量0 28
24~28 30~35 39~44 0
16~18 30~32 29~31 0
100 0
0
0
E、第一期冶炼 • (1)上一炉出完炉后,炉顶倾回,迅速扒出炉渣和炉坡
残存渣,用混合好的、有足够粘度的镁砂(卤水∶镁砖粉∶ 镁砂=1∶3∶5),针对炉衬损伤情况高温快补,不漏一铲, 且堵好出铁口。
(2)补完炉后炉底要垫上一定数量的精炼渣。
第五章 含钒铁水炼钢工艺及钢渣(钒渣)提钒

渣(钒渣)提钒
41
教学要求: 1、了解含钒铁水炼钢工艺及特点 2、理解钢渣提钒的方法及其工艺 3、掌握钒渣的主要用途及其提钒方法 重点:钒渣提钒方法 难点:钒渣提钒的工艺过程
一、普通铁水与含钒铁水冶炼的区别
在各钢铁企业中,由于入转炉的铁水条件和冶炼钢种不同,其 吹炼工艺也各有差异。 1、普通铁水炼钢工艺流程
留渣法操作适合于成渣困难的铁水条件,其脱磷率可达85%左 右,脱硫率可达40~50%左右。
注意:这种渣有一定氧化性(尤其是低碳钢的终渣),兑铁时会产 生爆炸性喷溅,不利于安全生产,但在兑铁前先加少量石灰稠化炉 渣,兑铁时细流慢兑,安全事故可完全避免。
⑵渣料配比 要造好炉渣,选择合适的渣料配比非常重要。加入炉内的渣料主
⑴造渣方法
造好渣是炼好钢的关键
攀钢目前采用的造渣方法是留渣操作法。
留渣法操作:是指将上一炉冶炼的终渣在出钢后留一部分或全部 在转炉内供下一炉冶炼时作部分初渣使用。
攀钢转炉多采用半钢冶炼,成渣困难,留渣操作不但加速了初 期渣的形成,而且较好的缓解了冶炼过程中温度不足的矛盾。
原因是:终渣一般具有较高的碱度和∑(FeO)含量,并且熔点不 高,本身还含有大量的物理热。将这种炉渣部分地或全部留在炉内, 可显著加速下一炉初期渣的成渣过程,提高吹炼前期的去磷和去硫 率,节省石灰用量和提高炉子的热效率。
2、用钒渣直接冶炼钒铁方法举例
⑴ 美 国 专 利 提 出 : 第 一 步 将 钒 渣 ( 含 V2O517.5~22.5% , SiO216.74~17.57%) 、 石 英 、 熔 剂 与 炭 在 电 弧 炉 内 冶 炼 出 钒 硅 合 金 (18.97%V,42.02%Si,32.16%Fe);第二步用氧化钒和钒渣精炼的钒 硅合金,降低硅得到钒铁合金。精炼可分一次精炼法和两次精炼法。
- 1、下载文档前请自行甄别文档内容的完整性,平台不提供额外的编辑、内容补充、找答案等附加服务。
- 2、"仅部分预览"的文档,不可在线预览部分如存在完整性等问题,可反馈申请退款(可完整预览的文档不适用该条件!)。
- 3、如文档侵犯您的权益,请联系客服反馈,我们会尽快为您处理(人工客服工作时间:9:00-18:30)。
1 钒铁概述
1.1简介
钒铁(Ferrovanadium alloy)通过还原而得到的铁和钒中间合金(铁钒二元合金),其钒含量不小于35.0%(重量),不大于85.0%(重量),常用的钒铁有含钒40%、60%和80%三种。
钒作为元素周期表中钒族元素中的一员,其原子数为23,原子量为50.942,熔点为1887度,沸点为3337度,纯钒呈现为闪亮的白色,质地坚硬,为体心立体机构。
大约80%的钒和铁一起作为钢里的合金元素。
含钒的钢很硬很坚实,但一般其钒含量少于1%。
四川攀枝花钒钛资源十分丰富,其中钒的储量占全国的62%,居世界第三位。
我国从1978年开始出口钒渣、V2O5、钒铁。
从此我国从钒进口国变为钒出口国。
1.2钒铁用途
钒铁是钢铁工业重要的合金添加剂。
钒可提高钢的强度、韧性、延展性和耐热性。
世界上消耗的钒约90%用于钢铁工业。
钒在普通低合金钢中主要是细化晶粒,增加钢的强度并抑制其时效作用;在合金结构钢中是细化晶粒,增加钢的强度和韧性,在弹昔钢中与铭或锰配合使用,增加钢的弹性极限,并改善其质量,在工具钢中王要细化钢的组织和晶粒,增加钢的回火稳定性,增强其二次硬化作用,提高其耐磨性,延长工具的使用寿命,在耐热钢和抗氢钢中,钒也起有益的作用,铸铁中加入的钒,由于形成碳化物而促进珠光体形成,使渗碳体稳定,石墨颗粒的形状细而均匀,细化基体的晶粒,因而使铸件的硬度、抗拉强度和耐磨强度提高。
表1 粒度要求表
1.4生产方法及特点
钒在地壳中的丰度为135×10-4%。
钒矿物有70多种,但单一的钒矿床很少(仅秘鲁的米纳拉格拉为单矿床。
已采完。
),都是与别的矿共生。
用作生产钒的原料有钒钦磁铁矿(含V0 .4%-1 .40),铀钒矿(合V2051.5%-2.05%),原油灰烬(合V20520%-40%),合钒磷铁(合V3%-6 %),废钒催化剂,生产氧化铝的残
渣等。
这些原料含钒低,都需要用湿法冶金的方法,首先从这些原料中提取五氧化二钒,然后再将五氧化二钒冶炼成钒铁及钒添加剂。
钒磁铁精矿是生产钒的主要原料,世界钒产量的90%是用这种原料生产的。
①以还原剂来区分:通常分为砧热法、铝热法、碳热法三种。
②以还原设备区分:在电炉中冶炼的合电炉法(包括碳热法、电硅热法和电铝热法)。
石用电炉加热,只依靠自身反应放热的方法称为铝热法(即炉外法)。
③以含钒原料不同区分:用五氧化二钒、三氧化二钒、钒滔原料冶炼钒铁的方法。
④根据热源不问可分为:碳热法、电热法、电硅热法、金属热法。
不同方法,特点不同,一种是耗电能大,工序复杂,但产品质量稳定,还原剂价格低。
另一种是耗铝量大,回收率低,合金品值高,不用电能。
2 电硅热法冶炼钒铁
2.1基本原理
片状五氧化二钒用75%硅铁和少量铝作还原剂,在碱性电弧炉中,经还原、精炼两个阶段炼得合格产品。
还原期将一炉的全部还原剂与占总量60~70%的片状五氧化二钒装入电炉,在高氧化钙炉渣下,进行硅热还原。
当渣中V2O5小于0.35%时,放出炉渣(称为贫渣,可弃去或作建筑材料用),转入精炼期。
此时,再加入片状五氧化二钒和石灰,以脱除合金液中过剩的硅、铝等,铁合金成分达到要求,即可出渣出铁合金。
精炼后期放出的炉渣称为富渣(含V2O5达8~12%),在下一炉开始加料时,返回利用。
合金液一般铸成圆柱形锭,经冷却、脱模、破碎和清渣后即为成品。
2.2特点
此法一般用于含钒40~60%的钒铁冶炼。
钒的回收率可达98%。
炼制每吨钒铁耗电1600千瓦·时左右。
2.3冶炼流程
冶炼操作分还原期和冶炼期两步,冶炼都是在电弧炉内进行。
用过量的钒铁还原上炉的精炼渣至炉渣中含V205低于0.35%,从炉内排出废渣开始精炼,再加入五氧化二钒和石灰等混合料精炼。
当合金中Si量小于2%时出炉,排出的精炼渣V20510%-15%,返回下炉使用。
(1)还原期:还原作业的第一步是先将钢屑、硅铁熔化,加入精炼期返回的精炼渣,再加入少量V205,熔炼后形成的渣称为贫渣,其V205含量小于0.35%,倒出贫渣,转入还原期第二步冶炼,加人铝粒,控制合金中的Si、V含量。
(2)精练期:目的在于脱硅,提高钒的含量,继续加入V205和石灰,使其与过量的硅一起转入渣中,提高合金中的钒含量,达到产品的要求。
(3)操作过程:首先,上一炉出完炉后,炉顶倾回,扒出炉渣和炉坡残存渣,用混合好且有足够粘度的镁砂,针对炉衬损伤情况高温快补,且堵好出铁口。
补充炉后炉底要垫上一定数量的精炼渣。
钢屑加入后,根据电极烧损情况落放或拆换电极,检查特系统,正常后给电。
此时用大电压,小电流,并且立即倒入上一炉以液态存在的精炼渣。
返完精炼渣后,加一期混合料。
根据电弧稳定情况增大电流至最大值。
一期混合料下完后,尽量将炉料推至三相电极中心区域。
当护料熔化到一定程度.可开始分批加入硅铁还原,同时调整炉渣碱度。
硅铁还原较充分后,碱度合适时加铝块还原,还原反应激烈,火焰较大时停电。
当炉渣中V205<0.35%时,可倒出贫渣,倒渣过程要用低电压,小电流。
倒渣后期要慢,
且用拉杆检查,防止铁水倒出。
贫渣倒完后用铁棍能取渣样送化验分析五氧化二饥含量。
其次、一期贫渣倒完后,用大点压给电加料,随着二期混合料的加入,电流逐渐给电最大位。
炉料基本熔化后开始加入硅铁还原,同时调整炉渣碱度,继续加硅铁还原,而后加铝贫化炉渣,出渣与一期相同。
最后精炼时,与二期给电加料相同。
按合金成分调整精炼期料量,先用大电压,大电流熔化炉料,炉料化渣后调整炉渣碱度。
炉渣碱度合适时,根据电弧长短及时改用小电压,大电流升温。
当炉渣与合金具有合适的温度和流动性时,搅拌,取合金样送化验分析V、Si、C、P、S成分,正常出炉。
出炉时先用小电压,小电流,从出渣口倒出精炼渣,并打开出铁口,停电出铁,再完成浇铸。
图2.3 电硅热法冶炼钒铁工艺流程图
3 电硅热法冶炼钒铁主要设备——三相电弧炉
3.1电弧炉简介
电弧炉,英文名称为electric arc furnace,是一种通过金属/非金属产生电弧过程中产生的高温来对矿石或金属等物质进行熔炼的工业炉,具有体积小、操作简单、灵活性大、温度受控、性能较强等诸多优点,起初仅用于冶炼合金钢,现还可用于碳素钢的生产,已在我们的生产生活中占据越来越重要的地位。
3.2三相电弧炉简介
三相电弧炉是一种以三相交流电为电源的电弧炉,其使用的电极一般为石墨电极或碳素电极,在电极与炉料之间产生电弧进而升高温度将矿石等熔化。
在有些三相电弧炉的炉底还装有电磁搅拌器,对炉料一直进行一个方向的搅拌进而提高电弧炉熔化炉料的效率;在某些超大型的电弧炉内还装有炉体回转机构,可将炉体进行一定角度的旋转,使得炉料受热更加均匀。
3.3三相电弧炉结构及其原理
电弧炉主要由电极夹持器、电极、炉盖、熔池、炉门、倾动摇架、液压钢等部件构成,如下图所示,其炉底、炉壁使用的是酸性或碱性耐火材料构建的,首先通过电极向炉内输送电能,然后电极与炉料发生作用产生电弧来升高炉内温度,最后高温使得矿石金属等被融化。
图3.3 三相电弧炉结构示意图。