低钒铁水提钒炼钢工艺分析
提钒的工艺原理及应用视频

提钒的工艺原理及应用视频一、工艺原理1. 提钒的定义提钒是一种金属加工工艺,通过在金属表面施加高压力,使金属发生塑性变形,从而改善材料的性能和加工工艺。
2. 提钒的原理提钒的原理是利用外力 (机械、液压等) 施加在金属表面上,使其产生压力。
这种压力可以改变金属的结构,优化材料的力学性能,例如提高硬度、强度和耐磨性。
3. 提钒的过程提钒的过程可以分为以下几个步骤:•金属表面处理:确保金属表面清洁,并去除表面的氧化物和污染物。
•设定提钒参数:根据不同金属的硬度和形状,设定合适的提钒参数,例如压力和提钒速度。
•施加外力:通过机械、液压等方式,施加高压力在金属表面,使其发生塑性变形。
•冷却和固化:在提钒过程中,通过冷却和固化,使金属恢复到所需的形状和力学性能。
•检测和评估:对提钒后的金属进行检测和评估,确保产品达到质量要求。
二、提钒的应用视频1. 提钒在汽车制造中的应用•提钒可以用于汽车车身板材的加工,增强板材的强度和耐压性能,提高汽车的安全性能。
•提钒还可以应用于汽车发动机的零部件制造,例如气缸盖和曲轴等,提高零部件的耐磨性和耐压力。
2. 提钒在航空航天领域的应用•在航空航天领域,提钒可以应用于飞机和航天器的结构件制造,提高结构件的强度和耐腐蚀性能,提升整个飞行器的性能。
•提钒还可以应用于航天器的发动机制造,增强发动机零部件的耐高温和耐压力能力。
3. 提钒在工程机械制造中的应用•工程机械制造中,提钒可以用于制造挖掘机、推土机等大型机械零部件,提高零部件的强度和耐磨性能,提升机械的工作效率和使用寿命。
•提钒还可以应用于工程机械的钻杆、钻头等零部件制造,提高钻杆的强度和耐磨性,提升钻探效果。
三、总结提钒作为一种金属加工工艺,在汽车制造、航空航天和工程机械制造等领域有着广泛的应用。
通过施加高压力,金属表面发生塑性变形,可以改善材料的性能和加工工艺。
在提钒过程中,需要注意金属表面处理、提钒参数设定、冷却和固化等关键步骤,以确保产品达到质量要求。
提钒炼钢剖析

过小反应速度慢。 供氧压力大可加强熔池搅拌强化动力学条件,有利于提高钒元素
氧化速度。 喷枪的结构包括喷嘴直径、孔数、角度等参数,这些条件直接影
响氧气的冲击深度、分布和利用率的高低。
在实际生产中,要使用专用氧枪喷头,采用小的氧流量、氧压控 制,低→高→低的枪位运行,保证化渣良好。
4
川威钒钛冶金科技开发有限公司
1.3 工艺流程
钒钛磁铁矿
冷却剂、供氧
↓ 含钒铁水
↓
高炉铁水———→铁水预处理→转炉提钒→钒渣
↓
↓
高炉渣
半钢→转炉炼钢
5
川威钒钛冶金科技开发有限公司
1.4 影响提钒的四大主要因素
A、铁水成分的影响
铁水中硅、钛含量增加,会降低钒渣中V2O5的浓度; 铁水中原始钒含量高得到的钒渣V2O5品位提高。
川威钒钛冶金科技开发有限公司
第二部分
提钒炼钢和普通铁水炼钢的差异
10
川威钒钛冶金科技开发Байду номын сангаас限公司
2.1、概念
提钒炼钢:一方面是将含钒铁水在提钒转炉中的钒元素提取出来, 另外方面将提钒后的半钢水通过脱碳转炉冶炼成钢水。
普通炼钢:就是通过转炉将高炉铁水冶炼成钢水。
川威钒钛冶金科技开发有限公司
2.2、工艺流程对比
对冷却剂除了要求具有冷却能力外,还要有氧化能力,带入的杂 质少。
冷却剂尽量在吹炼前期加入,吹炼后期不再加入任何冷却剂,使 熔池温度接近或稍超过转化温度,适当发展碳燃,有利于降低钒渣中 氧化铁含量,提高半钢温度和金属收得率。
川威钒钛冶金科技开发有限公司
D、供氧制度的影响 供氧制度包括氧枪枪位、结构、耗氧量、供氧强度、压力等诸多
含钒铁水转炉提钒渣冶炼方案(初稿)

含钒铁水转炉提钒渣冶炼方案目录1.钒相关基础知识 (4)1.1钒元素的发现与发展 (4)1.2国内钒的发展 (5)1.3钒的矿物简介 (6)1.4钒及其化合物的性质 (6)1.4.1金属钒的性质 (6)1.4.2金属钒的制备: (7)1.4.3钒的主要氧化物 (7)1.4.4含钒化合物的理化性能 (8)1.5钒在钢铁上的应用 (9)1.6钒的生产方法 (10)2.转炉提钒基本原理 (11)2.1转炉提钒的意义 (11)2.2转炉提钒的原理 (12)2.3铁质初渣与金属熔体间的氧化反应 (12)2.4转炉提钒脱钒、脱碳规律 (12)2.5铁水中钒与碳氧化的转化温度 (13)2.6影响转炉提钒的主要因素 (15)2.6.1铁水成分的影响 (15)2.6.2 铁水中钒的影响 (15)2.6.3.铁水硅的影响 (15)2.6.4.吹炼终点温度对钒渣中全铁含量影响 (16)2.6.5.供氧制度的影响 (17)3.提取钒渣方法 (17)3.1顶底复吹转炉提钒 (17)3.2转炉单联法提钒 (18)3.3攀钢转炉提钒工艺 (20)3.3.1转炉提钒工艺流程图 (20)3.3.2攀钢转炉提钒工艺过程 (20)3.3.3攀钢转炉提钒主要设备参数 (21)3.3.4攀钢转炉提钒用原材料 (21)3.3.5 不同氧枪的提钒效果 (22)3.3.6攀钢转炉提钒冷却制度 (23)3.3.7攀钢转炉提钒终点控制 (24)3.3.8出半钢和倒钒渣 (24)3.3.9攀钢提钒钒渣 (25)4.八钢炼钢提钒渣方案 .......................................................................... 错误!未定义书签。
1.钒相关基础知识1.1钒元素的发现与发展钒(V),呈银灰色,原子序数为23,原子量为50.942,在元素周期表中属VB族,具有体心立方晶格。
1801年,墨西哥矿物学家德尔·里奥在研究铅矿时,发现一种化学性质与铬、铀相似的新元素,其盐类在酸中加热时呈红色,故名为红色素。
提钒与转炉炼钢工艺

项目一 含钒铁水提钒
氧气顶吹转 炉吹炼提钒
观看提钒视频资 料录像1-1
项目目标
总体 :在已知原材料和工艺设备条件下编制一炉
铁水提钒的操作规程和完成一炉铁水提钒的吹炼
? 具体:熟悉钒钛资源、钒的用途、钒的性质及提取
钒方法的特点 ? 熟练掌握氧气顶吹转炉提取钒的任务、原理;氧气
顶吹转炉提取钒的主要原料种类及对其要求要点氧 气顶吹转炉吹炼一炉含钒铁水提取钒包括的项目及 参数控制、调节的方法 ? 了解氧气顶吹转炉吹炼提取钒所涉及到的主要种类、 作用及结构特点
3
12.0
4
10.0
化 学 成 分, %
SiO2
CaO
P
Ⅰ
Ⅱ
≯
27
0.8
0.08
0.8
28
1.0
0.10
0.8
29
1.0
0.10
0.8
31
1.0
0.10
0.8
1-4-1-2氧气顶吹转炉吹炼提取钒原理 工程实例
? 已知攀钢典型铁水成分:w[C]=4.0%,w[Si] =0.20%,w[V]=0.32%,w[Ti]=0.25%, 通过物理化学手册查出一些数据计算出 lg fv=-0.587,lg fc=0.865,求实际转化温 度T=?
本项目中的学习型工作任务
? 在获得优质、高产、低耗、长寿的技术经济指标 理念下,依据已知原材料性质及工艺设备,以完 成一炉铁水提钒得到合格产品的工作任务岗位技 能为总体目标,设置为一个综合性项目
? 以职业能力培养为主线,将一炉铁水提钒相对应 的主要知识点设置为若干个单元,每一单元的主 要知识点同最终目的(总的工作任务)联系起来
低钒铁水提钒炼钢工艺分析

氧化转化临界温度为 131317e 。可见, 提钒的终点
半钢温度不宜过高。提钒过程前期以钒氧化为主,
后期以钒还原为主, 吹钒反应可表示为:
k1
))) y
[V ]
(V )
( 1)
z )))
k2
式中 k1) ) ) 钒正向反应常数; k2) ) ) 钒逆向反应常数。
吹钒反应速率可表示为:
(
-
d
[ V] dt
半钢碳含量平均 314% , 范围 2194% ~ 4102% , 分布见图 2。根据图 2, 半钢 [ C] \312% 者占 85% 。 说明保碳操作较为合理。
图 2 半钢碳含量分布
4. 2 半钢温度 由于铁水到转炉后无铁水成份, 只能根据上一
炉的温度情况确定生铁块量, 并且是先进铁水再测 温, 生铁块的重量已无法改变, 只能用铁皮球来调整 温度。因铁水 [ Si] 存在一定的波动, 再加上温度控 制水平参差不齐, 半钢温度控制存在一定的波动, 总 体上控制较好, 平均 1373e , 范围 1331~ 1418e , 其 分布见图 3。根据图 3, 半钢温度控制在试生产要求 的 1340~ 1400e 者占 82% 。
7远程监控功能实现远程对高炉上料计量数据的监控管理功结束语在高炉上料计量自动计量管理系统设计中使用数据自动采集数据自动处理数据库网络通讯等多项技术使整个系统实时高效运行系统完成后将公司的计量管理提升到了一个新的高度为炼铁厂成本核算提供基础数据为分厂生产经营提供坚实决策依据同时为今后公司的erp系统提供了真实准确有效及时的基础数据
半钢温度与 [ V ]半的对应值
1250
1300
0. 180
0. 075
1350 0. 042
提钒与炼钢工艺

氧气 转炉 炼钢 技术
转炉 大型 化时 期
转炉 复合 吹炼 时期
转炉 综合 优化 时期
0.3 现代钢铁生产工艺流程
钢铁材料的冶炼工艺流程图定义:钢铁材料的生产不是
一步可以完成的,分为若干个阶段。各阶段过程间的联系及 其所获得的产品(包括中间产物)间流动线路图就称为钢铁 材料的冶炼工艺流程图。
0.3.1 钢铁联合企业的生产工艺流程 如图0-4所 示 0.3.2 长流程 以氧气转炉炼钢工艺为中心的钢铁联合企
粗钢产量达到 4.188亿t
2004 年产钢量为1.82亿 t 2003 2003
钢产量达到2.74亿t
钢产量首次突破2 亿t,达到2.234亿t
中国钢铁工业的发展战略
重在增加高附加值的产品,提高质量
重在提高产业集中度
三 个 重 在
钢铁大国向钢铁强 国的的根本转变
重在降低消耗
三个重在,一个根本转变
坚硬韧性大,塑性 好
其它元素
机械性能
可铸、不可锻
可铸、可锻、可压 延
钢系由生铁再炼而行,有较高的机械强度和韧性,还具有 耐热、耐腐蚀、耐磨等特殊性能。
炼钢的任务 铁水
炼钢过程
• • •
炼钢过程
脱碳 脱硫 脱硅
•
脱磷 合金化
•
钢
为什么要提钒
• 资源:铁矿、钒钛磁铁矿 • 钒钛磁铁矿的冶炼:主要是用回转窑-电 炉或高炉,冶炼出含钒铁水(含钒为 0.25~0.35%)。含钒铁水进行转炉提钒, 得到钒渣和半钢。钒渣进一步加工成钒制 品,半钢再去炼钢。出勤率、作业来自 课堂表现理论考核试题库
考核评价
实践环节考核——标准参照 考试 学生按照工作任务要求(评价标 准),完成任务,每个任务项目均有 详尽的考核标准,实行操作技能细化 要求
第五章含钒铁水炼钢工艺及钢渣钒渣提钒ppt课件

V2O5-Na2CO3相图
(二)用钒渣生产V2O5工艺 钒渣生产V2O5的工艺流程:主要有原料预处理、氧化焙烧、
熟料浸出、沉钒及熔化五个工序。
1、原料预处理 定义:就是将钒渣破碎到一定粒度后再与一定比例的钠盐添
加剂混合均匀的过程。包括钒渣破碎、球磨、除铁、配料(配入 添加剂)、混料等。
⑴ 原料预处理的工艺 ① 钒渣的破碎
⑶渣料加入时间和炉渣的控制 攀钢渣料一般分两批加入,第一批占总渣料的60%以上,其余在第二批
分小批加入。如拉碳后需调整炉渣或炉温,则再加入第三批渣料。 ①渣料加入时间
第一批渣料在兑铁前或开吹时加入,包括石灰、镁质材料和酸性材料。 第二批渣料在第一批渣料化好、化透后分小批量多次加入(每次不超过 0.5吨),这样有利于石灰熔化,避免炉渣“返干”,同时还可以较好控制 炉内泡沫渣,防止喷溅和溢渣,在吹炼终点前3~5min全部加完。 第三批渣料是否加入,根据拉碳后硫、磷去除情况而定。 注意:无论加几批渣料或加多少渣料,都必须保证终点炉渣化好,确 保渣料的有效利用。
产生的磷氧化物放出,在还原期加入钒渣、碎焦和粉状硅铁, 钒氧化物由碳和硅还原,最终脱氧由硅钙合金和铝进行,这 种方法会造成还原期钢渣碱度降低(还原后渣中SiO2增加)和 氧化性(因为钒渣中氧化铁高)提高,钢中金属夹杂物增加。
②在盛钢桶中加入混合物——此方法最好 在出钢时将钒渣和还原剂组成的混合物(钒渣粉+硅铁粉 或铝粉制成块)倒入盛钢桶,可避免钢脱氧时造成烧损。混 合物之间的相互作用就可达到合金化的目的。 钢水使钒氧化物发生热还原反应,还原出的钒进入钢水 中,钒还原率可达60~80%。 攀 钢 用 钒 渣 +FeSi75+ 萤 石 粉 制 成 混 合 物 , 比 例 100:30:5,加水玻璃作粘结剂,压制成块,干燥后使用。生 产出了09V、22MnSiV、16MnSiVN等钢种。
含钒铁水提钒

含钒铁水提钒含钒铁水提钒是一种常用的钒资源提取方式。
随着钒资源的重要性越来越被人们所重视,含钒铁水提钒的技术也逐渐受到人们的关注和研究。
下面将分步骤阐述含钒铁水提钒的过程。
第一步:采集含钒铁水含钒铁水是指含有钒的铁合金,主要产自炼钢、铸铁生产中的铁水。
在钢铁冶炼过程中,当钒元素的加入量达到一定比例时,钒就会部分溶解到铁水中,形成含钒铁水。
所以,采集含钒铁水是提取钒的第一步。
第二步:滴定测定含钒铁水中钒含量由于含钒铁水中钒的含量很低,一般在百分之一以下,因此需要进行测定。
滴定法是一种比较常用的方法,通过滴定剂加入含钒铁水中,再利用反应的化学变化计算出钒的含量。
第三步:加入氧化剂使铁水中钒转化为V2O5由于含钒铁水中钒含量较低,不能够直接回收利用。
因此需要将铁水中的钒转化为V2O5,以便进行钒资源的提取。
这个步骤的关键是加入适当的氧化剂,使钒被氧化为V2O5。
常用的氧化剂有氯硫酸等。
第四步:溶解V2O5,获得钒溶液经过氧化处理后的含钒铁水会生成V2O5,可通过浸出法或者锅炉法将其溶解,获得钒溶液。
此时的钒溶液中含有较高浓度的钒,可以用于制备钒化合物,或用于钒电池、钒催化剂等领域。
第五步:沉淀、干燥、热处理为了得到纯度较高的钒化合物,需要对钒溶液进行沉淀、干燥和热处理。
通过这三个步骤能将杂质去除,获得纯度较高的钒化合物。
这个过程需要根据制备不同的钒化合物来进行精细化的控制。
以上便是含钒铁水提钒的主要步骤。
虽然这种技术在一定程度上可以提高钒的回收利用率,但其还有一些缺陷,例如生产成本高、工艺流程复杂等,这些问题需要在后续的技术研究中得到解决。
铁水[Si]含量对提钒工序影响
![铁水[Si]含量对提钒工序影响](https://img.taocdn.com/s3/m/37ad1d8050e79b89680203d8ce2f0066f53364a5.png)
铁水 [Si]含量对提钒工序影响摘要:以120t提钒转炉为研究基础,通过理论分析、结合生产实际,研究铁水[Si]含量对提钒工序的影响,通过研究得知,铁水中的[Si]含量较高时,提钒吹炼终点温度提高,半钢残钒增加,另由于铁水[Si]含量升高,钒渣中的SiO2含量升高,钒渣流动性增加,提钒转炉出钢过程中钒渣下渣流失量增加,可捞渣回收部分钒渣。
铁水[Si]含量极低时,无冷料配吃条件,吹炼反应不完全,氧化率降低半钢残钒升高,可合理补硅,满足提钒吹炼条件。
关键词:提钒铁水[Si] 半钢残钒下渣流失转炉提钒的基本原理为选择性氧化,即通过控制适宜的热力学及动力学条件使得铁水中[V]最大限度地氧化进入钒渣,同时,抑制熔池中的碳氧反应,控制铁水中[C]尽量不被氧化,以保证半钢的化学热。
此外,为提高钒渣中氧化钒含量并降低铁的损耗,要求钒渣中(FeO)含量尽可能降至最低。
热力学条件好,有利于在较低温度、较低氧势条件下实现“提钒保碳”;动力学条件好,有利于提高钒氧化反应的扩散传质速率,促进钒的氧化,缩短吹炼时间,提高钒渣品位。
2021年承德建龙高炉受原料及炉况运行情况影响,铁水[Si]含量在0.01%-0.72%之间波动,铁水[Si]含量波动较大,不易于稳定提钒操作,且[Si]含量过低过高时,吹炼终点温度不能依靠配吃冷料进行有效控制,半钢残钒升高,钒渣渣态较稀,提钒工序钒损失增加。
一、铁水[Si]含量对提钒工序吹炼指标影响吹钒过程中,铁水中Fe、V、C、Si、Mn、Ti、P等元素的氧化速度取决于铁水中该元素的含量、吹钒时的热力学条件和动力学条件,而反应能力的大小又取决于铁水组分与氧的化学亲和力——标准生成自由能ΔGθ。
图1铁水中元素氧化的标准生成自由焓变在转炉提钒吹炼过程中,根据铁水中元素与样的亲和能力大小不同,进行选择性氧化。
如图1所示,铁水中Ti、Si优先氧化,而后钒、铬氧化。
随着温度的升高,铁水中金属元素与碳元素的氧化顺序发生变化,即铁水中元素氧化转化温度发生变化。
提钒与炼钢工艺

车间,改建成3座30t的氧气顶吹转炉炼钢车间, • 我国原有的一些空气侧吹转炉车间逐渐改建成中
小型氧气顶吹转炉炼钢车间
主页
上一页
下一页
后退
退出
转炉炼钢技术的发展趋势
• 合理优化工艺流程,形成紧凑式连续化的 专业生产线
19世纪中期至今天,以 生铁为原料,在高温下 精炼成钢,一直是钢铁 生产的主要方法。高炉 鼓风由热风代替冷风, 并建立了蓄热式热风炉, 鼓风动力采用电力,确 定了作为生铁精炼炉的 平炉、转炉、电炉的炼
钢法。
海绵铁
液态生铁
钢铁分为二步冶炼法
主页
上一页
下一页
后退
退出
现代钢铁生产工艺流程
• 钢铁联合企业的生产工艺流程
提钒与炼钢工艺
主页
上一页
下一页
后退
退出
课程性质 课程目标 课程体系
教学内容 考核评价 学习方法
主页
上一页
下一页
后退
退出
• 这是什么? • 它有什么用? • 它是用什么材料制成
的?
关键点:钢铁制成 的!
主页
上一页
下一页
后退
退出
钢与铁的区别
铁合金
生铁
钢
成分
含碳量 其它元素
机械性能
主页
上一页
下一页
后退
退出
各种精炼炉的炼钢效率 1- 碱性转炉炼钢法,2- 纯氧顶 吹转炉炼钢法;3- 氧气侧吹转炉 炼钢法,4- 平炉(氧气使用量 10~40Nm3/t), 5- 电炉,6平炉
主页
与平炉、电炉炼钢 法相比,氧气转炉 炼钢法具有生产率 高、钢中气体含量 低、钢的质量好等 特点。
提钒与转炼钢工艺

提钒与转炼钢工艺概述提钒与转炼钢工艺是一种用于加工和精炼钢材的工艺流程。
通过提钒工艺,钢材的含碳量得以提高,从而提高钢材的硬度和强度。
而转炼钢工艺则用于进一步减少钢材中的杂质,并调整钢材的成分和结构,以满足具体的要求。
本文将介绍提钒和转炼钢的基本概念和原理,以及相关的工艺流程和操作。
提钒工艺提钒原理提钒是指通过向钢材中添加合适的元素,使钢材中的碳含量提高,从而提高钢材的硬度和强度。
提钒过程中会有一个合适的温度范围,同时需要在氧化气氛中进行。
常用的提钒元素包括铬、钛、钒等。
提钒工艺流程提钒工艺的基本流程如下:1.准备工作:选择合适的钢材和提钒元素,准备好所需的设备和工具。
2.加热:将钢材加热至合适的温度范围,通常在800℃到1000℃之间。
加热时需要控制好加热速度和温度均匀性。
3.添加提钒元素:在加热过程中,将提钒元素逐渐添加到钢材中。
添加提钒元素的方式有多种,可以是粉末、块状或液体等。
4.搅拌和保温:在添加完提钒元素后,需要搅拌钢材以保证提钒元素均匀分布,并保持一定的保温时间,使提钒元素与钢材充分反应。
5.冷却:将经过提钒处理的钢材冷却至室温。
转炼钢工艺转炼钢原理转炼钢是指通过炼钢过程中的一系列操作,来进一步减少钢材中的杂质,并调整钢材的成分和结构。
转炼钢工艺可以改善钢材的力学性能和物理性能,提高钢材的质量和使用价值。
转炼钢工艺流程转炼钢工艺的基本流程如下:1.准备工作:选择合适的钢材和转炼剂,准备好所需的设备和工具。
2.预处理:将钢材进行预处理,去除表面的铁锈和杂质等。
3.熔融:将钢材加热至熔点以上,使其成为液体状态。
在熔融过程中,可以添加一定比例的转炼剂,如石灰石、脱硫剂等。
4.搅拌和保温:在熔融过程中,需要搅拌钢液以均匀混合转炼剂,并保持一定的保温时间,使转炼剂与钢液充分反应。
5.去除杂质:通过逐渐加大的磁场或引入气体等方式,将钢液中的杂质和气泡等逐渐移除。
6.过滤和冷却:在去除杂质后,通过过滤等方式进一步净化钢液,并将其冷却至室温。
攀钢提钒炼钢厂工艺技术及装备进步
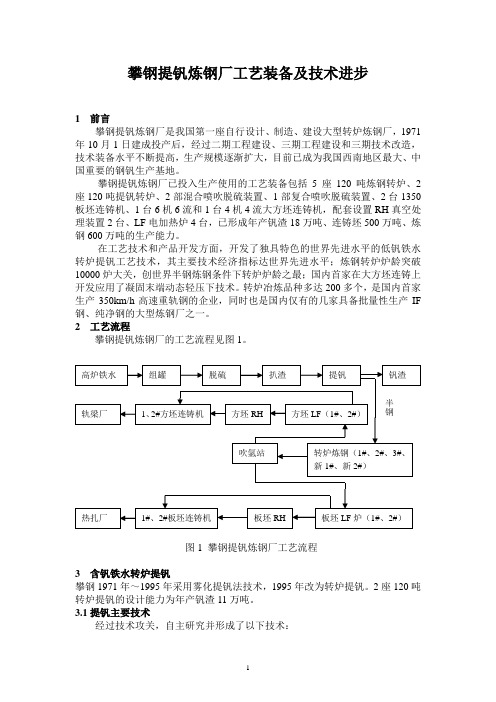
4.3挡渣出钢技术
针对原出钢挡渣采用加球机投放挡渣锥的挡渣效果差,下渣量较大,钢渣中有害成分污染钢水,影响钢坯质量,难以实现“洁净钢”生产。攀钢于2000年12月推广使用了新型的挡渣标挡渣技术,与原挡渣工艺相比,钢包内渣层厚度平均减少23mm,渣层厚度小于100mm的比例从64.98%提高到85.75%以上,为开发高纯净钢种创造了条件。采用新型挡渣工艺,有利于提高钢水质量,稳定脱氧工艺,减少出钢过程的回硫、回磷,该技术达到了国内先进水平。
⑷新转炉一次除尘系统采用了鲁奇公司的新型OG烟气湿法除尘技术,风机抽风量达210000m3/h,该技术是采用环隙式可调喉口,烟气流速最大可达180~190m/s(R—D喉口最高能达120 m/s),反冲水的粒径在75~100μm之间,除尘效果更好。从目前实际使用情况看,含尘浓度小于50~80mg/Nm3,净化效果较好。新转炉还配备了德国鲁奇公司的转炉煤气回收装置,实现了转炉煤气的自动回收,每炉可回收16000Nm3(CO浓度40%~50%)的煤气量,既满足了环保又实现了资源的综合利用。
2工艺流程
攀钢提钒炼钢厂的工艺流程见图1。
图1攀钢提钒炼钢厂工艺流程
3含钒铁水转炉提钒
攀钢1971年~1995年采用雾化提钒法技术,1995年改为转炉提钒。2座120吨转炉提钒的设计能力为年产钒渣11万吨。
3.1提钒主要技术
经过技术攻关,自主研究并形成了以下技术:
(1)渣态调整工艺技术。
(2)多炉出钒渣工艺技术和挡渣出半钢技术。
提钒的工艺原理及应用

提钒的工艺原理及应用1. 引言提钒是一种常用于金属表面处理的工艺,它基于化学反应原理,能够改善金属表面的性能,增加其耐腐蚀性和耐磨性。
本文将介绍提钒的工艺原理以及其在实际应用中的一些案例。
2. 提钒的原理提钒的原理是通过在金属表面形成一层氧化钒,从而提高金属表面的硬度、耐磨性和耐腐蚀性。
提钒主要包含以下几个步骤:2.1 清洗金属表面首先,需要对金属表面进行彻底清洗,以去除表面的杂质和氧化物。
常用的清洗方法包括水洗、酸洗和溶剂清洗等。
2.2 涂敷提钒溶液清洗后的金属表面需要涂敷提钒溶液。
提钒溶液通常是由含有氧化钒和其他配位剂的溶液组成。
这些配位剂可以提高提钒的效果和均匀性。
2.3 生成氧化钒层涂敷提钒溶液后,可以将金属置于高温环境中进行加热处理。
在高温下,溶液中的氧化钒会与金属表面发生反应,生成均匀的氧化钒层。
2.4 冷却处理生成氧化钒层后,需要对金属进行冷却处理,以稳定氧化钒层。
3. 提钒的应用提钒工艺具有广泛的应用领域,下面将介绍一些常见的应用案例:3.1 汽车行业在汽车制造过程中,很多金属零部件需要具有良好的耐腐蚀性和耐磨性。
提钒工艺可以增加这些部件的表面硬度,提高其使用寿命。
3.2 航空航天行业航空航天行业对金属材料的性能要求非常高。
提钒工艺可以改善金属表面的抗氧化和耐蚀性能,提高零部件的可靠性和使用寿命。
3.3 机械制造行业在机械制造行业中,很多机械零部件需要具有较高的耐磨性。
提钒工艺可以增强金属表面的硬度和耐磨性,提高机械零部件的工作效率。
3.4 电子行业电子产品中常用的金属连接器需要具备良好的导电性和耐腐蚀性能。
提钒工艺可以改善金属表面的导电性,并提高连接器的使用寿命。
3.5 医疗器械行业在医疗器械制造过程中,很多金属器械需要具备良好的抗菌性和耐蚀性能。
提钒工艺可以改善金属表面的抗菌性能,提高医疗器械的安全性和可靠性。
4. 总结提钒是一种常用于金属表面处理的工艺,它通过生成一层均匀的氧化钒层,提高金属的硬度、耐磨性和耐腐蚀性。
提钒的工艺原理及应用方法

提钒的工艺原理及应用方法1. 工艺原理提钒是一种常见的金属处理工艺,主要用于提高金属的硬度和耐磨性。
其工艺原理包括以下几个方面:•物理原理:提钒工艺主要是通过在金属表面形成化合物薄层来改善材料性能。
钒与金属元素反应形成金属间化合物,能够提高金属的硬度和耐磨性。
•化学原理:钒在金属中的作用可分为两种形式,一是固溶态作用,通过钒的固溶来提高金属的强度和硬度;二是析出态作用,通过钒的析出来增加金属的硬度和耐磨性。
•影响因素:提钒工艺的效果受到多种因素的影响,包括钒含量、提钒温度、保温时间等。
不同金属在进行提钒工艺时,这些因素的选择和控制都会有所不同。
2. 应用方法提钒工艺在实际应用中有多种方法,下面列举几种常见的应用方法:•溶钒提钒法:将含钒金属加热至钒的溶解温度,在固溶态下进行保温处理。
通过固溶态钒的作用,提高金属的硬度和耐磨性。
•散钒提钒法:将含钒金属加热至析出温度,在金属中析出钒化合物。
通过析出态钒的作用,提高金属的硬度和耐磨性。
•氧化钒提钒法:在金属表面形成钒氧化物薄层,通过钒氧化物的作用,提高金属的表面硬度和耐蚀性。
•电解钒提钒法:利用电解质溶液中的钒离子,在电极上析出钒,形成钒化合物薄层。
通过钒化合物的作用,提高金属的硬度和耐磨性。
3. 提钒工艺的优势和应用领域提钒工艺具有以下优势:•提钒工艺能够显著提高金属的硬度和耐磨性,提高材料的使用寿命。
•提钒工艺成本相对较低,操作简单,适用于大规模生产。
•提钒工艺可以与其他工艺相结合,进一步提高材料性能。
提钒工艺在以下领域有广泛的应用:•机械制造:提钒工艺可以应用于各类机械零部件的制造,提高零部件的硬度和耐磨性,提高机械设备的使用寿命。
•汽车工业:提钒工艺可以应用于汽车轴承、曲轴等零部件的制造,提高零部件的硬度和耐磨性,提高汽车的运行稳定性和寿命。
•航空航天:提钒工艺可以应用于航空航天领域的零部件制造,提高零部件的硬度和耐磨性,提高航空器件的可靠性和安全性。
提钒工艺技术

提钒工艺技术提钒是一种传统的工艺技术,已有数千年的历史。
它是一种将金属加工成薄片的技术,适用于多种不同的材料,包括黄铜、铝、不锈钢等。
提钒工艺技术主要分为三个步骤:准备材料、进行提钒加工、最后完成加工。
首先,我们需要准备材料。
通常,我们使用的材料是金属板或金属片。
我们需要确保材料表面光滑、平整,并且没有明显的缺陷。
接下来,进行提钒加工。
这个步骤可以分为多个小步骤,其中最重要的是切割和拍打。
切割是将金属板或金属片根据需要的形状和尺寸进行切割。
拍打是通过使用锤子和钳子等工具,将金属板或金属片逐渐加工成所需的薄片。
在拍打过程中,需要注意保持薄片的平整度和光滑度,以及避免出现裂痕或其他损坏。
最后,进行最后的加工。
这个步骤包括打磨和抛光。
打磨是通过使用砂纸或其他打磨工具,将薄片表面的不平整或粗糙处理掉,使其变得更加光滑。
抛光是将薄片表面加工得更加光亮,通常使用抛光研磨剂和抛光轮进行。
提钒工艺技术有着广泛的应用。
它可以用于制作各种工艺品、装饰品和家居用品,如金属饰品、金属盆、金属碗等。
同时,它也可以用于制作一些工业零部件,如汽车零部件、电子设备零部件等。
提钒工艺技术具有很多优点。
首先,它可以使金属材料变得更加柔软和易加工,从而方便后续的加工工艺。
其次,提钒技术可以制造出薄而轻的金属制品,也可以节约材料的使用。
另外,提钒工艺技术可以制造出各种不同形状和尺寸的金属制品,非常灵活多样。
最后,提钒工艺技术在制造过程中并不需要使用大量的化学材料,对环境友好。
总结起来,提钒工艺技术是一种传统的金属加工技术,已有数千年的历史。
它通过将金属加工成薄片的方法,可以制造出各种不同形状和尺寸的金属制品。
提钒工艺技术在制造工艺、装饰品和工业零部件等领域有着广泛的应用,具有柔软易加工、节约材料、灵活多样和环境友好等优点。
铁水提钒

பைடு நூலகம்理
原理
含钒生铁提钒工艺以选择性氧化为理论基础。向铁水吹入空气或氧气,必须使铁水中钒迅速、优先氧化,而 其他组分少氧化,方能获得含钒高的钒渣。吹炼过程中应使铁水中的碳氧化最少,保证半钢炼钢时仍有足够的化 学反应热。铁的损耗要降至最低限度,即半钢的收得率要高,以降低钒渣生产成本。
影响因素
钒渣的氧化性
温度控制
钒渣碱度
温度控制
图2钒的氧化反应属于放热的多相复杂反应,但其热效应值在数量上差别很大,反应产物的表示也各不相同。 铁水提钒过程中各元素的氧化反应的标准生成自由能与温度的关系示于图2。由图可见,提钒初期熔池温度比较低 (约1300℃左右)时
(△F°)Ti<(△F°)Si<(△F°)Cr<(△F°)V<(△F°)Mn<(△F°)C
简史
简史
从含钒铁矿中回收钒是从19世纪初期开始的。德国和法国在第二次世界大战时期,用高炉—托马斯转炉法从 含钒0.06%~0.10%的洛林铁矿中(不含钛)回收钒。以含钒铁矿作为高炉原料生产生铁时钒也被还原,获得含钒 0.10%~0.15%的铁水,用此生铁炼钢时钒又被氧化进入托马斯炉渣中,炉渣含钒量可以达到0.5%,是一种无直接 使用价值的低钒渣。德国赫尔曼·戈林钢厂将这种低钒渣与转炉钢厂的其他产物(如厂房屋顶积灰,含0.8%~ 1.0%钒)在另一座高炉内冶炼成含钒和含磷较高的生铁,再经托马斯转炉吹炼得到含钒量较高的钒渣,可直接作 为化工厂生产钒的原料,但含钒铁水提钒后含磷较高,给炼钢带来困难。
铁水预处理提钒讲课稿[整理版]
![铁水预处理提钒讲课稿[整理版]](https://img.taocdn.com/s3/m/c2a3935cb84ae45c3b358ce2.png)
5.0 10.0 15.0 20.0 25.铁0水Si
图1 铁水Si-V2O5回归分析图
表 2 不同铁水Si含量所对应的钒渣理论品位
铁水[Si]%(V2O5)% (V2O5)%
0.13
0.15
0.17
0.19
0.21
由表1可知,2005年1、2月份的铁水Si含量达到0.18%时,钒渣产渣率仅为3.35%, 比去年降低了0.4个百分点,按年处理提钒铁水400万吨计算,全年钒渣产量只能达 到13万吨左右。
⒊对提钒冷却剂成本的影响 根据理论计算,铁水Si含量每上升0.01个百分点,熔池温度升高4.52℃,冷却剂
用量增加:4.52℃÷35÷120=1.08kg/吨铁。 2004年铁水Si含量平均0.155%,2005年按1~2月份平均Si含量0.184%计算,比 2004年增加约0.03个百分点,冷却剂用量要在2004年基础上增加3.24kg/吨铁,达到 21.8 kg/吨铁,若冷却剂价格350元/吨计算,则提钒冷却剂成本为7.64元/吨铁,若 考虑铁皮价格因素的影响(2005年1、2月提钒冷却剂考虑铁皮价格后为430元/吨), 则提钒冷却剂成本将达到9.377元/吨铁。
三、影响提钒的主要因素
影响转炉提钒的主要因素
• 铁水成份及温度的影响 • 吹炼终点温度的影响 • 冷却剂的种类、加入量和加入时间的影响 • 供氧制度的影响
1、铁水成份及温度的影响
铁水钒的影响 :铁水中原始钒含量高有利于钒渣V2O5浓度的提高。
铁水硅的影响:Si高抑制钒的氧化;Si氧化成渣对钒渣“稀释”V2O5;Si氧化 放热使提钒所需的低温熔池环境时间缩短;铁水Si偏高时,渣态过稀,使出钢 过程中钒渣的流失增加。
- 1、下载文档前请自行甄别文档内容的完整性,平台不提供额外的编辑、内容补充、找答案等附加服务。
- 2、"仅部分预览"的文档,不可在线预览部分如存在完整性等问题,可反馈申请退款(可完整预览的文档不适用该条件!)。
- 3、如文档侵犯您的权益,请联系客服反馈,我们会尽快为您处理(人工客服工作时间:9:00-18:30)。
氧化转化临界温度为 131317e 。可见, 提钒的终点
半钢温度不宜过高。提钒过程前期以钒氧化为主,
后期以钒还原为主, 吹钒反应可表示为:
k1
))) y
[V ]
(V )
( 1)
z )))
k2
式中 k1) ) ) 钒正向反应常数; k2) ) ) 钒逆向反应常数。
吹钒反应速率可表示为:
(
-
d
[ V] dt
=关键词 > 低钒铁水 提钒 炼钢 工艺
TECHNOLOGY OF VANAD IUM EXTRACTION FROM LOW VANAD IUM MOLTEN IRON
W an Chaom ing Y i Banglun Zhong Zhenghua
( Pangang G roup Chengdu S teel&V anad ium Co. , L td, Chengdu 610303, Ch in a)
( 1)物流操作: [ S] [ 01060% 的半钢送 30 t炼 钢, 否则, 翻入 600 t混铁炉。
( 2)装入制度: 总装入量按 29~ 3015 t进行控 制。
( 3) 造渣工艺: ( a) 为保证半钢 炼钢脱磷的技 术要求, 钢渣总渣量控制在 11% 左右; 外加渣量按 半钢炼钢造渣渣系进行控制, 转炉终点钢渣的主要 成分: C aO38~ 45% , S iO2 10 ~ 12% , M gO10 ~ 12% , TF e22% 以下, 转炉终点渣碱度 315~ 415; 溅渣护炉 按现有规程执行。
半钢碳含量平均 314% , 范围 2194% ~ 4102% , 分布见图 2。根据图 2, 半钢 [ C] \312% 者占 85% 。 说明保碳操作较为合理。
图 2 半钢碳含量分布
4. 2 半钢温度 由于铁水到转炉后无铁水成份, 只能根据上一
炉的温度情况确定生铁块量, 并且是先进铁水再测 温, 生铁块的重量已无法改变, 只能用铁皮球来调整 温度。因铁水 [ Si] 存在一定的波动, 再加上温度控 制水平参差不齐, 半钢温度控制存在一定的波动, 总 体上控制较好, 平均 1373e , 范围 1331~ 1418e , 其 分布见图 3。根据图 3, 半钢温度控制在试生产要求 的 1340~ 1400e 者占 82% 。
半钢温度与 [ V ]半的对应值
1250
1300
0. 180
0. 075
1350 0. 042
根据表 4, [ V ]半 [ 01042% 时, 终点半钢温度为 1350e 。
另外, 吹钒温度过高时, 钒正向氧化反应较快, 但钒逆向还原反应更快, 铁水 [ V ] 氧化至最低点后 又会回钒, 因此, 终点半钢温度也不应过高, 最高不 应超过 1400e 。
2009年 1月 至 7 月, 共提钒 876 炉, 产粗钒渣 93618 t。实际的主要工艺参数为: 铁水量 2612 t( 25 ~ 2712 t) , 生 铁块 311 t( 2 ~ 415 t) , 铁水 温度 1256e ( 1206~ 1305e ) , 吹氧时间 516 m in( 5~ 615 m in) , 氧压 0165M Pa, 铁皮球 360 kg ( 300~ 600 kg) , 出钢加 75% S iC 200 kg。出钢时间 215~ 510 m in。 4. 1 半钢碳含量
[ Abstract] T he techno logy of vanadium ex traction from low vanad ium m o lten iron in the converter m ill o f PGG CSST is elaborated. By effective ly regulat ing the coolant am oun,t process tem perature and b low ing tim e etc, the grade o f vanad ium slag can be contro lled to h igher than 8% and that o f sem -i steel [ V ] to low er than 01050% , w hich w ill realize an efficient ut ilization o f vanad ium. [ K ey words] low vanadium m o lten iron, vanad ium extraction, stee l m ak ing, technology
第 32卷 第 1期 2010年 2月
四川冶金 S ichuan M eta llurgy
V o .l 32 N o. 1 Feb. , 2010
低钒铁水提钒炼钢工艺分析
万朝明 易邦伦 钟正华
(攀钢集团成都钢钒有限公司, 成都 610303)
=摘 要 > 阐述了攀成钢公司转炉炼钢厂进行低钒铁水提钒工艺及应用情况。通过对冷却剂加 入量、过 程温 度控制、吹炼时间等工艺参数的 有效控制, 可以使钒渣品 位达到 8% 以上, 半钢 [ V ] 在 01050% 以 下, 从 而达到 钒资 源的有效利用。
# 6#
四川冶金
第 32卷
2. 5 出钢、出渣 吹炼终点时, 从出钢口挡渣出尽半钢, 出钢时间
\215 m in, 再从炉口出钒渣。前 2炉洗炉渣出 1次 且单独堆放, 从第 3炉起每 2~ 3炉出 1次钒渣。
出半钢过程中, 在包内加 200 kg碳化硅脱氧出 钢。
3 半钢炼钢工艺制度
3. 1 半钢炼钢工艺特性 提钒后的半钢炼钢, 与铁水相比, 半钢中硅、锰
S /%
V /%
0. 053 0. 185 [ 0. 070 \ 0. 160
表3
铁皮球 技术要求
铁皮球 成分
CaO /% 1. 16 [2
S iO2 /% 5. 12 [7
TFe /% 61. 1 \ 60
样本 /个 6
1. 5 方法 在混铁炉铁水量约 150 t时, 高炉铁水翻入铁水
包后直接进 30 t转炉提钒。前 2 炉洗炉, 出 1次炉 渣且单独堆放, 从第 3炉起每 2 ~ 3炉出 1次钒渣。 半钢 [ S] \ 01060% 进混铁炉, 反之直接冶炼, 半钢 直接冶炼采用硅铁和碳化硅提温, 加复合造渣剂造 渣。
C /% 4. 26 3. 75~ 4. 67
图 1 30 t转炉低钒铁水转炉提钒生产工 艺流程
S i/% 0. 24 0. 1~ 0. 5
含钒铁水质量
M n /% 0. 33
0. 20 ~ 0. 43
P /% 0. 131 0. 11~ 0. 16
S /% 0. 054 0. 025~ 0. 146
1 条件与方法
1. 1 采用的工艺流程 提钒生产采用的工艺流程见图 1。
1. 2 铁水质量 含钒铁水条件见表 1。
1. 3 生铁块成分 提钒冷却用生铁块为我公司的铁水铸块, 其成
分见表 2。 1. 4 铁皮球成分
铁皮球冷却剂的成分见表 3。由表 3 可见, 铁 皮球质量符合要求。
表1
平均 最小 ~ 最大
V /% 0. 205 0. 155 ~ 0. 248
温度 /e 1256
1206 ~ 1305
作者简介: 万朝明, 男, 工程师。
第 1期
S ichuan M eta llurgy
# 5#
表2
生铁块 要求
C /% 4. 16
生铁块分 析结果
S i/% M n /% P /% 0. 25 0. 326 0. 129
率, 进一步增大提钒的难度。
2. 1 装入量
根据攀钢提钒炼钢厂提钒经验, 考虑到生铁块 的加入量, 每炉铁水装入量为 25~ 27 ,t 总装入量控
制在 28~ 30 t。 2. 2 半钢温度控制
铁水提钒是一项选择性氧化技术。它要求保碳
脱钒, 将 [ V] 降至 0105% 以下。但吹钒过程是钒的 氧化还原过程。根据计算, 低钒铁水的碳钒选择性
( b) 石灰、轻烧白云石、复合造渣剂的加入量和 加入方法: 石灰加入量 110~ 115 t /炉; 轻烧白云石 加入量按 018~ 112 t /炉。采用单渣法分二批加入 造渣材料。石灰和轻烧白云石分别按总量的 1 /2~ 2 /3在第一批料中加入, 剩余的石灰 量在初期渣形 成后分 2~ 3批次加入转炉炉内。
图 3 半钢温度分布
4. 3 半钢钒含量 共 分 析 49 个 半 钢 钒, 平 均 01042% , 范 围
01010% ~ 01111% , > 01050% 占 22% 。由于 受铁 水成份、生产条件和技术水平的影响, 部分炉次的半
第 1期
S ichuan M eta llurgy
# 7#
钢 [ V ] 出现偏高, 其分布情况见图 4。
)e =
(
-
d
[ V] dt
)正
+
(
d
[V dt
]
)逆
( 2)
当吹钒处于正逆反应相等的临界状态时, 作为
吹钒结束, [ dt
)e=
0
( 3)
根据热力学数据计算
lnk1= - 3479. 453 /T + 4. 3471
( 4)
lnk2= - 26465. 72 /T + 10. 41655 ( 5)
( c) 复合造渣剂 012 ~ 015 t/炉, 在加第一批造 渣材料时全部加入。复合造渣剂要压成球状, 粒度 为 15~ 35 mm. , 可由炉顶料仓加入。
( 4)供氧工艺制度: 氧枪采用恒 氧压变枪位操 作。氧气工作压力为 0185~ 110 MP a, 枪位按 018~ 115 m 控制。