化工公司持续清洁生产铬铁矿焙烧工艺采用无钙焙烧实施方案
无钙焙烧技术在国内的开发与推广研究

目前 国 内已先后 有三 家铬 盐厂 实现 了无 钙焙 烧
的产业 化 生产 。其 中 : 肃一 家铬 盐厂 自 20 甘 0 3年 初
首 次实 现 万 吨级工 业化 生产 以来 , 技术 不 断完善 , 产
经验 与实践 生产 经 验 不 足 , 当多 的研 究 成 果 难 以 相 做 大做 强 , 难于进 行 普及 与示 范 , 而且一 般研 究成 果 的中、 扩试 项 目规模 跨度 较 大 , 一般 科研 机构 难 于独 自完成 。另一方 面 , 目前 铬 盐 厂 家 大 多 已经 具 备 了
含钙 质矿 物 。从根 本上 杜绝 了因存在 含钙 物质 而 与
铬矿 在碱 性焙 烧条 件下 生成 铬酸 钙等 高致 癌物 质 的 可能 , 同时提高 了焙 烧熟 料 的水洗 浸 出性 能 、 优化 了 铬矿综 合 利用 的价 值 , 同时 也 加 大 了工艺 参 数 的 但 控制 难 度 。例 如 : 生 料配 比 、 料 粉 磨 细度 、 料 对 物 物
一
铬 渣 料直 接进 行后 期 的冶 金 作 业 , 过 连续 生 产替 通
果进行 评 价试 验和 创新 开发 , 于研究 单位 而 言 , 对 各 铬盐 厂家 所具 备 的天然 场地 是最 好 的一线 信息 来 源
和适 用验 证车 间 。两者 间需 要建 立起 增进 更加 密切
代 了对铬 渣后 期 的一 般化解 毒工 序 。 国内也有 一些
近 1 O年 来 , 着 “ 钙 焙 烧 ” 术 在 国 内 的不 随 无 技
断完 善 与成 熟 , 铬 盐 行 业 企业 中 也不 断 曝 露 出一 在 些 问题 , 到底 应该 选 择 或 使 用 哪 种类 型 的工 艺 技 术 需 要不 同厂 家 分 别 对 待 。 总结 现 有 的 “ 钙 焙 烧 ” 无 技术 , 从研 究类 型上 大体 分为 : 少碱 焙烧 、 碱焙 烧 、 足
德国铬铁矿无钙焙烧概况
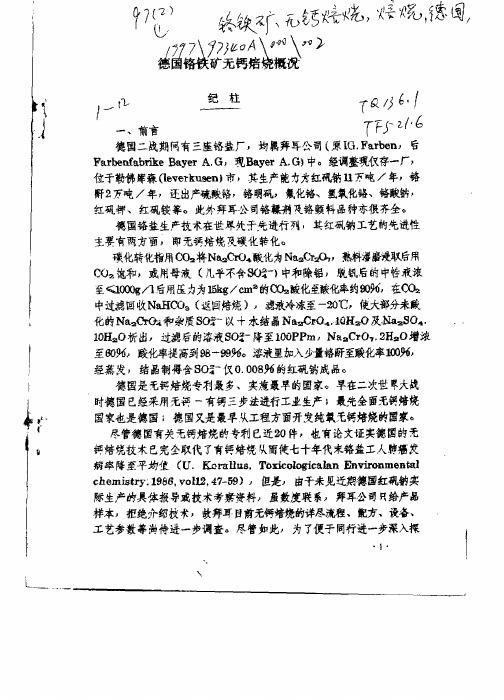
五、控制80 /A 。 。 i 。 l0 比的无钙培烧 有钙焙烧时,硅铝形成l点高、难溶于水的硅酸葛、铝酸钙等化 熔 合物。 无钙焙境对 硅铝 除生成熔点高、不术溶的的铝硅 酸盐 (a k O 或N  ̄ 盘毛 l N A  ̄ . aMg s 2)外 若铬矿中枣质S0 / 1 i 0 il A2 2 犀尔
D l4 6 用 10 E 2 3的 0 毋铬矿同8 份纯碱 、5 廿 4 6 返渣的麓合物于 90 5—
1 0 连续焙蛲。熟料逆流浸洗。选后的渣月水打成含固20 /l 1 0 0g 的 浆敢, 耿忉匿 扫 ( n 火气压 )送旋液分离器 为粗细两半。枉浆滤舌 烘干怍返渣循环陡用。细渣排敷。 矿I粗蜘渣组成见表2 ! 己 。
料喷Na H 溶液 )。 O
三、足碱_步晓成和浸渣旋l 离 二 液
德国大部分无镑培烧专利为足碱一步蛲麻泛 配碱率为理论量
10 。其填科一般用近渣 育的也用氧化 0 ̄ 或黄最矿蛲制碗酸后
的尾渣 ( 主要盛份为F 2 e0 ),为了 减少返渣P 硅、铝,使渣巾适于 作填料的键铁矿及未反应的铬铁矿富集 穗副爱 先栗用旋液分离o
故不会烧结,用螺旋输料机推入回转窑的反应带.安有喷嘴的糯碱管
’
4‘
.
从窑胁 至 ( 露尾约l 窑长的 )反应带 N O- Nac 8 /3 a I ̄ I 2 O 水溶液从
喷嗜 以细 蓦 . 吨洒在随窑运动着 的热粉料上 ,迅 即发生一 系列物理化学
变化 ( 蒸发,h H变Nac 。 2! ,升温、碱解、氧化… )形成小球粒一 O
发 <7m. C 6 7娜, F C 5 分C .5 用 e 解毒吉社减: 龃渣∞ 杜蹙 》1 U 鼬 , 含 z a 细渣的2 , 作返渣循环 。 从楹细渣含 O是 倍
铬铁矿无钙焙烧过程中氧含量对氧化率的影响
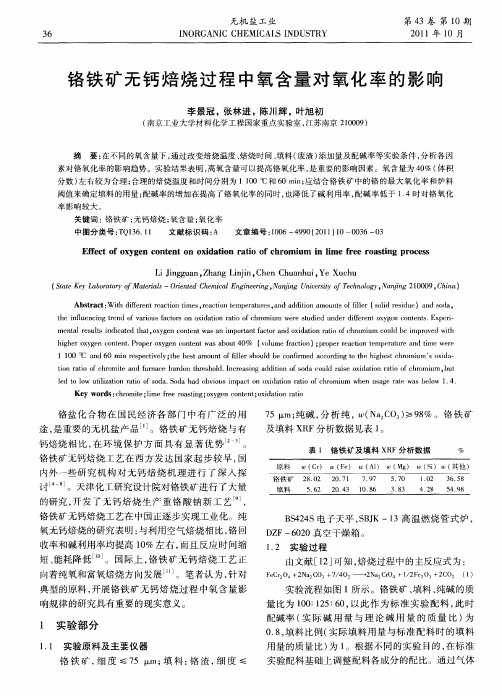
l d t o t iai n r t fs d . o a h d o vo si a to xd t n rt fc r mi m e s g ae wa eo . e o lw u i z t a i o o a S d a b iu mp c n o i ai ai o h o u wh n u a e r t sb l w 1 4. l o o o o Ke r s c r mi l r e r a t g o y e o tn ;x d t n r t y wo d : h o t i f o si ; x g n c ne t o iai a i e: me e n o o
hge xgncnetPo e oye otn w s bu 4 % (o me rco ) poe at ntm ea r adt ew r ihr ye ot .rp r xgncnet a ot 0 o n a vl at n ;rpr eco prt e n m ee u f i r i e下 , 通过 改变焙烧 温度 、 焙烧时 间、 填料 ( 废渣 ) 添加量及配碱率等实验 条件 , 分析 各因
素对铬氧化率的影响趋势 。实验结果表明 , 氧含量可 以提 高铬 氧化率 , 高 是重要的影响因素。氧含量为 4 %( 0 体积
分数 ) 左右较为合理 ; 理的焙烧温度和时间分别为 110q 6 i; 合 0 C和 0r n 应结合铬铁 矿 中的铬 的最大氧化率 和炉料 a
Efe to x e o e t o x da i n r to o hr m i m n l e f e o si o e s f c fo yg n c nt n n o i to a i fc o u i i r e r a tng pr c s m
化工公司清洁生产方案产生与筛选方案
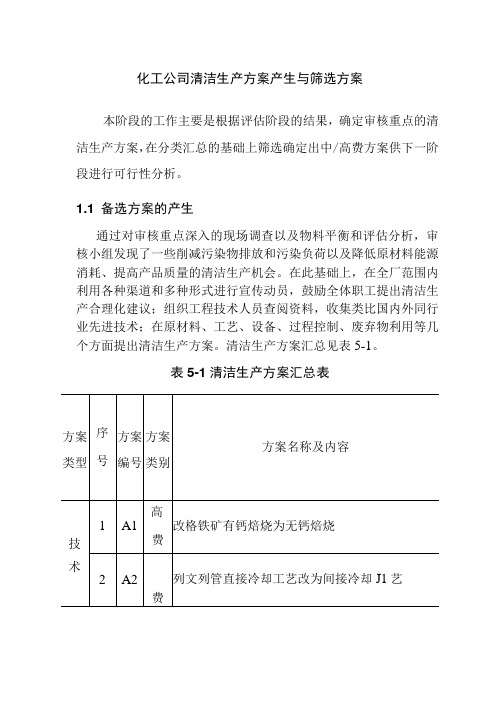
化工公司清洁生产方案产生与筛选方案
本阶段的工作主要是根据评估阶段的结果,确定审核重点的清
洁生产方案,在分类汇总的基础上筛选确定出中/高费方案供下一阶
段进行可行性分析。
1.1 备选方案的产生
通过对审核重点深入的现场调查以及物料平衡和评估分析,审核小组发现了一些削减污染物排放和污染负荷以及降低原材料能源消耗、提高产品质量的清洁生产机会。
在此基础上,在全厂范围内利用各种渠道和多种形式进行宣传动员,鼓励全体职工提出清洁生产合理化建议;组织工程技术人员查阅资料,收集类比国内外同行业先进技术;在原材料、工艺、设备、过程控制、废弃物利用等几个方面提出清洁生产方案。
清洁生产方案汇总见表5-1。
表5-1清洁生产方案汇总表
1.2 方案初步筛选
审核小组成员对表5-1中的清洁生产方案进行了认真细致的的分析,从清洁生产方案技术可行性、环境效益、经济效益、实施难易程度以及企业现有状况多方面论证,确定5万元以下为无/低费方案,5万元以上为中/高费方案,无低费方案实施难度不大,部分方案环境效益和经济效益都非常明显,因此审核小组经过讨论并经公司领导审批后组织实施。
表5-1中A1、A3、C1、C3、C4、DKD2和E1为中/高费
方案,投资比较大,需进一步分析论证其可行性。
21458814

对环境的 严重污染。 同时上述铬渣既含有大量氧化钙 , 又含有大量氧化镁 ,
解毒处理不仅费用 高,而且很难彻底,大量应用也很难.由于上述铬 渣还
含有大量致癌物铬酸钙,随着对环境保护要求的提高,我国东部多家铬盐 厂在二十世纪八九十年代相继被迫停产.停产,是一种消极的解决办法,
产 品的目的。该工艺的最大问题是,由于加入 了 含大量氧化钙的填料,因
此在焙烧和浸取过程中就会生成大量难溶于水 的所谓酸溶铬 ( 如铬铝酸钙
等) ,造成了 焙烧氧化率低,熟料的 水浸取率低,铬渣中六价铬带损严重. 据统计,铬损的 8% 由 3是 铬渣带损造成的.而铬渣中的这种酸溶六价铬在
积极的方法是从工艺路线上去解决铬渣的污染问题. 专利 Z 0167. 提 L 25479
维普资讯
铬
盐
I监4 7 出一种从根本上解决铬渣污染的无钙焙烧新工艺. 1 .本工艺的技术特点:
本工艺 (L 254 79 Z0167. ,下同 ) 与传统工艺 ( 有钙焙烧 ) 的根本 区别就 在于铬铁矿焙烧时的配方不同,是将铬铁矿焙烧时的填料石灰石.白云石
远大于 旧工 艺的经 济效 益,也就是说 ,该无钙焙 烧新 工 艺的经济效益和社
会效益是 巨大的. 2 .无钙焙烧铬渣的应用 由于本工艺无钙焙烧新工艺与传统有钙焙烧 旧工艺所配填料不同,因
此两种工艺铬渣的化学组成不同,从而造成两种铬渣的应用方面也有很大 不同.无钙焙烧铬渣和有钙焙烧铬渣的化学成分见表一: 表一 无钙焙烧铬渣和有钙焙烧铬渣化学成分表
% MO g CO a F2 SO e ̄ 0 i A , l 2 O C 2 r, 0 其 中 C r
铬铁矿氧化焙烧工艺的判定和评价
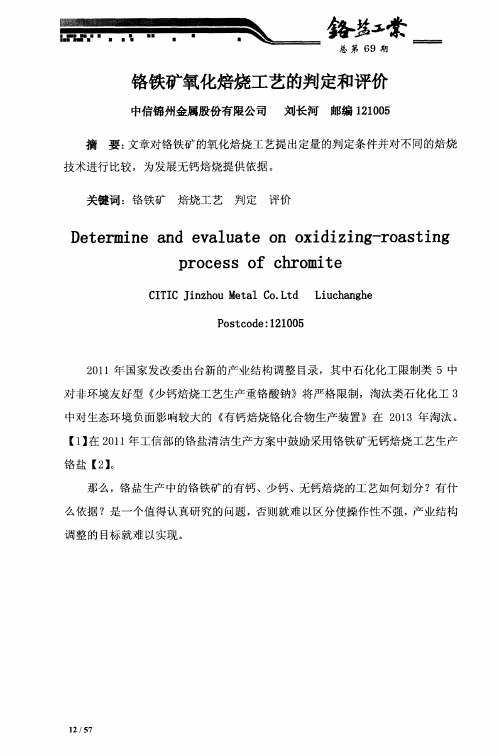
那么 ,铬盐生产 中的铬铁矿 的有钙 、少钙 、无钙焙烧 的工艺如何划分 ?有什
么依据 ?是一个值得认真研究 的问题 , 否则就难 以区分使操作性不强 , 产业结构
调整 的 目标 就难 以实现 。
总 第 6 期 9
1 、铬铁矿氧化焙烧工艺
国内外生产铬盐的工艺基本都很相近 ,见下 图一 l
当 A z。F 2s 0 6 1 / e0> . 4时配入加钙反应产物 为1 2 a 0 / 3— C 0・ S 0 、 i
4 a A 。。 F 2。、2 a F 2。、5 10 ・ e0 C 0・ 10 ・ e0 C 0・ e0 A 。 F 2。、C C 。; 当 A 。F 。 a r0 1 / e0 比 0
总之是要控制熟料在 高温下产 生的液相 量,使窑不结圈 。
这样 以加入氧化钙 与否,确 定其 工艺特 点可分为: 无钙焙烧—— 不外加入氧化钙 ,配钙系数 M 。 . 3 ≤0 0
/
有钙焙烧
有钙焙烧 ,配钙系数 M 。 . ∞≥10
少 ( )钙焙烧 ,配钙系数 0 0 <M 。 . 7 7 . 3 低 . 3 <10 7 0 0
通常有钙焙烧返烧 的是有钙渣 、无 钙焙烧 返烧 的是无钙渣 。
( )主 原 料 一 一铬 矿 3
在有钙焙烧 中各种铬矿都可 以用 , 因为加入 C O控制有害元素溶 出提 高碱 的 a
利用率 。如 阿尔 巴亚、土耳其 、菲律 宾、印度 、南非都可 以。而无钙焙烧 不配入
石灰类填料 , i 反应 当中最终 生成铝 硅酸镁钠 [a g 1S 。 ] N i。 制 S O在 N A 。i0 和 aS O抑 M 了硅和铝 的溶 出。主要 是应 用南 非矿 品位高,含硅低<2 0 为最好 。 .% ( )配碱量有 很大变 化 ,原则是配入石灰量 愈大相 对配入 的纯碱量愈 小, 4
铬及其化合物工业污染物排放标准编制说明-中华人民共和国环境
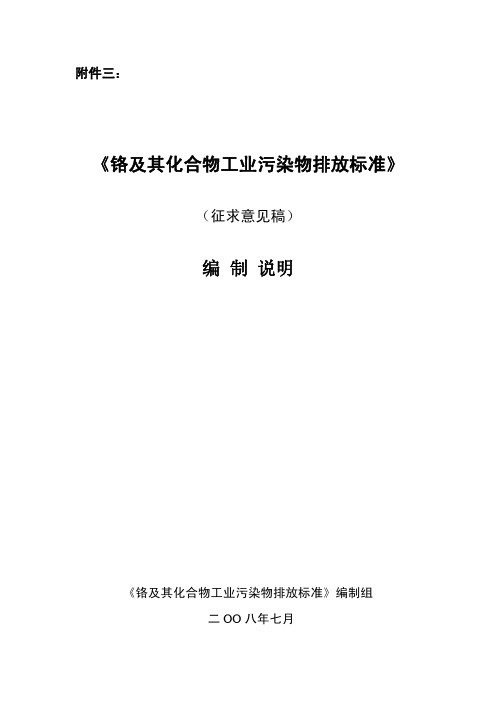
附件三:《铬及其化合物工业污染物排放标准》(征求意见稿)编制说明《铬及其化合物工业污染物排放标准》编制组二OO八年七月目录1.任务来源 (1)2.我国铬及其化合物生产概述 (1)2.1生产企业现状 (1)2.2主要产品、原材料种类和生产工艺 (2)2.3行业总产值 (4)2.4行业发展预测 (4)2.5与发达国家对比 (6)3.污染物排放和治理状况 (8)3.1废水排放状况 (8)3.2废气排放状况 (8)3.3主要污染物排放状况 (9)3.4污染治理状况 (9)4.标准制定的必要性 (10)4.1铬及其化合物生产的主要环境问题 (10)4.2国家对铬及其化合物环境保护工作提出了更高的要求 (11)4.3新技术的开发对排放标准的制定与实施提供了条件 (13)4.4我国现行标准不能适应铬及其化合物生产污染控制的要求 (13)5.制定原则和总体思路 (15)5.1标准制定的基本原则 (15)5.2标准制定的总体思路 (15)5.3标准制定的技术依据 (15)6.方法和技术路线 (15)7.主要技术内容的确定及说明 (16)7.1对生产工艺的总体要求 (16)7.2适用范围 (16)7.3术语和定义 (17)7.4污染物项目及控制指标的选择 (17)7.5水污染物排放控制要求 (17)7.6大气污染物排放限值 (21)8.与国内外排放标准的比较 (22)8.1新标准与国外相关标准对比 (22)8.2新标准与现行标准的对比 (23)9.标准实施的环境、经济、技术效益分析 (24)9.1达标技术分析 (24)9.2投资估算 (25)9.3效益分析 (25)铬及其化合物工业污染物排放标准 编制说明1.任务来源2003年国家环境保护总局办公厅下达了《关于公布2003年度环境标准编制单位名单的通知》(环办函〔2003〕508号),由济南市环境保护科学研究所牵头、中国无机盐工业协会、中国化工防治污染技术协会、济南裕兴化工总厂参加,开展《铬及其化合物工业污染物排放标准》的制订工作。
工业和信息化部、环境保护部关于加强铬化合物行业管理的指导意见

工业和信息化部、环境保护部关于加强铬化合物行业管理的指导意见文章属性•【制定机关】工业和信息化部,环境保护部(已撤销)•【公布日期】2013.08.23•【文号】工信部联原[2013]327号•【施行日期】2013.08.23•【效力等级】部门规范性文件•【时效性】现行有效•【主题分类】环境保护正文工业和信息化部、环境保护部关于加强铬化合物行业管理的指导意见(工信部联原〔2013〕327号)各省、自治区、直辖市、新疆生产建设兵团工业和信息化主管部门、环境保护厅(局):为保护环境和民众健康,加强铬化合物行业管理,根据《重金属污染综合防治“十二五”规划》(国函〔2011〕13号)、《铬化合物生产建设许可管理办法》(工业和信息化部令第15号,以下简称《管理办法》)和《“十二五”危险废物污染防治规划》(环发〔2012〕123号),提出以下意见:一、总体要求(一)指导思想。
以邓小平理论、“三个代表”重要思想、科学发展观为指导,加强铬化合物污染防治,促进铬化合物产业结构调整,加快转变铬化合物行业发展方式,确保铬化合物行业健康发展。
(二)基本原则。
坚持保护环境,铬化合物生产建设必须严格执行环境保护法律法规,达到相关标准和规范的要求;坚持技术进步,严格执行有关产业政策,加快淘汰落后产能,推行清洁生产工艺,减少有毒铬渣产生,提高资源综合利用水平;坚持许可管理,严格执行《管理办法》,现有、新建、改建、扩建铬化合物生产装置必须依法申请取得《铬化合物生产建设许可证书》(以下简称《许可证书》),并接受工业和信息化、环境保护行政主管部门的监督检查。
(三)发展目标。
铬化合物生产企业实现当年产生铬渣当年处置完毕,环境风险大幅降低;2013年年底前,淘汰铬化合物有钙焙烧工艺,推行清洁生产工艺;到“十二五”末,铬化合物生产厂点进一步减少,工艺技术装备达到国际先进水平,形成布局合理、环境友好、监管有力的铬化合物行业健康发展格局。
二、严格准入,推动行业有序发展(四)严格执行环境影响评价制度。
化学行业清洁生产方案精编

化学行业清洁生产方案精编一、背景分析:随着经济的快速发展,化学行业在国民经济中的地位日益提高。
然而,传统的化学生产方式存在着严重的环境污染问题,给环境和人类健康带来了巨大的威胁。
为了解决这一问题,制定一系列清洁生产方案是必不可少的。
二、清洁生产方案内容:1.持续推进绿色化学技术研发:加大对环境友好的绿色化学技术研发投入,通过优化生产工艺,减少或消除污染物的排放,实现清洁生产目标。
同时,加强与清洁能源产业的合作,推广清洁能源在化学行业的应用。
2.强化污染物排放监控:加强对化学生产企业的排污监管,建立完善的监测体系,定期监测污染物排放情况,确保企业达到国家排放标准。
对违规排放的企业进行处罚,并公开曝光违反环境法规的企业名单。
3.优化资源利用:推广循环利用、资源综合利用和废物资源化技术,减少对原材料的需求,降低资源浪费,并减少废物排放。
加强与相关企业和研究机构的合作,促进技术创新和经验交流。
4.加强环境管理:严格实施环境管理体系,建立健全的环境保护制度和标准,加强对化学企业环境管理能力的培训和提升。
加强环境监测,及时发现和处理环境问题,防止环境污染事故的发生。
5.提高员工环境保护意识:开展环境保护知识培训,提高员工环境意识和责任意识,规范员工行为,减少环境污染。
建立激励机制,表彰在环境保护方面做出突出贡献的员工和团队。
6.加强产业协同发展:加强与相关产业的合作,推动产业链上下游企业共同推进清洁生产。
建立清洁生产联盟,加强信息交流和合作,共同解决环境问题,共同推动行业的可持续发展。
三、清洁生产方案的重要性:1.保护生态环境:清洁生产可以减少大气、水体和土壤的污染,降低生态环境的破坏,从而对生态系统和生物多样性的保护起到重要作用。
2.提高企业竞争力:清洁生产可以提高企业的资源利用效率和生产效率,降低成本,提高产品质量,增强企业的竞争力。
3.维护公众健康:化学行业是一个高风险的行业,清洁生产可以减少污染物的排放,降低人员和周边居民的健康风险。
铬铁矿无钙焙烧的反应机理
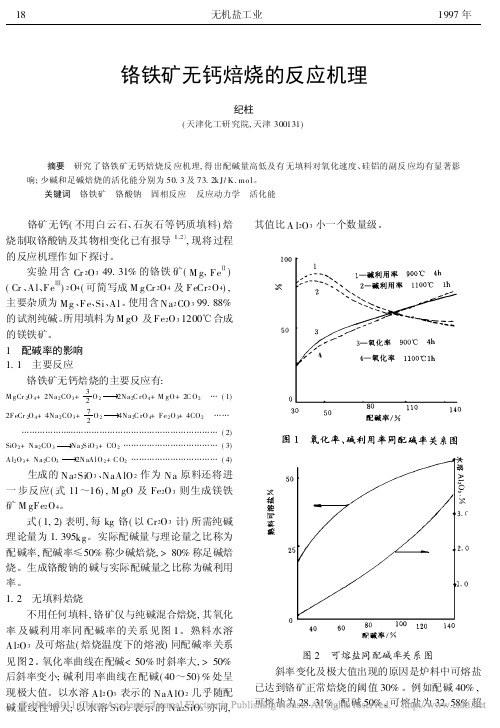
铬铁矿无钙焙烧的反应机理纪柱(天津化工研究院,天津300131) 摘要 研究了铬铁矿无钙焙烧反应机理,得出配碱量高低及有无填料对氧化速度、硅铝的副反应均有显著影响;少碱和足碱焙烧的活化能分别为50.3及73.2kJ/K.mo l。
关键词 铬铁矿 铬酸钠 固相反应 反应动力学 活化能 铬矿无钙(不用白云石、石灰石等钙质填料)焙烧制取铬酸钠及其物相变化已有报导〔1、2〕,现将过程的反应机理作如下探讨。
实验用含Cr2O349.31%的铬铁矿(M g,FeⅡ)(Cr、Al、FeⅢ)2O4(可简写成M g Cr2O4及FeCr2O4),主要杂质为Mg、Fe、Si、Al。
使用含Na2CO399.88%的试剂纯碱。
所用填料为M gO及Fe2O31200℃合成的镁铁矿。
1 配碱率的影响1.1 主要反应铬铁矿无钙焙烧的主要反应有:M gCr2O4+2Na2CO3+32O22Na2C rO4+M gO+2C O2(1)…2FeCr2O4+4Na2CO3+72O24Na2C rO4+Fe2O3+4CO2……(2)…………………………………………………………………SiO2+Na2CO3Na2S iO3+CO2(3)………………………………Al2O3+Na2C O32NaAlO2+C O2(4)…………………………… 生成的Na2SiO3、NaAlO2作为Na原料还将进一步反应(式11~16),M gO及Fe2O3则生成镁铁矿M gFe2O4。
式(1,2)表明,每kg铬(以Cr2O3计)所需纯碱理论量为1.395kg。
实际配碱量与理论量之比称为配碱率,配碱率≤50%称少碱焙烧,>80%称足碱焙烧。
生成铬酸钠的碱与实际配碱量之比称为碱利用率。
1.2 无填料焙烧不用任何填料,铬矿仅与纯碱混合焙烧,其氧化率及碱利用率同配碱率的关系见图1。
熟料水溶Al2O3及可熔盐(焙烧温度下的熔液)同配碱率关系见图2。
氧化率曲线在配碱<50%时斜率大,>50%后斜率变小;碱利用率曲线在配碱(40~50)%处呈现极大值。
铬铁矿无钙焙烧工艺参数控制研究
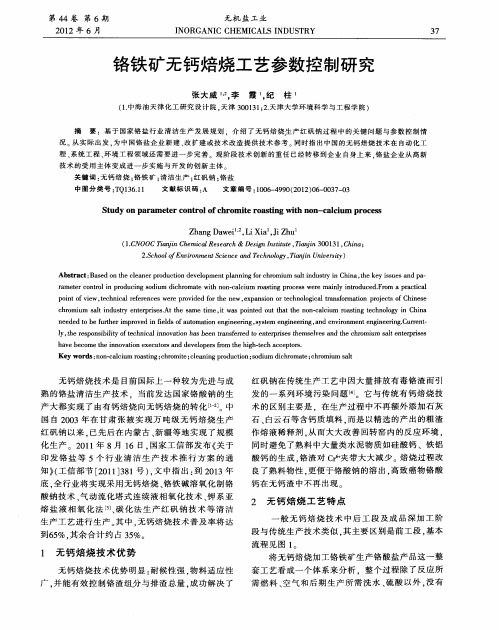
2Sh oo ni n e t c n e n eh o g ,i j nvrt) . ol c fE vr m n i c dTc nl y Ta i U ie i o Se a o nn sy
Ab t a t Ba e n t ece n r r d c in d v l p n ln i gf r h o u s l i d s y i h n , ek yis e n a sr c : s d o la e o u t e e o me t a n n r mim at n u t C i a t e u sa d p — h p o p o c r n h s r mee o to n p o u i g s d u d c r mae w t o —a cu r a t gp o e swe e man y i t d c d F o ap a t a a trc n r l r d c n o i m i h o t i n n c i m o si r c s r i l r u e . rm r ci l i h l n n o c
中 图分 类 号 :Q161 T 3 .1
文献标识码 : A
文章 编 号 :0 6 4 9 (0 2 0 — 0 7 0 10 — 90 2 1 )6 0 3 — 3
St udyon pa a e e o r lo h o ier a tng wih no r m t rc nt o fc r m t o si t n-c l i a cum oc s pr e s
程 、 统 工 程 、 境 工 程 领 域 还 需 要 进 一 步 完 善 现 阶 段 技 术 创 新 的 重 任 已经 转 移 到 企 业 自身 上 来 . 盐 企 业从 高新 系 环 铬
焙烧炉环保实施方案
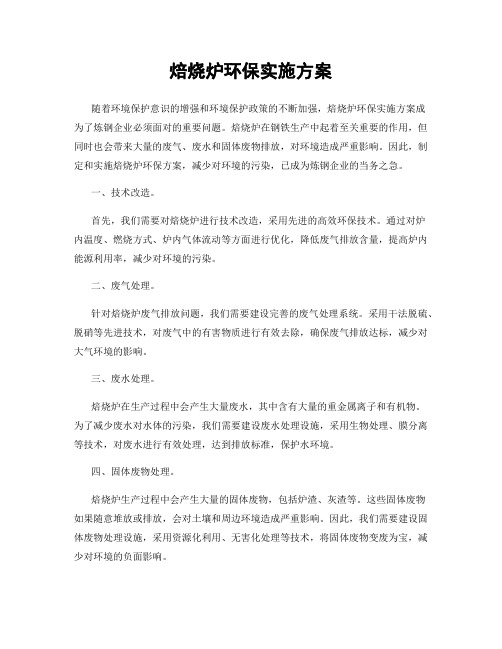
焙烧炉环保实施方案随着环境保护意识的增强和环境保护政策的不断加强,焙烧炉环保实施方案成为了炼钢企业必须面对的重要问题。
焙烧炉在钢铁生产中起着至关重要的作用,但同时也会带来大量的废气、废水和固体废物排放,对环境造成严重影响。
因此,制定和实施焙烧炉环保方案,减少对环境的污染,已成为炼钢企业的当务之急。
一、技术改造。
首先,我们需要对焙烧炉进行技术改造,采用先进的高效环保技术。
通过对炉内温度、燃烧方式、炉内气体流动等方面进行优化,降低废气排放含量,提高炉内能源利用率,减少对环境的污染。
二、废气处理。
针对焙烧炉废气排放问题,我们需要建设完善的废气处理系统。
采用干法脱硫、脱硝等先进技术,对废气中的有害物质进行有效去除,确保废气排放达标,减少对大气环境的影响。
三、废水处理。
焙烧炉在生产过程中会产生大量废水,其中含有大量的重金属离子和有机物。
为了减少废水对水体的污染,我们需要建设废水处理设施,采用生物处理、膜分离等技术,对废水进行有效处理,达到排放标准,保护水环境。
四、固体废物处理。
焙烧炉生产过程中会产生大量的固体废物,包括炉渣、灰渣等。
这些固体废物如果随意堆放或排放,会对土壤和周边环境造成严重影响。
因此,我们需要建设固体废物处理设施,采用资源化利用、无害化处理等技术,将固体废物变废为宝,减少对环境的负面影响。
五、环保意识培训。
除了技术改造和设施建设,我们还需要加强员工的环保意识培训。
通过开展环保知识宣传教育活动,提高员工对环保工作的重视程度,增强环保意识,使每个员工都能成为环保工作的参与者和推动者。
六、监测和评估。
为了确保焙烧炉环保实施方案的有效实施,我们需要建立完善的监测和评估机制。
定期对废气、废水、固体废物等环境排放进行监测,评估环保工作的效果,及时发现和解决存在的问题,确保环保工作的持续改进。
总结。
通过技术改造、废气处理、废水处理、固体废物处理、环保意识培训以及监测和评估等措施的综合实施,我们相信焙烧炉环保实施方案能够有效降低对环境的影响,实现绿色生产,为可持续发展做出应有的贡献。
专访重庆昌元化工集团有限公司党委书记陈朝军 不断寻求革新,实现铬盐清洁生产产业化

产业观察O B S E R V A T IO N ]专访重庆昌元化工集团有限公司党委书记陈朝军不断寻求革新,实现铬盐清洁生产产业化□本刊记者陈婉隐形冠军企业,最早由德国管理学家赫 尔曼•西蒙提出,是指在某个细分疔业或市场 占据领先地位的中小型企业,重庆昌元化工 集团有限公司(以下简称昌元集团)正是这样 一家企业,现在已成为全国“制造业单项冠军 示范企业”。
为什么这么说?日前,记者采访了重庆昌元化工集团有限公司党委书记陈朝军,请他说 明昌元集团高效环保的清洁生产工艺秘诀。
环境经济:请介绍一下昌元集团的发展 历程。
陈朝军:公司前身为重庆嘉陵化工厂,2009 年更名为重庆昌元化工有限公司,2012年成为2020.22M B;「EnvironmentalV d c o n o m y中外合资企业,2015年成立重庆昌元化工集团有限公司。
公司总部设在重庆荣昌,下辖白银昌元化工有限公司、重庆翘柏环境科技有限公司、重庆昌农环保材料有限公司、重庆盎硕科技有限公司等多家全资子公司。
公司专注于高锰酸钾的生产和技术革新,以创新为依托,成功研发出“气动流化塔法”清洁生产工艺。
创新引领企业发展,2006年公司成为全球最大的高锰酸钾制造商和经销商2011年跨界进入铬盐行业,2012年全资收购白银甘藏银晨铬盐公司,进行核心技术移植的探索和全新再改造,2(>16年公司在甘肃白银建设“1(>万吨/年重铬酸钠及配套清洁生产项目”,2019年一期项目5万吨/年建成投产,实现产业化。
环境经济:传统铬盐行业属于重污染行业,昌元集团基于哪些考虑进入铬盐行业?陈朝军:创新发展、追求卓越是企业的核 心文化,公司董事长李守昌是企业致力于技术 革新的领军人和带路人,公司的核心技术“气 动流化塔法”就是在他的带领下自主研发的。
李守昌董事长一直怀揣着一个“无机盐梦”,就 是要彻底改变无机盐行业的污染现状,推动行 业技术进步。
众所周知,铬盐传统焙烧法(干法)生产工 艺存在高污染、高能耗、低品质的缺陷,其产生 的废水、废渣中的六价铬是致癌物。
铬铁矿无钙焙烧简介
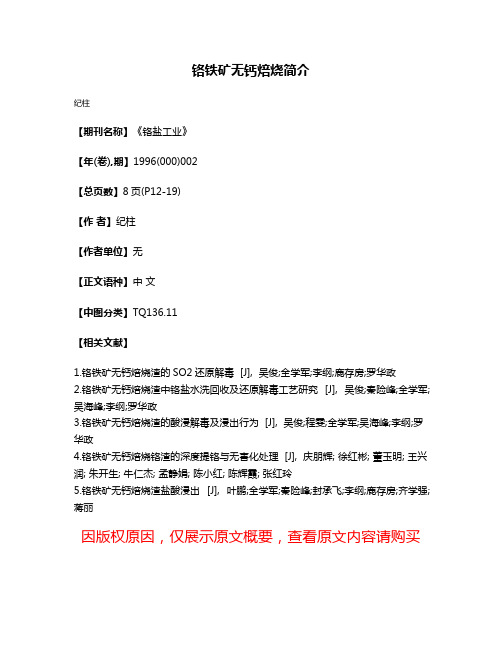
铬铁矿无钙焙烧简介
纪柱
【期刊名称】《铬盐工业》
【年(卷),期】1996(000)002
【总页数】8页(P12-19)
【作者】纪柱
【作者单位】无
【正文语种】中文
【中图分类】TQ136.11
【相关文献】
1.铬铁矿无钙焙烧渣的SO2还原解毒 [J], 吴俊;全学军;李纲;鹿存房;罗华政
2.铬铁矿无钙焙烧渣中铬盐水洗回收及还原解毒工艺研究 [J], 吴俊;秦险峰;全学军;吴海峰;李纲;罗华政
3.铬铁矿无钙焙烧渣的酸浸解毒及浸出行为 [J], 吴俊;程雯;全学军;吴海峰;李纲;罗华政
4.铬铁矿无钙焙烧铬渣的深度提铬与无害化处理 [J], 庆朋辉; 徐红彬; 董玉明; 王兴润; 朱开生; 牛仁杰; 孟静娟; 陈小红; 陈辉霞; 张红玲
5.铬铁矿无钙焙烧渣盐酸浸出 [J], 叶鹏;全学军;秦险峰;封承飞;李纲;鹿存房;齐学强;蒋丽
因版权原因,仅展示原文概要,查看原文内容请购买。
- 1、下载文档前请自行甄别文档内容的完整性,平台不提供额外的编辑、内容补充、找答案等附加服务。
- 2、"仅部分预览"的文档,不可在线预览部分如存在完整性等问题,可反馈申请退款(可完整预览的文档不适用该条件!)。
- 3、如文档侵犯您的权益,请联系客服反馈,我们会尽快为您处理(人工客服工作时间:9:00-18:30)。
化工公司持续清洁生产锚铁矿焙烧工艺采用无钙焙烧实施方案1.1无钙焙烧工艺是国际通行、国家推进的清洁生产工艺1.1.1国际形势当前世界铭盐工业面临的主要问题是铭污染问题,为减少格盐生产对环境的污染,国外铭盐生产已向集中化、大型化、自动化和采用无钙焙烧清洁生产工艺方向发展。
美国现仅有两家格盐厂,总生产能力为11.6万吨/年,俄罗斯两家铭盐厂在18万吨/年以上,日本两家公司为5万吨/年,英国一家公司生产能力为13.5万吨/年,其他如哈萨克斯坦、波兰、南非、罗马尼亚、伊朗等国家也仅有一个或两个生产厂家。
国外格盐工业发展有两种模式:一是工业发达国家对本国铭盐生产不再扩建和新建,而是在现有装置上完善生产工艺,加强设备改造,适当增加产量和品种;二是铝矿资源较丰富的国家引进国外先进技术建厂,发展本国格盐工业。
这两种模式都强调格盐生产工艺的先进性,据调查,国外铭盐生产已基本采用无钙焙烧工艺,排渣量少,通过工艺改进减少对环境造成的危害。
1.1.2国内趋势我国格盐工业起步于1958年,经历了40多年的曲折历程,随着国民经济的发展和世界铭盐需求增长的影响,呈现出蓬勃发展的态势。
规模由小到大,装备由落后到比较先进,由对环保的漠视到逐步意识到对企业生死攸关的影响,从盲目发展逐步过渡到有计划、有理性的控制发展。
据统计,我国目前铭盐生产厂为20家左右,2005年全国红矶钠的生产总量约26万吨,成为世界最大的格盐生产国。
但我国铝盐行业生产仍采用有钙焙烧老工艺,与国外相比,存在着生产厂点多、装置规模小、装备较差、生产工艺落后、环境污染较严重等问题,严重制约了格盐工业的健康发展。
有钙焙烧工艺因生产过程需添加大量钙质填料,造成吨红机钠铭渣排放量2~3吨左右,含钙格渣中有毒六价铝高达1~15%,并伴生致癌酸溶性六价铭(铭酸钙)难以解毒或利用。
目前国内格盐行业采用无钙焙烧工艺的只有年产量为1万吨的甘肃民乐化工厂,渣害问题成为我国格盐行业头等难题。
根据我国铝盐生产现状,国内现有生产能力加上改扩建能力已超过国内格盐消费的需要,不宜再布新点,老厂扩建也不应再走技术含量低的单纯扩大生产能力的老路。
重点应放在改革生产工艺,改进设备及提高自动化程度。
要重视引进国外先进技术,借鉴和吸纳国外先进铭盐生产经验,尽快改变我国格盐生产的落后面貌。
据统计,我国格渣堆积量已达400多万吨,引发严重公害,成为社会关注的焦点。
目前含格废气、废水的控制、回收和处理已取得较大进步,达到环保要求,但废渣由于受到有钙焙烧生产工艺的制约,其固有的污染问题无法从根本上解决,只有进行重大技术改造,走无钙焙烧清洁生产工艺路线,才可彻底消除格盐工业环境污染隐患。
有钙焙烧工艺存在着无法克服的严重污染问题,不符合国家环保政策,国家产业政策也明确规定要限制并逐步淘汰有钙工艺,鼓励无钙焙烧清洁生产技术的工业化应用。
只有大力推广清洁生产,减少污染物排放,才能从根本上扭转被动局面。
国家发改委和环保总局的发改环资[2005]2113号文中提出“鼓励开发资源利用率高、污染产生量少的无钙焙烧等清洁生产工艺技术”、“扶持无钙焙烧铝盐生产工艺技术完善”。
国家发改委40号令《产业结构调整指导目录(2005年本)》中也提出鼓励“用清洁生产技术建设和改造无机化工生产装置”,鼓励"尾矿、废渣等资源综合利用”,以及限制“单线2万吨/年以下或有钙焙烧辂化合物生产装置”的相关规定。
中国格盐工业大型化的同时,应推广采用新工艺,新技术,无钙焙烧工艺已是国内铝盐工业发展的必然趋势。
有钙焙烧属于高消耗、重污染型工艺路线,正在被低消耗、清洁型无钙焙烧工艺路线所取代。
从世界铝盐工业发展的趋势看,无钙焙烧工艺是国际通行,国家推进的清洁生产工艺。
1.2无钙焙烧工艺是振华公司生存与发展的必由之路格盐在我国国民经济中起着重要作用,近10年来,中国格盐生产迅猛发展,产量剧增,已成为格盐生产大国。
2001年我国铝盐产量统计见表6-1o表6-12001年我国主要厂家产量表由2001年全国统计数据可知,化工有限公司(原湖北黄石无机盐厂)在国内同行业中处于劣势。
经过振华公司不懈的努力,不断的进行工艺优化和技术开发,2003年年产量在全国铭盐行业排名提升至第四位,见表6.2。
表6-22003年我国主要厂铭盐产量表由表6-1和表6-2可以看出,与国外铭盐行业生产状况相比,我国铭盐生产厂家太多,规模太小,生产工艺几乎全部采用有钙焙烧,目前实行无钙焙烧工艺的只有甘肃民乐化工厂1万t/a规模的无钙焙烧示范装置,重庆民丰农化股份有限公司5万t/a的无钙焙烧新工艺生产装置正在投资建设中。
格盐环保问题,已成为格盐企业的生命线。
化工有限公司目前仍采用有钙焙烧,红机钠年产量为2.5万吨,铝渣年排放量约125万吨,厂区内现堆存有历年存渣14万吨。
面对国内铭盐行业发展“大型化、集中化、环保治理规范化”的方针政策,竞争、兼并、联合、优化组合、优胜劣汰的发展趋势,格盐生产要逐步达到国际认可和经验证明的规模经济一一5万t/a规模。
根据当前国家环保局和发改委对于铭盐行业的相关规定和要求,化工有限公司采用格铁矿无钙焙烧清洁生产工艺已是当前国内格盐行业健康稳定发展的必然趋势和形式所迫。
分析当前国内铭盐行业发展形势和振华公司目前所处局势,有限公司若采用5万t/a无钙焙烧清洁生产工艺装置,则在全国格盐行业排名中至少跃居第二;但若继续沿用企业现有生产装置,在大型化和优胜劣汰的必然发展趋势下,就只能在狭缝中求生存,公司将面临严峻的考验和被淘汰关停的威胁。
对于有限公司来说,焙烧工艺进行改革可谓是背水一战,势在必行,是企业可持续发展的必然要求。
因此,无钙焙烧工艺是振华公司生存与发展的必由之路。
1.3无钙焙烧的技术可行性无钙焙烧制红机钠清洁生产技术是天津化工研究院自1981年提出并开始研究的科技项目,1985年正式列为化工部研究课题,进行工艺条件试验(小试),1987〜1988年,由国家、企业共同筹资200万元在化工有限公司进行了300t∕a规模的无钙焙烧生产红矶钠新工艺的放大试验,打通了工艺流程,生产出了合格的红矶钠,1990〜1991年进一步做了添加促进造粒焙烧试验,提高了氧化率,缩短焙烧时间,1997年3000吨/年无钙焙烧生产红矶钠新工艺中间试验列入国家“九•五”重点科技攻关项目,2000年通过国家科技部委托国家石化工业局组织的专家现场考评。
2001年该项目荣获国家“九•五”科技攻关项目优秀成果奖。
国内格盐行业中甘肃民乐铭盐厂已采用了无钙焙烧工艺,国外工业发达国家格盐行业已全部采用无钙焙烧工艺生产红矶钠,实现了铝渣的减量化和资源综合利用。
无钙焙烧工艺技术已较为成熟。
无钙焙烧工艺的生产成本、产渣量等技术经济指标都明显优于有钙焙烧工艺,已成为重铭酸钠生产的主要发展趋势。
13.1无钙焙烧工艺流程格铁矿碱性氧化焙烧所用填料若含钙(白云石、生石灰、氧化钙等),称为有钙焙烧;若只用不含钙的返渣,则称为无钙焙烧。
无钙焙烧主要工艺流程为:格铁矿、返渣经烘干制粉与纯碱经计量后与窑灰混合均匀计量后进入回转窑进行高温碱性氧化焙烧,熟料经冷却后进入大槽浸取。
浸取用水为循环水或洗渣水,高浓度浸取水(碱性水)进入后工序,低浓度液循环使用,浸渣经湿磨机后先经螺旋分级机粗选,再经旋液器细分,粗浆经卧式离心选矿机洗涤过滤后与粗选渣一起作返渣,细浆经卧式离心选矿机洗涤过滤后作弃渣经解毒后综合利用,洗水均作浸取洗水回用。
后工段流程与有钙焙烧基本相同。
无钙焙烧工艺流程图见图6-1。
无钙焙烧工艺作为格盐行业的清洁生产工艺,具有工艺铝铁矿纯碱图67无钙焙烧工艺流程图1.3.2无钙焙烧技术可行性分析技术合理、资源有效利用率高等优势,其他工艺不可替代。
现将无钙焙烧和有钙焙烧从以下几个方面作对比进行技术可行性分析。
1反应原理格铁矿和纯碱以及填料发生的碱性氧化焙烧反应原理为:4(FeO e Cr2O3)+8Na2C03+702====8Na2CrO4+2Fe2O3+8CO2A1203+Si02+2Na2C03====2NaA102+Na2Si03÷2C02用回转窑焙烧格矿时,为了保证窑的正常运行,应控制炉料中熔液含量小于30%,否则炉料将严重烧结形成炉瘤甚至结圈,致使回转窑无法正常生产。
格铁矿碱性氧化焙烧的最高温度约1100℃,超过了炉料中纯碱和铭酸钠的熔点。
若炉料仅用铭矿和纯碱,其熔融物量超过30%,形成后结圈,无法运行。
(1)有钙焙烧工艺为保持良好的焙烧条件和较高的氧化率,添加大理石和白云石惰性钙质作为填料,使炉料在高温焙烧过程维持合适的熔融相比例,使回转窑正常运行。
但同时因加入的钙质填料使焙烧过程中的副反应一一水不溶性铭盐以铭酸钙等形式留存于铭渣中,致使吨产品的产渣量达2.5吨,且格渣难以解毒。
系统中游离氧化钙和其它副产物生成铭酸盐反应式:3MgCr20ι+9Ca0+302====9CaO∙4CrO3∙Cr2O3+3MgO 3FeCr2O t+9CaO+3.3∕402====9CaO∙4CrO3e Cr2O3+1.1∕2Fe203(2)无钙焙烧工艺是在不改变焙烧过程中熔融相比例、Cr2O3含量等表征特性前提下,通过调整工艺配料比和焙烧条件,控制温度在1150〜1200°C,使熟料在焙烧过程中生成大量铁酸镁这一耐高温惰性物质,同时生成铝硅酸镁钠,以改变铝渣物性,铝硅酸镁钠含硅铝且不溶于水,起到了固定硅铝作用,保证填料的重复循环使用性能。
浸出铭酸钠溶液后,铝渣经螺旋分级,含铁酸镁、铝硅酸镁钠高的粗粒格渣能代替全部钙质填料,含硅铝较高的细粒格渣外排,达到焙烧过程不从系统外引入钙质填料,吨产品外排格渣约为0.8t,仅为原料带入,大大降低排渣量,对环境影响降到最小,达到了清洁生产目的。
无钙焙烧利用焙烧过程中产生的铝硅酸镁钠代替系统外引入钙质填料,在技术原理上是可行的。
2.浸取工序对比分析有钙焙烧生成的钙化合物在焙烧时可起填料作用,但浸取时却产生多种不利副反应,形成辂铝酸钙(酸溶性六价铭)及多种水合钙盐,后者具有胶凝作用(水泥化),对溶液中六价格具有强烈吸附作用,且难以过滤洗涤,导致有钙焙烧浸取率低、浸取装置难以实现机械化操作。
无钙焙烧在配碱量超过理论量80%的条件下,格酸钠是熟料中仅有的六价格化合物,熟料浸取时铭酸钠也不同渣中任何杂质发生副反应,浸渣中的化合物在常压下均不水解,故无钙焙烧的浸取率超过99%o半工业试验时(抽滤盘内浸渣约It),浸渣含六价格(以C Q0∙3计)一般小于0.2随最低值为0.03%o3.各项技术指标对比分析现将国外无钙焙烧与企业有钙焙烧工艺原材料消耗等各技术指标进行比较,见表6-3。
表6-3企业有钙焙烧与国外无钙焙烧技术指标对比表由表可知,无钙焙烧可使红矶钠生产的铭渣排放量大大降低,格渣中有毒六价铝含量显著减少,因填料更替,铝渣不含致癌物格酸钙,利于资源化综合利用。