连续铸钢工艺篇BD
《连续铸钢》课件
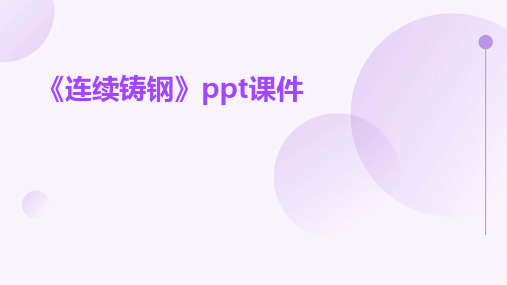
有色金属行业
连续铸钢也可用于生产 铜、铝等有色金属材料
。
机械制造行业
连续铸钢生产的钢材可 用于制造各种机械零件
和设备。
其他领域
连续铸钢还可应用于建 筑、石油、化工、航空
航天等领域。
02
连续铸钢工艺流程
钢水的准备
总结词
钢水准备是连续铸钢工艺流程的起始环节,其目的是确保钢 水具备合适的化学成分和温度,为后续工艺提供稳定的基础 。
智能化控制
通过智能化控制技术实现生产过程的 自动化和智能化,提高产品质量和降 低能耗。
拓展应用领域与市场
总结词
新材料领域
随着工业领域的发展和需求的不断变化, 连续铸钢技术的应用领域和市场也在不断 拓展。
连续铸钢技术在制造高性能、高强度材料 方面具有优势,可应用于航空航天、汽车 、高铁等领域。
新工艺领域
结晶器的选择与维护
总结词
结晶器是连续铸钢工艺中的重要设备,其选择和维护对铸坯的质量和连铸机的稳 定运行至关重要。
详细描述
根据铸坯的规格和材质,选择合适的结晶器材质和结构。同时,为确保结晶器的 使用寿命和减小能耗,需定期对结晶器进行维护和保养,如清洗、涂层保护和更 换等。
二次冷却工艺
总结词
二次冷却工艺是连续铸钢工艺中的关键环节之一,其目的是控制铸坯的冷却速度,进而影响铸坯的组织结构和机 械性能。
优化设备维护方案
制定科学合理的设备维护和保养方案,降低 维护成本。
提高操作人员素质
加强操作人员的培训和技能提升,提高操作 水平和应对能力。
灵活应对市场需求
加强市场调研和预测,灵活调整生产和销售 策略,应对市场需求波动。
04
连续铸钢的未来发展
炼钢连铸工艺流程的介绍

连铸工艺流程介绍将高温钢水浇注到一个个得钢锭模内,而就是将高温钢水连续不断地浇到一个或几个用强制水冷带有“活底”(叫引锭头)得铜模内(叫结晶器),钢水很快与“活底”凝结在 一起,待钢水凝固成一定厚度得坯壳后,就从铜模得下端拉出“活底”,这样已凝固成一 定厚度得铸坯就会连续地从水冷结晶器内被拉出来,在二次冷却区继续喷水冷却。
带有液 芯得铸坯,一边走一边凝固,直到完全凝固。
待铸坯完全凝固后,用氧气切割机或剪切机把 这种把高温钢水直接浇注成钢坯得新工艺,就叫连续铸钢。
炼后得钢水连续铸造成钢坯得生产工序,主要设备包括回转台.中间包•结品器、拉矫机等。
本专题将详细介绍转炉(以及电 炉)炼钢生产得工艺流程,主要工艺设备得工作原理以及控制要求等信息。
由于吋间得仓促与编辑水平有限,专题中难免出現 遗漏或緒误得地方,欢迎大家补充指正. 连铸得a 得:将钢水铸造成舸坯。
将装有精炼好钢水得钢包运至回转台,回转台转动到浇注位置后,將钢水注入中间包,中间包再由水口将钢水分配到各个结 晶器中去。
铸坯切成一定尺寸得钢坯。
回转塔 钢水包一 中间a电礒惑应搅拌器■-JL-支承导維冷却 嘴 【导读】:转炉生产出来得钢水经过精炼炉精炼以后,需要将钢水铸造成不同类型.不同规格得钢坯。
连铸工段就就是将精引锭轩n结晶器就是連铸机得核心设备之一,它使铸件成形并迅速凝固结晶•拉娇机与结晶振动您置共同作用,将结器内得铸件拉出,经冷却、电饌搅井后,切割成一定长度得板坯。
连铸钢水得准备连铸钢水得温度要求;钢水温度过高得危害;①出结晶器坯売萍,容易漏钢;②耐火材料侵蚀加快,易导致铸流失控,降低浇铸安全性;③增加非金属央杂■影响板坯内在质量;④铸坯柱状晶发达;⑤中心偏折加重.易产生中心线裂纹。
钢水温度过低得危害:①容易发生水口堵塞,浇铸中斷;②连铸表面容易产生结疱.夹渣、裂统等缺陷;③非金属央杂不易上浮,影响铸坯内在质量.二、钢水在钢包中得温度控制: 根据冶炼钢种严格控制出钢温度,使其在较窄得范囤内变化;其次,要最大限度地减少从出钢.钢包中.钢包运送途中及进入中间包得整个过程中得温降。
连续铸钢工艺教程
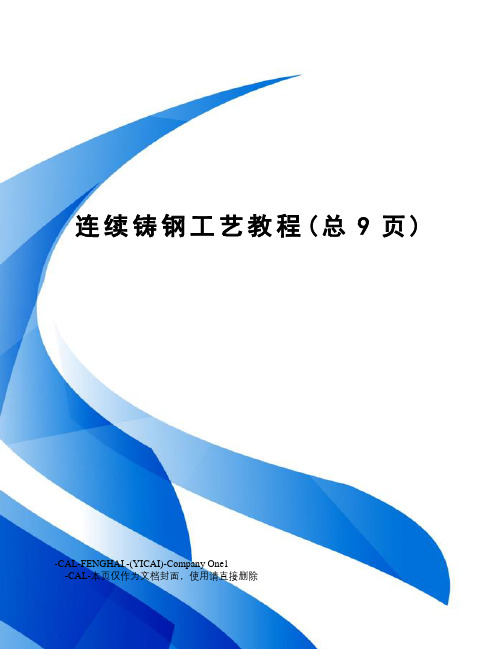
连续铸钢工艺教程(总9页) -CAL-FENGHAI.-(YICAI)-Company One1-CAL-本页仅作为文档封面,使用请直接删除连续铸钢工艺教程1.连铸工艺1.1连铸工艺介绍连铸全称连续铸钢,与模铸不同,它不是将高温钢水浇铸到一个个的钢锭模内,而是将高温钢水浇注到一个或几个用强制水冷、带有“活底”(叫引锭头)的铜模内(叫结晶器),钢水很快与“活底”凝结在一起,待钢水凝固成一定厚度的坯壳后,就从铜模的下端拉出“活底”,这样已凝固成一定厚度的铸坯就会连续不断地从水冷结晶器内被拉出来,,在二次冷却区继续喷水冷却,带有液芯的铸坯一边走一边凝固,直到完全凝固,待铸坯完全凝固后,用氧气切割或剪切机把铸坯切成一定尺寸的钢坯。
连铸是连接炼钢和轧钢的中间环节,是炼钢生产的重要组成部分,连铸生产的正常与否,不但会影响到炼钢生产任务的完成,还会影响到轧材的质量和成材率。
一台连铸机主要由大包回转台、中间包、中间包车、结晶器、结晶器振动装置、二次冷却装置、拉坯矫直装置、切割装置和出坯辊道等部分组成。
在连铸生产时通常用天车将钢包吊至大包回转台,然后大包转台将钢包旋至浇注位,经大包底部水口把钢水注入到中间包内,打开中间包塞棒后,钢水流入到下口用引锭杆堵塞并能上下振动的结晶器中,钢水沿结晶器周边冷凝成坯壳,当结晶器下端出口处坯壳有一定厚度时,带有液芯并和引锭杆连在一起的铸坯在拉矫装置的作用下,离开结晶器,沿着二冷段的支撑结构下移,与此同时铸坯被二次冷却装置进一步冷却并继续凝固,当引锭装置进入拉矫机后脱去引锭装置,铸坯在全部凝固或带有液芯的状态下被矫直,随后在水平位置被切割成定尺长度,经出坯辊道运送到规定地点,上述整个过程在实际生产中是连续进行的。
1.3连铸的主要设备1.3.1钢包回转台钢包回转台设置在电炉、精炼同一跨,它的本体是一个具有两个钢包支撑架的转臂,绕回转台中心回转,钢包回转台工作时,出钢跨一侧的天车将盛满钢水的钢包吊放到支撑架上,然后回转台旋转180o,将钢包转到连铸跨中间包上方的浇注位进行浇注,浇注完毕,再把空包转出的同时,又把另一个盛满钢水的钢包旋转到浇注位置,这样就可以快速更换钢包,实现多炉连浇。
连续铸钢工艺word文档良心出品

连续铸钢工艺1 、弧形连铸机有哪此特点? 立式和立弯式连铸机的结晶器都是直的, 而弧形连铸机采用的是具有某一曲率半径的弧形结 晶器, 其结晶器、 二次冷却装置都布置在某一半径的一个圆的四分之一弧度上。
铸坯在结晶器内凝固时就已弯曲,带液芯的铸坯从结晶器拉出来,沿着弧形轨道运行,继续喷水冷却, 在四分之一圆弧处完成凝固,然后矫直并拉出送至切割站。
弧形连铸机的高度仅为三分之一,建设费用低,钢水静压力小,铸坯在辊间的鼓肚小, 铸坯质量好;加长机身也比较容易,故可高速浇注,生产率高。
弧形连铸机的缺点是:因铸坯弯 曲矫直,容易引起内部裂纹;铸坯内夹杂物分布不均匀,内弧侧存在夹杂物的集聚;设备较为复杂,维修也较困难。
弧形连铸机虽有缺点, 但由于在设备和工艺上的技术进步, 仍然是世界各国钢厂采用最多的 一种机型。
2、 什么叫负滑脱?当结晶器下振的速度大于拉坯速度时, 铸坯对结晶器的相对运动为向上, 即逆着拉坯方向的 运动,这种运动称负滑脱或称负滑动。
3、 结晶器振动频率用什么数学模型控制? 对正弦式振动负滑脱率 £ v% Vmi-结晶器振动平均速度 m/min ;V —拉坯速度m/min 。
结晶器振动速度vm 可用下式表示Vm=( n fh/1000 )X sin2 n f式中:h —振幅mm由上式可求得结晶器振动的平均速度Vm=2fh将Vm 代入负滑脱率式中即可求得振动频率 f在连铸机中 £ v 皆取定值, 那么频率与拉速便成线性关系, 用这个关系式来控制随拉速变化 而变化的振动频率, 这个公式就是用负滑脱率控制振动频率的数学模型, 这个模型广泛应用 于国内外连铸生产中。
4、如何减小铸坯振痕?为了防止拉漏, 减小结晶器阻力,采取了结晶器振动技术,但是由于结晶器振动, 在铸坯表 面产生了横向痕迹,此痕迹称振痕,振痕为沟状,其间距h=v/f ,其中V 为拉坯速度,f 为振动频率。
研究表明, 振痕处易形成裂纹和成份的偏析, 随着振痕深度的加深而加重。
连续铸钢268页BD
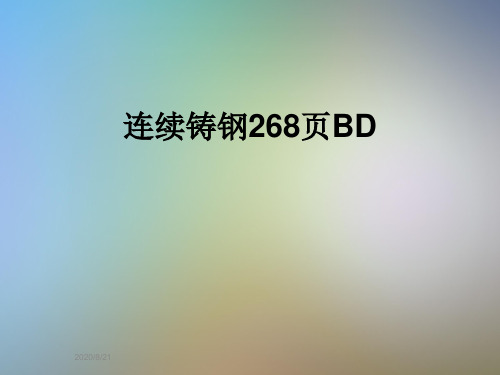
9.3.2 连铸工艺控制技术
1.中间包内钢水温度变化规律
中间包内钢水温度控制
2.中间包内钢水温降 主要取决于钢包及中间 包的热工状况。
中间包内钢水温度控制
3.浇注温度的确定
最大过热度的选取要根据钢种、铸坯断面 、浇注条件等因素确定。
注流控制与管理
1.中间包钢流 要求浇钢速率和拉速相适应,水口直径要与浇注 铸坯的钢水流量相配合。中间包流出钢水量为:
Mn/S25。
硫含量对钢延伸率的影响
9.3.1.2 连铸钢水成分控制
4)其它元素含量控制 含Ti不锈钢中的Ti、铝镇静钢中的Al,都极易发
生二次氧化,影响钢水的可浇性,需注意保护。 钢水中Cu0.2%,Sn0.02%。 5)连铸钢水脱氧控制 脱氧剂加入方法; 转炉挡渣出钢; 电炉偏心炉底出钢。
3.钢包内钢水加热调温 1)电弧加热法 如ASEA-SKF,VHD,VAD,LF等。 2)化学加热法 如RH-OB、CAS-OB、IR-UT等, CAS-OB吹氧4分,铝粉耗量
0.5Kg/t时,350吨钢包内钢水温 度可升高约20℃;
LF炉加热效果
连铸钢水温度调整
5.连铸中间包内钢水加热调温 加热方法有感应加热法和等离子加热法。 电磁感应加热,可使钢水温度相对稳定,且由于电磁搅拌的
9.3.3 连铸坯凝固与传热
一、连铸坯凝固传热特点 1.连铸坯的凝固过程就是一个传热过程
钢液固体+Q 单位重量钢水放出的热量Q包括:
连铸坯凝固与传热
连铸机可分为三个传热冷却区:
1)一次冷却区(结晶器) 2)二次冷却区(喷水区) 3)三次冷却区(空冷区)
从连铸机热平衡来看:
1)钢水从结晶器二冷区辐射区大约有60% 热量放出,铸坯才能完全凝固,这部分热量的放 出速度决定了铸机生产率和铸坯质量;
《连续铸造及其与轧制的衔接工艺》课件

1)连铸坯内部绝热技术和烧嘴加热技术相结合。 2)火焰切割机附近采用板坯边部加热装置。可采用电磁感应 加热或煤气烧嘴加热。
连续铸造及其与轧制的衔接工艺
1.3 连铸生产工艺 注意防止各种缺陷的产生,严格控制浇注温度,化学成分要求严格。控制
Mn/Si和Mn/S。 拉坯速度-重要的工艺参数。 根据钢种不同,控制二次冷却区的冷却强度,控制各种缺陷的产生。
连续铸造及其与轧制的衔接工艺
2连铸与轧制的衔接工艺 2.1钢坯断面规格及产量的匹配衔接
连续铸造及其与轧制的衔接工艺
1.1连续机类型 按铸坯断面形状分:厚板坯、薄板坯、大方坯、小方坯、
圆坯、异型坯、椭圆坯连铸机。 按铸坯运行轨迹分:立式、立弯式、垂直-多点弯曲式、
垂直-弧形、多半径弧形(椭圆形)、水平式、旋转式连 铸机。 1.2连铸机组成 钢水运转装置(钢水包、回转台)、中间包及更换装置、 结晶器及其振动装置、二冷区夹持辊及冷却水系统、拉引 矫直机、切断设备、引锭装置。
《连续铸造及其与轧制的衔 接工艺》
连续铸造及其与轧制的衔接工艺
1连续铸钢技术 将钢水连续注入结晶器,待钢水凝成硬壳后从结晶器出口
连续拉出或送出,经喷水冷却,全部凝固后切成坯料或直送 轧制工序。
(1)钢水在结晶器内得到迅速而均匀的冷却凝固,细晶 区较厚,柱状晶不发达。
连续铸钢工艺教程

连续铸钢工艺教程1.连铸工艺连铸工艺介绍连铸全称连续铸钢,与模铸不同,它不是将高温钢水浇铸到一个个的钢锭模内,而是将高温钢水浇注到一个或几个用强制水冷、带有“活底”(叫引锭头)的铜模内(叫结晶器),钢水很快与“活底”凝结在一起,待钢水凝固成一定厚度的坯壳后,就从铜模的下端拉出“活底”,这样已凝固成一定厚度的铸坯就会连续不断地从水冷结晶器内被拉出来,,在二次冷却区继续喷水冷却,带有液芯的铸坯一边走一边凝固,直到完全凝固,待铸坯完全凝固后,用氧气切割或剪切机把铸坯切成一定尺寸的钢坯。
连铸是连接炼钢和轧钢的中间环节,是炼钢生产的重要组成部分,连铸生产的正常与否,不但会影响到炼钢生产任务的完成,还会影响到轧材的质量和成材率。
一台连铸机主要由大包回转台、中间包、中间包车、结晶器、结晶器振动装置、二次冷却装置、拉坯矫直装置、切割装置和出坯辊道等部分组成。
在连铸生产时通常用天车将钢包吊至大包回转台,然后大包转台将钢包旋至浇注位,经大包底部水口把钢水注入到中间包内,打开中间包塞棒后,钢水流入到下口用引锭杆堵塞并能上下振动的结晶器中,钢水沿结晶器周边冷凝成坯壳,当结晶器下端出口处坯壳有一定厚度时,带有液芯并和引锭杆连在一起的铸坯在拉矫装置的作用下,离开结晶器,沿着二冷段的支撑结构下移,与此同时铸坯被二次冷却装置进一步冷却并继续凝固,当引锭装置进入拉矫机后脱去引锭装置,铸坯在全部凝固或带有液芯的状态下被矫直,随后在水平位置被切割成定尺长度,经出坯辊道运送到规定地点,上述整个过程在实际生产中是连续进行的。
连铸的主要设备1.3.1钢包回转台钢包回转台设置在电炉、精炼同一跨,它的本体是一个具有两个钢包支撑架的转臂,绕回转台中心回转,钢包回转台工作时,出钢跨一侧的天车将盛满钢水的钢包吊放到支撑架上,然后回转台旋转180o,将钢包转到连铸跨中间包上方的浇注位进行浇注,浇注完毕,再把空包转出的同时,又把另一个盛满钢水的钢包旋转到浇注位置,这样就可以快速更换钢包,实现多炉连浇。
连续铸钢质量篇

连续铸钢质量篇1. 引言连续铸钢是一种重要的钢铁生产工艺,它能够实现高效率的连续生产,同时具备优异的钢材质量。
本文将深入探讨连续铸钢质量的关键因素、常见问题以及解决方法。
2. 连续铸钢质量的关键因素连续铸钢质量的好坏取决于多个因素的综合影响。
以下是一些关键因素:2.1 铸造工艺铸造工艺是连续铸钢质量的基础。
合理的工艺流程可以确保熔池中的杂质被最大程度地剔除,并且保持合适的浇注速度和温度,以获得均匀的铸坯。
关键的铸造工艺参数包括浇注速度、结晶器摆动频率和角度等。
2.2 炉次管理炉次管理对连续铸钢质量的影响非常重要。
每个炉次的钢水温度、成分和浇注速度都需要仔细控制,以保证连续铸造的稳定性和一致性。
此外,炉次间的温度过渡也需要加以注意。
2.3 结晶器设计结晶器是连续铸钢中的关键组件之一。
合理的结晶器设计可以有效控制铸坯的凝固形态,避免出现过度凝固和偏析等问题。
优化结晶器的形状和尺寸,并采用适当的冷却水量,可以进一步提高连续铸钢的质量。
2.4 冷却条件冷却条件直接影响连续铸钢的凝固过程和组织形成。
合适的冷却速率可以避免组织异常和缺陷的产生。
调整冷却水量和冷却器的布置方式是改善冷却条件的常用方法。
2.5 管理与控制良好的管理和控制体系是确保连续铸钢质量的重要保证。
包括实时监测和控制系统、质量检测和控制手段、操作技术和培训等方面的工作。
3. 常见问题及解决方法在连续铸钢过程中,常会遇到一些质量问题。
下面列举了一些常见问题及相应的解决方法:3.1 出现通道疤通道疤是连续铸钢中的常见缺陷之一,它产生的原因多种多样,包括结晶器摆动不当、过度凝固等。
解决通道疤问题的方法通常有:调整结晶器摆动频率和角度,控制浇注速度和温度,改进冷却条件。
3.2 纵裂纵裂是连续铸钢中的另一个常见问题,它可能由于温度梯度过大、浇注速度过快等原因引起。
为了解决纵裂问题,可以通过优化冷却器布置、调整浇注速度和温度,以及合理控制结晶器的冷却水量等方法。
连续铸钢原理与工艺

连续铸钢原理与工艺连续铸钢是一种现代化的钢铁生产工艺,通过连续铸造设备将熔融的钢水连续地铸造成坯料,然后通过进一步的加工和处理,制成各种规格和型号的钢材产品。
本文将介绍连续铸钢的原理和工艺。
一、连续铸钢的原理连续铸钢的原理是基于连续铸造设备的运行机制。
在连续铸造设备中,钢水通过多孔陶瓷块或水冷铜管等冷却设备,进入到连续浇注器中,通过浇注器喷嘴喷射出来形成钢水流。
钢水流经过一系列的冷却装置,逐渐凝固成坯料,并通过一组辊道传送到下一道工序。
整个过程中,钢水的连续流动保证了钢水的连续铸造。
二、连续铸钢的工艺连续铸钢的工艺包括连铸准备、连铸浇注、坯料冷却和坯料切割等环节。
1. 连铸准备连铸准备包括预热连铸结构、浇注器和冷却设备的准备工作。
预热连铸结构是为了提高连铸结构的温度,以防止钢水凝固过早。
浇注器需要检查喷嘴的磨损情况,确保钢水能够均匀流出。
冷却设备的冷却水也需要进行检查和调整。
2. 连铸浇注连铸浇注是整个连续铸钢工艺的核心环节。
在连铸浇注过程中,钢水通过浇注器的喷嘴喷射出来,形成钢水流。
钢水流经过一系列的冷却装置,逐渐凝固成坯料。
冷却装置有助于提高坯料的质量和表面光洁度。
3. 坯料冷却坯料冷却是保证坯料质量的重要环节。
冷却装置中的冷却水通过坯料表面,吸收坯料的热量,使坯料逐渐冷却。
冷却水的温度和流量需要根据不同的钢种和坯料尺寸进行调整,以达到最佳冷却效果。
4. 坯料切割坯料冷却后,需要进行切割。
切割方式可以是机械切割或热切割。
机械切割适用于小型坯料,热切割适用于大型坯料。
切割后的坯料可以通过下一道工序进行进一步的加工和处理。
三、连续铸钢的优势连续铸钢相比传统的铸造工艺具有以下优势:1. 提高生产效率:连续铸钢工艺可以实现钢水的连续铸造,大大提高了生产效率。
相比传统的铸造工艺,连续铸钢的生产速度更快,能够满足大规模的钢材需求。
2. 降低能耗和排放:连续铸钢工艺在钢水连续铸造过程中,通过冷却装置吸收了大量的热量,减少了能耗和钢水的热量损失。
第六章 连续铸钢

坯辊道表面的垂直高度。H/D=25-40时,成为低头连铸机;
H/D<25时,则称为超低头连铸机。
水平连铸机
①特点:结晶器、二次冷却区、拉矫机、切割装置等设备 安装在水平位置上。中间包与结晶器是紧密相连的,相连处 装有分离环。拉坯时,结晶器不振动,而是通过拉坯机带 动铸坯做拉-反推-停不同组合的周期性运动来实现的。 ②优点:是高度最低的连铸机。设备简单、投资省、维护
1台连铸机有1个机组,又只能浇注1根铸坯,称为1机1流;若1台 连铸机有多个机组,又同时能够浇注多根铸坯,称其为多机多
流;1个机组能够同时浇注2根铸坯的称为1机2流。
三 弧形连铸机的主要设备
弧形连铸机工艺设备流程图
1—钢包 2—中间包 3—结晶器 4—二冷区 7—运送辊道 5—振动装置 6—铸坯 8—切割设备 9—拉坯矫直机
⑴长度:作为一次冷却,结晶器长度是一个非常重要的参 数。结晶器越长,在相同的拉速下,出结晶器坯壳越厚,浇铸 安全性更好。然而,结晶器过长,冷却效率就降低。目前世界 上通常采用的结晶器长度有两种,即700mm和900mm。高效 连铸机的结晶器长度为900mm比较合适。 ⑵结晶器倒锥度:结晶器铜板内腔必须设计成上大下小的形 状,即所谓的结晶器倒锥度。为什么?铸坯在结晶器内凝固
中间包是位于钢包与结晶器之间用于钢液浇
注的装臵,具有减压(减少钢液对结晶器的冲击
压力)、稳流(中间包可以保持一定的钢液深度,
攀钢1000~1100mm)、去渣(控制钢水流动
状态,有利于非金属夹杂物上浮)、储钢和分流 (将钢液分配给每个结晶器),在多炉连浇时起 承上启下作用 ,中间包冶金(将部分炉外精炼 手段移到中间包内实施)等重要作用。
方便。结晶器内钢液静压力最小,避免了铸坯的鼓肚变形, 中间包与结晶器之间是密封连接,有效地防止了钢液流动 过程的二次氧化;铸坯的清洁度高,夹杂物含量少,一般 仅为弧形连铸机的1/8-1/6。
铸钢工艺

课程结构第一章绪论和连铸生产概述一、连续铸钢工艺流程简述二、连铸与模铸的比较三、连铸生产正常化应具备的基本条件四、连续铸钢生产发展概况五、连续铸钢特点六、连铸机分类七、各类连铸机特点比较小结:第一章绪论和连铸生产概述一、连续铸钢工艺流程简述连续铸钢:把(一炉或多炉)高温钢水连续不断地浇铸成具有一定断面形状和一定尺寸规格铸坯的生产工艺过程。
工艺流程特点:铸坯能直接轧制成各种钢材构成:主体设备:浇注设备、LD、回转台、TD及小车、MD及振动装置、二次冷却支导装置、拉矫装置、切割装置等等。
一台连铸机组成:1)盛钢桶(盛钢桶支撑设备)2)中间包(中间包小车)3)结晶器(结晶器振动装置)4)二次冷却装置5)拉坯(娇直)装置6)切割装置(去毛刺装置)(喷印装置)7)铸坯运出装置等。
图1-1 带有直线段多半径弧形连铸机1-盛钢桶;2-中间包;3-结晶器;4-二次冷却;5-拉矫装置;6-切割装置;7-运胚和检验装置二、连铸和模铸的比较1)模铸工艺流程简述模铸:按炉将盛在盛钢桶内的钢水注入到具有一定形状和尺寸的钢锭模中铸成钢锭的浇注工艺。
特点:钢锭需经过初轧机轧制成钢坯,然后再进一步轧制成各种钢材。
2)连铸和模铸生产工艺比较图连铸具有的优越性:提高综合成材率;降低能耗;连铸产品的均一性高、质量好;易于实现机械化自动化。
三、连铸生产正常化应具备的基本条件完好的设备状态-实现连铸生产正常化的根本保证;完善的炼钢工艺-是连铸生产正常化的基础;科学的管理-是保证连铸生产的连续性和稳定性;高水平的人员素质-是搞好连铸生产的重要条件;同步发展新工艺新技术-满足连铸生产发展的需要。
四、连续铸钢生产发展概况五、连续铸钢特点(1)简化了钢坯生产的工艺流程,节省大量投资,省去了模铸工艺中脱模、整模、均热及初轧等工作。
(2)提高了金属收得率和成材率。
(3)提高了钢坯质量。
(4)改善了劳动强度,提高了劳动生产率,而且有助于铸钢生产的连续化和自动化。
2+连续铸钢与轧制的衔接工艺
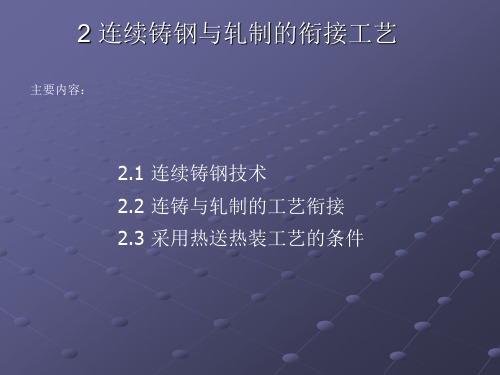
高温热装 低温热装 ( 400℃ 低温界限)
5、常规冷装炉轧制工艺
2.2.2薄板坯连轧连轧CSP工艺(连铸坯直接轧制工艺 )
2.2.3 2.2.3线、棒材车间典型的热装工艺布置(高、低温热装工艺)
采用热装热送工艺的优点:
(1)减少能源消耗、提高加热炉产量。(燃料消耗降低40%~67%,加热炉产 量提高20%~30%) (2)减少金属消耗(加热时间,金属损耗降0.3%) (3)降低建设投资、生产成本(厂房面积、起重设备、钢坯存量、人员) (4)缩短生产周期 (6)轧钢车间生产管理概念的革新、生产更灵活(按规格组织生产——》按钢 种组织生产)
2 连续铸钢与轧制的衔接工艺
主要内容:
2.1 连续铸钢技术 2.2 连铸与轧制的工艺衔接 2.3 采用热送热装工艺的条件
ห้องสมุดไป่ตู้
2.1 连续铸钢技术 什么是连续铸钢?
连铸是把液态钢用 连铸机浇注、冷凝、 连铸机浇注、冷凝、 切割而直接得到铸坯 的工艺, 的工艺,它是连接炼 钢和轧钢的中间环节。 钢和轧钢的中间环节。
5、电磁搅拌 :均匀成分、细化晶粒,加速铸坯凝固,使气体和夹杂 上浮 。 6、多点矫直和压缩浇注 :防止内外裂纹
2.2 连铸与轧制的工艺衔接
2.2.1 连铸-连轧衔接模式
1‘、连续铸轧 1、连铸坯直接轧制工艺 2、连铸坯A3线以上温度装炉 (热送直接轧制) 3、A3线A1线之间温度装炉 (直接热装轧制工艺) 4、A1线以下到400℃温度装 炉(热装轧制)
弧形连铸机工艺示意图
6、引锭装置 7、铸坯切割设备:定尺、火焰切割、液 压或摆动剪
铸坯鼓肚变形示意图
2.1.3 连铸生产工艺
连铸工艺必须保证铸坯的质量和产量, 连铸坯常见的缺陷有: 表面缺陷 内部缺陷 形状缺陷
连续铸钢生产

圆 坯 连
为40—80M的薄板坯料)等。
铸
机
方坯连铸机
D连铸生产过程
送、冷却等作业。连铸机设备部分的内容将在
“连铸设备与操作”课程中作详细介绍。
b 连铸机可以按多种方法进行分类:
• 连铸机可以按多种方法进行分类:
• (1)按结晶器的运动方式,连铸机可分为 固定式(即振动式)和移动式两类。前者是现 在生产上常用的以水冷、底部敞口的铜质 结晶器为特征的“常规”连铸机;后者是 轮式、轮带式等结晶器随铸坯一起运动的 连铸机。
• 中间包运载装置有中间 包车和中向包回转台, 它是用来支撑、运输、 更换中间包的设备。
•
• 结晶器是一个特殊的水冷钢模,钢液在结 晶器内冷却、初步凝固成形,并形成一定 的坯壳厚度,以保证铸坯校拉出结晶器时, 坯壳不被拉漏、不产生变形和裂纹等缺陷。 因此它是连铸机的关键设备。
• 结晶器振动装置是使结晶器能 按一定的要求做上下往复运动 以防止初生坯壳与结晶器粘连 而被拉裂。
引锭装置包括引锭头和引锭杆两部分,它的作用是
在开浇时作为结晶器的“活底”,堵住结晶器的
下口,并使钢液在引锭杆头部凝固:通过拉矫机
的牵引.铸坯随引锭杆从结晶器下口拉出。当引
锭杆拉出拉矫机后,将引锭杆脱去.进入正常拉
坯状态。
的作用是在铸坯行进过程中,
将它切割成所需要的定尺长度。铸坯运出装置包
括辊道、推钢机、冷床等,由它们完成铸坯的输
大于150mmx150mm叫大方坯;
机
矩形断顶的长边与宽边之比小
于3的也称为方坯连铸机):板
坯连铸机(铸坯断面为长方形,
其宽厚比一般在3以上):圆坯
连铸机(铸坯断面为圆形.直径
60—400);异形坯连铸机(浇注
连续铸钢

38
结晶器运动
39
结晶器的振动参数
周期:结晶器上下振动一次的时间为振动的周期 频率:结晶器每分钟振动的次数
振幅:结晶器从水平位置运动到最高或最低位置所移动的距离
40
5、二次冷却
41
二次冷却区简介
钢液进入结晶器之后,在水冷结晶器的作用下,凝固 成具有一定形状和厚度的坯壳。 一般地,钢液在结晶器里冷却成具有一定厚度坯壳的 过程称为一次冷却;坯壳出结晶器之后受到的冷却称 为二次冷却。 由于钢液熔点高,热容量大而导热性差,经过一次冷 却后,铸坯虽然已经成形,但其坯壳较薄,只有10~ 20mm,如果这种带液芯的铸坯不继续冷却和采用一 定方式支撑。那么,带液芯的高温铸坯在钢液静压力 下就会产生变形,甚至漏钢,所以,还必须对铸坯进 行一次强制冷却。二次冷却装置就是在结晶器之后, 对铸坯进行第二次冷却和支撑的装置。
L=(d/K)2 Vc
从钢液面到结晶器顶面一般留100mm,故实际结晶器长度 =L+100 ; 板坯结晶器长度在900~1000mm,小方坯结晶器长度在 800~900mm左右。
35
结晶器锥度
方坯: = (S1-S2)/S1×100% 板坯: = (L1-L2)/L1×100%
锥度过小,坯壳过早脱离结晶器壁,影响传热; 锥度过大,摩擦阻力增加,加速结晶器磨损; 根据经验: 方坯结晶器锥度取0.6~0.9%, 板坯结晶器锥度取0.9~1.05%。
1. 2. 3. 4. 5.
增加产量 提高钢收得率 降低能耗 降低生产成本(设备、人工等) 质量提高
11
连铸机主要类型
• •• •• • 有利于夹杂物上浮; 较弧形铸机夹杂物上浮好; 无弯曲、矫直形变; 内部缺陷少(凝固后弯曲、矫直); 铸机高、钢水静压力大、生产率低; 厂房高、铸机长等问题 。
新编连续铸钢手册 01第一篇 总论

表 1-3 20 世纪 70 年代大型转炉炼钢厂实现全连铸工厂
国别 工厂名
投产 年份
美国
麦克劳斯公司特 伦顿厂
1969
机型 铸机数 流 弧形 4 双流
铸坯断面 mm 230×(910~1524)
转炉 年产量 数量×吨位 万 t
5×110t 240
法国
敦刻尔克厂二转 炉车间
1972
弧形
3 双流
250×1650
追溯连铸技术发展的进程,大致可以分为以下几个阶段。
1.1 世界连续浇铸技术的发展经历 1.1.1 连续浇铸方法的提出
最早提出将液态金属连续浇铸成形的设想可追溯到 19 世纪 40 年代,1840 年美国的塞 勒斯(G.. E. Sellers),1843 年莱恩(J. Laing)以及 1846 年英国的贝赛麦(H. Bessemer)提 出了各种连续浇铸有色金属的方法,贝赛麦获得用双辊法浇铸可锻铸铁的专利(1856 年), 在 20 世纪 30 年代以前连续浇铸只是在有色金属中应用,例如低熔点金属铅、锌,也有用于 浇铝、铜的。
表 1-2 世界主要工业国 1970-1980 年间连铸坯产量与连铸比上升情况
国家
连铸增长
1970 年
连铸坯产量 万t
连铸比 %
1980 年
连铸坯产量 万t
连铸比 %
连铸坯平均年增长量 万t
连铸比平均年增长 %
日本 527 5.6 6627.1 59.5 610.0 5.39
德国 372.6
8.3 2016.2 46.0 164.4 3.77
由德国人德伦提出立式连铸机的雏形和 S. 容汉斯的结晶器振动技术组合。在 1933 年 容汉斯在德国建成一台浇铸黄铜的立式连铸机,并取得成功。1943 年容汉斯又建了一台浇 钢的试验机组,第二次世界大战结束,世界各主要工业国都对连铸技术进行研究,在 1946~ 1947 年间,第一批连续铸钢试验装置分别建于美国的巴布考克和威尔考克斯公司(Babcock & Wilcox)、英国的劳莫尔公司(Low Maor)、日本尼崎钢管厂,以后奥地利的布雷坦费尔 德钢厂、英国钢铁学会(BISRA)和美国阿·勒德隆(Alleghenyludlum)钢公司都建设了试 验设备。在此基础上,第一台生产型立式连续铸钢机于 1950 年在德国曼内斯曼(Mannesman) 建成。随后,1951 年原苏联红十月冶金厂建成一台浇铸不锈钢的立式半连续铸机,往后英 国巴路厂(Barrow)、加拿大阿特拉斯厂都建造立式连铸机,中国也于 1958 年在重庆第三钢 铁厂建成一台工业生产用双流矩形坯立式连铸机,当时德国、苏联是建设立式连铸机的积极 者。
新编连续铸钢手册 01第一篇 总论

1.1.3 弧形连铸机的问世和发展(20 世纪 60 年代)
检测自控项目扩展和使用面广,如:钢流下渣检测、结晶器液面自动控制、二冷动态控 制、铸坯定尺优化切割、漏钢预报、铸坯质量在线判定和控制、无缺陷坯生产技术。计算机 的介入不仅为自动控制提供了方便,并为监测、数据收集分析、前后工序的联系,建立生产 过程控制系统,包括冶炼、连铸、轧钢一体化以及质量保证体系在内的过程控制系统。
追溯连铸技术发展的进程,大致可以分为以下几个阶段。
1.1 世界连续浇铸技术的发展经历 1.1.1 连续浇铸方法的提出
最早提出将液态金属连续浇铸成形的设想可追溯到 19 世纪 40 年代,1840 年美国的塞 勒斯(G.. E. Sellers),1843 年莱恩(J. Laing)以及 1846 年英国的贝赛麦(H. Bessemer)提 出了各种连续浇铸有色金属的方法,贝赛麦获得用双辊法浇铸可锻铸铁的专利(1856 年), 在 20 世纪 30 年代以前连续浇铸只是在有色金属中应用,例如低熔点金属铅、锌,也有用于 浇铝、铜的。
由德国人德伦提出立式连铸机的雏形和 S. 容汉斯的结晶器振动技术组合。在 1933 年 容汉斯在德国建成一台浇铸黄铜的立式连铸机,并取得成功。1943 年容汉斯又建了一台浇 钢的试验机组,第二次世界大战结束,世界各主要工业国都对连铸技术进行研究,在 1946~ 1947 年间,第一批连续铸钢试验装置分别建于美国的巴布考克和威尔考克斯公司(Babcock & Wilcox)、英国的劳莫尔公司(Low Maor)、日本尼崎钢管厂,以后奥地利的布雷坦费尔 德钢厂、英国钢铁学会(BISRA)和美国阿·勒德隆(Alleghenyludlum)钢公司都建设了试 验设备。在此基础上,第一台生产型立式连续铸钢机于 1950 年在德国曼内斯曼(Mannesman) 建成。随后,1951 年原苏联红十月冶金厂建成一台浇铸不锈钢的立式半连续铸机,往后英 国巴路厂(Barrow)、加拿大阿特拉斯厂都建造立式连铸机,中国也于 1958 年在重庆第三钢 铁厂建成一台工业生产用双流矩形坯立式连铸机,当时德国、苏联是建设立式连铸机的积极 者。
- 1、下载文档前请自行甄别文档内容的完整性,平台不提供额外的编辑、内容补充、找答案等附加服务。
- 2、"仅部分预览"的文档,不可在线预览部分如存在完整性等问题,可反馈申请退款(可完整预览的文档不适用该条件!)。
- 3、如文档侵犯您的权益,请联系客服反馈,我们会尽快为您处理(人工客服工作时间:9:00-18:30)。
abv C d 2 2gh
4 d 4abv
C 2gh
注流控制与管理
2.中间包钢流的保护 1)气封式保护
2)浸入式水口保护
浇注工艺操作ຫໍສະໝຸດ 1.拉速确定 ①按结晶器出口处坯壳厚度计算
min K m
t m Km
L V
V
L
Km min
2
②按铸机冶金长度计算
D K 2
2.铸坯冷却控制
1)结晶器坯壳凝固 特征
凝固过程中,角 部首先产生气隙, 逐渐向中部扩展, 所以角部的坯壳最 薄。
浇注工艺操作
2.二次冷却
1)冷却强度
钢种类别 冷却强度l/kg
普碳钢、低合金钢 1.0-1.2
中高碳钢、合金钢 0.6-0.8
裂纹敏感性强的钢 0.4-0.6
高速钢 0.1-0.3
2)冷却水分配 铸坯凝固时,凝固前沿放出潜热,
3.钢包内钢水加热调温 1)电弧加热法 如ASEA-SKF,VHD,VAD,LF等。 2)化学加热法 如RH-OB、CAS-OB、IR-UT等, CAS-OB吹氧4分,铝粉耗量
0.5Kg/t时,350吨钢包内钢水温 度可升高约20℃;
LF炉加热效果
连铸钢水温度调整
5.连铸中间包内钢水加热调温 加热方法有感应加热法和等离子加热法。 电磁感应加热,可使钢水温度相对稳定,且由于电磁搅拌的
包衬温度对热流速度的影响
连铸钢水温度调整
连铸钢水温度调整是指在包内进行的温度矫正,包括 两种情况:
1)对包内钢水温度的不均匀性进行正常调整; 2)对包内钢水温度偏高或偏低进行的应急调整。 1.钢包吹气搅拌调温
冶金效果
吹气搅拌的冶金效果
连铸钢水温度调整
2.加废钢调温 钢水温度偏高,可在吹气搅拌的同时加入轻型废钢降温。 钢水每降低1℃,需加废钢0.7Kg/t钢。
作用,还可使钢中夹杂物上浮。 利用等离子加热,可以把整个浇注过程中钢水温度波动控制
在±5℃以内,且不产生增碳和三氧化二铝夹杂污染钢水的 问题。但有增氮的趋势。 9.3.1.2 连铸钢水成分控制 连铸对钢水质量的要求: ①成分稳定性(多炉连浇); ②钢水可浇性(流动性); ③抗裂纹敏感性; ④纯净性;
L V'
V' 4L K 2 D
浇注工艺操作
③按以下经验公式计算
铸坯断面周长
V f L S
铸坯断面面积
小方坯 f 65 100, 小方坯 f 55 75,
圆坯 f 45 60, 板坯 f 55 80
小断面取上限,大断面取下限。
V 0.118(1 B) dB
B是铸坯宽厚比
浇注工艺操作
Mn/S25。
硫含量对钢延伸率的影响
9.3.1.2 连铸钢水成分控制
4)其它元素含量控制 含Ti不锈钢中的Ti、铝镇静钢中的Al,都极易发
生二次氧化,影响钢水的可浇性,需注意保护。 钢水中Cu0.2%,Sn0.02%。 5)连铸钢水脱氧控制 脱氧剂加入方法; 转炉挡渣出钢; 电炉偏心炉底出钢。
9.3.2 连铸工艺控制技术
1.中间包内钢水温度变化规律
T ' Tmax Tmin 实施( Tmax 0, T‘ 0)浇注技术
中间包内钢水温度控制
2.中间包内钢水温降 主要取决于钢包及中间 包的热工状况。
中间包内钢水温度控制
3.浇注温度的确定
Tc Tl Tmax
最大过热度的选取要根据钢种、铸坯断面、 浇注条件等因素确定。
连铸对钢水的要求: 1)高温;2)稳定;3)均匀 故为确定合适的浇注温度,需知道各个阶段的 温度损失,多采用现场统计方法。
连铸钢水温度控制
1)出钢过程温降 2)钢包内温降 3)注流温降 4)中间包温降
影响因素: 钢流辐射热损失; 包衬传导热损失; 钢流对流热损失;
钢包容量和加入铁合金数 量。
钢水浇注温度 T t出钢 t过程 t液相
9.3 工 艺 篇
9.3.1 连铸钢水的准备 9.3.2 连铸工艺控制技术 9.3.3 连铸坯凝固与传热 9.3.4 连铸保护渣
9.3.1 连铸钢水的准备
对钢水温度进行准确控制以及成分控制、脱氧 控制及净化处理等。 9.3.1.1 连铸钢水温度控制
提供合格钢水的基本参数之一,是保证合理的 浇注温度。若浇注温度过低,易引起中包水口冻 结,迫使浇注中断;太高,易引起钢包水口失控, 坯壳减薄,造成漏钢。
1
Lf
m
dS dt
二次冷却
凝固潜热传至铸坯表面被二冷水带走,
Lf
m
dS dt
m (TL TS )
S
积分 S
m (TL TS ) Lf m
tl t0
tl Ci
%Ci
t过程 t1 t2 t3 t4 t5
钢水浇注温度确定
钢水浇注温度确定
浇注钢种 高碳钢、高锰钢
板坯、大方坯 +10℃
合金结构钢
+5~10℃
铝镇静钢、低合金钢 +15~ 20℃
不锈钢
+15~ 20℃
硅钢
+10℃
小方坯
+15~ 20℃ +15~ 20℃ +25~ 30℃ +20~ 30℃ +15~ 20℃
连铸钢水温度控制要点
1.连铸钢水温度控制着眼点 连铸工艺要求钢水出钢温度高、浇注温度范围窄,使控 制难度增加。
着眼点:1)尽可能减少过程温降; 2)提高出钢温度命中率。
2.稳定转炉出钢温度要点 保证入炉原料成分稳定和数量准确,吹炼条件相对稳定。
3.减少和稳定过程温降要点 1)钢包加砌绝热层,减少包衬散热损失; 2)加速钢包周转和包衬高温烘烤,实现“红包出钢”; 3)钢包以滑动水口或旋转水口取代塞棒水口; 4)钢包内液面保温(如加碳化稻壳),减少散热损失; 5)钢包加盖。
9.3.1.2 连铸钢水成分控制
1)碳含量控制 多炉连浇要求,各炉、包次之间钢水含碳量的差别
<0.02%,碳对钢的热裂纹敏感性有重要影响。 2)Si、Mn含量控制 Mn/Si比提高,可改善钢水的流动性,同时可避开
碳的热裂纹敏感区。
9.3.1.2 连铸钢水成分控制
3)S、P含量控制 S对钢的热裂纹敏感性有突出影响,一般要求
注流控制与管理
1.中间包钢流 要求浇钢速率和拉速相适应,水口直径要与浇注 铸坯的钢水流量相配合。中间包流出钢水量为:
Q C d 2 2gh
4
其中: C - 流量系数 0.97 - 0.86(镇静钢) 水口初始截面的变化系数
对硅钢、高碳、锰钢,取上限; 流动性差的低碳铝镇钢,取下限。
注流控制与管理