金属材料 磨损试验方法
摩擦磨损性能测试试验
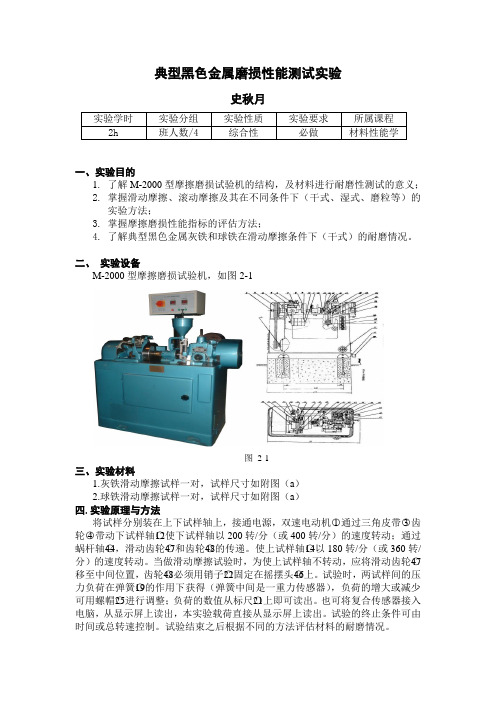
典型黑色金属磨损性能测试实验史秋月实验学时实验分组实验性质实验要求所属课程2h 班人数/4 综合性必做材料性能学一、实验目的1.了解M-2000型摩擦磨损试验机的结构,及材料进行耐磨性测试的意义;2.掌握滑动摩擦、滚动摩擦及其在不同条件下(干式、湿式、磨粒等)的实验方法;3.掌握摩擦磨损性能指标的评估方法;4.了解典型黑色金属灰铁和球铁在滑动摩擦条件下(干式)的耐磨情况。
二、实验设备M-2000型摩擦磨损试验机,如图2-1图2-1三、实验材料1.灰铁滑动摩擦试样一对,试样尺寸如附图(a)2.球铁滑动摩擦试样一对,试样尺寸如附图(a)四.实验原理与方法将试样分别装在上下试样轴上,接通电源,双速电动机○1通过三角皮带○3齿12使下试样轴以200转/分(或400转/分)的速度转动;通过轮○4带动下试样轴○48的传递。
使上试样轴○14以180转/分(或360转/47和齿轮○蜗杆轴○44,滑动齿轮○分)的速度转动。
当做滑动摩擦试验时,为使上试样轴不转动,应将滑动齿轮○47移至中间位置,齿轮○48必须用销子○22固定在摇摆头○46上。
试验时,两试样间的压力负荷在弹簧○19的作用下获得(弹簧中间是一重力传感器),负荷的增大或减少21上即可读出。
也可将复合传感器接入可用螺帽○25进行调整;负荷的数值从标尺○电脑,从显示屏上读出,本实验载荷直接从显示屏上读出。
试验的终止条件可由时间或总转速控制。
试验结束之后根据不同的方法评估材料的耐磨情况。
五、实验内容将加工好的滑动摩擦试样装在实验机上,在给定的条件下(干式、滑动摩擦、压力:200N、时间60min)进行试验,试验结束后将试样取下,评估耐磨性能。
根据所选取磨损试验方法的不同以及材料本质的差异,可以选择不同的耐磨性能评定方法,以期获得精确的试验数据,现简单例举下述几种方法以供参考。
1、称重法:采用试样在试验前后重量之差,本表示耐磨性能的方法,由于两试样之间的摩擦所引起的磨损量,可以采用精度达万分之一的分析天平称量出试样试验前后重量之差非凡获得。
摩擦磨损试验标准(一)
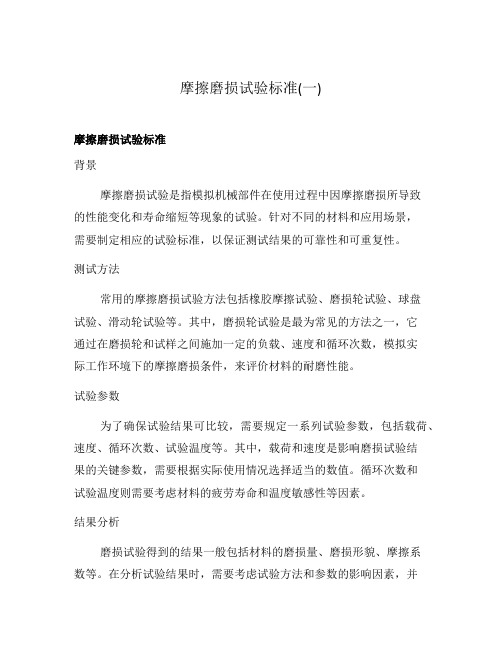
摩擦磨损试验标准(一)摩擦磨损试验标准背景摩擦磨损试验是指模拟机械部件在使用过程中因摩擦磨损所导致的性能变化和寿命缩短等现象的试验。
针对不同的材料和应用场景,需要制定相应的试验标准,以保证测试结果的可靠性和可重复性。
测试方法常用的摩擦磨损试验方法包括橡胶摩擦试验、磨损轮试验、球盘试验、滑动轮试验等。
其中,磨损轮试验是最为常见的方法之一,它通过在磨损轮和试样之间施加一定的负载、速度和循环次数,模拟实际工作环境下的摩擦磨损条件,来评价材料的耐磨性能。
试验参数为了确保试验结果可比较,需要规定一系列试验参数,包括载荷、速度、循环次数、试验温度等。
其中,载荷和速度是影响磨损试验结果的关键参数,需要根据实际使用情况选择适当的数值。
循环次数和试验温度则需要考虑材料的疲劳寿命和温度敏感性等因素。
结果分析磨损试验得到的结果一般包括材料的磨损量、磨损形貌、摩擦系数等。
在分析试验结果时,需要考虑试验方法和参数的影响因素,并结合实际使用环境进行评价。
此外,还需要注意试验误差的来源和限制,以确保结果的准确性和可靠性。
结论摩擦磨损试验标准是保证材料质量和性能的重要手段。
制定合理的试验方法和参数,准确分析试验结果,才能为实际应用场景提供可靠的参考数据。
因此,需要各行业相关专家和企业共同努力,不断完善和优化试验标准,推动材料科学和工程应用的发展。
不同产业的试验标准按照不同的产业领域和产品类型,摩擦磨损试验标准也有所不同。
以机械制造业为例,国际标准组织 ISO 发布了多项与摩擦磨损有关的标准,如 ISO 7148-2:1988 金属材料光洁度和粗糙度的测量和评价—第2部分:微表面形状的术语和 ISO 11505-2003 摩擦材料—旋转圆盘方法下生成的磨损方法。
而在汽车、建筑、航空等领域,也都有相应的标准适用于材料摩擦磨损性能的评价,并针对不同测试参数和环境规定了详细的规程和操作要求。
摩擦磨损试验设备进行摩擦磨损试验需要用到专门的设备和仪器,包括磨损仪、磨耗测试机、滑动磨损试验机等。
耐磨测试标准

耐磨测试标准耐磨测试是评估材料表面耐磨性能的重要手段,通过测试可以了解材料在受到摩擦、磨损等作用下的耐久性能,为材料的选择和设计提供依据。
耐磨测试标准是指对材料进行耐磨性能测试时所需遵循的一系列规范和要求,其制定的目的是为了保证测试结果的准确性和可比性。
本文将介绍一些常见的耐磨测试标准及其相关内容。
一、耐磨测试方法。
1. 磨损试验机方法,使用磨损试验机进行测试,根据不同的测试要求和材料特性,可以采用不同的测试方法,如滑动磨损测试、磨粒磨损测试等。
2. 磨损试验片方法,将被测材料制成试验片,在实验装置中进行磨损试验,通过对试验片的质量损失或者磨损痕迹进行分析,评估材料的耐磨性能。
3. 地面材料耐磨试验方法,主要用于评估地面材料的耐磨性能,包括耐磨地砖、地板材料等,通过模拟实际使用条件进行测试,评估材料的耐磨性能。
二、常见的耐磨测试标准。
1. ASTM G65-04标准,适用于金属材料的耐磨性能测试,采用干砂磨损试验方法,评估金属材料的耐磨性能。
2. ASTM G132-96标准,用于评估非金属材料的耐磨性能,通过旋转圆盘试验机进行测试,评估非金属材料的耐磨性能。
3. GB/T 1689-1998标准,适用于塑料、橡胶等材料的耐磨性能测试,通过滑动磨损试验机进行测试,评估材料的耐磨性能。
4. ISO 4649-2010标准,用于评估橡胶和橡胶制品的耐磨性能,采用滑动磨损试验方法,评估橡胶材料的耐磨性能。
5. DIN 53516标准,适用于橡胶材料的耐磨性能测试,通过橡胶磨损试验机进行测试,评估橡胶材料的耐磨性能。
三、耐磨测试标准的意义。
耐磨测试标准的制定和遵循对于材料的研发、生产和应用具有重要意义。
首先,标准化的测试方法和程序可以保证测试结果的准确性和可比性,为材料的评估和比较提供了依据。
其次,标准化的测试方法可以促进不同实验室和单位之间的技术交流和合作,推动行业的发展和进步。
最后,耐磨测试标准的制定可以规范行业内的测试行为,提高测试的科学性和规范性,为材料的质量控制和产品的设计提供支持。
金属摩擦磨损 国标

金属摩擦磨损国标摩擦磨损是指两个物体在相对运动中由于表面接触产生的能量损失以及表面损伤。
在工程应用中,特别是机械设计中,了解金属摩擦磨损是非常重要的。
准确的评估和控制摩擦磨损可以延长金属部件的寿命,提高设备的可靠性和效率。
为了实现这一目标,许多国家都制定了针对金属摩擦磨损的国家标准。
我国国家标准中,关于金属摩擦磨损的评估主要包括以下几个方面:磨损试验方法、磨损量的测定和摩擦磨损机理分析。
首先,磨损试验方法是评估金属摩擦磨损性能的重要手段之一。
根据不同的应用场景和测试要求,可以选择不同的试验方法。
例如,常用的试验方法包括滑动磨损试验、滚动磨损试验和撞击磨损试验等。
这些试验方法可以模拟不同形式和工况下的摩擦磨损情况,进而评估材料的耐磨性能。
其次,磨损量的测定是评估金属摩擦磨损性能的关键环节之一。
国家标准对磨损量的测定方法进行了详细规定,以确保测定结果的准确性和可比性。
常用的磨损量测定方法包括质量损失法、体积损失法和表面形貌观察法等。
这些方法通过定量或定性地描述金属表面的损伤程度,为后续的性能评估提供了基础数据。
最后,摩擦磨损机理分析是深入理解金属摩擦磨损行为的关键。
国家标准对摩擦磨损机理的分析提出了相应的要求。
通过对试验结果的分析以及金属材料的组织结构和性能等因素的综合考虑,可以揭示摩擦磨损的本质规律,为材料的选择和改进提供理论依据。
除了以上三个方面的内容外,国家标准还涉及到材料的分类和标记、试样制备和试验条件的规定等。
这些规定和要求为金属摩擦磨损的评估和控制提供了指导。
总之,国家标准对金属摩擦磨损的评估内容十分详细和全面。
通过遵循国家标准,可以实现对金属摩擦磨损性能的准确评估,并在工程设计和材料选择等方面提供有力支持。
然而,由于不同应用环境下的摩擦磨损条件各异,国家标准并不能完全满足所有实际需求。
因此,在具体应用中,需要结合实际情况并参考相关标准,灵活选择和调整评估指标和方法,以达到更好的评估效果。
金属的摩擦磨损实验

金属的摩擦磨损实验
金属的摩擦磨损实验是一种实验方法,用于研究金属材料在摩擦过程中的行为和性能。
该实验的目的是了解金属材料的摩擦系数、磨损率、耐久性以及在不同环境下的性能表现。
在金属的摩擦磨损实验中,通常采用滑动摩擦、滚动摩擦或冲击摩擦等实验条件,并采用各种摩擦磨损试验机进行测试。
根据实验要求,可以选择不同的试验机,如磨损试验机、往复摩擦试验机、滚动摩擦试验机等。
在实验过程中,需要测量金属材料的摩擦系数和磨损率。
摩擦系数是指材料在摩擦过程中所受的摩擦力与压力之比,反映了材料在摩擦过程中的润滑性能和耐磨性。
磨损率则是指材料在摩擦过程中损失的质量或体积与摩擦距离或时间的比值,反映了材料的耐久性和可靠性。
此外,在金属的摩擦磨损实验中,还需要考虑温度、湿度、载荷、速度等实验参数对金属材料性能的影响。
通过调整实验参数,可以研究金属材料在不同环境下的性能表现和变化规律,为材料的优化设计和改进提供依据。
总之,金属的摩擦磨损实验是一种重要的实验方法,可以帮助我们了解金属材料的性能和行为,为材料的优化设计和改进提供依据。
通过该实验,可以评估金属材料的耐磨性、耐久性和可靠性,为机械、汽车、航空航天等领域的工程应用提供技术支持。
冲击磨损试验

冲击磨损试验
冲击磨损试验是一种常见的材料磨损测试方法,它可以模拟材料在受到冲击或撞击时的磨损情况,从而评估材料的耐磨性能。
在工业生产中,材料的耐磨性能是非常重要的,因为它直接影响到机械设备的使用寿命和效率。
冲击磨损试验通常使用冲击试验机进行,试验时将样品固定在试验机上,然后用一定的冲击力撞击样品表面,通过测量样品表面的磨损量来评估材料的耐磨性能。
在试验过程中,可以改变冲击力、冲击角度、冲击次数等参数,以模拟不同的工作条件。
冲击磨损试验可以用于评估各种材料的耐磨性能,包括金属、塑料、陶瓷等。
在实际应用中,不同的材料在不同的工作条件下的耐磨性能也会有所不同。
例如,在高温、高压、高速等恶劣工作条件下,材料的耐磨性能会受到更大的挑战。
通过冲击磨损试验,可以评估材料的耐磨性能,并为材料的选择和设计提供参考。
在工业生产中,选择合适的材料可以有效地提高机械设备的使用寿命和效率,降低维护成本和生产成本。
冲击磨损试验是一种重要的材料磨损测试方法,它可以模拟材料在受到冲击或撞击时的磨损情况,评估材料的耐磨性能。
在工业生产中,选择合适的材料可以有效地提高机械设备的使用寿命和效率,降低维护成本和生产成本。
不锈钢的耐磨性能模拟与涂层改善

不锈钢的耐磨性能模拟与涂层改善不锈钢是一种常用的金属材料,具有良好的耐腐蚀性和机械性能,广泛应用于工业生产和日常生活中。
然而,在一些特殊领域,不锈钢的耐磨性能往往无法满足需求。
为了改善不锈钢的耐磨性,研究人员通过模拟及涂层等方式进行改良。
本文将探讨不锈钢的耐磨性能模拟与涂层改善的方法及其效果。
一、不锈钢的耐磨性能模拟不锈钢的耐磨性能模拟是通过模拟实际使用条件下的磨损状况,评估不锈钢材料的耐磨性能。
常见的模拟方法有摩擦磨损试验和磨料磨损试验。
1. 摩擦磨损试验摩擦磨损试验是利用试验机器模拟材料在摩擦过程中的磨损情况。
通过施加一定的载荷和摩擦力,在试验机器上对不锈钢样品进行往复摩擦,观察其表面磨损情况。
常用的摩擦磨损试验方法有球-盘法、环-盘法和滚动轴承法等。
2. 磨料磨损试验磨料磨损试验是利用磨料颗粒对不锈钢样品进行磨损的试验方法。
将一定大小、硬度和形状的磨料颗粒施加在不锈钢样品表面,并施加一定的载荷,通过试验机器进行磨损测试。
常用的磨料磨损试验方法有砂轮磨损法、研磨片磨损法和研磨球法等。
二、涂层改善不锈钢的耐磨性能涂层是一种覆盖在不锈钢表面的保护层,能有效改善不锈钢的耐磨性能。
常见的涂层材料包括激光熔覆涂层、喷涂涂层和电化学沉积涂层等。
1. 激光熔覆涂层激光熔覆涂层是通过激光熔化活性粉末材料,将其喷涂在不锈钢表面形成涂层。
这种涂层具有高硬度、低摩擦系数和耐磨性好的特点,能有效提高不锈钢的耐磨性能。
2. 喷涂涂层喷涂涂层是将硬度高、耐磨性好的粉末喷涂到不锈钢表面形成涂层。
喷涂涂层的工艺简单、成本低,能够增加不锈钢表面的硬度和耐磨性,提高其使用寿命。
3. 电化学沉积涂层电化学沉积涂层是利用电解作用,在不锈钢表面沉积一层金属涂层。
通过选择合适的金属材料,可以增加不锈钢的耐磨性能并提高其表面硬度。
三、不锈钢耐磨性能模拟与涂层改善的效果通过耐磨性能模拟和涂层改善,不锈钢的耐磨性能得到了显著提升。
模拟试验可以通过定量和定性的方式评估不锈钢的耐磨性能,为后续的改善工作提供了依据。
金属表面处理耐磨特性对比试验结果
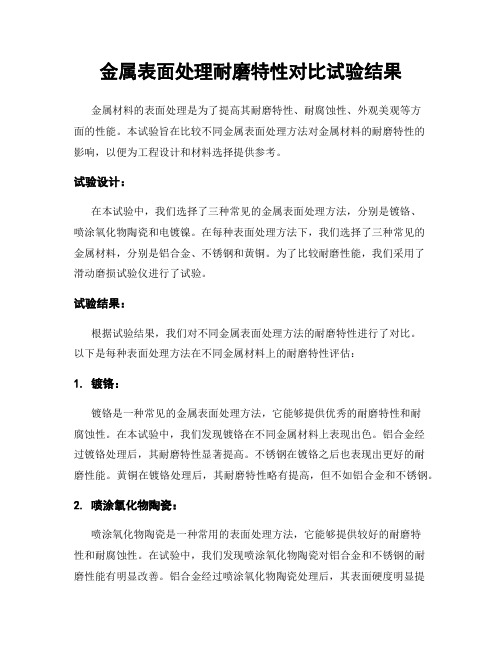
金属表面处理耐磨特性对比试验结果金属材料的表面处理是为了提高其耐磨特性、耐腐蚀性、外观美观等方面的性能。
本试验旨在比较不同金属表面处理方法对金属材料的耐磨特性的影响,以便为工程设计和材料选择提供参考。
试验设计:在本试验中,我们选择了三种常见的金属表面处理方法,分别是镀铬、喷涂氧化物陶瓷和电镀镍。
在每种表面处理方法下,我们选择了三种常见的金属材料,分别是铝合金、不锈钢和黄铜。
为了比较耐磨性能,我们采用了滑动磨损试验仪进行了试验。
试验结果:根据试验结果,我们对不同金属表面处理方法的耐磨特性进行了对比。
以下是每种表面处理方法在不同金属材料上的耐磨特性评估:1. 镀铬:镀铬是一种常见的金属表面处理方法,它能够提供优秀的耐磨特性和耐腐蚀性。
在本试验中,我们发现镀铬在不同金属材料上表现出色。
铝合金经过镀铬处理后,其耐磨特性显著提高。
不锈钢在镀铬之后也表现出更好的耐磨性能。
黄铜在镀铬处理后,其耐磨特性略有提高,但不如铝合金和不锈钢。
2. 喷涂氧化物陶瓷:喷涂氧化物陶瓷是一种常用的表面处理方法,它能够提供较好的耐磨特性和耐腐蚀性。
在试验中,我们发现喷涂氧化物陶瓷对铝合金和不锈钢的耐磨性能有明显改善。
铝合金经过喷涂氧化物陶瓷处理后,其表面硬度明显提高,耐磨性能也得到了显著提升。
不锈钢在喷涂氧化物陶瓷处理后,其耐磨性能也有了明显改进。
然而,黄铜在喷涂氧化物陶瓷处理下的耐磨性能提升有限。
3. 电镀镍:电镀镍是一种常用的金属表面处理方法,用于提高金属的耐磨性和耐腐蚀性。
在本试验中,电镀镍对铝合金的耐磨性能有很好的改善。
铝合金经过电镀镍处理后,其表面硬度得到显著提高,从而提高了耐磨性能。
不锈钢在电镀镍处理后,其耐磨性能略有改善。
然而,黄铜的耐磨性能在电镀镍处理下提升有限。
结论:根据本试验的对比结果,我们可以得出以下结论:1. 镀铬对不同金属材料的耐磨性能有良好的改善作用。
2. 喷涂氧化物陶瓷能够有效提高铝合金和不锈钢的耐磨性能。
金属材料滑动载流摩擦磨损测试方法

金属材料滑动载流摩擦磨损测试方法Test Method for Sliding Current-Carrying Friction and Wear of Metal目次目次 (I)前言 (II)1 范围 (1)2 规范性引用文件 (1)3 方法原理 (1)4 试样要求 (2)5 术语和定义 (2)5.1 接触压力 (2)5.2 线速度 (2)5.3 电流密度 (3)5.4 载流滑动距离 (3)5.5 平均载流摩擦系数 (3)5.6 载流摩擦系数波动性 (3)5.7 载流磨损率 (3)5.8 电流波动性 (4)5.9 燃弧率 (4)5.10 电弧能 (4)6 测试过程 (4)7 测试报告 (5)附录A (6)1金属材料滑动载流摩擦磨损测试方法1 范围本文件规定了金属材料的滑动载流摩擦磨损测试方法原理、试样要求、术语和定义、测试过程和测试报告。
本文件适用于金属材料滑动载流摩擦磨损的测试。
2 规范性引用文件下列文件对于本文件的应用是必不可少的。
凡是注日期的引用文件,仅注日期的版本适用于本文件。
凡是不注日期的引用文件,其最新版本(包括所有的修改单)适用于本文件。
GB/T 1031—2009 表面粗糙度参数及其数值GB/T 12444—2006 金属材料磨损试验方法试环-试块滑动磨损试验GB/T 17754—2012 摩擦学术语GB/T 2040—2008 铜及铜合金板材GB/T 3960—2016 塑料滑动摩擦磨损试验方法3 方法原理标引序号说明:1——旋转主轴2——盘试样3——销试样4——高速相机5——光敏元件6——卡具7——法向力传感器图1 测试方法原理12本文件测试方法采用滑动载流摩擦试验机,测试方法的基本原理见图1。
销试样装卡在导电卡具中,盘试样由旋转主轴驱动且两者绝缘,两个销试样和一个盘试样构成滑动载流摩擦副。
销试样和盘试样间的正压力由电液伺服阀和液压缸施加,实时动态法向力由法向力传感器测得。
材料力学性能第七章金属的磨损ppt课件

➢ 根据剥落裂纹起始位置及形态不同,分为:
➢ (1) 麻点剥落(点蚀)
➢ (2) 浅层剥落
➢
(3) 深层剥落(表面压碎)
46
2. 接触应力
➢ 两物体相互接触时,在表面上产生的局部压入应力称 为接触应力,也称为赫兹应力。
➢ 线接触(齿轮)与点接触(滚珠轴承)
上图为温度对胶合磨损的影响,可以看出, 当表面温度达到临界值(约80℃)时, 磨损量 和摩擦系数都急剧增加。
17
润滑油、润滑脂的影响
在润滑油、润滑脂中加人油性或极压添加剂能提高润 滑油膜吸附能力及油膜强度,能成倍地提高抗粘着磨 损能力。
油性添加剂是由极性非常强的分子组成,在常温条件 下,吸附在金属表面上形成边界润滑膜,防止金属表 面的直接接触,保持摩擦面的良好润滑状态。
磨损是一个复杂的系统工程
6
机件正常运行的磨损过程
(a)磨损量与 时间或行程关系曲线;
(b)磨损速率与 时间或行程关系曲线
7
3. 磨损的分类方法
粘着磨损 磨粒磨损
冲蚀磨损 疲劳磨损 微动磨损 腐蚀磨损
8
§7.2 磨损模型
一、粘着磨损 1. 磨损机理 ➢定义:在滑动摩擦条件下,当摩擦副相对滑动速 度较小(钢小于1m/s)时发生的, ➢原因:缺乏润滑油,摩擦副表面无氧化膜,且单 位法向载荷很大,σ接触>σs又称咬合磨损
36
主轴转速 : 60r/min ~ 12000r/min
主轴转速示值准确度: ± 2r/min
高温炉温度范围: 室温~ 800℃;
高温炉密封性能: 在连续充入氮气(纯度
99.9%以上)的条件下,炉内 氧气含量应能达到1%以下。 最大负荷:
《离子氮化2Cr13不锈钢变载荷条件下摩擦磨损行为研究》
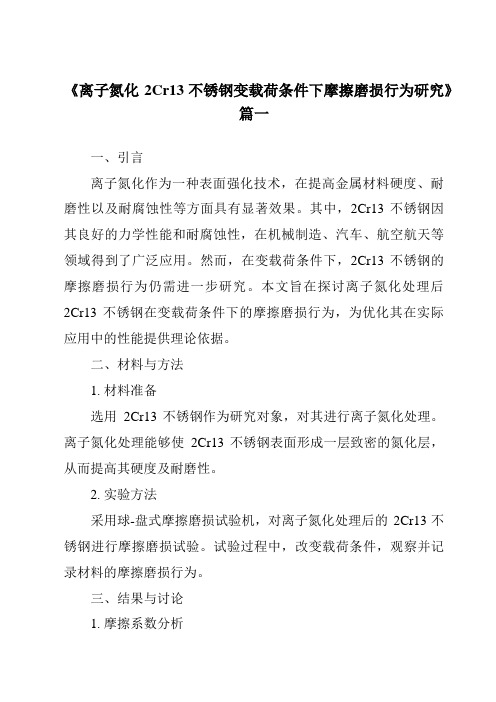
《离子氮化2Cr13不锈钢变载荷条件下摩擦磨损行为研究》篇一一、引言离子氮化作为一种表面强化技术,在提高金属材料硬度、耐磨性以及耐腐蚀性等方面具有显著效果。
其中,2Cr13不锈钢因其良好的力学性能和耐腐蚀性,在机械制造、汽车、航空航天等领域得到了广泛应用。
然而,在变载荷条件下,2Cr13不锈钢的摩擦磨损行为仍需进一步研究。
本文旨在探讨离子氮化处理后2Cr13不锈钢在变载荷条件下的摩擦磨损行为,为优化其在实际应用中的性能提供理论依据。
二、材料与方法1. 材料准备选用2Cr13不锈钢作为研究对象,对其进行离子氮化处理。
离子氮化处理能够使2Cr13不锈钢表面形成一层致密的氮化层,从而提高其硬度及耐磨性。
2. 实验方法采用球-盘式摩擦磨损试验机,对离子氮化处理后的2Cr13不锈钢进行摩擦磨损试验。
试验过程中,改变载荷条件,观察并记录材料的摩擦磨损行为。
三、结果与讨论1. 摩擦系数分析在变载荷条件下,离子氮化2Cr13不锈钢的摩擦系数表现出明显的变化。
随着载荷的增加,摩擦系数呈现先上升后稳定的趋势。
这可能是由于在较低载荷下,表面粗糙度对摩擦系数的影响较大;而在较高载荷下,表面硬化层起到了主要作用,使得摩擦系数趋于稳定。
2. 磨损率分析离子氮化2Cr13不锈钢的磨损率在变载荷条件下呈现出一定的规律性。
在较低载荷下,磨损率较高,随着载荷的增加,磨损率逐渐降低。
这表明离子氮化处理能够有效提高2Cr13不锈钢的耐磨性,尤其在较高载荷下表现更为显著。
3. 磨损形貌分析通过扫描电子显微镜(SEM)观察磨损形貌,发现离子氮化处理后的2Cr13不锈钢表面形成了较厚的氮化层,有效抵抗了磨损过程中的剥落和划痕。
在变载荷条件下,氮化层的硬度及韧性得到了充分发挥,使得材料表现出良好的耐磨性。
四、结论本研究表明,离子氮化处理能够显著提高2Cr13不锈钢在变载荷条件下的摩擦磨损性能。
在较低载荷下,表面粗糙度对摩擦系数的影响较大;而在较高载荷下,表面硬化层起到了主要作用,使得摩擦系数趋于稳定,同时降低了磨损率。
CSTM金属材料 销盘摩擦磨损试验 第2部分高温摩擦磨损试验方法
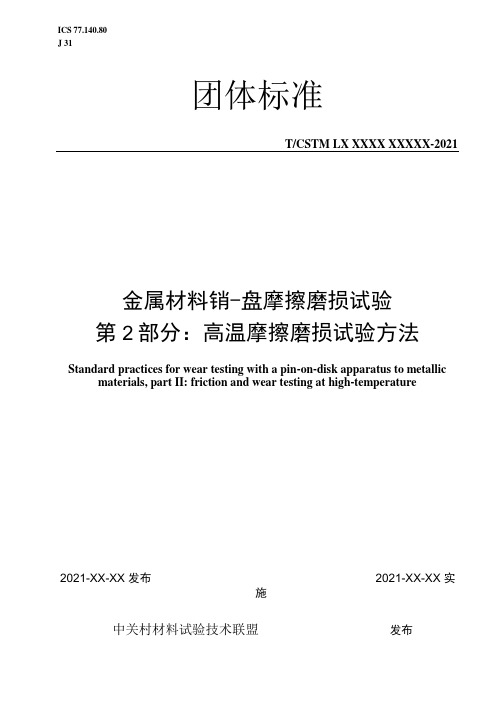
2021-XX-XX 发布施2021-XX-XX 实中关村材料试验技术联盟发布团体标准T/CSTM LX XXXX XXXXX-2021金属材料销-盘摩擦磨损试验 第2部分:高温摩擦磨损试验方法Standard practices for wear testing with a pin-on-disk apparatus to metallicmaterials, part II: friction and wear testing at high-temperatureICS 77.140.80 J 31本部分按照GB"1.1—2009《标准化工作导则第1部分:标准的结构和编写》给出的规则起草。
本标准由中国材料与试验团体标准委员会综合领域(FC99)提出。
本标准由中国材料与试验团体标准委员会金属磨损控制与成型技术委员会(FC99/TC01)归口。
本标准起草单位和主要起草人见附录A o金属材料销-盘摩擦磨损试验第2部分:高温摩擦磨损试验方法1范围本标准规定了金属材料在温度高于室温条件下销-盘摩擦磨损试验的术语及定义、试验原理、试样、 试验设备及仪器、实验方法、试验结果处理及试验报告。
本标准适用于金属及其复合材料在辅助热源加热下温度高于室温条件下销一盘滑动摩擦条件下磨损 量及摩擦系数的测定。
2规范性引用文件下列文件对于本文件的应用是必不可少的,凡是注日期的引用文件,仅注日期的版本适用于本文件。
凡是不注日期的引用文件,其最新版本(包括所有的修改单)适用于本文件。
数值修约规则金属材料磨损试验方法试环-试块滑动磨损试验静力单轴试验机的检验第1部分:拉力和(或)压力试验机测力 系统的检验与校准 摩擦学术语产品几何量技术规范(GPS )表面结构轮廓法测量标准第1 部分:实物测量标准 转速测量仪3术语与定义GB/T 17754和GB/T 12444界定的以及下列术语和定义适用于本标准,为了便于使用,以下重复列 出了 GB/T 17754和GB/T 12444中的某些术语和定义。
金属的磨损与接触疲劳

17/34
图7-4 耐磨性、硬度与断裂韧性关系 图7-5 磨损体积与硬度比(磨粒硬度与材料 硬度之比)的关系
18/34
§7.3 磨损试验方法
实物试验与实验室试验两类。 (1) 磨损试验结果分散度很大,一般试验要 有4~5对摩擦副,数据分散度大时还应增加。 (2) 一般取试验数据的平均值。分散度大 时需要用均方根值。 (3) 同一材料采用不同的磨损试验方法, 结果往往不同,甚至是颠倒的。
麻点剥落(点蚀)、 浅层剥落、深层剥落 (表面压碎)。
23/34
4、接触疲劳损伤过程
金属局部反复塑性变形→裂纹的形成→ 裂纹的扩展→金属表面的剥落,麻点。接触 疲劳=疲劳+磨损
接触应力:两物体相互接触时,在表面上 产生的局部压入应力。
24/34
二、接触疲劳破坏机理
金属局部反复塑性变形→裂纹的形成→ 裂纹的扩展→金属表面的剥落。
从综合切应力的分布和大小,材料的强 度相互比较,决定了裂纹产生的部位和接触 疲劳类型。
25/34
1、麻点剥落:裂纹起源于表面的接触疲劳损伤。 (1) 滑动加滚动条件下:切向摩擦力较大,
使最大综合切应力转移至表面。 (2) 表面存在质量缺陷:软点、硬点、夹杂
物等,造成抗剪强度不足。 深度:0.1-0.2mm的小块剥落。 形态:麻点是些针状或痘状的凹坑。
(2) 粘着点强度比双方金属都低时,磨损 量小,摩擦面较平滑。
(3) 粘着点比双方金属都高时,剪断可发 生在摩擦金属的任何一方,较软金属的磨损量 大。
8/34
3、磨损量的估算
粘着磨损量正比于法向载荷F,滑动距离L, (软材料压缩屈服强度或硬度)。
V KFlt KFlt ; V KFlt
镍基合金磨损量标准

镍基合金磨损量标准磨损是材料在摩擦、冲蚀等条件下逐渐失去原有形状和尺寸的过程。
在工程应用中,材料的磨损量是个重要的指标。
一般来说,磨损量越小,材料的耐磨性能越好。
因此,为了评估镍基合金的磨损性能,需要制定相应的磨损量标准。
一般来说,镍基合金的磨损量标准主要包括以下几个方面:1. 磨损试验方法:磨损试验是评估材料磨损性能的重要手段。
目前,常用的磨损试验方法包括滑动磨损试验、冲蚀磨损试验、磨粒磨损试验等。
针对不同的应用场景和工况,可以选择合适的磨损试验方法来评估镍基合金的磨损性能。
2. 磨损量的评价标准:对于镍基合金的磨损量,一般可以采用磨损量、磨损速率、磨损深度等指标来评价。
通过对磨损量的评价,可以更加客观地了解镍基合金在不同工况下的磨损性能。
3. 磨损量的限制要求:根据镍基合金在不同应用场景下的实际需求,可以针对其磨损量制定相应的限制要求。
例如,在航空航天领域,对于要求材料具有较高耐磨性能的部件,可以制定更为严格的磨损量限制要求。
4. 磨损量的检测方法:为了准确地测量镍基合金的磨损量,需要采用合适的检测方法。
常用的磨损量检测方法包括三维形貌观察、重量法、表面粗糙度检测等。
通过这些检测方法,可以准确地获取镍基合金的磨损量数据。
总的来看,镍基合金的磨损量标准是一个综合性的指标体系,涉及到磨损试验方法、评价标准、限制要求和检测方法等多个方面。
只有通过科学合理的磨损量标准,才能更好地评估镍基合金的磨损性能,为其在工程领域的应用提供可靠的参考依据。
同时,需要注意的是,随着科学技术的不断进步,镍基合金的磨损量标准也需要不断更新和完善,以适应不同工程应用领域对材料磨损性能的不同要求。
摩擦磨损性能测试试验
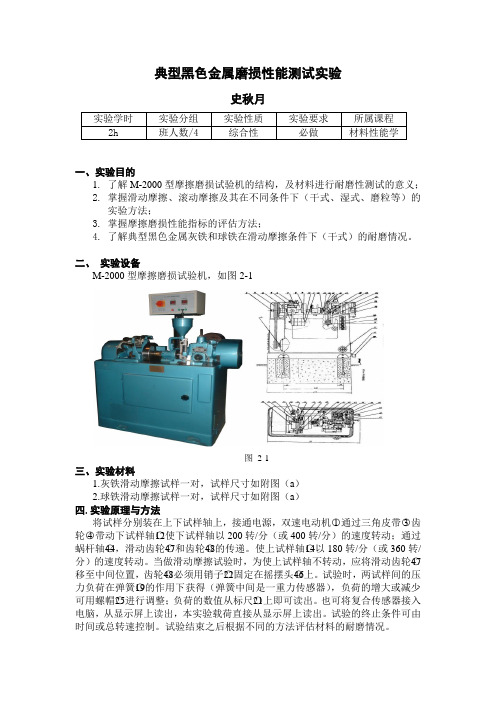
典型黑色金属磨损性能测试实验史秋月实验学时实验分组实验性质实验要求所属课程2h 班人数/4 综合性必做材料性能学一、实验目的1.了解M-2000型摩擦磨损试验机的结构,及材料进行耐磨性测试的意义;2.掌握滑动摩擦、滚动摩擦及其在不同条件下(干式、湿式、磨粒等)的实验方法;3.掌握摩擦磨损性能指标的评估方法;4.了解典型黑色金属灰铁和球铁在滑动摩擦条件下(干式)的耐磨情况。
二、实验设备M-2000型摩擦磨损试验机,如图2-1图2-1三、实验材料1.灰铁滑动摩擦试样一对,试样尺寸如附图(a)2.球铁滑动摩擦试样一对,试样尺寸如附图(a)四.实验原理与方法将试样分别装在上下试样轴上,接通电源,双速电动机○1通过三角皮带○3齿12使下试样轴以200转/分(或400转/分)的速度转动;通过轮○4带动下试样轴○48的传递。
使上试样轴○14以180转/分(或360转/47和齿轮○蜗杆轴○44,滑动齿轮○分)的速度转动。
当做滑动摩擦试验时,为使上试样轴不转动,应将滑动齿轮○47移至中间位置,齿轮○48必须用销子○22固定在摇摆头○46上。
试验时,两试样间的压力负荷在弹簧○19的作用下获得(弹簧中间是一重力传感器),负荷的增大或减少21上即可读出。
也可将复合传感器接入可用螺帽○25进行调整;负荷的数值从标尺○电脑,从显示屏上读出,本实验载荷直接从显示屏上读出。
试验的终止条件可由时间或总转速控制。
试验结束之后根据不同的方法评估材料的耐磨情况。
五、实验内容将加工好的滑动摩擦试样装在实验机上,在给定的条件下(干式、滑动摩擦、压力:200N、时间60min)进行试验,试验结束后将试样取下,评估耐磨性能。
根据所选取磨损试验方法的不同以及材料本质的差异,可以选择不同的耐磨性能评定方法,以期获得精确的试验数据,现简单例举下述几种方法以供参考。
1、称重法:采用试样在试验前后重量之差,本表示耐磨性能的方法,由于两试样之间的摩擦所引起的磨损量,可以采用精度达万分之一的分析天平称量出试样试验前后重量之差非凡获得。
钢丝球磨损试验方法

钢丝球磨损试验方法可以参考如下步骤:
准备试验材料:试验钢球符合GB/308.89要求,即材料为GCr15,硬度为64~66HRc,钢球直径为12.7mm。
清洗钢球和卡具:首先用石油醚清洗试验钢球和卡具,除去钢球表面上的锈斑,然后利用超声清洗机做进一步的清洗,清洁完毕后再用吹风机吹干。
试验前不能用手触摸钢球。
安装钢球:用镊子夹起清洁好的钢球并安装在转轴下部,并夹紧。
倒入液体:将水基纳米液压液倒入杯中,使液面淹没上方钢球球顶部约3~5mm。
设定参数:设定加载力为147N,温度为75℃,转速稳定在1450r/min,运行时间设定为30min。
加载并运行:先用手调整传感器下的加力丝杆至上下摩擦副刚好接触,然后将手动加载切换为自动加载。
点击“试验开始”按钮,在试验过程中观察摩擦系数变化情况。
卸载并结束试验:运行30min后,试验机停止,软件自动卸载,听到加载电机停止转动时切换到手动加载。
完成以上步骤后,可以检查钢丝球的磨损情况,记录相关数据。
请注意,这只是一个基本的试验方法,具体的试验条件和步骤可能会因不同的试验目的和试验条件而有所不同。
在进行试验时,请务必遵守安全规范,并采取适当的措施来保护人员和设备的安全。
- 1、下载文档前请自行甄别文档内容的完整性,平台不提供额外的编辑、内容补充、找答案等附加服务。
- 2、"仅部分预览"的文档,不可在线预览部分如存在完整性等问题,可反馈申请退款(可完整预览的文档不适用该条件!)。
- 3、如文档侵犯您的权益,请联系客服反馈,我们会尽快为您处理(人工客服工作时间:9:00-18:30)。
金属材料磨损试验方法
试环-试块滑动磨损试验
GB/T12444-2006 一.试验原理
试块与规定转速的试环相接触,并承受一定实验力,经规定转数后,用磨痕宽度计算试块的体积磨损,用称重法测定试环的质量磨损,试验中连续测量试块上的摩擦力和正压力,计算摩擦系数。
二.试验步骤
1.试验应在10℃—35℃范围内进行,对温度要求较严格的试验,应控制在
23±5℃之内。
2.试验应在无腐蚀性气体、无振动、无粉尘的环境中进行。
3.将试环及试块牢固的安装在试验机主轴及夹具上,试块应处于试环中心,
并应保证试块边缘与试环边缘平行。
4.启动试验机,使试环逐渐达到规定转速,平稳的将实验力施加至规定值
5.可以进行干摩擦,也可以加入适当润滑介质以保证试样在规定状态下正
常试验,对于润滑磨损实验,试验前应对所有与润滑剂接触的零件进行
清洗。
6.根据需要,在试验过程中记录摩擦力。
7.试验累计转数应根据材料及热处理工艺需要确定。
8.对于称重的试样,试验前后用适当的清洗液以相同的方法清洗试样,建
议现用三氯乙烷,再用甲醇清洗;清洗后一般在60℃下进行2H烘干冷
却至室温后,放入干燥器,立即称重。
三.试验结果处理
1.在块形试样磨痕中部及两端(距试样边缘1mm处)测量磨痕宽度,取三
次测量平均值作为一个试验数据。
2.标准尺寸试样三个位置的磨痕宽度之差大于平均宽度值20%,试验数据
无效。
3.试验报告中至少包括:试验机型号、试验形式、材料种类、热处理种类、
实验力(正压力)、试验转速及转数、润滑方式及润滑剂种类、试块的磨
痕宽度和体积磨损、试环磨损失去的质量、摩擦系数、环境温度、试块
加工方向。
四.准确度说明
1.本实验方法的偏差与执行标准的严格性密切相关。
相同材料重复性试验
的一致性与材料的均匀性、材料在摩擦中的相互作用、试验人员操作技
术密切相关。
2.由于本实验结果分散性较大,尤其干摩擦试验对试样初始表面条件十分
敏感,因此一般要做3次以上重复试验。
3.磨损量与滑动距离一般不呈线性关系,因此仅能对同样转数的试验结果
进行比较。