塑件常见不良原因及解决对策
塑胶件常见缺陷不良分析及对策讲解
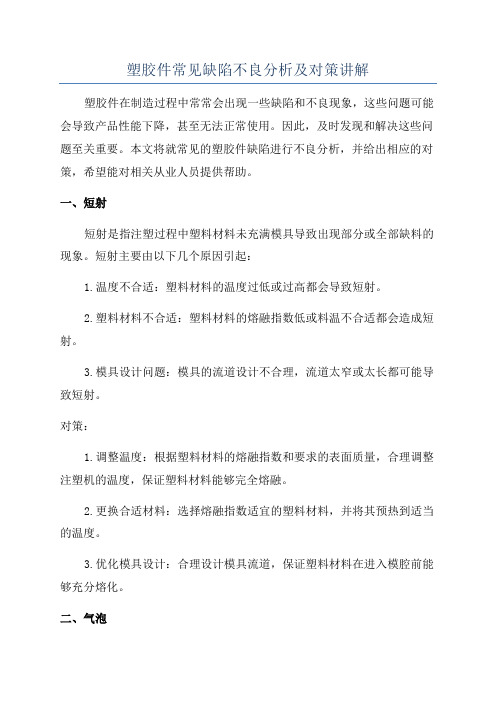
塑胶件常见缺陷不良分析及对策讲解塑胶件在制造过程中常常会出现一些缺陷和不良现象,这些问题可能会导致产品性能下降,甚至无法正常使用。
因此,及时发现和解决这些问题至关重要。
本文将就常见的塑胶件缺陷进行不良分析,并给出相应的对策,希望能对相关从业人员提供帮助。
一、短射短射是指注塑过程中塑料材料未充满模具导致出现部分或全部缺料的现象。
短射主要由以下几个原因引起:1.温度不合适:塑料材料的温度过低或过高都会导致短射。
2.塑料材料不合适:塑料材料的熔融指数低或料温不合适都会造成短射。
3.模具设计问题:模具的流道设计不合理,流道太窄或太长都可能导致短射。
对策:1.调整温度:根据塑料材料的熔融指数和要求的表面质量,合理调整注塑机的温度,保证塑料材料能够完全熔融。
2.更换合适材料:选择熔融指数适宜的塑料材料,并将其预热到适当的温度。
3.优化模具设计:合理设计模具流道,保证塑料材料在进入模腔前能够充分熔化。
二、气泡气泡是指塑胶件表面或内部出现的小气孔或气泡。
气泡可能导致产品外观不良或性能下降。
气泡的产生主要有以下几个原因:1.塑料材料中含有挥发性成分:一些塑料材料中含有挥发性成分,如果注塑温度过高,这些挥发性成分就会挥发出来形成气泡。
2.模具表面不洁净:如果模具表面不干净或有油污等杂质,气泡就会在塑料注入过程中被吸附在塑料中形成。
3.注塑机压力过高:注塑机压力过高会导致空气被压进模具中,形成气泡。
对策:1.调整注塑温度:根据塑料材料的特性,合理调整注塑温度。
温度过高易导致气泡产生,温度过低则容易短射。
2.模具清洁:保持模具表面干净,定期对模具进行清洗,去除杂质和油污。
3.控制注塑机压力:根据塑料材料的特性和模具的要求,合理控制注塑机的压力,避免空气进入模具。
三、热处理不当塑胶件经过热处理后,如果处理不当,可能导致产品性能下降或出现变形等问题。
常见的热处理问题有:1.温度不合适:热处理时,温度不合适会导致产品硬度不均匀或过硬。
塑料件缺陷及改进措施

塑料件缺陷及改进措施塑料件在实际应用中存在一些常见的缺陷,这些缺陷可能会对产品的质量和性能产生负面的影响。
下面将介绍一些常见的塑料件缺陷,并提出相应的改进措施。
1.熔接线痕:在注塑过程中,由于熔融塑料的流动不均匀,容易形成熔接线痕。
这些痕迹可能会导致产品强度降低、疲劳性能差等问题。
改进措施:调整注塑工艺参数,如制定适当的注射速度、保持压力等,以促进塑料的均匀流动,减少熔接线痕的产生。
2.气泡:注塑过程中,由于塑料内含有的气体随着高温熔融逸出,易形成气泡。
气泡会导致产品的密封性能下降、外观质量差等问题。
改进措施:提高注塑设备的真空度,减少气体残留。
此外,在塑料原料中加入消泡剂,能够降低气泡的产生。
3.龟裂:塑料零件在冷却过程中,由于不均匀的收缩率和内应力,易出现龟裂缺陷。
这种缺陷会导致产品的强度下降、易开裂等问题。
改进措施:采用合适的冷却方法,如适当提高冷却介质的温度、均匀冷却等,以减少塑料件的收缩和内应力的产生。
4.比色差:一些塑料件在生产过程中,由于塑料原料的不均匀混合或加工温度控制不当,易形成色差。
这会导致产品的外观质量差,影响产品的整体美观度。
改进措施:严格控制塑料原料的配比,确保原料的均匀混合。
同时,加强对注塑设备的温度控制,保持适当的加工温度,有助于减少温度对产品颜色的影响。
5.纹理不良:在塑料件表面会产生一些不良的纹理,如模具印痕、晶化痕迹等。
这些缺陷会降低产品的表面质量、减少产品的美观度。
改进措施:优化模具的设计和制造工艺,减少模具表面的磨损和粗糙度。
同时,在注塑过程中控制好注塑温度和注塑压力,以减小纹理缺陷的产生。
总而言之,塑料件的缺陷主要体现在熔接线痕、气泡、龟裂、比色差和纹理不良等方面。
为了改善塑料件的质量和性能,应从加工工艺、原料控制、模具改进等方面入手,提高生产工艺的稳定性和可控性。
同时,加强质量检测和监控,及时发现和解决问题,以确保塑料件的质量满足产品要求。
塑胶件常见的缺陷产生原因及解决办法

塑胶件常见的缺陷产生原因及解决办法一、设计方面的缺陷:1.不合理的尺寸设计:塑胶件的尺寸设计不合理可能导致尺寸偏差过大、尺寸不一致等问题。
解决方法是根据塑胶件的具体用途和要求进行合理的尺寸设计,并进行合适的工艺分析和模流分析。
2.没有考虑到材料的特性:不同塑料材料具有不同的热胀冷缩系数、熔融温度等特性,设计时没有考虑到这些特性可能导致尺寸偏差、变形等问题。
解决方法是根据塑料材料的特性进行合适的设计和模具制造选型。
3.模具设计问题:模具设计不合理或者制造质量不过关可能导致塑胶件的缺陷问题。
解决方法是进行合理的模具设计,并选择专业的模具制造厂家。
4.不合理的壁厚设计:塑胶件的壁厚设计不合理可能导致塑胶件变形、收缩不均匀等问题。
解决方法是根据塑胶件的材料特性和实际使用要求进行合理的壁厚设计。
二、材料方面的缺陷:1.材料质量问题:不合格的原料质量可能导致塑胶件出现异味、颜色不均匀等问题。
解决方法是选择合格的塑料原料供应商,并进行原料的严格检验。
2.材料混合不均匀:塑料材料在加工过程中没有充分混合均匀可能导致塑胶件的颜色不均匀等问题。
解决方法是进行充分的原料预处理和混炼,确保塑料材料的均匀性。
3.熔体温度不均匀:塑料材料在注塑过程中温度不均匀可能导致塑胶件尺寸偏差、表面气泡等问题。
解决方法是调整注塑机的温度控制系统,确保熔体温度均匀稳定。
三、工艺方面的缺陷:1.注塑工艺参数设置不当:注塑过程中,如射胶压力、射胶速度、冷却时间等工艺参数设置不当可能导致塑胶件出现尺寸偏差、气泡、表面缺陷等问题。
解决方法是根据塑料的特性和产品要求进行合理的工艺参数设置。
2.模具温控不均匀:模具温度不均匀可能导致塑胶件出现收缩不一致、尺寸偏差等问题。
解决方法是进行模具温度分析和温控系统的优化。
可以采用热流道模具、快速温度控制系统等技术手段解决问题。
3.模具保养不当:模具的使用寿命长,如果没有进行定期的保养和维修可能导致塑胶件出现模纹、模具磨损等问题。
塑料件缺陷原因及改进方法
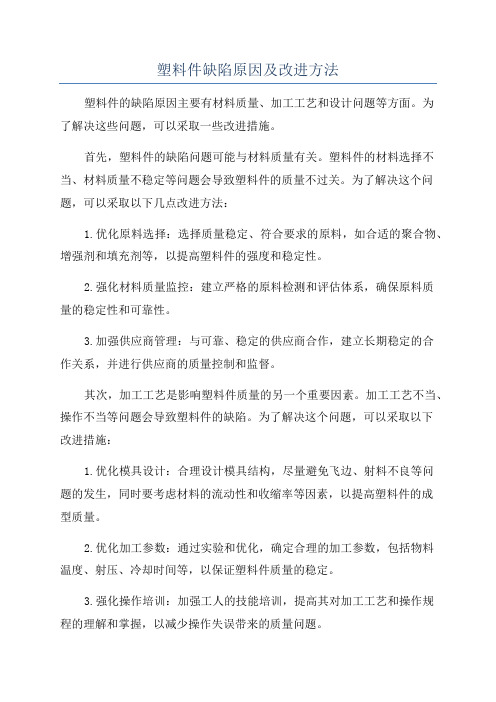
塑料件缺陷原因及改进方法塑料件的缺陷原因主要有材料质量、加工工艺和设计问题等方面。
为了解决这些问题,可以采取一些改进措施。
首先,塑料件的缺陷问题可能与材料质量有关。
塑料件的材料选择不当、材料质量不稳定等问题会导致塑料件的质量不过关。
为了解决这个问题,可以采取以下几点改进方法:1.优化原料选择:选择质量稳定、符合要求的原料,如合适的聚合物、增强剂和填充剂等,以提高塑料件的强度和稳定性。
2.强化材料质量监控:建立严格的原料检测和评估体系,确保原料质量的稳定性和可靠性。
3.加强供应商管理:与可靠、稳定的供应商合作,建立长期稳定的合作关系,并进行供应商的质量控制和监督。
其次,加工工艺是影响塑料件质量的另一个重要因素。
加工工艺不当、操作不当等问题会导致塑料件的缺陷。
为了解决这个问题,可以采取以下改进措施:1.优化模具设计:合理设计模具结构,尽量避免飞边、射料不良等问题的发生,同时要考虑材料的流动性和收缩率等因素,以提高塑料件的成型质量。
2.优化加工参数:通过实验和优化,确定合理的加工参数,包括物料温度、射压、冷却时间等,以保证塑料件质量的稳定。
3.强化操作培训:加强工人的技能培训,提高其对加工工艺和操作规程的理解和掌握,以减少操作失误带来的质量问题。
此外,塑料件的设计问题也会导致质量缺陷。
设计不当、结构不合理等问题会影响塑料件的使用寿命和功能。
1.优化产品设计:在设计阶段就要充分考虑材料特性、工艺要求和使用环境等因素,合理确定塑料件的结构和尺寸,以提高产品的可靠性和使用寿命。
2.强化模拟分析:通过使用CAD、CAE等软件工具进行模拟分析,预测设计在使用过程中的变形、应力分布等问题,在设计阶段就可以进行修正和优化。
3.进行实际测试:在设计验证阶段进行实际测试,包括强度测试、耐久性测试等,以验证设计的合理性和可靠性。
综上所述,塑料件的缺陷问题可能与材料质量、加工工艺和设计问题有关。
通过优化原料选择、加强材料质量监控、优化模具设计、优化加工参数、强化操作培训、优化产品设计、强化模拟分析和进行实际测试等改进方法,可以有效解决这些问题,提高塑料件的质量和可靠性。
塑件缺陷原因及改善方法

塑件缺陷原因及改善方法塑件是一种常见的工程材料,广泛应用于汽车、家电、电子、医疗设备等领域。
然而,在塑件生产过程中,常常会出现一些缺陷,如气泡、毛刺、热缩、变形等问题,这些缺陷会影响塑件的质量和性能。
因此,了解塑件缺陷的原因,并采取相应的改善方法,对于提高塑件质量和性能具有重要意义。
首先,塑件缺陷的原因有多种,下面是一些常见的原因及相应的改善方法:1.气泡:气泡是塑件生产过程中常见的缺陷,通常是由于原料中含有挥发性成分,或者模具中有气体积聚引起的。
改善方法包括:使用质量稳定的原料,避免使用含有挥发性成分的原料;在塑件生产过程中提高注塑压力,减少气泡的生成;对模具进行定期维护,清除模具中的积聚气体。
2.毛刺:毛刺是塑件表面出现的细小突起,通常是由于模具不平整或模具开合不良引起的。
改善方法包括:对模具进行定期检修和研磨,保持模具的平整度;调整模具开合速度和压力,使开合动作更加平稳;在设计模具时考虑减少毛刺的生成。
3.热缩:塑件在冷却后会发生热缩现象,导致尺寸变小。
这是由于塑料在冷却过程中会收缩引起的。
改善方法包括:在设计模具时考虑塑件的热缩率,合理设置模具尺寸,使得塑件在冷却后能得到正确的尺寸;控制注塑过程中的冷却时间和温度,避免过快或过慢的冷却导致过大的热缩。
4.变形:塑件在注塑过程中可能会发生变形,导致尺寸不准确或形状失真。
这是由于塑料在注塑过程中由于内应力不平衡引起的。
改善方法包括:优化模具设计,使模具在注塑过程中能够充分填充塑料,并保持良好的冷却效果;控制注塑过程的温度、压力和速度,减少内应力的释放。
此外,还有一些其他常见的塑件缺陷,如熔流线、白斑、开裂等。
这些缺陷的原因和改善方法也各不相同,需要具体问题具体分析。
总的来说,塑件缺陷的原因多种多样,通过针对不同的原因采取相应的改善方法,能够有效地提高塑件的质量和性能。
对于塑件生产企业来说,建立完善的质量控制体系,加强原材料的筛选和控制,定期维护和检修模具,改进注塑工艺,都是改善塑件质量和性能的重要措施。
塑胶常见不良及解决方法

塑胶常见不良及解决方法塑胶是一种常见的材料,广泛应用于各种行业和领域。
然而,由于塑胶的特性以及制造过程中的一些问题,常常会出现一些不良现象。
本文将重点介绍一些常见的塑胶不良及其解决方法。
1.氣泡:塑膠制品中常見的一種不良現象是氣泡,這會在成品表面或内部形成小气囊。
气泡的形成是由于塑胶熔融时含有的空气或挥发物没有充分释放出来。
解决方法包括降低加工温度、增加熔体压力、增加注射速度和使用抗气泡添加剂等。
2.热胀冷缩:塑胶制品在温度变化下会发生热胀冷缩,导致尺寸变化。
这可能会导致配件无法正常连接或安装。
为了解决这个问题,可以采用材料改性或加工工艺改进,如增加冷却时间、降低注射温度等。
3.白化:白化是指塑胶制品表面或内部出现白色斑点或条纹。
这种现象通常是由于塑胶在注射过程中发生气泡聚集或制品未达到均匀熔融所致。
解决方法包括优化注射工艺、增加熔体压力、使用抗白化添加剂等。
4.热裂纹:热裂纹是指在塑胶产品成型过程中出现的裂纹现象。
这通常是由于塑胶在成型过程中存在过大的应力集中,导致塑胶产生裂纹。
解决方法包括改变模具设计、增加冷却时间、预混塑胶料等。
5.变色:变色是指塑胶制品在使用或储存过程中出现颜色变化。
这可能是由于塑胶材料受到光、热、氧化等外界因素的影响所致。
解决方法包括选择适当的防褪色添加剂、合理储存塑胶制品等。
6.毛刺:毛刺是指塑胶制品表面出现不平整、刺状的小颗粒。
这通常是由于模具表面不平整或注射工艺不当所导致的。
解决方法包括优化模具设计、控制注射压力、调整注射速度等。
7.缩水:缩水是指塑胶制品在冷却过程中发生体积收缩。
这可能导致尺寸偏离设计要求。
解决方法包括优化塑胶成型工艺、增加冷却时间和选择合适的材料等。
8.潜伏期延长:有些塑胶在使用一段时间后会发生不良现象,如变形、断裂等。
这可能是由于塑胶受到环境因素、应力或热老化的影响导致的。
解决方法包括选择合适的材料、控制加工温度、降低应力等。
总结起来,塑胶制品的不良现象可能是由于材料、工艺或环境等多种因素造成的。
塑件常见不良原因及解决对策

原材料受潮,影响塑件的成型效果。
工艺参数问题
成型温度过高或过低
成型温度过高或过低,影响塑件的成型效果和性能。
成型压力不合适
成型压力不合适,导致塑件内部结构不均匀。
成型时间不足或过长
成型时间不足或过长,影响塑件的成型效果和性能。
设备问题
设备故障
01
成型设备出现故障,导致塑件成型不良。
设备维护不当
02
02
对于工艺参数问题,应严格按照工艺要求进行成型参数的设置和调整,确保成 型温度、压力和时间等参数的稳定和准确性。
03
对于设备问题,应加强设备日常维护和保养,定期对设备进行检查和维修,确 保设备性能稳定和正常运转。同时,还应加强设备操作人员的培训和管理,避 免因操作不当导致设备故障和塑件不良。
03
塑件生产的重要性
塑件作为重要的工业原材料,广泛应 用于汽车、电子、包装、建筑等领域 ,其质量和性能对产品整体性能和安 全性具有重要影响。
塑件制造技术的不断发展和进步,有 助于提高产品质量、降低生产成本、 增强产品竞争力,对工业生产和经济 发展具有重要意义。
02
塑件常见不良原因
模具问题
01
02
03Leabharlann 案例二:原材料问题导致的塑件不良
1. 严格控制原材料质量
选择质量稳定、性能优良的原材料。
2. 加强原材料存储管理
确保原材料在干燥、避光的条件下存储。
3. 定期检测原材料性能
对存储的原材料进行性能检测,确保其质量稳定。
案例三:工艺参数问题导致的塑件不良
• 总结词:温度控制不当、压力调整不准确、成型周期不稳定
案例二:原材料问题导致的塑件不良
• 总结词:材料成分不均、材料受潮、材料老化
常见的塑件问题分析及处理方法

在制品上有孔穴的地方都会产生熔接线痕,若要完全消除比较困难,熔融塑料在型腔中由于遇到嵌件孔洞、流速不连贯的区域、充模料流中断的区域而以多股形式汇合,这种低温熔料相汇合因不能完全熔合而产生线性的熔接缝,此外在发生浇口喷射充模也会生成熔接缝
1、原料流动性不够
2、射出速度快或慢,调整适当射胶速度
3、灌嘴孔径过小或灌嘴过长,则在灌嘴处温度下降,因此,冷却的原料最先射出,发生压力下降,而造成流痕。
4、射出压力低,调整适当射胶压力
5、保压不足
6、保压时间短
1、模温太低,增加模具温度,使原料容易流动。
2、模具冷却不适当,重调模具水管
3、冷料窝存储小,射出初期,温度低的原料被先充填造成流痕。
2、原料润滑性不足够
1、料温太高
2、原料在料筒内滞留时间太长
3、注塑机料筒受损使原料积聚
1、入水口太细太长
四、云雾
制品表面的光洁度不良
1、塑料的稳定性不足够
1、料温太高
2、模温过低
3、原料在料筒滞留得太长
4、脱模剂使用不当
1、模具抛光太差
五、起疮:(银色条纹)
这是出现在制件表面熔料流动方向上的银白色纹理,这种现象的原因虽然很多,但主要是原料干燥不彻底,由水分或挥发成分造成的
2、射出压力低,造成充填不足。提高射胶压力。
3、射胶进行太快转保压
4、保压过低
5、射出速度太慢,原料在未充满模穴之前就固化而造成短射的现象。增大射胶速度。
6、模具温度过低,也容易造成欠肉,但是提高模温则冷却时间延长,造成成型周期时间也延长,所以,必须考虑从与生产效率相关角度来决定适当的模温。
7、逆止阀破裂
1、入水口的设计不良
塑胶件常见缺陷产生的原因及解决方法

塑胶件常见缺陷产生的原因及解决方法1.原材料质量问题:塑胶件常见的原材料问题包括原材料中含有杂质、原料失效、原料配比不正确等。
这些问题会导致塑胶件的质量下降和性能降低。
解决方法是对原材料进行严格的检验和筛选,确保原材料的纯度和质量。
2.模具设计问题:模具设计不合理可能导致塑胶件的缺陷,例如模具壁厚不均匀、模腔表面粗糙等。
解决方法是对模具进行合理设计,确保模具的结构和尺寸满足产品要求,并提高模具的制造工艺和加工精度。
3.注塑工艺问题:注塑过程中的工艺参数设置不当会导致塑胶件出现缺陷,例如温度不稳定、压力不均匀、注射速度过快等。
解决方法是优化注塑工艺参数,确保温度、压力、速度等参数的稳定和均匀。
4.模具磨损和损坏:长时间使用会导致模具磨损和损坏,影响塑胶件的质量和外观。
解决方法是加强模具的保养和维护,定期进行模具清洁和润滑,并进行必要的修复和更换。
5.后道工艺问题:塑胶件的后道加工也可能引发缺陷,例如焊接不牢固、喷涂不均匀等。
解决方法是加强后道工艺的控制,提高工艺的稳定性和一致性。
综上所述,要解决塑胶件常见缺陷的问题,需要从原材料选择、模具设计、注塑工艺、模具维护和后道工艺等方面入手,通过优化和控制各个环节,提高产品的质量和性能。
同时,还需要建立健全的质量管理体系,对生产过程进行全面监控和检测,及时发现和解决问题。
最后,还应该加强员工的培训和技能提升,提高操作技术和质量意识,提高产品的一致性和稳定性。
只有通过不断改进和严格控制,才能有效降低塑胶件的缺陷率,提高产品的质量和市场竞争力。
塑胶件常见缺陷产生的原因及解决方法

塑胶件常见缺陷产生的原因及解决方法一、材料问题1.材料选择不当:选择不适合的塑胶材料或材料质量不达标,容易导致塑胶件的缺陷。
解决方法是根据具体要求选择合适的塑胶材料,并进行必要的材料测试和质量控制。
2.材料批次差异:不同批次的塑胶材料可能存在差异,如流动性、收缩率等,导致成型件的缺陷。
解决方法是进行材料测试和合理的材料配方设计,确保不同批次的材料性能稳定一致。
二、工艺问题1.注塑工艺参数不合理:注塑工艺参数(如注射速度、保压时间等)不合理会导致成型件的缺陷,如短流、气泡等。
解决方法是通过优化注塑工艺参数,使之更加合理和稳定。
2.注塑模具设计和制造问题:模具结构不合理、尺寸精度不达标等问题会导致成型件的缺陷,如模具表面瑕疵、尺寸偏差等。
解决方法是进行合理的模具设计和制造,并进行必要的模具修整和维护。
3.注塑材料温度控制不当:材料温度过高或过低都会导致成型件的缺陷,如熔接线、气泡等。
解决方法是通过调整料筒温度、模具温度等进行合理的温度控制。
4.模具开合不良:模具开合不良或夹模力不足会导致成型件的缺陷,如模具压痕、塌陷等。
解决方法是保持模具开合顺畅,并确保夹模力适当。
三、设计问题1.设计尺寸不合理:设计尺寸过大或过小、壁厚不均匀等问题会导致成型件的缺陷,如尺寸偏差、变形等。
解决方法是根据塑胶件的使用要求和成型工艺特点进行合理的尺寸设计,并进行必要的尺寸优化。
2.设计结构不合理:设计结构复杂、壁薄部位过多等问题容易导致成型件的缺陷,如留痕、焊痕等。
解决方法是简化设计结构、增加加强筋等措施,提高塑胶件的强度和表面质量。
3.装配接口设计不当:塑胶件的装配接口设计不当会导致装配困难、配套件脱落等问题,影响整体使用效果。
解决方法是合理设计装配接口,确保装配紧固可靠。
以上是塑胶件常见缺陷产生的原因及解决方法的概述。
在实际生产中,还需要根据具体情况进行详细分析和解决。
为了确保塑胶件的质量,需要在材料选择、工艺控制和设计优化等方面进行全面的控制和改进。
塑料件常见缺陷及对策手册

塑料件常见缺陷及对策手册
塑料件常见缺陷及对策手册如下:
1. 熔体流动不畅:主要表现为铸件的形状或尺寸变化,可能会影响产品的外观和使用效果。
解决方案包括提高模具温度、加大喷嘴孔径、增加压力等。
2. 表面气泡:主要是由于熔融状态下的气体逸出不完全导致的,会影响产品的外观和质量。
解决方法包括提高熔体温度、增加注射速度、调整模具结构等。
3. 热裂纹:主要是由于材料热应力引起的,会影响产品的性能和寿命。
解决方案包括减少注射压力、降低模具温度、改进模具结构等。
4. 缩孔:主要是由于熔体内部存在气体或材料中含水过多导致的。
解决方案包括预干燥原材料、增加熔体温度、减少注射速度等。
5. 毛边和毛刺:主要是由于模具设计不合理、注射速度过快等原因导致的。
解决方案包括调整模具结构、降低注射速度等。
6. 非均匀收缩:主要表现为铸件形状或尺寸的变化不一致,会影响产品的精度和性能。
解决方案包括增加模具温度、降低注射压力等。
7. 材料老化:主要是由于材料长时间暴露在高温、紫外线等环境下导致的。
解决方案包括选择耐老化的材料、优化制造工艺等。
以上是塑料件常见缺陷及对策手册的简单介绍,具体情况还需要根据实际生产中遇到的具体问题进行分析和处理。
注塑产品常见的13种质量缺陷原因分析及解决办法
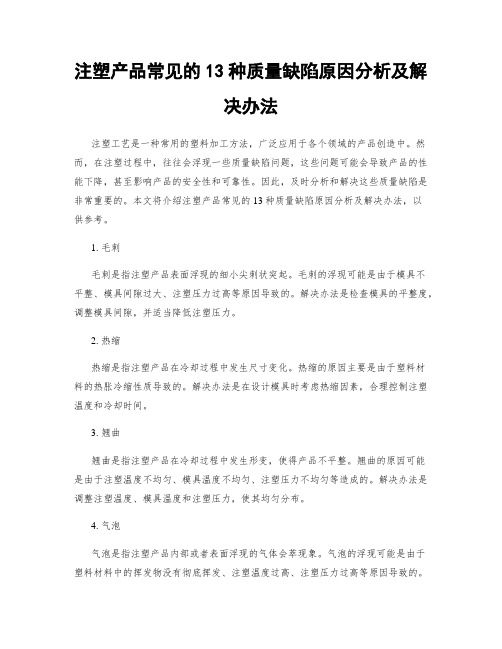
注塑产品常见的13种质量缺陷原因分析及解决办法注塑工艺是一种常用的塑料加工方法,广泛应用于各个领域的产品创造中。
然而,在注塑过程中,往往会浮现一些质量缺陷问题,这些问题可能会导致产品的性能下降,甚至影响产品的安全性和可靠性。
因此,及时分析和解决这些质量缺陷是非常重要的。
本文将介绍注塑产品常见的13种质量缺陷原因分析及解决办法,以供参考。
1. 毛刺毛刺是指注塑产品表面浮现的细小尖刺状突起。
毛刺的浮现可能是由于模具不平整、模具间隙过大、注塑压力过高等原因导致的。
解决办法是检查模具的平整度,调整模具间隙,并适当降低注塑压力。
2. 热缩热缩是指注塑产品在冷却过程中发生尺寸变化。
热缩的原因主要是由于塑料材料的热胀冷缩性质导致的。
解决办法是在设计模具时考虑热缩因素,合理控制注塑温度和冷却时间。
3. 翘曲翘曲是指注塑产品在冷却过程中发生形变,使得产品不平整。
翘曲的原因可能是由于注塑温度不均匀、模具温度不均匀、注塑压力不均匀等造成的。
解决办法是调整注塑温度、模具温度和注塑压力,使其均匀分布。
4. 气泡气泡是指注塑产品内部或者表面浮现的气体会萃现象。
气泡的浮现可能是由于塑料材料中的挥发物没有彻底挥发、注塑温度过高、注塑压力过高等原因导致的。
解决办法是控制注塑温度和压力,选择合适的塑料材料,并进行充分的挤出和干燥处理。
5. 缩孔缩孔是指注塑产品内部浮现的空洞状缺陷。
缩孔的原因可能是由于注塑温度过低、注塑压力不足、模具设计不合理等导致的。
解决办法是提高注塑温度、增加注塑压力,并优化模具设计。
6. 裂纹裂纹是指注塑产品表面或者内部浮现的裂纹状缺陷。
裂纹的浮现可能是由于注塑温度过高、注塑压力过大、冷却时间过短等原因导致的。
解决办法是降低注塑温度、减小注塑压力,并延长冷却时间。
7. 毛边毛边是指注塑产品边缘浮现的不平整现象。
毛边的原因可能是由于模具设计不合理、注塑压力过高、注塑速度过快等导致的。
解决办法是优化模具设计,降低注塑压力,并适当调整注塑速度。
塑料件常见缺陷及对策手册

塑料件常见缺陷及对策手册塑料件是现代工业中较为常见的一种材料,广泛用于各种机械、电子、医疗设备以及家电等领域。
但是,由于塑料本身的特性和生产加工技术不断更新换代,塑料件在生产过程中常出现一些常见缺陷,严重影响产品的质量和使用寿命。
针对这些常见缺陷,本文就提出了一些对策和解决方案,在生产中有所帮助。
1.针孔和气泡针孔和气泡是塑料制品生产中常见的缺陷,往往由于原料中的杂质和空气等引起。
如果针孔和气泡在外观上很明显,不仅会影响产品的美观度,还会导致产品的硬度和韧度变得不均匀,影响产品的机械性能。
针对这一问题,可以采取以下措施:(1) 优化塑料配方的设计,降低原料中的杂质含量;(2) 调节注塑机的注射速度和注塑温度,保证原料流动性良好;(3) 选择合适的模具设计,提高塑料制品的压力和速度,确保产品内部牢固性。
2. 热分解和氧化热分解和氧化是塑料制品在加热后或存放时间较长后表现出来的特点,也是塑料件常见的缺陷之一。
这种缺陷会使得塑料制品变得脆弱和失去抗老化能力,其外观和性能都会明显改变。
针对这一问题,可以采取以下措施:(1) 选用高质量的塑料原料或添加剂,降低其分解和氧化的风险;(2) 保证存储环境温度和湿度适宜,避免对塑料制品的影响;(3) 通过在塑料制品表面覆盖一层防护层来防止空气和其他化学物质对其的侵蚀。
3. 毛边和裂口毛边和裂口是塑料件在加工过程中常见的缺陷,往往由于模具的设计不当或材料的选用不当引起。
如果毛边和裂口很严重,会对产品的安全性造成威胁,同时也会降低产品的使用寿命。
针对这一问题,可以采取以下措施:(1) 优化模具设计,减少毛边和裂口的产生;(2) 使用高质量的塑料原料和添加剂,提高塑料制品的强度和韧性;(3) 增加塑料制品加工的压力和温度,提高塑料制品的内部固结性。
4. 颜色不均匀在塑料制品加工过程中,颜色不均匀是一个常见问题。
如果塑料部件的颜色不均匀,会影响产品的美观度,使得产品的整体质量变差。
塑件常见不良原因及解决对策

Seahort ; 二,縮陷sink mark ; 三,結合線 ; 四,波紋、流紋 ; 五,白紋、雙色 ; 六,焦斑、黑條紋 ;
七,毛邊 ; 八,噴射流 ; 九,針孔、氣泡 ; 十,銀條 ; 十一,翹曲、彎曲 ; 十二,剝離 ; 十三,白化、裂痕 ; 十四,傷痕 ;
或在模穴內開一個容料穴 9.模內流道轉彎有死角存在,宜設計成圓弧
狀 10.澆口太狹小,塑料瞬間流過是產生高熱.
由塑料中溢出揮發性氣體
十一,翹曲、彎曲
1,原因:由於塑膠成型尺寸流動方向的收 縮率比垂直方向的大,使制件各向收縮率 不同而翹曲。
2,主要類型有:變形、彎曲、扭曲。模具 設計決定了制件的翹曲傾向,要通過變更 成型條件來抑制這種情況十分困難,所以 最終解決問題的須從模具入手。
2,對策:1).使用流動性較好之塑料
2).模穴增開通氣孔
3).模穴加開容料穴,成型后予
以切除
4.結合處稍透氣
5.在添加玻璃纖維塑料的成型作業上,結合部會因 為纖維方向混亂而使強度降低,
此時可在結合部增加肉厚,成型后再予以切除.
平板狀成品之結合線處理方法: 1. 變換澆口之位置 2. 肉厚適當的增加或減少 3. 利用澆道與容料穴適當配合 4. 模穴內部溫度 ,部分做適當的變化 5. 變換射出速度 6. 成品表面烙印花紋,使結合線不明顯 7. 圈狀成品可合用下列澆注法,使結合線不明顯
十五,離型不良(成品粘模 ); 十六,異物混入 ; 十七,脆弱 ; 十八,尺寸精密度不良 ; 十九,其它注意事項;
一,充填不足short
1,現象:在成品上產生缺角 ; 2,原因:塑料注入模穴內,末端尚未填滿之前產生
塑料注塑常见不良原因和改善对策
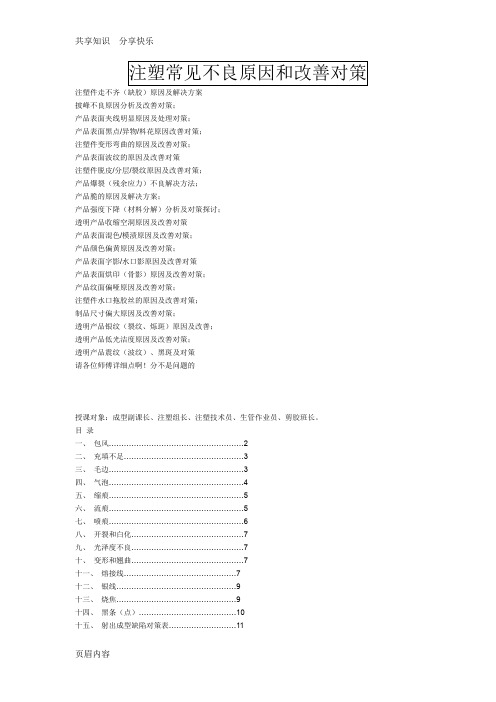
注塑常见不良原因和改善对策注塑件走不齐(缺胶)原因及解决方案披峰不良原因分析及改善对策;产品表面夹线明显原因及处理对策;产品表面黑点/异物/料花原因改善对策;注塑件变形弯曲的原因及改善对策;产品表面波纹的原因及改善对策注塑件脱皮/分层/裂纹原因及改善对策;产品爆裂(残余应力)不良解决方法;产品脆的原因及解决方案;产品强度下降(材料分解)分析及对策探讨;透明产品收缩空洞原因及改善对策产品表面混色/模渍原因及改善对策;产品颜色偏黄原因及改善对策;产品表面字影/水口影原因及改善对策产品表面烘印(骨影)原因及改善对策;产品纹面偏哑原因及改善对策;注塑件水口拖胶丝的原因及改善对策;制品尺寸偏大原因及改善对策;透明产品银纹(裂纹、烁斑)原因及改善;透明产品低光洁度原因及改善对策;透明产品震纹(波纹)、黑斑及对策请各位师傅详细点啊!分不是问题的授课对象:成型副课长、注塑组长、注塑技术员、生管作业员、剪胶班长。
目录一、包风 (2)二、充填不足 (3)三、毛边 (3)四、气泡 (4)五、缩痕 (5)六、流痕 (5)七、喷痕 (6)八、开裂和白化 (7)九、光泽度不良 (7)十、变形和翘曲 (7)十一、熔接线 (7)十二、银线 (9)十三、烧焦 (9)十四、黑条(点) (10)十五、射出成型缺陷对策表 (11)一、包风:(1)现象:空气或气体不及排出,被熔胶波前包夹在型腔内。
(2)可能原因:射出成型机1. 射速过高。
制品1. 壁厚差异太大。
壁厚差异太大时,薄壁处塑流迟缓,熔胶循厚壁快速超前,有可能对模穴中空气或气体进行包抄,形成包风。
模具1. 浇口位置不当。
浇口位置不当时,塑流有可能包抄空气或气体,形成积风。
更改浇口位置,可以改变充填模式,包风有可能避免。
2. 流道(Runner)或浇口尺寸不当多浇口设计时,流道或/和浇口尺寸如果不当,塑流有可能包抄空气或气体,形成包风。
3. 排气不良若是排气不良,波前收口处会卷入空气或气体,形成包风。
塑料件缺陷原因及改进方法

塑料件缺陷原因及改进方法
一、缺陷原因
1、原料质量低
塑料的弹性、热稳定性及耐腐蚀性是由其原料的质量和成形工艺决定的,原料质量低、成分不符合要求,缺乏纯度和着色,以及尺寸误差等,都会导致塑料件使用性能不稳定,影响整体产品质量。
2、成型条件不合理
塑料件的成型条件在很大程度上影响了其使用性能,不合理的成型条件,如温度太低或太高,塑料流动性差,成型时间太短或太长等,都会导致塑料件加工质量不高,从而影响使用性能。
3、模具设计不规范
塑料模具设计不规范,如分流错误,塑料流通不良,塑料不能完全填满模具,从而导致塑料件加工不精细,使用性能受到影响。
4、冷却条件不适宜
塑料件的冷却条件也影响其使用性能,冷却条件不适宜,会导致塑料件加工质量不高,从而影响整体塑料件使用性能。
5、模具结构不当
不当的模具结构,如模具尺寸过大或过小,模具表面平整程度不够,模具夹具不够,都会导致塑料件成型不正确,从而影响使用性能。
二、改进方法
1、改善原料质量
改善原料质量,确保原料的成分纯度,粒度细化和着色,以及尺寸误差等,以确保塑料件质量。
2、优化成型条件
优化成型条件。
塑件缺陷原因及改善方法
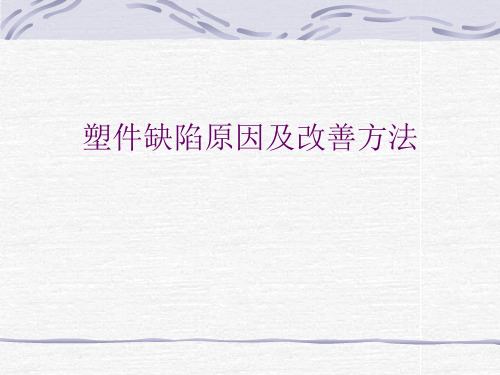
3. 厚壁塑件是最容易产生缩水的,为 减少缩水的出现,浇口形式的选择较为 关键,如翼式浇口对消除缩水的效果就 非常好。
4. 模具冷却不均衡或冷却不足,很易 产生缩水,对此,必须重视冷却系统的 设计和制造,对于易产生缩水的部位应 强化冷却措施。
5. 熔体温度太高,塑件冷却不足,容 易引起塑件凹陷,对此,应降低熔体温 度。
10.
注塑机的喷嘴孔太小或局部堵塞,
会使注射压力局部损失过大,易产生缩
水,对此,应更换大直径的喷嘴,或对
喷嘴进行清理疏通。
11.
树脂的收缩率越大,产生的缩水
可能越大,因此,应尽量先用低收缩率
的树脂为原料。
七.塑件产生气泡的原因和 改善方法?
塑件中之所以出现气泡,是因为有大 量气体混入熔体中,随熔体一起冷却成 型而得。其具体分析如下:
(1) 采用直浇口,在塑件保压结束后,型腔 中的压力比浇口前方的压力高,如此时直浇口 处的熔体尚未固化,就会发生熔体回流,使塑 件内部产生真空泡,对此,应避免选用直浇口。
(2) 浇口面积过小,或位置不正确,易于引 起真空泡,对此,要调整浇口截面积及位置。
(3) 浇口位置没有设在壁厚处,则易出现真 空泡,对此,浇口应设在塑件的厚壁处。
12. 止逆阀出现故障,会使熔体倒流, 导致熔体供料不足,对此,应检修止逆阀。
13. 射料杆与料筒间的间隙过大,熔体 便会顺其间隙回流,导致供料不足而欠注。 这种间隙过大多是过度磨损造成,对此, 要更换相关零件将其修复。
二.塑件产生夹水线的原因和 改善方法?
产生熔接痕的主要原因,系由若干胶 熔体的型腔中汇合在一起时,在其交汇处 未完全熔合在一起,彼此不能熔合为一体 而形成夹水线。其具体分析如下:
8. 保压压力过高,塑件成型时的内应力会过 高,脱模后,内应力的不均衡释放将使塑件产 生翘曲变形,对此,应适当降低保压压力。
塑胶制品不良及处理方法

塑胶制品不良及处理方法塑胶制品在工业和日常生活中广泛应用,但在制造过程中可能会出现一些质量问题。
本文将讨论几种常见的塑胶制品不良及处理方法。
1.塑胶制品外观不良外观不良是塑胶制品质量问题中最常见的问题之一、外观不良可以包括划痕、凹陷、色差、气泡等。
外观不良可能会影响产品的美观性以及使用寿命。
处理方法如下:-质量控制:操作人员应该定期对生产设备进行维护和清洁,以确保产品不受机器所带来的污染。
-原料筛选:选择优质的原料,确保原料没有杂质,可以减少外观不良的可能性。
-温度控制:应严格控制注塑机的温度,以确保塑料可以完全熔融,并避免过热或过冷引起的不良问题。
-模具维护:定期检查和维护模具,确保模具表面平整,避免刮伤或凹陷的问题。
2.塑胶制品尺寸不良塑胶制品尺寸不良是另一个常见的质量问题。
尺寸不良可能会导致产品无法正确组装或无法正常工作。
处理方法如下:-注塑机参数调整:通过调整注塑机的参数,如压力、速度和时间,可以控制产品的尺寸。
-模具调整:通过调整模具的设计和尺寸,可以改善产品的尺寸控制。
-质量检测:建立严格的质量检测流程,包括产品尺寸的测量,及时发现尺寸不良问题并及时采取措施进行修正。
3.塑胶制品强度不良塑胶制品的强度不良可能出现在注塑过程中未完全熔融,或者原料选择不当造成的问题。
处理方法如下:-材料选择:选择适合产品要求的塑料材料,确保材料具有足够的强度和硬度。
-模具温度控制:通过控制注塑机的温度,确保塑料可以完全熔融,并避免产品强度不足的问题。
-模具设计:合理设计模具,确保产品厚度均匀,并避免薄弱区域的出现。
4.塑胶制品耐腐蚀性不良一些塑胶制品需要具有一定的耐腐蚀性,以应对特殊环境下的腐蚀问题。
如果塑胶制品的耐腐蚀性不良,可能会导致产品的性能下降甚至失效。
处理方法如下:-材料选择:选择具有较高耐腐蚀性的塑料材料,如聚酯、聚酰亚胺等,以确保产品具有较好的耐腐蚀性。
-表面处理:对产品进行表面处理,如镀膜、喷涂等,以增加其耐腐蚀性。
- 1、下载文档前请自行甄别文档内容的完整性,平台不提供额外的编辑、内容补充、找答案等附加服务。
- 2、"仅部分预览"的文档,不可在线预览部分如存在完整性等问题,可反馈申请退款(可完整预览的文档不适用该条件!)。
- 3、如文档侵犯您的权益,请联系客服反馈,我们会尽快为您处理(人工客服工作时间:9:00-18:30)。
十九,其它注意事項;
•
因此無論料管或模具欲使其溫度保持不變必需 維持其進出之熱平衡,欲使其進出熱維持平衡則 必須維持一恆定的周期時間,如周期愈來愈快則 料管中之熱入不越出,以致不足以塑化原料,模 具中之熱又入多於出,以致模溫不斷升高,反之 將有相關之結果,因此在任何一個成型操作中, 尤其插入手動操作必須控制穩定周期時間,盡量 避免快慢不一,如其他條件維持不變則:
十一,翹曲、彎曲
• 1,原因:由於塑膠成型尺寸流動方向的收 縮率比垂直方向的大,使制件各向收縮率 不同而翹曲。 • 2,主要類型有:變形、彎曲、扭曲。模具 設計決定了制件的翹曲傾向,要通過變更 成型條件來抑制這種情況十分困難,所以 最終解決問題的須從模具入手。
• 3,對策: • 1,公、母模溫度不一,冷卻後有向公模或 母模彎曲變形。 • 2,料溫、模溫過低,則以高壓充模,分子取 向程度增高 • 3,因澆口位置不對,尤其是針對細長成品, 最易變形模具肉厚之懸殊太大,促使後冷卻收縮 面變形模具的粘模力過大,促使頂出力增加,頂 出時變形.
a.在A部輸入多量的水、B部輸入少量的水;在A部輸入低溫的水、B部輸入較高 溫的水 b.在A部之孔較接近成品、B部較遠離成品,通入等量的水 c.在A部開較大的孔,B部開較小的孔,通入等量的水 以上三方法皆可使模穴冷卻速度平衡,但最好的方法還是在設計產品時,盡量讓肉 厚平均,不要有特別厚的地方出現.
以下諸方法可供參考
• 圈狀成品肉厚與孔徑比例須恰當 • POM,t>1/4D • PS,AS,t>7/10D • ABS,變性PPO,t>1/2D • PS,AS料容易產生龜裂,宜特別留意
十四,傷痕
• 1,現象:成形品表面產生不正常之傷痕 • 2,原因:模具加工不良,模具設計不良 • 3,對策:拔模斜度修改之(一般在1-3° 之間).降低射出壓力.
陷縮 陷縮
增大通道 追加一澆道 陷縮
縮小樑柱厚度
三,結合線
• 1,現象:塑料流過空穴,或窗口狀開關口后,在 接合處發生接合困難而產生母痕 • 2,對策:1).使用流動性較好之塑料 • 2).模穴增開通氣孔 • 3).模穴加開容料穴,成型后予
•
以切除
4.結合處稍透氣
• 5.在添加玻璃纖維塑料的成型作業上,結合部會因 為纖維方向混亂而使強度降低, • 此時可在結合部增加肉厚,成型后再予以切除.
• 1,現象:在澆口附近的成品表面,產生年輪狀的 紋理,稱為波紋.而遠離澆口的紋理,則 • 稱為流紋. • 2,原因:塑料溫度過高,塑料溫度不均勻,模 溫過底,塑料冷卻太早時,隨后進入之塑料因免 強推擠而產生凹凸不平的紋路,光線照射下會產 生光波干涉,而有彩虹狀出現.
• 3,對策:增加塑料之流動性.壓力速度適當提高, 以防止波象:成形品內附金屬粉,塵埃等異物 • 2,原因:塑料在儲運中遭污染,料管或螺杆磨損 • 3,對策:加強塑料之管理,機械定期檢查,維修
十七,脆弱
• 1,現象:成形品的強度,剛性等物理性質,比原 材料標準值差很多 • 2,原因:原因很多,無法做說述 • 3,對策:盡量減低成品殘留內應力,降低二次料 混合比率
十八,尺寸精密度不良
• 1,原因:冷卻收縮為最大根本原因,成形條件不 良也會產生 • 2,對策:成形條件方面,改變模具溫度.控制室 溫,有良好的效果.冷卻收縮量,請自行參考模 具設計技術.
• 以上列舉的各種問題,其原因及對策大多數都與 周期(CYCLE TIME)的穩定性有關,因為無論 塑膠粒在料管適當之塑化,或是模具恆溫之保持, 都是熱平衡結果也就是說在整個連續操作中,料 管中之塑膠接受來自螺杆旋轉之磨擦熱,電熱片 之熱,尤其是電熱片之熱又與受熱的時間有關, 其熱量又跟著塑料送入模具,模具之熱來自於塑 料及熱水,損失在成品帶走的,散失在空氣中的, 冷卻水帶走的,
•
五,白紋、雙色
• 1,現象:成型品內部,或表面無法顯現原來的 光澤與顏色,表面出現霧狀、光度不足、透明度 不足; • 2,原因:染色劑選擇不當.螺杆混煉效果不良. 塑料內之添加物受熱分解,燒焦.模具磨 • 損,塑料模具溫度太低,離型劑影響…. • 3,對策:找出確定之原因,予以修正即可.
六,焦斑、黑條紋
八,噴射流 • 1,現象:在成形品表面,尚著澆口產生帶狀
• • 條紋 2,原因:在塑料由澆口射入模內時,邊冷卻, 邊射入而產生塑料固化現象 3,對策:加大澆口,或檢查修正澆道之設計 使用低速射出.模具加模溫控制
• 1, 現象:成品表面出現好像被針刺過的小 孔痕 跡. • 2,原因:塑料中含水 • 3,對策:使用干燥機除去水份
•
•
周期之加快將造成:短射、縮水、變形、粘 模. • 周期之延長將造成:溢料、毛頭、粘模、 變形、原料過熱、甚至燒焦、出現殘留在模中之 焦料又可能造成模具損壞,料管中過熱之原料又 可能造成料管之腐蝕及成品出現黑斑及黑紋. • 每种問題之發生因使用原料不同,其原因 及對策也不盡相同.某些原料具有某獨特之性質, 較易發生獨特的問題,以上所述為日常所見一般 性之問題原因及對策.
九,針孔、氣泡
十,銀條
• 1,現象:成形品表面出現閃耀的銀色絲紋 • 2,原因:水份、空氣、揮發性氣體,未除盡.模內有空 氣.塑料局部產生過熱,銀條發生部分不同,其原因也不 太一樣必須平常多加注意,較易找出正確原因 • 3,對策:
1.塑料充分干燥 • 2.背壓、螺杆轉速,可塑性化,須適當 • 3.高粘度塑料,如果溫度太低則在料管內易產生局部斷熱現象, 此時宜升高料管溫度
• • • • •
十五,離型不良(成品粘模 ); 十六,異物混入 ; 十七,脆弱 ; 十八,尺寸精密度不良 ; 十九,其它注意事項;
一,充填不足short
•1,現象:在成品上產生缺角 ; •2,原因:塑料注入模穴內,末端尚未填滿之前產生 冷卻固化現象或是塑料本身流動性不良,計量不 足,模內排氣不良,流動阻抗太大,鎖模力不足, 均會產生此現象. •3,對策:針對上述個別原因,找出真正毛病予以改 善.
殘留空氣被壓縮
3, 判斷方法: a.在料管內之斷熱現象.其焦斑黑 條,發生在澆口附近,呈不規則性之條紋 b.模內滯留空氣之斷熱現象,其焦 斑,黑條易發生在塑料流動末端部
4,對策: 塑料燒焦:使用安全性較佳之塑料添加劑 瓦斯燒焦: a.設法排出料管之氣體,或尋求合理之 塑化條件 b.降低充填速度 c.增加模內之透氣孔.透氣孔之尺寸約 0.02-0.04mm,尼龍透氣孔約0.0020.004mm,或是在模內開滯氣孔.
十二,剝離
• 1,現象:成形品表面,產生雲母狀之重疊 片 • 2,原因:塑料混入性質不同之塑料 • 3,對策:換新塑料.有時會因為分子配向 性太強而產生,請檢查之。
十三,白化、裂痕
• 1,白化:承受彎曲變形量大時,顏色變白.此易 發生在ABS料上 • 2,裂痕:成形品破裂,或經過長時間后產生裂痕 • 3,對策:白化:增加成品抗彎性 • 裂痕:清除成品內應力 • 如果成品有埋入心形則考慮予以預熱縮小 模內各處之溫差.以降低因溫差太大而引起熱脹 現象不均勻.
塑件成型不良常識
Sean xie
內 容 大 綱
• • • • • • 一,充填不足short ; 二,縮陷sink mark ; 三,結合線 ; 四,波紋、流紋 ; 五,白紋、雙色 ; 六,焦斑、黑條紋 ;
• • • • • • • •
七,毛邊 ; 八,噴射流 ; 九,針孔、氣泡 ; 十,銀條 ; 十一,翹曲、彎曲 ; 十二,剝離 ; 十三,白化、裂痕 ; 十四,傷痕 ;
十五,離型不良(成品粘模)
• • •
• •
設計
1,現象:成品卡在於模內,無法托出 2,原因:模具設計不適當 3,對策:
1,成型條件調整好 2,深盒式成品因彈性變性而卡住,宜改良其
容易變形
3,心型與模穴溫度差不適當
較不變形
4,模穴產生真空吸著,宜加入空壓吹離 5,托模梢卡住成品,宜改良設計 6,射嘴溫度太低
• • • • • • • •
平板狀成品之結合線處理方法: 1. 變換澆口之位置 2. 肉厚適當的增加或減少 3. 利用澆道與容料穴適當配合 4. 模穴內部溫度 ,部分做適當的變化 5. 變換射出速度 6. 成品表面烙印花紋,使結合線不明顯 7. 圈狀成品可合用下列澆注法,使結合線不明顯
四,波紋、流紋
七,毛邊
• 1,現象:在以母模合模面,中子附近,托模梢附 近.產生塑料溢出之毛頭. • 2, 原因:閉模力不足,或太高.模具變形,模 具結合不良,模具內有異物.塑料流動性太好, 塑料射入太多. • 3,對策:在公母模結合而產生之毛邊,如果在短 時間內由小毛邊變成大毛邊,則必須立即檢修模 具.其他原因所產生之毛邊,則須個別予以修正 即可.
• 1,現象:成形品上有點狀,或條紋狀之黑 斑.未變成黑色前之現象稱為變色 • 2, 原因: – 塑料燒焦:塑料內部之添加物過熱分解 – 瓦斯燒焦:a在料管內塑料融化時,混入空 氣,而產生斷熱壓縮現象,瞬間發出高熱, 而產生燒焦. • b模具內塑料急速充填時,模內空 氣無法排出.在成品末端結合線附近,被包圍 之空氣產生斷熱現象而分解,燒焦
•
•
• • • • • • •
4.螺杆產生逆流現象過劇,使空氣混入 5.螺杆牙部間隙太大,使料之傳送效果不良, 此時宜調整螺杆之回轉速度 6.螺杆鬆退距離太長 7.從射嘴牙部混入空氣 8.射嘴口之冷料進入模內,宜使用低速射出 或在模穴內開一個容料穴 9.模內流道轉彎有死角存在,宜設計成圓弧 狀 10.澆口太狹小,塑料瞬間流過是產生高熱. 由塑料中溢出揮發性氣體
二,縮陷sink mark
1,現象:成品冷卻收縮后,產生凹穴 ; 2,原因:1)、塑料注入模穴內,與模壁接 觸后, 開始冷卻硬化,而產生內張 力所引起 2)、在肉厚部分,因體積縮量較大,也 較易產生縮陷 3,對策:1、加上保壓,補充冷卻收縮量,使成品 各部分冷卻速度均衡如圖示