磨削用量的选择
不锈钢磨削的特点及磨削用量的选择原则
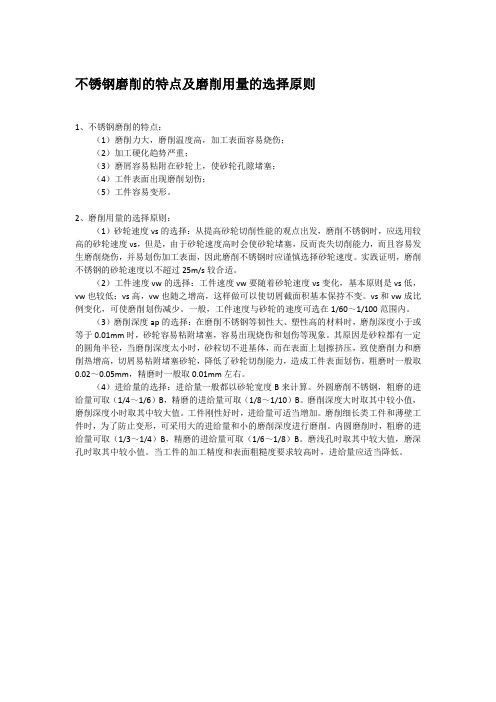
不锈钢磨削的特点及磨削用量的选择原则1、不锈钢磨削的特点:(1)磨削力大,磨削温度高,加工表面容易烧伤;(2)加工硬化趋势严重;(3)磨屑容易粘附在砂轮上,使砂轮孔隙堵塞;(4)工件表面出现磨削划伤;(5)工件容易变形。
2、磨削用量的选择原则:(1)砂轮速度vs的选择:从提高砂轮切削性能的观点出发,磨削不锈钢时,应选用较高的砂轮速度vs,但是,由于砂轮速度高时会使砂轮堵塞,反而丧失切削能力,而且容易发生磨削烧伤,并易划伤加工表面,因此磨削不锈钢时应谨慎选择砂轮速度。
实践证明,磨削不锈钢的砂轮速度以不超过25m/s较合适。
(2)工件速度vw的选择:工件速度vw要随着砂轮速度vs变化,基本原则是vs低,vw也较低;vs高,vw也随之增高,这样做可以使切屑截面积基本保持不变。
vs和vw成比例变化,可使磨削划伤减少。
一般,工件速度与砂轮的速度可选在1/60~1/100范围内。
(3)磨削深度ap的选择:在磨削不锈钢等韧性大、塑性高的材料时,磨削深度小于或等于0.01mm时,砂轮容易粘附堵塞,容易出现烧伤和划伤等现象。
其原因是砂粒都有一定的圆角半径,当磨削深度太小时,砂粒切不进基体,而在表面上划擦挤压,致使磨削力和磨削热增高,切屑易粘附堵塞砂轮,降低了砂轮切削能力,造成工件表面划伤。
粗磨时一般取0.02~0.05mm,精磨时一般取0.01mm左右。
(4)进给量的选择:进给量一般都以砂轮宽度B来计算。
外圆磨削不锈钢,粗磨的进给量可取(1/4~1/6)B,精磨的进给量可取(1/8~1/10)B。
磨削深度大时取其中较小值,磨削深度小时取其中较大值。
工件刚性好时,进给量可适当增加。
磨削细长类工件和薄壁工件时,为了防止变形,可采用大的进给量和小的磨削深度进行磨削。
内圆磨削时,粗磨的进给量可取(1/3~1/4)B,精磨的进给量可取(1/6~1/8)B。
磨浅孔时取其中较大值,磨深孔时取其中较小值。
当工件的加工精度和表面粗糙度要求较高时,进给量应适当降低。
普通平面磨床加工超精度、低粗糙度零件

普通平面磨床加工超精度、低粗糙度零件在大型工程机械制造厂磨削表面粗糙度Ra0.02--0.04μm、精度h4--h5的轴颈时,都是在昂贵的高精度平面磨床上进行。
但一般工程机械修造厂却没有高精度平面磨床,要磨削出这样的低的表面粗糙度,如此高的轴颈精度是非常困难的。
我们在现有设备M131W普通外圆平面磨床上进行大量试验,并对其进行必要的检测、刮研和调整,通过修整和精细的平衡砂轮,在磨粒上合适整出更多的等高微刃,就完全可以实现超高精度、低粗糙度的磨销,能有效地磨削出精度h4--h6,粗糙度Ra0.02--0.04μm的零件。
该法简单,方便易行,效果颇佳。
1、超精磨削机理超精磨削是靠砂轮工作面上可以修整出大量等高的磨粒微刃这一特性而得以进行的。
这些等高微刃能从工作表面上切除微薄的、尚具有一些微量缺陷以及微量形状和尺寸误差和余量。
因此,运用这些等微刃具是大量的,如果磨削用量适当,在加工面上有可能留下大量的极微细的切削痕迹,所以可得到很低的表面粗糙度。
此外,还由于在无火光花光磨阶段,仍有很明来的磨擦、滑挤、抛光和压光等作用,故使加工秘得的表面粗糙度进一步降低.2、对普通平面磨床的检修为了在变通平面磨床磨削出粗糙度Ra0.02--0.04μm的工件,应对旧变通平面磨床进行如下项目检测,不符合精度要求的,则要进行刮研检修。
(1)检修床导轨1. 检测和何等刮床身V形导轨:在垂直平面内的不直度,在1m长度上,不得超过0.01mm;在水平面内的不直度,在1m长度上,不得超过0.01mm;与滑鞍座导轨的不垂直度,在250mm长度上,不得超过0.02mm;接触点要求12--14点(25×25)mm。
2. 检测的何等刮床身平面导轨:V形导轨的不平等度,在1m长度上,不得超过0.02mm;在垂直平面内的不直度,在1m长度上,法得超过0.01mm;接触斑点要求12--14点(25×25)mm。
(2)检修滑鞍座导轨1. 检测和何等刮滑鞍座V形导轨;在垂直平面内的不直度,全部长度上不得超过0.01mm;接触斑点要求10--12点(25×25)mm。
磨工技师论文

磨工技师论文2007-11-29 21:30【论文摘要】介绍了一种在普通外圆磨床上高效磨削高精度、低粗糙度细长轴的新工艺,其特点是操作简便,容易掌握,对工人技术水平要求低,在磨削过程中随时都可知道切削力、挤压力的大小,这种工艺非常适用于长径比L/D≥50的细长轴、难加工材料和较硬材质的超精磨削。
0 引言在普通外圆磨床上超精磨削细长轴一直是老大难问题,特别是,当工件的长径比超过30(L/D>30)时,尤为困难。
美国中小型机械修造公司(厂)的长期实践表明,只要检修、调整好普通外圆磨床,合理地选择砂轮、磨削用量和工艺过程,就能满足细长轴的技术要求。
1 磨削前的几项准备工作1.1 校直细长轴校直方法有热校和冷校两种方法,热校比冷校理想。
校直后的弯曲度应控制在工件每1000mm 长度,其弯曲度在0.15mm以内。
1.2 中心孔中心孔是细长轴的基准、细长轴经过热处理后,中心孔将会产生变形,应对中心孔进行研磨,使其60°锥孔和圆度达到标准要求。
1.3 检修机床保证检修后的外圆磨床各项精度达到出厂时指标。
1.4 调整机床主要是调整头架与尾架间的中心距离。
将工件顶在两顶尖间,用手旋转工件。
感觉不松不紧为好,如果尾座顶尖是弹簧式的,可使弹簧顶尖压缩0.5~2m m,再顶住工件中心孔。
1.5 检查工件两顶尖顶住工件,先用百分表对细长轴的全长作径向跳动检查,特别是对中间弯曲度最大的地方,观察其跳动量方向是否一致。
然后再用千分尺检查工件的磨削余量和各项尺寸。
细长轴的磨削余量取较小值为宜。
图1 砂轮形状2 砂轮及磨削用量的选择2.1 砂轮的选择根据细长轴材料的不同,选择不同磨料、硬度、粒度的砂轮,这是很重要的。
磨细长轴的砂轮硬度应稍软,粒度应稍粗。
砂轮的形状如图1所示,中间呈凹形,因为中凹形砂轮不但可减少砂轮与工件的接触面积,而且砂轮整体宽度不变,可以减少细长轴在旋转中产生自激振动,砂轮的选择见表1。
表1 砂轮的选择工件材料砂轮磨料硬度粒度铸铁THR3~ZR446~70碳钢GZ GBR3~ZR146~70不锈钢GD GWR3~Z R146~702.2 切削用量的选择从表2中可以看出细长轴磨削的几个特点:表2 切削用量的合理选择磨削对象磨削用量名称粗磨精磨修整砂轮工作台纵向速度S/(m/min)横向切深t/(mm/单行程)1~1.50.07~0.100.3~0.80.05~0.01光修一次磨削工件工件线速度v/(m/min)工作台纵向速度S/(m/min)磨削切深t/(mm/双行程)2.5~81.20.01~0.152~50.6~0.80.005光磨数次 a.修整砂轮的走刀量S、切深t均比一般磨削大,可使砂轮的表面比较粗糙,以增强切削性能;b.磨削时工件的转速较低,精磨时更低,这是为了减少细长轴因旋转而产生的振荡,而走刀量较大,以便将一部分切向力转化为轴向力,减少径向力Py;c.磨削时切深t用双行程来达到。
磨削加工技术解读

五、磨床
磨床是用磨料磨具(砂轮,砂带,油石和研 磨料)为工具进行切削加工的机床。广泛用 于零件的精加工,尤其是淬硬钢件,高硬度 特殊材料及非金属材料(如陶瓷)的精加工。
磨床种类很多,其主要类型有:外圆磨床, 内圆磨床,平面磨床,工具磨床,刀具和刃 具磨床及各种专门化磨床.如曲轴磨床、凸 轮磨床、齿轮磨床、螺纹磨床等。。此外 还有珩磨机,研磨机和超精加工机床等。
磨料
磨粒 微粉<63μm
磨粒粒度号越大越细, 微粉粒度号越小越细。
2. 砂轮的特性及选择
3)磨料粒度
取决于加工表面的粗糙度的要求
选择原则:
加工表面粗糙度值越大 →选用越粗的磨料 加工表面粗糙度值越小 →选用越细的磨料 砂轮速度高或与工件接触面大时用粗磨料 磨软材料用粗磨料,磨硬材料用细磨料
2. 砂轮的特性及选用
(。2)磨削加工范围广 各种表面:内外圆表面、圆锥面、平面、齿面、螺旋面 各种材料:普通塑性材料、铸件等脆材、淬硬钢、硬质
合金、宝石等高硬度难切削材料。
(3)磨削速度高、耗能多,切削效率低,磨削温度 高,工件表面易产生烧伤、残余应力等缺陷。
(4)砂轮有一定的自锐性。
磨削加工
• 磨削是一种精加工方法。 • 可加工高硬度材料。 • 可加工各种表面。
磨外圆砂轮的旋转运动N砂;磨内孔砂轮的旋转 运动N内;工件旋转运动N周;工件纵向往复运动F 纵;砂轮横向进给运动f横(往复纵磨时是周期的间 歇运动;切入磨削时 是连续进给运动)。此外,机 床还有两个辅助运动:砂轮架的横向快速进退运动; 尾架套筒的伸缩移动。
头架
工作台
内圆磨具 砂轮架 横向进给机构 尾座
1、外圆磨床
主要用于磨削内,外圆柱和圆锥表面,也能磨阶梯轴 的轴肩和端面,可获得IT6-IT7及精度Ra在1.25-0.08μm之间。
数控磨床综合--技巧,难题,解决方案

数控磨床相关问题综合作者:王家征2012。
5。
6外圆磨床加工工件表面有螺旋线的解决方法产生原因1:修整砂轮方法不妥排除方法1:金钢钻应保持锐利,且颗粒无松动,修整时泠却液应充分,精修整砂轮修整量不宜过大.产生原因2:砂轮主轴与工作台移支平行度超差过大排除方法2:采用专用工具测量主轴平行度如超差应调整,生产中采用试切法验证平行度误差:磨削一根直径与长度比适中的外圆,使锥度达到最小值,精磨时应细修砂轮,在外圆一端或两端涂上一层薄薄的红印油,宽度与砂轮宽度相仿,然后进入切入磨微量进给,直至砂轮刚接触涂色区,擦去一层涂色痕迹,若砂轮宽度全部擦去痕迹表明砂轮母线与工件母线平行良好; 若接触右边局部部分表明主轴呈低头, 若左边接触则主轴呈抬头,注: 动态测量比静态好效果好。
误差方向确定后,且可用垫片测定修刮量。
可以修刮砂轮架滑鞍结合面或垫板底面,如果修整主轴平行度有困难,可以修整金钢钻座,使金钢钻修正中与砂轮中心一致,可减小由于砂轮主轴不平行而引起的砂轮表面修成双曲线。
产生原因3:磨削进给量应根据工件余量合理选择排除方法3:磨削进给量应选择与工件余量保持合适,特别应控制粗磨时的工件余量,否则过大而引起的暗藏的螺旋线就在精磨时显示出来,因此,磨削过程中必须逐级提高表面品质,保持经常修整砂轮防止螺旋线的产生而不消除。
产生原因4:床身导轨或砂轮架导轨在水平面内直线度误差大,影响修整轨迹。
排除方法4: 金钢钻安装位置,尽量使修整位置与磨削位置相同,金钢钻修整器在工作台纵向上的位置,应选择有利修整位置,以解决床身导轨在水平面的变曲。
产生原因5:砂轮主轴轴承间隙大,影响动态效应的刚度降低.排除方法5:应检查轴承间隙,过大时予以调整,参见《砂轮架主轴轴承付》。
产生原因6:头尾架刚性差,支承工件顶尖孔与顶尖小端接触产生支承刚性差. 可回转主轴的顶尖间磨削,可将头架调障至零, 尾架套筒有间隙过大现象予以修复. 工件顶尖孔尽量保持大端接触,尤其是外圆精度较高的工件,建议将中心锥面接触长度控制3—5mm(可将中心孔底孔扩大来达到).产生原因7:工件材料与砂轮不匹配使砂轮不能有效切除工件,而严重钝化。
不同类型平面磨床的区别及磨削操作特点

不同类型平面磨床的区别及磨削操作特点不同类型平面磨床的区别及磨削操作特点一、平面磨削的方式按照平面磨床和工作台的结构特点和配置形式,可将平面磨床分为五种类型,即卧轴矩台平面磨床、卧轴圆台平面磨床、立轴矩台平面磨床、立轴圆台平面磨床及双端面磨床等。
1、平面磨床的类型简介(1)卧轴矩台平面磨床砂轮的主轴轴线与工作台台面平行,工件安装在矩形电磁吸盘上,并随工作台作纵向往复直线运动。
砂轮在高速旋转的同时作间歇的横向移动,在工件表面磨去一层后,砂轮反向移动,同时作一次垂向进给,直至将工件磨削到所需的尺寸。
(2)卧轴圆台平面磨床砂轮的主轴是卧式的,工作台是圆形电磁吸盘,用砂轮的圆周面磨削平面。
磨削时,圆形电磁吸盘将工件吸在一起作单向匀速旋转,砂轮除高速旋转外,还在圆台外缘和中心之间作往复运动,以完成磨削进给,每往复一次或每次换向后,砂轮向工件垂直进给,直至将工件磨削到所需要的尺寸。
由于工作台是连续旋转的,所以磨削效率高,但不能磨削台阶面等复杂的平面。
(3)立轴柜台平面磨床砂轮的主轴与工作台垂直,工作台是矩形电磁吸盘,用砂轮的端面磨削平面。
这类磨床只能磨简单的平面零件。
由于砂轮的直径大于工作台的宽度,砂轮不需要作横向进给运动,故磨削效率较高。
(4)立轴圆台平面磨床砂轮的主轴与工作台垂直,工作台是圆形电磁吸盘,用砂轮的端面磨削平面。
磨削时,圆工作台匀速旋转,砂轮除作高速旋转外,定时作垂向进给。
(5)双端面磨床该磨床能同时磨削工件两个平行面,磨削时工件可连续送料,常用于自动生产线等场合。
2、平面磨削的形式以砂轮工作表面的不同,平面磨削可分为周边磨削、端面磨削以及周边一端面磨削三种方式。
①周边磨削:又称圆周磨削,是用砂轮的圆周面进行磨削。
卧轴的平面磨床属于这种形式。
②端面磨削:用砂轮的端面进行磨削。
立轴的平面磨床均属于这种形式。
③周边一端面磨削:同时用砂轮的圆周面和端面进行磨削。
磨削台阶面时,若台阶不深,可在卧轴矩台平面磨床上,用砂轮进行周边一端面磨削。
影响机械加工表面质量的因素及采取措施毕业论文

影响机械加⼯表⾯质量的因素及采取措施毕业论⽂毕业论⽂(设计)题⽬:影响机械加⼯表⾯质量的因素及采取措施影响机械加⼯表⾯质量的因素及采取措施摘要:机械产品的使⽤性能的提⾼和使⽤寿命的增加与组成产品的零件加⼯质量密切相关,零件的加⼯质量是保证产品质量基础。
衡量零件加⼯质量好坏的主要指标有:加⼯精度和表⾯粗糙度。
本⽂主要通过对影响零件表⾯粗糙度的因素、零件表⾯层的物理⼒学性能(表⾯冷作硬化、残余应⼒、⾦相组织的变化与磨削烧伤)、表⾯质量影响零件使⽤性能等因素的分析和研究,来提⾼机械加⼯表⾯质量的⼯艺措施。
关键词:机械加⼯;表⾯质量;影响因素;控制措施⽬录前⾔ (1)⼀、概述 (1)(⼀)、基本概念 (1)1、机械加⼯ (1)2、零件的失效 (2)3、磨削烧伤 (2)4、表⾯冷作硬化 (2)⼆、影响⼯件表⾯质量的因素 (2)(⼀)、加⼯过程对表⾯质量的影响 (2)1、⼯艺系统的振动对⼯件表⾯质量的影响 (2)2、⼑具⼏何参数、材料和刃磨质量对表⾯质量的影响 (2)3、切削液对表⾯质量的影响 (3)4、⼯件材料对表⾯质量的影响 (3)5、切削条件对⼯件表⾯质量的影响 (3)6、切削速度对表⾯粗糙度的影响 (4)7、磨削加⼯影响表⾯质量的素 (4)8、影响⼯件表⾯物理机械性能的素 (5)(⼆)、使⽤过程中影响表⾯质量的因素 (7)1、耐磨性对表⾯质量的影响 (7)2、疲劳强度对表⾯质量的响 (8)3、耐蚀性对表⾯质量的响 (8)三、机械加⼯表⾯质量对零件使⽤性能的影响 (8)(⼀)、表⾯质量对零件耐磨性的影响 (8)(⼆)、表⾯质量对零件疲劳强度的影响 (9)(三)、表⾯质量对零件耐腐蚀性能的影响 (9)(四)、表⾯质量对零件间配合性质的影响 (9)(五)、表⾯质量对零件其他性能的影响 (10)四、控制表⾯质量的途径 (10)(⼀)、降低表⾯粗糙度的加⼯⽅法....、 (10)(⼆)、改善表⾯物理⼒学性能的加⼯⽅法 (13)五、提⾼机械加⼯⼯件表⾯质量的措施 (15)六、结论 (16)七、参考⽂献 (16)前⾔随着⼯业技术的飞速发展机械化⽣产以⾛进各⼤⼩企业,与之息息相关的就是各式各样的机器。
第 章 切削用量及其计算

般采用普通速度,即υs≤35m/s。有时采用高速磨削,即υs>35m/s,如 45m/s, 50m/s,60m/s, 80m/s
或更高。磨削用量的选择步骤是:先选较大的工件速度υw,再选轴向进给量 fa,最后才选径向 进给量 fr。
(a)圆柱铣刀铣平面
(b)端铣刀铣平面
(c)立铣刀铣槽
图 14-1 不同铣削加工的切削要素
68.8 37.6
0.40 0.20 —
0.50 0.25
表 14-2 车削过程使用条件改变时的修正系数
(一)与车刀寿命有关
刀具 材料
工件材料
车刀形式
寿命 工作
T/min 30 60 90 120 150
修正系数
240 360
329
机械制造技术基础与工艺学课程设计教程
κ
' r
①组合机床切削用量应比普通机床低 30%,以减少换刀时间,提高经济效益。
②组合机床上的多种同时工作的刀具,其合理切削用量是不同的。如钻头要求υc 高 f 小,
而铰刀则要求υc 低 f 大。但动力头每分钟的进给量却是一样的。为使各刀具都有较合适的切削
用量,应首先列出各刀具独自选定的合理值,然后以“每分钟进给量相等”为标准进行折中,
前孔的半径之差。
(3)铣削加工要注意区分铣削要素
υc——铣削速度,m/min, υc
=
πd0n 1000
;
d0——铣刀直径,mm;
n——铣刀转速,r/min;
f——铣刀每转工作台移动距离,即每转进给量,mm/r;
fz——铣刀每齿工作台移动距离,即每齿进给量,mm/z;
υf ——进给速度,即工作台每分钟移动的距离,mm/min, υf=fn=f zzn;
磨削用量的选择
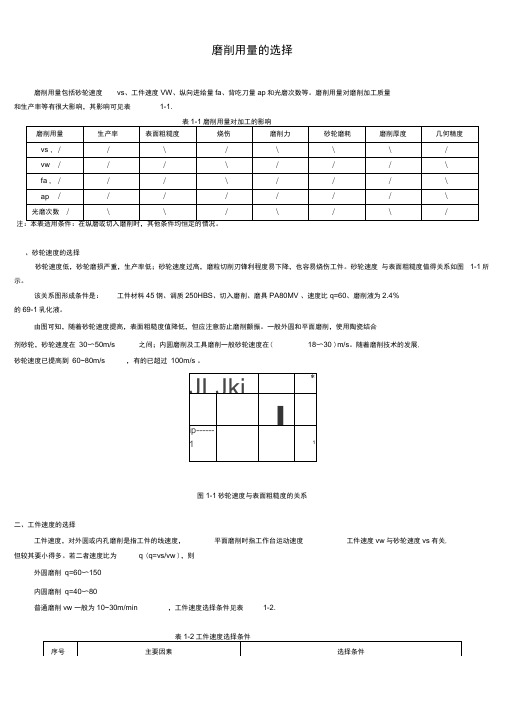
工件速度vw 与砂轮速度vs 有关,磨削用量的选择磨削用量包括砂轮速度 vs 、工件速度VW 、纵向进给量fa 、背吃刀量ap 和光磨次数等。
磨削用量对磨削加工质量和生产率等有很大影响,其影响可见表1-1.、砂轮速度的选择砂轮速度低,砂轮磨损严重,生产率低;砂轮速度过高,磨粒切削刃锋利程度易下降,也容易烧伤工件。
砂轮速度 与表面粗糙度值得关系如图 1-1所示。
该关系图形成条件是: 工件材料45钢、调质250HBS 、切入磨削、磨具PA80MV 、速度比q=60、磨削液为2.4%的69-1乳化液。
由图可知,随着砂轮速度提高,表面粗糙度值降低,但应注意防止磨削颤振。
一般外圆和平面磨削,使用陶瓷结合 剂砂轮,砂轮速度在 30〜50m/s 之间;内圆磨削及工具磨削一般砂轮速度在( 18〜30 )m/s 。
随着磨削技术的发展,砂轮速度已提高到 60~80m/s,有的已超过 100m/s 。
图1-1砂轮速度与表面粗糙度的关系二、工件速度的选择工件速度,对外圆或内孔磨削是指工件的线速度, 平面磨削时指工作台运动速度但较其要小得多。
若二者速度比为q (q=vs/vw ),则外圆磨削 q=60〜150 内圆磨削 q=40〜80普通磨削vw 一般为10~30m/min,工件速度选择条件见表1-2.三、纵向进给量的选择纵向进给量的大小影响工件的表面质量和生产率。
纵向进给量大,增加磨粒的切削负荷,磨削力大;纵向进给量小, 易使工件烧伤。
粗磨钢件fa= ( 0.3~0.7 ) B mm/r粗磨铸铁fa= ( 0.7~0.8 ) B mm/r精磨fa= ( 0.1~0.3 ) B mm/r四、背吃刀量的选择磨削背吃刀量通常数值很小。
一般外圆纵磨粗磨钢件ap=0.02~0.05mm粗磨铸铁ap=0.08~0.15mm精磨钢件ap=0.005~0.01mm精磨铸铁ap=0.02~0.05mm外圆切入磨普通磨削ap=0.001~0.005mm精密磨削ap=0.0025〜0.005mm内圆磨削背吃刀量更小一些。
磨削实习报告(多篇)
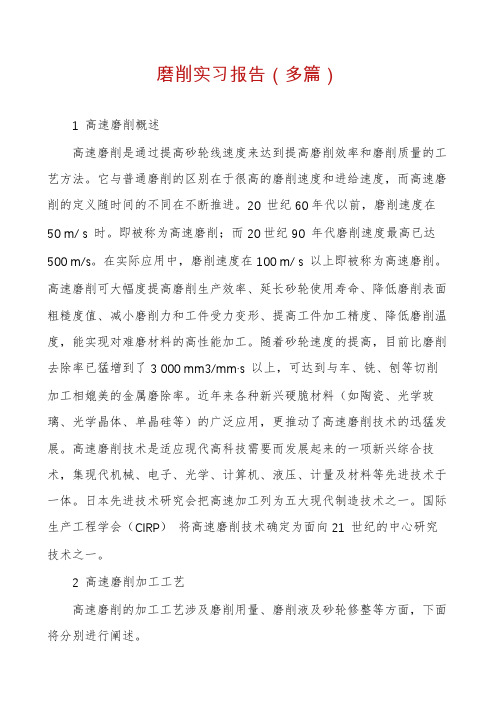
磨削实习报告(多篇)1 高速磨削概述高速磨削是通过提高砂轮线速度来达到提高磨削效率和磨削质量的工艺方法。
它与普通磨削的区别在于很高的磨削速度和进给速度,而高速磨削的定义随时间的不同在不断推进。
20 世纪60年代以前,磨削速度在50 m/ s 时。
即被称为高速磨削;而20世纪90 年代磨削速度最高已达500 m/s。
在实际应用中,磨削速度在100 m/ s 以上即被称为高速磨削。
高速磨削可大幅度提高磨削生产效率、延长砂轮使用寿命、降低磨削表面粗糙度值、减小磨削力和工件受力变形、提高工件加工精度、降低磨削温度,能实现对难磨材料的高性能加工。
随着砂轮速度的提高,目前比磨削去除率已猛增到了3 000 mm3/mm·s 以上,可达到与车、铣、刨等切削加工相媲美的金属磨除率。
近年来各种新兴硬脆材料(如陶瓷、光学玻璃、光学晶体、单晶硅等)的广泛应用,更推动了高速磨削技术的迅猛发展。
高速磨削技术是适应现代高科技需要而发展起来的一项新兴综合技术,集现代机械、电子、光学、计算机、液压、计量及材料等先进技术于一体。
日本先进技术研究会把高速加工列为五大现代制造技术之一。
国际生产工程学会(CIRP)将高速磨削技术确定为面向21 世纪的中心研究技术之一。
2 高速磨削加工工艺高速磨削的加工工艺涉及磨削用量、磨削液及砂轮修整等方面,下面将分别进行阐述。
2.1 磨削用量选择在应用高速磨削工艺时,磨削用量的选择对磨削效率、工件表面质量以及避免磨削烧伤和裂纹十分重要。
表1 给出了磨削用量与砂轮速度的关系。
除了砂轮速度以外,决定磨削用量的因素还有很多,因此应用中需综合考虑加工条件、工件材料、砂轮材料、冷却方式等因素,以选择最优的磨削用量。
2.2 磨削液在高速磨削过程中,所采用的冷却系统的优劣常常能决定整个磨削过程的成败。
冷却润滑液的功能是提高磨削的材料去除率,延长砂轮的使用寿命,降低工件表面粗糙度值。
它在磨削过程中必须完成润滑、冷却、清洗砂轮和传送切削屑四大任务,与普通磨削液要求类似。
表1-1 无心磨床粗磨的磨削用量(通磨钢制零件外圆)
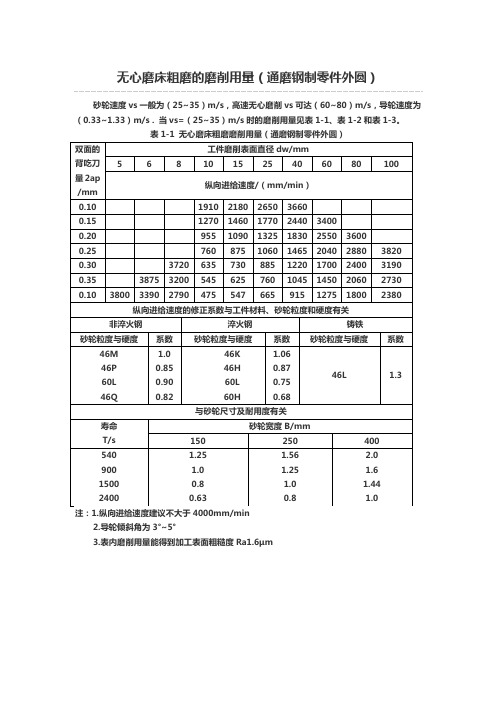
无心磨床粗磨的磨削用量(通磨钢制零件外圆)砂轮速度vs一般为(25~35)m/s,高速无心磨削vs可达(60~80)m/s,导轮速度为(0.33~1.33)m/s . 当vs=(25~35)m/s时的磨削用量见表1-1、表1-2和表1-3。
表1-1 无心磨床粗磨磨削用量(通磨钢制零件外圆)双面的背吃刀量2ap /mm工件磨削表面直径dw/mm5 6 8 10 15 25 40 60 80 100纵向进给速度/(mm/min)0.10 1910 2180 2650 36600.15 1270 1460 1770 2440 34000.20 955 1090 1325 1830 2550 36000.25 760 875 1060 1465 2040 2880 3820 0.30 3720 635 730 885 1220 1700 2400 3190 0.35 3875 3200 545 625 760 1045 1450 2060 2730 0.10 3800 3390 2790 475 547 665 915 1275 1800 2380纵向进给速度的修正系数与工件材料、砂轮粒度和硬度有关非淬火钢淬火钢铸铁砂轮粒度与硬度系数砂轮粒度与硬度系数砂轮粒度与硬度系数46M 46P 60L 46Q 1.00.850.900.8246K46H60L60H1.060.870.750.6846L 1.3 与砂轮尺寸及耐用度有关寿命T/s砂轮宽度B/mm150 250 400540 900 1500 2400 1.251.00.80.631.561.251.00.82.01.61.441.0注:1.纵向进给速度建议不大于4000mm/min2.导轮倾斜角为3°~5°3.表内磨削用量能得到加工表面粗糙度Ra1.6μm。
磨削烧伤及预防措施
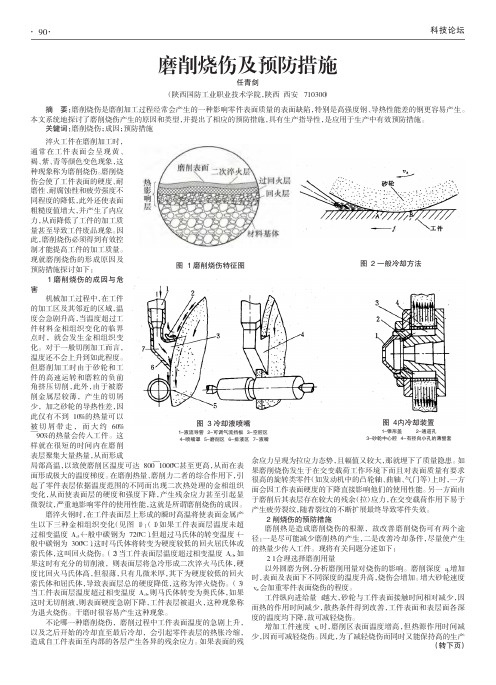
[3]朱正德.工件磨削烧伤及其检测、评定方法简析[J].柴油机设计与
另外在使用砂轮时可以在砂轮圆周上开槽,使砂轮间断磨削, 制造,2013,19(2):36-39.
工件受热时间短,金相组织来不及转变,同时又改善了散热条件,对 [4]刘高群,杨洪平.磨削烧伤研究[J].航空精密制造技,2011,47(2):54-
图 4 内冷却装置
1- 锥形盖 2- 通道孔 3- 砂轮中心腔 4- 有径向小孔的薄璧套
表层聚集大量热量,从而形成
余应力呈现为拉应力态势,且幅值又较大,那就埋下了质量隐患。如
局部高温,以致使磨削区温度可达 800 ̄1000℃甚至更高,从而在表 果磨削烧伤发生于在交变载荷工作环境下而且对表面质量有要求
防止烧Байду номын сангаас效果良好。
56.
2.3 冷却条件
[5] 郭 长 永 . 磨 削 烧 伤 的 成 因 及 预 防 措 施 [J] 科 技 信 息 ,2011,19:513 -
采用切削液带走磨削区的热量可以避免烧伤。目前通用的冷却 513.
方法效果较差,由于高速旋转的砂轮表面上产生强大气流层,实际
作者简介:任青剑(1960-),男,本科,陕西国防工业职业技术学院,
过相变温度 Ac3(一般中碳钢为 720℃),但超过马氏体的转变温度(一 径:一是尽可能减少磨削热的产生,二是改善冷却条件,尽量使产生
般中碳钢为 300℃),这时马氏体将转变为硬度较低的回火屈氏体或 的热量少传入工件。现将有关问题分述如下:
索氏体,这叫回火烧伤。(2)当工件表面层温度超过相变温度 Ac3,如
对于硬度太高的砂轮,钝化砂粒不易脱落,容易产生烧伤,因此 [2]黄新春,张定华,姚倡锋,任敬心.超高强度钢 AerMetloo 磨削烧伤研
刀具几何参数与切削用量的合理选择

切削热
合理的刀具几何参数和切 削用量可以降低切削热, 减少因热变形对加工精度 的影响,提高加工效率。
04 实际应用案例分析
案例一
总结词
根据工件材料和加工要求,选择合适的刀具几何参数和切削用量,提高加工效率和表面 质量。
详细描述
在车削加工中,刀具的几何参数如前角、后角和刃倾角对切削力和切削热有显著影响。 前角增大,切削力减小,切削热增加;后角增大,切削热减少,但切削力可能增大。选 择合适的切削用量,如切削速度、进给量和切削深度,可以优化加工效率和表面质量。
刀具主副偏角
主副偏角的大小影响切削层的形状和切削宽度。减小主副 偏角,可减小切削层的截面积,降低切削力,但刀尖强度 减弱。
切削用量对加工质量的影响
1 2
切削速度
切削速度过高可能导致工件表面粗糙度增加或产 生积屑瘤;切削速度过低则可能使切削力增大, 导致刀具磨损。
进给量
进给量过大会导致切削力增大,工件表面粗糙度 增加;进给量过小则可能影响加工效率。
案例四
总结词
根据工件材料、磨料和加工要求,选择合适的刀具几何参数和切削用量,以提高磨削效率和表面质量。
详细描述
在磨削加工中,刀具的几何参数如磨料粒度、结合剂硬度对磨削效率和表面质量有重要影响。磨料粒度越细,表 面粗糙度越低;结合剂硬度越高,磨粒越稳定。选择合适的切削用量,如磨削深度、磨削速度和进给速度,可以 优化磨削效率和表面质量。
谢谢聆听
进给量过小可能导致加 工效率低下,过大则可 能导致加工表面质量下 降。
切削深度的合理选择
01
切削深度影响切削力、切削热和 刀具寿命。
02
选择合适的切削深度可以降低切 削力,减少热量产生,提高刀具
钛合金零件切削用量与刀具参数的选择---中华工具网

钛合金零件切削用量与刀具参数的选择- 中华工具网钛合金零件切削用量与刀具参数的选择 主要加工方法钛合金零件的加工余量比较大,有的部位很薄(2~3mm),主要配合表面的尺寸精度、形位公差又较严,因此每项结构件都必须按粗加工→半精加工→精加工的顺序分阶段安排工序。
主要表面分阶段反复加工,减少表面残余应力,防止变形,最后达到设计图的要求。
其主要的加工方法有铣削、车削、磨削、钻削、铰削、攻丝等。
铣削用量及刀具的选择钛合金结构件中大量应用铣削加工,如零件内外型面。
刀具应选择具有高硬度、高抗弯强度和韧性、耐磨性好、热硬性好、工艺性好、散热性好的材料,主要为高速钢W6Mo5Cr4V2Al、W2Mo9Cr4VCo5(M42)和硬质合金YG8、K3O、Y330。
刀具几何参数应以保证刀具强度高、刚性好、锋利为原则,细长比不能过大,并分粗、精加工两种,加工时最好采用顺铣。
铣削刀具参数见表1,常规加工铣削用量见表2。
铣削时必须注入充足的水溶性油质切削液来降低刀具和工件的温度,切削液流量应不小于5L/min,以延长刀具的使用寿命。
在上述常规加工的基础上,为进一步提高铣削加工效率,我们在强力铣加工中心机床上进行了高效铣削试验,获得了较理想的切削用量、刀具和切削液,铣削用量数据见表3。
通过高效铣削与常规对比可以看出,高效铣削加工比常规加工效率提高了2~4倍,零件表面质量也得到较大的提高,加工周期大大缩短,制造成本相应降低。
车削用量及刀具的选择在刀具、切削用量、切削液选择合理的情况下,钛合金车削并不困难,与加工合金钢接近。
但车削钛合金表面氧化皮较为困难,一般在加工前用酸洗方法去掉表面薄层氧化皮,然后车削剩余的氧化皮,车削时切削深度应超过氧化皮深度1~5倍,走刀量可加大,但切削速度应降低。
刀具材料应选择YG类硬质合金材料。
刀具几何参数选择:前角g0=4°~8°,后角a0=12°~18°,主偏角Ø45°~75°,刃倾角l=0°,刀尖圆弧半径r=0.5~1.5mm。
表1-2 无心磨精精磨磨削用量(通磨钢制零件外圆)

无心磨精精磨磨削用量(通磨钢制零件外圆)表1-2 无心磨精精磨磨削用量(通磨钢制零件外圆)1.精磨行程次数N及纵向进给速度vf(mm/min)精度等级工件磨削表面直径dw(mm)5 10 15 20 30 40 60 80 100 N vf N vf N vf N vf N vf N vf N vf N vf N vfIT5级 3 1800 3 1600 3 1300 3 1100 4 1100 4 1050 5 1050 5 900 5 800 IT6级 3 2000 3 2000 3 1700 3 1500 4 1500 4 1300 5 1300 5 1100 5 1000 IT7级 2 2000 2 2000 3 2000 3 1750 3 1450 3 1200 4 1200 4 1100 4 1100 IT8级 2 2000 2 2000 2 1750 2 1500 3 1500 3 1500 3 1300 3 1200 3 1200纵向进给速度的修正系数工件材料壁厚和直径之比>0.15 0.12~0.15 0.10~0.11 0.08~0.09淬火钢 1 0.8 0.63 0.5 非淬火钢 1.25 1.0 0.8 0.63 铸铁 1.6 1.25 1.0 0.8导轮转速(r/s)2.与导轮转速及导轮倾斜角有关的纵向进给速度vf1°1°30’2°2°30’3°3°30’4°4°30’5°纵向进给速度vf(mm/min)0.3 300 430 575 720 865 1000 1130 1260 1410 0.38 380 550 730 935 1110 1270 1450 1610 1790 0.48 470 700 930 1165 1400 1600 1830 2030 2260 0.57 550 830 1100 1370 1640 1880 2180 2380 2640 0.65 630 950 1260 1570 1880 2150 2470 2730 3040 0.73 710 1060 1420 1760 2120 2430 2790 3080 3440 0.87 840 1250 1670 2130 2500 2860 3280 3630 4050纵向进给速度的修正系数导轮直径/mm200 250 300 350 400 500 修正系数0.67 0.83 1.0 1.17 1.33 1.67 注1.精磨用量不应大于粗磨用量(见表1-1)2.表内行程次数是按砂轮宽度B=150~200mm计算的。
「第一章 磨削加工的基本知识」
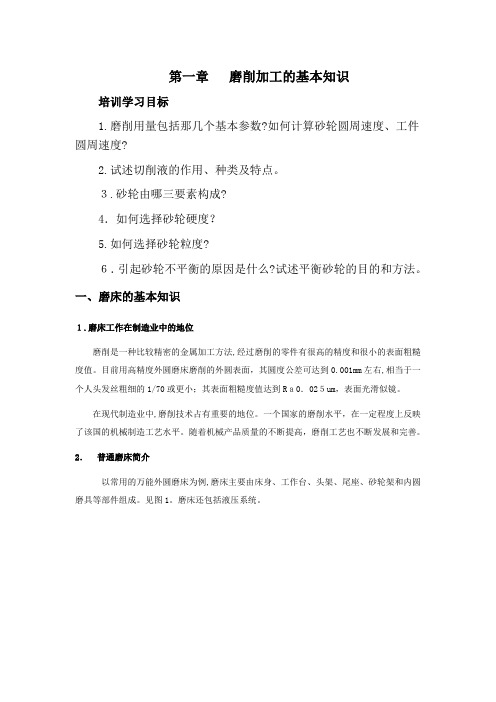
第一章磨削加工的基本知识培训学习目标1.磨削用量包括那几个基本参数?如何计算砂轮圆周速度、工件圆周速度?2.试述切削液的作用、种类及特点。
3.砂轮由哪三要素构成?4.如何选择砂轮硬度?5.如何选择砂轮粒度?6.引起砂轮不平衡的原因是什么?试述平衡砂轮的目的和方法。
一、磨床的基本知识1.磨床工作在制造业中的地位磨削是一种比较精密的金属加工方法,经过磨削的零件有很高的精度和很小的表面粗糙度值。
目前用高精度外圆磨床磨削的外圆表面,其圆度公差可达到0.001mm左右,相当于一个人头发丝粗细的1/70或更小;其表面粗糙度值达到Ra0.025um,表面光滑似镜。
在现代制造业中,磨削技术占有重要的地位。
一个国家的磨削水平,在一定程度上反映了该国的机械制造工艺水平。
随着机械产品质量的不断提高,磨削工艺也不断发展和完善。
2.普通磨床简介以常用的万能外圆磨床为例,磨床主要由床身、工作台、头架、尾座、砂轮架和内圆磨具等部件组成。
见图1。
磨床还包括液压系统。
(1)床身:磨床的支承。
(2)头架:安装与夹持工件,带动工件旋转,可在水平面内逆时针转90°;(3)内圆磨具:支承磨内孔的砂轮主轴。
(4)砂轮架:支承并传动砂轮主轴旋转,可在水平面±30°范围内转动;(5)尾坐:与头架一起支承工件;(6)滑鞍与横进给机构:通过进给机构带动滑鞍上的砂轮架实现横向进给;(7)横向进给手轮(8)工作台:a.上工作台:上面装有头架与尾坐;b.下工作台:上工作台可绕下工作台在水平面转±10°角度。
3.磨床的型号磨床的种类很多,按GB/T15375-1994磨床的类、组、系划分表,将我国的磨床品种分为三个分类。
一般磨床为第一类,用字母M表示,读作“磨”。
超精加工机床、抛光机床、砂带抛光机为第二类,用2M表示。
轴承套圈、滚球、叶片磨床为第三类,用3M表示。
齿轮磨床和螺纹磨床分别用Y和S表示,读作“牙”和“丝”。
机械制造与自动化专业《知识点1箱体零件概述及平面的加工讲义》

学习情境四箱体加工工艺方案制定与实施砂轮架箱体概述一、布置工作任务,明确要求二、观察砂轮架箱体样品,了解砂轮架箱体根本结构三、读图并分析零件图砂轮架箱体属于箱体类零件,它是磨床的根底件之一。
在磨床砂轮架中,由它将一些轴、套、轮、轴承等零件组装在一起,使其保持正确的相互位置关系,并且能按照一定的传动要求传递动力和运动,构成磨床的一个重要部件。
因此,砂轮架箱体的加工质量对磨床的精度、性能和寿命都有一定的影响。
1砂轮架箱体使用性能与设计要求各种砂轮架箱体的尺寸和结构形式虽有所不同,但其使用性能却根本一致,即保证砂轮主轴的高运动精度与位置精度,并能保持精度的高度稳定,抗振、吸振,高刚性、足够的强度,箱体受力、受热变形小,有足够的耐磨性,热处理变形小,机械加工性好等。
因此应在满足装配空间及操作空间要求的前提下,要求其结构尺寸小而紧凑、结构刚性高,主轴支承孔精度高并应严格同轴,中心孔轴线与定位端面应保持严格垂直,箱体的壁厚要足够且变化较小,材料的热处理性能应稳定等。
工模具磨床砂轮架箱体如图4-1所示。
2砂轮架箱体结构与技术要求〔1〕砂轮架箱体的结构分析从图4-1中可以看到,该磨床砂轮架箱体结构具有以下几个特点:1箱体的装配基准选择平导轨与V形导轨的组合方式,其定位准确,承载能力强,与磨床砂轮架的使用性能相适应;2箱体尺寸在满足装配关系与操作空间的要求下,尽量选取小值,因此整个箱体结构紧凑,体积较小;3箱体采用上开口封闭状结构形式,在壁厚较小的情况下,零件结构刚度较高;4箱体导轨长度有所加长,以利于箱体导向精度与承载强度;5箱体壁厚比拟均匀,有利于消除或减少零件的内应力对加工精度的影响;6砂轮架箱体上的主轴支承孔、箱体的装配基准——平导轨与V 形导轨面、轴向推力轴承的定位端面为箱体的重要外表;比拟重要的外表有其它组件与部件的安装基准面。
〔2〕砂轮架箱体的技术要求及其分析1砂轮主轴支承孔尺寸精度为IT7,属于一般精度等级;两主轴孔的相互位置精度-同轴度要求为0.03mm,为较高精度等级;主轴孔的形状精度包括在尺寸精度中,没有单独提出要求。
- 1、下载文档前请自行甄别文档内容的完整性,平台不提供额外的编辑、内容补充、找答案等附加服务。
- 2、"仅部分预览"的文档,不可在线预览部分如存在完整性等问题,可反馈申请退款(可完整预览的文档不适用该条件!)。
- 3、如文档侵犯您的权益,请联系客服反馈,我们会尽快为您处理(人工客服工作时间:9:00-18:30)。
磨削用量的选择
磨削用量包括砂轮速度vs、工件速度vw、纵向进给量fa、背吃刀量ap和光磨次数等。
磨削用量对磨削加工质量和生产率等有很大影响,其影响可见表1-1.
磨削用量生产率表面粗糙度烧伤磨削力砂轮磨耗磨削厚度几何精度vs ↗↗↘↗↘↘↘↗vw ↗↗↗↘↗↗↗↘fa ↗↗↗↘↗↗↗↘ap ↗↗↗↗↗↗↗↘
光磨次数↗↘↘↗↘↗↘↗
一、砂轮速度的选择
砂轮速度低,砂轮磨损严重,生产率低;砂轮速度过高,磨粒切削刃锋利程度易下降,也容易烧伤工件。
砂轮速度与表面粗糙度值得关系如图1-1所示。
该关系图形成条件是:工件材料45钢、调质250HBS、切入磨削、磨具PA80MV、速度比q=60、磨削液为%的69-1乳化液。
由图可知,随着砂轮速度提高,表面粗糙度值降低,但应注意防止磨削颤振。
一般外圆和平面磨削,使用陶瓷结合剂砂轮,砂轮速度在30~50m/s之间;内圆磨削及工具磨削一般砂轮速度在(18~30)m/s。
随着磨削技术的发展,砂轮速度已提高到60~80m/s,有的已超过100m/s。
图1-1 砂轮速度与表面粗糙度的关系
二、工件速度的选择
工件速度,对外圆或内孔磨削是指工件的线速度,平面磨削时指工作台运动速度。
工件速度vw与砂轮速度vs有关,但较其要小得多。
若二者速度比为q(q=vs/vw),则
外圆磨削 q=60~150
内圆磨削 q=40~80
普通磨削vw一般为10~30m/min,工件速度选择条件见表1-2.
序号主要因素选择条件
1速度比q 砂轮速度越高,工件速度越高;反之,前者越低,后者亦越低
2砂轮的形状和硬度直径砂轮直径越小,则工件速度越低
硬度
1、对于硬度高的砂轮,选择高的工件速度
2、硬度低的砂轮,工件速度宜低
3工件的性能和形状工件硬度1、工件硬度高时,选用高的工件速度
2、工件硬度低时,选用低的工件速度
三、纵向进给量的选择
纵向进给量的大小影响工件的表面质量和生产率。
纵向进给量大,增加磨粒的切削负荷,磨削力大;纵向进给量小,易使工件烧伤。
粗磨钢件 fa=(~)B mm/r
粗磨铸铁 fa=(~)B mm/r
精磨 fa=(~)B mm/r
四、背吃刀量的选择
磨削背吃刀量通常数值很小。
一般外圆纵磨
粗磨钢件 ap=~
粗磨铸铁 ap=~
精磨钢件 ap=~
精磨铸铁 ap=~
外圆切入磨普通磨削 ap=~
精密磨削 ap=~
内圆磨削背吃刀量更小一些。
磨削背吃刀量选择条件见表1-3.
五、光磨次数的选择
光磨即无进给磨削,光磨可消除在进给磨削时因弹性形变而未磨掉的部分加工余量,因此可提高工件的几何精度和降低表面粗糙度值。
由图1-2可见,表面粗糙度值随光磨次数的增加而降低。
但应注意:并不是光磨次数越多越好。
经过一定的光磨次数后,表面粗糙度值变化趋于稳定。
因此欲获得更高级别的表面粗糙度值仅靠增加光磨次数是不行的,而应采用其他加工方法。
光磨次数应根据砂轮状况、加工要求和磨削方式确定。
一般外圆磨削40#~60#砂轮,一般磨削用量,光磨次数是单行程2~4次。
内圆磨削40#~80#砂轮,一般磨削用量,光磨次数是单行程2~4次。
平面磨削30#~60#砂轮,一般磨削用量,光磨次数是单行程1~2次。
图1-2 光磨次数与表面粗糙度值的关系
a—普通WA60KV砂轮 b—WA+GCW14EB砂轮
六、磨削余量
磨削为精加工工序,余量一般较小。
不同的磨削加工,其加工余量的大小可参见表1-4至表1-7进行选择。
轴径热处理状态
长度
≤100>100~250>250~500>500~800>800~1200>1200~2000
≤10未淬硬
———淬硬
>10~18未淬硬
——淬硬
>18~30未淬硬
—淬硬
>30~50未淬硬淬硬
>50~80未淬硬淬硬
>80~120未淬硬淬硬
>120~180未淬硬淬硬
>180~260未淬硬淬硬
>260~360未淬硬淬硬
>360~500未淬硬
淬硬
表1-5 内圆磨削余量(单位:mm)。