缩松与缩孔相关知识
缩孔与缩松
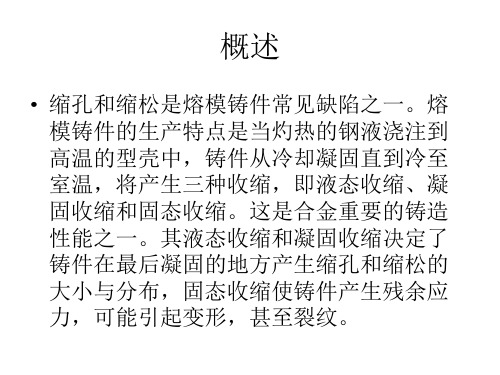
缩松形成过程
• 合金的凝固温度间隔比较宽,有时型壳的散热又比较慢,使凝固时合 金中两相区较宽,这就使铸件产生缩松,如上图 。a浇注后的某一时刻, 铸件截面上的三个区域分布。b随着温度的降低,铸件中的纯液相不存 在,成为固态和液态共存的凝固区域。枝晶间的通道变窄,阻碍较大, 合金的流动性变差,铸件中心的液态不易对较远的细小空洞进行补缩, 而且枝晶之间互相搭接,甚至形成与中心液态相隔绝的微小孔洞,根本 无法补缩。c合金凝固完毕,在铸件上就形成了很多分散而细小的缩松。
概述
• 缩孔和缩松是熔模铸件常见缺陷之一。熔 模铸件的生产特点是当灼热的钢液浇注到 高温的型壳中,铸件从冷却凝固直到冷至 室温,将产生三种收缩,即液态收缩、凝 固收缩和固态收缩。这是合金重要的铸造 性能之一。其液态收缩和凝固收缩决定了 铸件在最后凝固的地方产生缩孔和缩松的 大小与分布,固态收缩使铸件产生残余应ห้องสมุดไป่ตู้力,可能引起变形,甚至裂纹。
缩孔 的孔洞。
一 是什么?
• 定义:液态金属凝固过程中由于体积收缩所形成
• 特征:分布特征为集中缩孔,缩孔形状不规则,
表面粗糙,产生在铸件热节和最后凝固部位,常 伴有粗大树枝晶、夹杂物、气孔、裂纹、偏析等 缺陷。
• 鉴别方法:铸件内部的缩孔,一般采用超声探
伤或射线探伤法进行检验。敞露在铸件表面的缩 孔用肉眼即可确定。表面有缩陷、胀型、缩沉等 缺陷的铸件,内部往往有缩孔缺陷。
缩松
是什么
• 定义:缩松是指铸件最后凝固的区域没有得到液
态金属或合金的补缩形成分散和细小的缩孔。
• 特征:常分散在铸件壁厚的轴线区域、厚大部位、
冒口根部和内浇口附近。当缩松与缩孔容积相同 时,缩松的分布面积要比缩孔大得多。缩松隐藏 于铸件的内部,外观上不易被发现。
缩孔和缩松及其控制方法

缩孔和缩松及其控制方法缩孔和缩松是在材料加工和制造过程中常见的问题,对于产品的质量和性能有着重要影响。
本文将分别介绍缩孔和缩松的概念、原因以及控制方法。
一、缩孔缩孔指的是材料加工或制造过程中产生的孔洞或空隙,一般是由于材料内部气体无法完全排除或者材料收缩不均匀而引起的。
缩孔问题会导致产品的力学性能下降、密封性能降低以及外观质量不佳等问题。
造成缩孔的原因有多种,主要包括以下几个方面:1. 材料本身的问题:一些材料由于其特殊的化学成分或物理性质,容易产生气泡或者孔洞。
这些材料在加工或制造过程中容易出现缩孔问题。
2. 加工工艺的问题:加工过程中,如果温度、压力或者速度等参数控制不当,都有可能导致缩孔问题的发生。
例如,如果温度过高或者加热速度过快,就容易在材料内部产生气泡或者孔洞。
3. 设备的问题:加工设备的性能和状态也会影响材料的缩孔情况。
如果设备的密封性不好或者加工条件不能满足要求,就有可能导致缩孔问题。
针对缩孔问题的控制方法主要包括以下几个方面:1. 材料选择:选择合适的材料对于缩孔问题的控制非常重要。
一些具有较低缩孔倾向的材料可以有效地减少缩孔问题的发生。
2. 加工工艺优化:通过合理调整加工工艺参数,如温度、压力、速度等,可以减少缩孔问题的发生。
例如,采用适当的加热温度和加热时间可以降低材料内部气泡的产生。
3. 设备改进:改进加工设备的密封性能和控制能力,能够有效地减少缩孔问题。
定期检查和维护设备,确保其处于良好的工作状态也是很重要的。
二、缩松缩松是指在材料加工或制造过程中,由于材料的收缩不均匀而导致的形状尺寸偏差。
缩松问题会导致产品的尺寸不准确,甚至无法满足设计要求。
造成缩松的原因主要包括以下几个方面:1. 材料本身的问题:一些材料由于其特殊的物理性质,在加工或制造过程中容易出现收缩不均匀的情况,从而导致缩松问题的发生。
2. 加工工艺的问题:加工过程中,如果温度、压力或者速度等参数控制不当,都有可能导致材料收缩不均匀,出现缩松问题。
3.2.2 缩孔、缩松的形成及防止方法

缩孔、缩松的形成及防止方法副教授:陈云铸件中的缩孔与缩松液态金属在铸型内凝固过程中,由于液态收缩和凝固收缩导致体积缩小,若其收缩得不到补充,就在铸件最后凝固的部分形成孔洞。
大而集中的孔洞称为缩孔,细小而分散的孔洞称为缩松。
(a)铝合金缩孔、缩松(b)金相显微镜下缩松(c)扫描电镜下缩松一、缩孔的形成纯金属、共晶成分和凝固温度范围窄的合金,浇注后在型腔内是由表及里的逐层凝固。
在凝固过程中,如得不到合金液的补充,在铸件最后凝固的地方就会产生缩孔。
缩孔形成的条件:铸件呈逐层凝固方式凝固,成分为纯金属或共晶成分的合金。
缩孔产生的基本原因:是合金的液态收缩和凝固收缩值大于固态收缩值,且得不到补偿。
缩孔产生的部位在铸件最后凝固区域,如壁较厚大的上部或铸件两壁相交处,这些地方称为热节。
热节位置可用画内接圆的方法确定。
用画内切圆法确定缩孔位置二、缩松的形成铸件最后凝固的收缩未能得到补充,或者结晶温度范围宽的合金呈糊状凝固,凝固区域较宽,液、固两相共存,树枝晶发达,枝晶骨架将合金液分割开的小液体区难以得到补缩所致。
缩松形成的条件:铸件主要呈糊状凝固方式凝固,成分为非共晶成分或有较宽结晶温度范围的合金。
形成缩松的基本原因:是合金的液态收缩和凝固收缩值大于固态收缩值。
缩松一般出现在铸件壁的轴线区域、冒口根部、热节处,也常分布在集中缩孔的下方。
三、影响缩孔和缩松形成的因素1、合金成分结晶温度范围越小的合金,产生缩孔的倾向越大;结晶温度范围越大的合金,产生缩松的倾向越大。
铁碳合金成分和体积收缩的关系V总—总体积收缩容积;V孔—缩孔容积;V松—缩松容积2、浇注条件提高浇注温度时,合金的总体积收缩和缩孔倾向增大。
浇注速度很慢或向冒口中不断补浇高温合金液,使铸件液态和凝固收缩及时得到补偿,铸件总体积收缩减小,缩孔容积也减小。
V 总—总体积收缩容积;V 孔—缩孔容积;V 松—缩松容积铁碳合金成分和体积收缩的关系3、铸型材料铸型材料对铸件冷却速度影响很大 。
防止缩松缩孔

第四节防止缩孔缩松的途径一、缩孔和缩松的相互转化对于一定成分的合金,浇注温度一定时合金的收缩体积满足以下关系:总收缩体积=液态收缩体积+凝固收缩体积=缩孔体积+缩松体积=常数。
但是,缩孔和缩松体积可以相互转化,造成转化的根本原因是凝固方式的改变:即体积凝固还是逐层凝固。
表8-2给出了影响缩孔和缩松体积相互转化的因素。
表8-2 缩孔、缩松互相转换的影响因素二、防止缩孔和缩松的途径防止铸件中产生缩孔和缩松的基本原则是针对该合金的收缩和凝固特点制定正确的铸造工艺,使铸件在凝固过程中建立良好的补缩条件,尽可能地使缩松转化为缩孔,并使缩孔出现在铸件最后凝固的地方。
这样,在铸件最后凝固的地方安臵一定尺寸的冒口,使缩孔集中于冒口中,或者把浇口开在最后凝固的地方直接补缩,即可获得健全的铸件。
使铸件在凝固过程中建立良好的补缩条件,主要是通过控制铸件的凝固方向使之符合“顺序凝固原则”或“同时凝固原则”。
1、顺序凝固(progressive solidification)铸件的顺序凝固原则,是采用各种措施保证铸件结构上各部分,按照远离冒口的部分最先凝固,然后是靠近冒口部分,最后才是冒口本身凝固的次序进行,亦即在铸件上远离冒口或浇口的部分到冒口或浇口之间建立一个递增的温度梯度,如图8-8所示。
铸件按照顺序凝固原则进行凝固,能保证缩孔集中在冒口中,获得致密的铸件。
逐层凝固是指铸件某一断面上,先在铸件表面形成硬壳,然后它逐渐向铸件中心长厚,铸件中心最后凝固。
因此,顺序凝固和逐层凝固是两个不同的概念。
铸件的结构,以及由铸造条件所形成的温度场,是决定铸件凝固方向的主要因素,可用下例说明。
图8-9a是带冒口的板状铸件,厚度为δ,金属液从冒口浇入,即上注式。
右图是铸件纵截面上中心线的温度曲线及随时间变化情况。
因为金属液是从冒口浇入的,所以中心线上A、B、C三点的温度依次向冒口方向递增,t液—t固是合金的凝固温度范围。
图8-9b表示该铸件A、B、C三点的横截面上径向温度分布及随时间变化情况。
缩孔与缩松

缩孔与缩松杨群收汇编铸件在凝固过程中,由于合金的液态收缩和凝固收缩,往往在铸件最后凝固的部位出现孔,称为缩孔。
容积大而集中的孔称为集中缩孔,或简称缩孔;细小而分散的孔称为分散性缩孔,简称缩松,缩松的形状不规则、表面不光滑,可以看到发达的树枝晶末梢,有时呈氧化现象发青,可以和气孔区别开来。
在铸件中存在任何形态的缩孔都会由它们而减少受力的有效面积,以及在缩孔处产生应力集中现象,而使铸件的机械性能显著降低。
因此,缩孔是铸件的重要缺陷之一,必须设法防止。
一、产生缩孔缩松的因素缩孔形成的因素和过程是很复杂的,各种合金产生缩孔的过程及缩孔量的大小也各不相同,必须说明铸件的缩孔体积和合金的总的收缩(即液态收缩,凝固收缩和固态收缩之和)并不是同等的概念,但是这三个阶段的收缩对缩孔却能产生影响。
要研究如何解决缩孔问题,必须了解两个问题,一、合金的凝固特性和凝固收缩过程。
以铸铁为例,其凝固特性逐层凝固,其总的收缩过程即液态收缩、凝固态收缩(与石墨膨胀共存)和固态收缩。
二、决定铸铁收缩的影响因素主要是三个方面;即浇注温度,石墨析出量(化学成分及冷却方法)和铸型刚度(型壁移动)。
对以上专业词语,结合图形作简单通俗说明,从理论概念上知道一些。
液态收缩:从浇注温度到开始结晶。
(冒口起补缩作用)凝固态收缩:从开始结晶到完全成固态,在这个阶段里存在液态,枝晶状亚固态,石墨生成。
(工艺措施及压力起补偿作用)以上两个阶段是合金的体收缩阶段,在这两个阶段里要防止铸件的缩孔,主要靠冒口,冒口高度,浇注方法及工艺上的措施。
固态收缩:从完全凝固成固态,到室温阶段的收缩,在这个阶段的收缩是线收缩(靠制作模型时放的缩尺,来弥补线收缩时铸件几何尺寸的减少)。
固态收缩对铸件的缩孔一般影响不大,但是在降温线收缩过程中,往四周拉扯的应力也可使缩孔增大些。
铸铁的缩孔量也可以下式表示:缩孔量(%)=液态收缩+凝固态收缩+固态收缩-石墨膨胀对于缩孔的形成,金属的液态收缩和凝固态收缩远大于固态收缩。
铸件缩孔、缩松有何区别?如何解决?

铸件缩孔、缩松有何区别?如何解决?在铸造生产中,铸件气孔和铸件缩孔有时是伴生的,有时是独立存在。
当出现气孔和缩孔时,我们要快速的判断出缺陷是气孔还是缩孔对于解决问题十分必要。
气孔类缺陷与防治方法在铸造生产中,孔洞类缺陷是常见缺陷,也是给铸造厂造成损失比较大的缺陷之一。
孔洞类缺陷分为气孔和缩孔。
气孔多为由于金属液中侵入、裹入、卷入气体所至。
铸件气孔出现在铸件上的位置不同,其产生的原因也不同。
这就要求我们的铸造技术员在判断气孔缺陷病因时,要掌握各类气孔发生的原理,具有什么样的特征。
只有如此才能对症下药,将出现的气孔缺陷解决掉。
气孔特征:(1)卷入气孔:金属液在充型过程中因卷入气体而在铸件内形成气孔,多呈孤立存在的圆形或椭圆形大气孔,位置不固定,一般偏铸件中上部。
(2)侵入气孔:由型、芯、涂料、芯撑、冷铁产生的气孔侵入铸件表层而形成气孔,多呈梨形或椭圆形,尺寸较大,孔壁光滑,表面多呈氧化色。
(3)反应气孔:由金属液内部某些成分之间或金属液与型、芯在界面上发生化学反应而形成群分布的气孔。
位于铸件表层的针头形或腰圆形反应气孔称为表面针孔与皮下气孔,由金属液与型、芯涂料发生界面反应所至;分散或成群分布在铸件整个断面上或某个局部区域的针头反应气孔。
形成原因:(1)由于炉料潮湿、锈蚀、油污、气候的潮湿,熔练工具和浇包未烘干,金属液成分不当,合金液为精炼与精炼不足,使金属液中含有大量气体或气体物质,导致在铸件中析出气孔或反应气孔。
(2)型、芯未充分烘干,透气性差,通气不良,含水分和发气物质过多,涂料未烘干或含发气成分过多,冷铁、芯撑有锈斑、油污或未烘干,金属型排气不良,在铸件中形成侵入气孔。
(3)浇注系统不合理,浇注和充型速度过快,金属型排气不良,使金属液在浇注和充型过程中产生紊流、涡流或断流而卷入气体,在铸件中形成卷入性气孔。
(4)合金液易可吸气,在熔炼和浇注过程中未采取有效的精炼、保护和净化措施,使金属液中含有大量气体、夹渣和夹气成分,在充型和凝固过程中形成析出气孔和反应气孔。
焊接缩孔与缩松的机理及因素及防止措施
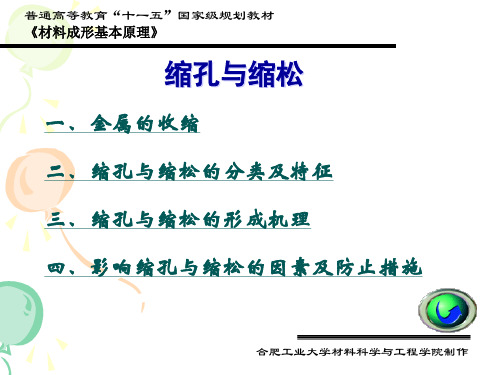
合肥工业大学材料科学与工程学院制作
普通高等教育“十一五”国家级规划教材 《材料成形基本原理》
温度 /℃ 温度 温度 m = ( 100 % n ( T ) L S ) V( LS) 0 L S V 液 V 液 浇 V 凝 S 固 V ( L V 固 /℃ /℃
合肥工业大学材料科学与工程学院制作
普通高等教育“十一五”国家级规划教材 《材料成形基本原理》
a)明缩孔
b)凹角缩孔
c)芯面缩孔
d)内部缩孔
合肥工业大学材料科学与工程学院制作
普通高等教育“十一五”国家级规划教材 《材料成形基本原理》
缩 孔 特 点
常出现于纯金属、共晶成分合金和结晶温度范围 较窄的以层状凝固方式凝固的铸造合金中; 多集中在铸件的上部和最后凝固的部位;铸件厚 壁处、两壁相交处及内浇口附近等凝固较晚或凝 固缓慢的部位(称为热节),也常出现缩孔; 缩孔尺寸较大,形状不规则,表面不光滑。
金属从浇注温度冷却到室温所产生的体收缩为液
态收缩、凝固收缩和固态收缩之和,即:
εV总=εV液+εV凝+εV固
其中,液态收缩和凝固收缩是铸件产生缩孔
和缩松的基本原因 。而固相收缩对应力、变形
与裂纹影响较大。
合肥工业大学材料科学与工程学院制作
普通高等教育“十一五”国家级规划教材 《材料成形基本原理》
二、缩孔与缩松的分类及特征 缩孔 缩松
普通高等教育“十一五”国家级规划教材 《材料成形基本原理》
(一)影响缩孔与缩松的因素
金属的性质 铸型的冷却能力 (收缩系数α大) (蓄热系数b小)
浇注温度与浇注速度 (高,快) 铸件尺寸 补缩能力 (大) (弱)
例:铸铁的缩孔、缩松倾向
【材料成型原理--铸造】第14章 缩孔与缩松

4/28
收缩三个阶段
铸造合金从浇注温度冷却到常温,一般要经历以下三个收缩阶段:
• 1.液态收缩:合金从浇注温度冷却到液相线温度发生的体收缩。
• 2.凝固收缩:金属从液相线温度到固相线温度间产生的体收缩。
对于纯金属和共晶合金,凝固期间的体收缩是由于状态的改变, 与温度无关,具有一定的数值。
6/28
铸铁的收缩 1液态收缩 2凝固收缩:白口铁参考铸钢(两部分)
灰口铁有石墨膨胀 3固态收缩:
珠光体转变前收缩 共析转变膨胀(铁素体膨胀+渗碳体收缩、石墨 膨胀) 珠光体转变后收缩
7/28
第二节 缩孔与缩松的形成机理
1、缩孔:铸造合金在凝固过程中,由于液态收缩和凝固 收缩的产生,往往在铸件最后凝固的部位出现孔洞,称 为缩孔,把尺寸较大而且集中的孔洞称为集中缩孔,简 称缩孔。
• 2、条件: 铸件由表及里逐层凝固。
11/28
二、缩松的形成
当某种成分下的合金结晶温度范围较宽时, 通常按体积凝固的方式凝固。凝固区域宽,晶 体容易发展成为树枝发达的粗大等轴晶,当固 相约占70%(体积分数)时,尚未凝固的液体被 分割为一个个互不相通的小熔池。
随温度降低,同样要发生液态收缩、凝 固收缩和固态收缩,由于合金的液态收缩和凝 固收缩大于固态收缩,出现的细小孔洞得不到 外部合金液的补充而形成分散性的细小缩孔, 即缩松。
20/28
21/28
• 由于按照体积凝固方式凝固,铸件表面在 凝固后期没有形成坚固的外壳,如果铸型刚度 不够,膨胀力将迫使型壁外移。尺寸精度变差。 • 随着石墨球的长大,共晶团之间的间隙逐 步扩大,使得铸件普遍膨胀。共晶团之间的间 隙就是球墨铸铁的显微缩松,并布满铸件整个 断面,所以球墨铸铁铸件产生缩松的倾向性很 大。 • 如果铸件厚大,球墨铸铁铸件这种较大的 缩前膨胀也会导致铸件产生缩孔。 • 如果铸型刚度足够大,石墨化的膨胀力能 够将缩松挤合。在这种情况下,球墨铸铁也可 看作是具有“自补缩”能力。
二、铸件中的缩孔和缩松讲解

1、缩孔与缩松的形成 (1)缩孔(又称集中缩孔)
• 形成 • 形状:倒锥形 • 形成部位最后凝固处 • 易形成缩孔的合金:纯金属,共晶成分
的合金→逐层凝固
图2-4 缩孔形成过程
Fig.2-4 The formation of Shrinkage Void
The formation of Thermal Stress
Internal Stress,Deformation and
Crack of Casting
• 结论:铸件中厚的部分最后冷却,总是 受拉应力,反之,薄的部分受压应力。
• 热应力的预防:采用同时凝固的方法 (不管壁厚如何,同时一起收缩,可避 免热应力的产生)。
Internal Stress,Deformation and Crack of Casting
铸造内应力:铸件冷却时因固态收缩受 阻碍,在铸件内部产生的应力。
一、内应力的形成
类型— 热应力、机械应力 1、热应力
• 热应力的形成 • 形成原因—铸件的壁厚不均匀,冷却和
收缩先后不一致造成内应力。
图2-8 热应力的形成
• 适用的合金:普通灰口铸铁(缩孔缩松 倾向小),锡青铜
2、机械应力
二、铸件的变形与预防
Deformation of the Cast and Its Prevention
具有内应力的铸件处在一种不稳定的状 态— 它会通过适当的变形来减缓自身的 内应力,趋于一种稳定状态。
例1 T型型材的变形 例2 机架的变形 例3 机床床身
顺序凝固法的总体思路:合金的收缩不 可避免,可使缩孔形成在铸件外部的冒 口内(该处为最后凝固处)。
铸件缩孔和缩松缺陷十点分析

铸件缩孔和缩松缺陷十点分析缩孔和缩松都是铸造生产中常见的铸件缺陷。
缩孔是铸件在冷凝过程中收缩,得不到金属溶液的补充而产生的孔洞,形状不规则,孔壁粗糙,一般位于铸件的热节处。
缩孔和气孔在外表上往往极为相似,经常容易混淆。
一般来说,气孔的内壁是平滑的,而缩孔的内壁则呈枝状结晶的末梢状。
缩松是铸件最后凝固的区域没有得到金属溶液的补缩而形成分散和细小的小孔,常出现在铸件的较厚截面以及厚薄截面交接处或热节点上。
缩松的分布面积要比缩孔大得多,往往隐藏于铸件的内部,有时肉眼察觉不到。
缩孔和缩松在铸件废品中占有较大的比例,必须引起足够的重视,以提高铸件合格率。
笔者结合多年的生产实践经验,谈谈铸件缩孔和缩松的产生原因及其防止措施。
1.铸件和模样设计(1)铸件截面尺寸变化过大。
如果在设计中铸件截面尺寸变化过大,薄截面的冷却速度比相邻厚截面的冷凝速度要快得多,这样就很难实现铸件的顺序凝固,同时也难于进行补缩。
设计时要尽量避免这种情况,否则应采用冷铁,以实现铸件的顺序凝固并利于补缩。
(2)铸件断面过厚,如果没有采取相应措施对其进行补缩,会因补缩不良形成缩孔。
(3)圆角太小。
铸件的凹角圆角半径太小,会导致型砂传热能力降低,凝固速度下降,同时由于该处型砂受热作用强,发气压力大,析出的气体可向未凝固的金属液渗入,导致铸件产生气缩孔。
(4)圆角太大。
圆角太大,则圆角部分就成了厚截面,如果相邻的截面较薄,就难以得到有效的补缩,造成补缩不良2.模样(1)模样或芯盒磨损致使铸件截面减薄,导致铸件截面厚度减薄而妨碍补缩。
(2)模样尺寸不当或模样结构不当,导致铸件截面过厚或过薄。
设计时应注意控制模样的厚度,尽量使邻近较厚截面的薄截面保持最大的厚度。
3.砂箱(1)上箱太浅。
生产中为了节省型砂用量或为了降低砂箱和造型成本而使用高度不够的上箱,这是造成缩松缺陷的常见原因。
上箱太浅,会降低金属液的静压力,以致难以进行补缩,补缩压力不够,会导致产生缩松或缩孔,或二者兼有之。
金属凝固理论 第12章 缩孔与缩松

4/51
二、收缩的三个阶段
1.液态收缩:铸造合金从浇注温度冷却到液相 线温度发生的体收缩称为液态收缩。
2.凝固收缩:金属从液相线温度到固相线温度 间产生的体收缩称为凝固收缩。
3.固态收缩:金属在固相线以下发生的体收缩 称为固态收缩。
2020/10/15
5/51
液态收缩和凝固收缩越严重,缩孔越大; 固态收缩越大,缩孔越小。
2020/10/15
10/51
五、铸铁的收缩
1、液态收缩
铸铁的液态体收缩系数v液随碳含 量的提高而增大。
根据状态图,随铸铁的碳含量增加, 其液相线温度下降,温差也增大。
所以,当浇注温度一定时, v液随 碳量的增加而增大。
2、凝固收缩
亚共晶白口铸铁的凝固收缩和碳钢 相似,是状态改变和温度降低共同 作用的结果。
3)机械阻力 当铸件由于本身结构具有突出部分或内腔部分有型芯, 在收缩时会受到铸型和型芯的阻力,而不能自由收缩, 这种阻力称为机械阻力。与造型材料的强度和退让性、 铸型和型芯的紧实度、箱档和芯骨的位置、及铸件本 身的厚度和长度有关。
2020/10/15
第十二章 缩孔与缩松
材料成型与控制专业
2020/10/15
1/51
主要内容
第一节 收缩 第二节 缩孔与缩松的形成机理 第三节 影响缩孔与缩松的因素及防止措施
2020/10/15
2/51
第一节 收缩
一、收缩的基本概念 1、金属收缩现象 金属从液态转变为固态发生的收缩: ① 液态金属冷却,随着温度下降,空穴数量减
碳钢的凝固收缩率如下表所示。
Wc%
v凝%
0.10 0.25 0.35 0.45 0.70 2.0 2.5 3.0 4.3 5.3
哪些因素影响缩孔、缩松形成,如何采取措施进行防止,举例说明合金成分对形成缩孔和缩松的影响。
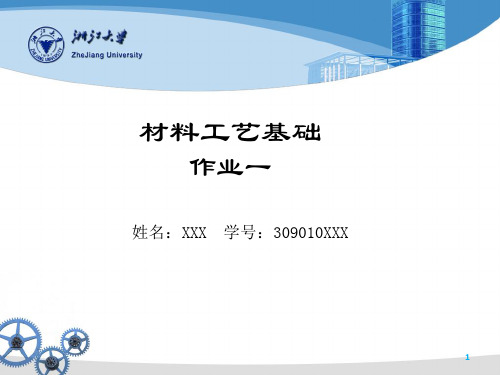
➢铸件内应力的预防措施
✓铸件产生铸造内应力的主要原因是合金的固态收缩。 ✓为了减小铸造内应力,在铸造工艺上可采取同时凝 固原则。所谓同时凝固原则,就是采取工艺措施保证 铸件结构上各部分之间没有温差或温差尽量小,使各 部分同时凝固。 ✓此外,还可以采取去应力退火或自然时效等方法, 将残余应力消除。
6
➢合金成分对形成缩孔和缩松的影响
举例:微量B和C对TiAl合金铸锭缩孔缩松的影响 对铸锭进行成分分析并利用体视显微镜和扫描电子显微
镜对铸锭的铸造收缩缺陷和组织进行分析。结果表明: Ti-47Al-2Cr-2Nb合金铸锭有很强的柱状晶生长趋势,在
轴线附近区域形成分散的缩松;加入0.8% B 后,铸锭的组织 得到细化,并削弱了柱状晶生长趋势,收缩缺陷分布集中以大 缩孔方式存在,显微缩松的密度和尺寸均降低。
4
➢缩孔、缩松形成的影响因素及防止措施
一. 形成原因
2. 工艺设计的原因 ✓浇注系统设计不合理: 浇注系统设计与铸件的凝固原则相矛盾时,可能 会导致铸件产生缩孔或缩松。主要表现为浇注位置不合适,不利于顺序凝 固,内浇口的位置及尺寸不正确。 ✓冒口设计不合理:冒口位置、数量、尺寸及冒口颈尺寸未能促进铸件顺 序凝固,都可能导致铸件产生缩孔和缩松。如果在暗冒口顶部未放置出气 冒口,或冷铁使用不当,也会导致铸件产生缩孔和缩松。 ✓浇注方面的原因: 浇注速度越快,缩孔体积越大。浇注温度太高,使液 态金属的液态收缩量增加;太低时,又会降低冒口的补缩能力,特别是采 用底注式浇注系统时更明显,铸件往往在下部产生缩孔和缩松。当冒口没 有浇满或对大中型铸件没有用金属液对明冒口进行补浇时,这将降低冒口 的补缩能力,引起铸件产生缩孔或缩松。
材料工艺基础
作业一
姓名:XXX 学号:309010XXX
材料成形基本原理第三节 缩孔与缩松

缩孔的形成机理
纯金属、共晶成分合金和结晶温度范围窄 的合金,在一般铸造条件下按由表及里逐层凝固
的方式凝固。由于金属或合金在冷却过程中发生的
液态收缩和凝固收缩大于固态收缩,从而在铸
件最后凝固部位形成尺寸较大的集中缩孔。
铸件中缩孔形成过程示意图
缩松的形成机理
结晶温度范围较宽的合金,一般按照体积凝固的方式凝固, 凝固区内的小晶体很容易发展成为发达的树枝晶。当固相达到一 定数量形成晶体骨架时,尚未凝固的液态金属便被分割成一个个 互不相通的小熔池。在随后的冷却过程中,小熔池内的液体将发 生液态收缩和凝固收缩,已凝固的金属则发生固态收缩。由于熔 池金属的液态收缩和凝固收缩之和大于其固态收缩,两者之差引 起的细小孔洞又得不到外部液体的补充,便在相应部位形成了分 散性的细小缩孔,即缩松。
4.0
23..13 -41..65
灰白铸口铁铸的铁缩的前收膨缩胀率具高有,自产补生缩作 用裂,纹缩、孔缩与孔缩、松缩的松倾的向倾较向小大。。
灰铸铁和球墨铸铁共晶石墨长大示意图
C C
C C
缩松的特点
缩松多出现于结晶温度范围较宽的合金中; 显微缩松一般出现在枝晶间和分枝之间; 常分布在缩孔附近或铸件厚壁的中心部位;
体?积凝凝固固 层?状凝凝固固
A
B
m
n
体树缩积枝松凝晶固 TL
G TS
层胞缩状孔凝晶固
TL TS G
铸件热节处的缩孔与缩松
三、缩孔与缩松的形成机理
缩孔的形成 缩松的形成
表表1111--42 亚亚共共晶晶铸铸铁铁的的凝液固态体收收缩缩率率εεVV液凝
碳碳的的质质量量分分数数 wC/wC%/ %2.0 2.02.5 2.53.03.0 3.35.5 ε凝V固液(收T缩浇-率TL=白1口00铸℃铁)/%5.1 1.54.6 1.74.21.8 3.27.0 ε εV液V(凝 T/浇%=140灰0℃铸)铁/% 4.3 0.62.8 1.41.42.3 -03..14
缩孔和缩松及其控制方法

缩孔和缩松及其控制方法缩孔和缩松是材料加工中常见的问题,会对产品的质量和性能产生不利影响。
本文将首先介绍缩孔和缩松的概念和原因,然后探讨相关的控制方法。
一、缩孔和缩松的概念和原因缩孔是指材料中存在的孔洞或空隙,在加工过程中由于内部应力的作用而发生收缩,导致孔洞的尺寸变小。
缩松是指材料中的实体部分在加工过程中由于受到挤压或拉伸而发生收缩,导致尺寸变小。
缩孔和缩松的产生原因有多种,主要包括材料的物理性质、加工工艺和设备的影响。
材料的物理性质包括材料的组织结构、成分和热膨胀系数等,这些因素会影响材料在加工过程中的变形和收缩特性。
加工工艺中的温度、压力和速度等参数的选择也会影响缩孔和缩松的产生。
设备的精度和稳定性也会对缩孔和缩松产生影响。
二、缩孔和缩松的控制方法为了减少或避免缩孔和缩松的产生,可以采取以下控制方法:1. 材料选择:选择具有较低膨胀系数和较好变形性能的材料,可以减少缩孔和缩松的产生。
此外,还可以选择具有合适组织结构和成分的材料,以提高材料的可加工性。
2. 加工工艺优化:在加工过程中,要合理选择温度、压力和速度等参数,以减少缩孔和缩松的产生。
同时,还需要注意加工工艺中的各个环节,如预处理、加热、冷却和保温等,以确保材料的均匀性和稳定性。
3. 设备维护和调整:保持加工设备的精度和稳定性,及时对设备进行维护和调整,可以减少因设备问题而引起的缩孔和缩松。
此外,还可以通过调整设备的参数,如温度、压力和速度等,来控制缩孔和缩松的产生。
4. 模具设计和加工:合理设计和加工模具,可以减少缩孔和缩松的产生。
模具的结构和形状应与产品的要求相匹配,以确保材料在加工过程中的均匀性和稳定性。
同时,还要注意模具的材料选择和表面处理,以提高模具的耐磨性和抗粘性。
5. 检测和控制:在加工过程中,要建立合适的检测和控制方法,及时发现和解决缩孔和缩松的问题。
可以使用非破坏性检测方法,如超声波检测和X射线检测,来检测材料中的缺陷和孔洞。
知识篇——铸件中缩孔与缩松的防止方法
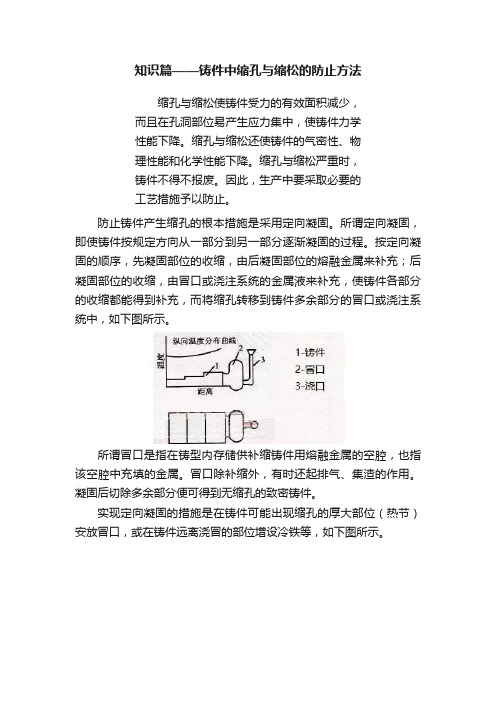
知识篇——铸件中缩孔与缩松的防止方法缩孔与缩松使铸件受力的有效面积减少,而且在孔洞部位易产生应力集中,使铸件力学性能下降。
缩孔与缩松还使铸件的气密性、物理性能和化学性能下降。
缩孔与缩松严重时,铸件不得不报废。
因此,生产中要采取必要的工艺措施予以防止。
防止铸件产生缩孔的根本措施是采用定向凝固。
所谓定向凝固,即使铸件按规定方向从一部分到另一部分逐渐凝固的过程。
按定向凝固的顺序,先凝固部位的收缩,由后凝固部位的熔融金属来补充;后凝固部位的收缩,由冒口或浇注系统的金属液来补充,使铸件各部分的收缩都能得到补充,而将缩孔转移到铸件多余部分的冒口或浇注系统中,如下图所示。
所谓冒口是指在铸型内存储供补缩铸件用熔融金属的空腔,也指该空腔中充填的金属。
冒口除补缩外,有时还起排气、集渣的作用。
凝固后切除多余部分便可得到无缩孔的致密铸件。
实现定向凝固的措施是在铸件可能出现缩孔的厚大部位(热节)安放冒口,或在铸件远离浇冒的部位增设冷铁等,如下图所示。
所谓冷铁是指为增加铸件局部的冷却速度,在砂型、砂芯表面或型腔中安放的金属物。
图中所示铸件中可能产生缩孔的厚大部分不止一个,若仅靠顶部冒口,难以向底部凸台补缩,如果在该凸台的型壁上安放两个外冷铁,加快了该处的冷却速度,使厚壁凸台反而最先凝固,从而实现了由下而上的定向凝固。
定向凝固与逐层凝固是两个不同的概念。
定向凝固是指铸件各部分的凝固顺序;逐层凝固是指铸件某截面上的凝固顺序。
逐层凝固的合金表层先凝固,然后逐渐向铸件中心增厚,铸件中心最后凝固。
冒口的补缩通道能长时间保持畅通,有利于实现铸件的定向凝固。
对于纯金属、共晶成分的合金,工艺上一般都采用定向凝固的原则,来提高铸件的致密性。
相反,倾向于糊状凝固的合金,结晶的固体骨架较好地布满整个铸件的截面,使冒口的补缩通道堵塞,难以实现定向凝固。
3.2.2 缩孔、缩松的形成及防止方法

缩孔、缩松的形成及防止方法副教授:陈云铸件中的缩孔与缩松液态金属在铸型内凝固过程中,由于液态收缩和凝固收缩导致体积缩小,若其收缩得不到补充,就在铸件最后凝固的部分形成孔洞。
大而集中的孔洞称为缩孔,细小而分散的孔洞称为缩松。
(a)铝合金缩孔、缩松(b)金相显微镜下缩松(c)扫描电镜下缩松一、缩孔的形成纯金属、共晶成分和凝固温度范围窄的合金,浇注后在型腔内是由表及里的逐层凝固。
在凝固过程中,如得不到合金液的补充,在铸件最后凝固的地方就会产生缩孔。
缩孔形成的条件:铸件呈逐层凝固方式凝固,成分为纯金属或共晶成分的合金。
缩孔产生的基本原因:是合金的液态收缩和凝固收缩值大于固态收缩值,且得不到补偿。
缩孔产生的部位在铸件最后凝固区域,如壁较厚大的上部或铸件两壁相交处,这些地方称为热节。
热节位置可用画内接圆的方法确定。
用画内切圆法确定缩孔位置二、缩松的形成铸件最后凝固的收缩未能得到补充,或者结晶温度范围宽的合金呈糊状凝固,凝固区域较宽,液、固两相共存,树枝晶发达,枝晶骨架将合金液分割开的小液体区难以得到补缩所致。
缩松形成的条件:铸件主要呈糊状凝固方式凝固,成分为非共晶成分或有较宽结晶温度范围的合金。
形成缩松的基本原因:是合金的液态收缩和凝固收缩值大于固态收缩值。
缩松一般出现在铸件壁的轴线区域、冒口根部、热节处,也常分布在集中缩孔的下方。
三、影响缩孔和缩松形成的因素1、合金成分结晶温度范围越小的合金,产生缩孔的倾向越大;结晶温度范围越大的合金,产生缩松的倾向越大。
铁碳合金成分和体积收缩的关系V总—总体积收缩容积;V孔—缩孔容积;V松—缩松容积2、浇注条件提高浇注温度时,合金的总体积收缩和缩孔倾向增大。
浇注速度很慢或向冒口中不断补浇高温合金液,使铸件液态和凝固收缩及时得到补偿,铸件总体积收缩减小,缩孔容积也减小。
V 总—总体积收缩容积;V 孔—缩孔容积;V 松—缩松容积铁碳合金成分和体积收缩的关系3、铸型材料铸型材料对铸件冷却速度影响很大 。
铸件缩孔与缩松

§2铸件的缩孔和缩松铸件凝结时因液态缩短和凝结缩短使铸件最后凝结部位出现孔洞,容积大而集中的称集中缩孔(缩孔),小而分别的称分别缩孔(缩松)。
一形成机理1缩孔合金性质不一样,缩孔形成的机理各异。
1)凝结过程中无体积膨胀合金如铸钢、白口铸铁、铝合金等。
浇铸后,型壁传热、逐层凝结、液态缩短和凝结缩短大于固态缩短。
如无赔偿,则在最后凝结部位出现缩孔。
2)有体积膨胀的合金(灰铁、球铁)自补缩能力:灰铁共晶凝结过程中,片状石墨尖端在共晶液中优先长大,其产生的体积膨胀绝大多半直接作用在初生奥氏体枝晶或共晶团的液体上,并推进液体经过枝晶间的通道去补缩因为液态和固态缩短所形成的小孔洞。
文档来自于网络搜寻缩前膨胀:石墨长大所产生的膨胀压力经过奥氏体或共晶团最后作用在铸型表面,使型腔扩大的现象。
灰铁的共晶凝结偏向于中间凝结方式,凝结中期已有完整凝结的外壳,能蒙受必定的石墨化膨胀压力,因此其缩前膨胀可忽视不计。
故其产生缩孔的偏向小。
只有当液态缩短和凝结缩短之和大于石墨化膨胀和固态缩短之和才会产生缩孔。
文档来自于网络搜寻球铁共晶凝结呈糊状凝结方式,凝结时期无牢固外壳。
如铸型刚度不够,则使型腔扩大,故球铁缩前膨胀比灰铁大好多。
当球铁液态缩短、凝结缩短和型腔扩大之和大于石墨化膨胀和固态缩短之和时,铸件将产生缩孔。
文档来自于网络搜寻总结:灰铸铁:石墨化膨胀产生的膨胀压力绝大多半直接作用在液体上(共晶团或A枝晶之间的),小部分作用在铸型型壁上。
球铁:石墨化膨胀产生的膨胀压力一小部分直接作用在液体上(共晶团1/3或A枝晶之间的),绝大多半作用在铸型型壁上。
缩松铸件凝结后期,最后凝结的节余金属液,因为温度梯度小,会按同时凝结原则凝结,即金属液中形成很多渺小的晶粒。
当晶粒长大相互连结后,将节余金属液切割成互不相通的小熔池。
这些小熔池在随后的凝结过程中得不到金属液的增补,就形成缩松。
文档来自于网络搜寻缩松按其散布状态分三种:弥散缩松、轴线缩松、局部缩松。
第14章 缩孔与缩松

§14-3
影响缩孔与缩松的因素及防止措施
产生缩孔、缩松因素与控制: 收缩必然性→缩孔或缩松→取决于凝固方式(层、糊) 影响凝固方式因素: 成分、温度梯度 影响缩孔和缩松大小的因素:金属的性质;铸型条件(激冷能力) 浇注条件;铸件尺寸 缩孔防止:合理设计浇冒口系统 → 缩孔于浇冒口中。 缩松防止:无法通过浇冒口消除。△T↑ 枝晶发达→ 缩松↑
液态金属注入铸型后,首先在表面形成硬壳,其中尚处于液态的
金属在此外壳中冷却时,由于液态和凝固收缩体积缩小。如果所减
小的体积得不到外来金属液的补充,则在铸件中形成集中于某处的 或分散的孔洞一缩孔或缩松。因此,液态收缩和凝固收缩是铸件产 生缩孔和缩松的根本原因。 有一些合金,在凝固过程中体积不但不收缩,反而膨胀,故凝固 收缩率为负值。
③危害: 机械性能、 气密性、耐蚀性、锻造裂纹
铸件中缩孔的形成示意图
Al-4.5%Cu合金中的显微缩松 a.含气量高的显微缩松与球形孔大特点示意图 灰铸铁——“自补缩能力” 球墨铸铁——膨胀力大——若铸型移动——缩松倾向大
若铸型刚性大——自补缩
图 灰铁与球铁在湿砂型中浇注的膨胀曲线 灰铸铁——“自补缩能力” 球墨铸铁——膨胀力大——若铸型移动——缩松倾向大
2、铸钢的收缩
(1)液态 (2)凝固
图 碳钢的比容与温度和含碳量的关系 1-0.35%C;2-0.25%C;3-0.8%C
(3)固态收缩 a.珠光体转变前收缩 b.共析转变期的膨胀
10.3 缩孔与缩松的形成原理
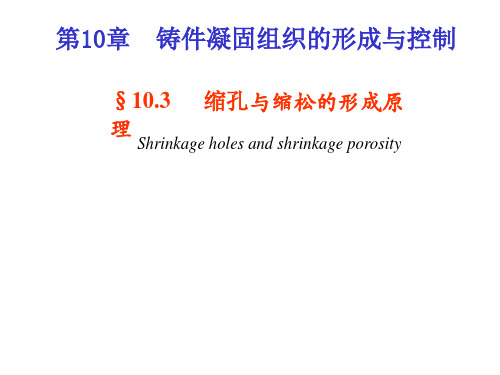
a) 明缩孔 b) 凹角缩孔 c) 芯面缩孔 d) 内部缩孔
2 缩松(Porosity) 缩松( )
分类:宏观缩松(简称缩松)和微观缩松(显微缩松) 分类:宏观缩松(简称缩松)和微观缩松(显微缩松) 分布:多出现于结晶温度范围较宽的合金中, 分布:多出现于结晶温度范围较宽的合金中,常分布在铸件壁的轴线 区域、缩孔附近或铸件厚壁的中心部位。 区域、缩孔附近或铸件厚壁的中心部位。
铸件在凝固过程中,由于合金的液态收缩和凝固收缩, 铸件在凝固过程中,由于合金的液态收缩和凝固收缩,往往在铸件最 容积大而集中的孔洞称为缩孔, 后凝固的部位出现孔洞 。容积大而集中的孔洞称为缩孔,细小而分散的孔 洞称为缩松 1 缩孔(Shrinkage hole) 缩孔( ) 热节:铸件厚壁处、 热节:铸件厚壁处、两壁相交处及内浇口附近等凝固较晚或凝固缓慢的部位 特征:尺寸较大,形状不规则,表面不光滑, 特征:尺寸较大,形状不规则,表面不光滑,有枝晶脉络状凸起 分类: 分类:内缩孔和外缩孔
1、液态收缩: ε v液 = α v液 (T浇 − TL ) ×100% 、液态收缩: 2、凝固收缩: 、凝固收缩: 3、固态收缩: ε v固 = α v固 (TS − T室 ) × 100% 、固态收缩:
ε L = α L (TS − T室 ) ×100%
2、铸钢的收缩 、
(1)液态 ) (2)凝固 )
凝
灰铸铁凝固收缩与碳当量的关系 灰铸铁凝固收缩与碳当量的关系 凝固收缩
(3)铸铁的固体收缩 )铸铁的固体收缩 曲线
图 Fe-C合金的自由线收缩曲线 合金的自由线收缩曲线 1-碳钢;2-白口铁;3-灰铸铁;4-球墨铸铁 -碳钢; -白口铁; -灰铸铁; -
10.3.2 缩孔与缩松的形成机理
- 1、下载文档前请自行甄别文档内容的完整性,平台不提供额外的编辑、内容补充、找答案等附加服务。
- 2、"仅部分预览"的文档,不可在线预览部分如存在完整性等问题,可反馈申请退款(可完整预览的文档不适用该条件!)。
- 3、如文档侵犯您的权益,请联系客服反馈,我们会尽快为您处理(人工客服工作时间:9:00-18:30)。
铸件缩孔、缩松产生的原因1、铸件结构方面的原因由于铸件断面过厚,造成补缩不良形成缩孔。
铸件壁厚不均匀,在壁厚部分热节处产生缩孔或缩松。
由于铸孔直径太小形成铸孔的砂芯被高温金属液加热后,长期处于高温状态,降低了铸孔表面金属的凝固速度,同时,砂芯为气体或大气压提供了通道,导致了孔壁产生缩孔和缩松。
铸件的凹角圆角半径太小,使尖角处型砂传热能力降低,凹角处凝固速度下降,同时由于尖角处型砂受热作用强,发气压力大,析出的气体可向未凝固的金属液渗入,导致铸件产生气缩孔。
2、熔炼方面的原因液体金属的含气量太高,导致在铸件冷却过程中以气泡形式析出,阻止邻近的液体金属向该处流动进行补缩,产生缩孔或缩松。
当灰铸铁碳当量太低时,将使铁水凝固时共晶石墨析出量减少,降低了石墨化膨胀的作用,使凝固收缩增加,同时也降低铁水的流动性。
认而降低铁水的自补缩能力,使铸件容易产生缩孔或缩松。
当铁水含磷量或含硫量偏高时,磷是扩大凝固温度范围的元素,同时形成大量的低熔点磷共晶,凝固时减少了补缩能力。
硫是阻碍石墨化的元素,硫还能降低铁水的流动性。
同时,铁水氧化严重,也降低液体金属的流动性,使铸件产生缩孔或缩松。
孕育铸铁或球墨铸铁在浇注前用硅铁等孕育剂进行孕育处理时,如果孕育不良,将导致铁水凝固时析出大量的渗碳体,从而使凝固收缩增加,产生缩孔或缩松。
3、工艺设计的原因(1)浇注系统设计不合理浇注系统设计与铸件的凝固原则相矛盾时,可能会导致铸件产生缩孔或缩松。
主要表现为浇注位置不合适,不利于顺序凝固,内浇口的位置及尺寸不正确。
对于灰铸铁和球墨铸铁,如果将内浇口开在铸件厚壁处,同时内浇口尺寸较厚,浇注后,内浇口则长时间处于液体状态。
在铁水凝固发生石墨化膨胀的作用下,铁水会经内浇口倒流回直浇道,从而使铸件产生缩孔和缩松。
(2)冒口设计不合理冒口位置、数量、尺寸及冒口颈尺寸未能促进铸件顺序凝固,都可能导致铸件产生缩孔和缩松。
如果在暗冒口顶部未放置出气冒口,或冷铁使用不当,也会导致铸件产生缩孔和缩松。
(3)型砂、芯砂方面的原因型砂(芯砂)的耐火度及高温强度太低,热变形量太大。
当在金属液的静压力或石墨化膨胀力的作用下,型壁或芯壁会产生移动。
使铸件实际需要的补缩量增加或在膨胀部位出现新的热节,导致铸件产生缩孔和缩松。
这种现象对大中型铸件是很敏感的。
另外,如果型砂中水分含量太高,将使型壁表面的干燥层厚度减少和水分凝聚区的水分增加,范围扩大,从而使型壁的移动能力增加,导致缩孔及缩松的产生。
(4)浇注方面的原因浇注温度太高,使液态金属的液态收缩量增加;太低时,又会降低冒口的补缩能力,特别是采用底注式浇注系统时更明显,铸件往往在下部产生缩孔和缩松。
当冒口没有浇满或对大中型铸件没有用金属液对明冒口进行补浇时,这将降低冒口的补缩能力,引起铸件产生缩孔或缩松。
铸件的缩孔和缩松的特征铸件形成后,在最后凝固部位,由于收缩出现的集中孔洞称为缩孔,分散而细小的孔洞称为缩松。
缩孔和缩松通常发生在铸件内部。
由于缩孔、缩松的存在,将减少铸件的有效承载截面积,甚至造成应力集中而大大降低铸件的物理和力学性能。
由于铸件的连续性被破坏,使铸件的气密性、抗蚀性等性能显著降低;加工后铸件表面的粗糙度提高。
所以,缩孔和缩松是铸件的主要缺陷之一,应予以防止。
金属在凝固过程中,当液态收缩与凝固收缩之和大于固态收缩时,就有可能在铸件内部留下孔洞。
由于金属性质和凝固条件的不同引起的缩孔、缩松类缺陷常有以下几种形式:1、缩孔缩孔的孔洞大而集中,缩孔的形状不规则,孔壁粗糙。
缩孔有出现在铸件外部和铸件内部两种,分别称为外缩孔和内缩孔。
外缩孔是指因金属液的凝固收缩而在铸件的外部或顶部形成的缩孔,一般在铸件上部呈漏斗状。
当铸件壁厚很厚时,有时出现在侧面或凹角处。
根据铸件的形状有所不同,漏斗状的下端有的较浅,有的一直深到铸件的内部。
一般来说,产生外缩孔的铸件其内部是致密的。
内缩孔是铸件凝固收缩时,在铸件内部产生的缩孔。
内缩孔呈不规则的粗糙孔壁,并且有凝固时产生的树枝状晶,一般为暗黑色或褐色。
内缩孔不限于铸件内部,有时在壁厚急变的拐弯处产生内缩孔,与表面相近,这时,内缩孔与外缩孔就难以区别了。
2、缩松缩松是铸件断面上出现的分散而细小的缩孔,有时借助放大镜才能发现。
铸件有缩松缺陷的部位,在气密性试验时,可能产生渗漏。
缩松的孔洞多而小,似海绵状,常出现在铸件最后凝固的部位,如在缩孔的下方或铸件截面的中央(轴线缩松)。
当铸件呈同时凝固时,特别是糊状凝固的金属(如球墨铸铁等),容易生成分散的孔洞,即缩松。
铸件质量检验生产中由于认识水平和生产条件的限制,铸件出现这种或那种缺陷是完全可能的。
铸件的质量是否符合技术条件所规定的要求,必须通过检验才能评定。
铸件质量检验是根据用户要求和图样技术条件等有关协议的规定,用目测、量具、仪表或其他手段检验铸件是否合格的操作过程。
铸件质量检验不仅是为了发现缺陷,而且可根据对缺陷的判断,进一步找出产生缺陷的原因,制定出防止缺陷的措施。
铸件质量的内容,从满足用户要求出发,应包括外观质量,内在质量和使用质量三个方面。
(1)铸件外观质量指铸件表面状况和达到用户要求的程度。
包括铸件表面的粗糙度、表面缺陷、尺寸公差、形状偏差、重量偏差等。
检查铸件的表面质量,一般用观察法或用有关量具、仪器等进行测量。
(2)铸件内在质量指一般不能用肉眼检查出来的铸件内部状况和达到用户要求的程度。
主要包括化学成分、物理和力学性能,金相组织以及存在于铸件内部的孔洞、裂纹、夹杂物等缺陷。
内在质量的检验可用化学分析、材料试验、金相检查、无损探伤等方法。
(3)铸件的使用质量指铸件能满足使用要求的性能。
如在强力、高速、磨损、腐蚀、高热等不同条件下的工作性能,切削性能、焊接性能、运转性能等。
目前,我国对铸件质量分等,已制定的相关标准为:JB/JQ 8200l一90《铸件质量分等通则》,对铸件外观质量制订的国家标准有:GB 6414—1986《铸件尺寸公差分等》,GB60601—1985《铸件表面粗糙度》,GB/T11351—1989《铸件质量公差》等。
防止铸件夹杂类缺陷的措施在金属熔炼方面的措施,防止在熔炼过程中带入其他有害金属;使用质量好的原材料,控制炉料及孕育剂、球化剂的尺寸不宜太大或太小。
精炼剂和变质剂应烘干后使用。
在熔炼过程中,加入适量的溶剂,使金属液中的夹杂物和有害元素等杂质容易生成熔点低、流动性好、密度与金属液相差较大的熔渣,易与金属液分离。
对金属液进行充分的精炼,去除金属液中的夹杂物。
对铸钢熔炼应进行充分脱氧和脱硫处理。
在金属液上覆盖一层溶剂,使上浮的熔渣能被吸附,有利于去除。
对于加入高熔点的中间合金,适当提高熔炼温度,有利于高熔点合金的熔化,有时可以采用搅拌措施,使金属液成分均匀。
应注意搅拌后,金属液应静置一段时间,待熔渣充分上浮后再浇注。
造型操作中,保证砂型紧实度均匀,砂芯应有足够的高温强度。
合型应准确无误,保证砂型的完好。
严格执行铸造工艺规程,防止砂型和砂芯烘干过程中,产生过烧现象。
合理设计浇注系统,在浇注系统中加设挡渣装置,如过滤网、集渣包等。
浇注前,可静置金属液,浇注中,要有挡渣措施,浇注速度不宜太快,浇包距离浇口杯不要太高,避免产生金属液飞溅,导致冷豆生成。
铸造应力的产生原因及特点1、铸造应力的产生通常说的铸造应力,有时是泛指,即不论产生应力的原因如何,凡铸件冷却过程中尺寸变化受阻,产生的应力都称作铸造应力。
但通常指的铸造应力多指残余应力。
铸件有残余应力时,经机械加工后可能产生新的变形,使零件精度降低或尺寸超差;若铸件承受的工作应力与残余应力方向相同而叠加,就可能超过材料强度极限而破坏;有残余应力的铸件在长期存放后,会产生变形;若在腐蚀介质中存放或工作时,还会产生应力腐蚀而开裂。
因此,应尽量减少铸件冷却过程中产生的残余应力并设法消除之。
铸件凝固结束后,铸件都要随着温度的下降发生固态收缩或相变,在固态相变的同时,有相变体(线)膨胀或收缩,由于厚壁铸件外层比内层冷却的快,壁厚不同的铸件厚壁冷的慢,薄壁冷的快。
从而导致外层与内层,厚壁与薄壁固态线收缩率(mm/s)不一致,使厚壁的外层和内层、厚壁与薄壁就相互制约收缩,发生拉伸或压缩变形。
在固态冷却前期,薄壁降温比厚壁快,产生的收缩量较大,从而使薄壁部位受到拉伸变形,产生拉应力,而在厚壁部位形成压缩变形,产生压应力;在冷却后期,厚壁的降温又比薄壁快,产生的收缩量较薄壁部位大,所以又在厚壁部位形成拉伸变形,产生拉应力,而在薄壁部位形成压缩变形,产生压应力。
如果在冷却前期和冷却后期形成的应力能相互抵消,则铸件最终不产生应力,而只在冷却过程中表现出来的应力称为临时应力。
如果两种应力不能相互抵消,则有一部分应力会残留在铸件上,这种应力称为残余应力。
除此之外,铸件的固态线收缩还受到外部因素的阻碍(如砂芯、冒口、浇注系统等),如果外部因素退让性不足,温度下降时不能实现应有的收缩值,铸件将产生拉应力。
在冷却过程中,固态收缩由于上述各种因素的影响,使铸件的收缩受阻,发生变形而产生应力,这种应力为铸造应力。
铸造应力包括:热应力、相变应力、收缩应力三种。
2、铸造残余应力铸件清理完后,仍然存在宏观的残余应力。
残余应力也称“内应力”。
铸件残余应力不是一种铸造缺陷,但对铸件产生裂纹和变形起着重要的作用。
铸件的残余应力(拉应力)大于材料的抗拉强度时,就会使铸件产生裂纹;当铸件存在残余应力时,会使铸件变“脆”;残余应力还会使铸件产生应力腐蚀开裂。
铸件残余应力有宏观和微观之分,按形成原因可分为热应力型残余应力、相变型残余应力、收缩应力型残余应力。
生产实践表明铸件残余应力主要为热应力型,即为残余热应力。
防止铸件产生缩孔、缩松的措施1、控制铸件的凝固方向凝固方向应符合定向凝固或同时凝固的原则。
(1)定向凝固采用各种措施保证铸件结构上各部分按照远离冒口的部分先凝固,然后是靠近冒口部分,最后是冒口本身的凝固。
建立顺序凝固的条件是液体补偿通道畅通。
可正确选择铸件的浇注位置,采用冷铁或其他激冷材料;放置尺寸足够大,数量足够多的冒口,保证有足够的金属液对铸件就近补缩;用发热冒口来提高冒口的温度、添加保温剂减缓冒口的冷却速度;适当提高冒口的高度;采用大气压力冒口来提高冒口补缩能力等。
(2)均衡凝固所谓均衡凝固就是利用膨胀和收缩动态叠加的自补缩和浇冒口的外部补缩,采取工艺措施,使单位时间的收缩与膨胀按比例进行的一种凝固工艺原则。
按照这一工艺原则,浇注系统和冒口系统要从铸件的薄壁处引入,补缩工艺设计以自补缩为基础,对于铸铁件,应充分利用石墨化膨胀自补缩,冒口只是补充自补不足的差额。
同时,冒口不应该放在铸件的热节上,冒口既要靠近热节,以利于补缩,又要离开热节,以减少冒口对铸件的热干扰。