3.2.2 缩孔、缩松的形成及防止方法
铸件中缩孔与缩松的防止方法
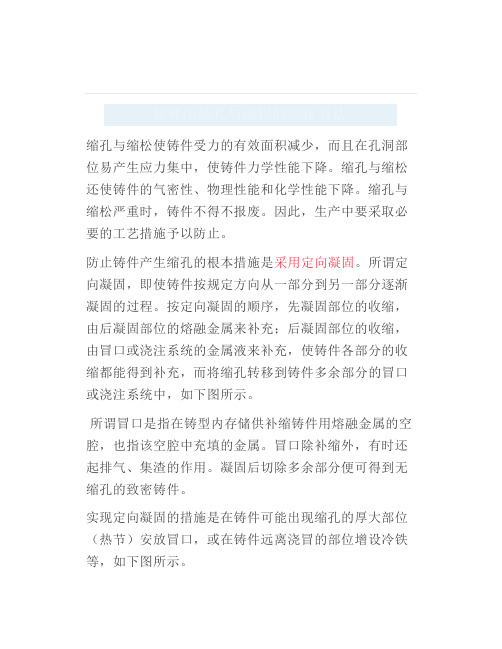
铸件中缩孔与缩松的防止方法缩孔与缩松使铸件受力的有效面积减少,而且在孔洞部位易产生应力集中,使铸件力学性能下降。
缩孔与缩松还使铸件的气密性、物理性能和化学性能下降。
缩孔与缩松严重时,铸件不得不报废。
因此,生产中要采取必要的工艺措施予以防止。
防止铸件产生缩孔的根本措施是采用定向凝固。
所谓定向凝固,即使铸件按规定方向从一部分到另一部分逐渐凝固的过程。
按定向凝固的顺序,先凝固部位的收缩,由后凝固部位的熔融金属来补充;后凝固部位的收缩,由冒口或浇注系统的金属液来补充,使铸件各部分的收缩都能得到补充,而将缩孔转移到铸件多余部分的冒口或浇注系统中,如下图所示。
所谓冒口是指在铸型内存储供补缩铸件用熔融金属的空腔,也指该空腔中充填的金属。
冒口除补缩外,有时还起排气、集渣的作用。
凝固后切除多余部分便可得到无缩孔的致密铸件。
实现定向凝固的措施是在铸件可能出现缩孔的厚大部位(热节)安放冒口,或在铸件远离浇冒的部位增设冷铁等,如下图所示。
所谓冷铁是指为增加铸件局部的冷却速度,在砂型、砂芯表面或型腔中安放的金属物。
图中所示铸件中可能产生缩孔的厚大部分不止一个,若仅靠顶部冒口,难以向底部凸台补缩,如果在该凸台的型壁上安放两个外冷铁,加快了该处的冷却速度,使厚壁凸台反而最先凝固,从而实现了由下而上的定向凝固。
定向凝固与逐层凝固是两个不同的概念。
定向凝固是指铸件各部分的凝固顺序;逐层凝固是指铸件某截面上的凝固顺序。
逐层凝固的合金表层先凝固,然后逐渐向铸件中心增厚,铸件中心最后凝固。
冒口的补缩通道能长时间保持畅通,有利于实现铸件的定向凝固。
对于纯金属、共晶成分的合金,工艺上一般都采用定向凝固的原则,来提高铸件的致密性。
相反,倾向于糊状凝固的合金,结晶的固体骨架较好地布满整个铸件的截面,使冒口的补缩通道堵塞,难以实现定向凝固。
铸钢件缩孔和缩松的形成与预防

F铸造oundry热加工热处理/锻压/铸造2011年第15期69铸钢件缩孔和缩松的形成与预防宁夏天地奔牛实业集团有限公司(石嘴山753001)王福京缩孔和缩松从本质上来说,是因为型内的金属产生收缩而引起的,但是不同种类的金属,其形成缩孔和缩松的机理有所不同。
1.产生机理从铸钢件角度来分析,钢液注满型腔后,由于型壁的传热作用,型内钢液形成自型壁表面至铸件壁厚中心温度逐渐升高的温度梯度。
随着型壁传热作用不断地进行,型内钢液温度不断降低。
当与型壁表面接触的钢液温度降至凝固温度时,铸件的表面就开始凝固,并形成一层固体状态的硬壳。
如果这时浇注系统已经凝固,那么硬壳内处于液体状态的钢液就与外界隔绝。
当型内钢液温度进一步降低时,硬壳内的钢液一方面因温度降低而产生液态收缩,另一方面由于硬壳的传热作用,使与硬壳接触的钢液不断结晶凝固,从而出现凝固收缩。
这两种收缩的出现,将使硬壳内钢液液面下降。
与此同时,处于固体状态的硬壳,也因温度的降低而产生固态收缩,对于铸钢件来说,由于液态收缩和凝固收缩的总和是大于固态收缩的,因此在重力作用下,硬壳内钢液液面将下降,并且与上部硬壳脱离接触。
随着型内钢液温度不断地降低和硬壳内钢液不断地凝固,硬壳越来越厚,而钢液越来越少。
当铸件内最后的钢液凝固后,铸件上部的硬壳下面就会出现一个孔洞,这个孔洞即为缩孔。
虽然凝固后的铸件自高温状态冷却至室温时,还将产生固态收缩,从而使整个铸件和其内部缩孔的体积稍有减小,但并不会改变缩孔体积与铸件体积的比值。
由于凝固层厚度的增加和钢液的减少是不断进行的,因而从理论上来说,缩孔的形状是漏斗状的。
并且因残存的钢液凝固时不能得到补缩,所以在产生缩孔的同时,往往也伴随着缩松的出现。
用肉眼能直接观察到的缩孔为宏观缩孔,而借助于放大镜或将断面腐蚀以后才能发现的缩孔为微观缩孔。
一般情况下,宏观缩孔可以用补焊的手段来解决,而微观缩孔就无法处理了,一般都是成片出现的微小孔洞。
缩孔和缩松及其控制方法

缩孔和缩松及其控制方法缩孔和缩松是在材料加工和制造过程中常见的问题,对于产品的质量和性能有着重要影响。
本文将分别介绍缩孔和缩松的概念、原因以及控制方法。
一、缩孔缩孔指的是材料加工或制造过程中产生的孔洞或空隙,一般是由于材料内部气体无法完全排除或者材料收缩不均匀而引起的。
缩孔问题会导致产品的力学性能下降、密封性能降低以及外观质量不佳等问题。
造成缩孔的原因有多种,主要包括以下几个方面:1. 材料本身的问题:一些材料由于其特殊的化学成分或物理性质,容易产生气泡或者孔洞。
这些材料在加工或制造过程中容易出现缩孔问题。
2. 加工工艺的问题:加工过程中,如果温度、压力或者速度等参数控制不当,都有可能导致缩孔问题的发生。
例如,如果温度过高或者加热速度过快,就容易在材料内部产生气泡或者孔洞。
3. 设备的问题:加工设备的性能和状态也会影响材料的缩孔情况。
如果设备的密封性不好或者加工条件不能满足要求,就有可能导致缩孔问题。
针对缩孔问题的控制方法主要包括以下几个方面:1. 材料选择:选择合适的材料对于缩孔问题的控制非常重要。
一些具有较低缩孔倾向的材料可以有效地减少缩孔问题的发生。
2. 加工工艺优化:通过合理调整加工工艺参数,如温度、压力、速度等,可以减少缩孔问题的发生。
例如,采用适当的加热温度和加热时间可以降低材料内部气泡的产生。
3. 设备改进:改进加工设备的密封性能和控制能力,能够有效地减少缩孔问题。
定期检查和维护设备,确保其处于良好的工作状态也是很重要的。
二、缩松缩松是指在材料加工或制造过程中,由于材料的收缩不均匀而导致的形状尺寸偏差。
缩松问题会导致产品的尺寸不准确,甚至无法满足设计要求。
造成缩松的原因主要包括以下几个方面:1. 材料本身的问题:一些材料由于其特殊的物理性质,在加工或制造过程中容易出现收缩不均匀的情况,从而导致缩松问题的发生。
2. 加工工艺的问题:加工过程中,如果温度、压力或者速度等参数控制不当,都有可能导致材料收缩不均匀,出现缩松问题。
缩孔的防止措施

缩孔的防止措施1. 背景介绍在工程领域中,缩孔是一种常见的问题,指的是混凝土浇筑过程中未能填满模板或者未完全充实的空洞或空隙。
缩孔可能会导致混凝土结构的强度和稳定性受到影响,从而影响到工程的质量和安全性。
为了防止缩孔问题的发生,在混凝土浇筑过程中需要采取一些防止措施。
2. 防止缩孔的措施以下是防止缩孔问题发生的几种常用措施:2.1 混凝土配合比设计混凝土配合比设计是防止缩孔的关键因素之一。
合理的配合比设计可以确保混凝土的流动性和可塑性,从而减少浇筑过程中的空隙和空洞。
在设计配合比时,需要考虑到使用的材料种类和质量、水胶比、粉料含量以及外加剂的使用等因素。
2.2 浇筑技术控制控制好混凝土的浇筑技术也是防止缩孔的重要措施之一。
以下是几个浇筑技术控制的要点:•振捣方式和时间:使用适当的振捣方式和时间可以帮助混凝土充实模板中的空隙和空洞。
振捣应该均匀地分布在整个浇筑区域,并且持续时间应该足够长,确保混凝土能够流动并充分充实。
•浇注方式:采用合适的浇注方式可以有效地减少缩孔的发生。
例如,在梁柱节点处可以采用低压喷射的方式进行浇注,将混凝土均匀地注入模板中,避免产生空洞。
2.3 加大修补措施如果在施工过程中发现缩孔问题,需要及时采取修补措施,以确保施工质量。
以下是一些常用的修补措施:•补丁修复:针对小面积的缩孔,可以使用混凝土补丁进行修复。
补丁的混凝土需要与原混凝土具有相同的成分和性能。
•重新浇筑:对于大面积的缩孔,需要重新浇筑混凝土。
在重新浇筑之前,需要清理和处理好原混凝土表面,确保新旧混凝土之间能够良好的结合。
重新浇筑时需要遵循之前提到的浇筑技术控制措施。
3. 缩孔的影响如果缩孔问题得不到有效的控制和修复,可能会带来以下几个方面的不良影响:•结构强度丧失:缩孔可能导致混凝土结构的强度丧失,从而影响到整个工程的安全性和稳定性。
•结构变形:缩孔也可能导致混凝土结构的变形增大,使得结构整体的稳定性下降。
•耐久性下降:缩孔会导致混凝土中的空隙增多,从而影响到混凝土的耐久性。
分析铸造缩松缺陷形成原因及对策

分析铸造缩松缺陷形成原因及对策铸造缩孔缺陷是在铸造过程中常见的一种问题,它会给制造业带来很多麻烦和损失。
本文将分析铸造缩孔缺陷的形成原因,并提出相应的对策,以期为相关行业提供帮助和指导。
一、铸造缩孔缺陷的形成原因分析1.1 完全凝固不均匀在铸造过程中,铸件凝固是逐渐进行的,如果凝固速度不均匀,就会导致缩孔缺陷的形成。
常见的原因包括铸件的凝固时间过短、冷却速度不均匀、局部温度过高等。
1.2 金属液收缩过大铸造过程中,金属液在凝固过程中会收缩,如果收缩过大,就容易形成缩孔。
这主要是由于铸件材料的物理性质不合理,或者是铸型的设计不合理所导致的。
1.3 铸造材料含有气体铸造材料中含有气体会在凝固过程中释放出来,如果释放过快,就会形成孔洞。
常见的原因是铸造材料中含有气体的含量过高,或者是在铸造过程中没有采取有效的排气措施。
1.4 基材与液态金属的相容性差如果铸件的基材与液态金属的相容性差,就容易在凝固过程中产生裂纹和缩孔。
一般来说,基材与液态金属的相容性差会导致界面张力增大,从而影响凝固过程。
二、对策提出2.1 优化铸造工艺参数通过优化铸造工艺参数,可以降低缩孔缺陷的发生概率。
具体来说,可以调整金属液的浇注温度和速度,控制铸件的凝固时间,改进冷却系统等措施。
2.2 优化铸造材料选择合适的铸造材料也是减少缩孔缺陷的关键。
应选择具有较低的收缩率和较好的流动性的材料,以确保凝固过程中的收缩程度可控。
2.3 采取有效的排气措施在铸造过程中,采取有效的排气措施可以减少气体对铸件凝固过程的干扰,从而降低缩孔缺陷的风险。
排气措施可以包括加入剂、提高浇注温度、采取适当的连续浇注等。
2.4 提高基材与液态金属的相容性为了减少缩孔缺陷的形成,可以通过提高基材与液态金属的相容性来增加界面的稳定性。
可以通过改变基材化学成分、调整金属液的配方等方式来实现。
三、结语以上是对铸造缩孔缺陷形成原因及对策的分析。
通过优化铸造工艺、材料选择、排气措施以及提高基材与液态金属的相容性等方法,可以有效降低缩孔缺陷的发生概率,提高铸件的质量和产能。
铸铁件缩松、缩孔、凹陷缺陷的原因分析与防止方法
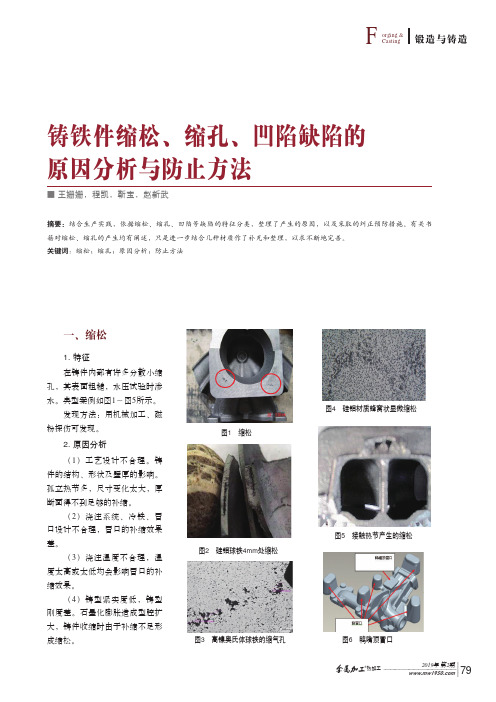
2019年第2期热加工79F锻造与铸造orging &Casting铸铁件缩松、缩孔、凹陷缺陷的原因分析与防止方法■王姗姗,程凯,靳宝,赵新武摘要:结合生产实践,依据缩松、缩孔、凹陷等缺陷的特征分类,整理了产生的原因,以及采取的纠正预防措施。
有关书籍对缩松、缩孔的产生均有阐述,只是进一步结合几种材质作了补充和整理,以求不断地完善。
关键词:缩松;缩孔;原因分析;防止方法一、缩松1. 特征在铸件内部有许多分散小缩孔,其表面粗糙,水压试验时渗水。
典型案例如图1~图5所示。
发现方法:用机械加工、磁粉探伤可发现。
2. 原因分析(1)工艺设计不合理。
铸件的结构、形状及壁厚的影响。
孤立热节多,尺寸变化太大,厚断面得不到足够的补缩。
(2)浇注系统、冷铁、冒口设计不合理,冒口的补缩效果差。
(3)浇注温度不合理,温度太高或太低均会影响冒口的补缩效果。
(4)铸型紧实度低,铸型刚度差。
石墨化膨胀造成型腔扩大,铸件收缩时由于补缩不足形成缩松。
图1 缩松图2 硅钼球铁4mm处缩松图4 硅钼材质蜂窝状显微缩松图3 高镍奥氏体球铁的缩气孔图5 接触热节产生的缩松图6 鸭嘴顶冒口2019年 第2期 热加工80F锻造与铸造orging &Casting(5)碳、硅含量低,磷含量较高;凝固区间大。
硅钼和高镍球墨铸铁对碳、硅含量和氧化铁液的敏感性特大,铁液严重氧化或碳、硅量低时,易出现显微缩松。
即便在薄壁处也容易出现缩松(见图2、图3、图4)。
(6)孕育不充分,石墨化效果差。
(7)残余镁量和稀土量过高。
钼含量较高时也会增加显微缩松。
(8)浇注速度太快。
(9)炉料锈蚀,氧化铁多。
(10)铁液在电炉内高温停放时间太长,俗称“死铁水”,造成严重氧化。
(11)冲天炉熔炼时底焦太底,风量太大,元素烧损大,铁液严重氧化。
(12)冒口径处形成接触热节产生缩松(见图5)。
(13)压箱铁不够(或箱卡未锁紧,箱带断裂等),浇注后由于涨箱造成缩松。
304不锈钢熔模铸造中缩孔、缩松的几种防止措施

熔模铸造中缩松的几种特有解决方案
缩松是铸造最常见的缺陷之一,是铸件在冷却过程中热节或远浇口部位得不到有效的补缩而产生的细小分散的孔洞。
熔模铸造因为热壳浇注的特点,在浇注系统设计时大大地限制了冒口、冷铁对于缩松的处理,但是却有一系列独特的解决方案。
1、型壳底部淬水
部位:铸件浇注位置底部。
铸件浇注位置底部远离浇冒口,补缩通道过长,如果铸件较高或底部有热节,就容易产生缩松。
原理:通过淬水使型壳底部温度迅速降低,对铸件起到底部激冷的作用。
操作:热壳浇注后,型壳立刻淬水,视铸件薄厚在水中停顿1-3秒,深度为易缩松的位置。
案例1圆环产品,材质304不锈钢,浇注温度1640℃
此产品组树后高度方向尺寸较大,见图1和图2,浇注后于圆环浇注位置的下半圆A处容易出现缩松,如图1,经分析认为补缩通道过长导致下半圆凝固时钢水得不到有效补缩,从而产生缩松。
工艺改进为型壳底部淬水,深度如图2所示,效果良好,基本解决下半圆的缩松问题。
图1 圆环剖面图图2 圆环组树淬水示意图
2、喷水激冷
3、局部补砂泥
4、中空型壳
5、加保温棉
6、工艺散热冷铁
7、冷铁、热贴。
二、铸件中的缩孔和缩松讲解

1、缩孔与缩松的形成 (1)缩孔(又称集中缩孔)
• 形成 • 形状:倒锥形 • 形成部位最后凝固处 • 易形成缩孔的合金:纯金属,共晶成分
的合金→逐层凝固
图2-4 缩孔形成过程
Fig.2-4 The formation of Shrinkage Void
The formation of Thermal Stress
Internal Stress,Deformation and
Crack of Casting
• 结论:铸件中厚的部分最后冷却,总是 受拉应力,反之,薄的部分受压应力。
• 热应力的预防:采用同时凝固的方法 (不管壁厚如何,同时一起收缩,可避 免热应力的产生)。
Internal Stress,Deformation and Crack of Casting
铸造内应力:铸件冷却时因固态收缩受 阻碍,在铸件内部产生的应力。
一、内应力的形成
类型— 热应力、机械应力 1、热应力
• 热应力的形成 • 形成原因—铸件的壁厚不均匀,冷却和
收缩先后不一致造成内应力。
图2-8 热应力的形成
• 适用的合金:普通灰口铸铁(缩孔缩松 倾向小),锡青铜
2、机械应力
二、铸件的变形与预防
Deformation of the Cast and Its Prevention
具有内应力的铸件处在一种不稳定的状 态— 它会通过适当的变形来减缓自身的 内应力,趋于一种稳定状态。
例1 T型型材的变形 例2 机架的变形 例3 机床床身
顺序凝固法的总体思路:合金的收缩不 可避免,可使缩孔形成在铸件外部的冒 口内(该处为最后凝固处)。
铸铁件常见铸造缺陷的防止方法

铸铁件经常会发生各种不同的铸造缺陷,如何防止这些缺陷发生,一直是铸件生产厂关注的问题。
本文介绍了笔者在这方面的一些认识和实践经验。
1 气孔特征:铸件中的气孔是指在铸件内部,表面或接近表面处存在的大小不等的光滑孔洞。
孔壁往往还带有氧化色泽,由于气体的来源和形成原因不同,气孔的表现形式也各不相同,有侵入性气孔,析出性气孔,皮下气孔等。
1.1 侵入性气孔这种气孔的数量较少,尺寸较大,多产生在铸件外表面某些部位,呈梨形或圆球形。
主要是由于铸型或砂芯产生的气体侵入金属液的未能逸出而造成。
防止措施:(1)减少发气量:控制型砂或芯砂中发气物质的含量,湿型砂的含水量不能过高,造型与修模时脱模剂和水用量不宜过多。
砂芯要保证烘干,烘干后的砂芯不宜存放太长时间,隔天使用的砂芯在使用前要回炉烘干,以防砂芯吸潮,不使用受潮、生锈的冷铁和芯撑等。
(2)改善型砂的透气性,选择合适的型空紧实度,合理安排出气眼位置以利排气,确保砂芯通气孔道畅通。
(3)适当提高浇注温度,开排气孔和排气冒口等,以利于侵入金属液的气体上浮排出。
1.2 析出性气孔这种气孔多而分散,一般位于铸件表面往往同批浇注的铸件大部分都发现有。
这种气孔主要是由于在熔炼过程中,金属液吸收的气体在凝固前未能全部析出,便在铸件中形成许多分散的小气孔。
防止措施:(1)采用洁净干燥的炉料,限制含气量较多的炉料使用。
(2)确保“三干”:即出铁槽、出铁口、过桥要彻底烘干。
(3)浇包要烘干,使用前最好用铁液烫过,包中有铁液,一定要在铁液表面放覆盖剂。
(4)各种添加剂(球化剂、孕育剂、覆盖剂)一不定期要保持干燥,湿度高的时候,要烘干后才能使用。
1.3 皮下气孔这种气孔主要出现在铸件的表层皮下2~3mm处,直径为1~3mm左右。
而且数量较多,铸件经热处理或粗加工去除外皮后,就会清晰地显露出来。
防止措施;(1)适当提高浇注温度,严格控制各种添加剂的加入量,尽可能缩短浇注时间。
(2)孕育剂的加入量最好控制在(质量分数)0.4%~0.6%,同时要严格控制孕育剂中A1的质量分数,w(Al)偏高容易和型腔表面的水分发生反应:2Al+3H2O=Al2O3+3H2↑,一般情况下孕育剂含Al量不宜超过1.5%。
缩孔和缩松及其控制方法

缩孔和缩松及其控制方法缩孔和缩松是材料加工中常见的问题,会对产品的质量和性能产生不利影响。
本文将首先介绍缩孔和缩松的概念和原因,然后探讨相关的控制方法。
一、缩孔和缩松的概念和原因缩孔是指材料中存在的孔洞或空隙,在加工过程中由于内部应力的作用而发生收缩,导致孔洞的尺寸变小。
缩松是指材料中的实体部分在加工过程中由于受到挤压或拉伸而发生收缩,导致尺寸变小。
缩孔和缩松的产生原因有多种,主要包括材料的物理性质、加工工艺和设备的影响。
材料的物理性质包括材料的组织结构、成分和热膨胀系数等,这些因素会影响材料在加工过程中的变形和收缩特性。
加工工艺中的温度、压力和速度等参数的选择也会影响缩孔和缩松的产生。
设备的精度和稳定性也会对缩孔和缩松产生影响。
二、缩孔和缩松的控制方法为了减少或避免缩孔和缩松的产生,可以采取以下控制方法:1. 材料选择:选择具有较低膨胀系数和较好变形性能的材料,可以减少缩孔和缩松的产生。
此外,还可以选择具有合适组织结构和成分的材料,以提高材料的可加工性。
2. 加工工艺优化:在加工过程中,要合理选择温度、压力和速度等参数,以减少缩孔和缩松的产生。
同时,还需要注意加工工艺中的各个环节,如预处理、加热、冷却和保温等,以确保材料的均匀性和稳定性。
3. 设备维护和调整:保持加工设备的精度和稳定性,及时对设备进行维护和调整,可以减少因设备问题而引起的缩孔和缩松。
此外,还可以通过调整设备的参数,如温度、压力和速度等,来控制缩孔和缩松的产生。
4. 模具设计和加工:合理设计和加工模具,可以减少缩孔和缩松的产生。
模具的结构和形状应与产品的要求相匹配,以确保材料在加工过程中的均匀性和稳定性。
同时,还要注意模具的材料选择和表面处理,以提高模具的耐磨性和抗粘性。
5. 检测和控制:在加工过程中,要建立合适的检测和控制方法,及时发现和解决缩孔和缩松的问题。
可以使用非破坏性检测方法,如超声波检测和X射线检测,来检测材料中的缺陷和孔洞。
压铸件缩孔缩松的原因及解决办法
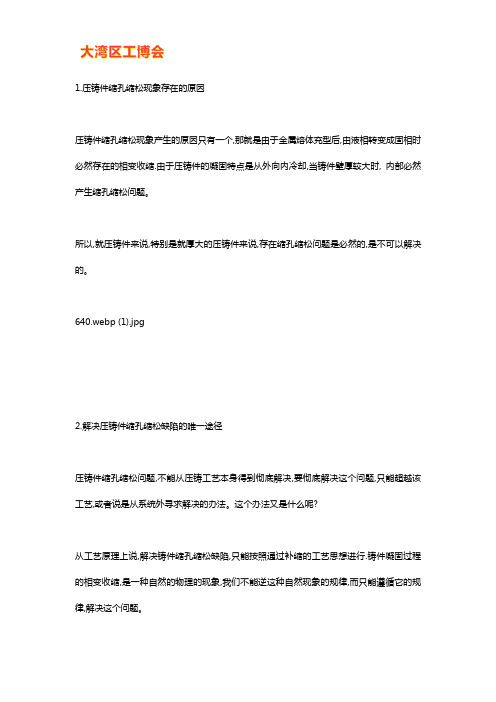
1.压铸件缩孔缩松现象存在的原因压铸件缩孔缩松现象产生的原因只有一个,那就是由于金属熔体充型后,由液相转变成固相时必然存在的相变收缩.由于压铸件的凝固特点是从外向内冷却,当铸件壁厚较大时, 内部必然产生缩孔缩松问题。
所以,就压铸件来说,特别是就厚大的压铸件来说,存在缩孔缩松问题是必然的,是不可以解决的。
640.webp (1).jpg2.解决压铸件缩孔缩松缺陷的唯一途径压铸件缩孔缩松问题,不能从压铸工艺本身得到彻底解决,要彻底解决这个问题,只能超越该工艺,或者说是从系统外寻求解决的办法。
这个办法又是什么呢?从工艺原理上说,解决铸件缩孔缩松缺陷,只能按照通过补缩的工艺思想进行.铸件凝固过程的相变收缩,是一种自然的物理的现象,我们不能逆这种自然现象的规律,而只能遵循它的规律,解决这个问题。
3.补缩的两种途径对铸件的补缩,有两种途径,一是自然的补缩,一是强制的补缩. 要实现自然的补缩,我们的铸造工艺系统中,就要有能实现“顺序凝固”的工艺措施.很多人直觉地以为,采用低压铸造方法就能解决铸件的缩孔缩松缺陷,但事实并不是这么回事.运用低压铸造工艺,并不等于就能解决铸件的缩孔缩松缺陷,如果低压铸造工艺系统没有设有补缩的工艺措施,那么,这种低压铸造手段生产出来的毛坯,也是可能百分之一百存在缩孔缩松缺陷的。
由于压铸工艺本身的特点,要设立自然的“顺序凝固”的工艺措施是比较困难的,也是比较复杂的.最根本的原因还可能是, ”顺序凝固”的工艺措施,总要求铸件有比较长的凝固时间,这一点,与压铸工艺本身有点矛盾。
强制凝固补缩的最大特点是凝固时间短,一般只及”顺序凝固”的四分之一或更短,所以,在压铸工艺系统的基础上,增设强制的补缩工艺措施,是与压铸工艺特点相适应的,能很好解决压铸件的缩孔缩松问题。
4.强制补缩的两种程度挤压补缩和锻压补缩实现铸件的强制补缩可以达到有两种程度.一种是基本的可以消除铸件缩孔缩松缺陷的程度,一种是能使毛坯内部达到破碎晶粒或锻态组织的程度.如果要用不同的词来表述这两种不同程度话,那么,前者我们可以用“挤压补缩”来表达,后者,我们可以用“锻压补缩”来表达。
铸铁件缩孔和缩松缺陷防止方法及应用实例
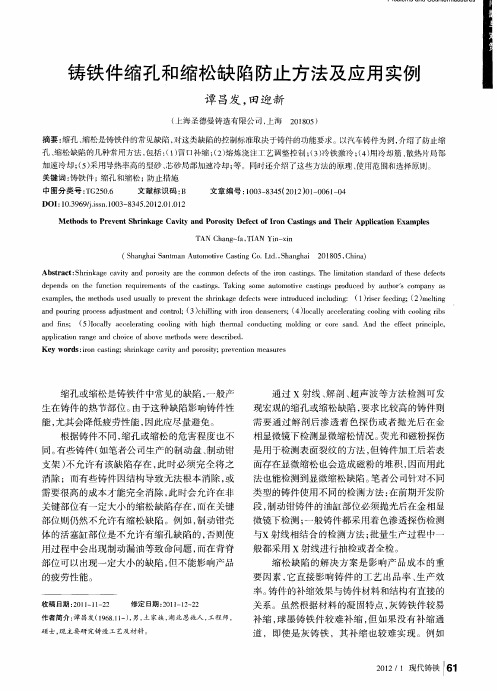
DOI 1. 6  ̄i n10 - 3 52 1.1 1 :03 9 .s. 3 84 . 20 . 2 9 s 0 0 0
M e h d o Pr v n h i k g v t n o o i  ̄e fI o si sa d Th i p ia i n Ex mp e t o s t e e t r n a e Ca i a d P r st De to r n Ca t S y y ng n er Ap l to a c ls
而 由于 Mg 大 铁液 的收缩 倾 向 , 防止 缩松 考 增 从
虑 , Mg 量应越 低越好 ; ( 残) 兼顾 到工 艺控 制 的难
采用冷却筋 、 散热片和导热率高 的型砂 、 芯砂局 部加速冷却等。 以下是笔者公司使用这些方法解
决缩 孔缩 松缺 陷 的实例 。
度 , 际生产 中一 般采 用 的控制 范 围为 005 实 .3%~
决 。要 注 意 的是 , 种方 法 只适用 于缩 松 或者 显 这
微缩松 比较轻微 , x射线检查没有发现每个铸件
都 有这种 缺 陷 , 就是 出现 缩松 缺陷 的铸 件 比例 也
不 高时 。 21 化 学成分 方面 的控 制 .
( ) 当提 高 C C 1适 E。 E高 , 铁液 凝 固过程 中石
与x射线 相 结合 的检 测 方法 ; 批量 生 产过 程 中一
关键部位有一定大小 的缩松缺陷存在 , 而在关键
部位 则仍 然 不允许 有 缩 松缺 陷 。例 如 , 动钳 壳 制 体 的活塞 缸部 位是 不 允许 有 缩孔 缺 陷 的 , 否则 使 用过 程 中会 出现 制 动漏 油等 致命 问题 , 而在 背脊 部位 可 以 出现 一定 大 小 的缺 陷 , 不 能影 响 产 品 但
3.2.2 缩孔、缩松的形成及防止方法

缩孔、缩松的形成及防止方法副教授:陈云铸件中的缩孔与缩松液态金属在铸型内凝固过程中,由于液态收缩和凝固收缩导致体积缩小,若其收缩得不到补充,就在铸件最后凝固的部分形成孔洞。
大而集中的孔洞称为缩孔,细小而分散的孔洞称为缩松。
(a)铝合金缩孔、缩松(b)金相显微镜下缩松(c)扫描电镜下缩松一、缩孔的形成纯金属、共晶成分和凝固温度范围窄的合金,浇注后在型腔内是由表及里的逐层凝固。
在凝固过程中,如得不到合金液的补充,在铸件最后凝固的地方就会产生缩孔。
缩孔形成的条件:铸件呈逐层凝固方式凝固,成分为纯金属或共晶成分的合金。
缩孔产生的基本原因:是合金的液态收缩和凝固收缩值大于固态收缩值,且得不到补偿。
缩孔产生的部位在铸件最后凝固区域,如壁较厚大的上部或铸件两壁相交处,这些地方称为热节。
热节位置可用画内接圆的方法确定。
用画内切圆法确定缩孔位置二、缩松的形成铸件最后凝固的收缩未能得到补充,或者结晶温度范围宽的合金呈糊状凝固,凝固区域较宽,液、固两相共存,树枝晶发达,枝晶骨架将合金液分割开的小液体区难以得到补缩所致。
缩松形成的条件:铸件主要呈糊状凝固方式凝固,成分为非共晶成分或有较宽结晶温度范围的合金。
形成缩松的基本原因:是合金的液态收缩和凝固收缩值大于固态收缩值。
缩松一般出现在铸件壁的轴线区域、冒口根部、热节处,也常分布在集中缩孔的下方。
三、影响缩孔和缩松形成的因素1、合金成分结晶温度范围越小的合金,产生缩孔的倾向越大;结晶温度范围越大的合金,产生缩松的倾向越大。
铁碳合金成分和体积收缩的关系V总—总体积收缩容积;V孔—缩孔容积;V松—缩松容积2、浇注条件提高浇注温度时,合金的总体积收缩和缩孔倾向增大。
浇注速度很慢或向冒口中不断补浇高温合金液,使铸件液态和凝固收缩及时得到补偿,铸件总体积收缩减小,缩孔容积也减小。
V 总—总体积收缩容积;V 孔—缩孔容积;V 松—缩松容积铁碳合金成分和体积收缩的关系3、铸型材料铸型材料对铸件冷却速度影响很大 。
焊接缩孔与缩松的影响因素与预防措施探析

焊接缩孔与缩松的影响因素与预防措施探析摘要:金属焊接过程中因其本身的物理特性,必然会产生焊接缩孔与缩松现象,对铸件的力学性能、气密性和物理化学性能有着较大的影响,严重影响了焊接质量。
基于此,笔者结合多年现场实际工作经验,详细分析了影响缩孔与缩松的因素,提出了防止途径,并从工艺角度提出了控制措施,以供参考。
关键词:焊接缩孔缩松影响因素预防措施引言金属在焊接过程中,因其本身的物理特性,必然会产生收缩现象。
而铸件在焊接凝固过程中,由于合金的液态收缩和凝固收缩,往往在其最后凝固的部位出现孔洞。
容积大而集中的孔洞称为缩孔,细小而分散的孔洞称为缩松。
前者常出现于纯金属、共晶成分合金和结晶温度范围较窄的铸造合金中,且多集中在铸件的上部和最后凝固的部位,以及铸件厚壁处、两壁相交处及内浇口附近等凝固较晚或凝固缓慢的部位(称为热节);后者多出现于结晶温度范围较宽的合金中,常分布在铸件壁的轴线区域、缩孔附近或铸件厚壁的中心部位。
铸件中存在的任何形态的缩孔和缩松,都会减小铸件的受力面积,在缩孔和缩松的尖角处产生应力集中,使铸件的力学性能显著降低。
此外,缩孔和缩松还会降低铸件的气密性和物理化学性能。
因此,必须采取有效措施予以防止。
2、影响缩孔与缩松的因素2.1影响缩孔与缩松大小的因素(1)金属的性质金属的液态收缩系数αV液和凝固收缩率εV凝越大,缩孔及缩松容积越大。
金属的固态收缩系数αV固越大,缩孔及缩松容积越小。
(2)铸型条件铸型的激冷能力越大,缩孔及缩松容积就越小。
因为铸型激冷能力越大,越易造成边浇注边凝固的条件,使金属的收缩在较大程度上被后注入的金属液所补充,使实际发生收缩的液态金属量减少。
(3)浇注条件浇注温度越高,金属的液态收缩越大,则缩孔容积越大;浇注速度越缓慢,浇注时间越长,缩孔容积就越小。
(4)铸件尺寸铸件壁厚越大,表面层凝固后,内部的金属液温度就越高,液态收缩就越大,则缩孔及缩松的容积越大。
(5)补缩压力凝固过程中增加补缩压力,可减少缩松而增加缩孔的容积。
浅谈铸件缩孔缩松产生的原因

浅谈铸件缩孔缩松产生的原因铸件缩孔和缩松是出现在铸件制造过程中的常见缺陷,对铸件的质量和性能产生重要影响。
缩孔和缩松的产生主要有以下几个原因:1.缩孔:缩孔是指铸件中出现内部凹陷或空洞的缺陷。
其主要原因如下:-铸型设计不合理:铸型的收缩系统设计不合理、浇注系统设计不合理、毛坯料和铸型之间的空隙设计不合理等,都会导致金属液在凝固过程中无法顺利填充,从而形成缩孔。
-浇注工艺参数不合理:包括浇注温度过低、浇注速度过快、浇注压力不足等。
这些因素都会影响金属液的流动性和凝固过程,从而产生缩孔。
-快速凝固导致温度梯度大:金属液凝固过程中温度梯度大,会加快金属的凝固速度,导致空洞无法充分填充,形成缩孔。
-毛坯料中夹杂物:毛坯料中的夹杂物如气孔、沙眼等也会导致铸件内部形成缩孔。
2.缩松:缩松是指铸件内部存在小裂纹或局部结构不致密的缺陷。
其主要原因如下:-热应力引起的冷裂纹:在铸造过程中,由于金属液凝固和收缩产生热应力,当应力超过金属的强度时,就会发生冷裂纹,形成缩松。
-毛坯中的气体和夹杂物:毛坯中存在气孔、气泡等夹杂物,会导致铸件内部产生局部脱实和裂纹,形成缩松。
-铸造温度过低:铸造温度过低会导致金属液在凝固过程中形成局部冷凝物,使得金属液无法顺利填充,产生缩松。
-浇注系统设计不合理:浇注系统设计不合理会导致金属液流动不畅,使得铸件内部无法顺利充实,形成缩松。
为防止铸造缺陷的产生,可以采取以下措施:-合理设计铸型:铸型的收缩系统设计要合理,保证金属液顺利充实,并通过改变浇注位置、浇注顺序等因素来减小缩松和缩孔的产生。
-优化浇注工艺参数:要根据具体的铸造材料和结构特点,合理控制浇注温度、浇注速度和浇注压力等参数,以减少缩松和缩孔的产生。
-毛坯清洁处理:在铸造前要对毛坯进行彻底清洁,以排除夹杂物和气泡等缺陷,减少铸件内部缺陷的产生。
-采用适当的热处理工艺:通过热处理来改善铸件内部组织结构,减少缩松和缩孔的产生,提高铸件的力学性能和耐热性能。
缩孔的原因和处理方法

缩孔的原因和处理方法
缩孔是指材料在加工过程中或使用过程中出现的体积缩小现象。
缩孔的原因主要有以下几点:
1. 气孔:材料中含有气体,在加工过程中未能充分排出,造成材料中出现气孔。
2. 晶粒收缩:材料在冷却过程中,晶粒会收缩,若冷却速度过快,则会出现晶粒收缩引起的缩孔。
3. 过度浇注:浇注过程中过度倾注造成气体较大的冲击,会在材料中形成缩孔。
4. 成分不合理:材料成分中某些元素的含量不合理,会引起材料中的相变,形成缩孔。
处理缩孔的方法主要有以下几种:
1. 提高熔体流动性:通过调整熔体的粘度和流动性,减少气体留存的可能性。
2. 控制冷却速度:过快的冷却速度会导致晶粒收缩,可以通过合理的控制冷却速度,使晶粒得到更充分的生长。
3. 控制浇注工艺:在浇注过程中,要控制倾注速度和浇注高度,以减少冲击和气体留存。
4. 优化材料成分:通过调整材料的成分,使其符合工艺要求,减少缩孔的发生。
5. 真空熔炼和真空浇注:通过在熔炼过程中使用真空技术,将气体从熔体中去除,避免缩孔的形成。
6. 加压熔炼和加压浇注:通过在熔炼和浇注过程中加压,可以将气体从熔体中排出,减少缩孔的发生。
7. 热处理:通过合理的热处理工艺,可以缩小材料中的缩孔,并改善材料的性能。
总之,处理缩孔主要是通过优化工艺参数、调整材料成分、采用加压、真空处理等方法来减少缩孔的形成。
球铁铸件缩孔、缩松的成因与防止
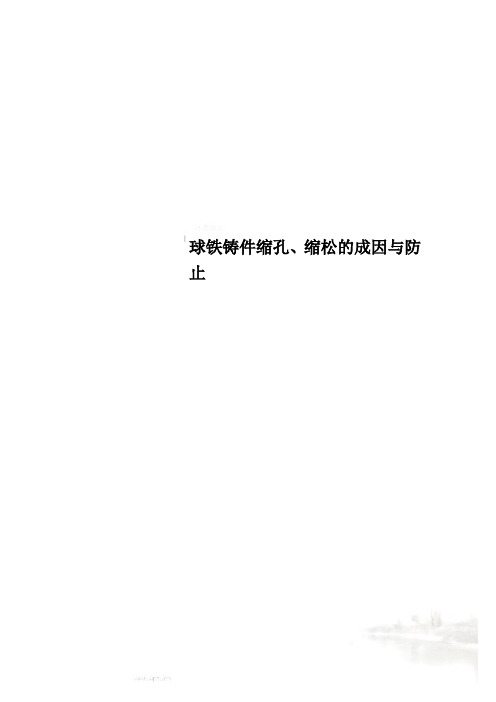
球铁铸件缩孔、缩松的成因与防止球铁铸件缩孔、缩松的成因与防止摘要:球墨铸铁大多数是共晶或过共晶成分,其糊状凝固方式使铸件外壳没有抵抗石墨化膨胀能力,因而铸型产生型壁迁移,增大铸件体积,极易产生内部缩孔、缩松。
球墨铸铁凝固时,在枝晶和共晶团间的最后凝固区域,收缩的体积得不到完全补充,留下的空洞形成宏观及微观缩松。
La 有助于消除缩松倾向。
分析缩孔缩松形成原因并提出相应的防止办法,有助于减少由此产生的废品损失。
关键词:球墨铸铁、收缩、缩孔、缩松1 前言1.1 缺陷形成原因球墨铸铁生产技术日臻完善,多年技术服务的实践表明,生产中出现的铸造缺陷,完全可以用成熟的经验予以消除。
据介绍:工业发达国家的铸造废品率可以控制在1%以下[1],国内先进水平也在2%左右,提高企业铸造技术水平,对减少废品十分重要。
1。
显微缩松显微镜观察微细连续缺失空间多角形疏松枝晶间、共晶团边界间众所周知,灰铸铁是逐层凝固方式,球墨铸铁是糊状凝固方式。
逐层凝固可以使铸件凝固时形成一个坚实的封闭外壳,铸件全封闭外壳的体积收缩可以减小壳体内的缩孔容积。
糊状凝固的特点是金属凝固时晶粒在金属液内部整个容积内形核、生长,固相与液相混合存在有如粥糊。
大多数球墨铸铁是共晶或过共晶成分,其糊状凝固方式使铸件外壳没有抵抗石墨化膨胀的能力,铸型产生型壁迁移,增大铸件体积,极易产生内部缩孔、缩松缺陷。
铸型冷却能力强,有利于铸件的容积凝固转变成逐层凝固,使铸件的分散缩松转变成集中缩孔。
然而,批量生产中湿砂型铸造很难被金属型或干砂型取代。
球墨铸铁凝固有以下三个特点,决定球墨铸铁是糊状凝固方式:①球化和孕育处理显著增加异质核心,核心存在于整个熔体,有利于全截面同时结晶。
②石墨球在奥氏体壳包围下生长,生长速度慢,延缓铸件表层形成坚实外壳;而片状石墨的端部始终与铁液接触,生长速度快,凝固时间短,促使灰铁铸件快速形成坚实外壳。
③球墨铸铁比灰铸铁导热率小 20%-30%,散热慢,外壳生长速度降低[3]。
铸件常见缺陷的产生原因及防止方法
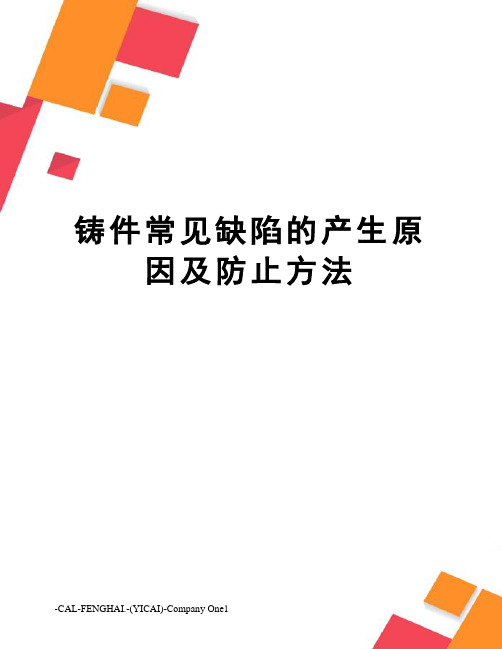
铸件常见缺陷的产生原因及防止方法-CAL-FENGHAI.-(YICAI)-Company One1铸件常见缺陷的产生原因及防止方法一、气孔(气泡、呛孔、气窝)特征:气孔是存在于铸件表面或内部的孔洞,呈圆形、椭圆形或不规则形,有时多个气孔组成一个气团,皮下一般呈梨形。
呛孔形状不规则,且表面粗糙,气窝是铸件表面凹进去一块,表面较平滑。
明孔外观检查就能发现,皮下气孔经机械加工后才能发现。
形成原因:1、模具预热温度太低,液体金属经过浇注系统时冷却太快。
2、模具排气设计不良,气体不能通畅排出。
3、涂料不好,本身排气性不佳,甚至本身挥发或分解出气体。
4、模具型腔表面有孔洞、凹坑,液体金属注入后孔洞、凹坑处气体迅速膨胀压缩液体金属,形成呛孔。
5、模具型腔表面锈蚀,且未清理干净。
6、原材料(砂芯)存放不当,使用前未经预热。
7、脱氧剂不佳,或用量不够或操作不当等。
防止方法:1、模具要充分预热,涂料(石墨)的粒度不宜太细,透气性要好。
2、使用倾斜浇注方式浇注。
3、原材料应存放在通风干燥处,使用时要预热。
4、选择脱氧效果较好的脱氧剂(镁)。
5、浇注温度不宜过高。
二、缩孔(缩松)特征:缩孔是铸件表面或内部存在的一种表面粗糙的孔,轻微缩孔是许多分散的小缩孔,即缩松,缩孔或缩松处晶粒粗大。
常发生在铸件内浇道附近、冒口根部、厚大部位,壁的厚薄转接处及具有大平面的厚薄处。
形成原因:1、模具工作温度控制未达到定向凝固要求。
2、涂料选择不当,不同部位涂料层厚度控制不好。
3、铸件在模具中的位置设计不当。
4、浇冒口设计未能达到起充分补缩的作用。
5、浇注温度过低或过高。
防治方法:1、提高磨具温度。
2、调整涂料层厚度,涂料喷洒要均匀,涂料脱落而补涂时不可形成局部涂料堆积现象。
3、对模具进行局部加热或用绝热材料局部保温。
4、热节处镶铜块,对局部进行激冷。
5、模具上设计散热片,或通过水等加速局部地区冷却速度,或在模具外喷水,喷雾。
6、用可拆缷激冷块,轮流安放在型腔内,避免连续生产时激冷块本身冷却不充分。
- 1、下载文档前请自行甄别文档内容的完整性,平台不提供额外的编辑、内容补充、找答案等附加服务。
- 2、"仅部分预览"的文档,不可在线预览部分如存在完整性等问题,可反馈申请退款(可完整预览的文档不适用该条件!)。
- 3、如文档侵犯您的权益,请联系客服反馈,我们会尽快为您处理(人工客服工作时间:9:00-18:30)。
缩孔、缩松的形成及防止方法
副教授:陈云
铸件中的缩孔与缩松
液态金属在铸型内凝固过程中,由于液态收缩和凝固收缩导致体积缩小,若其收缩得不到补充,就在铸件最后凝固的部分形成孔洞。
大而集中的孔洞称为缩孔,细小而分散的孔洞称为缩松。
(a)铝合金缩孔、缩松(b)金相显微镜下缩松(c)扫描电镜下缩松
一、缩孔的形成
纯金属、共晶成分和凝固温度范围窄的合金,浇注后在型腔内是由表及里的逐层凝固。
在凝固过程中,如得不到合金液的补充,在铸件最后凝固的地方就会产生缩孔。
缩孔形成的条件:铸件呈逐层凝固方式凝固,成分为纯金属或共晶成分的
合金。
缩孔产生的基本原因:是合金的液态收缩和凝固收缩值大于固态收缩值,且得不到补偿。
缩孔产生的部位在铸件最后凝固区域,如壁较厚大的上部或铸件两壁相交处,这些地方称为热节。
热节位置可用画内接圆的方法确定。
用画内切圆法确定缩孔位置
二、缩松的形成
铸件最后凝固的收缩未能得到补充,或者结晶温度范围宽的合金呈糊状凝固,凝固区域较宽,液、固两相共存,树枝晶发达,枝晶骨架将合金液分割开的小液体区难以得到补缩所致。
缩松形成的条件:铸件主要呈糊状凝固方式凝固,成分为非共晶成分或有较宽结晶温度范围的合金。
形成缩松的基本原因:是合金的液态收缩和凝固收缩值大于固态收缩值。
缩松一般出现在铸件壁的轴线区域、冒口根部、热节处,也常分布在集中缩孔的下方。
三、影响缩孔和缩松形成的因素
1、合金成分
结晶温度范围越小的合金,产
生缩孔的倾向越大;结晶温度范围
越大的合金,产生缩松的倾向越大。
铁碳合金成分和体积收缩的关系
V总—总体积收缩容积;V孔—缩孔容积;V松—缩松容积
2、浇注条件
提高浇注温度时,合金的总体积收缩和缩
孔倾向增大。
浇注速度很慢或向冒口中不断补浇高温合
金液,使铸件液态和凝固收缩及时得到补偿,
铸件总体积收缩减小,缩孔容积也减小。
V 总—总体积收缩容积;V 孔—缩孔容积;V 松—缩松容积
铁碳合金成分和体积收缩的关系
3、铸型材料
铸型材料对铸件冷却速度影响很大 。
湿型比干型的冷却能力大,使凝固区域
变窄,缩松减少。
金属型的冷却能力更大,
故缩松更显著减少。
四、缩孔和缩松的防止方法
缩孔和缩松都使铸件的力学性能下降,缩松还可使铸件因渗漏而报废。
因此,必须根据技术要求,采取适当的工艺措施予以防止。
1、控制铸件的凝固过程
实践证明,只要能使铸件实现“顺序凝固”(定
向凝固)或“同时凝固”,尽管合金的收缩较大,也
可获得没有缩孔的致密铸件。
“顺序凝固”原则是让铸件远离冒口的地方先凝
固,靠近冒口的地方次凝固,最后才是冒口本身凝
固,实现以厚补薄,将缩孔转移到冒口中去。
“顺序凝固”适用于收缩大或壁厚差别较大,易产生缩孔的合金铸件,如铸钢、高强度灰口铸铁和可锻铸铁等。
“同时凝固”原则,就是从工艺上采取必要
的措施,使铸件各部分的冷却速度尽量相等,以达
到铸件各部分几乎同时凝固完结。
“同时凝固”原则,适用于碳、硅含量较高
的灰口铸铁和球墨铸铁。
采用“顺序凝固”时,尽管冒口补缩作用好,但冷却速度不一致,易产生铸造应力、变形及裂纹等缺陷;冒口消耗金属多,降低了铸件的出品率,并且,冒口切割较为困难。
采用“同时凝固”时,铸件出现裂纹、应力和变形的倾向性小,不必设置冒口,使工艺简化,又能节省金属材料,而且,提高了铸造的出品率。
2、合理应用冒口、冷铁等工艺措施
冒口一般设置在铸件厚壁处和热节部位,是防止缩孔、缩松最有效的措施,冒口的尺寸应保证冒口比铸件补缩部位凝固得晚,并有足够的金属液供给。
冷铁通常是用铸铁、钢和铜等金属材料制成
的激冷物。
放入铸型内,用以加大铸件某一部分
的冷却速度,调节铸件的凝固顺序。
阀体铸件的冒口和冷铁位置
1—浇口;2—明冒口;3—暗冒口(或边冒口);4—冷铁
谢谢观看。