【材料成型原理--铸造】第14章 缩孔与缩松
铸件缩孔缩松产生的原因

铸件缩孔缩松产生的原因
一、金属铸件缩孔缩松的原因
1、模具质量不合格:模具的表面没有经过预处理,工作表面毛糙度不够,加工精度不高,导致熔模渗入的位置不正确,从而影响铸件缩孔的精度。
2、砂芯质量不合格没有经过预处理或抛光处理,表面毛糙度不均,加工精度低,砂芯内部出现裂纹,导致不同部位的造型不稳定,从而影响铸件缩孔的精度。
3、工艺条件不合理:模具配套不当,熔模温度过高或过低,模具保温不足,充型压力不足,熔模渗入缓慢,从而影响铸件缩孔的精度。
4、冷却不当:铸件出模后,冷却时间过长或过短,容易出现开裂现象,从而影响铸件缩孔的精度。
二、金属铸件缩孔缩松的改善措施
1、严格模具质量:采用高强度的整体钢,并且经过精密加工,表面经过研磨抛光,以保证熔模渗入的位置准确,从而提高铸件缩孔的精度。
2、严格砂芯质量:采用高质量的砂芯,经过彻底的预处理,能够保证砂芯表面毛糙度均匀,加工精度高,避免出现裂纹,从而确保缩孔的精度。
3、调整熔模温度:严格控制熔模的温度,熔模温度过高可以导致金属分子值过大,熔态液体容易流失。
铸钢件缩孔和缩松的形成与预防

F铸造oundry热加工热处理/锻压/铸造2011年第15期69铸钢件缩孔和缩松的形成与预防宁夏天地奔牛实业集团有限公司(石嘴山753001)王福京缩孔和缩松从本质上来说,是因为型内的金属产生收缩而引起的,但是不同种类的金属,其形成缩孔和缩松的机理有所不同。
1.产生机理从铸钢件角度来分析,钢液注满型腔后,由于型壁的传热作用,型内钢液形成自型壁表面至铸件壁厚中心温度逐渐升高的温度梯度。
随着型壁传热作用不断地进行,型内钢液温度不断降低。
当与型壁表面接触的钢液温度降至凝固温度时,铸件的表面就开始凝固,并形成一层固体状态的硬壳。
如果这时浇注系统已经凝固,那么硬壳内处于液体状态的钢液就与外界隔绝。
当型内钢液温度进一步降低时,硬壳内的钢液一方面因温度降低而产生液态收缩,另一方面由于硬壳的传热作用,使与硬壳接触的钢液不断结晶凝固,从而出现凝固收缩。
这两种收缩的出现,将使硬壳内钢液液面下降。
与此同时,处于固体状态的硬壳,也因温度的降低而产生固态收缩,对于铸钢件来说,由于液态收缩和凝固收缩的总和是大于固态收缩的,因此在重力作用下,硬壳内钢液液面将下降,并且与上部硬壳脱离接触。
随着型内钢液温度不断地降低和硬壳内钢液不断地凝固,硬壳越来越厚,而钢液越来越少。
当铸件内最后的钢液凝固后,铸件上部的硬壳下面就会出现一个孔洞,这个孔洞即为缩孔。
虽然凝固后的铸件自高温状态冷却至室温时,还将产生固态收缩,从而使整个铸件和其内部缩孔的体积稍有减小,但并不会改变缩孔体积与铸件体积的比值。
由于凝固层厚度的增加和钢液的减少是不断进行的,因而从理论上来说,缩孔的形状是漏斗状的。
并且因残存的钢液凝固时不能得到补缩,所以在产生缩孔的同时,往往也伴随着缩松的出现。
用肉眼能直接观察到的缩孔为宏观缩孔,而借助于放大镜或将断面腐蚀以后才能发现的缩孔为微观缩孔。
一般情况下,宏观缩孔可以用补焊的手段来解决,而微观缩孔就无法处理了,一般都是成片出现的微小孔洞。
铸件缩孔、缩松有何区别?如何解决?

铸件缩孔、缩松有何区别?如何解决?在铸造生产中,铸件气孔和铸件缩孔有时是伴生的,有时是独立存在。
当出现气孔和缩孔时,我们要快速的判断出缺陷是气孔还是缩孔对于解决问题十分必要。
气孔类缺陷与防治方法在铸造生产中,孔洞类缺陷是常见缺陷,也是给铸造厂造成损失比较大的缺陷之一。
孔洞类缺陷分为气孔和缩孔。
气孔多为由于金属液中侵入、裹入、卷入气体所至。
铸件气孔出现在铸件上的位置不同,其产生的原因也不同。
这就要求我们的铸造技术员在判断气孔缺陷病因时,要掌握各类气孔发生的原理,具有什么样的特征。
只有如此才能对症下药,将出现的气孔缺陷解决掉。
气孔特征:(1)卷入气孔:金属液在充型过程中因卷入气体而在铸件内形成气孔,多呈孤立存在的圆形或椭圆形大气孔,位置不固定,一般偏铸件中上部。
(2)侵入气孔:由型、芯、涂料、芯撑、冷铁产生的气孔侵入铸件表层而形成气孔,多呈梨形或椭圆形,尺寸较大,孔壁光滑,表面多呈氧化色。
(3)反应气孔:由金属液内部某些成分之间或金属液与型、芯在界面上发生化学反应而形成群分布的气孔。
位于铸件表层的针头形或腰圆形反应气孔称为表面针孔与皮下气孔,由金属液与型、芯涂料发生界面反应所至;分散或成群分布在铸件整个断面上或某个局部区域的针头反应气孔。
形成原因:(1)由于炉料潮湿、锈蚀、油污、气候的潮湿,熔练工具和浇包未烘干,金属液成分不当,合金液为精炼与精炼不足,使金属液中含有大量气体或气体物质,导致在铸件中析出气孔或反应气孔。
(2)型、芯未充分烘干,透气性差,通气不良,含水分和发气物质过多,涂料未烘干或含发气成分过多,冷铁、芯撑有锈斑、油污或未烘干,金属型排气不良,在铸件中形成侵入气孔。
(3)浇注系统不合理,浇注和充型速度过快,金属型排气不良,使金属液在浇注和充型过程中产生紊流、涡流或断流而卷入气体,在铸件中形成卷入性气孔。
(4)合金液易可吸气,在熔炼和浇注过程中未采取有效的精炼、保护和净化措施,使金属液中含有大量气体、夹渣和夹气成分,在充型和凝固过程中形成析出气孔和反应气孔。
铸钢缩孔和缩松产生的原因及预防措施!
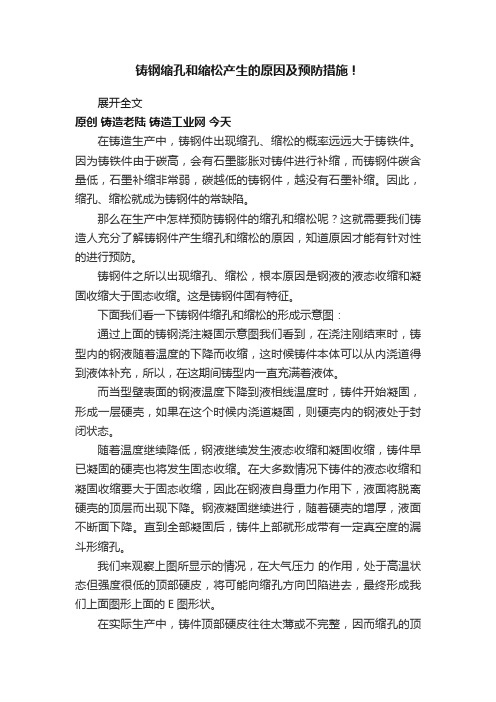
铸钢缩孔和缩松产生的原因及预防措施!展开全文原创铸造老陆铸造工业网今天在铸造生产中,铸钢件出现缩孔、缩松的概率远远大于铸铁件。
因为铸铁件由于碳高,会有石墨膨胀对铸件进行补缩,而铸钢件碳含量低,石墨补缩非常弱,碳越低的铸钢件,越没有石墨补缩。
因此,缩孔、缩松就成为铸钢件的常缺陷。
那么在生产中怎样预防铸钢件的缩孔和缩松呢?这就需要我们铸造人充分了解铸钢件产生缩孔和缩松的原因,知道原因才能有针对性的进行预防。
铸钢件之所以出现缩孔、缩松,根本原因是钢液的液态收缩和凝固收缩大于固态收缩。
这是铸钢件固有特征。
下面我们看一下铸钢件缩孔和缩松的形成示意图:通过上面的铸钢浇注凝固示意图我们看到,在浇注刚结束时,铸型内的钢液随着温度的下降而收缩,这时候铸件本体可以从内浇道得到液体补充,所以,在这期间铸型内一直充满着液体。
而当型壁表面的钢液温度下降到液相线温度时,铸件开始凝固,形成一层硬壳,如果在这个时候内浇道凝固,则硬壳内的钢液处于封闭状态。
随着温度继续降低,钢液继续发生液态收缩和凝固收缩,铸件早已凝固的硬壳也将发生固态收缩。
在大多数情况下铸件的液态收缩和凝固收缩要大于固态收缩,因此在钢液自身重力作用下,液面将脱离硬壳的顶层而出现下降。
钢液凝固继续进行,随着硬壳的增厚,液面不断面下降。
直到全部凝固后,铸件上部就形成带有一定真空度的漏斗形缩孔。
我们来观察上图所显示的情况,在大气压力的作用,处于高温状态但强度很低的顶部硬皮,将可能向缩孔方向凹陷进去,最终形成我们上面图形上面的E图形状。
在实际生产中,铸件顶部硬皮往往太薄或不完整,因而缩孔的顶部通常和能大气相通。
铸件凝固后期,在其最后凝固部分的残余钢液中,由于温度梯度小,金属液将同时凝固,即在钢液中出现许多细小的晶粒,当晶粒长大互相连接后,将剩余的钢液分割成互不相通的小熔池。
这些小熔池在进一步冷却和凝固时得不到液体的补缩,会产生许多细小的孔洞,这就是缩松。
缩松按糨的分布情况一般分为三种:一、弥散缩松,这种缩松是指细小的孔洞均匀分布在铸件的大部分体积内,易在结晶温度范围宽的合金铸件的冷却缓慢的厚大部位处产生。
铸铁件缩松、缩孔、凹陷缺陷的原因分析与防止方法
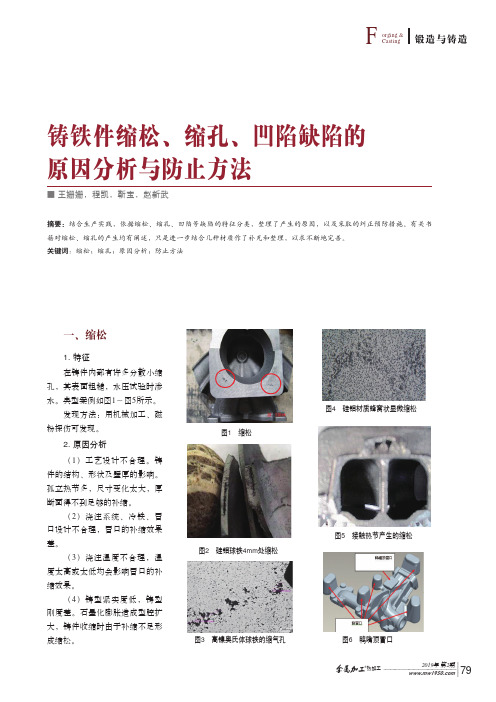
2019年第2期热加工79F锻造与铸造orging &Casting铸铁件缩松、缩孔、凹陷缺陷的原因分析与防止方法■王姗姗,程凯,靳宝,赵新武摘要:结合生产实践,依据缩松、缩孔、凹陷等缺陷的特征分类,整理了产生的原因,以及采取的纠正预防措施。
有关书籍对缩松、缩孔的产生均有阐述,只是进一步结合几种材质作了补充和整理,以求不断地完善。
关键词:缩松;缩孔;原因分析;防止方法一、缩松1. 特征在铸件内部有许多分散小缩孔,其表面粗糙,水压试验时渗水。
典型案例如图1~图5所示。
发现方法:用机械加工、磁粉探伤可发现。
2. 原因分析(1)工艺设计不合理。
铸件的结构、形状及壁厚的影响。
孤立热节多,尺寸变化太大,厚断面得不到足够的补缩。
(2)浇注系统、冷铁、冒口设计不合理,冒口的补缩效果差。
(3)浇注温度不合理,温度太高或太低均会影响冒口的补缩效果。
(4)铸型紧实度低,铸型刚度差。
石墨化膨胀造成型腔扩大,铸件收缩时由于补缩不足形成缩松。
图1 缩松图2 硅钼球铁4mm处缩松图4 硅钼材质蜂窝状显微缩松图3 高镍奥氏体球铁的缩气孔图5 接触热节产生的缩松图6 鸭嘴顶冒口2019年 第2期 热加工80F锻造与铸造orging &Casting(5)碳、硅含量低,磷含量较高;凝固区间大。
硅钼和高镍球墨铸铁对碳、硅含量和氧化铁液的敏感性特大,铁液严重氧化或碳、硅量低时,易出现显微缩松。
即便在薄壁处也容易出现缩松(见图2、图3、图4)。
(6)孕育不充分,石墨化效果差。
(7)残余镁量和稀土量过高。
钼含量较高时也会增加显微缩松。
(8)浇注速度太快。
(9)炉料锈蚀,氧化铁多。
(10)铁液在电炉内高温停放时间太长,俗称“死铁水”,造成严重氧化。
(11)冲天炉熔炼时底焦太底,风量太大,元素烧损大,铁液严重氧化。
(12)冒口径处形成接触热节产生缩松(见图5)。
(13)压箱铁不够(或箱卡未锁紧,箱带断裂等),浇注后由于涨箱造成缩松。
缩孔与缩松

缩孔与缩松缩孔缩松机械114硕陈聪概述· 缩孔和缩松是熔模铸件常见缺陷之一。
熔模铸件的生产特点是当灼热的钢液浇注到高温的型壳中,铸件从冷却凝固直到冷至室温,将产生三种收缩,即液态收缩、凝固收缩和固态收缩。
这是合金重要的铸造性能之一。
其液态收缩和凝固收缩决定了铸件在最后凝固的地方产生缩孔和缩松的大小与分布,固态收缩使铸件产生残余应力,可能引起变形,甚至裂纹。
缩孔的孔洞。
一是什么?· 定义:液态金属凝固过程中由于体积收缩所形成· 特征:分布特征为集中缩孔,缩孔形状不规则,表面粗糙,产生在铸件热节和最后凝固部位,常伴有粗大树枝晶、夹杂物、气孔、裂纹、偏析等缺陷。
· 鉴别方法:铸件内部的缩孔,一般采用超声探伤或射线探伤法进行检验。
敞露在铸件表面的缩孔用肉眼即可确定。
表面有缩陷、胀型、缩沉等缺陷的铸件,内部往往有缩孔缺陷。
缩松是什么· 定义:缩松是指铸件最后凝固的区域没有得到液态金属或合金的补缩形成分散和细小的缩孔。
· 特征:常分散在铸件壁厚的轴线区域、厚大部位、冒口根部和内浇口附近。
当缩松与缩孔容积相同时,缩松的分布面积要比缩孔大得多。
缩松隐藏于铸件的内部,外观上不易被发现。
二产生部位· (1)缩孔产生的部位:缩孔产生在铸件最后凝固并且得不到充分补缩的部位,它常产生在铸件的热节处。
因为它产生的部位还与内浇口在铸件上开设的部位、铸件上各部分不同的散热条件、浇注系统对铸件散热的影响以及同一模组上各铸件之间相互位置对散热的影响等因素都有关。
可以用画凝固等温线或画内切圆法估计缩孔的部位,也可以解剖铸件,确定铸件是否产生缩孔及其部位。
产生部位· (2)缩松产生的部位:缩松总是产生在铸件上冷却相对缓慢的部位,如铸件的热节处、壁的转接R 处、距离很近的夹壁处、内浇口附近或紧挨缩孔的下面。
三如何产生缩孔的形成过程如图所示,a液态合金填满铸型后,b因铸型吸热,靠近型腔表面的金属很快就降到凝固温度,凝固成一层外壳,c 随着温度的降低,外壳逐渐加厚,由于液态收缩和凝固收缩造成的体收缩大于已凝固外壳的固态收缩,所以,在重力的作用下,液体与顶面脱开,逐渐下降,出现了较大的空洞。
铸造金属凝固原理第-缩孔与缩

用不同刚性铸型浇注的球墨铸铁试样比较
14.3 防止铸件产生缩孔和缩松的途径
1 合适的凝固原则:顺序凝固和同时凝固 1 针对该合金的收缩和凝固特点制定正确的铸造工艺原
则,使铸件在凝固过程中建立良好的补缩条件,尽可 能地使缩松转化为缩孔,并使缩孔出现在铸件最后凝 固的地方。这样,在铸件最后凝固的地方安置一定尺 寸的冒口,使缩孔集中于冒口中,或者把浇口开在最 后凝固的地方直接补缩,即可获得健全的铸件。
③ 固态收缩 • 特点 • 在固态收缩阶段,铸件各个方向上都表现出线尺寸的缩小。
因此,这阶段对铸件的形状和尺寸的精度影响最大。
线收缩是铸件中产生应力、变形和裂纹的基本原因。
εV固 =αV固(TS -T0) ×100%
εL =αL (TS -T0) ×100%
④ 线收缩的开始温度 • 纯金属和共晶合金:在金属完全凝固以后开始 • 具有一定结晶温度范围的合金:枝晶数量增多,彼此相连
高碳硅含量灰铸铁 产生缩松合金,简化工艺 壁厚均匀薄件 球铁自补缩时 当应力、裂纹、变形成主要矛盾时。 — 复合凝固原则
③ 实现顺序凝固原则或同时凝固原则的工艺措施: — 正确布置浇注系统的引入位置,确定合理的浇注工艺; — 采用冒口; — 采用补贴; — 采用不同蓄热系数的造型材料或冷铁。
2 浇注系统的引入位置及浇注工艺 ① 浇注系统的引入位置 浇注系统的引入位置与铸件纵向温度分布的关系
构成连续的骨架,合金则开始表现为固态的性质,即开始 线收缩。
⑤ 线收缩与状态图的关系
2 铸钢的收缩
① 液态收缩
特点
εV液 =αV液 (T浇 -TL ) ×100%
提高含C量,TL下降,(T浇 – TL)提高,并且收缩系数αV液提
高(每增加1%C, α增V液大20%) ,故钢液收缩率提高。
铸钢件缩孔和缩松的形成与预防

F铸造oundry热加工热处理/锻压/铸造2011年第15期69铸钢件缩孔和缩松的形成与预防宁夏天地奔牛实业集团有限公司(石嘴山753001)王福京缩孔和缩松从本质上来说,是因为型内的金属产生收缩而引起的,但是不同种类的金属,其形成缩孔和缩松的机理有所不同。
1.产生机理从铸钢件角度来分析,钢液注满型腔后,由于型壁的传热作用,型内钢液形成自型壁表面至铸件壁厚中心温度逐渐升高的温度梯度。
随着型壁传热作用不断地进行,型内钢液温度不断降低。
当与型壁表面接触的钢液温度降至凝固温度时,铸件的表面就开始凝固,并形成一层固体状态的硬壳。
如果这时浇注系统已经凝固,那么硬壳内处于液体状态的钢液就与外界隔绝。
当型内钢液温度进一步降低时,硬壳内的钢液一方面因温度降低而产生液态收缩,另一方面由于硬壳的传热作用,使与硬壳接触的钢液不断结晶凝固,从而出现凝固收缩。
这两种收缩的出现,将使硬壳内钢液液面下降。
与此同时,处于固体状态的硬壳,也因温度的降低而产生固态收缩,对于铸钢件来说,由于液态收缩和凝固收缩的总和是大于固态收缩的,因此在重力作用下,硬壳内钢液液面将下降,并且与上部硬壳脱离接触。
随着型内钢液温度不断地降低和硬壳内钢液不断地凝固,硬壳越来越厚,而钢液越来越少。
当铸件内最后的钢液凝固后,铸件上部的硬壳下面就会出现一个孔洞,这个孔洞即为缩孔。
虽然凝固后的铸件自高温状态冷却至室温时,还将产生固态收缩,从而使整个铸件和其内部缩孔的体积稍有减小,但并不会改变缩孔体积与铸件体积的比值。
由于凝固层厚度的增加和钢液的减少是不断进行的,因而从理论上来说,缩孔的形状是漏斗状的。
并且因残存的钢液凝固时不能得到补缩,所以在产生缩孔的同时,往往也伴随着缩松的出现。
用肉眼能直接观察到的缩孔为宏观缩孔,而借助于放大镜或将断面腐蚀以后才能发现的缩孔为微观缩孔。
一般情况下,宏观缩孔可以用补焊的手段来解决,而微观缩孔就无法处理了,一般都是成片出现的微小孔洞。
铸件产生缩孔和缩松产生的原因及防止措施(音频讲解,实用方便)

铸件产⽣缩孔和缩松产⽣的原因及防⽌措施(⾳频讲解,实⽤⽅便)铸件缩松、缩孔问题防治⽅案来⾃制造⼯业联盟 00:00 10:29
缩孔是集中在铸件上部或最后凝固部位容积较⼤的孔洞
合⾦的液态收缩和凝固收缩愈⼤、浇注温度愈⾼、铸件愈厚,缩孔的容积愈⼤. 缩松是分
散在铸件某区域内的细⼩缩孔
形成原因:铸件最后凝固区域的收缩未能得到补⾜,或因为合⾦呈糊状凝固,被树枝状晶体
分隔开的⼩液体区难以得到补缩所⾄
逐层凝固合⾦,缩松倾向⼩。
糊状凝固合⾦缩松倾向⼤,缩孔倾向⼩。
防⽌缩孔和缩松的措施 1)选择合适的合⾦成分选⽤近共晶成分或结晶温度范围较
窄的合⾦ 2)⼯艺措施顺序凝固原则,获得没有缩孔的致密铸件。
定向凝固就是在铸
件上可能出现缩孔的厚⼤部位通过安放冒⼝等⼯艺措施,使铸件远离冒⼝的部位先凝固,然后
靠近冒⼝部位凝固,最后冒⼝本⾝凝固。
⽬的是铸件各个部位的收缩都能得到补充,⽽将缩孔转移到冒⼝中,最后予以清除措施
1、安放冒⼝
2、在⼯件厚⼤部位增设冷铁。
铸钢件缩孔及缩松缺陷的消除

铸钢件缩孔及缩松缺陷的消除【摘要】通过分析铸钢件缩孔及缩松产生的机理,总结出铸件产生缩孔及缩松缺陷的部位,提出从改进浇注系统、改变铸件结构、适当提高浇注温度及控制浇注速度等几个方面消除铸件中的缩孔及缩松。
缩孔及缩松缺陷是铸钢件生产中的一大难题,长期以来困扰着广大铸造工作者。
这两种缺陷多发生在铸件内部,通过机械加工或X 射线检查可以发现,要进行挽救比较困难,也有发生在表面上的,通过安放冒口可以消除。
这两种缺陷很相似,危害都很大,可以归为一类。
由于缩孔及缩松缺陷的消除需要综合考虑浇注系统、浇注温度、铸件结构、冒口及冷铁等工艺因素,在实际生产中难以控制。
本文拟对铸钢件生产中出现的缩孔、缩松缺陷的消除作一探讨,供有关人员参考。
一、缩孔及缩松缺陷产生的机理铁液在铸型内冷凝的过程中,体积要发生三次收缩:第一次是合金液从浇注温度冷却到开始凝固的温度,称为液态收缩; 第二次是从开始凝固的温度冷却到金属液全部凝固的温度,称为凝固收缩; 第三次是从全部凝固的温度冷却到室温,称为固态收缩。
液态收缩的大小与浇注温度有关,铁液每降低100 ℃,体积约缩小0. 78 % ~1. 2 % ,因此浇注温度越高,液态收缩越大。
一般情况下,在能保证流动性的前提下,应尽量降低铁液的浇注温度。
液态及凝固收缩受合金成分的影响较大,比如,在其他成分相同的情况下,碳、硅含量越大,收缩就越小; 而锰、硫含量越多,则收缩量越大。
一般铸钢件在凝固收缩阶段的线收缩率为2.0 % ~3. 5 % ,因此在砂型铸造中制造模样时,除了加放一定的加工余量外,还要按铸造合金的收缩特性,加上一定量的合金收缩率。
当金属液进入型腔后,靠近型壁的金属液散热快,冷却速度快,而后向铸件中心逐次凝固。
铸件在冷却凝固的过程中,一般液态收缩时可以得到浇包中液态金属的补缩,这个阶段的收缩对铸件质量影响不大; 固态收缩对形成缩孔、缩松缺陷的影响也不大,但如果在凝固收缩时得不到补缩,就会在铸件最后凝固的部位( 如温度最高的中心处) 形成细小或分散的孔洞,即缩孔、缩松缺陷。
铸件缩孔、缩松产生的原因
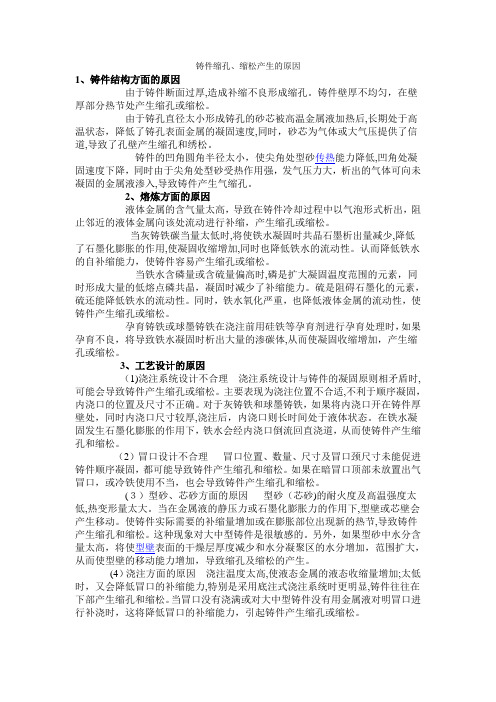
铸件缩孔、缩松产生的原因1、铸件结构方面的原因由于铸件断面过厚,造成补缩不良形成缩孔。
铸件壁厚不均匀,在壁厚部分热节处产生缩孔或缩松。
由于铸孔直径太小形成铸孔的砂芯被高温金属液加热后,长期处于高温状态,降低了铸孔表面金属的凝固速度,同时,砂芯为气体或大气压提供了信道,导致了孔壁产生缩孔和绣松。
铸件的凹角圆角半径太小,使尖角处型砂传热能力降低,凹角处凝固速度下降,同时由于尖角处型砂受热作用强,发气压力大,析出的气体可向未凝固的金属液渗入,导致铸件产生气缩孔。
2、熔炼方面的原因液体金属的含气量太高,导致在铸件冷却过程中以气泡形式析出,阻止邻近的液体金属向该处流动进行补缩,产生缩孔或缩松。
当灰铸铁碳当量太低时,将使铁水凝固时共晶石墨析出量减少,降低了石墨化膨胀的作用,使凝固收缩增加,同时也降低铁水的流动性。
认而降低铁水的自补缩能力,使铸件容易产生缩孔或缩松。
当铁水含磷量或含硫量偏高时,磷是扩大凝固温度范围的元素,同时形成大量的低熔点磷共晶,凝固时减少了补缩能力。
硫是阻碍石墨化的元素,硫还能降低铁水的流动性。
同时,铁水氧化严重,也降低液体金属的流动性,使铸件产生缩孔或缩松。
孕育铸铁或球墨铸铁在浇注前用硅铁等孕育剂进行孕育处理时,如果孕育不良,将导致铁水凝固时析出大量的渗碳体,从而使凝固收缩增加,产生缩孔或缩松。
3、工艺设计的原因(1)浇注系统设计不合理浇注系统设计与铸件的凝固原则相矛盾时,可能会导致铸件产生缩孔或缩松。
主要表现为浇注位置不合适,不利于顺序凝固,内浇口的位置及尺寸不正确。
对于灰铸铁和球墨铸铁,如果将内浇口开在铸件厚壁处,同时内浇口尺寸较厚,浇注后,内浇口则长时间处于液体状态。
在铁水凝固发生石墨化膨胀的作用下,铁水会经内浇口倒流回直浇道,从而使铸件产生缩孔和缩松。
(2)冒口设计不合理冒口位置、数量、尺寸及冒口颈尺寸未能促进铸件顺序凝固,都可能导致铸件产生缩孔和缩松。
如果在暗冒口顶部未放置出气冒口,或冷铁使用不当,也会导致铸件产生缩孔和缩松。
铸件缩孔和缩松缺陷,十点分析
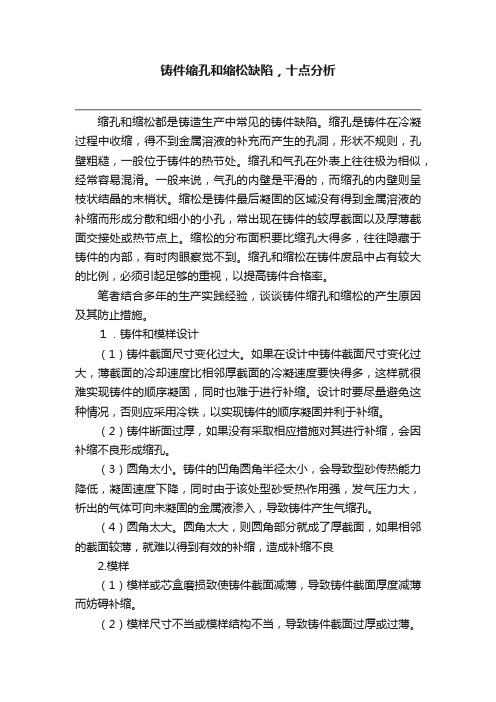
铸件缩孔和缩松缺陷,十点分析缩孔和缩松都是铸造生产中常见的铸件缺陷。
缩孔是铸件在冷凝过程中收缩,得不到金属溶液的补充而产生的孔洞,形状不规则,孔壁粗糙,一般位于铸件的热节处。
缩孔和气孔在外表上往往极为相似,经常容易混淆。
一般来说,气孔的内壁是平滑的,而缩孔的内壁则呈枝状结晶的末梢状。
缩松是铸件最后凝固的区域没有得到金属溶液的补缩而形成分散和细小的小孔,常出现在铸件的较厚截面以及厚薄截面交接处或热节点上。
缩松的分布面积要比缩孔大得多,往往隐藏于铸件的内部,有时肉眼察觉不到。
缩孔和缩松在铸件废品中占有较大的比例,必须引起足够的重视,以提高铸件合格率。
笔者结合多年的生产实践经验,谈谈铸件缩孔和缩松的产生原因及其防止措施。
1.铸件和模样设计(1)铸件截面尺寸变化过大。
如果在设计中铸件截面尺寸变化过大,薄截面的冷却速度比相邻厚截面的冷凝速度要快得多,这样就很难实现铸件的顺序凝固,同时也难于进行补缩。
设计时要尽量避免这种情况,否则应采用冷铁,以实现铸件的顺序凝固并利于补缩。
(2)铸件断面过厚,如果没有采取相应措施对其进行补缩,会因补缩不良形成缩孔。
(3)圆角太小。
铸件的凹角圆角半径太小,会导致型砂传热能力降低,凝固速度下降,同时由于该处型砂受热作用强,发气压力大,析出的气体可向未凝固的金属液渗入,导致铸件产生气缩孔。
(4)圆角太大。
圆角太大,则圆角部分就成了厚截面,如果相邻的截面较薄,就难以得到有效的补缩,造成补缩不良2.模样(1)模样或芯盒磨损致使铸件截面减薄,导致铸件截面厚度减薄而妨碍补缩。
(2)模样尺寸不当或模样结构不当,导致铸件截面过厚或过薄。
设计时应注意控制模样的厚度,尽量使邻近较厚截面的薄截面保持最大的厚度。
3.砂箱(1)上箱太浅。
生产中为了节省型砂用量或为了降低砂箱和造型成本而使用高度不够的上箱,这是造成缩松缺陷的常见原因。
上箱太浅,会降低金属液的静压力,以致难以进行补缩,补缩压力不够,会导致产生缩松或缩孔,或二者兼有之。
液态收缩和凝固收缩是铸件产生缩孔和缩松的基本原因
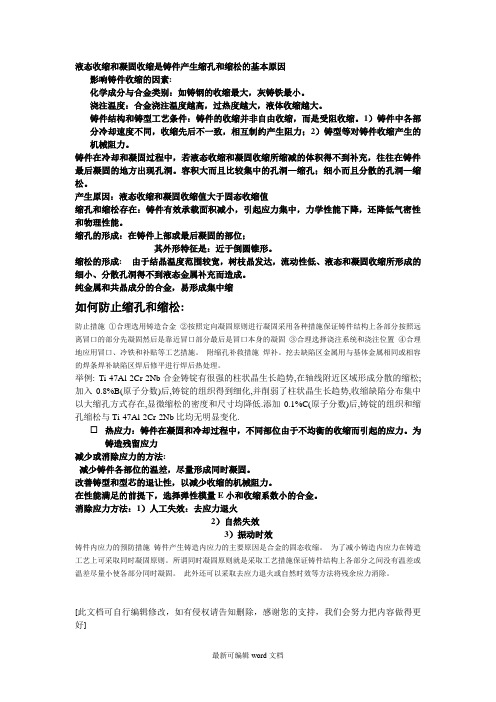
液态收缩和凝固收缩是铸件产生缩孔和缩松的基本原因影响铸件收缩的因素:化学成分与合金类别:如铸钢的收缩最大,灰铸铁最小。
浇注温度:合金浇注温度越高,过热度越大,液体收缩越大。
铸件结构和铸型工艺条件:铸件的收缩并非自由收缩,而是受阻收缩。
1)铸件中各部分冷却速度不同,收缩先后不一致,相互制约产生阻力;2)铸型等对铸件收缩产生的机械阻力。
铸件在冷却和凝固过程中,若液态收缩和凝固收缩所缩减的体积得不到补充,往往在铸件最后凝固的地方出现孔洞。
容积大而且比较集中的孔洞—缩孔;细小而且分散的孔洞—缩松。
产生原因:液态收缩和凝固收缩值大于固态收缩值缩孔和缩松存在:铸件有效承载面积减小,引起应力集中,力学性能下降,还降低气密性和物理性能。
缩孔的形成:在铸件上部或最后凝固的部位;其外形特征是:近于倒圆锥形。
缩松的形成:由于结晶温度范围较宽,树枝晶发达,流动性低、液态和凝固收缩所形成的细小、分散孔洞得不到液态金属补充而造成。
纯金属和共晶成分的合金,易形成集中缩如何防止缩孔和缩松:防止措施①合理选用铸造合金②按照定向凝固原则进行凝固采用各种措施保证铸件结构上各部分按照远离冒口的部分先凝固然后是靠近冒口部分最后是冒口本身的凝固③合理选择浇注系统和浇注位置④合理地应用冒口、冷铁和补贴等工艺措施。
附缩孔补救措施焊补。
挖去缺陷区金属用与基体金属相同或相容的焊条焊补缺陷区焊后修平进行焊后热处理。
举例: Ti-47Al-2Cr-2Nb合金铸锭有很强的柱状晶生长趋势,在轴线附近区域形成分散的缩松;加入0.8%B(原子分数)后,铸锭的组织得到细化,并削弱了柱状晶生长趋势,收缩缺陷分布集中以大缩孔方式存在,显微缩松的密度和尺寸均降低.添加0.1%C(原子分数)后,铸锭的组织和缩孔缩松与Ti-47Al-2Cr-2Nb比均无明显变化.热应力:铸件在凝固和冷却过程中,不同部位由于不均衡的收缩而引起的应力。
为铸造残留应力减少或消除应力的方法:减少铸件各部位的温差,尽量形成同时凝固。
二、铸件中的缩孔和缩松
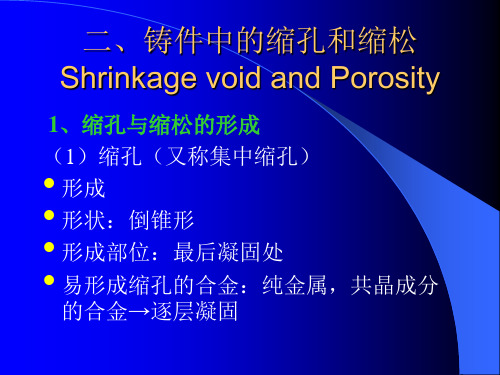
1、缩孔与缩松的形成 、 (1)缩孔(又称集中缩孔) 形成 形状:倒锥形 形成部位:最后凝固处 易形成缩孔的合金:纯金属,共晶成分 的合金→逐层凝固
• • • •
图2-4 缩孔形成过程
Fig.2Fig.2-4 The formation of Shrinkage Void
• •
图2-8 热应力的形成
The formation of Thermal Stress
Internal Stress,Deformation and Crack of Casting
• 结论:铸件中厚的部分最后冷却,总是 受拉应力,反之,薄的部分受压应力。 • 热应力的预防:采用同时凝固的方法 •
§3 铸造内应力、变形和裂纹
Internal Stress,Deformation and Crack of Casting
铸造内应力:铸件冷却时因固态收缩受 阻碍,在铸件内部产生的应力。 一、内应力的形成 类型— 热应力、机械应力 1、热应力 热应力的形成 形成原因—铸件的壁厚不均匀,冷却和 收缩先后不一致造成内应力。
(不管壁厚如何,同时一起收缩,可避 免热应力的产生)。 适用的合金:普通灰口铸铁(缩孔缩松 倾向小),锡青铜
图2-9 同时凝固的原则
2、机械应力
二、铸件的变形与预防
Deformation of the Cast and Its Prevention
具有内应力的铸件处在一种不稳定的状 态— 它会通过适当的变形来减缓自身的 内应力,趋于一种稳定状态。 例1 T型型材的变形 例2 机架的变形 例3 机床床身
宏观缩松和微观缩松的形成
2、缩孔和缩松的防止
球铁铸件缩孔、缩松的成因与防止
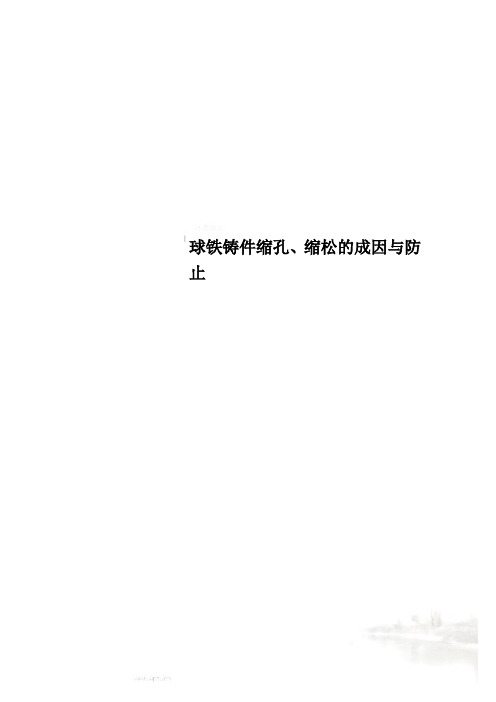
球铁铸件缩孔、缩松的成因与防止球铁铸件缩孔、缩松的成因与防止摘要:球墨铸铁大多数是共晶或过共晶成分,其糊状凝固方式使铸件外壳没有抵抗石墨化膨胀能力,因而铸型产生型壁迁移,增大铸件体积,极易产生内部缩孔、缩松。
球墨铸铁凝固时,在枝晶和共晶团间的最后凝固区域,收缩的体积得不到完全补充,留下的空洞形成宏观及微观缩松。
La 有助于消除缩松倾向。
分析缩孔缩松形成原因并提出相应的防止办法,有助于减少由此产生的废品损失。
关键词:球墨铸铁、收缩、缩孔、缩松1 前言1.1 缺陷形成原因球墨铸铁生产技术日臻完善,多年技术服务的实践表明,生产中出现的铸造缺陷,完全可以用成熟的经验予以消除。
据介绍:工业发达国家的铸造废品率可以控制在1%以下[1],国内先进水平也在2%左右,提高企业铸造技术水平,对减少废品十分重要。
1。
显微缩松显微镜观察微细连续缺失空间多角形疏松枝晶间、共晶团边界间众所周知,灰铸铁是逐层凝固方式,球墨铸铁是糊状凝固方式。
逐层凝固可以使铸件凝固时形成一个坚实的封闭外壳,铸件全封闭外壳的体积收缩可以减小壳体内的缩孔容积。
糊状凝固的特点是金属凝固时晶粒在金属液内部整个容积内形核、生长,固相与液相混合存在有如粥糊。
大多数球墨铸铁是共晶或过共晶成分,其糊状凝固方式使铸件外壳没有抵抗石墨化膨胀的能力,铸型产生型壁迁移,增大铸件体积,极易产生内部缩孔、缩松缺陷。
铸型冷却能力强,有利于铸件的容积凝固转变成逐层凝固,使铸件的分散缩松转变成集中缩孔。
然而,批量生产中湿砂型铸造很难被金属型或干砂型取代。
球墨铸铁凝固有以下三个特点,决定球墨铸铁是糊状凝固方式:①球化和孕育处理显著增加异质核心,核心存在于整个熔体,有利于全截面同时结晶。
②石墨球在奥氏体壳包围下生长,生长速度慢,延缓铸件表层形成坚实外壳;而片状石墨的端部始终与铁液接触,生长速度快,凝固时间短,促使灰铁铸件快速形成坚实外壳。
③球墨铸铁比灰铸铁导热率小 20%-30%,散热慢,外壳生长速度降低[3]。
第14章 缩孔与缩松

§14-3
影响缩孔与缩松的因素及防止措施
产生缩孔、缩松因素与控制: 收缩必然性→缩孔或缩松→取决于凝固方式(层、糊) 影响凝固方式因素: 成分、温度梯度 影响缩孔和缩松大小的因素:金属的性质;铸型条件(激冷能力) 浇注条件;铸件尺寸 缩孔防止:合理设计浇冒口系统 → 缩孔于浇冒口中。 缩松防止:无法通过浇冒口消除。△T↑ 枝晶发达→ 缩松↑
液态金属注入铸型后,首先在表面形成硬壳,其中尚处于液态的
金属在此外壳中冷却时,由于液态和凝固收缩体积缩小。如果所减
小的体积得不到外来金属液的补充,则在铸件中形成集中于某处的 或分散的孔洞一缩孔或缩松。因此,液态收缩和凝固收缩是铸件产 生缩孔和缩松的根本原因。 有一些合金,在凝固过程中体积不但不收缩,反而膨胀,故凝固 收缩率为负值。
③危害: 机械性能、 气密性、耐蚀性、锻造裂纹
铸件中缩孔的形成示意图
Al-4.5%Cu合金中的显微缩松 a.含气量高的显微缩松与球形孔大特点示意图 灰铸铁——“自补缩能力” 球墨铸铁——膨胀力大——若铸型移动——缩松倾向大
若铸型刚性大——自补缩
图 灰铁与球铁在湿砂型中浇注的膨胀曲线 灰铸铁——“自补缩能力” 球墨铸铁——膨胀力大——若铸型移动——缩松倾向大
2、铸钢的收缩
(1)液态 (2)凝固
图 碳钢的比容与温度和含碳量的关系 1-0.35%C;2-0.25%C;3-0.8%C
(3)固态收缩 a.珠光体转变前收缩 b.共析转变期的膨胀
缩孔与缩松

缩孔与缩松杨群收汇编铸件在凝固过程中,由于合金的液态收缩和凝固收缩,往往在铸件最后凝固的部位出现孔,称为缩孔。
容积大而集中的孔称为集中缩孔,或简称缩孔;细小而分散的孔称为分散性缩孔,简称缩松,缩松的形状不规则、表面不光滑,可以看到发达的树枝晶末梢,有时呈氧化现象发青,可以和气孔区别开来。
在铸件中存在任何形态的缩孔都会由它们而减少受力的有效面积,以及在缩孔处产生应力集中现象,而使铸件的机械性能显著降低。
因此,缩孔是铸件的重要缺陷之一,必须设法防止。
一、产生缩孔缩松的因素缩孔形成的因素和过程是很复杂的,各种合金产生缩孔的过程及缩孔量的大小也各不相同,必须说明铸件的缩孔体积和合金的总的收缩(即液态收缩,凝固收缩和固态收缩之和)并不是同等的概念,但是这三个阶段的收缩对缩孔却能产生影响。
要研究如何解决缩孔问题,必须了解两个问题,一、合金的凝固特性和凝固收缩过程。
以铸铁为例,其凝固特性逐层凝固,其总的收缩过程即液态收缩、凝固态收缩(与石墨膨胀共存)和固态收缩。
二、决定铸铁收缩的影响因素主要是三个方面;即浇注温度,石墨析出量(化学成分及冷却方法)和铸型刚度(型壁移动)。
对以上专业词语,结合图形作简单通俗说明,从理论概念上知道一些。
液态收缩:从浇注温度到开始结晶。
(冒口起补缩作用)凝固态收缩:从开始结晶到完全成固态,在这个阶段里存在液态,枝晶状亚固态,石墨生成。
(工艺措施及压力起补偿作用)以上两个阶段是合金的体收缩阶段,在这两个阶段里要防止铸件的缩孔,主要靠冒口,冒口高度,浇注方法及工艺上的措施。
固态收缩:从完全凝固成固态,到室温阶段的收缩,在这个阶段的收缩是线收缩(靠制作模型时放的缩尺,来弥补线收缩时铸件几何尺寸的减少)。
固态收缩对铸件的缩孔一般影响不大,但是在降温线收缩过程中,往四周拉扯的应力也可使缩孔增大些。
铸铁的缩孔量也可以下式表示:缩孔量(%)=液态收缩+凝固态收缩+固态收缩-石墨膨胀对于缩孔的形成,金属的液态收缩和凝固态收缩远大于固态收缩。
- 1、下载文档前请自行甄别文档内容的完整性,平台不提供额外的编辑、内容补充、找答案等附加服务。
- 2、"仅部分预览"的文档,不可在线预览部分如存在完整性等问题,可反馈申请退款(可完整预览的文档不适用该条件!)。
- 3、如文档侵犯您的权益,请联系客服反馈,我们会尽快为您处理(人工客服工作时间:9:00-18:30)。
4/28
收缩三个阶段
铸造合金从浇注温度冷却到常温,一般要经历以下三个收缩阶段:
• 1.液态收缩:合金从浇注温度冷却到液相线温度发生的体收缩。
• 2.凝固收缩:金属从液相线温度到固相线温度间产生的体收缩。
对于纯金属和共晶合金,凝固期间的体收缩是由于状态的改变, 与温度无关,具有一定的数值。
6/28
铸铁的收缩 1液态收缩 2凝固收缩:白口铁参考铸钢(两部分)
灰口铁有石墨膨胀 3固态收缩:
珠光体转变前收缩 共析转变膨胀(铁素体膨胀+渗碳体收缩、石墨 膨胀) 珠光体转变后收缩
7/28
第二节 缩孔与缩松的形成机理
1、缩孔:铸造合金在凝固过程中,由于液态收缩和凝固 收缩的产生,往往在铸件最后凝固的部位出现孔洞,称 为缩孔,把尺寸较大而且集中的孔洞称为集中缩孔,简 称缩孔。
• 2、条件: 铸件由表及里逐层凝固。
11/28
二、缩松的形成
当某种成分下的合金结晶温度范围较宽时, 通常按体积凝固的方式凝固。凝固区域宽,晶 体容易发展成为树枝发达的粗大等轴晶,当固 相约占70%(体积分数)时,尚未凝固的液体被 分割为一个个互不相通的小熔池。
随温度降低,同样要发生液态收缩、凝 固收缩和固态收缩,由于合金的液态收缩和凝 固收缩大于固态收缩,出现的细小孔洞得不到 外部合金液的补充而形成分散性的细小缩孔, 即缩松。
20/28
21/28
• 由于按照体积凝固方式凝固,铸件表面在 凝固后期没有形成坚固的外壳,如果铸型刚度 不够,膨胀力将迫使型壁外移。尺寸精度变差。 • 随着石墨球的长大,共晶团之间的间隙逐 步扩大,使得铸件普遍膨胀。共晶团之间的间 隙就是球墨铸铁的显微缩松,并布满铸件整个 断面,所以球墨铸铁铸件产生缩松的倾向性很 大。 • 如果铸件厚大,球墨铸铁铸件这种较大的 缩前膨胀也会导致铸件产生缩孔。 • 如果铸型刚度足够大,石墨化的膨胀力能 够将缩松挤合。在这种情况下,球墨铸铁也可 看作是具有“自补缩”能力。
18/28
片状石墨横向长大的作用
• 被共晶奥氏体包围的片状石墨,由于碳 原子的扩散作用,在横向上也要长大, 但是速度很慢。
• 石墨片在横向上长大而产生的膨胀力作 用在共晶奥氏体上,使共晶团膨胀,并 传到邻近的共晶团上或奥氏体枝晶骨架 上,使铸件产生缩前膨胀。
• 很显然,这种缩前膨胀会抵消一部分自 补缩效果,但是,由于这种横向的膨胀 作用很小而且是逐渐发生的,同时因灰 铸铁在共晶凝固中期,在铸件表面已经 形成硬壳,因此灰铸铁的缩前膨胀一般 只有0.1%-0.2%左右。
2、缩松:尺寸细小而且分散的孔洞称为分散性缩孔,简 称缩松。
3、对铸件性能的影响 1)减少铸件的有效受力面积,在尖角处产生应
力集中,导致裂纹的出现,显著降低其力学性能。 2)降低铸件的气密性,降低其承压能力。
8/28
一、缩孔的形成
纯金属、共晶成分合金和窄结晶温度范围的合金, 按逐层凝固方式凝固,由于其凝固前沿直接与液态金属 接触,当液体金属凝固成固体而发生体积收缩时,可以 不断得到液体的补充,在铸件最后凝固的地方产生缩孔。
对于Bi、Sb合金,在凝固过程中体积不但不收缩,反而膨胀, 因此,其凝固收缩率为负值。
• 3.固态收缩:金属在固相线以下发生的体收缩。
5/28
铸钢的收缩 1液态收缩 2凝固收缩:状态改变和温度降低
3 固态收缩:珠光体转变前收缩 共析转变膨胀(铁素体膨胀+渗碳体收缩) ( 马氏体膨胀) 珠光体转变后收缩
12/28
形成缩松的原因及条件
1、形成缩松基本原因和形成缩孔是相同的: 合金的液态收缩值和凝固收缩值之和大于固
态收缩。
2、形成缩松的条件: 合金的结晶温度范围较宽,倾向、灰铸铁和球墨铸铁铸件的缩孔和缩松
• 共晶灰铸铁和球墨铸铁有一个共同点,这就是初生奥氏体枝晶 具有很大连成骨架的能力,使补缩通道受阻。因此,这两种铸 铁都有产生缩松的可能性,但是,由于它们的共晶凝固方式和 石墨长大的机理不同,产生缩孔和缩松的倾向性有很大差别。
9/28
缩凹的产生
在液态金属中含气量不大的情况下,当液 态金属与顶面层脱离时,液面上部要形成真空。 在大气压力的作用下,顶面固体层可能向缩孔 方向凹进去。因此缩孔应包括外部的缩凹和内 部的缩孔两部分。当铸件顶面薄层强度很大时, 也可能不出现缩凹。
10/28
形成缩孔的原因及条件
• 1、基本原因: 合金的液态收缩和凝固收缩值之和大于固态收缩值。
材料成形原理
第十四章 缩孔与缩松
材料成型与控制专业
1/28
第一节 收缩的基本概念
1、收缩 (1)液态金属在冷却过程中,随着温度下降,空
穴数量减少,原子集团中原子间距缩短,液态金属的 体积减小;
(2)液态金属发生凝固时,状态的变化也导致金 属体积显著减小;
(3)金属在固态下继续冷却,原子间距还要缩短, 体积会进一步减小。
把铸件在液态、凝固态和固态冷却过程中发生的 体积减小现象称为收缩。
2/28
• 2、体收缩 金属从液态到常温的体积改变量称为体收缩。
• 3、线收缩 金属在固态时从高温到常温的线尺寸改变
量称为线收缩。
3/28
• 4、收缩率 在实际使用中,通常用相对收缩来表示金属的收缩特性,把
这一相对收缩称为收缩率。
14/28
凝固方式
共同点:奥氏体迅速达到中心,形成骨架,难于补缩 不同点:灰铁共晶区小,中间凝固,有凝固外壳
球铁共晶区大,体积凝固,无凝固外壳(石墨膨胀产生变形)
15/28
16/28
长大机制
17/28
灰铸铁的“自补缩能力”
灰铸铁共晶团中的片状石 墨,与枝晶间的共晶液体直接 接触,因此片状石墨长大时所 产生的体积膨胀大部分作用在 所接触的晶间液体上,迫使它 们通过枝晶间通道去充填奥氏 体枝晶间由于液态收缩和凝固 收缩所产生的小孔洞,从而大 大降低了灰铸铁产生缩松的严 重程度。这就是灰铸铁的所谓 “自补缩能力”。
• 所以,灰铸铁件产生缩松的倾向性较小。
19/28
球墨铸铁的缩前膨胀
• 球墨铸铁在凝固过程中,当石墨球长大到一定程度后, 四周形成奥氏体外壳,碳原子是通过奥氏体外壳扩散到共 晶团中使石墨球长大。
• 当共晶团长大到相互接触后,石墨化膨胀所产生的膨 胀力,只有一小部分作用在晶间液体上,而大部分作用在 相邻的共晶团上或奥氏体枝晶上,趋向于把它们挤开。因 此,球墨铸铁的缩前膨胀比灰铸铁大得多。