典型螺母冷镦工艺设计教学内容共33页
冷镦知识和工艺讲解课件
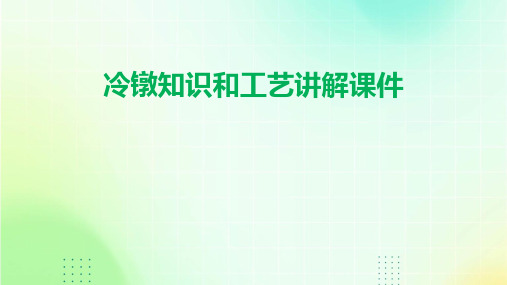
毛坯尺寸
根据产品需求,确定毛坯的尺寸 和形状,确保满足成型要求。
毛坯表面处理
对毛坯进行清洗、除锈等表面处 理,以提高成型质量和模具寿命
。
模具选择与安装
模具类型
根据产品形状和尺寸选择合适的模具类型,如开 式、闭式等。
模具设计
根据产品要求,进行模具结构设计,确保成型稳 定、生产效率高。
模具安装
将选定的模具安装到冷镦机上,确保安装位置准 确、稳定。
冷镦知识和工艺讲解课件
目录
• 冷镦工艺简介 • 冷镦设备与工具 • 冷镦材料 • 冷镦工艺流程 • 冷镦工艺质量控制 • 冷镦工艺的发展趋势与展望
01
冷镦工艺简介
冷镦工艺定义
01
冷镦工艺是一种金属塑性加工技 术,利用金属的塑性变形来制造 螺栓、螺母等紧固件。
02
在冷镦过程中,金属材料在模具 的挤压下发生塑性变形,从而获 得所需形状和尺寸的零件。
根据产品用途选择具有相应特性的材料以满 足使用要求。
考虑成本与性能平衡
在满足性能要求的前提下,尽量选择成本较 低的材料。
考虑工艺适应性
选择易于加工和处理的材料以提高生产效率 和降低成本。
符合环保要求
优先选择可回收、可再利用的材料,减少对 环境的污染。
04
冷镦工艺流程
毛坯准备
毛坯材料
选择适合冷镦工艺的材料,如低 碳钢、不锈钢等。
冷镦工艺的特点
01
02
03
高效率
冷镦工艺可以实现连续、 自动化生产,提高生产效 率。
优质产品
冷镦工艺可以获得高精度 、高表面质量的紧固件。
节能环保
冷镦工艺采用金属塑性加 工技术,相比切削加工可 以节约能源和减少废弃物 排放。
冷镦知识和工艺讲解

由于工模具形状不同,所施加给坯件的作用力,以及模具与坯件接触 的摩擦力也不一样,引致金属在各方向流动阻力的差异,从而金属在 各方向流动体积的分配也有所差异。
c.金属本身性质不均的影响
金属本身的性质不均,反映出金属成份的不均、组织不均、以及在变 形中内部温度的不均等。这些性质的不均匀性,在金属内部出现互相 平衡的附加应力,由于内力的存在,使金属在各自流动的阻力有所差 异,变形首先发生在阻力最小的部分。
2021/10/10
3
1 金属变形的基本概念
1.1 变形 变形是指金属受力(外力、内力)时,在保持自己完整性的条件下,
组成本身的细小微粒的相对位移的总和。 1.1.1 变形的种类 a.弹性变形 金属受外力作用发生了变形,当外力去掉后,恢复原来形状和尺寸的
能力,这种变形称为弹性变形。 弹性的好坏是通过弹性极限、比例极限来衡量的。 b.塑性变形 金属在外力作用下,产生永久变形(指去掉外力后不能恢复原状的变
形),但金属本身的完整性又不会被破坏的变形,称为塑性变形。 塑性的好坏通过伸长率、断面收缩率、屈服极限来表示。
2021/10/10
4
1.1.2 塑性的评定方法 为了评定金属塑性的好坏,常用一种数值上的指标,称为塑性指标。
塑性指标是以钢材试样开始破坏瞬间的塑性变形量来表示,生产实际 中,通常用以下几种方法: (1)拉伸试验 拉伸试验用伸长率δ和断面收缩率ψ来表示。表示钢材试样在单向拉 伸时的塑性变形能力,是金属材料标准中常用的塑性指标。δ和ψ的 数值由以下公式确定:
2021/10/10
13
1.1.4 提高金属塑性及降低变形抗力的工艺措施
针对影响金属塑性及变形抗力的主要因素,结合生产实际,采取有效 的工艺措施,是完全可以提高金属塑性及降低其变形抗力的,生产中, 常采取的工艺措施有:
螺丝冷镦机课程设计

螺丝冷镦机课程设计一、课程目标知识目标:1. 学生能够理解螺丝冷镦机的结构组成和工作原理;2. 学生能够掌握螺丝冷镦机操作步骤和安全规范;3. 学生能够了解螺丝冷镦机在制造业中的应用及重要性。
技能目标:1. 学生能够操作螺丝冷镦机完成简单的螺丝制造任务;2. 学生能够根据工艺要求,调整螺丝冷镦机的参数;3. 学生能够解决螺丝冷镦机操作过程中出现的简单问题。
情感态度价值观目标:1. 学生培养对机械制造行业的兴趣和热情;2. 学生树立安全生产意识,养成良好的操作习惯;3. 学生增强团队合作意识,提高沟通协调能力。
课程性质:本课程为机械制造专业课程,以实践操作为主,理论教学为辅。
学生特点:学生具备一定的机械基础知识,动手能力强,对新鲜事物充满好奇。
教学要求:结合学生特点,注重实践操作,强调安全规范,提高学生的综合运用能力。
将课程目标分解为具体的学习成果,以便后续的教学设计和评估。
二、教学内容1. 螺丝冷镦机结构及工作原理:- 螺丝冷镦机的主要部件及其功能;- 螺丝冷镦机的工作流程及原理。
2. 螺丝冷镦机操作与安全规范:- 螺丝冷镦机的操作步骤;- 螺丝冷镦机安全操作规范及注意事项;- 应急处理方法及安全防护措施。
3. 螺丝冷镦机参数调整与工艺应用:- 螺丝冷镦机参数调整方法;- 螺丝冷镦机在不同工艺中的应用;- 质量控制要点及常见问题解决。
4. 实践操作:- 简单螺丝制造任务的操作实践;- 团队协作完成复杂螺丝制造任务;- 操作过程中问题分析与解决。
教学内容安排与进度:第一周:螺丝冷镦机结构及工作原理;第二周:螺丝冷镦机操作与安全规范;第三周:螺丝冷镦机参数调整与工艺应用;第四周:实践操作及问题分析与解决。
教材章节关联:《机械制造工艺与设备》第三章:金属塑性成形设备;《机械制造工艺与设备》第四章:塑性成形工艺及模具设计。
三、教学方法1. 讲授法:- 对于螺丝冷镦机的结构、工作原理等理论知识,采用讲授法进行教学,结合多媒体课件,使抽象的知识形象化,便于学生理解。
冷镦基础知识和工艺分析ppt
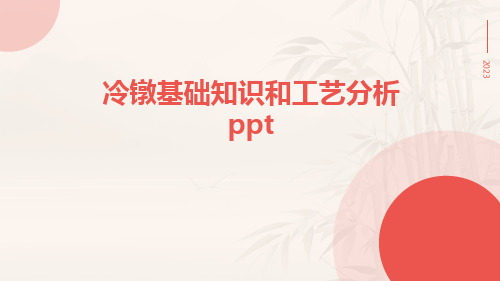
冷镦基础知识和工艺分析 ppt
contents
目录
• 冷镦成型工艺简介 • 冷镦成型工艺特点 • 冷镦成型工艺影响因素 • 冷镦成型工艺应用场景 • 冷镦成型工艺发展趋势 • 冷镦成型工艺常见问题及解决方案
01
冷镦成型工艺简介
冷镦成型工艺定义
冷镦成型工艺是指利用模具在常温下对金属坯料施加压力, 使其产生塑性变形而形成所需形状和尺寸的零件的一种成型 方法。
03
在冷镦成型工艺中,模具是关键的工艺装备之一,其结构形式、材料选择、热 处理工艺等因素直接影响到零件的质量和生产效率。
02
冷镦成型工艺特点
提高生产效率
加工效率
采用多工位冷镦成型方式,可同时处理多个零件,提高生产效率。
生产周期
通过减少或消除加热、矫直、打磨等辅助工序,缩短了生产周期。
提高零件强度
材料纯净度
3
材料中的杂质会对成型效果产生不良影响。
模具设计因素
模具结构
合理的模具结构可以降低成型难度和提高成型效 果。
模具材料
模具材料的硬度、耐磨性和抗冲击性能对成型效 果有影响。
模具加工精度
模具加工精度对成型件的尺寸和形状精度有影响 。
工艺参数选择
冷镦速度
速度过快会导致成型不充分,速 度过慢则会影响生产效率。
优化材料性能
材料利用率
冷镦成型工艺可以最大限度地利用原材料,提高材料的利用率,降低生产成本。
性能优化
通过合理的材料选择和冷镦工艺优化,可以进一步优化零件的性能,提高其使用 效果和寿命。
03
冷镦成型工艺影响因素
材料因素
1 2
材料硬度
硬度过高会导致成型困难,硬度过低则会使成 型效果不佳。
冷镦知识和工艺讲解
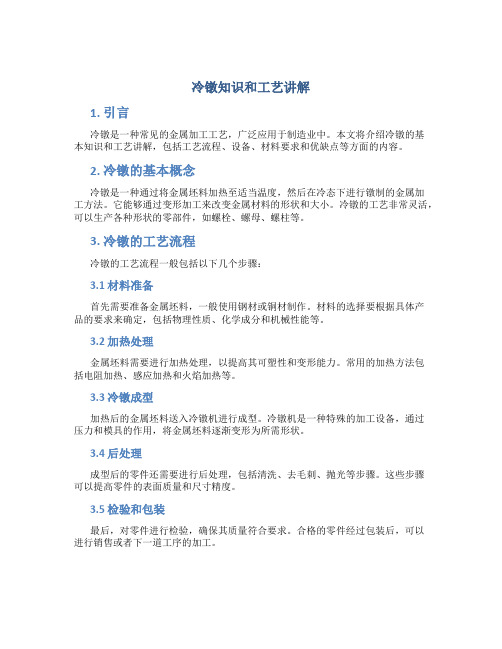
冷镦知识和工艺讲解1. 引言冷镦是一种常见的金属加工工艺,广泛应用于制造业中。
本文将介绍冷镦的基本知识和工艺讲解,包括工艺流程、设备、材料要求和优缺点等方面的内容。
2. 冷镦的基本概念冷镦是一种通过将金属坯料加热至适当温度,然后在冷态下进行镦制的金属加工方法。
它能够通过变形加工来改变金属材料的形状和大小。
冷镦的工艺非常灵活,可以生产各种形状的零部件,如螺栓、螺母、螺柱等。
3. 冷镦的工艺流程冷镦的工艺流程一般包括以下几个步骤:3.1 材料准备首先需要准备金属坯料,一般使用钢材或铜材制作。
材料的选择要根据具体产品的要求来确定,包括物理性质、化学成分和机械性能等。
3.2 加热处理金属坯料需要进行加热处理,以提高其可塑性和变形能力。
常用的加热方法包括电阻加热、感应加热和火焰加热等。
3.3 冷镦成型加热后的金属坯料送入冷镦机进行成型。
冷镦机是一种特殊的加工设备,通过压力和模具的作用,将金属坯料逐渐变形为所需形状。
3.4 后处理成型后的零件还需要进行后处理,包括清洗、去毛刺、抛光等步骤。
这些步骤可以提高零件的表面质量和尺寸精度。
3.5 检验和包装最后,对零件进行检验,确保其质量符合要求。
合格的零件经过包装后,可以进行销售或者下一道工序的加工。
4. 冷镦的设备冷镦机是冷镦过程中最重要的设备,它通常由下列部分组成:•送料装置:用于将金属坯料送入冷镦机,保持均匀的进料速度。
•压力机构:通过压力使金属坯料变形,完成冷镦过程。
•模具:冷镦模具决定了最终产品的形状和尺寸精度。
•冷却装置:用于冷却金属零件,防止变形和表面质量不良。
5. 冷镦材料的要求冷镦的材料要求主要包括以下几个方面:5.1 可镦性金属材料的可镦性是指其在冷态下的变形能力。
优秀的可镦性意味着材料容易变形,而不容易断裂。
一般来说,钢材的可镦性比较好,常用于冷镦加工。
5.2 易切削性金属材料的易切削性是指其在冷镦过程中,容易切断和形成所需形状。
易切削性好的材料在加工过程中能够减少切削力和模具磨损,提高生产效率和产品的质量。
冷镦模具设计介绍课件

04
冷镦模具的应用与发展
冷镦模具的应用范围
汽车零件制造
冷镦模具被广泛应用于汽车零件的制造,如 螺栓、螺母、齿轮等。
机械制造业
机械制造业中,冷镦模具用于生产各种紧固 件、连接件等。
建筑行业
在建筑行业中,冷镦模具用于生产钢筋、螺 杆等紧固件。
其他行业
如航空航天、电子、家具、家电等行业,都 离不开冷镦模具的应用。
冷镦模具的结构设计应考虑成形 工艺的特点,如拉伸、冲压等, 以及零件的形状、尺寸和材料等
因素。
冷镦模具的材料选择
01
根据成形工艺和零件材料的不同,冷镦模具的材料选择也有所 不同。
02
常用的冷镦模具材料包括优质碳素结构钢、合金结构钢、不锈
钢、硬质合金等。
在选择冷镦模具材料时,需要考虑材料的耐磨性、抗冲击性和
提高解决实际问题的能力。
展望
随着制造业的快速发展,冷镦模具设 计领域面临着越来越多的挑战和机遇 。未来,该领域将更加注重技术创新 和跨学科融合,推动产业升级和发展 。
新材料和新工艺的不断涌现将为冷镦 模具设计带来更多的可能性,如采用 高性能材料制造高精度、长寿命的模 具,以及利用3D打印技术实现快速原 型制作等。
此外,随着智能制造和数字化转型的 加速推进,冷镦模具设计将更加注重 信息化和智能化,实现数据驱动的设 计优化和生产自动化。
06
参考文献与致谢
参考文献
01
参考文献1
作者1,书名,出版社,出版年份 。
参考文献3
作者3,书名,出版社,出版年份 。
03
02
参考文献2
作者2,书名,出版社,出版年份 。
参考文献4
作者4,书名,出版社,出版年份 。
螺钉头冷镦课程设计说明书

螺钉头冷镦课程设计说明书SANY标准化小组 #QS8QHH-HHGX8Q8-GNHHJ8-HHMHGN#机械原理课程设计课程名称:机械原理课程设计设计题目:螺钉头冷镦设计院系:机械工程系学生姓名:学号:专业班级: 08机械设计制造及其自动化(1)班指导教师:日期: 2010年6月9日目录一.工作原理与功能分析二. 机构选用三. 原始数据及设计要求四. 设计方案五. 机构运动循环图六. 传动机构七.结果与结论八.参考文献.一.工作原理与功能分析(1) 自动间歇送料:胚料被自动定时送入模具,执行构件做直线间歇运动。
(2) 截料并运料:进料之后切断机构将棒料切断并送至敦料工位执行构件做直线间歇等速运动及间歇急回运动。
(3) 预墩及终墩:将胚料墩出螺钉,从摸中推出,执行件做直线急回运动。
(4)顶料:由起模将螺钉从模中推出,执行件做直线间歇运动。
二.机构选用 利用设计目录并根据技术要求确定执行机构三.原始数据及设计要求(1) 每分钟冷镦螺钉头120只;(2)螺钉头的直径24D mm =,长度632L mm =; (3) 毛胚料最大长度48mm ,最小长度12mm ; (4) 冷镦行程56mm 。
四.设计方案1.实现间歇送料方案一不完全齿轮 用一个完全齿轮和一个不完全齿轮,完全齿轮在电动机的驱动下匀速转动,当不完全齿轮的轮齿与完全齿轮啮合时,不完全齿轮带动履带轮转动,进行送料,转动过的弧长,即为送料长度.当不完全齿轮不进行啮合时,毛坯料不动,可在这段时间内进行剪切和冷镦. 优点:不完全齿轮机构的结构简单,制造容易,工作可靠,而且设计时从动轮的运动时间和静止时间的比例可在较大范围内变化.方案二槽轮机构槽轮机构与不完全齿轮的原理一样,是通过用主动轮的圆销带动槽轮转动,当圆销离开径向槽时,槽轮又静止不动.直至圆销再次进入另一个径向槽时,又重复上述运动.槽轮机构要控制槽轮的运动时间和静止时间,是根据槽轮上的槽数来定的.在外槽轮机构中,当主动拨盘回转一周时,槽轮的运动时间td 与主动拨盘一周的总时间之比,为槽轮机构的运动系数,用k表示,且k=td/t=1/2-1/Z,这里的z就是槽轮上的槽数.优点:槽轮机构的结构简单,工作可靠,刚性冲击较小,但与不完全齿轮比较起来,槽轮机构运动时间和静止时间的比例可调范围没有不完全齿轮那么大.方案三棘轮机构原理及优点:棘轮机构的主动件为摇杆,这里想到要用棘轮机构,也正是因为它用到摇杆,那么会有曲柄连杆去带动它,而后面的剪切和夹紧机构可以共用一个曲柄,使整体机构简单化,而且加工方便.最终方案:方案二1.槽轮机构选择理由:这三种方案中,不完全齿轮和槽轮是同样的原理,而且结构简单,制造容易,但不完全齿轮有较大冲击,根据冷镦机的设计要求,每分钟要做120个螺钉,那么1秒钟要送两次料,齿轮的转速要达到720deg/s,这是属于比较高速的机构,不完全齿轮就不大适合.我们最终选用槽轮机构,就是因为槽轮机构的机械效率高,并能平稳地间歇地进行转位.而第三方案棘轮机构,同样是因为转速问题,棘轮工作时的冲击也是比较大的,而且运动精度较差.但从整体设计角度来看,选用棘轮机构,能使整体的机构配合紧凑而且简单.如果这里是低速机构的话,那么将选择棘轮机构.机构实现:选择参数:槽轮机构里主动盘和槽轮的中心距离为L=100mm,圆销直径d=12mm,槽数Z=4 .机构图:这里的槽数为4,那么槽轮机构的运动系数k=.根据设计要求,主动轮转一周的时间为秒,那么槽轮的运动时间为秒,在这个时间内完成送料.由于槽轮每次转过的角度都为90度,那么根据L=φ/dπ(L为毛坯料的长度,d为履带轮的直径)根据需要加工的毛坯料长度,调节履带轮的直径,就可实现送不同长度毛坯料的要求.《结构见图纸》2. 截料机构剪切机构选用了曲柄滑块机构,主要是机构简单,且同样能达到间歇剪切材料的目的.当停止送料,加工材料在夹紧的状态下,完成冷镦,这时滑块正好移到加工材料的位置,同时完成剪切.然后在曲柄和连杆的带动下,滑块退回.在退回和再次到达加工材料位置这个过程中,机构完成了送料和预镦的过程.这个机构就是利用滑块的往返时间达到控制间歇剪裁的时间.运动简图及参数选择曲柄长度= 24 mm, 连杆长度= 90 mm, 滑块行程= 48 mm,偏距e= 0 mm机构设计:在滑块的正上方,是一个固定的刀具.总的配合起来就是一个固定的上刀刃和一个移动的下刀刃完成总的剪切.选择固定上刀刃的目的第一,是对加工材料起到定位和矫直的作用材料在履带的传送下是稍微与上刀刃接触的,这样,通过这个固定的上刀刃和基座上的凹槽,就能使加工材料固定在一条直线上,以便与冷镦的准确完成.第二,如果单用一个下面这个刀具对加工材料进行剪裁的话,那么加工材料在垂直平面上将受到一个很大的剪力.加工材料仅仅是一个细杆圆柱,那样剪切完后,材料要变形弯曲,这对后面工序的正常进行要造成很大的影响.比如说,弯曲后顶料顶不上,或者是螺钉杆再通过夹具的时候卡住了过不去.运动参数分析:这是刀具的运动参数分析,从图上我们可以看到当刀具的位移为0时(即刀具在加工位置的时候)他的速度为最大,这个时候有利于进行剪切,而且从其加速度曲线来看,机构的柔性冲击并不是很大.3. 夹紧机构夹紧机构是一个很重要的部分,也是这次设计的最关键部分,夹紧机构必须使工件真实夹紧,那样在冷镦过程中,工件才不会因为受到一个很大的冲击,致使工件飞出或者螺钉杆偏置移位.同时,夹紧需要一个时间过程,在夹紧期间要完成冷镦以及剪切.方案一用曲柄滑块机构,利用死点原理用滑块对工件进行压紧.曲柄为顺时针转动,我们的设计想法为,当曲柄转到与垂线成一个a度角的时候,下面的滑块正好接触到工件,那当曲柄继续转动的时候,滑块就会有继续往下运动的趋势,那么就要压紧工件,当曲柄转到左侧与垂线成a度角的时候,这时工件松开.从原理上来讲,是合理的,而且机构简单.但实际操作上来看,压紧时间仅为曲柄转过2a 的时间,时间过于少.而且当滑块达到最大位移的时候,即(b)图所示位置,滑块已经把工件压下一定的距离,这时会有一个很大的反冲力,有可能连杆在这个反冲力的作用下就要折断掉.在经过分析考虑后,我们舍弃了这种方法.方案二利用一个圆盘进行送料和冷镦在圆盘的径向上均布着小孔,截好的材料送进来正好嵌在孔里面,当圆盘转过一定角度的时候工件又继续送进去,这也能实现间歇送料.在径向孔的内部,有三个爪子,就象车床上夹紧材料的那个部分,通过圆盘自身的转动,带动齿轮转动从而使这三个爪子具有收紧和放松的功能.在爪子收紧时,正好进行冷镦,放松时,卸下工件.优点及缺点优点:把间歇送料和夹紧以及冷敦部分一并考虑 ,缺点:夹紧部分工艺复杂,要在圆盘内添加机构,让爪子动起来,实现收紧,对于我们来说,设计出来具有很大的难度.镦头在垂直方向工作,当冷敦工件时,工件所受到的力都传到圆盘上,加大圆盘的径向尺寸,在理论上是可以承受这样的载荷,但在考虑到机器的长久使用上,这种工作方式会让机器寿命减短,而无法实现生产效益.方案三利用凸轮机构. 需要同时夹紧预墩和终墩位置。
典型螺母冷镦工艺设计ppt

THANKS
感谢观看
3
背景:传统螺母制造方法生产效率低下,成本 较高,不能满足现代制造业发展需求。
螺母冷镦工艺定义
螺母冷镦工艺是一种利用金属材料的塑性变形和镦粗原理, 在室温下将原材料加工成所需形状和尺寸的工艺方法。
冷镦工艺是一种高效、节能、环保的加工方法,具有生产效 率高、成本低、产品质量稳定等优点。
工艺分类
根据加工原理,镦、复合型冷镦等。
典型螺母冷镦工艺设计
xx年xx月xx日
目 录
• 介绍 • 螺母冷镦工艺设计 • 螺母冷镦工艺的优缺点 • 案例分析 • 比较分析 • 总结
01
介绍
目的和背景
1
螺母冷镦工艺是一种在室温下将原材料通过压 力加工成型的工艺方法,广泛应用于机械制造 、汽车、航空航天等领域。
2
目的:提高生产效率、降低成本、提高产品质 量和经济效益。
方案2
由于采用普通设备,初期投资成本较低,但生产效率较低,反而 增加生产成本。
方案3
由于采用特种设备,虽然制造成本较高,但可满足特定领域的需 求,提高产品附加值。
各厂家的螺母冷镦工艺可靠性比较
方案1
采用自动化生产线,减少人为操作失误,提高产 品的一致性和可靠性。
方案2
由于人工操作较多,产品质量容易受到操作者技 能水平的影响。
方案3
由于特种设备的维护和操作技术要求较高,若维 护不当或操作失误容易导致生产事故。
06
总结
螺母冷镦工艺在机械制造行业的应用前景
应用领域广泛
螺母冷镦工艺是一种广泛应用 于机械制造行业的基本工艺, 可应用于汽车、航空航天、能
源等领域。
高效、高精度
螺母冷镦工艺具有高效、高精度 的特点,能够实现大批量、高效 率的生产。
冷镦件工艺

冷镦件工艺冷镦件工艺是一种常见的金属加工工艺,主要用于生产各种螺栓、螺钉和销轴等紧固件。
本文将介绍冷镦件工艺的基本原理、工艺流程以及其在工业生产中的应用。
一、冷镦件工艺的原理冷镦件工艺是通过在常温下将金属材料进行塑性变形,使其截面积减小,从而实现材料的延长和变细。
在冷镦件过程中,材料受到压力和剪切力的作用,使得材料发生塑性变形,最终形成所需的形状和尺寸。
1. 材料准备:选择合适的金属材料,如碳钢、合金钢等,并进行切割和清洗处理。
2. 镦头设计:根据产品的要求,设计合适的镦头形状和尺寸。
3. 镦头加工:使用加工设备对镦头进行加工,保证其尺寸和形状的精度。
4. 材料供给:将准备好的材料送入冷镦机的供给系统中。
5. 冷镦加工:通过冷镦机的压力和剪切力作用下,将材料进行冷镦加工。
6. 修整工艺:对冷镦件进行修整,以去除可能存在的毛刺和表面不平整。
7. 表面处理:根据产品要求,进行镀锌、喷涂等表面处理。
三、冷镦件工艺的优势1. 节约原材料:冷镦件工艺可以通过材料的塑性变形,最大限度地利用材料,减少废料产生。
2. 提高生产效率:冷镦件工艺可以实现连续生产,大大提高生产效率。
3. 优化产品性能:冷镦件工艺可以改善材料的内部结构,提高产品的强度和硬度。
4. 降低生产成本:相比于热镦件工艺,冷镦件工艺不需要加热和冷却设备,降低了生产成本。
四、冷镦件工艺的应用冷镦件工艺广泛应用于汽车、机械、航空航天等领域的紧固件生产。
螺栓、螺钉和销轴等冷镦件产品在这些领域中起着重要的作用,用于连接和固定各种零部件。
随着工业的发展和技术的进步,冷镦件工艺的应用范围也在不断扩大。
在汽车制造中,冷镦件产品广泛应用于发动机、底盘和车身结构等部位。
螺栓和螺母是汽车中最常见的冷镦件产品,用于连接和固定各种零部件。
冷镦件工艺能够保证产品的高精度和高强度,满足汽车在行驶中的安全性要求。
在机械制造中,冷镦件产品被广泛应用于各种机械设备的组装和维修中。
冷镦工艺讲解ppt课件

7
磷在钢中使变形抗力提高,塑性降低。含磷高于0.1%~0.2%的钢具 有冷脆性。一般钢的含磷量控制在百分之零点零几。
其他如低熔点杂质在金属基体的分布状态对塑性有很大影响。 总之,钢中的化பைடு நூலகம்成分愈复杂,含量愈多,则对钢的抗力及塑性的影
9
10
主应力由拉应力引起的为正号,主应力由压应力引起的为负号。 在金属压力加工中,最常遇到的是同号及异号的三向主应力图。在异
号三向主应力图中,又以具有两个压应力和一个拉应力的主应力图为 最普遍。 同号的三向压应力图中,各方向的压应力均相等时(б1=б2=б3),并 且,金属内部没有疏松及其它缺陷的条件下,理论上是不可产生塑性 变形的,只有弹性变形产生。 不等的三向压应力图包括的变形工艺有:体积模锻、镦粗、闭式冲孔、 正反挤压、板材及型材轧制等。 在生产实际中很少迂到三向拉伸应力图,仅在拉伸试验中,当产生缩 颈时,在缩颈处的应力线,是三向拉伸的主应力图,如图36-2所示
模具结构形状确定的设计最主要的依据。 1.2.3 变形中影响金属流动的主要因素 a 摩擦的影响 在变形中模具和坯件间的接触面上不可避免的有摩擦力存在,由于摩
擦力的作用,改变了金属流动的特征。如图36-5所示,在平板间镦粗 矩形坏料时,由于摩擦力的作用,使各向阻力不同,变形中,断面不 能继续保持矩形。按最小阻力定律,它会逐渐趋于圆形。若无摩擦力 作用,则坯件处于理想的均匀变形状态,变形前后在几何形状上仍然 相似。
11
在镦粗时,由于摩擦的作用,也呈现出三向压应力图,如图36-3所示。 总之,受力金属的应力状态中,压应力有利于塑性的增加,拉应力将
冷镦工艺讲解

在镦粗时,由于摩擦的作用,也呈现出三向压应力图,如图36-3所示。 总之,受力金属的应力状态中,压应力有利于塑性的增加,拉应力将 降低金属的塑性。
d.冷变形硬化对金属塑性及变形抗力的影响 金属经过冷塑性变形,引起金属的机械性能、物理性能及化学性能的 改变。随着变形程度的增加,所有的强度指标(弹性极限、比例极限、 流动极限及强度极限)都有所提高,硬度亦有所提高;塑性指标(伸 长率、断面收缩率及冲击韧性)则有所降低;电阻增加;抗腐蚀性及 导热性能降低,并改变了金属的磁性等等,在塑性变形中,金属的这 些性质变化的总和称作冷变形硬化,简称硬化。
1.1.4 提高金属塑性及降低变形抗力的工艺措施 针对影响金属塑性及变形抗力的主要因素,结合生产实际,采取有效 的工艺措施,是完全可以提高金属塑性及降低其变形抗力的,生产中, 常采取的工艺措施有: a.坯料状况 冷镦用原材料,除了要求化学成份、组织均匀,不要有金属夹杂等以 外,一般要对原材料进行软化退火处理,目的在于消除金属轧制时残 留在金属内部的残余应力,使组织均匀,降低硬度,要求冷镦前金属 的硬度HRB≤80。对中碳钢,合金钢一般采取球化退火,目的是除消 除应力、使组织均匀外,还可改善金属的冷变形塑性。 b.提高模具光滑度及改善金属表面润滑条件 这两项措施都是为了降低变形体与模具工作表面的摩擦力,尽可能降 低变形中由于摩擦而产生的拉应力。 c.选择合适的变形规范 在冷镦(挤)工艺中,一次就镦击成形的产品很少,一般都要经过两 次及两次以上的镦击。因此必须做到每次变形量的合理分配,这不仅 有利于充分利用金属的冷变形塑性,也有利于金属的成形。如生产中 采用冷镦、冷挤复合成形、螺栓的两次缩径、螺母的大料小变形等。
典型螺母冷镦工艺设计课件

05
螺母冷镦工艺发展趋势 与展望
新材料的应用
高强度钢的应用
随着新材料技术的发展,高强度钢在螺母冷镦工艺中 的应用越来越广泛。高强度钢具有较高的屈服强度和 抗拉强度,能够提高螺母的承载能力和使用寿命。
不锈钢的应用
不锈钢具有优良的耐腐蚀性能和美观的外观,在某些 特定场合下,如食品工业和医疗器械,不锈钢螺母的 需求逐渐增加。
螺母冷镦工艺的历史与发展
历史
螺母冷镦工艺起源于20世纪初,经 过多年的发展,技术不断进步和完善 。
发展
随着科技的进步和市场的变化,螺母 冷镦工艺将不断向高效、节能、环保 的方向发展,同时将不断探索新的应 用领域和市场。
02
螺母冷镦工艺流程
材料选择与准备
螺母冷镦工艺的材料选择与准备是工艺实施的基础。
要点二
技术特点
汽车行业是螺母冷镦工艺应用的重要领域,主要用于生产 汽车发动机、底盘、悬挂系统等部位所需的螺母紧固件。
汽车行业对螺母冷镦工艺的要求较高,需要保证高精度、 高强度、耐腐蚀等特性,同时要求生产效率高、成本低。
案例二:航空航天行业螺母冷镦工艺应用
应用概述
航空航天行业对紧固件的质量和性能要求极 高,因此也是螺母冷镦工艺的重要应用领域 。
技术特点
航空航天行业需要螺母冷镦工艺能够生产出 高精度、高强度、耐高温、耐腐蚀的紧固件
,同时要求产品的一致性和可靠性极高。
案例三:电子行业螺母冷镦工艺应用
应用概述
电子行业是另一个重要的螺母冷镦工艺应用领域,主要 用于生产电子产品所需的紧固件。
技术特点
电子行业对螺母冷镦工艺的要求较高,需要保证紧固件 的精度和稳定性,同时要求产品轻巧、美观,能够适应 自动化生产的需求。
冷镦知识和工艺讲解

1.1.2 塑性的评定方法
为了评定金属塑性的好坏,常用一种数值上的指标,称为塑性指标。 塑性指标是以钢材试样开始破坏瞬间的塑性变形量来表示,生产实际 中,通常用以下几种方法:
(1)拉伸试验
1.1.4 提高金属塑性及降低变形抗力的工艺措施
针对影响金属塑性及变形抗力的主要因素,结合生产实际,采取有效 的工艺措施,是完全可以提高金属塑性及降低其变形抗力的,生产中, 常采取的工艺措施有:
a.坯料状况
冷镦用原材料,除了要求化学成份、组织均匀,不要有金属夹杂等以 外,一般要对原材料进行软化退火处理,目的在于消除金属轧制时残 留在金属内部的残余应力,使组织均匀,降低硬度,要求冷镦前金属 的硬度HRB≤80。对中碳钢,合金钢一般采取球化退火,目的是除消 除应力、使组织均匀外,还可改善金属的冷变形塑性。
d.冷变形硬化对金属塑性及变形抗力的影响
金属经过冷塑性变形,引起金属的机械性能、物理性能及化学性能的 改变。随着变形程度的增加,所有的强度指标(弹性极限、比例极限、 流动极限及强度极限)都有所提高,硬度亦有所提高;塑性指标(伸 长率、断面收缩率及冲击韧性)则有所降低;电阻增加;抗腐蚀性及 导热性能降低,并改变了金属的磁性等等,在塑性变形中,金属的这 些性质变化的总和称作冷变形硬化,简称硬化。
主应力由拉应力引起的为正号,主应力由压应力引起的为负号。
在金属压力加工中,最常遇到的是同号及异号的三向主应力图。在异 号三向主应力图中,又以具有两个压应力和一个拉应力的主应力图为 最普遍。
同号的三向压应力图中,各方向的压应力均相等时(б1=б2=б3),并 且,金属内部没有疏松及其它缺陷的条件下,理论上是不可产生塑性 变形的,只有弹性变形产生。
冷镦基础知识和工艺分析课件
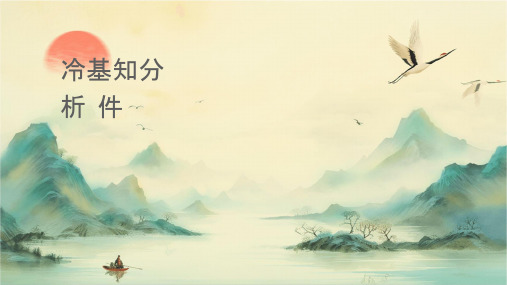
05
冷工
材料选择优化
总结词
选择合适的材料是冷镦工艺优化的关键,直接影响产品 的质量和生产效率。
详细描述
在选择材料时,应考虑材料的机械性能、加工难度、成 本等因素,根据产品用途和要求进行权衡。对于高强度、 耐磨性要求较高的产品,应选用高碳钢、合金钢等材料; 对于需要轻量化的产品,可选用铝合金、镁合金等轻质 材料。
模具设计优化
总结词
合理的模具设计能够提高冷镦产品的质量和生产效率, 降低生产成本。
详细描述
在模具设计过程中,应充分考虑产品的形状、尺寸、 精度要求等因素,合理设计模具结构、确定模具材料 和热处理工艺。同时,应注重模具的耐磨性和使用寿 命,以提高生产效率和产品质量。
设备调整优化
总结词
设备调整是实现冷镦工艺优化的重要环节,通过对设 备的合理调整可以提高生产效率和产品质量。
THANKS
感
01
02
03
04
螺栓、螺母等紧固件的生产。
汽车、摩托车等机械制造业的 零部件生产。
五金工具、电器等行业的零部 件生产。
其他需要大量金属塑性加工的 领域。
02
冷基知
冷镦材料
冷镦材料的选取对冷镦工艺的成功与 否具有决定性影响。
冷镦材料应具备足够的塑性和韧性, 以便在冷镦过程中不易开裂或破裂。 常用的冷镦材料包括低碳钢、不锈钢、 铜合金和铝合金等。
冷镦模具
冷镦模具的设计和制造质量直接影响产品的精度和生产效率。
冷镦模具应具备足够的强度和耐磨性,以确保在多次使用后 仍能保持精度。模具设计应充分考虑材料的流动性和成型性, 以获得理想的冷镦产品。
冷镦设备
冷镦设备是实现冷镦工艺的重要工具,其性能和稳定性对 生产过程具有重要影响。