铝合金加工参数
铝合金切削加工参数分析与选用
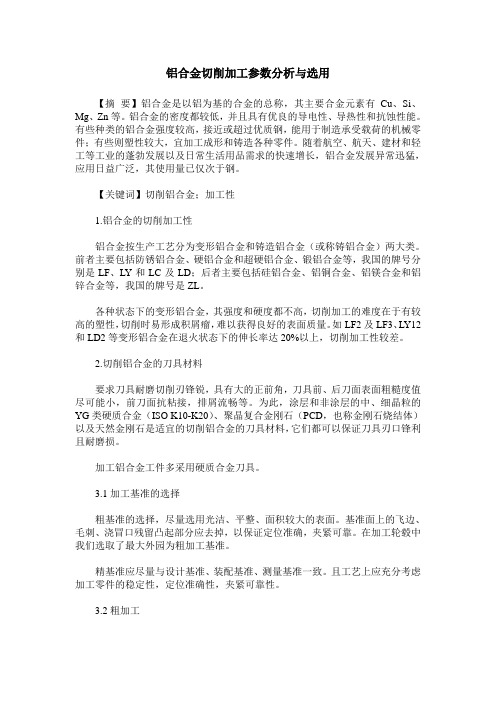
铝合金切削加工参数分析与选用【摘要】铝合金是以铝为基的合金的总称,其主要合金元素有Cu、Si、Mg、Zn等。
铝合金的密度都较低,并且具有优良的导电性、导热性和抗蚀性能。
有些种类的铝合金强度较高,接近或超过优质钢,能用于制造承受载荷的机械零件;有些则塑性较大,宜加工成形和铸造各种零件。
随着航空、航天、建材和轻工等工业的蓬勃发展以及日常生活用品需求的快速增长,铝合金发展异常迅猛,应用日益广泛,其使用量已仅次于钢。
【关键词】切削铝合金;加工性1.铝合金的切削加工性铝合金按生产工艺分为变形铝合金和铸造铝合金(或称铸铝合金)两大类。
前者主要包括防锈铝合金、硬铝合金和超硬铝合金、锻铝合金等,我国的牌号分别是LF、LY和LC及LD;后者主要包括硅铝合金、铝铜合金、铝镁合金和铝锌合金等,我国的牌号是ZL。
各种状态下的变形铝合金,其强度和硬度都不高,切削加工的难度在于有较高的塑性,切削时易形成积屑瘤,难以获得良好的表面质量。
如LF2及LF3、LY12和LD2等变形铝合金在退火状态下的伸长率达20%以上,切削加工性较差。
2.切削铝合金的刀具材料要求刀具耐磨切削刃锋锐,具有大的正前角,刀具前、后刀面表面粗糙度值尽可能小,前刀面抗粘接,排屑流畅等。
为此,涂层和非涂层的中、细晶粒的YG类硬质合金(ISO K10-K20)、聚晶复合金刚石(PCD,也称金刚石烧结体)以及天然金刚石是适宜的切削铝合金的刀具材料,它们都可以保证刀具刃口锋利且耐磨损。
加工铝合金工件多采用硬质合金刀具。
3.1加工基准的选择粗基准的选择,尽量选用光洁、平整、面积较大的表面。
基准面上的飞边、毛刺、浇冒口残留凸起部分应去掉,以保证定位准确,夹紧可靠。
在加工轮毂中我们选取了最大外园为粗加工基准。
精基准应尽量与设计基准、装配基准、测量基准一致。
且工艺上应充分考虑加工零件的稳定性,定位准确性,夹紧可靠性。
3.2粗加工由于铝合金零件加工尺寸精度和表面粗糙度预想达到高精度要求,在加工过程中必须遵循粗、精分开原则,尤其是形状复杂,精度要求较高且数量较多的零件,在精加工前对各加工面的加工余量予以去除。
常用挤压铝合金生产工艺参数表
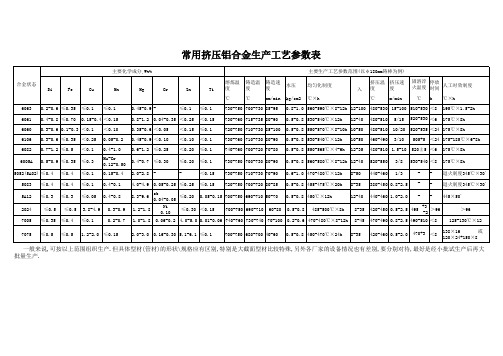
420-450 0.5-2.5 45470-490 0.8-2.5 490-510 <8 420-460 0.5-2.0 470+3 <8
1.2-2.0 ≤0.15
2.0-3.0 0.16-0.30 5.1-6.1 ≤0.1
700-750 680-700 40-60
0.5-0.8 450-470℃×24h
0.8-1.2 0.04-0.35 <0.25 0.35-0.6 <0.05 0.45-0.9 <0.10 0.6-1.2 ≤0.25 0.4-0.7 ≤0.30 2.0-2.8 <0.15 <0.10 <0.20 ≤0.20 -
0.3-0.6 0.1-0.3 <0.1 0.3-0.6 ≤0.35 0.7-1.2 ≤0.5 0.5-0.9 ≤0.35 ≤0.4 ≤0.4 ≤0.3 ≤0.5 ≤0.4 ≤0.5 <0.25 <0.1 ≤0.3 ≤0.1 ≤0.1 ≤0.05 3.8-4.9 ≤0.1
0.8-1.0 560-590℃×8-12h 12-100 480-530 15-100 510-530 <8 0.5-0.8 530-540℃×12h 12-40 480-510 5-15 520-530 <6
0.15-0.4 <0.15 <0.10 0.05-0.2 0.4-1.0 Mu-Cr 0.12-0.50 0.15-0.4 0.4-0.1 0.4-0.8 0.3-0.9 0.2-0.7
0.5-0.8 550-570℃×8-10h 10-50 0.5-0.8 530-540℃×12h 0.5-0.8 550-565℃×4-6h 10-50 12-35
480-510 10-20 520-535 <24 175℃×8h 460-490 3-10 505+5 <24 175-185℃×6-8h 175℃×8h 175℃×8h 退火制度345℃×30' 退火制度345℃×30' 445×50' >96 125-130℃×12 138×16 或 120×24+150×8
加工6061铝合金切削参数
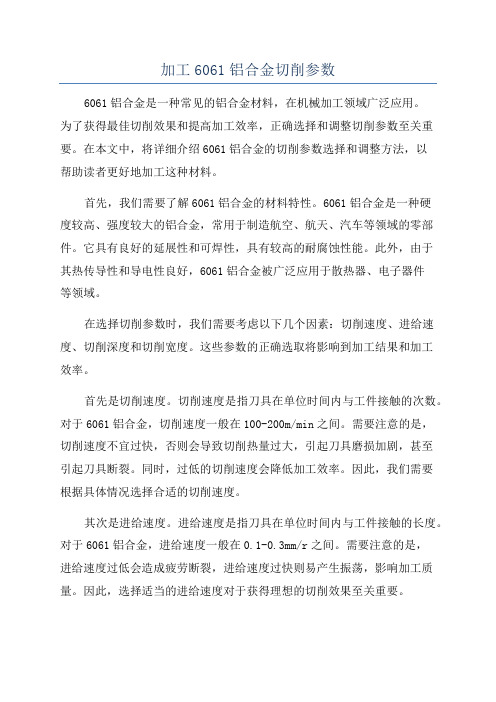
加工6061铝合金切削参数6061铝合金是一种常见的铝合金材料,在机械加工领域广泛应用。
为了获得最佳切削效果和提高加工效率,正确选择和调整切削参数至关重要。
在本文中,将详细介绍6061铝合金的切削参数选择和调整方法,以帮助读者更好地加工这种材料。
首先,我们需要了解6061铝合金的材料特性。
6061铝合金是一种硬度较高、强度较大的铝合金,常用于制造航空、航天、汽车等领域的零部件。
它具有良好的延展性和可焊性,具有较高的耐腐蚀性能。
此外,由于其热传导性和导电性良好,6061铝合金被广泛应用于散热器、电子器件等领域。
在选择切削参数时,我们需要考虑以下几个因素:切削速度、进给速度、切削深度和切削宽度。
这些参数的正确选取将影响到加工结果和加工效率。
首先是切削速度。
切削速度是指刀具在单位时间内与工件接触的次数。
对于6061铝合金,切削速度一般在100-200m/min之间。
需要注意的是,切削速度不宜过快,否则会导致切削热量过大,引起刀具磨损加剧,甚至引起刀具断裂。
同时,过低的切削速度会降低加工效率。
因此,我们需要根据具体情况选择合适的切削速度。
其次是进给速度。
进给速度是指刀具在单位时间内与工件接触的长度。
对于6061铝合金,进给速度一般在0.1-0.3mm/r之间。
需要注意的是,进给速度过低会造成疲劳断裂,进给速度过快则易产生振荡,影响加工质量。
因此,选择适当的进给速度对于获得理想的切削效果至关重要。
切削深度是指切削刀具在每次进给中切削下来的长度。
对于6061铝合金,切削深度一般在0.5-1.0mm之间。
需要注意的是,切削深度过大容易造成刀具振动,切削深度过小则会降低加工效率。
因此,选择适当的切削深度能够有效提高加工质量及效率。
最后是切削宽度。
切削宽度是指切削刀具与工件外圆或表面之间的距离。
对于6061铝合金,切削宽度一般在0.2-0.5mm之间。
需要注意的是,切削宽度过大会增加切削力,切削宽度过小则会降低加工效率。
铝合金加工参数

铝合金加工参数
由于在加工过程中发现工件刀纹不致影响表面质量,查找了一些资料,作了一些摘要:
1.由于铝合金强度和硬度相对较低,塑性较小,对刀具磨损小,且热导率较高,使切削温度较低,所以铝合金的切削加工性较好,属于易加工材料,切削速度较高,适于高速切削.但铝合金熔点较低,温度升高后塑性增大,在高温高压作用下,切削界面摩擦力很大。
容易粘刀;特别是退火状态的铝合金,不易获得低的表面粗糙度。
2.与钢材和黄铜相比,铝合金的特点,一是材质软,刚性差,二是弹性模量低,这两个因素显著影响了铝合金的切削加工性。
因此,在加工铝合金工件时,必须充分地夹紧和支撑工件,并保持刀具锋利;否则,工件往往会有离开切削刀具的倾向。
有时工件的表面出现不规则的槽痕和光亮的挤压斑,一种可能是由于刀具对工件的压力不正常引发的,还有一种可能是由于夹持不牢固而引起振颤时,刀具在工件的表面作间隙式的磨蹭,发生挤压现象和粉状切削;然后,当间隙或弹性消失时,刀具就咬人工件的表面,啃出槽痕。
3.为了获得光洁的工件表面,尽可能采用粗切削和精切削的组合,因为各种合格的工件毛坯总会有一些氧化层,致使刀具受到相当程度的磨损。
如果最后切削工序采用抛光过的锋利刀具进行精细切削,就能达到以上要求。
4.通常把铝合金的切削性分为两类:1类是指工业纯铝和硬度小于80HB的退火状态铝合金;2类是指淬火时效状态的变形铝合金。
而铝合金的切削加工工艺参数与此类别有关。
金钢石刀具的典型切削参数
铝合金的典型铣削参数
铝合金攻螺纹前的钻孔的典型参数
铝合金的典型铰孔参数
注:冷却剂为煤油-松节油(5:4)混合物;或用约33°E的矿物油, 或优质油.干铰孔的质量不高。
加工6061铝合金切削参数

加工6061铝合金切削参数6061铝合金是一种常用的高强度、耐蚀性好的铝合金材料,适用于各种加工领域,如航空航天、汽车制造、建筑等。
在进行切削加工时,合理选择切削参数可以提高加工效率和质量。
本文将从切削速度、进给量、切削深度等方面介绍6061铝合金的切削参数。
首先,切削速度是切削加工中最重要的参数之一、切削速度的选择应根据具体的刀具、切削条件和工件材料来确定。
一般来说,6061铝合金的切削速度范围为100~200 m/min。
较高的切削速度可以提高加工效率,但要注意控制切削温度,避免过高的切削温度导致刀具磨损和工件变形。
其次,进给量也是切削加工中需要关注的参数之一、进给量的选择应考虑到切削力、表面质量和切削效率等因素。
对于6061铝合金来说,一般的进给量范围为0.1~0.3 mm/r。
较大的进给量可以提高加工效率,但要注意避免过大的进给量导致切削力过大和表面质量下降。
此外,切削深度也是切削加工中需要重视的参数之一、切削深度是指每次切削时刀具切入工件的深度。
对于6061铝合金来说,一般的切削深度范围为0.5~5 mm。
切削深度的选择应根据刀具和工件的特性来确定,较大的切削深度可以提高加工效率,但要注意避免过大的切削深度导致切削力过大、刀具磨损和工件变形。
此外,刀具的选择也是影响切削参数的关键因素之一、对于6061铝合金的切削加工,通常可以选择高硬度、高刚性的硬质合金刀具。
硬质合金刀具可以更好地抵抗6061铝合金的磨损和热疲劳。
最后,还要考虑切削润滑液的选择。
切削润滑液可以降低切削温度、减小切削力和延长刀具寿命。
对于6061铝合金的切削加工,可以选择液体切削润滑剂或气体切削润滑剂。
液体切削润滑剂常用的有水溶性切削液和油类切削液,气体切削润滑剂常用的有空气、湿空气和氧气等。
总之,要合理选择6061铝合金的切削参数,需要综合考虑切削速度、进给量、切削深度、刀具选择和切削润滑液等因素。
通过合理选择切削参数,可以提高加工效率和质量,延长刀具寿命,减少切削成本。
铝合金加工参数

铝合金加工参数由于在加工过程中发现工件刀纹不致影响表面质量,查找了一些资料,作了一些摘要:1.由于铝合金强度和硬度相对较低, 塑性较小,对刀具磨损小,且热导率较高, 使切削温度较低,所以铝合金的切削加工性较好,属于易加工材料,切削速度较高, 适于高速切削.但铝合金熔点较低, 温度升高后塑性增大,在高温高压作用下,切削界面摩擦力很大。
容易粘刀;特别是退火状态的铝合金,不易获得低的表面粗糙度。
2.与钢材和黄铜相比,铝合金的特点,一是材质软,刚性差,二是弹性模量低,这两个因素显着影响了铝合金的切削加工性。
因此,在加工铝合金工件时,必须充分地夹紧和支撑工件,并保持刀具锋利;否则,工件往往会有离开切削刀具的倾向。
有时工件的表面出现不规则的槽痕和光亮的挤压斑,一种可能是由于刀具对工件的压力不正常引发的,还有一种可能是由于夹持不牢固而引起振颤时,刀具在工件的表面作间隙式的磨蹭,发生挤压现象和粉状切削;然后,当间隙或弹性消失时,刀具就咬人工件的表面,啃出槽痕。
3.为了获得光洁的工件表面,尽可能采用粗切削和精切削的组合,因为各种合格的工件毛坯总会有一些氧化层,致使刀具受到相当程度的磨损。
如果最后切削工序采用抛光过的锋利刀具进行精细切削,就能达到以上要求。
通常把铝合金的切削性分为两类:1类是指工业纯铝和硬度4.小于80H啲退火状态铝合金;2类是指淬火时效状态的变形铝合金。
而铝合金的切削加工工艺参数与此类别有关。
高速钢刀具和硬质合金刀具的典型切削参数金钢石刀具的典型切削参数铝合金的典型铣削参数铝合金麻花钻钻孔时的典型参数铝合金攻螺纹前的钻孔的典型参数铝合金的典型镗孔参数铝合金的典型铰孔参数工具(mm)如下的进给 > 10-25>>(mm/r )10注:冷却剂为煤油-松节油(5:4)混合物;或用约33° E的矿物油,或优质油. 干铰孔的质量不高。
标准铝压铸工艺参数表

标准铝压铸工艺参数表1. 压铸温度。
铝合金的压铸温度是影响产品质量的重要参数之一。
通常情况下,铝合金的压铸温度在650°C至750°C之间。
过高的温度会导致产品熔融不均匀,而过低的温度则会造成产品表面粗糙。
因此,在实际生产中,需要根据具体的铝合金材料选择合适的压铸温度。
2. 压射速度。
压射速度是指铝合金液态金属进入模腔的速度。
适当的压射速度可以确保产品充填充分,避免气孔和夹杂物的产生。
一般来说,压射速度应根据产品的形状和尺寸进行调整,以保证产品的成型质量。
3. 模具温度。
模具温度对铝合金压铸产品的表面质量和尺寸精度有着重要影响。
过高或过低的模具温度都会导致产品的缺陷,因此需要根据具体的铝合金材料和产品要求来确定合适的模具温度。
4. 注射压力。
注射压力是指压铸机对铝合金液态金属施加的压力。
适当的注射压力可以确保产品充填充分,避免产品内部产生气孔和夹杂物。
在实际生产中,需要根据产品的形状和尺寸来确定合适的注射压力。
5. 冷却时间。
冷却时间是指产品在模具中冷却的时间。
适当的冷却时间可以确保产品的尺寸精度和表面质量。
通常情况下,冷却时间需要根据产品的厚度和材料来确定,以确保产品达到理想的硬度和强度。
6. 顶杆力。
顶杆力是指顶出铝合金产品的力量。
适当的顶杆力可以确保产品顺利脱模,避免产品变形和损坏。
在实际生产中,需要根据产品的形状和尺寸来确定合适的顶杆力。
7. 模具开合力。
模具开合力是指模具在开合过程中所受的力量。
适当的模具开合力可以确保模具的正常运行,避免模具损坏和产品缺陷。
在实际生产中,需要根据模具的结构和尺寸来确定合适的模具开合力。
总结:以上是标准铝压铸工艺参数表的相关内容,希望能对大家在铝合金压铸加工过程中有所帮助。
在实际生产中,需要根据具体的产品要求和铝合金材料来确定合适的工艺参数,以确保产品质量和生产效率。
同时,也需要不断优化和调整工艺参数,以适应市场和客户需求的变化。
希望大家能够加强学习和实践,不断提升铝合金压铸加工的技术水平和质量管理水平。
pcd加工铝合金参数

pcd加工铝合金参数
PCD(聚晶金刚石)是一种高性能切削工具材料,常用于加工硬
质材料,包括铝合金。
在PCD加工铝合金时,需要考虑一些参数,以确保高效、精确的加工过程。
1. 切削速度
切削速度是指刀具切削材料的速度,通常用米/分钟(m/min)表示。
对于铝合金,建议切削速度为200-400 m/min。
当切削速度过高时,可能会导致切削工具损坏或铝合金表面产生热裂纹,而过低的切削速度则会导致加工效率低下。
2. 进给速度
进给速度是指刀具在切削中移动的速度,通常用毫米/转(mm/rev)表示。
对于铝合金,建议进给速度为0.05-0.15 mm/rev。
进给速度
过高可能导致刀具寿命缩短,而进给速度过低则会导致加工效率低下。
3. 切削深度
切削深度是指刀具在每个工作循环中切削材料的深度,通常用毫米(mm)表示。
对于铝合金,建议切削深度为1-3 mm。
切削深度过
大可能导致切削力和热量增加,从而影响刀具寿命和加工质量。
4. 刀具半径
刀具半径是指刀具切削部分的半径大小,通常用毫米(mm)表示。
对于铝合金,建议使用较小的刀具半径,以便更好地控制切削质量和表面光洁度。
5. 刀具材料
PCD刀具是PCD加工铝合金的最佳选择,因为它具有高硬度、高热稳定性和良好的耐磨性。
此外,还可以选择具有涂层的PCD刀具,以提高刀具寿命和加工效率。
总之,PCD加工铝合金需要仔细考虑各个参数,以确保高效、高质量的加工过程。
铝合金7系列和6系列加工参数
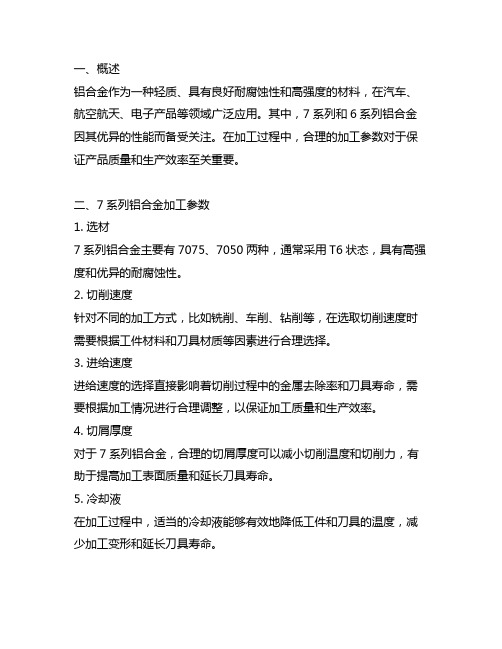
一、概述铝合金作为一种轻质、具有良好耐腐蚀性和高强度的材料,在汽车、航空航天、电子产品等领域广泛应用。
其中,7系列和6系列铝合金因其优异的性能而备受关注。
在加工过程中,合理的加工参数对于保证产品质量和生产效率至关重要。
二、7系列铝合金加工参数1. 选材7系列铝合金主要有7075、7050两种,通常采用T6状态,具有高强度和优异的耐腐蚀性。
2. 切削速度针对不同的加工方式,比如铣削、车削、钻削等,在选取切削速度时需要根据工件材料和刀具材质等因素进行合理选择。
3. 进给速度进给速度的选择直接影响着切削过程中的金属去除率和刀具寿命,需要根据加工情况进行合理调整,以保证加工质量和生产效率。
4. 切屑厚度对于7系列铝合金,合理的切屑厚度可以减小切削温度和切削力,有助于提高加工表面质量和延长刀具寿命。
5. 冷却液在加工过程中,适当的冷却液能够有效地降低工件和刀具的温度,减少加工变形和延长刀具寿命。
三、6系列铝合金加工参数1. 选材6系列铝合金主要有6061、6063两种,广泛应用于航空航天和轨道交通领域。
同样需要根据实际加工情况选择不同的状态和硬度。
2. 切削速度由于6系列铝合金具有较高的塑性,因此在选择切削速度时需要根据工件材料和刀具材质等因素进行合理调整,以避免刀具损坏和加工表面质量下降。
3. 进给速度进给速度的选择需要兼顾加工质量和生产效率,在实际加工中需要根据不同的工件和刀具情况进行合理调整。
4. 刀具材质对于6系列铝合金,选择合适的刀具材质能够有效地提高加工效率和保证加工质量。
5. 切削温度6系列铝合金的切削温度控制尤为重要,合理的切削温度能够避免刀具损坏和工件表面质量下降的问题。
四、结论7系列和6系列铝合金在实际加工中需要根据具体情况选择合适的加工参数,以保证产品质量和生产效率。
合理的切削速度、进给速度、切屑厚度等加工参数对于提高加工效率和延长刀具寿命都具有重要作用。
加工过程中的冷却液和刀具材质选择也同样重要。
pcd加工铝合金参数

pcd加工铝合金参数一、前言随着现代工业的发展,越来越多的材料被应用于各种领域。
铝合金作为一种轻质、高强度的材料,被广泛应用于汽车、航空、航天等领域。
而在铝合金的加工过程中,PCD加工是一种常用的方法。
本文将介绍PCD加工铝合金的参数设置。
二、PCD加工铝合金的参数1. 刀具选择PCD刀具是一种高效、高精度的切削工具,适用于加工铝合金等材料。
在选择PCD刀具时,需要考虑以下因素:(1)刀具形状:根据加工零件的形状和轮廓选择合适的刀具形状。
(2)刀具尺寸:根据加工零件的尺寸和要求选择合适的刀具尺寸。
(3)刀具材质:选择高品质的PCD材料,以保证刀具的寿命和加工效果。
2. 切削参数切削参数是影响加工效果的关键因素。
在PCD加工铝合金时,需要设置以下切削参数:(1)切削速度:切削速度是指刀具在加工过程中的线速度。
一般来说,切削速度越高,加工效率越高,但也会影响刀具的寿命。
在PCD加工铝合金时,切削速度一般在100-200m/min之间。
(2)进给量:进给量是指刀具在加工过程中每次切削的深度。
进给量越大,加工效率越高,但也会影响加工表面的质量。
在PCD加工铝合金时,进给量一般在0.05-0.2mm之间。
(3)切削深度:切削深度是指刀具在加工过程中每次切削的深度。
切削深度越大,加工效率越高,但也会影响加工表面的质量。
在PCD加工铝合金时,切削深度一般在1-3mm之间。
3. 冷却液选择在PCD加工铝合金时,冷却液的选择也非常重要。
冷却液可以降低加工温度,减少刀具磨损,提高加工效率。
在选择冷却液时,需要考虑以下因素:(1)冷却液的种类:根据加工材料的不同选择不同种类的冷却液。
(2)冷却液的浓度:冷却液的浓度越高,冷却效果越好,但也会影响加工表面的质量。
(3)冷却液的温度:冷却液的温度越低,冷却效果越好,但也会影响加工效率。
三、总结PCD加工铝合金是一种高效、高精度的加工方法。
在进行PCD加工铝合金时,需要选择合适的刀具、设置合理的切削参数、选择适当的冷却液。
侧铣铝合金加工参数

侧铣铝合金加工参数铝合金是一种常用的金属材料,具有轻质、强度高、导热性好等优点,在航空、汽车、电子等领域得到广泛应用。
在铝合金加工中,侧铣是一种常用的加工方法,可以用来加工平面、槽口、轮廓等形状。
为了保证加工质量和效率,合理的加工参数是非常重要的。
本文将介绍侧铣铝合金加工的一些关键参数。
1. 铣削速度:铣削速度是指刀具在加工过程中相对于工件表面的移动速度。
对于铝合金加工来说,选择合适的铣削速度可以提高加工效率、降低切削力、减少刀具磨损。
一般来说,铝合金的铣削速度较高,一般在120-300米/分钟之间。
2. 进给速度:进给速度是指刀具在单位时间内对工件的进给量。
合理的进给速度可以保证加工表面质量,控制加工温度,避免切削力过大。
对于侧铣铝合金来说,一般进给速度较快,一般在0.1-0.3毫米/刀齿。
3. 切削深度:切削深度是指刀具在一次切削中所削除的工件材料的厚度。
对于侧铣来说,切削深度的选择应根据工件的材料、硬度、刀具的强度等因素来确定。
一般来说,铝合金的切削深度不宜过大,一般在0.5-2毫米之间。
4. 刀具半径:刀具半径是指刀具的切削边缘到刀具轴线的距离。
刀具半径的选择直接影响到加工表面的粗糙度和加工效率。
对于侧铣来说,一般选择合适的刀具半径可以提高加工效率和表面质量。
5. 切削液:切削液在铝合金加工中起到冷却、润滑和清洁的作用,能够降低切削温度、减少摩擦和磨损,提高加工质量和刀具寿命。
选择适合的切削液对于侧铣铝合金加工非常重要。
6. 切削力:切削力是指刀具在加工过程中对工件的力量。
合理的切削力可以减少刀具磨损、提高加工质量,对于铝合金加工来说,一般切削力较小,但也需要根据具体情况进行调整。
在侧铣铝合金加工中,以上参数都需要根据具体情况进行调整。
不同的铝合金材料、刀具、工件形状等都会对加工参数产生影响。
因此,在实际加工过程中,需要根据实际情况进行试切和调整,以找到最佳的加工参数组合。
侧铣铝合金加工参数的选择对于保证加工质量、提高加工效率至关重要。
数控机床加工铝合金的最佳切削参数选择方法
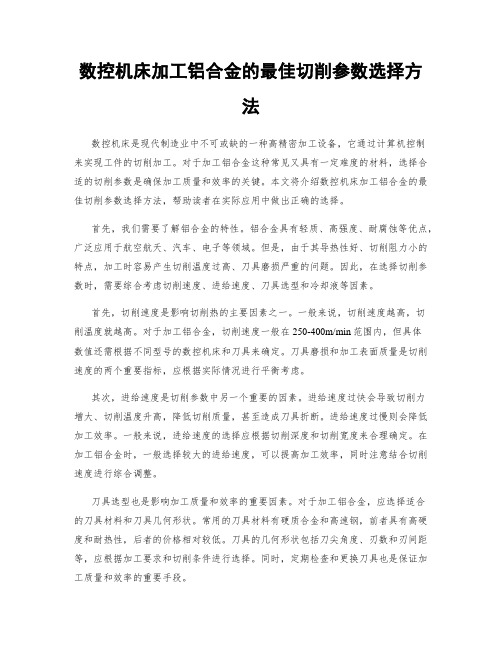
数控机床加工铝合金的最佳切削参数选择方法数控机床是现代制造业中不可或缺的一种高精密加工设备,它通过计算机控制来实现工件的切削加工。
对于加工铝合金这种常见又具有一定难度的材料,选择合适的切削参数是确保加工质量和效率的关键。
本文将介绍数控机床加工铝合金的最佳切削参数选择方法,帮助读者在实际应用中做出正确的选择。
首先,我们需要了解铝合金的特性。
铝合金具有轻质、高强度、耐腐蚀等优点,广泛应用于航空航天、汽车、电子等领域。
但是,由于其导热性好、切削阻力小的特点,加工时容易产生切削温度过高、刀具磨损严重的问题。
因此,在选择切削参数时,需要综合考虑切削速度、进给速度、刀具选型和冷却液等因素。
首先,切削速度是影响切削热的主要因素之一。
一般来说,切削速度越高,切削温度就越高。
对于加工铝合金,切削速度一般在250-400m/min范围内,但具体数值还需根据不同型号的数控机床和刀具来确定。
刀具磨损和加工表面质量是切削速度的两个重要指标,应根据实际情况进行平衡考虑。
其次,进给速度是切削参数中另一个重要的因素。
进给速度过快会导致切削力增大、切削温度升高,降低切削质量,甚至造成刀具折断。
进给速度过慢则会降低加工效率。
一般来说,进给速度的选择应根据切削深度和切削宽度来合理确定。
在加工铝合金时,一般选择较大的进给速度,可以提高加工效率,同时注意结合切削速度进行综合调整。
刀具选型也是影响加工质量和效率的重要因素。
对于加工铝合金,应选择适合的刀具材料和刀具几何形状。
常用的刀具材料有硬质合金和高速钢,前者具有高硬度和耐热性,后者的价格相对较低。
刀具的几何形状包括刀尖角度、刃数和刃间距等,应根据加工要求和切削条件进行选择。
同时,定期检查和更换刀具也是保证加工质量和效率的重要手段。
最后,冷却液的使用在加工铝合金时尤为重要。
冷却液不仅可以降低切削温度,还可以减少切削力和刀具磨损,提高加工质量和效率。
选择冷却液时应考虑其导热性、润滑性和抗腐蚀性等性能,同时要控制冷却液的喷射方式和压力,确保切削过程中刀具和工件始终处于良好的润滑和冷却状态。
m2丝锥加工铝合金的加工参数

m2丝锥加工铝合金的加工参数
加工铝合金使用M2丝锥的加工参数如下:
1. 速度:一般情况下,建议使用中速或高速进行加工,以确保加工效率和表面质量。
速度可以根据具体情况进行调整,一般在1000-2000转/分钟之间。
2. 进给量:进给量是指每分钟丝锥进给的距离。
对于铝合金,建议使用较小的进给量,以避免过度切削和过热。
进给量可以根据具体情况进行调整,一般在0.05-0.2毫米/转之间。
3. 冷却润滑剂:在加工铝合金时,应使用适当的冷却润滑剂来降低切削温度和减少切削力。
常用的冷却润滑剂包括切削液和切削蜡。
冷却润滑剂可以提高加工质量和工具寿命。
4. 切削深度:切削深度是指丝锥每次进给切削的深度。
对于铝合金,建议使用较小的切削深度,以避免过度切削和过热。
切削深度可以根据具体情况进行调整,一般在0.1-0.5毫米之间。
5. 切削角度:切削角度是指丝锥切削刃的倾斜角度。
对于铝合金,建议使用较小的切削角度,以减少切削力和切削温度。
一般来说,切削角度为5-10度之间。
需要注意的是,以上的加工参数仅供参考,具体的加工参数还需要根据具体的铝合金材料、丝锥规格和加工要求进行调整。
在实际加
工过程中,应根据试切实验和经验来确定最佳的加工参数。
铝合金加工参数

铝合金加工参数由于在加工过程中发现工件刀纹不致影响表面质量,查找了一些资料,作了一些摘要:1.由于铝合金强度和硬度相对较低,塑性较小,对刀具磨损小,且热导率较高,使切削温度较低,所以铝合金的切削加工性较好,属于易加工材料,切削速度较高,适于高速切削.但铝合金熔点较低,温度升高后塑性增大,在高温高压作用下,切削界面摩擦力很大。
容易粘刀;特别是退火状态的铝合金,不易获得低的表面粗糙度。
2.与钢材和黄铜相比,铝合金的特点,一是材质软,刚性差,二是弹性模量低,这两个因素显著影响了铝合金的切削加工性。
因此,在加工铝合金工件时,必须充分地夹紧和支撑工件,并保持刀具锋利;否则,工件往往会有离开切削刀具的倾向。
有时工件的表面出现不规则的槽痕和光亮的挤压斑,一种可能是由于刀具对工件的压力不正常引发的,还有一种可能是由于夹持不牢固而引起振颤时,刀具在工件的表面作间隙式的磨蹭,发生挤压现象和粉状切削;然后,当间隙或弹性消失时,刀具就咬人工件的表面,啃出槽痕。
3.为了获得光洁的工件表面,尽可能采用粗切削和精切削的组合,因为各种合格的工件毛坯总会有一些氧化层,致使刀具受到相当程度的磨损。
如果最后切削工序采用抛光过的锋利刀具进行精细切削,就能达到以上要求。
4.通常把铝合金的切削性分为两类:1类是指工业纯铝和硬度小于80HB的退火状态铝合金;2类是指淬火时效状态的变形铝合金。
而铝合金的切削加工工艺参数与此类别有关。
高速钢刀具和硬质合金刀具的典型切削参数金钢石刀具的典型切削参数铝合金的典型铣削参数铝合金麻花钻钻孔时的典型参数铝合金攻螺纹前的钻孔的典型参数铝合金的典型镗孔参数铝合金的典型铰孔参数注:冷却剂为煤油-松节油(5:4)混合物;或用约33°E的矿物油, 或优质油.干铰孔的质量不高。
铝合金加工参数

铝合金加工参数
1.由于铝合金强度和硬度相对较低,塑性较小,对刀具磨损小,且热导率较高,使切削温度较低,所以铝合金的切削加工性较好,属于易加工材料,切削速度较高,适于高速切削.但铝合金熔点较低,温度升高后塑性增大,在高温高压作用下,切削界面摩擦力很大。
容易粘刀;特别是退火状态的铝合金,不易获得低的表面粗糙度。
2.钢材和黄铜相比,铝合金的特点,一是材质软,刚性差,二是弹性模量低,这两个因素显著影响了铝合金的切削加工性。
因此,在加工铝合金工件时,必须充分地夹紧和支撑工件,并保持刀具锋利;否则,工件往往会有离开切削刀具的倾向。
有时工件的表面出现不规则的槽痕和光亮的挤压斑,一种可能是由于刀具对工件的压力不正常引发的,还有一种可能是由于夹持不牢固而引起振颤时,刀具在工件的表面作间隙式的磨蹭,发生挤压现象和粉状切削;然后,当间隙或弹性消失时,刀具就咬人工件的表面,啃出槽痕。
3.为了获得光洁的工件表面,尽可能采用粗切削和精切削的组合,因为各种合格的工件毛坯总会有一些氧化层,致使刀具受到相当程度的磨损。
如果最后切削工序采用抛光过的锋利刀具进行精细切削,就能达到以上要求。
4.通常把铝合金的切削性分为两类:1类是指工业纯铝和硬度小于80HB的退火状态铝合金;2类是指淬火时效状态的变形铝合金。
而铝合金的切削加工工艺参数与此类别有关。
高速钢刀具和硬质合金刀具的典型切削参数
金钢石刀具的典型切削参数
铝合金麻花钻钻孔时的典型参数
铝合金攻螺纹前的钻孔的典型参数
铝合金的典型镗孔参数
铝合金的典型铰孔参数。
铝合金锻造工艺参数

铝合金锻造工艺参数一、引言铝合金具有重量轻、强度高、耐腐蚀等优点,因此在航空航天、汽车、电子等领域得到广泛应用。
铝合金锻造是一种常见的加工方法,通过对铝合金进行锤击或挤压,使其在高温下改变形状和组织结构。
本文将介绍铝合金锻造工艺中的几个重要参数。
二、锻造温度锻造温度是铝合金锻造工艺中的重要参数之一。
铝合金的锻造温度一般在480℃~520℃之间,具体的温度取决于合金的成分和形状。
较高的锻造温度有助于提高材料的可塑性,使其更容易改变形状。
然而,过高的温度可能导致材料的晶粒长大,影响材料的力学性能。
因此,在确定锻造温度时需要综合考虑材料的可塑性和力学性能。
三、锻造速度锻造速度是指材料在锻造过程中的变形速度。
适当的锻造速度可以保证材料的均匀变形,避免出现过大的应变梯度,从而避免材料的开裂和变形不均匀。
一般情况下,锻造速度应根据锻件的形状和尺寸来确定,较大的锻件可以适当降低锻造速度,以保证变形的均匀性。
四、锻造比例锻造比例是指材料在锻造过程中的形变程度。
适当的锻造比例可以改善材料的力学性能,提高其强度和韧性。
锻造比例一般通过锻后截面积与锻前截面积的比值来表示。
较大的锻造比例可以使材料的晶粒细化,提高其强度和韧性。
然而,过大的锻造比例可能导致材料的宽度变窄,增加裂纹和缺陷的产生。
因此,在确定锻造比例时需要综合考虑材料的力学性能和形变能力。
五、锻造压力锻造压力是指施加在材料上的力大小。
适当的锻造压力可以使材料更容易变形,提高材料的可塑性。
锻造压力一般根据材料的硬度和变形能力来确定。
较高的锻造压力可以使材料更容易变形,但同时也会增加设备的负荷,增加设备的成本。
因此,在确定锻造压力时需要综合考虑材料的可塑性和设备的承载能力。
六、冷却方式冷却方式是指在铝合金锻造过程中对材料进行冷却的方式。
适当的冷却方式可以控制材料的组织结构和性能。
常用的冷却方式包括水冷和自然冷却。
水冷可以快速冷却材料,使其组织细化,提高材料的强度。
- 1、下载文档前请自行甄别文档内容的完整性,平台不提供额外的编辑、内容补充、找答案等附加服务。
- 2、"仅部分预览"的文档,不可在线预览部分如存在完整性等问题,可反馈申请退款(可完整预览的文档不适用该条件!)。
- 3、如文档侵犯您的权益,请联系客服反馈,我们会尽快为您处理(人工客服工作时间:9:00-18:30)。
铝合金加工参数
由于在加工过程中发现工件刀纹不致影响表面质量,查找了一些资料,作了一些摘要:1.由于铝合金强度和硬度相对较低,塑性较小,对刀具磨损小,且热导率较高,使切削温度较低,所以铝合金的切削加工性较好,属于易加工材料,切削速度较高,适于高速切削.但铝合金熔点较低,温度升高后塑性增大,在高温高压作用下,切削界面摩擦力很大。
容易粘刀;特别是退火状态的铝合金,不易获得低的表面粗糙度。
2.与钢材和黄铜相比,铝合金的特点,一是材质软,刚性差,二是弹性模量低,这两个因素显著影响了铝合金的切削加工性。
因此,在加工铝合金工件时,必须充分地夹紧和支撑工件,并保持刀具锋利;否则,工件往往会有离开切削刀具的倾向。
有时工件的表面出现不规则的槽痕和光亮的挤压斑,一种可能是由于刀具对工件的压力不正常引发的,还有一种可能是由于夹持不牢固而引起振颤时,刀具在工件的表面作间隙式的磨蹭,发生挤压现象和粉状切削;然后,当间隙或弹性消失时,刀具就咬人工件的表面,啃出槽痕。
3.为了获得光洁的工件表面,尽可能采用粗切削和精切削的组合,因为各种合格的工件毛坯总会有一些氧化层,致使刀具受到相当程度的磨损。
如果最后切削工序采用抛光过的锋利刀具进行精细切削,就能达到以上要求。
4.通常把铝合金的切削性分为两类:1类是指工业纯铝和硬度小于80HB的退火状态铝合金;2类是指淬火时效状态的变形铝合金。
而铝合金的切削加工工艺参数与此类别有关。
高速钢刀具和硬质合金刀具的典型切削参数
金钢石刀具的典型切削参数
铝合金的典型铣削参数
铝合金麻花钻钻孔时的典型参数
铝合金攻螺纹前的钻孔的典型参数
注:冷却剂为煤油-松节油(5:4)混合物;或用约33°E的矿物油, 或优质油.干铰孔的质量不高。