A356合金熔炼原理
《汽车轮毂用A356铝合金的精炼及净化》范文

《汽车轮毂用A356铝合金的精炼及净化》篇一一、引言随着汽车工业的飞速发展,汽车轮毂的制造材料及工艺成为行业关注的焦点。
A356铝合金因其优良的机械性能、铸造性能和抗腐蚀性能,被广泛应用于汽车轮毂的制造。
本文将详细解析A356铝合金的精炼及净化过程,以确保其达到汽车轮毂制造的高标准要求。
二、A356铝合金的基本特性A356铝合金是一种典型的压铸铝合金,具有良好的流动性和抗腐蚀性,能够满足汽车轮毂制造的严格要求。
然而,其成分中的杂质会对合金的性能产生影响,因此需要通过精炼和净化过程来提高其纯度和性能。
三、A356铝合金的精炼过程1. 原料准备:选择优质的A356铝合金原材料,进行预处理,去除表面杂质和氧化皮。
2. 熔炼:将预处理后的原材料放入熔炉中加热至熔化,这一过程需严格控制温度和时间,防止过烧和化学成分的变化。
3. 除气精炼:熔化后的铝液需通过除气机进行除气处理,以去除其中的氢气和其它气体杂质。
这一步骤对于提高合金的纯净度和机械性能至关重要。
4. 熔剂覆盖:在铝液表面覆盖一层熔剂,以防止空气和杂质的侵入,并进一步保护铝液的纯净度。
四、A356铝合金的净化过程1. 机械过滤:利用滤网等设备对铝液进行机械过滤,去除其中的固体杂质和悬浮颗粒。
2. 静置沉降:经过机械过滤后的铝液需静置一段时间,使微小杂质在重力的作用下沉降到底部。
3. 真空净化:采用真空技术对铝液进行进一步净化,通过降低压力使气体和杂质在铝液中上浮至表面,便于去除。
五、精炼及净化后的效果与质量控制经过精炼及净化后的A356铝合金,其纯度和性能得到显著提高,能够满足汽车轮毂制造的高标准要求。
为确保产品质量,需对精炼及净化后的铝合金进行严格的质量检测和控制,包括化学成分分析、机械性能测试等。
此外,还需对生产过程中的关键环节进行监控和记录,确保产品质量可追溯。
六、结论本文详细解析了汽车轮毂用A356铝合金的精炼及净化过程。
通过严格的精炼和净化措施,可以有效提高A356铝合金的纯度和性能,满足汽车轮毂制造的高标准要求。
A356铝合金半固态流变成形中的凝固行为及组织控制

A356铝合金半固态流变成形中的凝固行为及组织控制A356铝合金半固态流变成形中的凝固行为及组织控制摘要: A356铝合金是一种广泛应用于航空、汽车等领域的热处理铝合金,半固态流变成形是一种有效改善A356铝合金成形性能的技术。
本文通过研究A356铝合金半固态流变成形过程中的凝固行为及组织控制,旨在探索其对材料性能的影响,为铝合金半固态流变成形工艺的优化提供理论依据。
1. 引言随着工业技术的不断发展,高性能铝合金逐渐成为替代传统材料的理想选择。
A356铝合金作为一种常用的铝合金,具有优异的机械性能和耐腐蚀性能,在航空、汽车及其他工业领域被广泛应用。
然而,传统的铸造工艺制备A356铝合金存在着铸件缺陷、微观组织不均匀等问题,严重制约了其进一步发展。
半固态流变成形技术通过控制铝合金在半固态状态下的流变特性,可以有效改善铝合金的成形性能和材料的微观组织,成为铝合金加工的重要方法之一。
2. A356铝合金半固态流变成形的基本原理A356铝合金在半固态状态下的流变行为受到凝固行为的影响较大。
凝固是指熔融金属在冷却过程中由液态向固态转化的过程。
在半固态流变成形过程中,凝固过程会影响材料的流变性能和组织形成,因此对凝固行为的研究是研究A356铝合金半固态流变成形的重要前提。
3. A356铝合金半固态凝固行为的研究现状目前,对于A356铝合金半固态凝固行为的研究主要集中在以下几个方面:凝固曲线的测定与分析、凝固过程中的晶粒生长和凝固组织形成机制的研究、凝固活动能和凝固时间的计算等。
通过对凝固行为的研究,可以揭示铝合金在半固态状态下的变形行为,并为合理控制材料的组织形成提供理论基础。
4. A356铝合金半固态流变成形中的组织控制半固态流变成形过程中,通过合理控制A356铝合金的凝固行为,可以实现对材料组织的精确控制,进而影响材料的性能。
常见的组织控制方法包括凝固速率控制、液固相体积分数控制、添加剂控制等。
通过组织控制,可以调节材料的晶粒尺寸、相分布、亚稳相含量等,进而实现优化材料性能的目的。
铝合金的精炼、变质与细化答辩

10
精炼剂加入量0.019%时 在740℃取样(图7)
图7 气孔缺陷图
变质加入与否样品对比
11
图8 730℃未加入变质剂样 品图
图9 725℃加入变质剂 0.02%后样品图
细化剂加入与否的对比
12
图10 730℃未加入细化剂 样品图
图11 728℃加入细化剂 量0.12%样品图
型模具。
• 成品取样:用切割机在铝锭的中间处取约50mm 长度的试样。
金相试样的制备
• 切样和铣样:将所取样品切成合适大小的 试样,然后铣平整。 • 磨样:磨光分为粗磨、中磨、细磨。
• 抛光:去除金相磨面上因细磨而留下的磨 痕。 • 浸蚀:用浸蚀剂对试样浸蚀,以便于对组 织的观察。
6
金相试样的观察结果
配料计算 装炉 熔炼 喷吹精炼 扒渣 变质 搅拌 成分调整
不合格
4
检验包装
剪切码垛
牵引矫直
铸造
在线过滤
在线除气
取样分析
合格
静置保温
放料
取样
• 取样工具:长柄样勺、短柄样勺和饼型模具。 • 炉内取样:要用长柄样勺在炉膛内的中心处取样
5
,铝液取出后要倒入饼型模具。
• 炉外取样:在溜槽内用短柄样勺取样之后倒入饼
A356铝合金的精炼、变质和细化 工艺的研究
课题的提出
• A356铝合金是汽车轮毂的原料,虽然其具 有优良的力学性能,但是没有经过精炼、 变质和细化的A356铝合金具有晶粒粗大、 硅相质脆、吸气氧化等问题。因此,本文 对A356铝合金的精炼、变质和细化工艺进 行研究。
2
主要研究内容
• (1)A356铝合金存在的缺陷及精炼工艺
13
A356合金熔炼原理

A356合金熔炼原理一、铝轮毂采用的合金及化学成分现代汽车铸造铝合金车轮应用最广的材料是美国材料与试验协会(ASTM)牌号A356合金,相当于中国ZL101A、日本AC4CH、德国AlSi7Mg、法国A-S7G03、俄罗斯Aл9-1。
除A356合金外,德国还采用AlSi9Mg、AlSi10Mg、AlSi11Mg,法国还采用A-S11G、A-S12.5。
这些高Si合金都不热处理,它们液态流动性好、补缩能力强、铸造性能好、铸造缺陷少。
但机械性能和机加工艺性能不如A356合金。
A356合金又分为A356.2、A356.1、A356.0,其化学成分,分别为下表:二、熔炼温度和时间控制A356合金大约在580℃时开始有液态出现,到640℃就可全部熔化,一般最高熔炼温度控制在760℃,铝液温度超过770℃,明显开始氧化,夹杂物和含气量大幅增加,凝固后组织晶粒也会粗大,铝液质量开始下降。
所以,对A356合金的熔炼时,低温熔炼有利提高铝液质量,提高材料的机械性能。
请看下图:氧化物增量μg /c ㎡h640 700 770 800 ℃温度→温度对铝合金液氧化的影响另外A356合金熔化时,时间不能太长,特别是在高温下保温时间太长,不利于铝液质量。
浇注温度也不能太高,低压铸造浇注温度一般在685~710℃,重力铸造一般控制在730℃左右。
国内铝合金车轮生产厂家,凡采用低压铸造工艺,都用中间包转运铝液,并进行除渣除气,如中间包烤的不好,铝液在中间包降温很快,一般铝液出炉温度控制在760℃,也有控制在770℃,如果选好的烤包器,中间包温度可烤到600℃,这样铝液降温就慢,铝液可在740℃出炉。
铝液质量就会大大提高,而烧损也少。
三、熔炼过程对环境水分控制A356合金在熔炼过程中,空气含水蒸气的量,原材料含水量,炉膛和工具吸水量,精练剂和打渣剂含水量,旋转除气中氩气或氮气含水量,低压铸造机用的压缩空气含水量等等,这些都与铝合金液接触,都能与铝液起以下反应:2Al (l )+3H 2O (g )=r-Al 2O 3+6[H]这个反映比铝液和空气中的氧反应还激烈,当水含量为10-21时,上述反应仍然进行,即使铝液表面有氧化膜保护时,这个反应也能进行。
《汽车轮毂用A356铝合金的精炼及净化》范文
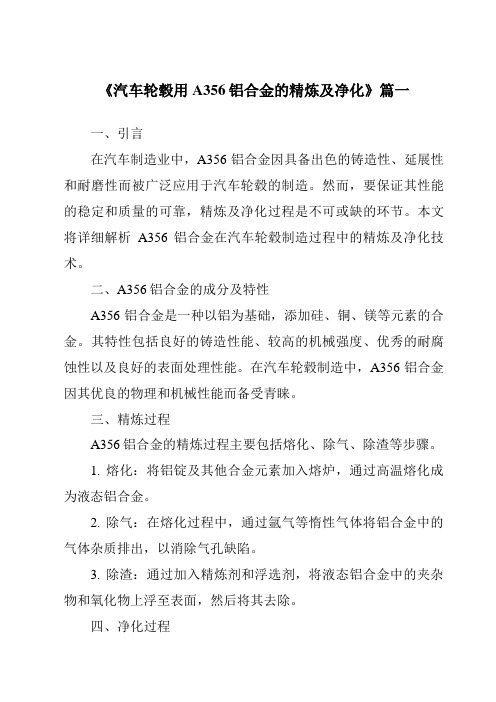
《汽车轮毂用A356铝合金的精炼及净化》篇一一、引言在汽车制造业中,A356铝合金因具备出色的铸造性、延展性和耐磨性而被广泛应用于汽车轮毂的制造。
然而,要保证其性能的稳定和质量的可靠,精炼及净化过程是不可或缺的环节。
本文将详细解析A356铝合金在汽车轮毂制造过程中的精炼及净化技术。
二、A356铝合金的成分及特性A356铝合金是一种以铝为基础,添加硅、铜、镁等元素的合金。
其特性包括良好的铸造性能、较高的机械强度、优秀的耐腐蚀性以及良好的表面处理性能。
在汽车轮毂制造中,A356铝合金因其优良的物理和机械性能而备受青睐。
三、精炼过程A356铝合金的精炼过程主要包括熔化、除气、除渣等步骤。
1. 熔化:将铝锭及其他合金元素加入熔炉,通过高温熔化成为液态铝合金。
2. 除气:在熔化过程中,通过氩气等惰性气体将铝合金中的气体杂质排出,以消除气孔缺陷。
3. 除渣:通过加入精炼剂和浮选剂,将液态铝合金中的夹杂物和氧化物上浮至表面,然后将其去除。
四、净化过程净化过程主要是通过化学和物理方法进一步去除A356铝合金中的杂质,提高其纯度和性能。
1. 化学净化:通过添加特定的化学试剂,与合金中的杂质发生化学反应,生成无害或低害的化合物,并通过精炼和浮选将其去除。
2. 物理净化:利用离心分离、真空蒸馏等技术,通过物理方法去除合金中的杂质和气体。
五、工艺控制及优化为了确保A356铝合金的精炼及净化效果,需要对整个过程进行严格的工艺控制及优化。
这包括控制熔炼温度、精炼剂和浮选剂的添加量、除气和除渣的时间和频率等。
此外,还需要定期对设备进行维护和检修,确保其正常运行和良好的工作状态。
六、结论A356铝合金的精炼及净化过程是汽车轮毂制造中不可或缺的环节。
通过精炼和净化,可以有效地去除合金中的杂质和气体,提高其纯度和性能,从而保证汽车轮毂的质量和性能。
在未来的汽车制造业中,随着对材料性能和质量的不断要求提高,A356铝合金的精炼及净化技术将不断得到优化和发展。
a356t6热处理标准

a356t6热处理标准
A356是一种铝合金,通常用于制造零件和构件,而热处理是一
种用来改变材料性能和结构的工艺。
针对A356铝合金的热处理标准
通常是根据具体应用和要求来制定的。
一般来说,A356铝合金的热
处理标准包括时效处理和固溶处理。
在时效处理中,A356铝合金经过固溶处理后,会进行人工时效
处理,通过控制温度和时间来达到所需的强度和硬度。
这个过程可
以显著提高合金的强度和耐腐蚀性能。
固溶处理是A356铝合金热处理的另一种方式,通过加热合金至
固溶温度,然后迅速冷却来改变合金的结构和性能。
这种处理可以
消除合金中的固溶体和沉淀相,从而提高其塑性和加工性能。
除了以上两种常见的热处理方法外,针对具体的应用和要求,
还可能会有其他特定的热处理标准。
这些标准可能涉及到温度、时间、冷却速率等具体参数的要求,以确保合金达到所需的性能指标。
总的来说,A356铝合金的热处理标准是根据具体的工程要求和
材料性能来制定的,可以通过精确控制热处理工艺来实现所需的性
能和结构。
希望这个回答能够全面回答你关于A356铝合金热处理标准的问题。
A356铝合金及性能研究

A356铝合金的组织及性能研究目录摘要错误!未指定书签。
错误!未指定书签。
1 绪论错误!未指定书签。
1.1 引言错误!未指定书签。
1.2 铝及其合金概述错误!未指定书签。
1.3 热处理工艺错误!未指定书签。
1.4 A356铝合金研究现状错误!未指定书签。
1.5 主要内容错误!未指定书签。
2 实验方法及过程错误!未指定书签。
2.1 合金成分错误!未指定书签。
2.2 试样制备和热处理方法错误!未指定书签。
2.2.1 试样切割.......................... 错误!未指定书签。
2.2.2 热处理............................ 错误!未指定书签。
2.3 金相观察错误!未指定书签。
2.3.1 金相试样的制备错误!未指定书签。
2.3.2 金相观察错误!未指定书签。
2.4 力学性能的测试错误!未指定书签。
2.4.1 硬度测试错误!未指定书签。
2.4.2 拉伸性能测试错误!未指定书签。
3 实验结果及分析错误!未指定书签。
3.1 金相组织观察结果错误!未指定书签。
3.1.1 热处理前的微观组织错误!未指定书签。
3.1.2 热处理后的微观组织错误!未指定书签。
3.2 力学性能分析错误!未指定书签。
3.2.1 表面硬度错误!未指定书签。
3.2.2 拉伸性能错误!未指定书签。
4 结论错误!未指定书签。
致谢错误!未指定书签。
参考文献错误!未指定书签。
百色学院本科毕业论文(设计)诚信保证书错误!未指定书签。
错误!未定义书签。
摘要:对A356铝合金分别进行金相观察和力学试验,研究其微观组织及性能,同时探讨热处理方式对A356铝合金组织及性能的影响,结果发现枝状晶比较粗大,分布松散,表面硬度、抗拉强度和屈服强度都较低,塑性较好。
经一定热处理后,粗大共晶硅熔断形成分布均匀、趋于球化的细小颗粒,除了塑性有所降低外,其他力学性能都有了显著提高。
最佳热处理工艺为(560℃+6h)固溶+(180℃+4h)人工时效。
A356.2铝合金圆铸棒炉前熔炼工艺控制

A356.2铝合金圆铸棒炉前熔炼工艺控制作者:张新奎来源:《科学与财富》2021年第02期摘要:A356.2铝合金是一个典型的AL-Si-Mg系三元合金。
它具有较好的流动性,良好的塑性和高冲压韧性,是汽车铸造轮毂的首选材质。
本文就A356.2铝合金圆铸棒炉前熔炼工艺进行总结,以便进一步规范及提高A356.2铝合金圆铸棒熔炼质量。
关键词:铝合金;圆铸棒;配料;精炼A356合金是美国铝业协会标准中的一个牌号系列,这个系列有三个合金:A356.0、A356.1、 A356.2。
其中A356.2合金是一个典型的AL-Si-Mg系三元合金。
它具有较好的流动性,线收缩小,无热裂倾向,可铸造薄壁和形状复杂的铸件。
而且通过热处理可达到较高的强度,良好的塑性和高冲压韧性,是汽车铸造轮毂的首选材质。
A356.2铝合金圆铸棒市场需求较大,但必须首要管控好炉前熔炼工艺操作。
1 熔炼前的准备A356.2化学成份主要成份为镁0.3%-0.45%;硅6.5%-7.5%;铁0.12%;其它杂质范围为微量。
本公司电解铝液均采用9985%AL来组织生产A356.2合金。
镁锭及硅锭投炉入料之前都必须要求无水分、泥砂、油污,带水的铝屑应烘干。
炉子在停歇后,若为冷炉状态,应对炉子进行预热,使炉膛温度达到700℃~800℃左右。
A356.2铝合金一般熔炼工艺都控制熔炼温度在760℃以下。
当铝液温度超过770℃时明显开始氧化,夹杂物和含气量大幅增加,凝固后组织晶粒也会粗大,铝液质量开始下降,材料机械性能变坏。
所以A356.2铝液熔炼温度应控制在770℃以内。
2 配料工艺控制2.1 A356.2配料工艺流程电解原铝液检斤后拉入熔铸车间→组织炉前单包取样,确认铁成份合格→组织天车吊运原铝液抬包倒入熔炼炉→加入硅锭,加入细化剂,高温熔化一个小时→加入固体料降温→ 加入镁锭→搅拌10-20分钟→取样分析→精炼30分钟→ 扒渣→静置20-30分钟组织铸造。
01_A356合金的熔炼
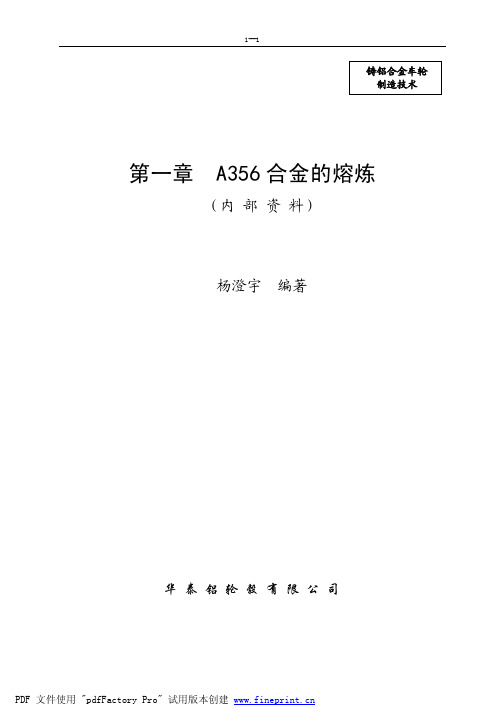
第一章 A356合金的熔炼(内部资料)杨澄宇编著华泰铝轮毂有限公司目录第1章A356合金的熔炼………………………………………………………………1-1 1.1 熔炼用的原材料…………………………………………………………………1-11.1.1 A356合金锭和各合金元素的作用…………………………………………1-11.1.2 回炉料的分级和回用………………………………………………………1-11.1.3 精炼剂………………………………………………………………………1-21.1.4 清渣剂………………………………………………………………………1-31.1.5 合金细化用的中间合金……………………………………………………1-31.2 A356合金熔炼设备………………………………………………………………1-31.2.1 铝合金快速集中熔化炉及投料机…………………………………………1-31.2.2 2.1t/h铝锭、铝屑兼用熔化保持炉…………………………………………1-41.熔化炉设备主要构成…………………………………………………………1-42.2.1t/h铝锭、铝屑兼用熔化炉正面配置图……………………………………1-53.铝锭、铝屑熔化炉设备流程图………………………………………………1-54.铝屑熔化炉熔化示意图………………………………………………………1-65.主要技术指标和操作要点……………………………………………………1-71.2.3 中间包及中间包预热装置…………………………………………………1-81.2.4 熔炼用的工具………………………………………………………………1-91.浇包…………………………………………………………………………1-92.撇渣勺…………………………………………………………………………1-93.钟形罩…………………………………………………………………………1-94.压罩…………………………………………………………………………1-101.2.5 石墨转子除气机……………………………………………………………1-101.石墨转子使用寿命……………………………………………………………1-112.石墨转子尺寸…………………………………………………………………1-111.3 A356合金熔炼工艺………………………………………………………………1-111.3.1 熔炼温度和时间……………………………………………………………1-111.3.2 熔炼过程中的吸气…………………………………………………………1-121.3.3 熔炼过程中的氧化…………………………………………………………1-121.3.4 熔炼过程中的精炼(炉内精炼)…………………………………………1-13 1.3.5 熔炼过程中的清渣…………………………………………………………1-14 1.3.6 熔炼过程中的合金细化……………………………………………………1-14 1.3.7 熔炼中的合金变质…………………………………………………………1-14 1.3.8 A356合金的炉外精炼………………………………………………………1-15 1.3.9 A356合金典型熔炼工艺……………………………………………………1-161.熔炼前的准备…………………………………………………………………1-162.配料准备………………………………………………………………………1-163.装料次序………………………………………………………………………1-164.熔化和精炼……………………………………………………………………1-16 1.4 A356合金熔炼铝液质量…………………………………………………………1-17 1.4.1 什么铝液为合格的铝液……………………………………………………1-17 1.4.2 铝液中氢含量与铸件的针孔………………………………………………1-17 1.4.3 铝液中夹杂物含量与铸件的渣孔…………………………………………1-18 1.4.4 A356合金铝液的流动性……………………………………………………1-19 1.4.5 A356合金铝液凝固时的收缩性……………………………………………1-19 1.5 熔炼工序设备……………………………………………………………………1-19 1.5.1快速集中熔化炉………………………………………………………………1-191.设备值点检……………………………………………………………………1-192.泄漏试验………………………………………………………………………1-203.安全动作确认…………………………………………………………………1-20 1.5.2保温炉………………………………………………………………………1-21 1.5.3除气机………………………………………………………………………1-211.传动机构………………………………………………………………………1-212.升降机构………………………………………………………………………1-21第1章 A356合金的熔炼1.1 熔炼用的原材料1.1.1 A356合金锭和各合金元素的作用生产铝合金车轮各工厂采购进来的A356合金锭称作A356.2,熔炼过程中的合金称A356.1,产品的合金称A356.0。
A356合金熔体重氢气的来源及控制共5页

A356合金熔体重氢气的来源及控制A356合金在铸造生产中,熔体的含氢量直接影响铸锭的冶金质量,并对最终产品的轮毂的力学性能、加工性能、抗蚀性、外观质量等造成很大的影响,因此,如何降低铝熔体重的含氢量、获得纯洁度高的A356合金熔体,就成了A356合金生产企业及轮毂生产企业生产工作者认真研究的课题,本文就A356合金熔体氢气的来源及处理方法进行了系统的分析,并提出了具体的预防、处理措施。
1、A356合金熔体中气体的种类A356合金在熔炼过程中,由于加热方法及熔炼炉材料不同,接触的炉气成分不同,主要有:氢气、氧气、水蒸气、二氧化碳等,这些气体主要有燃料燃烧产生的,而耐火材料、金属炉料及熔剂、工具等也带入一定量的气体。
炉气成分使由燃料种类及空气量来决定的。
普通焦炭坩埚炉炉气的主要成分为二氧化碳、一氧化碳和氮气。
煤气、柴油炉炉气成分主要为水蒸气和氮气,而对于电炉来说主要是氢气,因此,采用不同的熔化炉时,A356合金吸气量和产生针孔的程度是不同的。
铝合金生产实践证明,氢是唯一能大量溶解于铝或铝合金中的气体,是导致铝合金形成气孔的主要原因,是铝合金中最有害的气体,也是铝合金中溶解度最大的气体。
在铸件凝固过程中由于氢的析出而产生的孔隙,不仅减少了铸件的实际截面积而且是裂纹源。
由于针孔主要是氢气造成的,而在铝合金熔炼时,周围空气中的氢气含量并不多,氢的最通常的来源是铝和水蒸气的反应,因此,熔炼过程中造成水蒸气的原因也就是直接影响针孔的形成,其主要因素如下:①原材料、辅助材料的影响;②空气中绝对湿度大、会增加合金气体溶解量,形成季节性气孔;③合金熔化作影响:生产实践表明,铝液吸气是在表面进行的,与合金熔炼温度、熔炼时间等有较大关系。
合金熔化温度越高,熔化时间和熔化后的铝液保持时间越长,氢在铝液中扩撒越充分,铝液吸氢量就越大,出现针孔的几率就越大。
④熔炼设备及工具的影响:预热不到位,如铸模潮湿,有油污、含水量高,浇铸的合金锭含氢量高;A356合金易产生针孔缺陷,既与A356合金本身特性有关,也和一系列的外界因素有关,为避免A356合金锭中出现针孔,可采取适当的措施:①严格控制原材料的含氢量和夹杂量,铝液中气体和氧化夹杂含量与炉料中气体给氧化夹杂原始含量有关,为获得高质量的熔液,所加入的炉料必须充分预热,对于低质量的炉料或炉料在贮存过程中受潮,甚至表面严重氧化,则需进行重熔处理,重熔时,要严格控制熔炼工艺和精炼工艺。
《汽车轮毂用A356铝合金的精炼及净化》

《汽车轮毂用A356铝合金的精炼及净化》篇一一、引言随着汽车工业的快速发展,汽车轮毂作为车辆重要的承载和转向部件,其材质和制造工艺逐渐成为行业内研究的重点。
A356铝合金因其良好的铸造性能、机械性能和抗腐蚀性能,被广泛应用于汽车轮毂的制造中。
然而,A356铝合金的精炼及净化过程对最终产品的性能和质量具有重要影响。
本文将详细探讨A356铝合金的精炼及净化工艺,旨在为汽车轮毂制造提供理论基础和实践指导。
二、A356铝合金的特性A356铝合金是一种典型的铸造铝合金,具有优异的流动性、热导性和耐腐蚀性。
它主要含有铝、硅、铜等元素,通过合理的成分比例和热处理工艺,可以获得良好的机械性能和加工性能。
在汽车轮毂制造中,A356铝合金因其良好的铸造性能和抗腐蚀性能而得到广泛应用。
三、A356铝合金的精炼过程A356铝合金的精炼过程主要包括熔炼、除气、除渣等步骤。
首先,将原材料按照一定比例加入熔炼炉中,通过高温熔化得到液态铝合金。
然后,通过除气剂的使用,将液态铝合金中的气体杂质去除。
此外,还需通过机械搅拌和过滤等手段,去除液态铝合金中的非金属夹杂物和氧化皮等杂质。
这一过程对提高A356铝合金的纯度和性能至关重要。
四、A356铝合金的净化工艺A356铝合金的净化工艺主要包括熔剂处理、真空处理和过滤等步骤。
熔剂处理是通过在液态铝合金表面覆盖一层熔剂,防止空气中的杂质和氧化物的侵入。
真空处理则是利用真空环境,将液态铝合金中的气体杂质进一步去除。
过滤则是通过使用过滤网等设备,去除液态铝合金中的夹杂物和氧化物。
这些净化工艺可以有效提高A356铝合金的纯度和性能,为汽车轮毂的制造提供优质的原材料。
五、实践应用及效果在汽车轮毂制造过程中,采用精炼及净化后的A356铝合金,可以有效提高轮毂的机械性能、抗腐蚀性能和外观质量。
同时,精炼及净化工艺还可以降低杂质含量,提高合金的流动性,有利于轮毂的铸造和加工。
此外,通过优化精炼及净化工艺参数,还可以进一步提高A356铝合金的性能,为汽车轮毂的轻量化、高性能化提供有力支持。
《汽车轮毂用A356铝合金的精炼及净化》

《汽车轮毂用A356铝合金的精炼及净化》篇一一、引言随着汽车工业的快速发展,对汽车零部件的性能和质量要求也越来越高。
其中,汽车轮毂作为车辆的重要组成部分,其材料的选择和制造工艺的优化显得尤为重要。
A356铝合金因其良好的铸造性能、力学性能和抗腐蚀性能,被广泛应用于汽车轮毂的制造。
本文将详细介绍A356铝合金的精炼及净化工艺,以期为相关领域的研究和应用提供参考。
二、A356铝合金的成分及特性A356铝合金是一种以铝为基础,含有硅、铜、镁等元素的合金。
其具有良好的铸造性能、优良的力学性能、抗腐蚀性能和可回收性等特点。
此外,A356铝合金的流动性好,适合铸造复杂形状的零部件,因此被广泛应用于汽车轮毂的制造。
三、精炼工艺A356铝合金的精炼工艺主要包括熔炼、除气、除渣等步骤。
1. 熔炼:将A356铝合金的原料按照一定比例加入熔炉中,通过高温熔化得到液态铝合金。
熔炼过程中需严格控制温度和时间,以确保合金元素的充分溶解和均匀分布。
2. 除气:在液态铝合金中,会溶解一定量的气体,如氢气等。
这些气体会对合金的性能产生不利影响。
因此,需要采用真空除气法或气泡法等方法,将液态铝合金中的气体排除。
3. 除渣:在熔炼和除气过程中,会产生一些杂质和氧化皮等浮渣。
这些浮渣会污染液态铝合金,影响其性能。
因此,需要采用机械或化学方法,将浮渣从液态铝合金中去除。
四、净化工艺A356铝合金的净化工艺主要包括熔剂净化、气体搅拌和静置处理等步骤。
1. 熔剂净化:在精炼后的液态铝合金中加入一定量的熔剂,通过化学反应将杂质和氧化物等杂质去除。
常用的熔剂有氯化物、氟化物等。
2. 气体搅拌:通过气体搅拌法使液态铝合金中的杂质更好地聚集在液体表面,以便于后续的去除操作。
3. 静置处理:在经过上述处理后,将液态铝合金静置一段时间,使其中的杂质和气体进一步上浮或下沉,从而达到净化的目的。
五、结论通过对A356铝合金进行精炼和净化处理,可以有效提高其纯度和性能,满足汽车轮毂等零部件的制造要求。
01_A356合金的熔炼
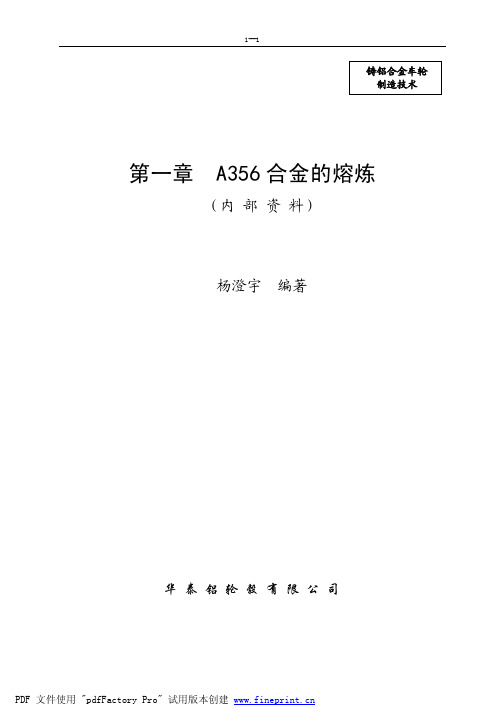
第一章 A356合金的熔炼(内部资料)杨澄宇编著华泰铝轮毂有限公司目录第1章A356合金的熔炼………………………………………………………………1-1 1.1 熔炼用的原材料…………………………………………………………………1-11.1.1 A356合金锭和各合金元素的作用…………………………………………1-11.1.2 回炉料的分级和回用………………………………………………………1-11.1.3 精炼剂………………………………………………………………………1-21.1.4 清渣剂………………………………………………………………………1-31.1.5 合金细化用的中间合金……………………………………………………1-31.2 A356合金熔炼设备………………………………………………………………1-31.2.1 铝合金快速集中熔化炉及投料机…………………………………………1-31.2.2 2.1t/h铝锭、铝屑兼用熔化保持炉…………………………………………1-41.熔化炉设备主要构成…………………………………………………………1-42.2.1t/h铝锭、铝屑兼用熔化炉正面配置图……………………………………1-53.铝锭、铝屑熔化炉设备流程图………………………………………………1-54.铝屑熔化炉熔化示意图………………………………………………………1-65.主要技术指标和操作要点……………………………………………………1-71.2.3 中间包及中间包预热装置…………………………………………………1-81.2.4 熔炼用的工具………………………………………………………………1-91.浇包…………………………………………………………………………1-92.撇渣勺…………………………………………………………………………1-93.钟形罩…………………………………………………………………………1-94.压罩…………………………………………………………………………1-101.2.5 石墨转子除气机……………………………………………………………1-101.石墨转子使用寿命……………………………………………………………1-112.石墨转子尺寸…………………………………………………………………1-111.3 A356合金熔炼工艺………………………………………………………………1-111.3.1 熔炼温度和时间……………………………………………………………1-111.3.2 熔炼过程中的吸气…………………………………………………………1-121.3.3 熔炼过程中的氧化…………………………………………………………1-121.3.4 熔炼过程中的精炼(炉内精炼)…………………………………………1-13 1.3.5 熔炼过程中的清渣…………………………………………………………1-14 1.3.6 熔炼过程中的合金细化……………………………………………………1-14 1.3.7 熔炼中的合金变质…………………………………………………………1-14 1.3.8 A356合金的炉外精炼………………………………………………………1-15 1.3.9 A356合金典型熔炼工艺……………………………………………………1-161.熔炼前的准备…………………………………………………………………1-162.配料准备………………………………………………………………………1-163.装料次序………………………………………………………………………1-164.熔化和精炼……………………………………………………………………1-16 1.4 A356合金熔炼铝液质量…………………………………………………………1-17 1.4.1 什么铝液为合格的铝液……………………………………………………1-17 1.4.2 铝液中氢含量与铸件的针孔………………………………………………1-17 1.4.3 铝液中夹杂物含量与铸件的渣孔…………………………………………1-18 1.4.4 A356合金铝液的流动性……………………………………………………1-19 1.4.5 A356合金铝液凝固时的收缩性……………………………………………1-19 1.5 熔炼工序设备……………………………………………………………………1-19 1.5.1快速集中熔化炉………………………………………………………………1-191.设备值点检……………………………………………………………………1-192.泄漏试验………………………………………………………………………1-203.安全动作确认…………………………………………………………………1-20 1.5.2保温炉………………………………………………………………………1-21 1.5.3除气机………………………………………………………………………1-211.传动机构………………………………………………………………………1-212.升降机构………………………………………………………………………1-21第1章 A356合金的熔炼1.1 熔炼用的原材料1.1.1 A356合金锭和各合金元素的作用生产铝合金车轮各工厂采购进来的A356合金锭称作A356.2,熔炼过程中的合金称A356.1,产品的合金称A356.0。
《汽车轮毂用A356铝合金的精炼及净化》范文
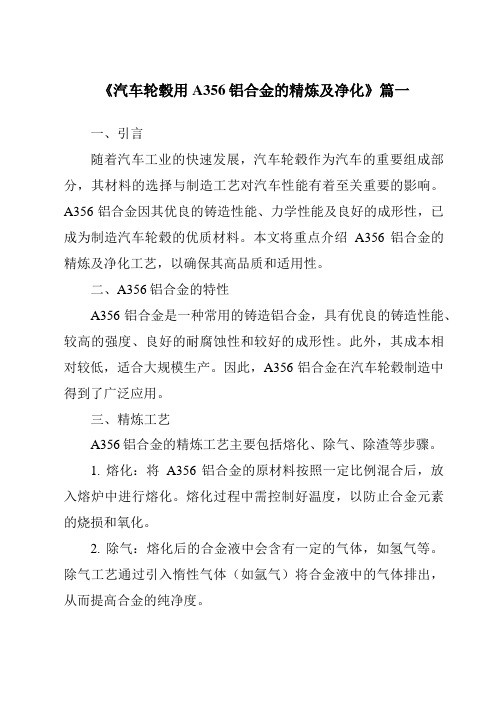
《汽车轮毂用A356铝合金的精炼及净化》篇一一、引言随着汽车工业的快速发展,汽车轮毂作为汽车的重要组成部分,其材料的选择与制造工艺对汽车性能有着至关重要的影响。
A356铝合金因其优良的铸造性能、力学性能及良好的成形性,已成为制造汽车轮毂的优质材料。
本文将重点介绍A356铝合金的精炼及净化工艺,以确保其高品质和适用性。
二、A356铝合金的特性A356铝合金是一种常用的铸造铝合金,具有优良的铸造性能、较高的强度、良好的耐腐蚀性和较好的成形性。
此外,其成本相对较低,适合大规模生产。
因此,A356铝合金在汽车轮毂制造中得到了广泛应用。
三、精炼工艺A356铝合金的精炼工艺主要包括熔化、除气、除渣等步骤。
1. 熔化:将A356铝合金的原材料按照一定比例混合后,放入熔炉中进行熔化。
熔化过程中需控制好温度,以防止合金元素的烧损和氧化。
2. 除气:熔化后的合金液中会含有一定的气体,如氢气等。
除气工艺通过引入惰性气体(如氩气)将合金液中的气体排出,从而提高合金的纯净度。
3. 除渣:在熔化和除气过程中,会产生一些渣状物,这些渣状物会降低合金的纯度和性能。
除渣工艺通过物理或化学方法将渣状物从合金液中去除。
四、净化工艺A356铝合金的净化工艺主要包括精炼剂加入、搅拌和静置等步骤。
1. 精炼剂加入:根据合金的成分和性能要求,加入适量的精炼剂。
精炼剂可以进一步去除合金中的杂质,提高其纯净度。
2. 搅拌:加入精炼剂后,进行适当的搅拌,使精炼剂与合金液充分混合,提高净化效果。
3. 静置:搅拌后,让合金液静置一段时间,使杂质和精炼剂充分反应并上浮到合金液的表面,然后将其去除。
五、结论通过上述的精炼及净化工艺,可以有效地提高A356铝合金的纯净度和性能,使其满足汽车轮毂制造的要求。
在精炼过程中,通过控制熔化温度、引入惰性气体除气和物理化学方法除渣等步骤,可以去除合金液中的气体和渣状物。
在净化过程中,通过加入精炼剂、搅拌和静置等步骤,可以进一步去除合金中的杂质,提高其纯净度。
a356铝合金的热处理工艺

a356铝合金的热处理工艺哎呀,说起A356铝合金的热处理工艺,这可真是个技术活儿。
你知道吗,A356铝合金,这玩意儿在汽车行业里可受欢迎了,因为它既轻又强,还耐腐蚀。
不过,要让这材料发挥出最佳性能,热处理工艺是关键。
首先,咱们得聊聊A356铝合金的“前身”——那就是熔炼。
熔炼过程就像是给金属“洗澡”,得把铝和其他合金元素混合在一起,加热到一定的温度,让它们完全融合。
这个过程得控制好温度,太高了材料会烧坏,太低了又融合不彻底。
接下来,就是铸造了。
把熔化的A356铝合金倒进模具里,等它慢慢冷却凝固。
这个过程得慢慢来,太快了材料会裂,太慢了又会影响材料的微观结构。
好了,重头戏来了,热处理。
热处理就像是给A356铝合金“做瑜伽”,通过控制温度和时间,让材料内部的微观结构发生变化,从而提高其性能。
这个过程包括好几个步骤:1. 固溶处理:把A356铝合金加热到一个特定的温度,让其中的合金元素充分溶解在铝基体中。
这个温度得控制好,太高了材料会过热,太低了溶解不充分。
2. 淬火:固溶处理后,得迅速把材料冷却下来,这就像是给材料“速冻”。
这个步骤能让材料内部的微观结构更加紧密,提高强度。
3. 时效:最后,把材料放在一个较低的温度下保持一段时间,让材料内部的微观结构进一步稳定。
这个过程就像是给材料“休息”,让它恢复体力。
整个过程得小心翼翼,因为温度和时间的控制非常关键。
太高或太低,太长或太短,都会影响材料的性能。
举个例子,我之前在工厂里看到过一次热处理过程。
工人们把A356铝合金棒料放进一个大炉子里,炉子里的温度得精确控制。
然后,他们用一个巨大的水槽来淬火,水花四溅,场面相当壮观。
最后,把材料放在一个恒温箱里时效,这个过程得持续好几个小时。
总之,A356铝合金的热处理工艺是个精细活儿,需要精确控制温度和时间。
这就像是烹饪一道美味的菜肴,火候和时间都得恰到好处,才能做出色香味俱全的佳肴。
而A356铝合金,经过精心的热处理后,就能成为汽车行业里的“美味佳肴”。
《汽车轮毂用A356铝合金的精炼及净化》范文
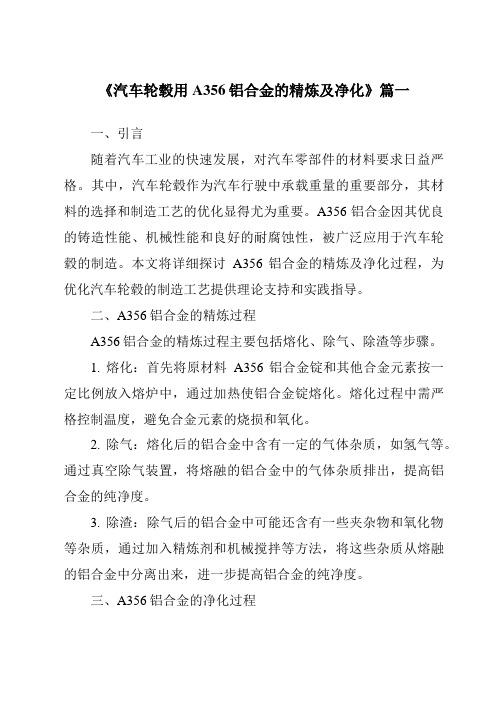
《汽车轮毂用A356铝合金的精炼及净化》篇一一、引言随着汽车工业的快速发展,对汽车零部件的材料要求日益严格。
其中,汽车轮毂作为汽车行驶中承载重量的重要部分,其材料的选择和制造工艺的优化显得尤为重要。
A356铝合金因其优良的铸造性能、机械性能和良好的耐腐蚀性,被广泛应用于汽车轮毂的制造。
本文将详细探讨A356铝合金的精炼及净化过程,为优化汽车轮毂的制造工艺提供理论支持和实践指导。
二、A356铝合金的精炼过程A356铝合金的精炼过程主要包括熔化、除气、除渣等步骤。
1. 熔化:首先将原材料A356铝合金锭和其他合金元素按一定比例放入熔炉中,通过加热使铝合金锭熔化。
熔化过程中需严格控制温度,避免合金元素的烧损和氧化。
2. 除气:熔化后的铝合金中含有一定的气体杂质,如氢气等。
通过真空除气装置,将熔融的铝合金中的气体杂质排出,提高铝合金的纯净度。
3. 除渣:除气后的铝合金中可能还含有一些夹杂物和氧化物等杂质,通过加入精炼剂和机械搅拌等方法,将这些杂质从熔融的铝合金中分离出来,进一步提高铝合金的纯净度。
三、A356铝合金的净化过程A356铝合金的净化过程主要包括滤渣、均匀化处理和铸造等步骤。
1. 滤渣:精炼后的铝合金通过滤渣装置,将剩余的杂质和夹杂物进一步去除,保证铸造出的轮毂表面光滑、无缺陷。
2. 均匀化处理:滤渣后的铝合金需要进行均匀化处理,使合金元素在熔体中均匀分布,提高合金的性能。
均匀化处理的温度和时间需严格控制,避免合金元素的过烧和氧化。
3. 铸造:均匀化处理后的铝合金即可进行铸造。
铸造过程中需控制好铸造温度、铸造速度和冷却速度等参数,以保证轮毂的尺寸精度和机械性能。
四、结论通过对A356铝合金的精炼及净化过程的探讨,我们可以得出以下结论:1. 精炼过程能有效去除铝合金中的气体杂质和夹杂物,提高铝合金的纯净度,为后续的铸造过程提供良好的原材料。
2. 净化过程通过滤渣、均匀化处理和铸造等步骤,进一步保证轮毂的尺寸精度和机械性能,提高轮毂的使用寿命和安全性。
a356铸造铝合金热处理强化工艺研究
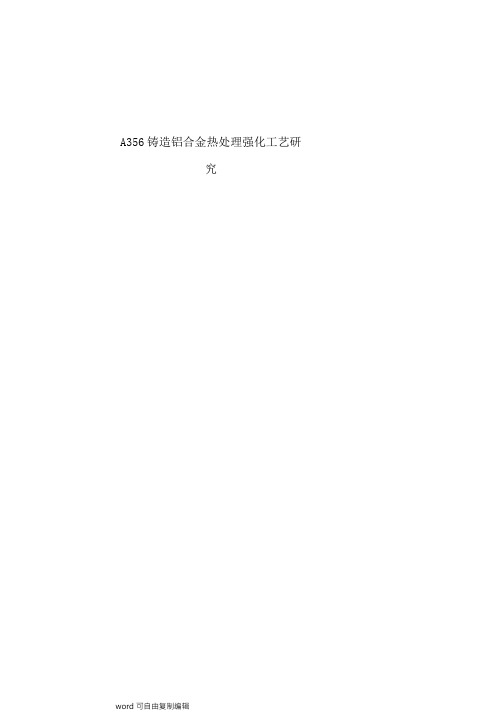
A356铸造铝合金热处理强化工艺研究摘要现代汽车正朝着轻量化、高速、安全舒适、低成本与节能的方向发展。
而目前满足上述要求的最有效的途径就减轻汽车自重。
铝及其合金加工材料由于具有密度小、比强度高等一系列优良特性成为实现汽车轻量化最理想的首选材料。
本文以A356铸造铝合金轮毂为研究对象,利用金相显微技术、扫描电镜、差热分析及力学性能测试等手段对合金的各种不同工艺的微观组织与性能进行了全面的测试与分析。
通过改变固溶处理工艺参数,研究了固溶处理工艺与合金的力学性能之间的关系。
当温度为535°C时,随着保温时间的延长,抗拉强度、硬度及延伸率基本上都是先升后降。
当保温时间为3.5〜4.5h时,轮缘的强度、硬度及延伸率才能达到很好的匹配。
A356铸造铝合金在545Cx3.5h下进行固溶处理具有较好的综合力学性能,轮缘抗拉强度为251MPa,硬度为82HV,延伸率为12%;轮幅抗拉强度为233MPa,延伸率为9%,故固溶处理的优先工艺为545Cx3.5h。
研究了室温停留时间与力学性能之间的关系,结果表明室温停留时间选择在2〜10h范围之内,但不应超过12h。
如果从生产周期及成本方面考虑,室温停留2h,合金就能达到预时效的目的,达到强度、硬度与塑性的良好匹配。
通过改变时效处理工艺参数,研究了轮缘的时效处理工艺与力学性能之间的关系,结果表明在设定的在三个温度上进行时效处理保温3h时,合金的综合力学性能均很好,因此对A356铝合金进行时效,能够使其达到一个强度、硬度与延伸率均为极值的平衡点。
当固溶处理工艺采用535Cx4.5h时,时效温度为135C时,时效时间至少为3h; 当采用优选的固溶工艺545Cx3.5h,时效温度为135C时,则当时效时间为0.5h时,即能达到使强度与塑性达到较高的水平。
当时效温度升高至145C时,则在保温1h 时,即能达到较好的强度与延伸率的配合。
比较了固溶处理工艺为535°Cx4.5h及545x3.5h两种工艺下合金的力学性能,表明对于A356铸造铝合金,如果在应用时对塑性的要求较高时,则固溶处理可采用工艺535Cx4.5h;如果对其塑性要求不高,而希望缩短生产周期,提高生产效率时,则建议采用工艺545x3.5h。
《2024年汽车轮毂用A356铝合金的精炼及净化》范文

《汽车轮毂用A356铝合金的精炼及净化》篇一一、引言随着汽车工业的快速发展,汽车轮毂作为汽车的重要组成部分,其材料的选择和制造工艺对汽车的性能和使用寿命具有重要影响。
A356铝合金因其优良的铸造性能、良好的机械性能以及适中的成本,已成为汽车轮毂制造的常用材料。
然而,A356铝合金的精炼及净化工艺对其性能和品质具有决定性作用。
本文将详细探讨A356铝合金的精炼及净化工艺,以期为汽车轮毂制造提供理论支持和实际指导。
二、A356铝合金的特点A356铝合金是一种常用的铸造铝合金,具有优良的铸造性能、良好的机械性能和适中的成本。
它含有硅、铜、镁等元素,这些元素的含量对合金的性能具有重要影响。
然而,A356铝合金在铸造过程中容易产生气孔、夹杂物等缺陷,因此需要进行精炼和净化处理。
三、精炼工艺1. 熔炼前准备:在熔炼前,应将原材料进行严格的检查和分类,去除杂质和异物。
同时,熔炼设备应进行清洗和干燥,以防止杂质污染。
2. 熔炼过程:将原材料加入熔炉中,通过加热使合金熔化。
在熔炼过程中,应控制好温度和加热速度,避免过热或过冷导致合金性能下降。
3. 气体精炼:在熔炼过程中,通过向熔体中通入惰性气体(如氩气),将合金中的气体(如氢气)排出,从而提高合金的纯净度。
4. 除渣:通过加入精炼剂或采用机械搅拌等方法,将合金中的夹杂物和氧化物等杂质去除。
四、净化工艺1. 熔体净化:通过调整熔体的化学成分和温度,使合金中的杂质元素以沉淀或浮渣的形式析出并去除。
2. 真空处理:在真空条件下,对熔体进行进一步的处理,以去除残留的气体和杂质。
真空处理可以提高合金的致密度和机械性能。
3. 铸件净化:在铸造过程中,通过调整铸造参数和控制冷却速度等方法,使铸件中的气孔和夹杂物等缺陷得到有效控制。
五、结论A356铝合金的精炼及净化工艺对汽车轮毂的性能和品质具有重要影响。
通过合理的精炼和净化工艺,可以提高A356铝合金的纯净度、致密度和机械性能,从而生产出高质量的汽车轮毂。
- 1、下载文档前请自行甄别文档内容的完整性,平台不提供额外的编辑、内容补充、找答案等附加服务。
- 2、"仅部分预览"的文档,不可在线预览部分如存在完整性等问题,可反馈申请退款(可完整预览的文档不适用该条件!)。
- 3、如文档侵犯您的权益,请联系客服反馈,我们会尽快为您处理(人工客服工作时间:9:00-18:30)。
A356合金熔炼原理一、铝轮毂采用的合金及化学成分现代汽车铸造铝合金车轮应用最广的材料是美国材料与试验协会(ASTM)牌号A356合金,相当于中国ZL101A、日本AC4CH、德国AlSi7Mg、法国A-S7G03、俄罗斯Aл9-1。
除A356合金外,德国还采用AlSi9Mg、AlSi10Mg、AlSi11Mg,法国还采用A-S11G、A-S12.5。
这些高Si合金都不热处理,它们液态流动性好、补缩能力强、铸造性能好、铸造缺陷少。
但机械性能和机加工艺性能不如A356合金。
A356合金又分为A356.2、A356.1、A356.0,其化学成分,分别为下表:二、熔炼温度和时间控制A356合金大约在580℃时开始有液态出现,到640℃就可全部熔化,一般最高熔炼温度控制在760℃,铝液温度超过770℃,明显开始氧化,夹杂物和含气量大幅增加,凝固后组织晶粒也会粗大,铝液质量开始下降。
所以,对A356合金的熔炼时,低温熔炼有利提高铝液质量,提高材料的机械性能。
请看下图:氧化物增量μg /c ㎡h640 700 770 800 ℃温度→温度对铝合金液氧化的影响另外A356合金熔化时,时间不能太长,特别是在高温下保温时间太长,不利于铝液质量。
浇注温度也不能太高,低压铸造浇注温度一般在685~710℃,重力铸造一般控制在730℃左右。
国内铝合金车轮生产厂家,凡采用低压铸造工艺,都用中间包转运铝液,并进行除渣除气,如中间包烤的不好,铝液在中间包降温很快,一般铝液出炉温度控制在760℃,也有控制在770℃,如果选好的烤包器,中间包温度可烤到600℃,这样铝液降温就慢,铝液可在740℃出炉。
铝液质量就会大大提高,而烧损也少。
三、熔炼过程对环境水分控制A356合金在熔炼过程中,空气含水蒸气的量,原材料含水量,炉膛和工具吸水量,精练剂和打渣剂含水量,旋转除气中氩气或氮气含水量,低压铸造机用的压缩空气含水量等等,这些都与铝合金液接触,都能与铝液起以下反应:2Al (l )+3H 2O (g )=r-Al 2O 3+6[H]这个反映比铝液和空气中的氧反应还激烈,当水含量为10-21时,上述反应仍然进行,即使铝液表面有氧化膜保护时,这个反应也能进行。
由于此反应,使铝液中的渣和气的含量增加很快。
通过计算可得1克铝液和1克水蒸气反应,可生成1.9克r-Al 2O 3和1224cm 3标准状态下的氢气。
另外使用不同的能源,燃气的气氛中含水蒸气量也不同。
如果用电阻炉或工频炉,铝液面的含水量,就是空气中的含水量,潮湿季节为0.8%左右;如果用柴油或天然气、石油液化气,燃烧的气氛中含水量为16%;如果用煤的气化炉产生的燃气熔炼铝,气氛中含水量为20%。
燃烧气氛中含的水蒸气与铝液起强烈的反应,而生成r-Al 2O 3和氢气。
铝与其它金属不同的是:在660.37℃液态铝中含氢量变成660.37℃固态铝中含氢量相差19倍,在凝固过程中一定要有氢的析出。
而2[H]→H 2,这就是铝合金易产生针孔的原因。
如果先把液态铝中氢除的比较理想,变成固态的铝,针孔产生就少,若液态铝除氢达到2.63g/cm 3以上,其中氢含量达到0.036cm 3/100g ,就不能产生针孔。
请看下图:氢溶解度(c ㎡/100g A l )1.230.92 0.690.0360.005400660.37750 850 ℃ 温度→温度对铝合金中氢溶解度的影响因此,在熔炼过程中对环境中,如炉膛和工具、原材料、各种溶剂和周围的气氛中的水含量,必须严格控制,特别是对Sr 变质的铝合金液,更要严格控制,因为含Sr 的铝液可把与水反应生成的原子的氢,基本吸附到铝液中,使铝液凝固时产生针孔。
四、熔炼过程中铝合金与氧的反应铝及铝合金与氧反应后所生成的氧化物存在形式,分为致密氧化物和疏松氧化物,致密氧化物不下沉,并起保护作用,而疏松氧化物要下沉,起不到保护作用。
按常用合金元素与氧的亲和力大小,可依次排列为下列顺序:Be—Li—Mg—Na—Ca—Sr—Al—Ce—Ti—Si—Mn—Cr—Zn—Fe—Ni—Cu……我们可按此次序,看看它们与Al反应生成氧化物的情况,其中Al以下的元素与氧亲和力比Al小的元素,在铝合金中为非表面活性元素,形成复杂的氧化物,其组织致密,对铝合金液起屏蔽保护作用,可防止铝合金液再氧化和吸气。
所以,Al —Si合金、Al—Cu合金、Al—Zn合金可以不加覆盖剂在大气中熔化。
但在Al之前的元素与氧亲和力比Al大,则在铝合金中是表面活性元素,它们与高温的炉气接触时,在Al之前先被氧化,所形成的氧化物膜组织疏松,对铝合金液无屏蔽保护作用。
所以,Al—Mg合金就一定要在覆盖剂保护作用下,才能在大气中熔炼。
只有Be的氧化膜是例外,它可充填MgO氧化膜的疏松间隙,使其致密层起保护铝合金液的作用。
4Al(l)+3O2 = 2r-Al2O3此反应也很激烈,因为表面有保护层,显得反应不激烈,当新的界面一出现,迅速发生反应生成保护层。
A356合金虽然也有Mg的含量,因含量低,铝的氧化层仍很致密,当Mg含量>1%时,保护层开始疏松,Mg含量越高,疏松越严重,当Mg 含量>4.5%时,保护层疏松开始严重,起不到保护作用。
Al—Mg合金中Mg的最低含量为4.5%。
所以Al—Mg合金熔炼时,要加覆盖剂。
五、A356合金熔炼时除渣除气过程A356合金在熔炼过程中主要生成的夹杂物:r—Al2O3、MgO、SiO2和Al9Fe2Si2等,如果熔炼温度> 750℃时,也生成少量的α—Al2O3。
同时还生成大量[H],溶解在铝液中。
在熔炼过程中还要想办法除去铝液中各种夹杂物和氢气。
主要手段是扒渣、精练和用石墨转子旋转除气除渣。
㈠扒渣用打渣剂(或除渣剂)撒在铝液表面,使渣水分离,将分离出的渣扒出炉外,因扒渣剂中有Na3AlF6(或K3SiF6),这种盐有强烈吸附Al2O3的能力,还有Na2SiF6(或K2SiF6),它可以与Al2O3和铝起下述反应:3Na2SiF6+2Al2O3=2Na3AlF6+2AlF3↑+3SiO2Na2SiF6 SiF4↑+2NaF6NaF+Al=3Na+Na3AlF6第一个反应可以吃掉一部分Al2O3,第三个反应使渣水分离,将渣扒出炉外,达到去渣的目的,同时还生成Na3AlF6,有强烈吸附r—Al2O3的作用,使渣和铝液得到分离。
㈡精练A356合金熔炼过程,可分别在炉内精练和炉外精练,在炉内精练又分为喷粉精练、压入法精练、用CCl4精练;炉外精练指在中间包内精练过程,一般都采用石墨转子旋转除渣除气精练。
1、喷粉精练靠喷粉装置用高纯氩气或氮气,将精练剂喷到铝液中进行精练。
精练剂的主要成分为:NaCl、KCl、Na2SiF6、Na3AlF6、C2Cl6、Na2CO3等组成,其熔点要比铝液温度低,比重要比铝液轻,都不能与铝液溶解。
Na3AlF6有强烈吸附Al2O3作用,Na2SiF6能吃掉一部分Al2O3,同时还能生成很多气体将渣和气带出液面,达到精练的目的。
2、压入法用的精练剂为块状,主要成分是75%C2Cl6,25%的Na2SiF6,其化学反应为:3C2Cl6+2Al=3C2Cl4↑+2AlCl3↑C2Cl6 C2Cl4↑+Cl2↑3Cl2+Al=2AlCl3↑大量气体将渣和气带出液面。
Na2SiF6反应同上述的除渣反应,能吃掉一部分Al2O3。
3、用CCl4精练用精练砖浸泡在CCl4液体中,将浸满CCl4的精练砖压入铝液中进行均匀搅拌,其化学反应为:CCl4(l) CCl4(g)(因沸点为76.5℃)CCl4(l) C+2Cl2↑2Al+3Cl2=2AlCl3↑(AlCl3187℃升华)Al2O3+3C+3Cl2=2AlCl3↑+3CO↑上述反应这些气体都不溶于铝液,都可除渣除气。
喷粉精练一般在740±10℃进行,压入法精练温度一般为730±10℃,CCl4精练温度为700±10℃。
㈢炉外精练炉外精练一般指在中间包内精练,现在普遍都采用石墨转子旋转除渣除气,要用高纯氩气或氮气。
石墨转子转速控制在400~450转/分,氩气压力为0.1~0.2Mpa,流量为0.8~1.5m3/h,铝液比重达到2.63g/cm3以上方为合格。
其原理为下图:六、A356合金在熔炼过程中的变质和细化晶粒度的大小对A356合金的热处理特性、材料质量都有很大的影响。
均匀的细晶粒组织给A356合金质量带来的最大作用是显著的提高其强度和延伸率,其次是使A356合金的热裂倾向减小和气密性提高,避免铸造时铸件表面开裂,提高铸造表面质量。
㈠加入细化剂(或称孕育处理)A356合金中加入0.08~0.20Ti,其目的是细化合金。
Ti的加入,可生成TiAl3,TiAl3的晶体结构和晶格常数与初晶α-Al和硅的晶体结构和晶格常数相近,TiAl3是初晶α-Al和硅的有效异质结晶核,可使初晶α-Al和硅细化。
A356合金在旋转除气时加入Al-Ti-B合金,其中TiB2也是异质结晶核,可使α-Al和共晶硅细化。
除加Al-Ti-B之外,近十年来世界各国开始加入Al-Ti-C,其中TiC也是异质结晶核,可使α-Al和共晶硅细化。
在液态A356合金中TiC聚集速度比TiB2慢,细化效果Al-Ti-C合金比Al-Ti-B合金更好些。
㈡A356合金的变质对A356合金变质一般用Na、Sr、Sb作变质剂,采用哪种变质要根据铸造什么铸件和采用什么铸造方法而定。
1、Na可使共晶硅的结晶由短圆针状变为细粒状,并降低共晶温度,增加过冷度,细化晶粒。
其细化效果,对冷得慢的砂型、石膏型铸件也较好,Na变质法的成本低,制备也较简单,适合批量小,要求不很高的产品。
其缺点是:Na是化学活泼性元素,在变质处理中氧化、烧损激烈,对人体和环境都有危害,特别是易使坩埚腐蚀损坏,它变质时间短,一般在40分钟内起变质作用,在铸造铝轮毂行业,几乎无人采用Na变质。
2、Sb是一种永久变质剂,可重熔100小时,仍有变质效果。
一般在铝轮毂行业中加入量为0.10~0.20%,为节省成本都是加入纯Sb。
铝液经除气后,在车轮上不产生针孔,在中小车轮采用此方法。
对大型车轮,随着冷却速度变慢,变质不完全,机械性能下降比Sr变质快,对大型车轮或轮辐和轮盘比较厚的车轮用Sb 变质一定要把Mg补到0.4%~0.45%含量,才能达到合格产品。
3、Sr是一种长效变质剂,一般在8小时内起变质作用,在车轮行业中一般加入量为0.01~0.04%,为减少针孔,Sr的加入量为0.01~0.02%。
也是一种理想变质剂,但Sr变质的铝液易吸氢,在低压铸造机铸造中易产生针孔。
对抛光轮和电镀轮很不利,要想没有针孔,要提高铝液质量外,需要良好的铸造工艺,可以做到没有针孔,但抛光面易出现渣孔和疏松问题,铸造机操作手必须严格控制冷却环的冷却度,可以做到没有针孔,也没有渣孔和疏松。