合金熔炼知识点总结
熔炼工艺基本知识的讲解

熔炼基本知识的讲解工艺操作规程:;如,,可以,必须通过熔炼过程,藉助物理的或化学的精炼作用,以排除这些杂质、气体、氧化物等,以提高熔体金属的纯洁度;3 除上述目的外,熔铸车间还有将回收的废料复化的任务这些回收的废料往往由于管理不严被混杂,成分不清,或者被油等杂物污染、或者是碎屑不能直接用于成品合金的生产,必须藉助熔炼过程双室炉以获得准确的化学成分,并铸成适用于再次入炉的铸锭;二、熔炼炉的准备为保证金属和合金的铸锭质量,并且要做到安全生产,事先对熔炼炉必需做好各项准备工作.这些工作包括烘炉,洗炉及清炉;1.烘炉凡新修或中修过的炉子,在进行生产前需要烘炉,以便清除炉中的湿气;2.洗炉实际生产中住往需要用一台炉子熔炼多种合金,由一种含金改为生产另一种合金时往往需要洗炉;①洗炉的目的洗炉就是将残留在熔池内各处的金属和炉渣清除出炉外,以免污染另一种合金,确保产品的化学成分;另外对新修的炉子,可减少非金属夹杂物;②洗炉原则1 新修,中修和大修后的炉子生产前应进行洗炉;2 长期停歇的炉子可以根据炉内清洁情况和要熔化的合金制品来决定是否需要冼炉;3 前一炉的合金元素为后一炉的杂质时应该洗炉;4 由杂质高的合金转换熔炼纯度高的合金时需要洗炉.③洗炉时用料原则1 向高纯度和特殊合金转换时,必须用100%的原铝或者铝锭;2 新炉开炉,一般合金转换时,可采用原铝锭或纯铝的一级废料;3 中修或长期停炉后,如单纯为清洗炉内脏物,可用纯铝或一级废料进行;4 洗炉时洗炉料用量不得少于炉子容量的40%;④洗炉时的要求1 装洗炉料前和洗炉后都必须放干,大清炉;2 洗炉时的熔体温度控制在800-850℃,在达到此温度时,应彻底搅拌熔体,其次数不少于三次,每次搅拌间隔时间半小时;3.清炉清炉就是将炉内残存的结渣彻底清除炉外;每当金属出炉后,都要进行一次清炉.当合金转换,一般制品连续生产5-15炉,特殊制品每生产一炉,都要进行大清炉;大清炉时,应先均匀向炉内撒入一层粉状熔剂,并将炉膛温度升至800℃以上,然后用三角铲将炉内各处残存的结渣彻底清除;三、熔炼工艺流程和操作熔炼时要控制好合金成分,除了采用措施控制烧损以外,还要做好几项工作,原材料的检查,合理的加料顺序,做好炉前的成分分析和调整等;1. 检查原材料炉料配到熔炼加料点,由于配料计算,称重及吊运等都可能发生差错,甚至还可能出现缺料或多料的情况;如果不进行检查,就可能使合金元素的含量超出或低于控制成分所要求的范围,甚至造成整炉的化学成分不符的废品;因此对原材料的检查这一工作是熔炼生产时的重要工序之一;1 清洁无腐蚀所配入的原材料要求表面清洁无腐蚀,炉料要做到三无无灰, 无油污、无水,否则将会影响合金熔体的纯洁度;2 成分符合要求如果原材料的成分不符合要求,就会直接影响合金成分的控制.为此:①对于无印记、或印记不清的炉料,在未确定成分前严禁入炉;②对于中间合金应有成分分析单,或标明炉号熔次,否则不准入炉;③另外,加工方法和材料的供应状态不同,对成分的要求也就不同;3 重量要准确原材料的重量准确与否,不但影响合金的成分,而且影响铸锭的尺寸;因此在检查原材料时对这一工作也不可忽视;2.装炉熔炼时装入炉料的顺序和方法不仅关系到熔炼的时间,金属的烧损,热能消耗还会影响到金属熔体的质量和炉子的使用寿命;1 装炉料顺序应合理正确的装料要根据所加入炉料性质与状态而定,而且还应考虑到熔化速度快,烧损少,以及化学成分的控制;通常,装料顺序可按下述原则进行;装炉时,先装小块或薄板废料,铝锭和大块料装在中间,最后装中间合金;熔点低的中间合金装在下层,高熔点的中间合金装在最上层,所装入的炉料应当在炉膛中均匀分布,防止偏重;小块或薄板料装在下层,这样可减少烧损,同时还可保护炉底免受大块料的直接冲击;有的中间合金熔点高,如A1-Ni和A1-Mn合金的熔点为750-800℃,装在上层,由于炉内上部温度高容易熔化,也有充分的时间扩散,使中间合金分布均匀,则有利于熔体的成分控制;炉料装平,各处熔化速度相差不多这样可以防止偏重时造成的局部金属过热;炉料应尽量一次入炉,多次加料会增加非金属夹杂物及含气量;2 特殊制品重要制品的炉料除上述的装炉要求外,在装炉前必须向炉内撒一定量的粉状熔剂,这可提高炉体的纯洁度,也可减少烧损;3.熔化炉料装完后即可升温度熔化.熔化是从固态转度为液态的过程;这一过程的好坏,对产品质量有重大影响;1 覆盖剂我公司没有熔化过程中随着炉料温度的升高,特别是当炉料上部熔化以后,金属外层表面所复盖的氧化膜很容易破裂,将逐渐失去保护作用;气体在这时候很容易侵入,造成内部金属的进一步氧化;并且已熔化的液滴或液流要向炉底流动,当液滴或液流进入底部汇集起来的液体中时,其表面的氧化膜就会混入熔体中;所以为了防止金属进一步氧化和减少进入熔体中的氧化膜,在炉料软化下塌时,应适当向金属表面撇上一层粉状熔剂覆盖;这样也可以减少熔化过程中的金属吸气;覆盖剂用量为炉料量的;2 加锌当炉料熔化一部份以后,即可向液体中均匀加入锌锭,以熔池中的熔体刚好能淹没锌锭为宜;3 搅动熔体熔化过程中应注意防止熔体过热;炉内的金属熔化,主要是靠火焰的辐射及炉壁传热,在上层炉料熔化后,下层炉料的受热主要靠上层高温炉料通过传导方式进行,此时热量由上层传递到下层进行的特别慢;此时上层金属在高温度下容易产生局部过热;当炉料化平之后,应适当搅动熔休,以使熔池里各处温度均匀,同时也利于加速熔化;4. 扒渣与搅拌当炉料在熔池里已充分熔化,并且熔体温度达到熔炼温度时,即可扒除熔体表面漂浮的大量氧化渣;1扒渣扒渣前应先向熔体上均匀撤入粉状熔剂,使渣冲与金属分离,有利于扒渣,可以少带出金属;为什么我公司不使用打渣剂仅仅是污染的原因扒渣操作要求平稳,防止渣滓卷入熔体内;扒渣要彻底,因浮渣的存在会增加熔体的含气量,并弄脏金属;2 加镁扒渣后便可向熔体内加入镁锭,同时要用2粉状熔剂进行覆盖,以防镁的烧损;添加镁锭的铝液温度控制应在750-755℃之间,温度低镁锭吸收不良,铝液因加入镁锭不在升温,导致铝液温度过低;温度高则造成镁锭燃烧,烧损过大;添加镁锭是注意,计算出镁锭的重量后,预留500-1000KG作为第二次加入;3 搅拌在取样之前,以及在补料后,都应当及时地进行搅拌;其目的在于使合金成分均匀分布和熔体温度趋于一致;这看来似乎是一种极简单的操作,但是在工艺过程中是很重要的工序;它关系到合金成分是否能获得准确的控制;一些比重较大的合金元素容易沉底,另外合金元素的加入不可能绝对均匀,这就造成了熔体上下层之间,炉内各区域之间合金元素的分布不均匀;如果搅拌不彻底没有保证足够长的时间和消灭死角,容易造成熔体化学成分不均匀;就是取样成分不具有代表性,结果就是造成误导,导致后续生产出现一系列成分问题,且原因查找困难;搅拌应当平稳进行,不应激起太大的波浪,以减少氧化夹杂卷入熔体中的机率; 5.调整成分在熔炼过程中,由于各种原因可能会使合金成分发生改变,这种改变可能使熔体的真实成分与配料计算值发生较大的偏差;因而须在炉料熔化后,取样进行快速分析,以便根据分析结果确定是否需要调整成分;1 取样熔体溶化经充分搅拌之后要进行取样预分析,确定熔体中杂质元素未超出控制要求;取样时的炉内熔体温度不应低于熔炼温度中限;取样温度要在730℃以上取样部位要有代表性,一般在二分之一熔体的中心部位取两组试样.取样前试样勺要进行预热;2)添加合金添加合金要注意的几点:1、铝液温度适合740-745℃2、注意添加合金干燥、清洁、无水分、油污、泥土、霜雪等杂物;3、注意添加合金的种类准确,不要混淆误加;4、注意重量的核对无误;3 成分调整成分调整的公式是什么当分析结果和要求成分不相符时,就应调整成分-补料,或冲淡;调整成分是为了保证合金的化学成分在规定的标准之内,避免由于主要的合金成分超出内部标准范围而降低合金的工艺性能和最终制品性能;调整组元及杂质的配比,也可以改善合金的铸造性能;①补料分析结果低于合金要求的化学成分时就需要补料;②冲淡分析结果高于标准的化学成分上限时就需要冲淡;配料加入量:Qkg=A-B÷C-A×W式中:Q—需要配入的中间合金或金属添加剂的重量A—要求达到的某元素含量百分比B—原铝液与重熔用铝锭中该元素的百分比C—配料用中间合金或金属添加剂中该元素的百分比W—原铝液重量包括重熔用铝锭为防止配料化学成分出现偏差,在配料计算时不允许按成分要求的上限下限配料,一般按中限配料,易燃、易烧损的原料可按中上限计算配料;③调整成分时应注意的事项若发现分析结果与实际相差太大,或有些值得怀疑之处,则应分析产生偏差的原因,如不加分析就进行补料,则会造成大量的成炉化学成分不符废品;因此冲淡补料不仅仅是一个计算过程,而且还应注意以下几个方面;a 试样有无代表性取样是否准确,能否有代表性,对合金成分的控制有直接的影响.要做到取样准确,而且有代表性,必须注意取样时熔体的温度和取样的部位;试样无代表性是因为,某些元素比重较大,溶解扩散速度慢,或易于偏析分层.故取样前应充分搅拌,以均匀其成分,由于熔池表面温度高,炉底温度低,取样前要多次搅拌,每次搅拌时间不得少于五分钟;b 取样部位和操作方法要合理由于熔池大,尽管取样前进行多次搅拌,熔池内各部位的成分仍然有一定的偏差,因此试样应在熔池中部最深部位的二分之一处取出;取样前应将试样模充分加热干燥,取样时操作方法该正确,使试样符合要求,否则试样有气孔,夹渣或不合要求,都会给快速分析带来一定的误差;c 取样时温度要适当某些比重大的元素,它的溶解扩散速度随着温度的升高而加快;如果取样前熔体温度较低,虽然经过多次搅拌,其溶解扩散速度仍然缓慢,此时取出的试样仍缺乏代表性,因此取样前应控制熔体温度适当高些;一般来说,取样时的温度不能低于熔炼温度的下限,Cu,Zn和Mn作为主要合金元素加入的合金取样温度就要高些,其部位应在熔池的中心;d 补料和冲淡时一般用中间合金,避免使用熔点较高和较难熔化的新金属;e 补料量或冲淡量在保证合金元素要求的前提下应越少越好,且冲淡时应考虑熔炼炉的容量和是否便于冲淡的有关操作.f 冲淡量如果在较多的情况下,还应补入其他合金元素,使这些合金元素的含量不低于它们所要求的化学成分.6.倒炉a. 倒炉前准备齐全倒炉工具预热干燥,并且做好倒炉后需要堵炉眼的工具附有岩棉的塞子套;b. 溜槽清理干净无杂物,检查保温炉如铝口是否顺畅,无堵塞;c. 检查劳保用品是否穿戴齐全;d. 进行倒炉作业;e. 严格来讲不允许在倒炉过程中进行补加合金,容易发生安全事故;7. 清炉倒完炉后,需要对熔炼炉进行清炉,使用扒渣车对炉内进行刮渣清理;需要大清炉是采用大清炉作业;8. 精炼工业生产的铝合金绝大多数在熔炼时都要有精炼过程,其目的是为了提高熔体的纯洁度;这些精炼方法可分为两类:即气体精炼法和熔剂精炼法;我公司采用的是气体精炼法;1精炼温度熔体粘度越高,则去气除渣越困难;而粘度决定于温度和化学成分,提高熔体温度会促使粘度降低;一定成分的合金其温度越低,则粘度也就越大;为此精炼温度应适当高些;但是精炼温度过高又会造成吸气量的增加和晶粒粗化;熔体精炼温度应控制在铸造温度上限加10~20℃范围内;2精炼剂的质量和用量用气体精炼时精炼时间长,除气效果要好;精炼熔剂的质量对精炼效果的影响很大,使用高质量的精炼剂进行精炼,可以大降低熔体的氢含量;而精炼气体的质量,尤其是精炼气体内的水氧含量,对精炼效果的影响也是非常大的;如果精炼气体质量不佳,精炼效果会大打折扣,严重时也可能产生负面的影响,即精炼不但没能除气,反而会增加熔体中的氢含量;另外,精炼时间或精炼剂的用量,也是一个重要参数;精炼过剩的后果是什么造成渣含量过多主要成分为氯化物;主要是除碱金属,精炼过剩只能跟其他元素反应;3熔体静置时间熔体静置时间对去气除渣的影响,对于铝合金来说,是一个不可忽视的因素;因为处在熔休中的非金属夹杂物,一般其颗粒度都很小;其分散程度也较高,在吸附造渣能力强的熔剂的作用下,尺寸较大及比重差较大的夹渣,容易上浮或下沉,然而尺寸较小或比重差较小的夹渣,它们的上浮或下沉则需要一定的时间;熔体精炼后到铸造开始的时间,成熔体为静置时间;熔体静置时间的规定如下:1对于非双零箔和非罐体料用途的普通制品:≥20分钟;2对于双零箔和罐体料用途的制品:≥30分钟;炉内静置时间与夹杂的关系LIMCA测量结果4精炼操作执行精炼操作规程;废料分级的标准。
合金熔炼复习总结

铸铁白口铸铁含碳量约2.5%,含硅量约1%,白口铸铁中的碳全部以渗碳体(Fe3C)形式存在,因断口呈亮白色,故称白口铸铁。
由于有大量硬而脆的Fe3C,白口铸铁硬度高、脆性大、难以切削加工。
故很少直接用来制造机械零件,主要用作炼钢原料、可锻铸铁的毛坯,以及不需切削加工、要求硬度高和耐磨性好的零件,如轧辊、犁铧及球磨机的磨球等。
白口铸铁作为抗磨材料的应用也非常广泛,先后经历了普通白口铸铁、高锰钢、镍硬铸铁和铬系白口铸铁等几个发展阶段,如采用镍硬铸铁作为粉碎机锤头的抗磨材料以满足其HRC≥55的要求,日本1965年引进Cr27高铬白口铸铁,生产破碎机锤头,1967年把该材料成功地应用在高炉的料钟上,合理地取代了原用高铬钢和低合金钢,明显提高了高炉料钟的使用寿命。
又如高铬白口铸铁主要用于磨球、村板、杂质泵、双金属复台轧辊等易损件的生产。
灰口铸铁含碳量大于4.3%,铸铁中的碳大部或全部以自由状态片状石墨存在,剩余部分则常以珠光体形式存在,断口呈灰色。
常用灰口铸铁中石墨的存在,使灰铸铁的抗拉强度、塑性和韧性远低于钢。
石墨片的数量越多、尺寸越大、分布越不均匀,对力学性能的影响就越大。
但石墨的存在对灰铸铁的抗压强度影响不大,因为抗压强度主要取决于灰铸铁的基体组织,因此灰铸铁的抗压强度与钢相近。
它具有良好铸造性能、切削加工性好,减磨性,耐磨性好、加上它熔化配料简单,成本低,广泛用于制作各种受压应力作用和要求消震的机床床身与机架、结构复杂的壳体与箱体、承受摩擦的缸体与导轨等。
灰铸铁铸造成形性优异、减磨减震性好,成本低廉,在汽车、冶金等行业得到广泛应用。
迄今为止,随着灰铸铁铸件的基体强度的提高,许多汽车的某些工件(如大型载重汽车柴油发动机缸体、缸盖、制动鼓等)的选用材料仍以高强灰铁为主,其市场前景广阔。
通过采取加大废钢比例,适当的合金化处理和强化孕育工艺改善灰铸铁的切削性能可以降低刀具成本、提高生产效率。
铸铁的含硅量决定着铸铁的状态。
合金熔炼知识点总结

合金熔炼知识点总结1.铸造性能:流动性,充型能力,收缩性,偏析。
气体及夹杂物等2.合金的流动性与充型能力的区别1)充型能力是液态金属充满型腔获得形状完整,轮廓清晰铸件的能力流动性是指液态铸造合金本身的流动能力。
2)流动性好的合金,其充型能力强3)流动性影响因素:合金的种类,化学成分及结晶特点3.收缩性:铸造合金从液态冷却到室温的过程中,其体积和尺寸缩减的现象称为收缩性。
1)收缩的三个阶段;液态收缩阶段,凝固收缩阶段,固态收缩阶段。
2)收缩方法:体收缩,线收缩3)影响收缩的因素:化学成分,浇注温度,铸件结构与铸型条件4)收缩对铸件质量的影响:产生缩松和缩孔[主要原因是液态收缩和凝固收缩]防治措施:调整化学成分,降低浇注温度和减少浇注速度,增加补缩能力,增加铸型激冷能力。
6.铸造应力:铸件在凝固冷却的过程中因温度的下降而产生收缩使铸件和长度发生变化,若这些变化受到阻碍便会在铸件中产生应力称为铸造应力。
1)铸造应力按其产生的原因可分为三种:热应力,固态相变应力,收缩应力2))铸造应力的防止和消除措施:采用同时凝固的原则提高铸型温度改善铸型和型芯的退让性进行去应力退火7.铸铁:铸铁是一系列主要由铁、碳和硅组成的合金的总称[铁,碳,硅,锰,磷,硫及其其他合金元素]1)铸铁中的碳以化合态渗碳体和游离态石墨形式存在2).影响铸铁组织和性能的因素:a.碳和硅[铸铁中碳、硅含量均高时,析出的石墨就愈多、愈粗大]b.硫[强烈阻碍石墨化,增加热脆性,恶化铸铁铸造性能硫含量限制在0.1-0.15%以下]c.锰[弱阻碍石墨化,具有提高铸铁强度和硬度的作用锰含量控制在0.6~1.2%之间]d.磷[对铸铁的石墨化影响不显著。
含磷过高将增加铸铁的冷脆性磷含量限制在0.5%以下]8.铸铁分类:1)按碳存在形式分:白口铸铁,灰口铸铁,麻口铸铁2)按石墨存在形式分:灰铸铁,可锻铸铁,球墨铸铁,蠕墨铸铁3)按化学成分分:普通铸铁,合金铸铁4)按性能分:耐热铸铁,耐磨铸铁,耐腐蚀铸铁9.灰铸铁(HT):指碳主要以片状石墨形式出现的铸铁,断口呈灰色。
铝合金熔炼及铸轧基础知识
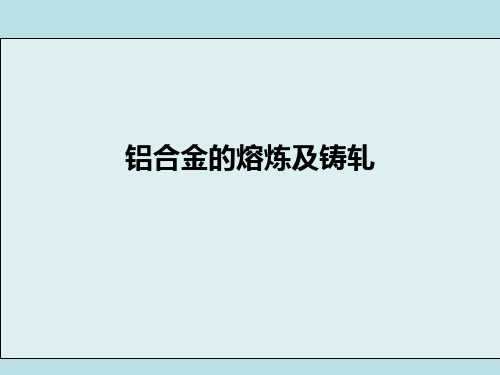
当 180完全不润湿 f ( ) 1,则 G** G*
当 90部分润湿
当 0完全润湿
f ( ) 1,则
2
f ( ) 0,则
G** 1 G* 2
G** 0
一般情况下,质点(c)与新相(s)或多或少润湿,即
0 180 ,这时总存在:
G** G*
异质形核与均质形核相比,其特点是: 形核过冷度小; 形核功小。
2
形核功:
G
16
3
3 SL
Tm LmT
r* 与ΔT 成反比,即过冷度ΔT 越大,r* 越小; ΔG*与ΔT2成反比,过冷度ΔT 越大,ΔG* 越小。
临界晶核的表面能为:
A
SL
4
(r )2
SL
16
3 SL
VSTm H m T
2
形核功为:G
16
3
3 SL
VS Tm H m T
2
所以:
界面的溶质分布规律不遵循状态图。其理论
尚未完全建立。
2.2 微重力凝固 即失重状态下的凝固,重力加速度g<9.8m/s2(如
太空中的凝固)。获得微重力环境的主要方法有:落塔、 落管;飞机、火箭的下降;太空轨道飞行。 2.3超重力凝固
重力加速度g>9.8m/s2环境下凝固。此条件下加速了 质量、动量及能量的传递。实现超重力的手段有:离心 机;飞机、火箭的加速上升等。
铝合金的熔炼及铸轧
主要内容
一、超级铝 二、金属的凝固 三、铝合金熔炼 四、铝合金铸轧
一、超级铝
1.1 超级铝 在现有金属装备基础上将金属合 金性能提高50%-80%。
1.2 实现的途径 (1)熔炼 (2)铸造 (3)变形 (4)热处理
合金熔炼
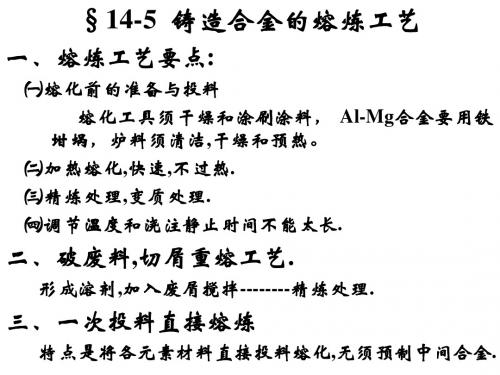
二 铝青铜的熔炼 (ZQAl9-4)
• • 须注意氧化和吸气 加熔剂→ 搅拌→脱氧 脱氧(1150-1180℃) → 加熔剂 Cu → P-Cu 搅拌 脱氧 ℃ 精炼(1160-1200℃) → 炉前检验 中间合金 → 回炉料 → 精炼 ℃ → 调节温度 → 加少许熔剂, 搅拌, 清渣,浇注,也 加少许熔剂, 搅拌, 清渣,浇注, 有用其他方法进行熔炼的。 有用其他方法进行熔炼的。
3:真空除氧 真空除氧: 真空除氧
㈢铜合金的熔剂精炼: 铜合金的熔剂精炼
• • • • • • • • 熔剂: 覆盖剂:减少元素氧化和铜液吸气 减少元素氧化和铜液吸气. 熔剂 覆盖剂 减少元素氧化和铜液吸气 精炼剂:精炼作用 精炼作用. 精炼剂 精炼作用 去除酸性夹杂物(SiO2·SnO2)用碱性熔剂 去除酸性夹杂物 用碱性熔剂 去除中性夹杂物(AL2O3)用碱性或酸性熔剂 用碱性或酸性熔剂. 去除中性夹杂物 用碱性或酸性熔剂 SiO2+Na2CO3→Na4SiO4+CO2↑ SnO2+ Na2CO3→Na2SnO3+CO2↑ AL2O3+ Na2CO3→Na2AL2O4+CO2↑ AL2O3+CaF→ALF3↑+CaO
二、铜合金精炼
㈠除氢精炼
• • • • • • • 1:吹氩精炼 吹氩精炼:10-15min(小件 15-20min(大件 小件) 大件) 吹氩精炼 小件 大件 2:氧化还原法精炼 氧化还原法精炼: 氧化还原法精炼 依据:氢氧平衡机理加锰矿 氢氧平衡机理加锰矿1-2% 依据 氢氧平衡机理加锰矿 MnO2→MnO+O2↑ 熔炼后期再加磷铜脱氧。 熔炼后期再加磷铜脱氧。 3:氯化锌法 氯化锌法:0.1-0.5%作用原理与铝合金相同 作用原理与铝合金相同. 氯化锌法 作用原理与铝合金相同 4:真空处理 使P[H]下降导致 下降。 真空处理:使 [H]下降导致[H]下降 [H]下降导致 下降。 真空处理
铸造合金及其熔炼复习重点

第一篇铸铁及其熔炼1、按石墨形态的不同,铸铁分为灰口铸铁;球墨铸铁;蠕墨铸铁。
2、在Fe-G-Si相图中,硅的作用(1)共晶点和共析点含碳量随硅量的增加而减少;(2)共晶转变和共析转变出现三相共存区;(3)改变共晶转变温度范围;提高共析转变温度;(4)减小奥氏体区域。
3、只考虑Si、P等元素对共晶点实际碳量影响的计算公式为CE=C+1/3(Si+P);4、亚共晶铸铁凝固特点:凝固过程中,共晶体不是在初析树枝晶上以延续的方式在结晶前沿形核并长大,而是在初析奥氏体晶体附近的枝晶间、具有共晶成分的液体中单独由石墨形核开始;石墨作为领先相与共晶奥氏体共生生长;5、过共晶铸铁的凝固特点:凝固过程则由析出初析石墨开始,到达共晶温度时,共晶石墨在初析石墨上析出,共晶石墨与初析石墨相连。
6、石墨的晶体结构是六方晶体。
7、如图所示,形成片状石墨的晶体生长是A向占优,而球状石墨是C向生长占优,8、F、C型石墨属于过共晶成分铸铁中形成的石墨A型B型D型F型9、球状石墨形成的两个必要条件:铁液凝固时必须有较大的过冷度;铁液与石墨间较大的表面张力。
10、球墨铸铁的球状石墨的长大包括两个过程:石墨球在熔体中直接析出并长大;形成奥氏体外壳,在奥氏体外壳包围下长大。
11、由于球状石墨的生长是在共晶成分下形成的石墨和奥氏体分离长大,因此其共晶过程又称之为离异共晶;12、灰铸铁的金相组织由金属基体和片状石墨组成,基体的主要形式有珠光体、铁素体、珠光体加铁素体。
13、普通铸铁中除铁以外,五大基本元素包括碳、硅、锰、硫、磷,其中碳、硅是最基本的成分,磷、硫是杂质元素,因此加以限制。
14、在铁碳双重相图中,稳定系和亚稳定系的共晶反应温度差别形成了共晶温度间隔,对于Ni、Si、Cr、S这四种元素来说,促进合金液在冷却过程中按稳定系转变的元素有Ni、Si,按亚稳定系转变的元素有Cr、S。
15、Cr元素在铸铁中的作用:(1)反石墨化元素,珠光体稳定元素;(2)Cr是缩小γ区元素;(3) 在含量超过2%易形成白口组织,(4) Cr含量在10%~30%,形成高碳化合物以及在铸件表面形成氧化膜,从而用作耐磨、耐热零件。
铸造合金及其熔炼课程重点

1.铁-碳相图的二重性: Fe-C合金中的碳有渗碳体Fe3C和石墨两种存在形式。
在通常情况下,碳以Fe3C的形式存在,即Fe-C 合金按Fe-Fe3C系转变。
但Fe3C是一亚稳相,在一定条件下分解为铁和石墨,所以石墨是碳存在的更稳定状态。
这样Fe-C相图就有Fe-Fe3C和Fe-G两种形式。
2.. Fe-C相图的应用①铸造工艺方面:根据相图确定合金的浇注温度,一般在液相线以上50-100 ℃。
共晶成分附近合金的流动性好,分散缩孔少,可获得致密铸件。
②热锻和热轧方面:钢处于奥氏体状态时强度较低,塑性较好,因此锻造或轧制选在单相奥氏区进行。
一般始锻或始轧温度控制在固相线以下100-200 ℃。
③热处理方面:一些热处理工艺如退火,正火,淬火的加热温度都是依据相图确定的。
3.碳当量:根据各元素对共晶点实际碳量的影响,将这些元素的量折算成碳量的增减,称之碳当量。
以CE表示,一般只考虑Si和P。
CE=C+1/3(Si+P)。
4.共晶度:铸铁的实际含碳量和共晶点实际含碳量的比值。
以Sc来表示。
S C=C铁/C c′。
5.热过冷:因纯金属的理论凝固温度是恒定的,凝固过程中过冷度完全取决于实际温度分布,即过冷度的大小和过冷区的形态是由传热所控制,这种过冷称为热过冷。
6.硅对相图的影响:①硅使共晶点和共析点左移,即减小共晶和共析含碳量,其中对共晶含碳量影响较显著。
②硅略微提高共晶和共析转变温度,并使转变在一个温度区间中进行,对共析转变温度范围的作用更为显著。
③硅的加入,使相图出现了共晶和共析转变的三相共存区④随着硅含量的增加,相图上的奥氏体区逐渐缩小。
7.片状G的形成过程:①形成条件: a. 螺位错台阶:即沿a向,又沿c向生长,最后长成具有一定厚度的片状石墨。
b. 旋转晶界:取决于Va/Vc。
普通HT中G呈片状,这是由于O、S等活性元素在G棱面上的吸附,使这个原本光滑的界面变得粗糙,只需小的过冷即沿a向生长,使Va﹥Vc,长成片状石墨。
铸造合金及其熔炼复习总结资料

铸铁1 为什么有双重相图的存在?双重相图的存在对铸铁件生产有何实际意义?硅对双重相图的影响又有何实际意义?答:1>从热力学观点看,在一定条件下,按Fe-Fe3C相图转变亦是有可能的,因此就出现了二重性2>通过双重相同,可以明显的看出稳定平衡在发生共晶转变及共析转变时,其温度要比介稳定平衡发生时的温度高,而发生共晶、共析转变时所需含C量,以及转变后的r中的含碳量,稳定平衡要比介稳定平衡低。
依此规律,就可以通过控制温度成分来控制凝固后的铸铁组织。
3>硅元素的作用:a:共晶点和共析点含碳量随硅量的增加而减少b:硅的加入使相图上出现了共晶和共析转变的三重共存区c:共晶和共析温度范围改变了,含硅量越高,稳定系的共晶温度高出介稳定系的共晶温度越多d:硅量的增加,缩小了相图上的奥氏体区2.铸铁中Si的含量范围以及其对Fe-G相图的影响A共晶点和共析点的含碳量随硅量的增加而减小E*点的含碳量也随硅的增高而减少B硅的加入使相图上出现了共晶和共析转变的三相共存区共晶区:l.r.G共析区r.F.G说明铁-碳-硅三元合金的共析和共晶转变,是在一个温度范围内进行,并且共析转变温度范围随硅量增大而扩大C随含硅量的增加,稳定系与介稳定系的共晶温度差别扩大即含硅量越高。
r+G的共晶温度高出r+Fe3C的共晶温度越多,Si越高,共析转变温度提高更多,有利于铁素体基体的获得D硅的增加,缩小了相图的奥氏体区,硅的含量超过10%,r区趋于消失3.铸铁中,石墨的六种形态及其形成机理六种石墨分布分类1、片状:形成条件:石墨成核能力强,冷却速度慢,过冷度小2、菊花状:实际上中心是D形外围是A形,开始时过冷大,成核条件差、先出D型,后期放出凝固潜热,过冷减小而析出A型3、块片状:过共晶时在冷速较小时形成4、枝晶点状:冷速打过冷大导致G强烈分枝5、枝晶片状冷速小初生γ枝晶 6、星状:过共晶冷速较大。
4.铸铁结晶过程(1)灰口铸铁是铁液以奥氏体-石墨共晶方式结晶而生成的组织,当铸铁的成分为亚共晶时,在发生共晶转变之前先结晶出初生奥氏体,而当成分为过共晶时,则在发生共晶转变之前先结晶出初生石墨。
鸿图铸造铝合金熔炼培训

•
•
除气原理:向铝液中加入精炼剂或者通入气体(N2、Ar)或混合气体,在铝液中直接 或间接生成大量不溶于铝液的气泡,铝液中溶解状态的气体原子向这些气体扩散,进 入其中,形成气体分子,同时伴随着气泡上浮到液面,气泡破裂,氮气逸入大气。 当气泡向上运动过程中遇到夹杂物,由于表面张力作用,夹杂物就粘附在气泡表面上, 最后气泡把夹杂物带到液面的渣中,在清除气体的同时也去除了夹杂物,达到精炼效 果。
4、熔炼时间的控制 为了减少铝熔体的氧化、吸气和铁的溶解,应尽量缩短铝熔体在炉内 的停留时间,快速熔炼。从熔化开始至浇注完毕,砂型铸造不超过4 小时,金属型铸造不超过6小时,压铸不超过8小时。 为加速熔炼过程,应首先加入中等块度、熔点较低的回炉料及铝硅中 间合金,以便在坩埚底陪尽快形成熔池,然后再加块度较大的回炉料 及纯铝锭,使它们能徐徐浸入逐渐扩大的熔池,很快熔化。在炉料主 要部分熔化后,再加熔点较高、数量不多的中间合金,升温、搅拌以 加速熔化。最后降温,压入易氧化的合金元素,以减少损失。 5、熔体的转送和浇注 尽管固态氧化铝的密度近似于铝熔体的密度,在进入铝熔体内部后,经 过足够长的时间才会沉至坩埚底部。而铝熔体被氧化后形成的氧化铝 膜,却仅与铝熔体接触的一面是致密的,与空气接触的一面疏松且有 大量直径为60--100A的小孔,其表面积大,吸附性强,极易吸附在水 汽,反有上浮的倾向。因此,在这种氧化膜与铝熔体的比重差小,将 其混入熔体中,浮沉速度很慢,难以从熔体中排除,在铸件中形成气 孔及夹杂。所以,转送铝熔体中关键是尽量减少熔融金属的搅拌,尽 量减少熔体与空气的接触。 采用倾转式坩埚转注熔体时,为避免熔体与空气的混合,应将浇包 尽量靠所炉咀,并倾斜放置,使熔体沿着浇包的侧壁下流,不致直接 冲击包底,发生搅动、飞溅等。
熔炼培训资料

铝合金的熔炼工艺一,铝的基础知识1,铝的比重:2.72,铝的熔点: 660℃(99,80), 655℃工业纯铝(≧99.50)3,铝的标准:国标,行业标准,企业标准(内控),协议标准4,铝及铝合金的分类1XXX纯铝系 2XXX铝铜系 3XXX铝锰系 4XXX铝硅系5XXX铝镁系 6XXX铝镁硅 7XXX铝锌系 8XXX 9XXX5,铝合金按合金成份分为铸造铝合金变形铝合金变形铝合金按热处理特点又分为热处理可强化铝合金,热处理不可强化铝合金1XXX 3XXX 4XXX 大多数属热处理不可强化铝合金5XXX 8XXX 属于不可热处理强化铝合金2XXX 6XXX 7XXX属于热处理可强化铝合金二,熔炼的工艺流程原料的准备-----装炉-------熔炼-----扒渣-------加合金-------搅拌-------取样-------调整成份-----转炉原料的准备:配料的任务1,控制合金成份和杂质含量,使之符合有关标准。
2 合理利用各种炉料降低生产成本。
3,保证炉料质量,正确配料为提高产品质量和成品率创造有利条件。
装炉:装炉的顺序。
先装碎料后装大快料,避免熔炼烧损,保护炉底。
熔炼1,熔炼炉的炉膛温度设定≦1050℃2,熔炼的温度要求3XXX730℃-770℃其他合金720℃-760℃扒渣1,化平料就扒渣使之减少渣的燃烧2,加合金之前扒渣加合金加合金温度735-750,从炉门口加入合金添加剂后要用耙子在炉门口搅拌,使之加快溶解,成份更加均匀。
搅拌加合金及添加剂后,启动电磁搅拌器,一个搅拌旋转周期5分钟要经过正反正三个旋转周期,特殊情况要增加旋转周期。
取样炉前取样很关键,必须按相应的程序进行,否则会造成分析误差。
调整成分根据炉前分析,进行成份调整,中间合金可以在流槽加入。
合金添加剂要加入炉内搅拌后重新取样。
合金熔炼学习知识重点情况总结

合金熔炼知识点总结1.铸造性能:流动性,充型能力,收缩性,偏析。
气体及夹杂物等2.合金的流动性与充型能力的区别1)充型能力是液态金属充满型腔获得形状完整,轮廓清晰铸件的能力流动性是指液态铸造合金本身的流动能力。
2)流动性好的合金,其充型能力强3)流动性影响因素:合金的种类,化学成分及结晶特点3.收缩性:铸造合金从液态冷却到室温的过程中,其体积和尺寸缩减的现象称为收缩性。
1)收缩的三个阶段;液态收缩阶段,凝固收缩阶段,固态收缩阶段。
2)收缩方法:体收缩,线收缩3)影响收缩的因素:化学成分,浇注温度,铸件结构与铸型条件4)收缩对铸件质量的影响:产生缩松和缩孔[主要原因是液态收缩和凝固收缩]防治措施:调整化学成分,降低浇注温度和减少浇注速度,增加补缩能力,增加铸型激冷能力。
6.铸造应力:铸件在凝固冷却的过程中因温度的下降而产生收缩使铸件和长度发生变化,若这些变化受到阻碍便会在铸件中产生应力称为铸造应力。
1)铸造应力按其产生的原因可分为三种:热应力,固态相变应力,收缩应力2))铸造应力的防止和消除措施:采用同时凝固的原则提高铸型温度改善铸型和型芯的退让性进行去应力退火7.铸铁:铸铁是一系列主要由铁、碳和硅组成的合金的总称[铁,碳,硅,锰,磷,硫及其其他合金元素]1)铸铁中的碳以化合态渗碳体和游离态石墨形式存在2).影响铸铁组织和性能的因素:a.碳和硅[铸铁中碳、硅含量均高时,析出的石墨就愈多、愈粗大]b.硫[强烈阻碍石墨化,增加热脆性,恶化铸铁铸造性能硫含量限制在0.1-0.15%以下]c.锰[弱阻碍石墨化,具有提高铸铁强度和硬度的作用锰含量控制在0.6~1.2%之间]d.磷[对铸铁的石墨化影响不显著。
含磷过高将增加铸铁的冷脆性磷含量限制在0.5%以下]8.铸铁分类:1)按碳存在形式分:白口铸铁,灰口铸铁,麻口铸铁2)按石墨存在形式分:灰铸铁,可锻铸铁,球墨铸铁,蠕墨铸铁3)按化学成分分:普通铸铁,合金铸铁4)按性能分:耐热铸铁,耐磨铸铁,耐腐蚀铸铁9.灰铸铁(HT):指碳主要以片状石墨形式出现的铸铁,断口呈灰色。
合金熔炼
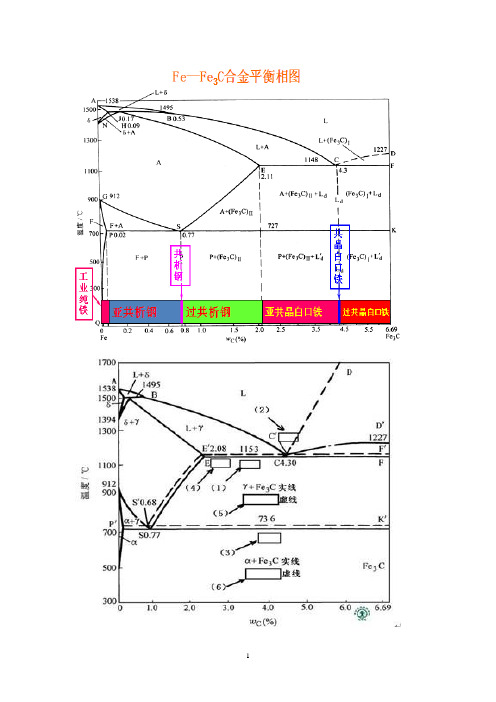
1.纯铁——含碳量<0.0218%,显微组织为铁素体。
2.钢——含碳量0.0218%~2.11%,特点是高温组织为单相奥氏体,具有良好的塑性,因而适于锻造。
根据室温组织的不同,钢又可以分为:亚共析钢:含碳量0.0218%~0.77%,具有铁素体α+珠光体P的组织,且含碳量越高(接近0.77%),珠光体的相对量越多,铁素体量越少。
共析钢:含碳0.77%,组织是全部珠光体P。
过共析钢:含碳量0.77%~2.11%,组织是珠光体P+渗碳体Fe3C。
白口铁——含碳量2.11%~6.69%,特点是液态结晶时都有共晶转变,因而具有良好的铸造性能。
但是即使在高温也是脆性材料,不能锻造。
根据室温组织不同,白口铁又分为:亚共晶白口铁:含碳2.11%~4.30%,组织是珠光体P+渗碳体Fe3C+莱氏体Ld'。
共晶白口铁:含碳4.30%,组织是莱氏体Ld'。
过共晶白口铁:含碳4.3%~6.69%,组织渗碳体Fe3C+莱氏体Ld'。
ES线是碳在奥氏体中的溶解度曲线。
奥氏体的最大溶碳量是在1148℃时,可以溶解2.11%的碳。
而在727℃时,溶碳量仅为0.77%,因此含碳量大于0.77%的合金,从1148℃冷到727℃的过程中,将自奥氏体中析出渗碳体,这种渗碳体称为二次渗碳体(Fe3CII)。
GS线冷却过程中,奥氏体向铁素体转变的开始线;或者说是加热过程中,铁素体向奥氏体转变的终了线(具有同素异晶转变的纯金属,其固溶体也具有同素异晶转变,但其转变温度有变化)。
第二章:灰铸铁灰铸铁:有片状石墨的铸铁。
(碳当量CE=C%+1/3Si)(有抗拉要求,无塑韧性要求)冲天炉:成本低,速度快,杂质多熔炼:感应电炉:速度快,热效率高碳当量:各元素对共晶点实际C量的影响,这些元素这算成碳量的增加或减少。
共晶度:铸铁中实际C的质量分数与C当量共晶值之比。
可衡量铸铁偏离共晶的程度。
共晶团:铸铁共晶转变过程中,由铁液中结晶出来的石墨-奥氏体(共生生长)所构成的集合体。
铝合金熔炼与铸造

铝合金熔炼与铸造铝合金是一种常见且广泛使用的金属材料,具有较低的密度、良好的导热性和耐腐蚀性,因此在许多行业中得到了广泛的应用。
铝合金的熔炼和铸造是制造铝合金制品的关键步骤。
本文将介绍铝合金熔炼和铸造的基本原理、工艺和注意事项。
一、铝合金熔炼1.1 熔炼原理铝合金熔炼的主要原理是将铝及其他合金元素加热至其熔点,使其融化成液态,以便进行后续的铸造工艺。
铝的熔点较低,约为660°C,因此相对较容易熔化。
而其他合金元素的加入可以改变铝合金的性质,例如提高其强度、耐腐蚀性或者改善加工性能。
1.2 熔炼工艺铝合金熔炼工艺一般分为两种:批量熔炼和连续熔炼。
批量熔炼是将一定量的铝和其他合金元素加入炉内,通过加热熔化成液态,并进行充分混合。
这种方法适用于小规模生产,常用的炉型有电阻炉和燃气炉。
而连续熔炼是将铝合金材料加入熔炉的顶部,通过炉内的加热和熔化过程,使得底部的液态铝合金不断流出。
这种方法适用于大规模生产,常用的炉型有回转炉和隧道炉。
1.3 熔炼注意事项在铝合金的熔炼过程中,需要注意以下几个方面。
首先,炉内的温度需要控制在适当的范围内,以避免过度燃烧或者过度冷却。
其次,需要保持良好的熔炼环境,防止氧气、水分或杂质等对炉内材料的影响。
最后,在加入其他合金元素时,需要根据配比和工艺要求进行准确的添加,以保证最终铝合金的性能。
二、铝合金铸造2.1 铸型设计铝合金铸造的第一步是进行铸型设计。
铸型设计的目的是根据最终产品的形状和要求,确定合适的铸造方法和材料,以及适当的铸型结构。
常见的铸型结构有砂型、金属型和陶瓷型等。
其中砂型是最常用的铸造方法,可以应用于各种形状和尺寸的产品。
2.2 铸造工艺铝合金的铸造工艺可以分为传统铸造和压铸两种。
传统铸造是将熔融的铝合金液体倒入铸型中,并通过自然冷却形成最终产品。
这种方法适用于小批量生产,但精度和表面光滑度相对较低。
压铸是将高压液压机将铝合金液体注入铸型中,通过压力传递和快速冷却,实现快速成型。
铝合金熔炼的基本知识

铝合金熔炼的基本知识装料熔炼时,装入炉料的顺序和方法不仅关系到熔炼的时间、金属的烧损、热能消耗,还会影响到金属熔体的质量和炉子的使用寿命。
装料的原则有:1、装炉料顺序应合理。
正确的装料要根据所加入炉料性质与状态而定,而且还应考虑到最快的熔化速度,最少的烧损以及准确的化学成分控制。
装料时,先装小块或薄片废料,铝锭和大块料装在中间,最后装中间合金。
熔点易氧化的中间合金装在中下层。
所装入的炉料应当在熔池中均匀分布,防止偏重。
小块或薄板料装在熔池下层,这样可减少烧损,同时还可以保护炉体免受大块料的直接冲击而损坏。
中间合金有的熔点高,如AL-NI和AL-MN合金的熔点为750-800℃,装在上层,由于炉内上部温度高容易熔化,也有充分的时间扩散;使中间合金分布均匀,则有利于熔体的成分控制。
炉料装平,各处熔化速度相差不多这样可以防止偏重时造成的局部金属过热。
炉料应进量一次入炉,二次或多次加料会增加非金属夹杂物及含气量。
2、对于质量要求高的产品(包括锻件、模锻件、空心大梁和大梁型材等)的炉料除上述的装料要求外,在装料前必须向熔池内撒20-30kg粉状熔剂,在装炉过程中对炉料要分层撒粉状熔剂,这样可提高炉体的纯洁度,也可以减少损耗。
3、电炉装料时,应注意炉料最高点距电阻丝的距离不得少于100mm,否则容易引起短路。
熔化炉料装完后即可升温。
熔化是从固态转变为液态的过程。
这一过程的好坏,对产品质量有决定性的影响。
A、覆盖熔化过程中随着炉料温度的升高,特别是当炉料开始熔化后,金属外层表面所覆盖的氧化膜很容易破裂,将逐渐失去保护作用。
气体在这时候很容易侵入,造成内部金属的进一步氧化。
并且已熔化的液体或液流要向炉底流动,当液滴或液流进入底部汇集起来时,其表面的氧化膜就会混入熔体中。
所以为了防止金属进一步氧化和减少进入熔体的氧化膜,在炉料软化下塌时,应适当向金属表面撒上一层粉状熔剂覆盖,其用量见表。
这样也可以减少熔化过程中的金属吸气。
铸造合金及其熔炼复习
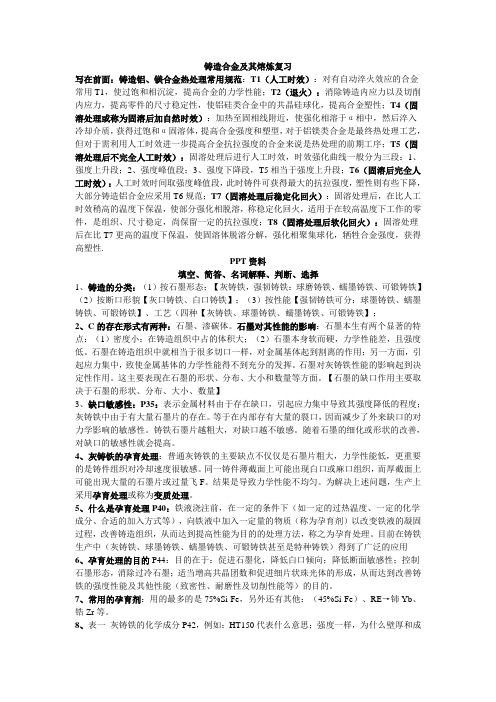
铸造合金及其熔炼复习写在前面:铸造铝、镁合金热处理常用规范:T1(人工时效):对有自动淬火效应的合金常用T1,使过饱和相沉淀,提高合金的力学性能;T2(退火):消除铸造内应力以及切削内应力,提高零件的尺寸稳定性,使铝硅类合金中的共晶硅球化,提高合金塑性;T4(固溶处理或称为固溶后加自然时效):加热至固相线附近,使强化相溶于α相中,然后淬入冷却介质,获得过饱和α固溶体,提高合金强度和塑型,对于铝镁类合金是最终热处理工艺,但对于需利用人工时效进一步提高合金抗拉强度的合金来说是热处理的前期工序;T5(固溶处理后不完全人工时效):固溶处理后进行人工时效,时效强化曲线一般分为三段:1、强度上升段;2、强度峰值段;3、强度下降段,T5相当于强度上升段;T6(固溶后完全人工时效):人工时效时间取强度峰值段,此时铸件可获得最大的抗拉强度,塑性则有些下降,大部分铸造铝合金应采用T6规范;T7(固溶处理后稳定化回火):固溶处理后,在比人工时效稍高的温度下保温,使部分强化相脱溶,称稳定化回火,适用于在较高温度下工作的零件,是组织、尺寸稳定,尚保留一定的抗拉强度;T8(固溶处理后软化回火):固溶处理后在比T7更高的温度下保温,使固溶体脱溶分解,强化相聚集球化,牺牲合金强度,获得高塑性.PPT资料填空、简答、名词解释、判断、选择1、铸造的分类:(1)按石墨形态;【灰铸铁,强韧铸铁:球磨铸铁、蠕墨铸铁、可锻铸铁】(2)按断口形貌【灰口铸铁、白口铸铁】;(3)按性能【强韧铸铁可分:球墨铸铁、蠕墨铸铁、可锻铸铁】、工艺(四种【灰铸铁、球墨铸铁、蠕墨铸铁、可锻铸铁】;2、C的存在形式有两种:石墨、渗碳体。
石墨对其性能的影响:石墨本生有两个显著的特点:(1)密度小:在铸造组织中占的体积大;(2)石墨本身软而硬,力学性能差,且强度低。
石墨在铸造组织中就相当于很多切口一样,对金属基体起到割离的作用;另一方面,引起应力集中,致使金属基体的力学性能得不到充分的发挥。
合金及熔炼总结

魏氏体组织:凝固过程中,在晶粒中出现贯穿晶体的铁素体相,降低力学性能。
共晶转变:一个液相同时结晶出两种成分的固相的三相平衡转变。
L=α+Fe3c匀晶转变:由液相结晶出单相固液体的二相平衡转变L=α包晶转变:已结晶出来的一定成分的固相与剩余液相生成另一种固相的恒温转变L+α=β熔晶转变:一个固相生成液相和另一种固相的三相平衡转变α—L+β偏晶转变:一个液相转变为一个固相和一个成分不同的液相的三相平衡L—α+L’合晶转变:两种不同成分的液相共同作用转变为一个固相的三相平衡L1+L2=β共析转变:一个固相分解为两个成分和结构不同的固相的三相平衡转变r=α+Fe3c包析转变:两个不同成分固相共同作用生成一个新固相的三相转变r+fe2b=α(910℃)相:合金中具有同一聚集状态,晶体结构,成分基本相同。
并有明确的界面与其他部分分开的均匀组织部分。
组织:用肉眼或显微镜所观察到的不同组成相的形状分布及各相之间的组合状态。
固溶体:以合金中某一组元为溶剂,在晶格中溶入其他组元原子,形成的一种合金相,并保持溶剂的晶格结构。
合金:由两种或两种以上的元素经过烧结熔炼或其他制备方法成为具有金属特性的材料。
金属间化合物:金属与金属或准金属形成的化合物微晶合金:凝固晶粒尺寸达微米纳米级准晶:介于晶体和非晶体之间的固体单晶体:由一个晶核长大的晶体非晶态合金:在急冷条件下,虽然形核与长大的结晶过程受到抑制,但发生连续的整体凝固,得到了保留液态短程有序结构或金属玻璃。
离异共晶:共晶两相没有共同生长的界面,他们以各自不同的速度独立生长,两相析出在时间和空间上彼此分离的,形成组织没有共晶的特征。
特点:晕圈和晶间偏析流动性:铁液填充铸型的能力。
铸造应力:铸件在凝固以后的冷却过程中,体积变化不能自由进行,于是在产生变形的同时还产生应力。
热冷倾向:冷:完全凝固后冷却至塑性,弹性转变温度以上,铸件中的内应力超过钢的强度。
热:固相线温度附近形成热裂:在凝固后期受到来自铸型型芯或其他方面的机械阻碍所造成的,提高石墨化能力线收缩下降,防止热裂。
合金熔炼知识点总结

合金熔炼知识点总结一、合金熔炼的基本原理1. 合金的定义合金是由两种或两种以上的金属或非金属混合而成的固态溶液体系。
合金相较原始金属,具有更好的性能和应用价值。
一般来说,合金的熔点要高于其中任何一种原料的熔点。
2. 合金熔炼的原理合金熔炼是指在一定温度下,将金属原料加热至熔点,使其熔化并混合在一起。
通过精确控制合金组分、温度和时间等参数,可以获得具有特定性能和结构的合金材料。
二、合金熔炼的原料选择1. 合金熔炼的基本原料合金熔炼的原料包括金属原料和非金属原料两大类。
金属原料一般分为主合金元素和合金添加元素,如铝、铜、镍、锌等。
非金属原料包括矿石、金属氧化物、还原剂等。
2. 原料选择的原则(1)选择纯度高的原料,以保证制备出的合金材料具有良好的性能。
(2)考虑合金成分的配比,根据合金材料的要求和应用情况,选择合适的主合金元素和添加元素。
(3)考虑原料的价格和供应情况,选择成本适中且易于获得的原料。
三、合金熔炼的熔炼设备1. 熔炼炉的类型熔炼设备主要包括电弧炉、感应炉、电阻炉、燃烧炉等多种类型。
不同类型的熔炼炉适用于不同的合金熔炼工艺和要求。
2. 熔炼设备的选择(1)根据合金熔炼的规模和生产要求选择合适的熔炼设备,如小型试验炉、中型工业炉或大型生产线设备。
(2)考虑能源消耗、设备维护、操作便利性等因素,选择适合的熔炼设备。
四、合金熔炼的工艺控制1. 温度控制合金熔炼过程中,温度是一个非常重要的参数,直接影响合金熔炼的成分均匀性、物理性能和化学性能。
因此,必须严格控制合金熔炼过程中的温度波动和温度均匀性。
2. 时间控制熔炼时间的长短也会影响合金熔炼的成分均匀性和结晶状态。
一般情况下,较长的熔炼时间有利于混合均匀,但也可能导致合金成分变化和能耗增加。
3. 流动控制在熔炼过程中,为了保证合金成分的均匀性,需要控制熔体的流动状态。
通过合理设计和控制炉型结构、搅拌器等参数,可以获得较好的熔体流动性。
4. 气氛控制熔炼过程中,需要考虑熔池中氧气、水蒸气等杂质气体的影响。
合金及熔炼总结

1.石墨形成过程
片状:G—六方结构,在基面上存在螺旋位错缺陷,为石墨生长提供了大量生长台阶
球状:1,较大的过冷度2,铁液和石墨间有较大的界面张力
蠕状:小球墨——畸变球墨——蠕状球墨,取决于蠕化元素的浓度
灰铸铁的性能:强度较差硬度有一定范围,较低的缺口敏感性,良好的减震性,良好的减摩灰铸铁强度较差的原因:
1 缩减作用:G片在铸铁中占一定体积,使得铸铁的有效截面积减少,即空洞
2 缺口敏感性:G片的片端类似于一些纤维裂纹,引起应力集中
球墨铸铁的铸造性能流动性:脱硫除气等净化铁液,流动性↑,经球化孕育处理后,铁液温度下降,流动性↑,mg加入铁液表面张力增加,流动性↑,球铁流动性不如铸铁好
2.球化过程及球墨中常见缺陷球化:铁液中加入球化剂,能使石墨在结晶生长时成球状
熔炼→球化处理→孕育处理→消除过冷倾向,促进石墨化,减小晶间偏析
常见缺陷产生原因及解决方法
①缩孔缩松浇筑温度不宜过高,增加铸型刚度,提高G膨胀体积,采用冒口冷铁补缩
②夹渣一次渣——球化处理硫氧化合物未除净二次渣——浇筑凝固前形成渣,尺寸较小降低铁液中硫含量,浇筑前清除表面熔渣。
铝合金熔炼知识问答

●●1;影响再结晶晶粒大小的因素有那些?一般来说,随合金元素及杂质含量的增加,晶粒尺寸减小。
因为不论合金元素溶于固溶体中,还是生成弥散相,均阻碍晶界迁移,有利于得到细晶粒组织。
但某些合金,若固溶体成分不均匀,则反而可能出现粗大组织。
熔炼温度越高,再结晶完成时间越短,在相同保温时间下,从而最终得到粗大的晶粒。
●2;什么是超轻铝合金?密度比一般铝合金低10%以上的铝合金叫超轻铝合金。
在铝中添加2%--3%的Li(锂),密度可降低10%,弹性模量可提高25—30%,因此AL—Li是典型的超轻铝合金。
●3;什么是软铝合金?抗拉强度<294Mpa的合金称为软铝合金。
一般有工业纯铝,铝锰合金,(如3003,3004等),铝硅合金4004,4043等。
●4;什么是防暴铝合金?在相互摩擦,碰撞中不产生火花,能在易燃易暴的环境中使用,不会燃烧和爆炸的铝合金叫防暴铝合金,其主要元素有Cu,Zn,Fe等高熔点元素,但必须控制Mg,Li等活性元素,如Mg 含量在0.05%以下。
●5;什么是再生铝合金?再生铝是由废旧铝和铝合金材料或含铝的废料,经重熔提炼而得到的铝合金或铝金素,它是;铝的一个重要来源,目前再生铝占铝年产量的1/3以上。
再生铝的性能与原铝的性能相同。
可用再生铝锭重溶,精练和净化,经调整化学成分制成各种铸造铝合金。
●6;铝合金熔炼的特点及典型的熔炼工艺流程;熔炼就是使金属合金化的一种方法。
他是采用加热的方法改变金属的状态,使机体金属和合金化组元按要求的配比熔制成成分均匀的熔体,并使其满足内部纯净度,铸造温度和其他特定条件的一种工艺过程。
如果熔体先天不足,将给制品的使用带来先天不足,因此熔炼是对压铸质量起支配作用的一道关键工序。
●7;铝合金熔炼的特点;铝非常活泼,很容易和氧气和水发生反应Al+O2→Al202 Al+H2O→Al203+H2 这些反应都是不可逆的,一经反映金属就不能还原,这样就造成了金属的大量损失(及烧损)而且生成物进入熔体,将会污染熔体,造成铸件内部缺陷。
- 1、下载文档前请自行甄别文档内容的完整性,平台不提供额外的编辑、内容补充、找答案等附加服务。
- 2、"仅部分预览"的文档,不可在线预览部分如存在完整性等问题,可反馈申请退款(可完整预览的文档不适用该条件!)。
- 3、如文档侵犯您的权益,请联系客服反馈,我们会尽快为您处理(人工客服工作时间:9:00-18:30)。
合金熔炼知识点总结1.铸造性能:流动性,充型能力,收缩性,偏析。
气体及夹杂物等2.合金的流动性与充型能力的区别1)充型能力是液态金属充满型腔获得形状完整,轮廓清晰铸件的能力流动性是指液态铸造合金本身的流动能力。
2)流动性好的合金,其充型能力强3)流动性影响因素:合金的种类,化学成分及结晶特点3.收缩性:铸造合金从液态冷却到室温的过程中,其体积和尺寸缩减的现象称为收缩性。
1)收缩的三个阶段;液态收缩阶段,凝固收缩阶段,固态收缩阶段。
2)收缩方法:体收缩,线收缩3)影响收缩的因素:化学成分,浇注温度,铸件结构与铸型条件4)收缩对铸件质量的影响:产生缩松和缩孔[主要原因是液态收缩和凝固收缩]防治措施:调整化学成分,降低浇注温度和减少浇注速度,增加补缩能力,增加铸型激冷能力。
6.铸造应力:铸件在凝固冷却的过程中因温度的下降而产生收缩使铸件和长度发生变化,若这些变化受到阻碍便会在铸件中产生应力称为铸造应力。
1)铸造应力按其产生的原因可分为三种:热应力,固态相变应力,收缩应力2))铸造应力的防止和消除措施:采用同时凝固的原则提高铸型温度改善铸型和型芯的退让性进行去应力退火7.铸铁:铸铁是一系列主要由铁、碳和硅组成的合金的总称[铁,碳,硅,锰,磷,硫及其其他合金元素]1)铸铁中的碳以化合态渗碳体和游离态石墨形式存在2).影响铸铁组织和性能的因素:a.碳和硅[铸铁中碳、硅含量均高时,析出的石墨就愈多、愈粗大]b.硫[强烈阻碍石墨化,增加热脆性,恶化铸铁铸造性能硫含量限制在0.1-0.15%以下]c.锰[弱阻碍石墨化,具有提高铸铁强度和硬度的作用锰含量控制在0.6~1.2%之间]d.磷[对铸铁的石墨化影响不显著。
含磷过高将增加铸铁的冷脆性磷含量限制在0.5%以下]8.铸铁分类:1)按碳存在形式分:白口铸铁,灰口铸铁,麻口铸铁2)按石墨存在形式分:灰铸铁,可锻铸铁,球墨铸铁,蠕墨铸铁3)按化学成分分:普通铸铁,合金铸铁4)按性能分:耐热铸铁,耐磨铸铁,耐腐蚀铸铁9.灰铸铁(HT):指碳主要以片状石墨形式出现的铸铁,断口呈灰色。
它是工业中应用最广的铸铁。
1)灰口铸铁的组织:铁素体+片状石墨铁素体.珠光体+片状石墨珠光体+片状石墨2)灰铸铁的性能特点:抗拉强度,塑性韧性均不如钢属于脆性材料; 铸造性能较好; 具有良好的减振性; 耐磨性好缺口敏感性低.3)灰铸铁的孕育处理目的:消除白口、细化组织,改善石墨形态,提高组织均匀性4)灰铸铁孕育处理工艺过程:在浇注前往铁水中加入硅铁(FeSi75)和硅钙合金。
等孕育剂,使铁水产生大量均匀分布晶核,使石墨片及基体组织得到细化5)灰铸铁孕育剂:硅铁(FeSi75)和硅钙合金。
6)孕育铸铁特点:强度和韧性优于普通灰铸铁组织较均匀,性能基本一致9)灰铸铁炉前检验方法:试样冷却至暗红色(600-700度)淬水打断测量试样白口宽度,观察截面组织。
[白口宽度大,碳当量低,断口发暗,硅量低,发亮则硅量合适,发黑,则碳高,色淡中心细粒则碳低]7)灰铸铁牌号:HT”+ 数字﹛数字表示其最低抗拉强度σb (MPa)﹜8)提高灰铸铁性能的途径:合理选择化学成分(提高Si/C);孕育处理(孕育铸铁;低合金化(Ni, Cu, Mn, Cr, Mo, V);合成铸铁,改进炉料质量;对铸件进行热处理9.灰铸铁热处理特点:去应力处理,石墨化退火10.碳当量:是表示铸铁中贵和磷对铁碳共晶综合影响指标11.共晶度:普通灰铸铁中含碳量与共晶点含碳量的比值12.铸件的冷却速度大小与那些有关:a.铸件壁厚(铸件壁愈厚,冷却速度愈慢,则石墨化倾向愈大,愈易得到粗大的石墨片和铁素体基体),b.浇注温度(浇注温度高,冷却速度慢,石墨化倾向愈大)C.铸型散热条件13.球墨铸铁:球墨铸铁是铁液经过球化处理后使石墨大部分或全部呈球状,有时少量为团絮状的铸铁。
1). 球墨铸铁化学成分:一般碳当量质量分数选在共晶点附近(4.6~4.7%),碳的质量分数一般为3.5~3.9%;硅:珠光体球铁1.7~2.6%Si,铁素体球铁2.5 ~ 3.2%Si;锰、硫、磷:适当控制;镁和稀土:适当控制.2)球墨铸铁组织:铁素体(F)+球状石墨(G),铁索体(F)-珠光体(P)+球状石墨(G),珠光体(P)+球状石墨(G),下贝氏体(B下)+球状石墨(G)。
3)球墨铸铁的性能:a.有高的强度和良好的塑性与韧性;b.良好的铸造性能、减摩性、切削加工性及低的缺口敏感性4)..球墨铸铁的牌号:QT500-07[抗拉强度最低值为500MPa,伸长率最低值为7%]5).球墨铸铁的生产工艺过程:a控制原铁水化学成分[S和P。
Mn含量要低C含量要高(3.6~4.0%C)]b.较高的铁水温度[出炉温度应高于1400℃]注【铁水→孕育处理→球化处理】6).球墨铸铁球化处理a).球化剂的作用是使石墨呈球状析出。
b).球化剂:稀土镁合金。
8).镁球化剂在铁水中的作用:化学性质活泼,脱硫,去氧能力强。
镁对石墨起球化作用,能够促进石墨呈球状。
9).球化处理工艺有:冲入法和型内球化法。
冲入法:a).H/D>1.5常用堤坝式包底b)先将处理包预热>600-800度(暗红色)c).再将碎成一定粒度的球化剂(15-30mm)装入堤坝内紧实,上面覆盖硅铁粒(粒度<或等于球化剂,然后再覆盖草木灰,珍珠岩等集渣剂。
d)出铁液时不能正对球化剂,冲入2/3—1/2包铁液是停止出铁让铁液沸腾1-3mim后扒渣,再′补入其他的1/3—1/2铁液同时在铁曹内进行孕育,再补加铁液时若液面逸出镁光及白黄火焰表示球化正常10)球墨铸铁孕育处理:a)孕育剂的主要作用是促进石墨化,防止球化元素所造成的白口倾向,细化共晶团,,提高力学性能b).孕育剂:FeSi750合金C)孕育处理方法:炉前一次孕育法,倒包孕育法,瞬时孕育法11)球墨铸铁的炉前检测A).炉前三角试片检验法:a).先取样,将铁液浇入炉前三角试片砂型中,待试样冷至暗红色时,淬入水中冷却,b).打断试样,观察断口来判断球化是否良好c).判断标准:断口呈银白色光泽,尖角白口清晰,侧面有明显的缩陷,组织较细,遇水有电石臭味。
12)球墨铸铁常见铸造缺陷:球化不良,球化衰退,石墨漂浮,缩孔缩松,皮下气孔,夹渣。
13)球墨铸铁的热处理工艺:a).石墨退火目的:得到塑性韧性高的铁素体,球墨铸铁。
b).正火与回火,使晶粒细化,组织均匀,强度和硬度提高。
目的:获得以珠光体为主的基体组织c).淬火与回火淬火目的:将组织转变为含碳低的细小马氏体回火目的:降低铸件中残余应力和脆性,保持铸件的高硬度和耐磨性。
问答题1、在球墨铸铁生产中对原铁液有什么要求?铁液化学成分确定依据什么原则?要求:铁水温度要高,>1450度,对原材料要求高,原则:高碳,低硅,锰,硫,磷,强化孕育。
2、球化处理后为什么还必须进行孕育处理?目的;促进石墨化,防止球化元素所造成的白口倾向,细化共晶团,,提高力学性能14)铸钢种类按化学成分分a).碳素钢1)低碳钢C<0.25% 铸造性能差、应用较少2)中碳钢C=0.25~0.45% 铸造性能较好、应用广泛3)高碳钢C=0.50~0.60 铸造性能差、应用较少。
b).合金钢【耐蚀.耐磨.耐热等特殊性能】1) 低合金钢2) 高合金钢按钢的用途分:碳素结构钢,碳素工具钢,合金结构钢,合金工具钢,不锈钢,耐热钢,15)碳钢a)碳钢的主要元素是铁和碳b)铸造钢分为:亚共析钢,(wc<0.77%﹚共析钢(wc=0.77%﹚过共析钢(wc>0.77%﹚铸造低碳钢(wc<0.25%﹚中碳钢(wc=0.25%-0.5%﹚高碳钢(wc>0.5%16)牌号表示方法:(1) 强度法——ZG( 后面加两组数字,第一组表示屈服强度,第二组表示抗拉强度。
之间用“—”隔开,例如:2)以化学成分表示的铸钢牌号18)铸态组织其特征a)晶粒粗大,有些情况还存在魏氏(或网状)组织(先共析铁素体形态)。
b)具有粒状铁素体和珠光体相互交错分布的组织c)使钢具有良好的强度和韧性。
通过适当的热处理(退火或正火),魏氏体或网状组织即令转变为粒状组织。
注:Ⅰ细化晶粒方法:增大冷却速度,降低浇注温度,加强钢液在凝固期间运动,变质处理,表面层晶粒细化Ⅱ魏氏组织:是先共析的铁素体或渗碳体结晶时沿着奥氏体晶面呈针片状析出,并由晶界插入晶粒内部,冷却后在亚共析钢中。
魏氏组织危害:是碳钢铸件常见缺陷,能够使铸件的力学性能降低,脆性增加,冲击韧度急剧下降,消除魏氏组织的方法:进行退火或正火处理,使钢的晶粒细化19)铸造碳钢的化学成分a)主要是:碳,硅,锰,磷,硫五大元素,碳是主要元素,硫磷是杂质元素。
b)碳,碳量增加,强度增加,塑性韧性降低,c)硅,具有脱氧作用,是有益元素d)硫,有害元素,能够降低钢的力学性能,产生热脆现象e)锰的作用:具有固溶强化作用,脱氧作用,减少硫的危害作用f)磷,有害元素,降低钢的塑性韧性,引起冷脆现象20)碳钢的热处理a)处理的目的是细化晶粒,消除魏氏体(或网状组织)和消除铸造应力。
b)处理方法:退火、正火或正火加回火。
由于碳钢的淬造性较差,不采用淬火处理。
注:Ⅰ, 正火的力学性能比退火高,且生产率高、成本低、应尽量采用正火代替退火Ⅱ, 正火比退火的内应力大,易产生裂纹、硬化的铸钢件,则需退火。
Ⅲ, 对于小型中碳钢铸件,则常用调质处理,以提高其综合力学性能。
21)碳钢的铸造性能a)流动性差,缩孔倾向较大,b)易形成热裂和冷裂等缺陷。
22)铸造工艺特点a)钢水的浇注温度高b),收缩大,流动性差,易氧化、吸气,因此铸造困难,c)易产生浇不到、气孔、缩孔、缩松、热裂、粘砂等缺陷。
23)获得健全铸钢件应采用的工艺措施:a)铸钢用砂具有高耐火性,良好的透气性和退让性,低的发气性等。
b)铸钢件要安置冒口和冷铁,以实现定向凝固。
防止铸件产生缩孔和缩松。
c)铸钢件的热处理:是生产铸钢件的必要工序d)铸件的壁不能太薄;24)铸造合金钢注:低合金钢的主要作用是提高力学性能,高合金钢的主要作用是改善物理化学性能25)铸造高锰钢a)性能特点﹕加工硬化,高韧性b)化学成分对高锰钢的影响:碳,锰【碳高,硬度高,韧性差。
锰小,不能形成单一奥氏体,过大不易加工硬化】磷,降低钢的韧性,硫,作用小c)组织:奥氏体+碳化物+磷﹙少量﹚d)水韧处理:将铸件重新加热到奥氏体区保温,使碳化物全部溶于奥氏体中,然后迅速淬入水中得到单一的奥氏体组织,这种热处理叫水韧处理f﹚高锰钢进行水韧处理目的:为了消除碳化物,获得单一奥氏体组织e)工艺性能:流动性好,收缩性大,内应力大,加工性能差,易产生裂纹,易粘砂26﹚铬元素性能作用:a﹚提高淬透性,b﹚缩小奥氏体区c﹚形成致密氧化膜26)铬不锈钢耐蚀原理a)铬不锈钢具有耐腐蚀性的合金元素。