模具设计制作方案
塑料模具设计方案

塑料模具设计方案一、背景介绍在现代工业生产中,塑料制品的应用越来越广泛。
而塑料制品的生产离不开塑料模具的设计与制造。
本文将针对塑料模具的设计方案进行详细介绍。
二、需求分析在开始设计塑料模具之前,我们需要对项目需求进行详细的分析。
这包括产品形状、尺寸、材料以及生产要求等。
1. 产品形状根据产品的形状,我们可以确定模具的结构类型。
常见的模具结构包括单腔模具、多腔模具、嵌件模具等。
2. 产品尺寸对于产品尺寸的要求,我们需要考虑到产品的公差范围和精度要求。
根据尺寸要求,我们可以确定模具的材料及加工方式。
3. 材料选择根据生产批量和产品要求,我们可以选择合适的模具材料。
常见的模具材料包括模具钢、铝合金等。
不同的材料具有不同的强度和耐磨性能。
4. 生产要求根据客户的要求,我们需要考虑到生产效率、模具寿命以及产品表面质量等因素。
这将直接影响到模具的设计和制造过程。
三、塑料模具设计流程根据需求分析阶段的结果,我们可以进行具体的模具设计。
塑料模具设计一般包括以下几个步骤:1. 产品设计在模具设计之前,我们需要通过CAD等设计软件完成产品的三维模型设计。
这将作为模具设计的基础。
2. 模具结构设计根据产品的形状和尺寸要求,我们可以确定模具的结构。
这包括模具腔体、模具芯、模具副以及模具附件的设计和安装。
3. 模具零件设计根据模具结构设计,我们可以开始设计各个模具零件的具体形状和尺寸。
这包括模具腔体、模具芯、滑块、顶针等零部件。
4. 模具注塑系统设计模具注塑系统是模具设计的重要组成部分。
我们需要考虑到注塑机的规格、熔融物料的流动性以及产品的冷却周期等因素。
5. 模具闭合系统设计模具闭合系统包括模具的开合、顶出及脱模等功能。
我们需要确保模具的闭合性能和稳定性,以及产品的顶出和脱模效果。
四、模具制造与试模在完成设计方案后,我们可以进行模具的制造和试模。
这包括以下几个步骤:1. 材料采购与加工根据设计方案,我们需要采购合适的模具材料,并进行相应的加工和热处理。
模具3大系统设计方案
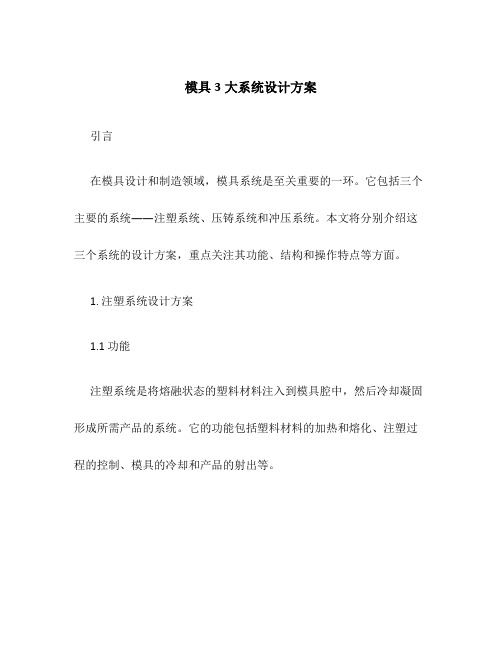
模具3大系统设计方案引言在模具设计和制造领域,模具系统是至关重要的一环。
它包括三个主要的系统——注塑系统、压铸系统和冲压系统。
本文将分别介绍这三个系统的设计方案,重点关注其功能、结构和操作特点等方面。
1. 注塑系统设计方案1.1 功能注塑系统是将熔融状态的塑料材料注入到模具腔中,然后冷却凝固形成所需产品的系统。
它的功能包括塑料材料的加热和熔化、注塑过程的控制、模具的冷却和产品的射出等。
1.2 结构注塑系统主要由料斗、加料机、螺杆、注射缸和模具等组成。
其中,料斗用于储存塑料颗粒,加料机用于将颗粒精确地送入螺杆中,螺杆通过旋转将塑料颗粒加热、熔化,并将熔融的塑料推入注射缸中。
注射缸提供持续而稳定的注射压力,将熔融塑料推入模具腔中。
模具则提供所需产品的形状和尺寸。
1.3 操作特点注塑系统的操作特点主要体现在以下几个方面: - 需要设定合适的温度、压力和时间参数,以实现对注塑过程的精确控制; - 需要周期性地清理和维护注射缸和模具,以确保系统的正常运行和延长使用寿命;- 需要根据产品要求调整注射速度、压力和冷却时间等参数,以获得满足要求的产品。
2. 压铸系统设计方案2.1 功能压铸系统是通过对金属材料的加热和注入,将熔融金属填充到模具腔中,然后冷却凝固形成所需产品的系统。
它的功能包括金属材料的加热和熔化、注入过程的控制、模具的冷却和产品的铸造等。
2.2 结构压铸系统主要由熔炉、注射机、模具和冷却系统等组成。
熔炉用于加热金属材料至熔化温度,注射机将熔融金属推入模具腔中。
模具提供所需产品的形状和尺寸,冷却系统则用于对模具和铸件进行冷却。
2.3 操作特点压铸系统的操作特点主要体现在以下几个方面: - 需要定期检查和维护熔炉和注射机,以确保其正常工作; - 需要调整金属的加热温度和熔化时间,以满足不同金属的要求; - 需要根据产品要求调整注射速度、压力和冷却时间等参数,以获得满足要求的铸件。
3. 冲压系统设计方案3.1 功能冲压系统是通过将金属材料放在模具中,然后施加高压力以改变材料形状的系统。
模具结构设计方案

模具结构设计方案模具是工业生产中常用的工具之一,广泛应用于塑料、金属、陶瓷等制品的生产过程中。
模具的结构设计对产品的成型质量、生产效率以及模具寿命等都有着重要的影响。
下面将以塑料模具为例,详细介绍模具结构设计的几个方面。
首先是模具的整体结构设计。
模具一般由上、下两部分组成,上模和下模之间通过模具螺栓连接。
上模通常由进料口、固定板、移动板、顶针等部分组成,下模则由底板、定位销、导向板等部分组成。
在整体结构设计中,需要注意上、下模的对位准确、顶出机构的稳定性以及模具的可拆卸性等。
其次是注塑模具中的流道系统设计。
流道系统是塑料模具中最关键的部分,直接影响产品的成型质量。
在流道系统的设计中,需要考虑塑料的充填速度、压力和温度等因素,合理选择流道的截面形状和尺寸。
同时,还需要设计出合适的喷嘴和冷却系统,以确保塑料在流道中充分流动和冷却。
第三是模具的冷却系统设计。
冷却系统对于模具寿命和产品质量有着重要的影响。
在冷却系统的设计中,需要合理设置冷却通道,并确保冷却通道与模具表面的距离足够近,以提高冷却效果。
同时,还需要注意冷却通道的位置和布局,以保证整个模具受热均匀,避免产生应力集中和变形等问题。
另外还需要考虑模具的顶出机构设计。
顶出机构主要用于将成型的产品从模具中弹出,避免产品粘模。
在顶出机构的设计中,需要确保顶出机构的稳定性和可靠性,同时考虑到产品的形状、材料和尺寸等因素,设计合适的顶出机构形式和数量。
最后是模具材料的选择。
模具材料的选择直接影响到模具的使用寿命和成本。
一般而言,模具材料要求具有较高的硬度、强度和耐磨性,同时还需具备一定的耐腐蚀性和导热性等特点。
在选择模具材料时,需要根据具体的生产需求和经济因素综合考虑,选择合适的模具材料。
综上所述,模具结构设计是一个复杂的工作,需要考虑多个方面的因素。
合理的模具结构设计可以提高产品的成型质量和生产效率,延长模具的使用寿命,减少生产成本。
因此,在进行模具结构设计时,需要充分考虑以上几个方面的原则和要点,以保证模具的性能和质量。
压铸模具设计方案
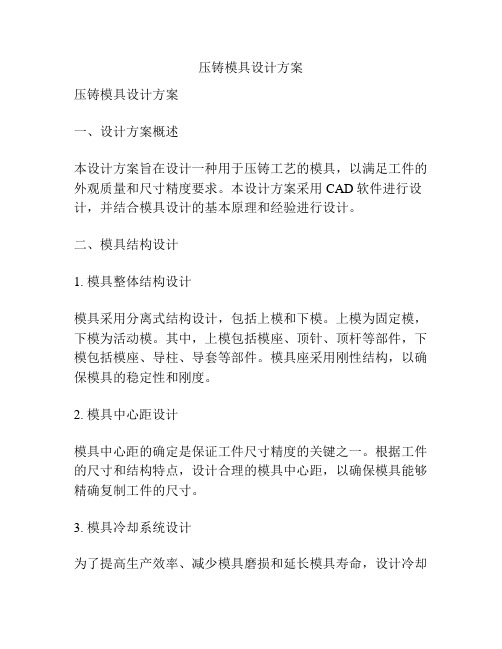
压铸模具设计方案压铸模具设计方案一、设计方案概述本设计方案旨在设计一种用于压铸工艺的模具,以满足工件的外观质量和尺寸精度要求。
本设计方案采用CAD软件进行设计,并结合模具设计的基本原理和经验进行设计。
二、模具结构设计1. 模具整体结构设计模具采用分离式结构设计,包括上模和下模。
上模为固定模,下模为活动模。
其中,上模包括模座、顶针、顶杆等部件,下模包括模座、导柱、导套等部件。
模具座采用刚性结构,以确保模具的稳定性和刚度。
2. 模具中心距设计模具中心距的确定是保证工件尺寸精度的关键之一。
根据工件的尺寸和结构特点,设计合理的模具中心距,以确保模具能够精确复制工件的尺寸。
3. 模具冷却系统设计为了提高生产效率、减少模具磨损和延长模具寿命,设计冷却系统对模具进行冷却。
冷却系统包括冷却孔和进水口,通过冷却水的流动,迅速冷却模具,以提高生产效率和模具寿命。
4. 模具材料选择模具的材料选择是保证模具寿命和使用效果的重要因素。
根据工件的材料和要求,选择适当的模具材料,保证模具具有良好的硬度和耐磨性。
三、模具生产工艺1. 加工工艺规程模具的加工工艺包括数控加工、外圆磨削等。
根据模具的具体结构和工艺要求,制定合理的加工工艺规程,以确保模具的加工质量。
2. 检测工艺模具加工完成后,进行检测以验证模具的质量。
检测工艺包括模具尺寸检测、表面质量检测等,通过合适的检测工艺,确保模具符合设计要求。
四、模具的维护、维修和更换为了保证模具的正常使用和延长其寿命,进行模具的定期维护、维修和更换。
维护工作包括清洁模具、添加润滑剂等,维修工作包括修复模具损伤、更换模具部件等,更换工作包括根据模具磨损程度,定期更换模具部件。
五、结论本设计方案是一种用于压铸工艺的模具设计方案,通过合理的结构设计、材料选择和加工工艺,可以满足工件的外观质量和尺寸精度要求。
同时,通过模具的定期维护、维修和更换,可以保证模具的正常使用和延长其寿命。
模具3大系统设计策划方案

模具3大系统设计策划方案模具(mold)是制造工业中常见的工具,用于制造具有特定形状和尺寸的零件或产品。
模具的设计策划对于产品的质量和生产效率至关重要。
下面将对模具设计策划中的三大系统进行详细介绍。
第一,CAD(计算机辅助设计)系统。
CAD系统是模具设计的核心工具,它通过虚拟仿真方案,实现模具设计参数的精确计算和可视化展示。
CAD系统可以生成3D模型,使设计师能够更直观地了解模具的形状和结构。
CAD系统还可以进行模具的工艺设计,包括模具分析、注塑流动分析等,帮助设计师预测模具在制造和使用过程中的问题,并提出相应的改进方案。
此外,CAD系统还可以与CAM系统进行集成,实现模具制造过程的自动化。
第二,CAM(计算机辅助制造)系统。
CAM系统是模具制造的关键工具,它能够将CAD系统生成的模型转化为可加工的实际工件。
CAM系统可以根据模具的几何参数和工艺要求,自动生成加工路径和操作指令。
CAM 系统还可以进行刀具选型和切削力分析,帮助制造商选择合适的切削工艺和设备。
此外,CAM系统还可以进行数控程序的生成和优化,提高模具制造的精度和效率。
第三,CAE(计算机辅助工程)系统。
CAE系统是模具设计和制造过程中的辅助工具,它可以对模具进行结构和性能的分析。
CAE系统可以进行模具的有限元分析,模拟模具在使用过程中的受力和变形情况,预测模具的耐久性和稳定性。
CAE系统还可以进行模具的模拟试验,比如模具的注塑成型试验和挤压成型试验,帮助工程师优化模具的设计和工艺参数。
此外,CAE系统还可以进行模具的模拟优化,帮助设计师找到最优的结构和材料组合,提高模具的质量和寿命。
综上所述,模具设计策划中的三大系统(CAD系统、CAM系统和CAE 系统)在模具设计、制造和评估过程中起着重要的作用。
这些系统通过虚拟仿真和精确计算,帮助设计师理解模具的形状和结构,分析模具的工艺和性能,优化模具的设计和工艺参数,提高模具的质量和生产效率。
模具写技术方案

模具制作技术方案简介模具是指用于制造产品的工业生产装备,广泛应用于各类制造工业中。
模具的设计与制作直接影响产品的质量和生产效率。
本文将介绍模具制作技术方案,包括模具设计流程、材料选择、加工工艺等内容。
模具设计流程模具设计是模具制作的关键环节,它包括以下几个步骤:1.产品分析:根据实际需求对产品进行分析,了解产品的外形、尺寸、材料等特点,为后续模具设计提供依据。
2.模具结构设计:根据产品特点和要求,设计模具的整体结构,包括上模板、下模板、导柱、导套、顶针等组成部分,确定模具的类型。
3.零件设计:对模具的各个零部件进行设计,包括模具芯、模具腔、滑块、冷却系统等。
4.模具装配设计:将各个零部件按照设计要求进行装配设计,确保模具能够正常运行。
5.模具结构强度计算:进行模具结构的强度计算,确保模具能够承受所需的工作负荷。
材料选择模具的材料选择直接关系到模具的使用寿命和制造成本。
常用的模具材料包括:•工具钢:具有较高的硬度、强度和耐磨性,广泛应用于模具制作中,如P20、718等。
•合金铝:具有较好的热导性和耐蚀性,适用于制作低压铸造模具。
•高速钢:具有良好的耐热性和切削性能,适用于制作加工较为坚硬的材料的模具。
在选择模具材料时,需要考虑产品的材料、加工工艺以及模具的使用环境和寿命等因素。
加工工艺模具的精密加工是保证模具质量的重要环节,常用的加工工艺包括以下几种:1.车削:利用车床进行模具材料的精确切削,通常用于模具的外轮廓加工。
2.铣削:利用铣床进行模具材料的切削加工,可用于模具的平面切削和轮廓加工。
3.磨削:通过磨床进行模具零部件的表面研磨和修整,以提高模具的精度和表面质量。
4.电火花加工:利用电火花机床进行模具材料的精确切削,适用于复杂形状的零部件加工。
5.线切割:利用线切割机进行模具材料的高速切削,适用于薄板材料的加工。
在加工过程中,需要根据具体的零部件特点和要求选择合适的加工工艺,并保证加工精度和效率。
模具设计制造流程
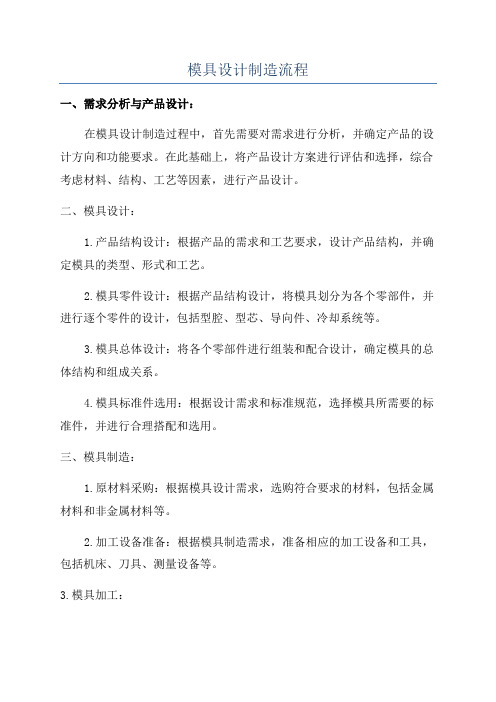
模具设计制造流程一、需求分析与产品设计:在模具设计制造过程中,首先需要对需求进行分析,并确定产品的设计方向和功能要求。
在此基础上,将产品设计方案进行评估和选择,综合考虑材料、结构、工艺等因素,进行产品设计。
二、模具设计:1.产品结构设计:根据产品的需求和工艺要求,设计产品结构,并确定模具的类型、形式和工艺。
2.模具零件设计:根据产品结构设计,将模具划分为各个零部件,并进行逐个零件的设计,包括型腔、型芯、导向件、冷却系统等。
3.模具总体设计:将各个零部件进行组装和配合设计,确定模具的总体结构和组成关系。
4.模具标准件选用:根据设计需求和标准规范,选择模具所需要的标准件,并进行合理搭配和选用。
三、模具制造:1.原材料采购:根据模具设计需求,选购符合要求的材料,包括金属材料和非金属材料等。
2.加工设备准备:根据模具制造需求,准备相应的加工设备和工具,包括机床、刀具、测量设备等。
3.模具加工:(1)粗加工:根据模具零部件的设计要求和图纸,进行粗加工,包括锯割、铣削、钻孔、车削等。
(2)精加工:对经过粗加工的模具零部件进行精度加工和形状修整,包括磨削、镗削、刮削等。
(3)热处理:对经过加工的模具零部件进行适当的热处理,提高材料的硬度和强度,提高模具的使用寿命。
(4)组装调试:将经过热处理的模具零件进行组装,进行配合检查和调试,确保模具的正常使用。
4.模具表面处理:对模具外表面进行腐蚀和耐磨处理,增加模具的使用寿命和工作效果。
四、模具试模与调整:1.模具试制:将制造好的模具进行产品试模,确认模具的工作效果和产品质量。
2.调整优化:根据试模结果,对模具进行调整和优化,改善模具工作效果和产品质量。
五、模具验收:1.尺寸精度检测:对模具的型腔、型芯等关键尺寸进行检测和测量,确保满足产品设计要求。
2.性能测试:对模具的耐磨性、硬度等性能进行测试,确保模具的使用寿命和工作性能。
3.试模效果评估:通过试模生产和产品检验,对模具的试模效果和产品质量进行评估,确保模具的合格和可用性。
挤出成型模具结构设计方案

挤出成型模具结构设计方案挤出成型模具在塑料加工中扮演着至关重要的角色,其结构设计直接影响着制品的质量和生产效率。
本文将探讨挤出成型模具的结构设计方案,旨在帮助提高生产效率和制品质量。
主要结构组成挤出成型模具主要由进料系统、螺杆、模腔和冷却系统组成。
进料系统负责将塑料颗粒送入螺杆,螺杆通过旋转和推进实现塑料的压缩和加热,而模腔则决定了最终制品的形状和尺寸。
冷却系统则用于快速降温和固化塑料制品。
结构设计要点1.螺杆设计:螺杆的设计直接关系到塑料在挤出过程中的压缩、混合和进料能力。
合理设计螺杆的螺距、螺槽深度和压力比可以有效提高生产效率和塑料的均匀性。
2.模腔设计:模腔的结构应考虑到制品的形状、尺寸和壁厚,以确保最终产品符合设计要求。
同时,必须考虑模腔的冷却系统,以避免制品变形和缺陷。
3.冷却系统设计:冷却系统的设计影响着挤出过程中塑料的温度控制和降温速度。
为了提高生产效率和制品质量,冷却系统应布局合理,确保塑料均匀、迅速地冷却固化。
4.材料选择:挤出成型模具的材料选择应考虑到耐磨性、耐腐蚀性和热传导性。
通常情况下,选择高强度、耐磨损的合金钢作为模具材料,以确保模具的寿命和稳定性。
结构优化建议1.流道优化:合理设计流道结构,减少塑料的流动阻力和压力损失,提高进料效率。
2.增加冷却通道:在模腔周围增加冷却通道,提高冷却效率,减少制品变形和翘曲。
3.模具光洁度:保持模具表面的光洁度,减少制品表面缺陷的产生。
4.辅助装置:考虑在模具中增加辅助装置,如拉伸机构或气动系统,以实现特定制品的形状和结构。
结语挤出成型模具结构设计是塑料加工生产中至关重要的环节,合理的设计方案可以提高生产效率、降低成本并保证制品质量。
通过本文的介绍,希望能对挤出成型模具的设计提供一定的指导和参考,以满足不同生产需求的要求。
冲压两板模具设计方案

冲压两板模具设计方案
冲压两板模具是一种常见的模具结构,由于其结构简单、制造成本低、生产效率高等优点,广泛应用于汽车、家电、建筑等行业的零件加工中。
下面是一个冲压两板模具设计方案的简要描述,具体包括下面几个方面:
首先,根据产品的形状、尺寸和材料特性等要求,确定模具的总体结构。
冲压两板模具由上模板和下模板组成,上模板用于安装冲头和导向机构,下模板用于安装压力板和导向机构。
为了确保模具的稳定性和使用寿命,模板可以采用优质的钢材制作,经过适当的热处理和表面处理。
其次,根据冲压工艺要求,设计适合的冲头和模具孔型。
冲头是冲压模具的核心部件,其形状和尺寸直接决定了模具加工的产品形状和尺寸。
冲头一般采用优质的硬质合金材料制作,以确保其耐磨性和硬度。
模具孔型根据产品的形状和结构要求进行设计,可以采用常见的圆孔、方孔、异形孔等。
再次,设计合适的导向机构和定位装置。
导向机构主要用于使上模板和下模板相对位置确定,以保证模具在使用过程中的稳定性和精度。
可以采用滑块导向、滚轮导向等不同的导向方式。
最后,考虑模具的开合方式和卸料装置。
开合方式可以采用机械手、气动缸等方式进行实现,以提高模具的生产效率和自动化程度。
卸料装置可以采用弹簧、气动装置等,以方便产品的卸料和减少操作人员的工作强度。
总之,冲压两板模具设计方案需要全面考虑产品的要求、生产工艺和设备条件等因素,以确保模具的质量、使用效果和经济效益。
设计方案中的每个细节都要经过合理的计算和分析,以提高模具的精度和稳定性。
同时,根据实际生产情况,不断优化模具的结构和工艺,提高模具的性能和使用寿命。
模具开发模具设计方案

模具开发模具设计方案
模具开发是指根据产品的加工工艺要求和设计要求,利用CAD、CAM等软件工具对模具进行全面、系统的设计。
模具开发的设计方案应包括以下几个方面:
1.产品分析:对产品进行全面的分析,了解产品的形状、尺寸、材料等特性,并根据产品的用途和需求确定模具的设计要求。
2.模具结构设计:根据产品分析的结果,确定模具的结构形式
和工作原理。
模具的结构包括上模、下模、导柱、导套、顶杆、顶针、卡板、模板等,需要确定每个零件的形状、尺寸和材料。
3.零件设计:对模具各个零件进行细节设计,包括上模、下模、导柱、导套、顶杆、顶针、卡板、模板等各个零部件。
在设计过程中需要考虑到零件的材料、加工工艺和装配方式。
4.模具工艺设计:确定模具的制造工艺,包括模具的加工方法、装配顺序、加工精度等。
在设计过程中需要考虑到模具的制造成本、生产周期和制造工艺的可行性。
5.模具试制方案:制定模具试制方案,包括模具的试制计划、
试制流程、试制工艺和试制设备等。
在试制过程中需要对模具进行试模和试产,检验模具的加工精度、装配性能和产品质量。
6.模具改进方案:根据模具试制过程中的问题和产品生产中的
需求,提出模具改进方案。
模具的改进包括结构改进、材料改
进、加工工艺改进等,旨在提高模具的加工精度、生产效率和产品质量。
总之,模具开发的设计方案需要综合考虑产品的加工工艺要求和设计要求,确定模具的结构形式、零件设计、工艺设计、试制方案和改进方案。
通过合理的设计方案,可以提高模具的加工精度、生产效率和产品质量,从而有利于产品的生产和发展。
纸塑模具设计加工方案

纸塑模具设计加工方案纸塑模具是指用于制造纸塑制品的模具,其设计加工方案主要包括以下几个步骤:1. 产品需求分析:根据客户提供的需求,确认所需制造的纸塑制品的形状、尺寸、材料等要求。
2. 设计初步方案:根据产品需求,设计出初步的模具结构和形状。
这一步需要考虑模具的形状是否能够满足产品的要求,模具的加工难度和成本是否合理等。
3. 模具结构优化:根据初步方案进行模具结构优化,考虑模具的结构强度、稳定性等因素。
同时,还需要考虑模具的拆装便利性,以保证模具的加工和维护的方便性。
4. 模具材料选择:根据产品的需求和模具的使用环境,选择合适的材料来制造模具。
模具材料通常需具备一定的硬度、耐磨性和耐腐蚀性,以保证模具的寿命和使用效果。
5. 模具制造:根据最终确定的模具设计方案和材料选择,进行模具的制造加工。
制造过程包括铣削、车削、磨削、打磨等工艺,以及热处理、表面处理等工艺,最后通过组装完成模具的制造。
6. 模具试产:制造完成的模具进行试产,确认模具的制造质量和精度是否满足产品需求。
如果有问题,及时调整和修复模具。
7. 模具调试:将试产的模具装配到相应的生产设备上,进行模具的调试。
调试过程包括模具的安装和调整,以及对模具的性能和工艺进行评估和优化。
8. 产品生产:当模具调试完成后,可以正式投入生产,通过纸塑制品生产设备进行生产。
在生产过程中,需要对模具进行维护和保养,及时发现并解决模具使用中的问题。
设计加工纸塑模具的方案需要考虑多个因素,包括产品需求、模具结构、材料选择和制造工艺等。
通过合理的设计和加工,可以保证模具的质量和准确度,从而生产出符合要求的纸塑制品。
模具结构设计方案

模具结构设计方案1. 引言模具在工业生产中起到了至关重要的作用。
它是制造产品的关键工具,因此模具的结构设计方案显得尤为重要。
本文将介绍模具结构设计方案的基本要素和步骤,以及一些注意事项。
2. 设计要素模具结构设计方案应考虑以下要素:2.1. 产品形状与尺寸模具的结构设计必须符合产品的形状与尺寸要求。
在设计过程中,需要充分理解产品的设计图纸和规格要求,确保模具能够精确制造出符合产品要求的零件。
2.2. 材料选择模具的材料选择直接关系到模具的使用寿命和性能。
常见的模具材料包括钢材、铝合金等。
在材料选择时,需要考虑产品的材料特性、使用环境等因素,以确保模具材料能够满足设计要求。
2.3. 结构稳定性模具的结构稳定性直接影响到产品的质量和加工精度。
设计时需要注意避免模具结构存在松动、变形等问题,以保证模具能够长时间稳定地工作。
2.4. 拆卸与维修模具在使用过程中可能需要进行拆卸和维修,因此设计时需要充分考虑模具的拆卸和维修性能。
模具应设计合理的拆卸结构,方便拆装及维修。
3. 设计步骤设计模具结构的步骤如下:3.1. 产品分析首先,对待加工的产品进行分析。
了解产品的形状、尺寸、材料等特点,确定模具所需的结构和工艺要求。
3.2. 模具类型选择根据产品的特点和加工要求,选择合适的模具类型。
常见的模具类型包括冲压模具、注塑模具、压铸模具等。
3.3. 模具结构设计根据产品的特点和模具类型,进行模具的结构设计。
根据产品的形状和工艺要求设计模具的尺寸、形状、结构等,并考虑材料选择和结构稳定性等因素。
3.4. 模具细节设计根据模具的整体结构设计,进一步设计模具的细节部分。
包括模具的导向、导轨、脱模机构、冷却系统等。
3.5. 模具装配与调试将设计好的模具进行装配,并进行相应的调试工作。
确保模具能够正常工作,满足产品加工的要求。
4. 设计注意事项在进行模具结构设计时,需要注意以下事项:4.1. 工艺性考虑在模具设计过程中,需要充分考虑产品的工艺要求。
模具设计及制造流程

电镀与喷涂
电镀和喷涂可以增强模具 表面的硬度和耐磨性,提 高模具的使用寿命。
防锈处理
对模具表面进行防锈处理, 可以防止模具在使用过程 中生锈,保持模具的性能。
检测与验证
检测设备
性能验证
采用高精度的检测设备,如三坐标测 量仪、激光干涉仪等,对模具进行全 面的尺寸检测和精度验证。
使用前应检查模具是 否完好无损,如有异 常应及时处理。
保养计划
01
根据模具的使用情况和厂家推荐,制定合理的保养 计划。
02
定期对模具进行润滑、清洁、检查和调整,确保其 处于良好状态。
03
保养过程中如发现损坏或磨损严重的零部件,应及 时更换。
维修与更换
对于损坏的模具零部件,应及时 进行维修或更换。
利用注塑机将热塑性塑料注入模具, 冷却后得到所需形状的塑料制品。
挤出成型
利用挤出机将塑料加热熔融后通过模 具挤出,冷却后得到连续的塑料制品。
吹塑成型
利用吹塑机将塑料加热熔融后吹入模 具,冷却后得到中空塑料制品。
压延成型
利用压延机将塑料加热熔融后通过模 具压延,冷却后得到塑料制品。
04
模具质量控制
尺寸控制
。
锻造工艺
自由锻造
利用自由锻锤或压力机对金属坯料进行锻打, 生产出接近零件形状的毛坯。
热锻
将金属坯料加热至高温后进行锻打,适用于 生产高强度、耐磨性好的零件。
模锻
利用模具对金属坯料进行锻打,生产出精密、 高强度的零件。
冷锻
在常温下对金属坯料进行锻打,适用于生产 小型、复杂的零件。
注塑工艺
注塑成型
螺纹模具设计方案
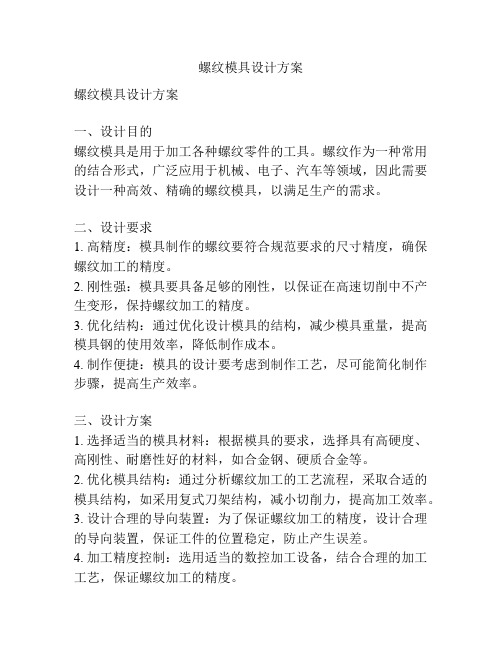
螺纹模具设计方案螺纹模具设计方案一、设计目的螺纹模具是用于加工各种螺纹零件的工具。
螺纹作为一种常用的结合形式,广泛应用于机械、电子、汽车等领域,因此需要设计一种高效、精确的螺纹模具,以满足生产的需求。
二、设计要求1. 高精度:模具制作的螺纹要符合规范要求的尺寸精度,确保螺纹加工的精度。
2. 刚性强:模具要具备足够的刚性,以保证在高速切削中不产生变形,保持螺纹加工的精度。
3. 优化结构:通过优化设计模具的结构,减少模具重量,提高模具钢的使用效率,降低制作成本。
4. 制作便捷:模具的设计要考虑到制作工艺,尽可能简化制作步骤,提高生产效率。
三、设计方案1. 选择适当的模具材料:根据模具的要求,选择具有高硬度、高刚性、耐磨性好的材料,如合金钢、硬质合金等。
2. 优化模具结构:通过分析螺纹加工的工艺流程,采取合适的模具结构,如采用复式刀架结构,减小切削力,提高加工效率。
3. 设计合理的导向装置:为了保证螺纹加工的精度,设计合理的导向装置,保证工件的位置稳定,防止产生误差。
4. 加工精度控制:选用适当的数控加工设备,结合合理的加工工艺,保证螺纹加工的精度。
5. 考虑模具的耐用性:在设计过程中,考虑模具的寿命,避免出现易损部件,降低模具的维修成本。
6. 设计合理的冷却系统:由于螺纹加工需要高速切削,容易产生高温,为了保护模具和工件的质量,设计合理的冷却系统,及时降低温度。
7. 模具维护方便:在设计过程中,考虑模具的维护保养,设计合理的拆装结构,方便清洗和更换易损件。
四、总结本设计方案针对螺纹模具的设计提出了一些关键要求和具体的设计措施。
通过选择合适的材料、优化模具结构、设计合理的导向装置和冷却系统等方式,可以提高螺纹模具的加工精度、效率和寿命,降低生产成本,提高生产效益。
最终达到优化器具设计方案的目的。
冲压模具设计和制造实例

冲压模具设计与制造实例例:图1所示冲裁件,材料为A3,厚度为2mm,大批量生产.试制定工件冲压工艺规程、设计其模具、编制模具零件的加工工艺规程. 零件名称:止动件 生产批量:大批 材料:A3 材料厚度:t=2mm一、 冲压工艺与模具设计1.冲压件工艺分析①材料:该冲裁件的材料A3钢是普通碳素钢,具有较好的可冲压性能. ②零件结构:该冲裁件结构简单,并在转角有四处R2圆角,比较适合冲裁. ③尺寸精度:零件图上所有未注公差的尺寸,属自由尺寸,可按IT14级确定工件尺寸的公差.孔边距12mm 的公差为,属11级精度.查公差表可得各尺寸公差为:零件外形:65 mm 24 mm 30 mm R30 mm R2 mm零件内形:10 mm孔心距:37±0.31mm 结论:适合冲裁. 2.工艺方案及模具结构类型该零件包括落料、冲孔两个工序,可以采用以下三种工艺方案:+①先落料,再冲孔,采用单工序模生产.②落料-冲孔复合冲压,采用复合模生产.③冲孔-落料连续冲压,采用级进模生产.方案①模具结构简单,但需要两道工序、两套模具才能完成零件的加工,生产效率较低,难以满足零件大批量生产的需求.由于零件结构简单,为提高生产效率,主要应采用复合冲裁或级进冲裁方式.由于孔边距尺寸12 mm有公差要求,为了更好地保证此尺寸精度,最后确定用复合冲裁方式进行生产.工件尺寸可知,凸凹模壁厚大于最小壁厚,为便于操作,所以复合模结构采用倒装复合模及弹性卸料和定位钉定位方式.3.排样设计查冲压模具设计与制造表 2.5.2,确定搭边值:两工件间的搭边:a=2.2mm工件边缘搭边:a1=2.5mm步距为:32.2mm条料宽度B=D+2a1=65+2=70确定后排样图如2所示一个步距内的材料利用率η为:η=A/BS×100%=1550÷70××100%=%查板材标准,宜选900mm×1000mm的钢板,每张钢板可剪裁为14张条料70mm×1000mm,每张条料可冲378个工件,则η为:η=nA1/LB×100%=378×1550/900×1000×100%=%即每张板材的材料利用率为%4.冲压力与压力中心计算⑴冲压力落料力 F总=τ=××2×450=KN其中τ按非退火A3钢板计算.冲孔力 F冲=τ=×2π×10×2×450=KN其中:d 为冲孔直径,2πd为两个圆周长之和.卸料力 F卸=K卸F卸=×=KN推件力 F推=nK推F推=6××=KN其中 n=6 是因有两个孔.总冲压力:F总= F落+ F冲+ F卸+ F推=+++=KN⑵压力中心如图3所示:由于工件X方向对称,故压力中心x0=32.5mm=13.0mm其中:L1=24mm y1=12mmL2=60mm y2=0mmL3=24mm y1=12mmL4=60mm y4=24mmL5=60mm y5=27.96mmL6=60mm y6=24mmL7=60mm y7=12mmL8=60mm y8=12mm计算时,忽略边缘4-R2圆角.由以上计算可知冲压件压力中心的坐标为,135.工作零件刃口尺寸计算落料部分以落料凹模为基准计算,落料凸模按间隙值配制;冲孔部分以冲孔凸模为基准计算,冲孔凹模按间隙值配制.即以落料凹模、冲孔凸模为基准,凸凹模按间隙值配制.刃口尺寸计算见表16.工作零件结构尺寸落料凹模板尺寸:凹模厚度:H=kb≥15mmH=×凹模边壁厚:c≥~2H=~2×=~mm 实取c=30mm凹模板边长:L=b+2c=65+2×30=125mm查标准JB/T :凹模板宽B=125mm故确定凹模板外形为:125×125×18mm.将凹模板作成薄型形式并加空心垫板后实取为:125×125×14mm.凸凹模尺寸:凸凹模长度:L=h1+h2+h=16+10+24=50mm其中:h1-凸凹模固定板厚度h2-弹性卸料板厚度h-增加长度包括凸模进入凹模深度,弹性元件安装高度等凸凹模内外刃口间壁厚校核:根据冲裁件结构凸凹模内外刃口最小壁厚为7mm,根据强度要求查冲压模具设计与制造表2.9.6知,该壁厚为4.9mm即可,故该凸凹模侧壁强度足够.冲孔凸模尺寸:凸模长度:L凸= h1+h2+h3=14+12+1440mm其中:h1-凸模固定板厚 h2-空心垫板厚 h3-凹模板厚凸模强度校核:该凸模不属于细长杆,强度足够.7.其它模具零件结构尺寸根据倒装复合模形式特点:凹模板尺寸并查标准JB/,确定其它模具模板尺寸列于表2:根据模具零件结构尺寸,查标准GB/选取后侧导柱125×25标准模架一副.8.冲床选用根据总冲压力 F总=352KN,模具闭合高度,冲床工作台面尺寸等,并结合现有设备,选用J23-63开式双柱可倾冲床,并在工作台面上备制垫块.其主要工艺参数如下:公称压力:63KN滑块行程:130mm行程次数:50次/分最大闭合高度:360mm连杆调节长度:80mm工作台尺寸前后×左右:480mm×710mm二、模具制造1、主要模具零件加工工艺过程制件:柴油机飞轮锁片材料:Q235料厚:1.2mm该制件为大批量生产,制品图如下:一冲裁件的工艺分析1、冲裁件为Q235号钢,是普通碳素钢,有较好的冲压性能,由设计书查得τ=350Mpa.2、该工作外形简单,规则,适合冲压加工.3、所有未标注公差尺寸,都按IT14级制造.4、结论:工艺性较好,可以冲裁.方案选择:方案一:采用单工序模.方案二:采用级进模.方案三:采用复合模.单工序模的分析单工序模又称简单模,是压力机在一次行程内只完成一个工序的冲裁模.工件属大批量生产,为提高生产效率,不宜采用单工序模,而且单工序模定位精度不是很高,所以采用级进模或复合模.级进模的分析级进模是在压力机一次行程中,在一副模具上依次在几个不同的位置同时完成多道工序的冲模.因为冲裁是依次在几个不同的位置逐步冲出的,因此要控制冲裁件的孔与外形的相对位置精度就必须严格控制送料步距,为此,级进模有两种基本结构类型:用导正销定距的级进模和用侧刃定距的级进模.另外级进模有多个工序所以比复合模效率低.复合模的分析复合模是在压力机一次工作行程中,在模具同一位置同时完成多道工序的冲模.它不存在冲压时的定位误差.特点:结构紧凑,生产率高,精度高,孔与外形的位置精度容易保证,用于生产批量大.复合模还分为倒装和正装两种,各有优缺点.倒装复合模但采用直刃壁凹模洞口凸凹模内有积存废料账力较大,正装复合模的优点是:就软就薄的冲裁件,冲出的工件比较平整,平直度高,凸凹模内不积存废料减小孔内废料的胀力,有利于凸凹模减小最小壁厚.经比较分析,该制件的模具制造选用导料销加固定挡料销定位的弹性卸料及上出件的正装复合模.二排样图设计及冲压力和压力中心的计算由3-6,3-8表可查得:a1=,a=,△=查书391.料宽计算: B=D+2a=62+2=64mm2.步距:A=D=a1=62+=62.8mm3.材料利用率计算:η=A/BS×100%=πR2-πR2+12/64=312-+/64×100%=%其中a是搭边值,a1是工作间隙,D是平行于送料方向冲材件的宽度,S是一个步距内制件的实际面积,A是步距,B是料宽,R1是大圆半径,R2是小圆半径,12×是方孔的面积,η为一个步距内的材料的利用率4.冲裁总压力的确定:L=231+2+12+2=周边总长计算冲裁力:F=KLtτ查设计指导书得τ=350MpaF=350≈180KN落料力:F落=τ=231350=卸料力:F卸=kF落==冲孔力:F冲=τ+12+2350=顶件力:F顶=-k2F落==冲裁总压力:F∑=F落+F卸+F冲+F顶=+++=F压=~F∑=246KN说明:K为安全系数,一般取;k为卸料力系数,其值为~,在上式中取值为;k2为顶件力系数,其值为~,式中取值为5.压力机的初步选用:根据制件的冲裁的公称压力,选用开式双柱可倾式压力机,公称压力为350k N 形号为J23-35 满足:F压≥F∑。
锻造模具造型设计方案

锻造模具造型设计方案设计方案一:设计理念:简洁、现代化1. 模具外形设计:采用流线型设计,外形光滑、简洁,呈现现代感。
2. 材质选择:选用高强度铝合金作为模具材质,既保证了模具强度,又减轻了模具自重。
3. 部件结构设计:通过分析模具的使用情况,采用可拆卸的模具结构设计,方便模具的维护和更换。
4. 贴合度优化:通过CAD技术对模具内外表面进行精确设计,确保模具各部件之间的贴合度,从而提高模具制造效率。
5. 细节设计:在模具的易损部位加入抗磨擦材料,延长模具寿命;同时,在模具表面进行喷砂处理,增加模具的使用稳定性。
6. 安全措施:在模具设计过程中,考虑到操作人员的安全,添加防护措施,如防滑手柄和自动关断装置,确保操作的安全性。
7. 技术创新:引入先进的热传导技术,提高模具制造过程中的加热效率,提高生产效率。
设计方案二:设计理念:经典、实用性强1. 模具外形设计:以整体稳定为设计理念,采用四方形结构,增加了模具的稳定性和刚性。
2. 材质选择:根据模具使用环境和使用寿命要求,选择耐磨、耐腐蚀、高强度的钢材作为模具材料。
3. 结构创新:通过应用仿生工程学原理,设计模具外形结构,提高了模具的抗压能力和抗疲劳能力。
4. 模具表面处理:采用高精度数控加工技术对模具表面进行精细处理,提高模具的平整度和表面质量。
5. 节能环保:在模具制造过程中,注重减少能量消耗,避免使用有害物质,保护环境。
6. 操作便捷性:通过模具内部结构的优化设计,确保模具的装拆过程简单方便,提高操作的便捷性。
7. 模具标识:在模具设计过程中,考虑到模具的管理和使用方便,添加模具标识,便于模具识别和跟踪。
设计方案三:设计理念:个性化、艺术性1. 模具外形设计:采用独特的造型设计,将模具打造成艺术品,增加模具的审美价值。
2. 材质选择:根据模具的艺术风格,选择质感好、色彩丰富的材料,如有机玻璃、陶瓷等,增加模具的观赏性。
3. 艺术元素融入:在模具的设计中融入艺术元素,如雕刻、图案等,增加模具的个性化和独特性。
教学竹编模具设计方案

一、设计背景随着我国传统文化的传承与发展,竹编工艺作为一种传统的手工艺技术,越来越受到人们的关注。
竹编工艺不仅具有很高的实用价值,还能美化环境,提高人们的生活品质。
为了更好地推广和传承竹编工艺,我们设计了一套教学竹编模具,旨在通过模具的帮助,让更多的人能够轻松学会竹编技艺。
二、设计目标1. 提高竹编工艺的普及程度,让更多人了解和喜爱竹编。
2. 降低竹编工艺的学习难度,使初学者能够快速上手。
3. 培养学生的动手能力和审美能力,提高综合素质。
三、设计原则1. 简便性:模具结构简单,易于操作。
2. 实用性:模具能够满足不同种类竹编作品的需求。
3. 安全性:模具材料无毒无害,使用过程中无安全隐患。
4. 美观性:模具设计美观大方,与竹编作品相得益彰。
四、设计方案1. 模具材料:选用环保、无毒、无害的竹材,确保模具的耐用性和安全性。
2. 模具结构:(1)主体框架:采用竹材制成,保证模具的稳定性和承重能力。
(2)分隔层:在主体框架内部设置分隔层,用于固定竹条,方便竹编作品的制作。
(3)支撑柱:在分隔层之间设置支撑柱,用于支撑竹条,保证竹编作品的形状和尺寸。
3. 模具尺寸:根据竹编作品的大小和形状,设计模具的尺寸。
例如,制作竹编篮子时,模具尺寸应略大于篮子的尺寸。
4. 模具功能:(1)固定竹条:模具能够将竹条固定在指定位置,使竹编作品的结构更加牢固。
(2)调整形状:通过调整分隔层和支撑柱的位置,可以改变竹编作品的形状和尺寸。
(3)提高效率:模具能够提高竹编工艺的效率,减少手工操作的难度。
5. 模具使用方法:(1)将竹条按顺序插入分隔层,使其紧贴模具。
(2)调整分隔层和支撑柱的位置,使竹条达到理想的形状和尺寸。
(3)在竹条上编织竹编作品,完成后取出竹条。
五、总结本教学竹编模具设计方案旨在为广大竹编爱好者提供一种简单、实用、安全、美观的竹编工具。
通过使用本模具,可以使竹编工艺的学习变得更加轻松,有利于竹编技艺的传承与发展。
模具设计方案

模具设计方案第1篇模具设计方案一、项目背景随着我国制造业的快速发展,模具行业在国民经济中的地位日益突出。
作为生产各种工业产品的基础工艺装备,模具在汽车、电子、家电、通讯等众多领域具有广泛应用。
为满足市场需求,提高产品质量,降低生产成本,本项目旨在设计一套合法合规的模具设计方案。
二、设计目标1. 满足产品功能需求,确保产品质量;2. 提高生产效率,降低生产成本;3. 合法合规,确保生产安全;4. 节能环保,降低资源消耗。
三、设计方案1. 产品分析与定位根据客户需求,对产品进行详细分析,明确产品结构、功能、尺寸等参数。
结合市场需求,对产品进行定位,确保设计方案符合产品发展方向。
2. 模具结构设计(1)根据产品结构特点,选择合适的模具类型;(2)采用模块化设计,提高模具的通用性和可维护性;(3)合理布局模具的冷却系统,确保产品成型过程中的温度控制;(4)优化模具的导向和定位系统,提高模具的运动精度。
3. 模具材料选择根据产品性能要求,选择具有良好机械性能、耐磨性和抗腐蚀性的模具材料。
同时,考虑材料成本和加工工艺,确保模具的经济性。
4. 模具制造与加工(1)采用先进的加工工艺,确保模具的制造精度;(2)加强模具加工过程中的质量检测,确保模具质量;(3)合理规划模具加工流程,提高生产效率。
5. 模具试模与优化(1)组织模具试模,验证模具结构、材料及工艺的合理性;(2)根据试模结果,对模具进行优化调整,确保产品质量;(3)跟踪模具生产过程,及时解决生产中出现的问题。
6. 模具验收与交付(1)按照相关法律法规,组织模具验收,确保模具符合国家标准;(2)提供完整的模具技术资料,包括模具结构图、模具零件清单等;(3)对客户进行模具操作和维护培训,确保客户正常使用模具。
四、质量保证与售后服务1. 质量保证(1)严格执行国家及行业标准,确保模具质量;(2)加强过程控制,对模具制造各环节进行质量把关;(3)提供模具质量保证书,承诺质量保证期限。
复制模具制作方案

复制模具制作方案在制造业中,模具是一个重要的制造工具,用于生产不同形状和尺寸的零部件。
复制模具是一种常用的模具制作方式,它可以通过对原型的复制来生产所需的产品。
本文将介绍复制模具制作的步骤和技巧。
1. 原型准备制作复制模具的第一步是准备好原型。
原型可以是一个实物模型或CAD设计制作的三维模型。
确保原型的表面光滑并且没有任何损伤,以免影响复制模具的效果。
2. 底模制作制作复制模具的下一步是制作底模。
底模是复制模具的基础,它可以保证模具的准确性和稳定性。
首先选择合适的制作材料,如矽胶、聚氨酯等。
其次根据原型大小和形状,设计合适大小的矩形模具和分割板,并使用切割工具将材料切成合适尺寸。
将制作好的底模放置在平坦的表面,并根据分割板的位置将底模上下分为两个部分。
3. 涂覆分离剂在制作复制模具之前,需要将底模涂覆一层分离剂,以确保复制模具可以完全脱离底模。
根据矽胶的材质特点,选择适合的分离剂,涂覆在底模的表面上。
4. 混合矽胶将两种不同的矽胶混合在一起,然后搅拌均匀。
根据原型的大小和形状,计算混合矽胶的总量,然后按照一定比例混合。
注意搅拌时间和速度,确保混合均匀无颗粒。
5. 倒矽胶将混合好的矽胶倒入底模中,然后将原型轻轻压在矽胶表面上,确保它与矽胶底面接触良好。
然后将底模拼合到一起,确保两个分割板的位置相同。
6. 取出原型等待矽胶干燥,通常需要24小时,然后打开底模,轻轻取出原型。
此时已经得到了一个用于制作复制模具的矽胶模具。
如果需要制作多个模具,可以重复上述步骤,制作多个矽胶模具。
7. 制作复制模具制作复制模具之前需要预先准备好制作材料,如玻璃纤维增强塑料等。
将制作材料混合并搅拌均匀,然后将其倒入矽胶模具中,确保填满所有空间。
等待材料干燥,根据需要可以重复上述步骤制作多个复制模具。
8. 完成通过以上步骤,制作出了复制模具。
选择合适的原型、底模和制作材料,可以制作出高质量的复制模具来生产所需的产品。
总之,复制模具制作需要细心、耐心和技巧,但这不难掌握,只要掌握好了制作步骤,就可以轻松地制作出高质量的复制模具。
压制半圆球体阴阳模具设计方案

压制半圆球体阴阳模具设计方案
设计方案:压制半圆球体阴阳模具
1. 设计模具尺寸:根据半圆球体的直径确定模具尺寸,确保模具能够完整地包裹住半圆球体。
2. 材料选择:模具可以选择使用金属材料,如铝合金、钢铁等,具有强度高、易加工的特点。
3. 模具结构:模具由上模和下模组成,上模为拱形凹槽结构,下模为凸台结构。
上模和下模之间通过螺栓固定。
4. 上模设计:上模的凹槽部分内壁应与半圆球体的外形相吻合,凹槽内应设置适当的放砂孔,以便于半圆球体的顶部和底部受力均匀。
上模的外缘应设置有导向结构,用于与下模的凸台对位和导向。
5. 下模设计:下模的凸台部分的外形应与半圆球体的内部相吻合,以确保模具压制时能够充分贴合半圆球体的内部曲面。
凸台的顶部应设置有导向结构,用于与上模的凹槽对位和导向。
6. 模具制造:根据设计方案,制作上模和下模的加工图纸,并选择合适的加工设备和工艺对模具进行制造。
加工过程中需要确保模具的几何形状和尺寸精度。
7. 模具调试:制造完成后,进行模具的装配和调试工作,确保上模和下模的配合精度和压制效果。
8. 模具应用:完成模具调试后,可以将半圆球体放入模具中进行压制,以得到阴阳两面模具效果。
需要注意的是,在设计模具时应考虑到半圆球体的材质和压制工艺,确保模具能够满足半圆球体的要求,并且在实际应用中要进行充分的模具保养和维护,延长模具的使用寿命。
- 1、下载文档前请自行甄别文档内容的完整性,平台不提供额外的编辑、内容补充、找答案等附加服务。
- 2、"仅部分预览"的文档,不可在线预览部分如存在完整性等问题,可反馈申请退款(可完整预览的文档不适用该条件!)。
- 3、如文档侵犯您的权益,请联系客服反馈,我们会尽快为您处理(人工客服工作时间:9:00-18:30)。
模具設計製作組員:王明偉、王建中、莊世懷德霖技術學院機械工程系日四技0941指導老師:張惠欽老師摘要模具是近代工業產品大量生產所倚藉的一項重要工業與技術。
模具製造的精密程度和技術層次,對於生產成品的品質,生產原料的有效利用,以及生產力的提高等方面,均有絕對性的影響。
而模具業又以塑膠模為最大宗。
與我們生活息息相關之家電產品,資訊產品及汽機車零件中,大部分皆為塑膠製品。
因此本計劃乃以一個塑膠產品為範例,逐步探討及說明整個塑膠模具的設計流程,同時並輔以虛擬實境的展現方式,來加強對初學者之學習效果。
一.模具的定義模具必須具有堅固的“複製空間”結構體。
在操作中,他呈密閉空間以確保熱熔樹脂在射出壓力及速度下,充填並擠壓模穴時,不發生脹裂或溢料。
此外還需在適當地方具有氣孔,以便在射出充填的短時間內,能讓熔融樹脂快速取代這個複製空間。
在成形循環未了,熱熔樹脂已固化時,可以在分模線處打開,在平行開模方向上,沒有任何嵌口(underercut)的情況下,將成品頂出來。
為了達到上述目的,則必須具備下列條件:1.在靜態部份(1)必須有“複製空間”結構體,例如模座及心型。
(2)射出成形機之鎖模裝置:動態模固定板。
(3)頂出成品的裝置:頂出前後板、頂出銷、頂出套筒。
(4)導引熱熔樹脂的通路:澆口、流道、注口襯道。
(5)固化機構:熱塑性樹脂採用冷卻管道(系統)。
熱固性樹脂採用電熱加熱棒。
2.在動態部份(1)在射出成形機鎖模壓力下,模具剛才須有足夠的抗壓縮強度,才不會發生塑性變形或被壓碎的情況。
(2)在射出成形機射出壓力下,模具鋼材在強行變形範圍內的變形量須比樹脂的收縮量小。
成品被頂出時,不會發生嵌口和表面刮傷的情形。
(3)在頂出壓力下,頂出銷截面積對頂出銷長度比不可過大,以防頂出銷彎曲,可採用階段式頂出銷。
頂出銷與成品接觸的面積應盡量大,以防成品有頂空的情形。
(4)特殊結構體需堅固,動作行程需確實,以防裝壞模具本體、滑塊、側蕊、壓板及旋退裝置。
二、模具的功能1.複製的功能將熱熔樹脂填滿由模腔及模蕊所構成的密閉空間,藉熱交換作用,使其固化(或硬化)被“複製”出來。
當然,一方面複製成品形狀(加入收縮率),另一方面是複製表面之咬花花紋。
2.熱交換功能(1)熱塑性塑膠:將熱熔樹脂所帶入的熱量,利用油冷、水冷或空冷方式,間接自模蕊、模座及其他模板處將熱量帶走,使其固化。
油或水皆係經冷卻循環管道流通這其中牽涉到冷卻速度及冷卻能力。
(2)熱固性塑膠:將熱熔局部架橋樹脂射入模穴空間後,利用電熱方式間接傳給模穴中樹脂,使其發生架橋硬化,他牽涉到硬化速度、硬化能力(在模具中)及硬化程度(在模具外)。
三、模具的製作流程圖四、基本理論1.決定模具強度在模具設計時應該考慮的:(1)對於成形機的鎖模力需具有足夠壓縮強度。
因此PL面必須設定出足夠的耐壓面積。
(2)對於溶融樹酯的射出壓力需具有足夠的壓縮、抗拉、彎曲強度,不會產生龜裂、彎曲而使模具模具無法打開或產生毛邊或動作不良等。
(3)依據製品形狀來考慮模具材質,利用嵌入模心的構造,使部分材質更高級化,並使其易於更換。
(4)冷卻孔、導梢孔、頂出梢孔、嵌件及滑塊機構等強度上易造成應力集中,導致龜裂現象也要一倂考慮。
強度:強度是指破損或破壞發生的界限,破損或破壞是材料的某一部份或全體引起分離。
S點:降伏點M點:最大荷重Z點:破斷剛性:任何物體上施加力量會產生變形,這種變形大小程度稱為剛性。
λλσAWawE==∈=//E:彈性係數σ:垂直應力∈:縱向變形w:負荷a:斷面積λ:彎曲量:原尺寸2.強度計算模具強度計算,因為模具內有橫澆道、進澆口、肉厚和不同的形狀等等,難以計算,實際資料又很少,在設計時需要注意模穴內的R部及承受拉應力與彎曲應力部分,還有應力集中、龜裂破損,都應加入安全率使強度更寬裕。
(1)鎖模、射出壓縮強度對於公模和母模的分模面而言,最好僅考慮鎖模力,對於組立板、模板、支柱等而言,需加入射出壓力考慮計算。
)/(2cmkgap=σS●●MZ伸長率荷重a 承受面積、σ壓縮應力、P 壓縮力(2) 壓縮強度計算頂出銷棒狀的長度對於斷面而言,非常長的時候,軸壓縮負荷超越某界限值,承受壓縮使棒開始彎曲,所以才用不同壓縮計算。
2L I E ‧‧‧πn p b =n :端末條件造成的係數(n=2.046) E :楊氏係數,鋼的場合=2.1X106kg/cm 2π:3.14I :長柱的最小斷面二次矩 L::長柱的長度(3) 剪斷力與銷的強度安裝於模具的銷,由於射出壓照成剪斷應力而破損。
‧‧T SE =τ F :剪斷力 S :斷面一次矩T :求剪斷應力點的肉厚 I :斷面二次矩 3. 決定模穴數必須考慮所用型機之規格及最經濟的產量,而後決定模穴數。
ㄧ般情形,成形品量少,或精度高,或形狀大之場合,使用ㄧ個模穴或2~4個模穴之型模。
反之,生產量多之場合,尺寸精度不高,需要較低成本之場合,使用多數模穴及成組模穴之型模。
4. 決定分模線及流道、澆口由此決定型模之基本構造,成形品毛邊及熔接線之位置,從而決定成形品之外觀及製造工時。
直接進澆口:豎橫口直接與模具的模穴連接,因此模具構造簡單,一般用於單模穴模具。
側邊近澆口:由小型、中形物的形狀產品大部分使用多模穴。
成行品在側面設置進澆口。
5. 處理嵌口部分及決定頂出方法成形品有崁口部份時,先行決定使用何種退出方法,於成形完成後,在型模取出。
例如使用分模型模,滑塊,螺紋旋出等模具構造。
頂出機構,ㄧ般採用頂出銷及頂出套筒等構造。
但如成形品上,不得有頂出壓痕(pin mark)或箱形、杯類型狀物體,使用刮料板方式。
或者成形品為聚乙烯樹脂者,以空氣吹出法亦被接受。
6. 模穴及心型材料及其加工方法之決定基於模具材料之硬度及加工法,決定採用壓入法、崁入法等。
等此等場合,必須考慮嵌入線及嵌入位置或嵌入方向。
7. 溫度控制方法之決定射出成形後,為使成形品能冷卻至常溫尺寸,模具溫度必須加以控制,為此目的,可用水、油、空氣等通入模具,以達到冷卻模具的目的。
五.模具設計首先,在可塑化工程融解的樹脂材料在射出工程中被射出充填至模具,然後以模具內的形狀來決定產品的外型。
(摘自: )當一個設計者拿到成品或者是概念圖之後,首先必須將成物件在腦海中有一個概略的藍圖。
此藍圖是需要由實務經驗的累積才能快速的建構,例如模仁外型,模穴數量等,模仁的外型太小容易讓塑膠在射出的時候因為壓力過大而溢滲出去,太大則是浪費成本。
模仁的材質跟模座比起來是屬於較高級的材質(模仁通常是 NAK80 模座通常是 S45C )而模穴數量則是決定生產的速度,不過在有限的機器支援條件之下設計者必須設計出恰好的穴數,否則設計過多的模穴也只是射不飽,白白的浪費加工成本與時間,設計過少的模穴會讓生產能力下降導致產能不足,設計者於腦中建構完成之後會依照其難易度來決定繪製2D 或者是3D 模具圖。
繪畫的過程中必須考慮到頂針與導柱的空間,若是空間過度壓縮容易讓模具在射出過程中因為壓力過大而損壞,反之:空間過大則是浪費不必要的成本支出,設計人員的設計重點就是時間要快,材料要省。
以這次的專題為例:三塊板的成品外型較為簡易,設計者之所以選擇三塊板樣式,以進行自動斷料主要是為了減少人力成本與工作時間的浪費,而且成品的表面本身是光學級,所以必須不能有指紋的存在。
更多请参考: 所以設計打中板來自動脫料,以確保模仁不會受損及成品表面的乾淨,本次繪圖過程中基本上是不需要進行3D 繪圖,只需要使用2D 的繪圖軟體便可以完成模具的設計,3D 繪圖雖然可以一目了然,但是在繪畫時間上卻比2D 繪圖比起來更花費時間。
雖然一般設計人員手上都會自備有空白的2D ,3D 模座圖,但是由於繪畫3D 的軟體需要經過程式本身的層層校對,對於比較簡單的模具來說是浪費時間,而設計人員最需要的就是時間。
現場加工人員也具有一定程度的辨圖能力,所以不需要使用到3D 軟體,除非是在有意外的組裝或者是加工狀況時才會使用3D 軟體繪圖來進行模擬組裝或檢視干涉問題。
兩塊板以下是設計時需要參考的圖表 1.大水口構造圖2.小水口構造圖3.模板的精度4.模板加工標準5.標準零件規格6.模板尺寸和參考價格7.鎖模力與射出關係(參考值)六.平面設計圖利用AutoCAD繪製平面設計圖,在設計的時候要參考標準模板的樣式,依照工件的大小來決定模版規格,採用標準模板可以節省成本和時間,是在CAD設計階段一開始最重要的程序。
首先會先設計產品,利用AutoCAD 可以輕易把產品的外型和尺寸繪製出來。
接著利用最大直徑和高度,來計算母模仁和公模仁大小深度,最大直徑是44.50、最高高度是8.08,利用下列公式來計算收縮率()δφφ+=1dDDφ= 模穴大小dφ= 設計尺寸δ= 收縮率產品材料為A.B.S塑膠收縮率為0.004~0.009(通常取0.005)=Dφ44.0(1+0.005)=Dφ44.22即可算出母模穴外徑收縮量,再利用公式算出高度收縮率。
=Dφ9.55七.立體裝配利用Pro/ENGINEER繪製立體圖,在設計階段完成後,如果需要更近ㄧ步檢查設計的模具,是否有問題,可以利用Pro/ENGINEER來繪製零件和組立。
開啟PRO’E 3.0 選擇零件-實體繪製成品選擇公制範本圖5-2 圖5-1利用”旋轉”指令畫出成品之外型。
完成繪製之後打勾,給定360度旋轉。
成品圖選擇”製造”-“模穴”繪製模具模穴。
(一樣是選擇公制樣本)在組裝的子目錄下選擇參照模型。
開啟剛剛完成的成品檔案。
此時會自動匯入至視窗中。
選擇根據參照合併,按下確定。
接下來建立手動元件。
在”建立”的子目錄下面選擇”手動”。
選擇”零件”-“實體”並且打上名稱。
選擇建立特徵。
選擇輪廓繪製方式,本次成品以旋轉實體為主,之後點選完成。
繪製出理想的公母模外型。
公母模輪廓完成圖。
輪廓外型圖。
設定分模線。
利用剛剛的分模線製做出分模面。
選擇”特徵”。
點選剛剛的分模線。
確定方向之後按下確定。
完成。
利用分模面分割公母模輪廓。
選擇兩個體積塊(公母模),並包含所有工件。
按下確定。
確定公模外型&命名。
確定母模外型&命名。
將體積塊轉換誠實體物件。
選擇剛剛兩個公母模體積塊。
體積塊實體化完成圖。
鑄模,將成品加入實體化之體積塊之中。
建立。
母模、成品、公模之爆炸圖。
EMX程式左側工具列為EMX工具列,選擇新模具。
開啟新專案,主要單位為公制(mm)。
設定模具數值。
(DB大水口參考圖8-4)載入大水口DB-Type。
先變更模具大小,由於S版在設計上是在分模面的左側所以刪除S版。
確定刪除。
並且將舊S版上的元件一併刪除。
建立一個新的S版於左側,並且修改各板之板厚。
(參照10-4)設定頂出版差銷尺寸。
(參考圖10-4)預覽圖。
於剛剛新增的S版上面增加一導軸襯。