影响铝合金产品质量的原因及预防措施
铝合金模板常见质量问题及预防措施

8.剪力墙模板支撑未采用三角撑保证支架刚度
此图为正 确做法
9.飘板上浮
封闭铝模板,易上浮
窗台中 部凸起
10.模板底板不平易造成上部天花水平度难调整
11.楼梯上盖模应留活口盖板
活口板
二、预防措施及作业交底
1.现场施工作业应具备的条件 2.铝模进场验收(或工厂预拼装验收) 3.测量放线的要求 4.施工工艺流程 5.安装工艺工法 6.模板拆除标准
3. 模板定位不准
虽然未加固成 型,但说明定 位有问题。
4. 模板变形严重
5. 模板因变形及边缝残渣导致的拼缝不严; 竖向应多节点而不直
肋板已变形 张开,模板 平面尺寸已
延长
模板在局部 形成多节点, 很难保证平
直度
6. 纵梁底因侧向次梁增长而被顶成折线形
梁底已明 显变成折
线形
7.梁墙交接处平整度较差
铝合金模板安装常见质量 问题及预防措施
模板质量问题汇总
1.模块设计组合不利装拆;模块拉结力不平衡;模板加固无整体性。
铝 2.模板加工精度不够,平面尺寸出现正偏差;孔位偏差大;未进行表处理。 模 安 3.模板编码标识不清、安装混乱 装 4.模板定位不准或不牢固 常 5.模板变形严重未予矫正 见 6.模板因变形及边缝残渣导致的拼缝不严;竖向应多节点而不直 质 7.纵梁底因侧向次梁增长而被顶成折线形 量 8.梁墙交接处平整度较差 问 9.剪力墙模板支撑未采用三角撑保证支架刚度,或支撑脚预埋不合格 题 10.飘楼及楼梯上盖模未留活口,且无拉结,上盖模板上浮
11.模板底板不平易造成上部天花水平度难调整
一、铝合金模板常见质量问题图片
1.模板加固设计问题
1.窗台模板与楼面结构是无拉结的,混凝土充满后必定上浮,因此必须有预埋螺栓拉结。 2.多转角短肢剪力墙,中间段不设D、F拉片(只设E拉片)两边均爆模。CDFG四排拉片应紧 靠竖向阴角模设置。
铝合金门窗安装后常见质量问题及防护措施

铝合金门窗安装后常见质量问题及防护措施(一)、铝合金门窗渗水一) 现象下雨时,雨水沿窗台缝、外框边缘、扇间缝或框与扇之间的缝隙处,向室内渗漏水。
二) 原因分析1、窗框四周嵌填不严实,框与洞口墙体间的缝隙未注密封胶,或密封胶质量不好,遇水软化、脱落;2、窗框四周注密封胶时,周边的保护膜未清除干净,在保护膜与铝合金边框间形成渗水通道;3、平开铝合金窗未装披水条,推拉铝合金窗未设排水孔;4、外窗台抹灰高或倒坡,形成向室内倒流水。
三) 预防措施1、铝合金窗框安装好后,应用柔性材料将四周缝隙嵌填严实,注胶前要撕去窗框缝隙处的保护膜,再进行窗框四周的注胶;2、要使用质量好的密封材料,注胶要严密、均匀、平整、光滑;3、铝合金框上横竖杆交接处和外露的螺钉头,均需注入密封胶,并随时将铝合金门窗表面的胶迹清理干净;4、平开铝合金门窗必须安装披水;推拉铝合金窗应在下框外槽边靠近底部近两端处,分别铣两个长圆形的排水孔,将窗上流下来的雨水引排至室外;5、外窗台应比内窗台低一砖,窗台抹出向外的坡度,坡度不小于15%,禁止反坡。
四) 治理方法1、查出封闭不严之处,重新按工艺标准进行密封;2、在铝合金横竖杆件交接处和外露的螺钉头处,进行注胶密封;3、平开窗补装披水;推拉窗在下框外槽边补贴排水孔;4、外窗台高或无向外坡度者,应按要求返工重做。
(二)、铝合金门窗玻璃裂纹一) 现象铝合金门窗上的玻璃安装不久后,出现门窗玻璃从边缘开始破裂一道小纹,随后裂纹延伸到另一边缘。
二) 原因分析1、裁割玻璃不齐,用钳子扳边时玻璃边已形成肉眼看不见的细纹,在门窗使用的过程中,稍受振动,细纹就逐渐增大。
2、裁割玻璃尺寸偏大,镶嵌时未用橡胶垫块,当玻璃受膨胀时,边缘与铝合金型材槽口直接接触受力产生裂纹。
3、玻璃槽口中构造上的螺钉头未处理好,玻璃与螺钉头接触处一点受力,造成玻璃裂纹;三) 预防措施1、裁割玻璃尺寸准确,边沿整齐,一般应比槽口实际尺寸小3mm;2、安装玻璃时,必须使用弹性垫块,不得使用木片等当垫块;3、安装玻璃前应先检查槽口,如发现翘曲不平或者螺钉露头,应经处理至符合要求后在镶玻璃。
铝合金门窗质量问题及预防措施

23 推拉 窗细部粗 糙 精度 差 、 隙大不 密封 . 空
产 生 的 主要 原 因 : 铝合 金 型 材 下 料 长度 控 制 误 差 偏 大 ,窗 扇 与 窗框 间 隙大 存在 空 气 渗 透通 道 , 空
外 观 。金 属 表 层 应 完 整 、 洁 、 坑 损 伤 或 腐 蚀 ; 光 无
13 窗扇 的启 闭 .
使 门窗 的框 扇 ( 杆 、 挺 、 棂) 生 弯 曲变 形 , 横 竖 窗 产 甚
至 损坏 无法 使用 的真 正 原 因。铝 合金 门窗 因其 重量 轻、 外观 感 好 而 广泛 使 用 , 其检 验 指标 ( 里仅 以 窗 这 为 例) 要 是 : 风 压 、 气 渗 透及 雨 水 渗 漏 三 项 物 主 抗 空 理 性 能 , 是建 筑 工程 中必 须达 到 的 必备 条 件 。 门 这 窗 的安 全 使 用 主要 是看 其 能承 受 风 压 的 强度 和 耐
能 好 , 观结 构 观感舒 适 , 外 采光 效果 好 等优 点 。它 适 用 于各 种 民用 、 商用及 工 业建 筑 。 目前 , 框 推拉 窗 无 的研 究 、 发 、 产 和应 用 已 取得 了令 人 鼓 舞 的 进 开 生
展 , 其 是在 该 产 品 的价 格 上 , 合 中 、 档 消 费 , 尤 适 高
对 存 在 的 质 量 问题 及 防 治 处理 提 出具 体 措 施 。
关 键 词 :铝合 金 门 窗 ; 项 性 能 ; 作 质 量 ; 扇 质 量 ; 装控 制 三 制 框 安
建 筑 外 门窗 是 各 类 房 屋 不 可 缺 少 的重 要 组 成 部 分 ,在 建 筑工 程 中不 仅 承 受 自然 环 境如 风 沙 、 雨 雪 的侵 蚀 及 自重 影 响 , 同时还 要 更 多 的承 受 使 用者 经 常 的开关 振动 的影 响 。在 这些 影 响 因素 中大风 是
铝合金窗户施工质量通病及防治措施
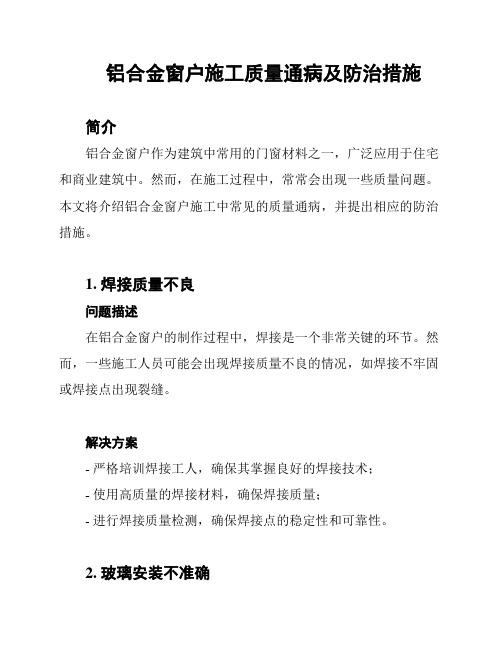
铝合金窗户施工质量通病及防治措施简介铝合金窗户作为建筑中常用的门窗材料之一,广泛应用于住宅和商业建筑中。
然而,在施工过程中,常常会出现一些质量问题。
本文将介绍铝合金窗户施工中常见的质量通病,并提出相应的防治措施。
1. 焊接质量不良问题描述在铝合金窗户的制作过程中,焊接是一个非常关键的环节。
然而,一些施工人员可能会出现焊接质量不良的情况,如焊接不牢固或焊接点出现裂缝。
解决方案- 严格培训焊接工人,确保其掌握良好的焊接技术;- 使用高质量的焊接材料,确保焊接质量;- 进行焊接质量检测,确保焊接点的稳定性和可靠性。
2. 玻璃安装不准确问题描述铝合金窗户中的玻璃安装是另一个容易出现质量问题的环节。
不准确的玻璃安装可能导致漏风、漏水等问题。
解决方案- 确保玻璃尺寸和窗户框架尺寸匹配,避免安装过大或过小的玻璃;- 使用优质的密封胶,并严格按照安装规范进行密封胶的使用;- 安装前仔细检查玻璃的质量,确保无划痕和破损;- 进行水密性和气密性测试,确保玻璃安装质量。
3. 窗户开关不灵活问题描述铝合金窗户的开关不灵活是用户常常遇到的问题之一。
开关不灵活可能会导致窗户无法正常开启和关闭,影响使用体验。
解决方案- 在施工过程中,确保窗框的尺寸和玻璃的尺寸相匹配,避免窗框变形导致开关不灵活;- 使用耐磨润滑剂,定期对窗户进行润滑保养;- 定期检查窗户的开关系统,如轨道、滚轮等部件,确保其正常运作。
4. 漏水和渗水问题问题描述漏水和渗水是铝合金窗户常见的质量问题之一。
严重的漏水和渗水问题可能会对建筑物的结构和使用安全造成威胁。
解决方案- 确保窗户的密封性能良好,使用高质量的密封胶;- 在安装框架时,确保框架与墙体之间使用密封胶进行密封,避免水分渗透;- 定期检查窗户周围的密封胶,如发现老化或破损,及时更换;- 定期检查窗户的排水系统,确保通畅和正常工作。
5. 玻璃开裂问题描述在铝合金窗户的使用过程中,玻璃开裂可能会发生。
开裂的玻璃不仅影响美观,还可能存在安全隐患。
铝合金圆铸锭质量缺陷分析
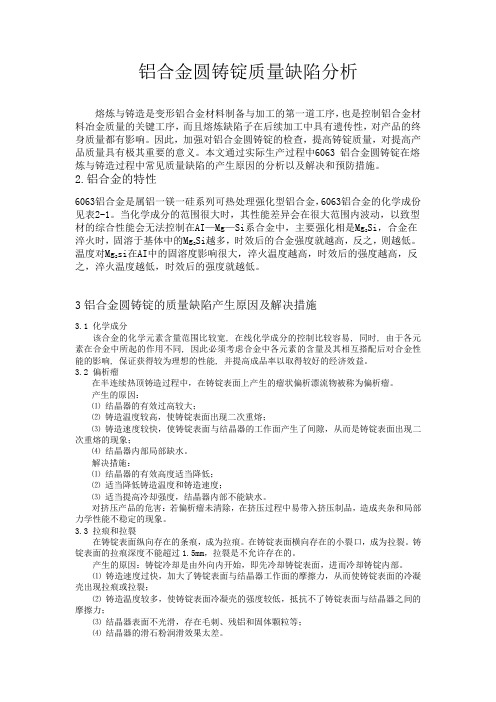
铝合金圆铸锭质量缺陷分析熔炼与铸造是变形铝合金材料制备与加工的第一道工序,也是控制铝合金材料冶金质量的关键工序,而且熔炼缺陷子在后续加工中具有遗传性,对产品的终身质量都有影响。
因此,加强对铝合金圆铸锭的检查,提高铸锭质量,对提高产品质量具有极其重要的意义。
本文通过实际生产过程中6063 铝合金圆铸锭在熔炼与铸造过程中常见质量缺陷的产生原因的分析以及解决和预防措施。
2.铝合金的特性6063铝合金是属铝一镁一硅系列可热处理强化型铝合金,6063铝合金的化学成份见表2-1。
当化学成分的范围很大时,其性能差异会在很大范围内波动,以致型Si,合金在材的综合性能会无法控制在AI—Mg—Si系合金中,主要强化相是Mg2淬火时,固溶于基体中的MgSi越多,时效后的合金强度就越高,反之,则越低。
2si在AI中的固溶度影响很大,淬火温度越高,时效后的强度越高,反温度对Mg2之,淬火温度越低,时效后的强度就越低。
3铝合金圆铸锭的质量缺陷产生原因及解决措施3.1 化学成分该合金的化学元素含量范围比较宽, 在线化学成分的控制比较容易, 同时, 由于各元素在合金中所起的作用不同, 因此必须考虑合金中各元素的含量及其相互搭配后对合金性能的影响, 保证获得较为理想的性能, 并提高成品率以取得较好的经济效益。
3.2 偏析瘤在半连续热顶铸造过程中,在铸锭表面上产生的瘤状偏析漂流物被称为偏析瘤。
产生的原因:⑴结晶器的有效过高较大;⑵铸造温度较高,使铸锭表面出现二次重熔;⑶铸造速度较快,使铸锭表面与结晶器的工作面产生了间隙,从而是铸锭表面出现二次重熔的现象;⑷结晶器内部局部缺水。
解决措施:⑴结晶器的有效高度适当降低;⑵适当降低铸造温度和铸造速度;⑶适当提高冷却强度,结晶器内部不能缺水。
对挤压产品的危害:若偏析瘤未清除,在挤压过程中易带入挤压制品,造成夹杂和局部力学性能不稳定的现象。
3.3 拉痕和拉裂在铸锭表面纵向存在的条痕,成为拉痕。
铝合金门窗工程质量通病整治措施
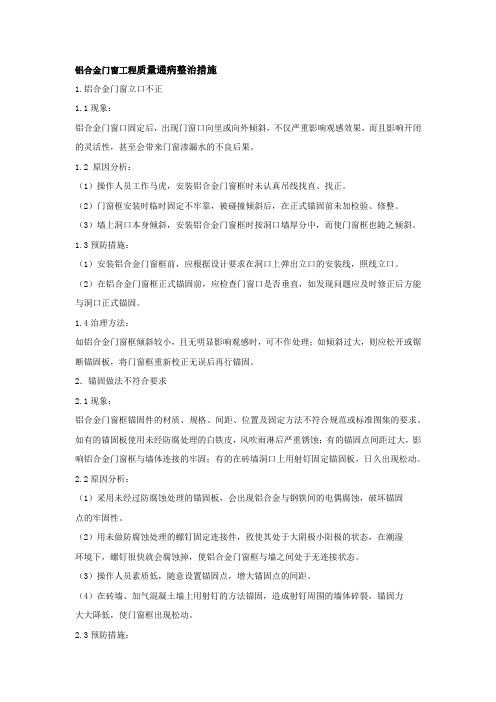
铝合金门窗工程质量通病整治措施1.铝合金门窗立口不正1.1现象:铝合金门窗口固定后,出现门窗口向里或向外倾斜,不仅严重影响观感效果,而且影响开闭的灵活性,甚至会带来门窗渗漏水的不良后果。
1.2 原因分析:(1)操作人员工作马虎,安装铝合金门窗框时未认真吊线找直、找正。
(2)门窗框安装时临时固定不牢靠,被碰撞倾斜后,在正式锚固前未加检验、修整。
(3)墙上洞口本身倾斜,安装铝合金门窗框时按洞口墙厚分中,而使门窗框也随之倾斜。
1.3预防措施:(1)安装铝合金门窗框前,应根据设计要求在洞口上弹出立口的安装线,照线立口。
(2)在铝合金门窗框正式锚固前,应检查门窗口是否垂直,如发现问题应及时修正后方能与洞口正式锚固。
1.4治理方法:如铝合金门窗框倾斜较小,且无明显影响观感时,可不作处理;如倾斜过大,则应松开或锯断锚固板,将门窗框重新校正无误后再行锚固。
2.锚固做法不符合要求2.1现象:铝合金门窗框锚固件的材质、规格、间距、位置及固定方法不符合规范或标准图集的要求。
如有的锚固板使用未经防腐处理的白铁皮,风吹雨淋后严重锈蚀;有的锚固点间距过大,影响铝合金门窗框与墙体连接的牢固;有的在砖墙洞口上用射钉固定锚固板,日久出现松动。
2.2原因分析:(1)采用未经过防腐蚀处理的锚固板,会出现铝合金与钢铁间的电偶腐蚀,破坏锚固点的牢固性。
(2)用未做防腐蚀处理的螺钉固定连接件,致使其处于大阴极小阳极的状态,在潮湿环境下,螺钉很快就会腐蚀掉,使铝合金门窗框与墙之间处于无连接状态。
(3)操作人员素质低,随意设置锚固点,增大锚固点的间距。
(4)在砖墙、加气混凝土墙上用射钉的方法锚固,造成射钉周围的墙体碎裂,锚固力大大降低,使门窗框出现松动。
2.3预防措施:(1)铝合金门窗选用的锚固件,除不锈钢外,均应采用镀锌、镀铬、镀镍的方法进行防腐蚀处理。
(2)在铝合金门窗与钢铁连接件之间用塑料膜隔开。
(3)锚固板应固定牢靠,不得有松动现象,锚固板的间距不应大于600mm,锚固板距框角不应大于180mm。
铝合金的铸造缺陷及其解决方案

铝合金的铸造缺陷及其解决方案关键信息项:1、铝合金铸造缺陷的类型名称:____________________________描述:____________________________2、造成铸造缺陷的原因因素:____________________________详细解释:____________________________3、解决方案的具体措施方法:____________________________实施步骤:____________________________4、预防铸造缺陷的策略策略:____________________________执行要点:____________________________11 铝合金铸造缺陷的类型111 气孔气孔是铝合金铸造中常见的缺陷之一。
气孔通常呈圆形或椭圆形,其尺寸大小不一。
112 缩孔和缩松缩孔是由于铸件在凝固过程中,金属液补缩不足而形成的较大孔洞。
缩松则是分散的细小缩孔。
113 夹渣夹渣指在铸件内部或表面存在的非金属夹杂物。
114 裂纹裂纹分为热裂纹和冷裂纹。
热裂纹在凝固末期高温下形成,冷裂纹则在较低温度下产生。
12 造成铸造缺陷的原因121 熔炼工艺不当熔炼过程中,如果温度控制不合理、熔炼时间过长或过短、搅拌不均匀等,都可能导致合金成分不均匀,气体和夹杂物含量增加。
122 浇注系统设计不合理浇注系统的结构和尺寸如果设计不当,可能导致金属液的流动不畅,产生卷气、冲砂等问题,从而形成气孔、夹渣等缺陷。
123 模具问题模具的温度不均匀、模具的排气不畅、模具的表面粗糙度不合适等,都可能影响铸件的质量,导致缺陷的产生。
124 铸造工艺参数不合理包括浇注温度、浇注速度、冷却速度等参数,如果选择不当,会直接影响铸件的凝固过程,从而引发各种缺陷。
13 解决方案的具体措施131 优化熔炼工艺严格控制熔炼温度和时间,采用合适的搅拌方式,确保合金成分均匀,减少气体和夹杂物的含量。
如何预防铝合金门窗生锈
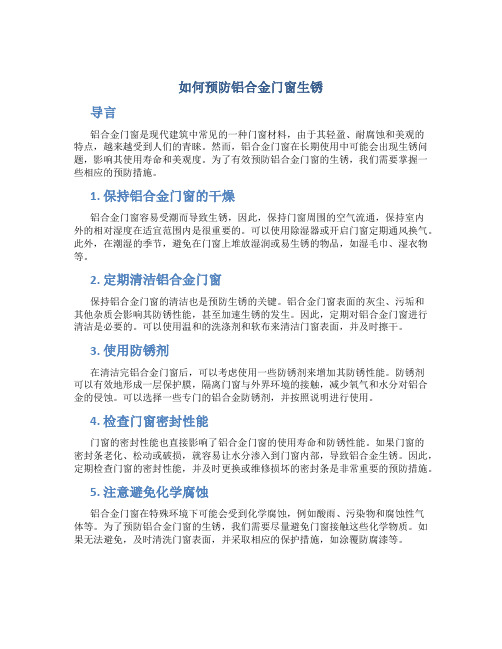
如何预防铝合金门窗生锈导言铝合金门窗是现代建筑中常见的一种门窗材料,由于其轻盈、耐腐蚀和美观的特点,越来越受到人们的青睐。
然而,铝合金门窗在长期使用中可能会出现生锈问题,影响其使用寿命和美观度。
为了有效预防铝合金门窗的生锈,我们需要掌握一些相应的预防措施。
1. 保持铝合金门窗的干燥铝合金门窗容易受潮而导致生锈,因此,保持门窗周围的空气流通,保持室内外的相对湿度在适宜范围内是很重要的。
可以使用除湿器或开启门窗定期通风换气。
此外,在潮湿的季节,避免在门窗上堆放湿润或易生锈的物品,如湿毛巾、湿衣物等。
2. 定期清洁铝合金门窗保持铝合金门窗的清洁也是预防生锈的关键。
铝合金门窗表面的灰尘、污垢和其他杂质会影响其防锈性能,甚至加速生锈的发生。
因此,定期对铝合金门窗进行清洁是必要的。
可以使用温和的洗涤剂和软布来清洁门窗表面,并及时擦干。
3. 使用防锈剂在清洁完铝合金门窗后,可以考虑使用一些防锈剂来增加其防锈性能。
防锈剂可以有效地形成一层保护膜,隔离门窗与外界环境的接触,减少氧气和水分对铝合金的侵蚀。
可以选择一些专门的铝合金防锈剂,并按照说明进行使用。
4. 检查门窗密封性能门窗的密封性能也直接影响了铝合金门窗的使用寿命和防锈性能。
如果门窗的密封条老化、松动或破损,就容易让水分渗入到门窗内部,导致铝合金生锈。
因此,定期检查门窗的密封性能,并及时更换或维修损坏的密封条是非常重要的预防措施。
5. 注意避免化学腐蚀铝合金门窗在特殊环境下可能会受到化学腐蚀,例如酸雨、污染物和腐蚀性气体等。
为了预防铝合金门窗的生锈,我们需要尽量避免门窗接触这些化学物质。
如果无法避免,及时清洗门窗表面,并采取相应的保护措施,如涂覆防腐漆等。
6. 定期涂漆保养定期对铝合金门窗进行涂漆保养也是预防生锈的重要方法。
涂漆可以形成一层保护膜,阻隔门窗与外界环境的接触,有效抵御氧气和水分的侵蚀。
选择质量好的防腐涂料,按照使用说明进行操作,定期对铝合金门窗进行涂漆保养,可以大大延长其使用寿命。
铝合金门窗的质量通病及防治方法完整版
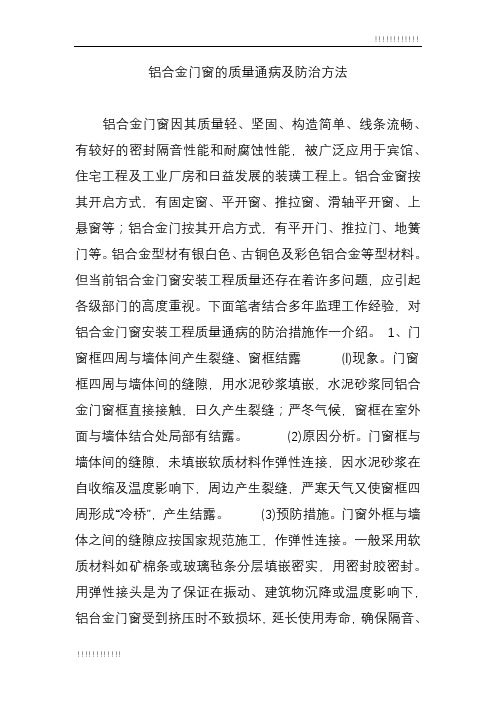
铝合金门窗的质量通病及防治方法铝合金门窗因其质量轻、坚固、构造简单、线条流畅、有较好的密封隔音性能和耐腐蚀性能,被广泛应用于宾馆、住宅工程及工业厂房和日益发展的装璜工程上。
铝合金窗按其开启方式,有固定窗、平开窗、推拉窗、滑轴平开窗、上悬窗等;铝合金门按其开启方式,有平开门、推拉门、地簧门等。
铝合金型材有银白色、古铜色及彩色铝合金等型材料。
但当前铝合金门窗安装工程质量还存在着许多问题,应引起各级部门的高度重视。
下面笔者结合多年监理工作经验,对铝合金门窗安装工程质量通病的防治措施作一介绍。
1、门窗框四周与墙体间产生裂缝、窗框结露(l)现象。
门窗框四周与墙体间的缝隙,用水泥砂浆填嵌,水泥砂浆同铝合金门窗框直接接触,日久产生裂缝;严冬气候,窗框在室外面与墙体结合处局部有结露。
(2)原因分析。
门窗框与墙体间的缝隙,未填嵌软质材料作弹性连接,因水泥砂浆在自收缩及温度影响下,周边产生裂缝,严寒天气又使窗框四周形成“冷桥”,产生结露。
(3)预防措施。
门窗外框与墙体之间的缝隙应按国家规范施工,作弹性连接。
一般采用软质材料如矿棉条或玻璃毡条分层填嵌密实,用密封胶密封。
用弹性接头是为了保证在振动、建筑物沉降或温度影响下,铝台金门窗受到挤压时不致损坏,延长使用寿命,确保隔音、保温性能的重要措施。
嵌填软质材料时,应分层嵌填,使其饱满密实。
目前采用的棉毡条、矿棉条等填嵌物,不易填嵌饱满;采用PL|发泡剂作安装填缝材料,因其能发泡膨胀,快速地填充缝隙,操作方便,且具有防水止漏作用.使用效果良好。
2、门窗框松动(1)现象。
门窗框安装后经使用产生松动,当工程质量2002. No. 5门窗扇关闭时撞击门窗框,使门窗口的灰皮或防雨胶产生裂缝。
(2)原因分析①安装锚固铁脚间距过大;②锚固铁脚采用的材料过薄;④锚固方法不正确。
(3)预防措施①锚固铁脚间距不得大于400mm,铁脚距铝框边角的距离不大于180mm;铁脚须经防腐处理,两端应伸出铝框,作内外锚固。
铝合金门窗安装质量通病及防治措施
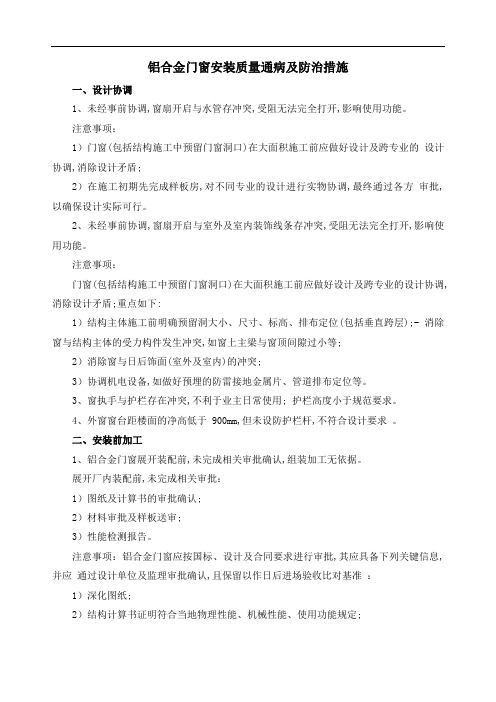
铝合金门窗安装质量通病及防治措施一、设计协调1、未经事前协调,窗扇开启与水管存冲突,受阻无法完全打开,影响使用功能。
注意事项:1)门窗(包括结构施工中预留门窗洞口)在大面积施工前应做好设计及跨专业的设计协调,消除设计矛盾;2)在施工初期先完成样板房,对不同专业的设计进行实物协调,最终通过各方审批,以确保设计实际可行。
2、未经事前协调,窗扇开启与室外及室内装饰线条存冲突,受阻无法完全打开,影响使用功能。
注意事项:门窗(包括结构施工中预留门窗洞口)在大面积施工前应做好设计及跨专业的设计协调,消除设计矛盾;重点如下:1)结构主体施工前明确预留洞大小、尺寸、标高、排布定位(包括垂直跨层);- 消除窗与结构主体的受力构件发生冲突,如窗上主梁与窗顶间隙过小等;2)消除窗与日后饰面(室外及室内)的冲突;3)协调机电设备,如做好预埋的防雷接地金属片、管道排布定位等。
3、窗执手与护栏存在冲突,不利于业主日常使用; 护栏高度小于规范要求。
4、外窗窗台距楼面的净高低于 900mm,但未设防护栏杆,不符合设计要求。
二、安装前加工1、铝合金门窗展开装配前,未完成相关审批确认,组装加工无依据。
展开厂内装配前,未完成相关审批:1)图纸及计算书的审批确认;2)材料审批及样板送审;3)性能检测报告。
注意事项:铝合金门窗应按国标、设计及合同要求进行审批,其应具备下列关键信息,并应通过设计单位及监理审批确认,且保留以作日后进场验收比对基准:1)深化图纸;2)结构计算书证明符合当地物理性能、机械性能、使用功能规定;3)铝合金型材规格、强度的合格证明文件,确保符合规定;4)性能检测报告符合规范、设计及合同要求(包括抗风压性能、水密性能、气密性能、空气声隔声性能、保温性能、遮阳性能、采光性能、启闭力、反复启闭性能等等)。
2、铝合金门窗半成品存在明显缺陷,反映厂内组装加工质量不达标。
注意事项:对首批进场的组装半成品应严格验收,并须详细具体地指出厂内加工的缺陷,以便能在组装前期及时纠正,预防缺陷重复及扩大;若有必要,可对半成品出厂付运前进行厂内抽检验证,预防耗时运输。
铝合金门窗渗漏原因分析及预防措施

铝合金门窗渗漏原因分析及预防措施铝合金门窗作为建筑门窗的主要类型之一,有着轻便、美观、稳定性好等优点,被广泛应用于各种建筑中。
然而,在使用过程中,铝合金门窗渗漏成为了一个常见问题,不仅影响了使用效果,还可能造成安全隐患和能源浪费。
因此,必须认真分析铝合金门窗渗漏的原因,采取有效的预防措施。
1.设计不当铝合金门窗的设计要素及构造关键因素复杂,如型材断面形状、将型材拼接间隙、抗风压性能等均会直接影响渗漏。
如果设计不当,在门窗拼合处或组合处会出现漏缝,从而导致门窗渗漏。
2.材料质量不合格铝合金门窗的质量取决于其材料质量,如果其型材、密封胶等材料质量不合格,容易造成门窗渗漏。
例如,密封胶材料常常出现老化、水分渗入等问题,从而导致密封性差,造成门窗渗漏。
3.施工技术不符合标准铝合金门窗的安装是影响渗漏的关键因素之一。
如安装不平整、角度不正、拼接不够紧密等都会对门窗的密封性产生不良影响。
另外,如果安装时不注意保持型材表面的光洁度,正常的气密性就会受到影响,导致门窗渗漏。
4.局部破损破损就是指模板损坏、螺纹筋露在外面、砖缝与底板之间有空隙等导致水渗透。
铝合金门窗由铝材件和密封条等构成,如果密封条老化破损,或者门窗的其他部分出现松动、脱落等问题,也会导致门窗渗漏。
1.合理的设计针对不同的应用场景,采用适合的铝合金型材断面形状和包装方式,以确保材料密性。
确保安装完毕后门窗的封边处发挥其效应。
2.优质的资料材料铝合金门窗外部结构的密封胶、玻璃胶等可确保门窗的密封性。
选择质量有保证的原材料,避免出现老化、开裂、过期等问题情况,提高门窗的密封性。
3.做好安装工作安装工作需采用专业操作人员进行,门窗需要符合安装要求,安装要正确。
门窗的安装角度、嵌入式部分的位置、加固方式以及控制填缝深度均需符合标准,这些都直接影响门窗的密封性。
4.定期维护按照门窗维护要求进行定期检查并及时维护,保持门窗密封性。
一旦发现门窗存在漏洞或者损坏的情况,需要及时处理,同时注意保养使用,延长门窗寿命。
铝合金门窗工程质量通病及防治措施
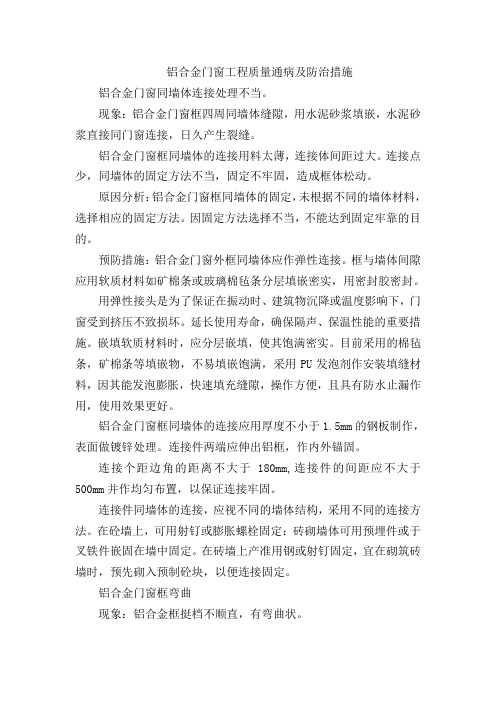
铝合金门窗工程质量通病及防治措施铝合金门窗同墙体连接处理不当。
现象:铝合金门窗框四周同墙体缝隙,用水泥砂浆填嵌,水泥砂浆直接同门窗连接,日久产生裂缝。
铝合金门窗框同墙体的连接用料太薄,连接体间距过大。
连接点少,同墙体的固定方法不当,固定不牢固,造成框体松动。
原因分析:铝合金门窗框同墙体的固定,未根据不同的墙体材料,选择相应的固定方法。
因固定方法选择不当,不能达到固定牢靠的目的。
预防措施:铝合金门窗外框同墙体应作弹性连接。
框与墙体间隙应用软质材料如矿棉条或玻璃棉毡条分层填嵌密实,用密封胶密封。
用弹性接头是为了保证在振动时、建筑物沉降或温度影响下,门窗受到挤压不致损坏。
延长使用寿命,确保隔声、保温性能的重要措施。
嵌填软质材料时,应分层嵌填,使其饱满密实。
目前采用的棉毡条,矿棉条等填嵌物,不易填嵌饱满,采用PU发泡剂作安装填缝材料,因其能发泡膨胀,快速填充缝隙,操作方便,且具有防水止漏作用,使用效果更好。
铝合金门窗框同墙体的连接应用厚度不小于1.5mm的钢板制作,表面做镀锌处理。
连接件两端应伸出铝框,作内外锚固。
连接个距边角的距离不大于180mm,连接件的间距应不大于500mm并作均匀布置,以保证连接牢固。
连接件同墙体的连接,应视不同的墙体结构,采用不同的连接方法。
在砼墙上,可用射钉或膨胀螺栓固定:砖砌墙体可用预埋件或于叉铁件嵌固在墙中固定。
在砖墙上产准用钢或射钉固定,宜在砌筑砖墙时,预先砌入预制砼块,以便连接固定。
铝合金门窗框弯曲现象:铝合金框挺档不顺直,有弯曲状。
原因分析:铝合金框受到挤压或撞击产生变形,采用材料厚度没有按规范要求组装,刚度不够。
预防措施:铝合金材料厚度按国家规定窗结构型材为1.4mm厚,门结构型材为2.2mm。
对变形的要进行修理后再安装,对框四周的缝隙嵌要适宜,防止过量,向内弯曲。
成品保护:铝合金门窗运输、搬运、堆放要小心谨慎轻放。
铝合金门窗安装后,要做保护罩,防止碰撞,引起变形、损坏。
铝合金压铸常见缺陷解决方案与预防措施

铝压铸十大缺陷解决方案与预防措施一、流痕和花纹外观检查:铸件表面上有与金属液流动方向一致的条纹,有明显可见的与金属基体颜色不一样的无方向性的纹路,无发展趋势。
1.流痕产生的原因有如下几点:1)模温过低2)浇道设计不良,内浇口位置不良3)料温过低4)填充速度低,填充时间短5)浇注系统不合理6)排气不良7)喷雾不合理2.花纹产生的原因是型腔内涂料喷涂过多或涂料质量较差,解决和防止的方法如下:1)调整内浇道截面积或位置2)提高模温3)调整内浇道速度及压力4)适当的选用涂料及调整用量二、网状毛翅(龟裂纹)外观检查:压铸件表面上有网状发丝一样凸起或凹陷的痕迹,随压铸次数增加而不断扩大和延伸。
产生原因如下:1)压铸模腔表面有裂纹2)压铸模预热不均匀解决和防止的方法为:1)压铸模要定期或压铸一定次数后,应作退火处理、消除型腔内应力2)如果型腔表面已出现龟裂纹,应打磨成型表面,去掉裂纹层3)模具预热要均匀三、冷隔外观检查:压铸件表面有明显的、不规则的、下陷线性型纹路(有穿透与不穿透两种)形状细小而狭长,有时交接边缘光滑,在外力作用下有断开的可能。
产生原因如下:1)两股金属流相互对接,但未完全熔合而又无夹杂存在其间,两股金属结合力又很薄弱2)浇注温度或压铸模温度偏低3)浇道位置不对或流路过长4)填充速度低解决和防止的方法为:1)适当提高浇注温度2)提高压射比压缩短填充时间,提高压射速度3)改善排气、填充条件四、缩陷(凹痕)外观检查:在压铸件厚大部分的表面上有平滑的凹痕(状如盘碟)。
产生原因如下:1)由收缩引起压铸件设计不当壁厚差太大浇道位置不当压射比压低,保压时间短压铸模局部温度过高2)冷却系统设计不合理3)开模过早4)浇注温度过高解决和防止的方法为:1)壁厚应均匀2)厚薄过渡要缓和3)正确选择合金液导入位置及增加内浇道截面积4)增加压射压力,延长保压时间5)适当降低浇注温度及压铸模温度6)对局部高温要局部冷却7)改善排溢条件五、印痕外观检查:铸件表面与压铸模型腔表面接触所留下的痕迹或铸件表面上出现阶梯痕迹。
铝合金模板施工的常见问题及防治措施

铝合金模板施工的常见问题及防治措施01立杆间距不符合方案要求➤典型实例➤隐患影响立杆间距不符合要求间距过大会明显降低支撑体系的承载能力,影响脚手架的整体稳定性,严重的可能导致坍塌,给工程带来巨大损失。
➤纠正措施按方案要求补设立杆支撑。
➤预防措施加强过程交底及施工验收,严格按方案要求施工,对于立杆设置不满足要求的及时整改。
楼板及梁底支撑配用早拆独立钢支撑的,支撑间距小于1.3MX1.3M。
02斜撑设置不满足方案要求➤典型实例➤隐患影响铝模斜撑设置不合要求直接影响模板的刚度和稳定性,易照成后期混凝土结构浇筑时模板失稳及偏位,导致混凝土成型质量感观差并且存在一定安全隐患。
➤纠正措施斜撑设置间距过大及安装不满足要求的需补设斜撑。
➤预防措施严格按方案要求施工,加强过程检查验收,不满足要求的及时整改,柱、墙体两侧安装斜支撑,支撑距墙体端部不大于750mm,支撑间距不大于1600mm,宽度大于2米的墙体设置不少于两道斜撑,宽度小于1.2米的墙体及剪力墙短肢设置不少于一根斜撑,楼板需预留斜撑固定预埋件。
03背楞、螺杆设置不符合方案要求➤典型实例➤隐患影响背楞及螺杆设置不合要求会导致铝模板墙板的移动和弯曲变形,造成混凝土成型质量差。
➤纠正措施背楞及对拉螺杆间距过大的需及时补设加固。
➤预防措施1、严格按方案要求施工,加强过程验收,墙柱侧模采用背楞及对拉螺杆加固,对底层背楞距离板面间距需不大于300mm,两道背楞间距不大于700mm,层高2.8至3米的墙柱,内墙柱必须设置不少于4道背楞,外墙柱必须设置不少于5道背楞;2、梁侧模背楞当梁高小于1米使可不设背楞,梁高1至1.2米时设置一道背楞,梁高大于1.2米时按墙体模板设置背楞对拉加固。
04背楞、螺杆缺失或使用位置错误➤典型实例➤隐患影响铝模背楞及螺杆缺失及设置不合理会造成铝模板墙板固定不牢,导致混凝土浇筑易爆模,影响混凝土结构外观质量,存在一定安全隐患。
➤纠正措施对于背楞螺栓间距布置过大的中间必须补设对拉螺栓,采用搭接的背楞应更换后再加固,尽量避免背楞搭接。
铝合金针孔铸造缺陷及原因

铝合金针孔铸造缺陷及原因一、引言铝合金针孔铸造缺陷是一种常见的缺陷,它会对铝合金零件的性能和质量产生不良影响。
本文将从铝合金针孔的定义、形成原因、检测方法和预防措施等方面进行详细介绍。
二、铝合金针孔的定义铝合金针孔是指在铝合金零件中出现的小孔状缺陷,其直径通常在0.1mm以下。
这种缺陷通常分布在零件表面或内部,并且不会对整个零件产生太大影响。
但是,在某些情况下,当针孔数量过多或者大小较大时,会导致零件强度下降、裂纹产生等问题。
三、形成原因1. 气体混入氧化物和其他杂质在液态金属中产生氧化反应时,会释放出大量氧气和其他气体。
如果这些气体不能及时排出,就会在凝固过程中形成气泡。
2. 金属液流动不畅当液态金属流动速度过快或者受到阻碍时,就会形成一些小洞,这些小洞就是针孔。
这种情况通常发生在铸造过程中温度较低的区域。
3. 模具表面不光滑如果模具表面不光滑,或者有一些凸起和凹陷,液态金属就会在这些地方停留,形成气泡和针孔。
4. 金属液中杂质含量过高铝合金中的杂质含量过高,会导致液态金属表面张力增大,从而形成针孔。
四、检测方法1. 目视检查目视检查是最简单、最直观的方法。
通过目视检查可以发现表面或者内部的缺陷。
但是,这种方法只适用于比较明显的缺陷。
2. X射线检测X射线检测可以发现内部缺陷,包括针孔、气孔等。
但是这种方法需要专业设备和技术人员进行操作,并且对环境要求较高。
3. 超声波检测超声波检测可以发现内部缺陷,并且对环境要求相对较低。
但是这种方法需要专业设备和技术人员进行操作,并且对零件形状和材料有一定要求。
五、预防措施1. 优化铸造工艺通过优化铸造工艺,可以减少气体混入和液态金属流动不畅等问题。
例如,在铸造过程中加入一些稳泡剂可以减少气体混入,同时增加浇注温度可以提高液态金属的流动性。
2. 优化模具设计通过优化模具设计,可以使液态金属在流动时更加顺畅,从而减少针孔产生的可能性。
例如,在模具表面涂上一层光滑的涂料,或者采用数控机床制作模具等方法。
铝合金门窗制作的质量通病和预防措施
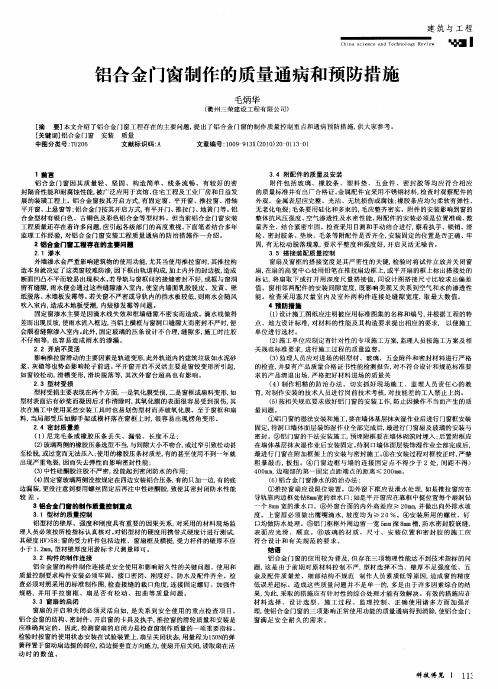
●l
铝合金 门窗 制作 的质量通病和预 防措施
毛炳华
( 州三 荣建 设工程 有 限公 司) 衢
[ 摘 要] 本文 介绍 了铝合 金 门窗 工程存 在 的主 要 问题 , 出 了铝 合 金 门窗的制 作质 量 控制重 点 和通病 预 防措 施, 大家 参考 。 提 供 [ 关键 词] 合金 门窗 安装 质量 铝 中图分类 号 : U 0 T 26 文献标 识码 : A 文章编号 :0 9 9 3 ( 0 0 2 1 3 0 1 0 1 X 2 1 ) 0 0 1 1
1荫 言 铝 合 金 门 窗 因其 质 量 轻 、 坚 固 、构 造 简 单 、 线 条 流 畅 、有 较 好 的 密 封隔音 性 能和 耐腐 蚀性 能, 广泛 应用 于宾馆 、 宅工 程及 工业厂 房和 日益 发 被 住 展的装 璜工程 上 。铝合 金窗按 其开 启方式 , 固定窗 、平开 窗、推 拉 窗、滑轴 有 平开 窗、 悬窗等 : 合金 门按其 开 启方式 , 平开 门、推拉 门、 簧 门等 。 上 铝 有 地 铝 合金 型材有银 白色 、古铜 色及 彩色铝 合金 等型材 料 。但 当前 铝合 金 门窗安装 工程质 量还存 在着 许多 问题, 引起 各级 部 门的高度 重视 。 面笔者 结合 多年 应 下 监理 工作 经验, 铝合 金 门窗 安装 工程 质量 通病 的防治 措旌 作 一介 绍 。 对 2铝 合金 门窗 工程 存在 的主 要 问题 2 1渗水 外墙渗 水会严 重影 响建筑 物的使 用功 能, 尤其 当使用推 拉窗 时, 推拉构 其 造本 身就 决定了这类 窗较难 防渗, 因下框 由轨道构成, 加上 内外 的封 边板, 造成 断面凹 凸不平 而较易 出现积 水 。 导轨与 窗框 问的接 缝密封 不好 , 若 或框 与 窗洞 留有缝 隙, 雨水便 会通过 这些 缝隙渗 入室 内, 室 内墙 面乳胶 脱皮 、发黄 、壁 使 纸脱 落 、 木墙 板发霉 等 。 关窗 不严密 或导 轨 内的挡水 板较低 , 若 则雨 水会 随风 吹入 室 内, 造成 木地板 受潮 , 内装 修发 霉等 问题 。 固定 窗渗 水主 要是 因滴水 线失 效和框 墙缝 隙不密 实而 造成 。滴水 线做 得 差而 出现反坡, 使雨水流 入框 边, 当铝上横框 与窗洞 口缝 隙大 而密封 不严时, 便 会顺 着缝 隙渗入 室 内。 此外 , 固定玻璃 的压 条设 计不 合理, 隙多, 缝 施工 时注胶 不仔 细 等 , 也容 易造 成 雨水 的渗 漏 。 2 2 开启 不灵活 影 响推拉窗滑 动的主要 因素是轨 道变形 , 外轨道 内的建筑 垃圾如水 泥砂 此 浆、 灰碴等 也势 必影 响轮子前 进 。 平开 窗开启 不灵活 主要 是窗铰 变 形所 引起, 如窗 铰松 动, 滑槽 变形 , 滑块 脱落 等, 其次 外窗 台超 高也 有 影响 。 2 3 型材受 损 . 型材 受损主要表现 在两个方 面, 一是氧 化膜受损, 二是 窗框或扇 料变形 , 如 型材表面 沾有砂 桨而 凝因 后才作 清除 时, 其氧化 膜的表 面很容 易 受到损 伤, 其 次在施 工 中使 用某些 安装 工具 时也易 划伤 型材而 弄破 氧化膜 。至 于窗框 和扇 料, 当局部 受压 如脚 手 架或 横杆 落在 窗框 上 时, 容 易 出现 楞 角变 形 。 很 24 密封 质量 差 () 1 尼龙 毛 条或 橡胶 压 条 丢失 、漏 装 、 长度 不足 : () 2玻璃两 侧的橡胶 压条选型 不当, 与间隙大 小不吻合, 或过 窄引致松 动甚 至 松脱, 或过宽而 无法压入 : 的橡胶压 条材质差 , 的甚至 使用不到 一年就 使用 有 出现严重 龟裂, 因而 失去 弹性而 影 响密封性 能 : () 3 中性 硅酮胶 注胶 不严 密, 能起 到密 闭防水 的作用 : 没 () 4 固定窗 玻璃两侧没 按规定在 四边安装 铝合压 条, 的只加 一边, 的底 有 有 边 漏装, 更没注 意 到要用 螺丝 固定后 再注 中性硅 酮胶, 致使 其密 封闭 防水性 能
高铁用大型复杂铝合金铸件的铸造缺陷与预防措施

高铁用大型复杂铝合金铸件的铸造缺陷与预防措施随着高铁领域的快速发展,大型复杂铝合金铸件作为重要的组成部分,在高铁列车的运行中起着至关重要的作用。
然而,在铸造过程中,往往会出现一些铸造缺陷,严重影响了铸件的质量和性能,需要采取相应的预防措施。
铸件缺陷是指在铸造过程中形成的、与铸件性能、外观或使用寿命不符的不良特征。
下面,我们将介绍一些常见的大型复杂铝合金铸件的铸造缺陷以及相应的预防措施。
首先,气孔是铝合金铸件中常见的缺陷之一。
气孔是由于熔融金属中存在的气体在凝固过程中无法完全排出而形成的。
气孔严重影响了铸件的力学性能和表面质量。
为了预防气孔的产生,可以采取以下措施:合理设计浇注系统,控制铸件内部气体的排出;在铸造过程中使用良好的熔炼材料,控制熔融金属中的气体含量;增加熔融金属的冷却速度,减少气体的溶解度。
其次,热裂纹也是大型复杂铸件中常见的缺陷。
热裂纹是由于铸件在凝固过程中所受到的内应力超过其强度极限而引起的。
热裂纹不仅会导致铸件的破裂,还会降低铸件的力学性能。
预防热裂纹的方法包括:合理设计铸造工艺,减少内应力的集中;控制铸件的凝固速度,减少内应力的产生;使用合适的冷却系统,降低铸件的温度梯度。
另外,夹杂物是指铸件中存在的非金属物质,如氧化物和碳化物等。
夹杂物会影响铸件的强度和韧性,并且还会导致铸件的断裂。
预防夹杂物的方法主要有:使用合适的熔炼材料和熔炼工艺,减少杂质的含量;控制熔融金属的温度和搅拌速度,促进夹杂物的沉淀;合理设计浇注系统,减少外界杂质的进入。
此外,组织非均匀性也是大型复杂铝合金铸件中常见的缺陷之一。
组织非均匀性会导致铸件性能的不一致,影响铸件的使用寿命。
预防组织非均匀性的方法包括:优化熔炼工艺,保证熔融金属的成分均匀;控制铸件的冷却速度,促使组织的均匀凝固;合理设计浇注系统,保证铸件的充型性能。
最后,裂纹也是大型复杂铝合金铸件的常见缺陷之一。
裂纹严重影响了铸件的力学性能和外观质量。
铝合金门窗渗漏原因分析及预防措施

铝合金门窗渗漏原因分析及预防措施
铝合金门窗在日常使用中,有时会出现渗漏现象。
渗漏是指门窗系统中的水分或空气
通过门窗构件的接缝或其他缺陷进入室内或室外的现象。
渗漏问题不仅会影响门窗的正常
使用,还可能导致室内环境潮湿、结露等问题。
我们需要对铝合金门窗渗漏的原因进行分析,并采取相应的预防措施。
1.1 材料问题:铝合金门窗使用的材料质量不达标或不合理选择,容易导致渗漏。
比
如门窗密封条的弹性不足,密封性能差,不能很好地防止水分和空气的渗透。
1.2 施工问题:门窗安装过程中施工不规范,例如门窗与墙体之间的缝隙没有进行适
当的填缝处理,或者填缝材料选择不当,密封性能不好;门窗的固定螺栓紧固不牢,容易
造成门窗松动和渗漏。
1.3 设计问题:门窗的设计不合理,例如门窗玻璃的凹凸不平,没有安装雨水槽或排
水系统,导致雨水无法顺利排出,进而渗入室内。
2.1 选择优质的材料:选择正规厂家生产的门窗,材料质量有保证,尤其是密封条的
材料要选择具有良好弹性和耐老化性能的产品,以确保密封性能。
2.4 加强门窗的维护:定期检查门窗的密封条和玻璃,如发现松动、老化等问题及时
更换。
及时清理门窗的排水系统,保持畅通。
2.5 进行严格的验收:在门窗安装完毕后,进行严格的验收,检查是否存在渗漏问题,如有问题及时解决。
铝合金门窗渗漏问题的原因多种多样,需要综合考虑材料、施工和设计等方面的因素。
通过选择优质材料、注重施工质量、加强门窗设计和维护等措施,可以从根本上预防铝合
金门窗的渗漏问题的发生。
- 1、下载文档前请自行甄别文档内容的完整性,平台不提供额外的编辑、内容补充、找答案等附加服务。
- 2、"仅部分预览"的文档,不可在线预览部分如存在完整性等问题,可反馈申请退款(可完整预览的文档不适用该条件!)。
- 3、如文档侵犯您的权益,请联系客服反馈,我们会尽快为您处理(人工客服工作时间:9:00-18:30)。
浅议影响铝合金产品质量的原因及预防措施[摘要]:铝能与许多元素形成合金,铝基合金也很轻,而且强度很好,有些铝及合金的比强度超过钢铁,其弹性率小,具有耐冲击性能。
铝合金则是在纯铝中加入适量的合金元素,以获得所需要的材料性能,从而提高铝的强度、抗蚀性、耐磨性、硬度等,以适应各种不同用途的需要。
[关键词]:铝合金质量气孔夹渣拉裂冷隔疏松
包瘤(金属瘤)偏析内外缩孔针孔裂纹元素化学成分中图分类号:u663.9+1 文献标识码:u 文章编号:1009-914x(2012)32- 0608-01
铝合金则是在纯铝中加入适量的合金元素,以获得所需要的材料性能。
这种向金属中添加某些其他元素改变金属的性质,以适应不同用途的需要,称之为合金化。
对于铝来说,合金化的主要目的就是为了提高铝的强度,改善其加工性能、抗蚀性、耐磨性、硬度、表面性能以及其他特殊性能,以适应各种不同用途的需要。
针对铸造产品常见的表面质量缺陷,我简单的谈谈影响合金产品质量的原因及预防措施。
首先,就铝锭而言。
如果循环水池长期不清理沉积物,就可造成铝锭外观发乌,不银亮,从而影响产品的销路。
所以,在生产中要定期的对循环水池进行清理。
同时,铝液浇注温度的高低也会影响产品的质量。
如铸模长时间被高温铝液使用,就可烧变形,从而
导致铸模的商标不清楚,从而产生更多的次品,所以铝锭产品的浇注温度一定要保持在720℃以下。
另外,我们以纯铝电工圆铝杆产品为例。
电工圆铝杆的内部质量缺陷主要有气孔和夹渣。
气孔。
浇铸时,如果铸坯内气孔含量过多,可能导致在轧制过程中断线或缠卷过程中被拉断,对产品质量造成很大影响。
产生气孔的主要原因有:铝液温度过高,导致含氢量过高;在浇铸过程中冷却水产生的大量蒸汽没有及时散去,部分蒸汽被融入铝液内部形成气孔;钢带上润滑油太少,没有形成一层较好的保护膜,造成蒸汽进入铝液。
防止气孔的主要措施:降低铝液温度,保证铝液在正常的浇铸范围内;在浇铸前安装除气装置或在保持炉内进行除气处理;在浇铸部位安装风扇将蒸汽吹散;在浇铸过程中调整好润滑油量,保证钢带上有一层保护油膜。
内部夹渣。
夹渣同样对电工圆铝杆的性能有很大影响,在生产过程中可能导致断坯或断线。
夹渣产生的原因有:没有进行有效的精炼处理,铝液内部含渣过多;铝液温度过高,产生较多的氧化浮渣;铝液在溜槽转注过程中没有使用浮漂,使铝液不断冲刷,造成渣滓融入铝液中。
主要防止措施:在保持炉内对铝液进行精炼并保证铝液静置时间;控制好保持炉内温度,确保铝液温度在标准范围内;在浇铸前加入过滤装置,如使用陶瓷过滤板进行过滤;在溜槽转注过程使用
浮漂,使铝液在氧化膜下层流动,保持液面平稳,避免将氧化渣冲入铝液中。
对于电工圆铝杆来说,元素的化学成分对他的质量的影响也不可小估。
如金属b、cr、mn、v等几种元素的含量影响电工圆铝杆的电阻率,当这几种元素含量高时,其电阻率也大。
预防措施:就是一定要在铸造前按比例添加一定量的精炼剂,以消除这些金属元素的干扰。
切记,精炼剂一定要按照工艺试验要求添加,否则就会适得其反,如铝硼合金添加过多,则会使b含量增加,也会影响电工圆铝杆的电性能。
另外,我们针对合金锭为例,它常见的内部质量缺陷主要有:夹渣、内外缩孔、裂纹等。
合金锭的一般夹渣:呈暗灰色的群集或单个分布在铸件上部水平面上,或在浇注缝隙的导入口,或两铸件壁的转接处,或盲端和铸件内部。
合金一般夹渣形成的原因:1、原材料及重熔料中混入了夹渣;
2、合金液中的熔渣及其他非金属氧化物未排除干净。
3、浇注系统设计不合理,浇注时把浮渣卷入型腔。
4、合金液进入型腔的速度过大,氧化膜或熔渣卷入型腔。
5、精炼后扒渣清理不完全,静置时间不够或在高温下搅拌合金液太多而造成再次氧化。
6、浇注时断流。
7、由于合金锭采用双级板式过滤,过滤速度慢,有些熔铸工为了早点干完,人为的将过滤片损坏,从而造成内部夹渣。
8、溜槽壁破损后,没有及时补救造成。
合金一般夹渣防止办法及补救措施:1、选用合格的原材料和重熔旧料。
2、严格遵守合金的熔炼工艺,保证获得纯净的合金液。
3、采用底注或缝隙型开放式浇注系统,设置撇渣、集渣结构、安设过滤网,加强浇注系统的挡渣作用。
4、缓慢平稳连续地进行浇注,保证合金液不断流,绝不用小容量浇包浇注大容量的铸型(件)。
5、充分精炼合金液,在浇注前一定要静置,并适当降低合金液的浇注温度。
6、采用带隔板的挡渣浇包浇注,在浇注前要撇除干净合金液表面上的氧化皮及熔渣。
7、要严格管理,减少人为因素。
8、每熔次生产完后,应及时组织人员对破损部分修补,防止由于铝液冲刷溜槽壁产生更多的夹渣。
外、内缩孔缺陷特征:为铸件上显露出的凹陷。
其表面粗糙整个凹陷部位结晶粗大,多发生在冒口下面或铸件厚薄截面的过渡区位,或两壁相交的尖角部位,在外检查、喷砂或氧化处理后均可发现。
外、内缩孔缺陷产生的原因:产生内外缩孔、疏松、显微疏松,主要是合金从液态向固态转变过程中,在结晶凝固冷却中,由于体积的收缩得不到补充的缘故:1、浇注温度过高或铸型导热系数小,热容量小,使铸件冷却太慢。
2、铸件的设计结构不合理,厚簿截面连接处壁厚差太大,形成热节、冷却慢、无合金液补缩。
3、合金液进入型腔的位置不正确。
4、在厚大部位没安设补缩冒口,或安放位置不当,或其补缩液量不够。
5、铸型的排气性不好,使型腔内的气垫反压大,阻碍合金液流向后凝固要补缩的部位。
6、浇
注速度太快。
外、内缩孔缺陷防止办法及补救措施:1、改进铸件的设计结构和形状,如降低厚壁与薄壁间的壁厚差,加粗或加厚加强筋,把厚大部位改成空心结构等防止产生热节、尽量使铸件各部位冷却均匀、同时凝固的办法。
2、在铸件的厚大部位安设补缩冒口,冒口的位置和大小应保证冒口内的合金液比此补缩部位的位置高、补缩量多,井有足够的补缩压力头(通常≥60mm)。
3、适当降低浇注温度和浇注速度。
4、在浇注后,当合金液涨满冒口上平面时,又从冒口中补浇合金液。
裂纹缺陷特征:在实心铸锭表面出现的直线状或波浪形的暗灰色裂口,在空心铸锭模断面出现的放射状或环状裂口,在肩铸锭表面出现的直线形或其他形状的裂口。
裂纹缺陷产生的原因:1、合金的化学成分出现偏差。
2、浇注温度太高,浇注速度太快。
3、合金液未进行精炼或精炼不充分,气体各夹杂物含量过多。
4、结晶器表面不光滑或润滑不良,或安装倾斜而拉裂。
裂纹缺陷防止办法及补救措施:1、控制准合金液的化学成分,特别是要控制好fe、si的含量。
2、适当降低合金液的浇注温度和浇注速度。
3、选用合适的精炼方法和精炼剂,对合金进行充分的精炼,降低气体和氧化夹渣物的含量。
4、均匀分配液流,检查并防止漏斗倾斜。
5、保持结晶器内表面光滑清洁及位置的水平。
总之,只要我们熟练掌握这些技术,并很好的按照工艺流程去
操作,就可以避免合金的诸多缺陷,从而生产出优质的产品。
参考文献
〔1〕王捷,电解铝生产工艺与设备[m],北京:冶金工业出版社,2006.
〔2〕向凌霄.原铝及其合金的熔炼与铸造[m],北京:冶金工业出版社,2005.
〔3〕肖亚庆.铝加工技术使用手册[m],北京:冶金工业出版社,2005.
〔4〕王祝堂,田荣璋.铝合金及其加工手册(第3版)[m],长沙:中南大学出版社,2005.
〔5〕潘复生,张丁非.铝合金及应用[m],北京:化学工业出版社,2006.
[6] 徐帮学,铝与铝合金产品国内外最新标准及其工程应用技术全书,银声音像出版社,2003.。