10kw英文中性说明书内页
HT10M_HT22M英文说明书
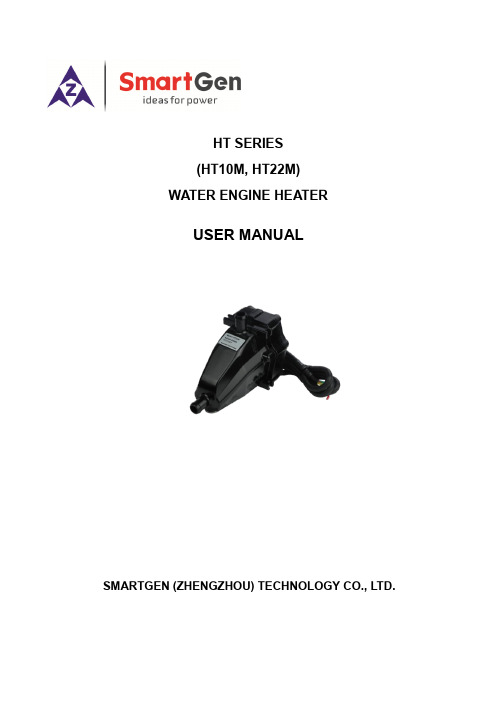
HT SERIES(HT10M, HT22M)WATER ENGINE HEATERUSER MANUALSMARTGEN (ZHENGZHOU) TECHNOLOGY CO., LTD.Chinese trademarkEnglish trademarkSmartGen— make your generator smartSmartGen Technology Co., Ltd.No.28 Jinsuo RoadZhengzhouP. R. ChinaAll rights reserved. No part of this publication may be reproduced in any material form (including photocopying or storing in any medium by electronic means or other) without the written permission of the copyright holder.Applications for the copyright holder’s written permission to reproduce any part of this publication should be addressed to SmartGen Technology at the address above.Any reference to trademarked product names used within this publication is owned by their respective companies.SmartGen Technology reserves the right to change the contents of this document without prior notice.Table 1 - Software VersionDate Version Note2018-03-23 1.0 Original release.CONTENTS1 OVERVIEW (4)2 PERFORMANCE AND CHARACTERISTICS (4)3 TECHNICAL PARAMETERS (5)4 INDICATOR (5)5 OPERATION (6)5.1 TEST RUNNING (6)5.2 RESET OVERHEAT PROTECTION (6)6 WIRE CONNECTION (6)7 HEATER CONNECTION (6)8 INSTALLATION INSTRUCTION (7)9 CAUTION (8)10 CASE AND INSTALLATION DIMENSIONS (9)APPENDIX: HEATER PACKING LIST (10)1 OVERVIEWHT Series Water Heater enjoys wide application on various engine coolant preheaters. It has fine cast aluminum enclosure and self-extinguishing engineering plastics end closure, multiple installation ways and easy and convenient use.If during cranking the outside temperature is lower than 4 ºC, engine coolant and lubricant may condense into solid state and lose their lubricating and cooling properties, which can damage the engine. Engine heater should be installed to ensure normal starting and running of the engine when the outside temperature is lower than 4 ºC.HT Series Water Heater combines the following features: cast stainless steel inner pipes and end closure with high corrosion resistance; power, heating and overheat protection light indicators; 3 kinds of heaters with different heating temperature are optional (Standard heater: 40 ºC; 50 ºC and 60 ºC heaters are needed to be customized).This product is suitable for various engine with (0~13.) L displacement.Please login our company's official website () to select heaters.2 PERFORMANCE AND CHARACTERISTICS─Fine cast aluminum enclosure and special surface treatment with high corrosion resistance and high/low temperature capability;─Stainless steel inner pipes and end closure with high corrosion resistance;─Coolant temperature is controlled by thermostat which is installed within the heater. It has simple connections and high reliability;─power, heating and overheat protection light indicators make it easy to observe the heater status;─There is a water drain valve with seal ring on the bottom of the heater so as to be used when needed;─Users can press ―Test‖ button to test-run the machine in the extremely high ambient temperature;─Overheating thermostat provides the protection of dry heating and overheating;─Multiple installation ways apply to different installation situations;─This product can work normally at -25 ºC temperature.3 TECHNICAL PARAMETERSHT series water heaters are divided into 2 types according to the power of the internal heating pipes; both types’ case and installation dimensions are all the same.Table 2 – Technical ParametersModelHT10MHT22MRated Power 1190W (220V1000W )2200W(220V1850W)Rated Voltage 240V Rated Current5A 9.2A Engine Displacement (L) 0~7 7~13Thermostat Set Point(40±3) ºCThermostat RangeStandard: Off: (40±3) ºC Reset: (25±6) ºCHT10M-1, HT22M-1: Off: (50±3) ºC Reset: (35±6) ºC HT10M-2, HT22M-2: Off: (60±3) ºC Reset: (45±6) ºCOverheating Thermostat Range Off: (110±3) ºC Reset: Manual Insulating Resistance ≥50MΩ Electrical Strength AC 1.5kV 1min Inlet/Outlet Size 3/4″(φ19mm) Max. Water Pressure 0.5MPa Protection Level IP54Vibration Resistance (5~8)Hz; Amplitude±7.5mm; Triaxial (8~500)Hz; a=2g; Triaxial Shock Resistance Half-sine Wave; a peak =50g; Triaxial Working Conditions -25 ºC~+70 ºC Storage Conditions -30 ºC~+70 ºCCase Dimensions 208mm×150mm×177mm Weight 1.2kg4 INDICATORFig.1 – Panel Indicator Drawing5 OPERATION5.1 TEST RUNNINGIf the heater is not heating and the overheat protection light is not on, users can press ―Test‖ button to perform the test-run operation.5.2 RESET OVERHEAT PROTECTIONWhen overheat alarm indicator is on, heater will enter into overheat protection status and stop heating. If heater temperature falls below the reset temperature limit of overheat protection thermostat (95℃), users need to press reset button and heater enters into auto mode again.6 WIRE CONNECTIONThe supplied power cable is 1.2 m long. Please follow the back cover application diagram when wiring; earth line must be soundly connected to earth.In the above diagram: L--Phase line (Red), N-Neutral line (Green), E-Earth line (Yellow).7 HEATER CONNECTIONPlease install the heater vertically according to the diagram before use. Paying attention to direction of heater inlet and outlet, and ensure that the heater position is below the lowest water lever of the engine and that all the air is exhausted out of the heater and it is topped off with water.Fig.2 – Heater Operating Schematic DiagramFig.3 – Heater Position Diagram 8 INSTALLATION INSTRUCTIONFig.4 – Installation Instruction9 CAUTIONBefore starting the machine, ensure that all the air is exhausted out of the heater and it is topped off with coolant. If water is used, please drain it off when generator is stopped to avoid internal corrosion. Otherwise, the remaining water freezes when temperature is lower than 0 °C, which can damage the enclosure.Corresponding antifreeze is strongly recommended.Earth line must be soundly connected to earth.Drain valve: Can be opened or closed using hexagonal tools.10 CASE AND INSTALLATION DIMENSIONS(Unit: mm)Fig.5 – Overall DimensionsAPPENDIX: HEATER PACKING LISTTable 3 – Packing ListNo. Name Number Remarks1 Heater 12 Bracket 13 Flat gasket4 GB/T 95 64 Spring washer 4 GB/T 93 65 Hexagon nut 4 GB/T 6170 M66 Hexagon screws 4 GB/T 5783 M6×257 Hose clamps 4 Φ 18 –Φ338 Certificate 19 User Manual 1_________________________________。
AIMS Power 10,000瓦直流到交流电源逆变器 (V 2.0) 使用说明书
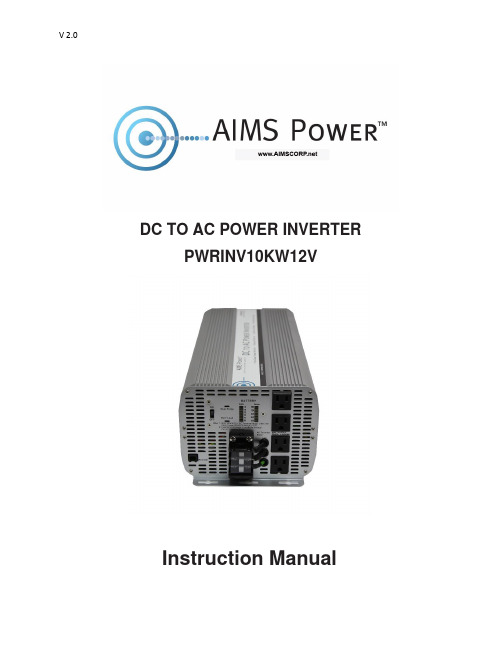
DC TO AC POWER INVERTER PWRINV10KW12VInstruction ManualIntroductionThe AIMS Power 10,000 watt inverter is the most technology advanced mobile DC to AC power inverter available. AIMS also offers the 8,000 Watt 12V or 12,000 Watt 24V.This inverter is used in a wide range of applications including back up power for remotehomes, off-grid systems, RVs, boats, commercial vehicles and mobile businesses. The10,000 watt inverter will operate most pumps, motors, lights, heaters, compressorbased appliances and hand tools.To get the most out of the power inverter, it must be installed and used properly. Readthe instructions in this manual before installing and using this product. Follow all safetyprecautions.FUNCTIONSFRONT VIEWA. On/Off switch: Leave in the OFF position during installation.B. Over temperature indicator: Lights when inverter protects itself against overheating. Invertershuts down while indicator is on. Inverter will restart automatically and indicator will turn off when the inverter cools.C. Over load indicator: Lights when inverter shuts down because of overload. Indicator will turn offand inverter will restart when overload is removed.D. Bar meters: Displays battery voltage and current. Current should be in the green zone forcontinuous operation. The inverter will operate for several minutes when the current is in the yellow zone. Operation with battery voltage or current in the red zone of a meter will result in protective shutdown of inverter.E. AC outlets: Maximum recommended output per outlet is 1500W.F. Remote port: Used with remote switch to turn inverter ON/OFF (sold separately).G. AC terminal block: Hard wire block providing inverter's full power.E: AC outletsD: Bar metersB: Over temperature indicatorA: On/Off switch C: Over load indicatorG: AC terminal Block F: Remote portREAR VIEWA: Fan: Do not obstruct, allow at least 12 inches for air flow.B: Battery terminals: Connect to 12V, or 24V, or 36V, or 48V (depending on inverter model) battery(s) or other DC power source. "+" is positive & " - " is negative. Reverse polarity connection will blow internal fuse and may damage inverter permanently. Make sure you check your input voltage and do not REVERSE POLARITY! This will void the warranty.C: Chassis ground lug: Connect to earth ground or to vehicle chassis using #8 AWG wire. Warning! Operation of the inverter without a proper ground connection may result in an electrical safety hazard.QUICK HOOK-UP AND TESTINGIf you would like to quickly hook-up the power inverter and check its performance before moving forward with your installation, please follow these guidelines:1. Unpack and inspect the power inverter, check to see that the power switch is in the OFF position.2. Before you connect the battery cables, make sure the power switch is in the off position. Connect Red (+) battery cable to Red (+) inverter terminal. Connect Black (-) battery cable to Black (-) inverter terminal. Connect Red (+) battery cable to Red (+) battery terminal. Connect Black (-) battery cable to Black (-) battery terminal. Alligator clamp cables may be used but only to connect to the battery. Do not use clamps on inverter terminals. Alligator clamps are not a permanent solution. You may see a spark during connection. Do not reverse the polarity. This may damage the inverter and void warranty. Caution! Loosely tightened connectors result in excessive voltage drop and may cause overheated wires and melted insulation. Reverse polarity connection will blow a fuse in inverter and may permanently damage the inverter. Damage caused by reverse polarity connection is not covered by our warranty. Warning! You may observe a spark when you make this connection since current may flow to charge capacitors in the power inverter. Do not make this connection in the presence of flammable fumes, as explosion or fire may result.A: FanB: Battery terminal (+)B: Battery terminal (-)C: Chassis grounding3. Set the power switch to the on position. Check the meters and indicators on the front panelof the inverter. The voltage bar graph should indicate 11 to 14 volts depending on the voltageof the power source. If it does not, check your power source and the connections to inverter.The other indicators should be off.4. Set power inverter switch to the OFF position, the indicator l ights may blink and theinternal alarm may sound momentarily. This is normal. Plug the test load into the ACreceptacle on the front panel of the inverter. Leave the test load switch off.5. Set power inverter switch to the ON position and turn the test load on, the inverter shouldsupply power to the load. If you plan to measure the true output R.M.S. voltage of inverter, ameter such as FLUKE 87A, BACKMAN 4410 or TRIPLETT 4200 must be used.INSTALLATION1. Where to installThe power inverter should be installed in a location that meets the following requirements:a. Dry - Do not allow water to drip or splash onto the inverter.b. Cool - Ambient air temperature should be between 0°C and 40°C, the cooler the better when operating in this rangec. Ventilation - Allow at least one inch of clearance around the inverter for air flow. Ensure the ventilation openings on the rear and bottom of the unit are not obstructed.d. Safety - Do not install the inverter in the same compartment as batteries or in any compartment capable of storing flammable liquids such as gasoline.2. CablesDC to AC inverters require high amperage/low voltage DC power to low amperage/high voltage AC power. To operate properly, connect inverter DC input terminals direct to battery with heaviest wire available see below:12 Volt Model: 2x set of 4/0 AWG (2 red + 2 black) and quantity 2- ANL500KIT-500 Amp fuse kits for positive (red) cablesBattery Cables InstallationWhen connecting the AC inverter to the battery terminals, it is important to connect the "+" wire to the "+" terminal and the wire to the "-" wire to the “-“ terminal. Do NOT reverse the polarity. It will void the warranty. Make sure you connect negative to negative and positive to positive.Red (+) * 2Black (-) * 2REDBLACKCaution!DO NOT allow the wires to cross or touch each other. Install the cables facing away from each other and screw tightly. When connecting the battery cables to the terminals of the inverter, make sure they do not touch the case.3. GroundingThe power inverter has a lug on the rear panel marked "chassis ground" This is to connect the chassis of the power inverter to the ground.The ground terminals in the AC outlets on the front panel of the inverter are also connected to the ground lug.The chassis ground lug must be connected to a grounding point, which will vary depending on where the power inverter is installed. In a vehicle, connect the chassis ground to the chassis of the vehicle. In a boat, connect to the boat's grounding systems in a fixed location, connect the chassis ground lug to an earth point, which will vary depending on where the power inverter is installed.The neutral (common)conductor of the power inverter AC output circuit is connected to the chassis ground. Therefore, when the chassis is connected to ground, the neutral conductor will also be grounded.This conforms to national electrical code requirements that separately derived AC sources (such as inverters and generators) have their neutral tied to ground in the same way that the neutral conductor from the utility line is tied to ground at the AC breaker panel.Caution! The Negative DC input of the power inverter is connected to the chassis. DO not install the power inverter in a positive ground DC system. A positive ground DC system has the positive terminal of the battery connected to the chassis of the vehicle or to the grounding point.Warning! Do not operate the power inverter without connecting it to ground. Electrical shock hazard may result.OPERATIONTo operate the power inverter, turn it on using the ON/OFF switch on the front panel. The power inverter is now ready to deliver AC power to your loads. If you are operating several loads from the power inverter, turn on separately after the inverter has been turned on. This will ensure that the power inverter does not deliver starting currents to all of the loads at once.1. Controls and indicatorsThe ON/OFF switch turns the control circuit in the power inverter on and off. It does not disconnect power from the power inverter.When the switch is in the OFF position, the power inverter draws no current from battery. When the switch is in the ON position but with no load, the power inverter draws less than 450 mA.2. Battery voltage indicatorThe battery voltage bar graph indicates the voltage at the input terminals of the power inverter. At low input current, this voltage is very close to the battery voltage. At high input current, this voltage will be lower than the battery voltage because of the voltage drop across the cable and connections.Ideally, the voltage should remain in the green area of the bar graph. If the voltage goes into the red area at top or bottom of the graph, inverter may shut-down.3. Battery current indicatorThe battery current bar graph indicates the current drawn from the battery by the power inverter, it will not indicate current by other loads also connected to the battery. The indicator only displays DC volts and amps.For long term operation, the current should be in the green area of the bar graph. Short term operation is possible with current in the orange area. If the current rises to the red area, the inverter will reduce its output voltage to protect itself.To measure AC current, use a TRUE RMS MULTI METER.4. Over temp indicatorThe over temp indicator indicates that the power inverter has shut itself down because it has become overheated. The power inverter may overheat because it has been operated at power levels above its rating, or because it has been installed in a location which does not allow it to dissipate heat properly.5. Over load indicatorThe over load indicator indicates that the power inverter has shut itself down because its output circuit has been short circuited or drastically overloaded. Switch the ON/OFF to OFF, correct the fault condition, and then switch the ON/OFF back to ON.THINGS TO CONSIDER REGARDING THE LOADThe 10,000W inverter will operate most AC loads within its power rating. When determining whether a microwave oven can be operated by the 10,000W inverter, remember that the power commonly advertised for microwave ovens is the cooking power (the power delivered to the food) not the power actually consumed by the microwave oven. The microwave oven will consume 40% to 100% more than its advertised cooking power. Check the rating sticker on the back of the oven to determine its actual power draw. The 10,000W inverter will operate small microwave ovens (0.2 to 0.3 cubic foot capacity) that draw is about 1700 watts.Some induction motors used in refrigerators, freezers, pumps, and other motor operated equipment require very high surge currents to start. The power inverter may not be able to start some of these appliances even though their rated current draw is within the rating of the power inverter.If a motor refuses to start, observe the battery voltage indicator while trying to start the motor. If the battery voltage indicator drops below 10.5V DC while inverter is attempting to start the motor, this may be why the motor won't start.Make sure that the battery connections are good and that the battery is fully charged. If the connections are good and the battery to is charged, but the voltage still drops below 11 volts, you may need a larger battery or larger battery bank.(*2 for 24V *3 for 36V *4 for 48V)INPUT VOLTAGEThe power inverter will operate from input voltage ranging from 10V-16V. If the voltage drops below input range, an audible low battery warning will sound and the voltage indicator will be in the lower red zone. The power inverter will shut down if the input voltage drops below 10V +/- .5V. This protects your battery from being over discharged.The power inverter will also shut down if the input voltage exceeds 17V +\-.5V. This protects the inverter against excessive input voltage.The voltage indicator will be in the upper red zone. Although the power inverter incorporates protection against over voltage, the inverter is at risk of permanent damage if the input voltage is allowed to exceed 17V +\-.5V.TROUBLESHOOTINGmon problemsa. Buzz in audio systems:Some inexpensive stereo systems and radios will emit a buzzing noise from their loudspeakers when operated from the power inverter. This is because the power supply in the device does not adequately filter the modified sine wave produced by the power inverter. The only solution is to use a sound system that incorporates a higher quality power supply.b. Television interference:Operation of the power inverter can interfere with television reception on some channels. If this situation occurs, the following steps may help to alleviate the problem.-Make sure that the chassis ground lug on the back of the power inverter is solidly connected to the ground system of your vehicle, boat or home.-Do not operate high power loads with the power inverter while watching television.-Move the television as far away from the power inverter as possible.-Keep the cables between the battery and the power inverter as short as possible and twist them together with about 2 to 3 twists per foot. This minimizes radiated interference from the cables.SPECIFICATIONSAIMS Corp., Inc. dba AIMS Power Warranty Instructions:This product is designed using the most modern digital technology and under very strict quality control and testing guidelines. If, however you feel this product is not performing as it should, please contact us:**************************(775)359-6703We will do our best to resolve your concerns. If the product needs repair or replacement, make sure to keep your receipt/invoice, as that will need to be sent back along with the package and RMA# prepaid to AIMS. You have a full 1 year warranty from date of purchase.This warranty is valid worldwide with the exception that freight and duty charges incurred outside the contiguous 48 United States will be prepaid by customer.Except as provided above, AIMS Power makes no warranty of any kind, express or implied, including without limitation the implied warranties of merchantability and fitness for a particular purpose. In no event shall AIMS be liable for indirect, special or consequential damages. This warranty only applies to AIMS Power branded products. All other name brand products are warranted by and according to their respective manufacturer. Please do not attempt to return non-AIMS Power branded products to AIMS Power.For additional products such as:-Modified sine wave inverters-Pure sine wave inverters-Low Frequency Inverters-Solar Charge Controllers-Micro Grid Tied Inverters-Inverter Chargers and Automatic transfer switches-Converters DC-DC-Custom cut cables-Batteries-Solar Panels & RacksPlease visit our web site: Tofindoutwheretobuyanyofourproducts,youmayalsoe-mail:************************ (775)359-6703.。
艾茨顿91PS 8-10kW UPS技术规格说明书
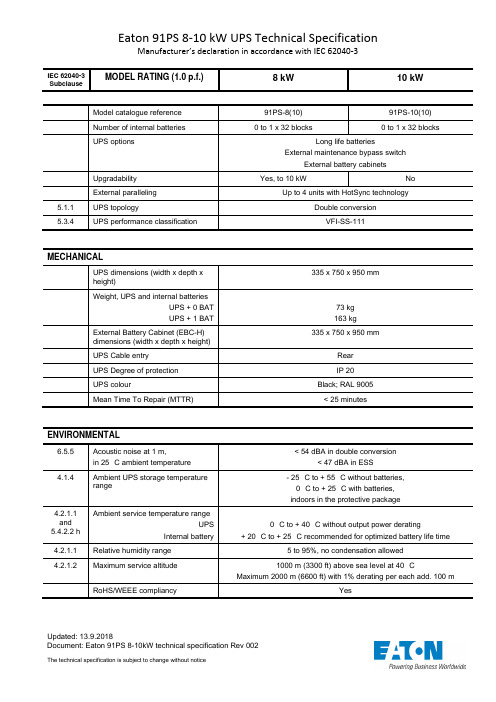
IEC 62040-3SubclauseMODEL RATING (1.0 p.f.)8 kW 10 kWModel catalogue reference 91PS-8(10) 91PS-10(10)Number of internal batteries 0 to 1 x 32 blocks 0 to 1 x 32 blocksUPS options Long life batteriesExternal maintenance bypass switchExternal battery cabinetsUpgradability Yes, to 10 kW NoExternal paralleling Up to 4 units with HotSync technology5.1.1 UPS topology Double conversion5.3.4 UPS performance classification VFI-SS-111MECHANICALUPS dimensions (width x depth xheight)335 x 750 x 950 mmWeight, UPS and internal batteriesUPS + 0 BAT UPS + 1 BAT73 kg 163 kgExternal Battery Cabinet (EBC-H)dimensions (width x depth x height)335 x 750 x 950 mm UPS Cable entry RearUPS Degree of protection IP 20UPS colour Black; RAL 9005Mean Time To Repair (MTTR) < 25 minutes ENVIRONMENTAL6.5.5 Acoustic noise at 1 m,in 25 °C ambient temperature < 54 dBA in double conversion < 47 dBA in ESS4.1.4 Ambient UPS storage temperaturerange - 25 °C to + 55 °C without batteries,0 °C to + 25 °C with batteries, indoors in the protective package4.2.1.1and 5.4.2.2 h Ambient service temperature rangeUPSInternal battery0 °C to + 40 °C without output power derating+ 20 °C to + 25 °C recommended for optimized battery life time4.2.1.1 Relative humidity range 5 to 95%, no condensation allowed4.2.1.2 Maximum service altitude 1000 m (3300 ft) above sea level at 40 °CMaximum 2000 m (6600 ft) with 1% derating per each add. 100 m RoHS/WEEE compliancy YesIEC 62040-3SubclauseMODEL RATING (1.0 p.f.)8 kW 10 kW EFFICIENCY5.3.2 r and6.4.1.6 Efficiency in double-conversion,rated linear load 100% load75% load50% load25% load95.6%95.5%95.0%92.5%95.5%95.6%95.3%93.4% Heat dissipation in doubleconversion 100% load75% load50% load25% load352 W270 W200 W150 W450 W330 W235 W165 W Efficiency in ESS, rated linear load100% load75% load50% load25% load98.2%98.0%97.3%95.0%98.2%98.1%97.7%96.4%ELECTRICAL CHARACTERISTICS INPUT5.2.1.a and 5.2.1 b Rated input voltage Rectifier inputVoltage toleranceBypass input1:1 220 V; 230 V; 240 V3:1 220/380 V; 230/400 V; 240/415 V187 to 276 Vrated voltage -15% / +10%5.2.1 c and 5.2.1 d Rated input frequencyFrequency tolerance50 or 60 Hz, user configurable40 to 72 Hz5.2.2 a and 5.2.2 b Number of input phasesRectifier inputBypass input1 phase + neutral, or 3 phases + neutral1 phase + neutral5.2.2 d Input power factor, doubleconversion 100% load75% load50% load25% load 1.000.990.980.921.000.990.980.965.2.2 c Rated input r.m.s. current 380V400V415V 13 A12 A12 A16 A15 A15 A5.2.2 f Maximum input r.m.s. current 15 A 19 A5.2.2 h and 5.2.2. i Input current distortion at rated inputcurrent Resistive loadNon-linear load< 5.0%< 6.5%< 4.0%< 5.5%IEC 62040-3SubclauseMODEL RATING (1.0 p.f.)8 kW 10 kW5.2.2 e In-rush current < Rated input current (input filter components only) 5.2.2 k AC power distribution systemcompatibilityTN, TT, IT (4-wire)Rectifier ramp-up, rectifier start and load step 4 A/s (default), configurable.Minimum 1 A/s.Back feed protection Yes, for rectifier and bypass linesELECTRICAL CHARACTERISTICSOUTPUT5.3.2 f Number of output phases 1 phase + neutralCrest factor 35.3.2 b Rated output voltage 220 V; 230 V; 240 V, configurable 5.3.2 b Output voltage variation, steadystate< 1%5.3.2 i Total voltage harmonic distortion100% linear load 100% non-linear load 1.5%2.0%5.3.2 q Voltage unbalance at referenceunbalanced loadN/A5.3.2 j Voltage transient (r.m.s) at 100%step loadRecovery time to steady state at100% step load4% 100 ms5.3.2 c Rated output frequencyOutput frequency variationSlew rate 50 or 60 Hz, configurable± 0.1 Hz0.8 - 1 Hz/s5.3.2 d and 5.3.2 e Maximum frequency range forsynchronization with bypassMaximum synchronized phase errorMaximum slew-rate whensynchronizing± 4 Hz as default. User settable 0.5 to 5 Hz.< 2° with static balanced load1 Hz/s5.3.2 k Rated output power 8 kW / 8 kVA 10 kW / 10 kVA5.3.2 l Overload capabilityOn inverter 10 min 102-110% load 60 sec 111-125% load 10 sec 126-150% load 300 ms >150% loadOverload capabilityOn inverter, stored energy mode 10 min 102-110% load 60 sec 111-125% load 10 sec 126-150% load 300 ms >150% loadIEC 62040-3SubclauseMODEL RATING (1.0 p.f.)8 kW 10 kWOverload capabilityESS mode Continuous < 110% load20 ms 1000% loadOverload capabilityOn bypass Continuous < 125% load20 ms 1000% load5.3.2 m Output current limitation, short-circuit capability109 A, 300 ms6.4.2.10.3and6.4.2.10.4Fault clearing capability Circuit breaker B20 / C105.3.2 o and 5.3.2 p Load power factor RatedPermitted range1.00.8 lagging to 0.8 leadingESS MODE CHARACTERISTICSTransfer time to double-conversionMains available Mains failureNo break Typically 2 msOutput voltage variation setting ± 10% of nominal voltage, defaultOutput frequency variation setting ± 4 Hz, defaultStorm detection UPS locks into double-conversion mode when three power linedisturbances have forced the unit to double-conversion three times (useradjustable) within a one-hour period (user adjustable).High Alert mode UPS will stay on double-conversion for one hour (user adjustable), afterwhich the unit will automatically return to operate on ESS.BYPASSType of bypass StaticBypass rating 10 kWBypass voltage range 220 V; 230 V; 240 Vtolerance -15% / +10% of rated voltage Transfer time break No breakMaintenance bypass Internal as standardBypass fuse i2t value,Pre-arc i2t Total clearing i2t2592 A2s 15480 A2s (at 240 V)Required external bypass protectivefuse, recommended rating63 A gGRated conditional short-circuitcurrent, I cc50 kA (with recommended protective fusing)IEC 62040-3SubclauseMODEL RATING (1.0 p.f.)8 kW 10 kWBATTERY CHARACTERISTICS5.4.2.2 d Battery technology 12 V, VRLA5.4.2.2 a Battery design life 5 or 10 years5.4.2.2 b Battery quantity InternalExternal 32 blocks, 192 cells per battery string28-40 blocks per string5.4.2.2 c Battery voltage InternalExternal384 V 336 V – 480 V5.4.2.2 e Nominal Ah capacity (C10) 9 Ah5.4.2.2 f Stored energy time See separate declaration5.4.2.2 o Recharge profile ABM or float5.4.2.2 q End of discharge voltage 1.67 VPC to 1.75 VPCConfigurable or automatic (load adaptive)5.4.2.2 r Charge current limit DefaultLoad ≤80%Load >80% 5 A, configurable1…12.5 A1…3.5 ABattery start option YesCOMMUNICATION CIRCUITS5.6 Standard connectivity ports Mini-slot ports for optional cards, Device USB and Host USB, RS-232service port, relay output, 5 building alarm inputs and a dedicated EPO,Web and SNMP cardComplete list of indications andinterface devicesSee User’s and Installation Guide COMPLIANCE WITH STANDARDSIEC 62040-1 Safety AccessDegree of protectionRestricted accessIP 20;protection against medium sized foreign matter (incl. finger),no protection against vertically dripping water.IEC 62040-2 Electromagnetic CompatibilityImmunityEmissionsEMC Category C3EMC Category C3 for 1-phase input, orEMC Category C2 for 3-phase input modelIEC62040-4 Environmental Aspects -Requirements and Reporting YesEN 50581。
Hybrid 10KW Service 说明书
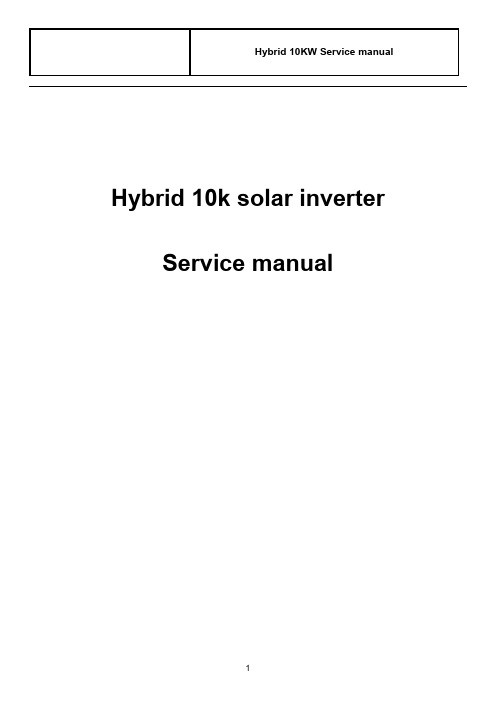
Hybrid 10k solar inverter Service manualTable of contents1.General information (3)1.1Getting start (3)1.2Important safety instructions (3)2.Introduction of the inverter (4)2.1Basic information (4)2.2Functional topology (4)2.3Main board (5)2.4DC-DC board (6)2.5SPS board (7)2.6PV EMI board (7)2.7CNTL board (7)2.8Relay board (8)2.9Grid board (8)2.10OP board (8)3.Trouble shooting (9)3.1Check the fault information (9)3.2Check the PCBs (17)4.Appendix (35)4.1PCBs replacement guideline (35)4.2Signal cables connection guideline (44)1. General information1.1 Getting startThis manual is for Hybrid 10k, it can help service personal perform the basic maintenance and repair service. This manual focus on the service, so you should get the basic operation of the inverter from the user manual, and make sure you had read and understood user manual before you use this service manual.The manual include 4 sections, as follows•General Information, this section showed the general information of the service manual.•Introduction of the inverter and each PCB, this section shows you all the PCBs of the Hybrid 10k. •Trouble shooting, this section will give you the way to find the trouble•Appendix, this section showed the information of the critical parts, and how to replace the boards of the inverter.1.2 Important safety instructionsWARNING: This chapter contains important safety and operating instructions.1. Before repair the unit, please read this manual carefully.2. To reduce risk of electric shock, disconnect all wirings before attempting any maintenance. Only turningoff the unit will not reduce this risk.3. Be very cautious when working with metal tools on or around batteries. A potential risk exists to drop atool to spark or short circuit batteries or other electrical parts and could cause an explosion.4. Warning!! Only qualified service persons are able to service this device.2. Introduction of the inverter2.1 Basic informationThis chapter will introduce the topology and each board of the inverter; it will give us the basic impression of the inverter.2.2 Functional topologyThe topology of the inverter shows as below:GRIDThere are four factors of the inverter: PV, battery, grid and load. PV and load is the single direction, PV only uses for input, and load for output. Batter and grid is the bi-direction, cause the battery can be charged and also can discharge, grid can be input and output. With these factors, we can make several combinations to meet every application, maximum the availability of the power system.2.3 Main boardThe main board contains the Boost1, Boost2 and INV/REC module. Boost module takes in charge of MPPT from solar. It transfers the energy from the solar to the BUS. INV/REC module, just as its name implies, it can invert the energy from the BUS to grid or load; also it can convert the energy from the grid to the BUS.The figure shows as below, and relevant modules are marked in red box.BOOST2BOOST1INV/RECThe topology of the main board:2.4 DC-DC boardDC-DC board only contains DC-DC module, the energy flows through this module between BUS and battery. When the battery discharges, the energy flows from battery to BUS. When the battery is being charged, the energy flows from BUS to battery. On the board, there are two symmetrical DC-DC module, each one supports 5KW.The figure shows as below, and relevant modules are marked in red box.The topology of the DC-DC board:DC-DC1 DC-DC2BUCK-BOOST1BUCK-BOOST22.5 SPS boardSPS is the acronym of the switching power supply; it contains PV SPS, grid SPS and battery SPS which means that the inverter can be poweredon by either of them.The figure shows as below, and relevant modules are marked in red box.2.6 PV EMI boardPV EMI board provides the EMI solution at the PV side; moreover it integrates the PV ISO detection and GFCI module. GFCI is used for detecting the leakage current from solar to grid, it’s required by IEC 62109-2. The figure shows as below, and relevant modules are marked in red box.2.7 CNTL boardControl board provides the digital control of the inverter.It takes the signals from the kinds of sensors, andprocesses them in CPU, and then issues thecommands to each module of the whole inverter.There are two CPU on the board, one is the master andthe other is slave. Actually it doesn’t mean that theslave must follow the master, it’s just the differen tdivision of the task. The master CPU takes in charge ofthe main control of the power module like DC-DC andREC/INV, and the slave CPU takes in charge of thecontrol of Boost, display and communication. They bothdetect some important signals, and the relevantcommand needs the permission of both.The figure shows as below, and relevant modules are marked in red.Relay board uses as a NS protection which is required by the VDE-AR-N 4105.2.9 Grid boardIP board includes the input relay and EMI solution at grid input.OP board includes the output relay and EMI solution at load side.3. Trouble shootingThis section describes how to find the trouble when the system is abnormal. We suggest you can follow the service procedure:a. Check the system status by LCD display.b. Observe the failure board, static checking.c. Replace the failure board.e. Power up checking.f. Test after repair.Following these sections will help service person to solve most of problem.3.1 Check the fault informationPlease follow the steps as below to find the issues!Make sure that you can finish all the steps and feedback us the results. Or we may not be able to give you the right solution.Step 1: Test the bypass mode.Before turning on the inverter, only connect the utility with the inverter. Without press any buttons, the LCD will light up. Press the “ON” button for at least 3 seconds, and wait for the utility connecting to load.If the connection is failed, please record the fault code.Step 2: Test the battery working mode.Before turning on the inverter, only connect the battery with the inverter which means no solar input and grid input. Press the “ON” button for at least 3 seconds, the LCD will light up and wait for the battery connecting to load.If the connection is failed, please record the fault code.Step 3: Test the on-grid mode.Before turning on the inverter, only connect the utility and solar with the inverter. Without press any buttons, the LCD will light up. And wait for the utility connecting to solar.If the connection is failed, please record the fault code.Step 4: Test the solar charging mode.Before turning on the inverter, only connect the solar and battery with the inverter. Without press any buttons, the LCD will light up. And wait for the solar connecting to battery.If the connection is failed, please record the fault code.Note: The numbers with means fault code; with means warning code. Please clarify them.Error 01Error 01 means BUS voltage is overt the limitation. Please disconnect the load, and restart the inverter to have a check.If the inverter can work normally after the restarting, error 01 is usually caused by the surge from the utility input or the energy feedback from the load.If the error persists, please check:If the error 01 happens immediately when the LCD is on, usually this is the control board problem, you can change the control board to have a check.If the error 01 happens when the output is available or charging, the possible cause is the DC-DC or main board, please contact with us to do the diagnose together.Error 02Error 02 means BUS voltage is under the limitation. Please disconnect the load, and restart the inverter to have a check.If the inverter can work normally after the restarting, error 02 is usually caused by the solar or load fluctuation.If the error persists, the possible cause is the DC-DC board or control board.Error 03Error 03 means BUS soft start is failed.Before the inverter turns on the output or starts charging, the SPS board will charge the BUS capacitors to 700~800V, and then the DC-DC board will be activated, to keep the BUS voltage at 700~800V. If everything is OK, then the inverter will turn on the inverting module. If the voltage couldn’t reach 700~800V or stay at this level, the error 03 will come out.Error 03 is related to the main board, DC-DC board, SPS board and control board.If you have the multimeter, it will help you to find out which board causes the error 03.First, please find the BUS+, neutral and BUS- on the main board or DC-DC board, and follow the table as below to do the measurement.If the reading is right, and still error 03, it’s usually the control board problem; you can change it and check again.If the reading is not right, it means that the issue is among the main board, DC-DC board and SPS board. First, you can unplug this cable on the SPS board,And then measure the diode voltage on the terminal CN7 of the SPS board by following table 3.1.If the value is right, it means SPS boardis good. You can check the main andDC-DC board.Please replace the boards that withwrong values, error 03 will be solved.Error 04Error 04 means inverting soft start is failed.After bus soft start is finished, and DC-DC board is turned on. The controller will turn on the inverting module, it will output the voltage from 0V to 230V (phase to neutral). If the voltage couldn’t reach 230V after a time, the inverter will give error 04.Error 04 is related to the main board, and control board.Please replace the control board and main board both, it will solve error 04.Error 05Error 05 means inverting current is overt the limitation. Please disconnect the load, and restart the inverter to have a check.If the inverter can work normally after the restarting, error 05 is usually caused by the surge from the utility input or the energy feedback from the load.If the error persists, please check:If the error 05 happens immediately when the LCD is on, the problem is related with SPS board, control board, HCT board and parallel board.If the error 05 happens when the output is available or charging, the problem is related with the main board, please replace it to have a check.Error 06Error 06 means over temperature. Please disconnect the load, and restart the inverter to have a check.If the error still persists even the inverter has cooled down, it means the temperature sensors are wrong.We have the sensors on main board and DC-DC board. Please contact with us, we will provide a special firmware for you to diagnose which sensor is wrong.Error 07Error 07 means relay checking fail. This error is usually caused by the rusting on the board which it is due to the dust and moisture.This error is related to the grid board, HCT board, and relay board. Please change these boards, this error will be solved.Error 08Error 08 means DC current sensors are wrong. We have DC current sensors on main and DC-DC boards.You can contact with us for the special firmware, it will help to identify which sensor is wrong. Or you can follow as below to check which sensor is wrong.Please find the terminals as below on the control board:Unplug them, and put the jumper (Or use something to short them) on the terminal like as below:Please turn on the inverter, and check if error 08 is solved. If thereis no error 08, it means that the sensors on the DC-DC board arewrong, you can change the DC-DC board to solve this error.Or the sensors on the main board are wrong, you can change themain board to solve this error.If the error still persists after replacing the main board, pleasechange the parallel card.Error 09Error 09 means solar input power is not normal. Please restart the inverter to check.This error is very rare to see, if you face this error, please contact with us.Error 11Error 11 means solar input is over current. This error is very rare to see, if you face this error, please contact with us.Error 12Error 12 means leakage current is over the limitation.For our inverter is the transformerless type, it means there is no galvanic isolation between the solar and grid.The loop of the leakage current will be like as below:Generally the photovoltaic cells are isolated with the ground, but sometimes, it may have the isolation problem, like the cable is broken or sinking in the water, the glass of the panels has something wrong. These factors may cause leakage current from solar panels to ground.By following the safety standard, the inverter needs to cut off the utility input if the current is over the limitation.Please check the installation of the solar panels to solve this error.If the error persists without solar panels connected, the senor of the leakage current is failed; you can change the PV EMI board to solve it.Error 13Error 13 means the isolated resistance of the solar panels is too low. If the error persists after you choose “Grid tie with backup” or “Off-grid mode”, please contact with us.Error 14Error 14 means the DC component of the output current is over the limitation when the grid is connected in.This error only happens when the grid is connected in.If the error persists when you restart the inverter, the error is related to the main board or HCT board. You can change these boards to have a check.Error 16Error 16 means the self-checking of the leakage current sensor is failed. Please replace the PV EMI board to solve the issue.Error 22Error 22 means the battery voltage is too high. Please check the real voltage and the voltage showed in the LCD display.If the voltage is higher than 60V, this error will happen.Error 23Error 23 means the overload is activated.Please check if some loads are too heavy for the inverter. Like air conditioner, pump and motors, this kind of loads demand large inrush current when they start up. The recommended rating of these loads is less than 1/3 rating of the inverter.Error 26Error 26 means the output is shorted. It is usually caused by the load output connection is shorted.Please check if the wire connection of the load is shorted, or the load is shorted by itself.Error 27Error 27 means the fans are blocked. When this error happens, please check if there is any fan stop working.Usually this error is caused by fans stop working. In few cases, it is caused by SPS board.Error 32Error 32 means the DC component of the output voltage is over the limitation. This error only happens when the inverter is in battery mode.Some loads like drier, they are half waveform consumer, and they will create the DC component on the voltage.The recommended rating of these loads is less than 1/2 rating of the inverter.Error 33Error 33 means the output voltage is lower than limitation. This error is similar with error 23.Error 34Error 34 means the output voltage is too high. This error is similar with error 04.Error 35Error 35 means the wire connection is not well. Please check the cables if they aretighten connected on the control board and the other boards connected withcontrol board.The cable shown in the figure will cause error 35.Error 36This error has been canceled, if you have this error, please contact with us.Error 37Error 37 means the current is over limitation on the input neutral.If the error persists without any loads, please replace the relay board.Error 60Error 60 means the power is not balance between each inverter which is working in parallel with each other.Please disconnect the grid input, and check if the load percentage is the same in the LCD display of each inverter.This error is usually caused by the parallel board.Error 61 and 62Error 61 and 62 means relay board is failed, please change it to check.Error 72Error 72 means the current sharing control is failed.This error is related with parallel board, sometimes control board also.When do parallel installation, please make sure that the output neutral of each inverter should be connected always, or it may cause error 72.Error 80, 81 and 82Error 80~82 means parallel CAN communication is lost. Please change the parallel board.3.2 Check the PCBsIn most situations, we need to take the PCBs out of the inverter and do some static measurement, then we can realize which part is damaged, and replace the relevant boards or components.Most fault conditions are due to the damaged of the power board, including main board, DC-DC board, and sometimes SPS board.3.2.1. Main board checkingStep1: Check the BOOST moduleBOOST1:Q3/Q4/Q5/D4/D6/D31BOOST2:Q11/Q12/Q13/A12/D13/D40All of the IGBTs are 11-330086-00G( IGBT FC/FGH40T120SMD 40A 1200V NPT BULK TO-247) All of the Diode are 11-200039-00G(D FAIRCHILD/RHRG75120 75A 1200V SFST RAD BULK)Step2: Check the INV/REC moduleR-phase INV/REC:IGBT1/IGBT2/IGBT3/IGBT4/D5/D11/D16/D17 S-phase INV/REC: IGBT5/IGBT6/IGBT7/IGBT8/D21/D25/D26/D273.2.2. DC-DC board checkingStep1: Check the battery side of the DC-DC system:C13/C14/C15/C16/C17/C91/C92/C94/C95/C97: 15-000072-00G (C-AL 3300UF 63V M RAD BULK 7.5 105℃18*45.5)DC-DC1 MOSFET: Q1/Q2/Q3/Q4 /Q5& Q6/Q7/Q8/Q9/Q10 & Q11/Q12/Q13/Q14/Q15 & Q16/Q17/Q18/Q19/Q20DC-DC2 MOSFET:Q49/Q50/Q51/Q52/Q53/Q54/Q55/Q56/Q57/Q58/Q59/Q60/Q61/Q62/Q63/Q64/Q65/Q66/Q67/Q68ALL of the mosfets are 11-320117-00G (MOSFET IR/IRFB3077 210A 75V N BULK TO-220)Note1: When you use the multimeter to measure the resistor of the transistor, because of the capacitor in the circuit, it will cause the changing of the values when you measure the DS and GD. So we recommend you measure the diode forward voltage of SD, and the resistor of GS. These two values can reflect the situation of the transistor more correctly.Step 2: Check the bus side of the DC-DC system:DC/DC1 IGBT: Q23/Q24/Q27/Q28DC/DC2 IGBT: Q69/Q70/Q74/Q75ALL of the IGBTs are 11-330087-00G (IGBT IR/IRGP4266DPBF 90A 650V N BULK TO-247)Step 3: Check the buck-boost circuit: BUCK-BOOST1 IGBTs: Q21/Q22/Q25/Q26BUCK-BOOST2 IGBTs:Q71/Q72/Q73/Q763.2.3. SPS board checkingStep 1: Check the bus soft start circuit:D66/D67: 11-200023-00G (D FC/RHRP8120 8A 1200V UFST RAD BULK) Q10: 11-320020-00G (MOSFET IR/IRF630N 9.3A 200V N BULK TO-220) R251: 14-600008-00G (RES 不燃性树脂型绕线3W 0.1 J N-IND)Note: If R251 is damaged, please replace U16 together.U16: 11-1040160G (IC PWM CNTL ON/UC3845BD1R2G 8/SOIC-8)replace the TX2 also.TX2: 41-070250-00G (TX 120:13:120 FER ER28/28)Step 2: Check the battery switching power supply circuit:D31/D38: 11-200077-00G (D PANJIT/SB10100 10A 100V SCKY RAD TO-220AC TAP) D24: 11-200056-00G (D ST/STPS30L60CT 30A 60V SCKY RAD TO-220 BULK) D27: 11-200015-00G (D PANJIT/SB10150 10A 150V SCKY RAD BULK)Q6: 11-320081-00G (MOSFET FAIRCHILD/FDA59N30 35A 300V N BULK TO-247) R70/R71/R105: 14-600017-00G(RES 不燃性树脂型绕线 3W 0.15 J N-IND) F2: 25-000061-00G (FUSE HOLLY LAND/20N-100L 10A 125V FAST7.3*2.7) Note: If R70/R71/R105 is damaged, please replace U7 together. U7: 11-104016-00G (IC PWM CNTL ON/UC3845BD1R2G 8/SOIC-8)Step 3: Check the AC switching power supply circuit:D10: X11-200001-01G (ASSY D RHRP860 8A 600V SFST RAD BULK) D16: 11-200011-00G (D PAJ/UF204 2A 400V UFST TAP)D5/D41: 11-200023-00G (D FC/RHRP8120 8A 1200V UFST RAD BULK)Q14/Q18: 11-320091-00G (MOSFET ST/STW6N120K3 6A 1200V N BULK TO-247) R111/R112/R141: 14-600010-00G (RES 不燃性树脂型绕线 2W 1 J N-IND) REC1/REC2:11-200068-00G (D PAJ/GBU4M 4A 1000V UFST RAD BULK) Note: If R111/R112/R141 is damaged, please replace U19 together. U19: 11-104002-00G (IC PWM CNTL TI/UC2844D8 SMD)Step 4: Check the PV switching power supply circuit:D1: X11-200001-01G (ASSY D RHRP860 8A 600V SFST RAD BULK) D9: 11-200011-00G (D PAJ/UF204 2A 400V UFST TAP)D3/D34: 11-200023-00G (D FC/RHRP8120 8A 1200V UFST RAD BULK)Q7/Q8: 11-320091-00G (MOSFET ST/STW6N120K3 6A 1200V N BULK TO-247) R24/R27/R72: 14-600010-00G (RES 不燃性树脂型绕线 2W 1 J N-IND) Note: If R24/R27/R72 is damaged, please replace U8 together. U8: 11-104002-00G (IC PWM CNTL TI/UC2844D8 SMD)After checking, please provide the information to the supplier or local service.4. Appendix4.1 PCBs replacement guideline4.2.1. Open the top cover and bottom cover Open the top cover by remove the screws as below:Open the bottom cover by remove the screws as below:4.2.2. How to replace the main boardWARNING! The screws marked in YELLOW should be screwed tightly. Or when inverter works, it will cause the electrical hazard.WARNING! The connector marked in YELLOW should be connected tightly. Or when inverter works, it will cause the electrical hazard.4.2.3. How to replace the DC-DC boardWARNING! The screws marked in YELLOW should be screwed tightly. Or when inverter works, it will cause the electrical hazard.4.2.4. How to replace the SPS boardWARNING! The connector marked in YELLOW should be connected tightly. Or when inverter works, it will cause the electrical hazard.4.2.5. How to replace the control board4.2.6. How to replace the PV EMI board4.2.7. How to replace the relay board4.2.8. How to replace the OP board4.2.9. How to replace the IP board4.2.10. How to replace the fans4.2 Signal cables connection guideline Single unit:Parallel unit:。
Eaton 9SX UPS 11 kVA 10 kW 产品说明说明书
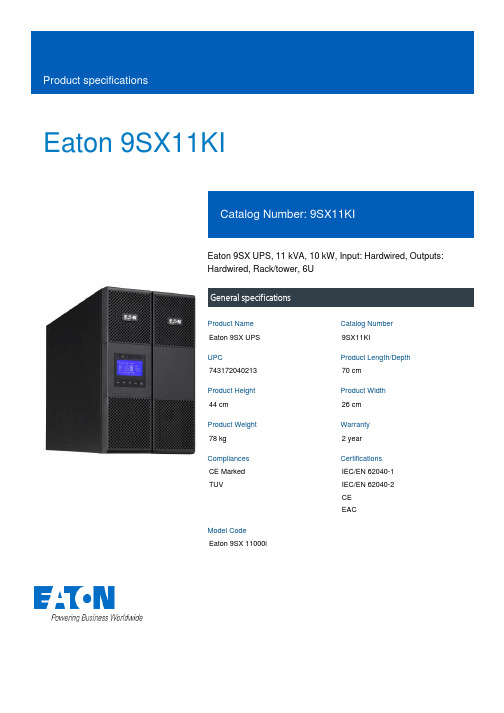
Eaton 9SX11KIEaton 9SX UPS, 11 kVA, 10 kW, Input: Hardwired, Outputs: Hardwired, Rack/tower, 6UGeneral specificationsEaton 9SX UPS 9SX11KI74317204021370 cm 44 cm 26 cm 78 kg 2 year CE Marked TUVIEC/EN 62040-1 IEC/EN 62040-2 CE EACEaton 9SX 11000iProduct Name Catalog Number UPCProduct Length/Depth Product Height Product Width Product Weight Warranty Compliances Certifications Model CodeSealed, lead-acidView runtime graphHot-swappable battery modules 2012 V / 7 AhYes Hardwired230V10 kW0.9200/208/220/230/240/250 V +/- 1%Sine wave230V default (200/208/220/230/240/250V) 21Online/Double-conversion11 kVAHardwired/fixed connection230V default (200/208/220/230/240/250V) 50/60 Hz>.99176-276 V (100-276 V with derating)NoBattery typeRuntime graphBattery replacement Battery quantityBattery managementBattery ratingExtended battery capability ReceptacleVoltageWattageOutput power factorOutput voltage rangeOutput waveformOutput nominal voltageVoltage distortion output (linear load) - max Feed typeTopologyVA ratingInput connection Input nominal voltage Nominal frequency Input power factor Input voltage range Includes network card CommunicationABM & Temperaturecompensated chargingmethod (user selectable)Automatic battery testDeep discharge protectionAutomatic recognition ofexternal battery unitsUSB port (HID compliant)Serial port (RS232)Mini terminal block forremote On/OffMini-terminal block forremote power offDry contacts (4 outputs,relay, DB9)40-70 HzNoMultilingual graphical LCD display YesOne slot for optional communication card Eaton Intelligent Power Manager, Eaton Intelligent Power Protector Other3000 m <50 dB at 1 meter 0° to 40°C (32° to 104°F)0-95% non-condensingFree standing model 1YesYes BlackInput frequency range Ethernet interface User interfacePotential free switch contact Expansion slotsSoftware compatibilityType of interface Altitude Noise level Temperature range Relative humidity Construction type Package contents Phase (output)Internal bypass Auto shutdown function Color Power ModuleExtended battery module (EBM)USB cable Serial cableBattery cable with comms for automatic battery cabinet recognition(2) Supports for tower mounting Link plate Safety instructions Quickstart guideEaton Corporation plc Eaton House30 Pembroke Road Dublin 4, Ireland © 2023 Eaton. All rights reserved. Eaton is a registered trademark.All other trademarks areproperty of their respective owners./socialmedia95No1NoEaton UPS and battery services Eaton UPS Services Quick Guide 2021Eaton 9SX-9PX UPS - 8-11 kVA-EBM 240V - Installation and user manualEaton 9SX UPS - 5/6/8/11 kVA - DatasheetEfficiency Rack mounting kit Phase (input)Hot swap power BrochuresManuals and user guidesTechnical data sheets。
艾顿DX-RT 10kVA 10kW 1x1(EBM型号)UPS产品说明说明书
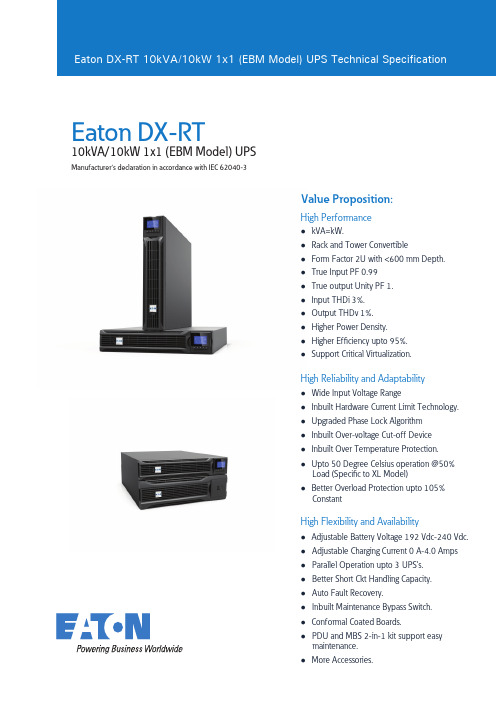
Eaton DX-RT10kVA/10kW 1x1 (EBM Model) UPSManufacturer’s declaration in accordance with IEC 62040-3Value Proposition:High Flexibility and Availability● Adjustable Battery Voltage 192 Vdc-240 Vdc. ● Adjustable Charging Current 0 A-4.0 Amps ● Parallel Operation upto 3 UPS’s. ● Better Short Ckt Handling Capacity.● Auto Fault Recovery.● Inbuilt Maintenance Bypass Switch.● Conformal Coated Boards.● PDU and MBS 2-in-1 kit support easy maintenance.● More Accessories.High Reliability and Adaptability● Wide Input Voltage Range● Inbuilt Hardware Current Limit Technology.● Upgraded Phase Lock Algorithm ● Inbuilt Over-voltage Cut-off Device ● Inbuilt Over Temperature Protection.● Upto 50 Degree Celsius operation @50% Load (Specific to XL Model)● Better Overload Protection upto 105% ConstantHigh Performance● kVA=kW.● Rack and Tower Convertible● Form Factor 2U with <600 mm Depth.● True Input PF 0.99● True output Unity PF 1.● Input THDi 3%.● Output THDv 1%.● Higher Power Density.● Higher Efficiency upto 95%.● Support Critical Virtualization.Model NameCatalog NamePlant Part NumberUPC CodeINPUT-Acceptable Input Voltage-Phase-Input voltage range to take 50% load -Input voltage range to take 100% load -Inrush Current Limit-Input Power Factor-Input Frequency Range-Input protection-Generator SetOUTPUT-Power(VA) max-Power(W) max-Power Factor-Waveform-Nominal voltage-Voltage Variation-Voltage distortionOutput Frequency-Synchronization range-Slew rate- Battery modeTransfer Time-Inverter Mode <--> Battery Mode-Batttery Mode <--> Inverter Mode-Inverter Mode --> bypass ModeFull Load Efficiency-Line mode with battery full charged -ECO modeDXRT10K-INDXRT10K-IN9104-32686XT1743172091697110VAC-275VACSingle phase with ground110VAC~275VAC160VAC~275VAC8*Irms≥0.99545-55Hz / 54-66Hz (extendable to 40~70HZ when load < 60%)upstream breaker1.5 x UPS Rating Power10000100001.0Pure sine wave208V/220V/230V/240V± 1 %< 1% THD@ linear load<5% @non-linear load45-55Hz / 54-66Hz (extendable to 40~70HZ when load < 60%)1 Hz/s(50/60±0.1) Hz0ms0ms0ms95% @ 230V output with typical load≥98%BATTERY-Inner Battery Rating/Type -External battery connection -Back-up Time (50% load) -Back-up Time (70% load) -Back-up Time (full load) -DC Voltage -Battery-Low Voltage-Battery Shutdown Voltage -Leakage current -Battery fuse current Charger-Charger current-Floating Voltage Phase -Charging time Features -ECO Mode-Battery Capacity Calculation -Fan Speed Control-Frequency Converter Mode(CVCF) -Maintenance Bypass Switch -ParallelOverload Capability -Line mode-Battery mode-Bypass ModeINDICATOR & ALARM -Display-Battery mode -Battery low -Overload -Fault INTERFACE -RS232 -USB-EPO Function -Comm slot box -Comm card-Dry Contact (Dry in/Dry out) -Input connection -Outlet socket100% Load 105%: Constant105% Load 125%: 10 minutes125% Load 150%: 30s>150% :500ms100% Load 105%: Constant 105% Load 125%: 1 minutes 125% Load 150%: 30s>150% :500ms105% Load 125%: Constant 125% Load 150%: 30s Load>150%: 500ms 12V/9AH*16 (16/17/18/19/20 adjustable)Connector 8 minutes typical 5 minutes typical 2.1 minutes typical192VDC (192V~240V adjustable)11.4V/pc @ 0 25% Load 10.5V/pc @ 25% Load 10.5V/pc @ 0 25% Load 9.6V/pc @ > 25% Load<300uA 100A default 2A (0~4A adjustable)13.65V/pc3 hours to 90% with internal batteryYES YES YESYES, 60% load factory optional optional (up to 3 units)Multi-language LCD + status LEDBeeps every four second Sounding every second Sounding twice every secondContinuous beepingYESYESYES YES Optional(NMC/Moudbus/Dry Contact)YES TB TBAmericas Region 1000 Eaton BoulevardCleveland, Ohio 44122, USA India Head OfficeEaton Power Quality Pvt. Ltd.2, EVR Street, Sedarpet Industrial Estate Pondicherry-605111Tel: +91 413 2672000180****5758Offices Across India DELHIUnit A1 & B1, 3rd Floor, TDI Centre Plot No. 7, Jasola, New Delhi-110025Tel: +91 11 45851800MUMBAIEL Floor, VITS Luxury, Business Hotel Andheri Kurla Road, Andheri (East)Mumbai-400059Tel: +91 22 40053817, Fax: +91 22 40053810CHENNAINo. 36, Nehru StreetOff. Old Mahabalipuram Road Sholinganallur, Chennai-600119Tel: +91 44 2532 0249BANGALOREUnit No. 501, 4th Floor, Prestige Atrium Central Street, Bangalore-560001Tel: +91 80 49012200, Fax: +91 80 49012239HYDERABADGround & First Floor, 8-3-1110/B/2Plot No. 104, Keshav Nagar ColonySrinagar Colony Post, Hyderabad-500073Tel: +91 40 40189601KOLKATARoom No. 203, 2nd FloorMatrix Tower, DN 24, Sector-V Salt Lake City, Kolkata-700091Tel: +91 33 40040991/92/93www.eaton.in | www.powerquality.eaton.inSALES AND SERVICE TOLL FREE HOTLINE:。
10.2KWH Power Wall Lithium-ion Battery用户操作指南说明书
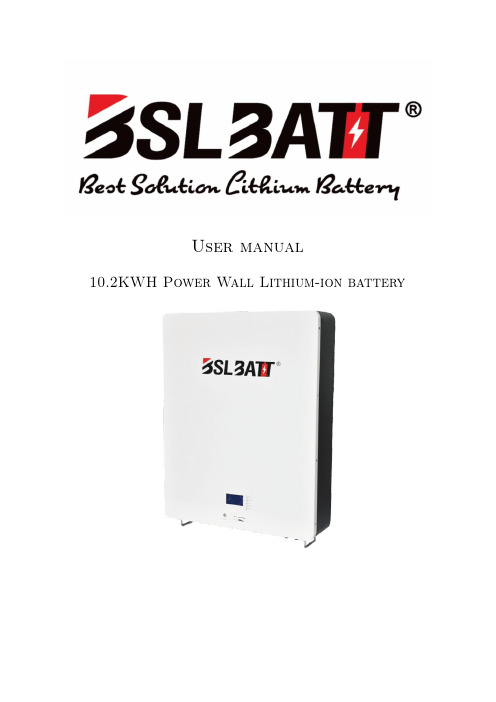
User manual10.2KWH Power Wall Lithium-ion batterySAFETY GUIDELINESWork or maintenance on the BSL battery should be carried out byqualified personnel only.Do not attempt to open or dismantle battery and/or cells.The electrolyte contained in the battery cells is highly corrosive.In the event of any damage to or leakage from the cells,treat contents with care, do not allow contact with exposed skin or eyes.DO NOT INGEST.The terminals of the BSL battery should always be considered live, therefore do not place tools or any other items across the terminals.Do not pierce,short or damage the terminals in any way.Do not touch theterminals of the battery.Fire Hazard:Do not discharge battery below specified minimum level as this poses an increased fire risk.Do not attempt to charge a swollen or damaged battery.In the event of fire,a CO2or Dry Powder extinguisher should be used.Class D extinguishers are not suitable.Dispose of batteries through the proper local regulations.Not suitable forregular refuse/recycling.Contents1Pin out diagram1 2Battery set-up32.1General (3)2.1.1Turning battery on and off (3)2.1.2CAN communication (3)2.1.3Smart shunt (3)2.1.4Dry contacts (3)2.1.5Other ports (3)2.2Multiple batteries (4)2.2.1Max number of parallel batteries (4)2.2.2Installing multiple batteries (4)2.2.3Cable sizing with multiple batteries (4)2.2.4Dip switch settings for multiple batteries (4)3Inverter set-up53.1Batteries per inverter size (5)3.2Battery set-up on Victron GX device (5)4Inverter settings(Victron)64.1General Tab (6)4.2Grid Tab (6)4.3Inverter Tab (7)4.4Charger Tab (7)4.5Assistant tab(a) (8)4.6Assistant tab(b) (8)4.7Assistant tab(c) (9)4.8Assistant tab(d) (9)4.9Assistant tab(e) (10)4.10Assistant tab(f) (10)4.11Assistant tab(g) (11)4.12Assistant tab(h) (11)5Other specifications12 List of Figures1Pin-out diagram for10.2kWh BSL battery (1)2Pin-out diagram for10.2kWh BSL battery (2)1Pin out diagramFigure1:Pin-out diagram for10.2kWh BSL battery.A-Reset switch(BMS Power button)B-Dip switches for parallel connectionC-Dry Contacts(mostly unused)D-RS485Left port(Port1)E-CAN Port(Port2)F-RS232Port(Unused)G-RS485Right Ports(Ports4&5)H-Circuit breaker(terminal power)I-Positive terminalJ-Negative terminalK-Carry handlesFigure2:Pin-out diagram for10.2kWh BSL battery.A-Power lightB-Run lightC-Alarm lightD-SOC indicator lightsE-Screen for displayF-Push buttons to change settings2Battery set-up2.1General2.1.1Turning battery on and offThe battery can be switched on or off by holding down the small recessed button marked “RESET”.2.1.2CAN communicationA VE.Can to CAN-bus BMS“Type B”cable is required for CAN-Bus communication between the BSL battery and the Victron GX device.Some inverters will use differ-ent cable configuration,please check this with inverter suppliers.(Black to inverter/GX device,red to battery).2.1.3Smart shuntA Battery Monitoring Device(Victron BMV/Smartshunt)is not required as State of Charge(SOC)is sent to the GX device via the CAN-Bus cable.2.1.4Dry contactsDry Contacts are mostly unused,but for communication with some non-smart systems please see the table below.Working current should be less than2A,mainly to connect with an external indicator light or buzzer.2.1.5Other portsPort1(RS485)and port3(RS232)are used for programming and retrieving information only and must be left open.2.2Multiple batteries2.2.1Max number of parallel batteriesA maximum of15batteries can be connected in parallel.Each battery will require a unique binary address which can be setup via the dip-switches located on the front of the battery.2.2.2Installing multiple batteriesWhen installing more than one battery in parallel,a standard RJ45patch network cable will be required for inter-battery communication.These cables will need to be connected to port4or5between all the connected batteries.The ports are paralleled therefore any port can be used for in or out connection.2.2.3Cable sizing with multiple batteriesIt is recommended to make use of a common rail bus-bar when more than4batteries are to be installed.All positive cables running between the battery and bus-bar must be the same length and all negative cables must be the same length.The batteries should be evenly grouped where possible.The recommended battery cable sizes from the batteries(going to the inverter)in par-allel are as follows:1battery-35mm2,2batteries-50mm2,3batteries-70mm2or 2×35mm2,4batteries-95mm2or2×50mm22.2.4Dip switch settings for multiple batteries3Inverter set-up3.1Batteries per inverter sizeInverter size Recommended N.O.batteries Minimum N.O.of batteries 15kVA4310kVA328kVA225kVA113kVA113.2Battery set-up on Victron GX device1.The VE.Can to CAN-bus BMS Type B cable needs to be connected to the VE-Canport on the GX device and the second unused VE.Can port needs to be terminated with the Victron blue terminator.Ensure that the cable is marked CCGX at the end.2.Press the enter button on the GX device.This should take you to the device listpage.Scroll down to settings,press enter,and scroll to services and press enter again.Navigate to the CAN settings and change the CAN speed from250KB to 500KB.3.Scroll to DVCC and select Switch DVCC on.Flag SHARED VOLTAGE SENSEand CHARGE LIMIT.Set CCL(charge current limit)to80amps/battery.4.Navigate back to the device list and the BSL battery should appear on the devicelist.5.Select the BSL battery set the parameters as follows:•Charge Voltage54.5V.•Charge Current Limit:80A per battery(recommended80A).•Discharge Current Limit:150A per battery(constant125A).4Inverter settings(Victron) 4.1General Tab4.2Grid Tab4.3Inverter Tab4.4Charger Tab4.6Assistant tab(b)4.8Assistant tab(d)4.10Assistant tab(f)4.12Assistant tab(h)5Other specifications。
UNT-MMI说明书
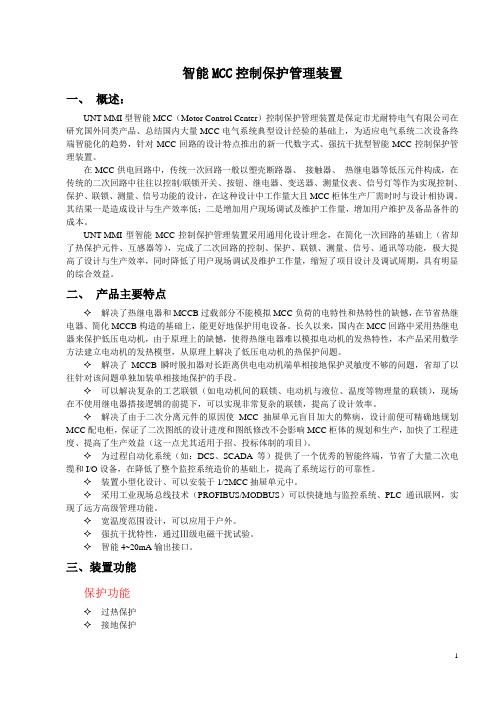
二、产品主要特点
解决了热继电器和MCCB过载部分不能模拟MCC负荷的电特性和热特性的缺憾,在节省热继电器、简化MCCB构造的基础上,能更好地保护用电设备。长久以来,国内在MCC回路中采用热继电器来保护低压电动机,由于原理上的缺憾,使得热继电器难以模拟电动机的发热特性,本产品采用数学方法建立电动机的发热模型,从原理上解决了低压电动机的热保护问题。
6:CT6
75kW﹤P200kW
用户外配互感器二次输出为1A
7:CT7
75kW﹤P200kW
用户外配互感器二次输出为5A
1:辅助电源为交流220V
2:辅助电源为直流220V
3:辅助电源为直流110V
Y:一体型
F:分体型
举例如下:控制单台接触器,不需420mA输出接口,无通讯功能,电机功率为20kW,辅助电源为交流220V,结构型式为一体型,则型号表示为:UNT-MMI-10031/Y;控制两台接触器,不需420mA输出接口,无通讯功能,电机功率为30kW,辅助电源为直流220V,结构型式为分体型,则型号表示为:UNT-MMI-20042/F。
可通过智能4~20mA输出接口监测本回路电流或其它物理量的状态
可监视接触器控制回路的接线完好性
通讯功能
可通过ProfiBus-DP工业现场总线实现系统组网
可通过RS485通讯接口,以ModBus@RTU通讯协议实现系统组网
四、功能原理描述:
易安居 8-10KW自动家用发电机系统说明书
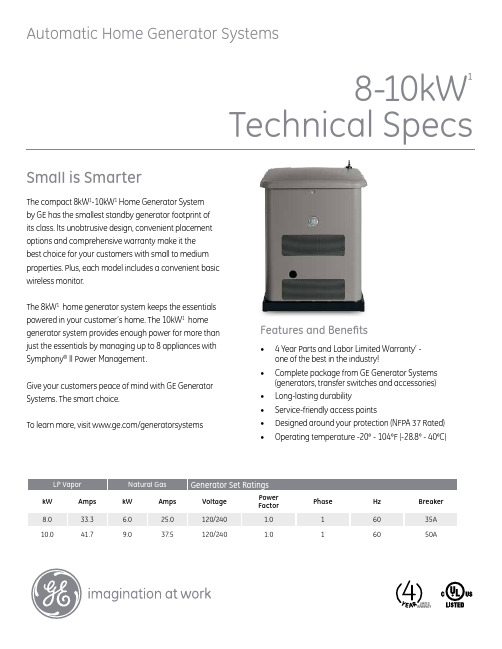
The compact 8kW 1-10kW 1 Home Generator System by GE has the smallest standby generator footprint of its class. Its unobtrusive design, convenient placement options and comprehensive warranty make it the best choice for your customers with small to medium properties. Plus, each model includes a convenient basic wireless monitor.The 8kW 1 home generator system keeps the essentials powered in your customer’s home. The 10kW 1 home generator system provides enough power for more than just the essentials by managing up to 8 appliances with Symphony ® II Power Management.Give your customers peace of mind with GE Generator Systems. The smart choice.To learn more, visit /generatorsystemsAutomatic Home Generator SystemsSmall is Smarter8-10kW ¹Technical Specs• 4 Year Parts and Labor Limited Warranty ² -one of the best in the industry!• Complete package from GE Generator Systems(generators, transfer switches and accessories)• Long-lasting durability• Service-friendly access points• Designed around your protection (NFPA 37 Rated) •Operating temperature -20° - 104°F (-28.8° - 40°C)Features and BenefitsNot for Prime Power or use where standby systems are legally required, for serious life safety or health hazards, or where lack of powerhampers rescue of fire-fighting operations.¹ This generator is rated in accordance with UL (UnderwritersLaboratories) 2200 (stationary engine generator assemblies) and CSA (Canadian Standards Association) standard C22.2 No. 100-04 (motors and generators).² Warranty details available at /generatorsystems.³ Installations must strictly comply with all applicable codes, industry standards, laws, regulations and provided installation manual. Running engines give off carbon monoxide, an odorless, colorless, poisonous gas so it is important to keep exhaust gas away from any windows, doors, ventilation intakes or crawl spaces. The installation manual contains specific instructions related to generator placement inaddition to NFPA 37, including the requirement that carbon monoxide detectors be installed and maintained in your home.Fuel consumption rates are estimated based on normal operating conditions. Generator operation may be greatly affected by elevation and the cycling operation of multiple electrical appliances – fuel flowrates may vary depending on these factors.Controller Fault CodesIs a trademark of General Electric Company and is under license by Briggs & Stratton CorporationPost Office Box 702Milwaukee, WI 53201 USA Assembled in USAWhy Choose GE?A GE whole house generator, with our ground-breaking Symphony ®II Power Management, has the flexibility toautomatically direct backup electricity to any appliance, light, TV or computer in a home. And unlike conventional backup power systems that may only provide access to 50% of a home’s power needs, Home Generator Systems by GE can power more of a home with a smaller, more fuel-efficient, smarter generator.WarrantyThe 4 Year Limited Parts and Labor warranty ² is one of the best comprehensive parts and labor warranties in the plete PackageWith GE Generator Systems, you can save time and money by ordering the complete package including transfer switch, generator and accessories.ReliableGE is a name your customers know and trust. You can be confident that each installed Standby Generator System will perform for many years.Order Your WayReady to place an order? Our team is ready to help. Rely on this model chart and call 1-87-RELY-ON-US.Briggs & Stratton Corp. reserves the right to makechanges in specifications and features shown herein, or discontinue the product described atany time without notice or obligation.GESB00104-3/13。
固德威 光伏并网逆变器MS系列 7-10kW 用户手册说明书

用户手册光伏并网逆变器MS 系列7-10kW版权声明用户手册 V1.0-2022-12-20因产品版本升级或其他原因,文档内容会不定期进行更新,如无特殊约定,文档内容不可取代产品标签或用户手册中的安全注意事项。
文档中的所有描述仅作为使用指导。
以及本手册中使用的其他GOODWE商标归固德威技术股份有限公司所有。
本手册中提及的所有其他商标或注册商标归其各自所有者所有。
商标授权注意未经固德威技术股份有限公司授权,本手册所有内容不得以任何形式复制、传播或上传至公共网络等第三方平台。
版权所有©固德威技术股份有限公司 2022。
保留所有权利。
用户手册 V1.0-2022-12-20目录目 录1 前言 ................................................................................11.1 适用产品 ....................................................................................................11.2 适用人员 ....................................................................................................11.3 符号定义 ....................................................................................................21.4 版本记录 ....................................................................................................22 安全注意事项 ...................................................................32.1 通用安全 .....................................................................................................32.2 直流侧 .........................................................................................................32.3 交流侧 .........................................................................................................32.4 逆变器 .........................................................................................................42.5 人员要求 .....................................................................................................42.6 EU符合性声明 (4)3 产品介绍 ..........................................................................53.1 应用场景 ....................................................................................................53.3 支持的电网形式 ..........................................................................................53.4 外观说明 ....................................................................................................53.4.1 外观介绍 .. (5)3.4.2 尺寸介绍 (6)3.4.3 指示灯说明 ...........................................................................................................63.4.4 铭牌说明 ..............................................................................................................74 设备检查与存储 ................................................................84.1 签收前检查 .................................................................................................84.2 交付件 ........................................................................................................84.3 设备存储 ....................................................................................................95 安装 ..............................................................................105.1 安装要求 ..................................................................................................105.2 安装逆变器 ...............................................................................................135.2.1 搬运逆变器 .........................................................................................................135.2.2 安装逆变器 (13)用户手册 V1.0-2022-12-20目录6 电气连接 (14)6.1 安全注意事项 (14)6.2 连接保护地线 (15)6.3 连接直流输入线 (15)6.4 连接交流输出线 (18)6.5 通信连接 (22)6.5.1 通信组网介绍 (22)6.5.2 安装通信模块(可选) (22)7 设备试运行 (24)7.1 上电前检查 (24)7.2 设备上电 (24)8 系统调测 (25)8.1 指示灯与按键介绍 (25)8.2 通过显示屏设置逆变器参数 (25)8.2.1 逆变器参数介绍 (27)8.3 通过U盘本地升级逆变器软件版本 (28)8.4 通过SolarGo App设置逆变器参数 (28)8.5 通过SEMS Portal进行设备监控 (28)9 系统维护 (29)9.1 逆变器下电 (29)9.2 拆除逆变器 (29)9.3 报废逆变器 (29)9.4 故障处理 (29)9.5 定期维护 (31)10 技术数据 (32)01 前言用户手册 V1.0-2022-12-201 前言1.1 适用产品1.2 适用人员本文档主要介绍了逆变器的产品信息、安装接线、配置调测、故障排查及维护内容。
10KW_中文_多功能正弦波逆变器UPS说明书

低压警告(电池电压过低时,蜂鸣
器响,提醒用户)
42.0Vdc ± 1.2Vdc (48V 电源)
低压断电(电池电池过低时关机) 40.0Vdc ± 1.2Vdc (48V 电源)
低压恢复(电池电压恢复正常时, 自动开机)
48.0Vdc ± 0.3Vdc
(48V 电源)
高压警告及断电(电池电压过高 时,蜂鸣器响,并关机)
开关 对应电池类型
档位
描述
12V
0
取消充电
1 美国胶体电池 14.0
2
玻璃棉电池 1 14.1
3
玻璃棉电池 2 14.6
4 密封铅酸电池 14.4
5 欧洲胶体电池 14.4
6 开放式铅酸电池 14.8
开路电压
浮充电压
24V 48V 72V 12V 24V 不充电(取消市电充电功能)
28.0 56.0 84.0 13.7 27.4 28.2 56.4 84.6 13.4 26.8 29.2 58.4 87.6 13.7 27.4 28.8 57.6 86.4 13.6 27.2 28.8 57.6 86.4 13.8 27.6 29.6 59.2 88.8 13.3 26.6
300W,600W,800W,1KW,1.5KW,2KW, 2:带市电充电功能,带 UPS 高
DC48V-AC220V 3KW,4KW,5KW,6KW,7KW,8KW,10KW, 速自动转换功能
12KW
3:频率 50HZ/60HZ,自行选择
DC72V-AC220V 1.5KW,2KW,3KW,4KW,5KW,6KW,
(125%<负载量<150%) ±10% :1 分钟后断开输出电压
(负载量>150%) ±10% :20 秒钟后断开输出电压
美国电器公司GE的10英寸沙拉锅产品说明书

CORDSET(DETACHABLE) - UK
4
FOOT 1” SOLID RUBBER
BASE ASSY/GREASE CAB-10”
1
BASE ASM/GRS CAB-10-120VC
BASE ASM/GRS CAB-10”-230V
1
INLET IEC 320 16 AMP
1
GREASE DRAWER ASSY.
2
HALF CLAMP .188 D STL ZP
1
BRACKET, PROBE MOUNT
8
SCREW 10-24X3/4X3/8 TYPE
1
CASTING-10” TOP ALUM. MACH-CAST GR, TOP IRON 10
1
CASTING-10” BOTTOM ALUM. MACH-CAST GR.BOT IRON 10
ROD, SPRING GUIDE
SPRING SUPPORT, TOP SPRING SUPPORT, TOP, SPT SPRING SUPPORT, TOP-10” SPRING, 14” AL SPRING, 14” AL SPRING, COMPRESSION, SPT SPRING, COMPRESSION, SPT SPRING COMPRESSION, 14” GR IRON SPRING,COMPRESSION, 10” IRON SPRING,COMPRESSION, 10” AL
6
2V-Z19095
2V-Z11400
7
2A-Z11406
2V-Z14936
2P-Z11408
2P-Z11408
2P-Z11409
8
10KW产品使用说明书(图)
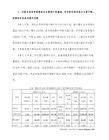
12、支持0~5V PID输入控制功率接口,可以控制输出功率为线性工作状态;
13、支持外接计算机,可以远程操控主机工作状态;
14、具有多个线圈叠加功率达100KW(10台以上属于高电压大功率设备,务必仅由经过专业培训合格的工程技术人员才能进行安装和调试,如果不避免,可能会导致人身强度或中度的伤害和设备损坏。严重可能会导致人身伤亡。
2、验货检查要求
请检查以下几项:◆确认产品运输过程中无损坏(目检看产品是否有损伤或缺口); ◆确保包装箱有说明书;◆检查产品并确认是您所订购的产品;◆如果您发现设备有损坏,请致电当地经销商或本公司
、负载电感:165uh,根据负载材质适当调整,使机器工作频率在16.5-17khz
二、环境适应能力
1、温度:-20℃~60℃;
2、湿度:≤95%
三、基本性能概述
1、电流与电压特性:恒流输出;
2、热效率≥95%;
3、IGBT过热保温度:75℃;
4、额定工作频率:12~28KHz(超出频率范围的预订另行配置);
5、半桥谐振一体化结构;
6、采用国内最新研制的谐振电容模块,使电路接线变得简单;
7、采用世界名牌IGBT模块驱动芯片;
8、采用世界名牌英飞凌IGBT模块;
9、采用先进高速霍尔传感器以及高可靠锁相环跟踪电路,使主机工作稳定;
10、具有软启动加热/停止模式;
11、自带简易数码显示操作面板,可以显示工作频率、输入电流、线圈输出电流大小、IGBT温度等参数,便于安装与调试(预订机器有效)
3B SCIENTIFIC 10 kV 高压电源说明书
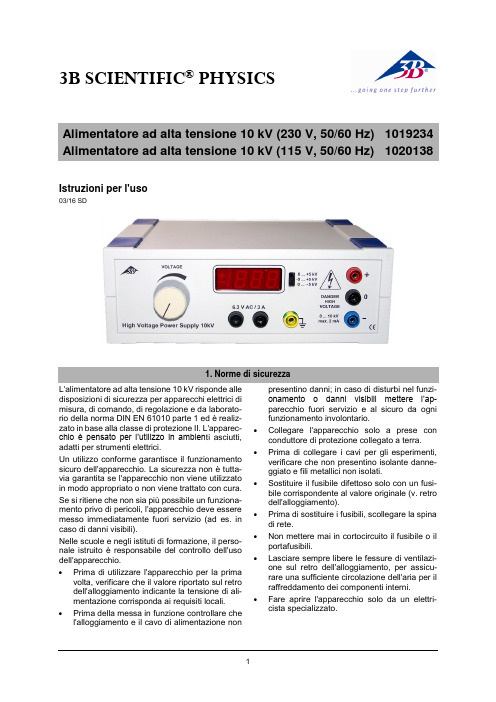
3B SCIENTIFIC ® PHYSICSIstruzioni per l'uso03/16 SDL'alimentatore ad alta tensione 10 kV risponde alle disposizioni di sicurezza per apparecchi elettrici di misura, di comando, di regolazione e da laborato-rio della norma DIN EN 61010 parte 1 ed è realiz-zato in base alla classe di protezione II. L'apparec-chio è pensato per l’utilizzo in ambien ti asciutti, adatti per strumenti elettrici.Un utilizzo conforme garantisce il funzionamento sicuro dell'apparecchio. La sicurezza non è tutta-via garantita se l'apparecchio non viene utilizzato in modo appropriato o non viene trattato con cura. Se si ritiene che non sia più possibile un funziona-mento privo di pericoli, l'apparecchio deve essere messo immediatamente fuori servizio (ad es. in caso di danni visibili).Nelle scuole e negli istituti di formazione, il perso-nale istruito è responsabile del controllo dell'uso dell'apparecchio.∙ Prima di utilizzare l'apparecchio per la primavolta, verificare che il valore riportato sul retro dell'alloggiamento indicante la tensione di ali-mentazione corrisponda ai requisiti locali. ∙ Prima della messa in funzione controllare chel'alloggiamento e il cavo di alimentazione nonpresentino danni; in caso di disturbi nel funzi-onamento o danni visibili mettere l’ap-parecchio fuori servizio e al sicuro da ogni funzionamento involontario.∙ Collegare l'apparecchio solo a prese con conduttore di protezione collegato a terra. ∙Prima di collegare i cavi per gli esperimenti, verificare che non presentino isolante danne-ggiato e fili metallici non isolati.∙Sostituire il fusibile difettoso solo con un fusi-bile corrispondente al valore originale (v. retro dell'alloggiamento).∙ Prima di sostituire i fusibili, scollegare la spina di rete.∙ Non mettere mai in cortocircuito il fusibile o il portafusibili.∙Lasciare sempre libere le fessure di ventilazi-one sul retro dell'alloggiamento, per assicu-rare una sufficiente circolazione dell'aria per il raffreddamento dei componenti interni.∙Fare aprire l'apparecchio solo da un elettri-cista specializzato.L’alimentatore ad alta tensione 10 kV è una sor-gente di alta tensione flottante, ad impiego univer-sale, per esperimenti di elettrostatica o per l’ali-mentazione di tubi elettronici.Fornisce un'alta tensione regolata, non pericolosa al contatto e impostabile in modo continuo con li-mitazione della corrente passiva. Un trasforma-tore integrato, resistente alle alte tensioni, viene utilizzato per il prelievo della tensione di riscalda-mento per i tubi elettronici. Una ventola con termo-stato evita il surriscaldamento.L’alimentatore ad alta tensione 1020138 è proget-tato per una tensione di rete di 115 V (±10%), 1019234 per 230 V (±10 %).Fig. 1 Elementi di comando1 Regolatore di alta tensione2 Display tensione3 Uscita tensione di riscal-damento4 Presa di terra5 Commutatore displayIl commutatore consente di cambiare l'indicazione fra le uscite per l'alta tensione:0 …+5 kV: indicazione dell'alta tensione fra le prese "0" e "+"-5 …+5 kV: indicazione dell'alta tensione fra le prese "-" e "+"0 …- 5 kV: indicazione dell'alta tensione fra le prese "0" e "-"6 Uscita alta tensione7 Interruttore di rete8 Fusibili9 Selettore di tensione 10 VentolaTensione dialimentazione: 115 / 230 V CA ± 10%,ved. retro dell'alloggia-mentoFrequenza di rete: 50 / 60 HzFusibili: ritardati, 115 V: 2 x 1 A,230 V: 2 x 0,5 AAlta tensione: 0 - 10000 V CC,max. 2 mATensione diriscaldamento: 6,3 V AC, max. 3 A, re-sistente all'alta tensionefino a 10 kV Protezione dasovraccarico: Primaria: Fusibile, v. re-tro dell’alloggiamentoSecondaria: Resistenzedi limitazione corrente Collegamenti: jack di sicurezza da 4 mm Display: digitalePrecisione di indicazione: 1% + 2 digit Temperatura ambiente: da 5 °C a 40 °CUmidità relativa max.: 80 %Dimensioni: ca. 240 x 220 x 90 mm3 Peso: ca. 2,1 kgCompatibilità elettromagnetica:Emissione di interferenze: E N 55011:2009 Immunità ai disturbi: EN 61326-1:2013Sicurezza elettrica:Norme di sicurezza: EN 61010-1:2010 Trasformatore: Trasformatore di sicu-rezza conforme a DINEN 61558-2-6Classe di protezione: 2Grado di inquinamento: 2Tipo di protezione: IP205.1 Indicazioni generali∙Prima di accendere l’alimentatore impostare il regolatore di alta tensione su 0 (battuta si-nistra).∙Collegare la struttura sperimentale all’alimen-tatore.∙Accendere l’alimentatore solo quando la struttura per l’esperimento è pronta.∙Le modifiche alla struttura dell’esperimento devono essere eseguite solo in assenza di corrente.∙Impostare la tensione desiderata nel regola-tore di alta tensione.∙Prima di spegnere l’alimentatore reimpostare il regolatore di alta tensione su 0 (battuta si-nistra).5.2 Presa di tensione∙Per la presa di un'alta tensione da +5 kV col-legare il polo positivo alla presa rossa "+" e il polo negativo alla presa nera "0". Realizzare la messa a terra della presa nera.∙Per la presa di un'alta tensione da -5 kV collegare il polo positivo alla presa nera "0" e il polo negativo alla presa blu "-". Realizzare la messa a terra della presa nera.∙Per la presa di un'alta tensione da 10 kV col-legare il polo positivo alla presa rossa "+" e il polo negativo alla presa blu "-".∙Per la presa di tensione di riscaldamento du-rante gli esperimenti con tubi elettronici, col-legare filamento caldo deitubi con le prese dell'uscita per la tensione di riscaldamento.+_+_+_5.3 Sostituzione dei fusibili∙Disconnettere l’alimentazione elettrica ed estrarre assolutamente la spina.∙Estrarre il portafusibili sul retro dell'alimenta-tore utilizzando un cacciavite piatto (vedere Fig. 2).∙Applicare il cacciavite dal lato del connettorea freddo.∙Sostituire il fusibile e reinserire il supporto. Fig. 2 Sostituzione dei fusibili∙Conservare l'apparecchio in un luogo pulito, asciutto e privo di polvere.∙Prima della pulizia, scollegare l'apparecchio dall'alimentazione.∙Non impiegare detergenti o soluzioni aggres-sive per la pulizia dell'apparecchio.∙Per la pulizia utilizzare un panno morbido e umido.∙Smaltire l'imballo presso i centri di raccolta e riciclaggio locali.Non gettare l'apparecchio neirifiuti domestici. Gli utenti pri-vati possono smaltire l’appa-recchio come disposto dal lo-cale gestore dello smalti-mento dei rifiuti urbani.∙Rispettare le disposizioni vigenti per lo smal-timento delle apparecchiature elettriche. 7.1 Determinazione della capacità di unasfera in uno spazio liberoDotazione supplementare necessaria:1 Elettrometro @ 230 V 1001025 oppure1 Elettrometro @ 115 V 1001024 1 Accessorio per elettrometro 1006813 1 Multimetro analogico Escola 30 10135261 Asta perforata di supporto 10027102 Piede a barilotto, 1 kg 1002834 Cavi per esperimentiLa struttura sperimentale di questa prova è costi-tuita da 2 parti. La fig. 2 corrisponde all'elettrizza-zione della sfera, la fig. 3 mostra il cablaggio dell'elettrometro per la misurazione della carica.7.2. Preparazione per l'analisi della devia-zione degli elettroni nel campo elettrico con il tubo di deflessione elettronica D Dotazione supplementare necessaria:1 Tubo di deflessione elettronica D 1000651 1 Portatubo D 1008507 1 Alimentatore ad alta tensione E 5 kV @230 V1013412 opputre1 Alimentatore ad alta tensione E 5 kV @115 V1017725 1 Set di cavi per esperimenti con tubi 1002847L'alimentatore ad alta tensione 10 kV serve ad alimentare il condensatore a piastre nel tubo.Fig. 3 Elettrizzazione della sfera 6.3 V AC+ 10 kV3B Scientific GmbH ▪ Rudorffweg 8 ▪ 21031 Amburgo ▪ Germania ▪ Fig. 4 Preparazione della misurazione della caricaFig. 5 Preparazione per l'analisi della deviazione degli elettroni nel campo elettrico con il tubo di deflessione elet-tronica DINOUT+IN300030001000100101mA =mA ~V ~V =10310,310310,310001001013030+-。
10kW 3-Phase 200 208 240V Switched PDU说明书
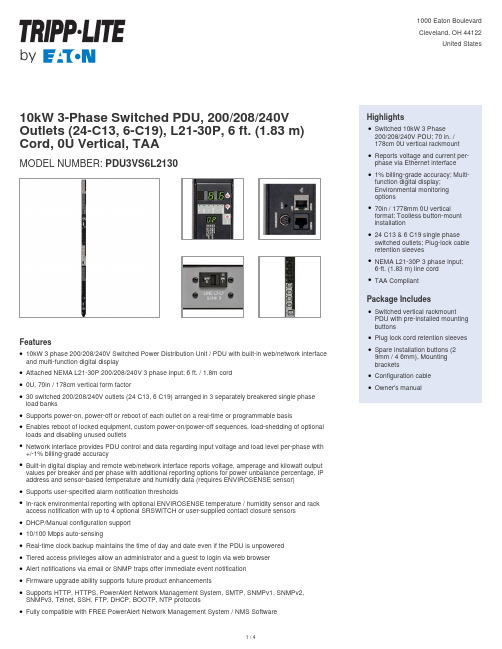
10kW 3-Phase Switched PDU, 200/208/240V Outlets (24-C13, 6-C19), L21-30P, 6 ft. (1.83 m) Cord, 0U Vertical, TAAMODEL NUMBER:PDU3VS6L2130Features10kW 3 phase 200/208/240V Switched Power Distribution Unit / PDU with built-in web/network interface and multi-function digital displayqAttached NEMA L21-30P 200/208/240V 3 phase input; 6 ft. / 1.8m cordq0U, 70in / 178cm vertical form factorq30 switched 200/208/240V outlets (24 C13, 6 C19) arranged in 3 separately breakered single phase load banksqSupports power-on, power-off or reboot of each outlet on a real-time or programmable basisqEnables reboot of locked equipment, custom power-on/power-off sequences, load-shedding of optional loads and disabling unused outletsqNetwork interface provides PDU control and data regarding input voltage and load level per-phase with +/-1% billing-grade accuracyqBuilt-in digital display and remote web/network interface reports voltage, amperage and kilowatt output values per breaker and per phase with additional reporting options for power unbalance percentage, IP address and sensor-based temperature and humidity data (requires ENVIROSENSE sensor)qSupports user-specified alarm notification thresholdsqIn-rack environmental reporting with optional ENVIROSENSE temperature / humidity sensor and rack access notification with up to 4 optional SRSWITCH or user-supplied contact closure sensorsqDHCP/Manual configuration supportq10/100 Mbps auto-sensingqReal-time clock backup maintains the time of day and date even if the PDU is unpoweredqTiered access privileges allow an administrator and a guest to login via web browserqAlert notifications via email or SNMP traps offer immediate event notificationqFirmware upgrade ability supports future product enhancementsqSupports HTTP, HTTPS, PowerAlert Network Management System, SMTP, SNMPv1, SNMPv2, SNMPv3, Telnet, SSH, FTP, DHCP, BOOTP, NTP protocolsqFully compatible with FREE PowerAlert Network Management System / NMS Softwareq HighlightsSwitched 10kW 3 Phase200/208/240V PDU; 70 in. /178cm 0U vertical rackmountqReports voltage and current per-phase via Ethernet interfaceq1% billing-grade accuracy; Multi-function digital display;Environmental monitoringoptionsq70in / 1778mm 0U verticalformat; Toolless button-mountinstallationq24 C13 & 6 C19 single phaseswitched outlets; Plug-lock cable retention sleevesqNEMA L21-30P 3 phase input;6-ft. (1.83 m) line cordqTAA CompliantqPackage IncludesSwitched vertical rackmountPDU with pre-installed mounting buttonsqPlug lock cord retention sleeves qSpare installation buttons (29mm / 4 6mm), MountingbracketsqConfiguration cableqOwner's manualqSpecificationsIncluded set of Plug-lock inserts keep C14 and C20 power cords solidly connected to PDU outlets q Toolless mounting supported in button-mount compatible racks, plus nut-and-bolt mounting brackets for other mounting applications (set of 2 9mm buttons pre-installed, 2 9mm and 4 6mm spare buttons included)qFederal Trade Agreements Act / TAA Compliant for GSA Schedule purchasesq© 2023 Eaton. All Rights Reserved. Eaton is a registered trademark. All other trademarks are the property of their respective owners.。
Eaton xStorage Home用户操作手册(4.2 kWh、6 kWh和10 kWh系统容量
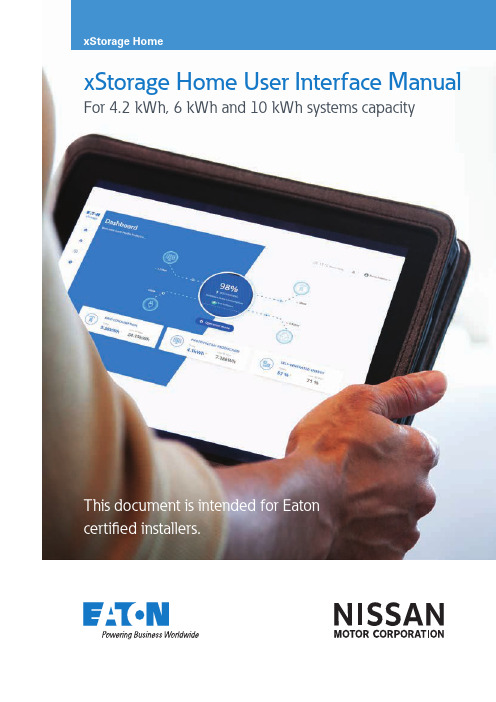
xStorage HomexStorage Home User Interface Manual For 4.2 kWh, 6 kWh and 10 kWh systems capacityThis document is intended for Eatoncertified installers.Content overview1 Introduction (3)Before you start (3)Technical disclaimer (3)Legal entity (3)2 Good to know (4)3 Commissioning xStorage Home (4)3.1 Starting the commissioning of xStorage Home (4)3.2 Step 1: Network settings (5)3.3 Step 2: Date & Time Configuration (7)3.4 Step 3: Topology (8)3.5 Step 4: Finish (9)3.6 Recommissioning the xStorage Home unit (10)4 Local and Cloud UI interface (11)4.1 How to use the local UI (11)4.2 How to connect to xStorage Cloud (12)5 User role-based access authorization (13)6 How to update xStorage Home hosted on the Cloud web portal (14)7 How to update xStorage Home from the local user interface (15)8 How to update the user interface on units running with the previous user interface (17)2XSTORAGE HOME USER INTERFACE MANUAL July 2019 1. IntroductionThank you for installing the xStorage Home systemThis manual provides Eaton certified installers with instructions on how to do the commissioning and the onboarding of xStorage Home using the xStorage Home user interface. This manual is complementary to the xStorage Home installation and user manuals.This manual also details the onboarding process and the update process of the xStorage Home unit. This update process can be done directly on the local web portal or through the Cloud web portal if the unit is connected to the Cloud ().Before you startThis manual contains important instructions that must be followed during the installation, operation and maintenance of the xStorage Home system. All instructions must be read before installing and operating the equipment. This manual should be retained for future reference.Please note that the xStorage Home system must only be installed by Eaton certified personnel, i.e. an Eaton technical support representative or an Eaton certified installer. There are no user serviceable parts inside the xStorage Homesystem. Failure to observe the above will void the guarantee provided and Eaton cannot be held legally accountable.This product is intended for residential application only. The contents of this manual are the copyright of the publisher and may not be reproduced (even in extracts) without the prior written approval of Eaton Corporation. While every care has been taken to ensure the accuracy of the information contained in this manual, Eaton assumes no liability for any error or omission. Eaton reserves the right to modify the designs of its products. The unauthorized copying and lending of this manual is prohibited.Technical disclaimerIn line with our goal to continuously improve the products and the customer service we provide, all specificationscontained in this document are subject to change with due notice. All drawings, descriptions or illustrations contained in this document serve to provide a clear overview and/or technical explanation of the present product and its various components and accessories.Legal entityEaton Energy StorageEaton Industries manufacturing GmbHAddress: Place de la Gare 21345 Le LieuSWITZERLANDWeb: /xstorage3XSTORAGE HOME USER INTERFACE MANUAL July 2019 4XSTORAGE HOME USER INTERFACE MANUAL July 2019 2. Good to know3. Commissioning xStorage HomeTo download the latest technical documentation, such as the user manual, the safety documentation and other relevant updates, visit our website /xstorage . Please note that in order to improve our customer experience we are constantly updating and enhancing the relevant technical and marketing materials.3.1 Starting the commissioning of xStorage Home•Access the local web user interface (UI) by entering https://<unit_IP> on your browser. The failover IP Address is 192.168.2.254. •Check that the PC or your device is below the subnet of xStorage Home. See section 4.1 for further details.•Once you’ve typed the IP address, the browser displays a warning message. Continuing the procedure will not cause any harms to your computer, tablet or smartphone.•To be able to proceed, click on ‘Advanced’ to expand the Advanced section from the warning page and click on ‘Continue’ to be directed to the local xStorage Home portal. • As an Eaton certified installer, click on “I’m a technician” to start the commissioning (see Figure 1).Only Eaton certified installers can install, configure and commission the xStorage Home system. Once the commissioning is fully completed, the xStorage Home system is ready to be used by the end-user and the end-user can decide if he/she wants to switch between Cloud and Local mode at any time.As an Eaton certified installer, you must have an email address registered in the Eaton e this registered email address when you sign in as a technician.It is possible to use multiple browsers except Internet Explorer which is not supported.Figure 1:Welcome pages of the local web user interface5XSTORAGE HOME USER INTERFACE MANUALJuly 2019 Default credentials for the end-user and Eaton certified installers are shown in Table 1.T able 1: Default credentials for the end-users and Eaton certified installers•Y ou can start the commissioning connected to the home internet network or the local router, via WiFi or an ethernet cable. •To connect via the ethernet cable, check that the xStorage Home system is listed below the right subnet as shown in Figure 9.• To connect via the WiFi local access point, use the following default SSID, password and IP address:• SSID: xstorage• Password: P4svF JA9• IP address: 192.168.3.993.2 Step 1: Network setting s•Click on ‘Network settings’.•Fill in the form to proceed with the configuration of the communication card and the onboarding of the xStorage Home system. • If you use an ethernet cable, it is recommended to use DHCP (see Figure 2).Figure 2: Network settings connection via an ethernet cable with DHCPIf you use a static address, you can edit the IP address as shown in Figure 3.Figure 3: Network settings connection via an ethernet cable using a static addressYou can also connect to the home internet network via WiFi as shown in Figure 4.WiFiFigure 4: Network settings connection via• Otherwise, an error message details the issue that prevented the communication card to connect to the network.Once the network configurations are completed, press “Next”, and move to the Date & Time Configuration page.At this stage, the application tests the network connectivity. Therefore, it navigates to the Date & Time page only if the network is correctly configured.6XSTORAGE HOME USER INTERFACE MANUAL July 2019 7XSTORAGE HOME USER INTERFACE MANUAL July 2019 Figure 5: Date & Time configuration page•It is mandatory to set up a date and time configuration. Both manual and automatic setups are available. •If you use a NTP server, ensure that the internet connection is well established. •Select the right date and time, then the country, city and time zone where the end-user is located as shown in Figure 5. • Once the configuration is finalized, press “Next” to move to the Topology step.3.3Step 2: Date & Time Configuration3.4 Step 3: TopologyAs an Eaton certified installer, you need to configure the topology of the installation at the end user’s home in order to finalize the commissioning process. You can find the details of this procedure in the xStorage Home installation manual and power meters manual available on /xstorage. Depending on the installation at the end user’s home, you may need to configure the following:• Power meter 1. Please select the meter from the drop-down menu;• Power meter 2. Please select the meter from the drop-down menu;• Photovoltaic panels.In the example shown in Figure 6, the power meter Sfere DDS1946-DS is set at both Power meter 1 and Power meter 2 and photovoltaic panels are installed and connected to xStorage Home.Figure 6: Example of a topology configuration with xStorage HomeFor the power meter Eastron SDM 120CT-Modbus, the procedure starts from Power meter 2 as indicated in the xStorage Home Power Meters manual that you can download on /xstorage.8XSTORAGE HOME USER INTERFACE MANUAL July 2019 9XSTORAGE HOME USER INTERFACE MANUAL July 2019 3.5 Step 4: FinishFigure 7: Final page1. Once you’ve completed the final stage of the setup process detailed in the xStorage Home installation manual, choose between connecting the unit to the Cloud or continue to use it in local mode.2. As the Eaton certified installer, go to the Home page of the xStorage Home portal and insert the end-user name and email address so that the end-user takes ownership of the unit as shown in Figure 7. The end-user is now ready to claim the ownership of the unit.3. Below is the procedure for the end user to claim the ownership of the unit.•The end-user needs to go to the log-in page on https:/// and sign-up with the end-user email address already registered by the installer •Once the sign-up is completed, an email is sent to the end user mailbox to finalize the account creation and claim ownership of the xStorage Home system. Ensure that the end-user registers the address ************************ in his/her contacts as the email may end up in the end-user spam box otherwise. •The email contains a link that enables the end-user to finalize the claim process. • At this stage, the xStorage Home system is onboarded, and the end-user can access it via https:///.3.6 Recommissioning the xStorage Home unitAn Eaton certified installer can always reinstall the xStorage Home system. From the local UI click on “Reinstall unit” in the menu, then click on the ‘Reinstall xStorage unit’ button as shown in Figure 8. In this case the commissioning process will start from the beginning and the Eaton certified installer will be redirected to the Network settings page. This option is only available for Eaton customer support representatives and Eaton certified installers.Figure 8: Reinstall the xStorage Home system10XSTORAGE HOME USER INTERFACE MANUAL July 2019 11XSTORAGE HOME USER INTERFACE MANUAL July 2019 4.1 How to use the local UIETH –IP: 192.168.2.254WLAN0 –Access Point SSID: xstorage IP: 192.168.3.99WLAN1 –SSID: end-user_router IP: 192.168.x.x4. Local and Cloud user interfaceEnd-users can use either the local or Cloud user interface (UI). The local and Cloud user interface (UI) work independently from each other. The local UI runs directly from the xStorage Home hybrid inverter while the Cloud UI is hosted on the cloud servers and available at https:///.You can use the user interface directly from the xStorage Home inverter. In case of a connection to the xStorage Home system via an ethernet cable, use the default IP. The default IP address of the local UI is https://192.168.2.254/, The username is “user” and the password is “user”. Check that the PC or your device is below the subnet of xStorage Home as shown in Figure 9. Once the IP address is typed, the browser displays a warning message. To proceed, click on ‘Advanced’ and the Advanced section will expand from the warning page. Click on ‘Continue’ to be directed to the local portal. This procedure will not cause harms to your computer, tablet or smartphone.Figure 9: Configuration of the PC ethernet card in order to connect to the local UIIn case of a connection via a local WiFi access point, the default SSID, password and IP address are: •SSID: xstorage •Password: P4svFJA9• IP address: 192.168.3.99xStorage Home can be connected to multiple interfaces. Figure 10 shows the multiple ways for you and the end-user to connect to xStorage Home:1. via an ethernet cable;2. via a local WiFi access point;3. via the router located at the end-user’s home.Figure 10: Interfaces of xStorage Home12XSTORAGE HOME USER INTERFACE MANUAL July 2019 If the xStorage Home system is connected to the cloud and the end-user tries and connects to the xStorage Home inverter, a message will appear. Click on “Disconnect from xStorage Cloud” to switch to the local mode as shown in Figure 11.Figure 11: How to disconnect the xStorage Home unit from the cloud in order to use the local UIFigure 12: How to connect the xStorage Home to the cloud from the local UI4.2 How to connect to xStorage CloudIf the end user uses the local mode, he/she can move to the cloud mode at any time as long as there is an internet connection available. The default IP address of the local UI is https://192.168.2.254/, the username is “user” and the password is “user”. Ensure that the PC or the device is below the subnet of xStorage Home as shown in Figure 9. Once the IP address is typed, the browser displays a warning message. To proceed, click on ‘Advanced’ so that the Advanced section expands from the warning page. Click ‘Continue’ to be directed to the local log-in portal. Once logged-in from the user settings, click on “Connect to xStorage Cloud” as shown in Figure 12. The xStorage Home unit is now available on the cloud portal at https:///.If there is an internet disconnection, the xStorage Home unit will try and reconnect to the same internet access. The unit will attempt to reconnect at least once a day. At any time, the end-user can use the local portal to disconnect the unit from the cloud. If the end-user disconnects the unit from the cloud, then xStorage Home will stop the attempt to reconnect to the cloud.5. User role-based access authorizationMultiple roles are available for the end-users from the Cloud portal. The end-users can be one or more users with different access roles:1. Owner. The owner has full ownership of the xStorage Home unit. Usually the Eaton certified installer sets the owner of xStorage Home at the end of the commissioning process.2. Technician. The technician is an Eaton certified installer in charge of remote maintenance. The technician has full access to the unit including diagnostic data. The technician profile should be removed by the end-user once the remote maintenance activity ends.3. Access management. The access management has similar rights of the owner with some limitations. Hence,• Access manager cannot perform unit updates.• Access manager cannot change the unit ownership.• From the unit general settings page, the access manager can only modify the default operation mode.4. Configure. The end-user with the Configure profile has same rights as the end-user with Access management but with limitations. Specifically, the person with the Configure profile cannot modify Users and Permissions.5. Viewer. The end-user with the Viewer profile has the same rights as the end-user with the Configure profile but with limitations. Hence,• The viewer cannot send command to the unit e.g. change operation modes from the dashboard.• The viewer cannot edit the unit settings page.• The viewer cannot modify scheduled events.• The viewer cannot put the hybrid inverter in Standby mode.You can configure up to 10 users maximum.13XSTORAGE HOME USER INTERFACE MANUAL July 2019 6. H ow to update xStorage Homehosted on the Cloud web portalTo update the system from the Cloud web portal, the end-user must have Owner role. Hence, only the owner has visibility on unit updates available from the Cloud web portal. The update option is available in the Unit Settings page. In that section, the end-user will be informed if a new update is available for that specific xStorage Home unit. By clicking on “check for updates” the end-user can also directly check if new updates are available as shown in Figure 13.Figure 13: Update page on the Cloud web portalOnce the update is accepted, all features from the Cloud web portal are disabled until the update process is completed. During the update process, the end-users associated with that unit will be notified by email, when the update starts and when the update is completed as shown in Figure 14.Figure 14: Example of emails sent during the xStorage Home update process14XSTORAGE HOME USER INTERFACE MANUAL July 2019 7. H ow to update xStorage Homefrom the local user interfaceIn case the user interface is running on the local mode, it is possible to update the xStorage Home firmware from the local UI. The default IP address of the local UI is https://192.168.2.254/, the username is “user” and the password is “user”. Please make sure that the ethernet card of your PC has the right IP and subnet as shown in Figure 9. Once the login is completed, from the unit settings click on “updates” as shown in Figure 15. Download the latest Firmware version from .Figure 15: Firmware updates page from the local UIThis file includes the necessary firmware bundle to update the xStorage Home unit.Figure 16: Select the file for the firmware update from the local UI15XSTORAGE HOME USER INTERFACE MANUAL July 2019 Once the file is selected press “Update firmware” to finalize the procedure as shown in Figure 17. When the update starts, a dialog box with a progress indicator is displayed and remains visible until the communication card reboots, or the update fails. The page must not be refreshed during this stage as it can interrupt the file upload to the communication card and cancel the update.When the file upload and the *.hex archive extraction to the communication card file system is completed, the progress indicator disappears. The communication card will reboot a few times and it can take 5 to 10 minutes until the update is completed and the communication card runs again.At this point, you can refresh the page, accessing https://<unit_IP> to check if the update has been completed.Figure 17: General settings view16XSTORAGE HOME USER INTERFACE MANUAL July 2019 8. H ow to update the user interface on unitsrunning with the previous user interfaceEnd-users using previous versions of the user interface can also easily upgrade to the new version using the following steps:• Navigate to the local UI of the communication card https:/ /<unit_IP> on your browser. The Failover IP Address is192.168.2.254.• Login with your credentials.• On the left menu select “Firmware updates”.• Update it using the file XSTH1PNP_V66677748.hex. This task will take about 5 minutes as shown in Figure 18.Figure 18: *.hex file moves to the new user interface• Navigate and log-in again into the local UI of the communication card.• On the left menu select again “Firmware updates”• This time use the latest inverter bootloader XSTH1P_BL_v002.ROM file or superior version.• Navigate and log-in again into the local UI of the communication card.• On the left menu select again “Firmware updates”.• This time use the latest *.hex file XSTH1PNP_YYYYMMDD.hex as shown in Figure 19.• Onboard the unit following the steps already described in the previous sections of this xStorage Home User Interface manual.Figure 19: Firmware update to use the new UI17XSTORAGE HOME USER INTERFACE MANUAL July 2019 EatonEMEA Headquarters Route de la Longeraie 7 1110 Morges, Switzerland © 2018 EatonAll Rights ReservedPublication No. CA00000000E / XXX July 2019Eaton is a registered trademark.All trademarks are propertyof their respective owners.Changes to the products, to the information contained in this document, and to prices are reserved; so are errors and omissions. Only order confirmations and technical documentation by Eaton is binding. Photos and pictures also do not warrant a specific layout or functionality. Their use in whatever form is subject to prior approval by Eaton. The same applies to Trademarks (especially Eaton, Moeller, and Cutler-Hammer). The Terms and Conditions of Eaton apply, as referenced on Eaton Internet pages and Eaton order confirmations.。
Eaton 9SX UPS 产品说明书
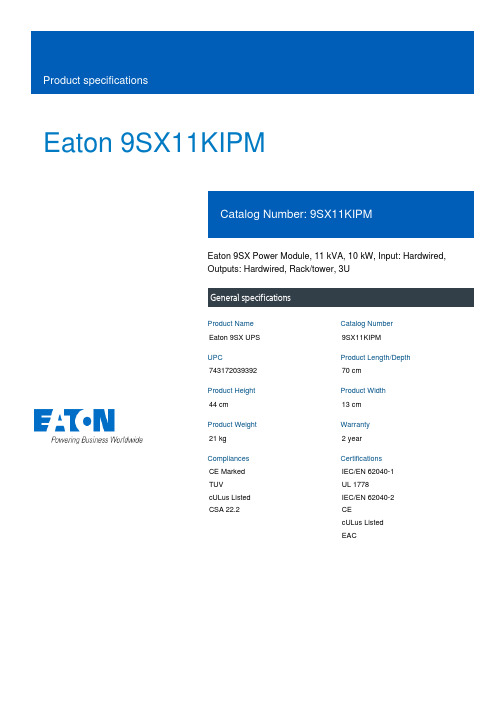
Eaton 9SX11KIPMEaton 9SX Power Module, 11 kVA, 10 kW, Input: Hardwired, Outputs: Hardwired, Rack/tower, 3UEaton 9SX UPS 9SX11KIPM74317203939270 cm 44 cm 13 cm 21 kg 2 year CE Marked TUV cULus Listed CSA 22.2IEC/EN 62040-1 UL 1778 IEC/EN 62040-2 CEcULus Listed EACProduct Name Catalog Number UPCProduct Length/Depth Product Height Product Width Product Weight Warranty Compliances Certifications60 HzSine wave12 (supercharger required for more than 6 EBM)10 kW0.9Rack/tower2NoHardwired/fixed connection100 V250 V50 HzEaton Intelligent Power Manager, Eaton Intelligent Power ProtectorNo battery951Eaton UPS Services Quick Guide 2021Eaton UPS and battery servicesEC DoC Eaton 9SXEaton 9SX-9PX UPS - 8-11 kVA-EBM 240V - Installation and user manualEaton 9SX UPS - 5/6/8/11 kVA - DatasheetSecondary frequency - maxOutput waveformMax number of battery packsWattageOutput power factorForm factorVoltage distortion output (linear load) - max Includes network cardInput connectionInput voltage - minOutput voltage - maxSecondary frequency - minSoftware compatibilityBattery replacementEfficiencyNumber of outputs hardwiredSpecial features BrochuresCertification reports Manuals and user guides Technical data sheetsDouble conversion topologyConstantly monitors powerconditions and regulatesvoltage and frequencyProvides more real power(watts) to protect moreequipment with a 0.9 powerfactorEnergy Star qualified,provides the highestefficiency level to reduceenergy and cooling costsInternal bypass allowsservice continuity in case ofUPS faultNext-generation graphicalLCD displayMeter energy consumption(at the UPS level)Construction typeFree standing modelOutput voltage - min200 VColorBlackExtended battery capabilityYesOutput voltage range200/208/220/230/240/250 V +/- 1%TopologyOnline/Double-conversionBTU RatingOnline: 2047Efficiency (eco-mode)98Runtime at half load0 minInput nominal voltage230V default (200/208/220/230/240/250V)Input power factor>.99Input frequency range40-70 HzInternal bypassYesInput voltage - max276 VVoltage typeACPhase (output)1Battery managementABM & Temperature compensated charging method (user selectable) Automatic battery test Deep discharge protection Automatic recognition of external battery unitsAuto shutdown functionYesVA rating11 kVAPotential free switch contact YesReceptacleHardwiredPhase (input)1Package contentsPower ModuleUSB cableSerial cable(2) Supports for tower mountingSafety instructions Quickstart guideNoise level<50 dB at 1 meterFeed type1Runtime graphView runtime graphUser interfaceMultilingual graphical LCD displayBattery quantityRack size3UVoltage230VHot swap powerNoTemperature range0° to 40°C (32° to 104°F)Ethernet interfaceNoCommunicationUSB port (HID compliant) Serial port (RS232)Mini terminal block forremote On/OffMini-terminal block forremote power offDry contacts (4 outputs, relay, DB9)Relative humidity0-95% non-condensingRack mounting kitNoOutput frequency50/60 HzRuntime at full load0 minType of interfaceOtherPrimary frequency - minEaton Corporation plc Eaton House30 Pembroke Road Dublin 4, Ireland © 2023 Eaton. All rights reserved. Eaton is a registered trademark.All other trademarks areproperty of their respectiveowners./socialmedia40 Hz Power Module 230V default (200/208/220/230/240/250V)One slot for optional communication card 176-276 V (100-276 V with derating)50/60 Hz70 Hz 3000 mTypeOutput nominal voltageExpansion slotsInput voltage rangeNominal frequency Primary frequency - max Altitude。
M10K-T Tugger 10,000 Lbs Towing Capacity 说明书
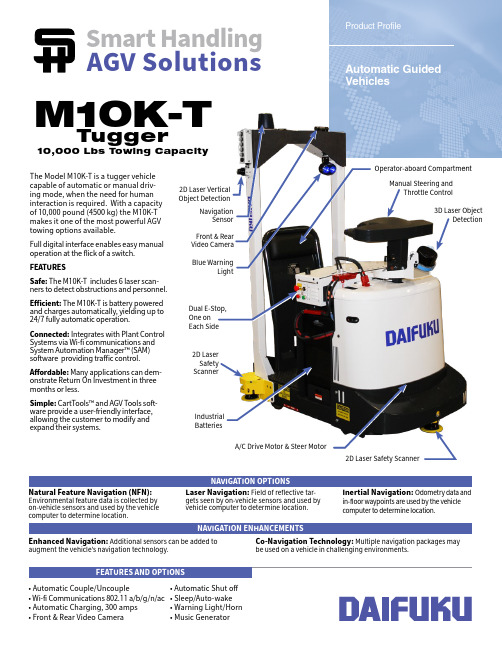
The Model M10K-T is a tugger vehicle capable of automatic or manual driv-ing mode, when the need for human interaction is required. With a capacity of 10,000 pound (4500 kg) the M10K-T makes it one of the most powerful AGV towing options available.Full digital interface enables easy manual operation at the flick of a switch.FEATURESSafe: The M10K-T includes 6 laser scan-ners to detect obstructions and personnel.Efficient: The M10K-T is battery powered and charges automatically, yielding up to 24/7 fully automatic operation.Connected: Integrates with Plant Control Systems via Wi-fi communications and System Automation Manager™ (SAM) software providing traffic control.Affordable: Many applications can dem-onstrate Return On Investment in three months or less.Simple: CartTools™ and AGV Tools soft-ware provide a user-friendly interface, allowing the customer to modify and expand their systems.Automatic Guided VehiclesProduct ProfileIndustrial BatteriesManual Steering and Throttle Control Dual E-Stop,One on Each Side Operator-aboard Compartm ent A/C Drive Motor & Steer Motor2D Laser Safety Scanner3D Laser Object Detection 2D Laser Safety Scanner NAVIGATION OPTIONS • Automatic Couple/Uncouple • Wi-fi Communications 802.11 a/b/g/n/ac • Automatic Charging, 300 amps • Front & Rear Video Camera • Automatic Shut off • Sleep/Auto-wake • Warning Light/Horn • Music GeneratorEnhanced Navigation: Additional sensors can be added to augment the vehicle’s navigation technology.Co-Navigation Technology: Multiple navigation packages may be used on a vehicle in challenging environments.NAVIGATION ENHANCEMENTSInertial Navigation: Odometry data andin-floor waypoints are used by the vehicle computer to determine location.Natural Feature Navigation (NFN): Environmental feature data is collected by on-vehicle sensors and used by the vehicle computer to determine ser Navigation: Field of reflective tar-gets seen by on-vehicle sensors and used by vehicle computer to determine location.Navigation Sensor Blue Warning Light Front & Rear Video Camera 2D Laser Vertical Object Detection30100 Cabot Drive Novi, MI 48377 USA +1-248-553-1000******************SAM ™, SmartCart ®, and CartT ools ™ are trademarks of Jervis B. Webb Company. All other trademarks are the property of their respective owners.NOTICE: The information, data and specifications in this brochure are subject to change without notice and should not be used for construction purposes. Daifuku does not represent or warrant that selection of compo-nents or accessories set forth in this brochure will necessarily result in proper installation, operation and/or maintenance of such equipment or system, and Daifuku disclaims responsibility for any and all damages and injuries resulting from selection, design, installation, operation or maintenance performed by non-Daifuku personnel. * For any applications greater than these specifications, please contact Engineering .© 2022 Weight / with batteries 1,400 lbs (635 kg) / 2,600 lbs (1179 kg) Dimensions W: 42.8" (1087 mm) L: 65" (1651 mm) H: 89" (2134 mm) Traction Power 200 lbs (91 kg)constant, 300+ lbs (136 kg) starting Safety 3 ANSI B56.5 compliant laser scanners Speed – 6 speeds 15 (4.5 mpm)to 360 fpm (109 mpm), 1 fpm (.025 mpm) increments Battery Options 24VDC Battery weight min/max 855 lbs (388 kg) / 1550 lbs (703 kg) - 510 AH lead acid Charge rate 140 amp -Standard Option - 450 AH sealed AGM gel Charge rate 140 amp - Standard Option - 558 AH TPPL Charge rate to 300 amp Automatic Charge 300 amp charge rate Manual ChargeUp to 82 amp charge rate Environment Atmosphere 0 to 40° C, 25% to 95% non-condensing humidity Dust/Water-proof No Floor Specs – Edges/Debris ¼” (6.35 mm) abrupt elevation change maximum, smoothed Expansion Joints ¼” (6.35 mm) minimum Grade Rating 3% Friction 0.6 coefficient of friction between wheels and floor, minimum Floor Conductivity Static dissipative, less than 3.5 x 107 ΩRadio Communication IEEE 802.11a/b/g/n/ac standard Detailed Specifications Drive Direction – Automatic Forward and Reverse (if equipped)Duty Cycle 88% @ Maximum Load Rating Drive Unit – Wheel 10" X 4" (254 mm X 102 mm) Poly Drive Type Gear driven steerable turntable Motor 3.8 kw AC Brake Spring actuated (fail-safe)Rear Wheels Poly 7" diameter x 3" wide (178 X 76 mm) (Shore A, durometer 85)Navigation Daifuku AGV – Natural Feature Navigation, Laser and Inertial Steer Angle Sensor Encoder Yes Steering /Stopping Accuracy +/- ½” (12.7 mm)HMI Display 5.7” (145 mm) color touch screen – errors & destinations Video Camera Front/rear, 1080P, supports up to 128GB microSD card Manual Movement Steerhead - Operator-aboard Minimum Path Radius 4’ (1219 mm) @ 100 FPM (30 mpm), 8’ (2438 mm) @ 160 FPM (48 mpm)Drive Stalled Detection Yes Distance Initiated Functions Yes – in 1” (25.4 mm) increments Program Method PC and Wireless Obstacle Detection 360°, programmable up to 9’ (2.8 meters)Emergency Stop 2 – Left/Right side WiringPer NEC ampacity guidelines。
- 1、下载文档前请自行甄别文档内容的完整性,平台不提供额外的编辑、内容补充、找答案等附加服务。
- 2、"仅部分预览"的文档,不可在线预览部分如存在完整性等问题,可反馈申请退款(可完整预览的文档不适用该条件!)。
- 3、如文档侵犯您的权益,请联系客服反馈,我们会尽快为您处理(人工客服工作时间:9:00-18:30)。
EQUIPMENT DESCRIPTIONRead this manual carefully and become familiar with your generator.Know its applications, its limitations and any hazards involved.This generator is an engine-driven, revolving field, alternating current (AC) generator. It was designed to supply electrical power for operating compatible electrical lighting, appliances, tools and motor loads0. The generator’s revolving field is driven at about 3,600 rpm by a twin-cylinder engine.CAUTION! DO NOT Exceed the generator’s wattage/amperage capacity. See “Don’t Overload Generator”.Every effort has been made to ensure that information in this manual is accurate and current. However, we reserve the right to change, alter or otherwise improve the product and this document at any time without prior notice.The Emission Control System for this generator is warranted for standards set by the Environmental Protection Agency. For warranty information refer to the engine owner’s manual.SAFETY RULESThis is the safety alert symbol. It is used to alert you to potential personal injury hazards. Obey all safety messages that follow this symbol to avoid possible injury or death.The safety alert symbol () is used with a signal word (DANGER, CAUTION, WARNING), a pictorial and/or a safety message to alert you to hazards. DANGER indicates a hazard which, if not avoided, will result in death or serious injury. WARNING indicates a hazard which, if not avoided, could result in death or serious injury.CAUTION indicates a hazard which, if not avoided, might result in minor or moderate injury. CAUTION, when used without the alert symbol, indicates a situation that could result in equipment damage. Follow safety messages to avoid or reduce the risk of injury or death.KNOW YOUR GENERATORRead this owner’s manual and safety rules before operating your generator.Compare the illustrations with your generator, to familiarize yourself with the locations of various(1) Circuit Breakers (AC) - Each receptacle is provided with a "push to reset" circuit breaker toprotect the generator electrical overload.(2) Volt Meter- Provides reading of voltage 220V output.(3) Choke Lever - Used when starting a cold engine.(4) Electric Start Switch- Must be in “ON”position to start engine. Set to “OFF”to stop arunning engine.(5) Hour Meter: Time the length of the generator use.(6) Output Indicator.- The indicator will bright when the voltage output form receptacle.(7) DC Circuit Protector –DC 12V receptacle is provided with a "push to reset" circuitprotector to protect the generator electrical overload.(8) 12 Volt DC Receptacle - Use this receptacle with battery charge cables to charge a 12 Voltbattery.(9) Grounding Fastener - Use this connection to properly ground the generator.(10) 127/220 Volt AC, 30 Amp Locking Receptacle - May be used to supply electrical powerfor the operation of 127/220 Volt AC, 30 Amp, three phase, 60 Hz electrical lighting, appliance, tool and motor loads.(11) 120 Volt AC, 20 Amp Duplex Receptacles - May be used to supply electrical power forthe operation of 120Volt AC, 20 Amp, single phase, 60 Hz electrical lighting, appliance, tool and motor loads.(12) 120 Volt AC, 30 Amp Locking Receptacle - May be used to supply electrical power forthe operation of 120 Volt AC, 30 Amp, single phase, 60 Hz electrical lighting, appliance, tool and motor loads.(13) Fuel Tank - Capacity of eight (8) U.S. gallons.(14) Oil Fill Cap - Add oil to engine here.(15) Air Cleaner - Uses a dry type filter element and foam pre-cleaner to limit the amount of dirtand dust sucked into the engine.ASSEMBLYYour generator requires some assembly and is ready for use after it has been properly serviced with the recommended oil and fuel.IMPORTANT: Any attempt to run the unit before it has been serviced with the recommended oil will result in an engine failure.Remove Generator from Carton1. Set palettes carton on a rigid flat surface.2. Carefully cut bands around shipping carton.3. Lift carton off generator.4. Remove all packing material, carton fillers, etc.5. Remove generator from shipping pallet.Install Wheel KitThe wheel kit is designed to greatly improve the portability of your generator.NOTE: Wheel kit is not intended for over-the-road use. You will need a socket wrench with 15mm sockets and a needle-nose plier to install this kit.Refer to Figure 1 and install the wheel kit as follows:1. Place generator on a hard flat surface.2. Stand at control panel end of generator and gently tilt generator up, high enough to place wooden blocks beneath cradle. This will allow you to add wheels.3. Install the four wheels stands using four bolts and nuts.Figure 1- Install Wheel KitCheck Battery / Attach Negative Battery WireThe sealed battery on the generator is fully charged and pre-installed except for the negative (black) battery cable.To install:1. Cut off tie wrap securing loose end of negative (black) cable.2. Remove nut and washer on negative battery terminal.3. Slide negative battery cable over screw on negative terminal (Figure 2).4. Reattach washer and nut and tighten.5. Verify that connections to battery and generator are tight and secure.Figure 2- Negative Battery connectionBEFORE STARTING THE ENGINEAdd Engine Oil and Fuel﹡Place generator on a level surface.﹡Refer to engine owner’s manual and follow oil and fuel recommendations and instructions.NOTE: Check oil often during engine break-in. Refer to engine owner’s manual for recommendations.NOTE: The generator’s revolving field rides on a prelubricated and sealed ball bearing that requires no additional lubrication for the life of the bearing.GROUNDING THE GENERATORThe National Electrical Code requires that the frame and external electrically conductive parts of this generator be properly connected to an approved earth ground. Local electrical codes may also require additional grounding of the unit. For that purpose, a GROUNDING FASTENER is provided on the generator end (Figure 3).Figure 3- Grounding FastenerGenerally, connecting a No. 12 AWG (American Wire Gauge) stranded copper wire to the grounding fastener and to an earth-driven copper or brass-grounding rod (electrode) provides adequate protection against electrical shock. Be careful to keep the grounding wire attached after connecting the stranded copper wire. However, local codes may vary widely. Consult with a local electrician for grounding requirements in your area.Properly grounding the generator helps prevent electrical shock if a ground fault condition exists in the generator or in connected electrical devices, especially when the unit is equipped with a wheel kit. Proper grounding also helps dissipate static electricity, which often builds up in ungrounded devices.OPERATING THE GENERATORIMPORTANT: Always unplug the battery float charger before starting the generator.Starting the EngineDisconnect all electrical loads from the generator. Follow start instruction steps in numerical order:1. Turn fuel valve to “On”position (Figure 4). Fuel valve handle should be vertical (pointingtoward ground) for fuel to flow.Figure 4- Fuel Valve2. Set Ignition switch to ”RUN” position (Figure 5).Figure 5- Ignition Switch3. Start engine according to instructions given in engine owner’s manual.Connecting Electrical Loads﹡Let engine stabilize and warm up for a few minutes after starting.﹡Plug in and turn on the desired 120 /208 Volt AC, three phase, 60 Hz electrical loads.﹡DO NOT connect 240 Volt loads to the 120 Volt receptacles.﹡DO NOT connect 50 Hz loads to the generator.﹡DO NOT OVERLOAD GENERATOR. See “Don’t Overload Generator”.Stopping the Engine1. Unplug all electrical loads from generator panel receptacles. NEVER start or stop engine withelectrical devices plugged in and turned on.2. Put idle control switch in “Off” position.3. Let engine run at no-load for 30 seconds to stabilize internal temperatures of engine andgenerator.4. Close the fuel shut-Off valve.5. Move Ignition switch to “Off” position.Charging a BatteryYour generator has the capability of recharging a discharged 12 Volt automotive or utility style storage battery. DO NOT use the unit to charge any 6 Volt batteries. DO NOT use the unit to crank an engine having a discharged battery.To recharge 12 Volt batteries, proceed as follows:1. Check fluid level in all battery cells. If necessary, add ONLY distilled water to coverseparators in battery cells. DO NOT use tap water.2. If battery is equipped with vent caps, make sure they are installed and are tight.3. If necessary, clean battery terminals.4. Connect battery charge cable connector plug to panel receptacle identified by the words“12-VOLTS D.C.”5. Connect battery charge cable clamp with red handle to the positive (+) battery terminal(Figure 6).6. Connect battery charge cable clamp with black handle to the negative (-) battery terminal(Figure 6).Figure 6- Battery Connections7. Start engine. Let engine run while battery recharges.8. When battery has charged, shut down engineNOTE: Use an automotive hydrometer to test battery state of charge and condition. Follow the hydrometer manufacturer’s instructions carefully. Generally, a battery is considered to be at 100% state of charge when specific gravity of its fluid (as measured by hydrometer) is 1.260 or higher.COLD WEATHER OPERATIONUnder certain weather conditions (temperatures below 40℉(4℃) and a high dew point), your generator may experience icing of the carburetor and/or the crankcase breather system.Build a structure that will enclose three sides and the top of the generator:1. Make sure entire muffler-side of generator is exposed. Note that your generator may appeardifferent from that shown in Figure 8.Figure 8- Permanent Cold Weather Shelter2. Ensure a minimum of two feet clearance between open side of box and nearest object.3. Face exposed end away from wind and elements.4. Enclosure should hold enough heat created by generator to prevent problems.RECEPTACLES127/220 Volt AC, 30 Amp, Locking ReceptacleUse a NEMA L21-30R plug (For option) with this receptacle. Connect a 4-wire cord set rated for 220 Volt AC loads at 30 Amps (or greater) (Figure 10). You can use the same 4-wire cord if you plan to run a 127 Volt load.The generator has a receptacle for three phase (220V) and single phase (127V) as follows:●Three phase application (220V) Insert the plug into the receptacle X, Y and Z.●Single phase lower application (127V) Insert the plug into the receptacle W and X, W and Y,W and Z.Maximum one-third (1/3) of generator output can be utilized from each phase.Figure 10- 127/220 Volt AC, 30 Amp Locking ReceptacleThis receptacle powers 127/220 Volt AC, 60 Hz, single-phase loads requiring up to 3,600 watts of power at 30 Amps for 127 Volts; three-phase loads requiring up to 10,800 watts of power (10.8 kW) at 30 Amps for 220 Volts. The outlet is protected by a 30 Amp push-to-reset circuit breaker.120 Volt AC, 30 Amp Locking ReceptacleUse a NEMA L5-30 plug (For option) with this receptacle. Connect a 3-wire cord set rated for 125 Volt AC loads at 30 Amps to the plug (Figure 11).Figure 11- 120 Volt AC, 30 Amp Locking ReceptacleUse this receptacle to operate 120 Volt AC, 60 Hz, single-phase loads requiring up to 3,600 watts (3.6 kW) of power at 30 Amps. The outlet is protected by a 30 Amp push-to-reset circuit breaker.120 Volt AC, 20 Amp, Duplex ReceptacleEach receptacle (Figure 13) is protected against overload by a 20 Amp push-to-reset circuit breaker.Figure 13 - 120 Volt AC, 20 Amp, Duplex ReceptacleUse each receptacle to operate 120 Volt AC, single-phase, 60 Hz electrical loads requiring up to 2,400 watts (2.4 kW) at 20 Amps of current. Use cord sets that are rated for 125 Volt AC loads at 20 Amps (or greater).12 Volt DC, 10 Amp ReceptacleThis receptacle allows you to recharge a 12 Volt automotive or utility style storage battery with the battery charge cables provided (Figure 14).Figure 13-12 Volt DC, 10 Amp ReceptacleThis receptacle cannot recharge 6 Volt batteries and cannot be used to crank an engine having a discharged battery.See the section “Charging a Battery” before attempting to recharge a battery.DON’T OVERLOAD GENERATORCapacityYou must make sure your generator can supply enough rated (running) and surge (starting) watts for the items you will power at the same time. Follow these simple steps:1. Select the items you will power at the same time.2. Total the rated (running) watts of these items. This is the amount of power your generatormust produce to keep your items running. See Figure 16.3. Estimate how many surge (starting) watts you will need. Surge wattage is the short burst ofpower needed to start electric motor-driven tools or appliances such as a circular saw or refrigerator. Because not all motors start at the same time, total surge watts can be estimated by adding only the item(s) with the highest additional surge watts to the total rated watts from step 2.Highest Additional Surge Watts = 1800Total Generator Output Required = 4875Power ManagementTo prolong the life of your generator and attached devices, it is important to take care when adding electrical loads to your generator. There should be nothing connected to the generator outlets before starting its engine. The correct and safe way to manage generator power is to sequentially add loads as follows:1. With nothing connected to the generator, start the engine as described in this manual.2. Plug in and turn on the first load, preferably the largest load you have.3. Permit the generator output to stabilize (engine runs smoothly and attached device operatesproperly).4. Plug in and turn on the next load.5. Again, permit the generator to stabilize.6. Repeat steps 4 and 5 for each additional load.NEVER add more loads than the generator capacity. Take special care to consider surge loads in generator capacity, as described above.GENERAL MAINTENANCE RECOMMENDATIONSThe Owner/Operator is responsible for making sure that all periodic maintenance tasks are completed on a timely basis; that all discrepancies are corrected; and that the unit is kept clean and properly stored. NEVER operate a damaged or defective generator.Engine MaintenanceSee engine owner’s manual for instructions.KEEP OUT OF REACH OF CHILDREN. DON'T POLLUTE. CONSERVERESOURCES. RETURN USED OIL TO COLLECTION CENTERS.Generator MaintenanceGenerator maintenance consists of keeping the unit clean and dry. Operate and store the unit in a clean dry environment where it will not be exposed to excessive dust, dirt, moisture or any corrosive vapors. Cooling air slots in the generator must not become clogged with snow, leaves or any other foreign material.NOTE: DO NOT use a garden hose to clean generator. Water can enter engine fuel system and cause problems. In addition, if water enters generator through cooling air slots, some of the water will be retained in voids and cracks of the rotor and stator winding insulation. Water and dirt buildup on the generator internal windings will eventually decrease the insulation resistance of these windings.Battery MaintenanceOther than float charging, described elsewhere, no maintenance is required for the battery. Keep the battery and terminals clean and dry.IMPORTANT: Battery charging should be performed in a dry location, such as inside a garage. Generator Cleaning﹡Use a damp cloth to wipe exterior surfaces clean.﹡Use a soft bristle brush to loosen caked on dirt or oil.﹡Use a vacuum cleaner to pick up loose dirt.﹡Low pressure air (not to exceed 25 psi) may be used to blow away dirt. Inspect cooling air slots and opening on generator. These openings must be kept clean and unobstructed.STORAGEThe generator should be started at least once every seven days and allowed to run at least 30 minutes. If this cannot be done and you must store the unit for more than 30 days, use thefollowing guidelines to prepare it for storage.Generator Storage﹡ Clean the generator as outlined in generator Cleaning?﹡ Check that cooling air slots and openings on generator are open and unobstructed. Engine StorageSee engine owner ’s manual for instructions.Other Storage Tips﹡ To prevent gum from forming in fuel system or on essential carburetor parts, add fuelstabilizer into fuel tank and fill with fresh fuel. Run the unit for several minutes to circulate the additive through the carburetor. The unit and fuel can then be stored for up to 24 months. Fuel stabilizer can be purchased locally.﹡ DO NOT store fuel from one season to another unless it has been treated as describedabove.﹡ Replace fuel container if it starts to rust. Rust and/or dirt in fuel can cause problems if it'sused with this unit.﹡ Store unit in a clean and dry area.TROUBLESHOOTINGWIRING DIAGRAM。