2020年整理福特-8D工作法.pdf
福特-8D培训教材
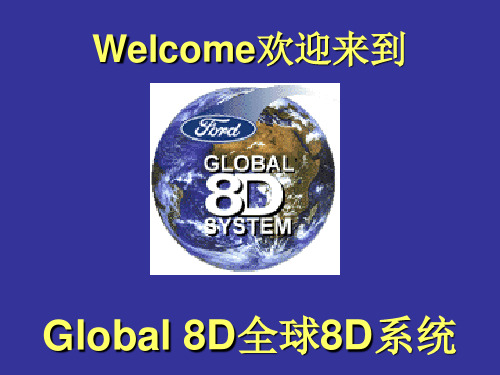
课程内容
章节 8D程序及分析工具综述 DO 全球8D程序的准备 D1 创建工作团队 D2 故障描述 D3 发展 ICAs D4 定义并验证根本起因和忽略点 D5 选择并确认永久性改正行动 D6 执行并验证永久性改正行动 D7 预防错误的重现 D8 肯定团队及个人的贡献
页数 6 24 51 74 110 134 162 203 228 246
Welcome欢迎来到
Global 8D全球8D系统
Course Content
Section
Page
Overview of the 8D process & analysis tools 6
DO Prepare for G8D process
24
D1 Establish the team
51
D2 Describe the problem
• Problem-Solving Worksheet, to help G8D teams to work through the G8D process. 故障解决工作表 帮助G8D小组完成G8D过程
• G8D Web application / Lotus Notes IC8D to track the status and progression of a G8D. G8D环球网应用软件/Lotus Notes IC8D 跟踪G8D进行 状况和级数
• The deviation might be ongoing, intermittent, or a onetime event (where there is always the potential it can reoccur). 这种背离也许会持续、间断或者仅仅是一次事件 (在潜在的某个位置会重新发生)
福特-8D工作法

8D报告百科名片8D又称团队导向问题解决方法、8D问题求解法(8D Problem Solving)是福特公司处理问题的一种方法,亦适用于制程能力指数低於其应有值时有关问题的解决,它提供了一套符合逻辑的解决问题的方法,同时对於统计制程管制与实际的品质提升架起了一座桥梁。
简介8D最早是美国福特公司使用的经典质量问题分析手法。
二战期间,美国政府率先采用一种类似8D的流程——“军事标准1520”,又称之为“不合格品的修正行动及部署系统”。
1987年,福特汽车公司首次用书面记录下8D法,在其一份课程手册中这一方法被命名为“团队导向的问题解决法”(Team Oriented Problem Solving)。
当时,福特的动力系统部门正被一些经年累月、反复出现的生产问题搞得焦头烂额,因此其管理层提请福特集团提供指导课程,帮助解决难题。
问题解决8步法8D(8 Disciplines)问题解决8步法8D的原名叫做8 Disciplines,意思是8个人人皆知解决问题的固定步骤。
原始是由Ford公司,全球化品质管制及改善的特殊必备方法,之后已成为QS9000/ISO TS16949、福特公司的特殊要求。
凡是做FORD 的零件,必须采用8D 作为品质改善的工具,目前有些企业并非FORD的供应商或汽车业的合作伙伴,也很喜欢用这个方便而有效的方法解决品质问题,成为一个固定而有共识的标准化问题解决步骤。
Discipline 1. 成立改善小组(Form the Team):由议题之相关人员组成,通常是跨功能性的,说明团队成员间的彼此分工方式或担任的责任与角色。
Discipline 2. 描述问题(Describe the Problem):将问题尽可能量化而清楚地表达,并能解决中长期的问题而不是只有眼前的问题。
Discipline 3. 实施及确认暂时性的对策(Contain the Problem):对于解决D2 之立即而短期行动,避免问题扩大或持续恶化,包含清库存、缩短PM时间、加派人力等。
福特-8D工作法PDF.pdf

8D报告百科名片8D又称团队导向问题解决方法、8D问题求解法(8D Problem Solving)是福特公司处理问题的一种方法,亦适用于制程能力指数低於其应有值时有关问题的解决,它提供了一套符合逻辑的解决问题的方法,同时对於统计制程管制与实际的品质提升架起了一座桥梁。
简介8D最早是美国福特公司使用的经典质量问题分析手法。
二战期间,美国政府率先采用一种类似8D的流程——“军事标准1520”,又称之为“不合格品的修正行动及部署系统”。
1987年,福特汽车公司首次用书面记录下8D法,在其一份课程手册中这一方法被命名为“团队导向的问题解决法”(Team Oriented Problem Solving)。
当时,福特的动力系统部门正被一些经年累月、反复出现的生产问题搞得焦头烂额,因此其管理层提请福特集团提供指导课程,帮助解决难题。
问题解决8步法8D(8 Disciplines)问题解决8步法8D的原名叫做8 Disciplines,意思是8个人人皆知解决问题的固定步骤。
原始是由Ford公司,全球化品质管制及改善的特殊必备方法,之后已成为QS9000/ISO TS16949、福特公司的特殊要求。
凡是做FORD 的零件,必须采用8D 作为品质改善的工具,目前有些企业并非 FORD 的供应商或汽车业的合作伙伴,也很喜欢用这个方便而有效的方法解决品质问题,成为一个固定而有共识的标准化问题解决步骤。
Discipline 1. 成立改善小组(Form the Team):由议题之相关人员组成,通常是跨功能性的,说明团队成员间的彼此分工方式或担任的责任与角色。
Discipline 2. 描述问题(Describe the Problem):将问题尽可能量化而清楚地表达,并能解决中长期的问题而不是只有眼前的问题。
Discipline 3. 实施及确认暂时性的对策(Contain the Problem):对于解决 D2 之立即而短期行动,避免问题扩大或持续恶化,包含清库存、缩短PM时间、加派人力等。
福特-8D工作法
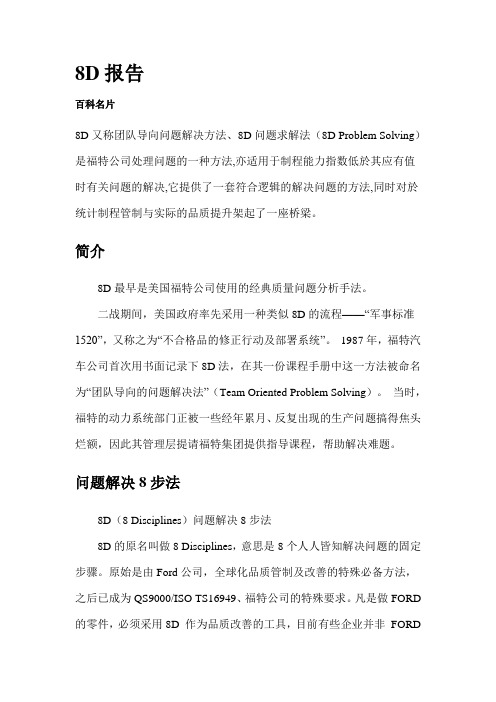
8D报告百科名片8D又称团队导向问题解决方法、8D问题求解法(8D Problem Solving)是福特公司处理问题的一种方法,亦适用于制程能力指数低於其应有值时有关问题的解决,它提供了一套符合逻辑的解决问题的方法,同时对於统计制程管制与实际的品质提升架起了一座桥梁。
简介8D最早是美国福特公司使用的经典质量问题分析手法。
二战期间,美国政府率先采用一种类似8D的流程——“军事标准1520”,又称之为“不合格品的修正行动及部署系统”。
1987年,福特汽车公司首次用书面记录下8D法,在其一份课程手册中这一方法被命名为“团队导向的问题解决法”(Team Oriented Problem Solving)。
当时,福特的动力系统部门正被一些经年累月、反复出现的生产问题搞得焦头烂额,因此其管理层提请福特集团提供指导课程,帮助解决难题。
问题解决8步法8D(8 Disciplines)问题解决8步法8D的原名叫做8 Disciplines,意思是8个人人皆知解决问题的固定步骤。
原始是由Ford公司,全球化品质管制及改善的特殊必备方法,之后已成为QS9000/ISO TS16949、福特公司的特殊要求。
凡是做FORD 的零件,必须采用8D 作为品质改善的工具,目前有些企业并非FORD的供应商或汽车业的合作伙伴,也很喜欢用这个方便而有效的方法解决品质问题,成为一个固定而有共识的标准化问题解决步骤。
Discipline 1. 成立改善小组(Form the Team):由议题之相关人员组成,通常是跨功能性的,说明团队成员间的彼此分工方式或担任的责任与角色。
Discipline 2. 描述问题(Describe the Problem):将问题尽可能量化而清楚地表达,并能解决中长期的问题而不是只有眼前的问题。
Discipline 3. 实施及确认暂时性的对策(Contain the Problem):对于解决D2 之立即而短期行动,避免问题扩大或持续恶化,包含清库存、缩短PM时间、加派人力等。
ford-G8D福特公司8D培训资料

• 让小组和领导以任务为中心 • 提供质量担保检查 • 作为高级的组织者 • 在过程中进行临时检查 • 确定需要什么资源和何时需要 • 完成G8D的检查表手册
2021/3/7
CHENLI
17
D0准备G8D
• 总结:
• 有时需要不止一个ERA来完全保护我们的 顾客。例如,一个ERA用来保护顾客,另 一个用来保护他们免受第一个ERA带来的 副作用。
2021/3/7
CHENLI
11
D0 准备G8D
• 紧急反应行动的选择和核实
– 为确保ERA能保护顾客,需要验证ERA。当您验证 ERA时,要在行动执行前证明ERA能够保护顾客并不 会产生新的问题。
– 从观测到结论的流向就像单行道街,看起来不能返回。 一旦结论达到了,对大多数人来说从新检查是极端困 难的。作为问题的解决者,您必须认识到您在路的哪 一边并在合适的时候跨过线。
2021/3/7
CHENLI
28
D2 描述问题
• 怎样描述问题
– 问题陈述 – 问题描述
• 问题陈述
– 问题陈述是确定未知原因引起的问题的对象和缺陷 的简单、简明的陈述。
G8D
• G8D 概述 • G8D 课程的目标 • G8D 过程概述 • G8D 过程介绍 • GI
1
G8D概述
• G8D是福特公司解决问题的标准方法。 • 由8个步骤和一个准备步骤组成。 • 这些步骤用来客观地确定、定义和解决问
题并防止相似问题的再次发生。
2021/3/7
– 建立小组是G8D过程的基本部分。极少有一个 人具有所有需要的资源、资料和技能来解决一 个复杂的问题。另一方面,一组合适的人员能 够包括所有必须的资源和聚集每一个人所具有 的技能。
福特(Ford)8D培训教材

也不要写工作报告
Page 10 of 47
成员包括:
❖ 指导员(CHAMPION) 一般为主管阶层,对小组的进度有 监督, 支持及决策决定 权力.
❖ 组长(LEADER)-负责协调,活动进行的引导,汇总小组的意 见及决策并呈报,尽量不要深入某部份细节,以免迷失方向.
❖ 问5次为什么的做法:
➢对于某个问题,为何会引起?其原因①先搞明白。 ➢为何会引起原因①的发生?将原因②也搞清楚。 ➢为何会引起原因②的发生?将原因③弄明白。 ➢为何会引起原因③的发生?将原因④弄明白。 ➢为何会引起原因④的发生?将原因⑤弄明白。
Page 20 of 47
❖ 用这种方式持续地去做,根本的原因就能显現出来。 ❖ 分析出来的根本的原因必须是能导出具有効果、
且有効率的再发防止对策才行。 ❖ 要注意的是问题发生的原因不一定只有一个。
❖ 通常第一个答案不会是真正的答案 ❖ 5 Why 可以找出真正的原因 ❖ 简单的案子可能4Why,3Why或2Why即找出根本原
因,但复杂的或许要5 Why, 6 Why, 7 Why…
Page 21 of 47
做5 Why 分析时应注意事项
因会影响结果时,不能说有因果关系)。
Page 23 of 47
5 Why 范例: 为何停机
❖ 问1:为什么机器停了? 答1:因为机器超载, 保险丝烧断了
❖ 问2:为什么机器会超载? 答2: 因为轴承的润滑不足
❖ 问3:为什么轴承会润滑不足? 答3: 因为润滑系统失灵了
❖ 问4: 为什么润滑系统会失灵? 答4: 因为润滑系统的轮轴耗损了
8D工作方法
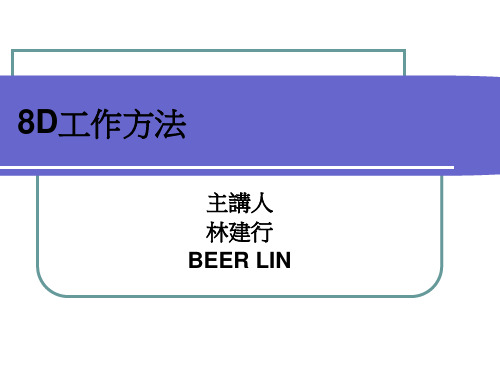
8D工作方法主要步驟 ~D8:小組祝賀
關鍵要點: 有選擇的保留重要文檔 流覽小組工作,將心得形成文件 瞭解小組對解決問題的集體力量,及
對解決問題作出的貢獻 必要的物質、精神獎勵。
生活中的辛苦阻挠不了我对生活的热 爱。20.12.3120.12.31Thursday, December 31, 2020
让自己更加强大,更加专业,这才能 让自己 更好。2020年12月下 午11时25分20.12.3123:25Dec ember 31, 2020
这些年的努力就为了得到相应的回报 。2020年12月31日星 期四11时25分40秒23:25:4031 December 2020
科学,你是国力的灵魂;同时又是社 会发展 的标志 。下午11时25分40秒 下午11时25分23:25:4020.12.31
8D工作方法主要步驟 ~D1:小組成立
目的:
成立一個小組,小組成員具備工藝/產品的 知識
有配給的時間並授予了許可權 同時應具有所要求的能解決問題和實施糾
正措施的技術素質。 小組必須有一個指導和小組長。
8D工作方法主要步驟 ~D1:小組成立
關鍵要點: 成員資格,具備工藝、產品的知識 目標 分工 程式 小組建設
制定一個實施永久措施的計劃 確定過程式控制制方法並納入文件 以確保根本原因的消除。 在生產中應用該措施時應監督其長期效果
方法:
防錯、統計控制
8D工作方法主要步驟 ~
D6:實施永久糾正措施
關鍵要點: 重新審視小組成員 執行永久糾正措施,廢除臨時措施
利用故障的可測量性確認故障已經排除
控制計劃、工藝文件修改
用的數據的總結 審核現有數據,識別問題、確定
福特公司8D的培训资料
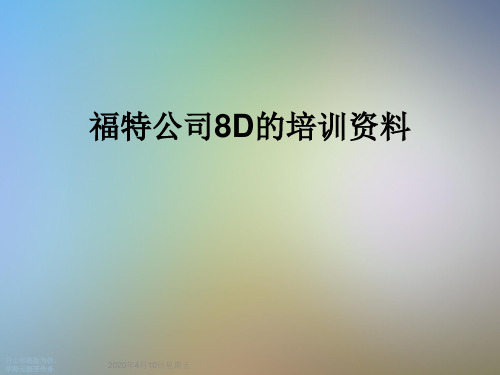
Symptoms vs. Problems
Symptoms 是显示一个或多个问题存在 的可测量的事件或结果。
Problems 是期望值的偏差,或未知原 因引起的任何有害作用。
Symptoms 是 Problems 的表现。 没有Symptoms 就不知道有 Problems
。 D0帮助我们对Symptoms 作出反应
书山有路勤为径, 学海无涯苦作舟
D0工具
当我们启动G8D时,只有Symptoms 是可以估 量或量化的。如果我们不能估量Symptoms 反应了我们没有足够的信息和充分的理由可以 启动G8D。
量化Symptoms 的数据可以从已有的数据中 得到,如保修量或保修费用,顾客满意度评估 等。也可以从其他方法来量化Symptoms。
规范等)。 因为ERA验证通常以常识为基础,很难用量化来
验证。如根据常识,对受到影响的产品停止发 运时,顾客就不会再受到影响。
书山有路勤为径,在起作用。
证实就是提供ERA运行时达到了预期目 的而又没产生新问题的有关证据。
两种验证方法: 到达顾客前的验证:测试、检查、观察
(Permanent Corrective
Actions)并客观地防止问题再发的过程。
G8D致力于寻找问题的根源、实施永久性对策 ,促进制造系统的不断改进。
一个有效的8D的实施不但可以解决问题、保护 顾客、还可以防止问题再发、有效提高产品质 量、提高顾客满意度、促使整个福特系统向世 界领先的汽车制造业迈进。
书山有路勤为径, 学海无涯苦作舟
柏拉图pareto chart
柏拉图依据费用、频率或总变差将所有的潜在 问题区域或来源作了分类。如少数问题占据了 绝大多数的费用或变差,则解决问题的精力就 要集中到这些主要原因上来。
8D工作方法与解决问题的技巧(pdf 128页)

青岛圣思企业管理有限公司
8D适用范围
• 该方法适用于解决各类可能遇到的简单或复杂的问题; • 8D方法就是要建立一个体系,让整个团队共享信息,努
力达成目标。 • 8D本身不提供成功解决问题的方法或途径,但它是解决
问题的一个很有用的工具; • 亦适用于过程能力指数低于其应有值时有关问题的解决; • 面对顾客投诉及重大不良时,提供解决问题的方法。 • 8D法是美国福特公司解决产品质量问题的一种方法,曾
品适用、安全和其它特性的要求。
• 产品质量的特性
•
一般工业产品的质量特性大体可分为以下七个方面:
•
(1)物质方面,如物理性能、化学成分等。
•
(2)操作运行方面,如操作是否方便,运转是否可靠、安全等。
•
(3)结构方面,如结构是否轻便,是否便于加工、维护保养和修理等。
•
(4)时间方面,如耐用性(使用寿命)、精度保持性、可靠性等。
•
(5)经济方面,如效率、制造成本、使用费用(油耗、电耗、煤耗)
等。
•
(6)外观方面,如外型美观大方,包装质量等。
•
(7)心理、生理方面,如汽车座位的舒适程度,机器开动后的噪音大小
等。
•
这些质量特性,区分了不同产品的不同用途,满足了人们的不同需要。
人们就是根据工业产品的这些特性满足社会和人们需要的程度,来衡量工业
青岛圣思企业管理有限公司
8D工作方法 青岛圣思企业管理有限公司
青岛圣思企业管理有限公司
目
录
• 1 8D工作方法简介 • 2 8D工作方法的起源 • 3 8D适用范围 • 4 8D的目的与目标 • 5 8D工作方法的运用 • 6 8D工作方法的8个步骤
长安福特8D培训(PDF139页)

Global 8DWelcome课程内容章节:8D过程及分析工具概述D0全球8D过程的准备D1 组建团队D2 陈述问题D3制定ICAs(临时措施)D4 确定并验证根本起因和问题逃出点D5选择并验证PCAs(永久措施)D6 执行并确认PCAs(永久措施)D7 预防问题重现D8 奖励团队及个人的贡献Course Objectives课程目标完成这门课程之后你应该能够:•描述G8D流程的每个步骤•以一个G8D团队成员的身份有效地参与到你的工作中去•帮助福特达到其远景目标:通过提供优秀的产品和令顾客满意的服务成为世界上汽车制造业的主导公司Overview of the G8D Process全球8D过程概述•福特汽车公司解决问题的标准流程•包括8个步骤,再加上一个准备步骤•客观地描述、确定以及解决问题•防止类似的问题再次发生Phases of the G8D Process全球8D过程的阶段•D0 G8D过程的准备•D1 组建团队•D2 描述问题•D3 制定ICAs(临时措施)•D4 确定,并验证根本原因和问题逃出点•D5选择和验证解决根本原因和遗漏点的永久措施(PCAs)•D6 执行并确认PCAs(永久措施)•D7 预防问题的重新发生•D8 奖励团队及个人的贡献Types of Problem situations问题的类型问题有两种类型:•变异引起的问题•从未满足要求的问题Summary 总结•G8D过程概述•G8D过程的阶段•问题的类型D0D0 –“准备G8D”•描述紧急反应措施•确定是否需要紧急反应措施•区别验证和确认•选择、验证、执行以及确认紧急反应措施•确定是否使用G8D过程来解决问题紧急反应措施(ERA)是保护顾客及相关的各方不受症状影响的任何措施,它在确认G8D是否有必要启动时应用。
Emergency Response Actions 紧急反应措施Problems vs. symptoms问题与症状•G8D把症状和问题区分开来•症状是可测量的事件或效果(它们必须是顾客体验到的),它表示一个或多个问题存在•如果没有症状,你就无法得知有问题存在Using Tools to Measure andQuantify Symptoms使用工具测量并量化症状•当症状能被测量或量化时,它才被考虑在内•在福特,通常有许多工具可以用来测量并量化故障---Paynter Chart / Paynter图---Pareto /柏拉图---Run (trend) chart / 运行(趋势)图Paynter charts / Paynter图•帮助追踪一个或多个症状•显示产品作用的效果•以图形或数据表格的形式表示Pareto柏拉图•柏拉图根据成本或是频率将所有潜在问题区域或是问题源排列出来•柏拉图有助于将几个重要数据从一列琐碎的数据中挑选出来Run (Trend) Chart趋势图•趋势图提供了过程随时间变化的信息•趋势图用来辨别数据变化趋势或数据变化状况Determine the need for an ERA确定是否需要ERA•ERA不是一直都必须•应该根据问题的严重性和它对顾客产生的影响来决定是否需要采取ERA•它是基于目前现有的信息而制定的措施•它可能是大到影响停止所有发运,也可能是小到什么都不用做•它是一个须立即执行的措施——你不必花太多时间来研究应急措施(ERA)Select and Verify an ERA选择并验证ERA•为确保ERA可以保护顾客,需要对他进行验证以保证按照期望的方式工作并且还不会产生新的失效模式•你可以在非生产件如样件或是通过计算机模拟的方式对一个ERA进行验证Implement & Validate of an ERA执行并确认ERA在顾客之前的确认包括:•测试•检查•观察•产品和过程中的质量检查顾客确认包括:•三包分析(Paynter图)G8D Application CriteriaG8D的适用标准要实施G8D需要满足七个标准:1.症状被定义2.确定了顾客3.存在性能差距4.原因未知5.管理层致力于从根本起因的层面去解决问题,并采取预防措施防止问题再次发生6.症状很复杂,不可能单凭一个人的能力完成7.问题在别的场所没有发生D0 Summary: /D0总结Prepare for Global 8D/ 准备G8D在这一阶段我们关注了:•用G8D的应用标准来判断是否需要采用G8D来解决问题•选择、验证、实施并确认ERAD1D1 –“Establish the Team”D1-组建团队为什么组建团队?•建立一个团队是G8D过程的真正开始•D1阶段的目的是组建一个团队,并且这个团队有能力和激情去解决一个问题Guidelines for Team Membership团队成员的指导方针当确定团队成员时:•团队成员的人数控制在4到10个之间•选择具有所需技能、知识、资源、权力等,这样的人作为团队成员来解决现有的问题•各类成员之间合理搭配•按需要调整团队成员Team Roles团队角色•团队成员应该以高效率的方式工作•G8D的过程依赖于所有团队成员的努力来达到团队的目标•为达到团队目标,每个成员扮演一个角色The Champion负责人•负责人是一个有权制定(和执行)关于临时措施、永久措施和预防措施的人,他/她在整个过程中支持团队解决问题The Champion负责人•设置优先权•指派团队完成G8D•帮助团队排除部门之间的障碍、获取需要的资源•创造授权环境•与团队一起评估检查清单•行使权利执行团队的建议•作为G8D团队和组织的联系点•转递G8D报告给有关的部门•负责人应该主持第一个会议说明这里需要的是么和对团队的期望是什么The Team Leader团队领导•团队领导是一个在整个G8D过程中负责领导团队成员的人,这个人有领导能力和人际关系的技能The Team Leader团队领导•领导团队成员完成G8D目标•担当团队的事务管理者•与团队一起制定目标和任务•询问和总结团队成员的意见•提出会议和团队活动的议程•主持会议•对G8D过程提出问题(不提供答案)•依照已制定的团队规则管理团队•作为主要联系点支持负责人The Team Member团队成员•团队成员是那些因为自己的经验和知识而被选中参加G8D团队的人,他们是各方面的专家,在团队里可以不履行其他的职责,在G8D过程中团队成员可能会改变The Team Member团队成员•进行调查工作•提出计划•使用他们的判断力、技能、经验和知识•找出答案•在每个G8D步骤提出建议•执行措施Other Roles其它角色•时间管理者•抄写员•调解员Guidelines for Implementing Team Roles实现团队角色的指导方针•角色不是特指某个人,而是指要行使的职责•成员通常要在会议持续期间或是更长的时间内充当某个固定的角色•会议中角色的互换会导致混乱•一些角色是可以共同扮演的•当一个团队领导人提出一项评论时,她或他就自动的偏离了领导这个角色•Champion是G8D流程中的一个角色但不认为是一个团队成员Team Operating Procedures团队运作程序团队运作程序的三个要素:•确定团队运作的基本规则•分配任务、维护和过程观察•使用有效沟通交流的技巧D1 Summary / D1总结本章节我们介绍了如何:•描述确定团队成员的原则•描述团队角色和职责、以及它们如何发挥作用•解释团队运作流程的三个要素D2D2 –“Describe the Problem”D2-“描述问题”•D2驱动G8D的其他步骤,因为在D2中,将问题清楚并且客观的描述会使问题最终得到有效的解决•D2帮助团队将焦点放在实际的问题上,避免直接对问题下结论或者作没有根据的设想D2 Section ObjectivesD2阶段目标•解释描述问题的流程•识别与问题相关的流程图•对问题进行陈述•对问题进行描述•作为描述问题的数据库•驱动了G8D的其他阶段D2 阶段帮助你将焦点放在现有问题上,以避免非常低的效率解决问题:•它帮助你尽可能准确的定义问题Why Describe the Problem?为什么要描述问题?Observations vs. Conclusions观测与结论当你描述一个问题时,你只是观测还是得出了结论?这两者是有很大的区别。
8D工作方法-1

互信任;
25
管理成功团队的六种方法:
让管理成为一种生活方式,要天天做; 确保你的下属能够见到你; 如果需要,定期与下属进行座谈 ; 不要放弃任何肯定别人成绩的机会; 批评过错,需要批评时要立即去做; 保持铁的纪律 。
方法:质量风险评定,FMEA分析 关键要点:
收集和组织所有有关数据以说明问题 问题说明是所描述问题的特别有用的数据的总结 审核现有数据,识别问题、确定范围 细分问题,将复杂问题细分为单个问题 问题定义,找到和顾客所确认问题一致的说明, “什么东西出了什么问题”,而原因又未知 风险等级
8
D3:实施并验证临时措施
5
D
二 、 D1:小组成立
D2:问题说明
8 D3:实施并验证临时措施 主 D4:确定并验证根本原因 要 D5:选择和验证永久纠正措施 步 D6:实施永久纠正措施 骤 D7:预防再发生
D8:小组祝贺
8D法流程图
6
D1:小组成立
ቤተ መጻሕፍቲ ባይዱ
跨部门团队 (CrossFunction
Team:参与解决问题的所有成员所组成的集体。 Team,CFT)
17
三、8D与其他工具方法
5W2H法
DMAIC改进模型、七步骤法
PDCA循环 QC成果1 QC成果2
18
四、8D报告、表单说明
8D报告 ANPQP–关注及对策要求 ANPQP–防止再发生对策报告书 七步工作法 一元管理表
19
五、顾客要求
(福特、 组织)
六、案例分析
( 案例-日1 案例-日2 ) ( 案例-法1 )
4)跨部门团队的工作过程有前后联系和逻辑顺序,对 预定目标的进度要求很高。
福特公司8D的培训资料

8
ERA的实施基于我们得到的信息; 根据问题的种类、成本因素、问题严重
程度以及顾客的抱怨程度ERA的实施多 种多样,小到可以什么都不做,大到可 以停止发运; ERA的实施要求迅速有效。
9
选为择验了、证确。保验E证RA并的实实施施能应够急保护措顾施客(,E必R须A进)行
21
成员角色
一旦G8D团队成员被选中,必须尽力、 有效的发挥作用。G8D过程依赖于团队 成员的努力去达到团队目标(解决问题 ),因此,每个成员应履行相应角色。
每一角色都相互依靠,没有一个可独自 完成。
22
The Champion
是执行ICA、PCA和预防措施的权威人,在 整个8D过程支持团队解决问题(协调作用) 。
在量化Symptoms 前,我们得考虑问题的严 重性,如果严重,在启动ERA时收集数据。
下面具体介绍几种量化Symptoms 的工具。
14
培恩图Paynter chart
培恩图可以量化我 们在G8D过程中采 取行动后的影响 。
Vehicle Instrument Panel
培恩图可以用来跟 踪产生同一症状的 一个或多个问题, 以及各种联合措施 的验证。
●D0让我们根据应用标准,正确启动 G8D。
●D0让我们定义、验证并实施ERA,以
保护顾客,维持我们产品的顾客满意度
。
7
应急措施(ERA)?
ERA是我们在决定采取G8D前采取的一 种保护顾客的不受问题影响的任何行动 。
有时针对同一问题点,可以有多个以及 连环的ERA (如一个ERA保护顾客, 另一个ERA消除第一个ERA的负面影响 ),其目的是充分的保护顾客。
8D方法(Ford版)

D5.选择和验证(yànzhèng)基本缘由和 遗漏点的PCA〔续〕
设计(shèjì)验证和报告〔DVP&R〕 FMEA 稳健设计(shèjì)
第十六页,共23页。
D6.实施(shíshī)和确认PCA
• 战略性效果
• 有列出纠正措施的有效性吗?
• 有效性经过验证(yànzhèng)了吗?
第三页,共23页。
8 D(8 Disciplines)(续)
需求时,辅导供方实施整个8D进程以识别系统的基本 缘由:
列出完成8D 进程的工具〔例如:DOE、SPC、 FMEA、散点图、反省单、控制图等等〕;
验证供方运用了适当的工具; 识别当评审8D报告时须讯问的8D进程; 验证供方能否准确执行和文件化8D进程; 确保供方经过启动和封锁效果曾阅历证了基本缘由, 验证供方已完整(wánzhěng)包括一切可疑资料,包括曾经 在装配工厂、运输中、仓库和进程中的零件。
8D方法(fāngfǎ)(Ford 版)
2021/11/9
第一页,共23页。
8 D(8 Disciplines)
福特汽车公司运用8D作为效果处置的方法〔见QS-9000要 求之4.14.1.1〕。当福特的供方具有零件或进程的效果时, 福特要求供方完成8D进程以确定缘由并实施纠正措施 (cuòshī)。 目的:
第十三页,共23页。
D4.定义和验证基本(jīběn)缘由和遗漏 点〔续〕
效果,或效果的征兆或结果被作为基本缘由给出。 质量工具
因果(yīnguǒ)图 FMEA 是/否剖析 实验验证〔DOE〕 稳健设计
第十四页,共23页。
D5.选择和验证基本(jīběn)缘由和遗漏 点的PCA
• 战略性效果 • 措施的日期(rìqī)能否指示? • 声明的措施能否掩盖一切进程的基本缘由? • 声明的措施能否掩盖一切系统的基本缘由? • 措施能否思索效果的时间? • 措施能否充沛思索条件? • 措施能否思索效果的大小? • 质量工具 • 因果图
福特8D问题解决方法

福特8D问题解决方法主办:上海普瑞思管理咨询有限公司时间:2010年3月12-13日(2天)地点:上海收费标准:¥2800 /人(含授课费、资料费、会务费、午餐费),三人以上团队¥2520/人课程目标:所谓8D方法 (eight disciplines),又称团队导向问题解决步骤,是福特公司处理问题的一种方法。
a) 此方式是团队运作导向以事实为基础,避免个人主见的介入,使问题的解决能更具条理。
b) 此方式宜由公司各部门人员的共同投入,求得创造性及永久性的解决方案。
c) 此方式可适用于任何问题,而且能促进相关目标的各部门间有效的沟通。
授课对象:企业中高层管理人员、企业品质管理人员、企业生产管理人员。
培训内容:1. 解决问题的概念和特征什么是问题什么是解决问题有效/无效解决问题的特征是什么2. 成立小组:问题解决团队建设简介解决问题的团队建设问题解决小组的活动特点如何确保小组的成功3. 解决问题的结构化模式及工具鉴别和选择问题---鉴别问题区域,明确定义问题课题的三个来源如何自选课题如何定义问题头脑风暴法---广泛的收集创新观念把握现状---找出问题症结为什么要把握现状如何把握现状找出问题症结层别法---找出问题症结柏拉图---找出问题症结以客户的实际问题来进行层别法和柏拉图练习与评点鉴别根本原因---鉴别和评估各种可能的原因鱼骨图---鉴别问题潜在的各种原因以客户的实际问题来进行鱼骨图练习与评点故障树分析(FTA)---如何找到问题的根源故障树练习与评点发展多种解决方案---寻找并鉴别多种问题解决方案系统图---复杂原因和措施的探究以客户的实际问题来进行系统图练习与评点筛选方案,制订行动计划---根据确定的标准筛选方案,制订详细的行动计划(预计的效果和可测量的监控措施等)决定矩阵---比较和评估可选择方案的工具以客户的实际问题来进行决定矩阵联习与评点目标设定的SMART原则甘特图(行动计划表)---规范工作安排的工具以客户的实际问题来进行甘特图练习与评点执行解决方案---严格按照计划执行方案SPC统计过程控制图 ---监控过程的变异波动是否稳定的工具SPC控制图种类平均极差控制图的画法平均极差控制图的分析方法其他种类的控制图简介以客户的实际问题来进行控制图的练习与评点效果评估标准化---评估结果,确保有效;标准化小组活动发表---泛化,效果最大化过程文件化――FMEAFMEA的意义FMEA的种类DFMEA和PFMEA的简介FMEA的应用小组发表的活动形势成功的案例4、总结:8D的八个步骤问题描述遏制症状寻找并验证根本原因选择并验证永久性措施实施并验证永久性措施系统性预防再发生祝贺小组5、结合贵公司实施8D工具案例研究6、结合贵公司实施8D工具案例分析讲师简介:Jack Cao 曹先生曹先生曾任职多家世界500强公司担任技术和管理岗位,如新产品研发、供应商质量管理、质量体系审核、工程主管、技术部经理、生产主管、质量总监等职,并多次接受美国、日本有关生产、质量最新管理方法的培训;曹先生以其丰富的现场管理经验,领导完成多项生产、质量技术改造工程;针对大批量生产的特点,以 PDCA、FMEA、MBF等质量循环为载体在生产线上推行可视质量管理,并达到良好效果;策划和推行以过程为导向的质量有效控制与现场持续改善活动,解决公司产品的关键质量问题,大大提高了产品的合格率。
- 1、下载文档前请自行甄别文档内容的完整性,平台不提供额外的编辑、内容补充、找答案等附加服务。
- 2、"仅部分预览"的文档,不可在线预览部分如存在完整性等问题,可反馈申请退款(可完整预览的文档不适用该条件!)。
- 3、如文档侵犯您的权益,请联系客服反馈,我们会尽快为您处理(人工客服工作时间:9:00-18:30)。
8D报告百科名片8D又称团队导向问题解决方法、8D问题求解法(8D Problem Solving)是福特公司处理问题的一种方法,亦适用于制程能力指数低於其应有值时有关问题的解决,它提供了一套符合逻辑的解决问题的方法,同时对於统计制程管制与实际的品质提升架起了一座桥梁。
简介8D最早是美国福特公司使用的经典质量问题分析手法。
二战期间,美国政府率先采用一种类似8D的流程——“军事标准1520”,又称之为“不合格品的修正行动及部署系统”。
1987年,福特汽车公司首次用书面记录下8D法,在其一份课程手册中这一方法被命名为“团队导向的问题解决法”(Team Oriented Problem Solving)。
当时,福特的动力系统部门正被一些经年累月、反复出现的生产问题搞得焦头烂额,因此其管理层提请福特集团提供指导课程,帮助解决难题。
问题解决8步法8D(8 Disciplines)问题解决8步法8D的原名叫做8 Disciplines,意思是8个人人皆知解决问题的固定步骤。
原始是由Ford公司,全球化品质管制及改善的特殊必备方法,之后已成为QS9000/ISO TS16949、福特公司的特殊要求。
凡是做FORD 的零件,必须采用8D 作为品质改善的工具,目前有些企业并非 FORD 的供应商或汽车业的合作伙伴,也很喜欢用这个方便而有效的方法解决品质问题,成为一个固定而有共识的标准化问题解决步骤。
Discipline 1. 成立改善小组(Form the Team):由议题之相关人员组成,通常是跨功能性的,说明团队成员间的彼此分工方式或担任的责任与角色。
Discipline 2. 描述问题(Describe the Problem):将问题尽可能量化而清楚地表达,并能解决中长期的问题而不是只有眼前的问题。
Discipline 3. 实施及确认暂时性的对策(Contain the Problem):对于解决 D2 之立即而短期行动,避免问题扩大或持续恶化,包含清库存、缩短PM时间、加派人力等。
Discipline 4. 原因分析及验证真因(Identify the Root Cause):发生 D2 问题的真正原因、说明分析方法、使用工具(品质工具)的应用。
Discipline 5. 选定及确认长期改善行动效果(Formulate and Verify Corrective Actions):拟订改善计划、列出可能解决方案、选定与执行长期对策、验证改善措施,清除 D4 发生的真正原因,通常以一个步骤一个步骤的方式说明长期改善对策,可以应用专案计划甘特图(Gantt Chart),并说明品质手法的应用。
Discipline 6. 改善问题并确认最终效果(Correct the Problem and Confirm the Effects):执行 D5 后的结果与成效验证。
Discipline 7. 预防再发生及标准化(Prevent the Problem):确保 D4 问题不会再次发生的后续行动方案,如人员教育训练、改善案例分享(Fan out) 、作业标准化、产出BKM、执行FCN 、分享知识和经验等。
Discipline 8. 恭喜小组及规划未来方向(Congratulate the Team):若上述步骤完成后问题已改善,肯定改善小组的努力,并规划未来改善方向。
8D适用范围该方法适用于解决各类可能遇到的简单或复杂的问题;8D方法就是要建立一个体系,让整个团队共享信息,努力达成目标。
8D本身不提供成功解决问题的方法或途径,但它是解决问题的一个很有用的工具;亦适用于过程能力指数低于其应有值时有关问题的解决;面对顾客投诉及重大不良时,提供解决问题的方法。
8D法是美国福特公司解决产品质量问题的一种方法,曾在供应商中广泛推行,现已成为国际汽车行业(特别是汽车零部件产家)广泛采用来解决产品质量问题最好的、有效的方法。
8D工作方法的8个步骤8D是解决问题的8条基本准则或称8个工作步骤,但在实际应用中却有9个步骤:D0:征兆紧急反应措施D1:小组成立D2:问题说明D3:实施并验证临时措施D4:确定并验证根本原因D5:选择和验证永久纠正措施D6:实施永久纠正措施D7:预防再发生D8:小组祝贺D0:征兆紧急反应措施目的:主要是为了看此类问题是否需要用8D来解决,如果问题太小,或是不适合用8D来解决的问题,例如价格,经费等等,这一步是针对问题发生时候的紧急反应。
关键要点: 判断问题的类型、大小、范畴等等。
与D3不同,D0是针对问题发生的反应,而D3是针对产品或服务问题本身的暂时应对措施。
D1:小组成立目的:成立一个小组,小组成员具备工艺/产品的知识,有配给的时间并授予了权限,同时应具有所要求的能解决问题和实施纠正措施的技术素质。
小组必须有一个指导和小组长。
关键要点: 成员资格,具备工艺、产品的知识;目标 ;分工 ;程序 ;小组建设D2:问题说明目的:用量化的术语详细说明与该问题有关的内/外部顾客抱怨,如什么、地点、时间、程度、频率等。
“什么东西出了什么问题”方法:质量风险评定,FMEA分析关键要点:收集和组织所有有关数据以说明问题;问题说明是所描述问题的特别有用的数据的总结;审核现有数据,识别问题、确定范围;细分问题,将复杂问题细分为单个问题;问题定义,找到和顾客所确认问题一致的说明,“什么东西出了什么问题”,而原因又未知风险等级。
D3:实施并验证临时措施目的:保证在永久纠正措施实施前,将问题与内外部顾客隔离。
(原为唯一可选步骤,但发展至今都需采用)方法:FMEA、DOE、PPM关键要点: 评价紧急响应措施;找出和选择最佳“临时抑制措施”;决策 ;实施,并作好记录;验证(DOE、PPM分析、控制图等)D4:确定并验证根本原因目的:用统计工具列出可以用来解释问题起因的所有潜在原因,将问题说明中提到的造成偏差的一系列事件或环境或原因相互隔离测试并确定产生问题的根本原因。
方法:FMEA、PPM、DOE、控制图、5why法关键要点: 评估可能原因列表中的每一个原因;原因可否使问题排除;验证;控制计划D5:选择并验证永久纠正措施目的:在生产前测试方案,并对方案进行评审以确定所选的校正措施能够解决客户问题,同时对其它过程不会有不良影响。
方法:FMEA关键要点: 重新审视小组成员资格;决策,选择最佳措施;重新评估临时措施,如必要重新选择;验证;管理层承诺执行永久纠正措施;控制计划D6:实施永久纠正措施目的:制定一个实施永久措施的计划,确定过程控制方法并纳入文件,以确保根本原因的消除。
在生产中应用该措施时应监督其长期效果。
方法:防错、统计控制关键要点: 重新审视小组成员;执行永久纠正措施,废除临时措施;利用故障的可测量性确认故障已经排除;控制计划、工艺文件修改D7:预防再发生目的:修改现有的管理系统、操作系统、工作惯例、设计与规程以防止这一问题与所有类似问题重复发生。
关键要点:选择预防措施;验证有效性;决策 ;组织、人员、设备、环境、材料、文件重新确定D8:小组祝贺目的:承认小组的集体努力,对小组工作进行总结并祝贺。
关键要点: 有选择的保留重要文档;流览小组工作,将心得形成文件;了解小组对解决问题的集体力量,及对解决问题作出的贡献;必要的物质、精神奖励。
对8D工作方法的评价1.优点发现真正肇因的有效方法,并能够采取针对性措施消除真正肇因,执行永久性矫正措施。
能够帮助探索允许问题逃逸的控制系统。
逃逸点的研究有助于提高控制系统在问题再次出现时的监测能力。
预防机制的研究有助于帮助系统将问题控制在初级阶段。
2.缺点8D培训费时,且本身具有难度。
除了对8D问题解决流程进行培训外,还需要数据挖掘的培训,以及对所需用到的分析工具(如帕累托图、鱼骨图和流程图,等等)进行培训。
[1]参考资料8D报告百科名片8D又称团队导向问题解决方法、8D问题求解法(8D Problem Solving)是福特公司处理问题的一种方法,亦适用于制程能力指数低於其应有值时有关问题的解决,它提供了一套符合逻辑的解决问题的方法,同时对於统计制程管制与实际的品质提升架起了一座桥梁。
目录1.简介8D最早是美国福特公司使用的经典质量问题分析手法。
二战期间,美国政府率先采用一种类似8D的流程——“军事标准1520”,又称之为“不合格品的修正行动及部署系统”。
1987年,福特汽车公司首次用书面记录下8D法,在其一份课程手册中这一方法被命名为“团队导向的问题解决法”(Team Oriented Problem Solving)。
当时,福特的动力系统部门正被一些经年累月、反复出现的生产问题搞得焦头烂额,因此其管理层提请福特集团提供指导课程,帮助解决难题。
问题解决8步法8D(8 Disciplines)问题解决8步法8D的原名叫做8 Disciplines,意思是8个人人皆知解决问题的固定步骤。
原始是由Ford公司,全球化品质管制及改善的特殊必备方法,之后已成为QS9000/ISO TS16949、福特公司的特殊要求。
凡是做FORD 的零件,必须采用8D 作为品质改善的工具,目前有些企业并非 FORD 的供应商或汽车业的合作伙伴,也很喜欢用这个方便而有效的方法解决品质问题,成为一个固定而有共识的标准化问题解决步骤。
Discipline 1. 成立改善小组(Form the Team):由议题之相关人员组成,通常是跨功能性的,说明团队成员间的彼此分工方式或担任的责任与角色。
Discipline 2. 描述问题(Describe the Problem):将问题尽可能量化而清楚地表达,并能解决中长期的问题而不是只有眼前的问题。
Discipline 3. 实施及确认暂时性的对策(Contain the Problem):对于解决 D2 之立即而短期行动,避免问题扩大或持续恶化,包含清库存、缩短PM时间、加派人力等。
Discipline 4. 原因分析及验证真因(Identify the Root Cause):发生 D2 问题的真正原因、说明分析方法、使用工具(品质工具)的应用。
Discipline 5. 选定及确认长期改善行动效果(Formulate and Verify Corrective Actions):拟订改善计划、列出可能解决方案、选定与执行长期对策、验证改善措施,清除 D4 发生的真正原因,通常以一个步骤一个步骤的方式说明长期改善对策,可以应用专案计划甘特图(Gantt Chart),并说明品质手法的应用。
Discipline 6. 改善问题并确认最终效果(Correct the Problem and Confirm the Effects):执行 D5 后的结果与成效验证。