渗碳件质量检查
马氏体级别”的探讨

对《汽车渗碳齿轮金相检验》标准中“马氏体级别”的探讨董秦铮(爱协林工业炉工程(北京)有限公司,北京 100086)摘要:通过生产中的试验例证和检验结果,针对《汽车渗碳齿轮金相检验》标准中“马氏体级别”的概念和评级方法进行了分析和讨论。
认为不宜将“马氏体级别”作为一项独立的质量指标。
关键词:马氏体级别;残留奥氏体;奥氏体晶粒度QC/T262—1999《汽车渗碳齿轮金相检验》是我国汽车行业中长期使用的一项覆盖面较广、影响较大的标准。
在该标准中,“马氏体级别”被作为一项重要的、不可缺少的质量指标。
标准中规定:马氏体等级按其针体大小确定,共分8个级别,评定马氏体级别和评定残留奥氏体级别一样,共同使用一套残留奥氏体、马氏体级别的标准图片(400倍,8张),所评定的结果均在1~5级内为合格。
但是,汽车零部件生产者对“马氏体级别”这一概念一直是有争议的。
争议的焦点集中在马氏体级别的实质概念,马氏体级别超差或合格的依据以及它对产品性能和质量的影响。
在实际生产中,除渗碳淬火工艺外,影响马氏体级别的还有哪些主要因素,如何防止马氏体级别超差,试样的马氏体级别超差后,如何处理等,也常常使人们感到困惑。
本文通过一些试验例证和检验结果,对这些问题进行分析和讨论,并对该标准中将马氏体级别作为一项独立的质量指标的必要性提出质疑。
1渗碳试块和工件的金相检验实例1.1试验工艺表1列举了实际生产中经不同炉次渗碳的试块和工件的金相检验结果。
工件和试块的材料均为20CrMnTi钢。
试验过程如下:①工件与试块同炉,930℃×(6~8)h渗碳,降温至840℃淬油,180℃×2.5h回火。
用金相显微镜按标准图片分别对试块的残留奥氏体和马氏体评级并检查表层奥氏体晶粒度。
将样品浸入80℃的苦味酸+少量洗涤剂混合液,于80℃浸泡腐蚀。
按YB/T5148-1993《金属平均晶粒度测定方法》评定表层奥氏体晶粒度。
②上述试验完成后,对同一试块进行冷处理(干冰+酒精,-40℃~-60℃×0.5h)。
热处理特殊外包工艺过程确认检查评价标准

记录以核实是否按委托工艺要求进行热处理作业。对最终检验记录还应进行实地抽验, 要求也被视为严重不合格,不得分。
记录当场测得的数据以确认其保存的记录是否真实、准确、可靠。
存在其他可整改问题,每项酌情扣 1~3 分。
评价准则:
1、 资质确认项目为否决项,出现严重不符合时应更换供应商。 2、 检查确认时其他项目中只允许出现一个严重不符合项,如又出现第二个严重不符合项,则也应考虑更换供应商。 3、检查后合计评分分值≥85 分确认通过;评分分值<70 分为不符合要求,应考虑更换供应商;70≤评分分值<85 分为整改单位,要求限期在 1 个月内将不合格 项目整改完成,第二次确认检查评分分值<85 分的供应商将同样视为不符合要求,应考虑更换供应商;各次检查所有开出的不符合项目均应进行有效整改。
料以证明这些机床是否符合高频、中频、工频表面 淬火的工艺应用频率要求,并查看这些淬火机床的 开机运作状态及相应功能(如自动冷却喷水等),判 断其机床是否处于良好正常运行。
2.3 热处理方法表面发黑工艺必须具备的基本设备: ⑴ 除锈池; ⑵ 去油池; ⑶ 发黑池; ⑷ 皂化池; ⑸ 发黑前后用的若干高温、常温清洗池; ⑹ 用于增加发黑光亮度效果的高温油池。 对照供应商提供的发黑工艺流程判断发黑处理
行有效控制。
第 2 页 共3页
热处理特殊外包工艺过程确认检查评价标准
热处理工艺过程(常规热处理:调质、淬火、渗碳、表面发黑等)
项目分类
检查内容和方法
评分标准
满分分值
4 确认供应商
4.1 检测设施确认:
的检测 能力满
⑴ 是否具备基本的硬度测试仪器;
所有检查内容符合要求,给予满分。
足工艺 过程要 求
⑵ 加热炉自动温控记录仪; ⑶ 人工操控的仪器(如测温、金相、化学分析等)。 ⑷ 各检测仪器设备是否检定合格有效并有相应检定证明。
金相组织检验标准与质量判定
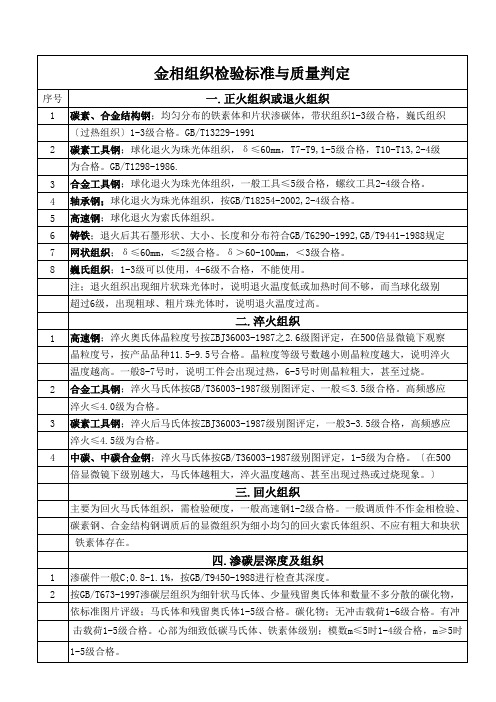
淬火≤4.5级为合格。
4 中碳、中碳合金钢;淬火马氏体按GB/T36003-1987级别图评定,1-5级为合格。〔在500 倍显微镜下级别越大,马氏体越粗大,淬火温度越高、甚至出现过热或过烧现象。〕
三.回火组织
主要为回火马氏体组织,需检验硬度,一般高速钢1-2级合格。一般调质件不作金相检验、
碳素钢、合金结构钢调质后的显微组织为细小均匀的回火索氏体组织、不应有粗大和块状
3 合金工具钢;球化退火为珠光体组织,一般工具≤5级合格,螺纹工具2-4级合格。 4 轴承钢;球化退火为珠光体组织,按GB/T18254-2002,2-4级合格。 5 高速钢;球化退火为索氏体组织。 6 铸铁;退火后其石墨形状、大小、长度和分布符合GB/T6290-1992,GB/T9441-1988规定
1-5级合格。
五.感应加热淬火淬硬层及组织
淬硬层金相组织检验在400倍显微镜小,在零件表面0.5mm处进行评定。按JB/T9204-1999 共分10级;1-2级过热〔粗、较粗马氏体〕,3-7级合格〔细、较细马氏体〕,8-10级加热 不足。〔微细马氏体+网络状极细珠光体+未溶铁素体〕均与标准图片对比评定。 注;HRC≥55时 3-7级合格,HRC<55时 3-9级合格。﹙JB/T9204-1999﹚
7 网状组织;δ≤60mm,≤2级合格。δ>60-100mm,<3级合格。
8 巍氏组织;1-3级可以使用,4-6级不合格,不能使用。 注;退火组织出现细片状珠光体时,说明退火温度低或加热时间不够,而当球化级别
超过6级,出现粗球、粗片珠光体时,说明退火温度过高。
二.淬火组织
1 高速钢;淬火奥氏体晶粒度号按ZBJ36003-1987之2.6级图评定,在500倍显微镜下观察
渗碳炉操作规程1

渗碳炉操作规程
1、检查提升炉盖机构动作、控制仪表是否正常,检查渗碳剂是否够用,确保线路及电器无故障。
2、检查待渗工件的外观质量,了解工件的渗碳技术要求和渗碳部位,确定防渗措施。
3、在对炉盖的操作时,一人扶着悬臂手柄(防止炉盖左右移动,撞坏氧探头),一人操作按钮,并对炉盖的行动位置进行密切关注。
(本炉所有动作设有互锁,炉盖没关好不能加热。
)
4、加热,加热前必须先开冷却水、开循环风机;根据工艺要求在仪表设置加热工艺参数并运行仪表。
开主令开关,工作指示灯亮,如果不亮可能是炉盖没有关好或线路故障。
5、在炉子整个工作过程中,要求操作员对系统密切关注,定期巡检,检查渗碳温度、碳势、渗碳剂的滴量、废气火焰颜色及长度是否符合工艺要求。
6、排出的废气应点燃,火焰颜色呈浅黄色,火焰应稳定,保持80~100mm长度;炉内压力保持恒定,一般为1960 ~ 4910Pa。
7、工艺结束后,炉温超过150℃时禁止关冷却水、关风机。
设备运行中严禁停冷却水,否则会损坏冷却水套和循环风机;冷却水出水口水温不得超过65℃,当出现任何意外事项时,请立即把总电源关闭。
8、煤油、甲醇属于易燃品,操作时请注意。
700℃以下禁止向炉内滴入甲醇,否则易发生爆炸事故。
9、如果设备长期不用请关闭总电源。
链条原材料及热处理加工的检验和评定标准
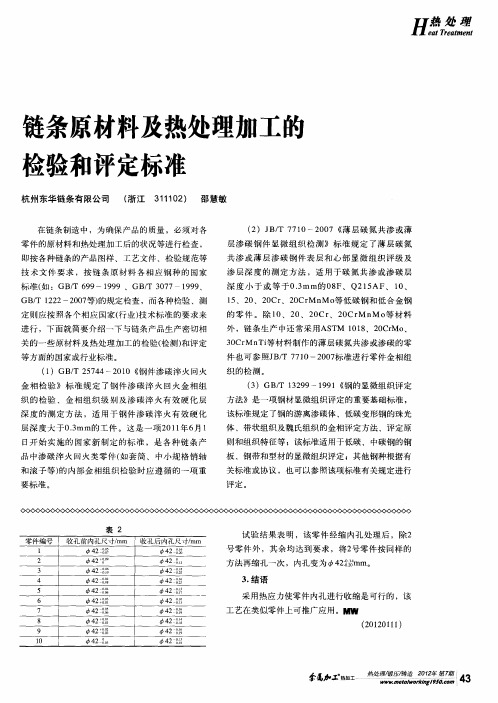
缺陷。根据 供需双方协议 ,也可用作评定其他钢类
低倍 组 织 的缺 陷 。
耐磨性能和整链抗拉强度等性能,通常链条原材料
检验规范 中都对表面脱碳 层规定了深度的要求 ,而 如何测定脱碳层深度则需遵照G / 2 —2 0 标准 BT2 4 0 8
标准适用于渗碳和碳氮共渗淬火硬化 层;并经最终 热处理 后 ,距表面3 于淬火硬化 层深度处硬度值 倍
小于 4 0 V的零 件 。不 能 满足 上 述 条件 的 钢 件 ,应 5H
T 5 7 —2 0 低、 中碳钢球化体评级》 、J / 0 4 0 7 BT 9 1 —2 0 中碳钢与 中碳 合金结构钢马 氏体等 21 08
链条原材料及热处理加工的
检验和评定标准
杭 州东华链 条有限公 司 ( 江 浙 3 1 0 ) 邵 慧敏 1 1 2
在 链 条制 造 中 ,为 确保 产 品的 质 量 ,必须 对 各 零 件 的原 材 料 和 热处 理 加 工 后 的状 况 等 进 行检 查 , 即 按 各种 链 条 的 产 品 图样 、工 艺 文件 、检 验规 范等 技 术 文 件 要 求 ,按 链 条 原 材 料 各 相 应 钢 种 的 国家 标 准 ( :G / 9 —19 、GBT 3 7 —19 、 如 BT69 99 / 0 7 9 9
( )J / 7 0 0 7 薄层碳氮 共渗或薄 2 B T 7 1 —2 0
层 渗 碳 钢 件 显 微 组 织 检 测 ) 准 规 定 了薄 层 碳 氮 )标
共渗或薄 层渗碳 钢件表 层和心部 显微组织 评级及
渗 层 深 度 的 测 定 方 法 ,适 用 于 碳 氮 共 渗 或 渗 碳 层 深 度 小 于 或 等 于 03 .mm的 0 F Q 1 AF 1 、 8 、 2 5 、 0
钢的渗碳热处理
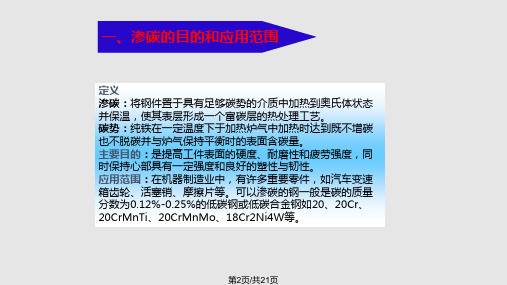
20钢 4%硝酸酒精 500× 渗碳后空冷
表层全脱碳,白亮部分为铁素体 次表层为部分脱碳层,即珠光体+少量铁素体
过渡区为珠光体+铁素体(白色网块)
第18页/共21页
20钢 4%硝酸酒精 150× 渗碳后淬火
表层脱碳,次表层也略有脱碳层,冷却不足 马氏体+屈氏体
第19页/共21页
2.回火 渗碳件淬火后尚需进行低温回火,回火温度通常为150~190℃。 3.冷处理 作用是减少或消除残余奥氏体,从而适当提高渗层硬度。由于冷处 理生产成本高,又增加了工序,目前生产中除特殊渗碳零件外,一般很少采用。
第12页/共21页
20钢 4%硝酸酒精 500× 930℃气体渗碳8小时,直接淬火 表层组织照片:马氏体+碳化物(白色颗粒)+残余奥氏体
第20页/共21页
感谢您的观看。
第21页/共21页
渗碳层厚度δ
图7 低碳钢渗碳缓冷后的显微组织 第9页/共21页
典型零件渗碳层厚度确定方法
零件种类 轴类 齿轮
薄片工件
渗碳层厚度δ(mm) (0.1~0.2)R (0.2~0.3)m (0.2~0.3)t
备注 R--半径(mm)
m--模数 t--厚度(mm)
第10页/共21页
五、渗碳后的热处理
1.淬火 淬火是为了获得马氏体组织,以得到高硬度。通常有三种方法, 即预冷直接淬火、一次加热淬火和二次加热淬火。渗碳零件淬火温度的 选择要兼顾高碳的渗层和低碳的心部两方面的要求。原则上,过共析层 的淬火温度低于Accm,而亚共析层的淬火温度高于Ac3。如果Accm> Ac3,很容易选择一个淬火温度来同时满足这两者的要求;果Accm≤Ac3, 则很难同时兼顾。在这种情况下,要根据对零件的主要技术要求、钢件 的心部能否淬透、渗碳后零件的表面含碳量和所采用的淬火方法等综合 考虑加以决定。
齿轮钢锻件等温正火质量检验规范

齿轮钢锻件等温正火质量检验规范1. 目的与范围1.1目的为正确评定渗碳齿轮钢钢制锻件及毛坯粗车零件的等温正火硬度均匀性及正火组织级别等相关质量物性,规范和完善公司对齿轮钢锻件等温正火零件的质量检验,特制定本评定规范。
1.2 范围本规定适用于公司及外协等温正火供应商。
2. 具体描述2.1等温正火质量要求2.1.1渗碳齿轮钢的等温正火硬度要求根据不同的钢材其等温正火硬度要求一般可参照下表1的范围,具体要求须按各工厂制造供应商签定的《零〔部〕件检验标准》执行,但须满足切削加工及热冷变形要求。
表1 公司常用齿轮钢零件的等温正火硬度要求2.1.2渗碳齿轮钢的等温正火金相组织要求按与锻件供应商签订的《零〔部〕件检验标准》或相关文件要求执行,如无相关文件要求则按GB/T13320执行,正火金相组织≤3级评定为合格。
2.2检验内容与方法2.2.1零件状态检查2.2.1.1公司内等温正火检验部门人员以抽查的方式,核对零件名称、材料牌号、操作记录纸的有关内容,以了解生产过程中的工艺执行情况,并作好相关的检查记录。
2.2.1.2外协等温正火检验部门人员核对零件名称、材料牌号、钢的冶炼炉号、钢材质保书及供应商对零件材料的化学成份(要求参见2.3表2),淬透性、低倍组织等复检报告和对零件的金相组织、硬度检测报告等本批产品相关内容,以了解外协正火零件的材料、金相组织及硬度情况,并做好相关的检查记录。
注:对于己批产的产品,其零件锻件的下料规格必须唯一,锻造供应商不得任意更改,但有变更必须向需方提交申请并得到批准后才可执行。
2.2.2外观检查零件正火后并经表面清理,表面应不得残留未脱落的氧化皮,不能有明显的变形弯曲及其它可见缺陷。
2.2.3硬度检验2.2.3.1正火硬度要求常用的齿轮钢参照表2.1.1表1执行,当有特殊要求的以工艺图纸规定为准。
正火硬度均匀性要求,若另有其它要求可按与锻件供应商签订的《零〔部〕件检验标准》执行。
怎样判断钢铁热处理前后的组织

钢铁中常见的金相组织区别简析一.钢铁中常见的金相组织1.奥氏体—碳与合金元素溶解在γ-fe中的固溶体,仍保持γ-fe的面心立方晶格。
晶界比较直,呈规则多边形;淬火钢中残余奥氏体分布在马氏体间的空隙处。
2.铁素体—碳与合金元素溶解在a-fe中的固溶体。
亚共析钢中的慢冷铁素体呈块状,晶界比较圆滑,当碳含量接近共析成分时,铁素体沿晶粒边界析出。
3.渗碳体—碳与铁形成的一种化合物。
在液态铁碳合金中,首先单独结晶的渗碳体(一次渗碳体)为块状,角不尖锐,共晶渗碳体呈骨骼状。
过共析钢冷却时沿acm线析出的碳化物(二次渗碳体)呈网结状,共析渗碳体呈片状。
铁碳合金冷却到ar1以下时,由铁素体中析出渗碳体(三次渗碳体),在二次渗碳体上或晶界处呈不连续薄片状。
4.珠光体—铁碳合金中共析反应所形成的铁素体与渗碳体的机械混合物。
珠光体的片间距离取决于奥氏体分解时的过冷度。
过冷度越大,所形成的珠光体片间距离越小。
在A1~650℃形成的珠光体片层较厚,在金相显微镜下放大400倍以上可分辨出平行的宽条铁素体和细条渗碳体,称为粗珠光体、片状珠光体,简称珠光体。
在650~600℃形成的珠光体用金相显微镜放大500倍,从珠光体的渗碳体上仅看到一条黑线,只有放大1000倍才能分辨的片层,称为索氏体。
在600~550℃形成的珠光体用金相显微镜放大500倍,不能分辨珠光体片层,仅看到黑色的球团状组织,只有用电子显微镜放大10000倍才能分辨的片层称为屈氏体。
5.上贝氏体—过饱和针状铁素体和渗碳体的混合物,渗碳体在铁素体针间。
过冷奥氏体在中温(约350~550℃)的相变产物,其典型形态是一束大致平行位向差为6~8o铁素体板条,并在各板条间分布着沿板条长轴方向排列的碳化物短棒或小片.典型上贝氏体呈羽毛状,晶界为对称轴,由于方位不同,羽毛可对称或不对称,铁素体羽毛可呈针状、点状、块状。
若是高碳高合金钢,看不清针状羽毛;中碳中合金钢,针状羽毛较清楚;低碳低合金钢,羽毛很清楚,针粗。
机械制造检验考试题库—填空题
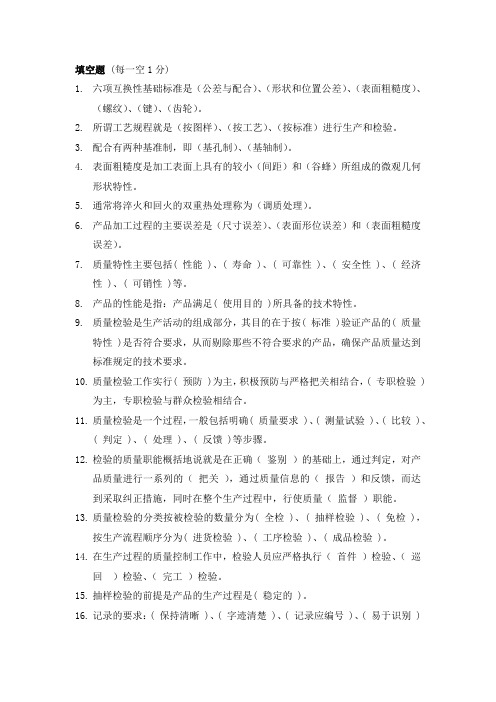
填空题 (每一空1分)1.六项互换性基础标准是(公差与配合)、(形状和位置公差)、(表面粗糙度)、(螺纹)、(键)、(齿轮)。
2.所谓工艺规程就是(按图样)、(按工艺)、(按标准)进行生产和检验。
3.配合有两种基准制,即(基孔制)、(基轴制)。
4.表面粗糙度是加工表面上具有的较小(间距)和(谷蜂)所组成的微观几何形状特性。
5.通常将淬火和回火的双重热处理称为(调质处理)。
6.产品加工过程的主要误差是(尺寸误差)、(表面形位误差)和(表面粗糙度误差)。
7.质量特性主要包括( 性能 )、( 寿命 )、( 可靠性 )、( 安全性 )、( 经济性 )、( 可销性 )等。
8.产品的性能是指:产品满足( 使用目的 )所具备的技术特性。
9.质量检验是生产活动的组成部分,其目的在于按( 标准 )验证产品的( 质量特性 )是否符合要求,从而剔除那些不符合要求的产品,确保产品质量达到标准规定的技术要求。
10.质量检验工作实行( 预防 )为主,积极预防与严格把关相结合,( 专职检验 )为主,专职检验与群众检验相结合。
11.质量检验是一个过程,一般包括明确( 质量要求 )、( 测量试验 )、( 比较 )、( 判定 )、( 处理 )、( 反馈 )等步骤。
12.检验的质量职能概括地说就是在正确(鉴别)的基础上,通过判定,对产品质量进行一系列的(把关),通过质量信息的(报告)和反馈,而达到采取纠正措施,同时在整个生产过程中,行使质量(监督)职能。
13.质量检验的分类按被检验的数量分为( 全检 )、( 抽样检验 )、( 免检 ),按生产流程顺序分为( 进货检验 )、( 工序检验 )、( 成品检验 )。
14.在生产过程的质量控制工作中,检验人员应严格执行(首件)检验、(巡回)检验、(完工)检验。
15.抽样检验的前提是产品的生产过程是( 稳定的 )。
16.记录的要求:( 保持清晰 )、( 字迹清楚 )、( 记录应编号 )、( 易于识别 )和( 检索 )。
材料热处理原理与工艺实验指导书

实验一钢的晶粒度及渗碳层深度的测定一、实验目的1、掌握用弦计算法测定晶粒度的方法。
2、了解加热温度对钢的奥氏体晶粒度的影响。
3、熟悉钢的化学热处理渗碳层的显微组织特征。
4、掌握钢的渗碳层深度的测定方法。
二、概述钢中晶粒大小直接影响其力学性能,评定晶粒大小的方法称晶粒测定法,影响奥氏体晶粒度的因素很多。
加热温度和保温时间起着决定性作用。
合金元素、原始组织状态、热加工、热处理等对奥氏体晶粒度也有一定的影响。
钢晶粒度测定法很多,有比较法、面积法、截点法、弦计算法等。
渗碳的目的是为了使钢件表层获得高的硬度和耐磨性,而中心具有良好的冲击韧性,渗碳用钢均是低碳钢和低合金钢,如10、15、20、15Cr、20CrMn Ti、20MnVB、20Cr、12Cr2Ni4A等等。
三、实验原理及内容(一)、测定奥氏体晶粒度的试样及晶粒显示方法测定奥氏体晶粒度的试样,应在交货状态的钢材上截取,试样的数量及取样部位按相应的标准规定执行。
试样尺寸建议为:圆形试样直径10~20mm,矩形试样10×20mm。
奥氏体晶粒度的显示方法主要有以下几种:渗碳法、网状F法、网状P法、加热缓冷法等,其中加热缓冷法适用于过共析钢,我们实验中采用过共析钢,故晶粒显示参照加热缓冷法,具体方法为:将一组试样经不同的温度加热、保温1.5h后,缓冷至600℃出炉。
除去试样表面氧化层,制成金相试样,根据碳化物沿奥氏体晶界析出的网络测定钢的晶粒度。
(用碱性苦味酸钠酒精溶液腐蚀使网状Fe3C变成黑色)。
(二)、钢的渗层组织及检查方法1、渗碳后的显微组织根据渗碳温度,渗碳时间及渗碳介质活性的不同,钢的渗碳层厚度与含碳量的分布也不同。
一般渗碳层厚度约为0.5-1.7mm。
渗碳层的含碳量,从表层向中心,含碳量逐渐下降。
渗碳后钢的表面含碳量约在0.85~1.05% 之间。
碳钢与合金钢渗碳后的组织状态有很大差别。
碳钢经渗碳后退火状态下从表面至中心部分的显微组织,最表面第一层为过共析区(含碳量0.8-1.2%),由珠光体和网状二次渗碳体组成,而合金渗碳钢渗碳后则为珠光体和粒状碳化物组成;第二层为共析区(含碳量在0.8%左右),由层状珠光体组织构成;第三层为亚共析过渡区,直至钢中心部分出现原始组织的界限为止(含碳量由0.8%以下直到碳钢原始含碳量为止),由珠光体和先共析铁素组成;中心为亚共析区,即未渗碳前的原始组织。
钢的渗碳和碳氮共渗、淬火、回火工艺
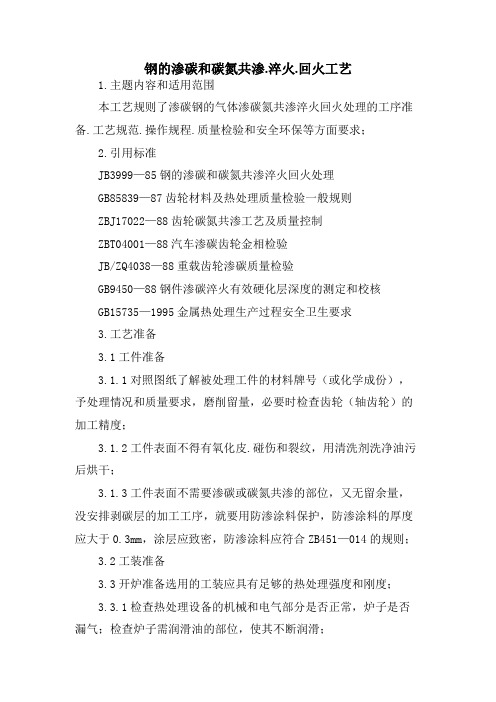
钢的渗碳和碳氮共渗.淬火.回火工艺1.主题内容和适用范围本工艺规则了渗碳钢的气体渗碳氮共渗淬火回火处理的工序准备.工艺规范.操作规程.质量检验和安全环保等方面要求;2.引用标准JB3999—85钢的渗碳和碳氮共渗淬火回火处理GB85839—87齿轮材料及热处理质量检验一般规则ZBJ17022—88齿轮碳氮共渗工艺及质量控制ZBT04001—88汽车渗碳齿轮金相检验JB/ZQ4038—88重载齿轮渗碳质量检验GB9450—88钢件渗碳淬火有效硬化层深度的测定和校核GB15735—1995金属热处理生产过程安全卫生要求3.工艺准备3.1工件准备3.1.1对照图纸了解被处理工件的材料牌号(或化学成份),予处理情况和质量要求,磨削留量,必要时检查齿轮(轴齿轮)的加工精度;3.1.2工件表面不得有氧化皮.碰伤和裂纹,用清洗剂洗净油污后烘干;3.1.3工件表面不需要渗碳或碳氮共渗的部位,又无留余量,没安排剥碳层的加工工序,就要用防渗涂料保护,防渗涂料的厚度应大于0.3mm,涂层应致密,防渗涂料应符合ZB451—014的规则;3.2工装准备3.3开炉准备选用的工装应具有足够的热处理强度和刚度;3.3.1检查热处理设备的机械和电气部分是否正常,炉子是否漏气;检查炉子需润滑油的部位,使其不断润滑;3.3.2检查测温仪表,热电隅是否正常,要定期进行校验;3.3.3定期清理气体渗碳炉炉罐中的碳黑和灰烬;3.4工件的表卡和试样3.4.1根据工件的形状和要求,选用适当的吊具和夹具;3.4.2工件间要有5~10mm的间隙;3.4.3应随炉放臵与装炉工件材质和予处理相同和符合GB8539—87“齿轮材料及热处理质量检验的一般规则”规则的样式,并放臵在有代表性的位臵,以备炉前操作抽样检查;4.渗碳和碳氮共渗淬火回火处理的工艺规范和操作规程4.1渗碳.碳氮共渗处理4.1.1装炉4.1.1.1工件装炉前应把炉温升到渗碳或共渗温度,连续生产时可干上一炉出炉后立即装炉;4.1.1.2工件应装在炉子的有效加热区内,加热区的炉温不得超过±15℃;4.1.1.3每炉装载量不大于设备的装载量;4.1.2气体渗碳工艺规范和操作规程4.1.2.1气体渗碳工艺规范参照图1,低碳合金渗碳钢的渗碳温度取上限;4.1.2.2排气期排气期的渗剂滴入量,参照表1,炉子到温后的排气时间的长短取决于排气程度,应取气进行分析,当CO2和O2的含量低于0.5%时,即可关闭试样孔,转入强渗期;无气体分析仪时,可观察废气火苗的颜色和状态,当火苗呈杏黄色,上升无力时,排气基本结束;一般地排气时间为1~1.5小时;4.1.2.3强渗期,关闭试样孔,点燃排出的废气;检查炉盖及通风机轴处是否漏气;调整煤油.异丙醇的滴入量,滴量多少取决于设备大小,装炉工件表面积的大小及炉子密封的情况,表1的滴量供选择时参考;强渗期炉气成份应控制在表2规则的范围内;有条件应采用红外线CO2碳位自控仪或露点仪控制炉气或用奥氏体分析仪对炉气进行分析,作为调正滴量的依据;强渗期的炉压控制在100~300pa;废气燃烧的火苗高度控制在200~250㎜的长度;根据工件有效硬化层要求和渗速经验,约达到1/2~2/3渗层深度时,抽验第一根试样,根据第一个试样的渗层确定第二个试样的时间,当有效硬化层深度达到或接近工件的有效硬化深度时,即可进入扩散期;4.1.2.4扩散期:扩散期的煤油.异丙醇滴量约为强渗期的0.5倍,为了保证炉压,并同时加滴甲醇,扩散期的时间与工件要求的有效硬化层深度有关,有效硬化层深度愈深,扩散时间要求愈长一些,与工件的碳势(试样的碳势)有关,碳势高要求扩散时间长一些,还与试样渗层深度有关,为了保证工件表面0.85~1.0%的碳浓度和合理的过滤层,扩散时间约为1~3小时;4.1.2.5降温期:抽验的第三个试样,如果网状碳化物≥5级为作正火处理,920℃出炉空冷,对20CrMnMo17Cr2Ni20CrNi2Mo当工件室冷到300-400℃时要放到回火炉中炉冷,防止在表面和次层在空冷时产生马氏体,形成表面裂纹;对于17CrNi2Mo.20Cr2NiMo等Cr.Ni渗碳钢即使碳化物不超级也要出炉空冷,空冷的炉温度为860~880℃;对于碳化物不超级的20CrMnTi.20CrMnMo~840℃,保渗碳齿轮,随炉冷到830温0.5~1H后直接淬火;4.1.3气体碳氮共渗工艺规范和操作规程;4.1.3.1气体碳氮共渗操作规程;4.1.3.2采用煤油加氨氧的气体碳氮共渗工艺曲线4.1.3.3共渗过程其炉气成分应符合下表规则4.2.1工件渗碳后直接淬火;对本质细晶粒钢工件渗碳后可采用直接淬火的方法,以获得所需要的表层和心部硬度以及有效硬化层深度,如20CrMo.20CrMnMo,以及含硼和稀土的合金钢渗碳件;直接淬火一般在炉中降温到830~850℃,均温0.5~1H出炉后淬火工件渗碳后直接淬火另一个条件是渗层金相组织网状碳化物≤4级;工件要求渗层深,炉中碳势又高的情况,容易造成碳化物超级,而对于模数≤5的20CrMnTi.20CrMnMo齿轮,渗碳深度1.2~1.3㎜(含磨量)碳化物不易超级,可以直接淬火,模数大于5的齿轮视渗层的金相组织中网状碳化物的级别而定,如果网状碳化物小于4级可以直接淬火;5级以上则要高温正火,消除网状碳化物或降低网状碳化物级别;4.2.2工件渗碳后空冷后再淬火,按方法有以下几种原因:a.工件渗碳后需要进行机械加工,如制碳层;b.容易发生过热的碳钢和非细晶粒合金钢件,以及某些不宜直接淬火的工件(如需要在压床上淬的齿轮);c.渗层组织如出现网状碳化物超级对于a.b两种情况,炉冷到850~860℃空冷,但对20CrMnMo渗件要求在400℃以下缓冷,否则易再次表层出现马氏体组织形成裂纹,对于C种情况,要求在900~930℃出炉直接空冷;4.2.312CrNi3.12Cr2Ni4.17CrNi2Mo.20CrNi4.20Cr2Ni4.20Cr2Ni4MoA.20Cr2Ni4WA等高强合金渗碳件,渗碳炉冷到920℃出炉空冷(用于制作大模数齿轮),400以下缓冷,并增加一次至二次650~680℃,5~6H的高温回火;这种高温回火称为催化或促变处理,它不仅能改善机械加工性能,更主要它是获得良好淬火组织的条件和保证;必须严格执行;4.2.4碳氮共渗的工件一般都从共渗温度或低于共渗温度出炉直接淬火;4.2.5经过渗碳淬火或碳氮共渗淬的工件,通常采用180℃±10℃的低温回火;4.2.5.1碳氮共渗齿轮回火的温度为180℃±10℃,回火时间3H;4.2.5.2模数1~3的齿轴渗碳淬火后温度200~210℃,时间3H,模数1~3的齿轮渗碳淬火后的回温度220℃±10℃,时间3H4.2.5.3模数3~5的齿轴.齿轮渗碳淬火后进行二次回火;第一次回火温度230℃,时间4H;第二次齿轴的回火温度230℃,回火时间3H;4.2.5.4模数≥6的齿轮.齿轴,渗碳后直接淬火的工件,需要进行三次回火;第一次回火温度230℃,回火时间3H;第二次回火,齿轴的回火温度230℃,时间3H,齿轮的回火温度240℃,时间3H;第三次回火,齿轴的回火温度220℃,时间3H,齿轮的回火温度240℃,时间3H;4.2.5.5模数≥6的齿轮齿轴渗碳后空冷,后加热淬火;进行二次回火;第一次回火温度230℃,时间4H;第二次回火,齿轴的回火温度220℃,时间4H,齿轮的回火温度240℃,时间4H;4.2.5.6前一次回火后,工件空冷到室温或≤50℃,才能进行下一次回火;4.2.5.7工件回火必须放在回火炉的有效加热区内(渗碳淬火的齿轮部分需量出回火炉底部300㎜);4.3渗碳和碳氮共渗淬火回火件的最后处理;4.3.1清理:进行喷砂,以清除赤面的油污和氧化模;4.3.2校直和矫正:用偏摆仪检查齿轴的变形,当超过允许变形时,应对其校直和矫正;随后进行去应力回火;条件允许(淬火工件量少时)应在淬火后马上进行校直,然后再回火;5.质量检验5.1外观:不得有裂纹和碰伤5.2表面硬度5.2.1硬度检验方法,按GB23083《金属洛氏硬试验法》或其他硬度试验法进行;5.2.2表面硬度的偏差范围,表面硬度不得超过下表规则:5.3.1有效硬化层检验方法,按GB《钢的渗碳硬化层有效硬化层深度的测定和校验》中的规则执行;5.3.2有效硬化层深度偏差不得超过下表规则;根据零件的要求,按有关标准进行检定;5.5变形:零件的变形应符合技术要求;6.安全与环保6.1操作者要穿戴好必须的劳动保护用品;6.2执行所用设备的安全操作规程;6.3气体渗碳或碳氮共渗出炉淬火时,同时淬火的工件量大时,应先检查油温,当油温>100℃时,应先降油温后淬火,以防止油槽着火;着火时需用灭火器,石棉被灭火,严禁用水灭火;6.4要防止渗碳炉滴注器渗漏,以免引起炉盖着火,烧毁电机或造成渗剂失火;6.5其它方面按GB15735—1995,金属热处理生产过程安全卫生要求;。
渗碳层深度检验方法(金相法)
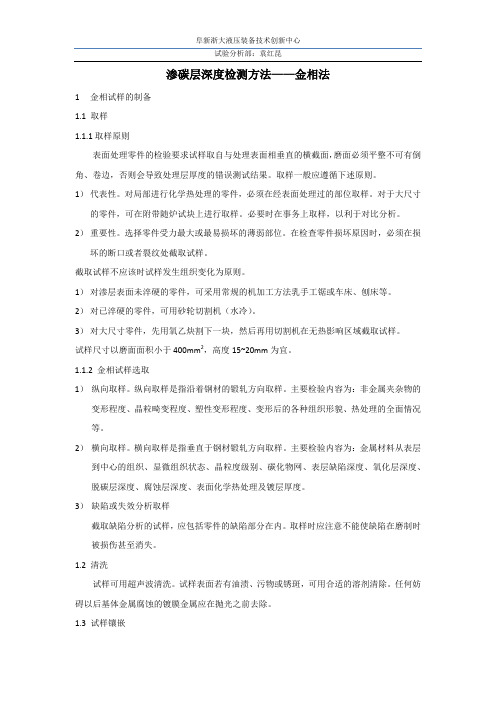
渗碳层深度检测方法——金相法1金相试样的制备1.1 取样1.1.1取样原则表面处理零件的检验要求试样取自与处理表面相垂直的横截面,磨面必须平整不可有倒角、卷边,否则会导致处理层厚度的错误测试结果。
取样一般应遵循下述原则。
1)代表性。
对局部进行化学热处理的零件,必须在经表面处理过的部位取样。
对于大尺寸的零件,可在附带随炉试块上进行取样。
必要时在事务上取样,以利于对比分析。
2)重要性。
选择零件受力最大或最易损坏的薄弱部位。
在检查零件损坏原因时,必须在损坏的断口或者裂纹处截取试样。
截取试样不应该时试样发生组织变化为原则。
1)对渗层表面未淬硬的零件,可采用常规的机加工方法乳手工锯或车床、刨床等。
2)对已淬硬的零件,可用砂轮切割机(水冷)。
3)对大尺寸零件,先用氧乙炔割下一块,然后再用切割机在无热影响区域截取试样。
试样尺寸以磨面面积小于400mm2,高度15~20mm为宜。
1.1.2 金相试样选取1)纵向取样。
纵向取样是指沿着钢材的锻轧方向取样。
主要检验内容为:非金属夹杂物的变形程度、晶粒畸变程度、塑性变形程度、变形后的各种组织形貌、热处理的全面情况等。
2)横向取样。
横向取样是指垂直于钢材锻轧方向取样。
主要检验内容为:金属材料从表层到中心的组织、显微组织状态、晶粒度级别、碳化物网、表层缺陷深度、氧化层深度、脱碳层深度、腐蚀层深度、表面化学热处理及镀层厚度。
3)缺陷或失效分析取样截取缺陷分析的试样,应包括零件的缺陷部分在内。
取样时应注意不能使缺陷在磨制时被损伤甚至消失。
1.2清洗试样可用超声波清洗。
试样表面若有油渍、污物或锈斑,可用合适的溶剂清除。
任何妨碍以后基体金属腐蚀的镀膜金属应在抛光之前去除。
1.3试样镶嵌若试样过于细薄或过软、易碎、或需检验边缘组织、或者为便于在自动磨抛机上研磨试样实验室通常采用可采用热压镶嵌法和浇注镶嵌法较为方便。
所选用先前方法均不得改变试样原始组织。
1.3.1热压镶嵌法将样品磨面朝下放入模中,树脂倒入模中超过样品高度,封紧模子并加热、加压。
热处理检验方法国家标准
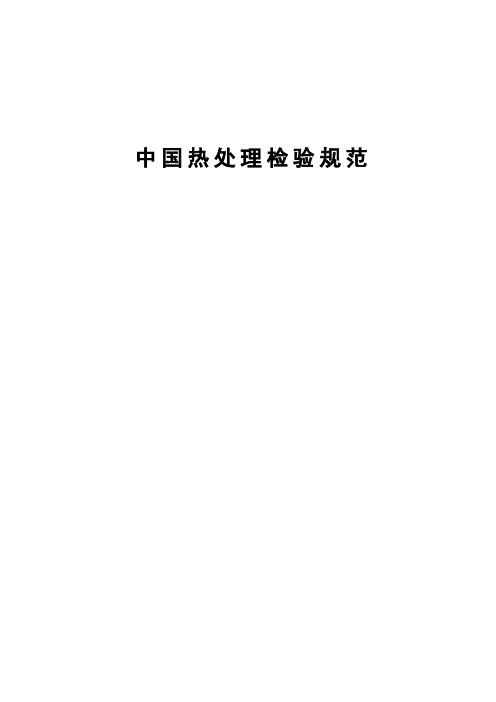
中国热处理检验规范热处理检验方法和规范金属零件的内在质量主要取决于材料和热处理。
因热处理为特种工艺所赋予产品的质量特性往往又室补直观的内在质量,属于“内科”范畴,往往需要通过特殊的仪器(如:各种硬度计、金相显微镜、各种力学性能机)进行检测。
在GB/T19000-ISO9000系列标准中,要求对机械产品零部件在整个热处理过程中一切影响因素实施全面控制,反映原材料及热处理过程控制,质量检验及热处理作业条件(包括生产与检验设备、技术、管理、操作人员素质及管理水平)等各方面均要求控制,才能确保热处理质量。
为此,为了提高我公司热处理产品质量,遵循热处理相关标准,按零件图纸要求严格执行,特制定本规范一、使用范围:本规范适用于零件加工部所有热处理加工零件。
二、硬度检验:通常是根据金属零件工作时所承受的载荷,计算出金属零件上的应力分布,考虑安全系数,提出对材料的强度要求,以强度要求,以强度与硬度的对应关系,确定零件热处理后应具有大硬度值。
为此,硬度时金属零件热处理最重要的质量检验指标,不少零件还时唯一的技术要求。
1、常用硬度检验方法的标准如下:GB230 金属洛氏硬度试验方法GB231 金属布氏硬度试验方法GB1818 金属表面洛氏硬度试验方法GB4340 金属维氏硬度试验方法GB4342 金属显微维氏硬度试验方法GB5030 金属小负荷维氏试验方法2、待检件选取与检验原则如下:为保证零件热处理后达到其图纸技术(或工艺)要求,待检件选取应有代表性,通常从热处理后的零件中选取,能反映零件的工作部位或零件的工作部位硬度的其他部位,对每一个待检件的正时试验点数一般应不少于3个点。
通常连续式加热炉(如网带炉):应在连续生产的网带淬火入回火炉前、回火后入料框前的网带上抽检3-5件/时。
且及时作检验记录。
同时,若发现硬度超差,应及时作检验记录。
同时,若发现硬度越差,应及时进行工艺参数调整,且将前1小时段的零件进行隔离处理(如返工、检)。
渗碳炉操作规程

渗碳炉操作规程
《渗碳炉操作规程》
1. 渗碳炉操作前,应检查设备是否完好,并确保工作环境安全。
操作人员需穿戴防护装备,包括耐高温手套、护目镜等。
2. 打开渗碳炉门,进行预热。
渗碳炉预热时间一般为30分钟,预热温度应根据具体工件材料和要求进行调整。
3. 将工件放入渗碳炉内,关闭炉门,并调整好温度和渗碳时间。
根据工件的要求,可进行多次渗碳处理。
4. 在渗碳炉操作过程中,应随时监控温度和气氛状态,确保符合加工要求。
5. 渗碳炉操作结束后,先停止供气,然后打开炉门,待温度降至安全范围后,将工件取出。
6. 渗碳炉操作结束后,应及时清理炉内残留物,并进行设备维护保养。
7. 渗碳炉操作结束后,将操作记录进行归档,包括工件种类、渗碳时间、温度等参数,以便日后的工艺追溯和改进。
以上即是《渗碳炉操作规程》,操作人员在进行渗碳炉操作时,务必按照规程严格执行,确保工件质量和操作安全。
渗碳 渗氮、氮碳共渗标准
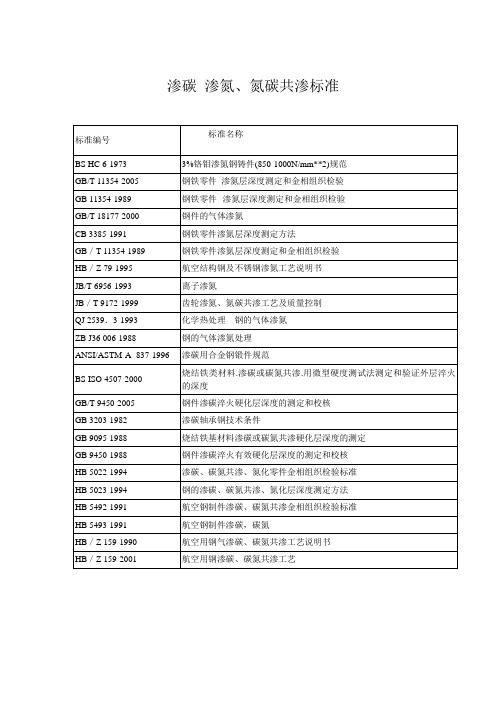
渗碳渗氮、氮碳共渗标准通俗地说,不锈钢就是不容易生锈的钢,实际上一部分不锈钢,既有不锈性,又有耐酸性(耐蚀性)。
不锈钢的不锈性和耐蚀性是由于其表面上富铬氧化膜(钝化膜)的形成。
这种不锈性和耐蚀性是相对的。
试验表明,钢在大气、水等弱介质中和硝酸等氧化性介质中,其耐蚀性随钢中铬含水量的增加而提高,当铬含量达到一定的百分比时,钢的耐蚀性发生突变,即从易生锈到不易生锈,从不耐蚀到耐腐蚀。
不锈钢的分类方法很多。
按室温下的组织结构分类,有马氏体型、奥氏体型、铁素体和双相不锈钢;按主要化学成分分类,基本上可分为铬不锈钢和铬镍不锈钢两大系统;按用途分则有耐硝酸不锈钢、耐硫酸不锈钢、耐海水不锈钢等等,按耐蚀类型分可分为耐点蚀不锈钢、耐应力腐蚀不锈钢、耐晶间腐蚀不锈钢等;按功能特点分类又可分为无磁不锈钢、易切削不锈钢、低温不锈钢、高强度不锈钢等等。
由于不锈钢材具有优异的耐蚀性、成型性、相容性以及在很宽温度范围内的强韧性等系列特点,所以在重工业、轻工业、生活用品行业以及建筑装饰等行业中获取得广泛的应用。
奥氏体不锈钢在常温下具有奥氏体组织的不锈钢。
钢中含Cr约18%、Ni 8%~10%、C约0.1%时,具有稳定的奥氏体组织。
奥氏体铬镍不锈钢包括著名的18Cr-8Ni钢和在此基础上增加Cr、Ni含量并加入Mo、Cu、Si、Nb、Ti等元素发展起来的高Cr-Ni 系列钢。
奥氏体不锈钢无磁性而且具有高韧性和塑性,但强度较低,不可能通过相变使之强化,仅能通过冷加工进行强化。
如加入S,Ca,Se,Te等元素,则具有良好的易切削性。
此类钢除耐氧化性酸介质腐蚀外,如果含有Mo、Cu等元素还能耐硫酸、磷酸以及甲酸、醋酸、尿素等的腐蚀。
此类钢中的含碳量若低于0.03%或含Ti、Ni,就可显著提高其耐晶间腐蚀性能。
高硅的奥氏体不锈钢浓硝酸肯有良好的耐蚀性。
由于奥氏体不锈钢具有全面的和良好的综合性能,在各行各业中获得了广泛的应用。
铁素体不锈钢在使用状态下以铁素体组织为主的不锈钢。
表面处理质量检验工作抽样规定

表面处理质量检验工作抽样规定一、镉镀层零件的抽检规定1、外观检验。
关键零件和重要零件应100%检查,其余按GB12609抽样进行检查。
2、厚度检验。
关键零件和重要零件应100%检查,其余按GB12609抽样进行检查。
3、结合力检验。
1)当新配镀液或镀液有较大变化时,必须进行结合力检验。
连续生产时须定期检验,检验周期为每槽产品1次/周。
2)镀层结合力检验可以在100mm×25mm×1mm或Φ10mm×100mm的试样上进行。
4、耐蚀性检验。
当新配镀液或镀液有较大变化时,必须进行耐蚀性检验。
或连续生产时定期检验。
5、氢脆性检验。
当抗拉强度σb≥140MPa的钢关键件、重要件进行镀镉时,必须进行延迟破坏试验。
二、化学镍镀层零件抽检规定1、外观检验。
大零件和重要零件应100%进行检验。
小零件应每批(或每槽)抽取5~10%进行验收。
其中若有一个零件不合格,再取双倍的零件复验,若仍有一个零件不合格,则该批(或槽)零件全部退回处理。
2、厚度检验。
从每一槽的不同位置抽取2~3件进行厚度测定。
允许用与零件同类材料、同槽化学镀的试件测定厚度。
3、结合力检验。
结合力的检验可以定期或按批抽查,检验次数根据工艺规程规定执行。
抽取1~2个零件进行试验,若有一个零件不合格,再取双倍数量的零件进行复验,若仍有一个零件不合格,则除该批零件需要返修外,并应采取措施,直至检验结合力合格为止。
4、硬度检验。
硬度检验按产品图纸和工艺文件的需要进行。
检验时,按批抽查,每批抽查数量为1~2件,每件测三点,在三点中有一点不合格,则退回生产单位返修或报废。
三、金镀层零件抽检规定1、外观检验。
镀金零件应100%进行外观检验,不合格的零件应退回处理。
必要时,可用3~5倍放大镜检查。
2、厚度检验。
进行厚度检验时,可从每一槽的不同位置上抽取2~3个零件,其中若有一个零件不合格,则取加倍数量的零件复验,若仍有一个零件不合格,则该槽零件应退回处理。
气体渗碳炉操作规程

气体渗碳炉操作规程一、前言气体渗碳炉是一种常用的热处理设备,主要用于将工件表面渗碳,从而提高工件的硬度和耐磨性,使工件具有更好的性能。
本文将介绍气体渗碳炉的操作规程,以保证热处理过程的安全和稳定。
二、操作规程1. 准备工作:(1)检查气体渗碳炉的工作状态,确保设备运转正常。
(2)检查炉子内部温度计、热电偶的正确性,并进行标定。
(3)检查加热元件(如石墨加热管)的状态和接线是否良好。
(4)检查渗碳剂(如乙烯)的储存状态和使用量,确保够用。
(5)检查装炉器具的码放位置、量热器的状态、气体出口、排气管和工件清理工具等,确保完好。
2. 加料:(1)打开气体渗碳炉的进气管道和排气管道。
(2)开启气瓶阀门,调节供气压力,并通过流量计监测加热气体的流量。
(3)打开加热元件开关,并预热炉子到设定温度。
(4)将已清理干净的工件放入装炉器具中,并根据工件的形状合理摆放。
(5)将装好工件的装炉器具放入气体渗碳炉中,并固定好。
(6)关闭炉子门,并调整好排气加压阀门的开度,使排气管道内压力与气瓶内压力相等。
3. 渗碳处理:(1)打开渗碳剂阀门,同时根据温度和渗碳剂的使用量调节加热气体的流量。
(2)根据工艺要求,控制温度、渗碳剂浓度和渗碳时间,一般渗碳时间为1-4小时,以达到期望的渗碳深度和硬度。
(3)注意检查加热元件的使用情况,如发现异常及时处理。
4. 温度降低:温度降低要缓慢进行,以避免工件变形和炉子爆炸,降温时要关闭渗碳剂阀门,并逐渐降低加热气体的流量和温度。
5. 取出工件:取出工件后要进行清理和检查,确保渗碳深度和硬度达到要求,并对工件的表面和几何尺寸进行测量和记录,以便后续的质量检验。
三、注意事项(1)操作炉子时要穿戴好防护工具,如防热手套、防护镜、防护服等,以保证安全。
(2)操作炉子时要掌握渗碳剂的使用量和流量控制,避免渗碳剂过多或过少。
(3)在渗碳过程中要定期检查加热元件的状态和温度,确保炉子运转正常。
(4)操作过程中要严格控制温度和渗碳时间,避免工件变形或渗碳不均匀。
热处理原理与工艺 作者 赵乃勤 第11章 化学热处理
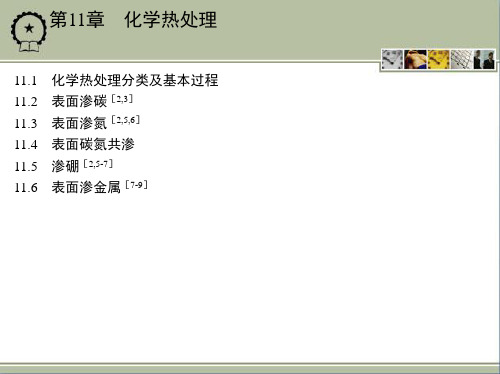
11.2.6 渗碳缺陷及控制
1.黑色组织 2.反常组织 3. 粗大网状碳化物组织 4.渗碳层深度不均匀 5.表层贫碳或脱碳 6.表面腐蚀和氧化
1.黑色组织
在含Cr、Mn及Si等合金元素的渗碳钢渗碳淬火 后,在渗碳层表面组织中出现沿晶界呈断续网 状的黑色组织。出现这种黑色组织的原因,可 能是由于渗碳介质中的氧向晶界扩散,形成Cr、 Mn和Si等元素的氧化物,即“内氧化”;也可 能是由于合金元素的优先氧化使晶界上及晶界 附近的合金元素贫化,淬透性降低,致使淬火 后出现非马氏体组织。
d)渗层硬度
5.渗碳件的质量检查
渗碳件的质量检查一般包括:①渗碳钢原材料 检查;②渗层质量检查,包括渗层深度、渗层 碳含量,碳化物、残留奥氏体及马氏体级别的 评定;③渗碳件心部游离铁素体级别的评定; ④渗层和心部硬度的检查;⑤渗碳件变形量的 检查和表面氧化、脱碳以及软点检查。
11.2.5 渗碳后钢的组织与性能[2]
5.表层贫碳或脱碳
图11-14
6.表面腐蚀和氧化
渗碳剂不纯,含杂质多,如硫或硫酸盐的含量 高,液体渗碳后零件表面粘有残盐,均会引起 腐蚀。渗碳后零件出炉温度过高,等温盐浴或 淬火加热盐浴脱氧不良,都可引起表面氧化, 应仔细控制渗碳剂的盐浴成分,并对零件表面 及时清洗。
11.3.1 渗氮的特点
渗氮(氮化)是将氮渗入钢件表面,从而提高其硬 度、耐磨性和疲劳强度的一种化学热处理方法。 渗氮的发展虽比渗碳晚,但却得到了广泛应用, 这是因为它具有以下优点:渗氮可以获得比渗 碳更高的表面硬度和耐磨性,钢渗氮后的表面 硬度可以高达950~1200HV (相当于65~72HRC), 而且到600℃仍可维持相当高的硬度(即热硬性); 渗氮还可获得比渗碳更高的弯曲疲劳强度;由 于渗氮温度较低(500~570℃之间),故变形很小; 渗氮也可以提高工件的耐蚀性能。但是,渗氮 的缺点是工艺过程较长,渗层也较薄,不能承 受太大的接触应力。目前除了钢以外,其它如 钛、钼等难熔金属及其合金也广泛地采用渗氮 工艺。
- 1、下载文档前请自行甄别文档内容的完整性,平台不提供额外的编辑、内容补充、找答案等附加服务。
- 2、"仅部分预览"的文档,不可在线预览部分如存在完整性等问题,可反馈申请退款(可完整预览的文档不适用该条件!)。
- 3、如文档侵犯您的权益,请联系客服反馈,我们会尽快为您处理(人工客服工作时间:9:00-18:30)。
渗碳件质量检查
零件渗碳前的检验:
1.根据GB699-88《优质碳素钢技术条件》和GB3077-88《合金结构钢技术条件》等标准,对零件材质进行分析,发现异常,及时处理并报告
2.零件表面不得有刀迹,尖锐角、氧化、生锈等,表面粗糙度应低于Ra3.2μm
3.零件内部应无偏析、疏松等缺陷,原材料带状组织应≤2~3级,魏氏组织≤1级,晶粒度≥5级
渗碳层总深度检验:
1.渗碳层总深度≤0.3mm的渗碳件,按GB9451-88《钢件薄表面总硬化层深度或有效硬化层深度的测定》的具体规定进行检验,常用显微组织测量法和显微硬度测量法
1)显微组织测量法是零件热处理后导致零件表层和心部显微组织的变化,测定零件总硬化层深度或有效硬化层深度
2)显微硬度测量法是零件经热处理后导致零件表面至心部“维氏显微硬度”
的变化,测定零件总硬化层深度或有效硬化层深度
2.日常生产渗碳层总深度一般用金相法检验,试样应是退火的平衡状态。
碳素钢渗碳层总深度为过共析层+共析层+1/2过渡层之间的垂直距离;合金钢渗碳层总深度为过共析层+共析层+全部过渡层(过共析层+共析层应为总渗碳层深的60%~70%)之间的垂直距离
3.渗碳工艺过程中间检验以试样为主,常用断口目测法和磨片蚀显法
断口目测法是将渗碳中间试样出炉后淬火打断观察断口,渗碳层为银白色瓷状,未渗碳部分为暗灰色纤维状,交界处的碳质量分数约为0.4%,此处至表面的垂直距离即定为渗碳层下限深度
磨片蚀显法是将渗碳中间试样(淬火或正火状态均可)断面磨平用体积分数为4%的硝酸酒精溶液浸蚀几秒钟后,出现黑圈,黑圈厚度即为粗略的渗碳层下限深度
4.同一批零件,渗碳层深度的波动,必须在图样规定的范围内同一零件渗碳层深度的波动范围是图样规定波动范围的1/2
碳深度梯度检验:
1.日常生产检验,可以用碳浓度(质量分数的)梯度和硬度的梯度检验互补,但质量仲裁应以硬度梯度(至心部硬度降)为准
2.常用剥层法,剥层检验交界处的碳的质量分数为0.4%,剥层在表面0.1mm内,碳浓度(质量分数)应达到图样要求,一般以0.8%~1.0%为合格,碳深度梯度过渡过应平缓,不得出现陡坡,浅层渗碳允许表面碳的质量分数低于0.8% 渗碳层淬火前的组织检验:
1.渗碳层淬火前的组织应是珠光体+碳化物+少量铁素体
2.渗碳层中有大块或网状碳化物,应建议两次淬火或一次正火,一次淬火,一般碳化物级别小于6级
3.渗碳后,心部出现3级以上带状组织或晶粒度小于5级时,应正火后,重新检验合格方可淬火
4.渗碳层中出现网状碳化物与游离铁素体不合格时应正火消除
渗碳件淬、回火后的硬度检验:
1.渗碳件表面硬度检验时,应去除氧化皮,脱碳层、增碳层,应以洛氏和维氏硬度计检验为准
2.硬度应符合图样或技术文件规定,一般碳钢(10、20钢)硬度在50~55HRC 或58~63HRC,合金钢硬度在58~63HRC
3.硬度终检以实物为准,但允许用随炉不同位置两个以上的试样代替实物检验。
试样材质、工艺过程与零件相同
4.硬度检验的百分比由工艺规定,但一般周期炉,每炉应抽验1~2个实物,连续炉每生产4~6盘或1~2个节拍应验实物1~2件
5.对无法用硬度计检验的凹槽尖角处,允许用和图样要求硬度相同级别的标准锉刀检验,当发生争议时应解剖实物,以在洛氏或维氏硬度计上检验为准6.同一批渗碳件,硬度波动范围应≤5HRC,同一只渗碳件表面硬度波动应≤3HRC,所有波动值都不超过图样规定的范围
7.图样或技术文件未规定检验心部硬度的一般不检验,汽车渗碳齿轮心部硬度检验位置在齿宽中部横截面上齿轮中心线与齿根圆相交处的硬度其它零件心部硬度值测在距表面3倍渗碳层上限深度处
8.汽车渗碳齿轮表面硬度检验在齿宽中部节圆附近,表面硬度检验位置应该在图样规定的位置或零件受力最大位置
9.不渗碳位置(镀铜、涂料保护部位、切削加工部位)的硬度检验,在去除涂层淬火、回火后,按图样规定检验
10.渗碳件表面出现软点、软块为不合格品
11.至心部硬度降(硬度梯度),在用硬度法测有效硬化层范围内,自表面向心部硬度降是每下降0.1mm硬度值差不大于45HV1(20CrMnMo、20CrMo,允许35~40HV1)
有效硬化层深度检验(DC):
1.有效硬化层深度检验按GB9450-88《钢件渗碳淬火有效硬化层深度的测定和校核》规定进行,有效硬化层深≤0.3mm的零件按GB9451-88《钢件薄表面总硬化层深度有效硬化层深度的测定》规定进行检验
2.有效硬化层深是从零件表面测至550HV1(极限硬度值)的垂直距离,采用的试验力9.807N(1kgf),用49.35N(5kgf)的试验力,测至515HV5(极限硬度值)。