浅谈齿轮渗碳淬火有效硬化层及硬度梯度
渗碳淬火齿轮有效硬化层深
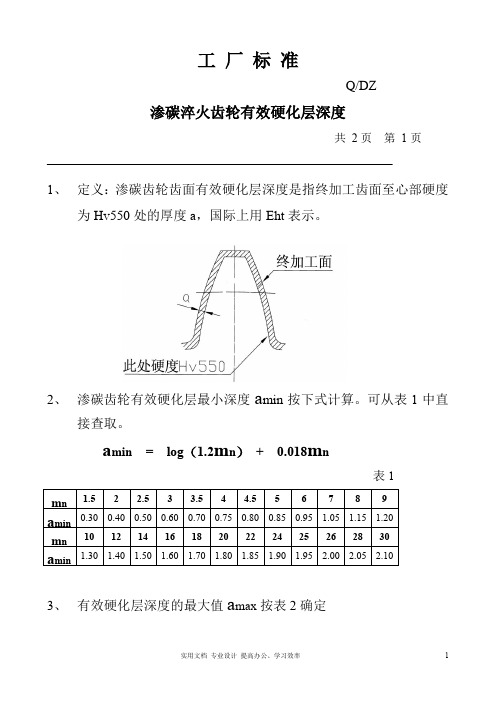
工厂标准
Q/DZ
渗碳淬火齿轮有效硬化层深度
共2页第1页
1、定义:渗碳齿轮齿面有效硬化层深度是指终加工齿面至心部硬度
为Hv550处的厚度a,国际上用Eht表示。
2、渗碳齿轮有效硬化层最小深度a min按下式计算。
可从表1中直
接查取。
a min= log(1.2m n)+ 0.018m n
表1
3、有效硬化层深度的最大值a max按表2确定
共2页第2页
表2
4、本规定适用于轧钢机械、连铸机械、炼焦机械、冶炼机械、装卸
机械的传动齿轮。
5、特殊工况用渗碳齿轮的有效硬化层深度,可根据接触剪应力的大
小另行确定。
6.、本表对于Mn≤8的齿轮而言,其推荐的渗碳深度是合理的,但对于Mn>8的齿轮而言,其数据缺乏合理性。
7. 对于合理的渗碳层深度各国、各公司的标准不同,而且差距还比较大。
各国及各行业推荐的渗碳层深度见表3
表3 各国及各行业推荐的渗碳层深度
注:根据JB/T 8853-2001《圆柱齿轮减速机》渗碳层的深度根据模数选择,当Mn=1.5~6时,渗碳层深度ht=(0.2~0.3)Mn;
当Mn=7~18时,渗碳层的深度ht=(0.15~0.25)Mn(小模数取大值,大模数取小值)。
谈齿轮渗碳淬火有效硬化层及硬度梯度

浅谈齿轮渗碳淬火有效硬化层及硬度梯度随着机械工业的发展,对齿轮的质量要求日益提高,而齿轮的强度寿命和制造精度与热处理质量有很大关系。
为了检验齿轮材料热处理质量,在1987年以前,我国的齿轮渗碳淬火内在质量检验标准多为终态金相检验标准。
由于检测仪器的精度、分辨率等因素以及检验人员的经验参差不齐,造成检验结果有很大差异和争议。
为了解决金相法内在检验存在的弊端,机械部在1987年借鉴了DIN.ISO等标准中有关内容,修订了我国现行齿轮渗碳淬火内在质量检验标准。
此检验标准中,其金相组织检验标准基本与原标准相似,主要是对渗碳层深度及碳浓度梯度的测定作了较大的修改。
下面就渗碳层深度和碳浓度梯度分别采用金相法与硬度法测定进行简述。
一、渗碳层深度的检测1.1、金相法1.1.1、取本体或与零件材料成分相同,预先热处理状态基本相似的圆试样或齿形试样进行检测。
1.1.2、送检试样热处理状态为平衡状态,即退火状态。
1.1.3、低碳钢渗层深度为:过共析层+共析层+1/2亚共析层。
1.1.4、低碳合金钢渗层深度为:过共析层+共析层+亚共析层。
1.2、硬度法1.2.1、取样方法同金相法取样方法一致。
1.2.2、送检试样状态为淬火+回火状态。
1.2.3、渗碳深度用有效硬化层来表示,其极限硬度根据不同要求进行选择。
1.2.4、有效硬化层深度(DCp):从试样表面测至极限硬度(如HV550)之间垂直距离。
1.3、两种关于渗碳深度检测的方法存在着一定的对应关系,下面用图形来描述。
从图中可看出:DCp(芯部)>DCp(HV500)>DCp(HV550)DCp(HV550)对应渗碳层中碳含量约为0.35~0.38%,此界限处即为金相法中1/2亚共析层处。
DCp(HV500)对应渗碳层中碳含量约为0.31~0.33%,此界限处为金相法中1/2亚共析层处。
DCp(芯部)对应渗碳层中碳含量为基体碳含量,一般为0.17~0.23%,此界限处为金相法中基体组织。
渗氮层、淬硬层、有效硬化层的硬度和厚度测试简介

0.05
0.02
0.35
0.15
0.1
0.05
0.4
0.2
0.15
0.05
0.5
0.25
0.2
0.1
0.6
0.3
0.25
0.1
0.65
0.3
0.3
0.1
0.75
0.3
3、总渗氮层深度
b、基体硬度的取点与测定,一般在3倍左右渗氮层深度的距离处测得的硬度值(至少取3点,平均值)做为基体硬度值。
c、对于渗氮层硬度变化很平缓的钢种,(如碳钢、低碳合金钢制件),其渗氮层深度可以从试样表面沿垂直方向测至比基体维氏硬度高30HV处。
d、当渗氮层深度有的特别浅,有的则较深时,检测力可以在0.2KG范围内选择(并注明,如HV0.2)
a、渗氮层脆性级别按维氏硬度压痕边缘碎裂程度分为5级
级别
渗氮层脆性级别说明
1
压痕边角完整无缺
2
压痕一边或一角碎裂
3
压痕二边或二角碎裂
4
压痕三边或三角碎裂
5
压痕四边或四角碎裂
b、渗氮层脆性检验一般采用维氏硬度计,试验力10公斤,试验力的加载必须缓慢(在5-9S内完成),试验力加载完成后必须停留5-10S,然后卸载试验力,特殊情况也可采用5KG或者30KG试验力。
一般零件推荐的化合物层厚度及公差表(单位/mm)
化合物层厚度
上偏差
化合物层厚度
上偏差
0.005
0.003
0.012
0.006
0.008
0.004
渗碳淬火齿轮有效硬化层深
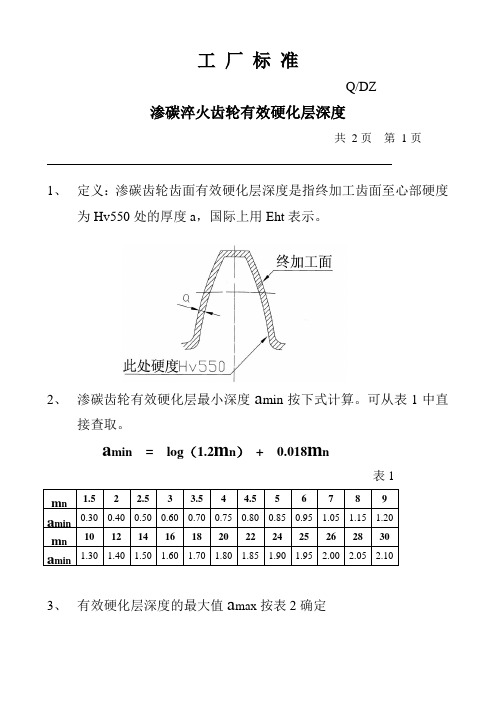
工厂标准
Q/DZ
渗碳淬火齿轮有效硬化层深度
共2页第1页
1、定义:渗碳齿轮齿面有效硬化层深度是指终加工齿面至心部硬度
为Hv550处的厚度a,国际上用Eht表示。
2、渗碳齿轮有效硬化层最小深度a min按下式计算。
可从表1中直
接查取。
a min= log(1.2m n)+ 0.018m n
表1
3、有效硬化层深度的最大值a max按表2确定
共2页第2页
表2
4、本规定适用于轧钢机械、连铸机械、炼焦机械、冶炼机械、装卸
机械的传动齿轮。
5、特殊工况用渗碳齿轮的有效硬化层深度,可根据接触剪应力的大
小另行确定。
6.、本表对于Mn≤8的齿轮而言,其推荐的渗碳深度是合理的,但对于Mn>8的齿轮而言,其数据缺乏合理性。
7. 对于合理的渗碳层深度各国、各公司的标准不同,而且差距还比较大。
各国及各行业推荐的渗碳层深度见表3
表3 各国及各行业推荐的渗碳层深度
注:根据JB/T 8853-2001《圆柱齿轮减速机》渗碳层的深度根据模数选择,当Mn=1.5~6时,渗碳层深度ht=(0.2~0.3)Mn;
当Mn=7~18时,渗碳层的深度ht=(0.15~0.25)Mn(小模数取大值,大模数取小值)。
小模数渗碳淬火齿轮硬化层问题
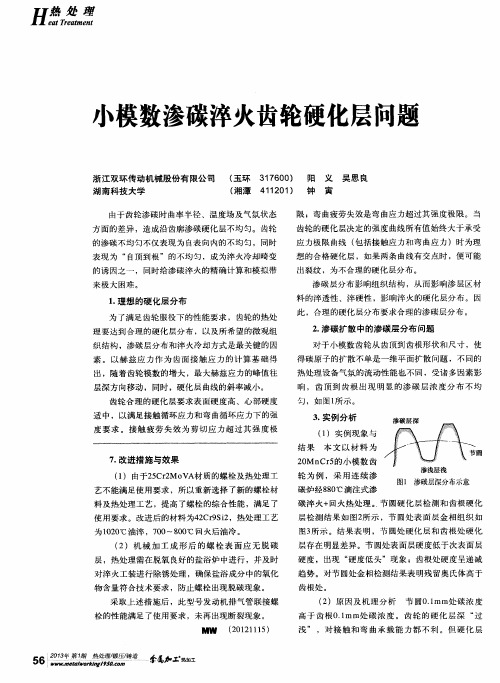
1 . 理想的硬化层分布
为 了满 足 齿轮 服役 下 的 性 能要 求 ,齿轮 的热 处 理 要达 到合 理 的硬 化 层 分 布 ,以 及所 希 望 的 微观 组 织 结 构 ,渗 碳 层 分布 和 淬 火 冷却 方 式是 最 关 键 的 因
2 . 渗碳扩散 中的渗碳 层分布 问题
对于 小 模 数 齿轮 从 齿 顶 到 齿根 形状 和 尺 寸 ,使 得 碳 原 子 的扩 散 不单 是 一 维平 面 扩 散 问题 ,不 同 的 热 处 理 设备 气氛 的流 动 性 能 也不 同 ,受诸 多 因素 影 响 ,齿 顶 到 齿 根 出现 明 显 的渗 碳 层 浓 度 分 布 不 均
图3 所 示 。结果 表 明 ,节 圆处 硬 化 层和 齿 根 处 硬 化
( 2 )机 械加 工 成形 后 的螺 栓表 面应 无 脱碳 层,热处理需在脱氧良好的盐浴炉 中进行,并及时 对淬火工装进行除锈处理 ,确保盐浴成分中的氧化
物 含量 符 合技 术 要求 ,防止 螺 栓 出现 脱度低于次表面层 硬度 ,出现 “ 硬度低头”现象 ;齿根处硬度呈递减
趋势 。对 节 圆处 金 相检 测 结 果表 明残 留奥 氏体 高 于
齿根 处 。
采取上述措施后 ,此型号发动机排气管联接螺
栓 的性 能 满足 了使用 要 求 ,未 再 出现 断 裂现 象 。
匀 ,如 图 1 所示 。
素 。以赫 兹应力作 为齿面接触应 力的计算 基础得
出 ,随 着 齿轮 模 数 的增 大 ,最大 赫 兹 应 力的 峰 值往 层深 方 向移 动 ,同时 ,硬 化 层 曲线的 斜率 减 小 。 齿 轮 合理 的硬 化 层要 求表 面 硬 度高 、心 部 硬 度 适 中 ,以 满 足接 触 循 环应 力 和 弯 曲循 环 应 力下 的 强 度 要 求 。 接 触 疲 劳 失 效 为 剪 切 应 力超 过 其 强 度 极
齿轮淬火深度

图片:齿轮淬火的“最佳”硬化层深与“适当”硬化层深戴忠森众所周知,齿轮的淬硬层深“过浅”,对接触和弯曲承载能力都不利。
但淬硬层也不是越深越好,最佳或适当的硬化层深度,可使齿面和齿根都具有较高的强度(承载能力)。
另外,不同的热处理方法,其“最佳”值也不是一样的。
二十世纪七、八十年代,随着齿轮强度计算方法ISO标准的公布,以及国内GB/3480“圆柱齿轮承载能力计算方法”标准的实施,特别是工业硬齿面齿轮的广泛采用,国内外齿轮工作者(专家、学者),就热处理硬化层深问题,进行了大量的试验研究和理论分析。
其实质都是基于接触(弯曲)疲劳强度,其核心问题是:疲劳裂纹发生(萌生)在何处?破坏后的形状是点蚀(pitting贝壳状),还是片蚀(剥落spalling)?研究表明,一般软齿面大多是点蚀,而硬齿面大齿轮大多是剥落(片蚀)。
疲劳裂纹的萌生,有可能在表面,也有可能在表层。
至今,有关硬齿面齿轮接触疲劳强度(剥落)计算的理论和方法,主要有:最大剪切应力τmax (τ45°);正交剪切应力(τyz);当量剪切应力(τeffa);深部接触应力;最大剪切应力/剪切强度的峰值;正交剪切应力/强度(硬度)(τyz/HV)max;当量剪切应力/强度的峰值等,通过理论计算可以确定接触疲劳强度(安全系数);或者确定最佳淬硬层深度。
这些理论和方法一直都有争议,因此至今也没有一个权威的理论和方法被大家所能完全接受。
所谓“最佳硬化层深”,其说法也是较含糊的,而且众说不一,以渗碳淬火齿轮为例,德国DIN3990,硬化(渗碳)层深度,给出一个经验公式:(推荐)Eht= 0.15mn(mn——法面模数)(1)。
该经验公式,有一个突出的问题,就是未考虑实际载荷的情况。
所以,对于轻载齿轮,允许比经验公式稍浅的硬化层深度。
Thomas Tobie近年来提出在用ISO/DIN 进行标准化承载能力计算时,考虑硬化层深度对承载能力的影响,引入了影响系数ZEht(接触承载能力影响系数);УEht(弯曲承载能力影响系数)。
如何解决渗碳或碳氮共渗零件有效硬化深度的测试

如何解决渗碳或碳氮共渗零件有效硬化深度的测试目前,在我国航空、航天、汽车、兵器等众多单位的零件加工和热处理工艺都涉及渗碳或碳氮共渗的问题,针对客户的需求,我司开发出半自动显微硬度测试系统,快速解决有效硬化层深度测量。
针对半自动显微硬度计测试系统FEM-7000的特点,介绍一下此系统在工厂中常用的功能,齿轮热处理方法使用碳氮共渗工艺的最多,,作到俗说的“表硬心软”,需要对渗碳的有效深度作检测。
现在的标准采用硬度梯度法,大多数都采用1Kgf 载荷,看HV550时的深度值。
具体做法如图示:以齿顶为基准,从表面向心部连续打多个点,分别测出各点之硬度,绘制硬度曲线齿轮剖面示意图硬度曲线示意图以往通过此方法作测试时,大家普遍困难的是此工作较繁杂。
一是要打多个点测硬度,二是要不断移动和记录载物台移动量,三是手工绘制曲线图。
这几个环节易出的问题分别是:一测量时人为误差,二移动物台的精度,三绘图的准确性。
往往做一个样品用很长时间,一天若需大量做此工作,人会很疲劳影响测试精度。
而现在利用半自动测试系统(FEM-7000) 可以大大提高效率与精度。
首先硬度计主机具有自动打压痕功能,第二由于采用自动载物台,可以在测试前将要测点的坐标值一次输入,仪器会自动找到设置点,位移回复精度在2 m以内,第三仪器测试后,由打印机打印一份标准报告,包括数据与曲线图,也可以利用Windows 中的Word软件自己编辑,在报告中任意插入文字、数字及图片,另外打印机还可以打印金相组织的图谱。
重点介绍半自动显微硬度测试系统的功能:FEM-7000半自动显微硬度测试系统是一台以日本F-T公司(FUTURE-TECH CORP.)生产的FM-700型显微硬度计为主机,由电脑控制的自动载物台及高分辨率的CCD图象采集游标测量装置组成的显微硬度测量系统。
该系统由三部分组成:1. FM-700显微硬度计2. 自动载物台及PC电脑控制器3. 高分辨CCD图象采集装置及电脑游标测量装置和数据处理激光打印系统。
齿轮加工中渗碳淬火和渗碳质量分析
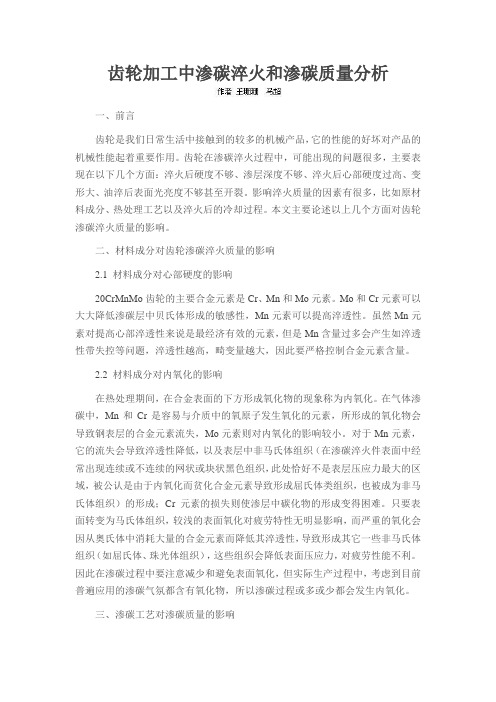
齿轮加工中渗碳淬火和渗碳质量分析一、前言齿轮是我们日常生活中接触到的较多的机械产品,它的性能的好坏对产品的机械性能起着重要作用。
齿轮在渗碳淬火过程中,可能出现的问题很多,主要表现在以下几个方面:淬火后硬度不够、渗层深度不够、淬火后心部硬度过高、变形大、油淬后表面光亮度不够甚至开裂。
影响淬火质量的因素有很多,比如原材料成分、热处理工艺以及淬火后的冷却过程。
本文主要论述以上几个方面对齿轮渗碳淬火质量的影响。
二、材料成分对齿轮渗碳淬火质量的影响2.1 材料成分对心部硬度的影响20CrMnMo齿轮的主要合金元素是Cr、Mn和Mo元素。
Mo和Cr元素可以大大降低渗碳层中贝氏体形成的敏感性,Mn元素可以提高淬透性。
虽然Mn元素对提高心部淬透性来说是最经济有效的元素,但是Mn含量过多会产生如淬透性带失控等问题,淬透性越高,畸变量越大,因此要严格控制合金元素含量。
2.2 材料成分对内氧化的影响在热处理期间,在合金表面的下方形成氧化物的现象称为内氧化。
在气体渗碳中,Mn和Cr是容易与介质中的氧原子发生氧化的元素,所形成的氧化物会导致钢表层的合金元素流失,Mo元素则对内氧化的影响较小。
对于Mn元素,它的流失会导致淬透性降低,以及表层中非马氏体组织(在渗碳淬火件表面中经常出现连续或不连续的网状或块状黑色组织,此处恰好不是表层压应力最大的区域,被公认是由于内氧化而贫化合金元素导致形成屈氏体类组织,也被成为非马氏体组织)的形成;Cr元素的损失则使渗层中碳化物的形成变得困难。
只要表面转变为马氏体组织,较浅的表面氧化对疲劳特性无明显影响,而严重的氧化会因从奥氏体中消耗大量的合金元素而降低其淬透性,导致形成其它一些非马氏体组织(如屈氏体、珠光体组织),这些组织会降低表面压应力,对疲劳性能不利。
因此在渗碳过程中要注意减少和避免表面氧化,但实际生产过程中,考虑到目前普遍应用的渗碳气氛都含有氧化物,所以渗碳过程或多或少都会发生内氧化。
渗碳齿轮最佳有效硬化层深度
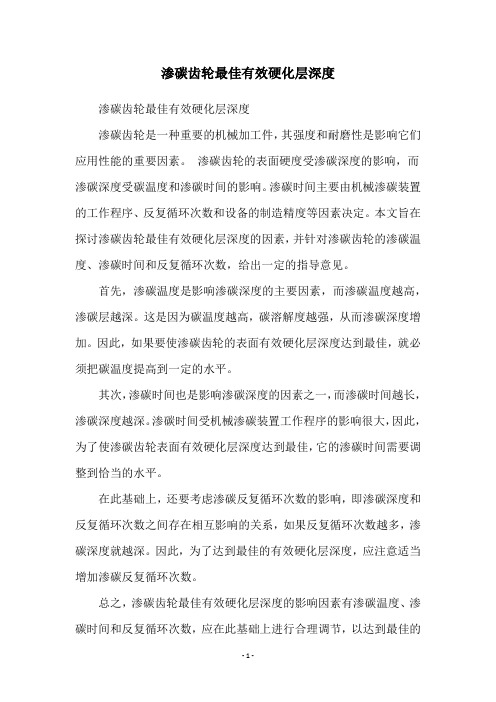
渗碳齿轮最佳有效硬化层深度
渗碳齿轮最佳有效硬化层深度
渗碳齿轮是一种重要的机械加工件,其强度和耐磨性是影响它们应用性能的重要因素。
渗碳齿轮的表面硬度受渗碳深度的影响,而渗碳深度受碳温度和渗碳时间的影响。
渗碳时间主要由机械渗碳装置的工作程序、反复循环次数和设备的制造精度等因素决定。
本文旨在探讨渗碳齿轮最佳有效硬化层深度的因素,并针对渗碳齿轮的渗碳温度、渗碳时间和反复循环次数,给出一定的指导意见。
首先,渗碳温度是影响渗碳深度的主要因素,而渗碳温度越高,渗碳层越深。
这是因为碳温度越高,碳溶解度越强,从而渗碳深度增加。
因此,如果要使渗碳齿轮的表面有效硬化层深度达到最佳,就必须把碳温度提高到一定的水平。
其次,渗碳时间也是影响渗碳深度的因素之一,而渗碳时间越长,渗碳深度越深。
渗碳时间受机械渗碳装置工作程序的影响很大,因此,为了使渗碳齿轮表面有效硬化层深度达到最佳,它的渗碳时间需要调整到恰当的水平。
在此基础上,还要考虑渗碳反复循环次数的影响,即渗碳深度和反复循环次数之间存在相互影响的关系,如果反复循环次数越多,渗碳深度就越深。
因此,为了达到最佳的有效硬化层深度,应注意适当增加渗碳反复循环次数。
总之,渗碳齿轮最佳有效硬化层深度的影响因素有渗碳温度、渗碳时间和反复循环次数,应在此基础上进行合理调节,以达到最佳的
有效硬化层深度。
渗碳淬火硬齿面齿轮制造难点的工艺研究

预加工齿形沉割起始点的曲率半径为Θ1沉, 要使渐开线
收稿日期: 2007206211; 修回日期: 2007207220 作者简介: 张立峰 (19722) , 男, 山西太原人, 工程师, 专科。
© 1994-2009 China Academic Journal Electronic Publishing House. All rights reserved.
其长度, 必须确保任意工作面 Θ1< Θ1′, 若被磨齿轮不 满足这个条件就容易产生渐开线长度不足。
112 齿根过渡曲线连接不好产生台阶
齿根缺陷是指磨齿生产实践中容易发生的齿根几
何形状缺陷。在制造过程中, 约有 50% 左右的齿轮有
凸台, 其中有的是齿根两边不对称, 一侧凸台明显, 一
侧过渡好一些; 有的是全齿宽都有凸台, 凸台约占齿
力和使用寿命得到很大提高, 并因结构尺寸小而使齿 轮装置的成本大大降低, 所以越来越广泛地被应用于 船舶、 冶金设备以及挖掘机、 轧机、 起重机上。 齿轮 产品的质量和性能, 除依赖于合理而先进的设计方法 外, 主要决定于齿轮制造水平的高低。
硬齿面齿轮主要有表面淬火齿面、 氮化齿面、 渗 碳淬火磨削齿面三种硬化齿面。 渗碳淬火硬齿面齿轮 精度高, 表面硬度高 (HRC60±2) , 硬度的分布梯度 小, 组织均匀, 不易产生表面裂纹, 且成本低, 解决 了表面淬火齿面、 氮化齿面中存在的一系列问题。 但 在制造过程中容易产生磨削裂纹、渐开线长度不足、齿 根过渡曲线连接不好而产生台阶等现象, 本文将针对 这些问题进行分析研究, 并提出相应的解决方案。 1 渗碳淬火硬齿面齿轮加工过程中存在的主要问题 111 渐开线长度不足
·177·
HRC40, 残余奥氏体小于 10% (见图 4) , 齿顶无碳化物 (见图 5) , 心部组织为低碳板条马氏体 (见图 6)。
渗碳齿轮有效硬化层深度的确定和齿轮疲劳强度试验方法

渗碳齿轮有效硬化层深度的确定和齿轮疲劳强度试验方法李光瑾;叶俭;祝兵寿;陈德华;哈胜男;祖庆川;王伟;薛耀先【摘要】不同用途的硬面齿轮,采用渗碳淬火的方法达到一定的有效硬化层深度.介绍多种使用了若干年的确定渗碳齿轮有效硬化层深度的经验方法.从近年重栽齿轮深层渗碳的实际应用中,深层渗碳深度呈现逐步降低的趋势,不仅对产品抗疲劳性能无碍,更有节能降耗、低碳制造的收获.为快速便捷测量齿轮的疲劳强度,引入一种弯冲试验法.【期刊名称】《柴油机设计与制造》【年(卷),期】2010(016)003【总页数】6页(P36-41)【关键词】齿轮;有效硬化层深度;弯冲试验【作者】李光瑾;叶俭;祝兵寿;陈德华;哈胜男;祖庆川;王伟;薛耀先【作者单位】上海市机械制造工艺研究所有限公司,上海,200070;上海市机械制造工艺研究所有限公司,上海,200070;常州减速机总厂有限公司,常州,213149;上海市机械制造工艺研究所有限公司,上海,200070;上海市机械制造工艺研究所有限公司,上海,200070;常州减速机总厂有限公司,常州,213149;常州减速机总厂有限公司,常州,213149;常州减速机总厂有限公司,常州,213149【正文语种】中文【中图分类】TK41 引言齿轮是一种应用广泛的机械传动零件,在机械装备中起着传递动力、改变转速和旋转方向的重要作用。
按齿轮的传动形式,一般将其分为三类:(1)圆柱齿轮用于平行两轴之间的传动;(2)锥齿轮用于相交两轴之间的传动;(3)蜗轮与蜗杆用于交叉两轴之间的传动。
与依靠摩擦力传递动力的带传动、通过链条与链轮齿啮合传递运动的链传动相比,齿轮传动具有结构简单、传动比相对固定、传动比精准、传递负荷大等优点。
统计分析表明,齿轮的失效,主要是轮齿表面的接触疲劳和齿根部的弯曲疲劳,所有关于材料以及组织性能的试验研究,基本都紧密围绕这一主题。
其中,对于已经选定的材料,选择并实施合适的热处理,对于确保齿轮在工况下的可靠性,热处理工艺过程的节能减排,有着显著的效益。
渗碳淬火齿轮有效硬化层深
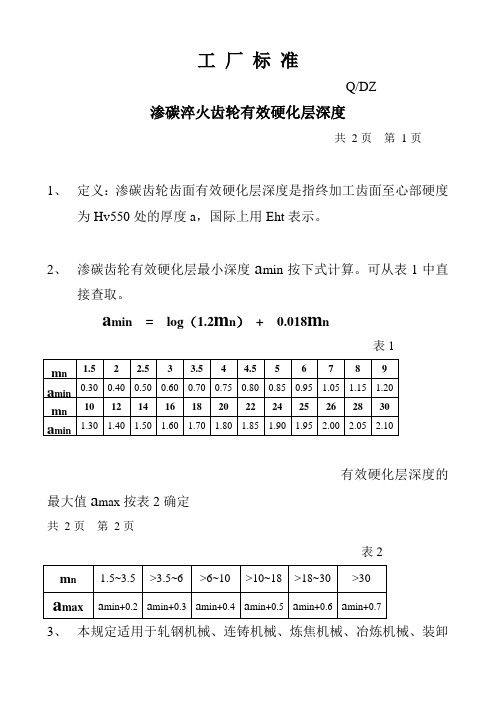
工厂标准
Q/DZ
渗碳淬火齿轮有效硬化层深度
共2页第1页
1、定义:渗碳齿轮齿面有效硬化层深度是指终加工齿面至心部硬度
为Hv550处的厚度a,国际上用Eht表示。
2、渗碳齿轮有效硬化层最小深度a min按下式计算。
可从表1中直
接查取。
a min= log(1.2m n)+ 0.018m n
表1
有效硬化层深度的
最大值a max按表2确定
共2页第2页
表2
3、本规定适用于轧钢机械、连铸机械、炼焦机械、冶炼机械、装卸
机械的传动齿轮。
4、特殊工况用渗碳齿轮的有效硬化层深度,可根据接触剪应力的大
小另行确定。
6.、本表对于Mn≤8的齿轮而言,其推荐的渗碳深度是合理的,但对于Mn>8的齿轮而言,其数据缺乏合理性。
7. 对于合理的渗碳层深度各国、各公司的标准不同,而且差距还比较大。
各国及各行业推荐的渗碳层深度见表3
表3 各国及各行业推荐的渗碳层深度
注:根据JB/T 8853-2001《圆柱齿轮减速机》渗碳层的深度根据模数选择,当Mn=1.5~6时,渗碳层深度ht=(0.2~0.3)Mn;
当Mn=7~18时,渗碳层的深度ht=(0.15~0.25)Mn(小模数取大值,大模数取小值)。
硬度梯度

浅谈齿轮渗碳淬火有效硬化层及硬度梯度北京时代利和科技发展有限公司随着机械工业的发展,对齿轮的质量要求日益提高,而齿轮的强度寿命和制造精度与热处理质量有很大关系。
为了检验齿轮材料热处理质量,在1987年以前,我国的齿轮渗碳淬火内在质量检验标准多为终态金相检验标准。
由于检测仪器的精度、分辨率等因素以及检验人员的经验参差不齐,造成检验结果有很大差异和争议。
为了解决金相法内在检验存在的弊端,机械部在1987年借鉴了DIN.ISO等标准中有关内容,修订了我国现行齿轮渗碳淬火内在质量检验标准。
此检验标准中,其金相组织检验标准基本与原标准相似,主要是对渗碳层深度及碳浓度梯度的测定作了较大的修改。
下面就渗碳层深度和碳浓度梯度分别采用金相法与硬度法测定进行简述。
一、 渗碳层深度的检测1.1、金相法1.1.1、取本体或与零件材料成分相同,预先热处理状态基本相似的圆试样或齿形试样进行检测。
1.1.2、送检试样热处理状态为平衡状态,即退火状态。
1.1.3、低碳钢渗层深度为:过共析层+共析层+1/2亚共析层。
1.1.4、低碳合金钢渗层深度为:过共析层+共析层+亚共析层。
1.2、硬度法1.2.1、取样方法同金相法取样方法一致。
1.2.2、送检试样状态为淬火+回火状态。
1.2.3、渗碳深度用有效硬化层来表示,其极限硬度根据不同要求进行选择。
1.2.4、有效硬化层深度(DCp):从试样表面测至极限硬度(如HV550)之间垂直距离。
1.3、两种关于渗碳深度检测的方法存在着一定的对应关系,下面用图形来描述。
从图中可看出:DCp(芯部)>DCp(HV500)>DCp(HV550)DCp(HV550)对应渗碳层中碳含量约为0.35~0.38%,此界限处即为金相法中1/2亚共析层处。
DCp(HV500)对应渗碳层中碳含量约为0.31~0.33%,此界限处为金相法中1/2亚共析层处。
DCp(芯部)对应渗碳层中碳含量为基体碳含量,一般为0.17~0.23%,此界限处为金相法中基体组织。
浅谈齿轮渗碳淬火有效硬化层及硬度梯度

浅谈齿轮渗碳淬火有效硬化层及硬度梯度随着机械工业的发展,对齿轮的质量要求日益提高,而齿轮的强度寿命和制造精度与热处理质量有很大关系。
为了检验齿轮材料热处理质量,在1987年以前,我国的齿轮渗碳淬火内在质量检验标准多为终态金相检验标准。
由于检测仪器的精度、分辨率等因素以及检验人员的经验参差不齐,造成检验结果有很大差异和争议。
为了解决金相法内在检验存在的弊端,机械部在1987年借鉴了DIN.ISO等标准中有关内容,修订了我国现行齿轮渗碳淬火内在质量检验标准。
此检验标准中,其金相组织检验标准基本与原标准相似,主要是对渗碳层深度及碳浓度梯度的测定作了较大的修改。
下面就渗碳层深度和碳浓度梯度分别采用金相法与硬度法测定进行简述。
一、渗碳层深度的检测1.1、金相法1.1.1、取本体或与零件材料成分相同,预先热处理状态基本相似的圆试样或齿形试样进行检测。
1.1.2、送检试样热处理状态为平衡状态,即退火状态。
1.1.3、低碳钢渗层深度为:过共析层+共析层+1/2亚共析层。
1.1.4、低碳合金钢渗层深度为:过共析层+共析层+亚共析层。
1.2、硬度法1.2.1、取样方法同金相法取样方法一致。
1.2.2、送检试样状态为淬火+回火状态。
1.2.3、渗碳深度用有效硬化层来表示,其极限硬度根据不同要求进行选择。
1.2.4、有效硬化层深度(DCp):从试样表面测至极限硬度(如HV550)之间垂直距离。
1.3、两种关于渗碳深度检测的方法存在着一定的对应关系,下面用图形来描述。
从图中可看出:DCp(芯部)>DCp(HV500)>DCp(HV550)DCp(HV550)对应渗碳层中碳含量约为0.35~0.38%,此界限处即为金相法中1/2亚共析层处。
DCp(HV500)对应渗碳层中碳含量约为0.31~0.33%,此界限处为金相法中1/2亚共析层处。
DCp(芯部)对应渗碳层中碳含量为基体碳含量,一般为0.17~0.23%,此界限处为金相法中基体组织。
渗碳齿轮齿根部的硬化层深度分析

3 试验结果分析
齿顶、齿根与 节 圆 硬 化 层 误 差 主 要 产 生 在 渗 碳 和 淬火冷却两个环节,齿顶、齿根硬化层深度与节圆硬化 层深度的偏差百分比见表Байду номын сангаас3。
齿顶硬化层深度偏差百分比齿顶硬化层深度节圆硬化层深度节圆硬化层深度100齿根硬化层深度偏差百分比齿根硬化层深度节圆硬化层深度节圆硬化层深度100齿根和渗碳气氛接触的面积小于扩散路径上的面积而节圆和渗碳气氛接触的面积大于扩散路径上的面积在相同的吸碳面积下齿根处渗碳层的碳浓度低于节圆处的碳浓度在淬火冷却时齿根处和淬火介质接触的面积小于热量传递路径上的面积而节圆处和淬火介质接触的面积大于热量传递路径上的面积在表面换热系数相同的条件下齿根冷却慢节圆冷却快
齿轮渗碳 时 ,除 了 齿 顶 面 的 渗 碳 扩 散 外 ,渐 开 线 齿面也在渗碳扩散,齿顶的渗碳层碳浓度是齿顶和齿 面两个面渗碳扩散的叠加( 图 5) ,再加上齿顶部位在 淬火冷却时冷却速度最快,因此渗碳淬火后齿顶部位 的硬化层深度较深,从表 3 结果可以看出齿顶硬化层 深度比节圆高 12. 9% ~ 21. 0% 。
( a) tooth profile sample; ( b) gear sample
2. 2 硬化层深度 试样渗碳淬火后的硬化层深度见表 1。由表 1 可
以看出,齿顶的硬化层深度最深,齿根最浅; 但齿轮试
第4 期
黎丽君: 渗碳齿轮齿根部的硬化层深度分析
97
样由于质量大,淬火冷却时受淬透性限制,心部硬度较 低,齿根的硬化层深度较浅。
表 1 4820H 钢试样渗碳淬火、回火后的硬化层深度 Table 1 Hardening case depth of the 4820H steel samples after
渗碳淬火齿轮件的硬化层深设计与控制
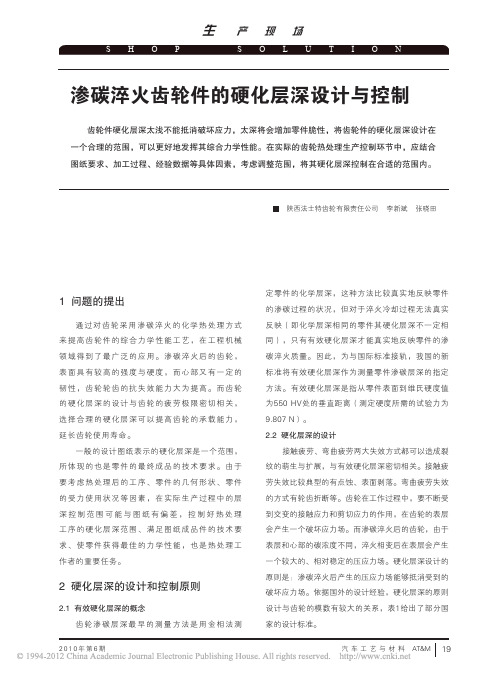
汽 车 工 艺 与 材 料 AT&M 19
生 产现场
SHOP
SOLUTION
表1
国家
美国ANSI/ ACMA2004
美国ANSI/ ACMA2001
英国 BS公司
德国DIN3990
模数/mm 层深/mm
1.45~1.85 0.25~0.50
设计标准
1.85~2.45
2.45~3.00
0.38~0.64
另据资料提供的经验公式也可作为齿轮硬化层深
设max·u )/〔HV·cosβb·(u
±1)2〕
(1)
式中,t 为渗碳层的最小深度,mm;a 为相啮合齿
轮 副 的 公 称 中 心 距 , m m ;α t 为 齿 轮 端 面 啮 合 角 , (°);δ max为最大接触应力,MPa;u 为相啮合 齿轮副齿数比(z 2/z 1);HV为齿面渗碳层的维氏硬 度;βb为基圆螺旋角,(°);小括号中的“+”用 于外啮合,“-”用于内啮合。
2.3 热处理工艺过程对硬化层深的控制
针对热处理渗碳环节,其对硬化层深的控制要综
渗碳工艺对WCCo梯度硬质合金的梯度结构和硬度的影响
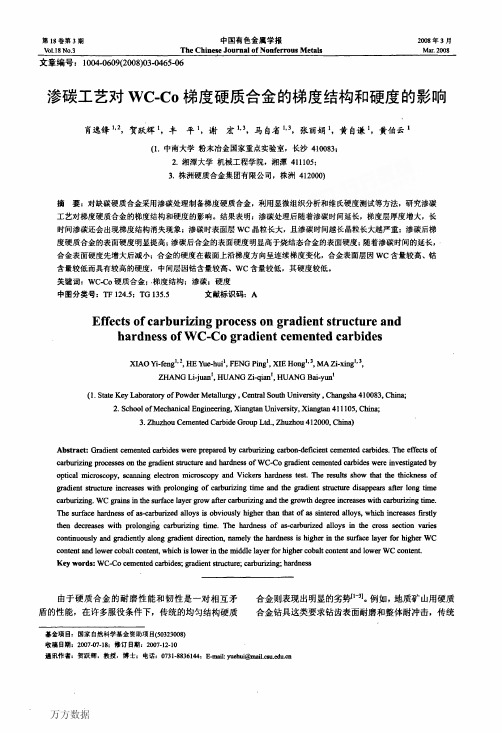
33.803%。
C03W3C+2C=3WC+3Co
(2)
C06W6C+5C=6WC+6Co
(3)
刘咏等【8-10】从扩散热力学和动力学详细讨论梯度 结构的形成机理,认为钴梯度的形成主要受碳扩散和 WC晶粒长大导致的液相流动的影响。渗碳处理初期, 表层由于碳势较高,先于内部出现液相,溶解在液相
所有待测试样的表面和横切面进行抛光处理。采 用Leica公司的MeF3A金相显微镜和Q550图像分析 仪,以及扫描电子显微镜(JSM-6360LV)进行微观结构
Key words:WC—Co cemented carbides;gradient structure;carburizing;hardness
由于硬质合金的耐磨性能和韧性是一对相互矛 盾的性能,在许多服役条件下,传统的均匀结构硬质
合金则表现出明显的劣势n-31。例如,地质矿山用硬质 合金钻具这类要求钻齿表面耐磨和整体耐冲击,传统
第18卷第3期 、bI.18 No.3
中国有色金属学报 The Chinese Journal of Nonferrous Metals
文章编号:1004.0609(2008)03-0465—06
2008年3月 M札2008
渗碳工艺对WC.Co梯度硬质合金的梯度结构和硬度的影响
肖逸锋1,一,贺跃辉1,丰平1,谢宏1一,马自省1一,张丽娟1,黄自谦1,黄伯云1
万方数据
第18卷第3期
肖逸锋,等:渗碳工艺对WC.Co梯度硬质合金的梯度结构和硬度的影响467
、ⅣC+Co+叩三相区之间形成富钴层。可见,W原子向 合金表面迁移也是梯度结构形成的原因之一。
图l烧结态缺碳硬质合金的显微组织 Fig.1 Microstructure of as—sintered WC一6Co carbon-deficient cemented carbides showing WC,Co and叩phase(bright,dark and gray phases referto WC,Co and,7 phase,respectively)
齿轮淬火的最佳[1]..(戴忠森)
![齿轮淬火的最佳[1]..(戴忠森)](https://img.taocdn.com/s3/m/6f0fd8f34693daef5ef73da0.png)
齿轮淬火的“最佳”硬化层深与“适当”硬化层深戴忠森众所周知,齿轮的淬硬层深“过浅”,对接触和弯曲承载能力都不利。
但淬硬层也不是越深越好,最佳或适当的硬化层深度,可使齿面和齿根都具有较高的强度(承载能力)。
另外,不同的热处理方法,其“最佳”值也不是一样的。
二十世纪七、八十年代,随着齿轮强度计算方法ISO标准的公布,以及国内GB/3480“圆柱齿轮承载能力计算方法”标准的实施,特别是工业硬齿面齿轮的广泛采用,国内外齿轮工作者(专家、学者),就热处理硬化层深问题,进行了大量的试验研究和理论分析。
其实质都是基于接触(弯曲)疲劳强度,其核心问题是:疲劳裂纹发生(萌生)在何处?破坏后的形状是点蚀(pitting贝壳状),还是片蚀(剥落spalling)?研究表明,一般软齿面大多是点蚀,而硬齿面大齿轮大多是剥落(片蚀)。
疲劳裂纹的萌生,有可能在表面,也有可能在表层。
至今,有关硬齿面齿轮接触疲劳强度(剥落)计算的理论和方法,主要有:最大剪切应);正交剪切应力(τyz);当量剪切应力(τeffa);深部接触应力;最大剪切力τmax(τ45°应力/剪切强度的峰值;正交剪切应力/强度(硬度)(τyz/HV)max;当量剪切应力/强度的峰值等,通过理论计算可以确定接触疲劳强度(安全系数);或者确定最佳淬硬层深度。
这些理论和方法一直都有争议,因此至今也没有一个权威的理论和方法被大家所能完全接受。
所谓“最佳硬化层深”,其说法也是较含糊的,而且众说不一,以渗碳淬火齿轮为例,德国DIN3990,硬化(渗碳)层深度,给出一个经验公式:(推荐)Eht= 0.15m n(m n——法面模数)(1)。
该经验公式,有一个突出的问题,就是未考虑实际载荷的情况。
所以,对于轻载齿轮,允许比经验公式稍浅的硬化层深度。
Thomas Tobie近年来提出在用ISO/DIN 进行标准化承载能力计算时,考虑硬化层深度对承载能力的影响,引入了影响系数Z Eht(接触承载能力影响系数);УEht(弯曲承载能力影响系数)。
- 1、下载文档前请自行甄别文档内容的完整性,平台不提供额外的编辑、内容补充、找答案等附加服务。
- 2、"仅部分预览"的文档,不可在线预览部分如存在完整性等问题,可反馈申请退款(可完整预览的文档不适用该条件!)。
- 3、如文档侵犯您的权益,请联系客服反馈,我们会尽快为您处理(人工客服工作时间:9:00-18:30)。
浅谈齿轮渗碳淬火有效硬化层及硬度梯度
随着机械工业的发展,对齿轮的质量要求日益提高,而齿轮的强度寿命和制造精度与热处理质量有很大关系。
为了检验齿轮材料热处理质量,在1987年以前,我国的齿轮渗碳淬火内在质量检验标准多为终态金相检验标准。
由于检测仪器的精度、分辨率等因素以及检验人员的经验参差不齐,造成检验结果有很大差异和争议。
为了解决金相法内在检验存在的弊端,机械部在1987年借鉴了DIN.ISO等标准中有关内容,修订了我国现行齿轮渗碳淬火内在质量检验标准。
此检验标准中,其金相组织检验标准基本与原标准相似,主要是对渗碳层深度及碳浓度梯度的测定作了较大的修改。
下面就渗碳层深度和碳浓度梯度分别采用金相法与硬度法测定进行简述。
一、渗碳层深度的检测
1.1、金相法
1.1.1、取本体或与零件材料成分相同,预先热处理状态基本
相似的圆试样或齿形试样进行检测。
1.1.2、送检试样热处理状态为平衡状态,即退火状态。
1.1.3、低碳钢渗层深度为:过共析层+共析层+1/2亚共析层。
1.1.4、低碳合金钢渗层深度为:过共析层+共析层+亚共析层。
1.2、硬度法
1.2.1、取样方法同金相法取样方法一致。
1.2.2、送检试样状态为淬火+回火状态。
1.2.3、渗碳深度用有效硬化层来表示,其极限硬度根据不同要
求进行选择。
1.2.4、有效硬化层深度(DCp):从试样表面测至极限硬度(如
HV550)之间垂直距离。
1.3、两种关于渗碳深度检测的方法存在着一定的对应关系,下面
用图形来描述。
从图中可看出:DCp(芯部)>DCp(HV500)>DCp(HV550)
DCp(HV550)对应渗碳层中碳含量约为0.35~0.38%,此界限处即为金相法中1/2亚共析层处。
DCp(HV500)对应渗碳层中碳含量约为0.31~0.33%,此界限处为金相法中1/2亚共析层处。
DCp(芯部)对应渗碳层中碳含量为基体碳含量,一般为0.17~0.23%,此界限处为金相法中基体组织。
1.4、结论
从图中可以看出,DCp(HV500)、DCp(HV550)是不相等的,而在金相法检测时,这两点是近似相等的,故用硬度法测试渗碳层深度结果更精确,更直观,减少了人为误差。
二、渗碳层碳浓度梯度(即硬度梯度)
为了防止渗碳淬火齿轮表面出现剥落、点蚀,提高齿轮承载能力,必须要求渗碳层渗碳浓度从表面至芯部应保持平滑的梯度。
这种斜度一般推荐为0.25mm深度,碳含量最多下降0.10%。
碳浓度梯度检测采用剥层法进行,因此方法操作比较复杂,检验时间比较长,在实际生产中不经常使用。
这一指标在现行国家标准中采用硬度梯度来反映。
硬度梯度在相关标准中又叫“至芯部硬度降”,即在有效硬化层范围内,自齿轮表面向芯部方向的硬度梯度,用“△HV/△EHt”
来表示,“△HV”为硬度变化量,“△EHt”为有效硬化层深度的变化量。
这一指标反映了有效硬化层内硬度的平缓程度,不但反映了渗碳层浓度梯度问题,同时也反映了淬火质量,指标中规定了有效硬化层深度下降0.1mm(△EHt),硬度下降应小于45HV(△HV)。
综上所述,渗碳层中碳浓度梯度检测采用硬度法优于剥层法。