渗碳淬火质量验收规范
热处理特殊外包工艺过程确认检查评价标准

记录以核实是否按委托工艺要求进行热处理作业。对最终检验记录还应进行实地抽验, 要求也被视为严重不合格,不得分。
记录当场测得的数据以确认其保存的记录是否真实、准确、可靠。
存在其他可整改问题,每项酌情扣 1~3 分。
评价准则:
1、 资质确认项目为否决项,出现严重不符合时应更换供应商。 2、 检查确认时其他项目中只允许出现一个严重不符合项,如又出现第二个严重不符合项,则也应考虑更换供应商。 3、检查后合计评分分值≥85 分确认通过;评分分值<70 分为不符合要求,应考虑更换供应商;70≤评分分值<85 分为整改单位,要求限期在 1 个月内将不合格 项目整改完成,第二次确认检查评分分值<85 分的供应商将同样视为不符合要求,应考虑更换供应商;各次检查所有开出的不符合项目均应进行有效整改。
料以证明这些机床是否符合高频、中频、工频表面 淬火的工艺应用频率要求,并查看这些淬火机床的 开机运作状态及相应功能(如自动冷却喷水等),判 断其机床是否处于良好正常运行。
2.3 热处理方法表面发黑工艺必须具备的基本设备: ⑴ 除锈池; ⑵ 去油池; ⑶ 发黑池; ⑷ 皂化池; ⑸ 发黑前后用的若干高温、常温清洗池; ⑹ 用于增加发黑光亮度效果的高温油池。 对照供应商提供的发黑工艺流程判断发黑处理
行有效控制。
第 2 页 共3页
热处理特殊外包工艺过程确认检查评价标准
热处理工艺过程(常规热处理:调质、淬火、渗碳、表面发黑等)
项目分类
检查内容和方法
评分标准
满分分值
4 确认供应商
4.1 检测设施确认:
的检测 能力满
⑴ 是否具备基本的硬度测试仪器;
所有检查内容符合要求,给予满分。
足工艺 过程要 求
⑵ 加热炉自动温控记录仪; ⑶ 人工操控的仪器(如测温、金相、化学分析等)。 ⑷ 各检测仪器设备是否检定合格有效并有相应检定证明。
渗碳淬火质量缺陷分析

齿轮渗碳后淬火的质量分析摘要:通过对齿轮渗碳淬火后出现质量问题的分析和处理,论述了齿轮淬火产生缺陷的原因,提出了控制淬火过程和合理选用淬火介质应该注意的一些问题。
1 齿轮渗碳淬火常见质量问题(1)淬火后硬度不足、硬度分布不均匀、硬化深度不够;(2)淬火后心部硬度过高;(3)淬火变形超差;(4)淬火开裂;(5)油淬后表面光亮度不够。
这类质量问题的出现往往与齿轮的材质、前处理、淬火加热、渗碳碳势和淬火冷却有关。
在排除材质、前处理和加热渗碳中的问题后,淬火介质及相关技术的作用就特别突出了。
近年来国外对淬火冷却问题的研究证明,它是提高热处理质量最值得注意的问题。
渗碳齿轮淬火常用油作冷却介质。
因此,下面将首先分析齿轮淬火产生质量问题与淬火介质特性和用法的关系,并指出了淬火介质冷却速度的特点。
最后介绍了常用淬火介质的特点和选用时的注意事项。
1.1 硬度不足与硬化层深度不够淬火冷却速度偏低是造成齿轮淬火硬度不足、硬度不均和硬化深度不够的原因,冷却偏低又可以分为高温阶段冷速不足、中低温阶段冷速不足以及低温阶段冷速不足等情况。
如对于中小齿轮,淬火硬度不足往往是中高温阶段冷速不足所致,而模数大的齿轮要求较深淬硬层时,提高低温冷却速度就非常必要了。
对于淬火用油,一般说,油的蒸气膜阶段短、中温冷速快、低温冷却速度快,往往能获得高而且均匀的淬火硬度和足够的淬硬深度。
工件装挂方式对淬火冷却效果也有明显影响。
要使淬火油流动通畅,并配备和使用好搅拌装置,才能得到更好的冷却效果。
提高淬火介质的低温冷却速度,可以增大淬硬层深度。
在渗层碳浓度分布相同的情况下,采用低温冷却速度高的淬火油,往往获得更深的淬火硬化层,因此,采用冷却速度快的淬火油,缩短渗碳时间,也能获得要求的淬硬层深度。
要求的渗碳淬硬层深度越大,这种方法缩短渗碳时间的效果越明显。
1.2 淬火后心部硬度过高这类问题主要与原材料淬透性、所选淬火油冷速过快或其低温冷却速度过高有关。
渗碳淬火组织评级

生产过程中酸洗法进行磨削烧伤的控制,当出现争议时可再用金相组织 法进行最终的判断
30g/L的硝酸水溶液
酸洗法介绍
溶液配比: 配好三种溶液 1、30g/L 的硝酸水溶液 2、50g/L 的盐酸酒精溶液 3、 50g/L 的氢氧化钠水溶液
酸洗法介绍
• 在酸洗前一定要用酒精或洗洁精去处零件表面的 油污和脏物,并用清水冲洗,确保零件表面非常
干净,这个清洗步骤非常重要,零件表面清洗不 干净会引起误判。
• 根据清水冲洗
水溶液
干净
50g/L 的盐酸 25秒 清水冲洗
酒精溶液
干净
吹干
清水冲洗 30秒 50g/L 的氢氧
况确定;常啮合齿轮1-5级,换档齿轮1-4级。
碳化物评级图
钢件渗碳金相检验
抛光态下的内氧化
腐蚀态下的内氧化
钢件渗碳金相检验
• 非马氏体组织:渗碳淬火件表面层中经常出现连续或不连续的 网状或块状黑色组织,主要由于内氧化而贫合金化元素导致形 成屈氏体类组织,一般规定不超过0.02mm.
• 减少非马氏体组织的措施: • 1)尽可能用低碳烃和高纯度气体做制备渗碳气体的原料气; • 2)尽可能选用含Cr、Ti、V、B元素的钢; • 3)从工艺和设备上采取措施,保证炉气不受空气污染; • 4)尽可能采用快速的淬火冷却介质和冷却方式。
钢件渗碳金相检验
钢件渗碳金相检验
钢件渗碳金相检验
• 适用于渗碳淬硬层有效深度大于0.3mm的汽车齿轮。 • 放大倍数:400X • 检验部位: 同芯部硬度 • 铁素体:1-3级
渗碳、淬火和回火
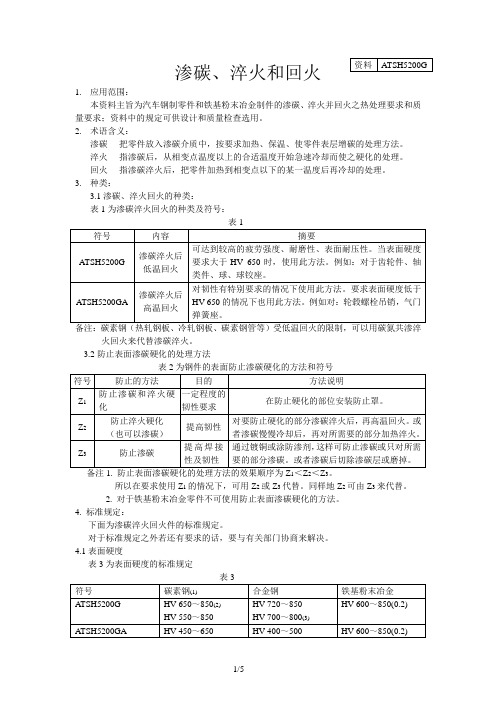
渗碳、淬火和回火1. 应用范围:本资料主旨为汽车钢制零件和铁基粉末冶金制件的渗碳、淬火并回火之热处理要求和质量要求;资料中的规定可供设计和质量检查选用。
2. 术语含义:渗碳----把零件放入渗碳介质中,按要求加热、保温、使零件表层增碳的处理方法。
淬火----指渗碳后,从相变点温度以上的合适温度开始急速冷却而使之硬化的处理。
回火----指渗碳淬火后,把零件加热到相变点以下的某一温度后再冷却的处理。
3. 种类:3.1渗碳、淬火回火的种类: 表1为渗碳淬火回火的种类及符号:备注:碳素钢(热轧钢板、冷轧钢板、碳素钢管等)受低温回火的限制,可以用碳氮共渗淬火回火来代替渗碳淬火。
3.2防止表面渗碳硬化的处理方法123 所以在要求使用Z 1的情况下,可用Z 2或Z 3代替。
同样地Z 2可由Z 3来代替。
2. 对于铁基粉末冶金零件不可使用防止表面渗碳硬化的方法。
4. 标准规定:下面为渗碳淬火回火件的标准规定。
对于标准规定之外若还有要求的话,要与有关部门协商来解决。
4.1表面硬度表3为表面硬度的标准规定1/5注(1)包括热轧钢板,冷轧钢板,碳素钢管。
(2)适用于小件中硬化层深要求在0.5T以上的时候。
(3)适用于差速器齿轮。
4.2硬化层深:4.2.1钢件表4为硬化层深度的标准规定。
在表面硬度要求低于Hv650时,使用全硬化层深。
表4例1:0.5G,磨削部位的磨削后的有效硬化层深度为0.5mm。
例2:0.5GT,磨削部位的磨削后的全层硬化深度为0.5mm。
2.希望使用不带( )的硬化层深的指定值。
3.一个零件中能同时指定磨削部位的层深和非磨削部位的层深。
此时要考虑磨削量方可指定。
对于孔的内径来讲,其磨削前的层深(0.2~0.4mm)已经很薄,因而在此种情况下,希望由表5来确定。
对于象差速齿轮或驱动小齿轮那样转速相差比较大的情况,回转速度大的一方的层深要比表6中的标准值大0.1。
2/5表6 单位mm4.2.2铁基粉末冶金它的硬化层深的标准规格是全硬化层深在0.5T 以上。
热处理渗碳 标准

热处理渗碳标准全文共四篇示例,供读者参考第一篇示例:热处理渗碳是一种通过对金属材料进行高温处理,使得碳元素渗入金属表面从而提高其硬度和强度的工艺方法。
这种工艺在金属加工和制造行业中被广泛应用,特别是在生产汽车零部件、机械零件等领域。
为了确保热处理渗碳的效果和质量,制定了一系列的标准,下面将详细介绍关于热处理渗碳的标准。
热处理渗碳的标准主要包括工艺标准、设备标准和质量标准。
工艺标准是指在进行热处理渗碳时的操作规程、温度控制、保护气氛、处理时间等方面的规定。
设备标准是指用于进行热处理渗碳的设备的技术要求、安全要求、操作规范等方面的规定。
质量标准是指热处理渗碳后金属材料硬度、强度、表面质量等方面的检测和评定标准。
在热处理渗碳的工艺标准中,通常会规定好处理的温度范围、保护气氛的要求、处理时间、冷却方式等。
温度是影响热处理渗碳效果的重要因素,一般来说,温度越高,渗碳的速度越快,但是如果温度过高会导致金属材料的变形、变质等问题。
在进行热处理渗碳时,必须按照工艺标准规定的温度进行处理,以确保产品的质量和性能。
保护气氛也是影响热处理渗碳效果的重要因素之一。
在热处理过程中,金属材料暴露在空气中容易被氧化,影响渗碳的效果。
在进行热处理渗碳时,通常会使用一定的保护气氛,如氮气、氢气等,以减少氧气的接触,保证金属材料的表面光洁度和渗碳效果。
处理时间和冷却方式也是影响热处理渗碳效果的重要因素。
处理时间不仅与温度、保护气氛等因素相关,还与金属材料的厚度、形状等因素有关。
通常情况下,处理时间越长,渗碳的深度和均匀度越好。
而冷却方式则影响着金属材料的组织结构和性能,一般来说,快速冷却可以获得更细小的晶粒和更高的硬度,但也容易导致金属材料的应力增大和变形。
在热处理渗碳的设备标准中,主要包括炉子、加热元件、控制系统、保护气氛系统等方面的技术要求和操作规范。
炉子是进行热处理渗碳的主要设备,通常会根据工件的尺寸、数量、形状等因素选用不同规格和类型的炉子。
渗碳件质量检查
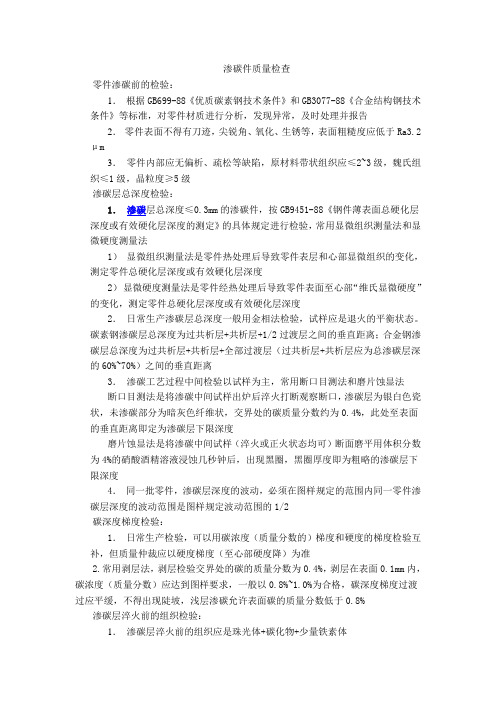
渗碳件质量检查零件渗碳前的检验:1.根据GB699-88《优质碳素钢技术条件》和GB3077-88《合金结构钢技术条件》等标准,对零件材质进行分析,发现异常,及时处理并报告2.零件表面不得有刀迹,尖锐角、氧化、生锈等,表面粗糙度应低于Ra3.2μm3.零件内部应无偏析、疏松等缺陷,原材料带状组织应≤2~3级,魏氏组织≤1级,晶粒度≥5级渗碳层总深度检验:1.渗碳层总深度≤0.3mm的渗碳件,按GB9451-88《钢件薄表面总硬化层深度或有效硬化层深度的测定》的具体规定进行检验,常用显微组织测量法和显微硬度测量法1)显微组织测量法是零件热处理后导致零件表层和心部显微组织的变化,测定零件总硬化层深度或有效硬化层深度2)显微硬度测量法是零件经热处理后导致零件表面至心部“维氏显微硬度”的变化,测定零件总硬化层深度或有效硬化层深度2.日常生产渗碳层总深度一般用金相法检验,试样应是退火的平衡状态。
碳素钢渗碳层总深度为过共析层+共析层+1/2过渡层之间的垂直距离;合金钢渗碳层总深度为过共析层+共析层+全部过渡层(过共析层+共析层应为总渗碳层深的60%~70%)之间的垂直距离3.渗碳工艺过程中间检验以试样为主,常用断口目测法和磨片蚀显法断口目测法是将渗碳中间试样出炉后淬火打断观察断口,渗碳层为银白色瓷状,未渗碳部分为暗灰色纤维状,交界处的碳质量分数约为0.4%,此处至表面的垂直距离即定为渗碳层下限深度磨片蚀显法是将渗碳中间试样(淬火或正火状态均可)断面磨平用体积分数为4%的硝酸酒精溶液浸蚀几秒钟后,出现黑圈,黑圈厚度即为粗略的渗碳层下限深度4.同一批零件,渗碳层深度的波动,必须在图样规定的范围内同一零件渗碳层深度的波动范围是图样规定波动范围的1/2碳深度梯度检验:1.日常生产检验,可以用碳浓度(质量分数的)梯度和硬度的梯度检验互补,但质量仲裁应以硬度梯度(至心部硬度降)为准2.常用剥层法,剥层检验交界处的碳的质量分数为0.4%,剥层在表面0.1mm内,碳浓度(质量分数)应达到图样要求,一般以0.8%~1.0%为合格,碳深度梯度过渡过应平缓,不得出现陡坡,浅层渗碳允许表面碳的质量分数低于0.8% 渗碳层淬火前的组织检验:1.渗碳层淬火前的组织应是珠光体+碳化物+少量铁素体2.渗碳层中有大块或网状碳化物,应建议两次淬火或一次正火,一次淬火,一般碳化物级别小于6级3.渗碳后,心部出现3级以上带状组织或晶粒度小于5级时,应正火后,重新检验合格方可淬火4.渗碳层中出现网状碳化物与游离铁素体不合格时应正火消除渗碳件淬、回火后的硬度检验:1.渗碳件表面硬度检验时,应去除氧化皮,脱碳层、增碳层,应以洛氏和维氏硬度计检验为准2.硬度应符合图样或技术文件规定,一般碳钢(10、20钢)硬度在50~55HRC 或58~63HRC,合金钢硬度在58~63HRC3.硬度终检以实物为准,但允许用随炉不同位置两个以上的试样代替实物检验。
渗碳层深度检验方法(金相法)
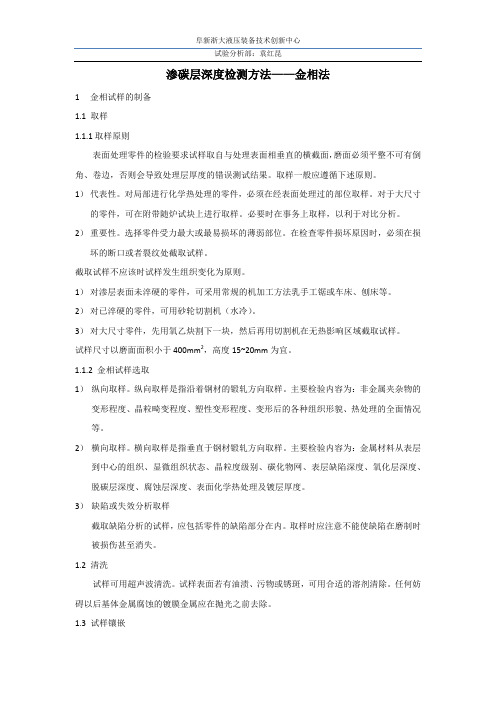
渗碳层深度检测方法——金相法1金相试样的制备1.1 取样1.1.1取样原则表面处理零件的检验要求试样取自与处理表面相垂直的横截面,磨面必须平整不可有倒角、卷边,否则会导致处理层厚度的错误测试结果。
取样一般应遵循下述原则。
1)代表性。
对局部进行化学热处理的零件,必须在经表面处理过的部位取样。
对于大尺寸的零件,可在附带随炉试块上进行取样。
必要时在事务上取样,以利于对比分析。
2)重要性。
选择零件受力最大或最易损坏的薄弱部位。
在检查零件损坏原因时,必须在损坏的断口或者裂纹处截取试样。
截取试样不应该时试样发生组织变化为原则。
1)对渗层表面未淬硬的零件,可采用常规的机加工方法乳手工锯或车床、刨床等。
2)对已淬硬的零件,可用砂轮切割机(水冷)。
3)对大尺寸零件,先用氧乙炔割下一块,然后再用切割机在无热影响区域截取试样。
试样尺寸以磨面面积小于400mm2,高度15~20mm为宜。
1.1.2 金相试样选取1)纵向取样。
纵向取样是指沿着钢材的锻轧方向取样。
主要检验内容为:非金属夹杂物的变形程度、晶粒畸变程度、塑性变形程度、变形后的各种组织形貌、热处理的全面情况等。
2)横向取样。
横向取样是指垂直于钢材锻轧方向取样。
主要检验内容为:金属材料从表层到中心的组织、显微组织状态、晶粒度级别、碳化物网、表层缺陷深度、氧化层深度、脱碳层深度、腐蚀层深度、表面化学热处理及镀层厚度。
3)缺陷或失效分析取样截取缺陷分析的试样,应包括零件的缺陷部分在内。
取样时应注意不能使缺陷在磨制时被损伤甚至消失。
1.2清洗试样可用超声波清洗。
试样表面若有油渍、污物或锈斑,可用合适的溶剂清除。
任何妨碍以后基体金属腐蚀的镀膜金属应在抛光之前去除。
1.3试样镶嵌若试样过于细薄或过软、易碎、或需检验边缘组织、或者为便于在自动磨抛机上研磨试样实验室通常采用可采用热压镶嵌法和浇注镶嵌法较为方便。
所选用先前方法均不得改变试样原始组织。
1.3.1热压镶嵌法将样品磨面朝下放入模中,树脂倒入模中超过样品高度,封紧模子并加热、加压。
渗碳淬火硬化层深度检测标准

渗碳淬火硬化层深度检测标准渗碳淬火是一种常用的表面处理方法,用于提高金属材料的硬度和耐磨性。
在渗碳淬火过程中,碳原子会渗透到金属表面,并与金属原子结合形成碳化物,从而形成硬化层。
硬化层的深度是评估渗碳淬火质量的重要指标之一。
渗碳淬火硬化层深度的检测标准主要有以下几种方法:1. 金相显微镜观察法:这是一种常用的检测方法,通过金相显微镜观察样品的横截面,可以清晰地看到硬化层的深度。
通常,硬化层的深度应符合相关标准要求。
2. 显微硬度计测量法:显微硬度计是一种常用的硬度测试仪器,可以测量材料的硬度。
通过在硬化层上进行一系列硬度测试,可以确定硬化层的深度。
通常,硬化层的深度应达到一定的数值范围。
3. 金相腐蚀法:金相腐蚀是一种将试样浸泡在特定腐蚀液中,以观察和测量试样表面的腐蚀情况的方法。
通过在硬化层上进行金相腐蚀实验,可以确定硬化层的深度。
通常,硬化层的深度应达到一定的腐蚀程度。
4. 电子显微镜观察法:电子显微镜是一种高分辨率的显微镜,可以观察到非常细小的结构。
通过在硬化层上使用电子显微镜观察,可以清晰地看到硬化层的深度。
通常,硬化层的深度应达到一定的微米级别。
以上是常用的渗碳淬火硬化层深度检测标准方法。
在实际应用中,可以根据具体情况选择合适的检测方法。
同时,还需要注意以下几点:1. 检测设备的准确性和精度:选择合适的检测设备,并确保其准确性和精度。
只有准确的检测结果才能有效评估渗碳淬火的质量。
2. 标准要求的合理性:检测标准应该合理,符合实际应用需求。
标准要求过高或过低都会影响渗碳淬火的质量评估。
3. 检测结果的可靠性:在进行检测时,需要保证样品的代表性和一致性。
只有可靠的检测结果才能准确评估渗碳淬火的质量。
总之,渗碳淬火硬化层深度的检测标准是评估渗碳淬火质量的重要指标之一。
通过选择合适的检测方法,并注意检测设备的准确性和精度,以及标准要求的合理性和检测结果的可靠性,可以有效评估渗碳淬火的质量。
这对于提高金属材料的硬度和耐磨性具有重要意义。
渗碳钢的渗碳淬火指定标准hes
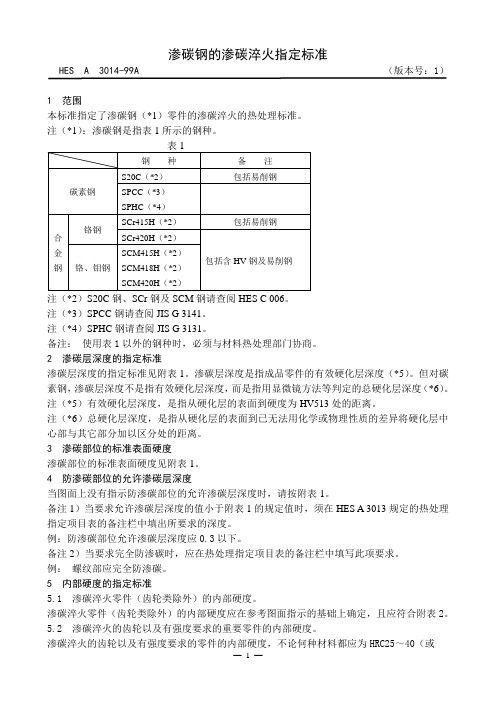
渗碳钢的渗碳淬火指定标准HES A 3014-99A(版本号:1)1 范围本标准指定了渗碳钢(*1)零件的渗碳淬火的热处理标准。
注(*1):渗碳钢是指表1所示的钢种。
注(*2)S20C钢、SCr钢及SCM钢请查阅HES C 006。
注(*3)SPCC钢请查阅JIS G 3141。
注(*4)SPHC钢请查阅JIS G 3131。
备注:使用表1以外的钢种时,必须与材料热处理部门协商。
2 渗碳层深度的指定标准渗碳层深度的指定标准见附表1。
渗碳层深度是指成品零件的有效硬化层深度(*5)。
但对碳素钢,渗碳层深度不是指有效硬化层深度,而是指用显微镜方法等判定的总硬化层深度(*6)。
注(*5)有效硬化层深度,是指从硬化层的表面到硬度为HV513处的距离。
注(*6)总硬化层深度,是指从硬化层的表面到已无法用化学或物理性质的差异将硬化层中心部与其它部分加以区分处的距离。
3 渗碳部位的标准表面硬度渗碳部位的标准表面硬度见附表1。
4防渗碳部位的允许渗碳层深度当图面上没有指示防渗碳部位的允许渗碳层深度时,请按附表1。
备注1)当要求允许渗碳层深度的值小于附表1的规定值时,须在HES A 3013规定的热处理指定项目表的备注栏中填出所要求的深度。
例:防渗碳部位允许渗碳层深度应0.3以下。
备注2)当要求完全防渗碳时,应在热处理指定项目表的备注栏中填写此项要求。
例:螺纹部应完全防渗碳。
5 内部硬度的指定标准5.1 渗碳淬火零件(齿轮类除外)的内部硬度。
渗碳淬火零件(齿轮类除外)的内部硬度应在参考图面指示的基础上确定,且应符合附表2。
5.2 渗碳淬火的齿轮以及有强度要求的重要零件的内部硬度。
渗碳淬火的齿轮以及有强度要求的零件的内部硬度,不论何种材料都应为HRC25~40(或HRC25~38),此种情况,内部硬度不应是参考指示(*7)。
注(*7)齿轮及强度有要求的其它零件,其强度特别是冲击强度对内部硬度影响很大。
如超过了HRC40会导致低冲击值。
防渗涂料法局部渗碳淬火典型工艺

局部防渗碳涂料法的低碳合金钢渗碳淬火工艺简介:本文介绍了采用防渗碳涂料法的低碳钢局部渗碳淬火先进工艺的工序流程、操作规程、技术要求和质量标准。
一.前言:20Cr2Ni4A系列高合金低碳钢局部渗碳淬火工艺,对非渗碳局部普遍采取镀铜防止渗碳。
这种工艺过程较为复杂,生产周期长,成本较高。
用防渗碳涂料法取代镀铜防渗碳的低碳钢局部渗碳淬火新工艺,用防渗碳涂料KT905或AC200代替镀铜防渗,工艺过程简单、周期短、防渗效果好,值得推广使用。
二.防渗碳涂料的局部渗碳淬火工艺介绍1.工艺准备1.1防渗涂料:准备好防渗碳涂料KT905或AC200。
1.2清洗剂:准备好8112清洗剂。
1.3渗碳剂:民用煤油。
盛放在吊桶中,其高度约比炉体高出2米左右,每次渗碳前要求检查桶中煤油数量,不足则补之。
1.4清理排气管及炉内碳黑及其它脏物,定期清理滴油器及滴管。
1.5检查密封情况是否良好,必要时更换密封石棉绳。
1.6检查控制设备及风扇运转情况是否常,检查热电偶位置,准备好校正温度的设备。
1.7准备好清洗零件的水槽、棉纱、砂纸、毛刷、胶手套、涂料盘、钢丝刷等。
2.工序流程去油污→清洗→水洗、干燥→刷涂料、干燥→渗碳→去涂料→预热→淬火→煮水、去盐及防锈→清理3.操作规程3.1去油污: 用砂纸或棉纱去除非渗碳部位的黄锈及整个零件的油污。
3.2清洗:在水槽中,用8112清洗剂按2%-4%配成水溶液,在30℃-40℃下浸泡渗碳零件后刷洗,经常去除溶液表而飘浮的油污。
3.3水洗干燥:清洗后的零件煮清水后靠余热自干,或清水冲洗后烘干(或自然干燥)。
3.4刷涂料干燥:首先清理工作台,使之无油污,然后在桶中搅匀AC200或KT905涂料到涂料盘中,用刷子将涂料均匀涂刷于零件非渗碳部位,一般涂0.2-0.4mm,当渗碳深度大于2mm时,待涂料干燥后再刷一遍。
涂料干硬后检查是否均匀,在脱块处补刷涂料,最后自然干燥或烘干,烘干时温度低于50℃。
钢的渗碳和碳氮共渗、淬火、回火工艺
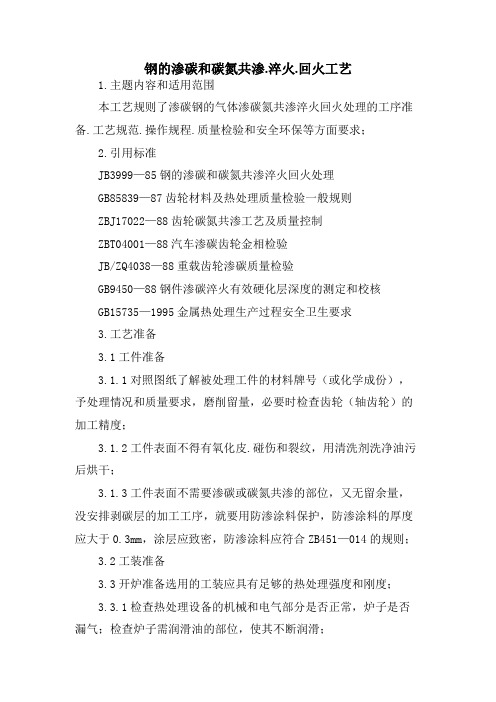
钢的渗碳和碳氮共渗.淬火.回火工艺1.主题内容和适用范围本工艺规则了渗碳钢的气体渗碳氮共渗淬火回火处理的工序准备.工艺规范.操作规程.质量检验和安全环保等方面要求;2.引用标准JB3999—85钢的渗碳和碳氮共渗淬火回火处理GB85839—87齿轮材料及热处理质量检验一般规则ZBJ17022—88齿轮碳氮共渗工艺及质量控制ZBT04001—88汽车渗碳齿轮金相检验JB/ZQ4038—88重载齿轮渗碳质量检验GB9450—88钢件渗碳淬火有效硬化层深度的测定和校核GB15735—1995金属热处理生产过程安全卫生要求3.工艺准备3.1工件准备3.1.1对照图纸了解被处理工件的材料牌号(或化学成份),予处理情况和质量要求,磨削留量,必要时检查齿轮(轴齿轮)的加工精度;3.1.2工件表面不得有氧化皮.碰伤和裂纹,用清洗剂洗净油污后烘干;3.1.3工件表面不需要渗碳或碳氮共渗的部位,又无留余量,没安排剥碳层的加工工序,就要用防渗涂料保护,防渗涂料的厚度应大于0.3mm,涂层应致密,防渗涂料应符合ZB451—014的规则;3.2工装准备3.3开炉准备选用的工装应具有足够的热处理强度和刚度;3.3.1检查热处理设备的机械和电气部分是否正常,炉子是否漏气;检查炉子需润滑油的部位,使其不断润滑;3.3.2检查测温仪表,热电隅是否正常,要定期进行校验;3.3.3定期清理气体渗碳炉炉罐中的碳黑和灰烬;3.4工件的表卡和试样3.4.1根据工件的形状和要求,选用适当的吊具和夹具;3.4.2工件间要有5~10mm的间隙;3.4.3应随炉放臵与装炉工件材质和予处理相同和符合GB8539—87“齿轮材料及热处理质量检验的一般规则”规则的样式,并放臵在有代表性的位臵,以备炉前操作抽样检查;4.渗碳和碳氮共渗淬火回火处理的工艺规范和操作规程4.1渗碳.碳氮共渗处理4.1.1装炉4.1.1.1工件装炉前应把炉温升到渗碳或共渗温度,连续生产时可干上一炉出炉后立即装炉;4.1.1.2工件应装在炉子的有效加热区内,加热区的炉温不得超过±15℃;4.1.1.3每炉装载量不大于设备的装载量;4.1.2气体渗碳工艺规范和操作规程4.1.2.1气体渗碳工艺规范参照图1,低碳合金渗碳钢的渗碳温度取上限;4.1.2.2排气期排气期的渗剂滴入量,参照表1,炉子到温后的排气时间的长短取决于排气程度,应取气进行分析,当CO2和O2的含量低于0.5%时,即可关闭试样孔,转入强渗期;无气体分析仪时,可观察废气火苗的颜色和状态,当火苗呈杏黄色,上升无力时,排气基本结束;一般地排气时间为1~1.5小时;4.1.2.3强渗期,关闭试样孔,点燃排出的废气;检查炉盖及通风机轴处是否漏气;调整煤油.异丙醇的滴入量,滴量多少取决于设备大小,装炉工件表面积的大小及炉子密封的情况,表1的滴量供选择时参考;强渗期炉气成份应控制在表2规则的范围内;有条件应采用红外线CO2碳位自控仪或露点仪控制炉气或用奥氏体分析仪对炉气进行分析,作为调正滴量的依据;强渗期的炉压控制在100~300pa;废气燃烧的火苗高度控制在200~250㎜的长度;根据工件有效硬化层要求和渗速经验,约达到1/2~2/3渗层深度时,抽验第一根试样,根据第一个试样的渗层确定第二个试样的时间,当有效硬化层深度达到或接近工件的有效硬化深度时,即可进入扩散期;4.1.2.4扩散期:扩散期的煤油.异丙醇滴量约为强渗期的0.5倍,为了保证炉压,并同时加滴甲醇,扩散期的时间与工件要求的有效硬化层深度有关,有效硬化层深度愈深,扩散时间要求愈长一些,与工件的碳势(试样的碳势)有关,碳势高要求扩散时间长一些,还与试样渗层深度有关,为了保证工件表面0.85~1.0%的碳浓度和合理的过滤层,扩散时间约为1~3小时;4.1.2.5降温期:抽验的第三个试样,如果网状碳化物≥5级为作正火处理,920℃出炉空冷,对20CrMnMo17Cr2Ni20CrNi2Mo当工件室冷到300-400℃时要放到回火炉中炉冷,防止在表面和次层在空冷时产生马氏体,形成表面裂纹;对于17CrNi2Mo.20Cr2NiMo等Cr.Ni渗碳钢即使碳化物不超级也要出炉空冷,空冷的炉温度为860~880℃;对于碳化物不超级的20CrMnTi.20CrMnMo~840℃,保渗碳齿轮,随炉冷到830温0.5~1H后直接淬火;4.1.3气体碳氮共渗工艺规范和操作规程;4.1.3.1气体碳氮共渗操作规程;4.1.3.2采用煤油加氨氧的气体碳氮共渗工艺曲线4.1.3.3共渗过程其炉气成分应符合下表规则4.2.1工件渗碳后直接淬火;对本质细晶粒钢工件渗碳后可采用直接淬火的方法,以获得所需要的表层和心部硬度以及有效硬化层深度,如20CrMo.20CrMnMo,以及含硼和稀土的合金钢渗碳件;直接淬火一般在炉中降温到830~850℃,均温0.5~1H出炉后淬火工件渗碳后直接淬火另一个条件是渗层金相组织网状碳化物≤4级;工件要求渗层深,炉中碳势又高的情况,容易造成碳化物超级,而对于模数≤5的20CrMnTi.20CrMnMo齿轮,渗碳深度1.2~1.3㎜(含磨量)碳化物不易超级,可以直接淬火,模数大于5的齿轮视渗层的金相组织中网状碳化物的级别而定,如果网状碳化物小于4级可以直接淬火;5级以上则要高温正火,消除网状碳化物或降低网状碳化物级别;4.2.2工件渗碳后空冷后再淬火,按方法有以下几种原因:a.工件渗碳后需要进行机械加工,如制碳层;b.容易发生过热的碳钢和非细晶粒合金钢件,以及某些不宜直接淬火的工件(如需要在压床上淬的齿轮);c.渗层组织如出现网状碳化物超级对于a.b两种情况,炉冷到850~860℃空冷,但对20CrMnMo渗件要求在400℃以下缓冷,否则易再次表层出现马氏体组织形成裂纹,对于C种情况,要求在900~930℃出炉直接空冷;4.2.312CrNi3.12Cr2Ni4.17CrNi2Mo.20CrNi4.20Cr2Ni4.20Cr2Ni4MoA.20Cr2Ni4WA等高强合金渗碳件,渗碳炉冷到920℃出炉空冷(用于制作大模数齿轮),400以下缓冷,并增加一次至二次650~680℃,5~6H的高温回火;这种高温回火称为催化或促变处理,它不仅能改善机械加工性能,更主要它是获得良好淬火组织的条件和保证;必须严格执行;4.2.4碳氮共渗的工件一般都从共渗温度或低于共渗温度出炉直接淬火;4.2.5经过渗碳淬火或碳氮共渗淬的工件,通常采用180℃±10℃的低温回火;4.2.5.1碳氮共渗齿轮回火的温度为180℃±10℃,回火时间3H;4.2.5.2模数1~3的齿轴渗碳淬火后温度200~210℃,时间3H,模数1~3的齿轮渗碳淬火后的回温度220℃±10℃,时间3H4.2.5.3模数3~5的齿轴.齿轮渗碳淬火后进行二次回火;第一次回火温度230℃,时间4H;第二次齿轴的回火温度230℃,回火时间3H;4.2.5.4模数≥6的齿轮.齿轴,渗碳后直接淬火的工件,需要进行三次回火;第一次回火温度230℃,回火时间3H;第二次回火,齿轴的回火温度230℃,时间3H,齿轮的回火温度240℃,时间3H;第三次回火,齿轴的回火温度220℃,时间3H,齿轮的回火温度240℃,时间3H;4.2.5.5模数≥6的齿轮齿轴渗碳后空冷,后加热淬火;进行二次回火;第一次回火温度230℃,时间4H;第二次回火,齿轴的回火温度220℃,时间4H,齿轮的回火温度240℃,时间4H;4.2.5.6前一次回火后,工件空冷到室温或≤50℃,才能进行下一次回火;4.2.5.7工件回火必须放在回火炉的有效加热区内(渗碳淬火的齿轮部分需量出回火炉底部300㎜);4.3渗碳和碳氮共渗淬火回火件的最后处理;4.3.1清理:进行喷砂,以清除赤面的油污和氧化模;4.3.2校直和矫正:用偏摆仪检查齿轴的变形,当超过允许变形时,应对其校直和矫正;随后进行去应力回火;条件允许(淬火工件量少时)应在淬火后马上进行校直,然后再回火;5.质量检验5.1外观:不得有裂纹和碰伤5.2表面硬度5.2.1硬度检验方法,按GB23083《金属洛氏硬试验法》或其他硬度试验法进行;5.2.2表面硬度的偏差范围,表面硬度不得超过下表规则:5.3.1有效硬化层检验方法,按GB《钢的渗碳硬化层有效硬化层深度的测定和校验》中的规则执行;5.3.2有效硬化层深度偏差不得超过下表规则;根据零件的要求,按有关标准进行检定;5.5变形:零件的变形应符合技术要求;6.安全与环保6.1操作者要穿戴好必须的劳动保护用品;6.2执行所用设备的安全操作规程;6.3气体渗碳或碳氮共渗出炉淬火时,同时淬火的工件量大时,应先检查油温,当油温>100℃时,应先降油温后淬火,以防止油槽着火;着火时需用灭火器,石棉被灭火,严禁用水灭火;6.4要防止渗碳炉滴注器渗漏,以免引起炉盖着火,烧毁电机或造成渗剂失火;6.5其它方面按GB15735—1995,金属热处理生产过程安全卫生要求;。
渗碳淬火质量验收规范
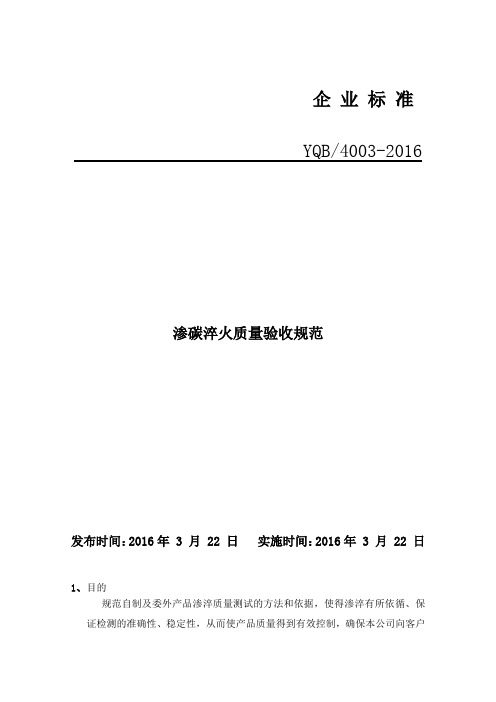
企业标准 YQB/4003-2016渗碳淬火质量验收规范发布时间:2016年 3 月 22 日实施时间:2016年 3 月 22 日1、目的规范自制及委外产品渗淬质量测试的方法和依据,使得渗淬有所依循、保证检测的准确性、稳定性,从而使产品质量得到有效控制,确保本公司向客户提供满意的产品;2、适用范围适用于各类自制或委外产品的渗淬质量检控;3、引用标准(1) GB/T13299-91 金属显微组织评定方法依据;(2) JB/T 9211-1999 中碳钢与中碳合金结构钢马氏体等级标准;(3) GBT 25744-2010 钢件渗淬回火金相检验标准;(4)GB/T 9450-2005 钢件渗淬硬化层深度的测定和校核依据;(5)GB/T11354-2005 金相组织检验依据;4、名词解释(1) 渗淬:渗碳淬火;(2)0收1退:同批次件抽检1件,如合格则整批次接受,不合格整批次退货;(3)试块:渗淬的随炉圆柱形试块,直径25mm*长度50mm,粗糙度Ra3.2;(4)心部硬度:在齿宽中部横截面上,轮齿中心线与齿根圆相交处的硬度;5、验收项目及标准渗淬零部件表面硬度、心部硬度、硬化层深、金相组织、表面质量、脱碳层深等;5.1渗淬件表面质量的检验1)为得到较为准确的检测结果,零件的检测部位均应进行表面打磨、去掉氧化皮等杂质(成品件或不允许表面打磨的零件检测时,先不进行表面打磨直接在零件不影响外观表面检测。
若检测结果不合格时,则须进行破坏性打磨检测,若打磨后检测合格,则判定合格);2)每一零件原则上应至少检测三次,取其平均值作为评价结果。
(第一针为测试针,零件较小或无法取多点除外);3)当热处理零件表面产生脱碳现象时,须将零件表面磨深0.5~2mm后再进行检测;4)渗淬件不允许外观有任何磕碰、锈蚀、尤其是齿面不得磕碰、缺肉;5.2硬化层深度检验5.2.1 金相法测量硬化层深度金相检验层深法是指从边界观察其金相直至金相过渡区为界限,使用此种方法检验可以借助金相显微镜,钢件可以借助4%硝酸酒精腐蚀法;1)显微镜放大倍数为100倍(用带刻度10倍的目镜与10倍的物镜),每小格的尺度为0.013mm;2)低碳钢淬火试样要进行正火,磨抛后用4%硝酸酒精浸蚀。
渗碳件检测

化学处理件检测一、适用范围本规定适用于本司目前生产的可控气氛渗碳件与碳氮共渗件的检测。
二、检测规范1.制样①按《产品检测通则》规定抽取样板,检测渗层深度的样板应在淬火后抽样,检测其它指标的样板可在回火后抽样。
②按图纸标注的检测位置切割检测截面,切取下来的样板尺寸,长、宽或直径应小于20mm,高度也应小于20mm。
③切割时装夹要稳定,光轴可直接压平在钳口底面夹紧,台阶轴在被切割一端应垫平压实夹紧,不得悬空,如不便于装夹的产品可外送线切割加工。
④切割时,在未打开电源开关前,应将切割片放下至零件上,调节冷却水管直接喷在切口位置,然后提起切割机手柄,打开电源开关,缓缓落下切割机手柄,轻轻加力,勿使进刀量过大,在零件将被切断时,应轻提手柄,避免样品毛刺过大。
切下后,先关闭电源开关,再关闭冷却水,松开夹紧螺丝,用镊子将样品取出。
⑤样板切下后应检查被切表面,如发现变色或切口偏斜,均视为不合格样品,应重新切样。
⑥将切下的待检样板,去除毛刺,将被检测面向下放在镶嵌机上,加注电木粉,加热到140℃,保温2-3分钟取出后即为试样毛坯,镶嵌机的使用按《镶嵌机使用说明》操作。
⑦对于尺寸较大,便于直接磨削的样板也可以不镶嵌。
2.磨样①检测表面硬度时,在预磨机上用600#砂纸加水磨制,达到表面光亮,可微见磨痕,但原机加工痕迹应通过磨削去除。
②检测渗碳层或金相组织时,先在预磨机上用600~800#砂纸加水磨制,磨削时,应及时观察表面的变化,当磨痕趋于同一方向时,将试样旋转90。
再磨,反复2-3次,直到被磨表面光亮、平整,可微见磨痕为止,然后将试样放在1500~2000#砂纸上加水磨制,方法同600#砂纸磨削相同,直至被磨表面基本达到镜面为止,再将达到镜面的试样拿到抛光机上抛光至完全看不到磨痕的光亮镜面为止。
3.腐蚀①对于仅检测硬度的试样,不需要腐蚀,可直接检查。
②对于检测渗层或金相组织的试样,按下面步骤进行腐蚀。
A.用棉签和肥皂将表面洗干净。
渗碳零件的质量检验及缺陷预防

渗碳零件的质量检验及缺陷预防渗碳化学热处理工艺是通过改变零件表面化学成分及显微组织,使得零件表面具有高硬度、高耐磨性、高接触疲劳强度,心部应具有良好的综合力学性能。
文章结合渗碳零件宏观质量检验及微观质量检验的基本内容,论述了渗碳零件的热处理缺陷产生的原因及不同缺陷的解决措施。
标签:渗碳零件;质量检验;解决措施1 概述在现代工业中,齿轮、凸轮及其他磨损件承受了一定的摩擦力、交变弯曲应力、接触疲劳应力、一定的冲击力。
失效形式有过量磨损,表面剥落、断裂等。
所以要求表面具有高硬度、高的接触疲劳抗力和良好的耐磨性,而心部有一定的塑韧性[1]。
通过改变这些零件表面化学成分及显微组织的渗碳、渗氮、渗硼等化学热处理工艺,使得零件表面具有高硬度、高耐磨性、高接触疲劳,心部应具有良好的综合力学性能[2]。
渗碳钢碳含量为0.12%~0.25%(质量),锰、铬、镍的作用是提高渗碳钢的淬透性,淬火时心部能获得大量的板条马氏体组织。
钛、钒、钨、钼等能细化晶粒。
锰、铬、镍等元素还能改善渗碳层性能。
渗碳层性能有表层含碳量、表层浓度梯度和渗碳层深度。
表层含碳量0.80%~1.05%(质量分数),碳的浓度梯度宜平缓过渡,以免性能变化太大,增大内应力。
铬、锰、钼有利于渗碳层增厚,而钛、钒减小渗碳层厚度。
镍、硅等元素不利于渗碳层增厚,一般渗碳钢中不用硅合金化。
钢中碳化物形成元素含量过高,在渗碳层中产生块状碳化物,造成表面脆性,所以碳化物和非碳化物形成元素含量要适当。
渗碳零件由于表面化学成分及显微组织都发生变化,加之要进行淬火及回火热处理工艺,所以常产生热处理缺陷,降低零件的弯曲强度、疲劳强度及耐磨性能。
因此,加强渗碳零件的质量检验及缺陷预防,对于提高力学性能、延长产品寿命、节约材料、促进可持续发展具有实际意义[3]。
2 渗碳零件的质量检验内容2.1 渗碳零件的外观及硬度检验渗碳零件的外观检验属于宏观检验方法,主要有渗碳零件表面的无氧化检验、锈蚀检验、剥落检验、机械碰伤检验、表面裂纹检验等。
热处理检验方法国家标准
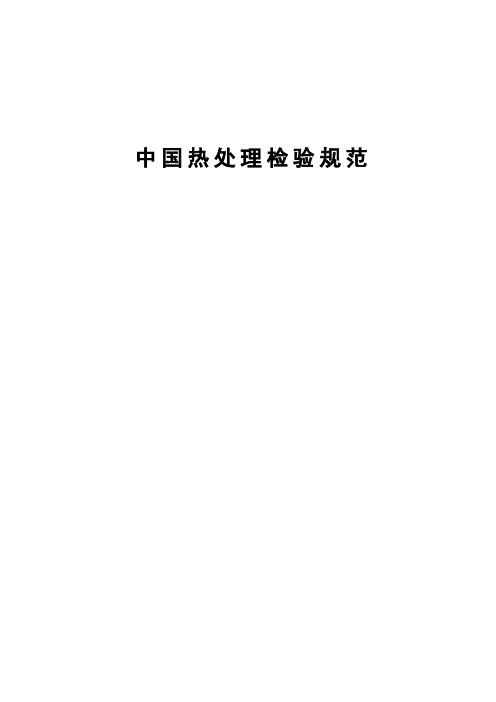
中国热处理检验规范热处理检验方法和规范金属零件的内在质量主要取决于材料和热处理。
因热处理为特种工艺所赋予产品的质量特性往往又室补直观的内在质量,属于“内科”范畴,往往需要通过特殊的仪器(如:各种硬度计、金相显微镜、各种力学性能机)进行检测。
在GB/T19000-ISO9000系列标准中,要求对机械产品零部件在整个热处理过程中一切影响因素实施全面控制,反映原材料及热处理过程控制,质量检验及热处理作业条件(包括生产与检验设备、技术、管理、操作人员素质及管理水平)等各方面均要求控制,才能确保热处理质量。
为此,为了提高我公司热处理产品质量,遵循热处理相关标准,按零件图纸要求严格执行,特制定本规范一、使用范围:本规范适用于零件加工部所有热处理加工零件。
二、硬度检验:通常是根据金属零件工作时所承受的载荷,计算出金属零件上的应力分布,考虑安全系数,提出对材料的强度要求,以强度要求,以强度与硬度的对应关系,确定零件热处理后应具有大硬度值。
为此,硬度时金属零件热处理最重要的质量检验指标,不少零件还时唯一的技术要求。
1、常用硬度检验方法的标准如下:GB230 金属洛氏硬度试验方法GB231 金属布氏硬度试验方法GB1818 金属表面洛氏硬度试验方法GB4340 金属维氏硬度试验方法GB4342 金属显微维氏硬度试验方法GB5030 金属小负荷维氏试验方法2、待检件选取与检验原则如下:为保证零件热处理后达到其图纸技术(或工艺)要求,待检件选取应有代表性,通常从热处理后的零件中选取,能反映零件的工作部位或零件的工作部位硬度的其他部位,对每一个待检件的正时试验点数一般应不少于3个点。
通常连续式加热炉(如网带炉):应在连续生产的网带淬火入回火炉前、回火后入料框前的网带上抽检3-5件/时。
且及时作检验记录。
同时,若发现硬度超差,应及时作检验记录。
同时,若发现硬度越差,应及时进行工艺参数调整,且将前1小时段的零件进行隔离处理(如返工、检)。
渗碳淬火的风机齿轮金相检验标准探讨

《热处理》 2018年第 33卷 第 4期
·37·
的考虑较少,而渗碳淬火的风机齿环的畸变问题却 是齿环加工制造的一个难题,所以很有必要编制一 个适合风机齿环的渗碳淬火金相检验标准。本文是 在科研项目 “控 制 渗 碳 淬 火 齿 轮 畸 变 研 究 ”的 基 础 上,研究了国内现行的国家和行业的渗碳淬火金相 检验标准后制订的渗碳淬火风机齿环的金相检验标 准草案。 参 考 的 标 准 有:GB/T25744—2010《钢 件 渗碳淬火 回 火 金 相 检 验 》[2];GB/T9450—2005《钢 件渗 碳 淬 火 硬 化 层 深 度 的 测 定 和 校 核》[3];JB/T 6141.3—1992《重载齿轮 渗碳金相检验》[4];JB/T 6141.2—1992《重 载 齿 轮 渗 碳 质 量 检 验 》[5];HB 5492—1991《航空钢制件渗碳、碳氮共渗金相组织检 验》; 渗 碳 硬 齿 轮 金 相检验》标准。
1 预备热处理组织的检验
随着渗碳淬火技术的发展与进步,渗碳淬火件 的预备热处理越来越受到重视,特别是关于控制渗 碳淬火件的畸变,过去仅关注渗碳和淬火等工序,没 有认真研究预备热处理对工件畸变的影响。近年来 的研究发现,预备热处理对渗碳淬火件畸变的影响 也很大,目前国内现行的渗碳淬火金相检验标准中, 都没有涉及预备处理组织的金相组验,即没有规定
YUBaifang,ZHANGZhonghe,JIANGShenzhu,WANGFeiyu, ZHANGErkang,SHAOShuai
(ShenyangBlowerWorksGroupCorporation,Shenyang110869,LiaoningChina) Abstract:Atthepresenttime,thereisnoyetmetallographicexaminationstandardforcarburized,hardenedand temperedpartintheblowertrade.Inview ofthisfact,thecorrespondingactualstateandtradestandardsfor carburized,hardenedandtemperedpartwerecomparedandanalyzed.Onthebasisoftheforegoingjobandfeature ofthecarburizedandhardenedblowergears,consultingtheachievementinscientificresearchoncontrolof distortionofcarburizedandhardenedblowergearsinwriter’scompanyandtheprogressincarburizingand hardeningtechnologiesathomeandabroad,ametallographicexaminationstandard(draft) adaptabletothe carburizedandhardenedbowergear,whichinvolvedsuchexaminationitemsaspriorheattreatingstructure,core structure,hardenedcasedepth,martensitegrade,retainedaustenitegrade,carbidegrade,andinternaloxidation grade,hasbeendrawnup. Keywords:blowergear;metallographicexamination;carburizing;hardening;standard
齿轮加工中渗碳淬火和渗碳质量分析
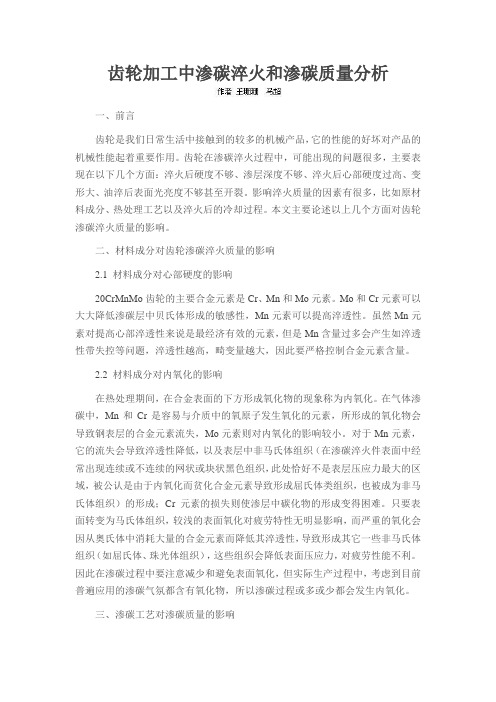
齿轮加工中渗碳淬火和渗碳质量分析一、前言齿轮是我们日常生活中接触到的较多的机械产品,它的性能的好坏对产品的机械性能起着重要作用。
齿轮在渗碳淬火过程中,可能出现的问题很多,主要表现在以下几个方面:淬火后硬度不够、渗层深度不够、淬火后心部硬度过高、变形大、油淬后表面光亮度不够甚至开裂。
影响淬火质量的因素有很多,比如原材料成分、热处理工艺以及淬火后的冷却过程。
本文主要论述以上几个方面对齿轮渗碳淬火质量的影响。
二、材料成分对齿轮渗碳淬火质量的影响2.1 材料成分对心部硬度的影响20CrMnMo齿轮的主要合金元素是Cr、Mn和Mo元素。
Mo和Cr元素可以大大降低渗碳层中贝氏体形成的敏感性,Mn元素可以提高淬透性。
虽然Mn元素对提高心部淬透性来说是最经济有效的元素,但是Mn含量过多会产生如淬透性带失控等问题,淬透性越高,畸变量越大,因此要严格控制合金元素含量。
2.2 材料成分对内氧化的影响在热处理期间,在合金表面的下方形成氧化物的现象称为内氧化。
在气体渗碳中,Mn和Cr是容易与介质中的氧原子发生氧化的元素,所形成的氧化物会导致钢表层的合金元素流失,Mo元素则对内氧化的影响较小。
对于Mn元素,它的流失会导致淬透性降低,以及表层中非马氏体组织(在渗碳淬火件表面中经常出现连续或不连续的网状或块状黑色组织,此处恰好不是表层压应力最大的区域,被公认是由于内氧化而贫化合金元素导致形成屈氏体类组织,也被成为非马氏体组织)的形成;Cr元素的损失则使渗层中碳化物的形成变得困难。
只要表面转变为马氏体组织,较浅的表面氧化对疲劳特性无明显影响,而严重的氧化会因从奥氏体中消耗大量的合金元素而降低其淬透性,导致形成其它一些非马氏体组织(如屈氏体、珠光体组织),这些组织会降低表面压应力,对疲劳性能不利。
因此在渗碳过程中要注意减少和避免表面氧化,但实际生产过程中,考虑到目前普遍应用的渗碳气氛都含有氧化物,所以渗碳过程或多或少都会发生内氧化。
渗碳验收规范标准最新

渗碳验收规范标准最新1. 引言本规范旨在规定渗碳工艺的验收标准,确保零件在经过渗碳处理后能满足设计和使用要求。
2. 适用范围本规范适用于所有需要进行渗碳处理的金属零件,包括但不限于齿轮、轴承、曲轴等。
3. 术语和定义- 渗碳:将碳元素渗入金属表面,形成硬化层的过程。
- 硬化层深度:渗碳后,表面到未渗碳区域的过渡层深度。
- 碳化物:渗碳过程中形成的碳化物颗粒。
4. 材料要求- 被处理材料应具有良好的渗碳性能,通常为低碳钢或合金钢。
- 材料应符合相关国家或行业标准。
5. 工艺流程- 清洁:零件表面应清洁无油污、锈蚀等。
- 加热:将零件加热至适当温度,通常在900°C至950°C之间。
- 渗碳:在含有碳源的气体或液体中进行渗碳。
- 冷却:渗碳后,零件应迅速冷却以固定碳化物结构。
6. 质量要求- 硬化层深度应符合设计要求,通常在0.5mm至2.5mm之间。
- 表面硬度应达到HRC58至HRC62。
- 碳化物分布应均匀,无明显聚集现象。
7. 检验方法- 硬度测试:使用洛氏硬度计进行表面硬度测试。
- 金相分析:通过显微镜观察碳化物的分布和形态。
- 深度测量:使用无损检测方法测量硬化层深度。
8. 验收标准- 所有检验项目均应满足第6条中的质量要求。
- 任何不符合要求的零件应进行返工或报废处理。
9. 记录和报告- 每次渗碳处理过程和检验结果都应详细记录。
- 应定期对记录进行审核,确保符合规范要求。
10. 规范的修订和更新本规范应根据技术进步和行业需求定期进行修订和更新。
请注意,上述内容为示例草案,实际应用时应根据具体工艺和产品要求进行调整。
渗碳淬火报告样本-20160830-001

青岛热处理检测报告No. 20160830-001 送检单位送检日期施工卡号/ 零件图号零件名称零件数量材料牌号炉批号试样名称试块试样编号检测依据检测设备载荷检测项目通用技术规范:渗碳淬火要求:表面硬度HRC58-62,心部硬度HRC40-45;层深0.80-1.00毫米;金相组织渗淬主要参数温度/压力/占空比/电压/氨气/保温/渗碳淬火检验结果金相组织硬度以及层深外观K M A’表面硬度心部硬度硬化深度齿轮表面外观1级-5级1级-5级1级-5级HRC58-62 HRC36-45 0.80-1.00 /1级3级3级61/60 41/42 0.8636 良实测硬度曲线图X=863.6 Y=0 HV0.3=550平均:X=863.6序号X Y D1 D2 HV0.3(L1,P1) 100 0 28.25 28.48 691.32(L1,P2) 200 0 28.76 28.98 667.22(L1,P3) 300 0 29.3 29.5 643.679(L1,P4) 400 0 28.3 29.23 672.159(L1,P5) 500 0 29.6 29.76 631.59(L1,P6) 600 0 29.33 30.28 625.95(L1,P7) 700 0 30.07 30.55 605.57(L1,P8) 800 0 31.08 31.53 567.299(L1,P9) 900 0 31.87 32.31 540.11(L1,P10) 1000 0 32.64 33.6 507.129检测结果层深0.8636毫米,表面硬度61/60HRC;备注数据仅对试块负责;。
- 1、下载文档前请自行甄别文档内容的完整性,平台不提供额外的编辑、内容补充、找答案等附加服务。
- 2、"仅部分预览"的文档,不可在线预览部分如存在完整性等问题,可反馈申请退款(可完整预览的文档不适用该条件!)。
- 3、如文档侵犯您的权益,请联系客服反馈,我们会尽快为您处理(人工客服工作时间:9:00-18:30)。
精密机械有限公司
企业标准 YQB/4003-2016
渗碳淬火质量验收规范
发布时间:2016年 3 月 22 日实施时间:2016年 3 月 22 日
精密机械有限公司发布
1、目的
规范自制及委外产品渗淬质量测试的方法和依据,使得渗淬有所依循、保证检测的准确性、稳定性,从而使产品质量得到有效控制,确保本公司向客户提供满意的产品;
2、适用范围
适用于各类自制或委外产品的渗淬质量检控;
3、引用标准
(1) GB/T13299-91 金属显微组织评定方法依据;
(2) JB/T 9211-1999 中碳钢与中碳合金结构钢马氏体等级标
准;
(3) GBT 25744-2010 钢件渗淬回火金相检验标准;
(4)GB/T 9450-2005 钢件渗淬硬化层深度的测定和校核依据;
(5)GB/T11354-2005 金相组织检验依据;
4、名词解释
(1) 渗淬:渗碳淬火;
(2)0收1退:同批次件抽检1件,如合格则整批次接受,不合格整批次退货;
(3)试块:渗淬的随炉圆柱形试块,直径25mm*长度50mm,粗糙度;
(4)心部硬度:在齿宽中部横截面上,轮齿中心线与齿根圆相交处的硬度;
5、验收项目及标准
渗淬零部件表面硬度、心部硬度、硬化层深、金相组织、表面质量、脱碳层深等;
渗淬件表面质量的检验
1)为得到较为准确的检测结果,零件的检测部位均应进行表面打磨、去掉氧化皮等杂质(成品件或不允许表面打磨的零件检测时,先不进行表面打磨直接在零件不影响外观表面检测。
若检测结果不合格时,则须进行破坏性打磨检测,若打磨后检测合格,则判定合格);
2)每一零件原则上应至少检测三次,取其平均值作为评价结果。
(第一针为测试针,零件较小或无法取多点除外);
3)当热处理零件表面产生脱碳现象时,须将零件表面磨深~2mm后再进行检测;
4)渗淬件不允许外观有任何磕碰、锈蚀、尤其是齿面不得磕碰、缺肉;硬化层深度检验
金相法测量硬化层深度
金相检验层深法是指从边界观察其金相直至金相过渡区为界限,使用此种方法检验可以借助金相显微镜,钢件可以借助4%硝酸酒精腐蚀法;
1)显微镜放大倍数为100倍(用带刻度10倍的目镜与10倍的物镜),每小格的尺度为;
2)低碳钢淬火试样要进行正火,磨抛后用4%硝酸酒精浸蚀。
渗层总层深=过共析+共析+亚共析的1/2处;
3)低碳合金钢淬火试样要进行等温退火(或渗碳后缓冷试样),磨抛后用4%硝酸酒精浸蚀;
4)渗层总层深=过共析+共析+亚共析(即测至心部组织不变处);
硬度法测量硬化层深度
1) 硬度法检测是使用维氏硬度计从边界向中心逐点检测,直至取值界限;2)取值的极限硬度一般按照图纸要求,如图纸无要求,渗淬工件取值550HV1作为极限硬度;
3)双方发生争议时,一律依据硬度法检测(推荐供应商使用硬度法作为判定标准),如图纸指定标准公斤力,则依据图纸规定的公斤力;如图纸未规定标准的公斤力,图纸规定层深在毫米以内则推荐使用300g力,图纸规定层深大于毫米则推荐使用1000g力;
渗碳后的硬度检验
1)渗淬零部件表面硬度依据洛氏硬度计检测;第一针为验证,每一零件原则上应至少检测三次,取其平均值作为评价结果(零件较小或无法取多点除外;若发生争议,则依据洛氏硬度计为准);
2)薄壁件(厚度在10mm以下)选用维氏硬度计检测,不可用洛氏硬度计检测;
3)洛氏硬度计硬度检测有效硬化深度超过0.4mm的各种表面硬化工件;当硬化层厚度在~0.8mm时,可采用HRA标尺;当硬化层厚度超过0.8mm时,可采用HRC标尺;渗淬零部件表面硬度一般要求HRC58±2,心部硬度
HRC35-45;检验位置依据图1示;
图1 渗碳后的金相组织检验
1)渗碳层碳化物评级标准共分8级。
常啮合齿轮1-6级合格,7级返修,8
级废品;非常啮合齿轮1-5级合格,6-7级返修,8级废品;
2)残余奥氏体和马氏体评级标准依据残余奥氏体量的多少和马氏体针的大
小,对照标准图片进行评定;该标准共分8级,马氏体针1-5级合格、残
余奥氏体小于等于30%,马氏体针6-8级返修、残余奥氏体大于等于30%以
上;
3)心部铁素体评级标准依据铁素体的形态、数量及其大小,对照标准图片
进行评定,该标准共分6级,1-4级合格,5-6级返修;
4)太阳系列齿轮碳化物全部要求小于等于4级,马氏体针小于等于4级,残余奥氏体小于等于20%,心部铁素体要求小于等于3级;检验位置依据图
2示;图2
6.渗淬件图片参考
———本规范由1111品质部提出。
编制:审核:批准:。