石灰石石灰法湿法烟气脱硫技术 ppt课件
合集下载
石灰石石灰法湿法烟气脱硫
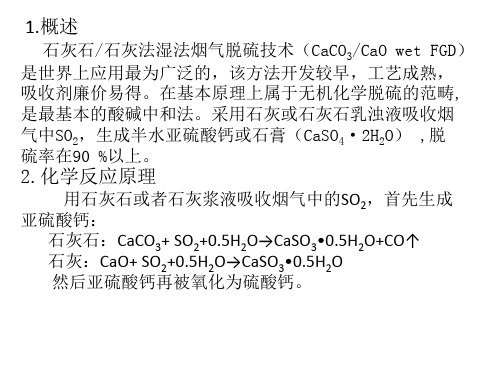
石灰石系统中最关键的反应是Ca2+的形成,因为 SO2,正是通过Ca2+与HSO3-反应而得以从溶液中出 去的。这一关键步骤也突出了石灰石系统和石灰 系统的一个极为重要的区别:石灰石系统中Ca2+ 的产生与H+浓度和CaCO3 的存在有关;而在石灰 系统中, Ca2+的产生仅与氧化钙的存在有关。因 此,为了保证液相有足够的Ca2+浓度,石灰石系 统在运行时,其pH较石灰系统的低,石灰石系统 的最佳操作pH为5.8~6.2,石灰系统约为8。
工艺流程图1
吸收塔
吸收塔多采用逆流方式布置, 烟气从喷淋区下部进人吸 收塔, 与均匀喷出的吸收浆液逆流接触。烟气流速为 3m/s左右, 液气比与煤含硫量和脱硫率关系较大, 一般在 8~25 /m3之间。空塔优点是塔内部件少, 结垢可能性小, 运行可靠性高。逆流运行有利于烟气与吸收液充分接触, 但阻力损失比顺流大。
1.概述
石灰石/石灰法湿法烟气脱硫技术(CaCO3/CaO wet FGD) 是世界上应用最为广泛的,该方法开发较早,工艺成熟, 吸收剂廉价易得。在基本原理上属于无机化学脱硫的范畴, 是最基本的酸碱中和法。采用石灰或石灰石乳浊液吸收烟 气中SO2,生成半水亚硫酸钙或石膏(CaSO4·2H2O) ,脱 硫率在90 %以上。
2.化学反应原理
用石灰石或者石灰浆液吸收烟气中的SO2,首先生成 亚硫酸钙:
石灰石:CaCO3+ SO2+0.5H2O→CaSO3•0.5H2O+CO↑ 石灰:CaO+ SO2+0.5H2O→CaSO3•0.5H2O 然后亚硫酸钙再被氧化为硫酸钙。
石灰石/石灰法湿法烟气脱硫的反应机理
石灰石系统和石灰系统的主要区别
工艺流程图1
吸收塔
吸收塔多采用逆流方式布置, 烟气从喷淋区下部进人吸 收塔, 与均匀喷出的吸收浆液逆流接触。烟气流速为 3m/s左右, 液气比与煤含硫量和脱硫率关系较大, 一般在 8~25 /m3之间。空塔优点是塔内部件少, 结垢可能性小, 运行可靠性高。逆流运行有利于烟气与吸收液充分接触, 但阻力损失比顺流大。
1.概述
石灰石/石灰法湿法烟气脱硫技术(CaCO3/CaO wet FGD) 是世界上应用最为广泛的,该方法开发较早,工艺成熟, 吸收剂廉价易得。在基本原理上属于无机化学脱硫的范畴, 是最基本的酸碱中和法。采用石灰或石灰石乳浊液吸收烟 气中SO2,生成半水亚硫酸钙或石膏(CaSO4·2H2O) ,脱 硫率在90 %以上。
2.化学反应原理
用石灰石或者石灰浆液吸收烟气中的SO2,首先生成 亚硫酸钙:
石灰石:CaCO3+ SO2+0.5H2O→CaSO3•0.5H2O+CO↑ 石灰:CaO+ SO2+0.5H2O→CaSO3•0.5H2O 然后亚硫酸钙再被氧化为硫酸钙。
石灰石/石灰法湿法烟气脱硫的反应机理
石灰石系统和石灰系统的主要区别
122石灰石石膏湿法烟气脱硫技术工艺原理及特点PPT35页
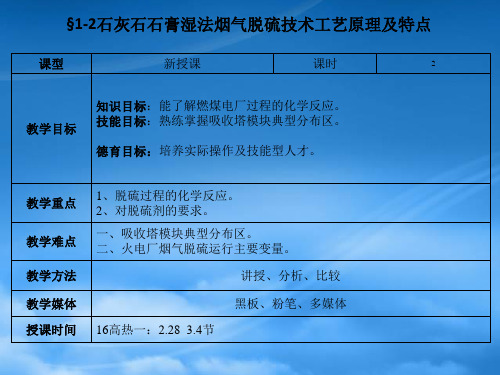
布置作业
无
作业情况
典型的工程全景
该工艺采用石灰石作为脱硫吸收剂,石灰石经破碎磨细成粉状与水混合搅拌制成吸收浆液。在吸收塔内,吸收浆液与烟气接触混合,烟气中的二氧化硫与浆液中的碳酸钙以及鼓入的氧化空气进行化学反应吸收脱除二氧化硫,最终产物为石膏。脱硫后的洁净烟气通过除雾器除去雾滴经烟囱排放,脱硫渣石膏可以综合利用。
黑板、粉笔、多媒体
授课时间
16高热一:2.28 3.4节
§1-2石灰石石膏湿法烟气脱硫技术工艺原理及特点
教材分析
本课题主要是通过分析燃煤电厂过程的化学反应、吸收塔模块典型分布区,为电厂的安全运行提供基本的数据。
教后记
熟练讲解实际电厂中脱硫装置吸收塔模块典型分布区。
二、石灰石湿法烟气脱硫工艺过程的描述
三、脱除SO2的化学反应机理
1、过程阶段: (1)气态反应物从气相内部迁移到气-液界面。 (2)气态反应物穿过气-液界面进入液相,并发生化学反应。 (3)反应组分从液相界面迁移到液相内部。 (4)进入也想的反应组分与液相组分发生反应。 (5)已溶解的反应物的迁移和由反应引起的浓度梯度产生的反应物的迁移。
14、脱硫塔的类型及结构 为了保证较高的脱硫效率,同时防止结垢和堵塞,要求脱硫塔具有持液量大,气液间相对速度高,较大的气液接触面积,吸收区长,气液接触时间长,内部构件少,压降小等特点。
15、脱硫装置的可利用率
指脱硫装置每年正常运行时间与发电机组每年总运行时间的百分比。 A – B-C 可用率 = x100% A A:发电机组每年的总运行时间,h B:脱硫装置每年因脱硫系统故障导致的停运时间,h C:脱硫装置强迫降低出力等效停运时间
成份
符号
作 用
氧化钙
CaO
无
作业情况
典型的工程全景
该工艺采用石灰石作为脱硫吸收剂,石灰石经破碎磨细成粉状与水混合搅拌制成吸收浆液。在吸收塔内,吸收浆液与烟气接触混合,烟气中的二氧化硫与浆液中的碳酸钙以及鼓入的氧化空气进行化学反应吸收脱除二氧化硫,最终产物为石膏。脱硫后的洁净烟气通过除雾器除去雾滴经烟囱排放,脱硫渣石膏可以综合利用。
黑板、粉笔、多媒体
授课时间
16高热一:2.28 3.4节
§1-2石灰石石膏湿法烟气脱硫技术工艺原理及特点
教材分析
本课题主要是通过分析燃煤电厂过程的化学反应、吸收塔模块典型分布区,为电厂的安全运行提供基本的数据。
教后记
熟练讲解实际电厂中脱硫装置吸收塔模块典型分布区。
二、石灰石湿法烟气脱硫工艺过程的描述
三、脱除SO2的化学反应机理
1、过程阶段: (1)气态反应物从气相内部迁移到气-液界面。 (2)气态反应物穿过气-液界面进入液相,并发生化学反应。 (3)反应组分从液相界面迁移到液相内部。 (4)进入也想的反应组分与液相组分发生反应。 (5)已溶解的反应物的迁移和由反应引起的浓度梯度产生的反应物的迁移。
14、脱硫塔的类型及结构 为了保证较高的脱硫效率,同时防止结垢和堵塞,要求脱硫塔具有持液量大,气液间相对速度高,较大的气液接触面积,吸收区长,气液接触时间长,内部构件少,压降小等特点。
15、脱硫装置的可利用率
指脱硫装置每年正常运行时间与发电机组每年总运行时间的百分比。 A – B-C 可用率 = x100% A A:发电机组每年的总运行时间,h B:脱硫装置每年因脱硫系统故障导致的停运时间,h C:脱硫装置强迫降低出力等效停运时间
成份
符号
作 用
氧化钙
CaO
石灰石石膏湿法脱硫化学分析PPT课件

第3页/共59页
方法涉及主要测试项目
测试对象
测试项目
烟气(4项)
氟化氢、氯化氢、三氧化硫、雾滴含量
石灰石(8项)
石灰石块粒度、石灰石粉细度、可磨性指数、活性、 氧化钙、氧化镁、盐酸不溶物、二氧化硅
石灰石浆液(3项) 密度、固含量、细度
附着水、结晶水、酸不溶物、硫酸盐(以二水硫酸
石膏(7项)
钙计)、亚硫酸盐(以半水亚硫酸钙计、碳酸盐
脱硫石膏 带 下 料 口 或 脱 硫 口玻璃或塑料瓶。 尽快测定 装,密封保存。GB5484-
渣储放处
P,G/500ml
2012密闭,防蒸发
第18页/共59页
样品采集和保存
• 5、石膏浆液 ➢ 采样地点位置可根据实际实验需要确定。 ➢ 用于测石膏浆液密度的样品,应单独用采样瓶采满后立即盖紧瓶塞。 ➢ 用于测水溶液离子的样品采后应尽快过滤,装瓶密封,尽快测试。
(以碳酸钙计)、水溶性氯离子(以氯离子计)
石膏浆液(7项)
pH值、密度、水溶性氯离子、水溶性硫酸盐、水溶 性钙、镁离子、总亚硫酸盐、固含量
石膏浆液滤液(3项)pH值、水溶性氯离子(以氯离子计)、固体悬浮物
脱硫废水(2项) pH值、固体悬浮物
第4页/共59页
二、各测试项目使用的标准
第5页/共59页
烟气试验方法
➢ 如样品需要备查,请将所采样品等分为两份,一份送往实验室测试,另一份按要求保存备查。 ➢ 送往实验室的样品一般会根据保存要求留样备查。
第14页/共59页
样品采集和保存
• 1、烟气
样品名称 氟化氢吸收液
采样位置 脱硫烟道断面
氯化氢吸收液 脱硫烟道断面
三氧化硫冷凝液 脱硫烟道断面
采样方法 容器/大小 保存时间
方法涉及主要测试项目
测试对象
测试项目
烟气(4项)
氟化氢、氯化氢、三氧化硫、雾滴含量
石灰石(8项)
石灰石块粒度、石灰石粉细度、可磨性指数、活性、 氧化钙、氧化镁、盐酸不溶物、二氧化硅
石灰石浆液(3项) 密度、固含量、细度
附着水、结晶水、酸不溶物、硫酸盐(以二水硫酸
石膏(7项)
钙计)、亚硫酸盐(以半水亚硫酸钙计、碳酸盐
脱硫石膏 带 下 料 口 或 脱 硫 口玻璃或塑料瓶。 尽快测定 装,密封保存。GB5484-
渣储放处
P,G/500ml
2012密闭,防蒸发
第18页/共59页
样品采集和保存
• 5、石膏浆液 ➢ 采样地点位置可根据实际实验需要确定。 ➢ 用于测石膏浆液密度的样品,应单独用采样瓶采满后立即盖紧瓶塞。 ➢ 用于测水溶液离子的样品采后应尽快过滤,装瓶密封,尽快测试。
(以碳酸钙计)、水溶性氯离子(以氯离子计)
石膏浆液(7项)
pH值、密度、水溶性氯离子、水溶性硫酸盐、水溶 性钙、镁离子、总亚硫酸盐、固含量
石膏浆液滤液(3项)pH值、水溶性氯离子(以氯离子计)、固体悬浮物
脱硫废水(2项) pH值、固体悬浮物
第4页/共59页
二、各测试项目使用的标准
第5页/共59页
烟气试验方法
➢ 如样品需要备查,请将所采样品等分为两份,一份送往实验室测试,另一份按要求保存备查。 ➢ 送往实验室的样品一般会根据保存要求留样备查。
第14页/共59页
样品采集和保存
• 1、烟气
样品名称 氟化氢吸收液
采样位置 脱硫烟道断面
氯化氢吸收液 脱硫烟道断面
三氧化硫冷凝液 脱硫烟道断面
采样方法 容器/大小 保存时间
石灰石、石灰法湿法烟气脱硫

在欧洲,特别是德国,1985年在原来最大容量的锅炉上安 装了FGD之后,欧洲就成了脱硫装置的最大市场。 到1990年,世界上运行中的FGD,以容量计,一半以上在 美国(72000MW以上),其次,具有大容量设备的国家是德 国,第三位是日本。其它如:澳大利亚、荷兰、丹麦、英国、
意大利及亚洲的泰国、印度、韩国等国也相继建成了脱硫
2.化学反应原理
用石灰石或者石灰浆液吸收烟气中的SO2,首先生成 亚硫酸钙:
石灰石:CaCO3+ SO2+0.5H2O→CaSO3•0.5H2O+CO↑ 石灰:CaO+ SO2+0.5H2O→CaSO3•0.5H2O 然后亚硫酸钙再被氧化为硫酸钙。
石灰石/石灰法湿法烟气脱硫的反应机理
石灰石系统和石灰系统的主要区别
④吸收剂浓度:在吸收塔浆液供给量一定的情况下,由于吸 收浓剂度(的提Ca高CO,3)会的引溶起解吸度收较剂低的,过其饱供和给凝量聚的,增最加终将使导反致应浆的液表 面积减少,影响脱硫效率。实践也证明了这点。一般认为吸 收塔的浆液浓度选择在20%~30% 为宜。 ⑤ 浆液pH值:浆液池pH值是石灰石-石膏法脱硫的重要运行 参C于S的Oa数石关S2的O,灰键3吸·0浆 石 因.收5H液的素。2O池溶之因的解一p此H溶和。值,解一C不选a度般S仅择O,认3影合·0而为响.适5且H吸石的2影O收灰p的响H塔石值S氧的、O,化2浆C的是a,液S吸保O而p收2H证·高H。值2系Op低H选统和值p择良H则在值好有5有运.利5利行~于 6.0 为宜。 的⑦要吸求收,剂首原先料是:吸脱收硫剂系的统纯对度吸,收高剂纯(度C的aS吸O3收)剂原将料有有利一于定产 生优质脱硫石膏;其次是吸收剂的粒度,粒度越小,单位体 积的表面积越大,利用率相对较高,有利于脱硫。通常要求 的吸收剂纯度在90% 以上,粒度在250 目以上。然而过高的 吸收剂纯度和过细的粒度会导致吸收剂制备价格的上升,使 系统运行成本增加。
石灰石石灰法湿法烟气脱硫技术 ppt课件
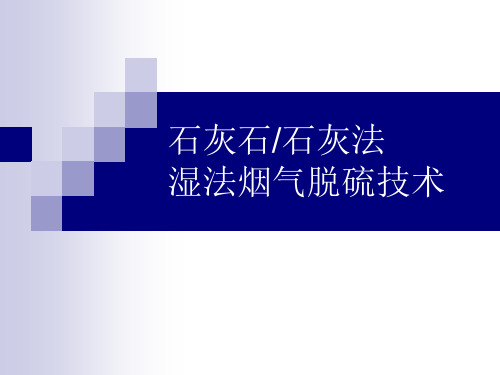
淋量; V —烟气流速(m / s),烟气在吸收塔内的流速; C t—吸收剂浓度(k g / m3 ); α、β、γ—常数,1>α> β> γ> 0; y1、y 2—吸收塔入口、出口处SO2浓度(mg/L); y θ—吸收塔内SO2平衡浓度(m g / L); η—吸收塔脱硫效率(% )。
影响传质单元数的主要因素为:液气比、烟气流速、钙硫比 (吸收剂浓度)、吸收塔的结构等。
吸收区高度为5~15m, 如按塔内流速3m/s计算, 接触反应时间2~5s。区内设 3~6个喷淋层, 每个喷淋层都装有多个雾化喷嘴, 交叉布置, 覆盖率达 200%~300%。喷嘴人口压力不能太高, 在0.5×105~2×105Pa之间。喷嘴出口 流速约10m/s。雾滴直径约1320~2950μm,大水滴在塔内的滞留时间1~10s, 小 水滴在一定条件下呈悬浮状态。喷嘴用碳硅制造, 耐磨性好, 使用寿命10年以上。
① 液气比的影响
液气比决定酸性气体吸收所需要的吸收表面。在其它参数 恒定的情况下,提高液气比相当于增大了吸收塔内的喷淋密度使 液气间的接触面积增大,传质单元数将随之增大,脱硫效率也将 增大。在实际工程中,提高液气比将使浆液循环泵的流量增大, 从而增加设备的投资和能耗。同时,高液气比还会使吸收塔内压 力损失增大,增加风机能耗。
吸收塔试验器脱硫系统的核心装置,要求有持液量大、气液相间的相对速 度高、气液接触面积大、内部构件少、压力降小等特点。目前较常用的吸收塔 主要有喷淋塔、调料塔、配设鼓泡塔、道尔顿型塔4类。其中喷淋塔是湿法脱 硫工艺的主流塔形。一般SO2去除率高的洗涤塔,往往是操度:在吸收塔浆液供给量一定的情况下,由于吸收剂 (的C提a高CO,3会)引的起溶吸解收度剂较的低过,饱其和供凝给聚量,的最增终加使将反导应致的浆表液面浓积度减 少,影响脱硫效率。实践也证明了这点。一般认为吸收塔的浆 液浓度选择在20%~30% 为宜。
影响传质单元数的主要因素为:液气比、烟气流速、钙硫比 (吸收剂浓度)、吸收塔的结构等。
吸收区高度为5~15m, 如按塔内流速3m/s计算, 接触反应时间2~5s。区内设 3~6个喷淋层, 每个喷淋层都装有多个雾化喷嘴, 交叉布置, 覆盖率达 200%~300%。喷嘴人口压力不能太高, 在0.5×105~2×105Pa之间。喷嘴出口 流速约10m/s。雾滴直径约1320~2950μm,大水滴在塔内的滞留时间1~10s, 小 水滴在一定条件下呈悬浮状态。喷嘴用碳硅制造, 耐磨性好, 使用寿命10年以上。
① 液气比的影响
液气比决定酸性气体吸收所需要的吸收表面。在其它参数 恒定的情况下,提高液气比相当于增大了吸收塔内的喷淋密度使 液气间的接触面积增大,传质单元数将随之增大,脱硫效率也将 增大。在实际工程中,提高液气比将使浆液循环泵的流量增大, 从而增加设备的投资和能耗。同时,高液气比还会使吸收塔内压 力损失增大,增加风机能耗。
吸收塔试验器脱硫系统的核心装置,要求有持液量大、气液相间的相对速 度高、气液接触面积大、内部构件少、压力降小等特点。目前较常用的吸收塔 主要有喷淋塔、调料塔、配设鼓泡塔、道尔顿型塔4类。其中喷淋塔是湿法脱 硫工艺的主流塔形。一般SO2去除率高的洗涤塔,往往是操度:在吸收塔浆液供给量一定的情况下,由于吸收剂 (的C提a高CO,3会)引的起溶吸解收度剂较的低过,饱其和供凝给聚量,的最增终加使将反导应致的浆表液面浓积度减 少,影响脱硫效率。实践也证明了这点。一般认为吸收塔的浆 液浓度选择在20%~30% 为宜。
石灰石石膏湿法脱硫工艺流程ppt课件

脱硫石膏物理化学性质与天然石膏具有共同的特征, 但作 为一种工业副产品, 它具有再生石膏的一些特点, 和天然石膏 相比又有一定的差异, 其中二水石膏的含量较天然石膏还要高 许多。
22
该石膏一般作为制造墙板或水泥而出售。由于其稳定 性好,对环境无害,从而也可以用于土地回填。WFGD中, 石膏脱水系统如图所示。石膏脱水系统的主要设备是水力 旋流器和真空皮带过滤机。
折流板除雾器结构与除雾原理
15
旋流板的结构如图所 示,气流在穿过板片间 隙时变成旋转气流,其 中的液滴在惯性作用下 以一定的仰角射出作螺 旋运动而被甩向外侧, 汇集留到溢流槽内,达 到除雾目的,除雾效率 可达到90%~99%。
旋流板除雾器示意图
16
• 吸收塔内的除雾器 • 通常为二级除雾器、安装在塔的顶部。 • 处理后的烟气残余水分不能超过75mg/m3,最好是不超过
自然氧化因锅炉和脱硫系统运行参数不同而氧化程度各异, 当氧化率在15~95%,钙的利用率低于80%范围内亚硫酸钙易 结垢,因为氧化率较高时(>15%),生成的硫酸钙不能与亚 硫酸钙一起沉淀析出;氧化率达不到一定程度(<95%),就 不能产生足够的石膏晶种而使石膏晶体迅速增长,导致石膏在 脱硫塔内结垢。
36
脱硫废水处理
37
脱硫废水处理包括以下4个步骤: A、废水中和 反应池由3个隔槽组成,每个隔槽充满后自流进入下个隔槽。在脱硫废水 进入第1隔槽的同时加入一定量的10%左右的石灰浆液,通过不断搅拌,其 pH值可从5.5左右升至9.0以上。 B、重金属沉淀 Ca(OH) 2的加入不但升高了废水的pH值,而且使Fe3+、Zn2+、Cu2+、Ni2+、 Cr3+等重金属离子生成氢氧化物沉淀。一般情况下3价重金属离子比2价更容 易沉淀,当pH值达到9.0~9.5时,大多数重金属离子均形成了难溶氢氧化物。 同时,石灰浆液中的Ca2+还能与废水中的部分F-反应,生成难溶的CaF2;与 As3+ 络合生成Ca3 (AsO3)2等难溶物质。此时Pb2+ 、Hg2+仍以离子形态留在 废水中,所以在第2隔槽中加入有机硫化物药剂TMT-15,使其Pb2+、Hg2+反 应形成难溶的硫化物沉积下来。 TMT-15是一种三嗪类组分(C3N3S3Na3,三聚硫嗪酸三钠盐),能在常温下 与废水中的各种重金属离子(汞、铅、铜、镉、镍、锰、锌、铬等)迅速反 应,生成不溶于水,且具有良好的化学稳定性的螯合物,从而达到捕捉去除 重金属的目的,也可以除去已经转变成络合物的重金属。TMT-15是15% (wt%)的C3N3S3Na3溶液,即使用量很少,也表现出极高的重金属排除效 率。
22
该石膏一般作为制造墙板或水泥而出售。由于其稳定 性好,对环境无害,从而也可以用于土地回填。WFGD中, 石膏脱水系统如图所示。石膏脱水系统的主要设备是水力 旋流器和真空皮带过滤机。
折流板除雾器结构与除雾原理
15
旋流板的结构如图所 示,气流在穿过板片间 隙时变成旋转气流,其 中的液滴在惯性作用下 以一定的仰角射出作螺 旋运动而被甩向外侧, 汇集留到溢流槽内,达 到除雾目的,除雾效率 可达到90%~99%。
旋流板除雾器示意图
16
• 吸收塔内的除雾器 • 通常为二级除雾器、安装在塔的顶部。 • 处理后的烟气残余水分不能超过75mg/m3,最好是不超过
自然氧化因锅炉和脱硫系统运行参数不同而氧化程度各异, 当氧化率在15~95%,钙的利用率低于80%范围内亚硫酸钙易 结垢,因为氧化率较高时(>15%),生成的硫酸钙不能与亚 硫酸钙一起沉淀析出;氧化率达不到一定程度(<95%),就 不能产生足够的石膏晶种而使石膏晶体迅速增长,导致石膏在 脱硫塔内结垢。
36
脱硫废水处理
37
脱硫废水处理包括以下4个步骤: A、废水中和 反应池由3个隔槽组成,每个隔槽充满后自流进入下个隔槽。在脱硫废水 进入第1隔槽的同时加入一定量的10%左右的石灰浆液,通过不断搅拌,其 pH值可从5.5左右升至9.0以上。 B、重金属沉淀 Ca(OH) 2的加入不但升高了废水的pH值,而且使Fe3+、Zn2+、Cu2+、Ni2+、 Cr3+等重金属离子生成氢氧化物沉淀。一般情况下3价重金属离子比2价更容 易沉淀,当pH值达到9.0~9.5时,大多数重金属离子均形成了难溶氢氧化物。 同时,石灰浆液中的Ca2+还能与废水中的部分F-反应,生成难溶的CaF2;与 As3+ 络合生成Ca3 (AsO3)2等难溶物质。此时Pb2+ 、Hg2+仍以离子形态留在 废水中,所以在第2隔槽中加入有机硫化物药剂TMT-15,使其Pb2+、Hg2+反 应形成难溶的硫化物沉积下来。 TMT-15是一种三嗪类组分(C3N3S3Na3,三聚硫嗪酸三钠盐),能在常温下 与废水中的各种重金属离子(汞、铅、铜、镉、镍、锰、锌、铬等)迅速反 应,生成不溶于水,且具有良好的化学稳定性的螯合物,从而达到捕捉去除 重金属的目的,也可以除去已经转变成络合物的重金属。TMT-15是15% (wt%)的C3N3S3Na3溶液,即使用量很少,也表现出极高的重金属排除效 率。
石灰石湿法烟气脱硫装置的运行参数检测与控制PPT课件
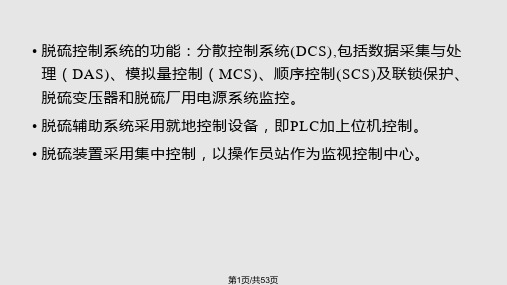
• U型管左右两半边管受到的科里奥利力大 小相等、方向相反,使U型管产生扭转, 扭转角
• B点和C点探测器 分 4别Kfr检第 q1测3m页两/共管53页的振幅和
3.液位检测
• (1)直读式液位仪表: 玻璃管液位计,就地测量
• (2)静压式液位仪表 差压式液位计:差压
变送器p 测得gh的差1压g(h1 h2)
第19页/共53页
5.浆液pH值检测
• 吸收塔浆液pH值是脱硫运行最主要的参数之一 • pH值计布置位置:吸收塔浆液再循环泵出口管道或吸收塔石膏
浆液排出管道 • pH值计:检测溶液中氢离子的浓度
pH lg[H ]
• 测量原理:电极电位与离子浓度的对数呈线性关系,氢离子浓 度变化会引起电极电位的变化。
第40页/共53页
• 该控制系统的设计还必须考虑浆液pH值测量仪表的纯滞后时间的影响。 • pH值计电极所测得的pH值的时间延迟:
l 1
l 2
0v v
1
2
v 、v 分别为出口管道 与 取样中浆液的 流速;
1
2
l 、l 分别出口管道与取样管道的长度。
1
2
第41页/共53页
2.吸收塔浆池液位控制
• 吸收塔水量平衡:水分蒸发和烟气带走的水分、石膏结晶水、废水排放;输入吸收塔的工艺水量。 • 被调量为浆池液位,调节量为输入吸收塔的工艺水量,为闭环断续控制系统。 • 要将烟气量(锅炉负荷)作为水位调节的提前补偿信号,以克服液位调节的较大惯性,加快调节速度。
• 脱硫装置运行参数检测的特点 (1)与化工过程参数检测与控制类似 (2)测量的特殊性:高浓度石灰石、石膏浆液,要考虑被测介质的氧化性、腐蚀性、高黏度、易结晶、易 堵塞等问题。 (3)检测系统组成:被测量、传感器、变送器和显示装置。
• B点和C点探测器 分 4别Kfr检第 q1测3m页两/共管53页的振幅和
3.液位检测
• (1)直读式液位仪表: 玻璃管液位计,就地测量
• (2)静压式液位仪表 差压式液位计:差压
变送器p 测得gh的差1压g(h1 h2)
第19页/共53页
5.浆液pH值检测
• 吸收塔浆液pH值是脱硫运行最主要的参数之一 • pH值计布置位置:吸收塔浆液再循环泵出口管道或吸收塔石膏
浆液排出管道 • pH值计:检测溶液中氢离子的浓度
pH lg[H ]
• 测量原理:电极电位与离子浓度的对数呈线性关系,氢离子浓 度变化会引起电极电位的变化。
第40页/共53页
• 该控制系统的设计还必须考虑浆液pH值测量仪表的纯滞后时间的影响。 • pH值计电极所测得的pH值的时间延迟:
l 1
l 2
0v v
1
2
v 、v 分别为出口管道 与 取样中浆液的 流速;
1
2
l 、l 分别出口管道与取样管道的长度。
1
2
第41页/共53页
2.吸收塔浆池液位控制
• 吸收塔水量平衡:水分蒸发和烟气带走的水分、石膏结晶水、废水排放;输入吸收塔的工艺水量。 • 被调量为浆池液位,调节量为输入吸收塔的工艺水量,为闭环断续控制系统。 • 要将烟气量(锅炉负荷)作为水位调节的提前补偿信号,以克服液位调节的较大惯性,加快调节速度。
• 脱硫装置运行参数检测的特点 (1)与化工过程参数检测与控制类似 (2)测量的特殊性:高浓度石灰石、石膏浆液,要考虑被测介质的氧化性、腐蚀性、高黏度、易结晶、易 堵塞等问题。 (3)检测系统组成:被测量、传感器、变送器和显示装置。
- 1、下载文档前请自行甄别文档内容的完整性,平台不提供额外的编辑、内容补充、找答案等附加服务。
- 2、"仅部分预览"的文档,不可在线预览部分如存在完整性等问题,可反馈申请退款(可完整预览的文档不适用该条件!)。
- 3、如文档侵犯您的权益,请联系客服反馈,我们会尽快为您处理(人工客服工作时间:9:00-18:30)。
吸收区高度为5~15m, 如按塔内流速3m/s计算, 接触反应时间2~5s。区内设 3~6个喷淋层, 每个喷淋层都装有多个雾化喷嘴, 交叉布置, 覆盖率达 200%~300%。喷嘴人口压力不能太高, 在0.5×105~2×105Pa之间。喷嘴出口 流速约10m/s。雾滴直径约1320~2950μm,大水滴在塔内的滞留时间1~10s, 小 水滴在一定条件下呈悬浮状态。喷嘴用碳硅制造, 耐磨性好, 使用寿命10年以上。
石灰石系统中最关键的反应是Ca2+的形成,
因为SO2,正是通过Ca2+与HSO3-反应而得以从溶 液中出去的。
这一关键步骤也重要的区别:石灰石系统中, Ca2+
的产生与H+浓度和CaCO3的存在有关;而在石灰 系统中, Ca2+的产生仅与氧化钙的存在有关。因
此,为了保证液相有足够的Ca2+浓度,石灰石系
③除雾器堵塞:在吸收塔中,雾化喷嘴并不能产生尺 寸完全均一的雾滴,雾滴的大小存在尺寸分布。较小的雾 滴会被气流所夹带,如果不进行除雾,雾滴将进入烟道, 造成烟道腐蚀和堵塞。除雾器必须保持清洁,目前使用的 除雾器有多种形式(如折流板型等),通常用高速喷嘴每 小时数次喷清水进行冲洗。
④脱硫剂的利用率:脱硫产物亚硫酸盐和硫酸盐可沉 积在脱硫剂颗粒表面,从而堵塞了这些颗粒的溶解通道。 这会造成石灰石或石灰脱硫剂来不及溶解和反应就随产物 排除,增加了脱硫剂和脱硫产物的处理费用。因此脱硫液 再循环池中的停留时间一般要达到5~10min。实际的停留 时间设计与石灰石的反应性能有关,反应性能越差,为使 之完全溶解,要求它在池内的停留时间越长。
石灰石/石灰法 湿法烟气脱硫技术
石灰石/石灰法湿法烟气脱硫技术(CaCO3/CaO wet FGD),是目前世界上技术最成熟、实用业绩最多以及运行 状况最稳定的脱硫工艺是世界上最成熟,应用最广泛的烟气 脱硫技术。在基本原理上属于无机化学脱硫的范畴,是最基 本的酸碱中和法。采用石灰或石灰石乳浊液吸收烟气中SO2, 生成半水亚硫酸钙或石膏(CaSO4·2H2O) ,脱硫率在90 % 以上。
吸收塔内的传质过程可用以下双膜模型公式表示: NTU = K×(L/G)α×(K1×Vβ+K2)×(K3×Ctγ+K4) ⑴ NTU = (y1-y2)/(y1-yθ-y2)×ln((y1-yθ)/y2) ⑵ η(%) = (y1-y2)/y1×100 ⑶
其中:N T U —传质单元数;传质单元数越大,吸收塔的脱硫效率越高。 K1, K2, K3, K4—常量; K —喷淋层布置相关系数; (L/G)—液气比(L/m3),与流经吸收塔单位体积烟气量相对应的浆液喷
吸收塔试验器脱硫系统的核心装置,要求有持液量大、气液相间的相对速 度高、气液接触面积大、内部构件少、压力降小等特点。目前较常用的吸收塔 主要有喷淋塔、调料塔、配设鼓泡塔、道尔顿型塔4类。其中喷淋塔是湿法脱 硫工艺的主流塔形。一般SO2去除率高的洗涤塔,往往是操作可靠性最差的。
3.湿法脱硫的影响因素
①设备腐蚀:化石燃料燃烧的排烟中含有多种微量的
化学成分,如氯化物。在酸性环境中,它们对金属(包括 不锈钢)的腐蚀性相当强。目前广泛应用的吸收塔材料是 合金C-276,其价格是常规不锈钢的15倍,为延长设备的 使用寿命,溶液中氯离子的浓度不能太高。为保证氯离子 不发生浓缩,有效地方法是在脱硫系统中根据物料平衡排 出适量的废水,以清水补充。
统在运行时,其pH较石灰系统的低,石灰石系统
的最佳操作pH为5.8~6.2,石灰系统约为8。
2.工艺流程及设备
典型的石灰石/ 石膏湿法FGD 系统工 艺流程主要由石灰石浆液制备和供应、吸 收塔、脱硫产物处置、烟风道、电气和自 动控制6个部分组成。
吸收塔
吸收塔多采用逆流方式布置, 烟气从喷淋区下部进人吸收塔, 与均匀喷出的 吸收浆液逆流接触。烟气流速为3m/s左右, 液气比与煤含硫量和脱硫率关系较 大, 一般在8~25 l/m3之间。空塔优点是塔内部件少, 结垢可能性小, 运行可靠性 高。逆流运行有利于烟气与吸收液充分接触, 但阻力损失比顺流大。
⑤脱硫产物及综合利用:半水亚硫酸钙通常是较细的 片状晶体,这种固体产物难以分离,也不符合填埋要求。 而二水硫酸钙是大的圆形晶体,易于析出和过滤。因此, 从分离的角度看,在循环池中鼓氧或空气将亚硫酸钙盐氧 化为硫酸盐是十分必要的,通常要保证95%的脱硫产物转 化为硫酸钙。
4.主要工艺参数
(1) 传质理论 ① S在O吸2从收气塔相内透,过SO气2膜的向吸气收可液用界双面膜传理递论、描扩述散,;吸收反应经历以下3 个过程: ② SO2在液膜表面溶解; ③ SO2从气液界面透过液膜向液相传递并随即与钙基吸收剂发生化学反应。
淋量; V —烟气流速(m / s),烟气在吸收塔内的流速; C t—吸收剂浓度(k g / m3 ); α、β、γ—常数,1>α> β> γ> 0; y1、y 2—吸收塔入口、出口处SO2浓度(mg/L); y θ—吸收塔内SO2平衡浓度(m g / L); η—吸收塔脱硫效率(% )。
②结垢和堵塞:CaSO3或CaSO4从溶液中结晶析出是 导致脱硫塔发生结垢的主要原因,特别是硫酸钙结构坚硬、 板结,一旦结垢难以去除,影响到所有与脱硫液接触的阀 门、水泵、控制仪器和管道等。硫酸钙结垢的原因是SO42和Ca2+的离子积在局部达到过饱和。为此,在吸收塔中要 保持亚硫酸盐的氧化率在20%以下。亚硫酸盐的氧化需要 在脱硫液循环池中完成,可通过鼓氧或空气等方式进行, 形成的硫酸钙发生沉淀。从循环池返回吸收塔的脱硫液中, 还因为含有足量的硫酸钙晶体,起到了晶种的作用,因此 在后续的吸收过程中,可防止固体直接沉积在吸收塔设备
1.反应原理
用石灰石或者石灰浆液吸收烟气中的SO2,首先生成亚 硫酸钙:
石灰石:CaCO3+ SO2+0.5H2O→CaSO3•0.5H2O+CO↑ 石灰:CaO+ SO2+0.5H2O→CaSO3•0.5H2O
然后亚硫酸钙再被氧化为硫酸钙。
石灰石石灰法湿法烟气脱硫反应机 理比较表格
石灰石系统和石灰系统的主要区别
石灰石系统中最关键的反应是Ca2+的形成,
因为SO2,正是通过Ca2+与HSO3-反应而得以从溶 液中出去的。
这一关键步骤也重要的区别:石灰石系统中, Ca2+
的产生与H+浓度和CaCO3的存在有关;而在石灰 系统中, Ca2+的产生仅与氧化钙的存在有关。因
此,为了保证液相有足够的Ca2+浓度,石灰石系
③除雾器堵塞:在吸收塔中,雾化喷嘴并不能产生尺 寸完全均一的雾滴,雾滴的大小存在尺寸分布。较小的雾 滴会被气流所夹带,如果不进行除雾,雾滴将进入烟道, 造成烟道腐蚀和堵塞。除雾器必须保持清洁,目前使用的 除雾器有多种形式(如折流板型等),通常用高速喷嘴每 小时数次喷清水进行冲洗。
④脱硫剂的利用率:脱硫产物亚硫酸盐和硫酸盐可沉 积在脱硫剂颗粒表面,从而堵塞了这些颗粒的溶解通道。 这会造成石灰石或石灰脱硫剂来不及溶解和反应就随产物 排除,增加了脱硫剂和脱硫产物的处理费用。因此脱硫液 再循环池中的停留时间一般要达到5~10min。实际的停留 时间设计与石灰石的反应性能有关,反应性能越差,为使 之完全溶解,要求它在池内的停留时间越长。
石灰石/石灰法 湿法烟气脱硫技术
石灰石/石灰法湿法烟气脱硫技术(CaCO3/CaO wet FGD),是目前世界上技术最成熟、实用业绩最多以及运行 状况最稳定的脱硫工艺是世界上最成熟,应用最广泛的烟气 脱硫技术。在基本原理上属于无机化学脱硫的范畴,是最基 本的酸碱中和法。采用石灰或石灰石乳浊液吸收烟气中SO2, 生成半水亚硫酸钙或石膏(CaSO4·2H2O) ,脱硫率在90 % 以上。
吸收塔内的传质过程可用以下双膜模型公式表示: NTU = K×(L/G)α×(K1×Vβ+K2)×(K3×Ctγ+K4) ⑴ NTU = (y1-y2)/(y1-yθ-y2)×ln((y1-yθ)/y2) ⑵ η(%) = (y1-y2)/y1×100 ⑶
其中:N T U —传质单元数;传质单元数越大,吸收塔的脱硫效率越高。 K1, K2, K3, K4—常量; K —喷淋层布置相关系数; (L/G)—液气比(L/m3),与流经吸收塔单位体积烟气量相对应的浆液喷
吸收塔试验器脱硫系统的核心装置,要求有持液量大、气液相间的相对速 度高、气液接触面积大、内部构件少、压力降小等特点。目前较常用的吸收塔 主要有喷淋塔、调料塔、配设鼓泡塔、道尔顿型塔4类。其中喷淋塔是湿法脱 硫工艺的主流塔形。一般SO2去除率高的洗涤塔,往往是操作可靠性最差的。
3.湿法脱硫的影响因素
①设备腐蚀:化石燃料燃烧的排烟中含有多种微量的
化学成分,如氯化物。在酸性环境中,它们对金属(包括 不锈钢)的腐蚀性相当强。目前广泛应用的吸收塔材料是 合金C-276,其价格是常规不锈钢的15倍,为延长设备的 使用寿命,溶液中氯离子的浓度不能太高。为保证氯离子 不发生浓缩,有效地方法是在脱硫系统中根据物料平衡排 出适量的废水,以清水补充。
统在运行时,其pH较石灰系统的低,石灰石系统
的最佳操作pH为5.8~6.2,石灰系统约为8。
2.工艺流程及设备
典型的石灰石/ 石膏湿法FGD 系统工 艺流程主要由石灰石浆液制备和供应、吸 收塔、脱硫产物处置、烟风道、电气和自 动控制6个部分组成。
吸收塔
吸收塔多采用逆流方式布置, 烟气从喷淋区下部进人吸收塔, 与均匀喷出的 吸收浆液逆流接触。烟气流速为3m/s左右, 液气比与煤含硫量和脱硫率关系较 大, 一般在8~25 l/m3之间。空塔优点是塔内部件少, 结垢可能性小, 运行可靠性 高。逆流运行有利于烟气与吸收液充分接触, 但阻力损失比顺流大。
⑤脱硫产物及综合利用:半水亚硫酸钙通常是较细的 片状晶体,这种固体产物难以分离,也不符合填埋要求。 而二水硫酸钙是大的圆形晶体,易于析出和过滤。因此, 从分离的角度看,在循环池中鼓氧或空气将亚硫酸钙盐氧 化为硫酸盐是十分必要的,通常要保证95%的脱硫产物转 化为硫酸钙。
4.主要工艺参数
(1) 传质理论 ① S在O吸2从收气塔相内透,过SO气2膜的向吸气收可液用界双面膜传理递论、描扩述散,;吸收反应经历以下3 个过程: ② SO2在液膜表面溶解; ③ SO2从气液界面透过液膜向液相传递并随即与钙基吸收剂发生化学反应。
淋量; V —烟气流速(m / s),烟气在吸收塔内的流速; C t—吸收剂浓度(k g / m3 ); α、β、γ—常数,1>α> β> γ> 0; y1、y 2—吸收塔入口、出口处SO2浓度(mg/L); y θ—吸收塔内SO2平衡浓度(m g / L); η—吸收塔脱硫效率(% )。
②结垢和堵塞:CaSO3或CaSO4从溶液中结晶析出是 导致脱硫塔发生结垢的主要原因,特别是硫酸钙结构坚硬、 板结,一旦结垢难以去除,影响到所有与脱硫液接触的阀 门、水泵、控制仪器和管道等。硫酸钙结垢的原因是SO42和Ca2+的离子积在局部达到过饱和。为此,在吸收塔中要 保持亚硫酸盐的氧化率在20%以下。亚硫酸盐的氧化需要 在脱硫液循环池中完成,可通过鼓氧或空气等方式进行, 形成的硫酸钙发生沉淀。从循环池返回吸收塔的脱硫液中, 还因为含有足量的硫酸钙晶体,起到了晶种的作用,因此 在后续的吸收过程中,可防止固体直接沉积在吸收塔设备
1.反应原理
用石灰石或者石灰浆液吸收烟气中的SO2,首先生成亚 硫酸钙:
石灰石:CaCO3+ SO2+0.5H2O→CaSO3•0.5H2O+CO↑ 石灰:CaO+ SO2+0.5H2O→CaSO3•0.5H2O
然后亚硫酸钙再被氧化为硫酸钙。
石灰石石灰法湿法烟气脱硫反应机 理比较表格
石灰石系统和石灰系统的主要区别