典型圆凸模加工工艺规程
典型凸模零件数控加工工艺研究与设计

典型凸模零件数控加工工艺研究与设计摘要:凸模类零件在生产中广泛存在,基于此,本文探讨了典型凸模零件数控加工工艺与设计。
关键词:凸模;零件;数控加工;设计在凸模零件工艺分析的基础上,设计了该零件的数控加工工艺,编制了抛物线轮廓加工程序。
将编制的凸模零件加工程序输入数控铣床后,进行了程序校验、试加工与优化。
结果表明,该数控工艺方案正确、合理,程序运行平稳,可保证零件加工精度,缩短加工时间,对同类零件的数控加工工艺设计具有借鉴意义。
一、数控加工简介数控加工是指在数控机床上进行零件加工的一种工艺方法,数控机床加工与传统机床加工的工艺规程从总体上一致,但也发生了明显变化。
用数字信息控制零件和刀具位移的机械加工方法。
它是解决零件品种多变、批量小、形状复杂、精度高等问题,以及实现高效化和自动化加工的有效途径。
二、零件工艺性某凸模零件毛坯为长方体,外形尺寸为95mm×95mm×25mm,材料45钢,切削性能较好,单件小批生产,未注表面粗糙度为Ra3.2μm,未注圆角半径为R5。
该零件由平面、带抛物线的凸台外轮廓、倾斜矩形腔、均布三角形槽及孔结构组成,结构较复杂,具有典型性。
考虑到该零件为单件小批生产,加工内容多且精度要求高,因此适合采用数控铣床加工。
该零件工艺为:①凸台抛物线外廓尺寸65±0.02 mm和 mm精度要求高,需分粗、精加工来保证尺寸精度,其中抛物线是编程的难点;②倾斜矩形槽尺寸40±0.02mm和 mm精度要求高,因而需分粗、精加工,编程时可采用刀具补偿功能和坐标旋转指令简化编程;③尺寸φ的沉孔加工精度要求高,普通机加工一般采用定心钻钻孔→钻孔→扩孔→粗镗→精镗孔的加工方案,为减少换刀次数和刀具成本,充分发挥数控机床性能,确定采用以铣代镗的新方法精加工该沉孔,因此最终确定该沉孔加工方案为定心钻钻孔→钻孔→扩孔→半精铣→精铣;④2-φ通孔精度要求高,为保证加工精度,该孔加工需从小到大逐步加工到位,因此确定的加工方案为定心钻钻孔→钻孔→扩孔→铰孔;⑤3个均布的三角形槽由于加工精度要求不高,确定加工方案为粗铣→精铣。
模具典型零件的加工
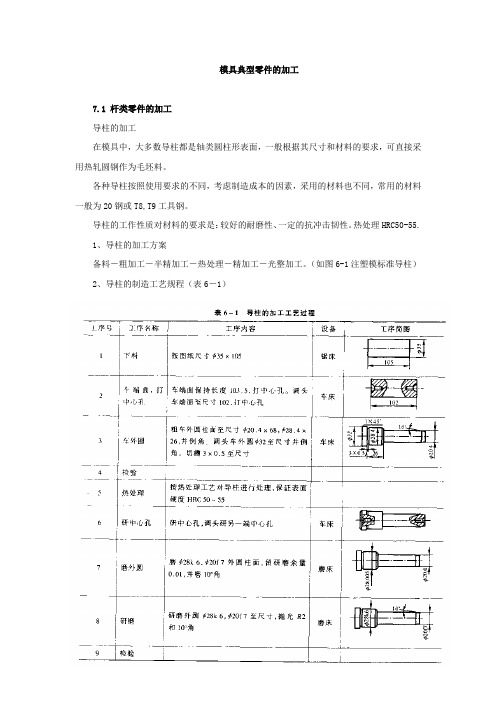
模具典型零件的加工7.1 杆类零件的加工导柱的加工在模具中,大多数导柱都是轴类圆柱形表面,一般根据其尺寸和材料的要求,可直接采用热轧圆钢作为毛坯料。
各种导柱按照使用要求的不同,考虑制造成本的因素,采用的材料也不同,常用的材料一般为20钢或T8,T9工具钢。
导柱的工作性质对材料的要求是:较好的耐磨性、一定的抗冲击韧性。
热处理HRC50-55.1、导柱的加工方案备料-粗加工-半精加工-热处理-精加工-光整加工。
(如图6-1注塑模标准导柱)2、导柱的制造工艺规程(表6-1)导柱的加工工序不是固定不变的,根据不同的生产类型、结构形式和尺寸精度、工厂设备情况,其工序的划分和工艺方法也就不同。
3、导柱加工过程中的定位一般采用设计基准和工艺基准重合的原则,在两端加工中心孔,以两中心孔轴线为各工序的定位基准,中心孔的形状和精度对导柱的加工质量有着直接的关系。
为了确保精加工时的精确定位作用,中心孔在热处理后必须进行对研和修整。
对研中心孔一般采用锥形砂轮或梅花顶尖:4、导柱的研磨一般对于配合精度要求较高的导柱,都要安排研磨工序,以提高表面质量和降低粗糙度。
二、模柄与顶杆的加工模柄的设计已标准化,常用的模柄有:压入式、旋入式、凸缘式、槽形式和浮动式等,和顶杆一样都属于台阶轴类零件,材料选用45钢,热处理HRC40-45,这类零件一般也是采用中心孔作为精加工的定位基准,终加工采用精磨工艺并靠磨端面,保证端面跳动要求。
7.2 套类零件的加工模具中的套类零件主要有:导套、护套和套类凸模等。
导套的材料和导柱一样,一般采用圆钢下料,热处理要求为HRC58-62,制造工艺也不是固定的。
导套的加工方案:备料-粗加工-半精加工-热处理-精加工-光整加工。
7.3 板类零件的加工一、板类零件加工质量的要求模具中各种板类零件较多,如:模座、垫板、固定板、卸料板、推件板等等。
虽然形状、材料、尺寸精度和使用性能要求各不相同,但都是有平面和孔系组成,这类零件的加工质量要求主要有以下几点:①平行度和垂直度要求,一般均按GB1184-80的规定,具体公差执行冷冲模和塑料模的有关国家标准。
圆形凸凹模机械加工

冷冲模的机械加工
坐标镗床的主要附件
坐 标 镗
床
镗孔夹头 1、2、9-1-锥柄 2-螺钉 3-刀 夹 4-带有刻度的螺钉
镗孔夹头的作用是按被 镗孔径的大小精确地调 节镗刀刀尖与主轴轴线 间的距离,镗头以其锥 柄插入主轴的锥孔内, 镗刀装在刀夹内。旋转 带有刻度的螺钉4,可 调整镗刀的径向位置, 以镗削各种不同直径的 孔。调整后用螺钉2将 刀夹锁紧。
坐标镗床的主要附件
万能转台安装在坐标
坐
镗床的工作台上,利用 圆盘的T形槽可将工件
夹紧在圆盘上,旋转手
标
轮可使圆盘和工件绕垂 直轴回转任意角度
(0º~360º),用于加工
在圆周上分布的孔。另
镗
外,旋转手轮可使圆盘
和工件绕水平轴作0º~
360 º的旋转,用于加
床
工和工件轴线成一定角 度的斜孔。
万能转台 1、2、9-手柄 3、5-手轮 4、8-游标盘 6-转台 7-刻度盘 10-偏心套
标 其距离精度一般可达0.02mm。 镗
床
12
冷冲模的机械加工
1) 应用 主要用于淬火后的工件和高硬
坐
度工件的高精度孔和有精确坐标精度的孔和孔系
以及成型表面的磨削。
标
2)坐标磨床 (2.43 单柱坐标磨床)坐标 磨床有立式和卧式两种形式,模具加工中多使用
立式。
磨
3)坐标磨床三个运动:图2.44
4)坐标磨削方法见表2.14 内孔磨削
4
冷冲模的机械加工
2-
φ8+
0. 0
0
1
5
Ra0.8
Ra0.8
φ
4
+0 0
.
0
凸模与型腔的加工
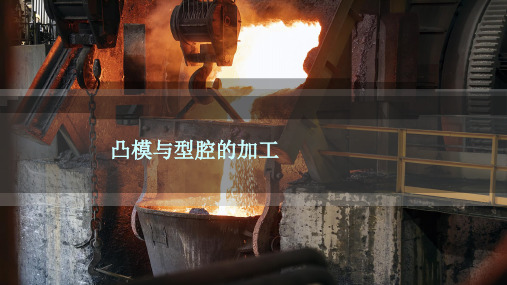
凸模与型腔的加工
凸模零件是用来成形制件内表面的。由于成形制件的形状 各异、尺寸差别较大,所以凸模零件的品种也是多种多样的。按 凸模断面形状的不同大致可以分为圆形凸模和异形凸模两类。
圆形凸模加工比较容易,一般可采用车削、铣削、磨削等进 行粗加工和半精加工,经热处理后在外圆磨床上进行精加工,再 经研磨、抛光后即可达到设计要求。异形凸模在制造上较圆形凸 模要复杂得多。
2020年12月29日星期二
返回目录
1.1 圆形凸模的加工
1.圆形冲裁凸模的加工
1)圆形冲裁凸模的结构 圆形冲裁凸模的结构如图6-20所示。
2020年12月29日星期二
图6-20圆形冲裁凸模的加工工艺路线为下料—车削加工(留磨削余量)— 热处理—磨削—(研磨)。 3)圆形冲裁凸模工作段的锥度问题 圆形冲裁凸模工作段的长度方向,不希望存在锥度。由于制造误 差,因而出现锥度。如图6-21(a)所示,锥度在直径尺寸公差范围内 是允许的;如图6-21(b)所示锥度在任何状态下都是不允许的。
(3)将刀具制成一定的锥度对斜面进行加土,这种方法一般很少使用。
2020年12月29日星期二
图6-24 工件斜置铣削
图6-25 刀具斜置铣削
返回目录
当加工非平面结构的凸模时,如图6-26所示,可根据 凸模形状、结构特点和尺寸大小采用车床、仿形铣床、数 控铣床或通用铣(刨)床等进行加工。
2020年12月29日星期二
图6-26 非平面结构的凸模
返回目录
2020年12月29日星期二
采用仿形铣床或数控铣床加工,可以减轻劳动强度,容易获得 所要求的形状尺寸。数控铣削的加工精度比仿形铣削高。仿形铣削 是靠仿形销和靠模的接触来护制铣刀的运动的,因此,仿形销和靠 模的尺寸形状误差、仿形运动的灵敏度等会直接影响零件的加工精 度。
凸模的加工方法
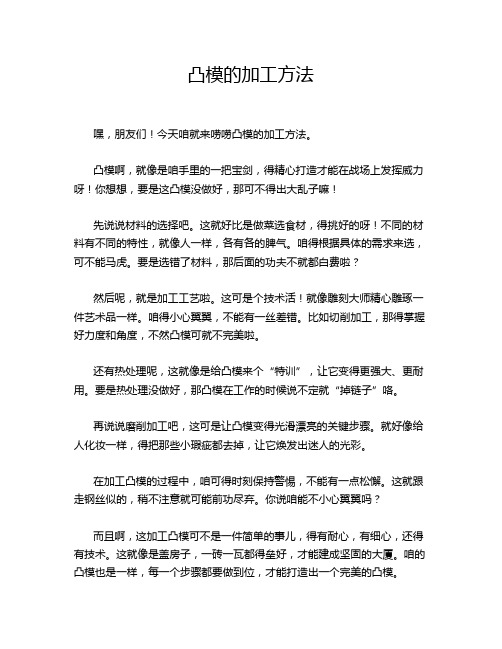
凸模的加工方法嘿,朋友们!今天咱就来唠唠凸模的加工方法。
凸模啊,就像是咱手里的一把宝剑,得精心打造才能在战场上发挥威力呀!你想想,要是这凸模没做好,那可不得出大乱子嘛!先说说材料的选择吧。
这就好比是做菜选食材,得挑好的呀!不同的材料有不同的特性,就像人一样,各有各的脾气。
咱得根据具体的需求来选,可不能马虎。
要是选错了材料,那后面的功夫不就都白费啦?然后呢,就是加工工艺啦。
这可是个技术活!就像雕刻大师精心雕琢一件艺术品一样。
咱得小心翼翼,不能有一丝差错。
比如切削加工,那得掌握好力度和角度,不然凸模可就不完美啦。
还有热处理呢,这就像是给凸模来个“特训”,让它变得更强大、更耐用。
要是热处理没做好,那凸模在工作的时候说不定就“掉链子”咯。
再说说磨削加工吧,这可是让凸模变得光滑漂亮的关键步骤。
就好像给人化妆一样,得把那些小瑕疵都去掉,让它焕发出迷人的光彩。
在加工凸模的过程中,咱可得时刻保持警惕,不能有一点松懈。
这就跟走钢丝似的,稍不注意就可能前功尽弃。
你说咱能不小心翼翼吗?而且啊,这加工凸模可不是一件简单的事儿,得有耐心,有细心,还得有技术。
这就像是盖房子,一砖一瓦都得垒好,才能建成坚固的大厦。
咱的凸模也是一样,每一个步骤都要做到位,才能打造出一个完美的凸模。
咱想想,要是凸模加工不好,那生产出来的东西能合格吗?那肯定不行呀!所以说,凸模的加工可太重要啦!咱可不能小瞧了它。
总之呢,凸模的加工方法可多着呢,每一种都有它的特点和要求。
咱得认真对待,就像对待自己最宝贝的东西一样。
只有这样,才能让凸模发挥出它最大的作用,为我们的生产生活助力呀!你们说是不是这个理儿?。
凸凹模工艺规程

刀量辅具
名称
规格
数量
游标卡尺
200mm
1
锯条
1
编制
校核
审查
共6张
第1张
河南工业职业技术学院
工序卡片
产品代号
零(部)件名称
零(部)件代号
工序号
10
003
凸凹模
06
工序名称
粗铣
材
料
Cr12
设
备
名称
铣床
型号
夹具名称
虎钳
刀量辅具
名称
规格
数量
游标卡尺
200mm
1
外圆刀
900
1
编制
校核
审查
共6张
第2张
河南工业职业技术学院
1
钼丝
1
编制
校核
审查
共6张
第5张
河南工业职业技术学院
工序卡片
产品代号
零(部)件名称
零(部)件代号
工序号
45
003
凸凹模
06
工序名称
钳工精修
材
料
Cr12
设
备
名称
型号
夹具名称
虎钳
刀量辅具
名称
规格
数量
游标卡尺
200mm
1
百分表
1
编制
校核
审查
共6张
第6张
河南工业职业技术学院
工 艺 规 程
零(部)件名称凸凹模
专 业模具设计与制造
班 级模具0902
姓 名
指 导 教 师
2011年9月20日
河南工业职业技术学院
工艺过程卡片
模具制造工艺圆形凸凹模的机械加工

φ1 8. 2 +00 . 0 13
4-M8-7H
A
φ2
6.2+
0. 0
01
6
2 3 .1 + 00. 1
R a 0 .8
131
155
85
技术要求 1. 热处理:淬火硬度60~63HRC。 2. 刃口表面粗糙度Ra0.4μm。
Ra6.3
( √)
图整体结构的多型孔凹模
6
冷冲模的机械加工
坐
坐标镗床主要用以镗削高精度孔 和有精确坐标精度的孔。可进行高精度
单圆形孔凹模
4
冷冲模的机械加工
多孔圆形凹模机械加工工艺过程
镶块结构的凹模 1-固定板 2-凹模镶件
固定板1材料45钢,不进行淬火处理。 凹模镶件材料Cr12,经淬火、回火和磨削后分别压入固定板的相应孔内。 各工序的精基准都是下表面和相邻垂直侧面。 单件小批生产凹模固定板的机械加工工艺路线:下料→铣六面→磨平 上、下平面和相邻垂直侧面→钳工划线→半精加工凹模固定孔、钻、 攻螺孔→坐标镗型孔→钳工→检验。
的铣削加工。
标
坐标镗床的孔加工坐标定位精度可
达0.004~0.01mm,加工面的表面粗糙
镗 度值小于Ra0.8μm。
坐标镗床的分类主要有:单轴坐标镗、
床 双轴坐标镗、数控坐标镗等
7
冷冲模的机械加工
坐标镗床的主要附件
光学中心测定器:光源的
光线通过物镜照明工件的定
坐
位部分,在目镜中可看到工
件上刻线的投影,同时,还
10
冷冲模的机械加工
影响坐标镗床镗孔精度的因素
坐
影响坐标镗床加工精度的因素有:机床的定位精度,
模具典型零件的加工工艺

镗孔工序可以在专用镗床、坐标镗床、 双轴镗床上进行,为了保证上、下模座的 导柱、导套孔距一致,在镗孔时可以将上、 下模座重叠在一起,一次装夹,同时镗出 导柱、导套的安装孔。
2.导柱、导套的加工
(1)导柱、导套的技术要求 1)为了保证良好的导向作用,导柱和 导套的配合间隙应小于凸、凹模之间的间 隙,导柱和导套的配合间隙一般采用H7/h6, 精度要求很高时为H6/h5。导柱与下模座孔, 导套与上模座孔采用H7/r6的过盈配合。
2)导柱和导套的工作部分的圆度公差 应满足: 当直径d≤30mm时,圆度公差不大于 0.003mm;当直径d>30~60mm时,圆度公 差不大于0.005mm;当直径d≥60mm时,圆 度公差不大于0.008mm。
(2)导柱和导套的加工工艺路线 1)导柱的加工工艺路线 对于图4-3(a)所示的导柱,采用如 表4-4所示的加工工艺路线。 导柱的心部要求韧性好,材料一般选用20 号低碳钢。 在导柱加工过程中,外圆柱面的车削 和磨削以两端的中心孔定位,使设计基准 与工艺基准重合。
(3)电火花线切割加工 如图4-21所示的凸模的电火花线切割工 艺过程如下: 1)准备毛坯,将圆形棒料锻造成六面体, 并进行退火处理。 2)在刨床或铣床上加工六面体的六个面。 3)钻穿丝孔。 4)钻孔、攻螺纹,加工出固定凸模用的两 个螺钉孔。
5)将工件进行淬火、回火处理,要求 表面硬度达到HRC 58~HRC 62。 6)磨削上、下两平面,表面粗糙度Ra <0.8μ m 。 7)去除穿丝孔内杂质,并进行退磁处 理。 8)线切割加工凸模。 9)研磨。线切割加工后,钳工研磨凸 模工作部分,使工作表面粗糙度降低。
第4章 模具典型零件的加工工艺
4.1
模架的加工
冲裁凸模和凹模的加工 塑料模型腔的加工
(模具设计)球型凸缘件拉深模设计
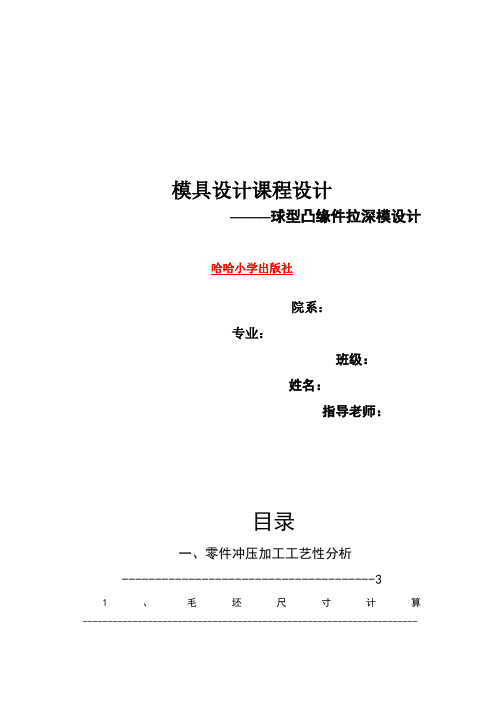
模具设计课程设计————球型凸缘件拉深模设计哈哈小学出版社院系:专业:班级:姓名:指导老师:目录一、零件冲压加工工艺性分析--------------------------------------31、毛坯尺寸计算-------------------------------------------------------------------------32、判断是否可一次拉深成形-------------------------------------------------------- 33、确定是否使用压边圈--------------------------------------------------------------- 44、凹凸模圆角半径的计算------------------------------------------------------------45、确定工序内容及工序顺序---------------------------------------------------------4二、确定排样图和裁板方案------------------------------------------41、板料选择--------------------------------------------------------------------------------42、排样设计--------------------------------------------------------------------------------4三、主要工艺参数的计算1、工艺力计算----------------------------------------------------------------------------62、压力机的选择-------------------------------------------------------------------------6四、模具设计1、模具结构形状设计------------------------------------------------------------------72、模具工作尺寸与公差计算--------------------------------------------------------7五、工作零件结构尺寸和公差的确定1、落料凹模板----------------------------------------------------------------------------82、拉深凸模--------------------------------------------------------------------------------93、凹凸模-----------------------------------------------------------------------------------9六、其他零件结构尺寸1、模架的选择----------------------------------------------------------------------------92、凹凸模固定板的选择--------------------------------------------------------------103、磨柄的选择---------------------------------------------------------------------------104、卸料装置-------------------------------------------------------------------------------105、推荐装置的选择------------------------------------------------------------------1 16、销、钉的选择---------------------------------------------------------------------117、模具闭合高度的校核------------------------------------------------------------11七、参考目录------------------------------------11零件图:材料:A3钢厚度:t=1mm一、零件冲压加工工艺性分析材料:该冲裁件的材料A3钢是低碳钢,拉深工艺性较好。
凸模板数控加工工艺设计

凸模板数控加工工艺设计图1.1 凸模板零件图1.1零件工艺性分析1.1.1 零件结构和功用分析凸模板如图1.1所示,凸模,又叫阳模,是成型塑件内表面的部件,在注射成型中通常装在注射机的动模板上,所以,习惯上又叫动模。
由于注塑成型中常让塑件留在凸模上,所以,在凸模上常装有顶出机构,以方便塑件的脱模。
凸模按结构形式,主要分为整体式凸模、组合式凸模。
该凸模板的结构简单,其结构特点是孔较多、两侧的腰形槽较小,因此在加工时需着重考虑对刀对零件精度的影响、切削力、转孔的速度和进给量等对零件的影响。
1.1.2 零件图纸分析1由零件图可知,该零件形状简单、腰子形键槽尺寸较小。
凸模板的尺寸精度要求并不是很高,采用铣削加工就可以达到要求,但是其形状位置精度要求较高,对称度0.03,同轴度要求为0.1,垂直度为0.04,由于模具对尺寸精度的要求比较高,加工中主要要保证的精度要求。
零件的尺寸标注采用统一的基准即设计基准,无多余尺寸与封闭尺寸。
1.1.3 主要技术要求分析(1)大平面的精度:上表面的粗糙度3.2,它的精度将直接影响到加工的精度精度。
(2)孔的位置精度:同一平面上导柱孔的位置度误差会影响生产出来的零件不合格,甚至合模时不能合上。
1.1.4 毛坯和材料的分析凸模板为单件,属于单件小批量生产。
凸模板材料为 YL15 ,毛坯重量约为0.9Kg。
毛坯为铝板切割而成,制作时毛坯的X轴方向加工余量为2mm公差为±0.02,毛坯的Y轴方向加工余量为20mm公差为±0.02,毛坯的Z轴方向加工余量为2mm 公差为±0.02。
加工毛坯时,为了保证加工面的加工精度,选择侧面的粗糙度较好一边为粗加工基准,从而保证其它面的垂直度和平行度。
加工其它两个侧面时,使用平口钳和已加工的侧面为定位基准,这样不仅可以使加工余量均匀而且保证加工精度。
在加工上表面和下表面时使用已加工面作为定位基准,满足“互为基准”及“基准重合”原则以保证加工精度。
第一节 凸模的加工方案与加工

3.特种工艺 所谓特种工艺,主要是指电火花加工、电解加工、 挤压、精密铸造、电铸等成形方法。 (二)模具工作零件的制造过程 1.毛坯准备 主要内容为工作零件毛坯的锻造、铸造、切割、 退火或正火等。 2.毛坯加工 主要内容为进行毛坯粗加工,切除加工表面上的 大部分余量。工种有锯、刨、铣、粗磨等。 3.零件加工 主要内容为进行模具零件的半精加工和精加工, 使零件各主要表面达到图样要求的尺寸精度和表面粗 糙度。工种有划线、钻、车、铣、镗、仿刨、插、热 处理、磨、电火花加工等。
教学案例 冲孔的凸模的加工
一、概述 模具的工作零件(或成型零件)一般比较复杂, 而且有较高的加工精度要求,其加工质量直接影响到 产品的质量与模具的使用寿命。模具工作零件工作型 面的形状多种多样,但归纳起来不外乎两类:一是外工 作型面,包括型芯与凸模等工作型面;二是内工作型 面,如各种凹模的工作型面,按照工作型面的特征又 可分为型孔与型腔两种。另外一大类为模具的结构零 件,例如各种固定板、卸料板、底座、导柱以及导套 等等…… (一)模具工作零件的加工方法 工作零件的加工方法根据加工条件和工艺方法可 分为三大类,即通用机床加工、数控机床加工和采用 特种工艺加工。
(10)钳工粗研:单面0.01~0.015mm研磨量(或 按加工余量表选择);
(11)热处理:工作部分局部淬火及回火; (12)钳工精研及抛光。
此类结构凸模的工艺方案不足之处就是淬火之前机 械加工成形,这样势必带来热处理的变形、氧化、脱碳、 烧蚀等问题,影响凸模的精度和质量。在选材时应采用 热变形小的合金工具钢如CrWMn,Cr12MoV等;采用 高温盐浴炉加热、淬火后采用真空回火稳定处理,防止 过烧和氧化等现象产生。
3、电火花线切割 凸模的电火花线切割: ①毛坯准备 将圆形棒料进行锻造,锻成六面体,并进行退火处理。 ②刨或铣六个面 在刨床或铣床上加工锻坯的六个面。 ③钻穿丝孔 在线切割加工起点处钻出直径为2~3mm电极丝穿丝孔。 ④加工螺钉孔 将固定凸模用的两个螺钉孔加工出来(钻孔、攻螺纹)。 ⑤热处理 将工件淬火、回火,并检查其表面硬度,硬度要求达到 58~62HRC。
凸模加工工艺过程卡片

36凸模加工工艺过程卡片文件编号毕业设计 凸模加工工艺过程卡片 产品型号 零(部)件图号 共2页 产品名称腰槽冲裁模 零(部)件名称凸模第1页 材料牌号毛坯种类毛坯外形尺寸40×18×60 每坯件数1 每台件数1备注工序号工序名称 工序内容车间设备工艺装备基本时间/min1 锻造将圆形棒料进行锻造,锻成六面体,并进行退火处理。
锻造车间 空气锤2铣六个面 在铣床上加工锻坯的六个面。
机加工车间铣床Ф50㎜的YG8硬质合金面铣刀 精密平口虎钳 游标卡尺3钻孔在线切割加工起点处钻出直径为2~3mm 电极丝穿丝孔。
机加工车间钻床Ф2㎜直柄短麻花钻通用夹具374加工螺钉孔 将固定凸模用的两个螺钉孔加工出来,即钻孔、攻螺纹。
机加工车间Ф5.2㎜直柄短麻花钻通用夹具M6丝锥描绘 5 热处理 将工件淬火、回火,并检查其表面硬度,硬度要求达到58~62HRC 。
热处理车间 6 磨削 磨光上、下两平面,表面粗糙度Ra 应低于0.8μm 。
机加工车间 磨床 通用夹具 CBN 砂轮底图号7钳工去除穿丝孔内杂质,并进行退磁处理。
钳工车间8线切割加工 按图样编制程序,并在纸带上钻孔编码,将纸带输入计算机,开动机床进行线切割加工。
电火花加工车间 线切割机通用夹具9 研磨 线切割后,钳工研磨凸模工作部分,使工作表面粗糙度降低。
钳工车间装订号姓名学号日期 2010年5月20号指导老师。
19冲裁模凸模的加工方法
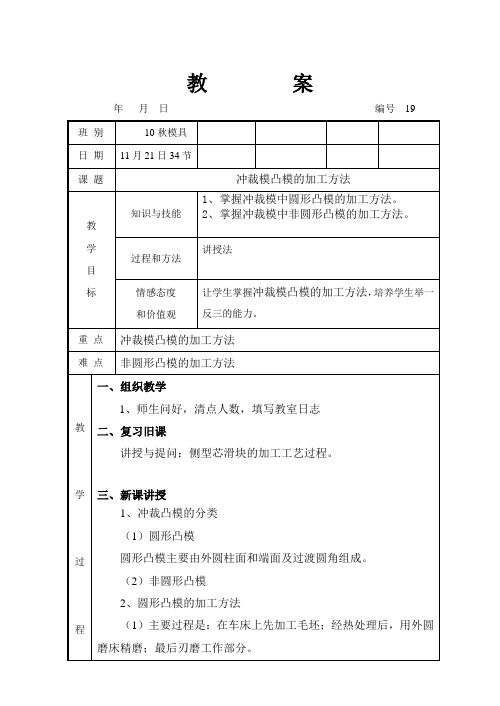
年月日编号19
班别
10秋模具
日期
11月21日34节
课题
冲裁模凸模的加工方法
教
学
目
标
知识与技能
1、掌握冲裁模中圆形凸模的加工方法。
2、掌握冲裁模中非圆形凸模的加工方法。
过程和方法
讲授法
情感态度
和价值观
让学生掌握冲裁模凸模的加工方法,培养学生举一反三的能力。
重点
冲裁模凸模的加工方法
难点
非圆形凸模的加工方法
(1)压印锉修
1)压印的方法
2)凹模压印锉修制造凸模的要点P21
(2,量具与刀具,安装及夹具。
2)刨削过程
先用机床用平口虎钳或专用夹具装夹凸模毛坯,然后刨削两端面,接着刨削两斜面,热处理,研磨,检验。
3)刨削凸模时的注意事项P22~23
四、课堂练习
五、课堂小节
教
学
过
程
一、组织教学
1、师生问好,清点人数,填写教室日志
二、复习旧课
讲授与提问:侧型芯滑块的加工工艺过程。
三、新课讲授
1、冲裁凸模的分类
(1)圆形凸模
圆形凸模主要由外圆柱面和端面及过渡圆角组成。
(2)非圆形凸模
2、圆形凸模的加工方法
(1)主要过程是:在车床上先加工毛坯;经热处理后,用外圆磨床精磨;最后刃磨工作部分。
冲裁模圆形凸模的加工方法和非圆形凸模加工方法的对比。
六、作业布置
课后反思
教
学
过
程
(2)双顶尖法加工
先车削出圆形凸模的两个端面,钻两端面顶尖孔,再用双顶尖法装夹圆形凸模毛坯,车削及磨削两端面。这种方法适用于细长圆形凸模的加工。
(3)工艺夹头法
凸缘工艺流程
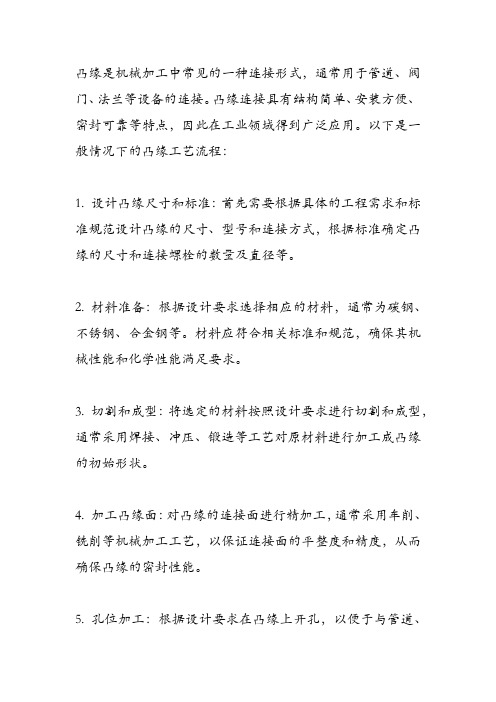
凸缘是机械加工中常见的一种连接形式,通常用于管道、阀门、法兰等设备的连接。
凸缘连接具有结构简单、安装方便、密封可靠等特点,因此在工业领域得到广泛应用。
以下是一般情况下的凸缘工艺流程:
1. 设计凸缘尺寸和标准:首先需要根据具体的工程需求和标准规范设计凸缘的尺寸、型号和连接方式,根据标准确定凸缘的尺寸和连接螺栓的数量及直径等。
2. 材料准备:根据设计要求选择相应的材料,通常为碳钢、不锈钢、合金钢等。
材料应符合相关标准和规范,确保其机械性能和化学性能满足要求。
3. 切割和成型:将选定的材料按照设计要求进行切割和成型,通常采用焊接、冲压、锻造等工艺对原材料进行加工成凸缘的初始形状。
4. 加工凸缘面:对凸缘的连接面进行精加工,通常采用车削、铣削等机械加工工艺,以保证连接面的平整度和精度,从而确保凸缘的密封性能。
5. 孔位加工:根据设计要求在凸缘上开孔,以便于与管道、
阀门等设备进行连接。
孔位加工通常采用钻孔、切割等工艺。
6. 表面处理:对凸缘表面进行除锈、喷砂、镀锌等表面处理,以提高凸缘的防腐蚀性能和外观质量。
7. 检验和验收:对加工完成的凸缘进行尺寸、外观、密封性能等方面的检验,确保凸缘符合设计要求和标准规范。
8. 包装和发运:对通过检验的凸缘进行包装,并根据客户订单要求进行发运,以便安装使用。
上述是一般情况下的凸缘工艺流程,实际情况可能会因不同的材料、尺寸、工艺要求等而有所不同。
在进行凸缘加工时,应严格按照相关标准和规范执行,确保凸缘的质量和使用性能。
凸件加工步骤过程及质量控制过程非机床加工
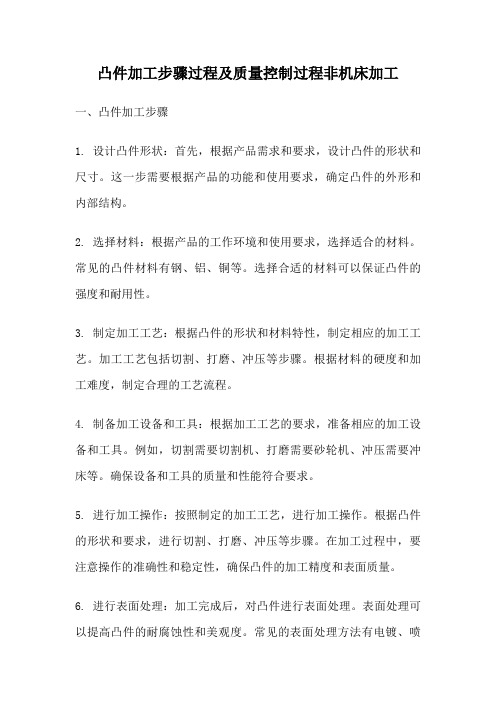
凸件加工步骤过程及质量控制过程非机床加工一、凸件加工步骤1. 设计凸件形状:首先,根据产品需求和要求,设计凸件的形状和尺寸。
这一步需要根据产品的功能和使用要求,确定凸件的外形和内部结构。
2. 选择材料:根据产品的工作环境和使用要求,选择适合的材料。
常见的凸件材料有钢、铝、铜等。
选择合适的材料可以保证凸件的强度和耐用性。
3. 制定加工工艺:根据凸件的形状和材料特性,制定相应的加工工艺。
加工工艺包括切割、打磨、冲压等步骤。
根据材料的硬度和加工难度,制定合理的工艺流程。
4. 制备加工设备和工具:根据加工工艺的要求,准备相应的加工设备和工具。
例如,切割需要切割机、打磨需要砂轮机、冲压需要冲床等。
确保设备和工具的质量和性能符合要求。
5. 进行加工操作:按照制定的加工工艺,进行加工操作。
根据凸件的形状和要求,进行切割、打磨、冲压等步骤。
在加工过程中,要注意操作的准确性和稳定性,确保凸件的加工精度和表面质量。
6. 进行表面处理:加工完成后,对凸件进行表面处理。
表面处理可以提高凸件的耐腐蚀性和美观度。
常见的表面处理方法有电镀、喷涂等。
7. 进行质量检验:加工完成后,对凸件进行质量检验。
质量检验包括尺寸测量、外观检查、功能测试等。
确保凸件的质量符合产品要求。
二、质量控制过程1. 设定质量标准:在加工凸件之前,制定凸件的质量标准。
质量标准包括尺寸偏差、表面质量、功能要求等。
根据产品的使用要求,设定合理的质量标准。
2. 进行过程控制:在凸件加工过程中,进行过程控制。
过程控制包括对加工参数的监控和调整,确保加工过程的稳定性和一致性。
例如,控制切割速度、打磨压力、冲压力等。
3. 进行质量检验:在加工完成后,进行质量检验。
质量检验可以采用非接触式测量仪器、显微镜等工具。
对凸件的尺寸、外观和功能进行检查,确保凸件的质量符合标准。
4. 进行纠正措施:如果发现凸件的质量不符合标准,需要进行纠正措施。
纠正措施可以包括调整加工参数、重新加工、更换材料等。
凸件加工步骤过程及质量控制过程非机床加工
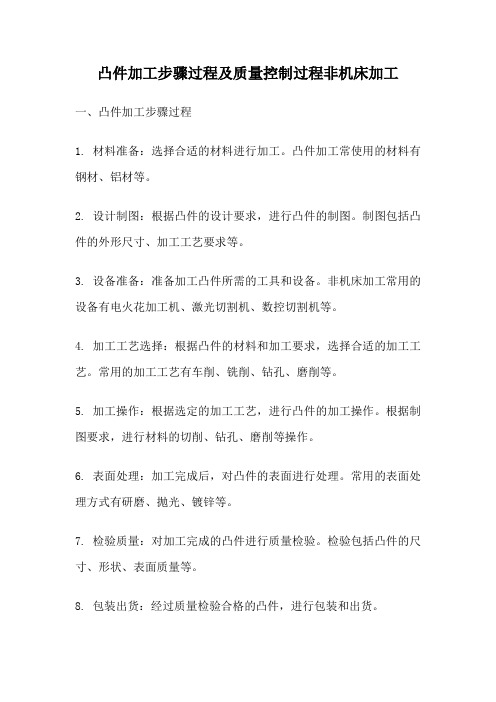
凸件加工步骤过程及质量控制过程非机床加工一、凸件加工步骤过程1. 材料准备:选择合适的材料进行加工。
凸件加工常使用的材料有钢材、铝材等。
2. 设计制图:根据凸件的设计要求,进行凸件的制图。
制图包括凸件的外形尺寸、加工工艺要求等。
3. 设备准备:准备加工凸件所需的工具和设备。
非机床加工常用的设备有电火花加工机、激光切割机、数控切割机等。
4. 加工工艺选择:根据凸件的材料和加工要求,选择合适的加工工艺。
常用的加工工艺有车削、铣削、钻孔、磨削等。
5. 加工操作:根据选定的加工工艺,进行凸件的加工操作。
根据制图要求,进行材料的切削、钻孔、磨削等操作。
6. 表面处理:加工完成后,对凸件的表面进行处理。
常用的表面处理方式有研磨、抛光、镀锌等。
7. 检验质量:对加工完成的凸件进行质量检验。
检验包括凸件的尺寸、形状、表面质量等。
8. 包装出货:经过质量检验合格的凸件,进行包装和出货。
二、质量控制过程1. 设定质量标准:根据凸件的设计要求和使用要求,设定凸件的质量标准。
包括尺寸精度、形状精度、表面质量等。
2. 过程控制:在加工过程中,进行过程控制,确保每一道工序的质量。
通过设定合理的参数和工艺,控制凸件的尺寸和形状。
3. 检验方法选择:根据凸件的质量要求,选择合适的检验方法。
常用的检验方法有量具测量、影像测量、三坐标测量等。
4. 检验过程:根据检验方法,对凸件进行检验。
检验包括尺寸测量、形状测量、表面质量检查等。
5. 不良品处理:对于检验不合格的凸件,进行不良品处理。
不良品可以进行返工修复或报废处理。
6. 记录与分析:对每一批凸件的检验结果进行记录和分析。
分析不良品的原因,并采取措施改善。
7. 客户满意度调查:定期对客户进行满意度调查,了解客户对凸件质量的满意度,以便不断改进质量控制过程。
通过以上的凸件加工步骤和质量控制过程,可以确保凸件的加工质量和满足客户的需求。
总结起来,凸件的非机床加工步骤包括材料准备、设计制图、设备准备、加工工艺选择、加工操作、表面处理、检验质量和包装出货。
第63讲 标准零件的使用方法(十二)圆形凸模(一)
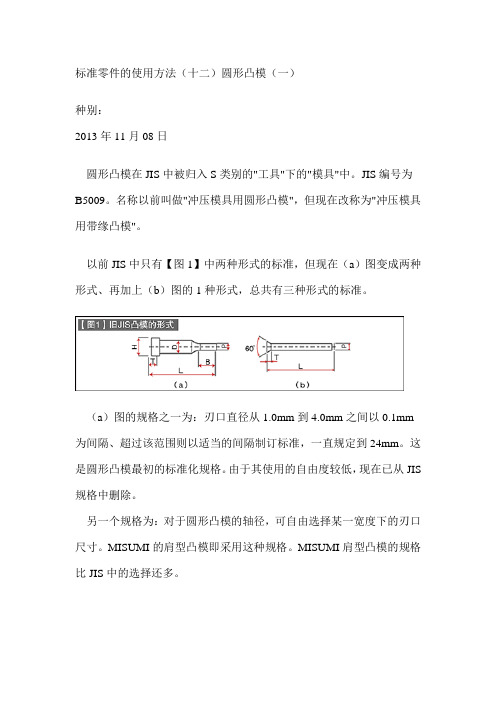
标准零件的使用方法(十二)圆形凸模(一)种别:2013年11月08日圆形凸模在JIS中被归入S类别的"工具"下的"模具"中。
JIS编号为B5009。
名称以前叫做"冲压模具用圆形凸模",但现在改称为"冲压模具用带缘凸模"。
以前JIS中只有【图1】中两种形式的标准,但现在(a)图变成两种形式、再加上(b)图的1种形式,总共有三种形式的标准。
(a)图的规格之一为:刃口直径从1.0mm到4.0mm之间以0.1mm 为间隔、超过该范围则以适当的间隔制订标准,一直规定到24mm。
这是圆形凸模最初的标准化规格。
由于其使用的自由度较低,现在已从JIS 规格中删除。
另一个规格为:对于圆形凸模的轴径,可自由选择某一宽度下的刃口尺寸。
MISUMI的肩型凸模即采用这种规格。
MISUMI肩型凸模的规格比JIS中的选择还多。
(b)图的标准也规定了所有尺寸,直径从0.1mm到4.9mm之间以0.1mm为间隔制订标准。
现在,此标准已从JIS中删除。
MISUMI有小型直杆型凸模的规格。
(a)图中凸缘部分的厚度(T)采用正公差。
以前为+0.3/0,现在为+0.25/0。
凸缘部分采用正公差的理由请见【图2】。
如【图2】的(b)所示,在进行凸模配合孔的加工时,要对凸缘部进行沉孔加工,但沉孔加工是精度较差的加工。
由于凸模和孔很难做到配合严密,因此组装时务必要使凸模的凸缘部突起,组装好后再将突起部磨平,这是采用这种方法的前提(指定该规格的当时这种组装方法很普遍)。
现在这种方式仍然被继续采用。
现在JIS中的种类如【图3】所示。
以后种类还可能不断增加,并适用于更多的用途。
虽然经过了与ISO 的整合,但有些种类可能会变得难以使用。
譬如凸模全长的长度。
以前的长度规格都是40、50、60的形式,但慢慢地变成了符合基准数的长度,如56、63、71,如50、60、70的形式已经不存在了。
- 1、下载文档前请自行甄别文档内容的完整性,平台不提供额外的编辑、内容补充、找答案等附加服务。
- 2、"仅部分预览"的文档,不可在线预览部分如存在完整性等问题,可反馈申请退款(可完整预览的文档不适用该条件!)。
- 3、如文档侵犯您的权益,请联系客服反馈,我们会尽快为您处理(人工客服工作时间:9:00-18:30)。
圆形凸模加工工艺规程
机电工程系
模具设计与制造
孙仕玺制作
工艺过程卡片产品代号零(部)件名称零(部)件号
凸模7
材
料
T10A 毛坯种类锻坯毛坯尺寸φ15㎜⨯55㎜每一毛坯可制零件数 1
工序序号工序
名称
工序内容设备夹辅具名称
刀具名称规
格
量具名称及规格
0 下料φ15㎜⨯55㎜锯床虎钳锯条游标卡尺
5 车车工作部分一侧的端面,钻中心孔
(长度控制在5mm以内)
卧式车床
三爪自定心卡
盘
游标卡尺
10 车车外圆(留磨削余量0.3mm)、车退
刀槽、切断
卧式车床
三爪自定心卡
盘、顶尖
900车刀
15 热处理淬火+回火,56-60HRC 高频炉
20 检验检验热处理是否达到要求硬度计游标卡尺
25 研磨中
心孔
研磨工作部分端的中心孔磨床M7120A
三爪自定心卡
盘、研磨顶尖
游标卡尺
30 磨外圆磨外圆保证0
020
.0
27
.
10
-
φ㎜及表面粗
糙度达图纸要求
平面磨床
三爪自定心卡
盘
砂轮直尺
编制孙仕玺学号2010051309 审查共 8 张第 1 张
工序卡片产品代号零(部)件名称零(部)件代号工序号0
凸模12 工序名称下料
材
料
T10A
设备名称锯床型号
夹具名称
刀量辅具
名称规格数量
游标卡尺200mm 1
锯条
编制孙仕玺校核审查共 6 张第 3 张
工序卡片产品代号零(部)件名称零(部)件代号工序号05
凸模12 工序名称车
材
料
T10A
设备名称卧式车床型号
夹具名称
刀量辅具
名称规格数量
游标卡尺200mm 1
三爪自定心卡
盘
编制孙仕玺校核审查共 6 张第 4 张
工序卡片产品代号零(部)件名称零(部)件代号工序号10
凸模12 工序名称车
材
料
T10A
设备名称卧式车床型号
夹具名称
刀量辅具
名称规格数量
游标卡尺200mm 1
三爪自定心
卡盘、顶尖
90°车刀
编制孙仕玺校核审查共 6 张第 5 张
工序卡片
产品代号 零(部)件名称 零(部)件代号 工序号 30
凸模
12
工序名称 磨外圆
材 料 T10A
设 备
名 称
平面磨床
型 号 夹具名称
刀 量 辅 具
名 称 规 格 数 量 游标卡尺 200mm
1 三爪自定心卡盘 砂 轮
编 制 孙仕玺 校 核
审 查
共 6 张 第 6 张
工序卡片产品代号零(部)件名称零(部)件代号工序号35
凸模12
工序名
称
切断
材
料
T10A
设
备
名称手摇磨床
型号
夹具名称
刀量辅具
名称规格数量
游标卡尺200mm 1
切断刀
编制孙仕玺校核审查共 6 张第7 张。