铸造工艺总汇-石膏型铸造与设计
石膏型精密铸造(石膏粉)
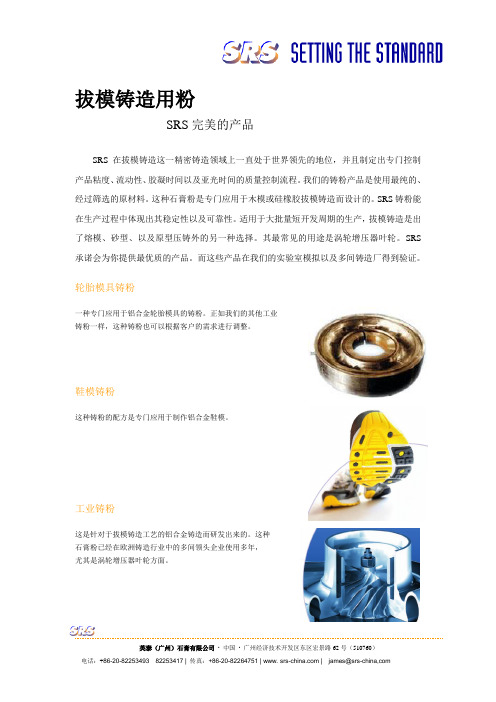
拔模铸造用粉
SRS完美的产品
SRS 在拔模铸造这一精密铸造领域上一直处于世界领先的地位,并且制定出专门控制产品粘度、流动性、胶凝时间以及亚光时间的质量控制流程。
我们的铸粉产品是使用最纯的、经过筛选的原材料。
这种石膏粉是专门应用于木模或硅橡胶拔模铸造而设计的。
SRS铸粉能在生产过程中体现出其稳定性以及可靠性。
适用于大批量短开发周期的生产,拔模铸造是出了熔模、砂型、以及原型压铸外的另一种选择。
其最常见的用途是涡轮增压器叶轮。
SRS 承诺会为你提供最优质的产品。
而这些产品在我们的实验室模拟以及多间铸造厂得到验证。
轮胎模具铸粉
一种专门应用于铝合金轮胎模具的铸粉。
正如我们的其他工业
铸粉一样,这种铸粉也可以根据客户的需求进行调整。
鞋模铸粉
这种铸粉的配方是专门应用于制作铝合金鞋模。
工业铸粉
这是针对于拔模铸造工艺的铝合金铸造而研发出来的。
这种
石膏粉已经在欧洲铸造行业中的多间领头企业使用多年,
尤其是涡轮增压器叶轮方面。
雕塑石膏实体铸型的制作工艺介绍
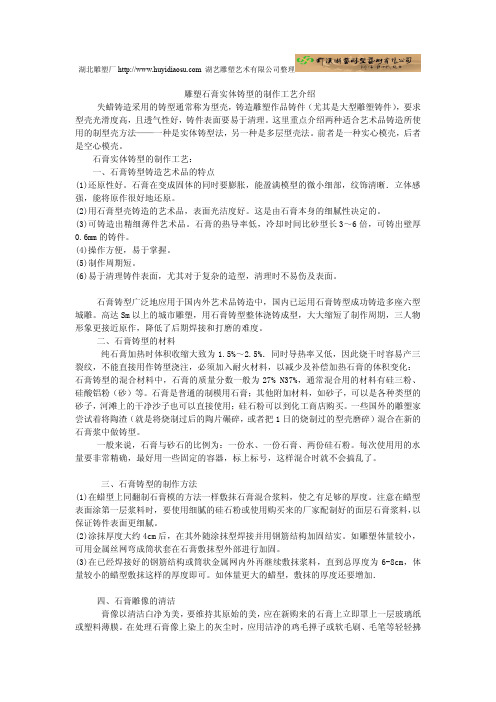
雕塑石膏实体铸型的制作工艺介绍失蜡铸造采用的铸型通常称为型壳,铸造雕塑作品铸件(尤其是大型雕塑铸件),要求型壳光滑度高,且透气性好,铸件表面要易于清理。
这里重点介绍两种适合艺术品铸造所使用的制型壳方法——一种是实体铸型法,另一种是多层型壳法。
前者是一种实心模壳,后者是空心模壳。
石膏实体铸型的制作工艺:一、石膏铸型铸造艺术品的特点(1)还原性好。
石膏在变成固体的同时要膨胀,能盈满模型的微小细部,纹饰清晰.立体感强,能将原作很好地还原。
(2)用石膏型壳铸造的艺术品,表面光洁度好。
这是由石膏本身的细腻性决定的。
(3)可铸造出精细薄件艺术品。
石膏的热导率低,冷却时间比砂型长3~6倍,可铸出壁厚0.6mm的铸件。
(4)操作方便,易于掌握。
(5)制作周期短。
(6)易于清理铸件表面,尤其对于复杂的造型,清理时不易伤及表面。
石膏铸型广泛地应用于国内外艺术品铸造中,国内已运用石膏铸型成功铸造多座六型城雕。
高达Sm以上的城市雕塑,用石膏铸型整体浇铸成型,大大缩短了制作周期,三人物形象更接近原作,降低了后期焊接和打磨的难度。
二、石膏铸型的材料纯石膏加热时体积收缩大致为1.5%~2.5%.同时导热率又低,因此烧干时容易产三裂纹,不能直接用作铸型浇注,必须加入耐火材料,以减少及补偿加热石膏的体积变化:石膏铸型的混合材料中,石膏的质量分数一般为27%N37%,通常混合用的材料有硅三粉、硅酸铝粉(砂)等。
石膏是普通的制模用石膏;其他附加材料,如砂子,可以是各种类型的砂子,河滩上的干净沙子也可以直接使用;硅石粉可以到化工商店购买。
一些国外的雕塑家尝试着将陶渣(就是将烧制过后的陶片碾碎,或者把1日的烧制过的型壳磨碎)混合在新的石膏浆中做铸型。
一般来说,石膏与砂石的比例为:一份水、一份石膏、两份硅石粉。
每次使用用的水量要非常精确,最好用一些固定的容器,标上标号,这样混合时就不会搞乱了。
三、石膏铸型的制作方法(1)在蜡型上同翻制石膏模的方法一样敷抹石膏混合浆料,使之有足够的厚度。
石膏型铸造讲义

石膏型铸造讲义
1
主要内容 概述 1、制石膏型用材料及其组成 2、石膏型精铸工艺
2
概述
1、工艺过程 石膏型精密铸造是20世纪70年代发展起来的一
种精密铸造新技术,其典型工艺过程见图0-1。 它是将熔模组装,并固定在专供灌浆用的砂箱
平板上,在真空下把石膏浆料灌入,待浆料凝结后 经干燥即可脱除熔模,再经烘干、焙烧成为石膏型, 在真空下浇注获得铸件。
3
概述
2、工艺特点
(1) 石膏浆料的流动性很好,又在真空下灌注成型, 其充型性优良,复模性优异,型精确、光洁。该工艺不 像一般熔模精密铸造受到涂挂工艺的限制,可灌注大型 复杂铸件用型。
(2) 石膏型的热导率很低,充型时合金液流动保持 时间长,适宜生产薄壁复杂件。
但铸型激冷作用差,组织粗大,当铸件壁厚差异大 时,厚大处容易出现缩松、缩孔等缺陷。
1.3
0.2
2.1-2.2 0.5 X10-6
3.25 3.1-4.3 X10-6 1.5
0.65
3.08-
5.3 X10-6
2.3
3.4
0.80
3.15
3.2-3.4 5.0 X10-6 2.6
4.6
0.85
3.95-
8.4 X10-6
2.0
3.5
0.65
4.02
5.73 7.2-10 X10-6
除石膏种类外,影响石膏强度的因素还有石膏的 细度、水固比、水温、搅拌时间等。
6
第一节 制石膏型用材料及其组成 2. 填料
为使石膏型具有良好的强度,减小其收缩和裂纹 倾向,需要在石膏中加入填料。
填料应有合适的熔点、耐火度,良好的化学稳定 性、合适的线膨胀率、发气量少,吸湿性小等性能, 常用作填料的材料及其性能见表1-1。
第2章石膏型精密铸造1

镁合金
1.2
1.6
锰黄铜 1.8~2.0 2.0~2.3
石膏型精密铸件的综合收缩率A可按下式计算:
A% (a c d)%
三、铸造斜度 石膏型精密铸件的铸造斜度可参考熔模铸造斜 度。
2.2.3浇注系统及冒口设计 石膏型精密铸件浇注系统及冒口设计可参考熔
模铸造或砂型铸造。应注意以下几点: 1、石膏导热性差,金属液保持流动时间长, 故浇注系统截面积尺寸可比砂型铸造减少 20%左右。
表2-3 尿素模料配方
序号 尿素
硼酸
硼酸钾 羧甲基纤维素
水
1 97~98 2~3
2 75~85
15~25
3
85
10
5
表2-4 无机盐模料配方
名称
KNO3 NaNO2 NaNO3 Al2(SO4)3 (NH4)2SO4 HO2
亚硝酸盐模料 55
45
—
—
—
—
硝酸盐模料 55
—
45
—
—
—
硫酸盐模料 —
2.1.2工艺特点 1、使用易熔模,不用开箱起模。 2、可制造尺寸精度高(可达CT4~6级)、大型 (1000mm×2000mm)、薄壁 (壁厚为1.5mm,局
部为0.5mm)、形状复杂的精密铸件。表面粗 糙度一般Ra1.6~3.2μm,最高可达0.8μm。 同时石膏型溃散性好,易于清除。
3、石膏型导热系数低,金属液浇入后保持流动 性时间长,铸件的成形性能好,但铸件凝固时间 长,致使铸件产生气孔、针孔、疏松、缩孔的倾 向大。
石膏型精铸专用模料主要有下列三方面要求: (1)模料强度高、韧性好,能承受石膏浆料灌
注的作用力而不变形损坏。 (2)模料线收缩小,保证熔模尺寸精确,防止
铜器石膏型失蜡铸造法简介

铜器石膏型失蜡铸造法简介中华文明的历史进程中有很多手工艺的(璀璨发明,失蜡浇铸法就是其中之一。
失蜡浇铸法最早见于商周时代的青铜器加工中,到明清则大为盛行。
其特点:精细入微、毫厘毕现,比较适合于美感要求比较高的工艺品的加工。
到了现代,由于新的现代材料不断出现和引入,目前的失蜡铸造法除始终保持古法的目的和宗旨外,在方式方法上已不完全一样。
以下就目前常用的石膏型失蜡铸造方法作简单介绍。
石膏型失蜡铸造法的基本流程:一制阴模古法的阴模由泥土作成,然后烧制成低温陶性质的阴模,称之为“陶范”,由于烧陶过程中有很多变形的可能,所以现代已不再使用陶范的方式,而改用强度较高的石膏制作阴模:制作时在整体的阳模(现代一般是玻璃钢材质)上,按易于拆分的原则,用石膏浆制作出多块合成的套模(此时特别要注意脱模剂的使用),待石膏型固化冷却后,可将阴模拆解分开,清洁阴模内表面,用水刷7-8分潮湿后背用;二制蜡型将备好的阴模拼合成整体,使之形成需铸造的工艺品的负型(即阴模),然后将调制并加温到一定温度的液态工艺品蜡液涂刷于阴模内表面,涂刷时注意每层尽量整体一次刷完整,待整体都冷却硬化固定后再涂刷下一层,逐层加厚,直到达到所需厚度。
蜡型的厚度视加工件的大小而定,4-10毫米不等。
要求厚薄均匀,附着密实。
蜡型制作完成后,清理内表面的毛刺、将阴模的边口处修理平滑。
备用;三灌内浆将刷制完成的蜡型带石膏阴模一起倒立(大形的还需在阴模外壳加以捆扎,以防灌注时内压过大使蜡模崩裂),如有多个刷蜡口则将其他的次要开口堵住,留主口朝上,将事先混合好的耐火材料用水调制成匀质的泥浆,灌注于蜡型内,要求:灌注到位、不留空泡、操作上一气呵成、避免分层现象。
静置6小时待蜡型内的耐火材料完全硬化后方可进行下阶段的操作;四修蜡模接浇道将已灌注好耐火材料内浆的模型整体正立过来,小心去掉最外面的石膏阴模(要按拼合规律逐次拆分,不可蛮干以免损伤里面的蜡型),全部阴模拆除后用小刀修除模块之间缝隙形成的蜡毛边、毛刺,清洁蜡型表面,如有损伤则用修补软蜡修补完整。
石膏铸造注意事项

石膏铸造注意事项石膏铸造是一种常见的制造工艺,广泛应用于艺术品制作、建筑装饰、医疗器械、工艺品等领域。
以下是石膏铸造时需要注意的事项:1. 原材料选择:石膏是石膏铸造的主要材料,应选择质量好、无杂质的石膏。
同时,可以根据不同的需求选择不同类型的石膏,如增强型石膏、特种石膏等。
2. 模具设计:模具是石膏铸造中至关重要的一环。
设计模具时需要确保模具结构合理、稳定,能够完整地复制所需的物体。
同时,要注意模具的开口方向以便于浇注和脱模。
3. 浇注粘度控制:控制石膏的粘度是石膏铸造中的关键步骤。
粘度过高会导致石膏流动性差,难以充填模具;粘度过低则容易形成气泡和缺陷。
因此,需要根据具体要求控制石膏的水石比,控制好水的用量,以获得适当的粘度。
4. 前处理:在浇注石膏之前,需要对模具进行预处理。
首先,要保证模具表面干净,没有灰尘和杂质。
其次,可以在模具表面涂抹一层脱模剂,以便于石膏脱模时不易粘连。
5. 浇注操作:浇注时要缓慢、均匀地将石膏倒入模具中,避免产生气泡和未充填的空隙。
同时,要控制浇注的速度和角度,以确保石膏能够充分填充模具。
6. 振动除气:在浇注完成后,可以通过轻轻震动模具来排除石膏中的气泡。
振动过程中要逐渐加大力度,同时避免过度振动导致石膏移位或损坏模具。
7. 固化和硬化:浇注完成后,需要将石膏模具放置在通风干燥的环境中进行固化和硬化。
固化时间通常为数小时到数天,具体时间要根据石膏类型和环境条件而定。
8. 脱模操作:石膏完全固化后,可以进行脱模操作。
需要注意的是,应轻轻敲击模具,使石膏从模具中脱离。
如遇到模具卡住的情况,可以使用适当的工具轻轻拍打或使用少许脱模剂帮助脱模。
9. 后处理:脱模后,可以对石膏制品进行一些修整和润饰。
可以使用砂纸、刀具等工具去除毛边和不平整的地方,使石膏制品表面光滑、细腻。
10. 储存和保护:完成石膏铸造后,要妥善储存和保护石膏制品。
可以使用密封袋或包装纸将石膏制品包裹好,避免受潮、受阳光直射和摩擦。
铝合金石膏型熔模铸造工艺
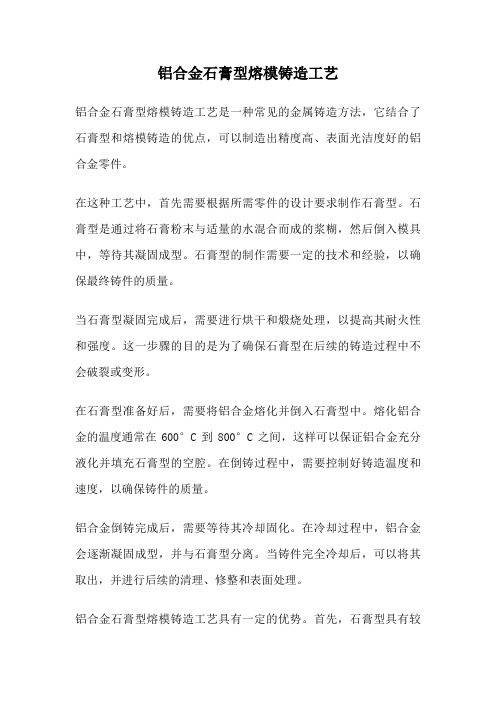
铝合金石膏型熔模铸造工艺铝合金石膏型熔模铸造工艺是一种常见的金属铸造方法,它结合了石膏型和熔模铸造的优点,可以制造出精度高、表面光洁度好的铝合金零件。
在这种工艺中,首先需要根据所需零件的设计要求制作石膏型。
石膏型是通过将石膏粉末与适量的水混合而成的浆糊,然后倒入模具中,等待其凝固成型。
石膏型的制作需要一定的技术和经验,以确保最终铸件的质量。
当石膏型凝固完成后,需要进行烘干和煅烧处理,以提高其耐火性和强度。
这一步骤的目的是为了确保石膏型在后续的铸造过程中不会破裂或变形。
在石膏型准备好后,需要将铝合金熔化并倒入石膏型中。
熔化铝合金的温度通常在600°C到800°C之间,这样可以保证铝合金充分液化并填充石膏型的空腔。
在倒铸过程中,需要控制好铸造温度和速度,以确保铸件的质量。
铝合金倒铸完成后,需要等待其冷却固化。
在冷却过程中,铝合金会逐渐凝固成型,并与石膏型分离。
当铸件完全冷却后,可以将其取出,并进行后续的清理、修整和表面处理。
铝合金石膏型熔模铸造工艺具有一定的优势。
首先,石膏型具有较高的精度和光洁度,可以制造出形状复杂、尺寸精确的铝合金零件。
其次,石膏型可以重复使用,降低生产成本。
此外,由于铝合金的低熔点和良好的流动性,石膏型熔模铸造工艺适用于各种铝合金材料。
然而,铝合金石膏型熔模铸造工艺也存在一些限制。
首先,由于石膏型的制备和处理过程较为复杂,需要一定的时间和技术。
其次,石膏型在高温下容易破裂或变形,需要特殊的处理和保护措施。
此外,由于铝合金的热膨胀系数较大,在铸造过程中需要考虑收缩和变形的问题。
总的来说,铝合金石膏型熔模铸造工艺是一种高精度、高质量的铸造方法。
它不仅可以满足各种复杂零件的制造要求,还能够提高生产效率和降低生产成本。
随着技术的不断进步,铝合金石膏型熔模铸造工艺在各个领域的应用将会越来越广泛。
石膏型铸造

缓凝剂主要有三类: (a)磷酸盐、碱金属硼酸盐、硼砂、硼酸等。 (b)有机酸及可溶性盐,如柠檬酸及其盐、琥珀 酸钠、乙基酸钠、甲基酸钠、草酸等。 琥珀酸钠的缓凝作用很强,只需要加入千分之几 就有明显的效果。 (c)蛋白胶、皮胶、硅溶胶、纸浆废液等。
增强剂用来增加石膏型的湿强度、干强度、焙烧 后强度以及高温强度。一般用某些硫酸盐如 Na2SO4、K2SO4、NiSO4、MgSO4等,其中以 MgSO4的效果最好。
• 石膏型需随炉冷却,当温度降至300℃以下时才可 以出炉,否则石膏型容易开裂,对复杂型温度应低 些。
填料
α-
半水
硅
石膏 硅石粉 线
100
石
%
高 高岭 莫来 铝 土 石矾
土
工 业 氧 化 铝
锆 英 粉
石 英 玻 璃
300℃ 空冷
微裂
极轻微 裂
不 裂
不裂
不裂
不 裂
不 裂
不不 裂裂
700℃ 空冷
碎裂 微裂
4.3.2浇注系统及冒口设计
• 对于石膏型铸造,浇注系统应满足如下要求: • A良好的排气能力,能顺利排出型腔气体,在顶部和易裹
气处开设出气口。 • B保证金属液充型平稳,避免出现紊流,卷气现象。 • C合理设置冒口,保证补缩。 • D脱模时浇注系统先熔脱,减小熔模对石膏型的胀型力。 • E浇注系统在铸件凝固时尽可能不阻碍铸件收缩,以防止
650~700℃左右,加压压力0.07MPa左右。
4.2.3 石膏型应用实例
图4-6是铝合金轮胎样件模具的石膏型 铸造实例。该样件从三维实体造型,制造 LOM原型(图4-6b)、硅橡胶模(图46c)、石膏型(图4-6d)到将烘干及焙烧 完毕的石膏型温度降低至180℃,浇注铝合 金制造出模具(图4-6f),总制造周期为4 天。
石膏材料和石膏型制造工艺-下
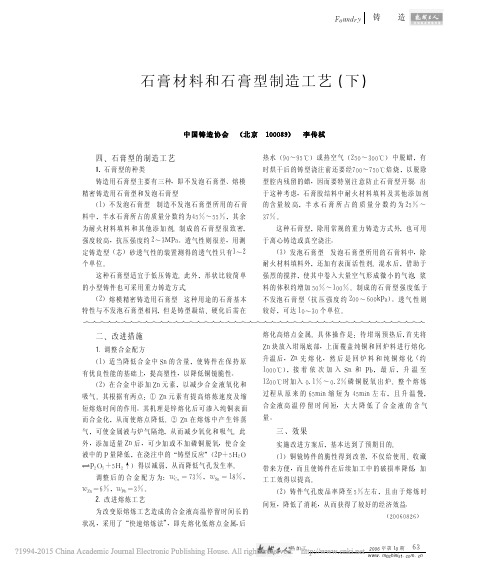
"""""""""""""""""""""""""""""""""""""""""""""" 熔化高熔点金 属% 具 体 操 作 是& 待 坩 埚 预 热后" 首 先将 二 ! 改进措施 $ % 调整合金配方 # "$ 适当降 低 合 金 中 1 2 的 含 量" 使 铸 件 在 保 持 原 有优良性能的基础上" 提高塑性" 以降低铜镜脆性% # &$ 在合 金 中 添 加 3 2 元 素" 以 减 少 合 金 液 氧 化 和 吸气 % 其根据有两点& " 3 2元素有提高熔炼速度及缩 短熔炼时间的作用% 其机理是锌 熔 化 后 可 渗 入 纯 铜 表 面 而合金化" 从而使熔 点 降 低% # 3 2在熔炼中产生锌蒸 气 " 可使金属液与炉气隔 绝" 从 而 减 少 氧 化 和 吸 气% 此 外 " 添加适量 3 2 后 " 可 少 加 或 不 加 磷 铜 脱 氧" 使 合 金 液中的 ) 量降低" 在浇注中的 ’ 铸型反应(# & )4$5&6 # $) &6 $ 4$5 & % $ 得以减弱" 从而降低气孔发生率% 调整 后 的 合 金 配 方 为&(78 9. ’% "(1 :% " 2 9" "() % (3 29/% ;9’% ! % 改进熔炼工艺 为改变原熔炼工艺造成的合 金 液 高 温 停 留 时 间 长的 " 即 先 熔 化 低 熔 点 金 属" 状况 " 采用了 ’ 快速熔炼法( 后 3 2 块放入坩埚底部" 上面 覆 盖 纯 铜 和 回 炉 料 进 行 熔 化% 约 升温 后"3 2 先 熔 化" 然 后 是 回 炉 料 和 纯 铜 熔 化 # "接 着 依 次 加 入 1 " , , ,- $ 2和 ) ;" 最 后 " 升 温 至 " & , ,- 时加入 , ! "% !, ! &% 磷 铜 脱 氧 出 炉% 整 个 熔 炼 过程 从 原 来 的 / $ < = 2缩短为# $ < = 2 左 右 " 且 升 温 慢" 合金液 高 温 停 留 时 间 短" 大 大 降 低 了 合 金 液 的 含 气 量 % !!
金属精密液态成形技术-第3章石膏型精密铸造

(1)石膏的选择
石膏有七种变体
生石膏 CaSO4·2H2O
(二水石膏)
熟石膏
(半水石膏)
αCaSO4·1/2H2O βCaSO4·1/2H2O
硬石膏 CaSO4
(无水石膏)
αⅢ 、Ⅱ 、Ⅰ
βⅢ
对石膏的要求
➢ 流动性:水固比低的情况下流动性好
➢ 凝结时间:初凝时间5~7min,终凝时间10min ➢ 强度 ➢ 线膨胀率:<5%,从填料和添加剂方面解决 ➢ 抗裂纹性能:加热过程多次相变,300℃激冷 ➢ 发气性:石膏型透气性差,浇不足,气孔
3.2.1 模料
石膏型精密铸造用的模样主要是熔模,也可使 用气化模、水溶性模(芯)。
对于一般中小型铸件,可使用熔模铸造用模料 ;但大中型复杂铸件,其尺寸精度和表面粗糙度 要求严格时,则应使用石膏型精铸专用模料。
模料
石膏型精铸专用模料主要有下列三方面要求: ➢ 模料强度高、韧性好,能承受石膏浆料灌
注的作用力而不变形损坏。 ➢ 模料线收缩小,保证熔模尺寸精确,防止
铸造工艺设计基础, 工程流体力学
能够合理地选择石膏 型熔模精密铸造的模样、 石膏浆料的原材料
石膏晶体结构及石 膏性能
3.1概述
3.1概述
石膏型铸造按脱模方法可分为下面两类: 熔模石膏型铸造(或石膏型精密铸造) 拔模石膏型铸造
石膏型精密铸造是使用熔模,用石膏浆料灌制 铸型,经干燥、脱蜡、焙烧后即可浇注铸件的方 法。是20世纪70年代发展起来的一种精密铸造新 技术。
(2)填料
石膏型对填料的要求 (1)有合适的线膨胀率 (2)有较高的熔点和耐火度 (3)有良好的化学稳定性 (4)发气量少、吸湿性小、保水性好 (5)填料在石膏型浆体中有良好的悬浮弥散性 (6)能降低石膏混合料的裂纹倾向
第2章石膏型精密铸造2

表2-10 填料种类对石膏混合料裂纹倾向的影响
填料 300→空冷 700→空冷 α -半 水石膏 100% 微裂 碎裂 硅石 粉 极轻 微裂 微裂 硅线 石 不裂 不裂 高岭 土 不裂 极轻 微裂 或不 裂 莫来 石 不裂 极轻 微裂 高铝 矾土 不裂 极轻 微裂 工业 氧化 铝 不裂 轻微 裂 锆英 粉 不裂 轻微 裂 石英 玻璃 不裂 不裂
加水量多少(亦即水固比大小),与多种因素
有关,既受到固态粉料中石膏、填料、添加剂的
品种及其比例的影响,又受粉料粒度、水温等的 影响。
表2-12 石膏浆料配比
序号 石膏 硅石粉砂 1 2 3 4 5 6 7 30 30 30 30 30 30 35.5 35 — 29.0 70 35 20 石英玻璃 — — — — 35 — 35.5 其他材料 — 铝矾土粉砂 35 上店土粉砂 50 莫来石粉砂 70 — 铝矾土粉砂 70 硅藻土2
理是尿素不同时期发气或热分解产物助长了石膏 膨化抗缩;
第二类是硝酸盐如Al(NO3)3、Fe (NO3)3、 Be(NO3)2、ZrO (NO3)2、Mn(NO3)2,作用原理是加
热分解生成的高熔点氧化物包复在石膏晶体表
面,形成耐热膜阻碍二水石膏脱水及晶体变形产 生的体积收缩;
第三类是有机化合物及复合盐,如琥珀酸纳、 柠檬酸盐、NaCl、氯化钡、MgSO4,可抑制石膏 同 质异构体转变所引起的体积收缩。
石膏型铸型制备.

课题名称石膏型铸型制备课次授课日期授课班级授课地点教学目的与要求知识目标:1.熟悉拔模石膏型铸型制备工艺;2.掌握工具、设备使用方法;3.熟悉铸型质量检验标准。
能力目标:能够完成叶轮铸件拔模石膏型铸型制备。
素质目标:1.分析问题解决问题的能力;2.容忍、团队协作精神;3.科学思维、认真敬业。
重点难点及解决方法重点:1.拔模石膏型铸型制备工艺;2.工具、设备使用方法。
难点:1.工具、设备使用方法;2.铸型质量检验。
教学设计(方法、教具、手段、内容)方法:讲授、实操教具:铜合金铸件手段:多媒体内容:一、任务布置二、生产准备三、铸型制备四、铸型检验课外作业影响叶轮铸件铸型质量的主要原因?授课内容授课时间叶轮铸件石膏型铸型制备一、任务布置二、生产准备三、铸型制备四、铸型检验5min 35min 140min 20min授课内容备注叶轮铸件石膏型铸型制备一、任务布置根据制定的工作计划,完成叶轮铸件石膏型铸型制备。
二、生产准备1.螺旋桨式搅拌机作用:搅拌配制好的浆料。
要求:螺旋桨的使用转速为200~500r/min。
2.压缩空气喷枪作用:将模样从铸型中吹出。
要求:吹入0.2~0.5MPa的压缩空气。
3.焙烧炉作用:对石膏型铸型进行烘干、焙烧。
要求:100℃(保温3h)→l50℃(保温5h)→250℃(保温20h)三、铸型制备1.按学号顺序分成6个小组;2.要求每组完成2个铸型制备;3.按照计划方案实施操作;4.注意操作安全。
四、铸型检验。
金属精密液态成形技术课件-石膏型精密铸造

石膏型鑄造可生產Sn、Pb、Za、Al、Cu、Ag、 Au鑄件,不能生產Mg、Fe鑄件。
石膏型精密鑄造小結
1、石膏型精密鑄造與熔模精密鑄造區別在於 用石膏漿料灌注鑄型。
2、石膏型精密鑄造主要用於大型薄壁複雜的 鋁鑄件中。
3、石膏漿料要正確選擇石膏種類、填料和水 與石膏的比例;在真空下攪拌和灌注石膏 漿料。
α石膏與合金 Sn Pb Zn Mg Cu Ag Au Fe
Al
合金熔點/℃ 232 327 420 650 1083 960 1063 1536
660
石膏熱分解溫度/℃ 1060 1160 700 620
1220-1240 1340 1320 900
1080-1360
鑄造可能性 √ √ √ × √ √ √ ×
(6)調壓鑄造 ——適於複雜薄壁鑄件
真空澆注罐效果圖
3.4.2澆注工藝參數
(1)鋁合金澆注溫度 一般控制在700℃,大型薄壁件,不宜超
過720℃。 (2)石膏型溫度
150~300℃ 大型複雜薄壁件取上限 中小型壁稍厚鑄件取下限
3.5鑄件清整
3.5鑄件清整
(1)脫除石膏型或石膏芯 脫除石膏型:國外常用5MPa的高壓水清 除石膏型
NaCl、NaF、MgCl2等 緩凝劑—減緩脫水石膏的溶解速度,降低溶解度,磷
酸鹽、鹼金屬硼酸鹽、有機酸等 減縮劑—減少石膏型收縮和裂紋傾向,有三類物質,
(鹵化物、硝酸鹽、有機化合物及複合鹽
3.3.2石膏漿料
(1)石膏漿料配比
石膏漿料的配方是石膏型工藝的關鍵技術之一。 高質量的石膏型是獲得高質量鑄件的前提。但純石 膏收縮過大,裂紋傾向大,焙燒時強度急劇下降, 甚至發生開裂。因此需要優選石膏型材料配方。實 驗證明,採用下表所示的配比製作的石膏型烘乾焙 燒後,不易開裂,強度較高。
石膏模法精密铸造工艺流程

石膏模法精密铸造工艺流程第1步:概念与设计概念与设计设计师将自己的构思手绘出草图,然后使用制图软件将草图以精确的尺寸进行电脑绘制,完成最初的设计图纸。
第2步:工匠雕刻蜡工匠雕刻蜡工匠参照设计图纸手工雕刻出蜡版,再利用失蜡浇铸的方法倒出银版,而蜡版的批量制作则需用银版压制橡胶模。
这是失蜡铸造制作工艺中要求最高的工序,所制银版必须光洁无痕,各部分结构合理,镶嵌宝石的位置尺寸准确无误。
第3步:胶模注蜡胶模注蜡橡胶模开好后进行注蜡操作。
注蜡机中的蜡应保持在70-75度之间,将蜡液注入胶膜,冷却后取出蜡模,依次重复,得到多件蜡模。
第4步:完成蜡型完成蜡型准备好此次批量制作时所需的所有蜡版。
第5步:种蜡树种蜡树将每个蜡环单独手工焊接到一根蜡棒上,最终得到一棵形状酷似大树的蜡树,准备进行浇铸。
第6步:称蜡树称蜡树种蜡树前先对橡胶底盘进行称重,种完蜡树再一次称重,两次称重的结果相减可以得出蜡树的重量,将蜡树的重量根据铜的密度比例进行换算,得出进行浇铸的金属量。
第7步:灌石膏灌石膏将种好的蜡树连底盘一起套上不锈钢筒,并将相应重量的石膏浆沿钢筒内壁缓缓注入,没过蜡树,抽真空后自然防止6-12小时,使石膏凝固。
第8步:烘焙石膏烘焙石膏将石膏模进行烘焙,作用是脱蜡,干燥和浇铸保温。
第9步:取出石膏模取出石膏模取出烘焙好的石膏模,并同时准备好需要浇铸的金属溶液。
第10步:浇注金属液体浇注金属液体将已经熔化配好的铜水,从水口注入。
第11步:离心工艺浇铸离心工艺浇铸使用真空感应离心浇铸机浇铸。
第12步:石膏模炸洗及清洗石膏模炸洗及清洗铸造后的石膏模处于高温状态,从浇铸机取出后自然放置10-30分钟,再放入冷水中进行炸洗。
石膏由于收缩作用炸裂后,取出金树,用钢刷刷去大块的石膏,放入30%的氢氟酸中浸泡10分钟,夹出后冲洗,除去剩余石膏,直到金树表面干净。
第13步:剪切铸件剪切铸件将金树上的铸件沿水口底部剪下晾干。
第14步:滚筒抛光工艺滚筒抛光工艺用不锈钢磨料和活性有机合成溶液放入滚筒,随旋转摩擦使表面平整光亮。
第八篇第七章-石膏型铸造285页
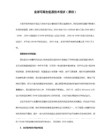
第七章石膏型铸造第一节石膏型铸造的工艺特点石膏型铸造采用易熔模料、硅橡胶、金属或木材等材质制成光洁精细的模样,灌以石膏浆料制成铸型,经烘干焙烧后浇注合金液最终获得光洁精密铸件。
因石膏浆料成形性及复制性很好,可浇出复杂薄壁精细的锌、铝、铜、金、银等有色合金铸件,铸件的最小壁厚可小于!"",表面粗糙度一般为!$%&!"左右,尺寸精度可达’(%()*#(%!(""+&)"";石膏型浇注后溃散性好便于清理;石膏对人体无害,不污染环境,价格较低,资源丰富。
石膏型铸造的缺点是石膏的热导率很小,铸型的透气性极低,易使铸件晶粒粗大和形成针孔,故主要用来生产整体大型复杂薄壁精密铸件和用其他方法难以铸造及有特殊要求的铸件。
第二节石膏型铸造方法的分类、工艺过程及应用一、石膏型铸造方法的分类按脱模方法不同可分为熔模石膏型铸造及模石膏型铸造两类,前者是加热熔模使其从石膏型中流出,后者是通过人力或机械方法将模样从型中拔出。
模石膏型铸造又可分为普通石膏型和发泡石膏型。
二、石膏型铸造的工艺过程三种石膏型铸造的工艺过程,见图,-.-!。
・・&/,$图!"#"$熔模石膏型铸造工艺过程图!"#"%发泡石膏型铸造工艺过程图!"#"&普通石膏型铸造工艺过程三、石膏型铸造的应用(一)熔模石膏型铸造主要用于整体复杂薄壁精密铸件,如大型电子仪器设备的框架、壳体、底座、飞机、导弹、雷达、宇航等行业用的泵体、附件壳体、机匣、叶轮、微波元件等,亦可用来铸造金银首饰,复制雕塑文物等艺术品。
(二)普通石膏型铸造主要用来生产各种模具如塑料、橡胶成形用模具,铸造模具,金属冲模等。
(三)发泡石膏型铸造用来生产叶轮类、框架类铸件和精密模具等。
・’(&%・第三节石膏及石膏型的理论基础一、石膏的名称、类型以及各种变体(一)石膏一般指二水石膏,化学式为!"#$%・&’&$。
第七章 石膏型铸造分解
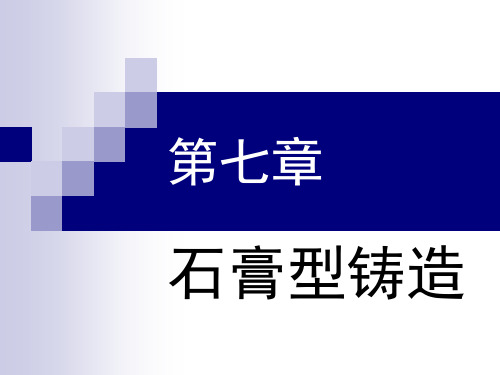
要求和石膏原材料性能来决定。有关手册
列出了比较常用的混合浆料的配比,可供
参考。
• (2)石膏混合浆体的搅拌、灌注
• 石膏混合料吸附大量的气体,在浆料搅拌时又 会卷入大量的气,致使浆料中有大量的气泡,影响石 膏型腔表面的质量。除发泡石膏型希望有大量孔洞可 以在大气下搅拌及灌注外,普通石膏型浆料应该在真
7.2.3 石膏型应用实例
图9-6是铝合金轮胎样件模具的石膏型
铸造实例。该样件从三维实体造型,制造
LOM原型(图9-6a)、硅橡胶模(图9-
6b)、石膏型(图9-6c)到将烘干及焙烧
完毕的石膏型温度降低至180℃,浇注铝合
凝结时间 /min 初凝 终凝 8~ 12~ 10 18 7~ 5~7 12 粒度 0.075mm (200目筛 余1%)
石膏类 型
抗压强度 /MPa
标准稠 度混水 量/%
α
β
15
8
40
50
5
5
• (2)填料 • 单纯使用α型石膏并不能用于铸型制 作,须加入耐火材料的填料。其主要目的 是减小石膏型的线收缩和裂纹倾向。常用 填料的种类较多,其中以SiO2-Al2O3系材 料应用较广泛。各种填料对石膏型性能的
锆 英 粉
不 裂
石 英 玻 璃 不 裂
300℃ 空冷
700℃ 空冷
碎裂
不 裂
极轻 极 微裂 极轻 轻 或不 微裂 微 裂 裂
轻 微 裂
轻 微 裂
不 裂
表7-4 填料类型对石膏混和料浆体胶凝时间的影响 工业 氧化 铝 9.0 α-半水 锆英 石膏 粉 100% 10.0 8
填 料
初 凝 时 间 终 凝 时 间
• 石膏型铸造的特点:
- 1、下载文档前请自行甄别文档内容的完整性,平台不提供额外的编辑、内容补充、找答案等附加服务。
- 2、"仅部分预览"的文档,不可在线预览部分如存在完整性等问题,可反馈申请退款(可完整预览的文档不适用该条件!)。
- 3、如文档侵犯您的权益,请联系客服反馈,我们会尽快为您处理(人工客服工作时间:9:00-18:30)。
图 1 石膏型精密铸造工艺过程
它是将熔模组装,并固定在专供灌浆用的砂箱平板上,在真空下把石膏浆料灌入,待浆料凝 结后经干燥即可脱除熔模,再经烘干、焙烧成为石膏型,在真空下浇注获得铸件。
7.1.2 工艺特点
1. 石膏浆料的流动性很好,又在真空下灌注成型,其充型性优良,复模性优异,型精确、光 洁。该工艺不像一般熔模精密铸造受到涂挂工艺的限制,可灌注大型复杂铸件用型。
3.2-3.4 3.95-4.02
5.73 4.7-4.9
12.5X10-6 0.5 X10-6 3.1-4.3 X10-6 5.3 X10-6
5.0 X10-6 8.4 X10-6 7.2-10 X10-6 5.1 X10-6
加入填料后石膏混合料强度 (Mpa)
7h 烘干 90℃,4h 焙烧 700℃,1h
取出母模(不可敲动),起模后应立即进行点火喷烧,否则易产生裂纹。 (五)喷烧 起模后应立刻点火并吹压缩空气进行喷烧,而使陶瓷型的表面有一定的强度和硬度。 (六)焙烧 焙烧的目的是使陶瓷型内残存的乙醇、水分和少量的有机物烧去,并使陶瓷层的强度增加。 全部由陶瓷浆料灌制的陶瓷型,焙烧温度可高达 800oC,焙烧时间 2~3h,出炉温度应在 2500C
2. 石膏型的热导率很低,充型时合金液流动保持时间长,适宜生产薄壁复杂件。但铸型激冷 作用差,当铸件壁厚差异大时,厚大处容易出现缩松、缩孔等缺陷。
3. 石膏型透气性极差,铸件易形成气孔、浇不足等缺陷,应注意合理设置浇注及排气系统。
7.2.3 应用范围
石膏型精密铸造适于生产尺寸精确,表面光洁的精密铸件,特别适宜生产大型复杂薄壁铝合 金铸件,也可用于锌、铜、金、银等合金铸件。铸件最大尺寸达 1000×2000mm、重量 0.03~908kg,
7.3 石膏型精铸工艺
7.3.1 模样
石膏型精密铸造用的模样主要是熔模,也可使用气化模、水溶性模(芯)。 1. 熔模模料 对一般中小型铸件也可使用熔模铸造通用模料,而大中型复杂铸件、尺寸精度和表面粗糙度 要求高的件则应使用石膏型精铸专用模料。 2. 水溶性模(芯)料
制作复杂内腔,无法用金属芯形成时,就得使用水溶芯或水溶石膏芯来形成内腔。常用的水 溶性模料有尿素模料、无机盐模料、羰芯等。
4.真空灌浆 为提高浆料的充填能力,应在真空条件下灌浆。 5.熔模脱除和石膏型烘干 6. 石膏型焙烧 石膏型焙烧的主要目的是去除残留于石膏型中的模料、结晶水以及其它发气物,同时完成石 膏型中一些组成物的相变过程,使其体积稳定。常见的焙烧工艺见图 3。焙烧炉可用天然气炉、 电阻炉。
图 3 石膏型焙烧工艺
后
后
0.5
1.3
0.2
1.5
2.8
2.3
3.4
2.4
3.8
2.6
4.6
2.0
3.5
0.65 0.80 0.86 0.85 0.65
石膏:填料(W/W) 40:60
3. 添加剂 为提高石膏型焙烧后强度、改变石膏型凝结时间和清理性,改变其线膨胀率等需在石膏浆料 中加人添加物。
7.3.3 石膏浆料
石膏浆料的配比及制备对石膏型及铸件质量影响很大,为此应严格加以控制。
1 ~40
3 30
35
35
45
4
40
60
55
5 35
55
40
6 30
70
38
7 65
28
5
2
若干
8 42
50
7.5
0.5
54
2. 石膏浆料的制备设备简图见图 2,操作要点见表 4。
图 2 浆料制备设备简图 1-电动机 2 一动密封装置 3 一搅拌室 4-搅拌浆叶 5-二通阀 6-灌浆室 7-真空表
表 4 石膏浆料的制备和操作要点
工序名称 加料
真空搅拌 备注
操作要点 在浆料搅拌器中现加入适量水,再边搅拌边加份料 待份料加完后,立即合上搅拌器顶盖抽真空,并继续搅拌.真空度再 30s 达到 规定值 0.05~0.06MPa,搅拌时间 2~3min,搅拌机转速 250~350r/min. 石膏浆料的初凝时间一般为 5~75min,搅拌必须在初凝前结束,开始灌注.
加工面最大尺寸 100
100~300 300~500
加工余量 0.8 1.0 1.5
3)收缩率 熔模收缩率 0.4~0.6%、石膏型脱水收缩率 0~0.5%、当金属收缩率 1.1~1.3%时, 综合线收缩率 1.5~2.0%。
7.2.2 浇注系统及冒口设计
1. 石膏型精密铸造的浇冒系统应满足下列要求: (1)有良好的排气能力,能顺利排出型腔中气体,在顶部和易憋气处要开设出气口。 (2)要保证合金液在型腔中流动平稳,顺利充满型胶,避免出现涡流,卷气现象。 (3)合理设置冒口,保证补缩。 (4)脱模时浇注系统应先蒋先,减小熔模对石膏型的膨胀力。 (5)浇注系统在铸件凝固过程中应尽可能不阻碍铸件收缩,以防止件变形和开裂。 2. 浇注系统类型选择 一般浇注系统可分顶注、中间注、底注和阶梯注几种。对高度大的薄壁筒形、箱形件也可用 缝隙式或阶梯式浇注系统。对某些铸件亦可采用平注和斜注。 3. 内浇口位置选择 石膏型表面硬度不够高、热导率小,因此内浇口一般不应直对型壁和型芯,防止冲刷型壁和 型芯,而应沿着型壁和型芯设内浇口。对复杂的薄壁件为防止件变形及裂纹,内浇口应均匀分布, 避免局部过热及浇不足缺陷。内浇口应尽可能设在铸件热节处,利于补缩。
8.1 概述
低压铸造是便液体金属在压力作用下充填型腔,以形成铸件的一种方法。由于所用的压力较 低,所以叫做低压铸造。其工艺过程(见图 1)是:在密封的坩埚(或密封罐)中,通入干燥的 压缩空气,金属液 2 在气体压力的作用下,沿升液管 4 上升,通过浇口 5 平稳地进入型腔 8,并 保持坩埚内液面上的气体压力,一直到铸件完全凝固为止。然后解除液面上的气体压力,使开液 管中未凝固的金属液流坩埚,再由气缸 12 开型并推出铸件。
1. 生产中常用的几种石膏浆科的成分配比见表 3。
表 3 几种石膏浆料成分配比(质量分数,%)
序号
半水石膏 硅石粉 硅砂 高岭土 石英玻 滑石
α型
β型
200/300 70/140 基料
璃
200/300 200/300
粉
硅藻土
水泥
添加剂 水 (外加) (外加)
1 30
70
1 ~50
2 30
50 20
以下,以防止产生裂纹。 带有水玻璃套的陶瓷型,焙烧温度(烘干)在 350~550oC。 (七)浇注与清理 陶瓷型浇注时定要注意挡渣。浇注温度与浇注速度可比同类型的砂型铸件稍高。陶瓷型铸件
最好待冷却至室温时再打箱,这样可1 概述
7.1.1 工艺过程
石膏型精密铸造是用世纪 70 年代发展起来的一种精密铸造新技术其工艺过程见图 1。
3. 模样制作 熔模压制工艺同熔模铸造。一般水溶尿素模料、无机盐模料及水溶石膏芯都是灌注成形的。 水溶性陶瓷芯一般是将各组分先混制成可塑配料,再加压成型,经 700℃左右烧结后待用。
7.3.2 石膏浆料的原材料
1. 石膏 天然石膏为CaSO4·2H20,又称二水石膏。二水石膏有七种变体。α型半水石膏做石膏型更为合 适。除石膏种类外,影响石膏强度的因素还有石膏的细度、水固比、水温、搅拌时间等。 2. 填料 为使石膏型具有良好的强度,减小其收缩和裂纹倾向,需要在石膏中加入填料。填料应有合 适的熔点、耐火度,良好的化学稳定性、合适的线膨胀率、发气量少,吸湿性小等性能,常用作 填料的材料及其性能见表 2。
表 2 石膏型用填料及性能
名称
熔点 (℃)
密度 (g/cm3)
线膨胀系数 (1/ ℃)
硅砂 石英玻璃 硅线石 莫来石 煤矸石 铝矾土
刚玉 氧化锆
锆英 滑石粉 波特兰水泥
石棉 无碱玻璃纤
维
1713 1700-1800
1800 1810
≈1800 2045 2690 2430
2.65 2.1-2.2
3.25 3.08-3.15
壁厚 0.8~1.5mm(局部 0.5mm)。石膏型精密铸造己被广泛应用于航空、宇航、兵器、电子、 船舶、仪器、计算机等行业的零件制造上。
7.2 石膏型精密铸件工艺设计
7.2.1 石膏型精密铸件工艺参数选择
1) 造斜度 同熔模铸造。 2) 加工余量(表 1)。
表 1 石膏型精密铸件的加工余量(mm)