空心转轴结构的优化设计
某型号空心传动轴的优化设计.doc
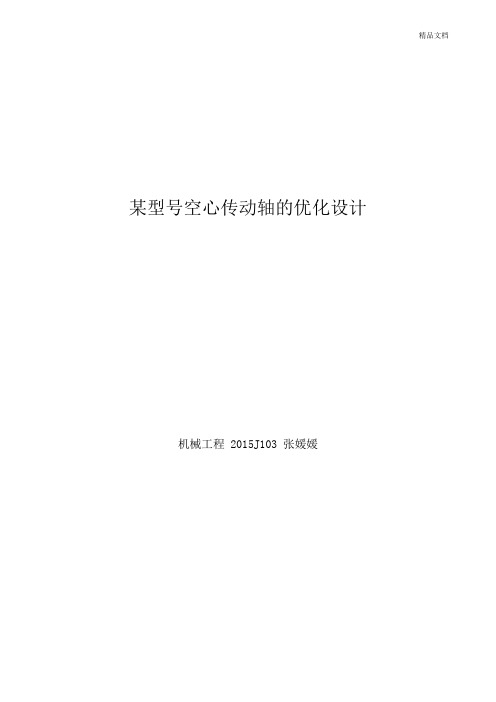
某型号空心传动轴的优化设计机械工程 2015J103 张媛媛欲设计如图1-1所示的某型号空心传动轴 ,其中D 和d 分别为空心轴的外径和内径 ,轴长L=4m 。
轴的材料密度ρ=7.8×10³kg/m ³ ,剪切弹性模量G=80GPa ,许用剪切成功[r]=40MPa ,单位长度许用扭转角[Ø]=1°/m ,轴索传递的功率P=5.5kW ,转速n=200r/min 。
在满足许用条件和结构尺寸限制条件的前提下对该空心轴进行优化 ,使该轴的质量最小。
一、确定工作变量图1-1所示传动轴的力学模型是一个受扭转的圆柱桶轴。
其外径D 和内径d 是决定圆轴的重要独立参数 ,故可作为设计变量 ,将其写成向量形式:X=[x 1 ,x 2 ]T =[D,d]T (1-1)二、简历目标函数若取质量最小为优化目标 ,则目标函数空心圆轴的质量可按下式计算: M=4πρL (D ²-d ²)(kg ) (1-2) L可见 ,这是一个合理选择D 和d 而使质量M 最小的优化问题。
注意:再设计时要确定目标变量的单位。
在确定目标函数和约束条件时 ,应保持它们单位的一致 ,即D 、L 的单位为毫米(mm ) ,质量M 的单位为千克(kg )。
三、上述设计应满足的使用条件和结构尺寸限制如下:(1)扭转强度、根据扭转强度 ,要求扭转剪应力需满足τmax =tW T ≤[τ] (1-3) 式中 ,T 为圆轴所受扭转 ,T=n 9549P (N •m );W t 为抗扭截面模量 ,W t=D D 16d -44)π((MPa)。
(2)扭转刚度 ,为了确保传动轴正常工作 ,除满足扭转强度条件外 ,还要限制轴的变形 ,限制即为刚度条件 ,通常要求单位长度的最大扭转度扭转角不超过规定的许用值 ,即Ø=pGI T ≤[Ø] (1-4) 式中 ,Ø为单位长度扭转角(rad );G 为剪切模量(MPa);I p 为极惯性矩(m 4)。
空心传动轴非概率可靠性优化设计
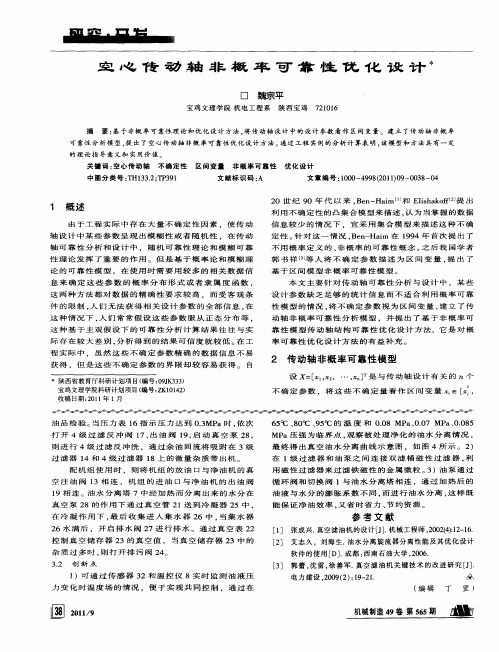
控 制 真 空 储 存 器 2 的 真 空 值 , 当 真 空 储 存 器 2 中 的 3 3
杂 质 过多 时 , 打 开排 污 阀 2 。 则 4
3. 2 创 新 点
1 )可 通 过 传 感 器 3 2和 温 控 仪 8实 时 监 测 油 液 压
可靠性分析模 型, 出了空心传动轴非概 率可靠性优化设计 方法。 提 通过工程 实例的分析计算表明 , 该模型和方法具有一定
的理 论 指 导意 义和 实 用价 值 。
关键词 : 心传动轴 空
不确 定 性
区 间变 量
非概率可靠性
优 化 设计
中 图分 类号 :H132T 3 1 T 3 .;P 9
力 变 化 时 温 度 场 的 情 况 ,便 于 实 现 共 同 控 制 。通 过 在
( 辑 丁 罡 ) 编
21 / 0 19
] 、 分别是区间变量的上界和下界) ( : 。令 :
对 传 动 轴 来 说 , 忽 略 弯 矩 的 影 响 , 动 轴 主 要 承 若 传
受 扭 矩 的 作 用 , 其 承 受 的 扭 矩 为 则 其 横 截 面 上 的 设 扭 转 剪 应 力 和 传 动 轴 的 扭 转 变 形 I分 别 为 : S ]
息 来 确 定 这 些 参数 的概 率 分 布 形 式或 者 隶 属 度 函数 , 这 两 种 方 法 都 对 数 据 的 精 确 性 要 求 较 高 ,而 受 客 观 条 件 的 限 制 , 们 无 法 获 得 相 关 设 计 参 数 的全 部 信 息 , 人 在
这 种 情况 下 , 们 常 常假 设 这些 参 数服 从正 态 分 布等 , 人 这 种 基 于 主 观 假 设 下 的 可 靠 性 分 析 计 算 结 果 往 往 与 实
改进轴的结构,避免应力集中的方法

改进轴的结构,避免应力集中的方法改进轴的结构,避免应力集中引言在工程设计中,轴是一种常见的机械元件,用于传递动力和旋转运动。
然而,由于受到载荷和运转条件的限制,轴常常出现应力集中的问题,从而导致疲劳寿命降低或甚至发生断裂。
本文将介绍几种改进轴结构的方法,以避免应力集中,提高轴的可靠性。
方法一:圆角处理应力集中往往发生在轴的几何形状发生突变的地方,例如轴的连接部分或孔边缘。
通过在这些突变处加入适当的圆角,可以使应力分布更均匀,从而避免应力集中。
具体操作如下:•在连接部分或孔边缘的边缘处增加一定半径的圆角。
•圆角的半径应根据轴的材料和运转条件进行合理选择。
方法二:减小直径变化直径变化也是引起应力集中的重要原因之一。
为了减小直径的突变,可以采取以下措施:•在直径变化的区域添加渐进型的过渡段,使直径变化更加平滑。
•使用渐变直径的轴,如锥形轴,以减小直径的突变程度。
方法三:优化轴的材料和工艺合理选择轴的材料和制造工艺对于避免应力集中也具有重要意义。
以下是几种常用的优化方法:•选择具有较好机械性能和耐疲劳性能的材料,如高强度合金钢或不锈钢。
•通过热处理等方式改善轴的材料性能。
•精确控制轴的制造工艺,确保其尺寸和形状的精度。
方法四:采用填充材料填充材料是一种常用的改进轴结构的方法,可以有效减轻应力集中。
以下是两种常见的填充材料技术:•炉渣填充:在轴内部注入炉渣等材料,使轴的内部空洞被填满,减少应力集中。
•纤维增强填充:在轴的周围包覆纤维增强材料,增强轴的抗拉强度,提高轴的可靠性。
方法五:采用轴套轴套是另一种常用的改进轴结构的方法,它可以在轴与其他零件之间起到缓冲和分散应力的作用。
以下是两种常见的轴套技术:•滑动套:在轴上加装一个滑动套,使轴与其他零件之间形成缓冲层,减少应力集中。
•耐磨套:在轴的表面覆盖一层耐磨材料,防止轴与其他零件直接接触,减少应力集中。
结论通过采用上述改进轴结构的方法,可以有效避免应力集中,提高轴的可靠性和使用寿命。
空心轴的动态特性分析与优化设计

空心轴的动态特性分析与优化设计空心轴是一种轴类零件,具有较小的重量和惯性矩,广泛应用于机械和工程设计中。
它的独特结构使得其动态特性受到一系列因素的影响,包括材料选择、几何形状以及制造工艺等。
本文将从多个角度对空心轴的动态特性进行分析与优化设计。
首先,材料选择是影响空心轴动态特性的重要因素之一。
常见的轴材料包括碳素钢、合金钢和铝合金等。
碳素钢具有优良的机械性能和较高的抗腐蚀能力,适用于一般工程应用。
合金钢由于添加了合适的合金元素,具有更高的强度和硬度,适用于承受较大载荷的工作条件。
铝合金轴由于其较低的密度和耐腐蚀性能,适用于体积和质量要求较小的应用场景。
因此,在设计空心轴时,应根据具体的工作条件选择合适的材料,以达到最佳的动态特性。
其次,空心轴的几何形状也对其动态特性有重要影响。
一般而言,较大的直径和较小的长度可以提高空心轴的刚度和抗弯强度。
此外,几何形状的对称性对空心轴的动态特性也有一定影响。
如果轴的几何形状不对称,可能会导致轴在运动中产生不平衡力矩,从而影响工作效率和稳定性。
因此,在设计空心轴时,应尽量保持几何形状的对称性,以确保良好的动态特性。
除了材料选择和几何形状,制造工艺也是影响空心轴动态特性的重要因素之一。
例如,热处理可以通过改变材料的晶体结构和硬度来提高轴的强度和耐用性。
此外,精密加工和表面处理可以改善轴的表面光洁度和尺寸精度,从而减小摩擦阻力和振动噪声。
因此,在制造空心轴时,应选择适当的制造工艺,以提高其动态特性。
针对以上因素,空心轴的优化设计可以从多个方面入手。
首先,可以通过材料选择和几何形状的优化来改善轴的刚度和抗弯能力。
例如,可以选择高强度的合金钢材料,并根据实际工作条件调整轴的直径和长度。
其次,可以通过精密制造和表面处理来提高轴的表面质量和尺寸精度。
例如,可以采用CNC加工和研磨工艺,以确保轴的精度和光洁度。
最后,可以借助计算机辅助设计和模拟分析工具对轴的动态特性进行模拟和优化。
空心轴优化设计

l ≥ lmin d ≥0
轴的体积达到最小化,本文取空心轴长度 l 为设计变量。综
D−d ≥0
合上述分析可得优化数学模型为:
■■1.4 小节
X = (x1, x2, x3)T = (D, d ,l)T 综分析上述模型可知,该模型具有 3 个设计变量,5 个
主要分析和阐述了空心传动轴的设计要求、优化设计的 约束条件以及相关数学模型,整理可以得到以下优化设计数
最后得到的结果如下:
空心传动轴的设计既需要传统的设计理念同时需要新的
X = (x1, x2, x3)T = (D, d ,l)T = (178.0648,177.0523 3001.7751)T 最后圆整后的结果为: X = (x1, x2, x3)T = (D, d ,l)T = (179,177,3002)T
运行结果: * * * 空心传动轴实现函数优化设计最优解 * * *
通过优化设计算法计算之后得到的结果一般情况下并
空心传动轴外径 D=178.0648 mm
不是整数,即都是小数,但是该空心传动轴的设计参数一
空心传动轴内径 d=177.0523 mm
般规范为整数,即需要对优化设计到的参数进行圆整处
空心传动轴长度 l=3001.7751 mm
E=2*10^5; tao=60; g(1)=(x(2))^4-(x(1)); g(2)=(16*M*x(1))/(pi*((x(1))^4-(x(2))^4)*0.7*E)((x(1)-x(2))/x(1))^(3/2); ceq=[];
2 相关参数的处理
理。当然在进行数据圆整处理时需要注意顾及目标函数和
空心传动轴设计体积 v=0.0008 m^3
约束条件,有可能在进行圆整处理之后就不再满足约束条件
空心轴类零件加工工艺设计及程序编制

论文题目: 年 级: 院 系: 学生姓名: 指导教师: 年 月空心轴类零件加工工艺设计及程序编制10级机电3班机电学院1231232013年5月摘要空心轴是在轴的中心制一个孔或通孔,它通常是和轴承配合在机架或箱体上以实现传递运动和动力。
空心轴有的内壁光滑,有的有键槽,轴体的外面有阶梯形圆柱。
空心轴不但占用空间体积少,还可减轻设备重量、简化结构。
空心轴零件内部可穿测量电线,压缩空气,加入液压油或润滑油,或者做机器人的手臂等,还可以和其他零件进行配合,螺纹连接等。
虽空心轴有如此多的好处与用处,但空心轴类零件的加工却有它的难处,例如细长轴、内工艺槽、键槽以及有工艺精度等的加工。
所采用的加工设备也根据加工类型的不同而不同,但大多数是用数车加工。
关键词:空心轴;工艺;程序;数控车床AbstractThe hollow shaft is prepared in the center of the axis of an aperture or through hole, which is usually fitted in the rack or cabinet and bearing to transmit motion and power. Some hollow shaft wall is smooth, some keyway stepped cylindrical shaft body outside. Hollow shaft not only take up less space volume, can also reduce the weight of the equipment, and simplify the structure. Inside the hollow shaft wear measurement wire, compressed air, adding hydraulic oil or lubricating oil, or do the robot arm, and other parts with threaded connection. Although there are so many benefits and useful hollow shaft, hollow shaft parts processing it has difficulties, such as slender shaft axis process tank, keyways, and process precision machining. The processing equipment used is also different depending on the type of machining, but most are processed with several vehicles. Keywords:Hollow shaft; process; program; CNC lathe;目录绪论 (1)第1章空心轴类零件的加工 (2)1.1空心轴类零件的公用与结构特点 (2)1.2空心轴类零件加工的技术要求 (2)1.3空心轴类零件加工的主要困难及措施 (2)1.4空心轴类零件的材料、毛坯以及热处理 (3)1.5空心轴类零件的加工工艺分析 (4)第2章空心轴类零件的程序编制 (5)2.1数控编程的概念 (5)2.2手编数控程序的特点与步骤 (6)2.3数控车编程如何确定加工方案 (7)第3章空心轴实例数控加工简单分析 (8)3.1实例加工工艺简单分析 (9)3.2 基本数控车的程序编制 (12)参考文献 (14)Deep hole in the machine tool spindle and DF Introduction (15)绪论国内空心长轴深孔的长径比很大,由于其刀具系统自身的刚性差,在切削过程中极易产生让刀变形和机械振动,不仅制约了生产效率的提高,造成零件内孔中心线偏移,也直接导致加工表面质量的下降。
转轴结构设计案例

转轴结构设计案例转轴结构是一种常见的机械结构,广泛应用于重型机械设备和工程项目中。
它通过合理设计转轴的结构和选用合适的材料,能够承受较大的载荷并且保持稳定运行。
本文将通过介绍一个转轴结构设计的实际案例,来探讨该结构的设计原理和优势。
案例背景某公司生产的重型机械设备需要设计一种用于承载旋转部件的转轴结构。
该结构需要能够承受大转矩和重力,并且能够保持稳定运行,同时要求具备一定的耐磨性和使用寿命。
设计师们面临着一系列挑战,如何保证结构的强度、稳定性和耐久性是他们需要解决的问题。
设计原理在实际的转轴结构设计中,需要考虑几个重要的因素来保证其性能。
首先是材料的选择,需要选用高强度、高耐磨的材料,如合金钢或特殊合金。
其次是转轴的结构设计,需要保证其刚度和强度。
一般来说,转轴结构包括轴心、轴颈和轴承,它们之间的连接采用螺纹连接或焊接。
另外,转轴结构还需要考虑承载部件的类型和质量。
在本案例中,由于旋转部件较重,设计师选择了双向支撑的结构,即在转轴两端设置了对称的支撑点。
这样一来,能够有效分担转轴承载的压力,提高结构的稳定性。
优势与应用转轴结构设计的优势在于能够承受大转矩和重力,并且保持稳定运行。
通过合理的结构设计和材料选择,转轴可以具备较高的强度和刚度,延长使用寿命,并且减小故障率。
这种结构广泛应用于重型机械设备、工程设备以及汽车行业。
例如,工程机械中的挖掘机、装载机等都采用了转轴结构来保证设备的正常运转。
值得一提的是,设计师还可以根据不同应用场景的需求,对转轴结构进行定制化设计。
例如,在某些特殊环境下需要转轴具备防腐蚀或耐高温等特性,设计师可以选择合适的材料和涂层来满足这些需求。
因此,转轴结构的设计具有一定的灵活性和可塑性。
结论通过对转轴结构设计案例的介绍,我们了解到合理的转轴结构设计是保证机械设备正常运转的关键。
设计师们需要根据实际需求选择合适的材料和结构,确保转轴具备足够的强度和稳定性。
转轴结构在重型机械设备和工程项目中的应用非常广泛,它的优势在于能够承受大转矩和重力,并保持稳定运行。
空心传动轴优化设计
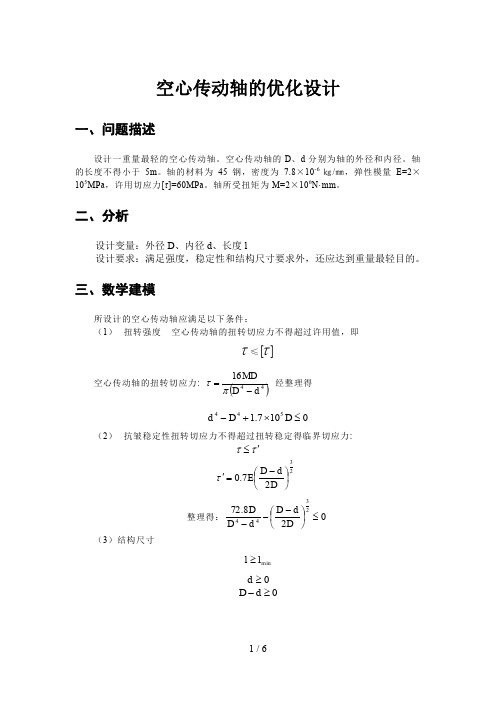
空心传动轴的优化设计一、问题描述设计一重量最轻的空心传动轴。
空心传动轴的D 、d 分别为轴的外径和内径。
轴的长度不得小于5m 。
轴的材料为45钢,密度为7.8×10-6㎏/㎜,弹性模量E=2×105MPa ,许用切应力[τ]=60MPa 。
轴所受扭矩为M=2×106N·mm 。
二、分析设计变量:外径D 、内径d 、长度l设计要求:满足强度,稳定性和结构尺寸要求外,还应达到重量最轻目的。
三、数学建模所设计的空心传动轴应满足以下条件:(1) 扭转强度 空心传动轴的扭转切应力不得超过许用值,即τ≤[]τ空心传动轴的扭转切应力: ()4416dD MD-=πτ 经整理得 0107.1544≤⨯+-D D d(2) 抗皱稳定性扭转切应力不得超过扭转稳定得临界切应力:ττ'≤2327.0⎪⎭⎫⎝⎛-='D d D E τ 整理得:028.722344≤⎪⎭⎫⎝⎛---D d D d D D(3)结构尺寸min l l ≥0≥d 0≥-d D⎥⎥⎥⎦⎤⎢⎢⎢⎣⎡=⎥⎥⎥⎦⎤⎢⎢⎢⎣⎡=l d D x x x X 321 则目标函数为:()()[]()3222166221012.61012.6min x x x d D l x f -⨯=⨯-=-- 约束条件为:0107.1107.1)(1541425441≤⨯+-=⨯+-=x x x D D d X g08.728.72)(2/3121424112/3442≤⎪⎪⎭⎫⎝⎛---=⎪⎭⎫⎝⎛---=X xx x x x x D d D d D D g055)(33≤-=-=x l X g0)(24≤-==x d X g 0)(215<+-=-=x x d D X g四、优化方法、编程及结果分析1优化方法综合上述分析可得优化数学模型为:()Tx x x X 321,,=;)(min x f ;()0..≤x g t s i 。
空心轴的原理和应用

空心轴的原理和应用一、空心轴的定义和特点空心轴是指在自转过程中,轴心内部是空心的一种轴结构。
与实心轴相比,空心轴具有以下特点: 1. 重量轻:由于轴心内部为空心,相同尺寸的空心轴和实心轴相比,空心轴重量更轻。
2. 节约材料:空心轴在制造过程中,材料利用率更高,对资源的消耗更少。
3. 强度高:空心轴通过合理的设计和加工工艺,具有较高的强度和刚性。
二、空心轴的原理空心轴的原理主要依靠材料的结构和力学性能。
1. 采用合适的材料:空心轴通常采用高强度、低密度的金属材料,如铝合金等。
这种材料具有较好的力学性能,可以满足轴的强度和刚性要求。
2. 合理的轴壁厚度:在设计空心轴时,需要根据实际载荷和使用环境确定轴壁的厚度。
过大或过小的轴壁厚度都会对轴的工作性能产生不利影响,需要通过合理的计算和试验确定最佳参数。
3. 优化的内部结构:空心轴的内部结构可以通过优化设计来提高轴的强度和刚性。
通过增加腹板、加强筋等方法,可以提高空心轴的承载能力和抗弯性能。
三、空心轴的应用空心轴由于其重量轻、材料节约、强度高等特点,在各个领域得到了广泛的应用。
1. 机械工程领域在机械工程领域,空心轴被广泛应用于各种机械装置和传动系统中。
例如: -汽车发动机:空心轴可以用作曲轴和凸轮轴等关键部件,在减轻整车重量的同时提高传动效率。
- 工业机械:空心轴可以用于传动装置、输送设备等,实现轻量化和高效率的要求。
2. 航空航天领域在航空航天领域,空心轴的应用尤为重要。
由于飞机和航天器对重量和空间的限制较高,使用空心轴可以显著提高载荷能力和燃油效率。
例如: - 飞机发动机:使用空心轴可以减轻发动机重量,提高飞机性能。
- 航天器:空心轴可以用于航天器的导轨、控制面等关键部件,提高航天器的灵活性和稳定性。
3. 体育器材领域在体育器材领域,空心轴也具有广泛的应用。
例如: - 高尔夫球杆:采用空心轴可以实现球杆的轻量化,提高球杆的控制性能。
- 自行车:在自行车的轴部件中,采用空心轴可以减轻整车重量,提高车辆的操控性和节能性。
空心车轴结构设计及工艺

空心车轴结构设计及工艺西南交通大学机车车辆研究所 黄志辉1 引言车轴是所有机车车辆零部件中最重要的零件之一,其质量好坏直接影响行车安全。
高速动力车运行速度快,国家下达的设计任务规定:最高运行速度250 km/h,试验速度280 km/h,为减轻轮轨之间的动作用力,要尽量减轻车轴质量,尤其是簧下质量。
在充分考虑我国目前的制造水平及工艺措施的条件下,对所有零部件的细小结构都作了减小质量的考虑。
车轴属簧下质量,必须考虑减轻质量,为此,将车轴设计成空心车轴。
车轴与车轮的应力一样,每转一周,应力将循环一次,随着运行速度提高,循环频率加快,易发生疲劳,设计时应保证车轴有足够的安全裕度,即有足够的疲劳寿命。
这要通过精心设计并采取相应的工艺措施来保证。
2 空心车轴结构设计大量实践经验及试验结果表明,车轴的结构设计与其疲劳寿命有着非常密切的关系,因而对车轴的结构设计必须给予仔细分析与研究。
2.1 空心车轴轴身内、外径的确定在保证车轴所受的最大应力不变的条件下,空心车轴轴身外径越大,内孔直径越大,则减轻质量的效果越好。
但为了减小轮轨动作用力,高速动力车采用双空心轴驱动,在此情况下,为避免内外空心轴及车轴在运动过程中相互干涉,其间必须留有足够的间隙,因此,车轴轴身外径的选择受到空间的限制。
经综合考虑,轴身外径定为 183 mm,见图1。
确定车轴内孔直径,首先要保证有足够的强度,其次是减轻质量,两者需协调;同时,车轴内孔直径不仅影响车轴的强度和应力分布,还影响轮轴的过盈量及压装工艺。
图1空心车轴局部结构图1.轴身2.轮座3.过渡圆弧4.轴颈5.内孔车轴主要承受弯、扭两种载荷,可从车轴的最大弯曲和扭应力来分析其强度。
车轴受弯和受扭的分析相同,得到的结论也一致,因此,仅分析车轴受弯的情况。
设截面模量为W (m3),车轴内、外径分别为d (m)、D (m),车轴的最大弯矩为M (N*m),则车轴的最大应力为σmax=M/W,单位为 (Pa)。
空心轴的优化设计方案

空心轴的优化设计方案
作者:郑光超
来源:《现代商贸工业》2011年第07期
摘要:介绍了机械传动中空心轴在满足强度和刚度的条件下,以质量最小为目标进行优化设计的理论方法;避免了传统计算方法“安全”与“降耗”的矛盾给设计者带来的困惑。
关键词:空心轴、优化设计、安全降耗
中图分类号:TB
文献标识码:A
文章编号:1672-3198(2011)07-0283-01
1 引言
在机械制造中,减轻重量,节约材料是设计工作者所要追求的一个目标,对于某些轴类的其它受力与其所受的扭矩相比较可以忽略的情形,从减轻重量节约材料的角度考虑,将其设计成空心是相当必要的。
这是因为横截面上的剪应力沿半径按线性规律分布,圆心附近的应力很小,材料没有充分发挥作用。
虽然这一理论早被人们所熟悉,并且得到广泛的应用,尤其是在飞机、轮船、汽车等运输机器的某些传动轴更多地采用空心轴以减轻重量。
但是按照传统的设计方法,是不可能使传动轴在满足强度和刚度条件下使其质量最小的。
随着计算机及计算软件的发展,使手工难以计算的高次方程通过计算机求解成为可能。
本设计计算方法正是在这样的背景条件下提拟出来的。
2 按满足强度要求推导最小质量方程式
5 结论
本优化设计方案是基于微型计算机及设计计算软件的普及而提出来的,是基于正确的理论推导出来的设计方法,因而其正确性毋庸置疑。
对于大型机械设计而言,不失是一种高效、安全、降耗的设计参考方法。
参考文献
[1]刘鸿文.材料力学(上册)[M].北京:高等教学出版社,1992. 注:“本文中所涉及到的图表、公式、注解等请以PDF格式阅读”。
高速动车组轴承的空心轴疲劳寿命分析与优化
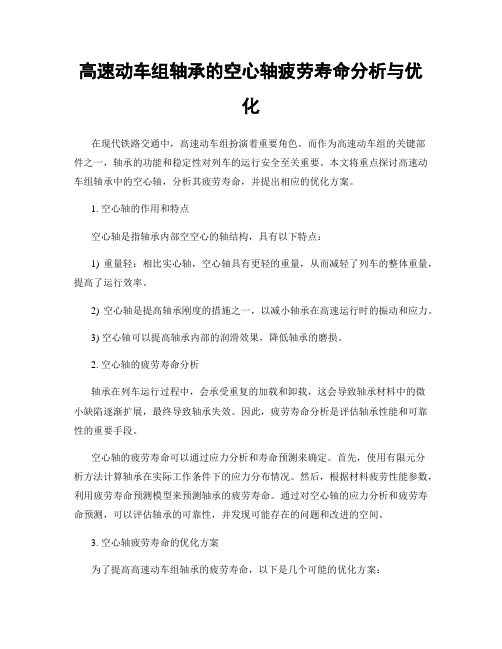
高速动车组轴承的空心轴疲劳寿命分析与优化在现代铁路交通中,高速动车组扮演着重要角色。
而作为高速动车组的关键部件之一,轴承的功能和稳定性对列车的运行安全至关重要。
本文将重点探讨高速动车组轴承中的空心轴,分析其疲劳寿命,并提出相应的优化方案。
1. 空心轴的作用和特点空心轴是指轴承内部空空心的轴结构,具有以下特点:1) 重量轻:相比实心轴,空心轴具有更轻的重量,从而减轻了列车的整体重量,提高了运行效率。
2) 空心轴是提高轴承刚度的措施之一,以减小轴承在高速运行时的振动和应力。
3) 空心轴可以提高轴承内部的润滑效果,降低轴承的磨损。
2. 空心轴的疲劳寿命分析轴承在列车运行过程中,会承受重复的加载和卸载,这会导致轴承材料中的微小缺陷逐渐扩展,最终导致轴承失效。
因此,疲劳寿命分析是评估轴承性能和可靠性的重要手段。
空心轴的疲劳寿命可以通过应力分析和寿命预测来确定。
首先,使用有限元分析方法计算轴承在实际工作条件下的应力分布情况。
然后,根据材料疲劳性能参数,利用疲劳寿命预测模型来预测轴承的疲劳寿命。
通过对空心轴的应力分析和疲劳寿命预测,可以评估轴承的可靠性,并发现可能存在的问题和改进的空间。
3. 空心轴疲劳寿命的优化方案为了提高高速动车组轴承的疲劳寿命,以下是几个可能的优化方案:1) 材料优化:选择更高强度、更耐疲劳的材料来制造空心轴,以提高轴承的疲劳寿命。
2) 结构优化:通过优化轴承的结构,例如增加支撑结构或增加填充物来减少轴承的应力集中,从而延长疲劳寿命。
3) 润滑优化:优化轴承的润滑方式和润滑剂,使轴承能够在高速运行过程中始终保持良好的润滑状态,减少轴承的磨损和摩擦,延长疲劳寿命。
4) 加工优化:改进轴承的加工工艺和精度控制,以减少轴承表面的不均匀应力和缺陷,提高轴承的使用寿命。
4. 空心轴疲劳寿命优化的挑战和前景虽然空心轴疲劳寿命的优化可以提高高速动车组轴承的性能和可靠性,但也存在一些挑战。
例如,材料的选择和加工、结构的优化和润滑系统的改进等方面都需要全面考虑。
多层空心轴的应力分析与优化设计

多层空心轴的应力分析与优化设计轴是一种常见的机械元件,广泛应用于各种机械设备中。
多层空心轴是一种特殊结构的轴,具有较高的强度和刚度。
本文将对多层空心轴进行应力分析与优化设计,以提高其性能。
1. 引言多层空心轴是由多个空心圆柱体组成的,其中心镶嵌着一个实心轴心。
由于其结构独特,相比于传统的实心轴,多层空心轴在减轻重量的同时也提高了刚度。
然而,在高负荷工况下,多层空心轴的应力集中问题和材料的选择成为研究的关键。
2. 多层空心轴的应力分析多层空心轴的应力分析是研究其性能的重要一步。
首先,通过有限元分析软件对多层空心轴进行模拟,得到其在不同工况下的应力分布情况。
然后,根据应力分布图,对应力集中的部分进行深入研究。
2.1 应力集中的原因分析多层空心轴的应力集中主要是由于轴心的结构造成的。
由于轴心为实心,在受到载荷时,与其相连的各层环形空心圆柱体无法完全实现力的传递,导致应力集中。
这种应力集中现象对轴的强度和耐久性造成较大影响。
2.2 应力集中的改善措施针对多层空心轴的应力集中问题,可以采取以下改善措施:2.2.1 增加轴心直径通过增加轴心直径,可以提高力的传递效果,减少应力集中。
但同时也会增加轴的重量和成本,需要综合考虑。
2.2.2 修改轴心形状通过修改轴心的形状,如采用圆柱锥形结构,可以减小应力集中现象。
这种方法能够在一定程度上提高多层空心轴的性能。
3. 多层空心轴的优化设计在进行应力分析的基础上,可以通过优化设计来提高多层空心轴的性能。
优化设计的目标是在满足强度要求的前提下,尽可能减小轴的重量。
3.1 材料的选择在多层空心轴的优化设计中,选择合适的材料是非常重要的。
需要考虑的因素包括材料的强度、刚度、耐磨性等。
同时,还需综合考虑材料的成本和可加工性。
3.2 结构的优化通过结构的优化,可以改善多层空心轴在应力集中区域的受载情况。
例如,通过适当调整空心圆柱体的厚度和直径,可以有效减小应力集中,提高轴的强度。
空心轴的实施步骤和方法
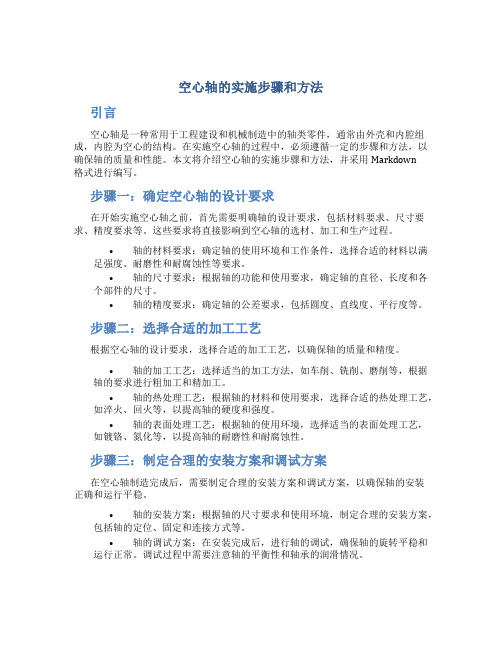
空心轴的实施步骤和方法引言空心轴是一种常用于工程建设和机械制造中的轴类零件,通常由外壳和内腔组成,内腔为空心的结构。
在实施空心轴的过程中,必须遵循一定的步骤和方法,以确保轴的质量和性能。
本文将介绍空心轴的实施步骤和方法,并采用Markdown格式进行编写。
步骤一:确定空心轴的设计要求在开始实施空心轴之前,首先需要明确轴的设计要求,包括材料要求、尺寸要求、精度要求等。
这些要求将直接影响到空心轴的选材、加工和生产过程。
•轴的材料要求:确定轴的使用环境和工作条件,选择合适的材料以满足强度、耐磨性和耐腐蚀性等要求。
•轴的尺寸要求:根据轴的功能和使用要求,确定轴的直径、长度和各个部件的尺寸。
•轴的精度要求:确定轴的公差要求,包括圆度、直线度、平行度等。
步骤二:选择合适的加工工艺根据空心轴的设计要求,选择合适的加工工艺,以确保轴的质量和精度。
•轴的加工工艺:选择适当的加工方法,如车削、铣削、磨削等,根据轴的要求进行粗加工和精加工。
•轴的热处理工艺:根据轴的材料和使用要求,选择合适的热处理工艺,如淬火、回火等,以提高轴的硬度和强度。
•轴的表面处理工艺:根据轴的使用环境,选择适当的表面处理工艺,如镀铬、氮化等,以提高轴的耐磨性和耐腐蚀性。
步骤三:制定合理的安装方案和调试方案在空心轴制造完成后,需要制定合理的安装方案和调试方案,以确保轴的安装正确和运行平稳。
•轴的安装方案:根据轴的尺寸要求和使用环境,制定合理的安装方案,包括轴的定位、固定和连接方式等。
•轴的调试方案:在安装完成后,进行轴的调试,确保轴的旋转平稳和运行正常。
调试过程中需要注意轴的平衡性和轴承的润滑情况。
步骤四:进行质量检验和性能测试在空心轴实施完成后,需要进行质量检验和性能测试,以确保轴的质量和性能符合设计要求。
•轴的质量检验:检查轴的外观质量,包括表面光洁度、变形和缺陷等;使用测量工具检测轴的尺寸,包括直径、长度和各个部件的公差等。
•轴的性能测试:对轴进行性能测试,包括静态测试和动态测试。
基于matlab煤液钻空心传动轴的优化设计
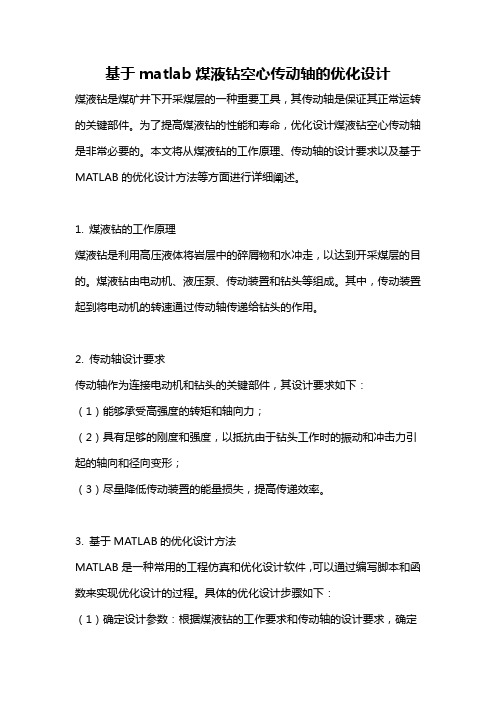
基于matlab煤液钻空心传动轴的优化设计煤液钻是煤矿井下开采煤层的一种重要工具,其传动轴是保证其正常运转的关键部件。
为了提高煤液钻的性能和寿命,优化设计煤液钻空心传动轴是非常必要的。
本文将从煤液钻的工作原理、传动轴的设计要求以及基于MATLAB的优化设计方法等方面进行详细阐述。
1. 煤液钻的工作原理煤液钻是利用高压液体将岩层中的碎屑物和水冲走,以达到开采煤层的目的。
煤液钻由电动机、液压泵、传动装置和钻头等组成。
其中,传动装置起到将电动机的转速通过传动轴传递给钻头的作用。
2. 传动轴设计要求传动轴作为连接电动机和钻头的关键部件,其设计要求如下:(1)能够承受高强度的转矩和轴向力;(2)具有足够的刚度和强度,以抵抗由于钻头工作时的振动和冲击力引起的轴向和径向变形;(3)尽量降低传动装置的能量损失,提高传递效率。
3. 基于MATLAB的优化设计方法MATLAB是一种常用的工程仿真和优化设计软件,可以通过编写脚本和函数来实现优化设计的过程。
具体的优化设计步骤如下:(1)确定设计参数:根据煤液钻的工作要求和传动轴的设计要求,确定设计参数,如轴的直径、材料、长度等。
(2)建立传动轴的有限元模型:根据设计参数和传动轴的几何形状,利用MATLAB中的有限元分析工具建立传动轴的有限元模型。
(3)应用约束条件和目标函数:根据传动轴的设计要求,将约束条件和目标函数转化为MATLAB中的数学表达式。
(4)选择优化算法:根据设计问题的特点和求解要求,选择合适的优化算法,如遗传算法、粒子群算法等。
(5)进行优化设计:利用MATLAB中的优化工具箱,结合选择的优化算法,对传动轴的设计参数进行优化求解,得到最优设计方案。
(6)评估设计方案:根据优化结果,对传动轴的性能和寿命进行评估,如果不满足要求,则返回第(3)步重新进行设计。
(7)制造和测试:根据最优设计方案,制造传动轴,并通过实验测试验证其性能和寿命。
通过以上步骤,我们可以利用MATLAB对煤液钻空心传动轴进行优化设计,提高煤液钻的工作效率和寿命。
空心球面机械零件设计优化研究

空心球面机械零件设计优化研究近年来,随着科技的发展和工业生产的进步,机械零件设计的优化研究变得越来越重要。
其中,空心球面机械零件的设计优化更是备受关注。
本文将探讨空心球面机械零件设计优化的原理、方法以及实际应用。
首先,我们需要了解空心球面机械零件的基本构成和作用。
空心球面机械零件是一种具有空心球面结构的零件,通常被应用于液压系统、汽车引擎等领域。
它的设计考虑了重量、强度和稳定性等方面的要求,以提高零件的整体性能。
在空心球面机械零件的设计优化中,最关键的问题是如何合理地确定零件的空心结构。
一方面,空心结构能够减轻零件本身的重量,提高机械系统的效率;另一方面,空心结构还可以增加零件的强度和稳定性。
因此,我们需要通过合理的工程设计方法,确定最佳的空心结构。
在确定空心结构时,我们可以借助计算机辅助设计软件,通过数值分析和仿真模拟来寻找最佳的设计方案。
通过建立正确的数学模型和相应的参数,我们可以获取零件受力情况、应变分布等重要信息。
基于这些数据,我们可以进行结构优化,寻找最佳的空心形状、尺寸和位置。
除了数值分析和仿真模拟,实验测试也是空心球面机械零件设计优化的重要手段。
通过在实验室中进行力学试验和工程实践,我们可以验证数值分析结果的准确性,并寻找零件设计中可能存在的问题。
通过不断地实验测试和数据对比,我们可以优化设计方案,进一步提高零件的性能和安全性。
需要注意的是,空心球面机械零件设计优化不仅仅关注零件的几何形状和材料选取,还需要考虑到工艺制造的可行性和经济性。
因此,工程师们还需在设计过程中充分考虑到这些因素,并寻找合适的平衡点。
只有在确保产品质量的前提下,我们才能实现设计的优化。
空心球面机械零件的设计优化不仅仅是理论研究,更是实际应用的推广。
随着现代工业生产的快速发展,我们已经看到越来越多的空心球面机械零件应用于各个领域。
通过优化设计,这些零件能够大幅度提高机械系统的性能和效率,为工业生产带来了可观的经济和社会效益。
空心转轴结构的优化设计
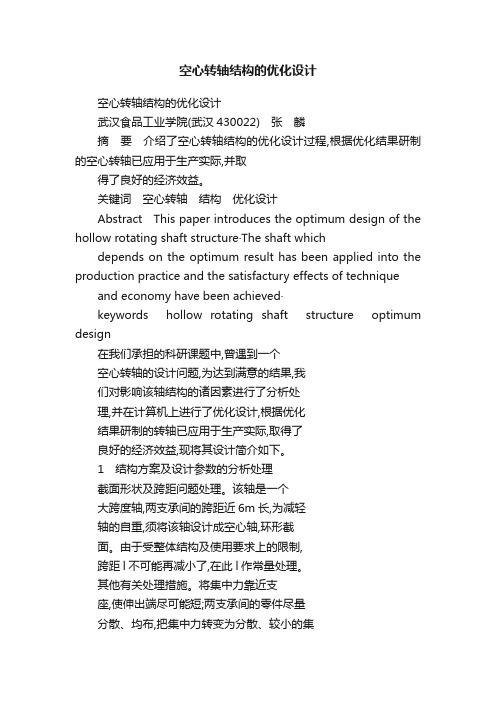
空心转轴结构的优化设计空心转轴结构的优化设计武汉食品工业学院(武汉430022) 张麟摘要介绍了空心转轴结构的优化设计过程,根据优化结果研制的空心转轴已应用于生产实际,并取得了良好的经济效益。
关键词空心转轴结构优化设计Abstract This paper introduces the optimum design of the hollow rotating shaft structure·The shaft whichdepends on the optimum result has been applied into the production practice and the satisfactury effects of technique and economy have been achieved·keywords hollow rotating shaft structure optimum design在我们承担的科研课题中,曾遇到一个空心转轴的设计问题,为达到满意的结果,我们对影响该轴结构的诸因素进行了分析处理,并在计算机上进行了优化设计,根据优化结果研制的转轴已应用于生产实际,取得了良好的经济效益,现将其设计简介如下。
1 结构方案及设计参数的分析处理截面形状及跨距问题处理。
该轴是一个大跨度轴,两支承间的跨距近6m长,为减轻轴的自重,须将该轴设计成空心轴,环形截面。
由于受整体结构及使用要求上的限制,跨距l不可能再减小了,在此l作常量处理。
其他有关处理措施。
将集中力靠近支座,使伸出端尽可能短;两支承间的零件尽量分散、均布,把集中力转变为分散、较小的集中力或均布载荷;避免在危险剖面开槽;增大突变处的过渡圆角半径R,改善轴的受力状况。
优化设计的控制因素。
由于该轴的转速不太高,传递的扭矩也不很大,加上采取了以上措施,用常规方法试算发现,该轴的强度条件较容易满足,而刚度条件却较难满足,即满足刚度要求的结构,强度一般无问题,设计中的主要矛盾是轴的空心段外径D、壁厚δ与刚度的关系,其变化规律如图1所示,a为外径D不变时壁厚δ与挠度f的关系曲线,可见壁太厚,自重增加,刚度情况反而变坏,壁太薄,刚度条件满足不了,扭转稳定性也难保证;b为壁厚δ不变时外径D与挠度f的关系曲线,c为自重变化曲线,可见,外径D越大,刚度越好,但自重、体积也越大,这也必将受到整机结构的限制。
大直径空心轴转子结构设计及机械强度计算.
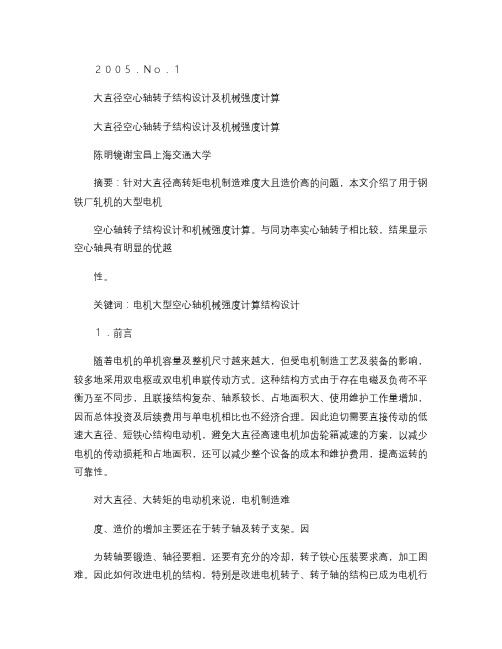
应用变得非常简单,且只须根据机械强度和电机制
造工艺的要求,选用一定厚度、规格、品种的厚钢板滚圆成一定的直径并焊接拼缝即可。这种结构的空
心轴,与同直径的实心轴相比,飞轮转矩小,结构牢
固和强度好,承受重负荷能力强。
根据ZD315/134,4100kW,40/80r/min电机的实际工况,最终确定电机空心轴的本体是由三段两种
现代大型电机的制造均要求转子采用绝缘性能优越、能提高绝缘强度和机械强度、减小吊装、浸漆吨位及尺寸的真空压力整体浸漆工艺。上海电机厂拥有目前亚洲最大的04800mm真空压力整体浸漆罐,但该罐及其附属设备也只能浸漆50吨以下,单体总长
不超过5200mm的电机转子。而ZD315/1344100kW
电机若设计采用实心轴的话,其转子总重量将达80吨,总长为6785rran,为此只能采用空心轴结构。全焊接空心轴因为在浸漆前就已将两端的两段实心轴部分联接在一起,因此加大了转子浸漆的吨位及整体长一10一
长度长且纵向矩形截面受力的圆柱销钉,在空心轴法兰与实心轴结合面处径向打人圆柱销钉。根据设计计算结果传动端侧共有24只M5×100的圆柱销钉,非传动端侧共有8只M5×100的圆柱销钉。
5结论
本文介绍了用于大直径转子电机的空心轴结构及强度计算。大型直流电机的传动轴采用空心轴结构,不仅机械强度好,结构刚度高,而且重量轻,实心轴分段锻造成本低,比整体实心轴结构更有优越性。众所周知,同步电机转子是凸极式结构,空心轴结构
[2]陈明镜.(1963),男,上海交通大学硕士研究生,主要研究直流电
机结构.运行控制和制造工艺等
・信息点滴・
德2004年新装太阳能发电设备容量世界第一
据德国太阳能业联合会公布的最新数据,德国2004年新装置的太阳能发电设备容量首次超过日
高速旋转空心轴的优化设计

高速旋转空心轴的优化设计
闫思江;韩晓玲;闫晗
【期刊名称】《锻压装备与制造技术》
【年(卷),期】2016(051)001
【摘要】基于结构优化处理器OptiStruct,采用有限元法对高速旋转空心轴进行优化设计,在既满足扭转刚度又满足临界转速的约束下,优化出质量最轻的旋转轴几何尺寸.本文给出了具体优化步骤和方法.
【总页数】3页(P104-106)
【作者】闫思江;韩晓玲;闫晗
【作者单位】青岛港湾职业技术学院,山东青岛266404;青岛港湾职业技术学院,山东青岛266404;大庆第二采油厂信息中心,黑龙江大庆163000
【正文语种】中文
【中图分类】TH391.7
【相关文献】
1.空心轴优化设计 [J], 庞春
2.空心轴的优化设计方案 [J], 郑光超
3.空心轴橡胶关节外壁折弯工艺分析及工装优化设计 [J], 蔡鹏飞
4.多层高速旋转过盈配合圆筒的应力分析及径向尺寸优化设计方法研究 [J], 张鹏飞;王志恒;席光
5.窄间隙焊接技术在机车转向架空心轴自动化焊接上的应用研究 [J], 张祥;渠源;张虎
因版权原因,仅展示原文概要,查看原文内容请购买。
- 1、下载文档前请自行甄别文档内容的完整性,平台不提供额外的编辑、内容补充、找答案等附加服务。
- 2、"仅部分预览"的文档,不可在线预览部分如存在完整性等问题,可反馈申请退款(可完整预览的文档不适用该条件!)。
- 3、如文档侵犯您的权益,请联系客服反馈,我们会尽快为您处理(人工客服工作时间:9:00-18:30)。
的主要矛盾是轴的空心段外径D、壁厚δ与
刚度的关系,其变化规律如图1所示,a为外
径D不变时壁厚δ与挠度f的关系曲线,可
见壁太厚,自重增加,刚度情况反而变坏,壁
太薄,刚度条件满足不了,扭转稳定性也难保
证;b为壁厚δ不变时外径D与挠度f的关
系曲线,c为自重变化曲线,可见,外径D越
良好的经济效益,现将其设计简介如下。
1 结构方案及设计参数的分析处理
截面形状及跨距问题处理。该轴是一个
大跨度轴,两支承间的跨距近6m长,为减轻
轴的自重,须将该轴设计成空心轴,环形截
面。由于受整体结构及使用要求上的限制,
跨距l不可能再减小了,在此l作常量处理。
其他有关处理措施。将集中力靠近支
(4)在锅炉的设计计算过程中,可以将曲
线、表格进行拟合,在优化迭代的过程中,通
过引入拟合公式迅速完成迭代进程。
5·2 展望
(1)锅炉受热面优化设计问题是一个影
响经济性和安全性的重要问题。在确保安全
的前提下,采用最优化方法进行设计可以获
得减少传热面积、节省金属耗量、降低受热面
造价的显著经济效果。
业出版社,1990
4 吴宗泽·机械结构设计·北京:机械工业出版社,1995
5 刘鸿文·材料力学·北京:人民教育出版社,1979
·31·机械 1999年 第26卷 第2期
就能产生一系列逐步得到改进的可行设计方
案供挑选。这样,根据经验和分析,或在程序
中增加选取可行初始点的功能,选用几个可
行初始点进行试算,然后,参照无缝钢管型材
规格,从所取得的最优解及几组次优解中选
取一组合适的解,在进行强度校核后,作为实
用方案采用。
该轴优化设计后的重量与按常规设计的
重量比较,只有其重量的1/3(常规设计按一
24πE(x14-x24)-0·00049l≥0
g3(X)=0·0005l-
12PHal2-4FH∑9i=1bi(3l2-4b2i)
3πE(x14-x24)≥0
g4(X)=1-584TE(x14-x24)≥0g5(X)=1-x1Dmax≥0 (下转第31页)
·27·机械 1999年 第26卷 第1期标函数最佳时的优化设计参数。
处理。轴的选材,主要是考虑其机械性能、耐
蚀性能、工艺性能及经济性等。故有,垂直面
最大静挠度fv为
fv=96Pval2-5πγl4(D2-d2)-32Fv∑9i=1bi(3l2+4bi2)24πE(D4-d4)
水平面最大静挠度fH为
fH=
12PHal2-4FH∑9i=1bi(3l2-4bi2)
式中:M(x)、M°(x)———载荷作用下和单位
力偶作用下轴的弯
矩;
L———主轴全长=π/64(D4-d4);
E———材料的弹性模量。
由于在一般工作温度下(<200℃),合金
元素为一般含量范围内的各种不同强度性能
的钢材的E值相差不大,即选用的钢材对轴
的刚度影响不大,因此,E值在这里作常量
座,使伸出端尽可能短;两支承间的零件尽量
分散、均布,把集中力转变为分散、较小的集
中力或均布载荷;避免在危险剖面开槽;增大
突变处的过渡圆角半径R,改善轴的受力状
况。
优化设计的控制因素。由于该轴的转速
不太高,传递的扭矩也不很大,加上采取了以
上措施,用常规方法试算发现,该轴的强度条
件较容易满足,而刚度条件却较难满足,即满
计参数,故定为设计变量
X=[x1,x2]=[D、d]T
图2
(2)目标函数
以轴的质量G作为目标函数,要求愈轻
愈好,则有
G(X)=π4(D2-d2)γl=π4(x12-x22)γl
(3)约束条件
如上所述,可把刚度作为主要约束条件,
即挠度f不超过许用值〔f〕,且扭转角ψ不
超过许用值〔ψ〕。根据有关资料推荐值:〔f〕
depends on the optimum result has been applied into the production practice and the satisfactury effects of technique
and economy have been achieved·
大,刚度越好,但自重、体积也越大,这也必将
受到整机结构的限制。由此可见,本轴优化
设计可以简化为用刚度作为控制因素,并尽
可能地把对结果不很敏感或容易处理的参数
按成熟的经验或实际要求作常量处理,减少
设计变量数,将复杂的问题简化,尽快取得可
靠实用的优化结果。
图1
2 建立优化设计的数学模型
如图2所示,空心轴外径为D,内径为
d,两支承跨距为l,轴的材料密度为γ,Pv、
PH分别为轴端集中力的垂直分力和水平分
力,Fv、FH分别为轴上垂直面、水平面的载
荷,a、bi为间距。
(1)设计变量
空心轴段在保证足够的强度、刚度条件
下,有一个外径D与壁厚δ的最佳组合问
·26·空心转轴结构的优化设计题,即轴的外径D与内径d为需要确定的设
3πE(D4-d4)
最大单位长度扭转角ψ为
ψ=584TE(D4-d4)
式中:T———横截面上的扭矩最大值。
根据试算结果及经验分析,设定设计变
量的边界条件为
Dmin≤D≤Dmax
dmin≤d≤dmax
主轴壁厚太薄时,有可能丧失扭转稳定
性,因而,还要对最小壁厚δmin加以限制
D-d
立一个锅炉的整体优化模型,并进行整体优
化设计,是我们今后面临的一个主要课题。
参考文献
1 冯俊凯,沈幼庭·锅炉原理及计算·北京:科学出版社,
1992
2 张可村·工程优化的算法与分析·西安:西安交通大学
出版社,1988
3 刘振凯·电力变压器优化设计方法的研究及应用·西
安交通大学硕士学位论文,1991
(上接第27页)
g6(X)=x1Dmin-1≥0
g7(X)=x2dmin-1≥0
g8(X)=1-x2dmax≥0
g9(X)=x1-x2-2δmin≥0
(4)数学模型
综上所述,构造该大跨度空心转轴结构
优化设计的数学模型为
minG(X) X∈R2
受约束于
gi(X)≥0 (i=1,2,…9)
=(0·0003~0·0005)l(mm),〔ψ〕=(0·5~
1·0)°/m。按机器工作条件分析,f=
0·0005l时尚可满足使用要求,为使计算结
果更接近全域最优解,对f值又增加约束如
下
0·00049l≤f≤0·0005l
根据材料力学的莫尔积分公式
f =∫LM(x)M°(x)dxEJ
(5)优化方法及结果
从建立的数学模型看,这是个二维九个
约束的小型约束优化问题,可采用多种约束
优化方法求解。本设计采用SUMT内点法,
并利用BFGS变尺度法求得极小点。
内点法由于要有一个严格的可行域内的
初始点X(o),从计算上看,比外点法复杂一
些,但内点法的突出特点是每个迭代点都是
可行点。即给定一个可行的初始方案之后,
(2)省煤器和空气预热器设计时,除了应
对结构参数进行优化选择外,还应该用最优
化方法来确定是用单级布置还是双级布置,
以及如何进行最优双级布置等问题。
(3)尾部受热面双级布置时,合理分配高
低温级省煤器及高低温空气预热器的吸热
量,对降低整个尾部受热面的造价、提高经济
性是很有利的。
(4)锅炉是一个有机的热工机械系统,建
2≥δmin
将以上约束条件写成规格化约束为
g1(X)=0·0005l-
96Pval2-5πγl4(x12-x22)-32Fv∑9i=1bi(3l2-4b2i)
24πE(x14-x24)≥0
g2(X)=
96Pval2-5πγl4(x12-x22)-32Fv∑9i=1bi(3l2-4b2i)
keywords hollow rotating shaft structure optimum design
在我们承担的科研课题中,曾遇到一个
空心转轴的设计问题,为达到满意的结果,我
们对影响该轴结构的诸因素进行了分析处
理,并在计算机上进行了优化设计,根据优化
结果研制的转轴已应用于生产实际,取得了
空心转轴结构的优化设计
武汉食品工业学院(武汉430022) 张 麟
摘 要 介绍了空心转轴结构的优化设计过程,根据优化结果研制的空心转轴已应用于生产实际,并取
得了良好的经济效益。
关键词 空心转轴 结构 优化设计
Abstract This paper introduces the optimum design of the hollow rotating shaft structure·The shaft which
般资料推荐,空心轴内径与外径的比值为
0·5~0·6),与手算的最好结果比较,也减轻
重量约15%。实践证明,该设计方法简便,
结果可靠实用。
参考文献
1 孙靖民等·机械结构优化设计·哈尔滨:哈尔滨工业大
学出版社,1986
2 刘惟信·机械最优化设计·北京:清华大学出版社,
1994
3 王文博等·机械和机械零部件优化设计·北京:机械工