PCB镀层缺陷成因分析及其对策
PCB加工过程中图形电镀“凹坑”产生原因和解决方法

PCB加工过程中图形电镀“凹坑”产生原因和解决方法凹坑"是指图形电镀后在大铜面、线路、焊盘、金手指上出现的点状凹陷.在大铜面上出现的较轻微的"凹坑",用砂纸打磨平整,不影响外观、电气性能.但对线路、边接(焊)盘,尤其是金手指上的凹坑,用砂纸打磨难以整平,将影响其外观、插拔、焊接等,往往不能被客户接受.电镀"凹坑"问题不当,在全在线漫延,其损失报废是可怕的,对生产厂家来说,在生产的各工序严加把关,进行控制是至关重要的.以下是我们处理分析图形电镀最近发生"凹坑"的一些体验,供同行们参考.1.氯离子偏低.在高分散性硫酸盐光亮镀铜液中,加入活性强的氯离子,使阳极极化位提高,形成胶状的CuCl2吸附在阳极表面,抑制Cu-e→Cu+反应.如果氯离子偏低,则含磷铜电阳极在电解过程中因缺少CL-,而不能与Cu+化合形成胶体吸附在阳极表面,因而不能正常进行溶解,导致电镀铜层表面产生凹凸不平.2.光亮剂偏低.在酸性硫酸铜镀液中加入光亮剂,可电镀出平整光亮的镀铜层.光亮剂由多种成份组成,其中含有光亮剂、整平剂、润湿剂和分散剂.光亮剂是含硫的烷基或苯基磺酸盐类,对镀铜层起到光亮作用;整平剂能被吸附在阴极表面,尤其是微观凸出部位从而对电沉积起到抑制作用,使镀铜层平整.湿润剂、分散剂一般为非离子型表面活性剂,它能降低镀液的表面张力,起到湿润及对镀液相互扩散作用.3.镀液本身被油污及有机杂质污染.4.待图形电镀板不满足生产要求.例如,未电镀前覆铜板材凹凸不平,图形电镀不能把凹凸处电平整.其次,板面在图形电镀前被脏污污染或干膜显影不凈及干膜上的油污太多、粘在板上,按正常前处理难以去除污物,导致有污物在位置不能电镀上铜.5.图形电镀前处理液被污染或因浓度低,不足以去除板面的氧化、脏污.控制凹坑问题的途径针对凹坑产生的原因,结合公司设备及药水的情况,杜绝凹坑的发生,主要有以下几方面:1.按频率定期对镀铜液化验分析补加.如氯离子含量在40ppm以下图形电镀时,板面失去光泽、粗糙、凹凸不平.因氯离子含量较少,难免有误差,应根据平时做板质量的好坏及氯离子添加量多少的经验做参考.特别注意在清洗完铜球并电解预镀(拖缸),为生成新的阳极膜而消耗更多的氯离子.需把各成份调整到以下数值:硫酸铜为70g/l;硫酸100ml/l; 氯离子为70ppm;PCM光亮剂为3.0ml/l.2.按250ml/千安培.小时含量添加光亮剂,光亮剂消耗量的多少与温度、槽面的大小、打气量、碳芯过滤、电镀图形面积大小及镀铜厚度等因素有关,特别是电解预镀(扦缸)后光亮剂的补加,防止光亮剂的消耗量大于添加量,长时间导致光亮剂偏低,通过做赫尔槽片来确定光亮剂的被加量.3.当镀液中含有有机杂质及油污时,电解时板面沾到油污处不能电镀上铜,导致板面凹凸不平、粗糙,需定期采用碳芯过滤,去除镀液中的有机杂质及油污.4.控制好待图形电镀板的质量.如来料板面凹坑带到图形电镀工序,电铜不可能把凹坑整平.这时需在图形电镀前打磨平整.干膜显影不凈、板面残胶及板面脏污,按正常的图形电镀前处理,不能去除,致使某些位置不能电镀上铜,形成凹坑.5图形电镀线前处理液被污染或浓度低,难以去除板面氧化物、油污、脏污.对被污染的图形电镀前处理液应更换或对前处理各参数不在控制范围内时需进行调整,我们以除油浓度控制在200ml/l~250ml/l,粗化率在0.8um~1.0um,并且水洗充分干凈.小结从以上追踪结果可知,"凹坑"产生的根本原因是光成像图形转移工序保养不彻底造成.当然,产生"凹坑" 地原因还有很多.解决问题的途径也不一样.不管如何,作好图形电镀线点点滴滴的维护保养,控制也是至关重的.。
电镀过程中镀层不良的描述、原因及对策

电镀过程中镀层不良的描述、原因及对策1、针孔。
针孔是由于镀件外表吸附着氢气,迟迟不开释。
使镀液无法亲润镀件外表,然后无法电析镀层。
跟着析氢点周围区域镀层厚度的添加,析氢点就构成了一个针孔。
特点是一个发亮的圆孔,有时还有一个向上的小尾巴"。
当镀液中短少湿润剂并且电流密度偏高时,容易构成针孔。
2、麻点。
麻点是由于受镀外表不洁净,有固体物质吸附,或许镀液中固体物质悬浮着,当在电场效果下到达工件外表后,吸附其上,而影响了电析,把这些固体物质嵌入在电镀层中,构成一个个小凸点(麻点)。
特点是上凸,没有发亮现象,没有固定形状。
总归是工件脏、镀液脏而构成。
3、气流条纹。
气流条纹是由于添加剂过量或阴极电流密度过高或络合剂过高而降低了阴极电流效率然后析氢量大。
假如当时镀液流动缓慢,阴极移动缓慢,氢气贴着工件外表上升的进程中影响了电析结晶的摆放,构成自下而上一条条气流条纹。
4、掩镀(露底)。
掩镀是由于是工件外表管脚部位的软性溢料没有除掉,无法在此处进行电析堆积镀层。
电镀后可见基材,故称露底(由于软溢料是半通明的或通明的树脂成份)。
5、镀层脆性。
在SMD电镀后切筋成形后,可见在管脚弯处有开裂现象。
当镍层与基体之间开裂,判定是镍层脆性。
当锡层与镍层之间开裂,判定是锡层脆性。
构成脆性的原因八成是添加剂,光亮剂过量,或许是镀液中无机、有机杂质太多构成。
6、气袋。
气袋的构成是由于工件的形状和积气条件而构成。
氢气积在"袋中"无法排到镀液液面。
氢气的存在阻挠了电析镀层。
使堆集氢气的部位无镀层。
在电镀时,只需留意工件的钩挂方向能够防止气袋现象。
如图示工件电镀时,当垂直于镀槽底钩挂时,不发生气袋。
当平行于槽底钩挂时,易发生气袋。
7、塑封黑体中心开"锡花”。
在黑体上有锡镀层,这是由于电子管在焊线时,金丝的向上抛物形太高,塑封时金丝显露在黑体外表,锡就镀在金丝上,像开了一朵花。
不是镀液问题。
8、"爬锡"。
PCB电镀镍工艺及故障原因与排除
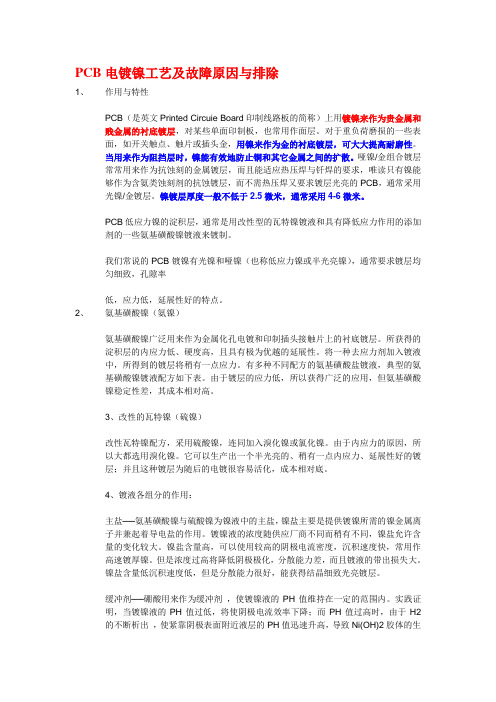
PCB电镀镍工艺及故障原因与排除1、作用与特性PCB(是英文Printed Circuie Board印制线路板的简称)上用镀镍来作为贵金属和贱金属的衬底镀层,对某些单面印制板,也常用作面层。
对于重负荷磨损的一些表面,如开关触点、触片或插头金,用镍来作为金的衬底镀层,可大大提高耐磨性。
当用来作为阻挡层时,镍能有效地防止铜和其它金属之间的扩散。
哑镍/金组合镀层常常用来作为抗蚀刻的金属镀层,而且能适应热压焊与钎焊的要求,唯读只有镍能够作为含氨类蚀刻剂的抗蚀镀层,而不需热压焊又要求镀层光亮的PCB,通常采用光镍/金镀层。
镍镀层厚度一般不低于2.5微米,通常采用4-6微米。
PCB低应力镍的淀积层,通常是用改性型的瓦特镍镀液和具有降低应力作用的添加剂的一些氨基磺酸镍镀液来镀制。
我们常说的PCB镀镍有光镍和哑镍(也称低应力镍或半光亮镍),通常要求镀层均匀细致,孔隙率低,应力低,延展性好的特点。
2、氨基磺酸镍(氨镍)氨基磺酸镍广泛用来作为金属化孔电镀和印制插头接触片上的衬底镀层。
所获得的淀积层的内应力低、硬度高,且具有极为优越的延展性。
将一种去应力剂加入镀液中,所得到的镀层将稍有一点应力。
有多种不同配方的氨基磺酸盐镀液,典型的氨基磺酸镍镀液配方如下表。
由于镀层的应力低,所以获得广泛的应用,但氨基磺酸镍稳定性差,其成本相对高。
3、改性的瓦特镍(硫镍)改性瓦特镍配方,采用硫酸镍,连同加入溴化镍或氯化镍。
由于内应力的原因,所以大都选用溴化镍。
它可以生产出一个半光亮的、稍有一点内应力、延展性好的镀层;并且这种镀层为随后的电镀很容易活化,成本相对底。
4、镀液各组分的作用:主盐──氨基磺酸镍与硫酸镍为镍液中的主盐,镍盐主要是提供镀镍所需的镍金属离子并兼起着导电盐的作用。
镀镍液的浓度随供应厂商不同而稍有不同,镍盐允许含量的变化较大。
镍盐含量高,可以使用较高的阴极电流密度,沉积速度快,常用作高速镀厚镍。
但是浓度过高将降低阴极极化,分散能力差,而且镀液的带出损失大。
Pcb常见问题缺陷类型及原因
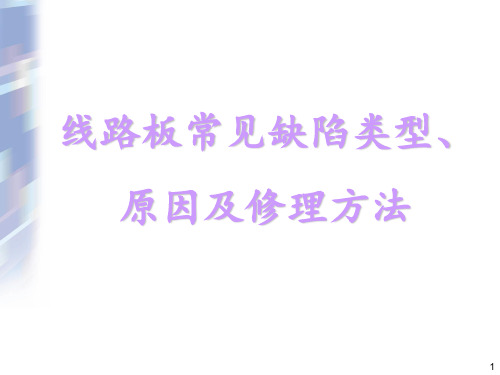
板污 板面有污渍
杂物、药水等污染
锡面不良/锡 薄
1>锡面高低不够 2>锡过薄过厚 3>锡面粗糙
喷锡机速度过快或前处理不好
工序
钻孔工序 干菲林工序
绿油工序
修理方法
不能修理
图例
蚀刻工序的 退锡段
不能修理
菲林制作
白字印上去的可翻 印,蚀刻上去的不能
修理
内层AOI工 序
不能修理
喷锡工序 FQC修理
不可修理
各工序都可 能
包金手指的红胶纸渍没有清洁干净
镀金工序 镀金
内层压板 外层镀金前
工序
轻微: 点金 严重: 不能修理
镀金工序
有布沾菲林水顺着金 手指方向往外擦
图例
16
F)板外围缺点
17
缺陷名称
状况
原因分析
漏斜边
该斜边的地方没 有斜边(金手指位 人为操作错误 置)
漏锣坑位
该锣坑位的地方 没有锣坑位
1>资料出错 2>人为操作错误
状况
原因分析
工序
修理方法
孔内有绿油/ 镀通孔内及锡面应喷 1>绿油冲板时没有冲干净 绿油上锡面 上锡,但被绿油覆盖 2>绿油曝光不良,导致冲不干净
甩绿油
绿油的附着力不够,用 胶纸撕拉时脱落
1>印绿油之前磨板不佳 2>绿油搅拌不均匀 3>印完绿油后锔板时间不够
绿油印歪
对位不正,导致绿油有 规则地上锡圈/锡面
现象
工序
修理方法
图例
蚀刻后各工 轻微可拖锡,严重不
序
可修理
锡面露铜
该上锡的地方没有 锡,而且露出铜面
1>绿油残留于铜面 2>喷锡前处理不佳
pcb常见缺陷原因与措

pcb常见缺陷原因与措施pptx汇报人:2023-12-15•PCB常见缺陷概述•常见缺陷原因分析•预防措施与改进建议目录•检测方法与技巧分享•案例分析:实际应用中的缺陷处理与改进方案•总结与展望:未来PCB行业的发展趋势及挑战01PCB常见缺陷概述定义材料缺陷设计缺陷环境缺陷制造缺陷分类PCB,即Printed Circuit Board,意为印刷电路板,是一种将电子器件和连接器件固定连接并实现电路连接的基板。
常见的PCB缺陷是指制造过程中产生的质量问题,这些缺陷可能影响电路板的性能和可靠性。
根据缺陷的表现形式和产生原因,PCB缺陷可以分为以下几类这类缺陷主要由于制造过程中的操作不当或工艺问题导致的,如孔洞、划痕、短路等。
这类缺陷与使用的材料有关,如材料质量问题、材料不均匀等。
这类缺陷与设计有关,如布线不合理、元件布局不当等。
这类缺陷与环境因素有关,如污染、湿度、温度等。
定义与分类缺陷对产品性能的影响直接性能影响一些缺陷如短路、断路等会直接导致电路板无法正常工作。
间接性能影响一些缺陷如材料不均匀、布线不合理等,虽然不会直接导致电路板无法工作,但会影响电路的性能和稳定性。
安全影响一些缺陷如材料质量问题、元件布局不当等,可能会影响产品的安全性能,如过热、过电压等。
02常见缺陷原因分析制造工艺问题是PCB板制造过程中可能出现的一系列工艺问题,如曝光、显影、蚀刻等环节的控制不当等。
总结词制造工艺问题可能会导致PCB板出现线条不清晰、短路、断路等问题,影响电路板的电气性能和可靠性。
详细描述制造工艺问题材料问题主要源于PCB板使用的原材料和组件的质量问题。
材料问题可能会导致PCB板出现开裂、脱落、短路等问题,影响电路板的性能和可靠性。
材料问题详细描述总结词设计问题主要源于PCB板的设计不合理,如布局、布线等设计因素。
总结词设计问题可能会导致PCB板的可制造性降低,增加制造难度和成本,同时也会影响电路板的电气性能和可靠性。
pcb常见缺陷原因与措施

污染物
空气中的微粒和有害气体可能污 染PCB的表面和内部,导致缺陷
。
静电
制造过程中的静电可能导致PCB 上的微粒移动,产生缺陷。
解决方法
控制温度和湿度
在制造过程中,应将温度和湿度控制在适当的范 围内。
空气净化
使用空气净化设备,减少空气中的微粒和有害气 体。
静电防护
采取静电防护措施,如使用防静电设备和材料, 减少静电的产生。
线路布局过于紧凑,导致 信号线交叉、重叠或干扰 。
走线不规范
走线弯曲、断裂或重叠, 导致信号传输不稳定。
未遵循最佳实践
设计时未遵循PCB设计的 最佳实践,如未考虑信号 完整性、电源完整性等因 素。
解决方法
优化布局
重新审查并调整线路布局 ,确保信号线之间保持适 当的间距,避免交叉、重 叠或干扰。
修正走线
制造工艺问题
02
制造过程中出现的问题,如曝光不良、显影不良、蚀刻不均等
。
压合工艺问题
03
多层板压合时,由于材料、温度等因素导致分层、扭曲等问题
。
解决方法
1 2
选用高质量板材
确保使用符合规格的板材,提高PCB的质量稳定 性。
优化制造工艺
通过对制造工艺的调整和改进,提高PCB的制造 质量。
3
压合工艺优化
加强制造质量控制:在制造过程中,应加强质量检查和控 制,确保不会出现短路的情况。
断路
优化制造工艺:在制造过程中,应采取适当的工艺和方法 ,确保线路的完整性和连续性。
定期维护和检查:在使用过程中,应定期对PCB进行检查 和维护,确保线路的完整性和连续性。
03
线路设计不良
原因分析
印制电路板镀层缺陷成因分析及其对策

印制电路板镀层缺陷成因分析及其对策1前言金属化孔质量与多层板质量及可靠性息息相关。
金属化孔起着多层印制线路电气互连的作用。
孔壁镀铜层质量是印制板质量的核心,不仅要求镀层有合适的厚度、均匀性和延展性,而且要求镀层在288℃热冲击10秒不能产生断裂。
因为孔壁镀铜层热冲击断裂是一种致命的缺陷,它将造成内层线路间和内层与外层线路之间断路;轻者影响线路断续导电,重者引起多层板报废。
目前,印制板生产中经常出现的金属化孔镀层缺陷主要有:金属化孔内镀铜层空洞、瘤状物、孔内镀层薄、粉红圈以及多层板孔壁与内层铜环连接不良等。
这些缺陷的绝大多数将导致产品报废,造成严重的经济损失,影响交货期。
2金属化孔镀层主要缺陷的产生原因及相应对策我们首先简单回顾一下多层印制板的制造工艺过程。
下料→制板→蚀刻→黑化→层压→钻孔→去沾污及凹蚀处理→孔金属化→全板电镀→制板→图形电镀→脱膜→蚀刻→丝印阻焊→热风整平→丝印字符本文将从钻孔工序、孔壁去树脂沾污及凹蚀处理工序、电镀及多层板层压工序等几个方面,分析金属化孔镀层的主要缺陷及产生原因,阐述如何优化工艺参数,进行严格的工艺及生产管理,以保证孔化质量。
2.1钻孔工序大多数镀层空洞部位都伴随出现钻孔质量差引起的孔壁缺陷,如孔口毛刺、孔壁粗糙、基材凹坑及环氧树脂腻污等。
由此造成孔壁镀铜层空洞,孔壁基材与镀层分离或镀层不平整。
下面,将对孔壁缺陷的成因及所采取的措施进行阐述:2.1.1孔口毛刺的产生及去除无论是采用手工钻还是数控钻,也无论是采用何种钻头和钻孔工艺参数,覆铜箔板在其钻孔过程中,产生毛刺总是不可避免的。
孔口毛刺对于金属化孔质量的影响历来不被人们所重视,但对于高可靠性印制板的金属化孔质量来讲,它却是一个不可忽视的因素。
首先,孔口毛刺会改变孔径尺寸,导致孔径入口处尺寸变小,影响元器件的插入。
其次,凸起或凹陷进入孔内的铜箔毛刺,将影响孔金属化过程中电镀时的电力线分布,导致孔口镀层厚度偏薄和应力集中,从而使成品印制板的孔口镀铜层在受到热冲击时,极易因基板热膨胀所引起的轴向拉伸应力造成断裂现象。
PCB常见缺陷原因与措施

PCB常见缺陷原因与措施引言Printed Circuit Board(PCB)是电子产品中不可或缺的组成部分。
而PCB在制造的过程中常常会出现各种缺陷,严重影响到电子产品的性能和质量。
本文将介绍PCB常见的缺陷原因,并提出相应的解决措施,以帮助读者更好地了解和解决PCB制造过程中的问题。
一、焊点问题1. 缺陷原因•锡焊不良:焊料不完全熔化、焊料过量或者焊料流动不顺畅都会导致焊点的质量下降。
•冷焊:焊接温度过低,导致焊料与焊盘间粘附力不足,形成冷焊现象。
•焊接过热:焊接温度过高,导致焊料流动过快,造成焊点高度不均匀、焊缝过大。
•焊接气泡:在焊接过程中,焊料中的挥发性成分产生气泡,导致焊点质量下降。
2. 解决措施•控制焊接温度:根据焊接材料的要求,合理设定焊接温度,以充分熔化焊料。
•控制焊接时间:根据焊接材料和焊接面积,控制焊接时间,确保焊料充分流动且均匀。
•检测焊接质量:通过焊接质量检测设备,对焊点进行检测,发现问题及时修复。
•提高焊接技术:通过培训和实践,提高焊接工人的技术水平,降低焊接缺陷率。
二、线路板污染问题1. 缺陷原因•灰尘和异物:制造环境不洁净,灰尘和其他杂物会污染线路板表面,影响电路连接质量。
•油污和氧化物:线路板表面受到油污和氧化物的污染,导致线路板表面粗糙、电路导通不良。
2. 解决措施•清洁环境:确保生产车间的清洁和通风,定期清理灰尘和杂物,防止其附着到线路板上。
•使用防护层:在制造过程中,使用防护层覆盖线路板表面,防止油污和氧化物的污染。
•采用合适的清洁剂:在清洗线路板时,选择合适的清洁剂,去除油污和氧化物,确保线路板表面干净和平滑。
•加强质检:建立完善的质检体系,对线路板进行全面检查,及时发现并处理污染问题。
三、连线问题1. 缺陷原因•线路断开:线路横截面积不足、线路受到外力破坏等原因导致线路断开,造成电路不通。
•线路短路:线路之间存在不必要的电气连接,造成电路短路。
•线路错位:线路连接错误,导致电气信号传输错误。
PCB电镀纯锡缺陷解析

PCB电镀纯锡缺陷解析来源:深圳龙人计算机发布者:penny 时间:2009-4-24 阅读:667次一、前言在线路板的制作过程中,多数厂家因考虑成本因素仍采用湿膜工艺成像,从而会造成图形电镀纯锡时难免出现“渗镀、亮边(锡薄)”等不良问题的困扰,鉴于此,本人将多年总结出的镀纯锡工艺常见问题的解决方法,与大家共同探讨。
二、湿膜板产生“渗镀”的原因分析(非纯锡药水质量问题)1.丝印前刷磨出来的铜面务必干净,确保铜面与湿油膜附着力良好。
2.湿膜曝光能量偏低时会导致湿膜光固化不完全,抗电镀纯锡能力差。
3.湿膜预烤参数不合理,烤箱局部温度差异大。
由于感光材料的热固化过程对温度比较敏感,温度低时会导致热固化不完全,从而降低湿膜的抗电镀纯锡能力。
4.没有进行后局/固化处理降低了抗电镀纯锡能力。
5.电镀纯锡出来的板水洗一定要彻底干净,同时须每块板隔位插架或干板,不允许叠板。
6.湿膜质量问题。
7.生产与存放环境、时间影响。
存放环境较差或存放时间过长会使湿膜膨胀,降低其抗电镀纯锡能力。
8.湿膜在锡缸中受到纯锡光剂及其它有机污染的攻击溶解,当镀锡槽阳极面积不足时必然会导致电流效率降低,电镀过程中析氧(电镀原理:阳极析氧,阴极析氢)。
如果电流密度过大而硫酸含量偏高时阴极析氢,攻击湿膜从而导致渗锡的发生(即所讲的“渗镀”)。
9.退膜液浓度高(氢氧化钠溶液)、温度高或浸泡时间长均会产生流锡或溶锡(即所讲的“渗镀”)。
10.镀纯锡电流密度过大,一般湿膜质量最佳电流密度适应于1.0~2.0A/dm2之间,超出此电流密度范围,有的湿膜质量易产生“渗镀”。
三、药水问题导致“渗镀”产生的原因及改善对策1.原因:药水问题导致“渗镀” 的产生主要取决于纯锡光剂配方。
光剂渗透能力强且在电镀的过程中对湿膜的攻击产生“渗镀”。
即纯锡光剂添加过多或电流稍偏大时就出现“渗镀”,在正常电流操作下,所产生的“渗镀”跟药水操作条件未控制好有关,如纯锡光剂过多、电流偏大、硫酸亚锡或硫酸含量偏高等,这些均会加速对湿膜之攻击性。
PCB镀层板面凹坑的成因之改善探刨

有 可 能 造 成 严 重 的 质 量 问 题 ,尤 其 是 Cu 质 量 与 板 面 洁 净 层 程度 关系更 为 密切和 重要 。
压 作 用 下 ,发 生 如 下 电 极 反 应 : 阴极 :
( 1)根 据 分 析 ,造 成 二 铜 板 面 凹 坑 状 的 镀 层 不 良 问
主 反 应 : Cu +2 _ “ e +Cu
副 反 应 : Cu +e— Cu
C u + e — Cu
题 的常 见原 因有 以下 几点 : 1 板面 有 肉眼 看不 到的显 影不 净层 ; 、
_ 文 编一 论选
人 失 望 ,镀 层 不 良伺 题 依 然 无 法 得 到 明显 改 善 和 解 决 。
看 不 到 的 显 影 不 净 层 、 显 影 机 太 脏 导 致 P 板 面 受 到 污 CB 染 、 由 于 后 煸 的 煸 炉 保 养 不 彻 底 致 使 板 面 残 留 有 未 挥 发 的
有 机 溶 剂 、 微 蚀 能 力 不 够 无 法 把 板 面 的 污 染 去 除 干 净 和 除
蕊 论 选 文编
技 师 论 文
电 l l蓑 I ! 2 露与 ;
P 镀 层 板 面 凹 坑 的 成 因 B C
及 改 善 探 讨
超 远 精密 电子 科技 有 限公 司, 兰飞 【 】 , 文
一
、
前 言
经 跟 进发 现所 有 的镀层 不 良板子 均具 有如 下特 性 : 1 采 用 湿 膜 工 艺 、
分析PCB制板电镀铜故障原因及预防措施

分析PCB制板电镀铜故障原因及预防措施硫酸铜电镀在PCB电镀中占着极为重要的地位,酸铜电镀的好坏直接影响PCB制板电镀铜层的质量和相关机械性能,并对后续加工产生一定影响,因此如何控制好酸铜电镀的质量是PCB电镀中重要的一环,也是很多大厂工艺控制较难的工序之一。
笔者根据多年在电镀和技术服务方面的些许经验,初步总结如下,希望对PCB行业电镀业者有所启发。
酸铜电镀常见的问题,主要有以下几个:1。
电镀粗糙;2。
电镀(板面)铜粒;3。
电镀凹坑;4。
板面发白或颜色不均等。
针对以上问题,进行了一些总结,并进行一些简要分析解决和预防措施。
电镀粗糙:一般板角粗糙,多数是电镀电流偏大所致,可以调低电流并用卡表检查电流显示有无异常;全板粗糙,一般不会出现,但是笔者在客户处也曾遇见过一次,后来查明时当时冬天气温偏低,光剂含量不足;还有有时一些返工褪膜板板面处理不干净也会出现类似状况。
电镀板面铜粒:引起板面铜粒产生的因素较多,从沉铜,图形转移整个过程,PCB制板电镀铜本身都有可能。
沉铜工艺引起的板面铜粒可能会由任何一个沉铜处理步骤引起。
碱性除油在水质硬度较高,钻孔粉尘较多(特别是双面板不经除胶渣)过滤不良时,不仅会引起板面粗糙,同时也造成孔内粗糙;但是一般只会造成孔内粗糙,板面轻微的点状污物微蚀也可以去除;微蚀主要有几种情况:所采用的微蚀剂双氧水或硫酸质量太差或过硫酸铵(钠)含杂质太高,一般建议至少应是CP级的,工业级除此之外还会引起其他的质量故障;微蚀槽铜含量过高或气温偏低造成硫酸铜晶体的缓慢析出;槽液混浊,污染。
活化液多数是污染或维护不当造成,如过滤泵漏气,槽液比重偏低,铜含量偏高(活化缸使用时间过长,3年以上),这样会在槽液内产生颗粒状悬浮物或杂质胶体,吸附在板面或孔壁,此时会伴随着孔内粗糙的产生。
解胶或加速:槽液使用时间太长出现混浊,因为现在多数解胶液采用氟硼酸配制,这样它会攻击FR-4中的玻璃纤维,造成槽液中的硅酸盐,。
pcb常见缺陷原因与措施

pcb常见缺陷原因与措施以pcb常见缺陷原因与措施为题,对pcb常见缺陷进行分析,并提出相应的解决措施。
一、常见pcb缺陷及其原因1. 焊盘剥落:焊盘剥落是pcb制造中常见的缺陷,主要原因包括焊接温度不合适、焊盘表面处理不当以及焊接压力不均等。
这些问题会导致焊盘与基板之间的粘附力不足,造成焊盘剥落。
2. 焊接短路:焊接短路是pcb制造中的另一个常见问题,主要原因是焊接过程中,焊料过多或焊接位置不准确,导致电路之间产生短路。
此外,焊接过程中的静电也是引起焊接短路的重要原因之一。
3. 焊接开路:焊接开路是pcb制造中的常见问题,主要原因是焊接温度不够高或焊接时间不足,导致焊料未完全熔化,无法与基板形成牢固的连接。
此外,焊盘与焊盘之间的距离也会影响焊接质量,距离过大会导致焊接开路。
4. 焊盘错位:焊盘错位是pcb制造中常见的缺陷,主要原因是焊盘布局设计不合理或制造过程中的误操作。
焊盘错位会导致焊接位置不准确,影响电路的连接性能。
5. 焊盘过度露铜:焊盘过度露铜是pcb制造中的常见缺陷,主要原因包括蚀刻不当、工艺参数设置错误以及材料选择不当等。
过度露铜会导致焊盘的机械强度下降,容易引起焊盘剥落或焊接开路。
二、常见pcb缺陷的解决措施1. 控制焊接温度和时间:合理控制焊接温度和时间是防止焊盘剥落、焊接短路和焊接开路的关键。
通过调整焊接参数,确保焊料能够充分熔化并与基板形成牢固的连接。
2. 加强焊盘表面处理:焊盘表面处理对焊盘的粘附性有很大影响。
通过选择合适的表面处理方法,如喷锡、化学镀金等,可以提高焊盘的附着力,减少焊盘剥落的风险。
3. 控制焊接压力和位置:合理控制焊接压力和位置是防止焊盘错位的关键。
通过调整焊接设备的参数,确保焊接位置准确,避免焊盘错位。
4. 优化焊接工艺:通过优化焊接工艺,如优化焊接温度曲线、调整焊接速度等,可以减少焊接短路和焊接开路的发生。
此外,加强对焊接操作人员的培训,提高他们的技术水平和操作规范性,也是防止焊接缺陷的重要手段。
电镀不良之原因分析及防范措施
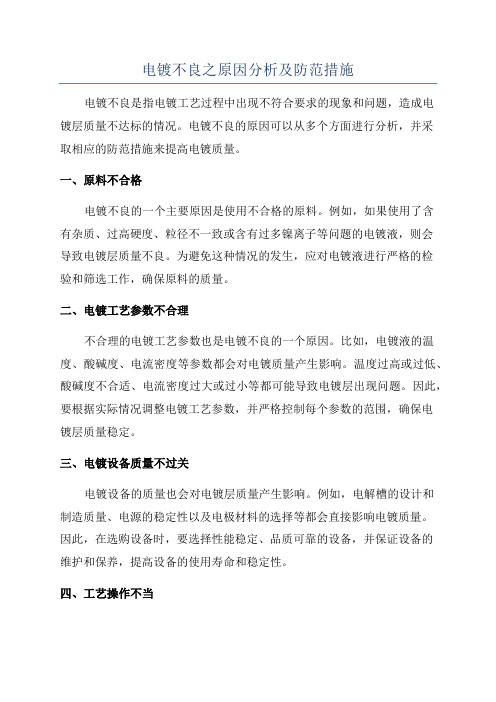
电镀不良之原因分析及防范措施电镀不良是指电镀工艺过程中出现不符合要求的现象和问题,造成电镀层质量不达标的情况。
电镀不良的原因可以从多个方面进行分析,并采取相应的防范措施来提高电镀质量。
一、原料不合格电镀不良的一个主要原因是使用不合格的原料。
例如,如果使用了含有杂质、过高硬度、粒径不一致或含有过多镍离子等问题的电镀液,则会导致电镀层质量不良。
为避免这种情况的发生,应对电镀液进行严格的检验和筛选工作,确保原料的质量。
二、电镀工艺参数不合理不合理的电镀工艺参数也是电镀不良的一个原因。
比如,电镀液的温度、酸碱度、电流密度等参数都会对电镀质量产生影响。
温度过高或过低、酸碱度不合适、电流密度过大或过小等都可能导致电镀层出现问题。
因此,要根据实际情况调整电镀工艺参数,并严格控制每个参数的范围,确保电镀层质量稳定。
三、电镀设备质量不过关电镀设备的质量也会对电镀层质量产生影响。
例如,电解槽的设计和制造质量、电源的稳定性以及电极材料的选择等都会直接影响电镀质量。
因此,在选购设备时,要选择性能稳定、品质可靠的设备,并保证设备的维护和保养,提高设备的使用寿命和稳定性。
四、工艺操作不当不正确的工艺操作也是电镀不良的一个常见原因。
例如,电镀工艺操作的速度太快或太慢,工件的浸泡时间控制不准确等都可能导致电镀层质量不良。
因此,操作人员在进行电镀工艺操作时要严格按照程序进行,并且进行必要的培训和技术指导,提高工艺操作的准确性和稳定性。
综上所述,电镀不良的原因可以从原料、工艺参数、设备质量和工艺操作等多个方面进行分析。
为了防范电镀不良的发生,可以采取以下措施:1.选用优质的原料,并进行严格检验和筛选;2.根据实际情况调整电镀工艺参数,并进行严格的控制;3.选购品质可靠的设备,并保证设备的维护和保养;4.进行工艺操作前进行必要的培训和技术指导,确保操作的准确性和稳定性;5.建立完善的质量控制体系,对电镀过程进行监控和检测,及时处理不良产品;6.加强与供应商的合作,建立长期稳定的合作关系,确保原料和设备质量的稳定性。
PCB浸镀银工艺之常见缺陷和改善方法介绍
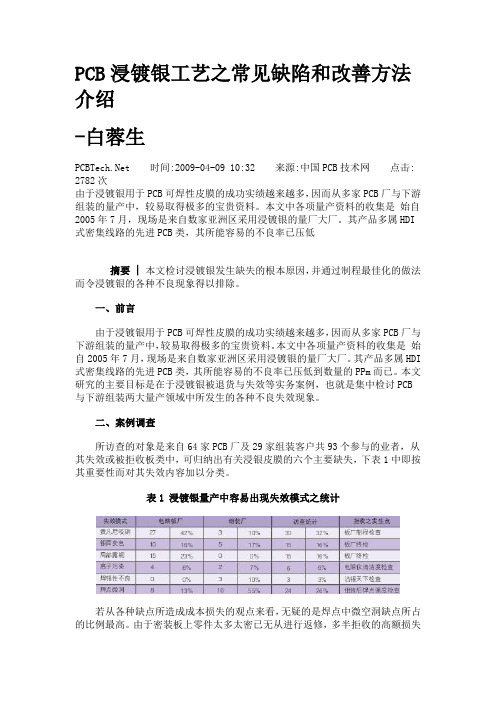
PCB浸镀银工艺之常见缺陷和改善方法介绍-白蓉生 时间:2009-04-09 10:32 来源:中国PCB技术网点击: 2782次由于浸镀银用于PCB可焊性皮膜的成功实绩越来越多,因而从多家PCB厂与下游组装的量产中,较易取得极多的宝贵资料。
本文中各项量产资料的收集是始自2005年7月,现场是来自数家亚洲区采用浸镀银的量厂大厂。
其产品多属HDI 式密集线路的先进PCB类,其所能容易的不良率已压低摘要 | 本文检讨浸镀银发生缺失的根本原因,并通过制程最佳化的做法而令浸镀银的各种不良现象得以排除。
一、前言由于浸镀银用于PCB可焊性皮膜的成功实绩越来越多,因而从多家PCB厂与下游组装的量产中,较易取得极多的宝贵资料。
本文中各项量产资料的收集是始自2005年7月,现场是来自数家亚洲区采用浸镀银的量厂大厂。
其产品多属HDI 式密集线路的先进PCB类,其所能容易的不良率已压低到数量的PPm而已。
本文研究的主要目标是在于浸镀银被退货与失效等实务案例,也就是集中检讨PCB 与下游组装两大量产领域中所发生的各种不良失效现象。
二、案例调查所访查的对象是来自64家PCB厂及29家组装客户共93个参与的业者,从其失效或被拒收板类中,可归纳出有关浸银皮膜的六个主要缺失,下表1中即按其重要性而对其失效内容加以分类。
表1 浸镀银量产中容易出现失效模式之统计若从各种缺点所造成成本损失的观点来看,无疑的是焊点中微空洞缺点所占的比例最高。
由于密装板上零件太多太密已无从进行返修,多半拒收的高额损失是发生在组装工厂中。
其中客户端尚未组装前,进料检验发现微洞问题而遭剔退者只有8件。
至于焊锡性问题方面则PCB厂全无不良纪录,组装厂也只有3件疑似者,而且仔细追究之下发现竟然是误叛为浸银之焊锡性不良。
事实上此一特殊案例是出自一种厚多层板高纵横比(HAR)的某些深孔中,波焊后发现上锡性不佳的半高孔壁虎,竟然直接与内层大地铜层相连接,以致在波焊中涌锡升起的瞬间,该接地处大量失热导致锡波的冷却固化所致,根本不是浸银皮膜的焊接问题。
PCB不良缺陷分析

PCB不良缺陷分析PCB(Printed Circuit Board)是电子设备中必不可少的组成部分,用于支持和连接电子元件。
由于PCB在电子设备中扮演着重要的角色,因此质量控制和缺陷分析对于确保产品质量和稳定性至关重要。
本文将重点介绍PCB的不良缺陷分析,并探讨如何预防和解决这些问题。
PCB的不良缺陷通常可以分为以下几类:制造工艺问题、材料问题、设计问题和组装问题。
首先,制造工艺问题可能是导致PCB不良缺陷的主要原因之一、制造过程中不当的焊接、探针测试、覆铜等操作可能导致PCB上的缺陷。
例如,不正确的焊接参数和工艺可能导致焊点开裂、电路通断不良等问题。
针对这些问题,制造商可以通过优化焊接工艺参数、加强员工培训和监督等方式来预防和解决。
其次,材料问题也是导致PCB不良缺陷的重要因素之一、不合格的材料可能会导致电路不良连接、短路和漏电等问题。
例如,使用过期的胶水、不合格的电子元件可能会降低PCB的质量。
制造商可以选择合格的供应商、进行严格的材料检验和审查来解决这些问题。
设计问题也是导致PCB不良缺陷的一个重要方面。
不合理的电路布局、不良的阻抗控制、信号干扰等问题可能会导致电路功能不正常。
为了解决这些问题,设计人员可以通过合理的布局设计、精确的阻抗控制和适当的信号层分离来提高PCB的质量。
最后,组装问题也是PCB不良缺陷的一个主要原因。
芯片和电子元件的安装不当可能导致焊接不良、引脚对焊等问题。
为了解决这些问题,制造商可以采用自动化组装技术、严格的质量控制流程和检查来确保组装质量。
为了解决PCB的不良缺陷问题,制造商可以采用以下几种方法。
首先,制定明确的质量标准和验收标准,确保产品质量可控。
其次,加强质量控制和检查流程,通过严格的检查和测试来发现和解决问题。
此外,合理的培训和技术支持也是解决问题的关键,制造商应该为员工提供必要的培训和技术指导。
总之,PCB不良缺陷对于产品质量和稳定性具有重要影响。
制造商应该重视质量控制和缺陷分析工作,通过合理的制造工艺、合格的材料和合理的设计来预防和解决PCB的不良缺陷问题。
PCB常见缺陷原因与措施分析[文字可编辑]
![PCB常见缺陷原因与措施分析[文字可编辑]](https://img.taocdn.com/s3/m/c3ad87a52f60ddccdb38a086.png)
阻焊与正常生产板阻焊颜色产生色差。
导致阻焊颜色出现变异,产生阻焊色差。
客户对阻焊颜色没有提出特别要求,由于绿色及黄色阻焊本身的 1、若客户对阻焊颜色有特别要求,建议客户在制作说明中进行备注。2、由
特性,在制程中控制较大很大,易出现色差,故终检在检验时, 于绿色及黄色油墨本身的特性,在制程中控制难度大,建议客户提供阻焊颜
与顾客沟通针对超公司生产能力的处理规则 ,加入到该顾客的特殊要求中
顾客设计的阻焊桥宽度满足做生产做阻焊桥要求,但 CAM人员在处理 对制作完成的文件进行检查时,使用矩形图查看 Pad to Pad spacing 信息,检查阻焊制
时,误将其做成阻焊开通窗。
作是否与顾客要求一致。
阻显焊影印时刷 底时 层, 油板墨面 受油Na墨2C印O3得或太K2厚CO,3 溶曝液光的时浸底蚀层,的造油成墨阻光焊聚桥合脱反落应。未完全,要 度 厚求 等 度工 进 要序 行 求在 调 后印 节 再刷 , 进阻 印 行焊 刷 其时 时 它, 进 厚必 行 的须 首 印依 板 刷据 制 。作ER,P并指且示油要墨求厚之度阻规焊进厚行度厚来度对测印量刷,之符刮合刀角度ER及P指力示
未作管控,按正常板出货。
色差异接收标准,终检在出货时依标准进行出货管控。
不良原因及改善措施
5、阻焊颜色做错
预审错误,由于顾客信息提供了两种阻焊颜色,未与顾客确认; 当顾客提供不同信息冲突时在预审表中记录与顾客确认;
NOPE更改时,顾客要求更改阻焊,CAM制作人员忘记更改ERP 制作更改单时,制作人员按《产品资料更改作业标准步骤》进行更改,防止
阻焊入孔较多且孔径较小,显影时未显影干净。
印刷,确认印刷时阻焊不入孔或进入极少油墨,避免显影不净。
PCB常见缺陷原因与措施
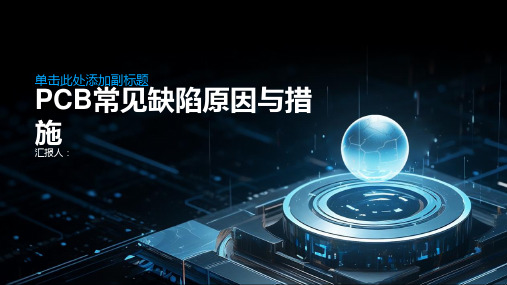
设备故障导致生产中断和额 外成本
设备升级和改造可以提高产 品质量和效率
04
预防和解决措施
提高制造工艺水平
选用合适的材料和设备,确保生 产过程中的稳定性和可靠性
加强员工培训,提高员工技能和 素质,确保生产过程中的操作规 范和质量控制
添加标题
添加标题
添加标题
添加标题
优化制造流程,减少生产过程中 的缺陷和不良品率
05
案例分析
具体案例描述
案例名称:阻焊膜 脱落
案例描述:阻焊膜 与线路板基材之间 的附着力不足,导 致阻焊膜部分或全 部脱落。
案例分析:阻焊膜 材料与基材不匹配 或涂布工艺问题, 需改进材料选择和 涂布工艺。
案例结论:阻焊膜 脱落是PCB制造过 程中常见的缺陷之 一,需关注材料和 工艺的选用。
缺陷原因分析
对于使用过程中的缺陷,加强 维护和保养,定期检查和维修
对于环境因素导致的缺陷,采 取相应的防护措施,如防潮、 防尘等
效果评估
缺陷识别:准确判断缺陷类型和位置 原因分析:深入剖析缺陷产生的原因 措施制定:根据原因制定有效的改进措施 效果跟踪:持续监测改进效果,确保问题得到解决
06
经验总结
对于常见缺陷的预防和应对策略的总结
建立完善的质量检测体系,对每 个生产环节进行严格的质量检测 和把关,确保产品的合格率和稳 定性
严格控制材料质量
严格控制材料采购、运输、 存储等环节,避免材料受损
选用优质材料,确保材料性 能稳定
对材料进行质量检测,确保 符合设计要求
采用合适的加工工艺,保证 材料加工质量
优化设计
优化电路设计:避免设计缺陷,提高电路可靠性 优化布局:合理分布元件,减小电磁干扰 优化布线:采用合适的线宽和间距,降低信号损失和干扰 优化层设计:合理利用多层板,减小信号传输阻抗
pcB金属孔镀层缺陷
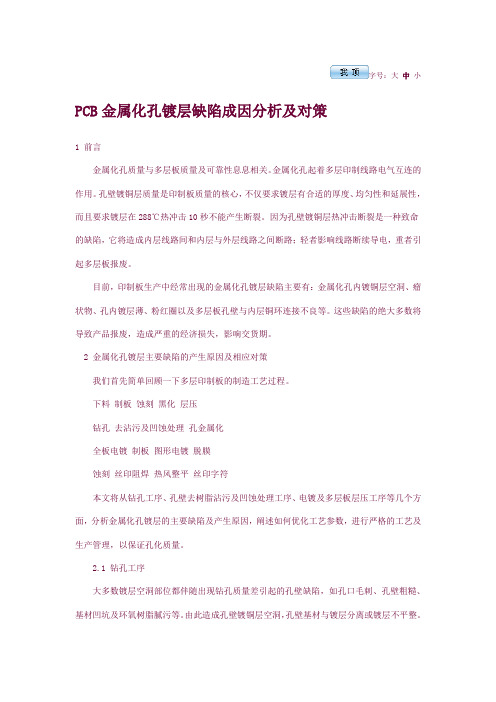
字号:大中小PCB金属化孔镀层缺陷成因分析及对策1 前言金属化孔质量与多层板质量及可靠性息息相关。
金属化孔起着多层印制线路电气互连的作用。
孔壁镀铜层质量是印制板质量的核心,不仅要求镀层有合适的厚度、均匀性和延展性,而且要求镀层在288℃热冲击10秒不能产生断裂。
因为孔壁镀铜层热冲击断裂是一种致命的缺陷,它将造成内层线路间和内层与外层线路之间断路;轻者影响线路断续导电,重者引起多层板报废。
目前,印制板生产中经常出现的金属化孔镀层缺陷主要有:金属化孔内镀铜层空洞、瘤状物、孔内镀层薄、粉红圈以及多层板孔壁与内层铜环连接不良等。
这些缺陷的绝大多数将导致产品报废,造成严重的经济损失,影响交货期。
2 金属化孔镀层主要缺陷的产生原因及相应对策我们首先简单回顾一下多层印制板的制造工艺过程。
下料制板蚀刻黑化层压钻孔去沾污及凹蚀处理孔金属化全板电镀制板图形电镀脱膜蚀刻丝印阻焊热风整平丝印字符本文将从钻孔工序、孔壁去树脂沾污及凹蚀处理工序、电镀及多层板层压工序等几个方面,分析金属化孔镀层的主要缺陷及产生原因,阐述如何优化工艺参数,进行严格的工艺及生产管理,以保证孔化质量。
2.1 钻孔工序大多数镀层空洞部位都伴随出现钻孔质量差引起的孔壁缺陷,如孔口毛刺、孔壁粗糙、基材凹坑及环氧树脂腻污等。
由此造成孔壁镀铜层空洞,孔壁基材与镀层分离或镀层不平整。
下面,将对孔壁缺陷的成因及所采取的措施进行阐述:2.1.1 孔口毛刺的产生及去除无论是采用手工钻还是数控钻,也无论是采用何种钻头和钻孔工艺参数,覆铜箔板在其钻孔过程中,产生毛刺总是不可避免的。
孔口毛刺对于金属化孔质量的影响历来不被人们所重视,但对于高可靠性印制板的金属化孔质量来讲,它却是一个不可忽视的因素。
首先,孔口毛刺会改变孔径尺寸,导致孔径入口处尺寸变小,影响元器件的插入。
其次,凸起或凹陷进入孔内的铜箔毛刺,将影响孔金属化过程中电镀时的电力线分布,导致孔口镀层厚度偏薄和应力集中,从而使成品印制板的孔口镀铜层在受到热冲击时,极易因基板热膨胀所引起的轴向拉伸应力造成断裂现象。
- 1、下载文档前请自行甄别文档内容的完整性,平台不提供额外的编辑、内容补充、找答案等附加服务。
- 2、"仅部分预览"的文档,不可在线预览部分如存在完整性等问题,可反馈申请退款(可完整预览的文档不适用该条件!)。
- 3、如文档侵犯您的权益,请联系客服反馈,我们会尽快为您处理(人工客服工作时间:9:00-18:30)。
PCB镀层缺陷成因分析及其对策
作者:杨维生
[摘要]分析了金属化孔镀层的主要缺陷及产生原因,从各主要工序出发,提出了如何优化工艺参数,进行严格的工艺及生产管理,以保证孔化质量的方法。
[关键词]多层印制板,金属化孔,镀层缺陷
1.前言
金属化孔质量与多层板质量及可靠性息息相关。
金属化孔起着多层印制线路电气互连的作用。
孔壁镀铜层质量是印制板质量的核心,不仅要求镀层有合适的厚度、均匀性和延展性,而且要求镀层在288℃热冲击10秒不能产生断裂。
因为孔壁镀铜层热冲击断裂是一种致命的缺陷,它将造成内层线路间和内层与外层线路之间断路;轻者影响线路断续导电,重者引起多层板报废。
目前,印制板生产中经常出现的金属化孔镀层缺陷主要有:金属化孔内镀铜层空洞、瘤状物、孔内镀层薄、粉红圈以及多层板孔壁与内层铜环连接不良等。
这些缺陷的绝大多数将导致产品报废,造成严重的经济损失,影响交货期。
2 金属化孔镀层主要缺陷的产生原因及相应对策
我们首先简单回顾一下多层印制板的制造工艺过程。
下料→ 制板→ 蚀刻→ 黑化→ 层压→ 钻孔→ 去沾污及凹蚀处理→孔金属化→ 全板电镀→ 制板→ 图形电镀→ 脱膜→ 蚀刻→ 丝印阻焊→ 热风整平→ 丝印字符
本文将从钻孔工序、孔壁去树脂沾污及凹蚀处理工序、电镀及多层板层压工序等几个方面,分析金属化孔镀层的主要缺陷及产生原因,阐述如何优化工艺参数,进行严格的工艺及生产管理,以保证孔化质量。
2.1 钻孔工序
大多数镀层空洞部位都伴随出现钻孔质量差引起的孔壁缺陷,如孔口毛刺、孔壁粗糙、基材凹坑及环氧树脂腻污等。
由此造成孔壁镀铜层空洞,孔壁基材与镀层分离或镀层不平整。
下面,将对孔壁缺陷的成因及所采取的措施进行阐述:
2.1.1 孔口毛刺的产生及去除
无论是采用手工钻还是数控钻,也无论是采用何种钻头和钻孔工艺参数,覆铜箔板在其钻孔过程中,产生毛刺总是不可避免的。
孔口毛刺对于金属化孔质量的影响历来不被人们所重视,但对于高可靠性印制板的金属化孔质量来讲,它却是一个不可忽视的因素。
首先,孔口毛刺会改变孔径尺寸,导致孔径入口处尺寸变小,影响元器件的插入。
其次,凸起或凹陷进入孔内的铜箔毛刺,将影响孔金属化过程中电镀时的电力线分布,导致孔口镀层厚度偏薄和应力集中,从而使成品印制板的孔口镀铜层在受到热冲击时,极易因基板热膨胀所引起的轴向拉伸应力造成断裂现象。
传统的去毛刺方法是用200~400号水砂纸仔细的打磨。
后来发展到用碳化硅磨料的尼龙刷机械抛刷。
但随着印制板技术的不断发展,9~18微米超薄型铜箔的推广应用,使印制板加工过程中的去毛刺技术也发生了很大变化。
据报道,国外己开始采用液体喷砂研磨法来去除孔口毛刺。
一般来说,对于去铜箔厚度在18微米以上的覆铜箔层压板孔口毛刺,采用机械抛刷法是十分有效的,只是操作时,必须严格控制好刷辘中碳化硅磨料的粒度和刷板压力,以免压力过大和磨料太粗使孔口显露基材。
用于去毛刺的尼龙刷辘中,碳化硅磨料的粒度一般为320~380#。
现代的双面去毛刺机共有四个刷辘,上下各半,能一次性将覆铜箔板两面的孔口毛刺同时去除干净。
在去除同样一面的孔口毛刺时,两个刷辘的转动方向是相反的。
一个沿顺时针方向转动,一个沿反时针方向转动,加上每个刷辘的轴向摆动,使孔口毛刺受到沿板面各个方向上刷板力的均匀作用,从而被彻底地除去。
去毛刺机必须配备高压喷射式水冲洗段。
液体喷砂研磨法,是利用一台专用设备,将碳化硅磨料借助于水的喷射力喷射在板面上,从而达到去毛刺的目的。
2.1.2 孔壁粗糙、基材凹坑对镀层质量的影响
在化学镀铜体系良好的状态下,钻孔质量差的孔壁容易产生镀铜层空洞。
因为在孔壁光滑的表面上,容易获得连续的化学镀铜层,而在粗糙的钻孔孔壁上,由于化学镀铜的连续性较差,容易产生针孔;尤其是当孔壁有钻孔产生的凹坑时,即使化学镀层很完整,但是在随后的电镀铜时,因为有电镀层折叠现象,电镀铜层也不易均匀一致,在钻孔凹坑处,容易存在镀层薄,甚至镀不上铜而产生镀层空洞。
2.1.3 环氧树脂腻污的成因
我们知道,印制板钻孔是一个很复杂的加工过程,基板在钻头切削刃机械力,包括剪切、挤压、扯裂、摩擦力的作用下,产生弹性变形、塑性变形与基材断裂、分离形成孔。
其中,很大部分机械能转化为热能。
特别是在高速切削的情况下,产生大量热能,温度陡然升高。
钻孔时,钻头温度在200℃以上。
印制板基材中所含树脂的玻璃化温度与之相比要低得多。
软化了的树脂被钻头牵动,腻在被切削孔壁的铜箔断面上,形成腻污。
清除腻污较困难,而且一旦在铜箔断面上有一定量的腻污,会降低甚至破坏多层板的互连性。
2.1.4 避免钻孔缺陷产生,提高钻孔质量的途径
孔口毛刺、孔壁粗糙、基材凹坑及环氧树脂腻污等缺陷,可通过加强以下几方面的工艺、质量控制,得以去除或削弱,从而达到提高钻孔质量的目的。
2.1.4.1 钻头的质量控制
钻头本身的质量,对钻孔的质量起着极为关键的作用,要求碳化钨合金材料的粒度必须非常细微,应达到
亚微级。
碳化钨合金无疏孔能耐磨,钻柄与切削刃部分的直径公差,均在0~0.005mm范围内,整个钻部、钻尖及柄部同心度公差在0.005mm以内,钻头的几何外形无缺损,即在40倍放大镜下观察,应无破口。
一只好的钻头还应该具备另外一个特性,即对称性。
钻头的两面在尺寸和形状上必须相同。
对称性差会产生磨损钻头刃。
为了保证钻头质量,必须对供货厂家严格选择,应从质量信得过的钻头生产厂家进货。
并对钻头进货进行检验,不合格的产品不准用于生产。
2. 1.4.2 钻头的形状选择
钻头的主要形状,一般分为普通型及锥斜型、铲型和特殊型,对于小孔特别是多层板小孔,最好采用后三种,后三种的特点是刃带的长度比较短,一般为0.5mm左右,它们可以明显减少钻孔的发热量,减少沾污。
2. 1.4.3 钻头排沟槽的长度
钻头排沟槽的长度,对排屑是否顺利起着至关重要的作用。
如果排屑的沟槽太短,钻屑无法顺利排山,钻孔的阻力增大,易造成钻头断裂,且易沾污孔壁。
所以,一般情况下,钻头排屑槽的长度,应为所叠板厚(包括上盖板)加上钻头进入下垫板深度和的1.15倍,即应使排屑槽的长度,至少有15%部分留在板外。
2.1.4.4 控制钻孔的工艺参数
这里所指的钻孔工艺参数包括每叠板的块数、钻数/进给比。
2.1.4.5 钻头的寿命控制
由于每个工厂的情况都不完全一致,钻头使用的寿命也有所差异,应根据具体的实验结果确定。
当孔的质量指标中,有一项己—下降到接近公差极限时,就需要更换钻头,换下去翻磨或报废。
一般情况下,多层板允许的最大钻孔数为1500个孔,而且,多层板一般不翻磨钻头。
2.1.4.6 上盖板、下垫板的使用
2.1.4.6.1 上盖板的使用
钻孔时使用的上盖板,可以起以下几个方面的作用:
1)防止压力脚对板面的损坏;
2)防止入口面毛刺的产生;
3)改善孔径精度;
4)减少小孔断钻头的机率。
假若不使用上盖板,那么,钻头在穿透薄的铜箔后,钻头的某一边有可能会与玻璃布撞击,导致钻头的一边受到较大的切削力,因而钻头会发生倾斜,从而影响定位精度。
而且,在穿透之后,钻头在退回时,受力不均衡,钻头易折断。
上盖板一般可采用0.2(O.4mm厚的硬铝箔。
2.1.4.6.2 下垫板的使用
使用下垫板,可以防止钻头碰到工作台面;还可防止出口面产生毛刺。