玻璃钢船艇模具制作工艺流程汇总
玻璃钢船艇模具制作工艺流程

欢迎阅读玻璃钢船艇模具制作工艺流程二、防潮层,批嵌腻子,喷易打磨胶衣1、糊防潮层:在木模表面上糊2层400g玻璃纤维布,用于加固木模强度,防止模具表面变形及防潮。
在玻璃钢固化后,再进行表面外理(如棱角、毛刺、重叠等)。
2、在胎膜上批嵌原子灰:在原子灰中加入适量固化剂,一般每桶原子灰在20℃的条件下,加入固化剂用量为2%,然后搅拌均匀,涂抹在胎膜上,用软管或挎尺照模型形状,将其挎圆顺,光滑。
反复按以上顺序操作,直至胎膜达到理想形状。
3、喷易打磨胶衣:打磨完成后,将胎膜表面灰尘、杂物清理干净后,将易打磨胶衣(产品胶衣可替代)均匀地喷涂在胎膜表面。
a)定)。
b)c)41光为止(2、抛光:用1号研磨剂均匀涂在胎模表面,用羊毛抛盘进行抛光,杜绝漏抛,1号研磨剂结束后再使用3号研磨剂,进行抛光清理干净。
3、脱模蜡处理:通常使用固体蜡和液体蜡两种。
a)固体蜡(8号蜡)一般以回旋法的方式用海绵擦拭,为了防止表面残留的蜡液引起厚度的增加,我们在上完第一层蜡以后通常要等半小时左右,使蜡完全渗透里层后,再用干净的线头擦去多余的蜡液,然后再上第二遍。
固体蜡在使用过程中擦的次数较多,一般15~16遍左右。
b)液体蜡(水蜡)一般以回旋法的方式用线头擦拭,它形成蜡模的时间较短,价格较昂贵,可以连续擦拭,液体蜡通常只需3~4次即可。
3、抛光:一般分别使用1号蜡、3号蜡进行两次抛光。
模型擦拭干净,将干净的4完毕后12、胶衣喷完后1-3小时,等胶衣固化后,表面基本不粘手或12小时之内进行首层铺层。
3、将调配好的树脂液涂刷到模具胶衣,随即铺一层短切毡(一般第一层不用纤维布;防止在模具表面上留下布印痕)。
用刷子、滚筒工具仔细滚压,排出气泡。
玻璃纤维是以GC-M-M-R-M-R-M……(GC表示胶衣,M表示短切毡,R表示玻璃纤维布)的积累方法进行逐层糊制的。
4、糊制过程中,要严格控制每层树脂胶液的用量,既要充分浸润纤维,又不能过多。
含胶量高,气泡不易排除,而且造成固化防热大,收缩率大,一般规定玻璃纤维短切毡的成型胶量为65%-70%,方格布为50%-55%。
玻璃钢船艇手糊成型工艺
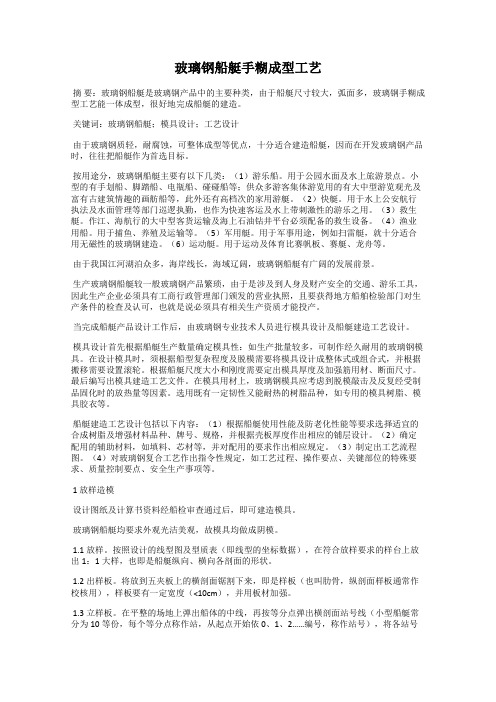
玻璃钢船艇手糊成型工艺摘要:玻璃钢船艇是玻璃钢产品中的主要种类,由于船艇尺寸较大,弧面多,玻璃钢手糊成型工艺能一体成型,很好地完成船艇的建造。
关键词:玻璃钢船艇;模具设计;工艺设计由于玻璃钢质轻,耐腐蚀,可整体成型等优点,十分适合建造船艇,因而在开发玻璃钢产品时,往往把船艇作为首选目标。
按用途分,玻璃钢船艇主要有以下几类:(1)游乐船。
用于公园水面及水上旅游景点。
小型的有手划船、脚踏船、电瓶船、碰碰船等;供众多游客集体游览用的有大中型游览观光及富有古建筑情趣的画舫船等,此外还有高档次的家用游艇。
(2)快艇。
用于水上公安航行执法及水面管理等部门巡逻执勤,也作为快速客运及水上带刺激性的游乐之用。
(3)救生艇。
作江、海航行的大中型客货运输及海上石油钻井平台必须配备的救生设备。
(4)渔业用船。
用于捕鱼、养殖及运输等。
(5)军用艇。
用于军事用途,例如扫雷艇,就十分适合用无磁性的玻璃钢建造。
(6)运动艇。
用于运动及体育比赛帆板、赛艇、龙舟等。
由于我国江河湖泊众多,海岸线长,海域辽阔,玻璃钢船艇有广阔的发展前景。
生产玻璃钢船艇较一般玻璃钢产品繁琐,由于是涉及到人身及财产安全的交通、游乐工具,因此生产企业必须具有工商行政管理部门颁发的营业执照,且要获得地方船舶检验部门对生产条件的检查及认可,也就是说必须具有相关生产资质才能投产。
当完成船艇产品设计工作后,由玻璃钢专业技术人员进行模具设计及船艇建造工艺设计。
模具设计首先根据船艇生产数量确定模具性:如生产批量较多,可制作经久耐用的玻璃钢模具。
在设计模具时,须根据船型复杂程度及脱模需要将模具设计成整体式或组合式,并根据搬移需要设置滚轮。
根据船艇尺度大小和刚度需要定出模具厚度及加强筋用材、断面尺寸。
最后编写出模具建造工艺文件。
在模具用材上,玻璃钢模具应考虑到脱模敲击及反复经受制品固化时的放热量等因素。
选用既有一定韧性又能耐热的树脂品种,如专用的模具树脂、模具胶衣等。
船艇建造工艺设计包括以下内容:(1)根据船艇使用性能及防老化性能等要求选择适宜的合成树脂及增强材料品种、牌号、规格,并根据壳板厚度作出相应的铺层设计。
制造模具玻璃钢船的工艺流程
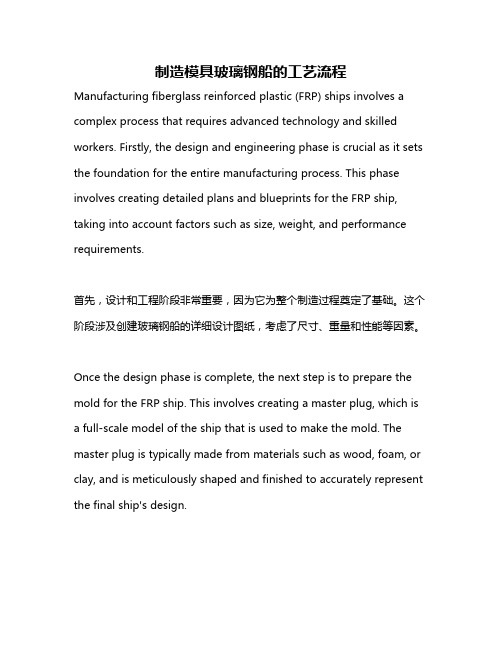
制造模具玻璃钢船的工艺流程Manufacturing fiberglass reinforced plastic (FRP) ships involves a complex process that requires advanced technology and skilled workers. Firstly, the design and engineering phase is crucial as it sets the foundation for the entire manufacturing process. This phase involves creating detailed plans and blueprints for the FRP ship, taking into account factors such as size, weight, and performance requirements.首先,设计和工程阶段非常重要,因为它为整个制造过程奠定了基础。
这个阶段涉及创建玻璃钢船的详细设计图纸,考虑了尺寸、重量和性能等因素。
Once the design phase is complete, the next step is to prepare the mold for the FRP ship. This involves creating a master plug, which is a full-scale model of the ship that is used to make the mold. The master plug is typically made from materials such as wood, foam, or clay, and is meticulously shaped and finished to accurately represent the final ship's design.设计阶段完成后,下一步是准备玻璃钢船模具。
玻璃钢船工艺流程
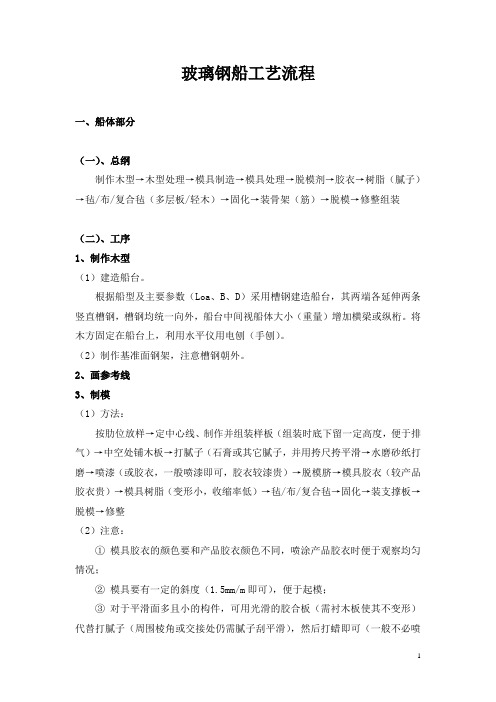
玻璃钢船工艺流程一、船体部分(一)、总纲制作木型→木型处理→模具制造→模具处理→脱模剂→胶衣→树脂(腻子)→毡/布/复合毡(多层板/轻木)→固化→装骨架(筋)→脱模→修整组装(二)、工序1、制作木型(1)建造船台。
根据船型及主要参数(Loa、B、D)采用槽钢建造船台,其两端各延伸两条竖直槽钢,槽钢均统一向外,船台中间视船体大小(重量)增加横梁或纵桁。
将木方固定在船台上,利用水平仪用电刨(手刨)。
(2)制作基准面钢架,注意槽钢朝外。
2、画参考线3、制模(1)方法:按肋位放样→定中心线、制作并组装样板(组装时底下留一定高度,便于排气)→中空处铺木板→打腻子(石膏或其它腻子,并用挎尺挎平滑→水磨砂纸打磨→喷漆(或胶衣,一般喷漆即可,胶衣较漆贵)→脱模脐→模具胶衣(较产品胶衣贵)→模具树脂(变形小,收缩率低)→毡/布/复合毡→固化→装支撑板→脱模→修整(2)注意:①模具胶衣的颜色要和产品胶衣颜色不同,喷涂产品胶衣时便于观察均匀情况;②模具要有一定的斜度(1.5mm/m即可),便于起模;③对于平滑面多且小的构件,可用光滑的胶合板(需衬木板使其不变形)代替打腻子(周围棱角或交接处仍需腻子刮平滑),然后打蜡即可(一般不必喷漆,但打腻子处如精度需要仍需喷漆);④支撑板要交叉组装,并用毡/布/复合毡等固定。
同时在与船体固定及支撑地面的部分做相应加强;⑤制模后要打抛光膏使模具质量更好。
4、脱模剂一次蜡即地板蜡(大量)+一次脱模剂适用于新模具,多打几次蜡,少打脱模剂,脱模后的船体外表面有一层保护模;脱模后,再打一次蜡(少量)+一次脱模剂。
5、胶衣(1)调配:胶衣+固化剂(过氧化甲乙酮,又名“白配方”,固化剂占胶衣重量的1-4%)(2)操作:①结构大的模具用喷枪喷洒,小的用刷子即可。
用喷枪喷洒时,胶衣与固化剂外混合,机器自动调配;②船体外彩色部分是先用分色纸将其挡住再喷主色部分,然后揭去分色纸挡住主色部分后喷彩色;③注意:胶衣不能太薄,应在0.4-0.6mm之间。
玻璃钢船艇建造工艺技术
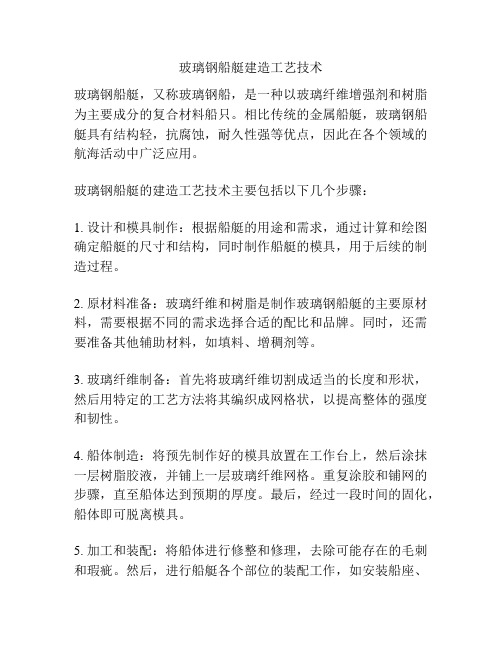
玻璃钢船艇建造工艺技术玻璃钢船艇,又称玻璃钢船,是一种以玻璃纤维增强剂和树脂为主要成分的复合材料船只。
相比传统的金属船艇,玻璃钢船艇具有结构轻,抗腐蚀,耐久性强等优点,因此在各个领域的航海活动中广泛应用。
玻璃钢船艇的建造工艺技术主要包括以下几个步骤:1. 设计和模具制作:根据船艇的用途和需求,通过计算和绘图确定船艇的尺寸和结构,同时制作船艇的模具,用于后续的制造过程。
2. 原材料准备:玻璃纤维和树脂是制作玻璃钢船艇的主要原材料,需要根据不同的需求选择合适的配比和品牌。
同时,还需要准备其他辅助材料,如填料、增稠剂等。
3. 玻璃纤维制备:首先将玻璃纤维切割成适当的长度和形状,然后用特定的工艺方法将其编织成网格状,以提高整体的强度和韧性。
4. 船体制造:将预先制作好的模具放置在工作台上,然后涂抹一层树脂胶液,并铺上一层玻璃纤维网格。
重复涂胶和铺网的步骤,直至船体达到预期的厚度。
最后,经过一段时间的固化,船体即可脱离模具。
5. 加工和装配:将船体进行修整和修理,去除可能存在的毛刺和瑕疵。
然后,进行船艇各个部位的装配工作,如安装船座、船舵、推进装置等。
6. 表面处理:为了提高玻璃钢船艇的耐候性和外观,还需要对船体进行表面处理。
常见的方法有磨光、喷漆和涂层等。
7. 测试和质量控制:在船艇制造完成后,需要对其进行各项测试以确保其性能和质量。
常见的测试项目包括强度测试、耐久性测试和漏水测试等。
总的来说,玻璃钢船艇的建造工艺技术较为复杂,需要严格的工艺流程和高技术水平。
通过合理的设计和制造,可以制造出质量优良、性能稳定的玻璃钢船艇,满足不同领域对船艇的需求。
玻璃钢船体的手工糊制
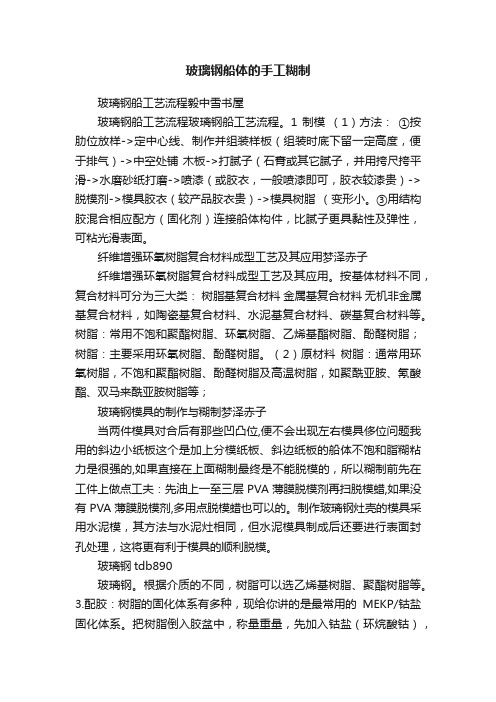
玻璃钢船体的手工糊制玻璃钢船工艺流程毅中雪书屋玻璃钢船工艺流程玻璃钢船工艺流程。
1 制模(1)方法:①按肋位放样->定中心线、制作并组装样板(组装时底下留一定高度,便于排气)->中空处铺木板->打腻子(石膏或其它腻子,并用挎尺挎平滑->水磨砂纸打磨->喷漆(或胶衣,一般喷漆即可,胶衣较漆贵)->脱模剂->模具胶衣(较产品胶衣贵)->模具树脂(变形小。
③用结构胶混合相应配方(固化剂)连接船体构件,比腻子更具黏性及弹性,可粘光滑表面。
纤维增强环氧树脂复合材料成型工艺及其应用梦泽赤子纤维增强环氧树脂复合材料成型工艺及其应用。
按基体材料不同,复合材料可分为三大类:树脂基复合材料金属基复合材料无机非金属基复合材料,如陶瓷基复合材料、水泥基复合材料、碳基复合材料等。
树脂:常用不饱和聚酯树脂、环氧树脂、乙烯基酯树脂、酚醛树脂;树脂:主要采用环氧树脂、酚醛树脂。
(2)原材料树脂:通常用环氧树脂,不饱和聚酯树脂、酚醛树脂及高温树脂,如聚酰亚胺、氰酸酯、双马来酰亚胺树脂等;玻璃钢模具的制作与糊制梦泽赤子当两件模具对合后有那些凹凸位,便不会出现左右模具侈位问题我用的斜边小纸板这个是加上分模纸板、斜边纸板的船体不饱和脂糊粘力是很强的,如果直接在上面糊制最终是不能脱模的,所以糊制前先在工件上做点工夫:先油上一至三层PVA薄膜脱模剂再扫脱模蜡,如果没有PVA薄膜脱模剂,多用点脱模蜡也可以的。
制作玻璃钢灶壳的模具采用水泥模,其方法与水泥灶相同,但水泥模具制成后还要进行表面封孔处理,这将更有利于模具的顺利脱模。
玻璃钢tdb890玻璃钢。
根据介质的不同,树脂可以选乙烯基树脂、聚酯树脂等。
3.配胶:树脂的固化体系有多种,现给你讲的是最常用的MEKP/钴盐固化体系。
把树脂倒入胶盆中,称量重量,先加入钴盐(环烷酸钴),钴盐的用量约为树脂重量的1-2%,搅拌均匀。
施工工艺:用毛刷在模具表面刷一层树脂,贴一层表面毡,用毛刷将表面毡紧紧贴合在模具上,要浸透树脂,不能有气泡。
玻璃钢船的制作流程

玻璃钢船的制作流程一、设计图纸。
做玻璃钢船呢,得先有个设计图纸。
这就像是给船画个蓝图,告诉咱们这船到底长啥样。
你得考虑船的用途呀,是用来钓鱼的小渔船呢,还是那种在湖面上慢悠悠划着玩的小船。
如果是钓鱼船,可能就需要有放鱼竿的地方,还有放鱼获的小角落。
要是游玩的小船,就得考虑能坐几个人舒舒服服的。
这个设计可不能马虎,它就像船的灵魂一样。
二、制作模具。
有了图纸之后呢,就开始做模具啦。
这模具就像是船的模子,船以后就照着这个模子长。
做模具的材料得选好,一般都是用木头或者泡沫之类的东西。
要是用木头呢,就需要木工师傅有一手好手艺,把木头切割呀、拼接呀,做成船的形状。
泡沫的话就比较轻便,但是也要处理得平滑。
在这个过程中,可需要细心和耐心啦,就像照顾一个小宝贝一样,哪里不平滑了就得修一修,哪里形状不对了就得改一改。
三、准备玻璃钢材料。
接下来就是准备玻璃钢材料啦。
玻璃钢是啥呢?其实就是玻璃纤维和树脂的组合。
玻璃纤维就像船的骨架,给船增加强度,树脂呢就像把这些骨架粘在一起的胶水。
玻璃纤维有各种不同的规格,得根据船的大小和需要的强度来选择。
树脂也有讲究,要选那种质量好、固化快的。
这时候就像在给船准备营养,只有营养好了,船才能长得结实。
四、铺层。
准备好材料就开始铺层啦。
把玻璃纤维一层一层地铺在模具上,然后用树脂浸透。
这就像给船穿衣服一样,一层一层地穿。
铺的时候要均匀,不能有的地方厚有的地方薄,就像给蛋糕抹奶油一样,要抹得平平整整的。
每铺一层都要把气泡挤出去,不然有气泡的话,船就不结实啦。
这个过程要特别小心,感觉就像是在给船做一件超级精细的艺术品。
五、固化。
铺好层之后就是固化啦。
让树脂在合适的温度和湿度下变硬,这个时候就像船在慢慢长大变硬。
要注意环境的温度和湿度哦,如果温度太低或者湿度太大,可能会影响固化的效果。
在这个过程中,就像在等待一个魔法的发生,看着软软的材料慢慢变得坚硬,那种感觉可奇妙啦。
六、脱模。
等固化好了之后呢,就可以脱模啦。
玻璃钢船舶模具制作工艺流程

玻璃钢船舶模具制作工艺流程英文回答:The process of making fiberglass ship molds involves several steps. Firstly, a design or blueprint of the ship is created. This design serves as a guide for the mold-making process. Next, a plug or pattern is made. This plug is a full-scale model of the ship and is usually made from wood, foam, or clay. The plug is carefully shaped and smoothed to ensure accuracy.Once the plug is complete, a release agent is applied to the surface to prevent the mold from sticking to the plug. Then, layers of fiberglass cloth are laid over the plug. The cloth is saturated with resin, which is usually a polyester or epoxy-based material. The resin hardens and forms a rigid structure, conforming to the shape of the plug.After the resin has cured, the mold is carefullyseparated from the plug. This can be a delicate process to ensure that the mold remains intact. The mold is then cleaned and prepared for use.To create the actual ship hull, the mold is coated with a release agent and layers of fiberglass cloth are applied. The cloth is again saturated with resin and allowed to cure. This process may be repeated several times to achieve the desired thickness and strength. Once the hull is fully cured, it is removed from the mold.The final step in the process is finishing anddetailing the ship hull. This may involve sanding, filling any imperfections, and applying a gel coat for a smooth and glossy finish. The ship hull is then ready for further assembly and installation of various components.中文回答:制作玻璃钢船舶模具的工艺流程包括几个步骤。
玻璃钢快艇制作工艺详解

一、有机玻璃钢:191不饱和树脂,玻璃纤维方格布(增强材料),填充料,固化剂、增进剂。
产品本钱高二、无机玻璃钢:氧化镁、氯化镁、玻璃纤维网格布,加入几种添加剂即可。
产品本钱低。
玻璃钢制作方式2020年01月13日评论(0)|阅读(67)玻璃钢制作方式小霸王(著)我是业余模型爱好者,几年来在玻璃钢船模制作上进行了斗胆的尝试,希望我的这套制作方式对大伙儿有所启发,同时希望大伙儿提出宝贵意见,以便于咱们一起提高。
1.将图纸或依照照片的样子进行1:1放样板。
一样需要主甲板,船底轮廓板和船尾板。
2.将三板固定在平板玻璃上,作为船体大体轮廓。
3.将石蜡凡士林和滑石粉按1:1:3混合,石蜡比例多油泥硬,做出的模型硬度高光洁,凡士林比例多油泥软,便于制作。
比例没有绝对的要求,可依照自己的喜好而定。
4.将配比好的原料加温混合融化。
一样不要直接在火上加热,如此容易烧焦,可采取大锅套小锅隔水加温。
5.用泡抹塑料和三合板加油泥按船体做出轮廓,现在船体超级粗糙。
油泥雕塑不可能一次完成,能够多糊几回。
6.船体轮廓做出以后,就将油泥糊在上面,这道工序和雕塑差不多。
油泥雕塑不可能一次完成,能够多糊几回。
7.精加工这道工序和雕塑差不多,需要技术和耐心。
8.用泡抹塑料和三合板加油泥按船体做出轮廓,现在船体超级粗糙。
油泥雕塑不可能一次完成,能够多糊几回。
油泥糊完以后就开始粗加工,一样采取刀刮,模型刨子刨,加工出大体形状来。
9.用自制的小熨斗和油画刀配合一边熨一边用油画刀附平,这道工序加工后也会留下熨痕,这时再用锋利的美工刀片在上面刮,你就会看到中意的成效。
10.用自制的小熨斗和油画刀配合一边熨一边用油画刀附平,这道工序加工后也会留下熨痕,这时再用锋利的美工刀片在上面刮,你就会看到中意的成效。
11.大体成型12.精加工用的工具13.通过精细加工以后的阳模。
14.在进行石膏浇注前,用地板蜡在阳模表面进行打蜡,反复进行3-4次,表面越光亮越好,便于起模。
玻璃钢船工艺流程
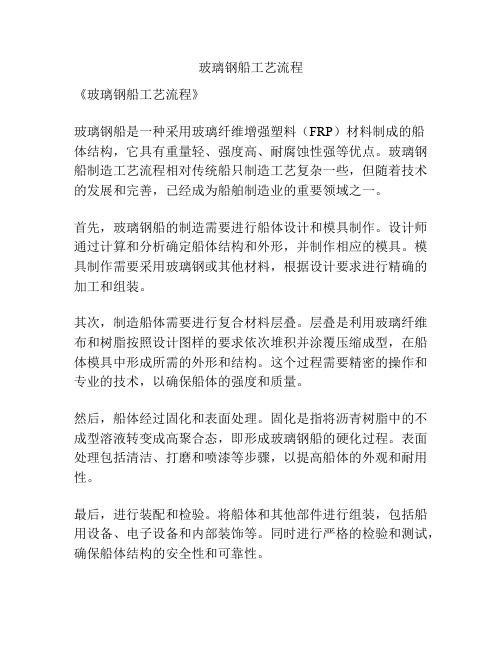
玻璃钢船工艺流程
《玻璃钢船工艺流程》
玻璃钢船是一种采用玻璃纤维增强塑料(FRP)材料制成的船
体结构,它具有重量轻、强度高、耐腐蚀性强等优点。
玻璃钢船制造工艺流程相对传统船只制造工艺复杂一些,但随着技术的发展和完善,已经成为船舶制造业的重要领域之一。
首先,玻璃钢船的制造需要进行船体设计和模具制作。
设计师通过计算和分析确定船体结构和外形,并制作相应的模具。
模具制作需要采用玻璃钢或其他材料,根据设计要求进行精确的加工和组装。
其次,制造船体需要进行复合材料层叠。
层叠是利用玻璃纤维布和树脂按照设计图样的要求依次堆积并涂覆压缩成型,在船体模具中形成所需的外形和结构。
这个过程需要精密的操作和专业的技术,以确保船体的强度和质量。
然后,船体经过固化和表面处理。
固化是指将沥青树脂中的不成型溶液转变成高聚合态,即形成玻璃钢船的硬化过程。
表面处理包括清洁、打磨和喷漆等步骤,以提高船体的外观和耐用性。
最后,进行装配和检验。
将船体和其他部件进行组装,包括船用设备、电子设备和内部装饰等。
同时进行严格的检验和测试,确保船体结构的安全性和可靠性。
总的来说,玻璃钢船的制造工艺流程需要经过多道工序,包括设计模具、层叠制作、固化处理、表面处理、装配检验等,每一道工序都需要专业的技术和经验。
随着技术的不断发展和完善,玻璃钢船已经成为船舶制造业中的重要一员,展现出其独特的优势和潜力。
玻璃钢船艇生产工艺
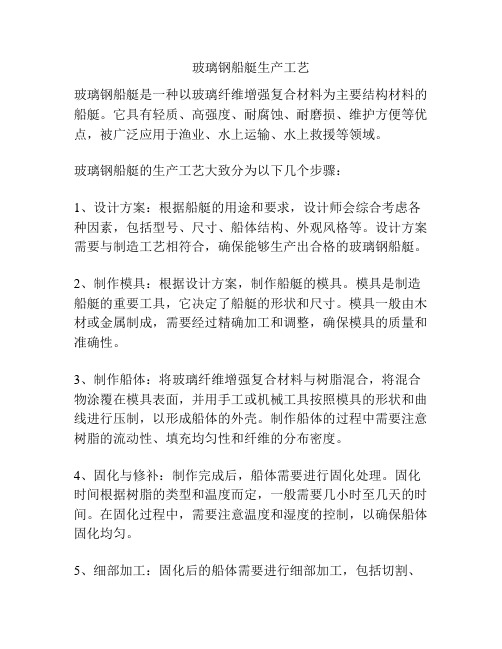
玻璃钢船艇生产工艺玻璃钢船艇是一种以玻璃纤维增强复合材料为主要结构材料的船艇。
它具有轻质、高强度、耐腐蚀、耐磨损、维护方便等优点,被广泛应用于渔业、水上运输、水上救援等领域。
玻璃钢船艇的生产工艺大致分为以下几个步骤:1、设计方案:根据船艇的用途和要求,设计师会综合考虑各种因素,包括型号、尺寸、船体结构、外观风格等。
设计方案需要与制造工艺相符合,确保能够生产出合格的玻璃钢船艇。
2、制作模具:根据设计方案,制作船艇的模具。
模具是制造船艇的重要工具,它决定了船艇的形状和尺寸。
模具一般由木材或金属制成,需要经过精确加工和调整,确保模具的质量和准确性。
3、制作船体:将玻璃纤维增强复合材料与树脂混合,将混合物涂覆在模具表面,并用手工或机械工具按照模具的形状和曲线进行压制,以形成船体的外壳。
制作船体的过程中需要注意树脂的流动性、填充均匀性和纤维的分布密度。
4、固化与修补:制作完成后,船体需要进行固化处理。
固化时间根据树脂的类型和温度而定,一般需要几小时至几天的时间。
在固化过程中,需要注意温度和湿度的控制,以确保船体固化均匀。
5、细部加工:固化后的船体需要进行细部加工,包括切割、打磨、抛光等工艺。
这些操作可以使船体表面更加平滑、光滑,减少摩擦阻力,提高船艇的性能。
6、组装与装配:将船体与其他零部件进行组装和装配,包括船舵、发动机、电气设备等。
组装和装配的过程中需要严格按照设计要求和技术标准进行操作,确保船艇的功能和安全性。
7、测试与质量控制:制造完成后,对船体进行严格的测试和质量控制。
测试包括静态测试、动态测试、水密性测试、耐磨性测试等,以确保船艇的性能和质量符合要求。
以上是玻璃钢船艇的生产工艺的基本步骤,不同类型和规模的船艇可能会有一些差异。
随着科技的进步和制造工艺的不断改进,玻璃钢船艇的生产工艺也在不断演变和完善,以满足市场需求和用户的要求。
玻璃钢船体制作原料和制作工艺流程

玻璃钢船体制作原料和制作工艺流程玻璃钢船体的制作原料主要包括玻璃纤维、树脂和填充剂。
玻璃纤维通常采用无碱玻璃纤维,具有较高的强度和耐腐蚀性能;树脂主要采用环氧树脂、酚醛树脂、聚酯树脂等,根据不同的使用环境和要求选择适当的树脂;填充剂包括硅酸盐、碳酸钙等,用于增加材料的硬度和强度。
第一步是模具制作。
根据船体的设计图纸,制作船体模具。
模具制作过程中要注意模具的平整度和精密度,确保模具表面的光滑度和尺寸的准确性。
第二步是纤维布放置。
将预先裁剪好的玻璃纤维布放置在模具表面,并根据船体的形状和结构进行适当的调整和切割。
在纤维布的放置过程中要确保纤维布的均匀性和紧密性,避免出现空隙和褶皱。
第三步是树脂涂布。
在纤维布放置完成后,使用刷子或喷枪将树脂涂布在纤维布上。
在涂布的过程中要确保树脂的均匀性和充分渗透性,避免出现结块和渗透不足的情况。
第四步是固化。
树脂涂布完成后,通过放置在恒温室或使用加热设备,加速树脂的固化过程。
树脂固化的时间和温度根据树脂的类型和选择的固化剂进行调控。
固化完成后,可以将船体从模具中取出。
第五步是后续加工。
在取出船体后,对船体进行修整、清理、抛光等工艺,使其表面光滑平整。
然后进行涂装、防腐等处理,增加船体的耐久性和美观度。
最后,进行船体的组装和安装船舶设备,完成整个船体制作过程。
以上是玻璃钢船体的制作原料和制作工艺流程的简要介绍。
在实际的制作过程中,还需要根据具体情况进行调整和改进,以满足不同船体的要求。
玻璃钢船体制作原料和制作工艺流程

玻璃钢船体制作原料和制作工艺流程做玻璃钢船,例子:捕鱼的的玻璃钢小船,3米长,一米宽,40CM高的来算吧,一体成形的。
材料你需要准备的如下:1。
树脂191A类型的,(20公斤,单价是13元左右/公斤)胶衣树脂2公斤,配套钴水和固化剂各1公斤2.玻璃纤维,分玻璃纤维毡和玻璃纤维布,(一共要毡就5-10公斤,12元左右/公斤,玻璃布10-20个平方吧,1。
5元左右/公斤)3.脱模蜡(一盒,大概50块左右)和原子灰(40左右一桶2。
5公斤重),滑石粉一袋(1000目以上的,一袋大概20左右)4。
木方,木板,铁丝,铁钉(有空气压缩机和钉枪就用钉枪)剪刀一把,砂纸从60-200目的准备各10张,水磨砂纸从400-800—1000的各不少于10张,木工曲线锯和配套木工锯条一板,角向打磨机1把(就是电磨),磨机砂片几片(进口的十几块一片,不容易炸片的,安全点)5。
塑料瓢,毛刷1寸到3寸的各几把6。
船体其它附加五金设备建议用不锈钢,材料多少就自己计算着办以上做法是按做一条船来算的,所以没有考虑模具树脂,都用191A的树脂来做吧,具体做法是先设计船的草图和尺寸———用木板木方按图纸做出船的外轮廓木质模型,模型做成阴模,船体部件做法一样,也就是里面空的,用滑石粉混合树脂补缝,用砂纸打磨平滑,因为这就是模具了,做一条船就不用再翻制树脂模型了,之后就把这个当船体的模具来用就行,有部件的就调好尺寸最后合模吧—-—调好尺寸,打磨光滑后的木模用原子灰很薄地刮一层并用粗砂纸和水磨砂纸打磨平整光滑并涂抹上脱模蜡,脱模蜡多打几遍,抹光滑之后——-刷上胶衣树脂,干后铺上纤维毡并刷上树脂———再干后就裁好玻璃纤维布铺上并刷好树脂,做到3层毡2层布就够结实牢固了,然后把配件按同样的方法做出来,用磨机打磨好边合模用,合模用纤维切碎混合滑石粉和树脂,干后打磨好,喷上漆即可,。
玻璃钢游艇制造工艺流程
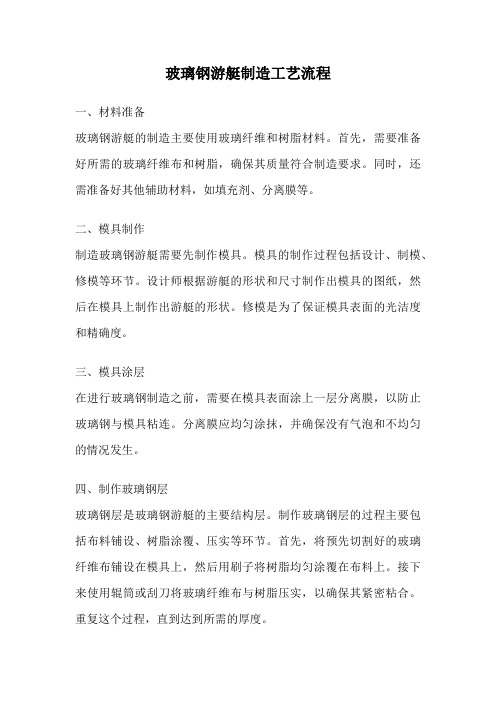
玻璃钢游艇制造工艺流程一、材料准备玻璃钢游艇的制造主要使用玻璃纤维和树脂材料。
首先,需要准备好所需的玻璃纤维布和树脂,确保其质量符合制造要求。
同时,还需准备好其他辅助材料,如填充剂、分离膜等。
二、模具制作制造玻璃钢游艇需要先制作模具。
模具的制作过程包括设计、制模、修模等环节。
设计师根据游艇的形状和尺寸制作出模具的图纸,然后在模具上制作出游艇的形状。
修模是为了保证模具表面的光洁度和精确度。
三、模具涂层在进行玻璃钢制造之前,需要在模具表面涂上一层分离膜,以防止玻璃钢与模具粘连。
分离膜应均匀涂抹,并确保没有气泡和不均匀的情况发生。
四、制作玻璃钢层玻璃钢层是玻璃钢游艇的主要结构层。
制作玻璃钢层的过程主要包括布料铺设、树脂涂覆、压实等环节。
首先,将预先切割好的玻璃纤维布铺设在模具上,然后用刷子将树脂均匀涂覆在布料上。
接下来使用辊筒或刮刀将玻璃纤维布与树脂压实,以确保其紧密粘合。
重复这个过程,直到达到所需的厚度。
五、填充材料加工游艇的内部结构通常需要填充材料来增加强度和刚度。
填充材料可以是泡沫、木材或其他合适的材料。
填充材料需要根据设计要求进行加工和安装,以保证结构的牢固性和稳定性。
六、表面处理制造好的玻璃钢游艇需要进行表面处理,以提高其外观质量和耐候性。
表面处理包括打磨、抛光、清洁等环节。
首先,需要对游艇表面进行打磨,以去除不平整和杂质。
然后进行抛光,使表面光滑亮丽。
最后,清洁表面,确保游艇外观整洁无污垢。
七、涂装涂装是玻璃钢游艇制造的最后一道工序。
涂装不仅可以增加游艇的美观度,还能提供保护作用。
涂装时需要选择合适的漆料,并按照规定的施工工艺进行涂装。
涂装后需要进行充分干燥,以确保漆面质量。
八、质量检验制造完成的玻璃钢游艇需要经过严格的质量检验。
质量检验包括外观检查、尺寸检测、强度测试等环节。
只有通过质量检验的游艇才能出厂销售。
九、包装和运输制造好的玻璃钢游艇需要进行适当的包装,并安全地运输到目的地。
包装过程中需要注意保护游艇的外观和结构,以免在运输中受到损坏。
玻璃钢船体的手工糊制

玻璃钢船体的手工糊制说起来用玻璃钢做各种模型也有不少经历了,可要总结性地写点什么,就不太容易了,因为涉及非金属复合材料的制造工艺。
十分担心有“以其昏昏,使人昭昭”的情况出现。
船模用玻璃钢制造时,同常采用的方法被称为“手工糊制”,简称“手糊”。
一.手糊玻璃钢制件的基本过程:在模具上涂好脱模剂——将加有固化剂的树脂混合涂料刷涂在模具上——再在胶层上铺放增强材料(如玻璃纤维布)——用刮刀、毛刷或压辊迫使胶液均匀地渗入织物,并排除气泡——待增强材料完全浸透后,再铺下一层,直至厚度——固化——脱模——切除飞边、毛刺——补涂缺胶部分——完成二.模具:在模型玻璃钢船体手糊制造中,使用的模具常见的是阳模和阴模。
(1)阳模——工作面凸起的模具形式。
由它制成的制品内表面质量高,尺寸精度高。
用它制造船体时,凸模表面应均匀地减去船体的厚度。
制成的船体缺少棱角且表面修整工作量较大,一般仅适用于单件制造。
(2)阴模——简单地说,用阳模脱出一个玻璃钢制件,修整后就可以作为以后的阴模。
这样生产出来的工件的外表面准确性高,后期工作量较小。
(3)组合模——例如将做船体的阴模做成左右可以分开的,就可以方便的脱模。
(4)模具的选材:根据制品的精度的从高到低以及加工批量,依次选用钢材、铝材、干燥的木材(如红松)、复合材料(树脂基体与填料的混合物)、石膏、石蜡(要加硬脂酸)等,在制造船模时,还有使用泡沫塑料,更多的有人直接使用已做好的船体作为阳模,糊出玻璃钢的阴模。
三.脱模剂:(1)薄膜类——玻璃纸、聚酯薄膜、聚乙烯薄膜、聚丙烯薄膜等,用油膏贴在模具表面,注意不要起皱和悬空。
(2)油膏类——石蜡、地板蜡、黄干油、凡士林、汽车腊、硅脂等,适用室温固化(低于摄氏80度)。
(3)溶液类——如聚乙烯醇水溶液、甲基硅油等,其中如聚乙烯醇水溶液使用较普遍。
四.飞边的切割:(1)手工方法——钢锯、电钻、锉刀都可用……(2)机械方法——用角向砂轮机换上玻璃钢专用的砂轮切片,效率很高,但要注意防尘,这些粉尘对健康都是有害的哦!五.树脂的选用首先要了解手糊成型所用树脂的要求:易浸渍纤维;容易脱气泡;垂直面涂刷时不易流胶;固化迅速;收缩小;层间黏结性能好……常用的是两大类:1,不饱和聚酯树脂——黏度小,浸渍性好,低分子物与气体易排除,凝胶时间可调节,能在常温常压下固化,但固化收缩率较大,制品强度较低;2,环氧树脂——黏结力强,制品强度高,也可以常温常压固化,但黏度大,需加稀释剂方可使用。
玻璃钢模具制作流程与检验标准

玻璃钢模具制作流程与检验标准(一)玻璃钢模具手糊成型工艺流程:玻璃钢模具手糊成型工艺是先在模型上涂一层脱模剂,然后将配好的树脂混合料用刮刀或刷子涂刷到模型上,再在其上铺陈裁好的玻璃布或其它增强材料,用刮刀或毛刷迫使树脂浸入玻璃布,排出气泡,待树脂浸透增强材料后,再铺放第2层增强材料,如此反复涂刷树脂和铺放增强材料,直至达到所需要的设计层数,然后进行固化、脱模和修整。
(二)玻璃钢模具原材料的选择:玻璃钢手糊成型模具的原材料主要是树脂、增强材料和辅助材料等。
合理地选择原材料是保证产品质量,降低成本的重要环节。
选择原材料时,必须满足以下条件:①满足产品设计的性能要求;②适应手糊成型工艺的特点;③价格便宜,货源充分。
目前的原材料主要有:树脂、增强纤维(玻纤布、短切毡、表面毡)、胶衣、固化剂、促进剂、脱模剂、色料、增韧剂、填料(石英粉、金刚石粉、铸石粉、石棉粉)等。
1、树脂的选择:选择手糊成型用的树脂品种十分重要,它直接关系到产品质量和生产工艺。
因此,必须根据产品性能、使用条件及工艺要求确定树脂的品种。
展开剩余91%⑴产品性能考虑,要注意:①树脂固化收缩问题:应选用低收缩树脂。
②断裂延伸率:应选用延伸性好的树脂,提高玻璃钢开裂时的强度。
⑵从工艺角度考虑,乙烯基树脂应满足:①良好的浸润性。
树脂对纤维的浸润是保证玻璃钢质量的一个重要因素,也是手糊工艺的先决条件。
如浸润不好,不仅使玻璃钢制品成型困难,也会使树脂——纤维间出现气泡;②适当的粘度。
手糊成型时的树脂粘度过低,会出现流胶现象,粘度过大,又会使成型浸润困难;③能在室温或低温下凝胶、固化,并要求固化时无低分子物产生;④无毒或低毒;⑤价格便宜,货源充足。
目前手糊成型工艺中最常用的树脂为不饱和聚酯树脂和环氧树脂,而酚醛树脂很少单独使用。
2、增强材料的选择:纤维品种一般要根据使用条件和工艺设计来进行选择。
⑴从使用条件考虑,要考虑制品的使用温度、强度、韧性、比重、绝缘性等因素。
制备玻璃钢船船体产品工艺

制备玻璃钢船船体产品工艺目录分别用手糊成型与喷射成型制备玻璃钢船船体产品工艺、设备,并进行方法比较 (2)一、不饱和聚酯树脂和玻璃纤维 (2)1.1分别用手糊成型与喷射成型制备玻璃钢船船体产品工艺、设备,并进行方法比较一、不饱和聚酯树脂和玻璃纤维1.1不饱和聚酯树脂不饱和聚酯树脂,一般是由不饱和二元酸二元醇或者饱和二元酸不饱和二元醇缩聚而成的具有酯键和不饱和双键的线型高分子化合物。
通常,聚酯化缩聚反应是在190~220℃进行,直至达到预期的酸值(或粘度),在聚酯化缩反应结束后,趁热加入一定量的乙烯基单体,配成粘稠的液体,这样的聚合物溶液称之为不饱和聚酯树脂。
不饱和聚酯树脂用途:建筑领域:制树脂冷却塔,8米3/小时-3000米3/小时的横流、逆流、喷射式塔及风筒、风机叶片、收水器等辅件。
玻璃钢树脂管、罐、槽等防腐产品及工程:包括大、中、小口径管道、管件、阀门、贮罐、贮槽、格栅、填仓板、塔器、烟囱、防腐地面及建筑防腐等。
玻璃钢树脂船艇:包括游艇、救生艇、交通艇、渔船、快艇、舢舨、养殖船、冲锋舟等。
玻璃钢树脂食品容器:高位水箱、食品运输罐、饮料罐。
1.2 玻璃纤维玻璃纤维(英文原名为:glass fiber或fiberglass )是一种性能优异的无机非金属材料,种类繁多,优点是绝缘性好、耐热性强、抗腐蚀性好,机械强度高,但缺点是性脆,耐磨性较差。
它是以玻璃球或废旧玻璃为原料经高温熔制、拉丝、络纱、织布等工艺制造成的,其单丝的直径为几个微米到二十几米个微米,相当于一根头发丝的1/20-1/5 ,每束纤维原丝都由数百根甚至上千根单丝组成。
玻璃纤维通常用作复合材料中的增强材料,电绝缘材料和绝热保温材料,电路基板等国民经济各个领域。
二、手糊法制作玻璃钢船船体2.1.1手糊成型的基本原理手糊成型又称接触成型,指在涂好脱模剂的模具上,采用手工作业,一边铺设增强材料,一边涂刷树脂,直到所需制品的厚度为止,然后通过固化和脱模而取得制品的成型工艺。
玻璃钢船工艺流程

玻璃钢船工艺流程玻璃钢船工艺流程是指在建造玻璃钢船时所采取的操作步骤和工艺方法。
下面将介绍一下玻璃钢船的工艺流程。
首先,玻璃钢船的工艺流程开始于制作模具。
制作模具需要按照船体的设计图纸,制作出船体的正剖面和侧剖面。
然后,采用木板或金属板制作模具,确保模具具有足够的强度和稳定性。
接下来,将模具涂抹脱模剂,以便船体脱模时能够顺利分离。
然后,在模具上搭建钢筋骨架,以提高船体的强度和稳定性。
钢筋骨架的搭建需要按照船体设计图纸上的要求进行,并确保各个部位的连接牢固。
在钢筋骨架搭建完毕后,开始制作船体的玻璃钢层。
玻璃钢层是玻璃纤维布与树脂混合物的复合材料,其制作需要将玻璃纤维布剪裁成合适的形状,并将其铺在模具上。
然后,用刷子沾取树脂混合物,均匀地涂抹在玻璃纤维布上,确保纤维布完全浸湿。
这个过程需要耐心而细致,以确保玻璃纤维布和树脂混合物的结合牢固。
待树脂混合物固化后,即可进行脱模。
首先,轻轻敲击模具,使船体与模具分离。
然后,将船体从模具中取出,进行清理和修整。
清理船体时需要将多余的玻璃纤维布和树脂切除,并用打磨机进行修整,使船体表面光滑平整。
最后,进行船体的组装和装配。
将船底、船板和船舱等部位按照设计图纸进行组装,并使用相应的连接件进行固定。
同时,根据船体的功能需求,进行相应的设备安装,如驾驶舱、发动机舱等。
以上就是玻璃钢船的工艺流程。
整个工艺流程包括制作模具、搭建钢筋骨架、制作玻璃钢层、脱模、清理修整和船体组装等环节。
每个环节都需要仔细操作,以确保最终制造出的玻璃钢船具有良好的质量和使用性能。
这些步骤的完成,为制造出高质量的玻璃钢船奠定了基础。
- 1、下载文档前请自行甄别文档内容的完整性,平台不提供额外的编辑、内容补充、找答案等附加服务。
- 2、"仅部分预览"的文档,不可在线预览部分如存在完整性等问题,可反馈申请退款(可完整预览的文档不适用该条件!)。
- 3、如文档侵犯您的权益,请联系客服反馈,我们会尽快为您处理(人工客服工作时间:9:00-18:30)。
玻璃钢船艇模具制作工艺流程万国(南通)玻璃钢有限公司VANGUARD(NANTONG)F.R.P.CO., LTD.A、外壳模具制作一、木工制作1、制作底板。
在地面上打基线,根据基线在地面上用木板组成底板框架,调整使之水平,用玻璃钢将框架与地面固定,然后在木框架上铺木工板,调整使之水平。
2、确定俯视图。
按型值表在地板上绘制站距以及各站板的半宽边线,然后将各个站板半宽边线的端点连接,这样俯视图就能确定下来。
3、制作木模型。
根据型值表在木工板上绘制个站板线型图,切割使之成型。
用木条等将各站板与底板固定,站板之间用木条互相支撑固定,另用木工板将整个模型框架封闭。
二、防潮层,批嵌腻子,喷易打磨胶衣1、糊防潮层:在木模表面上糊2层400g玻璃纤维布,用于加固木模强度,防止模具表面变形及防潮。
在玻璃钢固化后,再进行表面外理(如棱角、毛刺、重叠等)。
2、在胎膜上批嵌原子灰:在原子灰中加入适量固化剂,一般每桶原子灰在20℃的条件下,加入固化剂用量为2%,然后搅拌均匀,涂抹在胎膜上,用软管或挎尺照模型形状,将其挎圆顺,光滑。
反复按以上顺序操作,直至胎膜达到理想形状。
3、喷易打磨胶衣:打磨完成后,将胎膜表面灰尘、杂物清理干净后,将易打磨胶衣(产品胶衣可替代)均匀地喷涂在胎膜表面。
a) 、喷胶衣时,稀释剂:胶衣=1:1.5,固化剂用量为胶衣的1%-2%(温度决定)。
b) 、胶衣厚度为不小于 l mm,胶衣分 2 层,喷涂过程分几次完成,直至胶衣厚度达到理想程度。
c) 、易打磨胶衣固化时间一般控制在 45 分钟为佳。
4 、打磨成衣:胶衣固化 12 小时后打磨,首先选用相应的铁砂纸,用平板打磨机打磨,使胶衣表面颗粒基本光滑,再用水砂打磨,直至平滑光亮。
三、水磨,抛光,打蜡,上模具胶衣1、水磨:逐次用400#,600#,1000#,1200#的水砂纸水磨。
为了方便操作,一般制作长方体泡沫块裹上砂纸,沾水磨(一般水中放适量洗衣粉,起润滑作用,有效的增加了砂纸的利用率 ),按照模型形状往统一的方向砂磨,直到模型表面不在有亮光为止 ( 防止漏砂 ) ,达到平滑光亮。
水磨时要注意模型上要干净。
水磨结束后,将模型清理干净,用干净毛巾擦干,待干透后进行抛光 ( 模蜡处理 )。
2、抛光:用 1 号研磨剂均匀涂在胎模表面,用羊毛抛盘进行抛光,杜绝漏抛,1 号研磨剂结束后再使用 3 号研磨剂,进行抛光清理干净。
3、脱模蜡处理:通常使用固体蜡和液体蜡两种。
a) 固体蜡 (8 号蜡 ) 一般以回旋法的方式用海绵擦拭,为了防止表面残留的蜡液引起厚度的增加,我们在上完第一层蜡以后通常要等半小时左右,使蜡完全渗透里层后,再用干净的线头擦去多余的蜡液,然后再上第二遍。
固体蜡在使用过程中擦的次数较多,一般 15~16 遍左右。
b) 液体蜡 ( 水蜡 ) 一般以回旋法的方式用线头擦拭,它形成蜡模的时间较短,价格较昂贵,可以连续擦拭,液体蜡通常只需3~4 次即可。
3 、抛光:一般分别使用 1 号蜡、 3 号蜡进行两次抛光。
模型擦拭干净,将干净的抛光棉圈装好,抛光机插上电源试转。
先将 1 号蜡均匀涂抹在模型上,再用抛光机在模型上抛光。
后涂 3 号蜡,再进行抛光,抛光时以螺旋的方式进行,直到模型表面非常光滑美观。
通常抛一段时间后要清洗一下抛光棉或更换新的抛光棉。
4、刷模具胶衣:模具胶衣的操作过程是模具制造中至关重要的一步,高质量的模具表面要求十分精密的模具胶衣操作过程。
模具胶衣一般为黑色。
在使用之前,每批胶衣都需要先做小样试验,根据试验结果和施工时间来调配胶衣,以使胶衣在施工完毕后20~40分钟胶凝为宜。
通常建议模具胶衣厚度为0.8mm,为了保证胶衣树脂层厚薄均匀,胶衣涂刷工作分两次完成,每层0.3~0.4 mm厚,刷第二遍胶衣应与第一遍胶衣垂直方向。
为避免龟裂、起皱或漏刷等,应待第一次基本胶凝后方可再涂刷第二次。
涂刷第二次胶衣时,需穿鞋套进舱,以防打滑或粘连损坏。
四、铺层施工工艺1、玻璃钢制品的增强材料 ( 产品 ):在船的满载水线以上采用低碱及中碱玻璃纤维制品,满载水线以下采用物件玻璃纤维制品。
2、胶衣喷完后1-3小时,等胶衣固化后,表面基本不粘手或12小时之内进行首层铺层。
3 、将调配好的树脂液涂刷到模具胶衣,随即铺一层短切毡 ( 一般第一层不用纤维布;防止在模具表面上留下布印痕 ) 。
用刷子、滚筒工具仔细滚压,排出气泡。
玻璃纤维是以GC-M-M-R-M-R -M…… (GC 表示胶衣,M 表示短切毡,R表示玻璃纤维布 ) 的积累方法进行逐层糊制的。
4 、糊制过程中,要严格控制每层树脂胶液的用量,既要充分浸润纤维,又不能过多。
含胶量高,气泡不易排除,而且造成固化防热大,收缩率大,一般规定玻璃纤维短切毡的成型胶量为 65%-70%,方格布为 50%-55% 。
整个糊制过程实行多次成型。
每次糊制2-3mm 以后,要待固化放热高峰过后,方可进行下层的糊制。
5 、在铺层厚度超过 3mm -5mm 层时,我们就要考虑到玻璃纤维搭接所引起的厚度增加,玻璃纤维接缝重叠宽度要大于 5Omm,上、下层玻璃纤维铺覆接缝间距要大于 10Omm 。
糊制过程中,为了保证模具具有足够的强度,避免模具变形,可适当的粘接一些支撑件,紧固件等以完善模具结构。
6 、铺层时最重要的就是合作,配树脂的人要准备树脂和固化剂,待铺层的人将树脂用完后,立即配制、调匀,送到铺层的人手里,铺层一般分两组,两人一组,分左右两边一起进行,而辅助的人一定要跟紧配合好滚树脂的人,动作要快,不然错开的位置的树脂会固化,而气泡等未排除,就会影响模具的强度和硬度的质量 ( 层糊时重要的一点就是要把气泡排尽 ) 。
铺层结束后大约需要 30-40 分钟左右固化,2-3 小时后方可进行下一道工序。
五、模架制作1、制作脱模架:当模具铺层完毕后,即可开始制作模具的外部加强结构。
目的是:使外部力量平均传送至模具表面,组织模具的表面变形。
2、方法:先用细铁丝在模具上比划弯曲,根据比划好的铁丝,锯相应长的圆管,用弯管将圆管弯曲成型,方管分段锯槽,用锤子敲击使之弯曲,弧度与模具相匹配。
一般方管用作模具,圆管用作竖挡。
脱模架焊接结束后,需将模架作进一步修整加固,清理,刷油漆。
3 、模架固定:用玻璃纤维将模架与铺层之间黏结。
具体操作和铺层一样,玻璃钢固化后,等一段时间以后方可开始脱模。
六、脱膜,割边,清理,修补,水砂,抛光1 、脱膜:将吊钩分别固定在模具两端,吊钩和脱膜架固定好,先用多个脱膜楔均布插入模具和胎模之间,并用锤子敲打各个脱模楔,一定要均匀用力以防损坏模具,最后启动吊架,将玻璃钢模具与胎模完全分开。
2 、割边:预留沿边宽为5cm,对模具沿边进行切割修整。
3 、清理:将模具内部有毛刺,棱角的地方用板凿铲平,并清洗一边,以方便水砂。
4 、水砂:逐次用 400,600,100O , 1200 等砂纸裹在泡沫块上,沾上洗衣粉水,往一个方向砂磨,直至模具不再有光点,但表面光滑。
具体操作方法同 3.l 。
5 、修补:在水砂以前,检查整个模具内部,有缺损的地方用胶衣进行修补,等平整光顺后,方可再进行水砂,直至光滑。
6 、抛光:模具彻底光滑后,分别上一号蜡和二号蜡,再分别用抛光机进行抛光。
七、打蜡上产品胶衣1 、对模具进行检查、修补抛光之后,开始打蜡。
2 、打蜡完毕后,按照客户要求上橙色或灰白色胶衣 ( 外壳上橙色,内壳上灰白色),配胶衣需要数人,配料一个人 ( 配料工需看配料工注意事项 ),胶衣一般必须是预促过的,促进剂为 0.5%-4% 之间,配料时固化剂的量根据温度来确定,一般为 1%-2% 。
刷胶衣时需穿鞋套进舱,避免打滑或粘连胶衣而损坏。
3 、为了保证胶衣厚度,一般需刷两层,每层横竖各一次,以确保均匀。
第二次需在第一次基本或完全固化后再进行。
B 内模模具制作1、按结构图制作内模,产品外壳不脱离模具,直接在内部做。
首先用木档定位,用胶棒固定木档。
在木档与外壳接触的地方用玻璃纤维布把木档固定牢固。
做成水平面,然后按结构图用木工板制作内模。
2、贴宝丽板,批腻子:由于内模平滑面多、构件小,表面贴宝丽板,保证表面光洁,这样只需对模具进行简单的清理即可,节省时间,同时也可以延长模具的使用寿命。
3 、周围棱角或交接处需原子灰刮平滑修成圆角,并制作卡板,保证各处圆角一致大小。
走到处制作防滑,可以用印花玻璃等加工模具,制作成防滑板。
割边,清理,组合,(冲泡沫)1、割边:略。
2、组合:用行车将做好的产品与其配套产品放在一起,其边缘和底部用树脂加触变剂和剪碎了的玻璃纤维搅拌定位牢固,然后用玻璃纤维待搭接好后就可以充泡沫了。
3、充泡沫a 、根据艇体的外形钻直径为40mm 的充泡沫孔( 可在组合前就要钻好 ),用塑料薄膜将艇体覆盖,光留有泡沫孔,并将塑料与泡沫孔固定。
b 、检查 A 、B 料箱,料是否充足,否则加料至规定位置。
C 、设置好泡沫机的开关 (A、B 料冬天须加热,设定泡沫机加热温度不低于30-4O 度左右 ),比例为 1:l。
d 、按比例开始冲泡,要注意冲泡过程并不是一次完成的,冲一段时间后间隔几分钟,等待泡沫固化以后再继续,防止泡沫膨胀,破坏产品。
e 、泡沫机充好后 A 、B 料都要加至滤网以上,防止结晶堵塞泵口,把冲泡塞打上硅胶,盖在冲泡孔上确保水密,内部清理、批嵌、上蜡液胶衣一到二次。