弹簧夹头工艺的设计说明书
机械毕业设计-弹簧夹头工艺规程制定与夹具设计
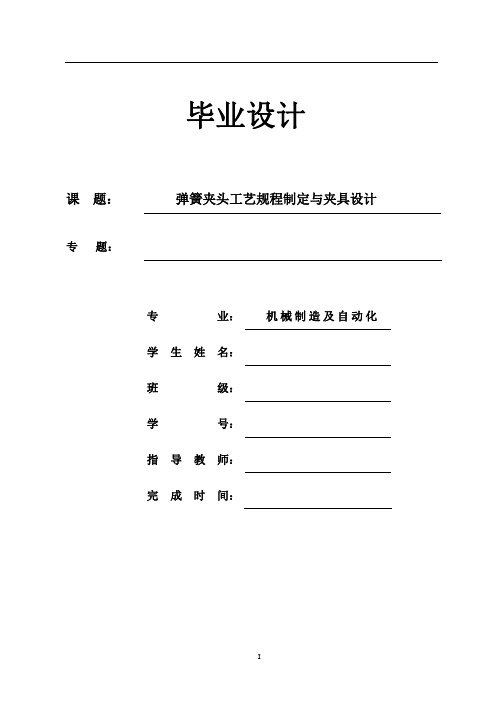
ABSTRACTThe design is based on the body parts of the processing order of the processes and some special fixture design. Body parts of the main plane of the surface and pore system. In general, the plane guarantee processing precision than that of holes machining precision easy. Therefore, this design follows the surface after the first hole principle. Plane with holes and the processing clearly divided into roughing and finishing stages of holes to ensure machining accuracy. Datum selection box input shaft and the output shaft of the supporting hole as a rough benchmark, with top with two holes as a precision technology reference. Main processes arrangements to support holes for positioning and processing the top plane, and then the top plane and the supporting hole location hole processing technology. In addition to the follow-up processes individual processes are made of the top plane and technological hole location hole and plane processing. Supported hole processing using the method of coordinate boring. The whole process of processing machine combinations were selected. Selection of special fixture fixture, clamping means more choice of pneumatic clamping, clamping reliable, institutions can not be locked, so the production efficiency is high, suitable for large batch, line processing, can meet the design requirements.Key words: Angle gear seat parts; fixture; (II)ABSTRACT (III)1 (1)1.1 (1)1.2 (1)1.3 (2)1.4 (2)2 (4)2.1 (4)2.1.1 (4)2.1.2 (4)2.2 (5)2.2.1 (5)2.2.2 (5)2.3 (6)2.3.1 (6)2.3.2 (6)2.4 (7)2.5 (9)2.6 (10)2.7 (10)2.8 (25)3 (27)3.1 (27)3.2 (28)3.3 (29)3.4 (30)3.5 (30)3.6 (31)3.7 (33)3.8 (34) (35) (36) (38)1.1“ ”1.2WTO1.31.41122122.12.1.112.1.221 67 67 mRa 2.32 38 33 38 33 mRa2.33 3mm 3mm m2.3Ra4 262.22.2.12.2.212.32.3.1122.3.22.4c 90800.4%—1.1% 0.25%—0.5% mg 20067 067 038 33 0 38 3370 3X1.180 M33X1.590 52100 26110120 3mm1301401500 670 670 38 330 38 3370 3X1.180 M33X1.590 26100 52110120 3mm1301401500 670 670 38 330 38 3370 3X1.180 M33X1.590 52100 26110120 3mm1301401502.5(1)65Mn(2)2.2-5 “ ” 65Mn HB 170—24111 3.2.230.2 3.2.27 mm.028 ~mm4.37.1 mm12.3.59 mm21 3.2.23mm 4.3~7.1 mm 0.2 3.2.27 mm 28.02.3.59 mm 1 CT7 2.3.9 mm 6.12.6mm , 0 1000mm [2] 6—7 CA6140 [2] 4—3 [2] 2 360° [4] 62.730. 6765Mn CA6140YG61.1 CA6140 200mm 1.30 H B =mm mm 2516 mm 5.4 0V =012 0 =06 v K =090 'v K =010 s =00 s r =mm 8.0. pa mm 2. f1.4mm 16mm 25 p a mm 4 100 400f =0.5 1.0rmm CA6140 4.2—9f =0.7rmm 1—30 CA6140 max F =3530N1.21 174 207HBS p a mm 4 f 75.0 r mm r K =045 R F =950Nf F roFf K =1.0 sFf K =1.0 krFf K =1.17 1.29—2f F =95017.1 =1111.5N 1-2f =r mm 7.0.1.9mm 5.1 T =min 60. 0V1.11 6YG 200 219HBS p a mm 4 f r mm 75.0 V =min 63mtv K =1.0 mv K =0.92 sv K 0.8 Tv K =1.0 Kv K =1.0 1.28'0V =t V v K =63 0.10.184.092.00.10.1 1-3min48m n =D V c '1000=127481000 =120min r 1-4CA61400n =125min rc Vc V =1000c Dn =1000125127 min 50m 1-5.1.25 HBS =160 245 p a mm 3 f r mm 75.0 min 50m VC P =KW7.1 krPc k =0.73 Pc r K 0=0.9C P =1.773.0 =1.2KW 1-6 1.30 n =min 125r E P =KW 9.5 C P E P C620—1p a =3.75mm f =r mm 7.0 n =min 125r =s r 08.2 V =min 50m 40 67YG61.1 C6140 200mm 1.30 H B =mm mm 2516 mm 5.4 0V =012 0 =06 v K =090 'v K =010 s =00 s r =mm 8.0. pa mm 5.2p a =25.2=mm 25.1 . f1.4mm 16mm 25 p a mm 4 100 400f =0.5 1.0rmm CA6140 4.2—9f =0.7rmm 1—30 CA6140 max F =3530N1.21 174 207HBS p a mm 4 f 75.0 r mm r K =045 R F =950Nf F roFf K =1.0 sFf K =1.0 krFf K =1.17 1.29—2f F =95017.1 =1111.5Nf =r mm 7.0.1.9mm 5.1 =min 60. 0V1.11 15YT 200 219HBS p a mm 4 f r mm 75.0 V =min 63mtv K =1.0 mv K =0.92 sv K 0.8 Tv K =1.0 Kv K =1.0 1.28'0V =t V v K =63 0.10.184.092.00.10.1 3-12min48m n =D V c '1000=127100048 =120min r 3-13CA61400n =125minr c Vc V =1000c Dn =1000125127 min 50m 3-14.1.25 HBS =160 245 p a mm 3 f r mm 75.0 min 50m VC P =kw7.1 krPc k =0.73 Pc r K 0=0.9C P =1.773.0 =1.2kw1.30 n =min 125r E P =kw 9.5 C P E P CA6140p a =1.25mm f =r mm 7.0 n =min 125r =s r 08.2 V =min 50m 50 38 33YG61.1 C6140 200mm 1.30 H B =mm mm 2516 mm 5.4 0V =012 0 =06 v K =090 'v K =010 s =00 s r =mm 8.0. pa mm 5.2p a =25.2=mm 25.1 . f1.4mm 16mm 25 p a mm 4 100 400f =0.5 1.0rmm CA6140 4.2—9f =0.7rmm 1—30 CA6140 max F =3530N1.21 174 207HBS p a mm 4 f 75.0 r mm r K =045 R F =950Nf F roFf K =1.0 sFf K =1.0 krFf K =1.17 1.29—2f F =95017.1 =1111.5Nf =r mm 7.0.1.9mm 5.1 =min 60. 0V1.11 15YT 200 219HBS p a mm 4 f r mm 75.0 V =min 63mtv K =1.0 mv K =0.92 sv K 0.8 Tv K =1.0 Kv K =1.0 1.28'0V =t V v K =63 0.10.184.092.00.10.1 3-12min48m n =D V c '1000=127100048 =120min r 3-13CA61400n =125minr c Vc V =1000c Dn =1000125127 min 50m 3-14.1.25 HBS =160 245 p a mm 3 f r mm 75.0 min 50m VC P =kw7.1 krPc k =0.73 Pc r K 0=0.9C P =1.773.0 =1.2kw1.30 n =min 125r E P =kw 9.5 C P E P CA6140p a =1.25mm f =r mm 7.0 n =min 125r =s r 08.2 V =min50m m t =7.0125127 =min 4.1 60 38 3365Mn CA6140YG61.1 CA6140 200mm 1.30 H B =mm mm 2516 mm 5.4 0V =012 0 =06 v K =090 'v K =010 s =00 s r =mm 8.0. pamm 2p a =mm 2 3-1. f1.4mm 16mm 25 p a mm 4 100 400f =0.5 1.0rmm CA6140 4.2—9f =0.7rmm 1—30 CA6140 max F =3530N1.21 174 207HBS p a mm 4 f 75.0 r mm r K =045 R F =950Nf F roFf K =1.0 sFf K =1.0 krFf K =1.17 1.29—2f F =95017.1 =1111.5N3-2f =r mm 7.0.1.9mm 5.1 T =min 60. 0V1.11 6YG 200 219HBS p a mm 4 f r mm 75.0 V =min 63mtv K =1.0 mv K =0.92 sv K 0.8 Tv K =1.0 Kv K =1.01.28'0V =t V v K =63 0.10.184.092.00.10.1 3-3min48m n =D V c '1000=127481000 =120min r 3-4CA61400n =125minr c Vc V =1000c Dn =1000125127 min 50m 3-5.1.25 HBS =160 245 p a mm 3 f r mm 75.0 min 50m VC P =KW7.1 krPc k =0.73 Pc r K 0=0.9C P =1.773.0 =1.2KW3-61.30 n =min 125r E P =KW 9.5 C P E P CA6140p a =3.75mm f =r mm 7.0 n =min 125r =s r 08.2 V =min 50m .sr n 28.370 3X1.1ap ap=1mm2.476 0.05/f a mm z , 2.4-82 23/min V mn100010002345.8/min 3.14160V n r d3.1-74 47.5/minn r v3.1416047.50.40/1000100060Dn v m s f V 0.052447.5/600.95/f f V a Zn mm sm f 0.18/57/min mf f V mm s mm l 3mm l=3mm1j t =573=0.052min=3.12s 100 M33X1.5. pa . f1.4mm 16mm 25 p a mm 4 100 400f =0.5 1.0rmm CA6140 4.2—9f =0.7rmm 1—30 CA6140 max F =3530N1.21 174 207HBS p a mm 4 f 75.0 r mmr K =045 R F =950Nf F roFf K =1.0 sFf K =1.0krFf K =1.17 1.29—2f F =95017.1 =1111.5Nf =r mm 7.0.1.9mm 5.1 =min 60. 0V1.11 15YT 200 219HBS p a mm 4 f r mm 75.0 V =min 63mtv K =1.0 mv K =0.92 sv K 0.8 Tv K =1.0 Kv K =1.0 1.28'0V =t V v K =63 0.10.184.092.00.10.1 3-12min48m n =D V c '1000=127100048 =120min r 3-13 CA61400n =125minr c Vc V =1000c Dn =1000125127 min 50m 3-1490 5265Mn CA6140YG61.1 CA6140 200mm 1.30H B =mm mm 2516 mm 5.4 0V =012 0 =06 v K =090 'v K =010 s =00 s r =mm 8.0. pa mm 2p a =mm 2 3-1. f1.4mm 16mm 25 p a mm 4 100 400f =0.5 1.0rmm CA6140 4.2—9f =0.7rmm 1—30 CA6140 max F =3530N1.21 174 207HBS p a mm 4 f 75.0 r mm r K =045 R F =950Nf F roFf K =1.0 sFf K =1.0 krFf K =1.17 1.29—2f F =95017.1 =1111.5N3-2f =r mm 7.0.1.9mm 5.1 T =min 60. 0V1.11 6YG 200 219HBS p a mm 4 f r mm 75.0 V =min 63mtv K =1.0 mv K =0.92 sv K 0.8 Tv K =1.0 Kv K =1.0 1.28'0V =t V v K =63 0.10.184.092.00.10.1 3-3min48m n =D V c '1000=127481000 =120min r 3-4CA61400n =125minr c Vc V =1000c Dn =1000125127 min 50m 3-5.1.25 HBS =160 245 p a mm 3 f r mm 75.0 min 50m VC P =KW7.1 krPc k =0.73 Pc r K 0=0.9C P =1.773.0 =1.2KW3-61.30 n =min 125r E P =KW 9.5 C P E P CA6140p a =3.75mm f =r mm 7.0 n =min 125r =s r 08.2 V =min50m.sr n 28.310026p a 13p a mmf 2.4.39 r mm f /25.0 V 2.4.41 s m V /45.0 n 010*******.4560782/min 3.1426V n r d min/500r n V 0 3.14265000.29/1000100060d n V m s l mml 20 1l mm ctg ctgk D l r 2.52120211)2~1(21 2l 02 l 11j t min 20.050025.02.520211fn l l l t j 11065MnX52K[7] 30—3415YT 100D mm 8ZZ=2mmp a 2p a mmf a [3] 2.4-75 0.12/f a mm Z V [7] 30—34 1.33/V m sn 1000Vn d 2.1V—d—2.1 n10001000 1.3360254/min 3.14100V n r d[3] 3.1-74300/min n r v3.14100300 1.57/1000100060dn v m s f V 0.128300/604.8/f f V a Zn mm sm f 4.8/288/min mf f V mm s mm a [7] 2.4-81,40a mm120 3mmKX 5211p a 1.5p a mm[3] 2.476 0.06/f a mm z ,[1] 3032 24/min V mn100010002462.1/min 3.1410V n r d[3] 3.1 74 75/minn r v 3.1410750.50/1000100060dn v m s f V 0.061875/60 1.35/f f V a Zn mm sm f 1.35/81/minm f f V mm s mm 11j t 12120632 1.05min 81j m l l l t f 2.810 240 417 420 8 1.14min2.5.2N t k t t t zz f j d /%)1)(( 0/ N t zz%)1)((k t t t f j d d t — j t —f t —k —j t min73.1 j t f t 2.5.43min 15.0 min 1.0 min25.01.015.0 f t k 2.5.48 13k d tmin14.1min 24.2%)131)(25.073.1(%)1)(( k t t t f j dmin 14.1min 12.1224.22 d d t tj t min53.0 j t f t 2.5.65Mn min 31.0 min 1.0 min41.01.031.0 f t k 2.5.48 13 k d tmin14.1min 06.1%)131)(41.053.0(%)1)(( k t t t f j dj t min53.0 j t f t 2.5.65Mn min 31.0 min 1.0 min41.01.031.0 f t k 2.5.48 13 k d tmin14.1min 06.1%)131)(41.053.0(%)1)(( k t t t f j d3.12612345Z3.24.24.2H7/h620Mn2 HRC60 :12.5F7*22K6*35GB2264-198012*18 GB2263-1980T10A HRC60 H7/p63.3:1 H7/n62 F7/m6 F7/k634C4.34.3C=(0.3 1.2)dC=8 C3.4[4]3.51/3[5] [6]min D W D d2D dD Wmin0.052D mm 0.011d mm min 0mm0.063D W mmcos )(min max y y j jmmS N c HB K R k mnZHBaZ RaZ y 014.081.9])[(1 cos 0.013j j y mmM j mm 005.0 A D mm 01.0 0.0960.5j w mm mm3.6d D D1H tF7D60 13+0.010+0.004611.8471.82.65869--2.6 3+0.016 +0.0063 3.36+0.016+0.00893.347104 5811812165 6+0.022+0.01010+0.019+0.010136 81215101628 10+0.028+0.013151810 1218+0.023+0.0122212202512 1522260.00815 18+0.034+0.016263016283618 2230+0.028+0.0153422 +0.041+0.02035+0.033392036A30.0122626 30424630 3548+0.0175225A 35635 42555942 48626648 50+0.050+0.02570+0.039+0.020743056670.043.7123453.8V1234[1] 1982. (1)[2] [M] 1984 20-23[3] [M] 1983 42-50[4] [ ] 1992[5] 1 [M] 1991[6] [M] 1979[7] [M] 1990[8] [M] 1994[9] [M] 1984[10] [M] 2002[11] , ( ) [M], ,2003.1[12] [M] 1995[13] [M] 1980[14] [M] 1991[15] [M] 2000 9-19[16] , , , ,1979.12[17] 2005 4-17[18] Machine Tools N.chernor 1984.[19] Machine Tool Metalworking John L.Feirer 1973.[20] Handbook of Machine Tools Manfred weck 1984 .[21] Sors l.fatigue design of machine components.oxford:pergramon press.1971!。
弹簧夹头工艺设计说明书
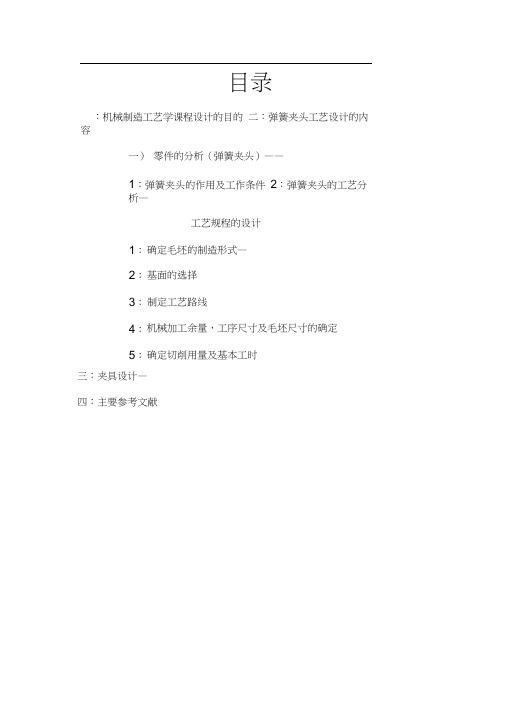
目录:机械制造工艺学课程设计的目的二:弹簧夹头工艺设计的内容一)零件的分析(弹簧夹头)——1:弹簧夹头的作用及工作条件2:弹簧夹头的工艺分析—工艺规程的设计1:确定毛坯的制造形式—2:基面的选择3:制定工艺路线4:机械加工余量,工序尺寸及毛坯尺寸的确定5:确定切削用量及基本工时三:夹具设计—四:主要参考文献:机械制造工艺学课程设计的目的培养分析解决生产技术问题的能力,初步掌握设计工艺规程和机床夹具的基本方法,并巩固、深化已学得的理论知识,进一步培养熟悉和运用有关图册、图表等技术资料的能力,训练识图、制图、运算及编制技术文件的基本技能。
:弹簧夹头工艺设计的内容一)零件的分析(弹簧夹头)1:弹簧夹头的作用及工作条件本次课程设计所采用的零件为弹簧夹头其作用如下:能精确的定位与夹紧工件(或刀具),具有抵抗扭矩和承受来自多方向切削力的功能。
具有增大驱动力(拉力)和转换驱动力为工件(或刀具)夹紧力的功能。
具有快速松开工件(或刀具)的功能。
具有在不降低加工精度和使工件不受损害前提下的高重复精度。
具有能在较宽的主轴转速范围内工作与只有极小的夹紧力损失的能力。
在高速切削中的转动惯量最小。
弹簧夹头通常在装有机床主轴的孔内使用,在工作中弹簧夹头必须保持与工件(或刀具)的定位基准相同如主轴。
弹簧夹头和工件或刀具)之间的相对运动将导致不正确的零件加工。
弹簧夹头与工件(或刀具)的相对转动或相对轴向移动都回使加工工件尺寸的一致性和几何精度受到影响。
弹簧夹头采用弹性较好的优质合金钢制成,并经热处理使头部外锥与夹爪内壁有较高硬度以保证坚硬耐磨。
每种规格的弹簧夹头所能夹紧工件的尺寸范围很小,所以它的应用范围很广,消耗量较大,适用于自动车床、万能铣床、螺纹磨床等各类设备。
2:弹簧夹头的工艺分析2)弹簧夹头的生产工艺特点分析:该零件的生产纲领:N=Q n (1+ a%+ 3 %式中N ――零件的年生产纲领(件/台);Q——产品的年产量(台/年);n――每台产品中,该零件的数量(件/台);a%—备品率;3%—废品率;设Q=4000,n=1, a% = 1 0 %, 3% = 1 %由上式可算得N=4440 件根据设计任务书的要求,制定零件在中批生产条件下的机械加工工艺规程,可制定该零件的年生产纲领为4440(件/年)。
弹簧套筒钻夹头工作原理

弹簧套筒钻夹头工作原理弹簧夹头设计图及工作原理1. 向固定式弹簧夹头夹头体1以锥柄插入机床主轴锥孔中,简夹2轴向固定。
旋紧螺母3,其内锥面迫使筒夹收缩将工件夹紧;反转螺母,简夹弹开,松开工件。
螺母与筒夹之间有相对转动,其配合锥面易于磨损,适用于轻便及一般工件加工。
限于筒夹的扩张量,工件基准面公差应不大于0.5毫米。
螺钉4用以防止简夹转动。
2. 向移动式弹簧夹头旋紧螺母时,简夹作轴向移动便夹紧工件。
支承钉用于工件轴向定位。
由于简夹与工件间有相对轴向位移,故其夹头工作表面易于磨损,适用于—般工作。
3. 间锥套式弹簧夹头中间锥套5置于夹头体1与筒夹2之间,并以销4作圆周固定。
转动螺母3,通过螺母内端面(或销6),使锥套作轴向移动,从而使筒夹收缩(或张开)。
4. 槽锥套式弹簧夹头以纵向切槽的锥套2代替筒夹。
旋紧螺母3时,其内锥面迫使锥套收缩夹紧工件。
适用于一般工作。
5. 端作用式弹簧夹头(1)筒夹两端均有卡爪。
旋紧螺母5时,由于夹头体3及锥套7内锥面作用,使两端卡爪同时收缩夹紧工件。
两个销6用防以防止锥套随螺母转动,弹簧2使筒夹4复位,支钉1用于工件轴向定位。
适于夹持较长的工件。
6. 端作用式弹簧夹头(2)两端带锥面的筒夹3与相应的锥套1和4相配。
当转动带左右螺纹的螺母5时,通过衬套7推动套4和简夹3左移,使简夹两端同时收缩夹紧工件;反转螺母5时,借弹簧作用松开工件。
键6用以圆周固定衬套7。
7. 紧式弹簧夹头通过主轴孔的拉杆与筒夹尾部的螺纹孔连接。
拉杆轴向移动(手动或机动)使简夹作径向收缩(或张开),以夹紧(或松开)工件。
工件无轴向定位。
8. 利用插头扳手操纵的弹簧夹头简夹5以尾部螺纹旋入锥齿轮3的螺孔中,并以圆销4作圆周固定,利用环2将锥齿轮3轴向固定于夹头体1中。
用插头扳手转动小锥齿轮6使筒夹作轴向移动,从而实现工件的夹紧〔或放松〕。
9. 手轮传动的弹簧夹头简夹7以尾邻螺纹旋入齿轮1螺孔中,并以键8作圆周固定。
弹簧夹头课程设计
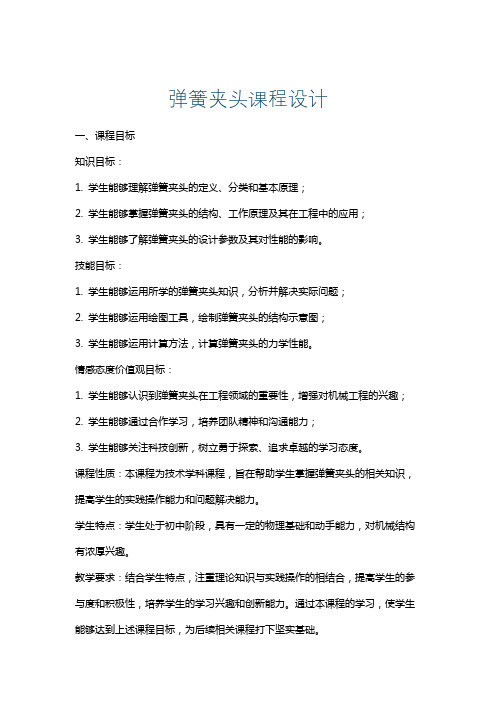
弹簧夹头课程设计一、课程目标知识目标:1. 学生能够理解弹簧夹头的定义、分类和基本原理;2. 学生能够掌握弹簧夹头的结构、工作原理及其在工程中的应用;3. 学生能够了解弹簧夹头的设计参数及其对性能的影响。
技能目标:1. 学生能够运用所学的弹簧夹头知识,分析并解决实际问题;2. 学生能够运用绘图工具,绘制弹簧夹头的结构示意图;3. 学生能够运用计算方法,计算弹簧夹头的力学性能。
情感态度价值观目标:1. 学生能够认识到弹簧夹头在工程领域的重要性,增强对机械工程的兴趣;2. 学生能够通过合作学习,培养团队精神和沟通能力;3. 学生能够关注科技创新,树立勇于探索、追求卓越的学习态度。
课程性质:本课程为技术学科课程,旨在帮助学生掌握弹簧夹头的相关知识,提高学生的实践操作能力和问题解决能力。
学生特点:学生处于初中阶段,具有一定的物理基础和动手能力,对机械结构有浓厚兴趣。
教学要求:结合学生特点,注重理论知识与实践操作的相结合,提高学生的参与度和积极性,培养学生的学习兴趣和创新能力。
通过本课程的学习,使学生能够达到上述课程目标,为后续相关课程打下坚实基础。
二、教学内容1. 弹簧夹头的概念与分类- 弹簧夹头的定义及其在机械工程中的应用- 弹簧夹头的分类及各类特点2. 弹簧夹头的结构与工作原理- 弹簧夹头的结构组成及各部分功能- 弹簧夹头的工作原理及力学性能分析3. 弹簧夹头的设计参数与性能- 弹簧夹头设计参数的选择方法- 设计参数对弹簧夹头性能的影响4. 弹簧夹头的应用案例分析- 案例介绍:弹簧夹头在不同工程领域的应用- 案例分析:弹簧夹头的选型与性能评价5. 弹簧夹头的绘制与计算- 弹簧夹头结构示意图的绘制方法- 弹簧夹头力学性能的计算方法教学内容安排与进度:第一课时:弹簧夹头的概念与分类第二课时:弹簧夹头的结构与工作原理第三课时:弹簧夹头的设计参数与性能第四课时:弹簧夹头的应用案例分析第五课时:弹簧夹头的绘制与计算本教学内容基于课程目标,结合教材相关章节,确保了知识的科学性和系统性。
车床上碟簧作动力时弹簧夹头夹紧及松开机构设计(全套图纸)

优秀机械毕业设计CAD图纸通过答辩QQ 194535455毕业设计说明书(论文)中文摘要摘要:本文是设计了一种车床用碟形弹簧做动力时弹簧夹头夹紧及松开机构。
该机构主要由弹簧夹头、拉杆、碟形弹簧、气动三联件等几部分组成。
工作原理主要是通过螺母套对碟形弹簧施加一定的轴向力,碟形弹簧安装在拉杆上,间接对拉杆产生推动力推动推承套向右移动,推成套装配在弹簧夹头上,弹簧夹头与法兰相接触,利用推承套上的锥度形状将轴向力转换成径向力,使弹簧夹头产生夹紧力对工件实现夹紧。
再通过气动三联件对气缸活塞杆产生推动力,而活塞杆与拉杆通过拨块相连接,所产生的推动力大于螺母套施加的力,拉杆得以向左移动,推承套失去推动力与弹簧夹头分离,弹簧夹头实现对工件的松开。
而本次设计的夹具与以往的卡爪式夹紧松开机构相比较,拥有更好的平衡性能、夹紧牢靠、结构紧凑、便于操作、加工及更换方便等主要优点。
在主轴高速旋转的情况下,也能达到需要的平衡要求。
是高效率和良好精度特点的现代车床夹具,可以有效地减少时间基本和配套工件加工的时间,大大提高了劳动生产率,有效地降低了劳动强度。
关键词:数控车床夹紧机构弹簧夹头夹紧动力毕业设计说明书(论文)英文摘要Title Design Control collet chuck clamping and release mechanism is in a lathe powered by a conical springAbstractThis article is designed to do when one kind of lathe with power disc spring collet chuck clamping and release mechanism. The agency consists of several parts collets, rod, disc springs, pneumatic FRL and other components. Works mainly on the disc springs exert a certain axial force through the nut sleeve, disc springs mounted on the rod, the rod indirectly generate driving force pushing the push bearing sleeve moves to the right, push the spring clip assembly head sets, spring chuck in contact with the flange using push bearing sleeve taper shape of the axial force is converted into a radial force, so that collet chuck generate clamping force on the workpiece clamping realization. And then the driving force generated by the cylinder piston rod pneumatic FRL, and the piston rod and the rod is connected by dialing block, the driving force is greater than the force exerted by the nut sleeve, lever to move to the left, push the bearing sleeve lose impetus with the spring chuck separation collets achieve workpiece release.The design of the fixture and conventional jaw clamp release mechanism compared with a better balance of performance, clamping reliable, compact, easy to operate, processing and easy replacement of major advantages. In the case of the main shaft rotates at high speed, but also to achieve the desired balance requirements. Modern lathe fixture high efficiency and good accuracy characteristics, can effectively reduce the time basic and auxiliary workpiece machining time, greatly improving labor productivity, effectively reducing labor intensity.Keywords:CNC lathes Clamping mechanism Collet chuck Clamping force目录目录 (I)前言 (1)第一章绪论 (2)1.1车床夹具及其应用 (2)1.1.1车床夹具的概述 (2)1.1.2车床夹具的分类 (3)1.1.3车床夹具的组成 (4)1.2选题目的和意义 (4)1.3国内外的研究现状和发展趋势 (6)1.3.1弹簧夹头的发展 (6)1.4车床上用碟簧作动力时弹簧夹头夹紧及松开机构。
后钢板弹簧工艺与夹具设计说明
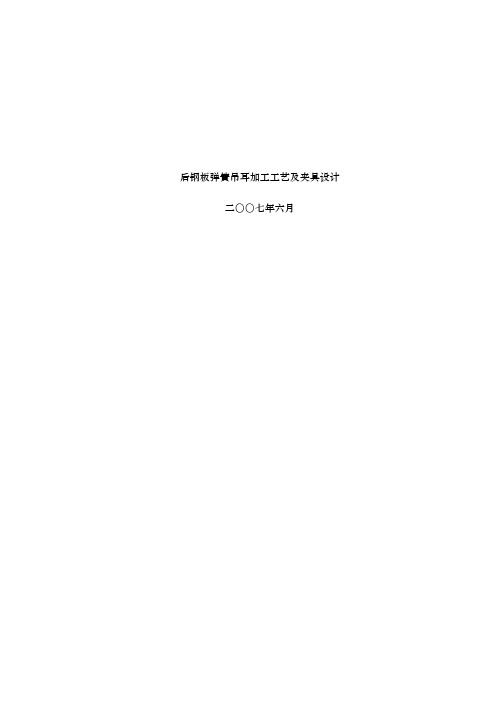
后钢板弹簧吊耳加工工艺及夹具设计二〇〇七年六月摘要本次设计是对后钢板弹簧吊耳零件的加工工艺规程及一些工序的专用夹具设计。
后钢板弹簧吊零件的主要加工表面是平面及孔。
由加工工艺原则可知,保证平面的加工精度要比保证孔的加工精度容易。
所以本设计遵循先面后孔的原则。
并将孔与平面的加工明确划分成粗加工和精加工阶段以保证加工精度。
基准选择以后钢板弹簧吊耳大外圆端面作为粗基准,以后钢板弹簧吊耳大外圆端面与两个工艺孔作为精基准。
主要加工工序安排是先以后钢板弹簧吊耳大外圆端面互为基准加工出端面,再以端面定位加工出工艺孔。
在后续工序中除个别工序外均用端面和工艺孔定位加工其他孔与平面。
整个加工过程均选用组合机床。
关键词后钢板弹簧吊耳,加工工艺,专用夹具目录摘要 (Ⅰ)ABSTRACT .............................................................. 错误!未定义书签。
目录 (1)1绪论 (1)2 后钢板弹簧吊耳加工工艺规程设计 (3)2.1零件的分析 (3)2.1.1零件的作用 (3)1.1.2零件的工艺分析 (3)2.2工艺过程设计所应采取的相应措施 (4)2.3后钢板弹簧吊耳加工定位基准的选择 (4)2.3.1 确定毛坯的制造形式 (4)2.3.2粗基准的选择 (4)2.3.3精基准的选择 (5)2.4工艺路线的制定 (5)2.4.1 工艺方案一 (5)2.4.2 工艺方案二 (6)2.4.3 工艺方案的比较与分析 (6)2.5机械加工余量、工序尺寸及毛坯尺寸的确定 (7)2.6确定切削用量及基本工时(机动时间) (8)2.7时间定额计算及生产安排 (16)2.8本章小结 (19)3 粗铣后钢板弹簧吊耳侧端面夹具设计 (20)3.1粗铣后钢板弹簧吊耳侧端面夹具设计 (20)3.2定位方案的分析和定位基准的选择 (20)3.3定位误差分析 (21)3.4铣削力与夹紧力计算 (21)3.5定向键与对刀装置设计 (22)3.6夹紧装置及夹具体设计 (24)3.7夹具设计及操作的简要说明 (25)3.8本章小结 (25)φ工艺孔夹具设计 (26)4 加工30mmφ工艺孔夹具设计 (26)4.1加工30mm4.2定位方案的分析和定位基准的选择 (26)4.4切削力的计算与夹紧力分析 (27)4.5钻套、衬套、钻模板及夹具体设计 (27)4.6夹具精度分析 (29)4.7夹具设计及操作的简要说明 (30)4.8本章小结 (30)φ工艺孔夹具设计 (31)5 加工10.5mmφ工艺孔夹具设计 (31)5.1加工10.5mm5.2定位方案的分析和定位基准的选择 (31)5.3定位元件的设计 (31)5.4定位误差分析 (33)5.5切削力的计算与夹紧力分析 (33)5.6钻套、衬套、钻模板及夹具体设计 (34)5.7夹具精度分析 (35)5.8夹具设计及操作的简要说明 (36)5.9本章小结 (36)结论 (37)参考文献 (38)致......................................................................... 错误!未定义书签。
弹簧夹头工艺设计说明书

目录一:机械制造工艺学课程设计的目的——————————1 二:弹簧夹头工艺设计的内容—————————————1 (一)零件的分析(弹簧夹头)————————1:弹簧夹头的作用及工作条件—————————2:弹簧夹头的工艺分析————————————(二)工艺规程的设计————————————1:确定毛坯的制造形式————————————2:基面的选择————————————————3:制定工艺路线————————————————4:机械加工余量,工序尺寸及毛坯尺寸的确定——5:确定切削用量及基本工时———————————三:夹具设计————————————————————四:主要参考文献——————————————————一:机械制造工艺学课程设计的目的培养分析解决生产技术问题的能力,初步掌握设计工艺规程和机床夹具的基本方法,并巩固、深化已学得的理论知识,进一步培养熟悉和运用有关图册、图表等技术资料的能力,训练识图、制图、运算及编制技术文件的基本技能。
二:弹簧夹头工艺设计的内容(一)零件的分析(弹簧夹头)1:弹簧夹头的作用及工作条件本次课程设计所采用的零件为弹簧夹头其作用如下:(1)能精确的定位与夹紧工件(或刀具),具有抵抗扭矩和承受来自多方向切削力的功能。
(2)具有增大驱动力(拉力)和转换驱动力为工件(或刀具)夹紧力的功能。
(3)具有快速松开工件(或刀具)的功能。
(4)具有在不降低加工精度和使工件不受损害前提下的高重复精度。
(5)具有能在较宽的主轴转速范围内工作与只有极小的夹紧力损失的能力。
(6)在高速切削中的转动惯量最小。
弹簧夹头通常在装有机床主轴的孔内使用,在工作中弹簧夹头必须保持与工件(或刀具)的定位基准相同如主轴。
弹簧夹头和工件(或刀具)之间的相对运动将导致不正确的零件加工。
弹簧夹头与工件(或刀具)的相对转动或相对轴向移动都回使加工工件尺寸的一致性和几何精度受到影响。
弹簧夹头采用弹性较好的优质合金钢制成,并经热处理使头部外锥与夹爪内壁有较高硬度以保证坚硬耐磨。
弹簧夹头说明书
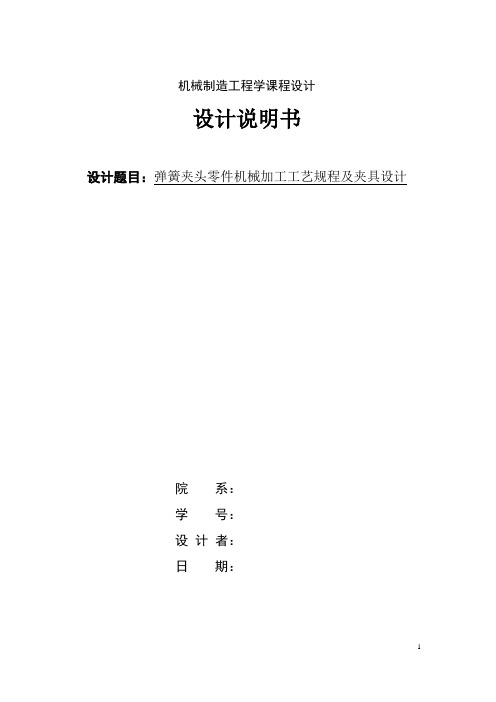
机械制造工程学课程设计设计说明书设计题目:弹簧夹头零件机械加工工艺规程及夹具设计院系:学号:设计者:日期:目录1零件工艺分析 (3)1.1零件的作用 (3)1.2零件的工艺分析 (3)2工艺规程设计及计算 (5)2.1毛坯制造 (5)2.2基准选择 (5)2.3工艺路线拟定 (5)2.4机械加工余量、工序尺寸及毛坯尺寸的确定 (6)2.5切削用量的确定 (7)2.6工艺文件填写 (10)3夹具设计 (11)3.1设计要求 (11)3.2夹具的设计 (11)3.3该夹具的简要说明 (11)4总结 (12)参考文献 (13)1零件工艺分析1.1零件的作用本次课程设计所采用的零件为弹簧夹头其作用如下:(1)能精确的定位与夹紧工件(或刀具),具有抵抗扭矩和承受来自多方向切削力的功能。
(2)具有增大驱动力(拉力)和转换驱动力为工件(或刀具)夹紧力的功能。
(3)具有快速松开工件(或刀具)的功能。
(4)具有在不降低加工精度和使工件不受损害前提下的高重复精度。
(5)具有能在较宽的主轴转速范围内工作与只有极小的夹紧力损失的能力。
(6)在高速切削中的转动惯量最小。
弹簧夹头通常在装有机床主轴的孔内使用,在工作中弹簧夹头必须保持与工件(或刀具)的定位基准相同如主轴。
弹簧夹头和工件(或刀具)之间的相对运动将导致不正确的零件加工。
弹簧夹头与工件(或刀具)的相对转动或相对轴向移动都会使加工工件尺寸的一致性和几何精度受到影响。
弹簧夹头采用弹性较好的优质合金钢制成,并经热处理使头部外锥与夹爪内壁有较高硬度以保证坚硬耐磨。
每种规格的弹簧夹头所能夹紧工件的尺寸范围很小,所以它的应用范围很广,消耗量较大,适用于自动车床、万能铣床、螺纹磨床等各类设备。
1.2零件的工艺分析假设生产类型为中批生产,由生产类型可知该零件的工艺特点为:毛坯的制造方法部分铸件用金属模,部分锻件用模锻,毛坯精度中等,加工余量中等;机床通常采用通用机床,部分采用专用机床;夹具广泛使用专用夹具和可调夹具;刀具和量具按零件产量和精度,部分采用通用刀具和量具,部分采用专用刀具和量具;工件的装夹方法部分采用划线找正,广泛采用通用或专用夹具装夹。
- 1、下载文档前请自行甄别文档内容的完整性,平台不提供额外的编辑、内容补充、找答案等附加服务。
- 2、"仅部分预览"的文档,不可在线预览部分如存在完整性等问题,可反馈申请退款(可完整预览的文档不适用该条件!)。
- 3、如文档侵犯您的权益,请联系客服反馈,我们会尽快为您处理(人工客服工作时间:9:00-18:30)。
目录1.机械制造工艺学课程设计的目的 (3)2.弹簧夹头工艺设计的内容 (4)2.1零件的分析(弹簧夹头) (4)2.1.1弹簧夹头的作用及工作条件 (4)2.2弹簧夹头的工艺分析 (5)2.2.1弹簧夹头的生产工艺特点分析 (5)2.2.2弹簧夹头的主要加工表面及设计基准分析 (5)3工艺规程的设计 (7)3.1确定毛坯的制造形式 (7)3.2基面的选择 (7)3.3制定工艺路线 (7)3.4机械加工余量、工序尺寸及毛坯尺寸的确定 (9)3.4.1外圆表面(Ф32,Ф36及锥面) (9)3.4.2外圆表面沿长度方向的加工余量(Ф36的端面) (9)3.4.3内孔 (9)3.4.4确定切削用量及基本工时 (10)参考文献 (14)1.机械制造工艺学课程设计的目的培养分析解决生产技术问题的能力,初步掌握设计工艺规程和机床夹具的基本方法,并巩固、深化已学得的理论知识,进一步培养熟悉和运用有关图册、图表等技术资料的能力,训练识图、制图、运算及编制技术文件的基本技能。
2.弹簧夹头工艺设计的内容2.1零件的分析(弹簧夹头)2.1.1弹簧夹头的作用及工作条件本次课程设计所采用的零件为弹簧夹头其作用如下:(1)能精确的定位与夹紧工件(或刀具),具有抵抗扭矩和承受来自多方向切削力的功能。
(2)具有增大驱动力(拉力)和转换驱动力为工件(或刀具)夹紧力的功能。
(3)具有快速松开工件(或刀具)的功能。
(4)具有在不降低加工精度和使工件不受损害前提下的高重复精度。
(5)具有能在较宽的主轴转速范围内工作与只有极小的夹紧力损失的能力。
(6)在高速切削中的转动惯量最小。
弹簧夹头通常在装有机床主轴的孔内使用,在工作中弹簧夹头必须保持与工件(或刀具)的定位基准相同如主轴。
弹簧夹头和工件(或刀具)之间的相对运动将导致不正确的零件加工。
弹簧夹头与工件(或刀具)的相对转动或相对轴向移动都回使加工工件尺寸的一致性和几何精度受到影响。
弹簧夹头采用弹性较好的优质合金钢制成,并经热处理使头部外锥与夹爪内壁有较高硬度以保证坚硬耐磨。
每种规格的弹簧夹头所能夹紧工件的尺寸范围很小,所以它的应用范围很广,消耗量较大,适用于自动车床、万能铣床、螺纹磨床等各类设备。
2.2弹簧夹头的工艺分析2.2.1弹簧夹头的生产工艺特点分析该零件的生产纲领:N=Qn (1+α%+β %)式中 N——零件的年生产纲领(件/台);Q——产品的年产量(台/年);n——每台产品中,该零件的数量(件/台);α%—备品率;β%—废品率;设Q=1000,n=1, α%=10%,β%=1%由上式可算得N=1110件根据设计任务书的要求,制定零件在中批生产条件下的机械加工工艺规程,可制定该零件的年生产纲领为1110(件/年)。
生产类型为中批生产。
由生产类型可知该零件的工艺特点为:毛坯的制造方法部分铸件用金属模,部分锻件用模锻,毛坯精度中等,加工余量中等;机床通常采用通用机床,部分采用专用机床;夹具广泛使用专用夹具和可调夹具;刀具和量具按零件产量和精度,部分采用通用刀具和量具,部分采用专用刀具和量具;工件的装夹方法部分采用划线找正,广泛采用通用或专用夹具装夹。
2.2.2弹簧夹头的主要加工表面及设计基准分析弹簧夹头为了保证其精度,它的Φ20的孔与30°的外圆锥表面与图中A面有一定的要求.三个等分槽也有一定的要求.现分述如下:a.应保证Φ20的孔与30°的外圆锥表面与图中A面与B面的圆跳动为0.015.A面的表面粗糙度为0.4.b.三个等分槽加工时应有两个焊用销子分别是直径为Φ5.0和Φ7.2的,插入Φ6的孔中,用来涨大和缩小该孔.完工时Φ6必须扩大至Φ7.2.由以上分析可知,应先加工A面的外圆,再以该圆为基准,加工Φ20的孔与30°的外圆锥表面 .三个等分槽加工时应要先扩再缩,用焊接来实现.3工艺规程的设计3.1确定毛坯的制造形式选取弹簧夹头的制造材料为弹簧钢,其具有优良的综合性能,如力学性能(特别是弹性极限、强度极限、屈强比)、抗弹减性能(即抗弹性减退性能,又称抗松弛性能)、疲劳性能、淬透性、物理化学性能(耐热、耐低温、抗氧化、耐腐蚀等)。
由前面可知其生产类型为中批生产,所以毛坯采用模锻件。
3.2基面的选择基面选择是工艺规程设计中重要工作之一。
基面选择的正确与合理可以使加工质量得到保证、生产率得到提高。
否则不但加工工艺过程中的问题百出,更有甚者还会造成零件大批报废使生产无法正常进行。
a.粗基准的选择:因为弹簧夹头的毛坯属于轴类零件,所以应选择外圆为粗基准.b.精基准的选择:精基准的选择主要应该考虑基准重合的问题.当设计基准与工序基准不重合时,应该进行尺寸换算.3.3制定工艺路线制定工艺路线的出发点是应当使零件的几何形状、尺寸精度及位置精度等技术要求能得到妥善保证,在生产纲领已经确定为成批生产的条件下,可以考虑采用万能性机床配以专用工夹具,并尽量使工序集中来提高生产率,除此之外还应当尽量考虑经济效果,以便使生产成本尽量下降。
工艺路线方案:工序1: 车焊用销子(Φ5.0)(Φ7.2)工序2: 夹外圆分别车外圆各部及锥面(须精加工的留磨量0.5mm),孔除须配合的孔留0.5mm磨量外,其余干到图纸尺寸。
工序3:钻孔(Ф10)。
工序4: 粗镗﹑细镗内孔,达到图纸要求.工序5:攻M12的内螺纹.工序6: 钻槽端部3个均布的小孔。
工序7: 铣三等份槽但不铣通,端面留4~5mm量。
工序8: 去毛刺.工序9: 淬火HRC45,发蓝。
工序10: 两端倒角.工序11: 焊三点,涨大(Φ7.2)工序12: 割开焊点.工序13: 去毛刺.工序14: 焊三点,缩小(Φ5.0)工序15: 顶两端倒角处磨外圆及锥面至尺寸。
工序16: 夹外圆磨内孔至尺寸。
工序17: 上磨床割开三条均布槽,去销子.工序18: 去毛刺.工序19: 刻标记.工序20: 终检、入库。
3.4机械加工余量、工序尺寸及毛坯尺寸的确定弹簧夹头所使用的材料为60Si2MnA,硬度为〉HV500,毛坯重量约为1kg,生产类型为中批生产,采用模锻毛坯3级精度组(成批生产)。
根据上述原材料及加工工艺分别对各加工表面的机械加工余量、工序尺寸及毛坯尺寸确定如下:3.4.1外圆表面(Ф32,Ф36及锥面)Ф32的外圆长度为30mm,结合Ф32的外圆为了简化模锻毛坯的外形,现直接取外圆毛坯直径为Ф50,长度取为80。
Ф32表面为自由尺寸公差,其表面粗糙度要求为3.2,只要求粗加工,此时留模量0.5mm可以满足要求。
Ф36外圆表面是需要保证的尺寸,需要进行精加工,精度等级为4,此时留模量为0.4mm 可以满足要求.结合锥面的最大直径及加工方法,考虑模锻毛坯外形的简化,可以去毛坯直径为Ф50,长度取为20,考虑到节省材料及零件尺寸要求,由以上分析可确定毛坯图(见附图)。
3.4.2外圆表面沿长度方向的加工余量(Ф36的端面)结合零件图查表,长度余量及公差分别取0为上偏差,-0.011下偏差3..4.3内孔毛坯是带有Ф10孔的棒料,其中Ф26的内孔精度要求不高,其中Ф20的内孔及M12的螺纹孔精度要求较高,精度等级介于IT7——IT8之间,参照机械制造工艺手册表1-29及表1-34确定工序尺寸及余量。
对于Ф20的孔:扩钻Ф19.5 2Z=1精镗Ф19.8 2Z=0.1细镗Ф20上偏差+0.021下偏差0 2Z=0.1对于Ф26的孔:钻孔25 2Z=7扩钻26 2Z=1对于M12的螺纹孔:直接用攻丝刀攻螺纹即可。
3.4.4确定切削用量及基本工时工序1:车两根焊用销子(Φ5.0, Φ7.2)这两根销子是用来涨大和缩小孔Φ5.0的,起个支撑的作用.故粗糙度也不高,直接加工出来就行了.工序2:车外圆及端面本工序采用计算法①加工条件工件材料60Si2MnA,模锻。
加工要求:车Ф36及Ф32端面,粗车外圆Ф32、Ф36及圆锥面。
机床:CA6140普通车床刀具:断面车刀:刀片材料YT15,刀杆尺寸16X25平方毫米,Kr=90度,γ0=15,α0=12,rε=0.05mm②计算切削用量粗车端面ⅰ:根据零件图及加工要求直接加工到尺寸ⅱ:走刀量f=0.4mm/r(表3-13)ⅲ:计算切削速度(表3-18)耐用度t=45minV=163m/minⅳ:确定机床主轴转速Ns=13.3r/s按机床选取机床主轴转速760r/min(表14-3)所以实际切削速度v=2.57m/s(154.4m/min)粗车外圆工序3:内孔加工(Φ20mm,Φ26mm)<1> 钻内孔为Φ20 mm,钻通.f=0.42mm/r,Klf=0.42*0.9=0.38mm/r(表3-38)v=0.25m/s(15m/min)(表3-42)Ns=1000v/πDw=250/31.4=7.96r/s按机床选取Nw=7.65r/s所以实际切削速度V=(π×10×7.65)÷1000=0.24m/s切削加工时:切入L1=32mm,切出L2=2mm L=40mmTm=(L+L1+L2)÷(Nw×f)=24.9s<2> 由于Φ20mm的孔要与别的零件(也就是刀具)相配合,故其精度要求比较高,所以得留下0.05mm的精磨余量.也就是在本工序把此孔加工到Φ19.95mm f=0.1mm/rNw=1000r/min(16.6r/s)v=122.2m/min(2.03m/s)切削工时(一个孔):(表7-1)L=9mm,L1=2mm,L2=1mmTm=(L+L1+L2)÷(Nw×f)=7.23s精镗孔至Ф20上偏差+0.021下偏差0选用一个刀杆,利用M120W外圆磨床同时对工件进行精磨孔,故切削用量及工时都与前面相同即:f=0.1mm/rNw=1000r/min(16.6r/s)Tm=7.23s<3> 加工孔Φ26mm,此孔由于不与别的零件配合,故粗糙度要求不高,直接车出来要求尺寸Φ26mm就行了.加工方法粗车。
工序4:攻M12的螺纹v=0.123m/s(表3-42)所以Ns=4.89r/s(293r/min)按机床选取Nw=272r/min则实际切削速度v=0.113m/s。
工序5:钻三孔(Φ6mm)由于此三孔不与别的零件配合,故直接钻到要求的尺寸Φ6mm即可.对于每一个孔:f=0.42mm/r,Klf=0.42*0.9=0.38mm/r(表3-38)v=0.25m/s(15m/min)(表3-42)Ns=1000v/πDw=250/31.4=7.96r/s按机床选取Nw=7.65r/s所以实际切削速度V=(π×10×7.65)÷1000=0.24m/s切削工时:切入L1=6mm,切出L2=2mm L=3.5mmTm=(L+L1+L2)÷(Nw×f)=3s工序6:铣三槽此三槽由于也不与别的零件配合,故可用1mm的成型铣刀直接加工出来. 注:以上所出现的表都见参考文献4。