影响碳钢的变形抗力和塑性的因素分析
碳钢热处理后的组织和性能变化的分析实验

碳钢热处理后的组织和性能变化的分析实验一、实验目的1、观察和研究碳钢经不同形式热处理后其显微组织的特点。
2、了解热处理工艺对钢组织和性能的影响。
3、了解硬度测定的基本原理及应用范围。
4、了解洛氏硬度试验机的主要结构及操作方法。
5、掌握金属显微试样的制作过程,正确地制作所要观察的试件。
二、实验内容1、制作经热处理后的试样,完成打磨、刨光、浸蚀的所有制作步骤。
2、热处理后的试件进行硬度测试。
3、热处理后的试样进行组织观察分析和比较。
三、实验设备的使用和注意事项(一)硬度计的原理、使用和注意事项金属的硬度可以认为是金属材料表面在接触应力作用下的抵抗塑性变形的一种能力。
硬度测量能够验出金属材料软硬程度的数量概念。
由于在金属表面以下不同深处材料所承受的应力和所发生的变形程度不同,因而硬度值可以综合地反映压痕附近局部体积内金属的弹性、微量塑变抗力、塑变强化能力以及大量形变抗力。
硬度值越高,表明金属抵抗塑性变形能力越大,材料产生塑性变形就越困难。
另外,硬度与其它机械性能(如强度指标σb及塑性指标ψ和δ)之间有着一定的内在联系,所以从某种意义上说硬度的大小对于机械零件或工具的使用性能及寿命具有决定性意义。
硬度的试验方法很多,在机械工业中广泛采用压入法来测定硬度。
压入法硬度试验的主要特点是:(1)试验时应力状态最软(即最大切应力远远大于最大正应力),因而不论是塑性材料还是脆性材料均能发生塑性变形。
(2)金属的硬度与强度指标之间存在如下近似关系:σb=K·HB式中:σb——材料的抗拉强度值HB——布氏硬度值K——系数退火状态的碳钢K=0.34~0.36合金调质钢K=0.33~0.35有色金属合金K=0.33~0.53(3)硬度值对材料的耐磨性、疲劳强度等性能也有定性的参考价值,通常硬度高,这些性能也就好。
在机械零件设计图纸上对机械性能的技术要求,往往只标注硬度值,其原因就在于此。
(4)硬度测定后由于仅在金属表面局部体积内产生很小压痕,并不损坏零件,因而适合于成品检验。
13.4影响塑性和变形抗力的因素

7,其它元素:主要是降低钢的塑性,提高变形抗力
合金元素对铁素体伸长率和韧性的影响
(二)组织状态对金属塑性的影响
晶格类型的影响 面心立方——12个滑移系,同一滑移面上3个滑移方向, 塑性最好,如铝,铜和镍等. 体心立方——12个滑移系,同一滑移面上2个滑移方向, 塑性较好,如钒,钨,钼等. 密排六方——3个滑移系,塑性最差,如镁,锌,钙等. 晶粒度的影响 晶粒度越小,越均匀,塑性越高.
第四节影响塑性和变形抗力的因素
一,塑性,塑性指标和塑性图 塑性:金属在外力作用下发生永久变形而不破坏其完整性的 能力. 1,塑性反映了材料产生塑性变形的能力; 2,塑性不是固定不变的,同一种材料,在不同的变形条件 下,会表现出不同的塑性. 3,影响金属塑性的因素主要有两方面: 1)内因:金属本身的晶格类型,化学成分和金相组织等; 2)外因:变形时外部条件,如变形温度和受力状况等.
A0 ,Ak
塑性指标还可以用镦粗实验和扭转试验测定. 镦粗试验(试样的高度为直径的1.5倍)中,以出现 第一条裂纹时的变形程度为塑性指标:
εc
,
H0 Hk = H0
×
100%
试样原始高度和表面出现第一条裂纹 时的高度
注:只有相同的指标才能相互比较
原始样
出现裂纹后的试样
镦粗试验
塑性图: 在不同的变形速度下,以不同温度下的各 种塑性指标( , , , ,ak等)为纵坐标, 以温度为横坐标绘制成的函数曲线.
碳钢的塑性随温度的变化曲线
(四)应变速率对塑性的影响
一方面,随变形速率的增大,金属的塑性降低:没有足 够的时间进行回复或再结晶,软化过程进行得不充分. 另一方面,随着变形速率的增加,在一定程度上使金属 的温度升高,温度效应显著,从而提高金属的塑性.但 对于有脆性转变的金属,则应变速率的增加可能引起塑 性的下降.
各元素对钢的影响

1、铬(Cr)铬能增加钢的淬透性并有二次硬化作用。
可提高高碳钢的硬度和耐磨性而不使钢变脆;含量超过12%时。
使钢有良好的高温抗氧化性和耐氧化性介质腐蚀的作用。
还增加钢的热强性,铬为不锈耐酸钢及耐热钢的主要合金元素。
铬能提高碳素钢轧制状态的强度和硬度。
降低伸长率和断面收缩率。
当铬含量超过15%时,强度和硬度将下降,伸长率和断面收缩率则相应地有所提高。
含铬钢的零件经研磨容易获得较高的表面加工质量。
铬在调质结构钢中的主要作用是提高淬透性。
使钢经淬火回火后具有较好的综合力学性能,在渗碳钢中还可以形成含铬的碳化物,从而提高材料表面的耐磨性。
含铬的弹簧钢在热处理时不易脱碳。
铬能提高工具钢的耐磨性、硬度和红硬性。
有良好的回火稳定性。
在电热合金中,铬能提高合金的抗氧化性、电阻和强度。
(1) 对钢的显做组织及热处理的作用A、铬与铁形成连续固溶体,缩小奥氏体相区城。
铬与碳形成多种碳化物,与碳的亲和力大于铁和锰而低于钨、钼等.铬与铁可形成金属间化合物σ相(FeCr)B、铬使珠光体中碳的浓度及奥氏体中碳的极限溶解度减少C、减缓奥氏体的分解速度,显著提高钢的淬透性.但亦增加钢的回火脆性倾向(2)对钢的力学性能的作用A、提高钢的强度和硬度.时加入其他合金元素时,效果较显著B、显著提高钢的脆性转变温度C、在含铬量高的Fe-Cr合金中,若有σ相析出,冲击韧性急剧下降(3)对钢的物理、化学及工艺性能的作用A、提高钢的耐磨性,经研磨,易获得较高的表面光洁度B、降低钢的电导率,降低电阻温度系数C、提高钢的矫顽力和剩余磁感.广泛用于制造永磁钢D、铬促使钢的表面形成钝化膜,当有一定含量的铭时,显著提高钢的耐腐蚀性能(特别是硝酸)。
若有铬的碳化物析出时,使钢的耐腐蚀性能下降E、提高钢的抗氧化性能F、铬钢中易形成树枝状偏析,降低钢的塑性G、由于铬使钢的热导率下降,热加工时要缓慢升温,锻、轧后要缓冷(4)在钢中的应用A、合金结构钢中主要利用铬提高淬透性,并可在渗碳表面形成含铬碳化物以提高耐磨性B、弹簧钢中利用铬和共他合金元素一起提供的综合性能C、轴承钢中主要利用铬的特殊碳化物对耐磨性的贡献及研磨后表面光沽度高的优点D、工具钢和高速钢中主要利用铬提高耐磨性的作用,并具有一定的回火稳定性和韧性E、不锈钢、耐热钢中铬常与锰、氮、镍等联合便用,当需形成奥氏体钢时,稳定铁素体的铬与稳定奥氏体的锰、镍之间须有一定比例,如Cr18Ni9等F、我国铬资源较少.应尽量节省铬的使用2、钼(Mo)钼在钢中能提高淬透性和热强性。
影响金属塑形因素

影响金属塑形因素碳碳对碳钢的塑性影响最大磷磷是钢中的有害杂质,引起冷脆性碳和杂质元素的影响硫硫也是钢中的有害杂质,引起热脆性氮蓝脆,引起时效脆性氢白点,氢脆氧热脆(也叫红脆,由于氧化物)化学成分1、固溶体的影响:合金元素使铁的晶格发生不同程度的畸变,从而使其抗力提高,塑性降低。
2、碳化物的影响:合金元素与钢中的碳形成硬而脆的碳化物,使钢强度提高,塑性降低合金元素的影响3、硫、氧化物的影响:合金元素与钢中的氧、硫形成氧化物和硫化物夹杂,造成钢的热脆性,降低了钢的热塑性4、相的影响:合金元素可改变钢中相的组成,造成组织的多相性,从而使钢的塑性下降5、组织与晶粒的影响:合金元素也可通过影响钢的铸造组织与晶粒大小来改变钢材的塑性。
6、低熔点元素的影响:造成钢的热脆性7、稀土元素的影响:可明显影响钢的性能,但加入量要合适。
相组成的影响:属单相系的纯金属和固溶体比多相系的塑性好(单相比多相的好)组织的影响:晶粒大小的影响:金属和合金的晶粒度越小,塑性越好。
其原因是:1)变形分散进行;2)晶界作用深化;3)有利位向晶粒数多铸造组织的影响铸锭的成分和组织不均匀,其塑性变形能力低。
其原因有如下几方面:1)非连续组织的存在;2)不均匀组织的存在;3)不利附加应力的存在:变形温度 -100℃:超低温脆性区,原子热运动几乎完全被冻结100-200℃原子热运动加剧200-400℃蓝脆,时效催化,晶界、滑移面上析出氮化物、氧化物700-800℃再结晶、扩散现象800-950℃硫化共晶产物、红脆950-1250℃均匀化奥氏体、硫化物扩散到晶粒内部>1250℃过热、过烧变形速度:提高变形速度还有下列影响:第一,降低摩擦系数;第二,减少热加工时的热量散失;第三,由于“惯性作用”,使复杂工件易于成形。
变形程度的影响:1)变形量(越大)与加工硬化程度(越大)相关2)变形量与热脆现象相关(变形量越大,晶界结合力越弱)3)变形量(越多)与变形内应力(越大)相关应力状态的影响:压应力个数越多,且数值越大,即静水压力越大,则金属的塑性越好应变状态的影响:主应变图中压缩分量越多,对于充分发挥材料的塑性越有利。
塑性影响因素
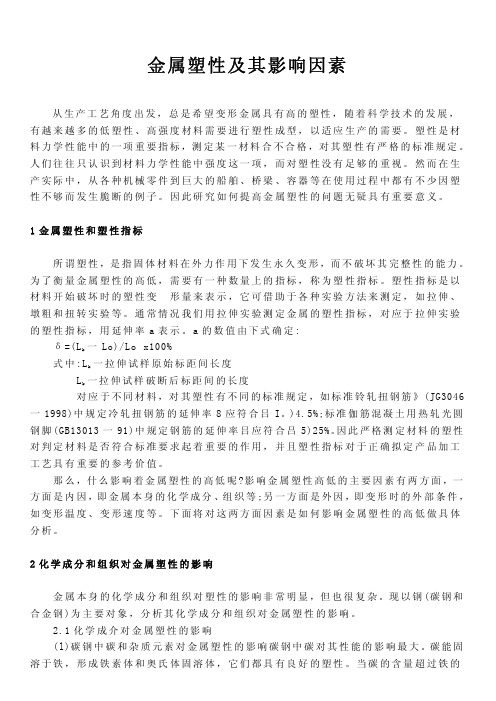
金属塑性及其影响因素从生产工艺角度出发,总是希望变形金属具有高的塑性,随着科学技术的发展,有越来越多的低塑性、高强度材料需要进行塑性成型,以适应生产的需要。
塑性是材料力学性能中的一项重要指标,测定某一材料合不合格,对其塑性有严格的标准规定。
人们往往只认识到材料力学性能中强度这一项,而对塑性没有足够的重视。
然而在生产实际中,从各种机械零件到巨大的船舶、桥梁、容器等在使用过程中都有不少因塑性不够而发生脆断的例子。
因此研究如何提高金属塑性的问题无疑具有重要意义。
1金属塑性和塑性指标所谓塑性,是指固体材料在外力作用下发生永久变形,而不破坏其完整性的能力。
为了衡量金属塑性的高低,需要有一种数量上的指标,称为塑性指标。
塑性指标是以材料开始破坏时的塑性变形量来表示,它可借助于各种实验方法来测定,如拉伸、墩粗和扭转实验等。
通常情况我们用拉伸实验测定金属的塑性指标,对应于拉伸实验的塑性指标,用延伸率a表示。
a的数值由下式确定:一Lo)/Lo x100%δ=(Lk一拉伸试样原始标距间长度式中:Lk一拉伸试样破断后标距间的长度Lk对应于不同材料,对其塑性有不同的标准规定,如标准铃轧扭钢筋》(JG3046一1998)中规定冷轧扭钢筋的延伸率8应符合吕I。
)4.5%;标准伽筋混凝土用热轧光圆钢脚(GB13013一91)中规定钢筋的延伸率吕应符合吕5)25%。
因此严格测定材料的塑性对判定材料是否符合标准要求起着重要的作用,并且塑性指标对于正确拟定产品加工工艺具有重要的参考价值。
那么,什么影响着金属塑性的高低呢?影响金属塑性高低的主要因素有两方面,一方面是内因,即金属本身的化学成分、组织等;另一方面是外因,即变形时的外部条件,如变形温度、变形速度等。
下面将对这两方面因素是如何影响金属塑性的高低做具体分析。
2化学成分和组织对金属塑性的影响金属本身的化学成分和组织对塑性的影响非常明显,但也很复杂。
现以钢(碳钢和合金钢)为主要对象,分析其化学成分和组织对金属塑性的影响。
碳钢的热处理工艺对组织与性能的影响

实验三碳钢的热处理工艺对组织与性能的影响一、实验目的1.了解碳钢热处理工艺操作。
2.学会使用洛氏硬度计测量材料的硬度性能值。
3.掌握热处理后钢的金相组织分析。
4.For personal use only in study and research; not for commercial use5.6.探讨淬火温度、淬火冷却速度、回火温度对45和T12钢的组织和性能(硬度)的影响。
7.巩固课堂教学所学相关知识,体会材料的成分-工艺-组织-性能之间关系。
二、实验内容1.45和T12钢试样淬火、回火操作,用洛氏硬度计测定试样热处理前后的硬度。
工艺规范见表6—1。
2.制备并观察标6—2所列样品的显微组织。
3.观察幻灯片或金相图册,熟悉钢热处理后的典型组织:上贝氏体、下贝氏体、片状马氏体、条状马氏体、回火马氏体等的金相特征。
三、概述1.淬火、回火工艺参数的确定。
Fe—Fe3C状态图和C—曲线是制定碳钢热处理工艺的重要依据。
热处理工艺参数主要包括加热温度,保温时间和冷却速度。
(1)加热温度的确定淬火加热温度决定钢的临界点,亚共析钢,适宜的淬火温度为A c3以上30~50℃,淬火后的组织为均匀而细小的马氏体。
如果加热温度不足(<A c3),淬火组织中仍保留一部分原始组织的铁素体,造成淬火硬度不足。
过共析钢,适宜的淬火温度为A c1以上30~50℃,淬火后的组织为马氏体十二次渗碳体(分布在马氏体基体内成颗粒状)。
二次渗碳体的颗粒存在,会明显增高钢的耐磨性。
而且加热温度较A cm低,这样可以保证马氏体针叶较细,从而减低脆性。
回火温度,均在A c1以下,其具体温度根据最终要求的性能(通常根据硬度要求)而定。
(2)加热,保温时间的确定加热、保温的目的是为了使零件内外达到所要求的加热温度,完成应有的组织转变。
加热、保温时间主要决定于零件的尺寸、形状、钢的成分、原始组织状态、加热介质、零件的装炉方式和装炉量以及加热温度等。
塑性成型原理 塑性影响因素-外部因素
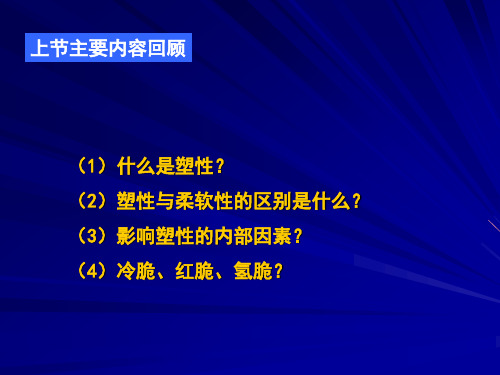
影响金属塑性的外部因素通过改变应力状态提高源自属塑性包覆钢板后的塑性成型
塑性成型示意图
影响金属塑性的外部因素
静水压力对提高金属塑性的良好影响
均质流体作用于一个物体上的压力; 这是一种全方位的力,并均匀地施向物体表面的各个部位
1. 拉伸应力会促进晶间变形、加速晶界的破坏,三向压 应力使晶间变形困难
2. 三向压应力有利于愈合塑性变形中晶内、晶间的各种 损伤
无氧铜 Qsn6.5-0.4
超硬铝合金
晶粒粗大化 金属间化合物
析出物 第二相
影响金属塑性的外部因素
2.应变速率
塑性成形设 备工作速度
水压机 1-10cm/s 机械压力机 30-100cm/s 通用锻锤 500-900cm/s
✓a-b: 加工硬化>软化 热效应
应变速率对塑性影响的示意图
✓c-d: 加工硬化<软化 热效应
➢ 影响塑性的内部因素
➢影响金属塑性的外部因素
➢ 提高金属塑性的主要途径
影响金属塑性的外部因素 1.变形温度
碳钢的塑性随温度变化图
影响金属塑性的外部因素
金属塑性 增高区
1区(100-200℃ )---原子热振动能力 2区(700-800℃ )---回复和再结晶 3区(950-1250 ℃)---均匀一致奥氏体
3. 消除杂质、液态相或组织缺陷的不良影响 4. 减轻不均匀变形而引起的附加拉应力
有没有不足之处?
影响金属塑性的外部因素 4.应变状态(变形状态)
轧制和挤压那个更能发挥金属的塑性能力?
主应变图对金属中缺陷形态的影响
影响金属塑性的外部因素 5.不连续变形的影响(变形程度) 6.尺寸因素的影响 7.其他(介质、气氛等)
分析影响金属塑性变形的主要因素

分析影响金属塑性变形的主要因素(一)影响金属塑性变形的主要因素影响金属塑性变形的主要因素有两个方面,其一是变形金属本身的晶格类型,化学成份和组织状态等内在因素;其二是变形时的外部条件,如变形温度、变形速度和变形的力学状态等。
因此,只要有合适的内、外部条件,就有可能改变金属的塑性行为1.化学成份和组织对塑性变形的影响化学成份和组织对塑性和变形抗力的影响非常明显也很复杂。
下面以钢为例来说明。
①化学成份的影响在碳钢中,铁和碳是基本元素。
在合金钢中,除了铁和碳外还包含有硅、锰、铬、镍、钨等。
在各类钢中还含有些杂质,如磷、硫、氨、氢、氧等。
碳对钢的性能影响最大。
碳能固溶到铁里形成铁素体和奥氏体固溶体,它们都具有良好的塑性和低的变形抗力。
当碳的含量超过铁的溶碳能力,多余的碳便与铁形成具有很高的硬度,而塑性几乎为零的渗碳体。
对基体的塑性变形起阻碍作用,降低塑性,抗力提高。
可见含碳量越高,碳钢的塑性成形性能就越差。
合金元素加入钢中,不仅改变了钢的使用性能,而且改变了钢的塑性成形性能,其主要的表现为:塑性降低,变形抗力提高。
这是由于合金元素溶入固溶体(α—Fe和γ-Fe),使铁原子的晶体点阵发生不同程度的畸变;合金元素与钢中的碳形成硬而脆的碳化物(碳化铬、碳化钨等);合金元素改变钢中相的组成,造成组织的多相性等,都造成钢的抗力提高,塑性降低。
杂质元素对钢的塑性变形一般都有不利的影响。
磷溶入铁素体后,使钢的强度、硬度显著增加,塑性、韧性明显降低。
在低温时,造成钢的冷脆性。
硫在钢中几乎不溶解,与铁形成塑性低的易溶共晶体FeS,热加工时出现热脆开裂现象。
钢中溶氢,会引起氢脆现象,使钢的塑性大大降低。
②组织的影响钢在规定的化学成份内,由于组织的不同,塑性和变形抗力亦会有很大的差别。
单相组织比多相组织塑性好,抗力低。
多相组织由于各相性能不同,使得变形不均匀,同时基本相往往被另一相机械地分割,故塑性降低,变形抗力提高。
晶粒的细化有利提高金属的塑性,但同时也提高了变形抗力。
第五章金属的塑性和变形抗力
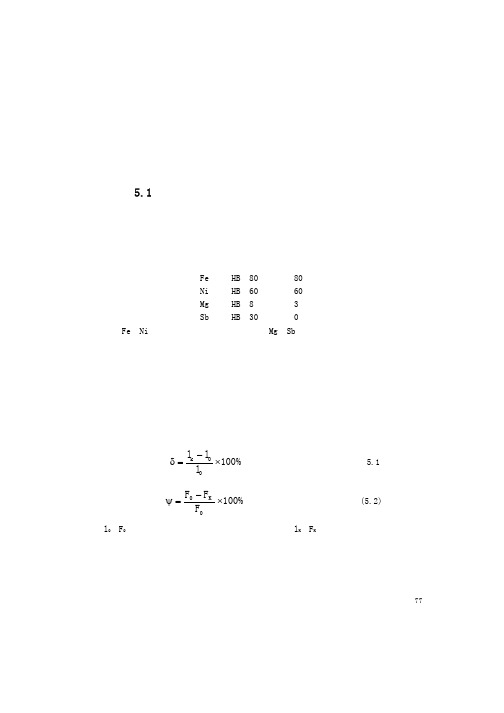
第五章 金属的塑性和变形抗力从金属成形工艺的角度出发,我们总希望变形的金属或合金具有高的塑性和低的变形抗力。
随着生产的发展,出现了许多低塑性、高强度的新材料,需要采取相应的新工艺进行加工。
因此研究金属的塑性和变形抗力,是一个十分重要的问题。
本章的目的在于阐明金属塑性和变形抗力的概念,讨论各种因素对它们的影响。
§5.1 塑性、塑性指标、塑性图和变形抗力的概念所谓塑性,是指固体材料在外力作用下发生永久变形而又不破坏其完整性的能力。
人们常常容易把金属的塑性和硬度看作成反比的关系,即认为凡是硬度高的金属其塑性就差。
当然,有些金属是这样的,但并非都是如此,例如下列金属的情况: Fe HB =80 ψ=80%Ni HB =60 ψ=60%Mg HB =8 ψ=3%Sb HB =30 ψ=0%可见Fe 、Ni 不但硬度高,塑性也很好;而Mg 、Sb 虽然硬度低,但塑性也很差。
塑性是和硬度无关的一种性能。
同样,人们也常把塑性和材料的变形抗力对立起来,认为变形抗力高塑性就低,变形抗力低塑性就高,这也是和事实不符合的。
例如奥氏体不锈钢在室温下可以经受很大的变形而不破坏,既这种钢具有很高的塑性,但是使它变形却需要很大的压力,即同时它有很高的变形抗力。
可见,塑性和变形抗力是两个独立的指标。
为了衡量金属塑性的高低,需要一种数量上的指标来表示,称塑性指标。
塑性指标是以金属材料开始破坏时的塑性变形量来表示。
常用的塑性指标是拉伸试验时的延伸率δ和断面缩小率ψ,δ和ψ由下式确定: %100l l l 00k ×−=δ (5.1) %100F F F 0K 0×−=ψ (5.2) 式中l 0、F 0——试样的原始标距长度和原始横截面积;l K 、F K ——试样断裂后标距长度和试样断裂处最小横截面积。
实际上,这两个指标只能表示材料在单向拉伸条件下的塑性变形能力。
金属的塑性指标除了用拉伸试验之外,还可以用镦粗试验、扭转试验等来测定。
中碳钢延迟裂纹的原因

中碳钢延迟裂纹的原因
中碳钢延迟裂纹的形成可能涉及多种因素,包括材料本身的性质、加工过程中的应力和环境条件等。
下面我将从不同的角度来回
答这个问题。
首先,材料本身的性质可能是引起中碳钢延迟裂纹的原因之一。
中碳钢通常含有适量的碳元素,这使得它具有一定的强度和硬度。
然而,过高或不均匀的碳含量可能导致材料内部的组织不稳定,从
而增加了裂纹的敏感性。
此外,材料中可能存在其他的夹杂物或缺陷,这些缺陷也可能成为裂纹萌生的起始点。
其次,加工过程中的应力可能是导致中碳钢延迟裂纹的另一个
重要原因。
在加工过程中,中碳钢可能会受到拉伸、压缩、弯曲等
多种应力作用。
如果加工过程中的应力超过了材料的承受范围,就
会导致材料内部产生裂纹,并且这些裂纹可能在后续的使用过程中
逐渐扩展,最终导致延迟裂纹的形成。
此外,环境条件也可能对中碳钢延迟裂纹的形成起到一定的影响。
例如,在高温、高湿度或者腐蚀性环境下,中碳钢的腐蚀性能
可能会受到影响,从而加速裂纹的扩展,导致延迟裂纹的出现。
综上所述,中碳钢延迟裂纹的形成是一个复杂的过程,可能涉
及材料本身的性质、加工过程中的应力以及环境条件等多个因素。
对于中碳钢延迟裂纹的预防,需要综合考虑以上因素,并采取相应
的措施,例如优化材料配比、改善加工工艺、加强对环境的控制等,以降低中碳钢延迟裂纹的风险。
第1章金属的塑性第3节-影响塑性的因素
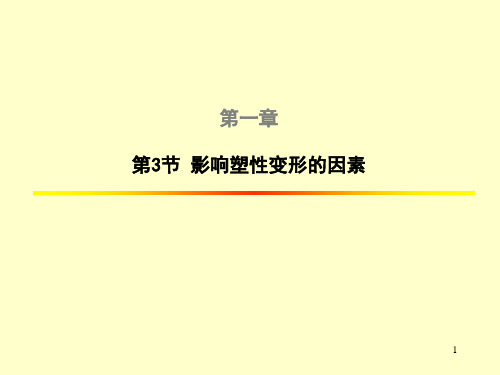
σ1σ2 大 气 压
卡尔曼仪器
(a)大理石;(b)红砂石;
脆性材料的各向压缩曲线
20
变形抗力是一个与应力状态有关的量。例如,假设棒材挤
压与拉拔的变形量一样,但变形力肯定不一样。从主应力图
与主应变图上可知,挤压力为 1 ,拉拔抗力也为 3 ,由 Tresca屈服准则:
1- 3= s
21
应变状态:压缩应变有利于塑性的发挥,拉伸应变 对塑性不利。
合 金 号 L4
LD2
LY11 LY11
11~16
11~16 31
150
150 65
294~315
340~350 308
18
变形温度、变形速度对塑性和变形抗力的影响应统一考虑, 通常称为温度-速度条件。
19
五、应力状态的影响
1
冲头 试样
试验腔室 液体注入口
—轴向压力;
2 —侧向压力
σ1σ2 大 气 压
2
材料的性质(内因)
加工条件(外因)
一、化学成分的影响
1.杂质的影响
一般而言,金属的塑性是随纯度的提高而增加的
例1. 纯铝:纯度99.96%,延伸率45% 98%,延伸率30% 例2. 化学纯铁具有非常大的塑性,但工业纯铁,例 如阿姆克铁,其塑性却不完全如此。铸态的阿姆克 铁在1000℃左右,塑性急剧下降。 例3. 铁中的杂质:磷—→冷脆性;
17
五、变形速度的影响
变形速度对塑性的影响,实质上是加工硬化和变形热效应的 共同作用。 热效应:金属在塑性变形时塑性变形能转化为热能的现象。 温度效应:塑性变形过程中,因金属发热而促使温度升高的效应
铝合金冷挤压时因热效应所增加的温度 挤压系数 11 挤压速度 (毫米/秒) 150 金属温度 ℃ 158~195
影响变形抗力的因素-变形力学等

(a)=3×10-4/s;(b)=3×10-2/s;(c)=3×100/s
五、变形程度的影响
从不同温度下变形程度的变化来看: 在冷状态时,随变形程度的增加,变形抗力显著提高;
由于塑性变形过程中,金属的晶粒产生弹性畸变。 在热状态下,也有强化产生。 由于随温度提高,软化速度增大。
变形抗力的影响因素(二)
影响轧制压力的因素
一、化学成分 二、组织结构 三、变形温度 四、变形速度 五、变形程度 六、应力状态
三、变形温度的影响
在不同温度下,采用不同的变形速度和变形程度时低碳钢的加工硬化曲线 (a)=3×10-4/s;(b)=3×10-2/s;(c)=3×100/s
随着钢的加热温度的升高,变形抗力降低。
三、变形温度的影响
某钢的变形抗力和温度的关系:
1200℃时
变形抗力为1.0
1100℃时
变形抗力为2.7
1000℃时
变形抗力为4.0
800℃时
变形抗力为6.7
常温时
变形抗力为20
三、变形温度的影响
温度升高,金属变形抗力降低的原因有以下几个方面: (1)回复与再结晶
回复软化金属,降低变形抗力;再结晶消除加工硬化,显著降低变
挤压时的单位压力(变 形抗力)=441Mpa
拉拔时的单位拉力(变 形抗力)=215.6MPa
谢谢大பைடு நூலகம்!
热变形时:变形速度 增加,变形抗力增加 显著;
冷变形时:变形速度 增加,变形抗力增加 不大。
四、变形速度的影响
热变形时变形速度增加,变形抗力增加显著的原因: (1)变形速度增加使软化过程不能充分地进行,加工硬
金属工艺学课程习题(综合)

⾦属⼯艺学课程习题(综合)习题《⾦属⼯艺学》部分第1章铸造填空题:1、铸造⽅法从总体上可分为普通铸造和特种铸造两⼤类,普通铸造是指砂型铸造⽅法,不同于砂型铸造的其他铸造⽅法统称为特种铸造,常⽤的特种铸造⽅法有:()、()、()、()、()等。
2、凝固过程中所造成的体积缩减如得不到液态⾦属的补充,将产⽣()或()。
3、对砂型铸件进⾏结构设计时,必须考虑合⾦的()和铸造()对铸件结构提出的要求。
4、()是铸造合⾦本⾝的物理性质,是铸件许多缺陷()产⽣的基本原因。
5、浇注位置是指造型时()在铸型中所处的位置,它影响铸件的质量。
6、铸造应⼒按产⽣的原因不同,主要可分为()和()两种。
7、铸件上各部分壁厚相差较⼤,冷却到室温,厚壁部分的残余应⼒为()应⼒,⽽薄壁部分的残余应⼒为()应⼒。
8、任何⼀种液态⾦属注⼊铸型以后,从浇注温度冷却⾄室温都要经过三个联系的收缩阶段,即()、()和()。
9、在低压铸造、压⼒铸造和离⼼铸造时,因⼈为加⼤了充型压⼒,故()较强。
提⾼浇铸温度是改善合⾦()的重要措施。
10、铸件浇铸位置的选择必须正确,如重要加⼯⾯、⼤平⾯和薄壁部分在浇铸时应尽量(),⽽厚⼤部位应尽量(),以便安放冒⼝进⾏()。
单项选择题:1、下列合⾦流动性最好的是:()①普通灰铸铁;②球墨铸铁;③可锻铸铁;④蠕墨铸铁。
2、摩托车活塞应具有良好的耐热性、热膨胀系数⼩,导热性好、耐磨、耐蚀、重量轻等性能。
在下列材料中,⼀般选⽤:()①铸造黄铜;②合⾦结构钢;③铸造铝硅合⾦;④铸造碳钢。
3、在下列铸造合⾦中,⾃由收缩率最⼩的是:()①铸钢;②灰铸铁;③铸造铝合⾦;④⽩⼝铸铁4、图⽰圆锥齿轮铸件,齿⾯质量要求较⾼。
材料HT350,⼩批⽣产。
最佳浇5①采⽤在热节处加明、暗冒⼝或冷铁以实现顺序凝固②尽量使铸件壁厚均匀以实现同时凝固③提⾼浇注温度④采⽤颗粒⼤⽽均匀的原砂以改善填充条件多项选择题:1、液态合⾦浇注温度冷却到室温所经历的收缩阶段有:()①⾼温收缩;②液态收缩;③凝固收缩④低温收缩;⑤固态收缩2、挖沙或假箱造型时候,分型⾯:()①⼀定是曲⾯;②⼀定是圆锥⾯;③可以是平;④⼀定是平⾯;⑤可以是曲⾯3、影响液态合⾦充型能⼒的主要因素是:()①合⾦的结晶特性;②浇注温度;③合⾦的收缩率;④铸造⼯艺凝固原则;⑤铸件壁厚和铸型条件4、影响液态合⾦充型能⼒的主要因素是:()①合⾦的结晶特性;②浇注温度;③合⾦的收缩率;④铸造⼯艺凝固原则;⑤铸件壁厚和铸型条件5、产⽣缩孔、缩松的基本原因:()①液态收缩;②固态收缩;③凝固收缩;④线收缩;⑤等温收缩结构改错题:1、如下图所⽰,浇铸位置是否合理?若不合理请改为合理。
《金属塑性成形原理》试卷及答案
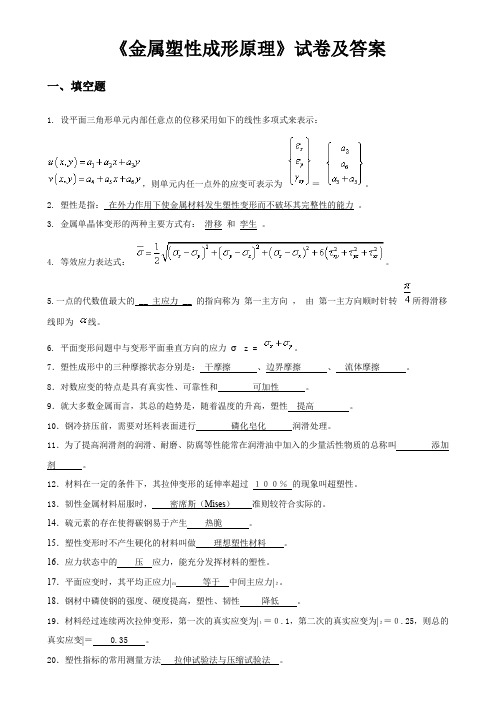
《金属塑性成形原理》试卷及答案一、填空题1. 设平面三角形单元内部任意点的位移采用如下的线性多项式来表示:,则单元内任一点外的应变可表示为=。
2. 塑性是指:在外力作用下使金属材料发生塑性变形而不破坏其完整性的能力。
3. 金属单晶体变形的两种主要方式有:滑移和孪生。
4. 等效应力表达式:。
5.一点的代数值最大的 __ 主应力 __ 的指向称为第一主方向,由第一主方向顺时针转所得滑移线即为线。
6. 平面变形问题中与变形平面垂直方向的应力σ z = 。
7.塑性成形中的三种摩擦状态分别是:干摩擦、边界摩擦、流体摩擦。
8.对数应变的特点是具有真实性、可靠性和可加性。
9.就大多数金属而言,其总的趋势是,随着温度的升高,塑性提高。
10.钢冷挤压前,需要对坯料表面进行磷化皂化润滑处理。
11.为了提高润滑剂的润滑、耐磨、防腐等性能常在润滑油中加入的少量活性物质的总称叫添加剂。
12.材料在一定的条件下,其拉伸变形的延伸率超过100%的现象叫超塑性。
13.韧性金属材料屈服时,密席斯(Mises)准则较符合实际的。
14.硫元素的存在使得碳钢易于产生热脆。
15.塑性变形时不产生硬化的材料叫做理想塑性材料。
16.应力状态中的压应力,能充分发挥材料的塑性。
17.平面应变时,其平均正应力 m等于中间主应力 2。
18.钢材中磷使钢的强度、硬度提高,塑性、韧性降低。
19.材料经过连续两次拉伸变形,第一次的真实应变为 1=0.1,第二次的真实应变为 2=0.25,则总的真实应变 =0.35 。
20.塑性指标的常用测量方法拉伸试验法与压缩试验法。
21.弹性变形机理原子间距的变化;塑性变形机理位错运动为主。
二、下列各小题均有多个答案,选择最适合的一个填于横线上1.塑性变形时,工具表面的粗糙度对摩擦系数的影响A工件表面的粗糙度对摩擦系数的影响。
A、大于;B、等于;C、小于;2.塑性变形时不产生硬化的材料叫做A。
A、理想塑性材料;B、理想弹性材料;C、硬化材料;3.用近似平衡微分方程和近似塑性条件求解塑性成形问题的方法称为B。
碳钢 屈服强度

碳钢屈服强度
碳钢是一种常见的金属材料,具有广泛的应用领域。
在工程设计和制造过程中,了解和掌握碳钢的屈服强度是非常重要的。
本文将对碳钢的屈服强度进行详细介绍,包括其定义、影响因素以及测试方法。
屈服强度是指材料在受到外力作用下发生塑性变形时所承受的最大应力。
对于碳钢来说,屈服强度是衡量其抗拉性能的重要指标之一。
通常使用屈服强度来评估材料的可靠性和安全性。
碳钢的屈服强度受多种因素的影响,包括材料的化学成分、热处理工艺以及形状和尺寸等。
碳钢中的碳含量和其他合金元素的含量会直接影响其屈服强度。
一般来说,碳含量越高,屈服强度越大。
此外,热处理过程中的冷却速率和退火温度也会影响碳钢的屈服强度。
在工程实践中,常用的测试方法是拉伸试验。
拉伸试验是通过在试样上施加拉力,使其逐渐拉伸,观察和记录试样在不同拉力下的应变和应力变化,从而得到屈服强度。
根据拉伸试验的结果,可以绘制应力-应变曲线,从曲线中读取屈服强度。
需要注意的是,碳钢的屈服强度是一个相对的概念,与具体的应用场景和要求有关。
在不同的工程领域,对碳钢的屈服强度的要求也不尽相同。
因此,在设计和选择材料时,需要根据实际情况来确定合适的屈服强度范围。
了解和掌握碳钢的屈服强度对于工程设计和制造具有重要意义。
通过合理选择化学成分和热处理工艺,可以改善碳钢的屈服强度。
通过拉伸试验等测试方法,可以确定碳钢的屈服强度,为工程实践提供可靠的依据。
在实际应用中,需要根据具体情况来确定碳钢的合适屈服强度范围。
只有充分了解和掌握碳钢的屈服强度,才能更好地应用和发挥碳钢的优良性能。
《金属塑性成型原理》(俞汉清主编)课后习题及答案

第一章1.什么是金属的塑性?什么是塑性成形?塑性成形有何特点?塑性----在外力作用下使金属材料发生塑性变形而不破坏其完整性的能力;塑性变形----当作用在物体上的外力取消后,物体的变形不能完全恢复而产生的残余变形;塑性成形----金属材料在一定的外力作用下,利用其塑性而使其成型并获得一定力学性能的加工方法,也称塑性加工或压力加工;塑性成形的特点:①组织、性能好②材料利用率高③尺寸精度高④生产效率高2.试述塑性成形的一般分类。
Ⅰ.按成型特点可分为块料成形(也称体积成形)和板料成型两大类1)块料成型是在塑性成形过程中靠体积转移和分配来实现的。
可分为一次成型和二次加工。
一次加工:①轧制----是将金属坯料通过两个旋转轧辊间的特定空间使其产生塑性变形,以获得一定截面形状材料的塑性成形方法。
分纵轧、横轧、斜轧;用于生产型材、板材和管材。
②挤压----是在大截面坯料的后端施加一定的压力,将金属坯料通过一定形状和尺寸的模孔使其产生塑性变形,以获得符合模孔截面形状的小截面坯料或零件的塑性成形方法。
分正挤压、反挤压和复合挤压;适于(低塑性的)型材、管材和零件。
③拉拔----是在金属坯料的前端施加一定的拉力,将金属坯料通过一定形状、尺寸的模孔使其产生塑性变形,以获得与模孔形状、尺寸相同的小截面坯料的塑性成形方法。
生产棒材、管材和线材。
二次加工:①自由锻----是在锻锤或水压机上,利用简单的工具将金属锭料或坯料锻成所需的形状和尺寸的加工方法。
精度低,生产率不高,用于单件小批量或大锻件。
②模锻----是将金属坯料放在与成平形状、尺寸相同的模腔中使其产生塑性变形,从而获得与模腔形状、尺寸相同的坯料或零件的加工方法。
分开式模锻和闭式模锻。
2)板料成型一般称为冲压。
分为分离工序和成形工序。
分离工序:用于使冲压件与板料沿一定的轮廓线相互分离,如冲裁、剪切等工序;成型工序:用来使坯料在不破坏的条件下发生塑性变形,成为具有要求形状和尺寸的零件,如弯曲、拉深等工序。
5金属的塑性与变形抗力-新解析

1区——位于100~200℃之间,塑性增加是由于在 冷变形时原子动能增加的缘故(热振动)。 2区——位于700~800℃之间,由于有再结晶和扩 散过程发生,这两个过程对塑性都有好的作用。
3区——位于950~1250℃的范围内,在此区域中 没有相变,钢的组织是均匀一致的奥氏体。
热轧时应尽可能地使变形在3区温度范围内进 行,而冷加工的温度则应为1区。
s k k kt 0
0的获得条件 :t=1000°C; =0.1 =10s-1
5.4 影响变形抗力的主要因素
一、化学成分和显微组织的影响 1、化学成分的影响
(1)碳
在较低的温度下随着钢中含碳量的增加,钢的变 形抗力升高。温度升高时其影响减弱。
在不同变形温度和变形速度下含碳量对碳钢变形抗力的影响 (实线为静压缩,虚线为动压缩)
三向压应力状态图最好,两压一拉次之,三向拉应 力最坏。 其影响原因归纳如下:
(1)三向压应力状态能遏止晶间相对移动,使晶间 变形困难。
(2)三向压应力状态能促使由塑性变形和其它原因 而破坏了的晶内和晶间联系得到修复。 (3)三向压应力状态能完全或局部地消除变形体内 数量很少的某些夹杂物甚至液相对塑性不良的影响; (4)三向压应力状态可以完全抵消或大大降低由不 均匀变形而引起的附加拉力,使附加拉应力所造成的 破坏作用减轻。
变形速度对碳钢变形抗力的影响 压下率:-50%;-10%;-2%
四、 变形程度对变形抗力的影响
大致可分三个方面: 金属的自然性质 变形的温度、速度条件 变形的力学条件
一、 金属的自然性质对塑性的影响
1、组织状态的影响
(1)纯金属有最好的塑性
(2)单相组织(纯金属或固溶体)比多相组织塑性 好 (3)晶粒细化有利于提高金属的塑性
影响材料弹性模量的因素
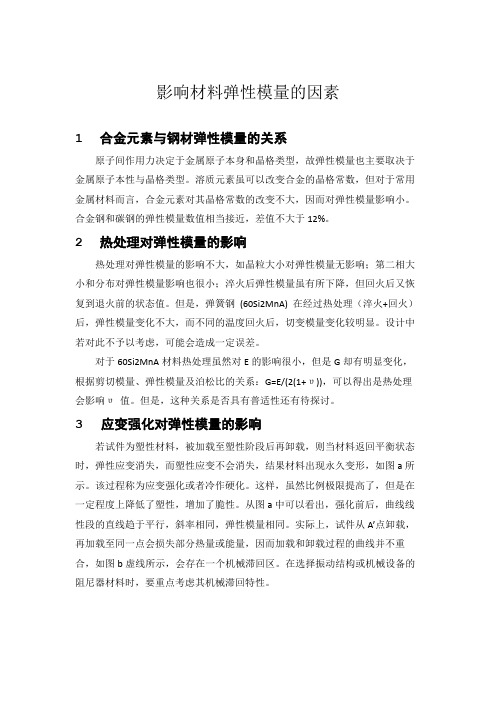
影响材料弹性模量的因素1合金元素与钢材弹性模量的关系原子间作用力决定于金属原子本身和晶格类型,故弹性模量也主要取决于金属原子本性与晶格类型。
溶质元素虽可以改变合金的晶格常数,但对于常用金属材料而言,合金元素对其晶格常数的改变不大,因而对弹性模量影响小。
合金钢和碳钢的弹性模量数值相当接近,差值不大于12%。
2热处理对弹性模量的影响热处理对弹性模量的影响不大,如晶粒大小对弹性模量无影响;第二相大小和分布对弹性模量影响也很小;淬火后弹性模量虽有所下降,但回火后又恢复到退火前的状态值。
但是,弹簧钢(60Si2MnA) 在经过热处理(淬火+回火)后,弹性模量变化不大,而不同的温度回火后,切变模量变化较明显。
设计中若对此不予以考虑,可能会造成一定误差。
对于60Si2MnA材料热处理虽然对E的影响很小,但是G却有明显变化,根据剪切模量、弹性模量及泊松比的关系:G=E/(2(1+υ)),可以得出是热处理会影响υ值。
但是,这种关系是否具有普适性还有待探讨。
3应变强化对弹性模量的影响若试件为塑性材料,被加载至塑性阶段后再卸载,则当材料返回平衡状态时,弹性应变消失,而塑性应变不会消失,结果材料出现永久变形,如图a所示。
该过程称为应变强化或者冷作硬化。
这样,虽然比例极限提高了,但是在一定程度上降低了塑性,增加了脆性。
从图a中可以看出,强化前后,曲线线性段的直线趋于平行,斜率相同,弹性模量相同。
实际上,试件从A’点卸载,再加载至同一点会损失部分热量或能量,因而加载和卸载过程的曲线并不重合,如图b虚线所示,会存在一个机械滞回区。
在选择振动结构或机械设备的阻尼器材料时,要重点考虑其机械滞回特性。
材料强化过程示意图4冷塑变形对弹性模量的影响冷塑变形使弹性模量稍有降低,一般降低4%~6%,这与残余应力有关。
当塑性变形量很大时,因产生形变使弹性模量出现各向异性,沿变形方向弹性模量最大。
这种冷塑变形所造成的材料弹性模量变化,将会对精密零件的冷成型精度造成影响。
变形抗力的影响因素-化学成分和显微组织的影响

影响变形抗力的因素
一、化学成分 二、组织结构 二、轧件温度 三、变形速度 四、变形程度 五、应力状态 ……
一、化学成分对变形抗力的影响
对于纯金属:原子间结合力大的,滑移阻力大,变形抗力 大。同种金属:纯度愈高的变形抗力愈小。
对于合金:随含C量或合Байду номын сангаас成分增加,变形抗力大。 原因: (1)溶入固溶体,基体金属点阵畸变增加; (2)形成化合物; (3)形成第二相组织。
1、晶粒尺寸: 晶粒越细小,变形抗力越大。晶粒体积相同时,细长晶粒
比等轴晶粒结构的变形抗力要大;晶粒尺寸不均匀时,比 均匀晶粒结构的变形抗力大。 2、单相组织和多相组织 单相组织比多相组织的变形抗力要低; 3、夹杂物 使变形抗力升高。
谢谢大家!
(1)Mn溶入铁素体引起固溶强化;
(2)Mn可以使钢材在轧后冷却时,得到比较细而且强度 较高的珠光体。
每增加0.1%Mn,热轧钢抗拉强度增加7.8~12.7MN/m2, 屈服强度增加7.8~9.8MN/m2。
一、化学成分对变形抗力的影响
3、硅 硅在碳钢中的含量≤0.5%。 每增加0.1%Si,热轧钢的抗拉强度增加7.8~8.8MN/m2,
屈服强度增加3.9~4.9MN/m2。
一、化学成分对变形抗力的影响
4、Cr 含铬钢,影响其变形抗力的是钢中的含碳量。 0.7%~1.0%的铬钢的变形抗力比相应含碳量的碳钢高5%
~10%。 GCr6~GCr15高碳铬钢,变形抗力稍高于碳钢。 高铬钢1Cr13~4Cr13,Cr17,Cr23等在高速下变形时,变
形抗力大为提高。
一、化学成分对变形抗力的影响
5、镍 镍在钢中可使变形抗力稍有提高。 但对25NiA、30NiA等钢来讲,其变形抗力与碳钢相差不大
- 1、下载文档前请自行甄别文档内容的完整性,平台不提供额外的编辑、内容补充、找答案等附加服务。
- 2、"仅部分预览"的文档,不可在线预览部分如存在完整性等问题,可反馈申请退款(可完整预览的文档不适用该条件!)。
- 3、如文档侵犯您的权益,请联系客服反馈,我们会尽快为您处理(人工客服工作时间:9:00-18:30)。
影响碳钢的变形抗力和塑性的因素分析一、金属的塑性与变形抗力1.1金属之所以能进行压力加工主要是由于金属具有塑性这一特点。
所谓塑性,是指金属在外力作用下,能稳定地产生永久变形而不破坏其完整性的能力。
金属塑性的大小,可用金属在断裂前产生的最大变形程度来表示。
一般通常称压力加工时金属塑性变形的限度,或“塑性极限”为塑性指标。
应当指出,不能把塑性和柔软性混淆起来。
不能认为金属比较软,在塑性加工过程中就不易破裂。
柔软性反映金属的软硬程度,它用变形抗力的大小来衡量,表示变形的难易。
不要认为变形抗力小的金属塑性就好,或是变形抗力大的金属塑性就差。
例如:室温下奥氏体不锈钢的塑性很好,能经受很大的变形而不破坏,但它的变形抗力却非常大;工业纯铁的变形抗力很低,柔软性很好,对于过热和过烧的金属与合金来说,其塑性很小,甚至完全失去塑性变形的能力,而变形抗力也很小;也有些金属塑性很高而变形抗力又小,如室温下的铅等。
金属的塑性不仅受金属内在的化学成分与组织结构的影响,也和外在的变形条件有密切关系。
同一金属或合金,由于变形条件不同,可能表现有不同的塑性,甚至由塑性物体变为脆性物体,或由脆性物体转变为塑性物体。
例如受单位拉伸的大理石是脆性物体,但在较强的平均应力下压缩时,却能产生明显的塑性变形而不破坏。
对金属与合金塑性的研究,是压力加工理论与实践的重要课题之一。
研究的目的在于选择合适的变形方法,确定合理的变形温度、速度条件以及采用的最大变形量,以便使低塑性难变形的金属与合金能顺利实现成型过程。
1.2金属塑性的测定方法由于变形力条件对金属的塑性有很大影响,所以目前还没有一种实验方法能测出可表示所有压力加工方式下金属塑性的指标。
为了正确选择变形温度、速度条件和最大变形量,必须测定金属在不同条件下允许的极限变形量—塑性指标。
每种实验方法测定的塑性指标,虽然只能表明金属在该变形过程中所具有的塑性,但也不应否定一般测定方法的应用价值,因为这些实验可以得到相对的和可比较的塑性指标。
这些数据可定性地说明在一定变形条件下,各种金属塑性的高低;对同一金属,能反映哪种变形条件下的塑性高。
这对正确选择变形温度、速度和变形量的范围都有直接参考价值。
表示金属与合金塑性变形性能的主要指标有:(1)拉伸试验时的伸长率与断面收缩率(2)冲击试验时的冲击韧性(3)扭转试验的扭转转速(4)锻造及轧制时刚出现裂纹瞬间的相对压下量(5)深冲试验时的压进深度,损坏前的弯折次数1.3金属塑性的测定方法测定金属塑性的方法是常用的有力学性能试验方法和模拟试验法(模仿某种加工变形过程的一般条件,用小试样进行试验的方法)两大类。
A力学性能试验(1)拉伸试验是在材料试验上进行的。
相当于一般液压机的变形速度。
相当于蒸汽锤、线材轧机、宽带钢轧机变形速度的下限。
如果要求更高或变化范围更大的变形速度,需设计制造专门的高速变形机。
在拉伸试验中可以确定伸长率和断面收缩率两个塑性指标,金属材料的伸长率和断面收缩率愈大,表示该材料的塑性愈好,即材料能承受较大的塑性变形而不破坏。
一般把伸长率大于百分之五的金属材料称为塑性材料(如低碳钢等),而把伸长率小于百分之五的金属材料称为脆性材料。
塑性好的材料,它能在较大的宏观范围内产生塑性变形,并在塑性变形的同时使金属材料因塑性变形而强化,从而提高材料的强度,保证了零件的安全使用。
此外,塑性好的材料可以顺利地进行某些成型工艺加工,如冲压、冷弯、冷拔、矫直等。
因此,选择金属材料作机械零件时,必须满足一定的塑性指标。
伸长率表示金属沿拉伸轴方向上在断裂前的最大变形。
由试验得知,一般塑性较高的金属,拉伸变形到一定阶段开始出现细劲,使变形集中在试样的局部区域直到拉断;同时,在细劲出现以前试样受单位拉应力,细劲出现以后使该处受三响拉应力。
由此可见,试样断裂前的伸长率,包括了均匀变形和集中的局部两部分,反映了在单向拉应力和三向拉应力作用下两个阶段的塑性总和。
伸长率大小于试样的原始计算长度有关,试样越长,集中变形数值的作用越小,伸长率就越小。
因此,&作塑性指标时,必须把计算长度固定下来才能相互比较。
对圆柱形试样规定有两种标准试样。
断面收缩率也反映在单向拉应力和三向拉应力作用下塑性指标,它与试样的原始计算长度无关。
因此在塑性材料中用作塑性指标,可以得出比较稳定的数值,故有其优越性。
(2)冲击弯曲试验。
冲击韧性值ak不完全是一种塑性指标,它是弯曲变形抗力和试样弯曲的综合指标。
因此,同样的ak值,塑性可能很不相同。
有时由于弯曲变形抗力很大,尽管破断前的弯曲变形程度较小。
反之,虽然破断前弯曲变形程度较大,但变形抗力很小,ak值也可能较小。
由于试样有切口(切口处受拉应力作用),并受冲击作用,因此所得的ak值能较敏感地反映材料的脆性倾向;如果试样中有组织结构的变化、夹杂物的不利分布、晶粒过分粗大和晶间物物质熔化等,可较明显地反映出来。
例如,在合金结构钢中,若二次碳化物由均匀分布状态变为沿境界成网状形式分布时,这种变化虽然在拉伸试验中,塑性指标不改变,而在冲击弯曲试验中,却使ak值降低了0.5-1倍;在某些合金中,由于脱氧不良也会使塑性降低,不过在拉伸试验中反映不出来,但其ak值在这种情况下却降低了1-2倍。
为了判明ak值的急剧变化是否由于塑性急剧变化而引起的,最好配合参与在试验条件下的强度极限变化情况。
例如,当变化不大或有所降低而ak值显著增大,这表明是由塑性急剧增高而引起的;而在ak值较高的温度范围内值很高,则不能证明在此度范围内塑性最好。
因此,按ak值来决定最好的热加工温度范围,就要具体分析,否则会得出不正确的结论。
(3)扭曲试验是在专用的扭转试验上进行的。
试验时,将圆柱形试样的一端固定,另一端扭转,用破断前的转数(n)表示塑性的大小。
试样将受纯剪力,切应力在试样断面中心为零,而在表面有最大值。
纯剪时一个主应力为拉应力,另一个主应力为压应力;这种变形所确定的塑性指标能反映材料同时受数值相等的拉应力和压应力作用时的塑性。
所以扭转试验,被广泛用于金属与合金的塑性研究。
在斜轧穿孔时,轧件在变形区内受扭转作用,所以,有人用扭转试验来确定合适的穿孔温度。
扭转试验结果可用如图5-1所示的曲线表示。
观察、测量首先出现裂纹处的变形量,此变形量就表示塑性大小。
此方法不需制备特殊轧辊,但确定极限变形量比较困难,因为试样轧后高度是均匀的,而伸长后原来一定高度的位置发生了变化,除非在原试样的侧面上刻竖痕;否则轧后便不易确定原始高度的位置,因而也就不好确定极限变形量。
另一种方法是在偏心辊上将矩形轧件轧成楔形件。
这种方法采用的上轧辊有刻槽,下轧辊是平的,由于切制的轧槽使两辊间距在轧制过程中产生变化,所B模拟试验法(1)顶锻试验也称镦粗试验,是将圆柱形试样在压力机或落锤上镦粗,把试样侧面出现第一条可见裂纹时的变形量,作为塑性指标,此种试验方法反映了应力状态与此相近的锻压变形过程(自由锻、冷镦等)的塑性大小。
在压力机上镦粗,相当于液压机和初轧机上的变形速度;而落锤试验,相当于锻锤上锻压变形过程的加工温度范围时,最好分别在压力机和落锤上进行顶锻试验。
试验表明,对同一金属在一定温度和速度条件下进行镦粗时,可能得出不同的塑性指标,这将取决于接触表面上外摩擦的条件和试样的原始尺寸。
因此,为使所得结果能进行比较,对顶锻试验必须定出相应的规程,说明进行试验的具体条件。
镦粗试验的缺点是在高温下对塑性较高的金属,尽管变形程度很大,试样侧面也可能不出现裂纹,因而得不出塑性极限。
不过在顶锻过程形成裂纹,有时因表面缺陷造成的,这在试验时是应注意的。
(2)楔形轧制试验有两种不同的做法,一种是在平辊上将楔形试样轧成扁平带状。
轧后以轧后根据厚度变化的楔形件来确定其塑性大小。
用此法测得的极限变形量与实验温度的关系曲线如图5-2所示用偏心辊试验方法比前一种优越,主要是可以准确地定出极限变形量,也免除了加工试样的麻烦。
但应指出,由于单辊刻槽造成上下辊之间产生轧制速度差。
这种速度差,既可能导致轧件表面损坏,也使变形力学条件发生一定变化,故对测定结果产生一定影响。
为克服上述缺点,近年来多采用双辊刻槽轧成楔形以测定塑性的大小。
双辊刻槽法其辊形如图5-3所示楔形轧制试验法的优点是:一次试验便可得到相当大的压下率范围,因此往往只需要进行一次试验便可以确定极限变形量;其次是试验条件可以很好地模拟轧制时的情况。
因此,这种方法广泛用于确定金属与合金轧制过程的塑性。
5.2影响塑性的因素及提高塑性的途径5.2.1金属的自然性质金属的自然性质即化学成分和组织状态对塑性的影响。
实际上这方面的问题很复杂,至今人们对这方面的了解还不全面。
下面以钢为研究对象,分析化学成分和组织对塑性的影响。
5.2.1.1化学成分的影响在碳钢中,Fe和C是基本元素。
在合金钢中,除Fe和C外还含有合金元素,常见的合金元素有Si、Mn、Cr、Ni、W、Mo、V、Co、Ti等。
此外由于矿石和加工等方面的原因,在各类钢中还含有一些杂质,如P、S、N、H、O等。
一般的影响规律是随着碳和杂质含量的增加,金属的塑性降低。
A碳碳对碳钢的性能影响最大,碳能固定于铁形成铁素体和奥氏体,它们都具有良好的塑性和降低的变形抗力。
当碳的含量超过铁的溶碳能力时,多余的碳便与铁形成化合物Fe3C,该化合物称为渗碳体。
渗碳体具有很高的硬度而塑性几乎为零,使碳钢的塑性降低,抗力提高。
随着含碳量的增加,渗碳体的数量也增加,塑性的降低与变形抗力的提高就更明显,对于冷成形的碳钢,含碳量应较低;在热成形时,虽然碳能全部溶于奥氏体中,但碳含量越高,碳钢的熔化温度越低,热加工的温度范围也越窄,奥氏体晶粒长大的倾向也越大,再结晶速度也越慢,这些热成形都是不利的。
B磷磷一般说来是钢中有害杂质,磷能溶于铁素体中,使钢的强度、硬度增加,但塑性、韧性则显著降低。
这种脆化现象在低温时更为严重,故称为冷脆。
一般希望冷脆转变温度低于工件的工作温度,以免发生冷脆。
冷脆对在高寒地带和其他低温条件下工作的结构件具有严重的危害性。
在某些情况下,磷也起有益作用,如增加耐腐蚀性,提高磁性,减少叠轧薄板黏结等。
钢材中的炮弹钢就是在钢中有意多添加磷,让钢含磷量高,使炮弹在爆炸的时候尽量炸出的弹片,增大炮弹的杀伤力。
C硫硫是钢中有害杂质,它在钢中几乎不溶解,而与铁形成FeS,FeS与Fe的共晶体其熔点很低,呈网状分布晶界上。
由于晶界处硫化铁共晶体塑性低或发生熔化而导致加工件开裂,这种现象称为热脆(或红脆)。
图5-4说明硫对低碳钢塑性的影响。
但当钢中含有足够数量的锰便可消除硫的有害作用。
锰的硫化物熔点较高,并且它在钢中不是以网状包围晶粒,而是以球状形式存在,从而使钢的塑性提高。
另外,硫化物夹杂促使钢中带状组织形成,恶化冷轧板的深冲性能,降低钢的塑性。