结晶器铜板各种镀层特性一览表
结晶器铜板电镀镀层设计与控制概述

结晶器铜板电镀镀层设计与控制概述结晶器铜板电镀镀层设计与控制是指在铜板表面进行电镀处理,形成一层均匀、致密、具有良好导电性和耐腐蚀性的铜镀层。
这种电镀镀层广泛应用于半导体、光电子、电子通信、航天航空等领域,是制造这些产品的关键步骤之一。
铜板电镀过程主要由镀液配制、镀液搅拌、铜板电解切削、铜板电镀和铜板后处理等环节组成。
在镀液配制方面,需要根据具体的工艺要求,选择适当的镀液配方和比例,以确保铜镀层的均匀性和致密性。
常用的镀液配方包括硫酸铜、硫酸、硫酸二甲酯、硫酸铁等成分。
在镀液搅拌方面,是为了保持镀液的均匀性,防止镀液中的成分沉积和析出。
通常采用机械搅拌或气泡搅拌的方式进行。
机械搅拌可以通过搅拌器、搅拌棒等设备进行,气泡搅拌则是通过在槽内通入气体产生气泡来实现。
在铜板电解切削方面,主要是通过在铜板上施加电流,使铜板表面的杂质被去除,并形成平整的表面。
切削电压、切削时间和切削液浓度是影响切削质量的关键因素。
在铜板电镀方面,需要控制铜板电流密度、电镀时间和温度等参数,以保证铜镀层的均匀性和致密性。
电流密度是指单位面积所通过的电流量,通常使用铜板与相同面积的不锈钢作为阳极进行电镀。
电镀时间通常根据需要的镀层厚度来确定,温度则是控制电镀速度和镀层均匀性的重要因素。
在铜板后处理方面,主要是对电镀后的铜板进行清洗、干燥、检验和包装等环节,以确保产品的质量和外观。
还需要对整个电镀过程进行良好的控制和监测,包括镀液的浓度、PH值、温度、电阻率等参数,以及电镀设备的稳定性和安全性。
结晶器铜板电镀镀层设计与控制是一个复杂的过程,需要综合考虑材料性能、工艺要求和设备的特点,通过合理的配方和严格的控制参数,确保铜镀层的质量和稳定性。
方坯结晶器铜管电镀Ni-co,cr复合镀层

方坯结晶器铜管电镀Ni- Co+ Cr 复镀层技术(简称复合镀技术)方坯结晶器铜管电镀Ni- Co+ Cr 复镀层技术(简称复合镀技术)为了提高产品的市场竞争力, 各钢铁企业从生产的各个环节进行技术开发、技术改造, 力求在生产的每一个环节上提高设备的工作效率, 降低生产成本, 确保产品的质量,使企业的经济效益最大化。
连铸是炼钢生产的重要环节, 连铸结晶器是连铸机的心脏, 结晶器质量的好坏在相当大的程度上影响着连铸机的生产效率、连铸进程的稳定性和连铸坯质量, 直接关系到炼钢生产和经济效益。
连铸小方坯结晶器铜管是方坯结晶器最重要的组件, 也是经常需要更换的部件。
济南东方结晶器有限公司开发的方坯结晶器铜管电镀N i- Co+ Cr 复镀技术, 能大幅度地提高方坯结晶器铜管的使用寿命, 提高连铸机的作业效率和连铸技术的水平, 推动连铸技术的发展完善; 可以把结晶器铜管在连铸生产中的成本降到1. 0 元之内, 有效地降低连铸生产成本, 提高产品的竞争力。
在连铸生产中, 影响结晶器铜管质量的有以下两个关键指标: 一是铜管内腔锥度曲线, 另一个则是铜管内表面镀层。
目前, 国内普遍采用的是结晶器铜管内表面电镀硬铬, 由于铬和铜的收缩比差别较大, 影响了两者之间的结合力, 也直接制约了结晶器铜管的使用寿命。
因此, 研究开发结晶器铜管新镀层是提高结晶器铜管使用寿命的关键。
N i- Co 合金镀层与铜管有很好的结合力,在较高的温度下有较高的硬度和耐磨性, 表面套镀一层铬, 可以解决镀层脱铬问题及镀铬层的种种影响, 起到抗磨损、保护铜管的作用, 从而大大提高结晶器铜管的使用寿命。
历尽艰辛终结硕果烟台电镀技术服务部同济南东方结晶器有限公司开发结晶器铜管内表面采用电镀Ni- Co+ Cr 复合镀层工艺技术。
从2001 年4 月开始, 他们进行电镀Ni- Co+ Cr 复合镀层的120mm2 方坯结晶器铜管的连铸试验, 先后历时一年时间、分6批进行了电镀工艺试验。
结晶器铜管镀铬层厚度标准

结晶器铜管镀铬层厚度标准
1. 国家标准和行业标准,不同国家和行业对于镀铬层的厚度标
准可能会有不同的规定,这些标准通常由相关的标准化组织或行业
协会制定,以确保产品质量和安全性。
2. 使用环境和要求,镀铬层的厚度标准通常会根据产品的使用
环境和要求来确定。
例如,对于结晶器铜管这样的产品,如果需要
在潮湿或腐蚀性环境中使用,镀铬层的厚度可能会相对较厚,以增
强产品的耐腐蚀性能。
3. 工艺和成本考虑,制定镀铬层厚度标准时,还需要考虑到镀
铬工艺的可行性和成本因素。
通常会进行工艺优化和成本效益分析,以确定最合适的镀铬层厚度。
总的来说,结晶器铜管镀铬层厚度标准是一个综合考虑产品要求、行业标准、使用环境和成本等因素的结果。
具体的厚度标准需
要根据产品的具体情况和要求来确定,并且需要符合相关的国家标
准和行业规定。
结晶器铜管镀铬阳极种类及形状对镀层及通钢量的影响

结晶器铜管镀铬阳极种类及形状对镀层及通钢量的影响结晶器铜管镀铬时,最早使用纯铅阳极,导电性一般,需经常刷洗才能导电。
之后使用铅锡合金阳极,导电性好些,不用频繁刷洗阳极,阳极溶解物明显减少。
镀铬时使用的阳极材料有DSA钛阳极(贵金属氧化涂层钛阳极)pbsn(铅锡),石墨,钛基二氧化铅电极,这些材料都有能力把铬离子氧化成铬酸离子,而使用不溶性钛阳极时,阳极的氧化过电位比铅电极约低450mv,节约电能消耗.同时钛阳极可以大电流密度运行,使用寿命长,铬镀层与基体结合牢固,表面光亮洁净.涂层钛阳极又称为尺寸稳定性阳极DSA(dimensionally stable anode),DSA通常是在起骨架和导电作用的金属基体上刷涂或者是滚涂一层或者多层的活性涂层氧化物,所以也被称为金属涂层电极[1]。
钌系尺寸稳定阳极析氯催化活性高,被大量的用在氯碱工业和氯酸盐工业中;铱系尺寸稳定阳极具有高活性及阳极耐腐蚀稳定性,常被用于酸性介质中析氧电催化材料[1,2]。
钛基DSA阳极自被发现以来由于其阳极材料环保、尺寸稳定性好、无二次污染、基体可以重复利用、涂层可修复等优点受到人们的广泛关注,随着其不断的发展已经广泛用于电镀工业、废水处理、氯碱工业等多个领域。
钛基IrO2涂层阳极在酸性析氧环境中具有良好的电催化活性和稳定性,而且在电解过程中IrO2的溶解相当小可以忽略,不会对镀液产生污染,寿命长,而且Ti基体可以重复利用,涂层可以修复。
研究发现,IrO2涂层阳极在酸性溶液中表现出优于其他贵金属氧化物涂层的电催化活性和稳定性,但和高电流密度、高温介质条件下其使用寿命并不理想,但若与惰性组元TiO2,SnO2,Ta2O5和Nb2O5组合起来使用则可以有效地增加其使用寿命。
当和Ta2O5结合使用时,可使得涂层和基体的结合稳定,涂层电解消耗速率减小,而且还可以提高电流密度,即使是在较高的电流密度下也具有较长的使用寿命。
六价铬电镀工艺中通常采用铅锡合金电极进行电镀,在电镀过程中表面发生析氧反应;但在使用中析氧电位高,而且在使用过程容易在阳极表面生成一层导电性很差的铬酸铅膜,使得电镀过程中槽压较高;另外由于膜层和基体间的应力作用以及气体和溶液对阳极表面冲刷作用导致该阳极表面有颗粒进入到镀液中污染镀液并使阳极尺寸发生变化,这无疑增加了成本和能耗。
连铸结晶器铜板及镀层的应用进展

第2 8卷第 4期
20 0 7年 7月
特 殊 钢
S E A T E P CI L S E L
V0. 8 N . 12 . o 4
Jl 2 0 ・3 ・ uy 0 7 9
・
工艺 材 料 进 展 ・
连 铸 结 晶 器 铜 板 及 镀 层 的 应 用 进 展
1 影 响结 晶器铜 板寿 命 的 因素 结 晶器在 使 用 过 程 中主 要 存 在 边 缘磨 损 、 面 宽 热裂 纹 、 面收缩 、 蚀 等 问题 , 晶 器 的 表 面是 影 窄 腐 结
2 结 晶器铜 板母 材 的选 择
连铸 结晶器最初采用紫铜板或脱氧铜板 , 虽然 其导热性好 , 强度 和硬度低 , 但 耐磨性差 , 高温下强 度更低。现在 的结 晶器普遍 采用 A .u C—r u gC 、r — 、 zC C.r s u M .r u C.r g u等铜合金板制 r _ . 、 gZ. 、 r . . zA C C ZM C
高泽平
( 湖南工业 大学材料与冶金工程系 , 株洲 4 2 0 ) 10 0 摘 要 在正 常冷却条件下 , 结晶器 内壁工作温度为 2 0 ̄ 5 5 3 0℃ , 晶器铜板应 具有 良好 的导热 性和抗变形 结
能力 , 有较高的高温强度 、 面精度和耐磨性 。A —u和 C —r u板使用寿命优 于脱 氧铜和 紫铜 。结 晶器铜板镀层 表 gC r — ZC
的作用是 : 避免结晶器铜板产生 星状裂纹 ; 防止铜渗 入铸坯 ; 提高 润滑性 和耐磨 性 。 目前 主要 采用 N +C 和 N - i r i c 镀层及其他开发的新合金镀 层。文 中分析 了铜板及镀层 的特点 和应 用情况。 o 关键 词 连铸结 晶器 铜板 镀层
结晶器铜板各种镀层特性一览表

结晶器铜板各种镀层特性一览表在正常冷却条件下,结晶器内壁工作温度为250~350℃ ,结晶器铜板应具有良好的导热性和抗变形能力,有较高的高温强度、表面精度和耐磨性。
Ag —Cu 和Cr —Zr —Cu 板使用寿命优于脱氧铜和紫铜。
结晶器铜板镀层的作用是:避免结晶器铜板产生星状裂纹;防止铜渗入铸坯;提高润滑性和耐磨性。
目前主要采用Ni+Cr 和Ni-co ,Co-Ni Ni-Co-Fe 系镀层及其他开发的新合金镀层。
镀层种类镀层特性特点主成分名称硬度高温磨损量(Hv )(mg) 电镀Cr 系Cr9002硬度高,耐磨损性强。
E-Cr40015不出现Cr 特有的细裂纹,耐腐蚀性强。
Ni 系Ni200 60耐热、耐腐蚀性强。
可厚电镀(电铸)。
母模的复制性好。
Ni 合金650 18硬度高,耐磨损性强。
Co 系Co-Ni200 13与Ni 、Ni 系合金相比,其高温耐磨损性更优越。
K-2200 13Co-Ni 的延性(耐裂纹性)有改善。
Ni-Co-Fe系镍钴铁合金 700 13硬度高,耐磨损性强。
其高温耐磨损性更优越热喷镀NiCr 系MMS-1650 5耐磨损性超好。
BK-2400 4保持高耐磨损性的同时,耐裂纹性及耐粘钢性得以改善。
几种结晶器镀层的特点及使用情况解析镀铬层硬度较高,化学稳定性好,缺点为:安全厚度受限制,镀层无论厚薄都有裂纹存在;随温度升高硬度迅速降低,与铜结合时,其线膨胀系数、导热率相差太大,镀层容易在高温状态起皮剥落[ 。
因此,镀铬层影响结晶器寿命,其使用受到一定的限制。
镀镍层化学稳定性较好,封闭能力很强,且能镀至3—8 mm。
但其硬度(200 HV左右)经不起连铸钢坯的磨损,因此镀层寿命不高;采用镀厚镍的结晶器,使用寿命相对延长。
在铜板表面先镀l一4 mm的镍,经加工后再镀铬。
镍起中间过渡作用,可提高铬层与基体的结合强度,而外表面硬铬提高其耐磨性。
虽镀层性能。
如硬度和耐磨性可以达到要求,网状裂纹可以消除,结晶器寿命得到延长,但双镀层工艺相对复杂,由于铬与镍的热膨胀系数相差近2倍,使得铬层与镍层间的结合强度仍较低[Bl。
结晶器保护渣的性能和特性汇总
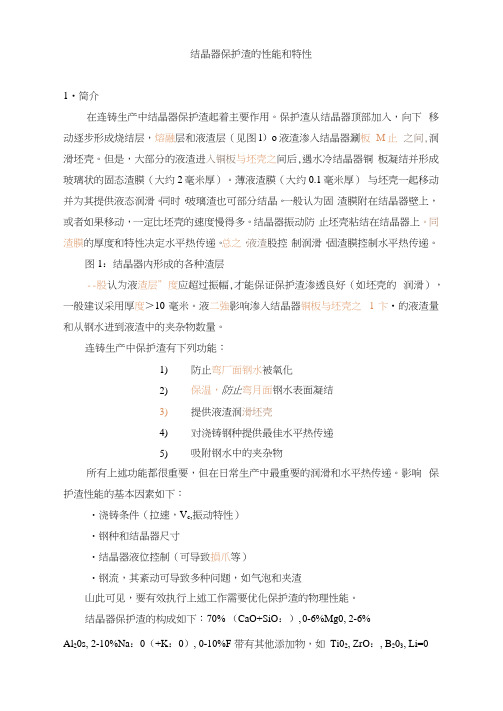
结晶器保护渣的性能和特性1•简介在连铸生产中结晶器保护渣起着主要作用。
保护渣从结晶器顶部加入,向下移动逐步形成烧结层,熔融层和液渣层(见图l)o液渣渗入结晶器涮板M止之间,润滑坯壳。
但是,大部分的液渣进入铜板与坯壳之间后,遇水冷结晶器铜板凝结并形成玻璃状的固态渣膜(大约2毫米厚)。
薄液渣膜(大约0.1毫米厚)与坯壳一起移动并为其提供液态润滑。
同时,玻璃渣也可部分结晶。
一般认为固渣膜附在结晶器壁上,或者如果移动,一定比坯壳的速度慢得多。
结晶器振动防止坯壳粘结在结晶器上。
同渣膜的厚度和特性决定水平热传递。
总之,液渣股控制润滑,固渣膜控制水平热传递。
图1:结晶器内形成的各种渣层--股认为液渣层”度应超过振幅,才能保证保护渣渗透良好(如坯壳的润滑),一般建议采用厚度>10毫米。
液二強影响渗入结晶器铜板与坯壳之1卞•的液渣量和从钢水进到液渣中的夹杂物数量。
连铸生产中保护渣有下列功能:1)防止弯厂面钢水被氧化2)保温,防止弯月面钢水表面凝结3)提供液渣润滑坯壳4)对浇铸钢种提供最佳水平热传递5)吸附钢水中的夹杂物所有上述功能都很重要,但在日常生产中最重要的润滑和水平热传递。
影响保护渣性能的基本因素如下:・浇铸条件(拉速,V c,振动特性)・钢种和结晶器尺寸・结晶器液位控制(可导致損爪等)・钢流,其紊动可导致多种问题,如气泡和夹渣山此可见,要有效执行上述工作需要优化保护渣的物理性能。
结晶器保护渣的构成如下:70% (CaO+SiO:), 0-6%Mg0, 2-6%Al20s, 2-10%Na:0(+K:0), 0-10%F 带有其他添加物,如Ti02, ZrO:, B203, Li=0和MnO。
碱度(%CaO/%SiO2)范围为0. 7-1. 3。
碳以焦碳,碳黑和石墨方式加入(2-20%), 1)可控制保护淹的熔化速度,2)可在结晶器上部形成CO (g),防止钢水氧化。
碳以固定碳方式存在]保护渣中,因而可防止保护渣结块,直到最后氧化掉。
结晶器铜板电镀镀层设计与控制概述

结晶器铜板电镀镀层设计与控制概述在电子、电器、机械、汽车等制造行业中,铜板电镀镀层是非常重要的一种涂层技术。
铜板电镀涂层的作用是提高基材的电导率、防腐保护、美观装饰等。
在该技术中,结晶器起到了至关重要的作用。
本文将从结晶器铜板电镀镀层设计与控制方面进行概述。
一、结晶器设计1.结晶器的种类根据不同的铜板电镀工艺和基材类型,结晶器的种类也有很多,如光板结晶器、铝基/镍基结晶器、钛合金结晶器等等。
结晶器的种类取决于其所需的耐蚀性、导热性、硬度和表面处理等特性。
2.结晶器的形状和尺寸在结晶器的设计中,其形状和尺寸也是至关重要的因素。
对于光板结晶器,其通常采用多孔状的设计形式;对于铝基/镍基结晶器,其需具备更高的耐腐蚀性和强度,所以可以采用复合材料的设计;对于钛合金结晶器,其表面应具备平滑度和均匀性,以免阻碍金属颗粒的出口。
3.结晶器的设计要点针对不同的铜板电镀工艺和使用要求,结晶器的设计还需要考虑到以下要点:(1)颗粒尺寸和分布;(2)可深度压裂和细分程度;(3)颗粒分离和扩散能力;(4)颗粒合成和沉积问题。
二、结晶器控制在铜板电镀过程中,结晶器电压的控制可以对镀层的性能进行调整。
对于结晶器而言,其电压可以通过改变阳极电流密度的方法进行控制。
增加结晶器电压可以促进金属颗粒的形成和沉积,从而提高镀层的颗粒度和均匀性。
在铜板电镀过程中,结晶器温度的控制可以对镀层的颗粒度和沉积速度产生影响。
通常情况下,结晶器的温度应该保持在一定的范围内,不过具体的温度控制方法则需根据不同的铜板电镀工艺而定。
在铜板电镀过程中,结晶器的流量也是需要进行控制的。
一般来说,结晶器的流量越大,则镀层颗粒度越细;反之则颗粒度越粗。
因此,流量的控制需要根据不同的铜板电镀工艺和使用要求进行调整。
总体来讲,结晶器铜板电镀镀层设计和控制是铜板电镀涂层技术中极为重要的一个环节。
结晶器的优化设计和控制,可以大大提高镀层的性能和使用寿命,从而增强铜板电镀涂层技术的竞争力和市场价值。
结晶器用铜板
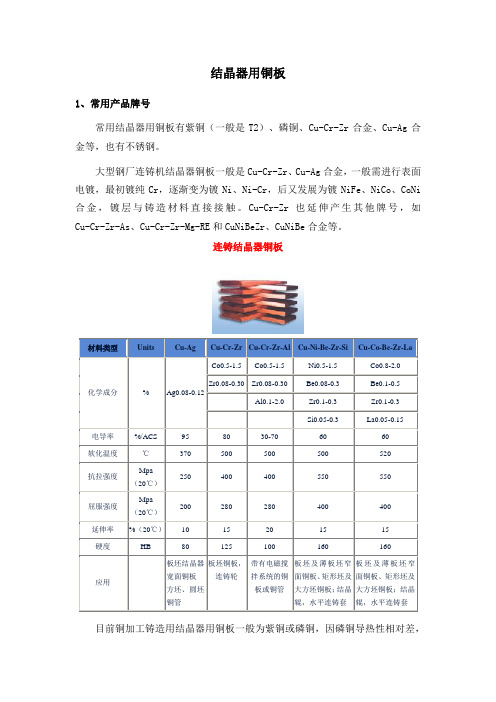
结晶器用铜板1、常用产品牌号常用结晶器用铜板有紫铜(一般是T2)、磷铜、Cu-Cr-Zr合金、Cu-Ag合金等,也有不锈钢。
大型钢厂连铸机结晶器铜板一般是Cu-Cr-Zr、Cu-Ag合金,一般需进行表面电镀,最初镀纯Cr,逐渐变为镀Ni、Ni-Cr,后又发展为镀NiFe、NiCo、CoNi 合金,镀层与铸造材料直接接触。
Cu-Cr-Zr也延伸产生其他牌号,如Cu-Cr-Zr-As、Cu-Cr-Zr-Mg-RE和CuNiBeZr、CuNiBe合金等。
连铸结晶器铜板目前铜加工铸造用结晶器用铜板一般为紫铜或磷铜,因磷铜导热性相对差,价格也高,紫铜更常见。
铜板有电镀和非电镀两种,黄铜等铸造温度相对较低的产品,进行电镀,镀层与铸造材料直接接触,如现有精诚公司立式半连续铸造黄铜等使用的结晶器;紫铜、高铜合金等铸造温度相对较高的产品,铜材一般不与铸造材料直接接触,而是通过石墨结晶器与铸造材料接触,铜板不需要电镀,如精诚公司与鑫科公司水平连铸磷青铜用结晶器铜板和立式半连续铸紫铜铸造等用结晶器。
2、产品规格主要有两种形式。
一种是黄铜等立式半连续铸造结晶器,其材质主要是紫铜,结构是封闭环形式,内腔比铸造材料外形略大,内面进行电镀,最外除了钢衬板外,其余全部是紫铜,厚度约60mm,长度约180~220mm。
一种是铜板形式,其材质包括上述各种牌号。
厚度规格一般约为40mm以下,长度约700~1000mm,宽度根据铸造材料宽度而定。
3、生产工艺结晶器材料应具有高强度,高硬度,耐磨性及导热性好的性能,Cr,Zr,Mg 都是降低铜导热性能较小的元素,且Cr,Zr,Mg均可提高铜的力学性能。
为了保证材料具有良好的综合性能,采用了如下的工艺:熔炼→铸锭→热锻→固溶析出热处理→机械加工→电镀。
熔炼:电解铜板加入坩埚中→加热→加入覆盖剂→熔化→脱氧→加入中间合金→均匀化→出炉(温度控制在≤1250℃)。
铸锭:将熔炼好的合金扒渣→测温→浇注在预热的模型中。
结晶器用铜板
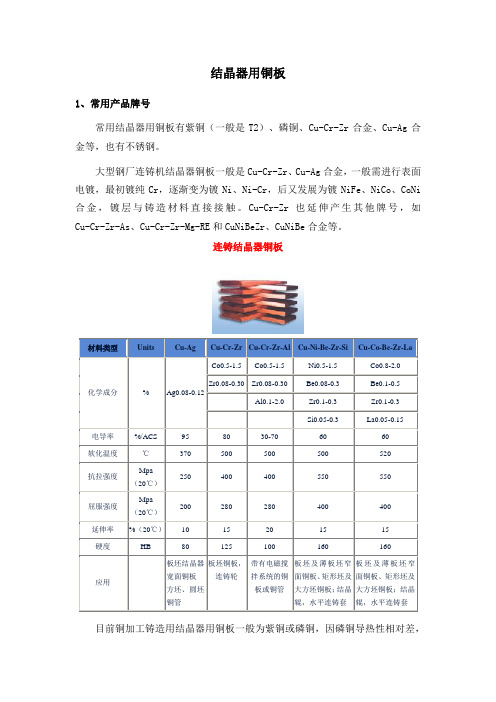
结晶器用铜板1、常用产品牌号常用结晶器用铜板有紫铜(一般是T2)、磷铜、Cu-Cr-Zr合金、Cu-Ag合金等,也有不锈钢。
大型钢厂连铸机结晶器铜板一般是Cu-Cr-Zr、Cu-Ag合金,一般需进行表面电镀,最初镀纯Cr,逐渐变为镀Ni、Ni-Cr,后又发展为镀NiFe、NiCo、CoNi 合金,镀层与铸造材料直接接触。
Cu-Cr-Zr也延伸产生其他牌号,如Cu-Cr-Zr-As、Cu-Cr-Zr-Mg-RE和CuNiBeZr、CuNiBe合金等。
连铸结晶器铜板目前铜加工铸造用结晶器用铜板一般为紫铜或磷铜,因磷铜导热性相对差,价格也高,紫铜更常见。
铜板有电镀和非电镀两种,黄铜等铸造温度相对较低的产品,进行电镀,镀层与铸造材料直接接触,如现有精诚公司立式半连续铸造黄铜等使用的结晶器;紫铜、高铜合金等铸造温度相对较高的产品,铜材一般不与铸造材料直接接触,而是通过石墨结晶器与铸造材料接触,铜板不需要电镀,如精诚公司与鑫科公司水平连铸磷青铜用结晶器铜板和立式半连续铸紫铜铸造等用结晶器。
2、产品规格主要有两种形式。
一种是黄铜等立式半连续铸造结晶器,其材质主要是紫铜,结构是封闭环形式,内腔比铸造材料外形略大,内面进行电镀,最外除了钢衬板外,其余全部是紫铜,厚度约60mm,长度约180~220mm。
一种是铜板形式,其材质包括上述各种牌号。
厚度规格一般约为40mm以下,长度约700~1000mm,宽度根据铸造材料宽度而定。
3、生产工艺结晶器材料应具有高强度,高硬度,耐磨性及导热性好的性能,Cr,Zr,Mg 都是降低铜导热性能较小的元素,且Cr,Zr,Mg均可提高铜的力学性能。
为了保证材料具有良好的综合性能,采用了如下的工艺:熔炼→铸锭→热锻→固溶析出热处理→机械加工→电镀。
熔炼:电解铜板加入坩埚中→加热→加入覆盖剂→熔化→脱氧→加入中间合金→均匀化→出炉(温度控制在≤1250℃)。
铸锭:将熔炼好的合金扒渣→测温→浇注在预热的模型中。
连铸机结晶器铜板镀层性能对比研究及镀层常见缺欠

连铸机结晶器铜板镀层性能对比研究及镀层常见缺欠连铸机结晶器铜板镀层常见缺陷一般为磨损、腐蚀、划伤、龟裂、脱落等。
对镀铬层来说前3种是正常的,对合金镀层来说前4种是正常的连铸机结晶器铜板镀层常见缺陷一般为磨损、腐蚀、划伤、龟裂、脱落等。
对镀铬层来说前3种是正常的,对合金镀层来说前4种是正常的,脱落是镀层的质量问题。
镀铬层脱落的一般原因是:(1)镀层在镀覆过程中,如果镀前处理不当,容易产生镀层结合不好,结合强度不够,遇到外力作用起层而脱落。
(2)正常的镀层,由于镀层材质与母材(铜或铜合金)比较,由于热膨胀系数差异较大,铜板受热后产生膨胀,镀层与母材之间产生内应力,当应力大于结合力时就出现起层脱落。
(3)由于生产中冷却的连续性、稳定性不好,出现较大的间歇性变化,这也是主要原因之一。
(4)由于铸坯表面出现结瘤造成磨损严重,出现耕犁划伤磨损而使镀层脱落。
结晶器是连铸的核心部件,结晶器铜板作为连铸从液态钢水到凝固成固态坯壳的重要导热部件,其质量好坏直接影响到铸坯的表面质量、连铸机拉速等指标。
熔融的钢水流经结晶器铜板,在外界冷却水的作用下结晶成坯,并被引锭杆从结晶器中拉出。
经常拉坯使结晶器铜板磨损严重,更换频繁,不仅降低生产效率,而且消耗大量的结晶器。
为提高结晶器铜板的使用寿命,国内外相关单位及专家对铜板材料及镀层展开了长期的、深入地研究,取得了很大的成果。
目前,国内外开始应用热解析技术进行结晶器设计最佳化及镀层选择的研究,热解析技术在结晶器铜板上的应用大大提高了提高结晶器铜板的寿命。
连铸机结晶器铜板采用镀层主要目的是:(1)提高铸机备件使用寿命,降低备件特别是有色金属消耗。
(2)提高铜板表面硬度、耐磨性、连铸机结晶器铜板采用镀层主要目的是:(1)提高铸机备件使用寿命,降低备件特别是有色金属消耗。
(2)提高铜板表面硬度、耐磨性、减少摩擦力,提高表面光滑程度,可以减少粘结,防止对某些合金钢钢坯因渗铜而产生星状裂纹,从而提高铸坯质量和成材率。
结晶器铜板电镀镀层设计与控制概述

结晶器铜板电镀镀层设计与控制概述一、引言铜镀层是电镀工艺中非常重要的一环,通常用于增加金属表面的导电性、耐腐蚀性以及美观性。
而结晶器铜板电镀镀层是其中的一种特殊镀层,能够在铜基板上形成致密均匀的结晶形态,具有优异的导电性和耐腐蚀性。
本文将就结晶器铜板电镀镀层的设计与控制进行概述,分析其工艺流程、关键参数及控制要点,以期为相关领域的研究和应用提供参考。
二、工艺流程结晶器铜板电镀镀层工艺流程主要包括表面预处理、电镀和后处理三个主要步骤。
1. 表面预处理:表面预处理是镀层工艺中非常重要的一环,其目的是清理基材表面的杂质和氧化物,以确保镀层与基材之间的粘接力和镀层的致密性。
通常包括去油、酸洗、活化、镍化等步骤。
2. 电镀:电镀是结晶器铜板电镀镀层的核心步骤,直接影响着镀层的质量和性能。
电镀过程中,铜离子在电场的作用下沉积到基材表面上,形成致密的结晶结构。
关键参数包括电镀液的成分、温度、pH值、电流密度、搅拌速度等。
合理控制这些参数可以有效提高镀层的致密性和均匀性。
3. 后处理:后处理是为了提高镀层的表面光洁度和耐腐蚀性而进行的一系列处理步骤,通常包括水洗、干燥、涂漆、包装等。
三、关键参数及控制要点1. 电镀液成分:结晶器铜板电镀镀层的电镀液一般由铜盐、添加剂、酸碱调节剂和助镀剂组成。
其中铜盐的种类和浓度、添加剂的种类和用量、酸碱调节剂的类型和浓度都会直接影响着镀层的结晶性、致密性和导电性。
需要对电镀液的成分进行精确控制,保证电镀液的稳定性和一致性。
2. 温度和pH值:电镀液的温度和pH值是影响镀层质量的重要参数。
一般来说,温度过高易导致镀层内应力过大、结晶不致密;温度过低则易导致镀层内应力过小、导电性不佳。
pH值偏离正常范围,也会使镀层结晶不良、表面粗糙。
因此需要根据具体工艺要求,合理控制电镀液的温度和pH值。
3. 电流密度和搅拌速度:电流密度是电镀过程中控制镀层厚度和结晶度的重要参数,搅拌速度则影响着电镀液的对流速度和溶液的均匀性。
结晶器铜板电镀镍钴铁工艺研究

结晶器铜板电镀镍钴铁工艺研究摘要:Ni-Cr, Ni—Fe。
Ni-Co Ni-Co- Fe镀层在结晶器铜板上的开发应用,详细阐述以上四种镀层的优劣,同时对结晶器铜板电镀镍钴铁的优越性进行了详细的阐述。
引言:结晶器铜板在工作过程中由于长时间经受高温铁水的冲刷,存在较严重的摩擦和磨损,其损坏的主要形式是产生热裂纹、磨损和腐蚀;表面的局部损坏又往往造成整个部件失效,最终导致设备报废。
据统计,一套结晶器的价格在7—120万元,我国冶会企业每年铜结晶器的消耗在2o亿元以上,是除了轧辊之外的第二大冶金耗材;而且铜及铜合金的资源紧缺,近期来价格又有不断上涨的趋势;因此提高结晶器铜板表面的耐磨性和耐热性是提高经济效益和生产效率的根本措施,具有很好的科学研究意义和实际应用价值。
1,结晶器铜板的表面处理表面处理技术,即利用各种物理的、化学的或机械的工艺方,法使材料表面获得特殊的成分、组织结构与性能,以提高其耐磨抗蚀性能,延长其使用寿命的技术,也可称为表面加工等。
常用的表面技术有:堆焊技术、熔结技术、电镀、电刷镀及化学镀技术、非金属镀技术、热喷涂技术、物理与化学气相沉积、化学热处理、激光表面处理、电子束技术相变硬化、离子注入等。
其中,利用电镀、热喷涂技术、化学热处理强化结晶器铜板在国内或国外已经有所应用。
(1)电镀在表面处理技术中,电镀是最有效的方法之一。
电镀是指在含有欲镀金属的盐类溶液中,在直流电的作用下,以被镀基体金属为阴极,以欲镀金属或其它惰性导体为阳极,通过电解作用,在基体表面上获得结合牢固的金属膜的表面工程技术。
目前,利用电镀强化的结晶器有单镀层铜板和复合镀层铜板。
单一镀层主要用铬或镍;现已开发结晶器复合镀层铜板,如Ni—cr,Ni-Fe,Ni—Fe—w,Ni—Fe—co,Ni co,Ni—w 等效果很好。
此外,还有Ni—w—P镀层等另外,为降低生产成本,优化我国冶金技术设备,国内已有人进行电镀镍及其合金的研究,其中,以铜铬锆为材质的结晶器电镀镍铁,镍钴,钴镍镀层已经在板坯连铸机获得应用。
结晶器铜板电镀镀层设计与控制概述

结晶器铜板电镀镀层设计与控制概述随着科技的不断发展,电镀技术在工业生产中发挥着越来越重要的作用。
电镀工艺可以通过在金属表面形成一层均匀、致密、具有良好性能的镀层,从而提高材料的抗腐蚀性、耐磨性和表面光泽度。
在电镀工艺中,结晶器铜板电镀是一种常见的表面处理工艺,特别适用于半导体、电子、通讯等领域。
结晶器铜板电镀是一种通过电化学方法在金属表面镀上一层铜薄膜的工艺。
其原理是在合适的工艺条件下,将含有铜离子的电解液通过阳极和阴极的电流作用下,在金属表面沉积形成一层致密、均匀的铜层。
想要获得理想的铜板电镀镀层,需要严格控制工艺参数,包括电解液成分、电流密度、温度、搅拌速度等。
只有合理设计和严格控制这些参数,才能确保获得高质量的镀层产品。
在结晶器铜板电镀工艺中,镀层的设计和控制是至关重要的。
镀层的设计需要考虑到材料的特性,需要保证镀层的致密性、平整度和良好的导电性。
需要从工艺参数入手,通过调整电解液成分、电流密度、温度等参数,来控制镀层的厚度、结晶度和表面质量。
只有合理设计和控制了这些参数,才能保证获得符合要求的铜板电镀镀层。
在结晶器铜板电镀工艺中,电解液的成分是至关重要的。
电解液中的铜盐对镀层的性能有着直接影响,因此需要合理选择电解液成分,保证镀层的致密性和均匀性。
需要定期检测电解液的成分,确保铜盐浓度、PH值、杂质含量等参数符合要求。
电流密度也是影响镀层质量的重要参数。
过高或过低的电流密度都会导致镀层的质量下降,影响镀层的均匀性和致密性。
在实际生产中,需要根据材料的特性和要求,合理设定电流密度,避免出现镀层过厚或者不足的情况。
温度和搅拌速度也是影响镀层质量的重要因素。
适当的温度和搅拌速度可以提高电镀效率,保证镀层的均匀性和致密性。
在镀层工艺中,需要严格控制温度和搅拌速度,避免出现温差过大或者搅拌不均匀的情况。
在结晶器铜板电镀工艺中,除了上述参数外,还需要考虑到阳极和阴极的设计,以及电镀设备的维护和保养。
结晶器铜板镀镍合金主要工艺参数控制

2 . 2温度
镀液温度会影响对流传质速度, 镀液的黏度 ( 进 而影响 电 迁 移速度) , 影 响电极电位 与表面活性物质的吸脱附性质 ( 进而影 响阴极极化效果) , 影响 允许采用 的阴极电流密度大小、 物质溶解 的好坏、 镀液成分的交互影响。同 时, 氨基磺酸镍 的稳定性差, 在高温下容易发生水解 。因此氨基磺 酸盐 电镀 液的温度不能超过7 O ℃, 一般控制在6 0  ̄ C 以下 。根据生产实际, 镀镍液温度
而且镀镍层的孔隙率是 比较高的, 为 了减少或防止针孔的产生 , 需要 向镀液 中加入少量的润湿剂 。
4杂质控 制 电镀液 中杂质 的来源是多方面的, 其 污染 物主要有 尘埃, 阳极泥渣 , 无 机杂质和有机杂质 。 4 . 1尘埃和 阳极泥渣 空气质量差时,空气 中的尘埃一旦落到镀镍槽 内, 会影 响镀液 的清洁
科 学 发 展
锻 鸯 与赌寓
结晶器铜板镀镍合金主要工艺参数控制
李
摘
尹 Leabharlann ( 马钢表 面工程 技术公司 安徽 马鞍 山 2 4 3 0 0 0 ) 要: 本文 以马钢特种 电镀厂结晶器铜板镀镍钻钨三元合 金为例 , 对其 工艺 条件 , 镀液组分 , 杂质情况, 以及控制方法 进行 分析。 并结合实际操作 经
度, 镀出的镍合金层会 出现粗糙、 毛刺 、 针孔等弊病 。 电镀厂镀槽四周配备 了 侧吸风装置, 能够有效避免灰尘直接落入槽内, 不生产时, 采用槽盖予 以隔
离。
另外, 可溶性阳极内含有大量的碳 、 硫、 锰、 铁等杂质, 组织不均一 , 溶解 性差, 易生成阳极泥渣 。电镀厂在 阳极框外包覆布套 以收集阳极泥渣 , 避免
控 制在5 5 5 ℃左右。 2 . 3 P H值 P H 值对 电镀 质量 影响很大, P H 值 过高和过低 时分 别会产生镀层氢 夹 杂和氢氧化物夹杂, 增 大镀层 内应力和孔隙率 。 要注意 的是, P H 值 ≤3 时, 氨 基磺 酸镍发生水解 , 使 电解液不稳定。因此 , P H / I  ̄ 要严格在一定范围内, 以 3 . 4 0 - ' 3 . 7 0 为宜。 3镀 液组分分析 目 前 结晶器铜板电镀使用 的镍钴钨三元合金 电镀液 , 主要成分包括: 氨 基磺 酸镍 , 氨基磺酸钻 , 钨盐 , 氯化镍 , P H 缓冲剂和润湿剂。 3 . 1 主盐: 氨基磺酸镍 , 氨基磺酸钴, 钨盐 氨基磺酸镍 , 氨基磺酸钴 , 钨盐作为 电镀液 中的主盐 , 是必不可少 的重
结晶器铜板镍-钴-碳化硅复合镀层性能实验研究
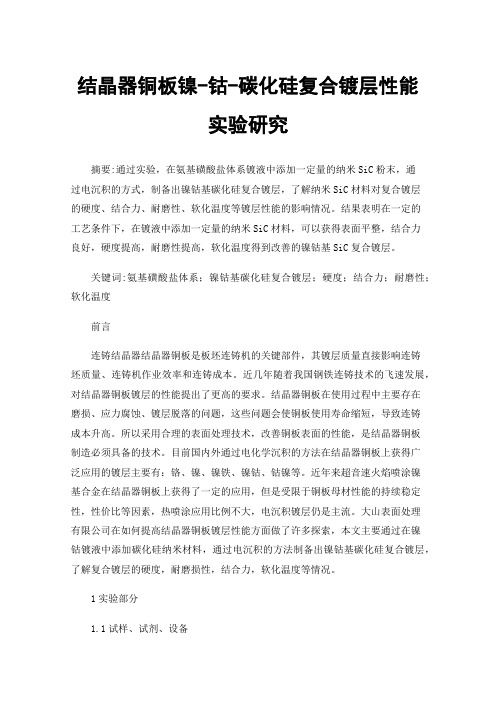
结晶器铜板镍-钴-碳化硅复合镀层性能实验研究摘要:通过实验,在氨基磺酸盐体系镀液中添加一定量的纳米SiC粉末,通过电沉积的方式,制备出镍钴基碳化硅复合镀层,了解纳米SiC材料对复合镀层的硬度、结合力、耐磨性、软化温度等镀层性能的影响情况。
结果表明在一定的工艺条件下,在镀液中添加一定量的纳米SiC材料,可以获得表面平整,结合力良好,硬度提高,耐磨性提高,软化温度得到改善的镍钴基SiC复合镀层。
关键词:氨基磺酸盐体系;镍钴基碳化硅复合镀层;硬度;结合力;耐磨性;软化温度前言连铸结晶器结晶器铜板是板坯连铸机的关键部件,其镀层质量直接影响连铸坯质量、连铸机作业效率和连铸成本。
近几年随着我国钢铁连铸技术的飞速发展,对结晶器铜板镀层的性能提出了更高的要求。
结晶器铜板在使用过程中主要存在磨损、应力腐蚀、镀层脱落的问题,这些问题会使铜板使用寿命缩短,导致连铸成本升高。
所以采用合理的表面处理技术,改善铜板表面的性能,是结晶器铜板制造必须具备的技术。
目前国内外通过电化学沉积的方法在结晶器铜板上获得广泛应用的镀层主要有:铬、镍、镍铁、镍钴、钴镍等。
近年来超音速火焰喷涂镍基合金在结晶器铜板上获得了一定的应用,但是受限于铜板母材性能的持续稳定性,性价比等因素,热喷涂应用比例不大,电沉积镀层仍是主流。
大山表面处理有限公司在如何提高结晶器铜板镀层性能方面做了许多探索,本文主要通过在镍钴镀液中添加碳化硅纳米材料,通过电沉积的方法制备出镍钴基碳化硅复合镀层,了解复合镀层的硬度,耐磨损性,结合力,软化温度等情况。
1实验部分1.1试样、试剂、设备试样:脱氧磷铜试样,规格100mmx80mmx5mm,纯度Cu≥99.8试剂:氨基磺酸镍、氨基磺酸钴、氯化镍、低泡润湿剂、硼酸、碳化硅(40nm级)、分散剂、氨基磺酸、磷酸,纯度均采用生产现场使用的电镀级化学品设备:0~10A高频直流电源、实验电镀槽、无尘空气搅拌泵、微型过滤机,钛篮、超声波振动清洗器、马弗炉、耐磨试验机、弯曲实验机、显微维氏硬度计。
- 1、下载文档前请自行甄别文档内容的完整性,平台不提供额外的编辑、内容补充、找答案等附加服务。
- 2、"仅部分预览"的文档,不可在线预览部分如存在完整性等问题,可反馈申请退款(可完整预览的文档不适用该条件!)。
- 3、如文档侵犯您的权益,请联系客服反馈,我们会尽快为您处理(人工客服工作时间:9:00-18:30)。
结晶器铜板各种镀层特性一览表
在正常冷却条件下,结晶器内壁工作温度为250~350℃ ,结晶器铜板应具有良好的导热性和抗变形能力,有较高的高温强度、表面精度和耐磨性。
Ag —Cu 和Cr —Zr —Cu 板使用寿命优于脱氧铜和紫铜。
结晶器铜板镀层的作用是:避免结晶器铜板产生星状裂纹;防止铜渗入铸坯;提高润滑性和耐磨性。
目前主要采用Ni+Cr 和Ni-co ,Co-Ni Ni-Co-Fe 系镀层及其他开发的新合金镀层。
镀层种类
镀层特性
特点
主成分
名称
硬度
高温磨损量
(Hv )
(mg) 电镀
Cr 系
Cr
900
2
硬度高,耐磨损性强。
E-Cr
400
15
不出现Cr 特有的细裂纹,耐腐蚀性强。
Ni 系
Ni
200 60
耐热、耐腐蚀性强。
可厚电镀(电铸)。
母模的复制性好。
Ni 合金
650 18
硬度高,耐磨损性强。
Co 系
Co-Ni
200 13
与Ni 、Ni 系合金相比,其高温耐磨损性更优越。
K-2
200 13
Co-Ni 的延性(耐裂纹性)有改善。
Ni-Co-Fe
系
镍钴铁合
金 700 13
硬度高,耐磨损性强。
其高温耐磨损性更优越
热喷镀
NiCr 系
MMS-1
650 5
耐磨损性超好。
BK-2
400 4
保持高耐磨损性的同时,耐裂纹性及耐粘钢性得以改善。
几种结晶器镀层的特点及使用情况解析
镀铬层硬度较高,化学稳定性好,缺点为:安全厚度受限制,镀层无论厚薄都有裂纹
存在;随温度升高硬度迅速降低,与铜结合时,其线膨胀系数、导热率相差太大,镀层容易在高温状态起皮剥落[ 。
因此,镀铬层影响结晶器寿命,其使用受到一定的限制。
镀镍层化学稳定性较好,封闭能力很强,且能镀至3—8 mm。
但其硬度(200 HV左
右)经不起连铸钢坯的磨损,因此镀层寿命不高;采用镀厚镍的结晶器,使用寿命相对延长。
在铜板表面先镀l一4 mm的镍,经加工后再镀铬。
镍起中间过渡作用,可提高铬层
与基体的结合强度,而外表面硬铬提高其耐磨性。
虽镀层性能。
如硬度和耐磨性可以达
到要求,网状裂纹可以消除,结晶器寿命得到延长,但双镀层工艺相对复杂,由于铬与镍的热膨胀系数相差近2倍,使得铬层与镍层间的结合强度仍较低[Bl。
热喷涂Ni·cr层具有高硬度(600 I-IV)、高温耐蚀性和抗高温氧化性,能显著提高结
晶器使用寿命 J。
但热喷涂工艺在操作上比较复杂。
国内开发的Ni—Fe合金镀层熔点一般为l 400 oC,耐高温能力强,抗热冲击性能好。
由于铁的加入导致其硬度(500 HV)高于镀镍层,耐磨性为镀镍层的2倍,结晶器寿命比
单一镀镍层的延长2倍-l。
但Ni.Fe镀层抗电位腐蚀和抗热交变性能很差,并且Ni.Fe 合金镀液不易控制,控制不好,成品率会降低。
Ni-co合金镀层受热后表层陶瓷化,润滑性好,可避免粘结现象;软化温度高,在较高
温下能形成稳定的高硬度耐磨表面;摩擦系数较低,铜板镀层不易产生热裂纹;与母材的结合力强,适用于铜板表面温度较高和缓冷却型结晶器铜板-l ,可使结晶器的使用寿命
提高到2 000炉次以上。
近年来国内外开发的新合金镀层,主要有:Ni—P、Ni—W—Fe、Ni—W —P、Ni—Co—W、Ni—Fe—W—Co、RE—Ni—W—P—SiC、Ni-Co-Fe陶瓷涂层、纳米复合镀层等。
新合金镀层结合力强、硬度高、耐磨、抗氧化性能好,显著提高了高速连铸结晶器使用寿命和铸坯表面质量。
国内结晶器铜板表面处理大多局限于使用Cr、Ni、Ni—Fe、Ni—Cr镀层,其中电镀Cr、Ni
—Cr层不可避免的缺陷限制了其应用。
Ni—Fe层也因为其缺点正在逐步被Ni、Ni—co层取代。
电镀Ni层是目前工艺较成熟、应用较多的镀层。
国内Ni—co层的研究已经取得了一定成果并有着良好的应用前景。
Ni-Co-Fe系电镀层无论在镀层性能、操作工艺和生产成本上
都具有优势,是最具有发展前景的镀层。