连铸结晶器铜板涂层的研究进展
连铸结晶器铜板及镀层的应用进展

第2 8卷第 4期
20 0 7年 7月
特 殊 钢
S E A T E P CI L S E L
V0. 8 N . 12 . o 4
Jl 2 0 ・3 ・ uy 0 7 9
・
工艺 材 料 进 展 ・
连 铸 结 晶 器 铜 板 及 镀 层 的 应 用 进 展
1 影 响结 晶器铜 板寿 命 的 因素 结 晶器在 使 用 过 程 中主 要 存 在 边 缘磨 损 、 面 宽 热裂 纹 、 面收缩 、 蚀 等 问题 , 晶 器 的 表 面是 影 窄 腐 结
2 结 晶器铜 板母 材 的选 择
连铸 结晶器最初采用紫铜板或脱氧铜板 , 虽然 其导热性好 , 强度 和硬度低 , 但 耐磨性差 , 高温下强 度更低。现在 的结 晶器普遍 采用 A .u C—r u gC 、r — 、 zC C.r s u M .r u C.r g u等铜合金板制 r _ . 、 gZ. 、 r . . zA C C ZM C
高泽平
( 湖南工业 大学材料与冶金工程系 , 株洲 4 2 0 ) 10 0 摘 要 在正 常冷却条件下 , 结晶器 内壁工作温度为 2 0 ̄ 5 5 3 0℃ , 晶器铜板应 具有 良好 的导热 性和抗变形 结
能力 , 有较高的高温强度 、 面精度和耐磨性 。A —u和 C —r u板使用寿命优 于脱 氧铜和 紫铜 。结 晶器铜板镀层 表 gC r — ZC
的作用是 : 避免结晶器铜板产生 星状裂纹 ; 防止铜渗 入铸坯 ; 提高 润滑性 和耐磨 性 。 目前 主要 采用 N +C 和 N - i r i c 镀层及其他开发的新合金镀 层。文 中分析 了铜板及镀层 的特点 和应 用情况。 o 关键 词 连铸结 晶器 铜板 镀层
结晶器铜板热喷涂技术的研究进展
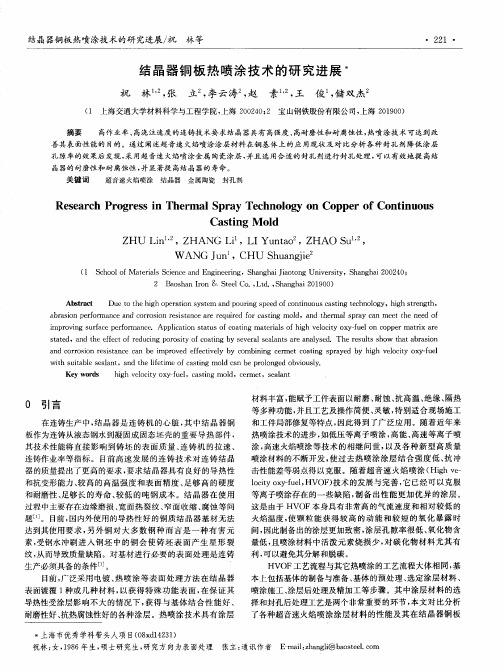
材料丰 富 , 能赋予 工件表 面以耐 磨 、 耐蚀 、 高 温 、 抗 绝缘 、 隔热 等多种 功能 , 并且工 艺及操 作简 便 、 敏 , 别适 合 现场施 工 灵 特 和工件 局部修 复等特 点 , 因此得 到 了广 泛 应用 。随着 近 年来 热喷涂技 术 的进 步 , 如低压 等离 子喷涂 , 高能 、 速 等离 子喷 高
结晶 器铜 板 热喷涂技 术的研 究进展 / 祝
林等
・2 1・ 2
结 晶器铜 板 热 喷ห้องสมุดไป่ตู้技 术 的研 究进 展
祝 林 , 张 立 李云涛 赵 , , 素h , 王 俊 储双杰。 ,
( 上 海 交 通 大 学 材 料 科 学 与 工 程学 院 , 海 20 4 ; 宝 山 钢 铁 股 份 有 限公 司 , 1 上 0202 上海 2 10 ) 0 9 0
摘要
高作业率 、 高浇注速度的连铸技 术要 求结 晶器具有 高强度 、 高耐磨性和耐腐蚀 性, 热喷涂技术 可达 到改
善其表 面性能的 目的。通过 阐述超音速 火焰喷涂涂层材料 在铜基体上 的应 用现状及 对比分析各种 封孔剂 降低涂层 孔隙率的效果后发现 , 用超音速火焰喷涂金属 陶瓷涂层 , 采 并且 选用合适 的封孔剂进行封孔 处理 , 以有效地提 高结 可 晶器的耐磨性和耐腐蚀性 , 并显著提 高结晶器的寿命 。
ZHU n 一,ZH ANG i,L n a H A0 u 一, Li L IYu t o ,Z S
WANG u C J n , HU h a gi S un j e
( S h o fM ae il S in ea d En ie r g h n h i ioo g Unv riy h n h i 0 2 0 1 c o l tras ce c n gn ei ,S a g a a tn iest ,S a g a 0 4 ; o n J 2
结晶器铜板划伤问题研究及措施探讨

结晶器铜板划伤问题研究及措施探讨闫凡熙① 王计超 张佩立 岳志坤 李滨(首钢京唐钢铁联合责任有限公司炼钢作业部 河北唐山063210)摘 要 对结晶器铜板在使用过程中出现划伤、搓伤缺陷进行分析,采用合金分析仪对划伤部位进行检测,表明窄面铜板角部镀层出现起皮、脱落缺陷,在大面夹紧时将起皮镀层压入结晶器角缝,致使铜板在结晶器宽度调节过程中发生划伤、搓伤。
对镀层缺陷进一步分析,镀层缺陷主要为镀层质量差、镀层偏厚、断面安排不合理、日常检查不到位等原因造成。
并对这一问题进行措施探讨,可以在控制镀层厚度、合理安排浇铸端面、开发内、外倒角铜板、优化镀层成分等方面着手,最终达到延长铜板寿命的目的。
关键词 结晶器 铜板划伤 镀层起皮 镀层脱落中图法分类号 TG155.4 文献标识码 BDoi:10 3969/j issn 1001-1269 2022 Z2 0301 前言随着钢铁工业的不断发展及连铸技术的日益提高,发展高效率、高质量连续铸钢技术已成为钢铁工业的一个重要方向,同时连铸比已成为衡量钢铁工业水平的重要标志之一[1-3]。
其中结晶器是连铸机的心脏部位,在连铸机中起到至关重要的作用,其质量的好坏直接影响到连铸机作业率[4-5]。
鉴于结晶器在连铸生产中的重要性,本文对结晶器在使用过程中产生铜板划伤缺陷这一问题进行研究分析,并对相关措施进行探讨,用于减少铸机非计划检修,提高铸机生产稳定性。
2 结晶器铜板划伤情况结晶器铜板在铸机作业过程承受着高温氧化、温度梯度过大而产生的变形、冷却水与保护渣成分化学腐蚀、高温蒸汽引起的气蚀、引锭、拉坯、振动产生的摩擦磨损等恶劣工况,使铜板产生调宽伤痕、宽度收缩、磨损和腐蚀等缺陷。
铜板表面损伤示意图如图1所示[6-7]。
图1 铜板表面损伤示意图[6]一般铜板调宽伤痕为铜板表面轻微缺陷,可以通过在线打磨予以处理。
但是结晶器在使用过程中偶尔会出现宽面铜板划伤、搓伤等严重缺陷,具体宏观形貌如图2所示。
结晶器铜板电镀Co—Ni及热喷涂技术在宽板坯结晶器的应用实践

结晶器铜板电镀Co—Ni及热喷涂技术在宽板坯结晶器的应用实践【摘要】概述了连铸结晶器铜板表面处理技术及涂层的应用现状,指出电镀Co-Ni技术和热喷涂合金技术是当前最具代表性的新技术;分析了Co-Ni、热喷涂涂层的组织结构、热稳定性能和耐磨损性能,并与纯Ni、Ni-Fe、Ni-Co、涂层进行了比较分析,探讨了两种涂层具有优异性能的原因;介绍了宽面镀Co-Ni 铜板和窄面热喷涂铜板配套结晶器,在国内最宽的板坯连铸机南钢中厚板板卷厂1#连铸机上的应用实践,Co-Ni镀层和热喷涂涂层大大提高了结晶器铜板的使用寿命,解决了宽板坯结晶器铜板下角部局部磨损的难题,取得了良好的经济效益,具有很好的应用前景。
【关键词】连铸结晶器铜板;表面技术;电镀技术;热喷涂技术引言连铸结晶器铜板质量的好坏直接影响铸坯的质量和连铸机的作业率。
南钢中厚板卷厂1#连铸机是国内最宽、宽厚比最大的连铸机,其结晶器原设计的Ni-Co 镀层以及窄面弧面倒角设计在实际生产中,使用寿命并没有达到原设计要求。
通过对各种结晶器铜板镀层的全面了解与尝试,针对1#连铸机结晶器铜板尺寸宽、宽厚比大的特点,最终采用电镀、热喷涂等方法对结晶器铜板表面进行改性处理,经过表面处理再制造不仅是对结晶器铜板尺寸上的修复,更是具有高强度、高韧性、优越耐腐蚀性能、抗磨损性能和抗热疲劳性能的表面功能涂层,大大提高结晶器铜板表面性能,使得结晶器的寿命大大延长,提高了生产的效率和连铸坯质量。
1 连铸结晶器表面处理技术及涂层的应用现状结晶器表面处理技术从最初的镀Cr开始,目前已经逐步形成了镀Ni、镀Ni-Fe、镀Ni-Co、镀Co-Ni、热喷涂合金等几种主要涂层,产品的性能也逐步提高。
电镀Co-Ni和热喷涂结晶器的一次修复过钢量的数值较高,资料显示最高分别达到了15万吨和20万吨,具有优异的性能。
电镀Co-Ni和热喷涂合金技术是当前最具代表性的结晶器表面处理新技术。
随着钢厂对生产效率和铸坯质量的日渐提高,对结晶器材料表面的性能提出了越来越高的要求,对结晶器铜板的需求向着高机械强度、良好的导热性、耐磨性和耐腐蚀性能的方向发展。
冷气动力喷涂技术修复连铸结晶器应用研究进展
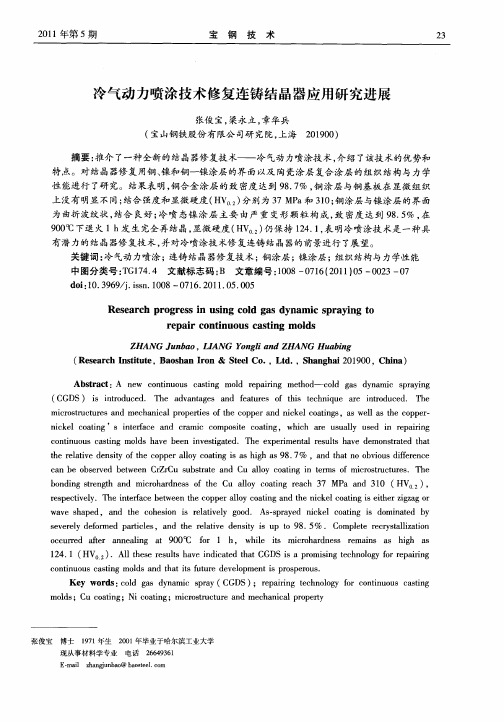
关 键 词 : 气动力喷 涂 ; 铸 结 晶器修 复技 术 ;铜涂 层 ; 涂层 ; 织结构 与 力学性 能 冷 连 镍 组 中图分 类号 : G 7 . 文献标 志 码 : 文章 编号 :0 8— 7 6 2 1 )5— 0 3— 7 T 14 4 B 10 0 1 ( 0 1 0 0 2 0
Absr c t a t:A ne w c n i u u c si g o tn o s a tn mod e iig l rparn meh d c l g s y a c p a ig t o - o d a d n mi s r yn
( G S) i n o ue . T e a vnae ad fa rs f ti tcnq e r nrd cd T e CD s t d cd h d atgs n et e o hs eh iu ae t u e . h i r u i o
不锈钢板坯连铸结晶器窄面铜板涂层新技术

足宽 面铜 板 的 5 % ,其 使 用 状 况 直 接 关 系 到 连 0 铸 机 的性 能 ,并 与铸 坯 的质 量 与 产 量 密 切 相关 。
因此 ,结 晶器铜 板涂 层合 理 的设计 是保 证铸 坯 质
量、减小溢漏率、提高其使用寿命 的基础。
有 所要 求 的断 面形 状 和一定 坯壳 厚度 的铸 坯 ,并
K e w o ds: sa nes te o i u usc si y r ti l sse lc ntn o a tng;nar w a e c p rp ae;l s rc ai g ro fc o pe lt a e o tn
O 前 言
结 晶器 是 连铸 机 的核心设 备 之一 。其 作用 是 将 连续 不 断地 注入 其 内腔 的钢液通 过 水冷铜 壁 强 制冷却 ,导 出钢液 的热 量 ,使之 逐渐 凝 固成 为具
Co tn n na r w a e c p r pl t o t i l s t e l b a i g o r o f c o pe a e f r sa n e s s e lsa
c n i uo s c s i o d o tn u a tng m l
使 这种 芯部 仍 为液相 的铸 坯 连续 不断 地从 结 晶器 下 口拉 出 ,为其 在 以后 的二 冷 区域 内完全 凝 固创 造 条件 。在 钢水 注入 结 晶器 逐渐形 成 一定厚 度 坯 壳 的凝 固 过 程 中 ,结 晶 器 一 直 承 受 着 钢 水 静 压
1 结 晶 器 铜板 涂 层 技 术 对 比分 析
2 1 . 02NO4
重 型 机 械
・7 ・
・
新技 术 新 设 备 ・
不锈 钢 板 坯 连铸 结 晶器 窄 面 铜 板 涂 层 新 技术
板坯连铸机结晶器研究课件

摘要结晶器是钢坯连续铸造的关键设备,其设计和制造的优劣直接影响到连铸生产的正常与稳定。
本文就目前连铸结晶器采用的铜板材料及铜板材料表面处理技术的发展现状进行了总结和分析。
指出针对板坯结晶器窄面铜板易高温变形、磨损的情况,采用高强度、高导热率的弥散强化铜材料,进而延长结晶器的维修周期,提高生产效率。
同时针对现有结晶器铜板表面改性技术的优缺点,发展新型合金涂、镀层技术,进一步提高涂、镀层的硬度,耐磨和耐腐蚀性能。
目前结晶器铜板表面处理的几种方法:电镀法、热喷涂法、化学热处理法以及具有潜在发展前景的激光熔覆法。
激光熔覆法由于具有清洁无污染,成品率高以及性价比高等特点,具有广阔的发展和应用空间。
而且,通过优化熔覆工艺参数,设计合理的熔覆材料体系,能够形成与铜板呈冶金结合的优良抗热耐磨复合涂层,从而显著提高结晶器的使用寿命。
关键词:结晶器;化学热处理;激光熔覆;铜板AbstractThe progress of mould plates was reviewed in continuous casting. The techniques such a solution or aging or forming or fine crystal and their combination were an effect tiveme thod which benefit for high conductivity and high strengthen of copper base alloy. Copper base composite maerial through dispersion technique and composite hardening and surface strengthening have more promising for mouldes in the future.Based on the current study stat of surface strength ening on copper crystallizer, several surface treatment means,such as electro plating thermal spraying,penetration and laserclad dingte chnique with potential development are described. Because of cleanliness without any pollution, high finished product ratio and high performance costratio, laser cladding has wide development and application range. Moreover, by optimizing process parameters and designing suitable material system, fine hea-t resistant and wear-resistant coating having metallurgy bonding with copper substrate can be fabricated, therefore, it may notably improve the service life of copper crystallizer.Key words:Copper crystallizer; Electroplating; Thermal Chemical heat treatme;Copper plate目录摘要 (I)Abstract (II)第1章绪论 (1)1.1连扎连铸简介 (1)1.2工艺流程 (3)1.3板坯连铸机质量优势 (4)1.4研究背景 (5)1.5国内外状况 (6)1.6结晶器概述 (7)1.7结晶器存在的问题 (9)1.8结晶器使用前的安全检查 (9)1.9本章小结 (10)第2章结晶器夹紧装置的选择计算 (11)2.1结晶器夹紧装置简介 (11)2.2结晶器夹紧受力分析及计算选择 (12)2.3结晶器宽边调整机构的安装 (14)2.4本章小结 (14)第3章结晶器调宽装置的选择计算 (15)3.1调宽装置简介 (15)3.2调宽装置的确定和基本参数的选择 (16)3.3调宽装置驱动选择 (18)3.4窄边调整机构的安装 (18)3.5本章小结 (19)第4章结晶器铜板及水箱的选择计算 (20)4.1结晶器铜板的设计 (20)4.1.1结晶器长度的选择 (20)4.1.2结晶器断面尺寸和倒锥度 (22)4.1.3结晶器铜板材质及表面镀层的选择 (23)4.1.4铜板厚度计算 (24)4.2水箱设计 (25)4.3本章小结 (26)第五章结晶器振动装置的应用和发展 (27)5.1振动装置的概述 (27)5.2结晶器的振动方式 (27)5.3总结 (30)5.4本章小结 (31)结论 (32)参考文献 (33)致谢 (35)第1章绪论1.1连扎连铸简介连铸连轧全称连续铸造连续轧制(Continue Casting Direct Rolling,简称CCDR),是把液态钢倒入连铸机中轧制出钢坯(称为连铸坯),然后不经冷却,在均热炉中保温一定时间后直接进入热连轧机组中轧制成型的钢铁轧制工艺。
连铸结晶器表面电镀Ni-W-P-B4C复合镀层的性能研究
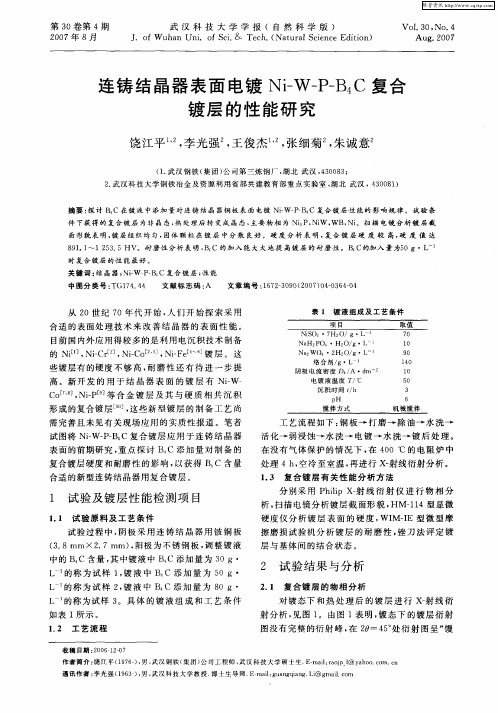
关键 词 : 晶 器 ; i — — 复合 镀 层 ; 能 结 N— PB C W 性 中 图分 类 号 : G1 4 4 T 7.4 文献标志码 : A 文 章 编 号 :6 23 9 ( 0 7 0 - 3 40 1 7 — 0 0 2 0 ) 40 6 — 4
络 合剂 / L g・ 阴 极 电 流 密度 Dk A ・ m / d
电 镀 液 温度 丁/ ℃ 沉 积 时 间 th /
p H
1 0 4
1 O
5 O
c 引, — C 等 合 金 镀 层 及 其 与 硬 质 相共 沉 积 o Ni 9 p
形 成 的复合镀层 l 这些 新 型镀层 的制 备工 艺 尚 _ 1 ,
活化一 弱 浸蚀一水 洗一 电镀一 水 洗 一 镀 后 处理 。 在没 有气 体保护 的情 况 下 , 4 0。 电阻 炉 中 在 0 C的 处理 4h 空冷 至室温 , , 再进行 X 射线 衍射 分析 。 一 1 3 复合镀 层有 关性 能分析 方法 .
复 合镀层硬 度 和耐磨性 的影 响 , 以获 得 B C含 量 l
从2 O世 纪 7 O年代 开 始 , 们 开 始探 索采 用 人 合 适 的表面处 理 技术 来 改 善结 晶 器 的表 面 性 能 。
目前 国内外应 用得较 多 的是 利用 电沉积 技术制 备
的 Ni Ni r Ni o ’ , i e ~ C , — C C , — C N — C 镀 层 。 这 C F
表 1 镀 液 组 成 及 工 艺 条 件
项目
NiO4・7 0/g ・L S H2 Na 2 H PO4・H2 g・L O/ Na W O4・2H2 g・L一 z 0/
表面电镀技术上连铸结晶器的应用进展
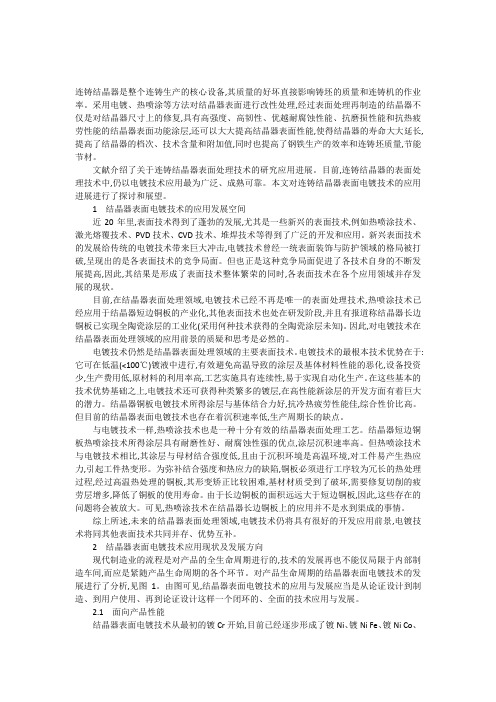
连铸结晶器是整个连铸生产的核心设备,其质量的好坏直接影响铸坯的质量和连铸机的作业率。
采用电镀、热喷涂等方法对结晶器表面进行改性处理,经过表面处理再制造的结晶器不仅是对结晶器尺寸上的修复,具有高强度、高韧性、优越耐腐蚀性能、抗磨损性能和抗热疲劳性能的结晶器表面功能涂层,还可以大大提高结晶器表面性能,使得结晶器的寿命大大延长,提高了结晶器的档次、技术含量和附加值,同时也提高了钢铁生产的效率和连铸坯质量,节能节材。
文献介绍了关于连铸结晶器表面处理技术的研究应用进展。
目前,连铸结晶器的表面处理技术中,仍以电镀技术应用最为广泛、成熟可靠。
本文对连铸结晶器表面电镀技术的应用进展进行了探讨和展望。
1结晶器表面电镀技术的应用发展空间近20年里,表面技术得到了蓬勃的发展,尤其是一些新兴的表面技术,例如热喷涂技术、激光熔覆技术、PVD技术、CVD技术、堆焊技术等得到了广泛的开发和应用。
新兴表面技术的发展给传统的电镀技术带来巨大冲击,电镀技术曾经一统表面装饰与防护领域的格局被打破,呈现出的是各表面技术的竞争局面。
但也正是这种竞争局面促进了各技术自身的不断发展提高,因此,其结果是形成了表面技术整体繁荣的同时,各表面技术在各个应用领域并存发展的现状。
目前,在结晶器表面处理领域,电镀技术已经不再是唯一的表面处理技术,热喷涂技术已经应用于结晶器短边铜板的产业化,其他表面技术也处在研发阶段,并且有报道称结晶器长边铜板已实现全陶瓷涂层的工业化(采用何种技术获得的全陶瓷涂层未知)。
因此,对电镀技术在结晶器表面处理领域的应用前景的质疑和思考是必然的。
电镀技术仍然是结晶器表面处理领域的主要表面技术。
电镀技术的最根本技术优势在于:它可在低温(<100℃)镀液中进行,有效避免高温导致的涂层及基体材料性能的恶化,设备投资少,生产费用低,原材料的利用率高,工艺实施具有连续性,易于实现自动化生产。
在这些基本的技术优势基础之上,电镀技术还可获得种类繁多的镀层,在高性能新涂层的开发方面有着巨大的潜力。
连铸机结晶器铜板镀层性能对比研究及镀层常见缺欠

连铸机结晶器铜板镀层性能对比研究及镀层常见缺欠连铸机结晶器铜板镀层常见缺陷一般为磨损、腐蚀、划伤、龟裂、脱落等。
对镀铬层来说前3种是正常的,对合金镀层来说前4种是正常的连铸机结晶器铜板镀层常见缺陷一般为磨损、腐蚀、划伤、龟裂、脱落等。
对镀铬层来说前3种是正常的,对合金镀层来说前4种是正常的,脱落是镀层的质量问题。
镀铬层脱落的一般原因是:(1)镀层在镀覆过程中,如果镀前处理不当,容易产生镀层结合不好,结合强度不够,遇到外力作用起层而脱落。
(2)正常的镀层,由于镀层材质与母材(铜或铜合金)比较,由于热膨胀系数差异较大,铜板受热后产生膨胀,镀层与母材之间产生内应力,当应力大于结合力时就出现起层脱落。
(3)由于生产中冷却的连续性、稳定性不好,出现较大的间歇性变化,这也是主要原因之一。
(4)由于铸坯表面出现结瘤造成磨损严重,出现耕犁划伤磨损而使镀层脱落。
结晶器是连铸的核心部件,结晶器铜板作为连铸从液态钢水到凝固成固态坯壳的重要导热部件,其质量好坏直接影响到铸坯的表面质量、连铸机拉速等指标。
熔融的钢水流经结晶器铜板,在外界冷却水的作用下结晶成坯,并被引锭杆从结晶器中拉出。
经常拉坯使结晶器铜板磨损严重,更换频繁,不仅降低生产效率,而且消耗大量的结晶器。
为提高结晶器铜板的使用寿命,国内外相关单位及专家对铜板材料及镀层展开了长期的、深入地研究,取得了很大的成果。
目前,国内外开始应用热解析技术进行结晶器设计最佳化及镀层选择的研究,热解析技术在结晶器铜板上的应用大大提高了提高结晶器铜板的寿命。
连铸机结晶器铜板采用镀层主要目的是:(1)提高铸机备件使用寿命,降低备件特别是有色金属消耗。
(2)提高铜板表面硬度、耐磨性、连铸机结晶器铜板采用镀层主要目的是:(1)提高铸机备件使用寿命,降低备件特别是有色金属消耗。
(2)提高铜板表面硬度、耐磨性、减少摩擦力,提高表面光滑程度,可以减少粘结,防止对某些合金钢钢坯因渗铜而产生星状裂纹,从而提高铸坯质量和成材率。
连铸结晶器铜板电镀层的研究进展

引 言
作 为整 个钢 材 连续 浇 铸 生 产 的 核心 装 置 , 晶 结 器质 量 的好 坏直 接影 响到铸 坯 的质量 和连 铸机 的作 业 率 。 由于钢水 直 接 通过 结 晶器 表 面冷 却 为 铸 坯 ,
量 , 反 映结 晶器 寿命 水平 的重 要指标 , 是 同时也是 连 铸生 产控 制水平 的综 合反 映 。 目前结 晶器铜 板 多采 用含有 微量 铬 和锆 的铜 板 , 早 有 些 钢厂 直 接 使用 最 裸铜板 组装 结 晶器 , 果不 仅导致 结 晶器通 钢量低 、 结 铜板修 复次 数低 、 连铸 成本 高 , 而且伴 随着钢 水 的直
o n i u u si o d f Co tn o s Ca t ng M l
L Ch n—e ,CAO e — i , YI Re — e V u l i W im n N n h ,YU — h n Zu z a , HOU e g y n F n —a
( . D pr e to hmir ,S a g a U i ri ,S a g a 2 0 4 1 e at n fC e sy h nh i nv sy h n hi 0 4 4,C ia . D pr n f m t e t hn ;2 e a meto t
Ch mity, F da i e st பைடு நூலகம் sr u n Un v r i y,S a g i 2 0 3,Ch n h n ha 0 43 i a;3. Ba se lM a hi ey Pln ,S a g a o t o te c n r a t h n h iBa s—
el q im n Man n neC ,Ld h n h i 2 10 C ia e E up e t it a c o t.S ag a e 0 9 0, hn )
连铸结晶器铜板电镀层技术
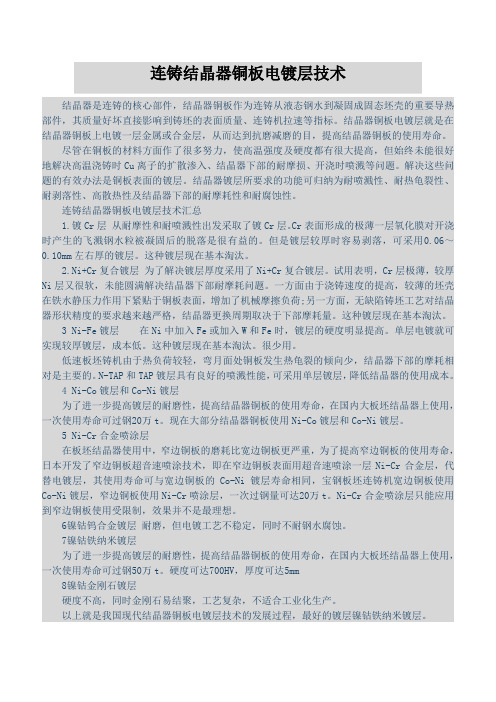
连铸结晶器铜板电镀层技术结晶器是连铸的核心部件,结晶器铜板作为连铸从液态钢水到凝固成固态坯壳的重要导热部件,其质量好坏直接影响到铸坯的表面质量、连铸机拉速等指标。
结晶器铜板电镀层就是在结晶器铜板上电镀一层金属或合金层,从而达到抗磨减磨的目,提高结晶器铜板的使用寿命。
尽管在铜板的材料方面作了很多努力,使高温强度及硬度都有很大提高,但始终未能很好地解决高温浇铸时Cu离子的扩散渗入、结晶器下部的耐摩损、开浇时喷溅等问题。
解决这些问题的有效办法是铜板表面的镀层。
结晶器镀层所要求的功能可归纳为耐喷溅性、耐热龟裂性、耐剥落性、高散热性及结晶器下部的耐摩耗性和耐腐蚀性。
连铸结晶器铜板电镀层技术汇总1.镀Cr层从耐摩性和耐喷溅性出发采取了镀Cr层。
Cr表面形成的极薄一层氧化膜对开浇时产生的飞溅钢水粒被凝固后的脱落是很有益的。
但是镀层较厚时容易剥落,可采用0.06~0.10mm左右厚的镀层。
这种镀层现在基本淘汰。
2.Ni+Cr复合镀层为了解决镀层厚度采用了Ni+Cr复合镀层。
试用表明,Cr层极薄,较厚Ni层又很软,未能圆满解决结晶器下部耐摩耗问题。
一方面由于浇铸速度的提高,较薄的坯壳在铁水静压力作用下紧贴于铜板表面,增加了机械摩擦负荷;另一方面,无缺陷铸坯工艺对结晶器形状精度的要求越来越严格,结晶器更换周期取决于下部摩耗量。
这种镀层现在基本淘汰。
3 Ni-Fe镀层在Ni中加入Fe或加入W和Fe时,镀层的硬度明显提高。
单层电镀就可实现较厚镀层,成本低。
这种镀层现在基本淘汰。
很少用。
低速板坯铸机由于热负荷较轻,弯月面处铜板发生热龟裂的倾向少,结晶器下部的摩耗相对是主要的。
N-TAP和TAP镀层具有良好的喷溅性能,可采用单层镀层,降低结晶器的使用成本。
4 Ni-Co镀层和Co-Ni镀层为了进一步提高镀层的耐磨性,提高结晶器铜板的使用寿命,在国内大板坯结晶器上使用,一次使用寿命可过钢20万t。
现在大部分结晶器铜板使用Ni-Co镀层和Co-Ni镀层。
- 1、下载文档前请自行甄别文档内容的完整性,平台不提供额外的编辑、内容补充、找答案等附加服务。
- 2、"仅部分预览"的文档,不可在线预览部分如存在完整性等问题,可反馈申请退款(可完整预览的文档不适用该条件!)。
- 3、如文档侵犯您的权益,请联系客服反馈,我们会尽快为您处理(人工客服工作时间:9:00-18:30)。
连铸结晶器铜板涂层的发展与研究结晶器是连铸机的核心,是将钢水注入其中,经过急冷却,使钢水外层形成连续的硬壳,随后将其拉入支撑导向段扇形段冷却凝固,并拉出铸坯的装置。
结晶器的技术性能将直接影响连铸坯的表面质量、连铸机的生产效率及连铸生产成本等指标。
结晶器一直承受着钢水静压力、摩擦力、钢水热量的传递,长期处于机械应力和热应力的综合作用下,工作条件极其恶劣。
结晶器的好坏对连铸设备使用寿命极其自身精度和使用的可靠性,都有直接重大影响。
高效连铸技术的发展对结晶器质量提出了更高的要求,高强度、高耐磨性、高耐腐蚀性和良好的导热性成为衡量结晶器质量优劣的重要指标。
连铸生产过程中,结晶器铜板工作表面与1530℃-1570℃的钢水接触,背面通过30℃-40℃的冷却水,存在巨大的温度梯度和热应力。
结晶器铜板在使用过程中主要存在高温腐蚀、边缘磨损、热裂纹、窄面收缩等问题,所以要求结晶器具有传热好、耐磨损、耐高温、耐腐蚀等性能。
因此选用合适的结晶器表面处理是连铸是生产必须具备的条件。
一、连铸结晶器铜板涂层技术的发展随着连铸技术的不断发展,结晶器铜板母材也随之发展换代,由最初的紫铜铜板逐渐发展到AgCu、CrZrCu、BeNiCu、BeCoCu、等合金板。
早期的结晶器铜板采用裸铜板,其导热性能极其优异,除其高温强度、耐磨性、耐蚀性等性能无法满足连铸生产的要求外,当连铸拉速提高到一定程度时,钢坯会出现大量的星状裂纹,造成结晶器铜板更换频繁,寿命不高。
因此改善结晶器铜板表面性能对提高其寿命,降低生产成本具有主要的意义。
在连铸结晶器表面改性中一般采用电镀、化学镀、电铸、复合镀、激光熔覆、热喷涂和高温自蔓延等方法处理后,可以较大程度的改善其表面性能,达到提高连铸坯质量、延长结晶器寿命和降低生产成本的目的。
在这些表面改性方法中,应用比较广泛的是电镀和热喷涂。
1.电镀1.1镀Cr层镀层研究初期,从耐摩性和耐喷溅性出发采取了镀Cr层。
Cr表面形成的极薄一层氧化膜对开浇时产生的飞溅钢水粒被凝固后的脱落是很有益的。
镀铬层表面硬度较高,化学稳定性好。
缺点为:安全厚度受限制,镀层无论厚薄都有裂纹存在;随温度升高硬度迅速降低,与铜结合时,其线膨胀系数、导热率相差太大,镀层容易在高温状态起皮剥落,同时电镀过程中六价Cr离子对环境污染严重,因而使用受到了一定的限制。
1.2镀Ni层由于在0-1000℃时Ni的线性膨胀系数为1.8×10-5K-1,与铜的线性膨胀系数相差较小,电镀Ni工艺很快取代了电镀Cr工艺。
镀Ni层化学稳定性好,封闭能力很强,且能镀厚至3-8mm,经过电镀处理,镀层与基体的结合力得到了有效改善,但其硬度(200Hv)经不起连铸坯的磨损,因此寿命不高。
1.3镀Ni-Cr层为了解决镀层厚度采用了Ni+Cr复合镀层。
由于Ni的热膨胀系数接近于Cu,剥离问题大大改善,厚度增加。
Ni解决了附着力和厚度问题,Cr解决了喷溅性和表面硬度问题。
为了解决Ni热传导率较差问题,引入了斜面层工艺,弯月面处的Ni层厚度可控制在0.2mm左右,出口处Ni层厚度控制在3mm左右。
试用表明,Cr层极薄,较厚Ni层又很软,未能圆满解决结晶器下部耐摩损问题。
一方面由于浇铸速度的提高,较薄的坯壳在铁水静压力作用下紧贴于铜板表面,增加了机械摩擦负荷;另一方面,无缺陷铸坯工艺对结晶器形状精度的要求越来越严格,结晶器更换周期取决于下部摩耗量。
1.4镀Ni-Fe层:由于Fe元素的加入导致其硬度(500Hv)高于镀Ni层,耐磨性为镀Ni层的2倍,使用寿命比镀Ni层显著提高。
Ni-Fe镀层的缺点是:其镀液不易控制,化学稳定性较差,特别是在高温条件下受热腐蚀急剧扩大导致裂纹的产生,而且脆性增大及高的内应力,且与基体的结合强度明显降低,因此Ni-Fe镀层的抗热交变性能很差。
1.5镀Ni-Co层:为了进一步提高镀层的耐磨性,提高结晶器铜板的使用寿命,国外又发展了Ni-Co镀层(含Co的镍基合金),其性能较Ni-Fe镀层又有了进一步的提高。
由于镍、钴元素原子半径和原子结构相近、电化学性质相近,使得镀层结构更稳定;Ni-Co合金镀层受热后表层陶瓷化,形成玻璃质的氧化钴薄膜,起到良好的自润滑作用,可避免粘结现象;软化温度高,在较高温度下能形成稳定的高硬度耐磨表面;摩擦系数较低,铜板镀层不易产生热裂纹。
但其硬度随温度的升高有所下降,当温度上升至600℃时,其镀层硬度下降为180Hv,由于硬度与耐磨性有关,因此Ni-Co镀层仅适用于中低拉速的连铸结晶器,其平均过钢量为8-10万吨。
1.6镀Co-Ni层:与w(Ni)80%的Ni-Co合金镀层相比,w(Co)80%的Co-Ni合金镀层性能更为优越。
侯岩峰等的研究表明,w(Co)80%的Co-Ni合金镀层具有六方密排结构,属于Ni溶解在Co中的单相固溶体,与纯Ni层相比,w(Co)80%的Co-Ni 合金镀层晶粒更加细化,硬度适中,韧性相对较好;适用于钢厂较高拉速的生产,过钢量高。
能很好满足钢厂中、高拉速的要求,即电镀层在高温区不容易出现热裂、浸蚀掉块问题。
其平均过钢量为15-20万吨。
但由于Co-Ni涂层是含Ni的Co基合金,Co的成本较高,导致该涂层的生产成本较高。
1.7镀Ni-P层:Ni-P涂层与以上几种涂层有所不同,其是在Ni涂层电镀过程中加入非合金元素P形成非晶态NI-P合金涂层,由于有Ni3P相弥散析出而Ni2P合金镀层的摩擦系数小,使得Ni2P合金经400 ℃时效后,其耐磨性优于铜锡合金、电镀镍、硬铬等耐磨材料。
由于其膨胀系数与铜基材较接近,使得涂层不易过早脱落,而且在使用温度下Ni2P合金镀层具有良好的耐磨性、热疲劳性、高硬度性,在镀态时的硬度约为800HV左右,经过电镀后的热处理后硬度可以达到接近1000HV(最高可到达1300HV);较高的硬度耐磨损性能比较好,可以满足钢厂提高一次过钢量的目的,其缺点是在高拉速连铸生产中容易出现镀层表面横裂的现象,因此其适用于中低拉速的连铸结晶器,其平均过钢量为10-20万吨。
1.8镀Ni-W层:Ni-W合金镀液具有良好的深镀、均镀能力,其化学性能好、稳定性高,具有较强的高电流密度承受能力,而且镀层应力小,结合强度高,硬度可达535 HV ,表面平整光亮。
2.热喷涂热喷涂是指将喷涂材料加热到熔融或半熔融状态,用高速气流将其雾化、加速,使其以高速喷射在铜板表面,形成喷涂层的一种金属表面加工方法。
热喷涂特点如下:1)焰流温度高,热量集中,能够熔化高熔点和高硬度的粉末材料;2)喷涂后涂层平整、光滑,并可精确控制涂层厚度;3)对铜板表面的热影响区很小;4)工艺规范稳定,容易操作。
但还存在以下缺点:热喷涂涂层是以机械结合为主。
由于等离子喷涂工艺所制备的涂层表面粗糙度大,耐应变性差,从而影响高温工作时的热冲击性;而且,涂层中孔隙的存在可导致低温条件下涂层的失效,产生开裂及影响高温工作时的热障性和抗热腐蚀性。
国内外应用比较广泛的涂层有Ni-Cr层、陶瓷涂层(Ni-WC、Ni-CrC)等。
2.1热喷涂Ni-Cr层经研究表面结晶器铜板表面热喷涂涂层组织非常致密,并且涂层与铜板母材结合良好,剪切结合强度大于240N/mm2;热喷涂涂层中的硬质陶瓷颗粒相既能限制晶粒长大,又兼具高温红硬性能,而镍电镀层组织由于发生再结晶,会造成电镀层软化。
故热喷涂涂层具有更为优异的综合性能:显微硬度约为镍电镀层的4倍,300℃时的高温耐磨性能则约为镍电镀层的5倍。
(毕刚,连铸结晶器铜板表面涂层热喷涂技术研究,表面技术,2009,38(4),75-77)2.2陶瓷涂层陶瓷涂层的硬度为700 ~1 200 HV,具有优异的高温性能,使用中陶瓷层不开裂、不剥落,磨损均匀,耐磨性好,使用寿命达到普通镀Ni层的20~30倍。
二、连铸结晶器铜板新涂层的研究与进展2.1Ni-Co-P涂层Ni2P合金主要用来提高镀层的耐磨性,其中的P与Ni为饱和置换固溶体。
朱诚意等人研究了Ni-W-P合金镀层,其镀层硬度达到570~590HV,并且由于少量W和P的加入,使得镀层形成了比较致密的固溶体,保证了与基体的结合力,有效地避免了镀层使用过程中产生起泡、脱皮等现象。
袁庆龙等报道了Ni3-P相弥散析出可以降低镀层的摩擦系数,而且W的存在使合金的熔化温度和热稳定性都有相应的提高。
由于其镀液稳定性高,电镀工艺简单,因此Ni-W-P合金镀层将成为具有开发前景的镀层。
2.2 Ni-Co-W涂层W 不能在水溶液中单独电沉积,但在铁系元素存在下能实现诱导共沉积,这就为制备含W三元合金奠定了基础。
Matsuyama T等在硫酸盐体系中加入柠檬酸和钨酸钠制备了Ni-Co-W三元合金镀层。
其耐磨性能也比Co-Ni镀层强,相同条件下磨损量为Co-Ni合金镀层的2 /3,此镀层具有很好的应用前景,然而这种镀层目前尚处于研究阶段,未见有工业化应用的报道。
2.3复合涂层和传统的制备复合镀层的等离子喷涂、内部氧化、表面注入及热挤压法相比,复合电镀具有操作简单,固体颗粒含量容易控制,可以避免高温高压操作等优点。
由于在金属和合金中掺入第二相固体颗粒,可在很大程度上改善材料表面硬度、强度、耐磨性、高温耐热性及耐蚀性等力学、化学性能。
这种性能优异的镀层符合连铸结晶器使用的苛刻条件,因此可以认为其在连铸结晶器表面应用上拥有较大的前景。
常作为第二强化相的惰性颗粒有: Al2O3、ZrO2、SiC、B4 C及WC等。
目前复合镀层的研究比较多,但立足于结晶器铜板镀层开发的则相对较少,其主要障碍在于镀液成分和生产过程的严格控制。
三、连铸结晶器铜板表面涂层的前景与展望为适应高效连铸发展的需要,研制的新型结晶器铜板表面涂层必须具有高硬度、高耐磨性,以抵抗高拉速下坯壳的磨损,同时,基体也必须有较高的强度和较高的抗软化温度,以减少铜板基体在高温下的变形,保证拉坯截面的几何精度。
强度、硬度、耐磨性、导热性、热力学性能是衡量结晶器镀层质量好坏的主要指标,因此应该从各方面入手,通过具有高强度、高耐磨性、高硬度、高导热性能的几种金属进行复合电镀,探索出满足连铸结晶器优良性能要求的复合镀层。
作为钢铁大国,连铸技术在国内得到普遍应用,然而以宝钢、西峡龙成为例,结晶器铜板镀层仍多采用Ni、Co-Ni、 Ni-Co 、Ni-P合金镀层,而极具应用前景的Ni-W-P等三元合金镀层和多种性能优越的复合镀层还仅停留在研究阶段,没有得到实际应用。
因此对结晶器镀层研究应该从内应力、结合力、抗磨损性能、抗腐蚀性能、抗冲压性能、高导热性能及高寿命等方面入手,同时应该考虑选取优质铜板母材,综合国内外的先进技术,紧密结合连铸生产实际,着手于新型复合镀层的研究,提高结晶器综合性能,尽快实用化,满足高速连铸结晶器发展的需要。