PVD薄膜沉积工艺及设备
半导体pvd设备原理

半导体pvd设备原理
半导体物理气相沉积(PVD)设备是一种常用于制备薄膜材料的技术。
这种设备基于物理原理,通过在真空环境下加热材料,使其升华并沉积在基底上,形成所需的薄膜。
PVD设备的工作原理如下:
将待沉积的材料放置在真空室中。
真空室的设计是为了排除外部空气,以确保材料在无氧环境下处理。
然后,通过加热材料,使其升华成为气态。
升华的材料蒸汽会扩散到真空室中,并沉积在基底表面上。
基底通常是需要涂覆薄膜的物体,例如电子器件或太阳能电池。
沉积过程可以通过不同的方法实现。
其中一种常用的方法是磁控溅射,它利用磁场将金属靶材的离子击打到基底上。
这种方法可以控制沉积速率和薄膜的成分。
另一种常用的方法是电子束蒸发,它使用电子束加热材料,使其升华并沉积在基底上。
电子束蒸发具有较高的沉积速率和较好的薄膜均匀性。
PVD设备的优点在于可以制备高质量的薄膜,并具有较好的控制能力。
通过调节沉积条件,可以控制薄膜的成分、厚度和结构。
这使得PVD设备在半导体制造、光电子学和纳米器件制备等领域得到广泛应用。
然而,PVD设备也存在一些局限性。
首先,沉积速率相对较低,需要较长的时间来制备较厚的薄膜。
此外,PVD设备对材料的选择性较差,只能用于制备一些高熔点的材料。
总的来说,半导体PVD设备是一种重要的制备薄膜材料的工具。
通过控制沉积条件,可以制备具有特定性质和结构的薄膜,满足不同应用的需求。
随着技术的不断进步,PVD设备将继续在材料科学和工程中发挥重要作用。
pvd涂层工艺

pvd涂层工艺PVD涂层工艺是一种常见的表面处理技术,用于在各种材料上形成薄膜涂层。
PVD是物理气相沉积(Physical Vapor Deposition)的缩写,主要包括蒸发、溅射和离子镀等技术。
PVD涂层工艺的基本原理是利用物理方法将固态材料转化为气态,然后通过沉积在工件表面形成一层薄膜。
首先,将待处理的材料作为靶材放置在真空腔室中,然后通过加热或者离子轰击等方式将靶材转化为气态,形成蒸汽。
接着,将工件放置在腔室的靶材正对位置,通过离子轰击或者磁控溅射等方式将蒸汽沉积在工件表面,形成均匀而致密的薄膜涂层。
PVD涂层工艺具有许多优点。
首先,由于是在真空环境下进行,因此可以避免氧化和污染等问题,从而提高了涂层的质量和附着力。
其次,PVD涂层可以在各种材料上进行,如金属、陶瓷、玻璃等,具有广泛的应用范围。
此外,PVD涂层具有较高的硬度、耐磨性和耐腐蚀性,可以提高材料的使用寿命和性能。
根据不同的需求,PVD涂层可以选择不同的工艺。
其中,蒸发是最常见的一种工艺,通过加热靶材使其蒸发,然后在工件表面形成涂层。
溅射是另一种常用的工艺,通过离子轰击靶材使其溅射,然后沉积在工件表面。
此外,还有离子镀、磁控溅射等工艺,可以根据具体需要选择合适的工艺。
在实际应用中,PVD涂层工艺具有广泛的应用领域。
例如,在汽车行业中,PVD涂层可以用于改善汽车零部件的耐磨性和耐腐蚀性,提高汽车的整体质量和使用寿命。
在电子行业中,PVD涂层可以用于生产显示屏、太阳能电池等产品,提高其光学性能和耐候性。
此外,PVD涂层还可以应用于航空航天、医疗器械、机械制造等领域,为各种材料赋予特殊的功能和性能。
然而,PVD涂层工艺也存在一些挑战和限制。
首先,PVD涂层的设备和工艺较为复杂,需要高度的技术和设备支持。
其次,涂层的厚度和均匀性受到一定的限制,无法在大面积和复杂形状的工件上实现均匀的涂层。
此外,PVD涂层的成本相对较高,不适合大规模生产。
pvd镀膜设备原理

pvd镀膜设备原理PVD镀膜设备,全称是物理气相沉积(Physical Vapor Deposition)镀膜设备,是一种常用的薄膜制备技术。
它利用高能离子束或高温蒸发源将材料原子或分子蒸发,然后沉积在基底表面,形成均匀的薄膜。
PVD镀膜设备主要包括蒸发源、真空系统和基底台三个组成部分。
蒸发源是主要设备,通过加热材料使其蒸发,并产生高能离子束。
真空系统则能够提供高真空环境,以确保薄膜沉积的质量。
基底台则是放置待镀膜基底的位置。
PVD镀膜设备主要有以下几种工作原理:蒸发、溅射和离子镀。
蒸发是最常见的PVD镀膜技术之一。
蒸发源内的材料通过加热,使其蒸发并沉积在基底上。
蒸发源的加热方式有电阻加热、电子束加热和感应加热等。
蒸发源内的材料蒸发后形成蒸汽,蒸汽经过运输管道进入真空室,在高真空环境下,蒸汽与基底表面相遇,凝结成薄膜。
溅射是另一种常见的PVD镀膜技术。
在溅射过程中,材料源被离子束轰击,使其离子化并溅射出来,然后沉积在基底上。
溅射镀膜可以通过直流溅射、射频溅射、磁控溅射等方式进行。
溅射镀膜的薄膜均匀性更好,适用于复杂形状的基底。
离子镀是一种利用离子束轰击基底表面的技术。
在离子镀过程中,材料被加热并离子化,然后通过高能离子束轰击基底表面,使薄膜原子或分子沉积在基底上。
离子镀技术可用于提高薄膜的致密性和附着力。
PVD镀膜设备在各个领域有着广泛的应用。
在电子行业中,PVD技术可用于制备导电薄膜、光学薄膜和防腐蚀薄膜等。
在光学行业中,PVD技术可用于制备反射镜、透镜和滤光片等。
在装饰行业中,PVD 技术可用于制备金属涂层,增加产品的质感和美观度。
此外,PVD 技术还可用于制备硬质涂层、陶瓷涂层和生物医学涂层等。
总结起来,PVD镀膜设备是一种基于物理气相沉积原理的薄膜制备技术。
通过蒸发、溅射和离子镀等工作原理,能够在基底表面形成均匀致密的薄膜。
该技术在电子、光学、装饰等领域有着广泛应用,为产品的性能和外观提供了强大支持。
pvd原理及工艺流程

pvd原理及工艺流程
PVD(Physical Vapor Deposition)是一种物理蒸发沉积技术,通过将材料加热至蒸发温度,使其蒸发成气态,然后再将蒸发的材料沉积到基材表面形成薄膜。
PVD工艺流程一般包括以下步骤:
1. 清洁基材:将基材放入超声波清洗机中使用溶剂或碱性溶液进行清洗,去除杂质和污垢。
2. 加热基材:将经过清洗的基材放入真空室中,通过加热使其达到蒸发温度。
3. 蒸发源蒸发:打开蒸发源,使其蒸发材料释放出来。
4. 沉积:蒸发材料在真空室中形成气体,然后通过吸附作用沉积到基材表面。
5. 冷却:在沉积过程中,基材需要保持一定的温度以确保薄膜的质量,在沉积完成后,基材需要冷却至室温。
6. 分离:将沉积好的基材从真空室中取出,完成PVD工艺。
PVD工艺流程中的主要设备包括真空室、蒸发源(可以是电阻加热、电子束、离子束等)、
基材夹具、高真空泵等。
不同的材料和应用场景可能会有一些额外的步骤或设备,但整体流程大致相似。
PVD技术广泛应用于镀膜、表面改性和纳米材料制备等领域。
PVD镀膜工艺简介

PVD镀膜工艺简介PVD镀膜(Physical Vapor Deposition)是一种利用物理气相沉积的技术,在高真空环境下,通过蒸发、溅射等方式将金属、合金、化合物等材料以薄膜的形式沉积到基材表面的一种工艺。
PVD镀膜工艺被广泛应用于各个领域,如光学、电子、机械、汽车、建筑等。
蒸发是PVD镀膜中最早应用的一种工艺。
通过加热源将材料加热至蒸发温度,使其转变为气态,然后在真空室内的基板上形成薄膜。
蒸发工艺可以通过电阻加热、电子束加热等方式来进行。
这种工艺的特点是操作简单,成本较低,但适用于蒸发温度较低的材料。
溅射是PVD镀膜中应用较广泛的一种工艺。
通过高能粒子的轰击使靶材表面的原子或离子脱落,然后被沉积在基板表面上形成薄膜。
溅射工艺一般可分为直流溅射、射频溅射、磁控溅射等不同方式。
这种工艺具有较高的沉积速率和较好的膜层均匀性,适用于多种材料的沉积。
离子镀是一种利用离子轰击作用在基材表面上形成薄膜的工艺。
通过向沉积膜层的材料供应高能离子,使其在基板表面发生化学反应并沉积形成薄膜。
离子镀工艺能够提高薄膜的致密性和附着力,适用于复杂形状的基板和高精密要求的镀膜。
在PVD镀膜过程中,需要注意以下几个关键环节。
首先,要确保真空室内的气压稳定,并保持高真空状态,以避免杂质对薄膜质量的影响。
其次,镀膜前需对基材进行表面处理,如清洗、抛光等,以提高薄膜的附着力。
再次,镀膜材料的纯度和均匀性对薄膜性能起着重要影响,因此需要对材料进行精细的处理和选择。
最后,要通过适当的加热、冷却以及离子轰击等方式,使沉积的薄膜具有良好的致密性和均匀性。
PVD镀膜工艺具有许多优点。
首先,它可以在室温下进行,避免了高温对基材产生的热应力和变形。
其次,沉积的薄膜具有较高的质量和均匀性,具有良好的机械性能和化学稳定性。
再次,PVD镀膜可用于多种材料的沉积,如金属、合金、化合物等,具有较大的灵活性和可扩展性。
此外,PVD镀膜还具有低污染性、无溶剂使用、高效节能等环保优势。
pvd电镀工艺流程及详解
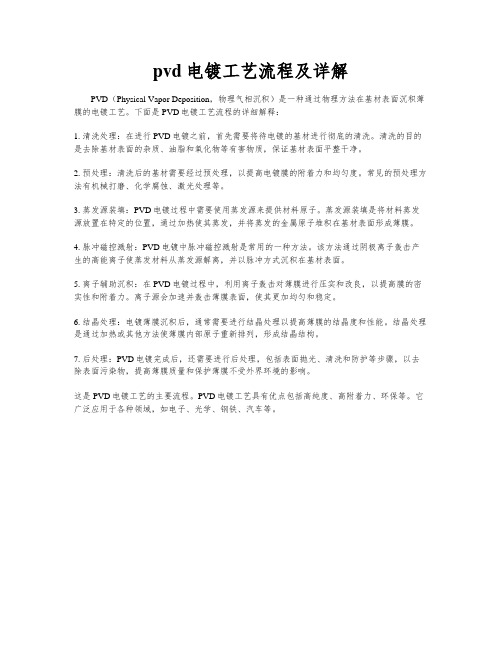
pvd电镀工艺流程及详解
PVD(Physical Vapor Deposition,物理气相沉积)是一种通过物理方法在基材表面沉积薄膜的电镀工艺。
下面是PVD电镀工艺流程的详细解释:
1. 清洗处理:在进行PVD电镀之前,首先需要将待电镀的基材进行彻底的清洗。
清洗的目的是去除基材表面的杂质、油脂和氧化物等有害物质,保证基材表面平整干净。
2. 预处理:清洗后的基材需要经过预处理,以提高电镀膜的附着力和均匀度。
常见的预处理方法有机械打磨、化学腐蚀、激光处理等。
3. 蒸发源装填:PVD电镀过程中需要使用蒸发源来提供材料原子。
蒸发源装填是将材料蒸发源放置在特定的位置,通过加热使其蒸发,并将蒸发的金属原子堆积在基材表面形成薄膜。
4. 脉冲磁控溅射:PVD电镀中脉冲磁控溅射是常用的一种方法。
该方法通过阴极离子轰击产生的高能离子使蒸发材料从蒸发源解离,并以脉冲方式沉积在基材表面。
5. 离子辅助沉积:在PVD电镀过程中,利用离子轰击对薄膜进行压实和改良,以提高膜的密实性和附着力。
离子源会加速并轰击薄膜表面,使其更加均匀和稳定。
6. 结晶处理:电镀薄膜沉积后,通常需要进行结晶处理以提高薄膜的结晶度和性能。
结晶处理是通过加热或其他方法使薄膜内部原子重新排列,形成结晶结构。
7. 后处理:PVD电镀完成后,还需要进行后处理,包括表面抛光、清洗和防护等步骤,以去除表面污染物,提高薄膜质量和保护薄膜不受外界环境的影响。
这是PVD电镀工艺的主要流程。
PVD电镀工艺具有优点包括高纯度、高附着力、环保等。
它广泛应用于各种领域,如电子、光学、钢铁、汽车等。
PVD镀膜工艺范文

PVD镀膜工艺范文PVD(Physical Vapor Deposition)是一种通过物理手段将具有良好特性的薄膜沉积在基底材料表面的工艺。
它是一种干法沉积工艺,主要适用于金属、陶瓷和有机材料的沉积。
1.蒸发法:蒸发法主要通过加热源将材料加热到高温,使其蒸发成气态后,通过凝结在基底材料表面。
蒸发法主要分为电子束蒸发和电弧蒸发两种。
电子束蒸发是将材料放置在真空腔中,利用加热的钨丝或电铲,通过加热材料使其蒸发成气态,然后通过真空腔中的电子束,将材料蒸发沉积在基底材料表面。
这种方法最大的优点是沉积速度快,但腔体设计复杂,设备价格较高。
电弧蒸发是将材料放置在电弧区域中,通过电弧的高温熔化材料,使其蒸发成气态,然后通过电弧区域的高能电子束,将材料蒸发沉积在基底材料表面。
这种方法的优点是设备价格较低,但沉积速度较慢,由于电弧区域会产生气体等污染物质,膜的制备也较为复杂。
2.溅射法:溅射法是利用高能离子轰击材料表面,将材料溅射成离子,然后沉积在基底材料表面。
溅射法主要分为磁控溅射、电弧溅射、激光溅射等。
磁控溅射是最常见的溅射方法之一,它通过在真空腔中施加磁场,电离气体形成的离子在磁场的作用下,从材料表面溅射。
这种方法优点是可以得到均匀的膜厚,且适用于多种材料的沉积。
电弧溅射是在电弧区域形成高温电弧,使材料表面离子化并溅射出去,然后通过磁场将离子引导到基底材料表面。
这种方法主要适用于贵金属和高熔点材料的沉积。
激光溅射是通过激光束在材料表面进行高能量的瞬间轰击,使材料离子化并溅射出去,然后通过磁场将离子引导到基底材料表面。
这种方法的优点是可以对不同材料进行选择性的溅射,适用于薄膜和纳米颗粒的制备。
1.防护涂层:PVD镀膜可以形成一层坚硬、耐磨的薄膜,可以增加材料的抗腐蚀性和耐磨性。
在汽车工业、机械工业和航空航天工业中得到广泛应用。
2.装饰涂层:PVD镀膜可以制备出具有不同颜色和光泽度的薄膜,可以用于制作首饰、钟表、厨具等装饰品。
PVD简介(物理气相沉积)
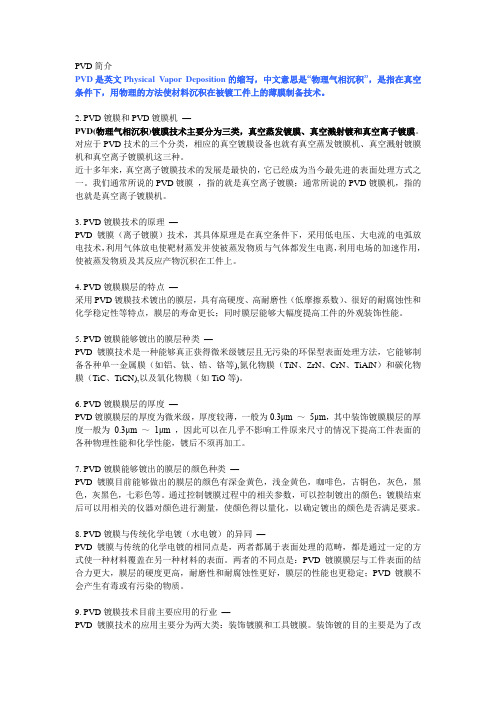
PVD简介PVD是英文Physical Vapor Deposition的缩写,中文意思是“物理气相沉积”,是指在真空条件下,用物理的方法使材料沉积在被镀工件上的薄膜制备技术。
2. PVD镀膜和PVD镀膜机—PVD(物理气相沉积)镀膜技术主要分为三类,真空蒸发镀膜、真空溅射镀和真空离子镀膜。
对应于PVD技术的三个分类,相应的真空镀膜设备也就有真空蒸发镀膜机、真空溅射镀膜机和真空离子镀膜机这三种。
近十多年来,真空离子镀膜技术的发展是最快的,它已经成为当今最先进的表面处理方式之一。
我们通常所说的PVD镀膜,指的就是真空离子镀膜;通常所说的PVD镀膜机,指的也就是真空离子镀膜机。
3. PVD镀膜技术的原理—PVD镀膜(离子镀膜)技术,其具体原理是在真空条件下,采用低电压、大电流的电弧放电技术,利用气体放电使靶材蒸发并使被蒸发物质与气体都发生电离,利用电场的加速作用,使被蒸发物质及其反应产物沉积在工件上。
4. PVD镀膜膜层的特点—采用PVD镀膜技术镀出的膜层,具有高硬度、高耐磨性(低摩擦系数)、很好的耐腐蚀性和化学稳定性等特点,膜层的寿命更长;同时膜层能够大幅度提高工件的外观装饰性能。
5. PVD镀膜能够镀出的膜层种类—PVD镀膜技术是一种能够真正获得微米级镀层且无污染的环保型表面处理方法,它能够制备各种单一金属膜(如铝、钛、锆、铬等),氮化物膜(TiN、ZrN、CrN、TiAlN)和碳化物膜(TiC、TiCN),以及氧化物膜(如TiO等)。
6. PVD镀膜膜层的厚度—PVD镀膜膜层的厚度为微米级,厚度较薄,一般为0.3μm ~5μm,其中装饰镀膜膜层的厚度一般为0.3μm ~1μm ,因此可以在几乎不影响工件原来尺寸的情况下提高工件表面的各种物理性能和化学性能,镀后不须再加工。
7. PVD镀膜能够镀出的膜层的颜色种类—PVD镀膜目前能够做出的膜层的颜色有深金黄色,浅金黄色,咖啡色,古铜色,灰色,黑色,灰黑色,七彩色等。
半导体 pvd工艺流程

半导体 pvd工艺流程半导体PVD工艺流程半导体PVD(物理气相沉积)工艺是一种常用的半导体加工技术,主要用于制备薄膜材料,如金属、合金、氧化物等,其工艺流程包括多个步骤,下面将详细介绍。
1. 基片准备半导体PVD工艺的第一步是基片准备。
基片是晶体硅或其他材料的片状基础材料。
在这一步骤中,需要对基片进行清洗,去除表面的杂质和污染物,以确保后续工艺的顺利进行。
常用的清洗方法包括溶液浸泡、超声波清洗等。
2. 蒸发源加载蒸发源是PVD工艺中的关键设备,用于提供薄膜材料。
在这一步骤中,需要将目标材料装载到蒸发源中。
装载时需要注意保持蒸发源的清洁,避免杂质和污染物的混入。
3. 抽真空在半导体PVD工艺中,需要在蒸发室内建立真空环境。
这是为了防止气体分子对薄膜材料的干扰,确保薄膜的质量和性能。
抽真空的过程通常使用真空泵进行,将蒸发室内的气体抽出。
4. 加热基片在进行薄膜沉积之前,需要对基片进行加热处理。
加热可以使基片表面的晶格结构更加均匀,提高薄膜的结晶性和致密性。
加热温度的选择应根据具体材料和工艺要求进行。
5. 蒸发沉积当基片加热到一定温度后,薄膜材料开始从蒸发源中蒸发,并沉积在基片表面上。
蒸发源中的材料会通过热蒸发或电子束蒸发的方式转化为气相,然后在真空环境中沉积在基片上。
6. 薄膜厚度控制在薄膜沉积过程中,需要对薄膜的厚度进行控制。
这可以通过监测薄膜的生长速率和时间来实现。
常用的监测方法包括椭偏仪、石英晶体监测器等。
根据需要,可以采取闭环控制或开环控制的方式进行薄膜厚度的控制。
7. 后处理薄膜沉积完成后,需要进行后处理步骤来改善薄膜的性能。
后处理可以包括退火、氧化、磁控溅射等。
退火可以提高薄膜的结晶性和致密性,氧化可以增加薄膜的化学稳定性,磁控溅射可以改善薄膜的结构和性能。
8. 薄膜性能测试对沉积的薄膜进行性能测试。
常用的测试方法包括薄膜厚度测量、表面形貌观察、结构分析、电学性能测试等。
通过测试可以评估薄膜的质量和性能是否符合要求。
pvd 物理气相沉积工艺

pvd 物理气相沉积工艺
PVD物理气相沉积工艺是一种常用的薄膜制备技术,广泛应用于微电子、光电子、材料科学等领域。
它采用物理方式将固态材料转化为气相,再通过各种方法沉积到基底上,从而形成具有特定功能和性能的薄膜材料。
PVD物理气相沉积工艺有多种方法,其中最常见的包括磁控溅射、电弧离子镀、激光溅射等。
这些方法都基于相同的原理,即通过外加能量将材料转化为气态,然后将气态材料沉积到基底上。
在磁控溅射工艺中,通过在真空环境下施加磁场,使金属靶材表面的原子被电子轰击击碎,并以高速运动的方式沉积到基底上。
这种方法可以制备出高质量、致密的薄膜,具有优异的粘附力和膜层均匀性。
电弧离子镀工艺则利用电弧放电产生的高能离子束,在真空环境下将金属靶材表面的原子击碎并沉积到基底上。
电弧离子镀工艺可以制备出具有较高密度和较高结晶度的薄膜,适用于制备金属薄膜和复合薄膜。
激光溅射工艺则利用激光束对靶材进行照射,将靶材表面的原子击碎并沉积到基底上。
激光溅射工艺具有高度的可控性和可重复性,可以制备出高质量、高纯度的薄膜,广泛应用于光学薄膜、显示器件等领域。
PVD物理气相沉积工艺具有许多优点,例如制备过程简单、操作方便、沉积速率高、薄膜质量好等。
它可以制备出各种材料的薄膜,如金属薄膜、合金薄膜、氧化物薄膜等,具有广泛的应用前景。
总的来说,PVD物理气相沉积工艺是一种重要的薄膜制备技术,具有广泛的应用领域和优势。
通过不同的方法和参数的选择,可以制备出具有不同性质和功能的薄膜材料,为各种领域的研究和应用提供了重要的支持和推动。
PVD薄膜沉积工艺及设备

缺点
蒸镀化合物时由于热分解现象 难以控制组分比,低蒸气压物
质难以成膜
需要溅射靶,靶材需要精制, 而且利用率低,不便于采用掩
膜沉积
装置及操作均较复杂,不便于 采用掩膜沉积
15
三 PVD薄膜沉积中常见问题
如何提高PVD薄膜 的粘附性
基片的预处理 9 水洗 9 有机溶剂清洗 9 超声波清洗 9 蚀刻
四 PVD薄膜的表征
PVD薄膜的表征
电学性能:四探针 粘附性:划痕法 内应力:X射线衍射法 膜厚:台阶仪 表面粗糙度:AFM
21
五 纳米加工平台现有设备介绍
磁控溅射-LAB18
22
五 纳米加工平台现有设备介绍
LAB18系统组成
控
抽
制 系
电源
加热
真 空
统
系
统
真空腔体
冷却系统
五 纳米加工平台现有设备介绍
3
一 PVD薄膜沉积的基本原理
PVD技术的分类
物理气相沉积(PVD)
真空蒸镀
溅射镀膜
离子镀
电子束(EB)蒸发 热蒸发 直流溅射 射频溅射 脉冲直流溅射
4
一 PVD薄膜沉积的基本原理
真空蒸镀
真空蒸镀是将镀料在真空中加热、蒸发,使蒸 发的原子或原子团在温度较低的基板上凝结, 形成薄膜。
热蒸发、EB蒸发。
三 PVD薄膜沉积中常见问题
镀膜前对基片进行离子轰击
三 PVD薄膜沉积中常见问题
镀膜时的加热 衬底和膜之间加
入接触金属(Cr、 Ni、Ti、W等)
三 PVD薄膜沉积中常见问题
如何在大台阶表面沉积厚度均匀的 薄膜
三 PVD薄膜沉积中常见问题
基片与蒸发源间的距离 镀膜时的压力 基片加偏压
微纳制造导论-PVD工艺
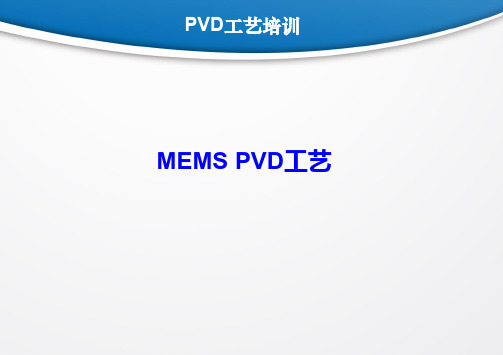
PVD工艺培训MEMS PVD工艺薄膜制备工艺与设备◆薄膜制备概述◆PVD原理与工艺◆现有设备介绍薄膜制备概述01PVD 原理与工艺02现有设备介绍03主要内容PVD 工艺培训发展历程二次大战期间,德国为了适应当时战争的需求,在镜片和反光镜上镀制铝膜,真空蒸发镀膜开始进入实际应用。
20世纪80年代以来,以真空技术为基础利用物理化学方法等方面,并且吸收了等离子体、电子束、分子束、离子束等系列新技术,把原始单一的真空镀膜技术发展到包括真空蒸发镀膜、溅射镀膜、离子镀膜、化学气相沉积、分子束外延、离子束流沉积以及薄膜厚度的测量和监控,薄膜的结构、形态、成分、特性等诸多技术在内,被称为“薄膜科学与技术”的新学科领域。
目前,随着高新技术的发展,作为新技术革命的光导、能源、材料和信息科学等领域所要求的具有特殊形态材料的薄膜,已经成为光学、微电子、传感器、信息、能源等一系列先进技术的基础,并已广泛渗透到当代科学技术的各个领域中,而且,开发和应用这些具有特殊用途的薄膜材料本身就是高新技术的重要组成部分。
薄膜应用20世纪60年代,随着高真空、超高真空技术的发展,真空镀膜进入高速发展时期,各种功能薄膜的应用已经扩展到工业生产各个领域,归纳起来,主要有以下几个方面:●电子工业用薄膜●光学工业用薄膜●机械、化工、石油等工业用薄膜●民用与食品工业用薄膜薄膜应用●电子工业用薄膜半导体电子元件中的电极、绝缘层等方面,传感器中的压电材料等方面,太阳能电池中的薄膜材料等诸多方面的应用。
●光学工业用薄膜照相机、望远镜、放映机等光学设备需要的减反射膜、反射膜,分光镜与滤光片的薄膜涂层,照明光源中的冷光镜膜,集成光学元件中的半导体膜等方面的应用。
●机械、化工、石油等工业用薄膜刀具、模具上的硬质薄膜,化学容器表面的耐腐蚀薄膜,涡轮发动机表面的耐高温薄膜以及其他极端特殊场合需要的特质薄膜等方面的应用。
●民用与食品工业用薄膜汽车、玩具、家电、钟表、工艺美术品等需要的装饰与保护用薄膜,药品、化妆品、食品行业包装需要的薄膜等方面的应用。
pvd设备
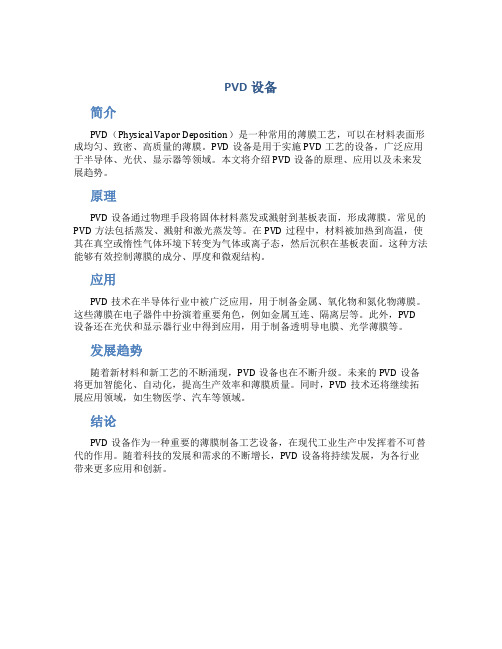
PVD设备
简介
PVD(Physical Vapor Deposition)是一种常用的薄膜工艺,可以在材料表面形成均匀、致密、高质量的薄膜。
PVD设备是用于实施PVD工艺的设备,广泛应用于半导体、光伏、显示器等领域。
本文将介绍PVD设备的原理、应用以及未来发展趋势。
原理
PVD设备通过物理手段将固体材料蒸发或溅射到基板表面,形成薄膜。
常见的PVD方法包括蒸发、溅射和激光蒸发等。
在PVD过程中,材料被加热到高温,使其在真空或惰性气体环境下转变为气体或离子态,然后沉积在基板表面。
这种方法能够有效控制薄膜的成分、厚度和微观结构。
应用
PVD技术在半导体行业中被广泛应用,用于制备金属、氧化物和氮化物薄膜。
这些薄膜在电子器件中扮演着重要角色,例如金属互连、隔离层等。
此外,PVD
设备还在光伏和显示器行业中得到应用,用于制备透明导电膜、光学薄膜等。
发展趋势
随着新材料和新工艺的不断涌现,PVD设备也在不断升级。
未来的PVD设备将更加智能化、自动化,提高生产效率和薄膜质量。
同时,PVD技术还将继续拓展应用领域,如生物医学、汽车等领域。
结论
PVD设备作为一种重要的薄膜制备工艺设备,在现代工业生产中发挥着不可替代的作用。
随着科技的发展和需求的不断增长,PVD设备将持续发展,为各行业带来更多应用和创新。
PVD设备及工艺简介

PVD设备及工艺简介1. 引言物理气相沉积(Physical Vapor Deposition,PVD)是一种常见的表面处理技术,广泛应用于不同领域的成膜和涂层制备。
PVD技术可以在材料表面形成不同性质的薄膜,具有较高的硬度、耐磨性和化学稳定性。
本文将对PVD设备和相关工艺进行简要介绍。
2. PVD设备分类根据不同的工艺需求,PVD设备可以分为以下几类:2.1 蒸发设备蒸发设备主要由蒸发源、基底(衬底)和真空系统组成。
常见的蒸发源包括电阻加热、电子束和激光蒸发源。
蒸发源加热后,材料开始蒸发并沉积在基底上形成薄膜。
2.2 磁控溅射设备磁控溅射设备利用磁场和高能离子束来溅射材料。
在真空室中,通过施加磁场和加速电压,使得离子在靶材表面打击,从而产生溅射材料沉积在基底上的效果。
磁控溅射设备一般包括靶材、基底和真空系统。
2.3 磁电控溅射设备磁电控溅射设备是磁控溅射设备的一种改进型,它通过进一步控制离子束的能量和磁场分布,提高了沉积薄膜的结构和性能。
磁电控溅射设备一般增加了靶材的偏转磁场和偏转电场控制装置。
2.4离子镀设备离子镀设备是一种利用离子束作用于基底表面的沉积方法。
离子束可以提高沉积速率和改善薄膜质量。
离子镀设备一般包括离子源、基底和真空系统。
3. PVD工艺3.1 清洗与预处理在PVD沉积之前,基底通常需要进行清洗和预处理,以去除表面的污染物和提高附着力。
清洗可以采用化学溶液浸泡、超声波清洗等方法,预处理包括亚洲台湾地区衬底表面活化和合适的基底温度控制等。
3.2 沉积PVD沉积是将材料以蒸发或溅射等方式沉积在基底上形成薄膜。
具体的沉积工艺参数需要根据材料的性质和需要的膜层特性进行调整,如溅射功率、工作气压、蒸发温度和沉积速率等。
3.3 后处理PVD沉积完成后,常常需要进行后处理步骤以改善薄膜的质量和性能。
后处理可以包括退火、离子束辐照等步骤,以优化薄膜的结构和性能。
4. 应用领域PVD技术广泛应用于不同领域,包括电子学、光学、航空航天、医疗器械等。
pvd沉积工艺

pvd沉积工艺PVD沉积工艺一、简介PVD(Physical Vapor Deposition)是一种通过物理方法将材料从固态直接转变为薄膜形态的沉积工艺。
其主要原理是在真空环境下,通过蒸发、溅射或弧放电等方式将材料原子或分子从源材料中释放出来,然后沉积到基底表面形成薄膜。
二、PVD沉积工艺的分类根据源材料的不同,PVD沉积工艺可以分为以下几种类型:1. 蒸发沉积蒸发沉积是将固态源材料加热至其蒸发温度,使其原子或分子蒸发并沉积到基底表面的过程。
蒸发沉积通常采用电子束蒸发、阻焊蒸发或热丝蒸发等方式进行。
2. 磁控溅射磁控溅射是通过在真空室中施加磁场,使源材料表面形成等离子体,并利用离子轰击的方式将材料溅射到基底表面。
磁控溅射具有较高的沉积速率和较好的均匀性,广泛应用于金属、合金、氧化物等材料的沉积。
3. 弧放电沉积弧放电沉积是通过在源材料和基底之间施加高电压,产生电弧放电并将源材料溅射到基底表面。
弧放电沉积具有较高的溅射速率和较高的沉积温度,适用于一些高熔点材料的沉积。
4. 磁控磁控溅射沉积磁控磁控溅射沉积是将磁控溅射和磁控溅射两种沉积方式进行结合,可同时利用两种方式的优点,提高沉积速率和薄膜质量。
三、PVD沉积工艺的应用PVD沉积工艺在各个领域都有广泛的应用。
以下是几个常见的应用领域:1. 光学镀膜PVD沉积工艺可用于光学镀膜,例如在眼镜片、镜面反射器、太阳能电池板等器件上沉积透明导电膜、反射膜、防反射膜等。
2. 电子器件制造PVD沉积工艺可用于制造半导体器件、集成电路、显示屏等电子器件。
例如,在集成电路制造中,可利用PVD沉积工艺沉积金属互连线、金属电极等。
3. 工具涂层PVD沉积工艺可用于涂层刀具、模具等工具表面,提高其硬度、耐磨性、耐腐蚀性等性能。
4. 装饰涂层PVD沉积工艺可用于制作金属色彩、金属质感等装饰涂层。
例如,在钟表、手机壳等产品上沉积金属薄膜,增加其外观质感。
四、PVD沉积工艺的优势和挑战PVD沉积工艺相比其他沉积工艺具有以下优势:1. 沉积速率较快:PVD沉积工艺的沉积速率较高,能够快速制备薄膜。
PVD及设备

20K时,泵的极限压力约为冷凝
Shanghai Tianma Microelectronics
19
真空系统
油扩散泵
利用加热使真空泵油蒸 发,油蒸气高速扩散到A处 时转向下,将连接真空室的 Flange处的气体带走,来自 真空室的气体从8处管道排 走,而油本身被冷却后又回 到泵底部的油箱内。工作压 强为1.3×10-2Pa~1.3×107Pa,启动压强为1.3Pa
Shanghai Tianma Microelectronics
18
真空系统
②低温吸附:气体分子以一个单分子层厚 (10-8厘米数量级)被 吸附到涂在冷板上的吸附剂表面上。吸附的平衡压力比相同温度 下的蒸气压力低得多。如在 20K时氢的蒸气压力等于大气压力, 用 20K的活性炭吸氢时吸附平衡压力则低于10-8 帕。这样就可 能在较高温度下通过低温吸附来进行抽气。
-特征- ・排气能力可从大气压到10-1Pa。 ・真空部内不需要润滑油,可以制造洁净的真空。 ・泵价格非常昂贵。 ※驱动齿轮部需要润滑油 (主要厂家:荏原製作所、BOCEdwards)
Shanghai Tianma Microelectronics
16
低温泵
真空系统
利用低温表面冷凝气体的真空 泵,又称冷凝泵。低温泵是获得 清洁真空的极限压力最低、抽气 速率最大的真空泵,广泛应用于 半导体和集成电路的研究和生 产,以及分子束研究、真空镀膜 设备、真空表面分析仪器、离子 注入机和空间模拟装置等方面。
Shanghai Tianma Microelectronics
3
薄膜的物理制备技术
物理气相沉积 (PVD)
真空 蒸发
溅射 射
离子镀
电阻加热 感应加热 电子束加热 激光加热
PVD加工工艺流程

PVD加工工艺流程
PVD(物理气相沉积)加工技术是一种将金属材料薄膜沉积在基材表
面的工艺方法。
它广泛应用于各种行业,如光学、电子、医疗和装饰等。
以下是PVD加工的基本工艺流程。
1.准备工作
在开始PVD加工之前,需要做一些准备工作。
首先,选择适当的基材,如玻璃、塑料、陶瓷或金属等。
其次,对基材表面进行清洁和处理,以确
保薄膜能够牢固附着在基材上。
清洁可以使用化学溶液或高压水来完成。
2.蒸发源
3.真空室
4.沉积薄膜
在蒸发源产生的蒸汽进入真空室后,蒸汽将沉积在基材表面上。
沉积
过程可以通过多种方式实现,如物理气相沉积、磁控溅射或电弧离子镀等。
根据需要,可以使用单一金属或合金材料进行沉积。
5.控制层厚度
控制薄膜的厚度是PVD加工的关键。
可以通过调节蒸发源的温度、时
间和蒸发速率来控制薄膜的厚度。
还可以使用感应器或激光干涉仪等装置
来测量和监控薄膜的厚度,以确保其符合要求。
6.薄膜成型
沉积在基材表面的薄膜通常是非晶态的,需要经过退火或其他处理来改善其结晶性和质量。
这可以通过加热、冷却或应力处理来实现。
薄膜成型后,可以进行后续加工,如切割、打磨和抛光等。
7.薄膜质量检验
最后,需要对薄膜的质量进行检验。
可以使用显微镜、扫描电子显微镜(SEM)和X射线衍射等设备来检测薄膜的表面形貌和结构。
还可以使用厚度计和硬度计等仪器来测试薄膜的厚度和硬度。
PVD薄膜沉积工艺及设备

PVD薄膜沉积工艺及设备薄膜沉积工艺是指将材料以薄膜的形式沉积在基底上的过程。
薄膜沉积广泛应用于半导体、光电子、化学、材料等领域,对于制备各类微电子器件、光电子器件、传感器、涂层材料等起着重要作用。
其中,物理气相沉积(PVD)是一种常用的薄膜沉积工艺,本文将对PVD薄膜沉积工艺及设备进行详细介绍。
PVD薄膜沉积工艺是通过物理方法,将目标材料表面原子或分子从固体态转化为气相态,并在此过程中形成凝聚到基底表面的薄膜。
PVD薄膜沉积工艺包括了蒸发沉积、溅射沉积和离子束沉积等几种不同的方法。
以下分别对这几种方法进行介绍。
蒸发沉积是最简单的一种PVD薄膜沉积方法。
其基本原理是将固态目标材料加热到一定温度,使其表面原子或分子获得足够的热能,从而转化为气相态,并经过扩散到基底表面沉积形成薄膜。
蒸发沉积可以通过热蒸发、电子束蒸发和激光蒸发等方法实现。
溅射沉积是一种利用目标材料被离子轰击而从固态转化为气相,然后沉积到基底表面的PVD薄膜沉积方法。
溅射沉积主要包括磁控溅射和电弧溅射两种方式。
在磁控溅射中,通过施加磁场使得离子在靶表面形成环状轨道,从而实现离子轰击靶材并将其剥离成粒子,最终沉积到基底表面形成薄膜。
电弧溅射则是通过高能电弧加热靶材并使用气体离子轰击的方式实现薄膜的沉积。
离子束沉积是一种将目标材料通过离子化并施加高能电场使其沉积到基底表面的薄膜沉积方法。
离子束沉积主要包括了离子束辅助沉积和离子束极化沉积两种方式。
离子束辅助沉积利用高能离子束轰击基底表面,提高基底表面的活性,从而促进薄膜的成核和生长。
离子束极化沉积则是通过施加电场使离子束发生极化,改变离子束的性质,进而实现薄膜的沉积。
PVD薄膜沉积设备是实现PVD薄膜沉积工艺的关键工具。
常见的PVD薄膜沉积设备包括蒸发器、溅射器和离子束设备等。
蒸发器通常由源材料装置、加热装置和抽气系统等组成。
源材料装置用于装载目标材料,加热装置则用于加热目标材料,使其蒸发成为气相。
pvd设备原理

PVD(Physical Vapor Deposition)是一种常用的薄膜沉积技术,旨在通过物理手段将材料从固态直接转变为蒸汽或离子状态,并在基底表面形成薄膜。
PVD设备是用于执行PVD工艺的专用设备。
PVD设备的原理如下:1.蒸发源:PVD设备包含一个或多个蒸发源,通常是热丝、电子束或磁控溅射源。
这些蒸发源中的材料,例如金属或化合物,被加热到高温以产生蒸汽或离子。
2.气氛控制:PVD设备中的气氛控制系统用于维持特定的工作气氛,通常是真空环境。
通过降低背景压力,可以减少与大气中的气体相互作用,确保薄膜沉积的纯度和质量。
3.基底/靶材:需要被沉积薄膜的基底或靶材放置在设备中的夹具上。
基底通常是平坦的材料,如玻璃、金属或半导体衬底,而靶材则是用于溅射的材料。
4.沉积过程:在PVD设备中,蒸发源产生的蒸汽或离子沿着设备的导向路径朝向基底或靶材方向传输。
薄膜形成的过程可以通过以下两种主要方式之一实现:●热蒸发:蒸发源中的材料被加热到高温,使其转变为蒸汽状态,并然后在基底表面冷凝形成薄膜。
●溅射:通过施加电场或磁场,将靶材上的原子或离子从固态解离,并在真空环境中以快速而直线运动的方式击打基底表面,形成薄膜。
5.薄膜控制:通过控制PVD设备中的工艺参数,如温度、沉积时间和沉积速率等,可以调整薄膜的厚度、成分和结构。
此外,还可以使用控制技术,如旋转夹具或倾斜靶材,以均匀地沉积薄膜。
总之,PVD设备通过物理手段将材料从固态转变为蒸汽或离子状态,并沉积在基底表面,形成薄膜。
蒸发源、气氛控制、基底/靶材和沉积过程是PVD设备的关键组成部分,用于实现薄膜沉积的控制和精确性。
- 1、下载文档前请自行甄别文档内容的完整性,平台不提供额外的编辑、内容补充、找答案等附加服务。
- 2、"仅部分预览"的文档,不可在线预览部分如存在完整性等问题,可反馈申请退款(可完整预览的文档不适用该条件!)。
- 3、如文档侵犯您的权益,请联系客服反馈,我们会尽快为您处理(人工客服工作时间:9:00-18:30)。
15
三 PVD薄膜沉积中常见问题
如何提高PVD薄膜 的粘附性
基片的预处理 水洗 有机溶剂清洗 超声波清洗 蚀刻
三 PVD薄膜沉积中常见问题
镀膜前对基片进行离子轰击
三 PVD薄膜沉积中常见问题
镀膜时的加热 衬底和膜之间加 入接触金属(Cr、 Ni、Ti、W等)
三 PVD薄膜沉积中常见问题
如何在大台阶表面沉积厚度均匀的 薄膜
PVD(物理气相沉积)薄 膜工艺及设备介绍
赵德胜
1
主要内容
一 二 三 四 五 PVD薄膜沉积的基本原理 PVD薄膜沉积各种方式的比较 PVD薄膜沉积中常见问题 PVD薄膜的表征 纳米加工平台现有设备介绍
2
一 PVD薄膜沉积的基本原理
在半导体行业PVD主要用于金属化
物理气相沉积(Physical Vapor Deposition, PVD)技术:表示在真空条件下,采用物理方 法,将材料源-固体或液体表面气化成气体原 子、分子或部分电离成离子,并通过低压气体 (或等离子体)过程,在基体表面沉积具有特 殊功能薄膜的技术。
三 PVD薄膜沉积中常见问题
基片与蒸发源间的距离 镀膜时的压力 基片加偏压
四 PVD薄膜的表征
PVD薄膜的表征
电学性能:四探针 粘附性:划痕法 内应力:X射线衍射法 膜厚:台阶仪 表面粗糙度:AFM
21
五 纳米加工平台现有设备介绍
磁控溅射-LAB18
22
五 纳米加工平台现有设备介绍
LAB18系统组成 控 制 系 统 电源 加热 抽 真 空 系 统
12
一 PVD薄膜沉积的基本原理
离子镀:在真空条件 下,利用气体放电使 气体或蒸发物质离化 ,在气体离子或被蒸 发物质离子轰击作用 的同时,把蒸发物或 其反应物蒸镀在基片 上。 离子镀把辉光放电、 等离子体技术与真空 蒸发镀膜技术结合在 一起
一 PVD薄膜沉积的基本原理
物理气相沉积技术基本原理的三个过程
一 PVD薄膜沉积的基本原理
热蒸发原理及特点
热蒸发是在真空状况下,将所要蒸镀的材料 利用电阻加热达到熔化温度,使原子蒸发, 到达并附着在基板表面上的一种镀膜技术。 特点:装置便宜、操作简单广泛用于Au、Ag、 Cu、Ni、In、Cr等导体材料。
一 PVD薄膜沉积的基本原理
E-beam蒸发原理
热电子由灯丝发射后,被加速阳极加速,获得 动能轰击到处于阳极的蒸发材料上,使蒸发材 料加热气化,而实现蒸发镀膜。 特点:多用于要求纯度极高的膜、绝缘物的蒸 镀和高熔点物质的蒸镀
电极 约5MHZ
晶体
膜厚
蒸气
34
五 纳米加工平台现有设备介绍
ei-5z腔体内部
35
五 纳米加工平台现有设备介绍
ei-5z主界面
36
五 纳米加工平台现有设备介绍
ei-5z的性能指标
真空度:5E-6Pa 基片最高温度:300℃ 电子枪功率:8KW 厚度均匀性:< ±5% 可加工样品尺寸:6寸每次8片,4寸每次8片, 2寸每次180片,以及小样品夹具 现有蒸发源:Au、Ti、Ni、Cr、Au88Ge12、Al 、In、Sn、Ag、Pd
五 纳米加工平台现有设备介绍
ei-5z工艺参数
材料名称 High Vol(KV) 本底真空(Pa) 蒸发温度(℃) 蒸发功率(%) 蒸发速率(A/S) 蒸发厚度(A) Ti 7.5 8E-5 23 28 2 50 坩埚号 X/Y—Position X/Y—Sweep 衬底转(r/m) 预蒸发时间 Gain/Time-C/Limit Tooling 5 3 3 8 2min 5 85 10 3 3.5 0
Thick(A)
39
五 纳米加工平台现有设备介绍
ei-5z操作注意事项
开机前注意检查水电气正常; 做工艺之前检查坩埚源的状态,如源不够及 时通知相应工作人员; 禁止在低真空条件下打开电子枪电源; 蒸发前注意晶振片的频率和所要蒸发材料的 量 蒸镀过程中,注意观察所蒸发的材料是否正 确,电子束斑位置; 禁止非授权操作人员执行开机和关机步骤。
熔融的 蒸镀源 电子束
水 水冷 坩埚
一 PVD薄膜沉积的基本原理
溅射镀膜
溅射-用带有几十电子伏以上动能的粒子或粒 子束照射固体表面,靠近固体表面的原子会获 得入射粒子所带能量的一部分进而向真空中放 出,这种现象称为溅射。
一 PVD薄膜沉积的基本原理
溅射镀膜
磁控溅射-电子在电场的作用下加速飞向基片 的过程中与氩原子发生碰撞,电离出大量的氩 离子和电子,电子飞向基片,氩离子在电场的 作用下加速轰击靶材,溅射出大量的靶材原子 ,呈中性的靶原子(或分子)沉积在基片上成 膜。
五 纳米加工平台现有设备介绍
三种设备的比较
性质 沉积 粘附 均匀 致密 速率 性 性 性 方法 LAB 18 ei-5z 热蒸发 可控 可控 优 良 优 优 良 优 良 差 可控 可控 差 高 高 低
46
膜厚 控制
成本
不可 一般 控
上机培训价格(暂定)
• 溅射(LAB 18):450元/人 • 电子束蒸发(ei-5z):450元/人 • 热蒸发:350元/人
镀料的气化 镀料原子、分子或离子的迁移 镀料原子、分子或离子在基体上凝结
14
二 PVD薄膜沉积各种方式的比较
真空蒸镀、溅射镀膜和离子镀的比较
方法
真空 蒸镀 溅射 镀膜 离子 镀
优点
工艺简便,纯度高,通 过掩膜易于形成所需要 的图形 附着性能好,易于保持 化合物、合金的组分比
缺点
蒸镀化合物时由于热分解现象 难以控制组分比,低蒸气压物 质难以成膜 需要溅射靶,靶材需要精制, 而且利用率低,不便于采用掩 膜沉积 附着性能好,化合物、 装置及操作均较复杂,不便于 合金、非金属均可成膜 采用掩膜沉积
48
五 纳米加工平台现有设备介绍
热蒸发操作注意事项
不要用坚硬物品敲击触摸屏。 如果系统有异常声音或气味应马上停止工作,关闭总 电源,查出问题后再工作。 如果系统长期不用,要使真空腔处于真空状态关闭机 器。 充气阀充气完毕后要及时关闭。 单独用一个真空室工作时,一定要保持另一个真空室 处于低真空状态,不可是大气压状态。 束源炉在升温的过程中通过面板上的调节旋钮调节电 流不能超过3A,蒸发过程中温度不稳定可增加电流。 束源炉的温度或蒸发舟的温度必须降低到100度以下才 可关闭真空系统,开启真空室。
一 PVD薄膜沉积的基本原理
什么是辉光放电?
辉光放电是指在稀薄气体中,两个电极之间加 上电压时产生的一种气体放电现象。
10
一 PVD薄膜沉积的基本原理
直流溅射:适用于金 属材料 射频溅射:是适用于 各种金属和非金属材 料的一种溅射沉积方 法
一 PVD薄膜沉积的基本原理
脉冲溅射:一种用于消除直流反应溅射 中异常放电技术。 反应溅射:在溅射过程中,在工艺气体 中混入活性气体,在溅射过程中发生反应 生成氧化物、氮化物等的溅射方式。
真空腔体
冷却系统
五 纳米加工平台现有设备介绍
LAB18 Vacuum界面
24
五 纳米加工平台现有设备介绍
LAB18 Deposition界面
25
ห้องสมุดไป่ตู้
五 纳米加工平台现有设备介绍
LAB18 腔体内部
26
五 纳米加工平台现有设备介绍
LAB 18的性能指标
真空度:2E-7Torr 工艺气体:Ar、O2、N2 衬底升温:450℃ 反溅功率:100W 直流源:500W 射频源:300W 脉冲直流:300W 厚度均匀性:< ±5% 可加工样品尺寸:6寸和4寸每次一片,2寸每 次4片,小样品夹具
3
一 PVD薄膜沉积的基本原理
PVD技术的分类
物理气相沉积(PVD) 真空蒸镀 电子束(EB)蒸发 热蒸发 溅射镀膜 直流溅射 射频溅射 脉冲直流溅射 离子镀
4
一 PVD薄膜沉积的基本原理
真空蒸镀
真空蒸镀是将镀料在真空中加热、蒸发,使蒸 发的原子或原子团在温度较低的基板上凝结, 形成薄膜。 热蒸发、EB蒸发。
40
五 纳米加工平台现有设备介绍
热蒸发设备外观
液晶显示器 腔体
加热控制显示
41
五 纳米加工平台现有设备介绍
热蒸发真空示意图
42
五 纳米加工平台现有设备介绍
• 热蒸发操作界面
五 纳米加工平台现有设备介绍
热蒸发的性能指标
真空度:5E-6Pa 基片最高温度:200℃ 可蒸发材料:Al、Au、In、Ag、Ni等金 属
38
五 纳米加工平台现有设备介绍
Power(%)
40 30 20 10 0 5 0 50 100 150 200
Time(S)
Power
250
Rate
Rate(A/S)
0 0 50 100 150 200 250 400 200 0 0 50 100 150 200 250
Time(S) Time(S) Thick
31
五 纳米加工平台现有设备介绍
电子束蒸发- ei-5z
操作界面 真空腔体
32
五 纳米加工平台现有设备介绍
ei-5z系统组成 控 制 系 统
膜 厚 控 制 坩 埚 电 子 枪
真空腔体
抽 真 空 系 统
冷却系统
五 纳米加工平台现有设备介绍
膜厚控制
监视蒸镀速率的方法 是利用共振的石英晶 体。结晶的石英晶体 具有压电性的,在共 振频率时,石英晶体 产生震荡电压,晶体 放大并回授以驱动晶 体,就可监督蒸镀速 率。
Ag
速率:8.1A/S
29
五 纳米加工平台现有设备介绍
LAB18 工艺参数
材料 Au Al Ni Ti Ag Pt 速率(A/S) 8.9 2.7 3.6 2 8 6