热处理工艺总结 (2)
(完整版)金属热处理知识点概括

(一)淬火--将钢加热到Ac3或Ac1以上,保温一段时间,使之奥氏体化后,以大于临界冷速的速度冷却的一种热处理工艺。
淬火目的:提高强度、硬度和耐磨性。
结构钢通过淬火和高温回火后,可以获得较好的强度和塑韧性的配合;弹簧钢通过淬火和中温回火后,可以获得很高的弹性极限;工具钢、轴承钢通过淬火和低温回火后,可以获得高硬度和高耐磨性;对某些特殊合金淬火还会显著提高某些物理性能(如高的铁磁性、热弹性即形状记忆特性等)。
表面淬火--表面淬火是将钢件的表面层淬透到一定的深度,而心部分仍保持未淬火状态的一种局部淬火的方法。
分类——感应加热表面淬火、火焰加热表面淬火、电接触加热表面淬火、电解液加热表面淬火、激光加热表面淬火、电子束加热表面淬火、离子束加热表面淬火、盐浴加热表面淬火、红外线聚焦加热表面淬火、高频脉冲电流感应加热表面淬火和太阳能加热表面淬火。
单液淬火——将奥氏体化后的钢件投入一种淬火介质中,使之连续冷却至室温(图9-1a线)。
淬火介质可以是水、油、空气(静止空气或风)或喷雾等。
双液淬火——双液淬火方法是将奥氏体化后的钢件先投人水中快冷至接近MS点,然后立即转移至油中较慢冷却(图9-1b线)。
分级淬火——将奥氏体化后的钢件先投入温度约为MS点的熔盐或熔碱中等温保持一定时间,待钢件内外温度一致后再移置于空气或油中冷却,这就是分级淬火等温淬火--奥氏体化后淬入温度稍高于Ms点的冷却介质中等温保持使钢发生下贝氏体相变的淬火硬化热处理工艺。
等温淬火与分级淬火的区别是:分级淬火的最后组织中没有贝氏体而等温淬火组织中有贝氏体。
根据等温温度不同,等温淬火得到的组织是下贝氏体、下贝氏体+马氏体以及残余奥氏体等混合组织。
(二)回火--将淬火后的钢/铁,在AC1以下加热、保温后冷却下来的金属热处理工艺。
回火的目的:为了稳定组织,减小或消除淬火应力,提高钢的塑性和韧性,获得强度、硬度和塑性、韧性的适当配合,以满足不同工件的性能要求。
热处理实习报告总结

热处理实习报告总结——热处理上星期在铸造车间最后一道大工序热处理上实习完了,作为铸造的最后一道工序,热处理对轮毂的性能及后面的加工都起着很关键的作用。
经过热处理可以提高轮毂毛坯的力学强度及性能,使后面的机加和涂装能游刃有余的完成。
热处理工作区在整个铸造车间占了一大半的地,主要是因为这个工序比较复杂,由固溶、淬火和时效组成,有的轮子还需要特殊的抛丸。
固溶区就有八个区,占了近二十米,而时效有五个区也有十多米,所以整个工序占用的场地非常大,而在我实习的时候看到还准备新加一条热处理线。
占用场地大这是其一,这道工序消耗的时间也特别多,按照规定,固溶需要6±小时,而人工时效也需要±小时,一个轮毂从投料开始到包装出来最多也只需要2天时间,由此可见其特殊性啊。
呆了几天下来把自己所看到的和所学到的说一下:热处理过程中有三个步骤:固溶、淬火和时效。
固溶为第一个工序,把刚预钻孔完的轮毂放上料框,送进回溶入炉第一区开始固溶。
固溶分为八个区,第一区为升温区,温度规定控制在420~540度,实际中,由于经常开门进料,所以温度有时会低到420度,但一般都控制在440~480度,很少上500度;第二区到第七区为保温区,温度控制在535±5度,实际温度也是在535左右;第八区为出料区,温度控制为520~545度,实际温度为535度左右。
每框轮毂固溶的规定时间为6±小时,频率为~,实际固溶时间为6小时。
固溶的对铝合金轮毂的作用是:把铝合金中的强化相溶入α铝中,使其内部发生反应。
通常固溶区为半小时进一框,所以出框也是半小时出一次。
固溶区出框后,马上便要进行淬火处理,就是把刚固溶处于高温的轮毂浸入水中,改变其力学性能。
淬火的目的是使过冷奥氏体进行马氏体或贝氏体转变,得到马氏体或贝氏体组织,然后配合以不同温度的回火,以大幅提高钢的强度、硬度、耐磨性、疲劳强度以及韧性等,从而满足各种机械零件和工具的不同使用要求。
热处理工年终总结范文(精选5篇)
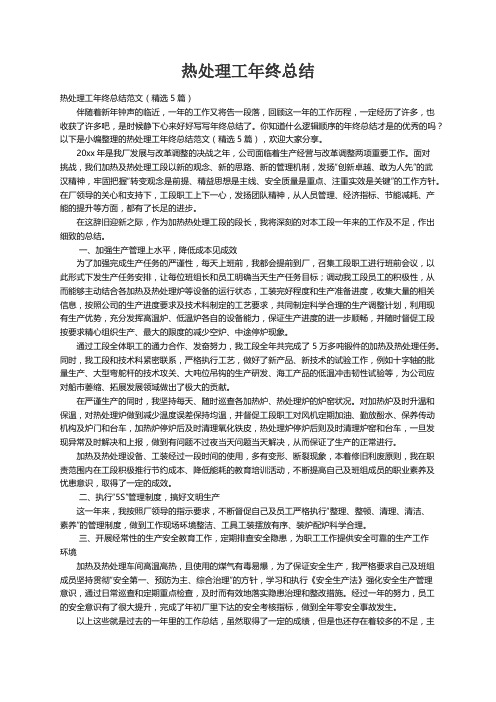
热处理工年终总结热处理工年终总结范文(精选5篇)伴随着新年钟声的临近,一年的工作又将告一段落,回顾这一年的工作历程,一定经历了许多,也收获了许多吧,是时候静下心来好好写写年终总结了。
你知道什么逻辑顺序的年终总结才是的优秀的吗?以下是小编整理的热处理工年终总结范文(精选5篇),欢迎大家分享。
20xx年是我厂发展与改革调整的决战之年,公司面临着生产经营与改革调整两项重要工作。
面对挑战,我们加热及热处理工段以新的观念、新的思路、新的管理机制,发扬“创新卓越、敢为人先”的武汉精神,牢固把握“转变观念是前提、精益思想是主线、安全质量是重点、注重实效是关键”的工作方针。
在厂领导的关心和支持下,工段职工上下一心,发扬团队精神,从人员管理、经济指标、节能减耗、产能的提升等方面,都有了长足的进步。
在这辞旧迎新之际,作为加热热处理工段的段长,我将深刻的对本工段一年来的工作及不足,作出细致的总结。
一、加强生产管理上水平,降低成本见成效为了加强完成生产任务的严谨性,每天上班前,我都会提前到厂,召集工段职工进行班前会议,以此形式下发生产任务安排,让每位班组长和员工明确当天生产任务目标;调动我工段员工的积极性,从而能够主动结合各加热及热处理炉等设备的运行状态,工装完好程度和生产准备进度,收集大量的相关信息,按照公司的生产进度要求及技术科制定的工艺要求,共同制定科学合理的生产调整计划,利用现有生产优势,充分发挥高温炉、低温炉各自的设备能力,保证生产进度的进一步顺畅,并随时督促工段按要求精心组织生产、最大的限度的减少空炉、中途停炉现象。
通过工段全体职工的通力合作、发奋努力,我工段全年共完成了5万多吨锻件的加热及热处理任务。
同时,我工段和技术科紧密联系,严格执行工艺,做好了新产品、新技术的试验工作,例如十字轴的批量生产、大型弯舵杆的技术攻关、大吨位吊钩的生产研发、海工产品的低温冲击韧性试验等,为公司应对船市萎缩、拓展发展领域做出了极大的贡献。
热处理总结
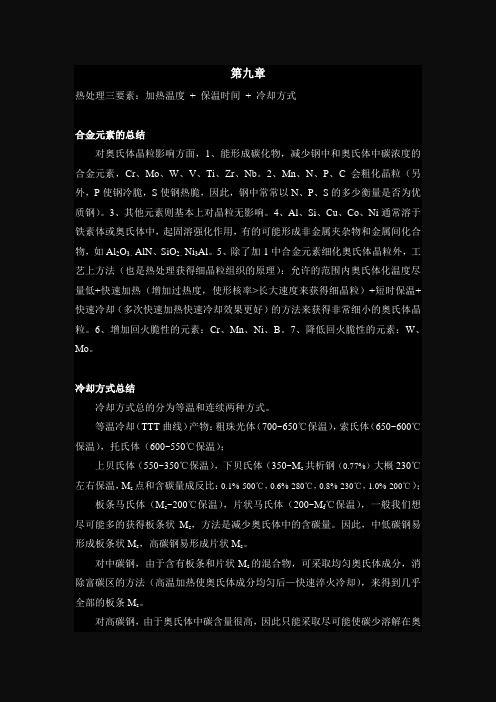
淬火:将钢加热到Ac3或Ac1以上一定温度(得到细小的奥氏体为依据),保温后以大于临界冷却速度冷却得到马氏体(或下贝氏体)的热处理工艺。
回火:将淬火钢加热到A1以下,使其转变为稳定的回火组织,并以适当的方式冷却的工艺过程。
均匀化退火:(Ac3或Acm以上150~300℃)。碳钢一般为1100~1200℃,合金钢一般为1200~1300℃,保温时间一般为10~15h,采用炉冷。当加热温度高、成本高,除非成分有区域偏析或较大的枝晶偏析才用,后加正火补充。
完全退火:(Ac3+20~30℃),保温时间:T= K•D min(K为1.5~2min/mm,D为工件有效厚度),采用炉冷,室温组织:铁素体+珠光体。用于消除魏氏组织(针片状)、带状组织,细化晶粒(相对组织而言);亚共析钢的预备热处理,均匀成分,消除加工硬化,降低硬度,为下一步切削加工做准备。
常见钢的编号(P307)
碳素结构钢(Q)低合金高强度钢(Q)碳素工具钢(T)
滚动轴承钢(G)焊接用钢(H)易切削钢(Y)
铸钢(ZG)锅炉用钢(g)桥梁用钢(q)
沸腾钢(F)半镇静钢(b)镇静钢(z)
机器零件、构件用钢,包括:渗碳钢(表层高强度硬度、耐磨性、抗疲劳强度,心部高强韧性,主要用于齿轮;低碳合金钢表面渗碳,淬火低温回火)、调质钢(综合性能高,主要用于轴类、连杆,中碳钢,调质处理)、弹簧钢(高碳钢,淬火350℃回火)、轴承钢(高强度硬度、耐磨性、抗疲劳强度高碳钢;淬火低温回火)。
常见的工程结构钢:型材、棒材、板材、管材、带材,由于他们都需要冷变形和焊接,采用低碳低合金钢;由于尺寸大、形状复杂,不能进行整体淬火回火,因此大部分工为热轧空冷(正火),室温组织:铁素体加少量珠光体。
2cr13热处理工艺

2cr13热处理工艺
1、2Cr13热处理工艺
2Cr13是一种高强度、高硬度的钢种,具有较高的抗腐蚀性和耐磨性。
它的热处理工艺是最常见的钢材热处理工艺,也是该钢材最常见的热处理工艺。
2Cr13的热处理工艺大体可分为以下几个常见的步骤:
(1)热处理前的处理:首先需要对2Cr13通过机械分级和机械抛光,使其表面光洁无毛刺,消除应力并达到最佳的热处理条件。
(2)加热:其次,2Cr13离心钢需要进行热处理,一般在1120℃~1180℃之间,将2Cr13加热到一定的温度,时间为3-8小时。
具体温度和时间的选择要根据2Cr13的碳含量和用途而定。
(4)退火:2Cr13在回火之后,要进行退火,通常在100℃左右,保持大约一小时;一般情况下,退火温度就是回火温度,并在一定时间内间断冷却或小幅冷却,防止室温罕见的大规模晶粒组织变化,并最大程度保持组织构造的稳定。
(5)淬火:2Cr13的淬火可以在室温或低温下进行,一般在50℃-450℃,具体温度根据2Cr13的用途而定,淬火时间一般为1-4小时,通过淬火可以增加其耐磨性等特性。
(6)冷却:在淬火完成后,2Cr13还需要进行冷却。
冷却方式分为急冷和缓冷两种,急冷方式主要是冷水冷却,但这种方式会使2Cr13的表面生成硬质晶界,缓冷方式则可以选择空气冷却或悬浮浴冷却。
冷却后,2Cr13可以减少残余应力。
(7)最终效果:通过2Cr13的热处理,可以增加其耐磨性,抗氧化性和抗腐蚀性,降低其易磨性,改善2Cr13的机械性能和成形性能,最终达到优良的使用性能。
总之,2Cr13的热处理是其最常见和最重要的处理工艺,虽然热处理设备较昂贵,但2Cr13的广泛应用,使其成为钢制品制造中的重要材料。
热处理专业年度质量总结(3篇)
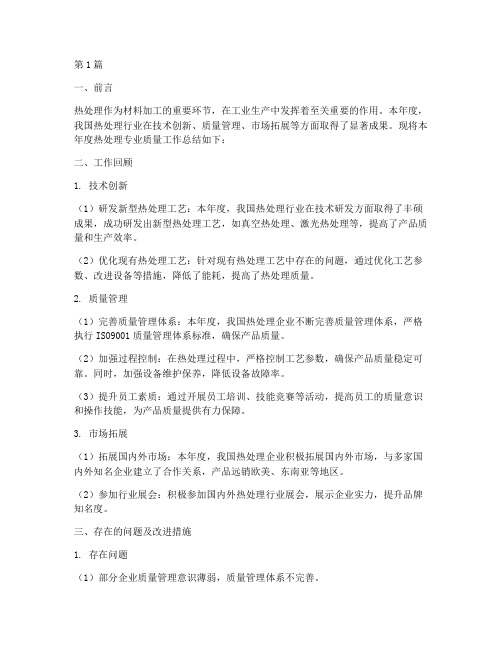
第1篇一、前言热处理作为材料加工的重要环节,在工业生产中发挥着至关重要的作用。
本年度,我国热处理行业在技术创新、质量管理、市场拓展等方面取得了显著成果。
现将本年度热处理专业质量工作总结如下:二、工作回顾1. 技术创新(1)研发新型热处理工艺:本年度,我国热处理行业在技术研发方面取得了丰硕成果,成功研发出新型热处理工艺,如真空热处理、激光热处理等,提高了产品质量和生产效率。
(2)优化现有热处理工艺:针对现有热处理工艺中存在的问题,通过优化工艺参数、改进设备等措施,降低了能耗,提高了热处理质量。
2. 质量管理(1)完善质量管理体系:本年度,我国热处理企业不断完善质量管理体系,严格执行ISO9001质量管理体系标准,确保产品质量。
(2)加强过程控制:在热处理过程中,严格控制工艺参数,确保产品质量稳定可靠。
同时,加强设备维护保养,降低设备故障率。
(3)提升员工素质:通过开展员工培训、技能竞赛等活动,提高员工的质量意识和操作技能,为产品质量提供有力保障。
3. 市场拓展(1)拓展国内外市场:本年度,我国热处理企业积极拓展国内外市场,与多家国内外知名企业建立了合作关系,产品远销欧美、东南亚等地区。
(2)参加行业展会:积极参加国内外热处理行业展会,展示企业实力,提升品牌知名度。
三、存在的问题及改进措施1. 存在问题(1)部分企业质量管理意识薄弱,质量管理体系不完善。
(2)热处理工艺水平有待提高,部分企业仍采用传统热处理工艺。
(3)市场竞争激烈,企业面临成本压力。
2. 改进措施(1)加强质量管理,完善质量管理体系,提高产品质量。
(2)加大技术研发投入,提高热处理工艺水平。
(3)优化生产流程,降低生产成本,提高企业竞争力。
四、展望展望未来,我国热处理行业将继续秉持“质量第一”的原则,以技术创新为动力,以市场为导向,不断提升产品质量,为我国制造业的发展贡献力量。
总之,本年度我国热处理专业在技术创新、质量管理、市场拓展等方面取得了显著成果。
热处理年度工作总结(2篇)
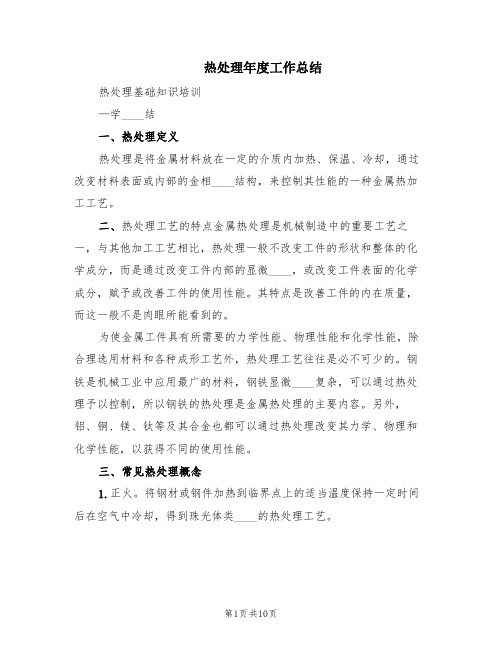
热处理年度工作总结热处理基础知识培训—学____结一、热处理定义热处理是将金属材料放在一定的介质内加热、保温、冷却,通过改变材料表面或内部的金相____结构,来控制其性能的一种金属热加工工艺。
二、热处理工艺的特点金属热处理是机械制造中的重要工艺之一,与其他加工工艺相比,热处理一般不改变工件的形状和整体的化学成分,而是通过改变工件内部的显微____,或改变工件表面的化学成分,赋予或改善工件的使用性能。
其特点是改善工件的内在质量,而这一般不是肉眼所能看到的。
为使金属工件具有所需要的力学性能、物理性能和化学性能,除合理选用材料和各种成形工艺外,热处理工艺往往是必不可少的。
钢铁是机械工业中应用最广的材料,钢铁显微____复杂,可以通过热处理予以控制,所以钢铁的热处理是金属热处理的主要内容。
另外,铝、铜、镁、钛等及其合金也都可以通过热处理改变其力学、物理和化学性能,以获得不同的使用性能。
三、常见热处理概念1.正火。
将钢材或钢件加热到临界点上的适当温度保持一定时间后在空气中冷却,得到珠光体类____的热处理工艺。
2.退火。
将亚共析钢工件加热至20—____度,保温一段时间后,随炉缓慢冷却(或埋在砂中或石灰中冷却)至____度以下在空气中冷却的热处理工艺。
3.固溶热处理。
将合金加热至高温单相区恒温保持,使过剩相充分溶解到固溶体中,然后快速冷却,以得到过饱和固溶体的热处理工艺。
4.时效。
合金经固溶热处理或冷塑性形变后,在室温放置或稍高于室温保持时,其性能随时间而变化的现象。
5.固溶处理。
使合金中各种相充分溶解,强化固溶体并提高韧性及抗蚀性能,消除应力与软化,以便继续加工成型。
6.时效处理。
在强化相析出的温度加热并保温,使强化相沉淀析出,得以硬化,提高强度。
7.淬火。
将钢奥氏体化后以适当的冷却速度冷却,使工件在横截面内全部或一定的范围内发生马氏体等不稳定____结构转变的热处理工艺。
8.回火。
将经过淬火的工件加热到临界点以下的适当温度保持一定时间,随后用符合要求的方法冷却,以获得所需要的____和性能的热处理工艺。
公共基础知识热处理工艺基础知识概述

《热处理工艺基础知识概述》一、引言热处理工艺作为材料加工领域中的一项关键技术,在提高材料性能、延长使用寿命、改善加工工艺等方面发挥着至关重要的作用。
从古代的简单金属加工到现代的高科技材料处理,热处理工艺经历了漫长的发展历程。
本文将对热处理工艺的基础知识进行全面综合的概述,包括基本概念、核心理论、发展历程、重要实践以及未来趋势等方面,旨在为读者提供一个系统而深入的了解。
二、基本概念1. 定义热处理是指将材料加热到一定温度,保温一段时间,然后以适当的速度冷却,以改变材料的组织结构和性能的工艺过程。
通过热处理,可以改善材料的硬度、强度、韧性、耐磨性、耐腐蚀性等性能,满足不同工程应用的要求。
2. 分类热处理工艺主要分为普通热处理和表面热处理两大类。
普通热处理包括退火、正火、淬火和回火;表面热处理包括表面淬火和化学热处理。
(1)退火:将材料加热到适当温度,保温一段时间,然后缓慢冷却。
退火的目的是降低材料的硬度,改善切削加工性能,消除残余应力,稳定尺寸等。
(2)正火:将材料加热到临界温度以上,保温一段时间,然后在空气中冷却。
正火的目的与退火相似,但冷却速度较快,得到的组织比退火的更细,强度和硬度也较高。
(3)淬火:将材料加热到临界温度以上,保温一段时间,然后快速冷却。
淬火的目的是提高材料的硬度和强度,但淬火后材料的脆性增加,需要进行回火处理。
(4)回火:将淬火后的材料加热到适当温度,保温一段时间,然后冷却。
回火的目的是降低材料的脆性,提高韧性和塑性,稳定组织和尺寸。
(5)表面淬火:通过快速加热材料表面,使其达到淬火温度,然后迅速冷却,使表面获得高硬度,而心部仍保持较好的韧性。
(6)化学热处理:将材料置于一定的化学介质中加热,使介质中的某些元素渗入材料表面,改变材料的化学成分和组织结构,从而提高材料的表面性能。
三、核心理论1. 相变理论热处理过程中,材料的组织结构会发生相变。
相变是指物质从一种相转变为另一种相的过程。
热处理实践心得体会

一、引言热处理是金属加工中一项重要的工艺,通过对金属工件进行加热、保温、冷却等过程,使其组织结构发生变化,从而提高材料的性能。
在我国制造业中,热处理工艺得到了广泛的应用,对于提高产品质量、延长使用寿命具有重要意义。
在本次热处理实践过程中,我深刻体会到了热处理工艺的重要性,以下是我对热处理实践的心得体会。
二、热处理实践过程1. 热处理工艺原理热处理工艺主要包括退火、正火、淬火、回火等几种基本工艺。
退火是将金属工件加热到一定温度,保温一段时间,然后缓慢冷却,以消除内应力、细化晶粒、改善组织结构。
正火是在较高温度下加热,然后缓慢冷却,使金属工件获得一定的硬度和韧性。
淬火是将金属工件加热到一定温度,然后迅速冷却,使其获得较高的硬度和耐磨性。
回火是在淬火后对工件进行加热,以降低硬度,提高韧性。
2. 热处理实践步骤(1)工件准备:首先对工件进行表面处理,如清洗、去油等,确保工件表面干净、无杂质。
(2)装炉:将工件装入炉内,注意工件之间要保持一定距离,避免相互接触。
(3)加热:根据工件材质和热处理要求,设定合适的加热温度和时间。
加热过程中,要控制炉内温度均匀,防止工件产生热应力。
(4)保温:加热到规定温度后,保持一定时间,使工件内部温度均匀。
(5)冷却:根据工件材质和热处理要求,选择合适的冷却方式,如水冷、油冷、空气冷却等。
(6)检验:热处理完成后,对工件进行外观检查、硬度测试、金相分析等,以确保热处理质量。
三、热处理实践心得体会1. 热处理工艺的重要性通过本次热处理实践,我深刻认识到热处理工艺在金属加工中的重要性。
热处理可以改善金属材料的性能,提高其强度、硬度、耐磨性、耐腐蚀性等,从而延长工件的使用寿命,降低生产成本。
2. 热处理工艺的复杂性热处理工艺涉及多个因素,如加热温度、保温时间、冷却速度等。
在实际操作中,要充分考虑这些因素,确保热处理质量。
此外,热处理工艺对设备、人员素质要求较高,需要不断学习和积累经验。
热处理技师工作总结5篇
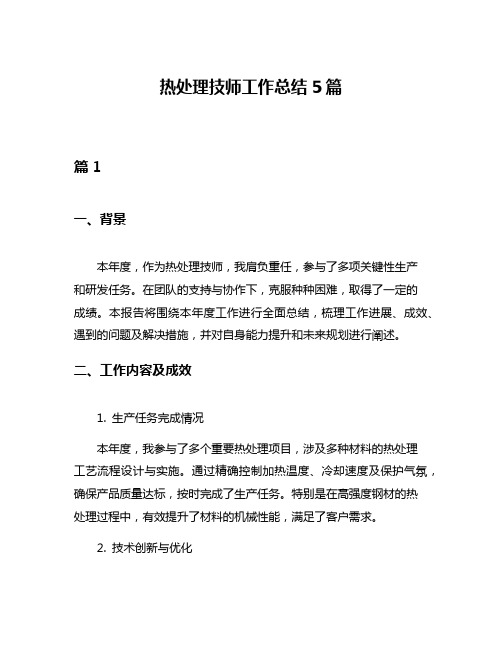
热处理技师工作总结5篇篇1一、背景本年度,作为热处理技师,我肩负重任,参与了多项关键性生产和研发任务。
在团队的支持与协作下,克服种种困难,取得了一定的成绩。
本报告将围绕本年度工作进行全面总结,梳理工作进展、成效、遇到的问题及解决措施,并对自身能力提升和未来规划进行阐述。
二、工作内容及成效1. 生产任务完成情况本年度,我参与了多个重要热处理项目,涉及多种材料的热处理工艺流程设计与实施。
通过精确控制加热温度、冷却速度及保护气氛,确保产品质量达标,按时完成了生产任务。
特别是在高强度钢材的热处理过程中,有效提升了材料的机械性能,满足了客户需求。
2. 技术创新与优化(1)针对传统热处理工艺能耗较高的问题,开展了节能技术研究与应用。
通过优化加热设备功率配置和改进热传导介质,实现了能源消耗降低XX%。
(2)针对复杂零件的热处理变形问题,进行了工艺参数精细化调整与新材料应用研究,成功降低了产品变形率,提高了尺寸精度。
(3)参与了热处理数据库的建设与完善工作,通过收集、整理与分析大量数据,为工艺优化提供了有力支持。
3. 质量管理与提升严格执行质量管理体系要求,参与制定和完善热处理相关作业指导书和质量控制标准。
通过定期的质量检查和数据分析,及时发现并解决了多起潜在质量问题。
同时,强化了与检测部门的沟通协作,确保产品质量的持续改进与提升。
4. 设备维护与管理负责热处理设备的日常运行维护与管理,制定设备维修保养计划并严格实施。
对设备故障进行快速诊断与修复,确保生产线的稳定运行。
积极参与设备的选型与采购工作,提出合理化的改进建议。
三、遇到的问题及解决措施1. 问题一:新材料应用过程中热处理工艺不稳定。
解决措施:组织技术攻关小组,对新材料的热处理特性进行深入研究和试验验证,优化工艺参数,确保稳定生产。
2. 问题二:热处理过程中安全隐患较多。
解决措施:加强安全培训,提高员工安全意识;完善安全操作规程和应急处置预案;加强设备安全检查与维护工作。
金属热处理原理及工艺总结_整理版
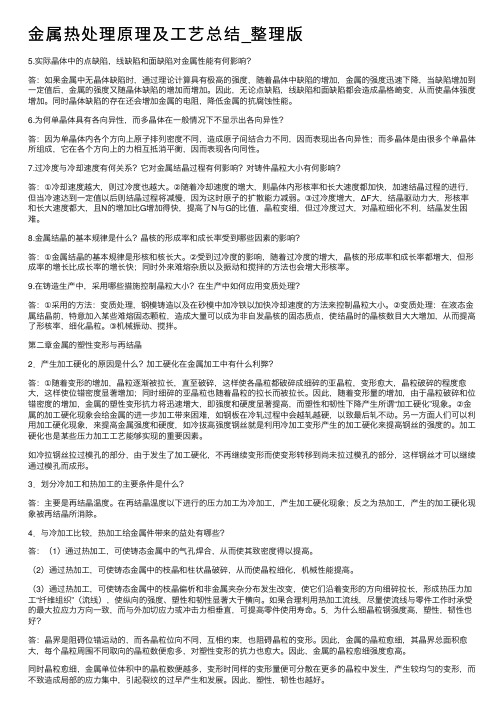
⾦属热处理原理及⼯艺总结_整理版5.实际晶体中的点缺陷,线缺陷和⾯缺陷对⾦属性能有何影响?答:如果⾦属中⽆晶体缺陷时,通过理论计算具有极⾼的强度,随着晶体中缺陷的增加,⾦属的强度迅速下降,当缺陷增加到⼀定值后,⾦属的强度⼜随晶体缺陷的增加⽽增加。
因此,⽆论点缺陷,线缺陷和⾯缺陷都会造成晶格崎变,从⽽使晶体强度增加。
同时晶体缺陷的存在还会增加⾦属的电阻,降低⾦属的抗腐蚀性能。
6.为何单晶体具有各向异性,⽽多晶体在⼀般情况下不显⽰出各向异性?答:因为单晶体内各个⽅向上原⼦排列密度不同,造成原⼦间结合⼒不同,因⽽表现出各向异性;⽽多晶体是由很多个单晶体所组成,它在各个⽅向上的⼒相互抵消平衡,因⽽表现各向同性。
7.过冷度与冷却速度有何关系?它对⾦属结晶过程有何影响?对铸件晶粒⼤⼩有何影响?答:①冷却速度越⼤,则过冷度也越⼤。
②随着冷却速度的增⼤,则晶体内形核率和长⼤速度都加快,加速结晶过程的进⾏,但当冷速达到⼀定值以后则结晶过程将减慢,因为这时原⼦的扩散能⼒减弱。
③过冷度增⼤,ΔF⼤,结晶驱动⼒⼤,形核率和长⼤速度都⼤,且N的增加⽐G增加得快,提⾼了N与G的⽐值,晶粒变细,但过冷度过⼤,对晶粒细化不利,结晶发⽣困难。
8.⾦属结晶的基本规律是什么?晶核的形成率和成长率受到哪些因素的影响?答:①⾦属结晶的基本规律是形核和核长⼤。
②受到过冷度的影响,随着过冷度的增⼤,晶核的形成率和成长率都增⼤,但形成率的增长⽐成长率的增长快;同时外来难熔杂质以及振动和搅拌的⽅法也会增⼤形核率。
9.在铸造⽣产中,采⽤哪些措施控制晶粒⼤⼩?在⽣产中如何应⽤变质处理?答:①采⽤的⽅法:变质处理,钢模铸造以及在砂模中加冷铁以加快冷却速度的⽅法来控制晶粒⼤⼩。
②变质处理:在液态⾦属结晶前,特意加⼊某些难熔固态颗粒,造成⼤量可以成为⾮⾃发晶核的固态质点,使结晶时的晶核数⽬⼤⼤增加,从⽽提⾼了形核率,细化晶粒。
③机械振动、搅拌。
第⼆章⾦属的塑性变形与再结晶2.产⽣加⼯硬化的原因是什么?加⼯硬化在⾦属加⼯中有什么利弊?答:①随着变形的增加,晶粒逐渐被拉长,直⾄破碎,这样使各晶粒都破碎成细碎的亚晶粒,变形愈⼤,晶粒破碎的程度愈⼤,这样使位错密度显著增加;同时细碎的亚晶粒也随着晶粒的拉长⽽被拉长。
铸造热处理实习报告

一、实习背景为了更好地了解铸造工艺和热处理技术,提高自己的专业技能,我于20xx年xx月至20xx年xx月在XX铸造厂进行了为期一个月的实习。
实习期间,我深入了解了铸造工艺流程、热处理工艺及其在生产中的应用,收获颇丰。
二、实习内容1. 铸造工艺流程(1)原材料准备:了解铸造用金属材料的种类、性能及选用原则。
(2)造型与造芯:学习造型、造芯的方法、工艺要求及注意事项。
(3)熔炼与浇注:了解熔炼设备的种类、熔炼工艺及浇注方法。
(4)铸件清理:学习铸件清理的方法、工艺要求及注意事项。
2. 热处理工艺(1)热处理原理:了解热处理的基本原理、热处理过程及其对材料性能的影响。
(2)热处理工艺:学习各种热处理工艺(退火、正火、淬火、回火等)的工艺参数、操作方法及注意事项。
(3)热处理设备:了解热处理设备的种类、工作原理及操作方法。
(4)热处理缺陷分析:学习热处理缺陷的产生原因、预防措施及处理方法。
三、实习过程1. 铸造工艺实习(1)原材料准备:实习期间,我学习了铸造用金属材料的种类、性能及选用原则,了解了常用金属材料的化学成分、力学性能等。
(2)造型与造芯:在师傅的指导下,我学习了造型、造芯的方法,掌握了砂箱、砂芯的制备工艺,了解了不同铸造工艺的特点。
(3)熔炼与浇注:实习期间,我参观了熔炼车间,了解了熔炼设备的种类、熔炼工艺及浇注方法,掌握了熔炼过程中的安全操作规程。
(4)铸件清理:在师傅的带领下,我学习了铸件清理的方法,了解了清理过程中的注意事项,掌握了清理设备的使用方法。
2. 热处理工艺实习(1)热处理原理:在实习期间,我学习了热处理的基本原理,了解了热处理过程对材料性能的影响。
(2)热处理工艺:在师傅的指导下,我学习了各种热处理工艺的工艺参数、操作方法及注意事项,掌握了热处理工艺的操作技能。
(3)热处理设备:实习期间,我参观了热处理车间,了解了热处理设备的种类、工作原理及操作方法,掌握了热处理设备的使用方法。
热处理报告
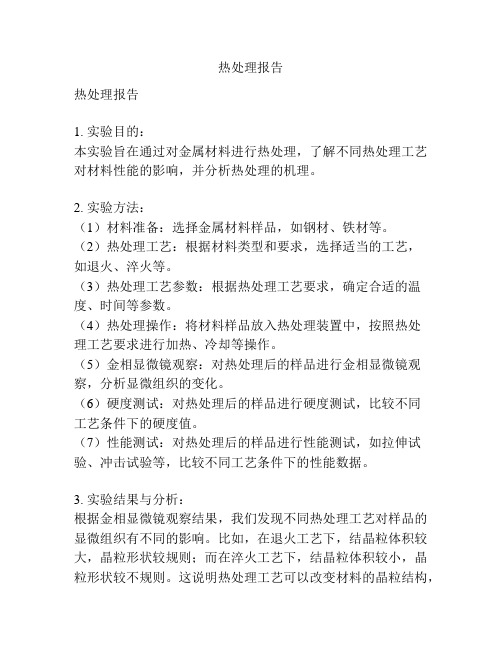
热处理报告热处理报告1. 实验目的:本实验旨在通过对金属材料进行热处理,了解不同热处理工艺对材料性能的影响,并分析热处理的机理。
2. 实验方法:(1)材料准备:选择金属材料样品,如钢材、铁材等。
(2)热处理工艺:根据材料类型和要求,选择适当的工艺,如退火、淬火等。
(3)热处理工艺参数:根据热处理工艺要求,确定合适的温度、时间等参数。
(4)热处理操作:将材料样品放入热处理装置中,按照热处理工艺要求进行加热、冷却等操作。
(5)金相显微镜观察:对热处理后的样品进行金相显微镜观察,分析显微组织的变化。
(6)硬度测试:对热处理后的样品进行硬度测试,比较不同工艺条件下的硬度值。
(7)性能测试:对热处理后的样品进行性能测试,如拉伸试验、冲击试验等,比较不同工艺条件下的性能数据。
3. 实验结果与分析:根据金相显微镜观察结果,我们发现不同热处理工艺对样品的显微组织有不同的影响。
比如,在退火工艺下,结晶粒体积较大,晶粒形状较规则;而在淬火工艺下,结晶粒体积较小,晶粒形状较不规则。
这说明热处理工艺可以改变材料的晶粒结构,进而影响材料的性能。
从硬度测试结果来看,通常情况下,淬火工艺可以提高材料的硬度,而退火工艺会使材料变软。
这是因为淬火可以形成由高硬度的马氏体组成的组织结构,而退火可以通过晶粒长大和松弛应力来降低硬度。
从性能测试结果来看,不同热处理工艺对材料的性能有着显著的影响。
例如,在拉伸试验中,淬火工艺可以提高材料的强度和硬度,但降低其延展性;而退火工艺则可以提高材料的延展性,但降低其强度和硬度。
这表明热处理工艺的选择应根据具体需求来进行。
4. 实验结论:通过本实验,我们得出以下结论:(1)热处理工艺可以显著改变金属材料的显微组织和性能。
(2)不同热处理工艺对材料的影响具有针对性,应根据具体需求来选择适当的工艺。
(3)热处理工艺的参数(如温度、时间等)对材料性能的影响也很大,需要进行优化和调整。
5. 实验总结与改进:本实验通过对金属材料的热处理,深入了解了热处理工艺对材料性能的影响,并对热处理的机理有了一定的了解。
热处理基础知识总结

热处理基础知识总结热处理是指材料在固态下,通过加热、保温和冷却的手段,以获得预期组织和性能的一种金属热加工工艺。
一、热处理1、正火:将钢材或钢件加热到临界点AC3或ACM以上的适当温度保持一定时间后在空气中冷却,得到珠光体类组织的热处理工艺。
2、退火:将亚共析钢工件加热至AC3以上20—40度,保温一段时间后,随炉缓慢冷却(或埋在砂中或石灰中冷却)至500度以下在空气中冷却的热处理工艺。
3、固溶热处理:将合金加热至高温单相区恒温保持,使过剩相充分溶解到固溶体中,然后快速冷却,以得到过饱和固溶体的热处理工艺。
4、时效:合金经固溶热处理或冷塑性形变后,在室温放置或稍高于室温保持时,其性能随时间而变化的现象。
5、固溶处理:使合金中各种相充分溶解,强化固溶体并提高韧性及抗蚀性能,消除应力与软化,以便继续加工成型。
6、时效处理:在强化相析出的温度加热并保温,使强化相沉淀析出,得以硬化,提高强度。
7、淬火:将钢奥氏体化后以适当的冷却速度冷却,使工件在横截面内全部或一定的范围内发生马氏体等不稳定组织结构转变的热处理工艺。
8、回火:将经过淬火的工件加热到临界点AC1以下的适当温度保持一定时间,随后用符合要求的方法冷却,以获得所需要的组织和性能的热处理工艺。
9、钢的碳氮共渗:碳氮共渗是向钢的表层同时渗入碳和氮的过程。
习惯上碳氮共渗又称为氰化,以中温气体碳氮共渗和低温气体碳氮共渗(即气体软氮化)应用较为广泛。
中温气体碳氮共渗的主要目的是提高钢的硬度,耐磨性和疲劳强度。
低温气体碳氮共渗以渗氮为主,其主要目的是提高钢的耐磨性和抗咬合性。
10、调质处理(quenching and tempering):一般习惯将淬火加高温回火相结合的热处理称为调质处理。
调质处理广泛应用于各种重要的结构零件,特别是那些在交变负荷下工作的连杆、螺栓、齿轮及轴类等。
调质处理后得到回火索氏体组织,它的机械性能均比相同硬度的正火索氏体组织更优。
它的硬度取决于高温回火温度并与钢的回火稳定性和工件截面尺寸有关,一般在HB200—350之间。
各种热处理工艺造成变形的原因总结

各种热处理工艺造成变形的原因总结引言:热处理工艺是一种常见的金属加工方法,它通过对金属材料进行加热和冷却来改变其结构和性能。
然而,热处理过程中往往会导致材料发生变形,这对于一些精密零件的加工和制造带来一定的困扰。
本文将从各种热处理工艺的角度,总结造成变形的原因,并探讨相应的解决方法。
一、淬火过程中的变形原因淬火是一种通过快速冷却来使金属材料达到高强度和硬度的热处理工艺。
然而,淬火过程中常常会出现变形现象。
造成淬火变形的主要原因有以下几点:1. 冷却速度不均匀:淬火过程中,材料表面和内部的冷却速度不一致,导致应力不均匀分布,从而引起变形。
2. 材料内部组织不均匀:金属材料内部的组织不均匀,如晶粒尺寸、相含量等差异,会导致淬火时的收缩和变形不一致。
3. 冷却介质选择不当:不同的冷却介质对材料的冷却速度有不同的影响,选择不当可能导致应力集中和变形。
解决方法:针对淬火过程中的变形问题,可以采取以下措施:1. 控制冷却速度:通过优化冷却介质的选择和控制冷却速度,使材料表面和内部的冷却速度尽可能一致,减少应力的不均匀分布。
2. 优化材料组织:通过调整材料的化学成分和热处理工艺,使材料内部的组织更加均匀,减少淬火时的收缩和变形差异。
3. 采用适当的淬火工艺:根据材料的特性和要求,选择适当的淬火工艺,控制冷却速度和温度,减少变形的发生。
二、退火过程中的变形原因退火是一种通过加热和缓慢冷却来改善材料的性能和结构的热处理工艺。
然而,退火过程中同样存在变形的问题。
造成退火变形的主要原因有以下几点:1. 温度不均匀:退火过程中,材料的温度分布不均匀,导致应力分布不均匀,从而引起变形。
2. 冷却速度过快:退火结束后,如果冷却速度过快,会导致材料内部的残余应力无法得到充分释放,从而引起变形。
3. 材料内部缺陷:金属材料内部存在各种缺陷,如气孔、夹杂物等,这些缺陷在退火过程中会扩散和移动,导致变形的发生。
解决方法:针对退火过程中的变形问题,可以采取以下措施:1. 控制温度均匀性:通过合理设计加热设备和工艺参数,确保材料的温度分布均匀,减少应力的不均匀分布。
热处理个人工作总结9篇

热处理个人工作总结9篇第1篇示例:热处理是一种重要的金属材料加工工艺,我在这个岗位上工作了一段时间,通过不断的学习和实践,我对热处理工艺有了更深刻的了解,也积累了一定的经验。
在这里,我总结了一下我的工作情况,希望对自己的工作有一个清晰的认识,也希望我的总结能够对热处理工艺有所帮助。
我在热处理工作中积累了丰富的经验。
热处理是一项技术含量较高的工作,所以我在工作中注重积累经验,总结不同工件的热处理特点和要求,不断总结和归纳出适合不同材料的热处理工艺和方法,提高了工作的效率和质量。
通过对不同工件的热处理实践,我也学会了如何根据工件的材料、形状、尺寸等特点来选择合适的热处理工艺,保证工件的质量和性能。
我在工作中不断学习和提高自己的技能。
热处理工艺是一个不断发展和变化的领域,新的材料、新的工艺不断涌现,所以我始终保持对相关知识的学习和研究。
通过参加热处理相关的培训和学习,我不仅了解了最新的热处理工艺和设备,也学到了新的热处理方法和技巧,为自己的工作注入了新的动力和活力。
我还和同事们一起探讨和交流热处理的经验和技巧,相互学习,共同进步。
我在工作中非常重视质量和安全。
热处理工艺是一项关乎产品质量和安全的工作,所以在我工作中,我始终把质量和安全放在首位,严格按照工艺要求和作业规程进行操作,确保热处理工艺的稳定性和可靠性,杜绝产品质量问题和安全事故的发生。
我也积极参与公司的质量管理和安全培训,提高自己的专业知识和技能,做到知识更新。
我在工作中注重团队合作和沟通。
热处理工艺需要多个岗位之间的协作和配合,所以我在工作中注重团队合作和沟通,和生产、技术、质检等部门紧密配合,共同解决工艺中出现的问题,确保热处理工艺的顺利进行。
我也主动参与部门的讨论和交流,表达自己的看法和建议,为工艺的改进和优化提供有益的建议和决策。
热处理工艺是一个细致和重要的工作,我在这个岗位上工作以来,通过努力学习和实践,积累了丰富的经验,提高了自己的技能,也注重质量和安全,注重团队合作和沟通。
热处理原理与工艺(自总结)

1影响对流换热系数的因素(1)流体运动的情况:自然对流和强迫对流(2)流体的性质:热导率、热容、密度、粘度(3)工件的形状及在炉内的位置2影响热导率的因素(1)碳元素、合金元素含量越多,热导率越小(2)物相:奥氏体<淬火马氏体<回火马氏体<珠光体(3)温度:对于纯铁、碳钢,温度越高,热导率越小3随炉加热、到温入炉、高温入炉、高温入炉到温出炉、预热加热(1)随炉加热:工件装入炉中后,随着炉子升温而加热,直至所需加热温度。
(2)到温入炉:先把炉子温度升高到工件要求的加热温度,再把工件放入炉内加热。
(3)高温入炉:先把炉子温度升高到高于工件要求的加热温度,再把工件放入炉内直至达到所需温度(4)预热加热:工件先在已升温至较低温度的炉子中加热,到温后再转移至预定工件加热温度的炉中加热至工件所要求的温度。
4铁加热时的氧化反应小于570℃加热时,氧化产物为四氧化三铁;大于570℃加热时,氧化产物为氧化亚铁。
5内氧化:氧沿晶界或其他通道向内扩散,与晶界附近的Si、Mo等元素结合成氧化物的现象。
(原因:SiO2、MoO的分解压小于FeO的分解压,故Si、Mo先被氧化。
)6脱碳:钢在加热时,钢中的碳与气氛作用,使钢表面失去一部分碳,含碳量降低的现象。
碳势:表征炉气对钢表层增碳或脱碳的能力。
纯铁在一定温度下于加热炉气中加热时达到既不增碳也不脱碳并与炉气保持平衡时表面的含碳量。
7炉气碳势测量方法(炉气中CO、H2、H2O、CO2、CH4、O2有定量关系,CO、H2含量是恒定的,知道其余4中气体任一种含量即可知所有气体含量,从而可以得到碳势。
)(1)实际碳势曲线:直接测定不同温度时炉气成分及与之平衡的钢的含碳量。
(2)红外线CO2分析仪:测定炉气中CO2含量(CO2含量越高,碳势越低)(3)露点仪:测定炉气中H20的含量(H2O含量越高,碳势越低)(4)氧探头:测定炉气中氧含量(氧分压)(电势越高,碳势越高)8脱碳过程:①脱碳反应②碳由内部向表面扩散钢在不同炉气碳势中脱碳后的组织分析半脱碳层:脱碳层组织自表面至中心,由铁素体加珠光体组织过渡到珠光体,再至原始含碳量的缓冷组织,这种脱碳层为半脱碳层。
热处理实训总结

第四阶段是对板厚为8mm试样热处理和未热处理的进行维式硬度测试,主要目的是通过硬度测试试验获得材料微观结构的有关信息。维式硬度计原理图:
采用两相对面间夹角α为136°的金刚石正四棱锥体压头,在试验力作用下压入试样表面,保持规定时间后,卸除试验力,测量试样表面压痕对角线长度,试验力除以压痕表面积的商就是维氏硬度值。即HV=0.1891F/d2。
压痕如图所:
实验结果:
未处理的母材硬度值128热影响区硬度值128焊缝硬度值153
热处理的母材硬度值126热影响区硬度值127焊缝硬度值143
通过此次实训加深对课堂所学理论的理解和掌握,达到根据零件的工作条件正确选择材料及正确制定实施热处理工艺的目的,特安排了本次综合实践。《金属材料与热处理》与《电弧焊基础》是在若干基础科学的生产实践基础上发展起来的一门科学,但它的一些主要理论是通过实践并总结了实践的规律而建立起来的。实践不仅通过自己的实践来验证课堂的理论知识,加深理解、理论联系实际,而且也可以培养观察问题、发现问题、分析问题和解决问题的能力。这次实训给我们每个人一个很好的机会学习那些书本上不能学到的知识,通过我们自己的动手操作,还查找各种图书资料以及到网上搜寻相关资料,使我们的知识得以巩固和完善,不仅增长了我们的见识,而且对生产操作有了一定的直观认识。巩固已学的专业基础课和部分专业课程相关的知识,我们了解了更多的专业技术知识及应用状况,拓展了专业知识面,“纸上得来终觉浅,绝知此事需躬行”通过这次到实训让我了解了很多。真的,有许多东西看似已经懂了,但真正到了实际却又是另一种情况。有时自己认为自己已掌握的东西可能仅是一些肤浅的表面或总体的一个方面,甚至有时是错误的认识,而如果没有实地实践,我们是无法发现这些问题的。
维氏硬度的表示方法是:硬度值、符号HV、试验力、试验力保持时间(10-15s不标)。如640HV30表示在试验力为294.2N下保持10-15s测得的维氏硬度值为640。又如300HV0.1表示在试验力为0.9807N下保持10-15s测得的显微维氏硬度值为300。注意硬度符号后试验力单位为千克力(kgf)。
- 1、下载文档前请自行甄别文档内容的完整性,平台不提供额外的编辑、内容补充、找答案等附加服务。
- 2、"仅部分预览"的文档,不可在线预览部分如存在完整性等问题,可反馈申请退款(可完整预览的文档不适用该条件!)。
- 3、如文档侵犯您的权益,请联系客服反馈,我们会尽快为您处理(人工客服工作时间:9:00-18:30)。
1.退火
将钢件加热到Ac3+30~50度或Ac1+30~50度或Ac1以下的温度后,一般随炉温缓慢冷却。
2.细化晶粒,改善力学性能,为下一步工序做准备
3.消除冷、热加工所产生的内应力。
应用要点:1.适用于合金结构钢、碳素工具钢、、高速钢的锻件、焊接件以及供应状态不合格的原材料
2.一般在毛坯状态进行退火。
2.正火
将钢件加热到Ac3以上30~50度,保温后以稍大于退火的冷却速度冷却。
目的:1.降低硬度,提高塑性,改善切削加工与性能
2.细化晶粒,改善力学性能,为下一步工序做准备
3.消除冷、热加工所产生的内应力。
应用要点:正火通常作为锻件、焊接件以及渗碳零件的预先热处理工序。
对于性能要求不高的低碳的和中碳的及件,也可作为最后热处理。
对于一般中、高合金钢,空冷可导致完全或局部淬火,因此不能作为最后热处理工序。
3.淬火
将钢件加热到相变温度Ac3或Ac1以上,保温一段时间,然后在水、硝盐、油、或空气中快速冷却。
目的:淬火一般是为了得到高硬度的,有时对某些高合金钢(如不锈钢、耐磨钢)淬火时,则是为了得到单一均匀的,以提高耐磨性和耐蚀性。
应用要点:1.一般用于含碳量大于百分之零点三的碳钢和合金钢;2.淬火能充分发挥钢的强度和耐磨性潜力,但同时会造成很大的内应力,降低钢的塑性和冲击韧度,故要进行回火以得到较好的综合力学性能。
4.回火
将淬火后的钢件重新加热到Ac1以下某一温度,经保温后,于空气或油、热水、水中冷却。
目的:1.降低或消除淬火后的内应力,减少工件的变形和开裂;2.调整硬度,提高塑性和韧性,获得工作所要求的力学性能;3.稳定工件尺寸。
应用要点:1.保持钢在淬火后的高硬度和耐磨性时用低温回火;在保持一定韧度的条件下提高钢的弹性和屈服强度时用中温回火;以保持高的冲击韧度和塑性为主,又有足够的强度时用高温回火;2.一般钢尽量避免在230~280度、不锈钢在400~450度之间回火,因为这时会产生一次回火脆性。
5.调质
淬火后高温回火称调质,即将钢件加热到比淬火时高10~20度的温度,保温后进行淬火,然后在400~720度的温度下进行回火。
目的:1.改善切削加工性能,提高加工表面光洁程度;2.减小淬火时的变形和开裂;3.获得良好的综合力学性能。
应用要点:1.适用于淬透性较高的合金结构钢、和高速钢;2.不仅可以作为各种较为重要结构的最后热处理,而且还可以作为某些紧密零件,如丝杠等的预先热处理,以减小变形。
6.时效
将钢件加热到80~200度,保温5~20小时或更长时间,然后随炉取出在空气中冷却。
目的:1.稳定钢件淬火后的组织,减小存放或使用期间的变形;2.减轻淬火以及磨削加工后的内应力,稳定形状和尺寸。
应用要点:1.适用于经淬火后的各钢种;2.常用于要求形状不再发生变化的紧密工件,如紧密丝杠、测量工具、床身机箱等。
7.冷处理
将淬火后的钢件,在低温介质(如干冰、液氮)中冷却到-60~-80度或更低,温度均匀一致后取出均温到室温。
目的:1.使淬火钢件内的全部或大部转换为马氏体,从而提高钢件的硬度、强度、耐磨性和疲劳极限;2.稳定钢的组织,以稳定钢件的形状和尺寸。
应用要点:1.钢件淬火后应立即进行冷处理,然后再经低温回火,以消除低温冷却时的内应力;2.冷处理主要适用于合金钢制的紧密刀具、量具和紧密零件。
8.火焰加热表面淬火
用氧-乙炔混合气体燃烧的火焰,喷射到钢件表面上,快速加热,当达到淬火温度后立即喷水冷却。
目的:提高钢件表面硬度、耐磨性及疲劳强度,心部仍保持韧性状态。
应用要点:1.多用于中碳钢制件,一般淬透层深度为2~6mm;2.适用于单件或小批量生产的大型工件和需要局部淬火的工件。
9.感应加热表面淬火
将钢件放入感应器中,使钢件表层产生,在极短的时间内加热到淬火温度,然后喷水冷却。
目的:提高钢件表面硬度、耐磨性及疲劳强度,心部保持韧性状态。
应用要点:1.多用于中碳钢和中堂合金结构钢制件;2.由于肌肤效应,高频感应淬火淬透层一般为1~
2mm,一般为3~5mm,高频淬火一般大于10mm.
10.渗碳
将钢件放入渗碳介质中,加热至900~950度并保温,使钢件便面获得一定浓度和深度的渗碳层。
目的:提高钢件表面硬度、耐磨性及疲劳强度,心部仍然保持韧性状态。
应用要点:1.用于含碳量为0.15%~0.25%的低碳钢和制件,一般渗碳层深度为0.5~2.5mm;2.渗碳后必须进行淬火,使表面得到马氏体,才能实现渗碳的目的。