浅谈CRTSⅡ型无砟轨道板制造技术及工艺解析
浅谈CRTSⅡ型板式无砟轨道工艺性试验

石武客专采用 C R T S I I 型板式无砟轨道技术 , 其 轨道结构主要 由轨道板 、 乳化沥青砂浆充填层 、 混凝 土底座及钢轨扣件等构成 。根据要求 , 为了保证施
轨道 板精调一 水 泥乳 化沥青 砂浆 灌 注一 养 护一 揭 板
验证。
2 . 2 底座 板 施工
套上锚杆并用翼型螺帽固定 , 待轨道板粗铺后 , 圆锥 体便可拆除, 但锚杆须在 C A砂浆灌浆后 , 方可拆除 同时将压紧装置拆除。
2 . 4 轨道 板粗 铺 底 座板砼 强 度 大于 1 5 MP a , 且 砼 浇 注 时 间大 于
1 ) 采用Leabharlann 1 8 a 作为直线段侧模支立 , 标准钢模板
2 . 2 . 1 准备 工作
工现场无砟轨道施工质量 , 正式施工 前要进行无砟 轨道工艺性试验 , 只有各项试验结果验收符合要求 ,
才能正式进行现场作业。
试验段布置如图 1 所 示, 将 钢筋加工厂 5 0 m X 8 . 1 m 的地 面 全 部 硬 化 来 模 拟 梁 面, 硬 化 厚 度 1 5 0 m m, 混 凝 土 表 面 平 整 度 要 求: 3 m m / 4 m 、
试验段基底硬化 基底清理一两布一膜 、 高强 度挤塑板铺设 安装底座板模板 浇筑底座板砼一 砼养生一定位锥埋设 、 G R P点设置一轨道板粗铺_ +
用水润湿土工布以利于将土工布吸附在聚乙烯薄膜
上 。两 布 一膜施 工注 意事项 :
l 0 0
甘
肃
科
技
第2 9 卷
( 1 ) 铺 设应平 整 、 无皱褶 且无破损 , 如 发 现 破
在一缘设有凹槽或孔 , 利用它可借助夹具将圆锥体
CRTSII型板式无砟轨道施工技术

施工效率、更低的施工成本和更好的稳定性,具有较大的竞争优势。
03
推广价值
CRTSII型板式无砟轨道施工技术对于提高我国高速铁路和城市轨道交通
的建设水平、推动相关产业的发展具有重要意义,值得在更广泛范围内
推广应用。
对未来研究的建议与展望
1 2
技术创新
进一步研究CRTSII型板式无砟轨道施工技术的优 化方案,提高施工效率和质量稳定性。
保证混凝土的性能和耐久性。
技术创新与优势分析
总结词
创新性、优势明显
详细描述
CRTSII型板式无砟轨道施工技术不仅继承了传统无砟 轨道施工技术的优点,如高平顺性、高稳定性、低维护 成本等,还在轨道板预制、精调、混凝土浇筑与养护等 方面进行了技术创新。这些创新使得CRTSII型板式无 砟轨道施工技术具有更高的施工效率、更低的施工成本 、更好的结构性能和更高的耐久性等优势。与其他类型 的无砟轨道施工技术相比,CRTSII型板式无砟轨道施 工技术在适用范围、施工效果、经济效益等方面表现出 了明显的优势。
社会效益
项目建成后将极大改善区域交 通条件,促进经济发展和人员
流动
06
结论与展望
技术总结
施工工艺
CRTSII型板式无砟轨道施工工艺包括底座板施工、轨道板 预制、轨道板调整、水泥乳化沥青砂浆充填等步骤,确保 轨道板的平顺性和稳定性。
技术特点
CRTSII型板式无砟轨道施工技术具有高精度、高稳定性、 低维护成本等特点,能够提高列车运行的安全性和舒适性。
混凝土浇筑
在模板内浇筑混凝土,确 保混凝土的密实度、平整 度和外观质量。
轨道板预制
模具制作
根据轨道板的设计尺寸, 制作预制轨道板的模具。
CRTSII型轨道板施工工艺
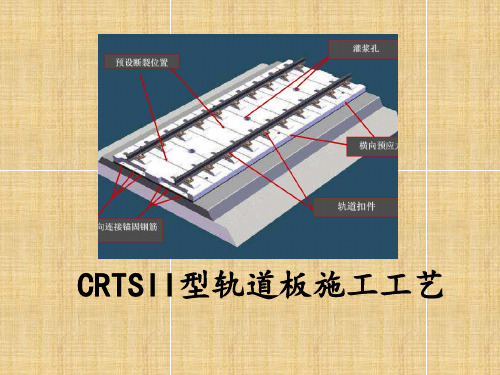
桥上无砟轨道一般构造断面图
轨道板 砂浆垫层 混凝土底座板 土 工 布 +薄 膜 +土 工 布 侧向挡块 侧向挡块
1.2路基、 1.2路基、隧道上无砟轨道结构 路基
• 路基、隧道上CRTSⅡ型板式无砟轨道板的支承层, 采用C15素混凝土垫层或干硬性材料压筑成型(称之 为水硬性支承层,HGT),设计宽度为3.25m,厚度 为0.3m。 • 支承层施工与桥上底座板施工基本相同,主要区别 有以下几点: • 1、支承层无两布一膜滑动层、高强挤塑板以及钢 筋。 • 2、支承层直接浇注在路基、隧道基床表层上。 • 3、路基、隧道上支承层施工无需设置临时端刺区、 后浇注带等施工结构和工序。 • 4、支承层需每隔2.5~5m进行切缝处理,切缝深度 至少10cm。
• (5)防水层 • 防水层不允许破损及空鼓现象的存在。防水层空鼓检查 可采用拖拽铁链的方法进行。破损及空鼓的防水层部位 必须整修。 • (6)桥面预埋件 • 要求预埋件平面、高程位置要准确。采用测量检查。对 不能满足无碴轨道施工要求的,视情况进行处理。 • (7)桥面排水坡 • 桥面排水坡构成应符合设计要求。对排水坡存在 • 误差的桥面,应保证设计的汇水、排水能力,不允许 • 反向排水坡的存在,特别是两线中间部位。对可能造 • 成排水系统紊乱的桥面应打磨整修处理。
• 10.长桥上底座板段落划分 10.长桥上底座板段落划分
• 按照上述定义要求,每个施工单元至少 1880m(780+320+780) ,一般4~5km 为宜,同时划 分时要遵守以下条件和原则: • ①施工单元要根据作业面布置情况事先统一规划, 确定相邻作业面张拉顺序和分工责任; • ②临时端刺不能设置在连续梁上,且距连续梁至少 两孔梁; • ③左右线临时端刺布置要错开两孔梁; • ④钢板连接器与剪力齿槽间距75m ; • ⑤未与梁剪切连接的长度≤150m ; • ⑥钢板连接器距硬泡沫板间距≥5m; • ⑦简支梁上的后浇带一般设在梁跨中间,后浇带缝 与轨道板缝不能重合。
CRTS-II型板式无砟轨道施工工艺细则

CRTS-II型板式无砟轨道施工工艺细则目录1 普通路基CRTSⅡ型板式轨道施工....................................................................... 961.1 施工工艺流程图....................................................................................................................... 961.1.1 HGT层施工工艺流程图........................................................................................................ 961.1.2 轨道板施工工艺流程图....................................................................................................... 971.2 HGT层施工................................................................................................................................ 971.2.1 施工前的准备....................................................................................................................... 971.2.2 混凝土支承层铺设............................................................................................................... 981.2 轨道板施工............................................................................................................................... 99锚杆安装........................................................................................................................................... 99轨道板粗放....................................................................................................................................... 99轨道板精调................................................................................................................................... 101轨道板边缝密封........................................................................................................................... 104轨道板的固定............................................................................................................................... 106轨道板垫层灌浆........................................................................................................................... 106轨道板纵向连接........................................................................................................................... 111轨道板接缝施工........................................................................................................................... 112轨道板剪切连接........................................................................................................................... 1132 桥梁CRTSⅡ型板式轨道施工........................................................................... 1152.1 施工工艺流程图................................................................................................................... 115底座施工工艺流程图................................................................................................................... 115轨道板施工工艺流程图(同路基)........................................................................................... 116底座施工....................................................................................................................................... 116两布一膜滑动层及泡沫板的铺设............................................................................................... 116后浇带连接器及剪力钉的安装................................................................................................... 117绝缘钢筋的制作安装................................................................................................................... 118模板的安装................................................................................................................................... 119混凝土的施工............................................................................................................................... 120摩擦板及过渡板上底座板施工................................................................................................... 121临时端刺施工............................................................................................................................... 1223 CRTSⅡ型板式轨道无缝线路施工.................................................................. 129技术标准....................................................................................................................................... 129施工总方案................................................................................................................................... 130施工流程及工艺........................................................................................................................... 130无缝长轨铺设............................................................................................................................... 131长轨移动闪光焊接....................................................................................................................... 132、长轨铝热焊焊接....................................................................................................................... 133、无缝线路应力放散................................................................................................................... 134特殊条件下的施工措施............................................................................................................... 134移动闪光焊冬季施工措施........................................................................................................... 134铝热焊冬季施工措施................................................................................................................... 134冬季无缝线路应力放散施工措施............................................................................................... 135区间无缝线路龙口轨焊接施工措施........................................................................................... 137注意事项....................................................................................................................................... 137轨道整理....................................................................................................................................... 138轨道整理....................................................................................................................................... 138钢轨预打磨................................................................................................................................... 1391 普通路基CRTSⅡ型板式轨道施工京津城际轨道交通工程车站路基正线CRTS-Ⅱ型板式无碴轨道板的承载层采用C15素混凝土垫层(HGT层),HGT层设计宽度为,厚度为。
CRTS II双块式无砟轨道版施工解读

模板安装过程中为了不影响粗调完轨排精度,尽量避免人为因素造成模板与粗调完的 轨排之间发生碰撞。 利用龙门吊将纵向模板吊放至安装面的两侧,梁面底部必须清扫 干净,使其平整,且与底座板侧面密贴,纵向模板连接使用螺栓连接,两侧利用加工 好的三脚架,梁面打眼使其固定,且与纵向模板外侧牢固密贴。横向模板在工具轨吊 装之前利用龙门吊放至断缝处。横向模板与纵向模板使用法兰连接,中间安放8.4cm宽 的槽钢,顶面加固定横向模板装置,保证板缝宽度10cm的要求。模板安装完成后,道 床板顶面安装栏杆,固定侧向模板,及轨道锁定装置。 6.2.10 轨道精调 1 全站仪设 站 全站仪观测4对连续的CPⅢ点,自动平差、计算确定设站位置。如偏差大于2mm时, 应重新设站。改变测站位置后,必须至少交叉观测后方利用过的4个CPⅢ点,并复测 至少已完成精调的一组轨排。 全站仪设站示意图(图2) 2 测量轨道数 据 轨检小车放置于轨道上,安装棱镜。全站仪测量轨道状态测量仪顶端棱镜,小车 自动测量轨距、超高、水平位置等,接收观测数据,通过配套软件,计算轨道平面位 置、水平、超高、轨距等数据,将误差值迅速反馈到轨道状态测量仪的天宝S8手薄上, 指导轨道调整。 3 调整轨道中线 通过固定于防护墙上的轨向锁定器(连撑带拉结构) 调整中线偏量。 4调整轨道高程 用普通六角螺帽扳手,旋转竖向螺杆,调整轨道水平、 超高。调整螺杆时要缓慢进行,每旋转90°其高程变化1mm ,调整后用手检查螺杆是 否受力,如未受力则调整 控制点 全站仪 P 附近的螺杆。 5 顺接过渡 前一站调整完成 后,下一站调整时需重叠上一站调整过的8至10根轨枕。过渡段从顺接后第一个轨排架 开始,每枕的数据递减值宜小于0.2mm,直到绝对偏差约为零为止。 6.2.11 钢轨、扣 件、轨枕保护 精调完成后,将钢轨、扣件、轨枕利用保护套覆盖,以免浇筑时污染。
CRTSII型板式无砟轨道施工技术

两布一膜,硬泡沫板 水硬性材料支承层/ 混凝土承载层 施工
二、轨 道板铺 设工艺
钢筋混凝土承载层 (底座混凝土) 施工
轨道设标网 (GVP点布设) 轨道基础网 (GRP点布设)
定线并放置定 位锥
线间堆碴
轨道板物流 及存放
铺放轨道板 (粗定位)
悬臂龙门吊
精调数据准备
精调轨道板 (精定位)
精调测量系统
对侧缝和纵缝进行密封处 理并固定轨道板 移动式沥青水 泥砂浆搅拌机 CA砂浆服务站(供 给站)的建设 CA砂浆灌注 桅杆吊 用张拉锁件连 接纵向钢筋
2、剪切筋安装孔的钻设。钻孔前应在设计植筋位置使 用钢筋探测雷达探明轨道板及底座板内的钢筋布置情况, 以此微调并确定钻孔位置。钻孔使用植筋专用钻孔机(一般 由锚固胶供应商提供),钻孔完成后,使用高压风管(枪)吹 除孔内霄粉。植筋施工应随即进行,否则应用砂丝团或软 布团封堵孔口。 3、剪切连接筋的绝缘处理。为确保剪切筋与板(轨道 板及底座板)内钢筋处于隔离绝缘状态,剪切筋表面应事先 均匀涂抹一层植筋胶(即锚固用胶),并确保表面无遗漏之 处。面胶凝固后再进行植入施工。 4、剪切连接筋的安装。孔内注入(适量,试验确定)植筋胶 并植入剪力销钉(筋)。剪切筋植入时应轻轻插入,并避免 与板内钢筋接触。
十、侧向挡块的施工
十、侧向挡块的施工
十、侧向挡块的施工
侧向挡块施工前,应对桥上预埋套筒位置进行检查,要求内侧(靠近 底座板一侧)预埋套筒中心(轴线)距底座板边缘距离为8~12cm,超过此范 围要求的应进行整修。其整修基本原则是在内侧连接筋(与桥面的)设计位 置(距底座板边缘10cm)钻孔并清孔(强吹风),其后注入锚固胶并植入钢筋。 侧向挡块外侧钢筋可保持现状不动,在此基础上,安装其他钢筋并根据实 际情况进行适当连接调整。 侧向挡块应保证 “纵、横向一条线”。侧向挡块施工推荐使用成批 加工制做的组合钢模具。施工时,应先安装固定橡胶垫板及硬质泡沫材料, 其中,橡胶垫板可通过与挡块钢筋连接并固定(与底座板砼紧贴),硬质泡 沫材料可采用胶合剂与底座板混凝土粘合固定(要求与橡胶垫板紧靠),硬 质泡沫材料及橡胶垫板应在砼灌注面用塑料薄膜覆盖,其后再安装挡块模 具。 模具应成批安装并挂线作业。混凝土灌注施工时应按规定进行振捣, 振捣作业采用微型振捣棒。灌注完成后的侧向挡块应及时养护。
CRTSⅡ型板式无砟轨道设计

采用先进的加工工艺和技术,确保材料的加工质量和性能,如轨道 板的预制、砂浆的搅拌等。
力学性能分析
1 2 3
静力学分析
对轨道结构进行静力学分析,计算其在静载作用 下的应力、应变和位移等参数,以确保其承载能 力和稳定性。
动力学分析
对轨道结构进行动力学分析,计算其在动载作用 下的振动频率、振幅和阻尼等参数,以提高其减 震性能和舒适度。
结合新材料、新技术的发展,探索 CRTSⅡ型板式无砟轨道的创新设计 和优化方案,推动其可持续发展。
THANKS
感谢观看
砂浆垫层的制备与铺设
砂浆配合比设计
根据工程要求和材料性能,设计合理 的砂浆配合比,确保其满足强度、耐 久性等方面的要求。
砂浆垫层铺设
将制备好的砂浆垫层均匀铺设在基础 面上,确保其平整、密实,无气泡和 裂缝。
轨道板的安装与固定
定位测量
使用高精度的测量仪器,对轨道板的位置进行精确测量,确保其符合设计要求。
磁悬浮交通
在某些磁悬浮交通项目中,CRTSⅡ型板式无砟轨道也被选为首选轨 道结构。
成功案例介绍
京沪高铁
作为我国最早的高速铁路之一,京沪高铁采用了CRTSⅡ型板式无砟轨道,实现了列车时速350公里的稳定运行, 为我国高速铁路的发展树立了典范。
京广高铁
京广高铁作为我国南北交通的大动脉,全线采用CRTSⅡ型板式无砟轨道,大大提高了列车的安全性和舒适性。
结构优化设计
根据工程实践和理论分析,对轨 道板、水泥乳化沥青砂浆充填层、 混凝土底座等关键结构进行优化 设计,以提高轨道的承载能力和
减震性能。
材料设计原理
材料选择
选择优质的水泥、砂、石等原材料,确保轨道结构的强度和耐久性。
高铁CRTSⅡ型板式无砟轨道板揭板施工技术分析

特殊 工况 ,对板 轨道 进行 应力验 算 。其次 ,底 座板 的设 计 ,采用德 国规范 中拉压杆件开裂后 的刚度折减理论 ,而
ห้องสมุดไป่ตู้
对底 座混凝土板按照正 常使用极 限状 态和承载能力进行设
计 。使 用 的主要 软件 技术 是有档 肩纵 连板 式轨 道 系统软
向分2 0 4 " 承轨道台 ,承轨台设计适应于有档肩扣件 ,经过打
磨以后才能确定其在线路上唯一位置的属. 1 生,所以每一块板 都有各 自的 宁编号。而异型板包括补偿板 、特殊板 、小曲 线半径板和道岔板 ,其中补偿板 、特殊板 、小曲线半径板均 在标准板基 础上发展变化而来 ,与标准板有相似 的结构特 征 ,分别用于补偿调整线路长度 、道岔前后过渡 、曲线半径
张 双
3 2 0 0 0) ( 中铁 四局 五公 司, 江 西 九 江 3
摘要 :C RT S I I 型板 式 无砟 轨道是 我 国高速铁路 和客运 专线的 主要 轨道构 成形式 。文章在 查阅资料 的基础上 结
合 实际 ,主要分析 了C RT S I I 型板 式无砟轨道 板的 结构 组成、技 术特点 、设计原 理 、方法 ,进而 阐释 了C RT S I I 型板式 无砟 轨道板揭 板施 工技 术在 高铁上 的应用。
高铁C R T S I I 型 板 式 无 砟 轨 道 板 揭 板 施 工 流 程 是 一 道 极
2 0 0 mm,曲线独断根据超 高设计 情况计算确定 。此外 ,其 采用 了特殊 的摩擦板 和端 刺结构 ,作为桥梁 与路 基之间的
过 渡。摩擦板上轨道结构 与桥梁上略有不 同 ,它们之间采 用单层 土工布 ,通过剪切联接。 C R T S I I 型板式 无砟 轨道 技 术概括 起来 主要 有 四个 特 点 ,分别 是横 向施 加预 应力 、承 轨 台用数 控磨 床打 磨处 理 、板 与板间纵 向联接 、4 c m深预裂缝 。首先 ,其轨道板 为横 向先 张结构 ,每6 5 c m 设4 c m深预裂缝 ,承轨台打磨处 理 ,板 与板 间通过6 根2 0 m m螺纹钢筋进 行纵 向联接 ,解决
第二篇 无砟轨道CRTSⅡ型轨道板的施工

7/89
二、施工工艺及关键技术
⑤混凝土中应选用高效减水剂及能够改善混凝土性能的高活性复合 掺合料,混凝土的胶凝材料总量不宜超过480 kg/m3,用水量不应超过 150 kg/m3。 ⑥预应力筋放张时,混凝土抗压强度不得低于设计强度的80%,且 不应低于48MPa。 ⑦设计坍落度:0mm~180mm,含气量:2~3%。 混凝土16h强度达到48MPa的配制特点 轨道板在生产厂房内集中预制,实行工厂化管理。轨道板厂设计生 产能力根据工程量和施工工期确定。半成品轨道板厂房设三条先张法长 线台座生产线,每条生产线作业周期为24 h(其中养护时间约16h),采 用三班作业制,每天生产半成品轨道板81块。 确定优选原材料 本项目要求根据《铁路混凝土工程施工质量验收补充标准》铁建设 【2005】160号和《客运专线铁路CRTSII型板式无砟轨道混凝土轨道板 (有挡肩)暂行技术条件》科技基【2008】173号的要求选用材料,通 过试验优选混凝土用原材料如下: 水泥: P·II42.5水泥;高活性复合掺和料;砂:新中砂;碎石: 5~20mm 外加剂:高效减水剂
4/89
二、施工工艺及关键技术
CRTSⅡ型轨道板预制施工工艺流程 2.1 CRTSⅡ型轨道板预制施工工艺流程 轨道板采用长线台座预制,每个台座配备27套模具,轨道板横向预 应力通过在台座进行整体先张拉实现,一个台座的27块轨道板必须在2 小时内一次性连续浇筑成型。一个台座内各施工工序的作业时间及人员 安排计划详见表2.1-1。CRTSⅡ型轨道板预制工艺详见图2.1-1。
运输砼
试件制作 水池同 温条件 养护
6/89
二、施工工艺及关键技术
2.2 原材料及混凝土配合比 高速铁路CRTSⅡ型轨道板为C55高性能钢筋混凝土,是采用现代混 凝土技术制作的新型混凝土,它以耐久性作为设计的主要指标,保证混 凝土的适用性和强度并达到高耐久性、高工作性、高体积稳定性和经济 性。 混凝土的性能要求 依据设计图纸、《铁路混凝土工程施工质量验收补充标准》铁建设 【2005】160号、《客运专线铁路CRTSII型板式无砟轨道混凝土轨道板 (有挡肩)暂行技术条件》科技基【2008】173号和《客运专线高性能 混凝土暂行技术条件》科技基【2005】101号;同时借签其他轨道板场 的相关经验。 ①混凝土的抗压强度和弹性模量应符合设计要求。 ②混凝土的抗冻性能应满足F300的要求。 ③混凝土的电通量应小于1000C。 ④混凝土内总碱含量不应超过3.5kg/m3。当骨料具有潜在碱活性时 ,总碱含量不应超过3.0kg/m3。混凝土中总氯离子含量不应超过胶凝材 料总量的0.06%。
CRTSⅡ型无砟轨道板制造综合技术

CRTSⅡ型无砟轨道板制造综合技术Ⅱ型无砟轨道板制造综合技术摘要】CRTSⅡ型无砟轨道板制造是CRTSⅡ型无砟轨道系统技术的关键,本文以曲阜轨道板场CRTSⅡ型无砟轨道板制造为例,介绍CRTSⅡ型无砟轨道板场规划布置和预制、打磨生产。
关键词】CRTSⅡ型,轨道板场规划,预制,打磨1 前言伴随着中国高速铁路跨越式发展,无砟轨道技术得到了不断完善和飞速发展。
与有砟轨道板相比,其具有轨道稳定性高、平顺性好、结构耐久性强、维修工作量显著减少、列车安全性和舒适性显著提高等优点;其具有结构稳定,利于工厂化生产,利于提高施工效率等特点。
2 工程概况曲阜轨道板场共计生产CRTSⅡ型无砟轨道标准板23878块。
标准板长6.45m,宽2.55m,厚0.2m(详见图1 CRTSⅡ型轨道板结构图),为横向先张预应力混凝土结构。
纵向设置10对承轨道台,承轨台间设置横向预裂缝;横向每个承轨台配有6根10 mm预应力筋,纵向配有6根20mm精轧螺纹钢筋,板与板之间通过张拉锁和精轧螺纹钢筋连成整体。
3 曲阜轨道板场规划轨道板在厂房内集中预制,实行工厂化施工管理。
毛坯板采用先张法长线台座法生产,设两条生产线,每条生产线作业周期为24小时(其中作业时间8h,养护时间约16h),生产能力41块;采用两班作业制,每天生产毛坯板82块;成品板生产线以数控磨床为中心,采用三班作业制,每班打磨27-36块,每天打磨81-108块;设置4个月成品板储存区,1个月毛坯板储存区,最大存板能力约12000块。
4 施工工艺4.1 施工工艺流程CRTSⅡ型无砟轨道板施工工艺流程详见图2。
4.2钢筋网片制作在轨道板内依次布置有Ф5mm预应力筋、下层钢筋网片、Ф10mm 预应力筋及上层钢筋网片。
Ф5mm和Ф10mm预应力筋在场内采用定长切割机进行下料。
上、下钢筋网片在定型胎具上绑扎,通过横移小车运送至制板车间进行安装。
轨道板内预应筋及上下层钢筋网片各层的交点均通过环氧涂层、绝缘热缩套管、绝缘垫片进行了绝缘处理。
浅析CRTS Ⅱ型无砟轨道板裂纹控制技术

浅析CRTS Ⅱ型无砟轨道板裂纹控制技术摘要:在高速铁路建设中,无碴轨道施工是重要的施工项目,轨道板的制作是其中的关键过程。
本文通过杭长铁路客运专线轨道板制作实践经验,对影响轨道板质量的裂纹原因及采取的防裂措施进行阐述和说明。
关键词:无碴轨道;轨道板;温差裂纹;控制;技术1.前言轨道板预制是线上工程质量控制重点,轨道板预制质量决定着高速铁路的平顺性和稳定性及外观质量。
根据南杭、杭涌、京沪客专预制轨道板施工经验,影响轨道板预制质量的最大问题是裂纹。
工程概况杭长铁路客运专线浙江段【HCZJ-6标段】光明铁道轨道板厂位于浙江省龙游县小南海镇,共承担杭长铁路客运专线HCZJ-6标段及HCZJ-7标段24895块CRTSⅡ型板式无砟轨道的预制任务。
受浙江西北地区气侯影响,轨道板预制施工同时面临夏季高温条件下施工和冬季低温条件下施工的困难,对混凝土的拌制和施工养护有较高的要求。
根据南杭、杭涌、京沪客专预制轨道板施工经验,影响轨道板预制质量的最大问题是裂纹。
3.裂纹的类型(1)约束裂纹:是由外荷载引起的,包括结构计算中的主要应力以及其他的结构次应力造成的受力裂缝。
(2)温差裂纹:主要由混凝土水化热与外界温差引起。
(3)收缩裂纹:主要由养护规定温度、湿度与环境温度、湿度差引起。
裂纹的成因温差裂缝主要是由温差造成的,即由于混凝土具有热胀冷缩性质,当外部环境或结构内部温度发生变化,混凝土将发生变形,若变形遭到约束,则在结构内产生应力,当应力超过混凝土抗拉强度时即产生温度裂缝。
温度裂缝区别其他裂缝最主要特征是随温度变化而变化。
温差可分为以下三种: 水化热引起的混凝土内外温差、结构整体的温度升降差、结构从上表面至下表面的温度梯度。
水化热引起的混凝土内外温差。
混凝土浇筑初期,水泥在水化过程中要产生大量的热量,并且其大部分热量是在3d以内放出。
由于混凝土是热的不良导体,水化热积聚在混凝土内部不易散发,其内部的温度大多在浇筑后的3d~5d达到最高值。
CRTSⅡ型板式无砟轨道施工技术
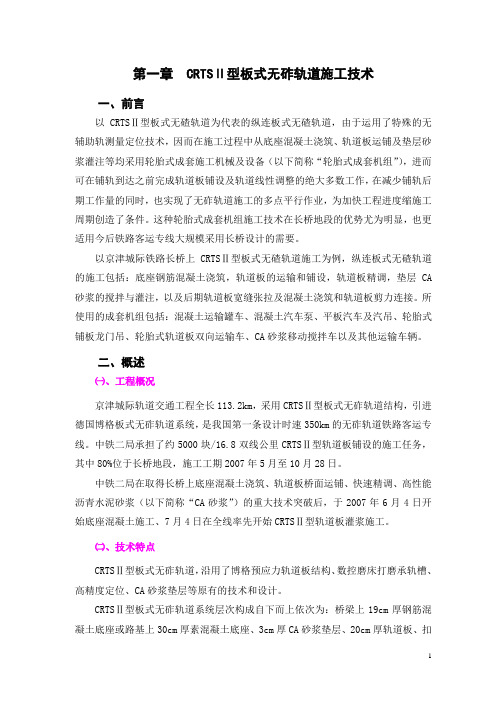
第一章 CRTSⅡ型板式无砟轨道施工技术一、前言以CRTSⅡ型板式无碴轨道为代表的纵连板式无碴轨道,由于运用了特殊的无辅助轨测量定位技术,因而在施工过程中从底座混凝土浇筑、轨道板运铺及垫层砂浆灌注等均采用轮胎式成套施工机械及设备(以下简称“轮胎式成套机组”),进而可在铺轨到达之前完成轨道板铺设及轨道线性调整的绝大多数工作,在减少铺轨后期工作量的同时,也实现了无砟轨道施工的多点平行作业,为加快工程进度缩施工周期创造了条件。
这种轮胎式成套机组施工技术在长桥地段的优势尤为明显,也更适用今后铁路客运专线大规模采用长桥设计的需要。
以京津城际铁路长桥上CRTSⅡ型板式无碴轨道施工为例,纵连板式无碴轨道的施工包括:底座钢筋混凝土浇筑,轨道板的运输和铺设,轨道板精调,垫层CA 砂浆的搅拌与灌注,以及后期轨道板宽缝张拉及混凝土浇筑和轨道板剪力连接。
所使用的成套机组包括:混凝土运输罐车、混凝土汽车泵、平板汽车及汽吊、轮胎式铺板龙门吊、轮胎式轨道板双向运输车、CA砂浆移动搅拌车以及其他运输车辆。
二、概述㈠、工程概况京津城际轨道交通工程全长113.2km,采用CRTSⅡ型板式无砟轨道结构,引进德国博格板式无砟轨道系统,是我国第一条设计时速350km的无砟轨道铁路客运专线。
中铁二局承担了约5000块/16.8双线公里CRTSⅡ型轨道板铺设的施工任务,其中80%位于长桥地段,施工工期2007年5月至10月28日。
中铁二局在取得长桥上底座混凝土浇筑、轨道板桥面运铺、快速精调、高性能沥青水泥砂浆(以下简称“CA砂浆”)的重大技术突破后,于2007年6月4日开始底座混凝土施工、7月4日在全线率先开始CRTSⅡ型轨道板灌浆施工。
㈡、技术特点CRTSⅡ型板式无砟轨道,沿用了博格预应力轨道板结构、数控磨床打磨承轨槽、高精度定位、CA砂浆垫层等原有的技术和设计。
CRTSⅡ型板式无砟轨道系统层次构成自下而上依次为:桥梁上19cm厚钢筋混凝土底座或路基上30cm厚素混凝土底座、3cm厚CA砂浆垫层、20cm厚轨道板、扣件系统和无缝长钢轨,轨道板标准长度650cm 、宽255cm 。
无砟轨道CRTSⅡ型轨道板预制技术
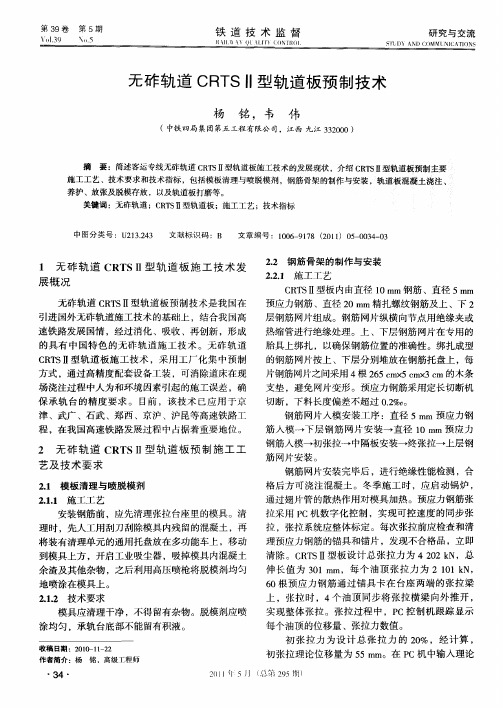
22 钢 筋 骨架的 制作与安 装 . 2 . 施工 工艺 .1 2
C T Ⅱ型板 内 由直径 1 m钢筋 、直径 5mm RS 0m 预应 力钢筋 、直径 2 m精 扎螺纹 钢筋及 上 、下 2 0m 层钢 筋 网片 组成 。钢筋 网片纵横 向节点 用绝缘 夹或 热缩 管进行 绝缘处理 。上 、下层 钢筋 网片在专用 的 胎具 上绑扎 ,以确保 钢筋 位置 的准确性 。绑扎 成型 的钢 筋 网片按上 、下层分 别堆放 在钢 筋托盘 上 ,每 片钢筋 网片之 问采用 4 2 5 r 5e x m 的木条 根 6 e m 3c cx 支垫 ,避免 网片变形 。预应 力钢 筋采用定 长切 断机
收 稿 日期 :2 1— l 2 00 1-2
6 0根 预应 力 钢筋 通 过锚 具 卡 在 台座 两端 的张 拉梁
上 ,张拉时 ,4 个油顶 同步将张拉横梁 向外推开 , 实 现 整体 张拉 。张拉 过程 中 ,P c控 制 机跟 踪 显示 每个 油顶 的位移 量 、张拉力数 值 。 初 张 拉 力 为 设 计 总 张 拉 力 的 2 %,经 计 算 , 0
切断 ,下料 长度偏差 不超 过 02 。 . 。 %
的具 有 中 国特 色 的无砟 轨 道 施 工 技 术 。无 砟 轨 道
CT R SⅡ型 轨 道板 施 工技 术 ,采用 工 厂化 集 中预制
方 式 ,通 过高精度 配套设 备工装 ,可 消除道床 在现
场 浇注过 程 中人 为和环境 因素 引起 的施 工误差 ,确 保 承 轨 台 的精 度 要 求 。 目前 ,该 技术 已应 用 于 京 津 、武广 、石武 、郑西 、京沪 、沪 昆等高速铁 路工 程 ,在我 国高速铁 路发 展过程 中 占据 着重要 地位 。
CRTSⅡ型轨道板无砟道床铺设施工工艺

CRTSⅡ型板式无砟轨道道床施工方法及工艺(1)施工方法路基及隧道地段混凝土支承层均采用人工模筑法施工,桥上混凝土底座施工前需人工铺设滑动层及高强度挤塑板,然后采用人工立模、绑筋、泵送混凝土进行浇筑的施工方法施工。
轨道板采用轮胎式跨双线龙门吊进行轨道板的铺设安装施工,然后对已铺轨道板进行调整定位;轨道板精调定位完成后即可开始水泥沥青砂浆的灌注施工;水泥沥青砂浆达到一定强度进行窄接缝施工、轨道板纵联、宽接缝施工等作业,完成CRTSⅡ型板式无砟轨道道床施工。
(2)施工工艺流程CRTSⅡ型板式无砟轨道道床施工工艺流程图(3)施工工艺操作要点①施工准备桥梁、隧底及路基基础面状态检查、评估桥梁架设完成六个月且桥面保护层达到设计允许铺设强度后,路基沉降满足无砟轨道铺设要求后,方开始无砟轨道施工。
②测量放样根据CPⅢ控制网采用全站仪自由设站极坐标法或光学准直法进行底座模板轨道中心线平面放样。
高程测量采用全站仪自由设站三角高程或几何水准法施测。
③桥上滑动层高强度挤塑板施工滑动层铺设前,应按照设计要求,对梁面高程、梁面平整度、相邻梁端高差、防水层、轨道预埋件、剪力齿槽状态、伸缩缝状态等进行验收。
不符合设计要求时,需进行整修。
桥上滑动层、高强度挤塑板施工控制点依据CPⅢ测设,根据控制点弹出墨线,确定滑动层铺设位置。
高强度挤塑板设于桥梁接缝处,通过胶合剂与桥面粘贴,其顶面根据设计要求铺设滑动层,并防止混凝土浇筑时污染泡沫板。
高强度挤塑板规格尺寸应按桥面拼接需要加工为定尺规格。
铺设完成的高强度挤塑板应做好保护,安装钢筋网时要选择合适的垫块间距,以免钢筋刺穿高强度挤塑板。
一旦破损,必须更换。
④桥上混凝土底座施工桥上混凝土底座施工工艺流程见下图。
桥上混凝土底座施工工艺流程图A.测量放线 通过CP Ⅲ控制点进行底座边线放样,每隔10m 测设一个断面,做好标记,并对每个标记点进行高程测量,作为底座立模依据。
底座施工前,应根据施组及相关技术要求布设临时端刺。
crtsⅱ型板式无砟轨道施工过程

crtsⅱ型板式无砟轨道施工过程本文将介绍crtsⅱ型板式无砟轨道施工过程。
crtsⅱ型板式无砟轨道采用了半挂式铺轨法,是一种完全不用砟子铺筑的无砟轨道。
crtsⅱ型板式无砟轨道具有施工简便、安装快捷、经济节能、环保等优势。
下面将详细介绍其施工过程。
一、基础处理及验线crtsⅱ型板式无砟轨道施工前必须进行现场基础处理。
基础处理包括打基础、夯实土方、伸缩缝、配重及延伸等。
基础处理完毕后,进行验线。
验线是根据勘测及设计数据,按照钢轨中心线来确定轨道的位置,并在场地上用测量及刷油漆等方法标出轨道的位置及范围,为后续的施工提供依据。
二、轨道组装轨道组装是crtsⅱ型板式无砟轨道施工的第一步。
轨道组装前,需要把轨道板按照设计要求框定,并在框定尺寸范围内进行筛砂夯实。
然后在轨道头部及尾部加装配重,确保轨道的垂直度和水平度。
三、浇筑混凝土浇筑混凝土是crtsⅱ型板式无砟轨道的核心环节。
混凝土浇筑前,必须先在轨道下面设置喷淋塑料膜,以避免混凝土砂浆渗透到地面,影响环境。
当混凝土浇筑到较低位置时,需要用振动锤进行混凝土浇筑压实,以提高其密实度,确保混凝土的均匀压实。
浇筑完混凝土后,需要进行养护,通常养护周期为7天,这期间需要保持混凝土表面湿润,以达到其密实度和硬度的最佳效果。
四、铺设轨道及添砂轨道铺设是crtsⅱ型板式无砟轨道的工作之一。
在轨道铺设时要注意,轨道铺设方向必须与设计要求相一致。
轨道铺设完毕后,需要进行添砂。
添砂主要是为了填平轨道与地面之间的空隙。
在添砂时,需要用专用的具有加油泵的输送车,将砂子送到轨道头部,然后使用根据设计要求调整好的压实机进行砂子的压实。
五、压浆及养护压浆是crtsⅱ型板式无砟轨道施工的一个重要环节。
压浆是为了填补轨道板之间的缝隙,并加强其牢固度。
压浆时,需要使用压浆机器将浆料注入轨道板之间的缝隙,并充分压实。
压浆完毕后,需要进行养护。
养护期间需要保持压浆表面充分湿润,并保持养护期满前养护场地的整洁和干燥。
浅谈石武客专CRTSⅡ型板式无砟轨道施工

浅谈石武客专CRTSⅡ型板式无砟轨道施工[摘要]本文结合石家庄至武汉客运专线SWZQ-2标无砟轨道的施工实践,就高铁和客专无砟轨道施工的关键工序和技术控制进行了简要阐述。
【关键词】客运专线;无砟轨道施工;关键工序;技术控制中铁十九局集团施工的石武客专管段线路全长50.104km,均采用CRTSⅡ型板式无砟轨道。
内容包括:轨道板粗铺、精调及CA砂浆灌注、轨道板张拉和剪切连接等。
现就关键工序和技术控制进行阐述。
1.轨道板粗铺1.1工艺流程。
复测CPⅢ点→轨道板运输→安装定位锥和测设GRP点→测量标注轨道板板号→轨道板吊装→放置6个支点木条(2.8cm)→轨道板粗铺定位。
1.2粗铺要求。
①轨道板上桥前要进行检测,不合格轨道板禁止上桥。
同时要对轨道板清理:板度、承轨台面、扣件表面,灌浆孔疏通,在调节千斤顶位置周围粘贴防吸性泡沫材料;②底座板表面高程得测并处理完毕,表面要进行高压清洗;③再次确认上桥前轨道板方向和装车顺序;④底座板上轨道板基准网放样完成且平差计算通过后才可进行轨道板粗铺。
相邻轨道基准点相对精度应满足平面位置±0.2mm,高程±0.1mm;⑤底座板上做好标识,放便时用墨线弹出轨道板边线位置,提高轨道板粗铺效率和精度。
粗铺后轨道板定位精度10mm;⑥在砼底座板上放置300×50×35mm垫木,质地要硬,每侧放置3个,分别放在轨道板两头及板中。
2.轨道板精调2.1精调原理。
通过全站仪自动测量轨道板实际位置坐标并录入计算机,经程序计算出实际位置与设计间偏差,根据显示器上的偏差量进行调整,使轨道板快速调整到偏差允许范围内。
控制计算中心通过与工控机相连的数传电台建立通讯,指挥安装在对中三脚架上的测量机器人对轨道板上的四套测量标架上的各微型球棱镜的实际坐标进行测量,并将测量的数据通过数传电台返回到轨道板精密调整系统软件内,处理计处后获得轨道板当前的实际位置;然后与事先输入的轨道板应有的理论设计值进行比对,将计算后得到的调整值通过485总线发送到与轨道板上前、中、后三对共计6个调整点相对应的6个调整数量显示器上。
CRTS II 型无碴轨道板施工工法(2)

CRTS II 型无碴轨道板施工工法CRTS II型无碴轨道板施工工法一、前言CRTS II型无碴轨道板是一种新型的轨道板结构,相比传统的有碴轨道板具有更高的质量和可靠性。
本文将详细介绍CRTS II型无碴轨道板施工工法,包括工法特点、适应范围、工艺原理、施工工艺、劳动组织、机具设备、质量控制、安全措施、经济技术分析和工程实例。
二、工法特点1. 高质量:CRTS II型无碴轨道板采用高强度的混凝土,具有较高的承载能力和耐久性。
2. 无碴设计:通过减少轨道板与钢轨之间的摩擦,CRTS II型无碴轨道板能够减少噪音和振动,提升列车运行的平稳性。
3. 快速施工:CRTS II型无碴轨道板采用预应力技术,施工速度快,可以缩短工期。
4. 易于维护:CRTS II型无碴轨道板的维护成本较低,且容易进行检修和更换。
三、适应范围CRTS II型无碴轨道板适用于城市轨道交通、高速铁路、物流园区等多种场景,能够满足不同路段和不同运行速度的要求。
四、工艺原理CRTS II型无碴轨道板的施工工法基于以下原理:1. 混凝土浇注:首先在轨道板基座上进行混凝土浇注,形成轨道板基座。
2. 预应力:在混凝土浇筑后,采用预应力技术对轨道板进行加固,增加承载能力和稳定性。
3. 安装固定装置:将轨道板固定在基座上,确保轨道板与基座的紧密连接。
4. 精确校正:通过调整固定装置,使轨道板达到准确的位置和高度。
五、施工工艺1. 基座准备:清理轨道床顶面,施工基座模板。
2. 混凝土浇注:在基座上进行混凝土浇筑并振实。
3. 预应力施工:在混凝土浇筑后,进行预应力工作,使轨道板获得足够的强度。
4. 装配完成:安装固定装置,对轨道板进行精确校正并进行初步固定。
5. 防水处理:根据需要对轨道板进行防水处理。
6. 完善固定:进行最终固定,确保轨道板与基座紧密连接。
六、劳动组织根据施工工艺的要求,需要进行劳动组织的安排,包括人员配置、工作流程和协调管理。
- 1、下载文档前请自行甄别文档内容的完整性,平台不提供额外的编辑、内容补充、找答案等附加服务。
- 2、"仅部分预览"的文档,不可在线预览部分如存在完整性等问题,可反馈申请退款(可完整预览的文档不适用该条件!)。
- 3、如文档侵犯您的权益,请联系客服反馈,我们会尽快为您处理(人工客服工作时间:9:00-18:30)。
浅谈CRTSⅡ型无砟轨道板制造技术及工艺中交隧道局第五工程有限公司李奇涛【摘要】CRTSⅡ型板式无砟轨道板是引进德国博格板的基础上在中国进行改进、创新的结果。
相比京津城际时的CRTSⅡ型板制造最大的区别在于用普通硅酸盐水泥代替超细水泥。
由于CRTSⅡ型板工艺要求的特殊性与国内原材料、模具加工精度的差异性等决定了制造技术的复杂性及工艺研究艰巨性。
现结合现场的实际情况和前期的工艺试生产情况,总结了CRTSⅡ型无砟轨道板的制造技术和工艺,轨道板的质量有了显著的提高,得到了上级领导的好评。
现将CRTSⅡ型无砟轨道板的制造技术和工艺研究进行简单的介绍。
【关键字】CRTSⅡ型板无砟轨道施工工艺1 概述1.1 轨道板结构特征京沪高速铁路CRTSⅡ型无砟轨道板外形尺寸为6450mm×2550mm×200mm,为先张法预应力混凝土结构,体积约3.452 m3,重约8.63 t(不计扣件,扣件重约0.6t)。
设2列共20个承轨台,每对承轨台间设置预裂缝,结构特征见图1。
轨道板承轨面通过数控磨床磨削加工,见图2。
板与板之间通过纵向的6根精轧螺纹钢筋连接。
图1 CRTSⅡ型无砟轨道板结构图2 打磨后承轨面1.2 轨道板预制的特点1)轨道板同步张拉、放张。
采用液压自动张拉控制系统,实现同步张拉、放张。
2)轨道板同步跟踪养护。
采用轨道板同步养护温度控制设备,实现了轨道板实时跟踪养护。
3)高精度模板工程。
模板承轨槽部分的平整度及直线度是保证毛坯板质量的关键之一,利用高精度测量仪器对模板及毛坯板进行定期监测并实时调整。
减少打磨量,提高打磨效率。
4)采用可调速度的混凝土布料机,实现混凝土灌注的均匀性,每套模板配置8台变频振动电机,实现了振动效果与混凝土和易性的匹配。
5)采用真空吸盘脱模,保证了近9t重的轨道板平稳从模板中脱出。
6)通过高精度数控磨床对轨道板承轨面进行磨削,实现轨道板承轨面磨削加工工序的自动化,保证轨道板几何尺寸的精度。
7)轨道板半成品、成品的存放采用专用存板基础,确保其稳固且控制三个支点的高度差。
配置可以调速的起重设备并设计专用的吊具,确保轨道板存放平稳而不变形。
2、轨道板工艺流程见图3。
图3 CRTSⅡ型无砟轨道板预制工艺流程图3、钢筋加工轨道板设上下层钢筋网片,下层钢筋网片由横向46φ8mm环氧镀层钢筋和纵向4φ16mm的普通螺纹钢筋及8φ8mm普通钢筋组成。
上层钢筋网片由横向52φ8mm环氧镀层钢筋和纵向6φ20mm的精轧螺纹钢及14φ8mm普通钢筋组成。
所有纵横向钢筋交叉点间设绝缘垫片并用绝缘扎丝绑扎牢固,预应力钢筋与钢筋网片接触点处设置绝缘热缩管,轨道板剖面见图4。
图4 CRTSII型无砟轨道板局部纵剖面图3.1 绝缘热缩套管的加工在专用胎具上安装绝缘热缩套管,热缩套管的外形尺寸、材质和加工间距应符合设计要求。
对绝缘热缩管加热时,采用液化气喷枪加热,注意热缩管的受热要均匀,防止过热而损坏绝缘性能或受热过低而收缩不紧,见图5。
图5 热缩套管加工3.2 钢筋网片的编组上下层钢筋网片在专用胎具上进行编组。
横向采用环氧涂层钢筋,纵、横向钢筋间设绝缘垫片及绝缘扎丝,编组好的钢筋网片须进行绝缘检测确保任意钢筋交叉点的电阻值不小于2MΩ,检测合格的钢筋网片堆放在专用托架上备用,见图6。
图6 上下层钢筋网片编组3.3 预应力钢筋的下料预应力钢筋采用定长切断机下料,用专用工装进行定期检测预应力钢筋下料长度,偏差应控制在万分之二范围内,预应力钢筋的切断和移运时应保持顺直,防止变形、碰伤、污染,预应力钢筋总长70.22m。
4 模板工程4.1 模板功能及细部参数1)模板功能模型用于轨道板生产中混凝土灌注成型,它在保证轨道板外观质量、尺寸精度和钢筋丝位、预埋件位置精度及混凝土密实度等内在质量方面起着决定性或重要作用,见图7。
2)细部参数模型轮廓尺寸为(mm):长×宽×高=6950×2590×861;模型内腔尺寸(mm):长×宽×高=6450×2550×200;模型底板上面平面度(mm):误差≤2;模型内腔未注公差尺寸精度:误差≤1.5 mm;每套模型承轨台壳体数量:20件,分两列,每列10件;每承轨台壳体定位孔数量及孔径:2-φ10 mm;每列承轨台壳体定位孔直线度:误差≤0.2 mm承轨台壳体定位孔孔距精度:误差≤0.2 mm;承轨台壳体安装平面度:误差≤0.15mm;承轨台壳体未注尺寸(形位)公差各部技术要求:精度误差≤0.5mm;各曲面过渡圆滑,无明显棱角、突起、褶皱;无划痕、裂纹;每套模型承轨两台壳体定位孔数量:40个(φ10mm),分4列,每列10个;每模型20件承轨台壳体安装平面机加工后平面度:误差≤0.3mm;每模型20件承轨台壳体安装后平面度:误差≤0.5mm;四列承轨台壳体定位孔中心线平行度:误差≤0.3 mm;每列承轨台壳体安装后直线度:误差≤0.3mm;两列承轨台壳体安装后中心线平行度:误差≤0.3 mm;塑料套管定位装置数量:40组;分4列,每列10组(每件承轨台壳体2组);每列塑料套管定位装置中心线直线度:误差≤0.2 mm;四列塑料套管定位装置中心线平行度:误差≤0.3 mm。
图7 CRTSII型无砟轨道板模板示意图4.2 模板安装1)安装前的布局工艺测量张拉钢丝钳口高程,全局布置模板:采用莱卡DNA03数字水准仪测出张拉台座上张拉钢丝钳口的高程,并求出台座的高程平均值。
按设计要求张拉池两端张拉台座的高度应处于同一水平,最大允许相差±1mm。
如果满足此要求,将27块模板在同一水平面安装。
如果两端高度差H超出±1 mm,则安装时将此高度差H均分到各个模板上。
2)首块模板安装工艺粗调模板高程:先吊出模板将其放置在支撑钢板上,按照模板边沿高程比张拉槽口高程平均值高1.5~2.0mm的原则将模板粗调平。
纵向槽口定位:采用张拉钢丝法或经纬仪定位法,以两端张拉台座上的Φ5钢筋张拉槽口中心为基准线,移动模具,使模板V型槽口中线与之对齐,其精度要求达到±1mm。
精调模板高程:用数字水准仪通过测量模板中1、4、7、10、11、14、17、20号承轨台的高程,调节地脚螺母使其高程在同一水平面上,误差范围±0.3mm。
3)非首块模板的安装工艺支撑钢板的调整:调节地脚螺母使支撑钢板与前一个已安装模板的支撑钢板基本处于同一水平面。
吊入已制作好的合格模板,安置于8个支撑钢板上。
纵向槽口定位:采用张拉钢丝法或经纬仪定位法,以两端张拉台座上的Φ5钢筋张拉槽口中心为基准线,移动模具,使模板V型槽口中心线与之对齐,其精度要求达到±1mm,并使模板长方向棱边与相邻已安装的模板边平行,并调整模板的位置,使相邻模板紧靠的长棱的内边缘距离控制在50mm,外缘距离控制在34mm。
(此处要考虑后续模板的安装位置,确保有足够的空间下放最后一块模板)。
高程定位:用数字水准仪通过测量模板中1、4、7、10号承轨台的高程,调节地脚螺母使其与已安装的模板在同一水平面上,误差范围小于1.0mm,同一模板内部承轨台达到同一平面,其高程精度要求达到±0.3mm。
4.3 模板的调整由于模板的加工的限制,导致模板的精度和外观质量存在一定缺陷,因此,安装时需要大量的时间进行调整模板。
用高精度的经纬仪进行平整度的调整,全站仪进行承轨槽直线度的调整,通过控制模板的精度来减少打磨量,提高打磨效率。
模板部分侧立面倾斜度不足致使轨道板局部棱边破损、掉角。
模板的缝隙过大,造成轨道板棱边及分缝处的漏浆、粘皮现象。
分丝隔板的高度不够,拆除分丝隔板时,导致上边缘有不同程度的掉角。
分丝隔板扭曲,安装后上下错台现象严重,会影响轨道板的外观质量和外形尺寸。
承轨台模板边缘及螺栓桩垫片光滑度不够导致混凝土边缘破损。
灌浆孔橡胶模具的膨胀系数与混凝土结构的不同导致拆模时该处破损严重。
因此,模板的整修和安装对轨道板的外观质量影响极大,需要投入大量技术力量和时间来调整模板,针对不同的模板问题制定出有效的整修方案。
4.4 模板的清理轨道板进行脱模作业后,应立即进行模板的清理工作,清理工作应仔细认真,每个地方都应用干净的擦布擦拭干净,不得留有混凝土的残渣和任何垃圾,模板不得用利器和榔头等钝器敲击,以免发生凹坑和变形。
模板清理人员应把模板上的垃圾堆放在一起,以方便吸尘作业的人员。
模板清理作业人员应穿戴专用的鞋套,防止在模板上留下脚印和垃圾,影响轨道板的外观质量。
清理模板的同时,保证吹气孔畅通后,用防水贴纸粘贴吹气孔,确保粘贴牢固。
吸尘的同时,将台座旁边踏板一并吸尘,防止进入模板作业时将垃圾带入模板中。
吸尘结束后,在模板的缝隙处打硅胶,防止产生掉角和粘皮的现象。
橡胶端模由专门的人员进行清理作业,注意要轻拿轻放,防止对橡胶端模造成损伤。
清理完成后,放置在相应的模板的端部,注意橡胶端模的方向,以便喷涂脱模剂的同时一起喷涂。
4.5 喷涂脱模剂模板清理完成后,在模板与模板的结合处粘贴5mm的单面胶,粘贴要顺直、牢固,防止漏浆。
然后采用喷雾枪喷涂脱模剂。
脱模剂宜采用水溶性脱模剂,并根据实际情况调整比例和喷涂量,注意喷涂要均匀无沉积。
4.6 预埋套管安装安装预埋套管时,需要穿戴专用的鞋套,防止弄脏模板。
喷涂脱模剂后进行预埋套管安装作业,作业人员先将预埋套管安装在模板的螺栓桩上,然后用橡皮榔头敲紧。
并逐个检查预埋套管是否已敲紧及开裂现象,防止在混凝土振捣时预埋套管跳出螺栓桩或混凝土浆进入预埋套管。
5 钢筋安装5.1 φ5预应力钢丝入模在预埋套管安装到第5块模板时可进行φ5的预应力钢丝安装,以缩短工序间衔接时间。
安装φ5的预应力钢丝时,要在预应力钢丝的槽口的地方粘贴止浆单面胶,防止发生漏浆现象。
5.2 安装下层钢筋网片φ5的预应力钢丝就位后可以进行下层钢筋网片入模。
作业人员应注意接地端子在模板的位置是否正确,起吊时保证有六个吊点,吊点的位置应符合设计要求,以免网片发生变形。
入模时网片上不得碰撞预埋套管和模板,防止预埋套管松动和模板刮伤。
5.3 安装φ10预应力钢丝下层钢筋网片入模完成后开始φ10预应力钢筋安装。
张拉台座的两端分别安排一人,每两块模板一人将三根一组预应力钢筋抬入模板内,并依次分开锁定在张拉钢梁的滑块上,应避免预应力钢筋发生缠绕现象。
采用专用工装确保张拉锚具外露钢筋长度一致,减少应力偏差。
预应力钢筋安装完成后用专用压杆压住锚具,防止张拉过程中张拉锚具跳出滑块。
5.4 分丝隔板安装初张拉完成后依次安装分丝隔板,分丝隔板安装时应按编号一一对应地安装在指定的相邻模板接缝处,并保证全部锁紧。
由于模板预留钢筋齿槽加工精度差,安装时可借助外力使预应力钢筋全部入槽。