高速干式滚齿切削热力耦合与工艺参数分析
小模数齿轮的高速干切滚齿技术
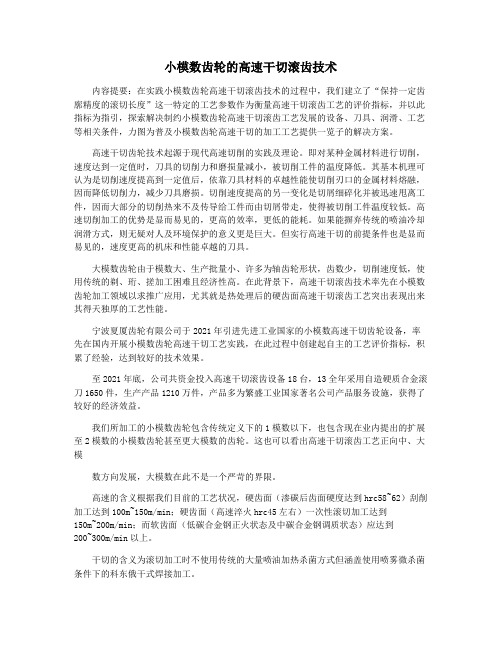
小模数齿轮的高速干切滚齿技术内容提要:在实践小模数齿轮高速干切滚齿技术的过程中,我们建立了“保持一定齿廓精度的滚切长度”这一特定的工艺参数作为衡量高速干切滚齿工艺的评价指标,并以此指标为指引,探索解决制约小模数齿轮高速干切滚齿工艺发展的设备、刀具、润滑、工艺等相关条件,力图为普及小模数齿轮高速干切的加工工艺提供一览子的解决方案。
高速干切齿轮技术起源于现代高速切削的实践及理论。
即对某种金属材料进行切削,速度达到一定值时,刀具的切削力和磨损量减小,被切削工件的温度降低。
其基本机理可认为是切削速度提高到一定值后,依靠刀具材料的卓越性能使切削刃口的金属材料熔融,因而降低切削力,减少刀具磨损。
切削速度提高的另一变化是切屑细碎化并被迅速甩离工件,因而大部分的切削热来不及传导给工件而由切屑带走,使得被切削工件温度较低。
高速切削加工的优势是显而易见的,更高的效率,更低的能耗。
如果能摒弃传统的喷油冷却润滑方式,则无疑对人及环境保护的意义更是巨大。
但实行高速干切的前提条件也是显而易见的,速度更高的机床和性能卓越的刀具。
大模数齿轮由于模数大、生产批量小、许多为轴齿轮形状,齿数少,切削速度低,使用传统的剃、珩、搓加工困难且经济性高。
在此背景下,高速干切滚齿技术率先在小模数齿轮加工领域以求推广应用,尤其就是热处理后的硬齿面高速干切滚齿工艺突出表现出来其得天独厚的工艺性能。
宁波夏厦齿轮有限公司于2021年引进先进工业国家的小模数高速干切齿轮设备,率先在国内开展小模数齿轮高速干切工艺实践,在此过程中创建起自主的工艺评价指标,积累了经验,达到较好的技术效果。
至2021年底,公司共资金投入高速干切滚齿设备18台,13全年采用自造硬质合金滚刀1650件,生产产品1210万件,产品多为繁盛工业国家著名公司产品服务设施,获得了较好的经济效益。
我们所加工的小模数齿轮包含传统定义下的1模数以下,也包含现在业内提出的扩展至2模数的小模数齿轮甚至更大模数的齿轮。
高速滚齿干切技术
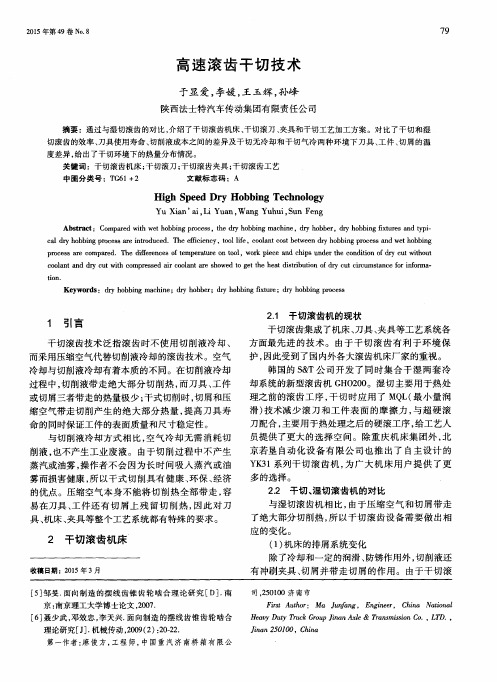
多 的选 择 。
的优点 。压缩空气本身不能将切削热全部带走 , 容 易在 刀具 、 工 件 还 有 切 屑 上 残 留切 削 热 , 因 此 对 刀
具、 机床、 夹具 等整 个工 艺 系统都有 特 殊 的要 求 。
2 _ 2 干切、 湿切滚 齿 机 的对 比
与 湿切 滚齿 机 相 比 , 由于 压缩 空 气 和 切 屑 带走 了绝大 部分 切 削热 , 所 以干 切 滚 齿设 备 需 要 做 出相
关 键 词 :干 切 滚 齿 机 床 ; 干切 滚 刀 ; 干切滚齿夹具 ; 干 切 滚 齿 工 艺
中图分类号 :T G 6 1 + 2
文献标 志码 :A
Hi g h S p e e d D r y Ho b b i n g T e c h n o l o g y
Yu Xi a n’ a i , L i Yu a n, Wa n g Yu h u i , S u n Fe ng
却系统 的新型滚齿机 G H 0 2 0 0 。湿切主要用于热处 理之前 的滚 齿 工 序 , 干切 时应 用 了 MQ L ( 最 小 量 润
滑) 技术 减 少 滚 刀 和 工 件 表 面 的摩 擦 力 , 与 超 硬 滚
刀配合 , 主要用 于 热处理 之后 的硬 滚工 序 , 给工 艺人 员提供 了更大 的 选 择 空 间 。除 重 庆机 床 集 团外 , 北
齿轮成形磨削加工热力耦合数值仿真研究

削热会在齿轮表 面产 生较高的温度 , 容易引起工件表 面烧 伤 ; 另一方 面磨削热 会在工件 表层产生 梯度变化较
大 的温度场 , 从而形成磨削残余应力 , 造成工件 表层 金相组织 变化 , 既会影 响齿轮 磨削加工 的精度 , 也会影 响
齿轮使用 的寿命 。文 章借 助工程分 析软 件 A b a q u s 和 Ma t l a b , 基 于磨 削移 动热 源理 论和 三角形 热源 分布模
Ab s t r a c t : Ge a r f o r m g r i n d i n g, wh i c h i s c o m mo n l y u s e d f o r g e a r f i n i s h ma c h i n i n g,c a n g r e a t l y i mp r o v e
c o u pl i n g o f g e a r f o r m g r i nd i ng pr o c e s s
Z HANG Ku i — b a n g , HAN J i a n g, XI A Li a n, YANG Qi n g - y a n
中图分类号 : T G5 8 0 文献标识 码 : A 文章 编号 : 1 0 0 3 — 5 0 6 0 ( 2 0 1 5 ) 1 0 — 1 2 9 7 — 0 6
Nu me r i c a l s i mu l a t i o n o f t h e r mo - me c ha n i c a l
( S c ho ol o f Ma c h i n e r y a n d Au t o mo b i l e En g i n e e r i n g,He f e i Un i v e r s i t y o f Te c h n o l o g y,H e f e i 2 3 0 00 9 ,Chi na )
汽车齿轮的高速干式滚齿技术
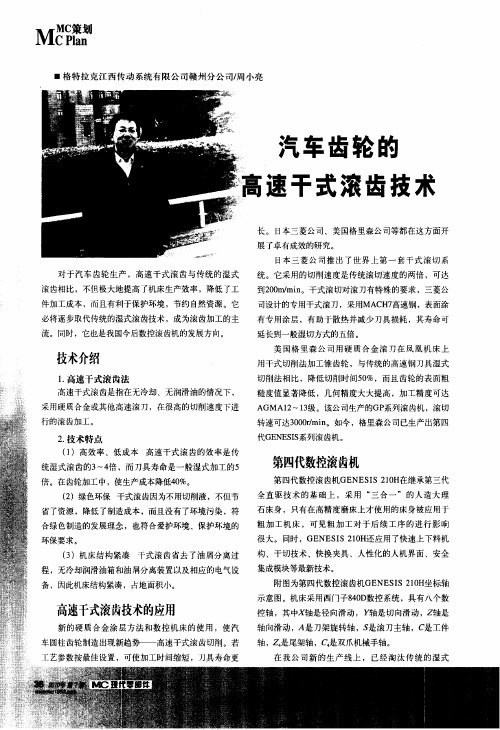
有专用涂层 ,有 助于散热并减少 刀具损 耗 ,其寿命可
延长到一般湿切方式的五倍 。
美 国格 里森 公 司用 硬质 合金 滚 刀在 凤凰 机 床上
技术介绍
1高速干式滚齿法 .
高速干式滚齿是指在无冷却 、无润滑油的情况下 ,
用干式切削法加 工锥齿轮 ,与传统 的高 速钢 刀具湿式 切削法相 比 ,降低切削时 间5 %,而且 齿轮 的表面粗 0 糙度值显著降低 ,几何精度大大提高 ,加 工精度可达
从该表可以看出 ,GE NES S2 0 I 1H的加工效率是普
通数控滚齿机的35 多,大大节约了加 工时间 ,提高了 . 倍 切削效率 。
( 上按第3页 ) 5 磨削过程以及内置的测量设备保证 ] U E T R6 高 ' C N E L J 度的加工安全性和使用高效性 。
相对于传统连杆磨床必须对四个单 个连 杆轴颈 分别
l
() 2 绿色环保 干式滚齿因为不用切削液 , 不但节
i 省了资源,降低了制造成本,而且没有了环境污染,符 i 合绿色制造的发展理念,也符合爱护环境、保护环境的
l 环保要求。 ; ()机床结构 紧凑 干式滚 齿省去 了油 屑分离过 3
; 程 ,无冷却润滑油箱和油屑分离装置以及相应的 电气设
; 统湿式 滚齿的3 倍 ,而 刀具 寿命是一 般湿式加工 的5 ~4
; 倍。在齿轮加工 中,使生产成本降低4 %。 0
第四代数控滚齿机
第四代数控滚齿机GE NES S2 0 I 1H在继承第三代 全直 驱技 术 的基 础上 ,采 用 “ 三合 一 ”的 人造 大理 石床身 ,只有在高 精度磨床上才使 用的床身被应用于 粗加 工机 床 ,可 见粗加 工 对于 后续 工序 的进 行 影响 很大。同时 ,GE S S2 0 NE I 1 H还应用 了快速上下料机 构、干切技术 、快 换夹具 、人性化 的人 机界面 、安全
高速干式切削滚齿机设计关键技术研究

工 程 技 术
高速 千式 切 削滚 齿机 设 计 Nhomakorabea键 技 术 研 究
刘 续 超 ( 肥学院 安徽合肥 2 0 3 ) 合 3 0 1
摘 要: 滚齿机作 为齿轮 加工机床 中的一种 , 主要 用来加 工 圆柱齿轮 和蜗轮等 。 传统滚齿机进行 齿轮加 工, 削液 的飞溅和形成 的油雾对生 态环 境和人 类特 别有 害, 质切 削液 的排放也 严重 的污 染环境 。 变 而且 这种 加工 方法造 成机床 的材料 用量 、 能耗 油耗及 附 加费 大, 已经 不适 应 当前 工业发展 的要求 , 鉴于此 , 本文 对高速干 式 切削滚齿机 设计进 行 了探 讨 。
1 高速干式切削滚齿机设计的关键技术分析
1 1 高速 干式 切 削滚齿 机 的传 动 系统 设计 . 滚 齿 机 的 传 动 设 计 重 点 在 于 整 个 系 统 的 设 计 , 方 面 主要 取 决 这 r数控 技 术 、 电 和 主轴、 力矩 电机 的 发展 。 别 是六 轴 数 控 四 特
关 键 词 : 式 切 削 滚 齿 机 设 计 干
中图分 类 号 : B T 1
文 献标 识 码 : A
文 章 编号 : 6 2 3 9 ( 0 0 ( ) 0 9 - 】 1 7 - 7 l2 1 ) 2 b一 0 2 0 O 度通 常 需要达 到 2 0 / i 以上 , 速干式 0 rr n a 高 削 为 避 免 崩 刃 , 的 各 运 动 应 具 有 消 除 间 床 隙 的 装 置 , 单 蜗 杆 单 蜗 轮 工 作 台 分 度 副 而 是 不具 备 的 。 此 , 要 有 新 的 7架 和 工 作 为 需 ] 台 结 构 出现 。 为 高速 、 图2 高精 度 刀 具 主 轴 结构图。 型高速 、 新 高精 度 滚 刀 主运 动 的 传 动是 由主 电机 通过 两 级高 精 度齿 轮副 减速 , 将运 动 传给 刀具 主 轴 。 传动 过程 中为消 除 在 反 向 间 隙采 用 了一 齿 差 结 构 。 同时 , 为保 证 主 轴 的径 向及 轴 向窜 动 精 度 采 用 了具 有 预 加 负荷 的高 精 度滚 动 轴承 , 避免 在 高速 条 为 件 下 主轴 的发 热 采 用 了压 力空 气加 润 滑 油 对主 轴 进行 快速 循 环润 滑 , 样确 保 滚 丰 这 轴具 有 高 速 、 高精 度 、 刚性 的 性 能 。 高 1 4 滚刀 安装设 计 . 强 力 切 削 要 求 机 床 安 装 滚 刀的 部位 也 必须具有相应 的刚性。 中 锥 度 柄 的设 计 可满 足 刚 性 和 精 度 要求 。 用 带孔 滚 刀时 , 使 通过 纵 向或 端 面 的 几 个 键 槽 , 以 将 主 轴 可 的 力矩 安 全 地 传 递 到滚 刀 。 外 , 有针 对 此 还 带柄 滚 刀 而 设 讣 的 内 置 夹 套 式 接 | 但 是 1, 必 须 保 证 切 削 力小 能 大 干 夹 套 的 承 载 力 。 另一 种 接 口也 是 为 带 孔 滚 刀而 设 计 的 , 丰 轴 端 部 另 加 一 个端 画 驱 动 器 , 过 一 个 弓 通 之 平 行 的 轴 将 主 轴 的 力矩 传 递 到 刀具 。 机 床 上 同 时 有 一个 特 殊 的夹 紧 心 轴将 这个 平 行 轴 夹 紧 。另外 , 刀托 座 的 设 计 也 很 重 滚 要, 轴承 的设 计 条 件 包 括两 点 , 保证 有 极 既 强 的 径 向 刚 度 , 对 滚 刀或 滚 刀 心 轴 不 能 又 有 过 大 的 轴 向 推 力 。 种 轴 向 推 力 在 力I 这 I 工 温度较 高时还会加火 。 土轴 采 用 一 个 角 接 触 推 力球 轴 承 来 保 证 足 够 的 径 向 刚 度 。 要 确 保 轴 承 对 滚 刀具 有 足 够 的 承 载 力 , 时 同 又 能 快 速 换 刀 , 须 注 意 托 鹰 与滚 7 心 轴 必 ] 接 触 部 位 的形 状 。 触部 位 必 须 尢 间 隙 、 接 刚 性 好 、 以 把 滚 刀 的旋 转 运 动 传递 到轴 承 , 可 而 形 成 的 轴 向 推 力 又 较 小 , 时 能 保 持 滚 同 刀 的 径 向旋 转 。 度 托 庵 的 设 讣 可 以成 功 锥 地解决这个问题 。
切削加工热力耦合建模及其试验研究
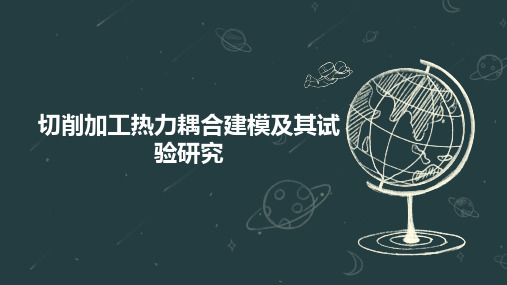
文献综述
自20世纪初以来,切削加工热力耦合建模及其试验研究一直是机械工程领域的 研究热点。早期的研究主要集中在基于经验的公式拟合和简化模型的建立上, 如摩擦学、传热学和弹塑性力学等。随着计算机技术和数值计算方法的快速发 展,研究者们开始采用数值模拟方法对切削加工过程中的热力耦合行为进行模 拟,从而更准确地预测切削温度和刀具磨损等情况。
3、本研究采用实验与数值模拟相结合的方法,对切削加工过程中的热力耦合 行为进行了深入研究。通过考虑材料变形、摩擦生热和热传导等多种因素,建 立了相应的数学模型,从而更准确地预测切削温度和刀具磨损等情况。
参考内容
高速切削加工技术及其加工工艺在现代化工业制造中具有广泛的应用前景。这 种技术以其高效率、高精度和高表面质量的特点,成为机械制造、汽车工业、 航空航天等领域的热点技术。本次演示将详细介绍高速切削加工技术的定义和 特点,高速切削加工工艺及其在各行业的应用前景,最后对高速切削加工技术 的未来发展方向和挑战进行总结。
高速切削加工工艺是指利用高速切削加工技术进行切削加工的工艺流程和技术 参数。高速切削加工工艺包括以下步骤:首先,选用合适的刀具材料,如硬质 合金、陶瓷等,这些材料具有高硬度、高耐磨性和高耐热性等特点。其次,确 定合理的切削参数,如切削速度、进给速度、刀具角度等,这些参数需要根据 工件材料、刀具材料等因素进行调整。最后,选择适合的冷却剂和润滑剂,以 降低切削温度和减小刀具磨损。
高速切削加工技术是一种采用高速度、高进给和高转速的切削加工方法。它具 有以下特点:首先,高速切削加工技术可以实现高效率的加工,有效缩短了加 工周期,提高了生产效率。其次,高速切削加工技术可以实现高精度的加工, 有效提高了工件的精度和表面质量。最后,高速切削加工技术还可以实现低温 切削,降低了切削力和切削热,避免了工件的热变形和烧伤等问题。
绿色制造—高速干切削概述

绿色制造—高速干切削概述高速干切削是一种先进的切削加工技术,它在提高加工效率的同时,也有效地降低了环境污染和能源消耗。
本文将概述高速干切削技术的原理、应用领域以及对绿色制造的积极影响。
一、高速干切削的原理高速干切削是指在高速旋转的切削工具与工件接触时,不使用冷却液进行冷却和润滑的切削过程。
其原理是通过提高切削速度、降低加工温度和减少摩擦力来实现高效率的切削加工。
在高速干切削过程中,切削温度相对较低,切削力较小,从而减少了工具磨损和加工成本。
二、高速干切削的应用领域高速干切削技术广泛应用于机械制造、航空航天、汽车、电子、光学器件等领域。
例如,高速干切削技术在汽车制造中被用于发动机零部件的加工,可大幅提高生产效率和减少废液处理成本。
同时,在电子器件制造领域,高速干切削技术具备高精度和高表面质量等优势,被广泛应用于半导体芯片、光纤组件等的加工。
三、高速干切削对绿色制造的影响1. 节约能源:高速干切削不需要冷却液,大大减少了能源消耗。
与传统切削相比,高速干切削可节约能源30%以上,减少了对环境的负荷。
2. 降低环境污染:传统切削过程中,大量的冷却液被使用后会成为废液,对环境造成严重的污染。
而高速干切削技术无需冷却液,减少了废液的产生,降低了对水资源的消耗和水污染的风险。
3. 提高生产效率:高速干切削技术采用高速切削工具和高速传动设备,加工速度更快,提高了生产效率。
同时,由于无需处理废液等附加工序,工艺流程更加简化,进一步提高了生产效率。
4. 减少工具磨损:高速干切削的切削速度相对较高,与工件接触时间短,减少了工具磨损。
这可以延长工具的使用寿命,减少了资源消耗和废弃物的产生。
综上所述,高速干切削技术具有降低能源消耗、减少环境污染、提高生产效率和减少工具磨损的优势,为绿色制造的实践提供了重要的技术支持。
随着高速干切削技术的进一步发展和应用,相信将在制造业领域取得更加显著的绿色效益和可持续发展。
小模数齿轮的高速干切滚齿技术
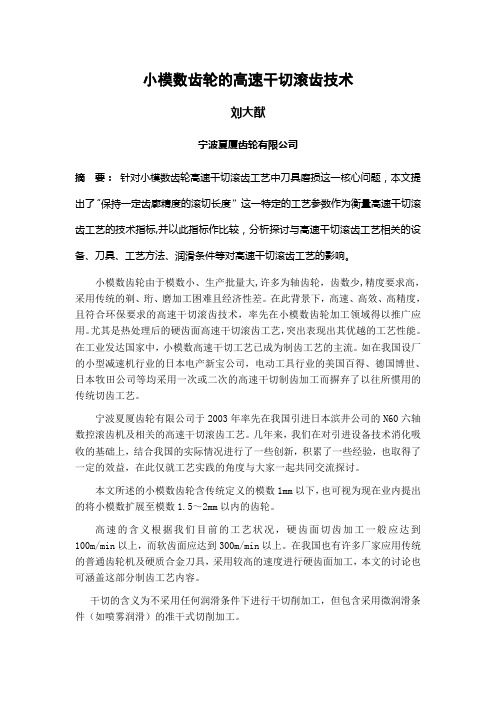
小模数齿轮的高速干切滚齿技术刘大猷宁波夏厦齿轮有限公司摘要:针对小模数齿轮高速干切滚齿工艺中刀具磨损这一核心问题,本文提出了“保持一定齿廓精度的滚切长度”这一特定的工艺参数作为衡量高速干切滚齿工艺的技术指标,并以此指标作比较,分析探讨与高速干切滚齿工艺相关的设备、刀具、工艺方法、润滑条件等对高速干切滚齿工艺的影响。
小模数齿轮由于模数小、生产批量大,许多为轴齿轮,齿数少,精度要求高,采用传统的剃、珩、磨加工困难且经济性差。
在此背景下,高速、高效、高精度,且符合环保要求的高速干切滚齿技术,率先在小模数齿轮加工领域得以推广应用。
尤其是热处理后的硬齿面高速干切滚齿工艺,突出表现出其优越的工艺性能。
在工业发达国家中,小模数高速干切工艺已成为制齿工艺的主流。
如在我国设厂的小型减速机行业的日本电产新宝公司,电动工具行业的美国百得、德国博世、日本牧田公司等均采用一次或二次的高速干切制齿加工而摒弃了以往所惯用的传统切齿工艺。
宁波夏厦齿轮有限公司于2003年率先在我国引进日本滨井公司的N60六轴数控滚齿机及相关的高速干切滚齿工艺。
几年来,我们在对引进设备技术消化吸收的基础上,结合我国的实际情况进行了一些创新,积累了一些经验,也取得了一定的效益,在此仅就工艺实践的角度与大家一起共同交流探讨。
本文所述的小模数齿轮含传统定义的模数1mm以下,也可视为现在业内提出的将小模数扩展至模数1.5~2mm以内的齿轮。
高速的含义根据我们目前的工艺状况,硬齿面切齿加工一般应达到100m/min以上,而软齿面应达到300m/min以上。
在我国也有许多厂家应用传统的普通齿轮机及硬质合金刀具,采用较高的速度进行硬齿面加工,本文的讨论也可涵盖这部分制齿工艺内容。
干切的含义为不采用任何润滑条件下进行干切削加工,但包含采用微润滑条件(如喷雾润滑)的准干式切削加工。
一、建立一个工艺比较系,确立比较指标我们从实践中知道,高速干切滚齿工艺的实施牵涉到设备、刀具、工艺及润滑条件等。
绿色高速干式切削技术的研究内容及其发展_绿色制造_先进制造技术_489

绿色高速干式切削技术的研究内容及其发展_绿色制造_先进制造技术1 引言制造业是人类社会的传统产业,它的历史可以追溯到远古时代,人们磨制石器、铜器和铁器用来捕猎。
制造业为人类社会带来物质财富的同时,又给环境造成了严重的污染。
而切削加工作为制造技术的主要基础工艺,是产生污染的重要原因之一。
金属切削加工方法有湿式和干式切削法之分。
目前采用最多的是湿式切削法(即在金属切削加工时,用一定压力和流量的液体(切削液)连续不断地冷却、润滑刀具和工件加工部件的方法)。
这种方法已经使用多年,通常在金属切削加工时使用切削液主要有3个功能:润滑作用,冷却作用,清洗和排屑作用。
这些功能对工件已加工表面质量和刀具耐用度具有明显的影响。
随着高速切削加工技术的迅猛发展,加工过程中切削液的用量越来越大,有时高达80-1OOL/min。
但大量使用切削液造成了许多负面影响,主要表现在以下几个方面。
(1)增加了制造成本。
据国外许多统计资料表明,切削液及切削液的供给、保养、回收及切削废液的处理等费用加在一起,占总制造成本的13%-17%,而刀具消耗的费用仅占制造成本的2%-4%。
(2)造成了环境污染问题。
切削液是金属切削加工中造成环境污染的一个重要根源。
如乳化液不仅含有油,而且含有烧碱、油酸酯、乙醇和苯酚等有害物质。
如果这些切削液未经处理直接排人外界,会对环境造成严重污染。
(3)直接危害操作工人的身体健康。
切削液产生的油烟会引起工人肺部和呼吸道的多种疾病。
切削液与人体直接接触会诱发多种皮肤病[1]。
人类社会已经迈入2l世纪,随着制造技术的发展和环保意识的提高,发展以绿色无污染的高速切削工艺和加工方法成为人们追求的目标。
在这种背景下,取消或减少切削液和润滑剂的使用已成为金属切削工艺发展的必然趋势,于是干式切削工艺的研究便应运而生,干式切削(Dry Cutting)的概念逐步形成。
2 高速干式切削加工技术的提出及发展从20世纪90年代开始,国外对干式切削技术进行了大量研究,1995年干切削的科学意义被正式确立,1997年的国际生产工程研究会(CIRP)年会上,德国Aachen工业大学的F.Klocke教授作了“干切削”的主题报告;1999年1月在美国国家科学基金“设计与制造学科”受资助者会议上,国际著名的刀具制造厂MAPAL公司的总裁B.P.Erdel博士也作了有关美国干切削发展的主题报告[2]。
干式滚齿刀具的参数化设计及优化
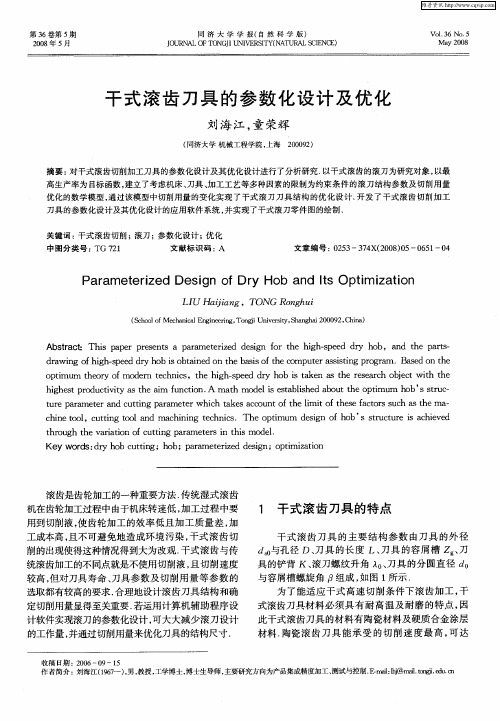
优化的数学模型 , 通过该模型 中切削用量 的变化 实现 了干式滚 刀刀具结 构 的优 化设计 , 开发 了 干式 滚齿 切削加工
刀具的参数化设计及其优化设计的应用软件系统 , 并实现 了干式滚刀零件 图的绘制 , 关键词 : 干式滚齿切削 ;滚刀 ; 参数化设计 ;优化
中 图 分 类 号 : G 2 T 71 文献标识码 : A 文 章 编 号 : 2 3 7 X(0 8 0 —0 5 —0 0 5 —3 4 2 0 )5 6 1 4
Vl . 6 No. 0 3 1 5 Ma 08 y2 0
干 式滚 齿 刀具 的 参数 化 设 计 及 优 化
刘 海 江 , 荣辉 童
( 同济大学 机械 工程学 院 , 上海 209 ) 0 0 2
摘要 : 对干式滚齿切削加工刀具的参数化设计及其 优化设计进行了分析研究 . 以干式 滚齿的滚刀为研究对象 , 以最 高生产率为 目标函数 , 建立 了考虑机床 、 刀具 、n v  ̄ m-_ 艺等多种 因素 的限制为约束条 件的滚 刀结构参数及 切削用量
A s r c = Th s p p r p e e t a a e e ie e in f r t e h g —p e r o , a d t e p rs b ta t i a e r s n s a p r m t rz d d s o h ih s e d d y h b g n h a t— d a n f ih s e d d y h b i o t i e n t eb s f h o p t ra ss ig p o r m .B s d o h r wi g o g —p e r o b an d o h a i o e c m u e s it r g a h s s t n a e nt e
齿轮滚齿加工及热后精加工的技术状况分析-2128
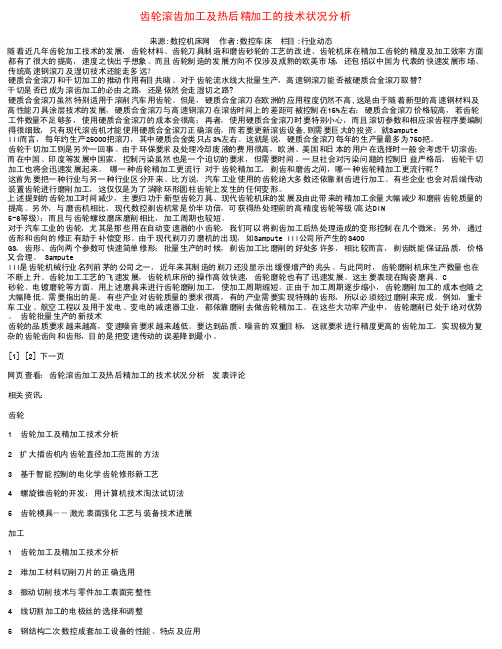
齿轮滚齿加工及热后精加工的技术状况分析来源:数控机床网 作者:数控车床 栏目:行业动态 随着近几年齿轮加工技术的发展,齿轮材料、齿轮刀具制造和磨齿砂轮的工艺的改进、齿轮机床在精加工齿轮的精度及加工效率方面都有了很大的提高,速度之快出乎想象。
而且齿轮制造的发展方向不仅涉及成熟的欧美市场,还包括以中国为代表的快速发展市场。
传统高速钢滚刀及湿切技术还能走多远?硬质合金滚刀和干切加工的推动作用有目共睹。
对于齿轮流水线大批量生产,高速钢滚刀能否被硬质合金滚刀取替?干切是否已成为滚齿加工的必由之路,还是依然会走湿切之路?硬质合金滚刀虽然特别适用于滚削汽车用齿轮。
但是,硬质合金滚刀在欧洲的应用程度仍然不高,这是由于随着新型的高速钢材料及高性能刀具涂层技术的发展,硬质合金滚刀与高速钢滚刀在滚齿时间上的差距可被控制在15%左右;硬质合金滚刀价格较高,若齿轮工件数量不足够多,使用硬质合金滚刀的成本会很高;再者,使用硬质合金滚刀时要特别小心,而且滚切参数和相应滚齿程序要编制得很细致,只有现代滚齿机才能使用硬质合金滚刀正确滚齿,而若要更新滚齿设备,则需要巨大的投资。
就Samputeili而言,每年约生产25000把滚刀,其中硬质合金类只占3%左右。
这就是说,硬质合金滚刀每年的生产量最多为750把。
齿轮干切加工则是另外一回事。
由于环保要求及处理冷却废液的费用很高,欧洲、美国和日本的用户在选择时一般会考虑干切滚齿;而在中国、印度等发展中国家,控制污染虽然也是一个迫切的要求,但需要时间。
一旦社会对污染问题的控制日益严格后,齿轮干切加工也将会迅速发展起来。
哪一种齿轮精加工更流行 对于齿轮精加工,剃齿和磨齿之间,哪一种齿轮精加工更流行呢?这首先要把一种行业与另一种行业区分开来。
比方说,汽车工业使用的齿轮绝大多数还依靠剃齿进行加工。
有些企业也会对后端传动装置齿轮进行磨削加工,这仅仅是为了消除环形圆柱齿轮上发生的任何变形。
上述提到的齿轮加工时间减少,主要归功于新型齿轮刀具、现代齿轮机床的发展及由此带来的精加工余量大幅减少和磨前齿轮质量的提高。
齿轮滚齿加工及热后精加工的技术状况分析

随着近⼏年齿轮加⼯技术的发展,齿轮材料、齿轮⼑具制造和磨齿砂轮的⼯艺的改进、齿轮机床在精加⼯齿轮的精度及加⼯效率⽅⾯都有了很⼤的提⾼,速度之快出乎想象。
⽽且齿轮制造的发展⽅向不仅涉及成熟的欧美市场,还包括以中国为代表的快速发展市场。
传统⾼速钢滚⼑及湿切技术还能⾛多远? 硬质合⾦滚⼑和⼲切加⼯的推动作⽤有⽬共睹。
对于齿轮流⽔线⼤批量⽣产,⾼速钢滚⼑能否被硬质合⾦滚⼑取替?⼲切是否已成为滚齿加⼯的必由之路,还是依然会⾛湿切之路? 硬质合⾦滚⼑虽然特别适⽤于滚削汽车⽤齿轮。
但是,硬质合⾦滚⼑在欧洲的应⽤程度仍然不⾼,这是由于随着新型的⾼速钢材料及⾼性能⼑具涂层技术的发展,硬质合⾦滚⼑与⾼速钢滚⼑在滚齿时间上的差距可被控制在15%左右;硬质合⾦滚⼑价格较⾼,若齿轮⼯件数量不⾜够多,使⽤硬质合⾦滚⼑的成本会很⾼;再者,使⽤硬质合⾦滚⼑时要特别⼩⼼,⽽且滚切参数和相应滚齿程序要编制得很细致,只有现代滚齿机才能使⽤硬质合⾦滚⼑正确滚齿,⽽若要更新滚齿设备,则需要巨⼤的投资。
就Samputensili⽽⾔,每年约⽣产25000把滚⼑,其中硬质合⾦类只占3%左右。
这就是说,硬质合⾦滚⼑每年的⽣产量最多为750把。
齿轮⼲切加⼯则是另外⼀回事。
由于环保要求及处理冷却废液的费⽤很⾼,欧洲、美国和⽇本的⽤户在选择时⼀般会考虑⼲切滚齿;⽽在中国、印度等发展中国家,控制污染虽然也是⼀个迫切的要求,但需要时间。
⼀旦社会对污染问题的控制⽇益严格后,齿轮⼲切加⼯也将会迅速发展起来。
哪⼀种齿轮精加⼯更流⾏对于齿轮精加⼯,剃齿和磨齿之间,哪⼀种齿轮精加⼯更流⾏呢? 这⾸先要把⼀种⾏业与另⼀种⾏业区分开来。
⽐⽅说,汽车⼯业使⽤的齿轮绝⼤多数还依靠剃齿进⾏加⼯。
有些企业也会对后端传动装置齿轮进⾏磨削加⼯,这仅仅是为了消除环形圆柱齿轮上发⽣的任何变形。
上述提到的齿轮加⼯时间减少,主要归功于新型齿轮⼑具、现代齿轮机床的发展及由此带来的精加⼯余量⼤幅减少和磨前齿轮质量的提⾼。
基于切削热-力耦合效应的表面强化技术及其工艺试验研究
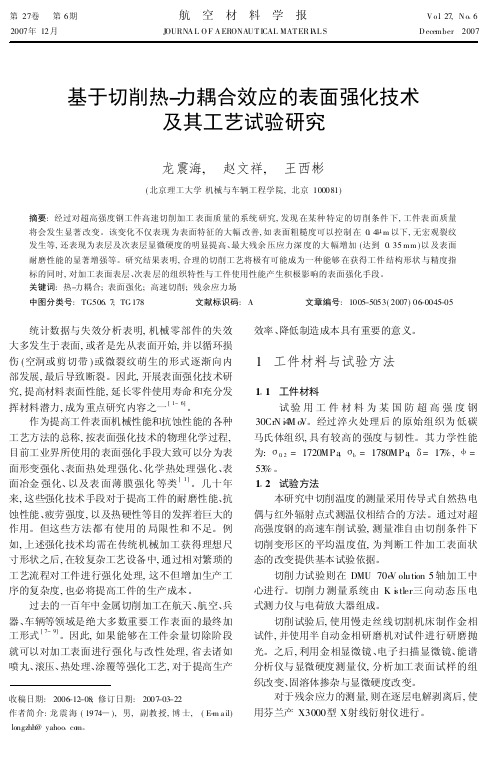
钢材料时 , 非自由切削效应 ( 切削副刃的 切屑流动 干涉明显加强 ) 将占据主导作 用。因此, 当切 削速 度提高至一定范围后, 背吃刀量与每齿进给量之间 的交互作用对切削力产生显著的正增影响。不仅如 此, 高速铣削过程中刀具切入、 切出工件时所引发的 冲击振动也大幅增加切削过程的不稳定性
[ 1]
02
= 1720MP a ,
b
= 1780MP a ,
= 17 %,
=
53 %。 1 2 试验方法 本研究中切削温度的测量采用传导式自然热电 偶与红外辐射点式测温仪相结合的方法。通过对超 高强度钢的高速车削试验, 测量准自由切削条件下 切削变形区的平均温度值, 为判断工件加工表面状 态的改变提供基本试验依据。 切削力试验则在 DMU 70e V olution 5 轴加工中 心进行。切削力 测量系统由 K is tler 三向动态 压电 式测力仪与电荷放大器组成。 切削试验后, 使用慢走丝线切割机床制作金相 试件 , 并使用半自动金相研磨机对试件进行研磨抛 光。之后 , 利用金相显微镜、 电子扫描显微镜、 能谱 分析仪与显微硬度测量仪, 分析加工表面试样的组 织改变、 固溶体掺杂与显微硬度改变。 对于残余应力的测量, 则在逐层电解剥离后 , 使 用芬兰产 X3000 型 X 射线衍射仪进行。
收稿日期 : 2006 -12-08; 修订日期 : 2007 -03-22 作者简 介 : 龙 震 海 ( 1974 longzhh@ yahoo co m。 ), 男 , 副教 授 , 博 士 , ( Em a il)
[ 1~ 6]
效率、 降低制造成本具有重要的意义。
1 工件材料与试验方法
1 1 工件材料 试验 用 工 件 材 料 为 某 国 防 超 高 强 度 钢 30CrN i4 M oV。经过淬火处理后 的原始组织为 低碳 马氏体组织, 具有较高的强度与韧性。其力学性能 为:
高速斜角切削过程的热-力耦合分析与研究
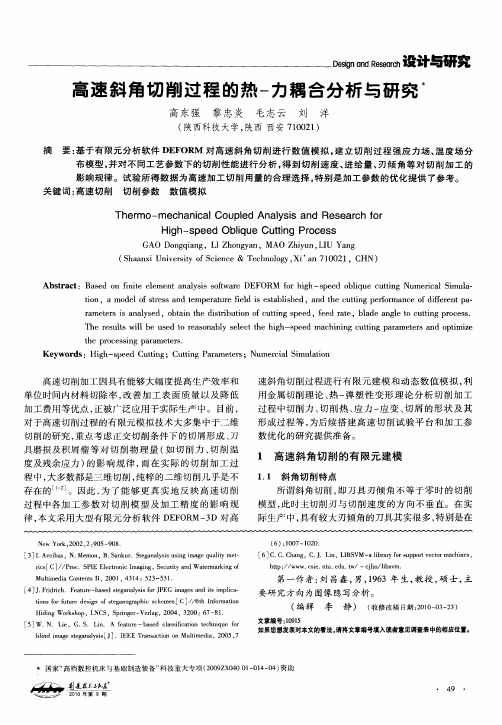
高 东 强 黎 忠 炎 毛 志 云 刘 洋
( 陕西 科技 大 学 , 陕西 西 安 7 02 ) 10 1
摘 要 : 于 有 限元分 析软 件 D F RM 对 高速 斜角 切 削进 行 数 值 模 拟 , 立切 削过 程 强应 力场 、 度 场分 基 E O 建 温 布模 型 , 对 不 同工艺 参数 下 的切 削性 能进 行分 析 , 到切 削 速 度 、 给量 、 并 得 进 刃倾 角 等对 切 削加 工 的
[ ] . . h n ,C J i, I S M- l rr o up  ̄vc r ahns 6 C C C a g ..Ln LB V a i a r po et m cie, b yf s o
具磨 损及 积 屑瘤 等 对 切 削 物 理 量 ( 切 削 力 、 削 温 如 切
度及 残余 应力 ) 的影 响 规 律 , 在 实 际 的切 削加 工 过 而
程 中 , 多数 都是 三维 切 削 , 大 纯粹 的二维 切 削几 乎是不 存在 的 - 。 因此 , 了能 够 更 真 实 地 反 映高 速 切 削 1] 2 为 过程 中各 加 工 参 数 对 切 削 模 型 及 加 工 精 度 的影 响规
t r c s i g pa a ee s he p o e sn r m t r . Ke ywo ds Hih—s e d Cutn r : g p e t g;Cu tn r me e s;Nume c a i l t n i ti g Paa tr r ilS mu a i o
影响 规律 。试 验所得 数 据 为高速 加 工切 削 用量 的合 理选择 , 别是 加工 参数 的优 化提 供 了参 考。 特
高速干切滚齿工艺参数的多目标优化与决策方法

第32卷第7期中国机械工程V o l .32㊀N o .72021年4月C H I N A M E C HA N I C A LE N G I N E E R I N Gp p.832G838高速干切滚齿工艺参数的多目标优化与决策方法倪恒欣㊀阎春平㊀陈建霖㊀侯跃辉㊀陈㊀亮重庆大学机械传动国家重点实验室,重庆,400044摘要:为降低高速干切滚齿加工能耗㊁提高滚齿加工质量,提出一种基于改进多目标灰狼优化(MO GWO )算法和逼近理想解排序法(T O P S I S )的高速干切滚齿工艺参数多目标优化与决策方法.分析了滚齿工艺参数,将切削参数和滚刀参数作为优化变量,构建了面向最小加工能耗和最优加工质量的多目标优化模型,采用改进MO GWO 算法对所建的模型进行迭代寻优,利用T O P S I S 对优化的工艺参数解进行多属性决策.实验结果验证了所提方法的有效性.关键词:高速干切滚齿;工艺参数;多目标优化;灰狼优化算法;逼近理想解排序法中图分类号:T H 16D O I :10.3969/j .i s s n .1004 132X.2021.07.010开放科学(资源服务)标识码(O S I D ):M u l t i Go b j e c t i v eO p t i m i z a t i o na n dD e c i s i o n Gm a k i n g M e t h o do fH i g hS pe e d D r y G e a rH o b b i n g P r o c e s s i n g Pa r a m e t e r s N IH e n g x i n ㊀Y A N C h u n p i n g ㊀C H E NJ i a n l i n ㊀HO U Y u e h u i ㊀C H E N L i a n gS t a t eK e y L a b o r a t o r y o fM e c h a n i c a lT r a n s m i s s i o n ,C h o n g q i n g U n i v e r s i t y ,C h o n g q i n g,400044A b s t r a c t :T o r e d u c e e n e r g y c o n s u m p t i o n a n d i m p r o v e g e a r h o b b i n g q u a l i t y ,am u l t i Go b j e c t i v e o pGt i m i z a t i o n a n d d e c i s i o n Gm a k i n g m e t h o d o f h i g h Gs p e e d d r y g e a r h o b b i n g p r o c e s s i n g p a r a m e t e r sw a s p r o Gp o s e db a s e do n i m p r o v e d m u l t i Go b j e c t i v e g r e y w o l f o p t i m i z a t i o n (MO GWO )a l go r i t h ma n dT O P S I S .T h e g e a r h o b b i n gp r o c e s s i n gp a r a m e t e r sw e r ea n a l y z e d ,a n dc u t t i n gpa r a m e t e r sa n dh ob p a r a m e t e r s w e r e t a k e na s o p t i m i z a t i o nv a r i a b l e s .A m u l t i Go b j ec t i v eo p t i m i z a t i o n m ode lf o rm i n i m u me n e rg y c o n Gs u m p t i o na n do p t i m a l g e a rh o b bi n gq u a l i t y w a se s t a b l i s h e d .T h e i m p r o v e d MO GWOa l go r i t h m w a s u s e d t o o p t i m i z e t h em o d e l i t e r a t i v e l y ,a n dT O P S I Sw a s s u b s e q u e n t l y ut i l i z e d t om a k em u l t i Ga t t r i b u t e d e c i s i o n o n t h e o p t i m i z e d p r o c e s s i n g p a r a m e t e r s .E f f e c t i v e n e s s o f t h e p r o p o s e dm e t h o dw a s v e r i f i e db y e x pe r i m e n t a l r e s u l t s .K e y wo r d s :h i g hs p e e dd r yg e a rh o b b i n g ;p r o c e s s i n gp a r a m e t e r ;m u l t i Go b j e c t i v eo p t i m i z a t i o n ;g r e y w o l fo p t i m i z a t i o na l g o r i t h m ;t e c h n i q u ef o ro r d e r p r e f e r e n c eb y s i m i l a r i t y t oa ni d e a ls o l u t i o n (T O P S I S)收稿日期:20200525基金项目:国家重点研发计划(2020Y F E 0201000)0㊀引言高速干切滚齿工艺作为一种绿色高效的齿轮成形工艺,在加工过程中不使用切削液且切削速度高,近年来得到了大量的关注和研究[1].高速干切滚齿工艺对加工条件要求较高,不合理的加工工艺参数会严重影响齿轮的形状误差㊁齿向误差以及加工能耗.工艺参数优化与决策能有效优化加工工艺参数,而无须改变加工硬件环境.国内外学者在常见的机械加工方式如车削㊁磨削㊁铣削㊁钻削等工艺优化上已取得不错的研究成果,但大部分研究集中于经济型指标如加工成本㊁加工时间㊁加工质量等的优化,只有部分学者注意到环境因素的重要地位,将能耗㊁碳耗作为优化目标.对于滚齿工艺参数优化,相关文献较多着眼于刀具寿命㊁切削热能㊁加工成本㊁加工时间㊁加工能耗㊁加工精度等目标.K L O C K E 等[2]对滚齿的粗加工和精加工进行研究,将刀具寿命作为研究目标,通过不同的工艺设计来实现在两种切削过程中使用相同刀具.干式滚齿工艺不使用切削液,切削空间内的热能积累导致较大的机床热变形,针对此,Y A N G 等[3]建立了以切削空间平均温度最低为目标的热能平衡优化模型,并采用粒子群算法对优化模型进行了验证求解.考虑到干式滚削工艺中的滚刀寿命㊁机床热变形误差和齿轮工件质量对切削参数比较敏感,Z H A N G 等[4]提出了一种干式滚齿参数优化模型,并采用迭代测试方法来获取最优工艺参数.S A R I 等[5]对干式滚齿精加工中滚刀的磨损问题进行了研究,基于磨损研究和理论分析构建出面向实际应用的刀238具寿命方程,为滚刀参数优化决策提供了新的途径.S U N等[6]对齿轮的加工精度展开研究,将最小齿形几何误差作为优化目标,采用改进的粒子群算法对滚齿加工参数进行了优化.陈鹏等[7]以自动化加工效率和齿轮单件成本为优化目标,对齿轮高速干式滚切工艺参数优化展开了系统研究,构建了工艺参数自适应优化修正模型.李聪波等[8]以最小能耗和最短加工时间为目标,通过实验设计和帝国主义竞争算法对数控滚齿加工参数进行了优化求解.C A O等[9]将滚齿过程看作一个 黑箱 ,提出一种基于支持向量机和蚁狮优化算法的参数优化决策,并利用加工实例对滚齿工艺参数进行了低碳优化.上述研究主要通过建立工艺参数与待优化目标之间的映射关系,利用人工智能算法进行优化求解时,还需要将滚刀参数作为优化变量,建立以加工能耗和齿轮加工质量为优化目标的多目标参数优化方法,对多目标优化的求解获得的非支配解集进行重新排序和决策.鉴于此,本文针对具体的高速干切滚齿工艺优化问题展开研究,提出一种基于改进多目标灰狼优化(m u l t iGo b j e c t i v e g r e y w o l fo p t i m i z a t i o n, MO GWO)算法和逼近理想解排序法(t e c h n i q u e f o r o r d e r p r e f e r e n c eb y s i m i l a r i t y t oa n i d e a l s oGl u t i o n,T O P S I S)的高速干切滚齿工艺参数多目标优化与决策方法.分析了滚齿工艺参数,将切削参数(轴向进给速度㊁主轴转速)和滚刀参数(滚刀直径㊁滚刀头数)作为优化变量,构建了以最小加工能耗和最优加工质量为目标的多目标优化模型.采用改进MO GWO算法对所建模型进行迭代寻优,利用T O P S I S对优化得到的工艺参数解集进行多属性决策,获取性能排序后的工艺参数解,并通过对比结果验证本文方法和结果的有效性.1㊀滚齿工艺问题描述工艺参数是完成工艺过程的一系列技术数据.在滚齿加工中,机床性能参数㊁滚刀参数㊁齿轮工件参数㊁切削参数等共同组成了滚齿加工工艺参数,不同的工艺参数对齿轮加工质量㊁加工能耗㊁加工时间㊁加工成本㊁加工效率等目标有着显著的影响.实际加工中,机床和齿轮工件是由加工任务确定的,而切削参数和滚刀参数可进行相应的调整和优化.切削参数和滚刀参数的不同取值直接影响加工能耗和齿轮加工质量,而加工能耗㊁齿轮加工质量作为评价滚齿加工的环境指标和经济指标,已获得了企业的广泛关注.因此,本文针对上述滚齿工艺参数展开多目标优化与决策研究.本文将滚齿工艺问题描述表示为X={X1, X2, },其中,X i={w i,c i,h i}为第i(i=1,2, )个滚齿工艺参数集,w i㊁c i㊁h i分别为第i个滚齿工艺参数集中的齿轮工件参数㊁切削参数和滚刀参数,且w i㊁c i㊁h i分别包含多个工艺参数属性.针对某个齿轮工件加工,可以将滚齿工艺参数变量问题描述属性表示为w=(m n,z2,αn,β0, d2,B),其中,m n为齿轮模数;z2为齿轮齿数;αn 为齿轮压力角;β0为齿轮螺旋角;d2为齿轮外径; B为齿宽.与滚齿工艺参数变量问题对应的待决策工艺参数变量描述属性表示为c=(v a,n0, a p),h=(d0,z0,k),其中,v a为轴向进给速度;n0为主轴转速;a p为切削深度;d0为滚刀直径;z0为滚刀头数;k为滚刀槽数.待决策的工艺参数决定了滚齿工艺中的加工能耗和最终的齿轮加工质量,因此,如何优化和决策滚齿工艺参数成为了亟需解决的问题.2㊀高速干切滚齿工艺参数多目标优化模型2.1㊀优化变量目前的高速干切滚齿加工大多为小模数批量加工,且滚刀的切削深度对机床变形和主轴转速的影响较小,远远不足以影响切削效果,故将切削深度a p划分到工艺参数问题描述属性里,将对切削效果影响更大的v a㊁n0作为待优化切削参数;滚刀参数d0㊁z0对加工过程影响较大,因此将k 设为定值,将d0㊁z0作为待优化滚刀参数.2.2㊀多目标模型2.2.1㊀加工能耗模型常见的机械系统能耗表示方法有功率表示法和单位能耗法[10].对于滚齿加工来说,其总加工能耗可以表示为不同时段的能耗总和.一般来说,滚齿加工的待机时段㊁空切时段和切削时段是耗能最多的3个阶段,需要对这3个阶段的能耗进行系统分析,以构建滚齿加工能耗模型.滚齿机的启动过程是一个相对快速的过程,其能耗通常可以忽略不计.待机时段是指机床开启后的平稳运行阶段,机床的动力辅助系统已开始运行,但是与切削有关的动力部件尚未运转,此时的功率消耗基本是一个定值,很容易从功率分析仪中获取.待机时段的能耗E s=P s t s338高速干切滚齿工艺参数的多目标优化与决策方法 倪恒欣㊀阎春平㊀陈建霖等式中,P s㊁t s分别为滚齿待机时段的功率和时间.滚齿空切时段是指机床的滚刀主轴㊁工作台主轴等动力部件在无载荷工况下的运行阶段,此时的齿轮工件尚未被滚切.空切时段的能耗E a=P a t aP a=P s+P s c+P nP n=κ1n0+κ2n20[11]t a=j s(L a v a+L r v r)式中,P a㊁t a分别为空切时段的功率和时间;P s c为主轴系统运转时的辅助系统(如冷却润滑系统和风扇系统)的功率;P n为机器空载运行时的功率;κ1㊁κ2为机器空载运行功率系数;L a㊁L r分别为滚齿轴向空切长度和滚齿径向空切长度;v r为径向进给速度;j s为走刀次数,j s=1,2, .切削时段能耗E c=P c t cP c=P s+P s c+P n+P r+P a pP r=F c v=C K1K2K3m X n f Y a a Z p v-U z V2v/d0[12]v=πd0n0/1000P a p=ε1P r+ε2P2r t c=z2(E i n+B+U o u t)z0n0f a㊀㊀f a=z2v a n0z0式中,P c㊁t c分别为切削时段的功率和时间;P r为废料移除时的功率;F c为滚齿力;v为切削速度;C㊁X㊁Y㊁Z㊁U㊁V 为切削力参数指数;K1为工件材料修正系数;K2为工件硬度修正系数;K3为工件螺旋角修正系数;P a p为切削过程的额外损失功率;ε1㊁ε2为额外损失功率计算系数;E i n㊁U o u t分别为滚齿切入长度和滚齿切出长度;f a为轴向进给量.齿轮工件的总加工能耗E=E s+E a+E c.2.2.2㊀齿轮加工质量模型滚齿加工质量受齿形误差㊁齿向误差㊁齿廓包络误差㊁公法线变化误差㊁综合切向误差㊁综合径向误差㊁节距累积误差等因素的影响[2].滚刀在轴向切削时,以进给量f a为单位进行等距跳动,产生齿向误差;滚切齿坯时,实际得到的齿形是多边形,因此存在齿形误差[13].本文同时考虑齿向误差和齿形误差,以两者组成的综合误差来评价齿轮加工质量,综合误差越小,齿轮加工质量越好.齿向误差δx和齿形误差δy分别为δx=(f a c o sβ0)2s i nαn 4d0δy=π2z20m n s i nαn 4z2k2为更全面地描述齿轮加工质量,引入权重系数w1㊁w2(w1+w2=1)来考虑δx和δy对滚齿加工质量的贡献程度,齿轮加工质量Q表示为Q=w1δx+w2δy2.3㊀优化模型和约束条件基于上述分析,建立了以降低滚齿加工能耗㊁提高滚齿加工质量为目标的多目标优化模型: m i n f(v a,n0,d0,z0)=(m i n E,m i n Q)(1)㊀㊀㊀s.t.㊀v a,m i nɤv aɤv a,m a x(2) n m i nɤn0ɤn m a x(3)F cɤF c,m a x(4)0.0312f2a/rɤR a(5)式中,v a,m i n㊁v a,m a x分别为轴向进给速度的最小值和最大值;n m i n㊁n m a x分别为主轴转速的最小值和最大值;F c,m a x 为最大滚齿力;r为滚刀刀尖半径;R a为表面粗糙度值.式(2)㊁式(3)分别限制了轴向进给速度和主轴转速;式(4)表示切削力应不大于最大切削力,以保证加工过程能够正常进行;式(5)表明滚齿加工必须满足基本的齿轮表面粗糙度要求.3㊀基于改进MO GWO算法和TO P S I S的多目标优化与决策方法3.1㊀基于改进MO G W O算法的解集寻优MO GWO算法[14]具有收敛性强㊁参数少㊁易实现等特点,在车间调度㊁参数优化㊁图像分类等领域广泛应用.本文所取的待优化工艺参数变量既包含连续的变量v a㊁n0㊁d0,又包含离散的变量z0.利用MO GWO算法优越的寻优性能,在满足各种变量约束的条件下,对高速干切滚齿工艺参数优化问题进行多目标求解.3.1.1㊀社会等级分层灰狼内部存在社会支配等级关系,狼群从上到下通常被划分为4个等级:α狼㊁β狼㊁δ狼㊁ω狼.处于第一等级的α狼是支配狼,负责捕食㊁栖息等决策活动,其余狼都必须服从α狼的命令.第二等级的β狼协助α狼作决策,是下一代α狼的第一候选者.第三等级的δ狼服从α狼和β狼,并支配第四等级的ω狼.ω狼对保持整个狼群的繁衍生存起着重要的支撑作用.优化时,候选狼的位置信息(v a,n0,d0,z0)(t)i表示第t次迭代时的第i个工艺参数解,猎物为本文待优化的目标.每次迭代时,工艺参数的优化过程由α狼㊁β狼㊁δ狼所代表的工艺参数解来指导完成.3.1.2㊀包围猎物搜索猎物时,灰狼会逐渐接近并包围猎物,灰狼活动行为的数学模型为D=C☉X p(t)-X(t)(6)X(t+1)=X p(t)-A☉D(7)A=2a r1-a E(8)C=2r2(9)438中国机械工程第32卷第7期2021年4月上半月式中,☉表示H a d a m a r d乘积操作;A㊁C为协同系数向量; X p(t)为最优工艺参数解的位置向量;X(t)为当前工艺参数解的位置向量;X(t+1)为第t+1次迭代时工艺参数解的位置向量;D为当前候选工艺参数解与最优工艺参数解之间的距离;a为更新系数;随机向量r1和r2中的元素取值区间为[0,1];E为元素全为1的向量,与r1的维数相同.本文主要改进a的变化方式,为使狼群能够在更大范围内搜索目标,a的更新方式为a=a i n i t-e x p(-l t/T)(10)式中,a i n i t表示初始值更新系数值;l为调节系数;T为迭代次数.3.1.3㊀狩猎为模拟灰狼的搜索行为,选出最佳候选工艺参数解的位置,在每次迭代寻优过程中,利用狼群中的α狼㊁β狼㊁δ狼来识别潜在猎物的位置,保留α狼㊁β狼㊁δ狼各自的位置信息,并根据已保留的位置信息搜索候选狼(包括ω狼)的位置信息.具体的狩猎行为及数学模型如图1所示,图中的R为猎物定义的随机圆半径,可以看出,候选狼的位置最终落在α狼㊁β狼㊁δ狼定义的随机圆内,即α狼㊁β狼㊁δ狼首先预测出潜在猎物(加工能耗㊁齿轮加工质量)的可能区域,然后候选狼在α狼㊁β狼㊁δ狼的指引下在猎物附近随机更新位置信息.图1㊀灰狼狩猎行为及数学模型F i g.1㊀H u n t i n g b e h a v i o r s a n dm a t h e m a t i c a lm o d e l so f g r e y w o l f 3.1.4㊀攻击猎物目标猎物停止移动时,狼群攻击猎物以完成整个捕食过程.当向量A的元素大于1时,灰狼尽量分散开,扩大搜寻猎物的范围;当向量A的元素小于-1时,候选狼的下一个位置可以是现在的位置或是猎物的位置;当向量A的元素取值在[-1,1]之间时,狼的下一个位置是当前位置和猎物位置之间的任何位置.整个优化过程根据灰狼位置的改变不断进行更新,直到得到最优的工艺参数.基于改进MO GWO算法的工艺参数寻优流程如图2所示.图2㊀基于改进MO G W O算法的工艺参数寻优流程图F i g.2㊀P r o c e s s i n gp a r a m e t e r o p t i m i z a t i o n f l o wc h a r tb a s e do n i m p r o v e dMO G W Oa l g o r i t h m 3.2㊀基于T O P S I S的工艺参数解集性能评估TO P S I S是一种针对现有评估指标进行优劣性能评价的方法[15],本文利用TO P S I S在决策问题上的优势,建立工艺参数性能决策矩阵,综合考虑加工能耗㊁齿轮加工质量与滚齿工艺参数之间的关系,对工艺参数解集的综合性能进行评估,具体的工艺参数性能排序过程如图3所示.图3中,P1㊁P2㊁ ㊁P n为经过MO GWO算法获取的多组非支配解,R=[r i j]nˑm是基于评价指标建立的决策矩阵,共n组待决策工艺参数㊁m 个评价指标,i表示第i组工艺参数,j表示第j个评价指标;B=[b i j]nˑm为对评价指标同向化处理后的矩阵,以使评价指标数值方向一致;S=[s i j]nˑm为正规化后的矩阵;w=(w1,w2, , w m)表示m个评价指标的权重向量;z i j为加权后向量的元素;最差参数方案z-=(z-1,z-2, ,z-m)538高速干切滚齿工艺参数的多目标优化与决策方法 倪恒欣㊀阎春平㊀陈建霖等图3㊀工艺参数性能排序过程图F i g.3㊀P r o c e s s c h a r t o f p r o c e s s i n gp a r a m e t e rp e r f o r m a n c e s e q u e n c i n g由每列元素的最差值组成;最优参数方案z+=(z+1,z+2, ,z+m)由每列元素的最优值组成;D-i 为第i组工艺参数与最差参数方案的距离;D+i为第i组工艺参数与最优参数方案的距离;E i为对第i组工艺参数的评分,E i越大,该组工艺参数解的性能越优.4㊀实验验证笔者采用Y E3120C N C7高速干切滚齿机加工小模数齿轮,加工中与能耗有关的参数[11]取值如下:P s=2200W,t s=5m i n,P s c=200W,κ1=-0.078,κ2=0.2ˑ10-5,ε1=0.035,ε2=0.13ˑ10-4;齿轮加工质量权重系数w1=w2=0.5.与加工过程有关的参数取值如下:m n=2.5mm,z2=45,αn=20ʎ,β0=17ʎ,B=45mm, E i n=2mm,U o u t=2mm,L a=21.168mm,L r=104.5mm,v r=1500mm/m i n,a p=8.45mm,k=17,j s=1.与切削力相关的参数[12]取值如下: C=18.2,X=1.75,Y=0.65,Z=0.81,U=0.26, V=0.27,K1=1,K2=1.05,K3=1.11.基于MA T L A B编写改进MO GWO算法,设置灰狼数目N=20,最大迭代次数T=200,参数维度为4,网格数目为10,网格膨胀参数为0.1,初始更新系数a i n i t=2,调节系数l=2,各工艺参数的取值范围为68mm/m i nɤv aɤ92mm/m i n650r/m i nɤn0ɤ780r/m i nd0=78mm,79mm, ,89mmz0=2,3经过算法迭代后的工艺参数解集如表1所示,迭代寻优过程如图4所示.表1㊀经MO G W O寻优后的工艺参数解集T a b.1㊀S o l u t i o n s e t s o f p r o c e s s p a r a m e t e r s o p t i m i z e db y MO G W O工艺参数解工艺参数解集优化目标值F a(mm/m i n)n0(r/m i n)d0(mm)z0Q(mm)E(J)P192.00780.008920.059139532.85P292.00770.448830.08278096.10P392.00780.008930.41162001.60P468.00650.007820.11275028.91P568.12751.927820.077123726.31P680.76780.008930.37770749.87P769.97780.008930.0187912967.43P868.00780.008930.01715020240.11P968.00780.008930.0189276028.27P1068.00752.458930.0196997636.35P1174.33780.008930.0211553378.30P1268.93728.768130.028242757.99P1376.55780.008930.024459793.79P1468.00754.068930.0202506325.94P1574.55780.008930.022731206.51P1668.00760.208930.0211061023.99图4㊀迭代寻优结果F i g.4㊀I t e r a t i v e o p t i m i z a t i o n r e s u l t s㊀㊀分析上述结果发现,随着Q的增大,E逐渐减小.上述解中的滚刀头数z0=3的解集方案较多,增加滚刀头可以缩短滚齿切削时间,降低切削阶段的加工能耗.由表1可知,寻优后得到16个工艺参数解,获取的解中存在着一些劣解,解P8㊁P9的性能需要基于TO P S I S进行重新评估.表1中,滚刀直径d0=89mm对应的工艺参数解较多,更大的直径可以适当缩短齿轮切削时间以提高生产效率,此外,大直径滚刀使得滚刀内孔相对较大,增大滚刀的刚性,延长使用寿命.由图5可以看出,v a与E㊁Q之间没有一个确定的约束关系,较大的v a会导致较小的加工能耗638 中国机械工程第32卷第7期2021年4月上半月和较大的滚齿误差;较大的n 0会导致较高的加工能耗和较大的滚齿误差.由此可知,要获取最小的加工能耗和最优的齿轮加工质量,需要考虑实际加工对加工能耗和齿轮加工质量的要求,对优化后的工艺参数解集进行决策.(a )v a GE 关系图(b )v a GQ 关系图(c )n 0GE 关系图(d )n 0GQ 关系图图5㊀工艺参数变量与优化目标之间的关联关系图F i g .5㊀R e l a t i o nd i a gr a m sb e t w e e n p r o c e s s p a r a m e t e r v a r i a b l e s a n do p t i m i z a t i o no b je c t i v e s 为了获取直观明确的工艺参数解,以最小加工能耗和最优齿轮加工质量为目标,将m i n E ㊁m i n Q 作为工艺参数解性能评价指标,对MO GWO 算法寻优得到的工艺参数解进行多属性决策.加工能耗㊁齿轮加工质量分别为环境评价指标和经济评价指标,对滚齿加工的影响作用是相同的,因此本文设置权重w E =w Q =0.5,并按照图3所示的流程建立决策矩阵,依次进行矩阵规范化处理㊁理想解获取㊁参数解综合评价,以评估出性能更优的工艺参数解,决策后的工艺参数解如表2所示.表2㊀决策后的工艺参数解集T a b .2㊀S o l u t i o n s o f d e c i s i v e p r o c e s s i n gpa r a m e t e r s 排序评分对应解排序评分对应解10.1602P 890.0336P 220.1499P 3100.0312P 530.1427P 6110.0223P 1140.1176P 9120.0221P 150.1036P 7130.0151P 1660.0935P 10140.0104P 1570.0482P 4150.0071P 1380.0359P 14160.0065P 12㊀㊀由表2中的评分可看出工艺参数解P 8㊁P 3㊁P 6为相对较优的解,解P 8调整后的工艺参数v a =68mm /m i n ,n 0=780r /m i n ,d 0=89mm ,z 0=3可优先作为滚齿加工的工艺参数.以提高齿轮加工质量为首要目标时,应采用解P 8对应的工艺参数;以降低能耗为首要目标时,应采用解P 3对应的工艺参数,即v a =92mm /m i n ,n 0=780r /m i n ,d 0=89mm ,z 0=3.根据优化结果,工艺人员可按照实际加工要求选取合理的工艺参数解集,在加工能耗和滚齿加工质量上达到一个最优的平衡.为了进一步验证本文所提方法的有效性,采用标准灰狼算法构建多目标优化模型,算法基本参数与前文保持一致,采用TO P S I S 对结果进行排序和决策.2种方法获取的最优解如表3所示,本文所提方法使加工能耗降低了5.59%,齿轮误差降低了23.53%.表3㊀结果对比T a b .3㊀C o m pa r i s o no f r e s u l t s 方法v a (mm /m i n )n 0(r /m i n )d 0(mm )z 0Q(mm )E(J)本文方法68.00780.008930.01715020240.11传统算法76.65745.918930.02115860292.915㊀结论(1)基于高速干切滚齿工艺过程,分析了滚齿工艺参数,将轴向进给速度㊁主轴转速㊁滚刀直径㊁738 高速干切滚齿工艺参数的多目标优化与决策方法倪恒欣㊀阎春平㊀陈建霖等滚刀头数作为待决策变量,系统分析了滚齿加工能耗的构成及齿轮加工质量的表征形式,构建了以最小加工能耗㊁最优加工质量为目标的多目标优化模型.(2)本文利用改进MO GWO算法对多目标优化模型进行求解,获取了多组工艺参数解,并通过T O P S I S对优化的工艺参数解进行多属性决策,得到性能评估后的工艺参数解集.与传统灰狼算法优化结果的对比验证了本文方法的有效性.本文针对加工能耗和齿轮加工质量进行了综合优化,为体现本文方法及结果的实用性,后续将开展相关的切削试验.另外,考虑到废弃刀具带来的环境问题,如何建立工艺参数与刀具能耗㊁刀具寿命之间的关联关系,将是下一步的研究方向.参考文献:[1]㊀K A R P U S C H E W S K I B,K N O C H E HJ,H I P K E M,e t a l.H i g hP e rf o r m a n c eG e a r H o b b i ng w i t hP o wGd e rGm e t a l l u r g i c a l H i g hGs p e e dGs t e e l[J].P r o c e d i aC I R P,2012,1:196G201.[2]㊀K L O C K E F,LÖP E N HA U S C,S A R I D.P r o c e s sC o n c e p t sf o r G e a r F i n i s h H o b b i n g[J].P r o c e d i aC I R P,2016,41:875G880.[3]㊀Y A N G X,C A O H,L IB,e ta l.A T h e r m a lE n e r g yB a l a n c eO p t i m i z a t i o n M o d e l o fC u t t i n g S p a c eE n a bGl i n g E n v i r o n m e n t a l l y B e n i g nD r y H o b b i n g[J].J o u rGn a l o fC l e a n e rP r o d u c t i o n,2018,172:2323G2335.[4]㊀Z HA N G Y,C A O HJ,C H E NP,e t a l.A nA d a p t i v e P a r a m e t e rO p t i m i z a t i o n M o d e l a n dS y s t e mf o rS u sGt a i n a b l eG e a rD r y H o b b i n g i nB a t c hP r o d u c t i o n[J].J o u r n a l o f M e c h a n i c a l S c i e n c e a n d T e c h n o l o g y,2017,31(6):2951G2960.[5]㊀S A R ID,T R OßN,LÖP E N HA U SC,e t a l.D e v e l o pGm e n t o f a nA p p l i c a t i o nGo r i e n t e dT o o lL i f eE q u a t i o nf o rD r y G e a rF i n i s h H o b b i n g[J].W e a r,2019,426/427P a r tB:1563G1572.[6]㊀S U NS,WA N G S,WA N G Y,e ta l.P r e d i c t i o na n d O p t i m i z a t i o no fH o b b i n g G e a rG e o m e t r i cD e v i a t i o n s[J].M e c h a n i s m a n d M a c h i n e T h e o r y,2018,120:288G301.[7]㊀陈鹏,曹华军,张应,等.齿轮高速干式滚切工艺参数优化模型及应用系统开发[J].机械工程学报,2017,53(1):190G197.C H E N P e n g,C A O H u a j u n,Z HA N G Y i n g,e ta l.T h e P r o c e s s P a r a m e t e r s O p t i m i z a t i o n M o d e l o fG e a rH i g hGs p e e d D r y H o b b i n g a n dI t s A p p l i c a t i o nS y s t e m D e v e l o p m e n t[J].J o u r n a l o fM e c h a n i c a lE nGg i n e e r i n g,2017,53(1):190G197.[8]㊀李聪波,付松,陈行政,等.面向高效节能的数控滚齿加工参数多目标优化模型[J].计算机集成制造系统,2020,26(3):676G687.L I C o n g b o,F U S o n g,C H E N X i n g z h e n g,e t a l.M u l t iGo b j e c t i v eC N CG e a rH o b b i n g P a r a m e t e r sO pGt i m i z a t i o n M o d e lf o r H i g h E f f i c i e n c y a n d E n e r g yS a v i n g[J].C o m p u t e r I n t e g r a t e dM a n u f a c t u r i n g S y sGt e m,2020,26(3):676G687.[9]㊀C A O W D,Y A N C P,WU D J,e ta l.A N o v e l M u l t iGo b j e c t i v e O p t i m i z a t i o n A p p r o a c h o f M a c h iGn i n g P a r a m e t e r sw i t hS m a l l S a m p l eP r o b l e mi nG e a rH o b b i n g[J].I n t e r n a t i o n a l J o u r n a l o fA d v a n c e d M a n uGf a c t u r i ng T e ch n o l o g y,2017,93:4099G4110.[10]㊀刘飞,刘培基,李聪波,等.制造系统能量效率研究的现状及难点问题[J].机械工程学报,2017,53(5):1G11.L I U F e i,L I U P e i j i,L IC o n g b o,e ta l.T h eS t a t u ea n dD i f f i c u l t P r ob l e m s o fR e s e a rc h o nE n e r g y E f f iGc i e n c y o f M a n u f a c t u r i n g S y s t e m s[J].J o u r n a lo fM e c h a n i c a l E n g i n e e r i n g,2017,53(5):1G11.[11]㊀L IC,L I L,T A N G Y,e t a l.AC o m p r e h e n s i v eA pGp r o a c ht o P a r a m e t e r s O p t i m i z a t i o n o f E n e r g yGaGw a r eC N C M i l l i n g[J].J o u r n a l o f I n t e l l i g e n tM a n uGf a c t u r i n g,2019,30(1):123G138.[12]㊀WA N GS L,Y A N G Y,Z HO U J,e ta l.E f f e c to f M a c h i n i n g P r e c i s i o nC a u s e db y N C G e a rH o b b i n gD e f o r m a t i o n[J].A p p l i e d M e c h a n i c sa n d M a t e r iGa l s,2011,86:692G695.[13]㊀M I C HA L S K I J,S K O C Z Y L A S L.A C o m p a r a t i v eA n a l y s i so f t h eG e o m e t r i c a lS u r f a c eT e x t u r eo faR e a l a n dV i r t u a lM o d e l o f aT o o t hF l a n ko f aC yGl i n d r i c a lG e a r[J].J o u r n a l o f M a t e r i a l sP r o c e s s i n gT e c h n o l o g y,2008,204(1/3):331G342.[14]㊀M I R J A L I L I S,S A R E M I S,M I R J A L I L I S M,e t a l.M u l t iGo b j e c t i v eG r e y W o l fO p t i m i z e r:aN o v e lA lGg o r i t h mf o r M u l t iGc r i t e r i o n O p t i m i z a t i o n[J].E xGp e r t S y s t e m A p p l i c a t i o n,2015,47:106G119.[15]㊀WA N G E n d o n g.B e n c h m a r k i n g W h o l eGb u i l d i n gE n e r g y P e r f o r m a n c ew i t h M u l t iGc r i t e r i aT e c h n i q u ef o rO r d e r P r e f e r e n c e b y S i m i l a r i t y t o I d e a l S o l u t i o nU s i n g a S e l e c t i v e O b j e c t i v eGw e i g h t i n g A p p r o a c h[J].A p p l i e dE n e r g y,2015,146:92G103.(编辑㊀张㊀洋)作者简介:倪恒欣,女,1993年生,博士研究生.研究方向为智能制造系统与装备㊁绿色制造㊁工艺优化等.发表论文1篇.E m a i l:n i h e n g x i n1120@126.c o m.阎春平(通信作者),男,1973年生,教授㊁博士研究生导师.研究方向为智能制造系统与装备㊁绿色制造㊁制造系统工程等.发表论文30余篇.EGm a i l:y c p@c q u.e d u.c n.838中国机械工程第32卷第7期2021年4月上半月。
高速干式切削在齿轮加工中的应用研究
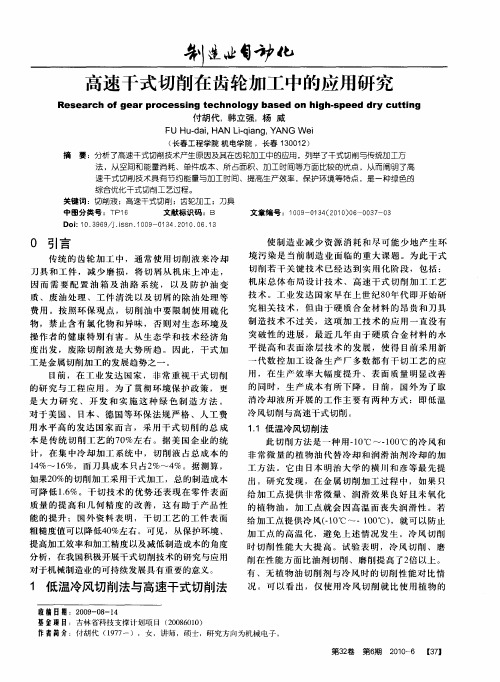
关键 词 :切削液 ;高速干式切削 ;齿轮加 工 ;刀具
中 图 分 类 号 :T 1 P 6 文 献 标 识 码 :B 文童 编 号 :1 0 — 1 4 2 1 ) 6 0 7 0 9 0 ( 00 0—0 3 — 3 0 3
Doi 1 3 6 / . s 1 0 -0 4. 0 . 6 1 : 9 9 j i n. 0 9 1 2 1 0 . 0. s 3 0 3
质 、废 油 处 理 、工 件 清 洗 以及 切 屑 的除 油 处 理 等 费 用 。按 照 环 保 观 点 ,切 削 油 中要 限 制 使 用 硫 化
究 相 关 技 术 ,但 由 于硬 质合 金材 料 的 昂贵 和 刀具
物 ,禁 止 含 有 氯 化 物 和 异 味 ,否 则 对 生 态 环 境 及
、 l
l I 8
高速干式切 削在齿轮加工 中的应 用研 究
Res ear f gearpr ch o ocess ng t i echnol ogy bas i ed on h gh- speed dr y cut i tng
付胡 代 ,韩 立 强,杨 威
0 引言
传 统 的 齿 轮 加 工 中 ,通 常 使 用 切 削 液 来冷 却
刀具 和 工 件 ,减 少 磨损 ,将 切 屑从 机 床 上 冲 走 , 因 而 需 要 配 置 油 箱 及 油 路 系 统 , 以 及 防 护 油 变
使 制 造 业 减 少 资 源 消 耗 和 尽 可 能 少 地 产 生 环
能 的提 升 ; 国外 资料 表 明 ,干 切 工艺 的 工件 表面 粗糙 度值 可 以降低 4 %左 右 。可 见 ,从保 护 环境 、 0
用 ,在 生 产 效 率 大 幅 度 提 升 、表 面 质 量 明 显 改 善 的 同时 ,生 产 成 本 有 所 下 降 。 目前 , 国外 为 了取
切削加工热力耦合建模及其试验研究
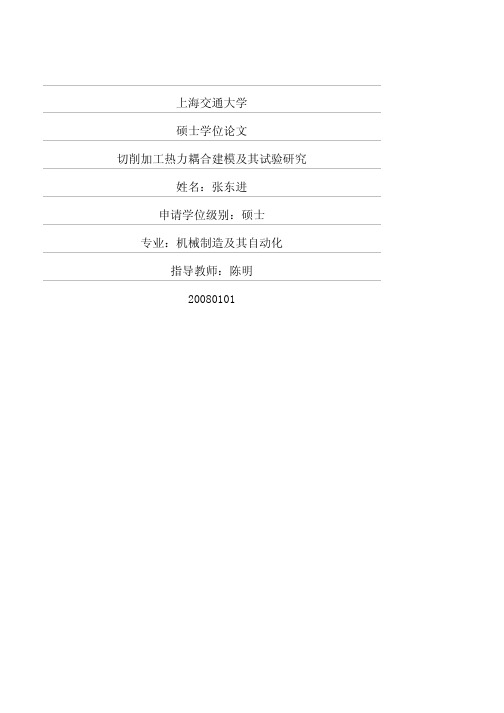
上海交通大学硕士学位论文
摘要
frequently and played a more and more important role in metal cutting field. This paper analyzes coupled thermo-mechanical simulation related basic theory and resolving method of the essential phases of simulation. Adaptive meshing and split line technology are introduced to develop two different models. Results of maximam Mises stress, maximam temperature, chip deformation index, interfaces maximam temperature are in small relative error of 0.01%. So each kind of modeling method can be selected if necessary. Differential method is hired to predict the cutting forces of machining aluminum alloy thin-wall part, and the radial force is used to simulate the milling deformation. The deformation results are between 0 and 0.03mm, and the connection trace can be explained with the result curves. Residual stresses of the turbine slot component are simulated by software AdvantEdge and the surface residual stresses of 3 points are compared. Results of the comparison are explained on the microscope level. General finite element software Abaqus is used to build a plain strain model of cutting superalloy GH4169 and saw-tooth chip is got. It proves the existing of adiabatic shearing phenomenon and expains the relationship between adiabatic shearing and the brittle breaking. The relation between saw-tooth chip indexes and cutting speed is got at the same time.
- 1、下载文档前请自行甄别文档内容的完整性,平台不提供额外的编辑、内容补充、找答案等附加服务。
- 2、"仅部分预览"的文档,不可在线预览部分如存在完整性等问题,可反馈申请退款(可完整预览的文档不适用该条件!)。
- 3、如文档侵犯您的权益,请联系客服反馈,我们会尽快为您处理(人工客服工作时间:9:00-18:30)。
高速干式滚齿切削热力耦合与工艺参数分析许少宁;沈洪壵【摘要】为了方便优化高速干式切削工艺,对高速干式滚齿机切削进行热力耦合和工艺参数影响分析.首先结合高速干式滚齿加工的技术特点,对干式滚齿中切削力和切削温度场进行了理论建模.在此基础上,对滚刀单个刀齿的切削温度场进行有限元仿真分析,以获得滚刀前刀面的切削温度分布情况,实现仿真研究滚齿切削的可能性.然后以最高切削温度为研究目标,分析进给量、滚刀转速等工艺参数对滚齿加工过程的影响.最后在滚齿机上展开了干式滚齿切削实验.结果表明:随着滚刀转速的提升机床切削温度快速升高后慢慢降低并趋于稳定,且高转速有利于节约能耗;研究结果可对切削工艺的优化策略提供指导,为滚齿机的设计制造提供理论基础.【期刊名称】《机电工程》【年(卷),期】2016(033)007【总页数】7页(P836-842)【关键词】高速干式滚齿;热力耦合;有限元仿真;工艺参数【作者】许少宁;沈洪壵【作者单位】浙江省机械工业情报研究所,浙江杭州310009;浙江省机械工程学会,浙江杭州310009;浙江大学机械工程学院,浙江杭州310027【正文语种】中文【中图分类】TP24滚齿加工具有效率高、适应性好等技术特点,是目前齿轮加工行业应用最为广泛的加工技术之一,约占整个齿轮加工量的45%。
传统的湿式滚齿加工通常需要使用冷却液来冷却刀具和工件,切削速度一般不高,且易造成环境污染。
高速干式滚齿加工是在高速干式切削基础上发展起来的一种先进的齿轮加工方法,它是指在不使用冷却液和润滑油剂的情况下,采用较高的切削速度进行滚齿加工的方法。
相对于湿式加工方式,高速干式滚齿加工能够提高生产效率、降低加工能耗、简化工艺流程、提高加工精度和表面完整性、延长刀具寿命、保护环境及工人身体健康等[1-2]。
我国在高速干式滚齿方面研究起步较晚。
黄强等[3]从机床、刀具和工艺3个方面对高速干式滚齿加工的关键技术及其解决方案进行了分析和综述,认为干态高速滚齿的顺利进行需要在切削理论上进行全面突破,在刀具、机床和工艺技术上进行综合改进。
周鹏举等[4-5]推导了高速干式滚齿的切削温度场及平均切削温度计算公式,并探讨高速干式滚齿的切削机理。
郭茜[6]建立了高速干式滚齿的切削力模。
刘海江等[7]以最高生产率为目标函数,建立了多种因素限制的滚刀结构参数及切削用量优化的数学模型,并进行干式滚刀刀具结构的优化设计。
尹洋等[8]论述了零传动干式滚齿机关键部件设计原则,提出了干式滚刀选用原则。
当前,国内外针对高速干式滚齿的研究主要聚焦在高速切削加工机理、高速机床设计、高速刀具设计及优化等方面,对高速干式滚齿加工过程优化控制方面研究较少。
本研究首先对高速干式滚齿切削过程中的切削力和温度场进行了理论建模,并利用ANSYS对滚刀单个刀齿的切削温度场进行有限元仿真分析,以获得滚刀前刀面的切削温度分布情况,并以最高切削温度为研究目标函数,研究进给量、滚刀转速对滚齿加工过程的影响。
最后,在滚齿机上展开高速干式切削实验验证。
1.1 高速干式滚齿切削力建模本研究对滚刀单一刀刃做受力分析。
根据齿轮范成法原理,可得滚齿过程切削形态如图1所示。
滚刀水平旋转过α角度,红色为待切除齿坯材料。
此时,滚刀顶刃及两侧刃分别对工件产生切削作用,切削层截面如图2所示。
由于范成法滚齿过程为一个齿廓的渐进成形,因此滚齿过程切削层随滚刀刀齿的不同而变动,图2中的截面面积S1、S2、S3仅为相应刀齿的一个瞬态面积。
在滚齿切削过程每个滚刀刃齿的3个切削刃一般都同时有切削运动,3个切削刃分别为一个主切削刃和两个侧切削刃,因此在分析滚齿切削力过程中将切屑截面分成3部分的面积以分别计算相应的切削力,每个切削刃的切削情况可根据传统切削力模型计算。
如图2所示,3个切削刃分别对应各自的切削面积S1、S2、S3,因为切削过程的材料参数相同,在不考虑切屑惯性力Fm的前提下,可得出3个切削刃的切削力的大小,3个切削刃在滚齿过程中产生的切削力主要区别在于各自切削面积的不同。
刀齿各切削刃的切削力表达式为:其中,FSi=τSi,i=1,2,3。
那么切削力合力为:式中:τ—屈服剪切应力,φ—剪切角,β0—摩擦角,γ0—刀具前角。
1.2 高速干式滚齿切削温度场建模滚刀在滚齿切削过程中需要克服齿坯件金属塑性变形和弹性变形所需要的变形功,同时也要克服切屑与刀具前刀面摩擦、后刀面与工件摩擦做需要的摩擦功,切削过程所消耗的切削功都将转化为切削热。
这些热量在传递给切屑、刀具、工件后,使得切屑、刀具、工件的温度上升,形成相应的温度场。
1.2.1 热源强度计算首先计算前刀面产生的热量中传入切屑与传入刀具的部分。
设其中传入切屑的比例为R2,可由以下式计算:那么前刀面传递给切屑的发热量为:式中:Ff—前刀面摩擦力,vc—切屑流速,v—切削速度,—与热源面积长宽比有关的面积因子,aw—切屑宽度,λt—t时刻刀具材料的导热系数,θs—剪切面对切屑的平均升温,θ0—刀具初始温度,c2—刀具材料比热容,ρ2—刀具材料密度,lf—前刀面与切屑的接触长度,ξ—切削变形系数。
前刀面摩擦力,切屑流速以及切削变形系数计算公式为:剪切面对切屑的平均升温θs为:式中:ac—切屑厚度,c1—切屑材料比热容,ρ1—切屑材料密度,R1—剪切面产生热量传入切屑的比例计算公式为:1.2.2 断续切削温度场在滚齿持续稳定切削工作情况下,滚齿过程剪切面与前刀面对工件、切屑、滚刀进行不间断的加热作用,并达到一个平衡状态,各部分的温度将保持在一个相对稳定的水平。
本研究利用剪切面与前刀面作为热源面,对切屑与前刀面的贴合部位进行温度场的计算,得到滚刀上的温度分布情况。
由于在干切削过程中无冷却液作用,切削过程中切屑、刀具与周围空气的热交换系数小,因此将刀具切屑的空气接触面定义为绝热边界,用镜像热源法将热源面延伸成无限长、有限宽的数个热源面。
此时切削温度场初始热源面的模型如图3所示,其中热源位置集中于剪切面和前刀面,热源宽度为切屑宽度,定义为aw,热源面长度为剪切面长度和切屑刀具接触长度,分别定义为Ls与Lf。
剪切面的热流强度为Qs,取该热源面上一段足够窄的热源带当做线热源,其宽度为dLs,因此线热源强度为q s=Qs·dLs,可得到该线热源对于O点的温度影响为:对dθs在Ls上积分,得θs的表达式为:式中:n—热源持续周期数,n=t/T。
热源周期如图4所示。
同理,可以得到前刀面对于O、B点温度分布情况的影响状况为:式中:Qs=FsvsR1/awLs,Qf=FfvcR2/awLf取滚刀各刀齿中切削面积最大的刀齿为研究对象,建立有限元模型并对其进行温度场分析。
其中参数化模拟仿真与有限元模块的数据传递关系如图5所示。
本研究利用参数化分析的方法,将干式滚齿加工齿轮、滚刀及工艺相关参数为驱动变量,在得到加工该齿轮过程的具体滚削过程参数数据后,以这些数据有有限元建模与边界条件的创建条件,从而实现干式滚齿过程的有限元仿真。
滚齿过程中各刀齿的切削状态不一样,这里选取具有最大切削面积的刀齿进行滚刀的温度场仿真。
模型具有恒定的热流输入,定义滚刀的导热系数、比热容和密度等材料参数,采用自由网格划分方式对模型进行网格划分,如图6(a),施加载荷以后,得到仿真结果,如图6(b~c)所示。
根据温度分布云图及热流矢量图,干式滚齿切削温度场分布特征为:(1)最高值主要集中于滚刀刀齿顶部,对滚刀根部的影响已经减小,故在此忽略其对周边刀齿的影响;(2)刀齿顶部温度梯度基本保持与滚刀轴线水平,即在刀齿3个切削刃中,以顶刃为主要切削刃,其对温度影响相对较大;(3)滚刀前刀面热流量最大值发生于切屑与前刀面的分离处,此处温度梯度最大。
根据刀齿温度场分布情况,可以对单个刀齿采取单独研究的方法。
按照以上有限元仿真步骤,对不同工艺参数下的模型进行有限元仿真,以分析不同工艺参数对温度场的影响。
本研究主要研究目标为在保证滚齿质量的前提下,更大的提高生产效率、缩小经济成本。
而干切削由于不使用切削液,容易导致切削过程切削温度升高、刀具磨损严重等特点,其中切削温度的提高尤为明显。
因此,根据滚齿温度表达式,以干式滚齿最高切削温度为衡量指标,分析滚齿工艺参数对切削形态等间接变量的影响,进而研究滚齿工艺对于干切温度的关系,实现干切温度的优化配置,从而得到干式滚齿最优化加工工艺,流程如图7所示。
3.1 高速干式滚齿切削力建模进给量对干式滚齿切削过程的影响进给量即齿坯转动一周时滚刀在齿坯轴向的推进距离,是滚齿过程重要工艺参数。
进给量的大小将直接影响切削温度推导过程的切削面积、切屑厚度等影响因素,所以在研究干式滚齿切削过程中,滚齿进给量的研究具有非常重要的意义。
不同进给量下各滚刀刀齿切削过程总切削面积的变化情况以及最大切削面积随着进给量的变化情况如图8所示。
从图8中看出,各刀齿间的切削面积各不相同,不同进给量时同一刀齿的切削面积也不同;随着进给量增加,各刀齿切削面积都具有相应的增加量,变化趋势相同;不同的进给量具有最大切削面积的刀齿号也不同,最大切削面积刀齿数左移;进给量增加,切削面积增大,但模数较小时,切削面积增大趋势较缓。
不同进给量下各滚刀刀齿所切除的切屑体积的变化情况如图9所示。
滚刀每个刀齿都可以有3个刀刃进行切削,由于切削状态不一,所以切屑体积除了在总体上符合先增后递减的趋势外,在个别刀齿上存在体积的无规律变化。
滚齿过程中最大切削面积处切削厚度随进给量的变化情况如图10所示。
从两个图中切屑体积及厚度的变化情况可推导出:(1)进给量增加,切屑体积增加,不同刀齿变化规律不同;(2)进给量增加,发生最大切削体积的刀齿号不同,所对应的刀齿号具有左移趋势;(3)进给量增加,切屑厚度的变化趋势符合最大切削切削面积的变化情况。
进给量给滚齿过程带来的切削面积、材料切除量的变化也将直接的带来切削热流密度、切削温度的变化。
不同进给量下滚齿过程的最高切削温度随进给量的变化情况如图11所示。
从图中的变化趋势得到:(1)切削温度随进给量增加而提高。
原因为进给量增加到来的切削面积等参数的增加,切削温度的变化趋势与与切削面积、切削厚度趋势一样;(2)当进给量增加一倍时,切削温度增加值有限,因此在考虑切削效率时,可以在切削条件的允许下尽量增大进给量。
进给量变化给切削面积、厚度,切屑体积等带来的变化情况,可以用于推测滚齿过程最危险刀齿标号的位置以及用于推算进给量对于滚齿切削温度的变化情况。
根据以上的进给量对于滚齿过程相关切削变量的影响情况,可以为相关的滚齿工艺设计提供参考依据。
3.2 滚刀转速对干式滚齿切削过程影响在滚齿过程中,在以滚刀转速为单一变量时,滚刀与齿坯间的相互转动位置与转动过程轨迹将恒定不变,所以滚刀转速将不对切削面积、厚度、各刀齿切削状态以及切屑体积等相关参数产生影响。