影响切削用量的因素
切削用量三要素计算公式

切削用量三要素计算公式切削用量三要素计算公式是指在切削过程中,根据切削速度、进给速度和切削深度来计算切削用量的公式。
切削用量是切削过程中切除材料或切削液的量,是衡量切削过程中切削效果的一个重要指标。
在切削加工过程中,切削用量的合理控制对于提高切削效果、延长刀具寿命和提高加工效率都起到至关重要的作用。
切削用量三要素包括切削速度、进给速度和切削深度。
切削速度是指刀具与工件相对运动的速度,单位通常是m/min。
进给速度是指切削刃每转一周,工件上移动的距离,单位通常是mm/rev。
切削深度是指刀具切削刃在一个工件上的进入深度,单位通常是mm。
切削用量的计算公式为:切削用量=切削速度×进给速度×切削深度切削用量的计算公式可以根据不同的切削形式和加工要求进行调整。
下面将分别介绍一些常用的切削用量计算公式。
1.对于铣削加工:切削用量=切削宽度×进给速度×加工长度其中,切削宽度是指铣刀径向切削刀具之间的距离,通常是成刀具直径的倍数。
2.对于车削加工:切削用量=切削深度×进给速度×加工长度其中,切削深度是指刀具在工件中切削的最大深度。
3.对于钻削加工:切削用量=钻孔直径×进给速度×加工长度其中,钻孔直径是指钻头直径,进给速度是指每转一周,工件上移动的距离。
4.对于镗削加工:切削用量=镗孔直径×进给速度×加工长度其中,镗孔直径是指镗刀直径。
需要注意的是,切削用量的计算公式只是一个理论值,实际加工时往往需要根据具体材料性质、刀具情况、工件形状和加工要求等因素进行适当调整。
切削用量的合理选取对于加工质量的影响非常大。
合理的切削用量可以确保工件表面质量良好,避免切削过程中产生过大的切削力和切削热量,减少工件表面的热影响区,避免刀具磨损过快和强制振动的产生,提高切削效率和工件精度。
因此,在选择切削用量时应充分考虑刀具材料、刀具形状、刀具刃数、切削方式、切削速度和切削深度等因素,并根据实际情况进行调整。
简述切削用量的选用原则。
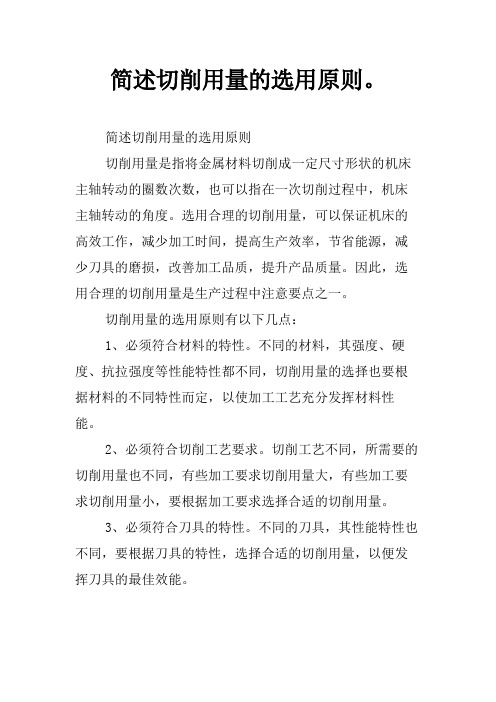
简述切削用量的选用原则。
简述切削用量的选用原则切削用量是指将金属材料切削成一定尺寸形状的机床主轴转动的圈数次数,也可以指在一次切削过程中,机床主轴转动的角度。
选用合理的切削用量,可以保证机床的高效工作,减少加工时间,提高生产效率,节省能源,减少刀具的磨损,改善加工品质,提升产品质量。
因此,选用合理的切削用量是生产过程中注意要点之一。
切削用量的选用原则有以下几点:1、必须符合材料的特性。
不同的材料,其强度、硬度、抗拉强度等性能特性都不同,切削用量的选择也要根据材料的不同特性而定,以使加工工艺充分发挥材料性能。
2、必须符合切削工艺要求。
切削工艺不同,所需要的切削用量也不同,有些加工要求切削用量大,有些加工要求切削用量小,要根据加工要求选择合适的切削用量。
3、必须符合刀具的特性。
不同的刀具,其性能特性也不同,要根据刀具的特性,选择合适的切削用量,以便发挥刀具的最佳效能。
4、必须符合机床的特性。
不同的机床,其转速、功率等性能特性也不同,切削用量的选择也要根据机床的特性来决定,以保证机床的最佳效能。
5、必须符合工件尺寸要求。
切削用量必须根据工件尺寸的大小来选择,如果工件尺寸较大,则切削用量越大,反之,切削用量越小。
6、必须符合加工精度要求。
当加工的精度越高时,切削用量就越少,而加工的精度越低时,切削用量就越大。
7、必须考虑切削方法的特点。
切削方法的特点包括:切削的深度和宽度,刀具的刃口形状,机床的转速,切削液的种类和流量等,这些都会影响切削用量的选择。
8、必须考虑切削液的特点。
不同的切削液具有不同的特性,要根据切削液的性质,选择适当的切削用量,以更好地发挥切削液的效用。
以上就是切削用量的选用原则的简介,要想使机床的加工效率达到最高,切削用量的选用是必不可少的,并且要根据不同材料、不同机床、不同刀具、不同加工工艺等多种因素,来确定适当的切削用量,以保证加工质量和加工效率。
切削用量的合理选择
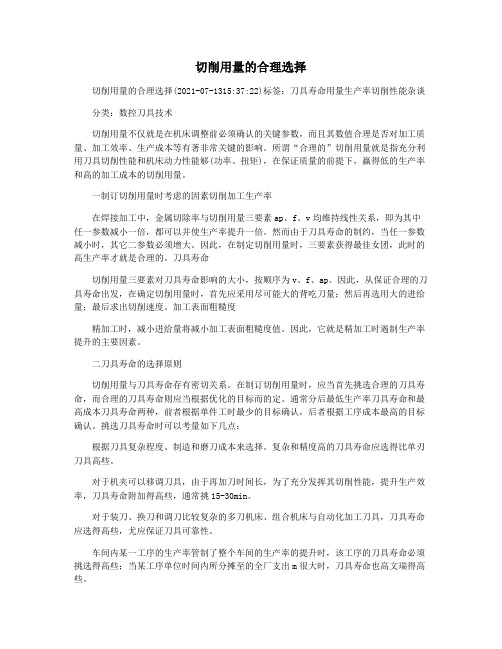
切削用量的合理选择切削用量的合理选择(2021-07-1315:37:22)标签:刀具寿命用量生产率切削性能杂谈分类:数控刀具技术切削用量不仅就是在机床调整前必须确认的关键参数,而且其数值合理是否对加工质量、加工效率、生产成本等有著非常关键的影响。
所谓“合理的”切削用量就是指充分利用刀具切削性能和机床动力性能够(功率、扭矩),在保证质量的前提下,赢得低的生产率和高的加工成本的切削用量。
一制订切削用量时考虑的因素切削加工生产率在焊接加工中,金属切除率与切削用量三要素ap、f、v均维持线性关系,即为其中任一参数减小一倍,都可以并使生产率提升一倍。
然而由于刀具寿命的制约,当任一参数减小时,其它二参数必须增大。
因此,在制定切削用量时,三要素获得最佳女团,此时的高生产率才就是合理的。
刀具寿命切削用量三要素对刀具寿命影响的大小,按顺序为v、f、ap。
因此,从保证合理的刀具寿命出发,在确定切削用量时,首先应采用尽可能大的背吃刀量;然后再选用大的进给量;最后求出切削速度。
加工表面粗糙度精加工时,减小进给量将减小加工表面粗糙度值。
因此,它就是精加工时遏制生产率提升的主要因素。
二刀具寿命的选择原则切削用量与刀具寿命存有密切关系。
在制订切削用量时,应当首先挑选合理的刀具寿命,而合理的刀具寿命则应当根据优化的目标而的定。
通常分后最低生产率刀具寿命和最高成本刀具寿命两种,前者根据单件工时最少的目标确认,后者根据工序成本最高的目标确认。
挑选刀具寿命时可以考量如下几点:根据刀具复杂程度、制造和磨刀成本来选择。
复杂和精度高的刀具寿命应选得比单刃刀具高些。
对于机夹可以移调刀具,由于再加刀时间长,为了充分发挥其切削性能,提升生产效率,刀具寿命附加得高些,通常挑15-30min。
对于装刀、换刀和调刀比较复杂的多刀机床、组合机床与自动化加工刀具,刀具寿命应选得高些,尤应保证刀具可靠性。
车间内某一工序的生产率管制了整个车间的生产率的提升时,该工序的刀具寿命必须挑选得高些;当某工序单位时间内所分摊至的全厂支出m很大时,刀具寿命也高文瑞得高些。
简要说明切削用量三要素选择的原则
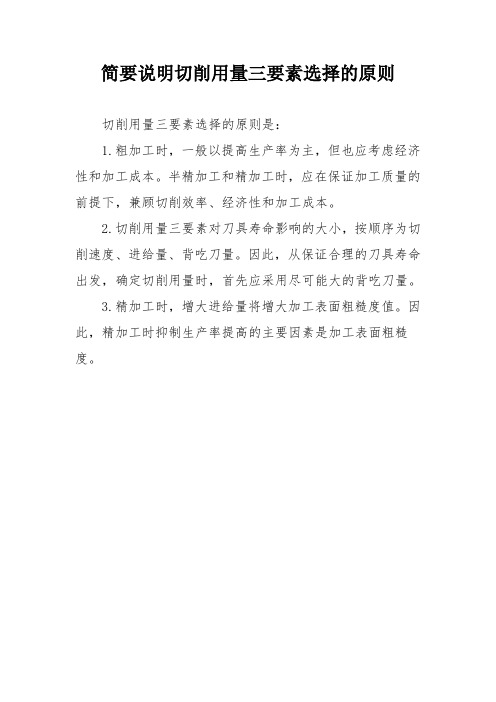
简要说明切削用量三要素选择的原则
切削用量三要素选择的原则是:
1.粗加工时,一般以提高生产率为主,但也应考虑经济性和加工成本。
半精加工和精加工时,应在保证加工质量的前提下,兼顾切削效率、经济性和加工成本。
2.切削用量三要素对刀具寿命影响的大小,按顺序为切削速度、进给量、背吃刀量。
因此,从保证合理的刀具寿命出发,确定切削用量时,首先应采用尽可能大的背吃刀量。
3.精加工时,增大进给量将增大加工表面粗糙度值。
因此,精加工时抑制生产率提高的主要因素是加工表面粗糙度。
数控车削切削用量的选择原则
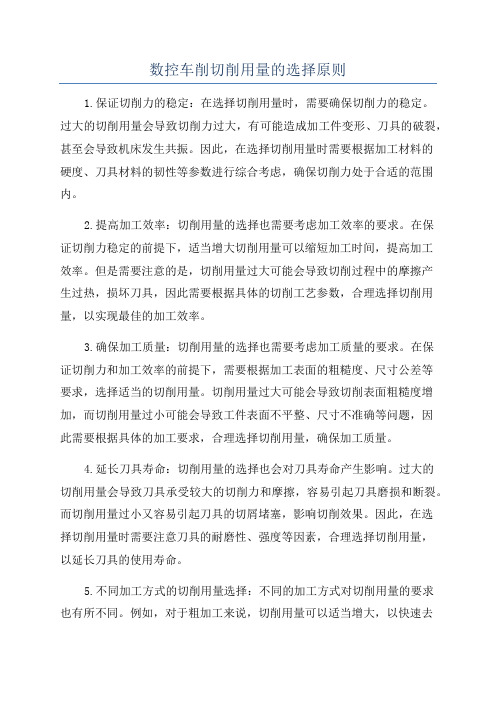
数控车削切削用量的选择原则1.保证切削力的稳定:在选择切削用量时,需要确保切削力的稳定。
过大的切削用量会导致切削力过大,有可能造成加工件变形、刀具的破裂,甚至会导致机床发生共振。
因此,在选择切削用量时需要根据加工材料的硬度、刀具材料的韧性等参数进行综合考虑,确保切削力处于合适的范围内。
2.提高加工效率:切削用量的选择也需要考虑加工效率的要求。
在保证切削力稳定的前提下,适当增大切削用量可以缩短加工时间,提高加工效率。
但是需要注意的是,切削用量过大可能会导致切削过程中的摩擦产生过热,损坏刀具,因此需要根据具体的切削工艺参数,合理选择切削用量,以实现最佳的加工效率。
3.确保加工质量:切削用量的选择也需要考虑加工质量的要求。
在保证切削力和加工效率的前提下,需要根据加工表面的粗糙度、尺寸公差等要求,选择适当的切削用量。
切削用量过大可能会导致切削表面粗糙度增加,而切削用量过小可能会导致工件表面不平整、尺寸不准确等问题,因此需要根据具体的加工要求,合理选择切削用量,确保加工质量。
4.延长刀具寿命:切削用量的选择也会对刀具寿命产生影响。
过大的切削用量会导致刀具承受较大的切削力和摩擦,容易引起刀具磨损和断裂。
而切削用量过小又容易引起刀具的切屑堵塞,影响切削效果。
因此,在选择切削用量时需要注意刀具的耐磨性、强度等因素,合理选择切削用量,以延长刀具的使用寿命。
5.不同加工方式的切削用量选择:不同的加工方式对切削用量的要求也有所不同。
例如,对于粗加工来说,切削用量可以适当增大,以快速去除材料。
而对于精加工来说,切削用量需要较小,以保证加工表面的质量。
对于深孔加工来说,由于切削油液的润滑不足,切削用量需要较小,以减小切削过程中的磨损和发热。
总之,数控车削切削用量的选择需要综合考虑切削力、加工效率、加工质量、刀具寿命等因素,根据具体加工要求和材料特性,合理选择切削用量,以实现高效、高质量的加工。
切削用量的合理选择

表7-5 硬质合金车刀及高速钢车刀粗车外圆和端面时的进给量
3)切削速度 切削速度vc是根据刀具耐用度T确定的。在背吃刀量ap和进给量f
确定后,根据规定的刀具耐用度T,计算刀具耐用度T所允许的切削n计,再选取机床主轴实际转速n,最后由机床主轴实 际转速n计算实际切削速度vc。
对切削加工实际生产来 说,较方便的是根据切 削用量手册查表确定切 削用量。切削用量手册 中的数据是在积累了大 量的生产经验及试验研 究工作的基础上,经过 科学的数据处理后制定 出来的。查表确定切削 用量后,还可根据具体 生产条件适当调整。
把各公式的计算结果绘 制成各种图表,直接从 其上选择切削用量。针 对具体机床制成的切削 用量图表,更适合于生 产现场使用。
3)切削速度 c 半精加工和精加工的切削速度
也是受刀具耐用度的限制,因此,
切削速度与粗加工时的计算方法相同。但由于半精加工和精加工切削条
件较好,刀具耐用度比粗加工时规定得大,所以半精加工和精加工时的
切削速度一般比粗加工时高。
1.3 提高切削用量的途径
提高切削用量的途径很多,可归纳为以下几个方面: (1)采用切削性能更好的新型刀具材料。 (2)改善工件材料的加工性。 (3)改进刀具结构和选用合理刀具几何参数。 (4)提高刀具的制造和刃磨质量。 (5)采用新型的、性能优良的切削液和高效率的冷却方法。
(7-1)
若加工余量A太大或加工工艺系统刚性比较差,则加工余量A
可经二次或更多次走刀去除。若分二次走刀,则它们的背吃刀量
的表达式分别为
ap1=(3/4~2/3)A ap2=(1/3~1/4)A
(7-2) (7-3)
2)进给量 当背吃刀量确定后,根据加工工艺系统允许的切削力,进一步确定
切削用量选用原则

切削用量选用原则切削用量是指在加工过程中对工件进行切削时所使用的切削刀具、刀具材料、切削速度、进给量等参数的选择和调整。
合理选用切削用量是提高加工效率、保证加工质量和延长切削工具寿命的重要因素之一。
本文将从切削刃数、切削深度、切削速度、进给量和切削方式等方面介绍切削用量选用的原则。
一、切削刃数的选择原则切削刃数是指刀具上的切削刃数目。
切削刃数的选择应根据工件材料和加工要求进行。
对于硬度较高的材料,应选用切削刃数少、刀具强度大的刀具,以提高刀具的抗断裂能力和刀具寿命;对于材料硬度较低的工件,可以选用切削刃数多的刀具,以提高切削效率。
二、切削深度的选择原则切削深度是指刀具在每次切削中所能切削的最大距离。
切削深度的选择应根据工件材料、刀具强度和加工要求来确定。
一般情况下,切削深度应尽可能大,以提高切削效率。
但是,在选择切削深度时也要考虑刀具的抗断裂能力和加工表面质量,避免过大的切削深度导致刀具断裂或加工表面粗糙。
三、切削速度的选择原则切削速度是指刀具在切削过程中的线速度。
切削速度的选择应根据刀具材料、工件材料和加工要求来确定。
切削速度过高会导致刀具过热,影响切削质量和刀具寿命;切削速度过低则会降低切削效率。
因此,切削速度的选择应综合考虑切削质量、刀具寿命和切削效率的要求。
四、进给量的选择原则进给量是指刀具在单位时间内沿着工件表面移动的距离。
进给量的选择应根据工件材料、切削刃数和加工要求来确定。
进给量过大会导致切削力过大,影响加工表面质量和刀具寿命;进给量过小则会降低切削效率。
因此,进给量的选择应综合考虑切削力、加工表面质量和切削效率的要求。
五、切削方式的选择原则切削方式包括顺向切削、逆向切削和侧向切削等。
切削方式的选择应根据工件形状、切削刃数和加工要求来确定。
顺向切削适合于切削刃数少、工件表面平整度要求高的情况;逆向切削适合于切削刃数多、切削力大的情况;侧向切削适合于切削刃数多、工件形状复杂的情况。
切削方式的选择应综合考虑加工要求、切削质量和切削效率。
切削用量的合理选择
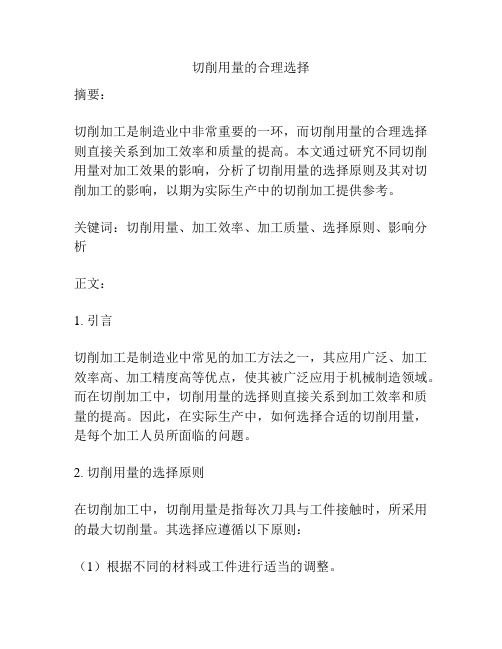
切削用量的合理选择摘要:切削加工是制造业中非常重要的一环,而切削用量的合理选择则直接关系到加工效率和质量的提高。
本文通过研究不同切削用量对加工效果的影响,分析了切削用量的选择原则及其对切削加工的影响,以期为实际生产中的切削加工提供参考。
关键词:切削用量、加工效率、加工质量、选择原则、影响分析正文:1. 引言切削加工是制造业中常见的加工方法之一,其应用广泛、加工效率高、加工精度高等优点,使其被广泛应用于机械制造领域。
而在切削加工中,切削用量的选择则直接关系到加工效率和质量的提高。
因此,在实际生产中,如何选择合适的切削用量,是每个加工人员所面临的问题。
2. 切削用量的选择原则在切削加工中,切削用量是指每次刀具与工件接触时,所采用的最大切削量。
其选择应遵循以下原则:(1)根据不同的材料或工件进行适当的调整。
不同材料或工件应根据其硬度、刚性等特性进行不同的切削用量选择,以确保刀具寿命长、加工效率高。
(2)保证切削力合理。
切削用量过大会导致切削力增大,进而使切削加工过程中产生振动、噪音等不良现象,因此应保证切削力在合理范围内。
(3)控制切削温度。
切削温度过高不仅会影响刀具寿命,还会对工件表面产生烧伤等影响,因此需要选择合适的切削用量,控制切削温度在可控范围内。
3. 切削用量对加工效果的影响(1)切削用量对加工速度的影响切削用量的选择对加工速度具有一定的影响。
切削用量越大,所需要的切削次数就越少,加工效率也就越高。
(2)切削用量对质量的影响切削用量过大会使工件表面粗糙度增加,从而降低工件加工精度。
但若切削用量过小,则会导致加工时间较长,无法提高加工效率。
4. 切削用量的合理选择对加工质量的提高在实际生产中,选择合理的切削用量能够提高加工效率和质量。
正确选择切削用量,不仅可以保证刀具寿命长,还能有效控制切削温度、切削力等,从而避免切削加工过程中产生振动、噪音等现象,提高加工质量。
5. 结论通过对切削用量选择的原则及其对加工效果的影响分析,本文认为在切削加工中,选择合适的切削用量是确保加工效率和质量的保障。
切削用量的三要素 计算题

切削用量的三要素计算题1.引言1.1 概述概述部分应该对整篇文章的主题进行简要介绍和概括。
可以参考以下内容进行编写:在制造业中,切削加工是一种常见且重要的加工方法,广泛应用于金属材料的加工和加工过程中。
在切削加工过程中,刀具的切削用量是一个关键参数,它直接影响到加工质量、加工效率和工件的表面精度。
因此,准确计算切削用量对于优化切削加工过程、提高加工效率和降低成本具有重要意义。
切削用量是指在单位时间内切削刀具对工件的切削量。
它通常由切削速度、进给速度和切削深度三个要素组成。
切削速度是刀具在切削过程中相对工件表面的切削速度,它直接影响到切削过程中的温度分布、切削力和切削表面质量。
进给速度是指刀具在切削过程中的移动速度,它决定了单位时间内切削刀具对工件的切削量。
切削深度则是指切削刀具与工件间的物理距离,它直接关系到切削过程中的切削力和切削表面的加工精度。
本文将详细介绍切削用量的三个要素,包括切削速度、进给速度和切削深度的计算方法和影响因素。
首先,我们将对切削速度的计算方法进行介绍,并探讨切削速度对切削过程的影响。
然后,我们将讨论进给速度的计算方法和进给速度对切削用量的影响。
最后,我们将重点关注切削深度的计算方法和切削深度对切削过程的影响。
通过深入理解和准确计算切削用量的三个要素,制造业可以优化切削加工过程,提高加工效率,减少切削工具的磨损,并最终降低加工成本。
同时,本文还将展望未来的发展方向,并提出一些可能的研究方向和解决方案。
通过对切削用量的全面了解,我们可以更好地应对制造业中的挑战,提高产品质量,提升市场竞争力。
1.2文章结构1.2 文章结构本文将按照以下顺序进行论述切削用量的三要素:1. 切削深度(Cutting Depth):切削深度是指在一次切削过程中刀具与工件之间的最大距离。
它直接关系到切削过程中金属去除的量和切削力的大小。
我们将探讨切削深度的计算方法、切削深度对切削过程的影响以及如何选择合适的切削深度。
切削用量 切削用量三要素

切削用量切削用量三要素切削用量是指切削速度v c 、进给量f (或进给速度v f )、背吃刀量 a p 三者的总称,也称为切削用量三要素。
它是调整刀具与工件间相对运动速度和相对位置所需的工艺参数.它们的定义如下:(一)切削速度v c切削刃上选定点相对于工件的主运动的瞬时速度。
计算公式如下v c=( π d w n )/1000 (1—1)式中v c ——切削速度(m/s) ;dw —-工件待加工表面直径(mm );n —-工件转速(r/s )。
在计算时应以最大的切削速度为准,如车削时以待加工表面直径的数值进行计算,因为此处速度最高,刀具磨损最快。
(二)进给量f工件或刀具每转一周时,刀具与工件在进给运动方向上的相对位移量。
进给速度v f 是指切削刃上选定点相对工件进给运动的瞬时速度。
v f=fn (1—2 )式中v f ——进给速度(mm/s );n ——主轴转速(r/s );f --进给量(mm )。
(三)背吃刀量a p通过切削刃基点并垂直于工作平面的方向上测量的吃刀量。
根据此定义,如在纵向车外圆时,其背吃刀量可按下式计算:a p = ( d w — d m )/2 ( 1-3 )式中 d w ——工件待加工表面直径(mm );dm -—工件已加工表面直径( mm ).涂层刀片为了提高刀具(刀片)表面的硬度和改善其耐磨性、润滑性,通过化学气相沉积和真空溅射等方法,在硬质合金刀片表面喷涂一层厚度5~12μ m以下的TiC、TiN或Al 2O 3等化合物材料。
TiC 涂层刀片,硬度可达3200HV,呈银灰色,耐磨性好,容易扩散到基体内与基体粘结牢固,在低速切削温度下有较高的耐磨性。
TiN 涂层刀片TiN硬度为2000HV,呈金黄色,色泽美观,润滑性能好,有较高的抗月牙洼型的磨损能力,与基体粘结牢固程度较差。
Al 2O 3 涂层刀片硬度可达3000HV,有较高的高温硬度的化学稳定性,适用于高速切削。
除上述单层涂覆外,还可TiC—TiN, TiC+TiN+Al 2O 3等二层、三层的复合涂层,其性能优于单层。
切削用量 切削用量三要素

切削用量切削用量三要素切削用量切削用量三要素切削用量切削用量三要素切削用量是指切削速度 v c 、进给量 f 〔或进给速度 v f 〕、背吃刀量 a p 三者的总称,也称为切削用量三要素。
它是调整刀具与工件间相对运动速度和相对位置所需的工艺参数。
它们的定义如下:〔一〕切削速度 v c切削刃上选定点相对于工件的主运动的瞬时速度。
计算公式如下v c=( π d w n )/1000 (1-1)式中 v c ——切削速度 (m/s) ;dw ——工件待加工外表直径〔 mm 〕;n ——工件转速〔 r/s 〕。
在计算时应以最大的切削速度为准,如车削时以待加工外表直径的数值进行计算,因为此处速度最高,刀具磨损最快。
〔二〕进给量 f工件或刀具每转一周时,刀具与工件在进给运动方向上的相对位移量。
进给速度 v f 是指切削刃上选定点相对工件进给运动的瞬时速度。
v f=fn 〔 1-2 〕式中 v f ——进给速度〔 mm/s 〕;n ——主轴转速〔 r/s 〕;f ——进给量〔 mm 〕。
〔三〕背吃刀量 a p通过切削刃基点并垂直于工作平面的方向上测量的吃刀量。
根据此定义,如在纵向车外圆时,其背吃刀量可按下式计算:a p = 〔 d w — d m 〕 /2 〔 1-3 〕式中 d w ——工件待加工外表直径〔 mm 〕;dm ——工件已加工外表直径〔 mm 〕。
涂层刀片为了提高刀具〔刀片〕外表的硬度和改善其耐磨性、润滑性,通过化学气相沉积和真空溅射等方法,在硬质合金刀片外表喷涂一层厚度 5~ 12μ m以下的TiC、 TiN或 Al 2O 3等化合物材料。
TiC 涂层刀片,硬度可达 3200HV,呈银灰色,耐磨性好,容易扩散到基体内与基体粘结牢固,在低速切削温度下有较高的耐磨性。
TiN 涂层刀片 TiN硬度为 2000HV,呈金黄色,色泽美观,润滑性能好,有较高的抗月牙洼型的磨损能力,与基体粘结牢固程度较差。
切削用量三要素范文
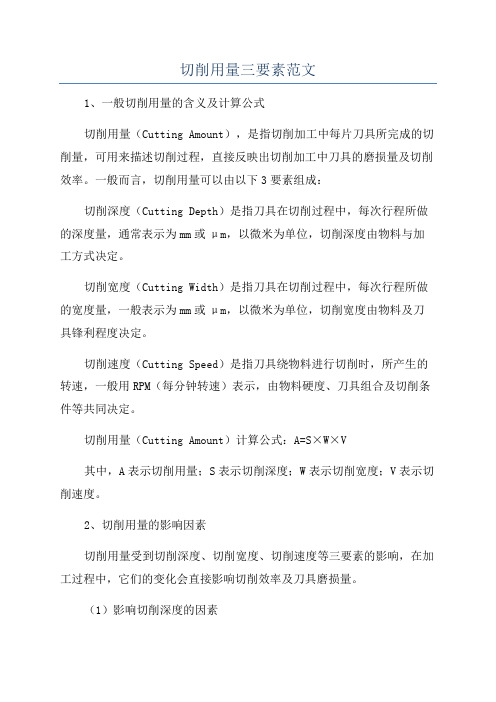
切削用量三要素范文
1、一般切削用量的含义及计算公式
切削用量(Cutting Amount),是指切削加工中每片刀具所完成的切削量,可用来描述切削过程,直接反映出切削加工中刀具的磨损量及切削效率。
一般而言,切削用量可以由以下3要素组成:
切削深度(Cutting Depth)是指刀具在切削过程中,每次行程所做的深度量,通常表示为mm或μm,以微米为单位,切削深度由物料与加工方式决定。
切削宽度(Cutting Width)是指刀具在切削过程中,每次行程所做的宽度量,一般表示为mm或μm,以微米为单位,切削宽度由物料及刀具锋利程度决定。
切削速度(Cutting Speed)是指刀具绕物料进行切削时,所产生的转速,一般用RPM(每分钟转速)表示,由物料硬度、刀具组合及切削条件等共同决定。
切削用量(Cutting Amount)计算公式:A=S×W×V
其中,A表示切削用量;S表示切削深度;W表示切削宽度;V表示切削速度。
2、切削用量的影响因素
切削用量受到切削深度、切削宽度、切削速度等三要素的影响,在加工过程中,它们的变化会直接影响切削效率及刀具磨损量。
(1)影响切削深度的因素
切削深度主要受到机床行程、切削精度及切削条件等因素影响,如它们的变化将会使切削深度发生变化,进而会影响切削用量。
粗加工时切削用量的选择原则
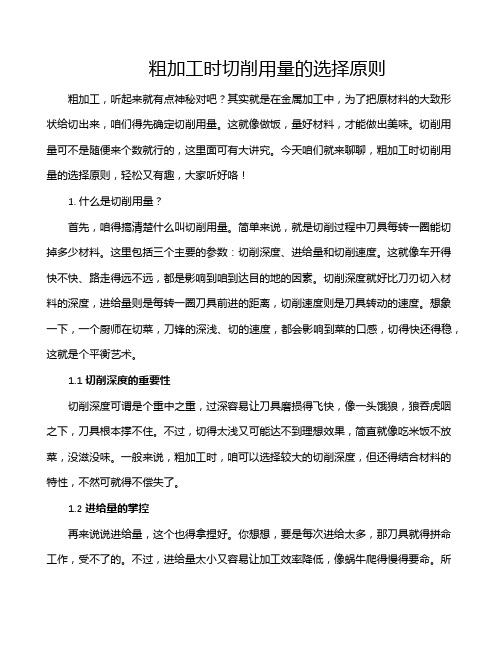
粗加工时切削用量的选择原则粗加工,听起来就有点神秘对吧?其实就是在金属加工中,为了把原材料的大致形状给切出来,咱们得先确定切削用量。
这就像做饭,量好材料,才能做出美味。
切削用量可不是随便来个数就行的,这里面可有大讲究。
今天咱们就来聊聊,粗加工时切削用量的选择原则,轻松又有趣,大家听好咯!1. 什么是切削用量?首先,咱得搞清楚什么叫切削用量。
简单来说,就是切削过程中刀具每转一圈能切掉多少材料。
这里包括三个主要的参数:切削深度、进给量和切削速度。
这就像车开得快不快、路走得远不远,都是影响到咱到达目的地的因素。
切削深度就好比刀刃切入材料的深度,进给量则是每转一圈刀具前进的距离,切削速度则是刀具转动的速度。
想象一下,一个厨师在切菜,刀锋的深浅、切的速度,都会影响到菜的口感,切得快还得稳,这就是个平衡艺术。
1.1 切削深度的重要性切削深度可谓是个重中之重,过深容易让刀具磨损得飞快,像一头饿狼,狼吞虎咽之下,刀具根本撑不住。
不过,切得太浅又可能达不到理想效果,简直就像吃米饭不放菜,没滋没味。
一般来说,粗加工时,咱可以选择较大的切削深度,但还得结合材料的特性,不然可就得不偿失了。
1.2 进给量的掌控再来说说进给量,这个也得拿捏好。
你想想,要是每次进给太多,那刀具就得拼命工作,受不了的。
不过,进给量太小又容易让加工效率降低,像蜗牛爬得慢得要命。
所以,进给量要根据加工材料的硬度和刀具的强度来调节,做到既能高效,又能保持刀具的使用寿命,简直就是个平衡木上的杂技。
2. 切削速度的选择切削速度的选择就像选歌一样,得找到适合的那一首。
不同的材料和刀具组合,适合的切削速度各不相同。
速度太快,刀具磨损快得像老鼠追逐猫;速度太慢,又不够效率,简直像蜗牛在比赛。
选对切削速度,才能事半功倍。
2.1 材料特性的考虑在选择切削速度时,咱得考虑材料的特性。
比如,硬度高的材料,咱就得适当降低速度,给刀具留点面子,别让它受太多伤。
而对于软材料,切削速度可以稍微提高,犹如火箭飞一般,飞得快,效果还好。
数控车床加工工艺编程-切削用量三要素
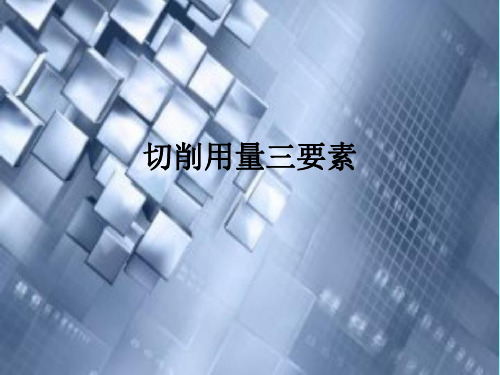
切削用量是表示主运动及进给运动大小的参数。
它包括:切削速度Vc (或主轴转速n)、 切削深度ap、进给量f 三要素。
1)切削深度是指工件上已加工表面和待加工 表面间的垂直距离。
在工艺系统刚性和机床功率允许的条件下, 尽可能选取较大的切削深度,以减少进给次 数。当工件的精度要求较高时,则应考虑留 有精加工余量,一般为0.1~0.5mm。 切削深度ap计算公式:ap= 式中: dw—待加工表面外圆直径,单位 mm dm—已加工表面外圆直径,单位mm.
2)切削速度是切削刃选定点相对于工件的主 运动的瞬时速度。
① 车削光轴切削的速度,由工件材料、直径、刀 具的材料及加工性质等因素所确定。 切削速度Vc计算公式: v = πdn / 1000
式中: d—工件或刀尖的回转直径,单位mm n—工件或刀具的转速,单位r/min
② 车削螺纹主轴转速n 切削螺纹时,车床的主轴转 速受加工工件的螺距(或导程)大小、驱动电动机升 降特性及螺纹插补运算速度等多种因素影响,因此对 于不同的数控系统,选择车削螺纹主轴转速n存在一 定的差异。 数控车床车螺纹时主轴转速计算公式:n≤–k 式中: p—工件螺纹的螺距或导程, 单位mm。 k—保险系数,一般为80。
• 3)进给速度
进给速度是指单位时间内,刀具沿进给方向移动的 距离,单位为mm/min,也可表示为主轴旋转一周时 刀具在进给方向上相对工件的位移量,单位为mm/r。
• 我们怎么来确定进给速度的原则呢?
• ①当工件的加工质量能得到保证时,为提高生产率 可选择较高的进给速度。
• ②切断、车削深孔或精车时,选择较低的进给速度。 • ③刀具空行程尽量选用高的进给速度。 • ④进给速度应与主轴转速和切削深度相适应。
切削用量参数与切削层参数

切削用量参数与切削层参数一、引言切削是制造业中常用的加工方法之一,其关键在于选择合适的切削用量参数和切削层参数。
切削用量参数主要包括切削速度、进给量和切削深度,而切削层参数则包括切削面积、切削温度和切削力等。
本文将分别介绍这些参数的作用及其优化策略。
二、切削用量参数1. 切削速度切削速度是指切削刀具在单位时间内切削工件的线速度,通常用米/分钟表示。
切削速度的选择直接影响到切削加工的效率和质量。
过低的切削速度会导致切削效率低下,而过高的切削速度则容易使刀具磨损加剧。
在选择切削速度时,需要考虑材料的硬度、切削刀具的材质以及加工工艺等因素。
2. 进给量进给量是指切削刀具每转一圈所移动的距离,通常用毫米/转表示。
进给量的选择与切削速度密切相关,合理的进给量可以提高切削效率,同时还能减少切削刀具的磨损。
过大的进给量会导致切削刀具过快磨损,而过小的进给量则会降低切削效率。
在选择进给量时,需要考虑材料的硬度、切削刀具的结构以及加工工艺等因素。
3. 切削深度切削深度是指切削刀具与工件之间的距离,通常用毫米表示。
切削深度的选择与切削速度和进给量密切相关,合理的切削深度可以提高切削效率和加工质量。
过大的切削深度会导致切削刀具过快磨损,而过小的切削深度则会降低切削效率。
在选择切削深度时,需要考虑材料的硬度、切削刀具的结构以及加工工艺等因素。
三、切削层参数1. 切削面积切削面积是指切削刀具与工件接触的面积,通常用平方毫米表示。
切削面积的大小直接影响到切削过程中的热量分布和切削力的大小。
合理控制切削面积可以提高切削加工的质量和效率。
过大的切削面积会导致切削温度过高,而过小的切削面积则会增加切削力。
2. 切削温度切削温度是指切削过程中产生的热量,通常用摄氏度表示。
切削温度的大小直接影响到切削刀具的磨损和工件表面质量。
合理控制切削温度可以延长切削工具的使用寿命和提高加工质量。
过高的切削温度会导致切削刀具过快磨损,而过低的切削温度则会影响加工效率。
切削用量三要素

根据已选定的背吃刀量ap、进给量f及刀具耐用度T,就可 按公式计算切削速度Vc和机床转速n。
切削用量及选择
① 粗车时,ap 、f均较大,所以Vc较低,精加工时,ap 、f均较小, 所以Vc较高。
② 工件材料强度、硬度较高时,应选较低的Vc;反之,Vc较高。 材料加工性越差,Vc较低。
对于粗加工来说,要尽可能保证较高的金属切除率和必要 的刀具耐用度。
提高切削速度,增大进给量和背吃刀量,都能提高金属切除率。但在
这三个因素中,影响刀具耐用度最大的是切削速度,其次是进给量,影 响最小的是背吃刀量。所以,在选择粗加工切削用量时,应优先考虑采
用大的背吃刀量,其次考虑采用大的进给量,最后才能根据刀具耐用度 的要求,选定合理的切削速度。
由此可见,选择切削用量的基本原则是首先选取尽可能大 的背吃刀量;其次要在机床动力和刚度允许的范围内,同时又满 足已加工表面粗糙度的要求的情况下,选取尽可能大的进给量, 最后利用《切削用量手册》选取或用公式计算确定最佳切削速度。
切削用量及选择
3.2 切削用量三要素的确定
(1)背吃刀量的选择
背吃刀量根据加工余量确定。
切削用量及选择
半精加工、精加工时首先要保证加工精度和表面质量, 同时应兼顾必要的刀具耐用度和生产效率,此时的背吃刀量 根据粗加工留下的余量确定。为了减小工艺系统的弹性变形, 减小已加工表面的残留面积,半精加工尤其是精加工,一般 多采用较小的背吃刀量和进给量。为抑制积屑瘤和鳞制的产 生,用硬质合金刀具进行精加工时一般多采用较高的切削速 度;高速钢刀具则一般多采用较低的切削速度。
已加工表面和待加工表面间的垂直距离,单位为mm。
对于外圆车削的深度可用下式计算:
ap=(dw-dm)/ 2 mm
- 1、下载文档前请自行甄别文档内容的完整性,平台不提供额外的编辑、内容补充、找答案等附加服务。
- 2、"仅部分预览"的文档,不可在线预览部分如存在完整性等问题,可反馈申请退款(可完整预览的文档不适用该条件!)。
- 3、如文档侵犯您的权益,请联系客服反馈,我们会尽快为您处理(人工客服工作时间:9:00-18:30)。
影响切削用量的因素
切削用量是切削加工中一个重要的参数,影响着加工质量、加工效率
和切削工具的寿命。
以下将介绍影响切削用量的几个主要因素:
1.材料性质:不同材料具有不同的硬度、强度、韧性等性质,这些性
质对切削用量有直接影响。
硬度高的材料通常需要较大的切削力才能达到
要求的加工精度,因此需要较大的切削用量。
而材料的韧性高则需要较小
的切削用量,以避免过度切削导致刀具断裂。
2.切削速度:切削速度是指单位时间内切削刀具通过加工件上相同长
度的距离。
切削速度的高低直接影响到切削用量。
一般而言,切削速度越高,切削用量越小;切削速度越低,切削用量越大。
3.切削深度:切削深度是指切削刀具垂直于工件表面进入的深度。
切
削深度的大小直接影响到切削用量。
一般而言,切削深度越大,切削用量
越大;切削深度越小,切削用量越小。
4.进给量:进给量是指切削刀具在单位时间内对工件进行加工的长度。
进给量的大小直接影响到切削用量。
一般而言,进给量越大,切削用量越大;进给量越小,切削用量越小。
5.切削润滑方式:切削润滑方式主要包括全润滑和干式切削两种。
全
润滑方式下,通过使用冷却液进行切削润滑可以降低摩擦和热量的产生,
减少切削用量。
而干式切削方式下,由于缺乏润滑,摩擦和热量较大,容
易导致切削用量增加。
6.切削刀具材料和几何形状:切削刀具的材料和几何形状直接影响到
切削用量。
良好的刀具材料和几何形状能够提高切削效率和降低切削用量。
例如,使用硬质合金刀具和适当的刀具形状可以降低切削力,减小切削用量。
7.切削条件:切削条件包括冷却液的类型和喷射方式、进给方式等。
这些条件的正确选择可以降低切削用量。
合适的冷却液类型和喷射方式能够减少摩擦和热量的产生;合理的进给方式能够降低切削力,减小切削用量。
总之,切削用量受到材料性质、切削速度、切削深度、进给量、切削润滑方式、切削刀具材料和几何形状以及切削条件等多个因素的影响。
在实际生产中,应根据具体情况选择合理的切削用量,以提高加工质量和效率,并延长刀具的使用寿命。