热硫化橡胶衬里防腐施工方案doc
橡胶衬里施工方案
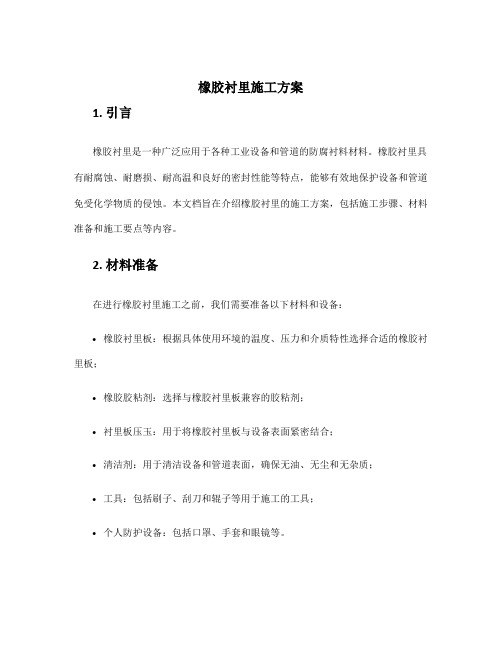
橡胶衬里施工方案1. 引言橡胶衬里是一种广泛应用于各种工业设备和管道的防腐衬料材料。
橡胶衬里具有耐腐蚀、耐磨损、耐高温和良好的密封性能等特点,能够有效地保护设备和管道免受化学物质的侵蚀。
本文档旨在介绍橡胶衬里的施工方案,包括施工步骤、材料准备和施工要点等内容。
2. 材料准备在进行橡胶衬里施工之前,我们需要准备以下材料和设备:•橡胶衬里板:根据具体使用环境的温度、压力和介质特性选择合适的橡胶衬里板;•橡胶胶粘剂:选择与橡胶衬里板兼容的胶粘剂;•衬里板压玉:用于将橡胶衬里板与设备表面紧密结合;•清洁剂:用于清洁设备和管道表面,确保无油、无尘和无杂质;•工具:包括刷子、刮刀和辊子等用于施工的工具;•个人防护设备:包括口罩、手套和眼镜等。
3. 施工步骤3.1 清洁表面在施工之前,首先要将设备和管道表面进行彻底清洁。
使用清洁剂和刷子清洗表面,确保无油、无尘和无杂质。
清洁之后,用清水冲洗干净,并等待表面完全干燥。
3.2 切割衬里板根据实际需要,使用刀具将橡胶衬里板切割成合适的尺寸和形状。
确保衬里板的大小与设备或管道表面相匹配。
切割时要注意保持板材的完整性和平整性,以免影响施工效果。
3.3 涂覆胶粘剂在设备和管道表面均匀涂覆一层橡胶胶粘剂。
使用刷子或辊子将胶粘剂均匀地涂抹在表面上,确保完全覆盖。
胶粘剂的厚度应根据橡胶衬里板的厚度和介质特性来确定。
3.4 将衬里板固定到表面将切割好的橡胶衬里板迅速放置在涂有胶粘剂的设备或管道表面上。
确保衬里板与表面完全贴合,并用衬里板压玉将其压实。
压实时要均匀用力,以确保衬里板与表面之间没有气泡和缝隙。
3.5 检查施工质量待衬里板固定后,仔细检查施工质量。
检查衬里板与表面的贴合度和平整度,确保没有缺陷和松动。
如发现问题,及时修复并重新固定衬里板。
3.6 完成施工完成衬里板的固定后,等待胶粘剂完全干燥。
根据胶粘剂的要求,通常需要等待24小时以上。
在等待期间,确保施工现场干燥通风,并防止外界物体对施工区域的干扰。
橡胶衬里施工方案
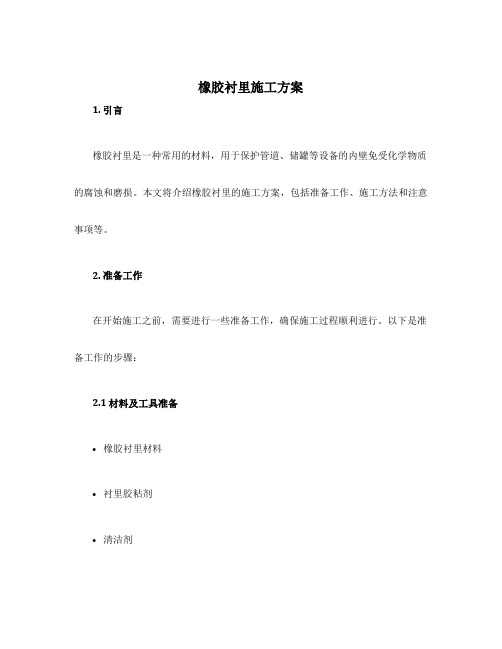
橡胶衬里施工方案1. 引言橡胶衬里是一种常用的材料,用于保护管道、储罐等设备的内壁免受化学物质的腐蚀和磨损。
本文将介绍橡胶衬里的施工方案,包括准备工作、施工方法和注意事项等。
2. 准备工作在开始施工之前,需要进行一些准备工作,确保施工过程顺利进行。
以下是准备工作的步骤:2.1 材料及工具准备•橡胶衬里材料•衬里胶粘剂•清洁剂•刷子和刮刀•打磨工具•铺设工具2.2 表面清洁在施工之前,需要彻底清洁待衬里的表面,以确保橡胶衬里能够充分附着。
2.3 检查和修复表面缺陷检查待衬里的表面,如果存在凹坑、裂缝或其他缺陷,需要进行修复。
修复方法可以包括填充和打磨等。
2.4 试验衬里胶粘剂在开始正式施工之前,要进行衬里胶粘剂的试验,以确保其适用于所选的橡胶衬里材料。
3. 施工方法在准备工作完成后,可以开始进行橡胶衬里的施工。
以下是施工的步骤:3.1 涂胶粘剂使用刷子或刮刀将衬里胶粘剂均匀涂抹在待衬里的表面上。
确保胶粘剂涂抹均匀,以实现最佳的附着性能。
3.2 铺设橡胶衬里在涂抹胶粘剂后的一段时间内,将橡胶衬里平铺在表面上。
确保橡胶衬里完全覆盖待衬里表面,并且没有皱折或空气泡。
3.3 粘合橡胶衬里使用辊轮或其他工具将橡胶衬里压紧,以确保其与表面充分粘合。
确保橡胶衬里与胶粘剂紧密接触,并且没有空隙。
3.4 清洁和修整在粘合橡胶衬里后,清洁并修整表面,以确保整个施工过程的美观和质量。
4. 注意事项在橡胶衬里施工过程中,需要注意以下事项,以确保施工质量和安全性:•使用合适的工具和设备,确保施工过程的安全性。
•严格按照施工工艺和制定的施工方案进行施工,不得随意更改。
•注意橡胶衬里材料的质量和储存条件,在施工之前进行检查。
•在施工过程中,遵循环保和安全规范,确保施工现场的安全和环保。
•在施工完成后,进行必要的检查和测试,确保施工质量达到预期要求。
结论本文介绍了橡胶衬里的施工方案,包括准备工作、施工方法和注意事项等。
只有在合理的准备和严格的施工管理下,才能确保橡胶衬里的施工质量和使用效果。
橡胶衬里防腐
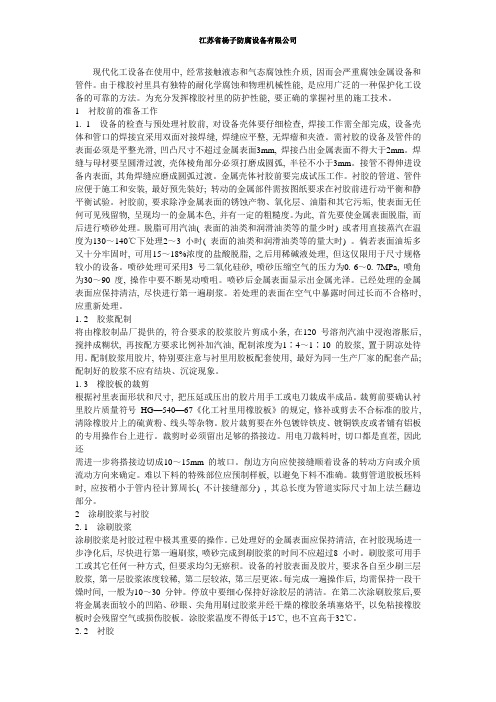
现代化工设备在使用中, 经常接触液态和气态腐蚀性介质, 因而会严重腐蚀金属设备和管件。
由于橡胶衬里具有独特的耐化学腐蚀和物理机械性能, 是应用广泛的一种保护化工设备的可靠的方法。
为充分发挥橡胶衬里的防护性能, 要正确的掌握衬里的施工技术。
1衬胶前的准备工作1. 1设备的检查与预处理衬胶前, 对设备壳体要仔细检查, 焊接工作需全部完成, 设备壳体和管口的焊接宜采用双面对接焊缝, 焊缝应平整, 无焊瘤和夹渣。
需衬胶的设备及管件的表面必须是平整光滑, 凹凸尺寸不超过金属表面3mm, 焊接凸出金属表面不得大于2mm。
焊缝与母材要呈圆滑过渡, 壳体棱角部分必须打磨成圆弧, 半径不小于3mm。
接管不得伸进设备内表面, 其角焊缝应磨成圆弧过渡。
金属壳体衬胶前要完成试压工作。
衬胶的管道、管件应便于施工和安装, 最好预先装好; 转动的金属部件需按图纸要求在衬胶前进行动平衡和静平衡试验。
衬胶前, 要求除净金属表面的锈蚀产物、氧化层、油脂和其它污垢, 使表面无任何可见残留物, 呈现均一的金属本色, 并有一定的粗糙度。
为此, 首先要使金属表面脱脂, 而后进行喷砂处理。
脱脂可用汽油( 表面的油类和润滑油类等的量少时) 或者用直接蒸汽在温度为130~140℃下处理2~3 小时( 表面的油类和润滑油类等的量大时) 。
倘若表面油垢多又十分牢固时, 可用15~18%浓度的盐酸脱脂, 之后用稀碱液处理, 但这仅限用于尺寸规格较小的设备。
喷砂处理可采用3 号二氧化硅砂, 喷砂压缩空气的压力为0. 6~0. 7MPa, 喷角为30~90 度, 操作中要不断晃动喷咀。
喷砂后金属表面显示出金属光泽。
已经处理的金属表面应保持清洁, 尽快进行第一遍刷浆。
若处理的表面在空气中暴露时间过长而不合格时, 应重新处理。
1. 2胶浆配制将由橡胶制品厂提供的, 符合要求的胶浆胶片剪成小条, 在120 号溶剂汽油中浸泡溶胀后, 搅拌成糊状, 再按配方要求比例补加汽油, 配制浓度为1∶4~1∶10 的胶浆, 置于阴凉处待用。
橡胶衬里施工方案

橡胶衬里施工方案橡胶衬里技术是目前在建筑和工业领域中广泛应用的一种防水、防潮、防腐方式。
橡胶衬里具有良好的柔韧性和抗腐蚀性能,能有效保护建筑结构和设备不受水分侵蚀和化学物质侵蚀,延长使用寿命。
本文将介绍一种基于橡胶衬里的施工方案,以帮助读者了解橡胶衬里施工的步骤和要点。
1. 施工前准备在进行橡胶衬里施工前,首先需要进行施工前准备工作。
包括清理施工区域,确保表面干净整洁,去除表面的油污、灰尘、杂物等,使基层表面平整,无明显凹凸。
检查基层结构是否存在裂缝、缺陷等问题,如有需要修补。
2. 衬里材料准备橡胶衬里施工所需的材料主要包括橡胶衬里卷材、专用胶水、底漆等。
在施工前,需要将材料按照施工要求准备齐全,确保施工过程顺利进行。
3. 衬里施工步骤3.1 底漆处理在进行橡胶衬里施工前,需要先进行底漆处理。
使用专用底漆,按照说明书要求进行施工。
底漆施工完成后,等待干燥。
3.2 橡胶衬里铺贴将预先准备好的橡胶衬里卷材按照要求进行铺贴。
在铺贴的过程中,需要注意保证衬里的平整、无皱、无空鼓等现象。
使用专用胶水将橡胶衬里固定在基层表面上。
3.3 焊接处理对橡胶衬里进行焊接处理,确保衬里的密封性。
根据施工要求,使用专用设备对衬里进行热焊接处理,使衬里之间的接缝处牢固密封,防止水分渗入。
4. 质量验收橡胶衬里施工完成后,需要进行质量验收。
检查整体施工效果,确保橡胶衬里与基层结合牢固,无空鼓、皱褶等问题。
对焊接处进行检查,保证密封性良好,无漏水现象。
5. 施工后维护橡胶衬里施工完成后,需要进行相应的维护保养工作。
注意定期清洁和检查橡胶衬里的情况,及时处理存在的问题,延长橡胶衬里的使用寿命。
橡胶衬里施工方案的实施过程中,需要注意细节,严格按照施工要求进行操作,确保施工质量和效果。
希望本文介绍的橡胶衬里施工方案能够帮助读者更好地了解橡胶衬里施工的步骤和要点,为相关工程的实施提供参考。
衬胶防腐施工方案

衬胶防腐施工方案1. 引言衬胶防腐施工是一种常用的防腐方法,特别适合于化工设备、储罐、管道和地下水工程等设施的防腐。
本文档将详细介绍衬胶防腐的施工方案,包括施工前的准备工作、施工过程的步骤和注意事项等。
通过该文档的指导,施工人员能够正确高效地进行衬胶防腐施工。
2. 施工前的准备工作在进行衬胶防腐施工之前,需要进行一系列的准备工作,以确保施工的顺利进行。
2.1 材料准备首先,需要准备好所需的材料,包括衬胶、底漆、中涂料、面涂料、溶剂等。
这些材料应根据实际施工需要进行选择,确保其质量合格、符合施工规范。
2.2 表面处理在施工前,需要对施工表面进行处理,以保证施工材料的粘接力和衬胶防腐层的牢固性。
表面处理的方法有机械除锈、喷砂清理等,根据不同的材料和施工要求选择合适的处理方法。
2.3 设备和环境检查在进行衬胶防腐施工前,需要对施工设备和环境进行检查,确保其符合施工要求。
检查内容包括设备的光洁度、温度、湿度等,以及施工现场的通风情况和防火安全等。
3. 施工步骤3.1 衬胶涂刷准备在进行衬胶涂刷前,需要将衬胶进行搅拌均匀,以使其成分充分混合。
准备完成后,使用专用刷子或喷枪将衬胶涂刷于施工表面上。
3.2 底漆涂刷在衬胶涂刷完成后,需要进行底漆的涂刷。
底漆涂刷的目的是增强衬胶与基础材料的粘接力并提高防腐效果。
底漆涂刷需要进行两遍,确保涂刷均匀,并且每遍涂刷间需要进行充分干燥。
3.3 中涂料涂刷底漆涂刷完成后,进行中涂料的涂刷。
中涂料的主要作用是增加防腐层的厚度,提高防腐性能。
根据需求,可以进行一到两遍的涂刷。
3.4 面涂料涂刷最后,进行面涂料的涂刷。
面涂料的主要作用是保护中涂料层,增加装饰效果。
面涂料需要进行两到三遍的涂刷,确保涂层的均匀和美观。
3.5 防腐层干燥在完成涂刷后,需要等待防腐层干燥。
干燥时间根据所使用的材料和环境条件而定,通常需要24小时以上。
在干燥期间,需要注意对施工现场的保护,避免外力对防腐层的损害。
橡胶衬里施工技术方案

橡胶衬里施工技术方案橡胶衬里是一种防腐蚀、耐磨损的材料,广泛应用于各种化工设备、储罐、污水处理设备等。
橡胶衬里的施工技术方案包括以下几个方面:1.材料准备和预处理:首先,需要准备好所需的橡胶衬里材料,包括橡胶片、胶粘剂、填料等。
在施工前,需要对材料进行预处理,如将橡胶片放置在室内自然展开一段时间,使其回复弹性,避免在施工过程中产生变形或开裂。
2.衬里面板的制作:根据设备的尺寸和形状,将橡胶片切割成适当的尺寸,并按照设备内部的曲率进行修剪。
然后,将橡胶片用胶粘剂粘贴在金属板上,确保其与金属板紧密粘接。
3.衬里面板的安装:在进行面板安装前,需要先将设备表面清洁干净,确保无油污、灰尘等杂质。
将橡胶面板按照设备内部的形状和尺寸,一个个粘贴在设备表面,确保每个面板之间的缝隙均匀,并用压力机或胶棒加压,使其与设备表面紧密贴合,排除空气。
4.补强和修补:在施工过程中,有时会出现橡胶面板的破损或缺失,需要进行补强和修补。
一般采用补片的方法,将橡胶片按照破损部位的形状修剪成合适的尺寸,用胶粘剂粘贴在破损处,确保与原衬里面板紧密贴合。
5.焊接和密封处理:在一些需要连接或固定的部位,如法兰、排气口等,需要采用焊接或密封处理,以确保其密封性。
橡胶衬里可以使用热压机进行焊接,将衬里面板进行热熔处理,使其与金属接头紧密连接。
对于需要密封的部位,可以使用密封胶或胶粘剂,填补缝隙,确保密封效果。
6.耐磨层涂覆:为了增加橡胶衬里的耐磨性能,可以在衬里面板上涂覆一层耐磨层。
耐磨层可以采用橡胶胶粘剂、橡胶嵌入物、金属焊丝等材料制成。
将耐磨层涂覆在衬里面板上,使其具有更高的耐磨性。
7.质量检验和保养:在施工完成后,需要对衬里施工进行质量检验,检查施工过程中是否存在问题,如是否有漏胶、气泡、开裂等情况。
对于存在问题的部位,需要进行修补和处理。
施工完成后,还需要定期进行保养,检查衬里的状况,如有破损和老化等情况,及时进行修补或更换。
总之,橡胶衬里施工技术方案涉及材料准备、表面处理、面板制作与安装、补强与修补、焊接与密封处理、耐磨层涂覆和质量检验与保养。
橡胶衬里施工技术方案强烈推荐

橡胶衬里施工技术方案强烈推荐橡胶衬里作为常用的防腐材料,被广泛应用于化工、电力、冶金等各个行业。
其具有优异的性能,如耐腐蚀、耐磨损、耐高温、抗老化等,是一种性价比高的防腐材料。
为了保证橡胶衬里的防腐效果,施工过程中需要严格控制工艺和工作流程。
下面就橡胶衬里施工技术方案进行详细介绍。
一、前期准备工作:1. 地基处理:清洁表面,去除松散混凝土、油污、灰尘及其他物质。
2. 基层处理:腐蚀采取除锈、打磨、喷砂等方法,切割吊顶防水被面,清理零散构件、扳手盖等遮蔽物。
3. 清洗处理:使用清洗剂洗刷地面,并彻底清洗积水沟,排干道中杂物及污水。
4. 水泥垫层:在混凝土地面上依次进行水泥砂浆、耐酸砂浆、普通砂浆层的抹灰和压平,保证基础整体性能。
5. 预埋件处理:钢筋预埋件洗刷去锈、涂刷防锈油。
二、胶皮材料施工:1. 混合胶料:按比例将A、B两部分胶料进行搅拌,保持混合均匀,避免过量混合。
2. 手工绕线:将胶皮材料绕于管件内,两层钢丝网套入,管道内外对接处喷1~2次涂料。
3. 机械绕线:将机械绕线机器的引线接通,将胶;皮材料由机器带动,绕于管件内,两层钢丝网套入,管道内外对接处喷1~2次涂料。
4. 填充胶料:用不锈钢填充器将胶皮材料中的气泡、缝隙等填满,确保胶皮材料等厚度,表面平滑饱满。
填缝时要注意不要引起反弹,应将填缝杆理直、理顺、实满,每次压实找平后即可填下一缝。
三、橡胶衬里辅料施工:1. 胶皮材料:经过再次混合后,进行单层或者双层涂敷,干燥过程中避免阳光直射或暴雨、强风等。
要按规定时间涂干第一层,然后再涂第二层着量,一定要保证厚度规格。
2. 过度滑线:将待处理管道端口用自攻螺丝固定钢片,然后用电动机将钢片全长套在管子上,确保钢片与管口连接紧密,然后使用过度滑线器进行滑线。
3. 开始衬里:衬里时应将衬材的塑化剂分装并注入胶皮材内,再将其放入被衬物内,用麻袋翻折,将胶皮材料周围的空气从中隔离出来,保证衬材将物体内的空气隔绝。
橡胶衬里施工技术方案(强烈推荐!)

橡胶衬里施工技术方案(专业化工施工单位编制—强烈推荐!!!)工程名称:编制单位:一、总则××公司以一流的产品质量、一流的技术,以客户至上的精神,保质保量的完成“山东××化工有限公司衬胶设备"1。
1根据“山东××公司衬胶设备”1。
2根据相关标准1.3根据××公司各种胶板及内衬的施工规范.工程概况:二、材料来源1.所有橡胶衬里材料均由××公司生产,水洗塔衬里材料外购。
2.所有衬里的施工均由××公司承担.3.所有材料将视××公司施工进度提前发至建设工地现场,提供合格证和发货清单给甲方,在甲方对其供货渠道和质量认可后方可开始施工。
4.材料经需方认可后存放于事先准备好的仓库中。
三、材料介绍1.预硫化丁基胶板性能××公司生产的预硫化丁基胶板 P—CIIR-28 4㎜,完全满足水洗塔介质腐蚀耐磨损的要求,有关物理化学指标如下:橡胶衬里组分:橡胶衬里的物理性能:(预硫化丁基胶板P—CIIR—28)胶板物化性能表底涂材料的性能粘接剂材料性能:1.硫化丁基胶衬里工艺预硫化橡胶板衬里工艺规程1。
目的规范预硫化橡胶板衬里各道工序作业。
2。
适用范围预硫化橡胶板防腐衬里。
3。
引用标准GB18241.1—2001 橡胶衬里第一部分设备防腐衬里HGJ32—1990 橡胶衬里化工设备4.职责技术部:负责控制工艺规程实施过程中的操作性及工艺修订工作。
质检部:负责各道工序质量控制,协助工艺规程修订.生产部:负责工艺规程的实施工作,并及时反馈意见,协助工艺规程修订。
5。
预硫化橡胶板衬里工艺流程钢体检查处理胶板准备喷砂胶粘剂制备下料清洗涂底涂料打毛清洗涂刷胶粘剂贴衬检查处理封口验收6.橡胶衬里设备检查处理6.1橡胶衬里设备、管道及管件结构设计制作应符合HGJ32-90标准中第4条规定。
橡胶板防腐衬里工程施工方案
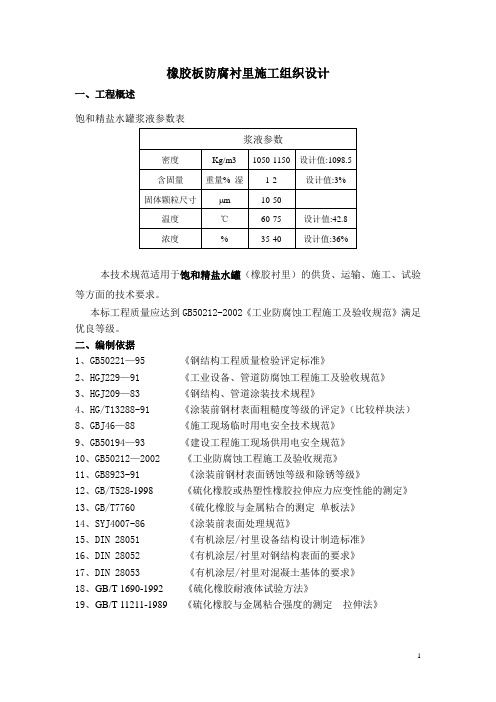
橡胶板防腐衬里施工组织设计一、工程概述饱和精盐水罐浆液参数表本技术规范适用于饱和精盐水罐(橡胶衬里)的供货、运输、施工、试验等方面的技术要求。
本标工程质量应达到GB50212-2002《工业防腐蚀工程施工及验收规范》满足优良等级。
二、编制依据1、GB50221—95 《钢结构工程质量检验评定标准》2、HGJ229—91 《工业设备、管道防腐蚀工程施工及验收规范》3、HGJ209—83 《钢结构、管道涂装技术规程》4、HG/T13288-91 《涂装前钢材表面粗糙度等级的评定》(比较样块法)8、GBJ46—88 《施工现场临时用电安全技术规范》9、GB50194—93 《建设工程施工现场供用电安全规范》10、GB50212—2002 《工业防腐蚀工程施工及验收规范》11、GB8923-91 《涂装前钢材表面锈蚀等级和除锈等级》12、GB/T528-1998《硫化橡胶或热塑性橡胶拉伸应力应变性能的测定》13、GB/T7760 《硫化橡胶与金属粘合的测定单板法》14、SYJ4007-86 《涂装前表面处理规范》15、DIN 28051 《有机涂层/衬里设备结构设计制造标准》16、DIN 28052 《有机涂层/衬里对钢结构表面的要求》17、DIN 28053 《有机涂层/衬里对混凝土基体的要求》18、GB/T 1690-1992 《硫化橡胶耐液体试验方法》19、GB/T 11211-1989 《硫化橡胶与金属粘合强度的测定拉伸法》三、目的本施工组织设计主要内容包括施工平台搭建、衬里壳体的母材验收标准、喷砂施工、以及橡胶内衬施工、各种措施等。
四、施工组织机构设置为配合贵方圆满完成该项工程,我们精心设计、合理选材、严密施工,以期达到延长产品使用寿命,减少维修次数,降低运营成本的目的,从而增强企业的社会效益和经济效益。
1、机构设置图:(见下图)2、项目经理岗位责任制:2.1组织现场的施工工作。
2.2组织监督现场召开每日工作会议,并做好会议记录。
橡胶衬里施工方案

橡胶衬里工程施工方案为了达到预期的防腐效果,我们从用材,设计,施工到管理方面综合考虑。
正确造材,合理的设计,认真施工,妥善管理。
以期达到延长设备使用寿命,减少维修次数,降低经营成本的目地,从而有效地增强企业的社会效益与经济效益。
、编制依据:1、SHJ400乙86《涂装前钢材表面处理规范》2、HGJ229-91《工业设备,管道防腐蚀工程施工及规范》3、GB8923《涂装前钢材表面锈蚀等级和除锈等级》4、HG/T20677-1990《橡胶衬里化工设备》5、HGJ33-91《衬里钢壳设计规定》6、我公司在同类工程中的施工经验。
二、开工前的准备:1 、材料组织:防腐蚀工程的选材直接关系到工程的使用寿命,因此一定要按照腐蚀介质的程类和特征,工程的重要程度,作用部位的大小,物理机械作用的实际情况,结合材料的耐腐蚀性能及特点,合理的选用.我们的选材原则是:A:材料的物理,化学性能满足设计要求.B:材料的耐蚀,耐候性佳.C:总的经济效果优越.内壁采用喷砂除锈,然后衬丁基橡胶板。
2、人员组织:在开工前组织有领导能力,管理能力,组织能力和丰富现场施工经验的人担任项目经理,选派有丰富施工经验,有扎实的技术理论知识的工程师担任技术负责人,在开工前组建技术领导小组,组织图纸的自审及会审,并拟定参加工程施工的劳动组织,由技术领导小组织对施工班组进行技术交底.3、机具组织:在开工前对计量器具进行校验,对机械进行安装调试,以便使开工后的计量数字准确无误,机械无故障。
拟投入工程的主要机具一览表序号名称91011121314 搅拌机7.5KW 轴流风机电火花测漏仪6m3/mm 空压机砂罐气体缓冲罐工具车手提砂轮机操作平台直尺剪刀坡口刀钢卷尺白布数量2台2台1台4台4台4台5辆20台1台10 把20 把20 把20 把10 卷产地武汉北京天津蚌埠自制自制四川石家庄石家庄石家庄郑州上海徐州性能完好完好完好完好完好完好完好完好完好完好完好完好完好注:以上工具用量可根据现场实际情况增减。
热硫化橡胶衬里防腐施工方案doc
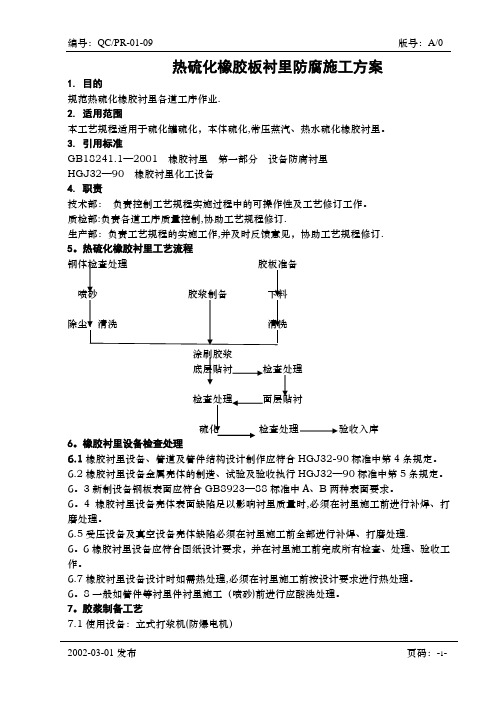
热硫化橡胶板衬里防腐施工方案1.目的规范热硫化橡胶衬里各道工序作业.2.适用范围本工艺规程适用于硫化罐硫化,本体硫化,常压蒸汽、热水硫化橡胶衬里。
3.引用标准GB18241.1—2001 橡胶衬里第一部分设备防腐衬里HGJ32—90 橡胶衬里化工设备4.职责技术部:负责控制工艺规程实施过程中的可操作性及工艺修订工作。
质检部:负责各道工序质量控制,协助工艺规程修订.生产部:负责工艺规程的实施工作,并及时反馈意见,协助工艺规程修订.5。
热硫化橡胶衬里工艺流程钢体检查处理胶板准备喷砂下料涂刷胶浆底层贴衬检查处理检查处理面层贴衬硫化检查处理验收入库6。
橡胶衬里设备检查处理6.1橡胶衬里设备、管道及管件结构设计制作应符合HGJ32-90标准中第4条规定。
6.2橡胶衬里设备金属壳体的制造、试验及验收执行HGJ32—90标准中第5条规定。
6。
3新制设备钢板表面应符合GB8923—88标准中A、B两种表面要求。
6。
4橡胶衬里设备壳体表面缺陷足以影响衬里质量时,必须在衬里施工前进行补焊、打磨处理。
6.5受压设备及真空设备壳体缺陷必须在衬里施工前全部进行补焊、打磨处理.6。
6橡胶衬里设备应符合图纸设计要求,并在衬里施工前完成所有检查、处理、验收工作。
6.7橡胶衬里设备设计时如需热处理,必须在衬里施工前按设计要求进行热处理。
6。
8一般如管件等衬里件衬里施工(喷砂)前进行应酸洗处理。
7。
胶浆制备工艺7.1使用设备:立式打浆机(防爆电机)7。
2胶浆制备前应检查胶浆胶片及溶剂质量。
7。
3胶浆制备条件见表1.7.4胶浆制备过程中应远离火源,并控制打浆机温度.7。
5胶浆制备完毕检查质量合格后,倒入专用密封容器以备使用。
8.衬里施工工艺8。
1一般要求8.1.1施工环境温度以15-30℃为宜,相对湿度不大于70%,温度低于15℃或不高于露点温度3℃时应采用增温措施,但不能使用明火,当温度高于35℃以上时应尽量缩短操作时间及避免阳光直照设备外壳.当相对湿度高于70%以上时应采用除湿措施。
橡胶衬里防腐施工方案
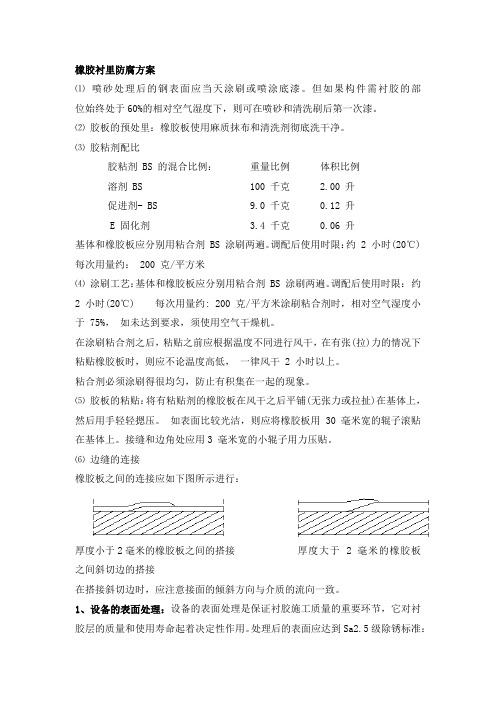
橡胶衬里防腐方案⑴喷砂处理后的钢表面应当天涂刷或喷涂底漆。
但如果构件需衬胶的部位始终处于60%的相对空气湿度下,则可在喷砂和清洗刷后第一次漆。
⑵胶板的预处里:橡胶板使用麻质抹布和清洗剂彻底洗干净。
⑶胶粘剂配比胶粘剂 BS 的混合比例:重量比例体积比例溶剂 BS 100 千克 2.00 升促进剂- BS 9.0 千克0.12 升E 固化剂 3.4 千克0.06 升基体和橡胶板应分别用粘合剂 BS 涂刷两遍。
调配后使用时限:约 2 小时(20℃) 每次用量约: 200 克/平方米⑷涂刷工艺:基体和橡胶板应分别用粘合剂 BS 涂刷两遍。
调配后使用时限:约2 小时(20℃) 每次用量约: 200 克/平方米涂刷粘合剂时,相对空气湿度小于 75%,如未达到要求,须使用空气干燥机。
在涂刷粘合剂之后,粘贴之前应根据温度不同进行风干,在有张(拉)力的情况下粘贴橡胶板时,则应不论温度高低,一律风干 2 小时以上。
粘合剂必须涂刷得很均匀,防止有积集在一起的现象。
⑸胶板的粘贴:将有粘贴剂的橡胶板在风干之后平铺(无张力或拉扯)在基体上,然后用手轻轻摁压。
如表面比较光洁,则应将橡胶板用 30 毫米宽的辊子滚贴在基体上。
接缝和边角处应用3 毫米宽的小辊子用力压贴。
⑹边缝的连接橡胶板之间的连接应如下图所示进行:厚度小于2毫米的橡胶板之间的搭接厚度大于 2 毫米的橡胶板之间斜切边的搭接在搭接斜切边时,应注意接面的倾斜方向与介质的流向一致。
1、设备的表面处理:设备的表面处理是保证衬胶施工质量的重要环节,它对衬胶层的质量和使用寿命起着决定性作用。
处理后的表面应达到Sa2.5级除锈标准:即Sa2.5级,彻底除掉金属表面上的油脂、氧化皮、锈蚀产物等一切杂物。
表面无任何可见残留物,呈现均一定的金属本色、并有一定的粗糙度。
除锈后的表面应用干燥、洁净的空气吹扫干净,应在8小时之内涂刷第一胶浆,防止重新锈蚀。
2、胶板的外观质量检查:胶板不应有>0.5mm的外来杂质。
橡胶衬里施工技术方案

橡胶衬里施工技术方案工程名称:热电联供车间阴、阳床内部衬胶编制单位:一、总则我公司以一流的产品质量、一流的技术,以客户至上的精神,保质保量的完成“热电联供车间阴、阳床内部衬胶”1.1根据“衬胶设备”1.2根据相关标准1.3根据贵公司各种胶板及内衬的施工规范。
工程概况:二、材料来源1.所有衬里的施工均由我公司承担。
2.所有材料将视我公司施工进度提前发至建设工地现场,提供合格证和发货清单给甲方,在甲方对其供货渠道和质量认可后方可开始施工。
3.材料经需方认可后存放于事先准备好的仓库中。
三、材料介绍1.预硫化丁基胶板性能预硫化丁基胶板 P-CIIR-28 2㎜,完全满足介质腐蚀耐磨损的要求,有关物理化学指标如下:橡胶衬里组分:橡胶衬里的物理性能:(预硫化丁基胶板P-CIIR-28)胶板物化性能表底涂材料的性能粘接剂材料性能:1.硫化丁基胶衬里工艺预硫化橡胶板衬里工艺规程1.目的规范预硫化橡胶板衬里各道工序作业。
2.适用范围预硫化橡胶板防腐衬里。
3.引用标准GB18241.1-2001 橡胶衬里第一部分设备防腐衬里HGJ32-1990 橡胶衬里化工设备4.职责技术部:负责控制工艺规程实施过程中的操作性及工艺修订工作。
质检部:负责各道工序质量控制,协助工艺规程修订。
生产部:负责工艺规程的实施工作,并及时反馈意见,协助工艺规程修订。
5.预硫化橡胶板衬里工艺流程钢体检查处理胶板准备喷砂胶粘剂制备下料清洗涂底涂料打毛清洗涂刷胶粘剂贴衬检查处理封口验收6.橡胶衬里设备检查处理6.1橡胶衬里设备、管道及管件结构设计制作应符合HGJ32-90标准中第4条规定。
6.2橡胶衬里设备金属壳体的制造、试验及验收执行HGJ32-90标准中第5条规定。
6.3新制设备钢板表面应符合GB8293-88标准中A、B两种表面要求。
6.4橡胶衬里设备壳体表面缺陷足以影响衬里质量时,必须在衬里施工前进行补焊、打磨处理。
6.5橡胶衬里设备应符合图纸设计要求,并在衬里施工前完成所检查、处理、验收工作。
橡胶衬里的施工方案

橡胶衬里的施工方案
橡胶衬里是一种具有强大耐磨性和耐化学腐蚀的纸浆制品,广泛应用于化工、矿山、煤炭、电力、冶金、电子等行业中的输送设备和容器内衬、地面铺设等领域。
在进行橡胶衬里的施工方案时,需要按照以下步骤进行:
一、准备工作
1. 检查施工现场,确保环境干燥、清洁,并清除任何杂物。
2. 仔细检查设备和容器的表面,确保没有严重的破损和锈蚀,并进行必要的修复和处理。
二、基层处理
1. 将基层表面进行打磨、清洗,确保表面光滑、洁净。
2. 铺设防潮层,可采用防潮胶、环氧防潮底涂等材料,以提高橡胶衬里的附着力和耐候性。
三、橡胶衬里施工
1. 将橡胶衬片进行切割,按照设备和容器的尺寸进行定制,确保精准贴合。
2. 使用专用的橡胶胶水或胶粘剂,将橡胶片粘贴在基层表面上。
注意要均匀涂胶,避免出现气泡和空隙。
3. 在橡胶片表面进行压实,确保其与基层的贴合牢固。
4. 检查施工质量,修补可能存在的瑕疵和不平整处。
四、后期处理
1. 施工完毕后,需进行全面检查,确保橡胶衬里的质量符合要求。
2. 清理施工现场,清除任何杂物和残留胶水。
橡胶衬里施工方案的要点是确保基层表面的光滑洁净,橡胶衬片的粘贴牢固和无空隙,并进行全面的质量检查。
在施工中,应严格按照标准操作,确保施工质量,提高橡胶衬里的使用寿命和安全性。
橡胶防腐施工方案

橡胶防腐施工方案1. 引言本文档旨在提供一份橡胶防腐施工方案,以保护设施免受腐蚀的影响。
本方案旨在通过使用橡胶材料及适当的施工技术,提供一种可行的解决方案。
2. 施工准备在进行施工前,需要进行以下准备工作:- 确定防腐施工的具体区域;- 清理施工区域,确保表面干净无尘;- 准备好所需的工具和材料;- 确保工作人员具备必要的防护措施。
3. 施工步骤3.1 表面处理- 清理施工区域,将残留的油脂、锈迹等污物清除干净;- 使用砂纸或钢丝刷将表面进行打磨,以增加粘接力;- 清洁表面,确保无尘。
3.2 橡胶涂料施工- 根据橡胶涂料的使用说明,将涂料充分搅拌均匀;- 使用合适的刷子或滚筒将橡胶涂料均匀涂布在施工区域上;- 确保涂料的厚度均匀且到达所需的防腐效果;- 根据橡胶涂料的干燥时间,进行适当的晾干。
3.3 检查和维护- 在施工完成后,进行必要的检查,确保施工质量符合要求;- 定期检查防腐层的状况,并进行必要的维护;- 如发现任何问题或损坏,及时修补或更换防腐层。
4. 安全注意事项在进行橡胶防腐施工时,需要注意以下安全事项:- 使用合适的个人防护装备,如手套、护目镜等;- 遵循橡胶涂料的使用说明,避免接触皮肤或吸入有害气体;- 在通风良好的环境下施工,避免因有害气体积聚而影响工作人员健康;- 妥善存放和处理废弃物,避免对环境造成污染。
5. 总结本橡胶防腐施工方案提供了一种保护设施免受腐蚀的有效方法。
通过遵循施工准备、施工步骤和安全注意事项,可以确保防腐层的质量和性能。
定期检查和维护也是确保防腐效果的重要措施。
橡胶衬里方案教材

防腐衬里施工组织设计方案一、编制依据1、GB50221—95 《钢结构工程质量检验评定标准》2、HGJ229—91 《工业设备、管道防腐蚀工程施工及验收规范》3、HGJ209—83 《钢结构、管道涂装技术规程》4、GBJ46—88 《施工现场临时用电安全技术规范》5、GB50194—93 《建设工程施工现场供用电安全规范》6、HG/T20677-1990 《橡胶衬里化工设备》7、HG/T2451-2004 《设备防腐橡胶衬里》8、JC/T424-2005 《耐酸耐温砖》8、根据我公司多年来在同类工程中现场防腐施工经验二、施工前准备检查设备基体是否合格达到防腐施工要求。
将现场所用的能源如水、电接至设备旁待用;配设电源系统、照明设备和安全设备以及环境空气调节设备;根据设备基体结构,塔建防雨防尘工棚;喷砂设备、喷砂材料与涂层材料的到位以及设置工作间与工作台;现场施工时所做的粘接强度样块,将根据设备的面积按施工经验而定。
施工所需的水、电点与设备的距离控制在10m范围内。
1、人员组织:整个工程分四个班,同时进行架子班、喷砂班、玻璃鳞片同时进行工作。
在基体喷砂后。
每班施工人员又分成三组,三组人员紧密协作,为一个共同的目标保质保期完成任务。
由公司选派身体健康、在火电厂烟气脱硫工程中有丰富防腐施工经验、懂得喷砂除锈、玻璃鳞片衬里、橡胶衬里技术的人员参加本项工程施工,并组织有扎实技术知识、丰富现场施工经验的技术负责人,在开工前三天到达施工现场,搭设临时设施、对压缩空压机进行调试,并深入施工现场,观察了解腐蚀状况及施工环境,掌握第一手资料,对施工班组进行技术交底,让班组对工程施工做到心中有数,不打盲目仗。
2、由公司组织和配备性能完好的机械和计量准确的计量器具进入施工现场,并在开工前对机械进行调试,对计量器具进行校验,以便在施工中机械无故障,计量数字准确无误。
施工器具:准备好施工所用的空气压缩机、砂罐、缓冲罐、砂袋、喷砂枪、烙铁、压辊、各种毛刷、钢板尺、弯尺、划规和剪刀。
- 1、下载文档前请自行甄别文档内容的完整性,平台不提供额外的编辑、内容补充、找答案等附加服务。
- 2、"仅部分预览"的文档,不可在线预览部分如存在完整性等问题,可反馈申请退款(可完整预览的文档不适用该条件!)。
- 3、如文档侵犯您的权益,请联系客服反馈,我们会尽快为您处理(人工客服工作时间:9:00-18:30)。
热硫化橡胶板衬里防腐施工方案1.目的规范热硫化橡胶衬里各道工序作业。
2.适用范围本工艺规程适用于硫化罐硫化,本体硫化,常压蒸汽、热水硫化橡胶衬里。
3.引用标准GB18241.1-2001 橡胶衬里第一部分设备防腐衬里HGJ32-90 橡胶衬里化工设备4.职责技术部: 负责控制工艺规程实施过程中的可操作性及工艺修订工作。
质检部:负责各道工序质量控制,协助工艺规程修订。
生产部:负责工艺规程的实施工作,并及时反馈意见,协助工艺规程修订。
5.热硫化橡胶衬里工艺流程钢体检查处理胶板准备喷砂胶浆制备下料涂刷胶浆底层贴衬检查处理检查处理面层贴衬硫化检查处理验收入库6.橡胶衬里设备检查处理6.1橡胶衬里设备、管道及管件结构设计制作应符合HGJ32-90标准中第4条规定。
6.2橡胶衬里设备金属壳体的制造、试验及验收执行HGJ32-90标准中第5条规定。
6.3新制设备钢板表面应符合GB8923-88标准中A、B两种表面要求。
6.4橡胶衬里设备壳体表面缺陷足以影响衬里质量时,必须在衬里施工前进行补焊、打磨处理。
6.5受压设备及真空设备壳体缺陷必须在衬里施工前全部进行补焊、打磨处理。
6.6橡胶衬里设备应符合图纸设计要求,并在衬里施工前完成所有检查、处理、验收工作。
6.7橡胶衬里设备设计时如需热处理,必须在衬里施工前按设计要求进行热处理。
6.8一般如管件等衬里件衬里施工(喷砂)前进行应酸洗处理。
7.胶浆制备工艺7.1使用设备:立式打浆机(防爆电机)7.2胶浆制备前应检查胶浆胶片及溶剂质量。
7.3胶浆制备条件见表1。
7.4胶浆制备过程中应远离火源,并控制打浆机温度。
7.5胶浆制备完毕检查质量合格后,倒入专用密封容器以备使用。
8.衬里施工工艺8.1一般要求8.1.1施工环境温度以15-30℃为宜,相对湿度不大于70%,温度低于15℃或不高于露点温度3℃时应采用增温措施,但不能使用明火,当温度高于35℃以上时应尽量缩短操作时间及避免阳光直照设备外壳。
当相对湿度高于70%以上时应采用除湿措施。
8.1.2施工现场应防尘、防火,保持干燥,通风良好,施工人员的手、工作服及衬里用具应保持清洁。
8.1.3施工人员进入设备内施工应穿软底鞋以防止损坏衬里层。
8.2喷砂8.2.1喷砂前橡胶衬里设备应完成所有检查处理验收工作。
8.2.2喷砂前应预先检查设备是否正常并穿戴劳保用品。
8.2.3喷砂用砂为钢砂,粒径为8-16目。
钢砂应不含有粘土及其它杂物。
使用前钢砂必须烘干或晒干,过筛后才能重新使用。
8.2.4喷砂时应从设备一端开始,逐渐向另一端移动。
8.2.5喷砂时喷嘴与金属表面一般距50-80mm;喷射角度不小于30º,走枪速度均匀,不能有漏喷和欠喷现象。
8.2.6喷砂质量等级应达到GB8923-88标准中Sa3级规定:(1)显出均匀一致的金属本色。
(2)除净金属氧化物和其它附着物。
(3)喷砂后应处于干燥状态,不得被其它物质污染。
8.3衬里施工8.3.1除尘、清洗橡胶衬里设备喷砂验收合格后及时除清灰尘、砂粒,用溶剂清洗,以便涂刷第一遍胶浆以防返锈。
8.4胶板准备8.4.1衬里胶板质量应符合GB18241.1-2001标准规定。
8.4.2衬里胶板在使用前应检验合格。
8.4.3胶板复合胶板联合衬里时原则上衬里厚度不大于δ4mm的情况下在胶板下料贴衬前应将两种胶板复合成型,衬里厚度大于δ4mm时应采用分层贴衬。
具体工艺要求执行技术部门下达的工艺指令。
8.5胶板下料8.5.1胶板下料前应检查胶板外观质量,并对不符合GB18241.1-2001标准要求的缺陷进行处理。
8.5.2下料时要求准确合理,尽量减少接缝数量,尽量减少贴衬应力,减轻贴衬难度。
8.5.3形状复杂的工件(部位)应预先制作样板,按样板下料。
8.5.4管道胶板下料时,应按略小于管道内径的原则计算其周长(不包括接缝宽度),其总长度应等于管道实际长度加上法兰翻边。
8.5.5胶板下料时必须预留接缝宽度。
8.5.6胶板下料完毕后,对胶板接缝边进行削边,剖口宽度为胶板厚度的3.5-5倍。
8.5.7剖口应宽窄一致,平直。
8.5.8削剖口时注意接缝方向及介质流向,特别是联合衬里时必须严格注意。
8.5.9胶板下料削边完毕后用溶剂清洗粘合面,并根据技术部门下达的工艺指令对贴合面进行打毛。
8.6涂刷胶浆8.6.1胶浆使用前应充分搅匀,并检查胶浆浓度,如浓度过大时用溶剂稀释。
8.6.2设备喷砂清洗完毕后,应在4h内涂完第一遍胶浆,以防返锈。
8.6.3第一遍胶浆溶剂完全挥发后才能进行第二遍胶浆涂刷。
8.6.4胶浆涂刷次数:金属壳体表面涂刷三遍,胶板表面涂刷二遍,双层贴衬时,胶板表面各涂刷胶浆二遍。
8.6.5多层贴衬时,底层贴衬完毕后,必须用溶剂清洗粘合面后再涂刷胶浆。
8.6.6胶浆涂刷时应薄而均匀,防止胶浆堆积、流淌或起泡。
8.6.7前后两遍胶浆的涂刷方向应依次交错涂刷。
8.6.8涂刷管道胶浆时,管道应斜放并转动。
8.6.9设备壳体不影响衬里质量的缺陷在涂刷未遍胶浆前,用同类胶条填平。
8.6.10涂刷最后一遍胶浆后,必须在3h内进行贴衬。
8.6.11胶浆涂刷后,应防止灰尘、油、水或其它杂物落入。
8.7胶板贴衬8.7.1胶板贴衬时未遍胶浆溶剂已完全挥发。
8.7.2胶板贴衬时设备壳体缺陷已用同类胶条填平并已涂刷胶浆。
8.7.3贴衬时胶浆层应保持完整,如被粘掉、擦伤等应重新补刷胶浆晾干后再进行贴衬。
8.7.4胶板贴衬先后顺序视设备结构而定,并依据下料削口顺序。
8.7.5胶板贴衬时不能使用排气线,特殊情况依据技术部门下达的工艺指令。
8.7.6胶板贴衬时用垫布卷取铺放,铺放位置应准确,不得起褶或受拉变薄,影响贴衬质量。
8.7.7胶板贴衬时必须划线贴衬,确保贴衬边口平直及接缝宽窄一致、平直。
8.7.8胶板辅放完毕后,依次脱开垫布进行辊压。
8.7.9辊压时必须先将拐角处用角辊辊压无气孔后再进行拐角边辊压,严禁先压边后辊压拐角造成气孔。
8.7.10辊压时应划线依次辊压,确保粘合紧密,并防止产生气泡。
每块胶板贴衬完毕后用窄辊压实接缝边。
8.7.11胶板贴切衬接缝方向遵循下列原则:a.接缝方向顺向介质流向;b.转动设备接缝方向顺向转动方向。
8.7.12胶板贴衬接缝宽度及方法:单层贴衬时一般采用搭接,接缝宽度≥25mm;多层贴衬时内层胶一般采用对接,接缝宽度≥20mm,过搭宽度不大于3mm,面层胶采用搭接,接缝宽度≥25mm。
8.7.13胶板贴衬时接缝应平直,不得采用十字接缝,应采用T字接缝。
8.7.14多层贴衬时,上、下层接缝应错位,一般应不小于100mm,特殊部位最少不少于50mm。
8.7.15硫化后需加工部位,胶层厚度应留有加工余量。
8.7.16管道贴衬时,涂刷胶浆晾干后,先将胶板根据管道内径粘成圆筒状(略小于管道内径),然后用垫布垫好轻轻拖入管内定位后脱布辊压。
8.7.17管道辊压遵循先压里后翻边的原则,法兰边先用同类胶板加厚涂刷胶浆后再翻边。
8.7.18多层贴衬时,每层贴衬完毕后必须进行外观质量检查及电火花检测,检测依据GB18241.1-2001标准、HGJ32-90标准中第7条,对缺陷及漏电部位进行修复后才能进行第二层贴衬。
8.7.19胶板厚度大于4mm贴衬时,应对胶板进行预热,预热温度为50-60℃。
8.7.20胶板贴衬全过程中,严禁用烙铁铲剖口或搭边。
8.7.21胶板贴衬面层完毕后,进行外观检查及火花检测。
并对缺陷进行修复,检测依据GB18241.1-2001标准、HGJ32-90标准中第7条。
8.7.22缺陷修复方法:a.气泡及漏电部位:先将气泡及漏电部位切开,四边切成20-25mm宽剖口,然后用同类胶板下料成同样尺寸并切成20-25mm宽剖口,采用对接方法修复。
b.凹陷及外伤印痕及嵌杂物等:先清除杂物用同类胶条补平。
使用工具:烙铁;温度:80-100℃。
8.7.23胶板面层贴衬完毕后,用烙铁烙实接缝边。
烙铁温度为80-100℃。
8.7.24胶板贴衬时必须强调贴衬外观质量及美观性。
8.7.25衬里设备贴衬完毕后,应停放24h以上(最长不得超过7天)然后硫化。
8.8硫化8.8.1硫化罐硫化a.使用设备:4m×12m硫化罐,3.8mm×14m硫化罐,1.7m×4m硫化罐,空压机。
b.硫化方法为恒压混气硫化法。
亦即在恒压条件下进行硫化,压力为0.3MPa压缩空气,再逐步加入蒸汽置换冷空气,硫化完毕后再加入压缩空气降温。
c.硫化注意事项:.硫化前应先做好一切准备工作,如法兰堵头,固定等,硫化前必须对吊装、装罐时损坏部位进行修复。
.硫化过程中严格控制上下温差,确保硫化温度基本一致。
.升温及正硫化过程中确保蒸汽压力稳定,如发生故障应及时补充压缩空气,待故障排除后继续硫化,或补充压缩空气降温中止硫化。
.硫化过程中每隔10分钟排一次冷凝水。
.硫化人员必须坚守岗位,并做好硫化记录。
8.8.2本体硫化a.本体硫化前题条件是受衬设备能承受0.3Mpa以上压力,现场配备有蒸汽。
b.本体硫化采用恒压硫化方式。
c.本体硫化前必须做好下列工作:·外保温:受衬设备必须用保温棉保温,保证受衬设备内外温度基本一致。
·设置硫化管道(包括蒸汽管道、压缩空气管道)确保硫化时汽量供应及能及时调节设备内部温差,确保同步硫化。
·在设备最低处设置排冷却水装置及根据设备情况在设备顶部设置排空装置。
·在设备上、中、下三部位设置测温装置,以便及时测量温度及调整温差。
·设置二个以上压力表。
·设备所有接管法兰必须用带压堵头密封,并能保证法兰面及接管硫化。
·设置测量外壁温度装置。
·配备空压机。
d.硫化前先加入压缩空气,硫化升温时要根据设备温差情况逐步升温,勿快速升温。
e.本体硫化曲线必须依据设备具体及现场情况确定,具体参考执行技术部下达的工艺指令。
8.8.3常压蒸汽硫化a.常压蒸汽硫化是在100℃左右完成硫化的一种硫化方法,其硫化压力<0.075Mpa,现场备有蒸汽。
b.常压蒸汽硫化受衬设备为常压设备(能全部密封)。
c.硫化前必做好下列工作:·外保温受衬设备必需用保温棉保温,保证受衬设备内外温度基本一致。
·设置硫化管道(包括蒸汽管道、压缩空气管道),确保硫化时汽量供应及能及时调节设备内部温差,确保同步硫化。
·在设备最低处设置排冷却水装置及根据设备情况在设备顶部设置排装置。
·在设备上中下三部位设置测温装置,以便及时测量温度及调整温差。
·设置二个以上压力表。
·设备所有接管法兰的须密封,并能保证法兰面及接管硫化。
·设置测量外壁温度装置。
·配备空压机。