橡胶技术网
橡胶技术网 - 耐高温低压缩变形三元乙丙胶料的试验

〔1〕朱明华 编《仪器分析》高等教育出版社 1983 年 5 月 P27~39 。 〔2〕李浩春主编《分析化学手册 · (第二版) ·第五分册 ·气相色
谱分析》化学工业出版社 1999 年 3 月 P59~190 。
www1 chemstandard1 com1 cn/
能正常工作 。为了解决这一问题 , 我们从乙丙胶的 牌号 、硫化剂 、促进剂 、补强剂等方面做了大量的 对比实验 , 从中选出了较好的配方 , 来满足乙丙胶 在高温条件下低压缩变形的要求 。
2 材质的选择
21 1 三元乙丙胶牌号的确定 一般来讲乙烯含量在 60 %左右三元乙丙胶的
加工性能和硫化胶物理机械性能较好 , 所以多数乙 丙胶乙烯含量均控制在这个范围内 。故选择了如下 厂家生产的不同牌号乙丙胶做对比试验 。见表 1 。
30 43 高
从不同厂家生产的不同牌号的乙丙胶在 150 ℃ 高温下做压缩变形对比试验 , 结果如下 : 4045 胶2 361 4 ; EP33 胶2401 6 ; 505A 胶2341 2 。数 据 表 明 : 4045 和 505A 二个牌号的压缩变形值比较好 , 而且 基本接近 。三种牌号都是日本产的 , 其中 4045 是 目前我国大量进口的 , 所以采用 4045 牌号胶进行
3 采用二次硫化提高耐热性
因硫化体系选用的过氧化物 、少量硫磺 、二硫 化四乙基秋兰姆 、共交联剂等都具有耐热性 , 硫化 曲线平坦 、宽广 。为进一步加深硫化程度 , 提高耐 热性 , 减小压缩变形 , 采用在空气老化箱中 130 ℃ ×8h 二次硫化 。分析认为第一次硫化分解后的游 离基还存在 , 二次硫化时游离基可能起作用 。经二 次硫化后测得的压缩变形 (150 ℃×24h) 为 241 8 , 达到预期目的 。
橡胶的工艺流程

橡胶的工艺流程(精品)2014—10—22橡胶技术网橡胶工艺流程开始1 综述橡胶制品的主要原料是生胶、各种配合剂、以及作为骨架材料的纤维和金属材料,橡胶制品的基本生产工艺过程包括塑炼、混炼、压延、压出、成型、硫化6个基本工序.橡胶的加工工艺过程主要是解决塑性和弹性矛盾的过程,通过各种加工手段,使得弹性的橡胶变成具有塑性的塑炼胶,在加入各种配合剂制成半成品,然后通过硫化是具有塑性的半成品又变成弹性高、物理机械性能好的橡胶制品。
2 橡胶加工工艺2.1塑炼工艺生胶塑炼是通过机械应力、热、氧或加入某些化学试剂等方法,使生胶由强韧的弹性状态转变为柔软、便于加工的塑性状态的过程.生胶塑炼的目的是降低它的弹性,增加可塑性,并获得适当的流动性,以满足混炼、亚衍、压出、成型、硫化以及胶浆制造、海绵胶制造等各种加工工艺过程的要求.掌握好适当的塑炼可塑度,对橡胶制品的加工和成品质量是至关重要的。
在满足加工工艺要求的前提下应尽可能降低可塑度。
随着恒粘度橡胶、低粘度橡胶的出现,有的橡胶已经不需要塑炼而直接进行混炼。
在橡胶工业中,最常用的塑炼方法有机械塑炼法和化学塑炼法。
机械塑炼法所用的主要设备是开放式炼胶机、密闭式炼胶机和螺杆塑炼机。
化学塑炼法是在机械塑炼过程中加入化学药品来提高塑炼效果的方法.开炼机塑炼时温度一般在80℃以下,属于低温机械混炼方法.密炼机和螺杆混炼机的排胶温度在120℃以上,甚至高达160-180℃,属于高温机械混炼。
生胶在混炼之前需要预先经过烘胶、切胶、选胶和破胶等处理才能塑炼.几种胶的塑炼特性:天然橡胶用开炼机塑炼时,辊筒温度为30—40℃,时间约为15—20min;采用密炼机塑炼当温度达到120℃以上时,时间约为3-5min。
丁苯橡胶的门尼粘度多在35—60之间,因此,丁苯橡胶也可不用塑炼,但是经过塑炼后可以提高配合机的分散性顺丁橡胶具有冷流性,缺乏塑炼效果。
顺丁胶的门尼粘度较低,可不用塑炼.氯丁橡胶得塑性大,塑炼前可薄通3-5次,薄通温度在30-40℃。
橡胶配方常用的原材料名称对比

天然胶:RSSIX;RSS1#;RSS2#;RSS3#;RSS4#;RSS5#。
质量按顺序降低。
CSR﹕中國標準膠SMR 马来西亚标准胶SIR﹕印度尼西亞標準膠TTR﹕泰國標準膠ISNR﹕印度標準膠SSR﹕新加坡標準膠ENR-50 环氧化天然橡胶CV 恒粘橡胶LV:低粘橡胶,门尼值为45+-5度,可以不经过素炼直接混炼。
充油天然橡胶:低温防滑性好。
MG:易操作橡胶SP接枝橡胶SBR 1205:苯乙烯25%;丁二烯75%。
溶液型聚合。
可以部分取代SBR1006/1008/1009/密炼机密炼会增加10-15%体积。
耐磨耐曲折,耐低温,耐压缩变形。
SSBR303人造胶:溶液型苯乙烯丁二烯橡胶,苯乙烯48%;丁二烯52%。
主要用于透明料,与RB,IR共用10-20PHR。
S1430:1,3 丁二烯-苯乙烯聚合物。
可增加硬度,柔韧性和耐磨。
S2250/KA8802人造胶:丁二烯,苯乙烯,丙烯晴聚合体。
BIIR2244/X2:异丁烯,异戊二烯,丁基橡胶。
HP100:氯磺化聚乙烯CSM》96%。
四氯化碳《0.2%MILLATHANE-97:聚脂聚氨基甲酸乙酯橡胶。
聚醚类合成尿素橡胶IR-307人造胶:聚异戊二烯99.99%,可做透明底,奶嘴,接着剂,胶囊。
E-BR:乳液聚合顺式聚丁二烯橡胶,含高芳氢油35份。
UBE BR150L人造胶:100%聚丁烯。
BR9000:一般顺丁橡胶BR9175:充油顺丁橡胶37.5%BR9075:充油顺丁橡胶IM(PIB): 聚异丁烯XNBR﹕羧基丁晴橡胶HNBR﹕氫化丁晴橡胶PBR﹕丁比橡胶ACM﹕丙烯酸脂橡膠AEM:乙烯-丙烯酸橡胶CSM﹕氯磺化聚乙烯CPE﹕氯化聚乙烯CO﹕均聚氯醇橡膠ECO﹕共聚氯醇橡膠PUR(PU)﹕聚氨脂橡膠AU﹕聚脂型聚氨脂橡膠EU﹕聚迷型聚氨脂橡膠Q﹕硅橡膠MQ﹕二甲基硅橡膠MVQ﹕甲基乙烯基硅橡膠MPQ﹕甲基苯基硅橡膠MPVQ﹕甲基苯基乙烯基硅橡膠MFVQ﹕氟硅橡胶MNVQ﹕晴硅橡胶TPF﹕四丙氟橡胶PNF﹕氟化磷晴橡胶CNR﹕羧基亞硝基氟橡胶TPE﹕熱塑型彈性體TPNR﹕熱塑型天然橡膠SIS﹕熱塑型苯乙烯-异戊二烯嵌段共聚物TPO﹕熱塑型聚烯氰TPEE﹕熱塑型聚脂彈性體LPB﹕液体聚丁二烯LCR﹕液体氯丁橡膠PNBR﹕粉末丁晴橡膠EV A﹕乙烯乙酸乙烯脂SBS﹕熱塑型苯乙烯-丁二烯嵌段共聚物SEBS﹕苯乙烯-乙烯-丁烯-苯乙烯嵌段共聚物TPV﹕熱塑型硫化膠EEA﹕熱塑型乙烯-丙烯酸乙脂彈性體PVC-TPE﹕聚氯乙烯熱塑型彈性體LNBR﹕液体丁晴橡膠PSR﹕液体聚硫橡膠PCR﹕粉末氯丁橡膠1,2-PB:低分子量的1,2聚丁二烯橡胶碳母料CMB:碳35.5%/聚合物54.5%/加工油4.4%UL00328 塑胶粒:醋酸乙烯醋28%,聚乙烯72%ELV ALOYAC系列塑胶粒:乙烯丙烯酸正丁酯聚合物》99% LEVANELT800改质剂:乙烯与乙烯酯组成之聚合物。
橡胶技术网 - 通用橡胶配方集锦一NR SBR

3 2 ,2 ,42三甲基21 ,22二氢喹啉聚合物 3 3 N2异丙基2N′2甲基苯基对苯二胺 ;防老剂 4010NA
3. 说明 1) 天然橡胶必须预先进行塑炼 。 2) 不添加软化剂 、增塑剂的原因是因为配
方中加入了大量的再生胶 。 3) 硬度 60°的配方 B 中不加石蜡类防老剂
和防老剂 3C 是因为再生胶中本来就含有防老 剂 ,因此即使不添加 ,同样也具有耐老化性能 。
3. 说明 1) SBR 1502 是非污染性丁苯橡胶 。因此 ,
若添加污染性防老剂 3C 时本应采用 SBR 1500 , 但由于当时一并购进材料 , 所以还是采用了 SBR 1502 。
2) 不使用碳酸钙而使用陶土类填充剂 ,是 配方设计者选择哪种配合剂的问题 ,或者是因 为该橡胶厂实际购买的配合剂品种多 ,便于选 择。
用量 ,份
SBR (J SR1502) 高耐磨炉黑
陶土 环烷系操作油
防老剂 3C 石蜡 (石蜡类防老剂)
1 号氧化锌 硬脂酸
硫黄 (沉淀) 促进剂 DM 促进剂 TT 活性剂有机胺 (Acting B)
合计
100 30 35 25 2. 5 3 5 1 1. 5 1. 5 0. 15 0. 5 205. 15
© 1995-2006 Tsinghua Tongfang Optical Disc Co., Ltd. All rights reserved.
·22 ·
世 界 橡 胶 工 业
2005
定 。对此 ,该文作者的配方方法如下 : λ 硬度为 60°~65°的橡胶配方 ,选择炭黑 、
170. 3
3 高分子量脂肪酸酯与不溶性填充剂的混合物 3 3 22(吗啉二硫代)2苯并噻唑
橡胶技术网 - 硫化产品常见问题及解决方法

5
脱模开裂
1、过硫
2、脱模时模温过高,橡胶分子仍处于剧烈运动中,遇冷空气时局部先冷却,与后冷却的部分形成内应力,极易造成脱模裂伤
6、按规定清洗模具
2、胶料或模具被油脂或其他物质污染,在被污染的地方造成分层
3、脱模剂喷洒太多,使部分侵入胶料中,造成分层、开裂
4、混炼不均或喷霜
5、胶料塑性太差
1、适当增加薄通次数
2、如果油污发生在制品表面,该处就有开裂的可能,因此,胶料要妥善保管,模具在使用前要清理干净
3、处粘模部分外,其他地方可不涂或少涂
4、胶料在使用前要经过充分热炼,可以部分消除混炼不均和喷霜现象,热炼好的胶料最好立即使用,不能停放太久,否则,喷霜现象还可能发生
7、对合线处局部疏松,胶料之间结合强度小
8、缓压太迟
1、增加或检查压力波动的原因
2、使硫化压力降到合适的水平,防止过大或过小。如果降压后飞边增厚,可酌情减少加料量或加大流胶槽,有条件时,可使模具在压力下冷却,然后启模,这样因冷却收缩可以部分或全部抵消上述体积增大现象,减少或杜绝对合线开裂
3、这常常是造成制品抽边的主要原因,制品外部硫化后,由于胶料传热慢,内部还处于未硫化状态,如果这是降压启模,内部硫化反应中的挥发会迅速外溢,同时由于温度下降,胶料严重收缩,这两方面的因素使得对合处抽边,应当调整硫化条件,采用低温长时间硫化法或分阶段升温硫化法
1、压力不足或压力波动,使硫化过程中胶料内部压力大于硫化压力
2、硫化压力过大,胶料被严重压缩,起模时,压力急剧下降,硫化胶体积增大,制品其他部分因受模具限制无法膨胀,而模具对合线处则可自由膨胀,因膨胀不均造成的内应力就导致开裂
橡胶技术网 - HG4-329-66密封橡胶制品(环状)化工部标准

本标准适用于由耐油、耐热、耐酸碱等胶料制成的各种断面形状的全胶或夹织物的密封橡胶制品,用于各类机械设备中,于规定的温度、压力下和不同的工作介质中起密封作用。
一、技术条件1、密封橡胶制品的规格尺寸及公差应按照订货方规定程序批准的图纸制造。
图纸上应注明工作面和标志部位,以及选用胶料组号。
2、密封橡胶制品用胶料按其特性分为四组:Ⅰ组:耐油胶料;Ⅱ组:普通胶料;Ⅲ组:耐热胶料;Ⅳ组:耐酸碱胶料。
3、各组胶料的特性及工作条件应符合表1规定:表14、胶料物理机械性能应符合表2规定:表25、密封橡胶制品图纸上未注明尺寸公差的部位其公差按表3规定:mm 表36、密封橡胶制品的工作表面应平整,不允许有气泡、杂质、凹凸不平等缺陷。
在非工作表面上,全胶制品的外观质量指标应符合表4规定;夹织物制品外观质量指标应符合表5规定:表4表5二、检验规则7、产品应由制造厂的技术检查部门检查验收。
8、产品以同类型不多于5000件为一批。
9、产品应按第一章第6条规定逐件进行外观质量检查。
10、产品的主要尺寸及公差按表3规定进行抽验,抽验数量不少于2%(每种规格应不少于5件)。
抽验结果如不合格,应再取双倍试样进行复验,复验后仍有一项不合格,则应逐件进行检查。
11、每批产品所用胶料的物理机械性能,应按第三章的检验方法,对表2所规定的项目进行试验,如试验结果不合格,应再取双倍试样,对不合格项目进行复试,复试后仍有一项不合格,则该批胶料另行处理。
12、老化系数、耐油、耐酸碱试验可定期进行,但每月不少于一次,脆性温度试验每季不少于一次。
三、检验方法13、产品的主要尺寸,用精确度为0.05毫米的量具进行测量,内径超过500毫米的产品,可用分度为1毫米的量具进行测量。
14、产品的外观质量用目测方法和量具检查。
15、胶料的物理机械性能试验按以下方法进行:(1)胶料物理机械性能试验试样制备按GB527-65规定;(2)扯断力、扯断抻长率、扯断永久变形按GB528-65规定;(3)硬度(邵尔A型)按GB531-65规定;(4)老化系数按HGB4019-60(按抗张积)规定;(5)脆性温度按HGB4034-60规定;(6)耐油重量变化率按HGB4041-60规定;(7)耐酸碱系数按HGB4042-60(按抗张积)规定。
密封件标准大全
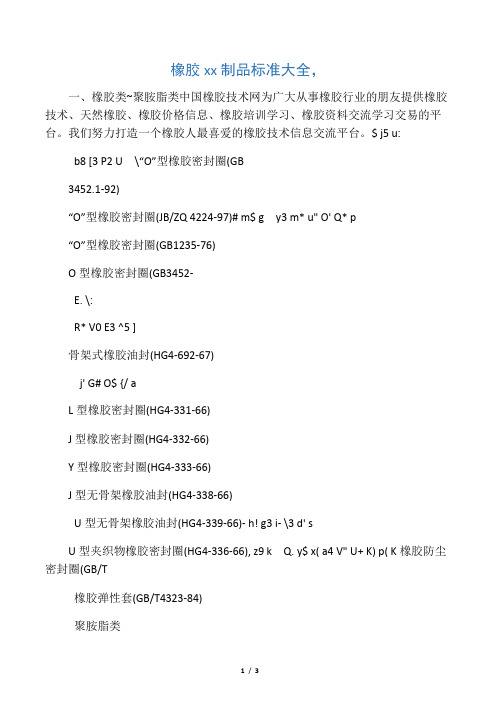
橡胶xx制品标准大全,一、橡胶类~聚胺脂类中国橡胶技术网为广大从事橡胶行业的朋友提供橡胶技术、天然橡胶、橡胶价格信息、橡胶培训学习、橡胶资料交流学习交易的平台。
我们努力打造一个橡胶人最喜爱的橡胶技术信息交流平台。
$ j5 u:b8 [3 P2 U \“O”型橡胶密封圈(GB3452.1-92)“O”型橡胶密封圈(JB/ZQ 4224-97)# m$ g y3 m* u" O' Q* p“O”型橡胶密封圈(GB1235-76)O型橡胶密封圈(GB3452-E. \:R* V0 E3 ^5 ]骨架式橡胶油封(HG4-692-67)j' G# O$ {/ aL型橡胶密封圈(HG4-331-66)J型橡胶密封圈(HG4-332-66)Y型橡胶密封圈(HG4-333-66)J型无骨架橡胶油封(HG4-338-66)U型无骨架橡胶油封(HG4-339-66)- h! g3 i- \3 d' sU型夹织物橡胶密封圈(HG4-336-66), z9 k Q. y$ x( a4 V" U+ K) p( K橡胶防尘密封圈(GB/T橡胶弹性套(GB/T4323-84)聚胺脂类z形油封JB/ZQ4075-973 x# f" n3 ?3 A7 y% B孔用YX型密封圈(JB/ZQ4264-86)橡胶技术网% M) ? A:q5 H5 }- _$ Y+ F! e防尘圈(JB/ZQ4507-86)单向xx橡胶xx圈(GB10708.1-89)橡胶技术网4 h P8 A1 d' L9 d) F3 [橡胶防尘密封圈(GB孔用Yx形密封圈(JB/ZQ 4264-97)气缸用密封圈(JB/T 6657-93)" O* q2 }0 {$ T" V1 \; X旋转轴唇形密封圈(GB/T9877.1-88)VD形橡胶密封圈JB/T 6994-93)U形内骨架橡胶密封圈(JB/T 6997-93)J形无骨架橡胶油封(HG4-338-66)% Z( o9 {" K! x2 m0 m8 a% I旋转轴唇形密封圈基本尺寸和公差(GBl3871-92)往复运动橡胶密封圈外观质量(GB/T15325-94)橡胶技术网#W7e.\7t9d+n9f7Y0 s+ ~旋转轴唇形密封圈外观质量(GB/T15326-94)# t, g3 T) M, D5 P& [(一)JB1713-75JB/T1716-1991填料垫(二)JB1716-75(一)JB1718-75JB/T1719-1991垫片(二)JB1719-75JB/T1720-1991垫片(三)JB1720-75JB/T1721-1991垫片JB/T1747-1991填料压环JB1747-75JB/T5209-1991塑料填料JB1714-75 JB1715-75! R" j/ m! t5 G) o。
橡胶与金属的粘合是橡胶制品制造过程中的重要环节

橡胶与金属的粘合是橡胶制品制造过程中的重要环节,如果粘合不良或无法粘合,一些橡胶制品如轮胎、钢丝输送带、橡胶软管,橡胶骨架油封、汽门油封,橡胶金属组合垫圈、组合胶套等橡胶金属复合制品就无法制作。
就橡胶密封制品而言,上世纪80年代初,青岛密封件厂协同青岛化工厂研制成功了RM-1粘合剂,替代日本TD870成功生产出与国外同等水平的骨架油封,使引进的国外技术得以消化吸收,开辟了骨架油封制作的新工艺。
上世纪90年代,由于汽车工业的发展,不少厂家要求用氟橡胶制作骨架油封、汽车油封,但是粘合问题不好解决,严重的制约了该产品的开发,当时青岛双星集团密封件厂成功的研制了FG-1氟橡胶与黑色金属的热硫化粘合剂,使氟橡胶与金属骨架牢牢的粘合成一体,顺理成章的研发成功斯太尔发动机曲轴前后油封和气门油封替代了进口,满足了配套需要,该粘合剂一直使用至今。
因此橡胶与金属粘合是极其重要的应用技术,应引起生产企业的高度重视。
1 金属骨架的表面处理) 骨架表面无油污、无锈蚀,有一定粗糙度的新鲜表面才能有效的与金属粘合,因此骨架必须进行表面处理,处理大体有两种方法:一是机械法处理。
如采用履带式的抛丸清理机326或滚筒式的抛丸清理机Q3110,将粒径0.5mm的钢砂喷射到骨架表面,将表面的锈蚀等有害物料喷掉,使表面新鲜并增大表面积,加大骨架与胶粘剂间的接触面;二是化学法。
即酸洗处理,磷化钝化处理,其工艺过程是碱液去油,酸液去锈,磷化上磷化膜,然后进行钝化烘干,碱液是有多种材料如苛性钠、硅酸钠(表面湿润剂)、焦磷酸钠(阴离子表面活性剂)、烷基磺酸钠组成的水溶液,清洗温度80-90℃,时间视表面的油污多少而有差异,一般是5min左右。
去油污的骨架经流动的自来水冲洗后,进行酸洗处理,而不同的金属去锈时对酸的品种是有选择性的。
例如,铁件要用盐酸清洗处理。
铜件和不锈钢骨架采用硫酸、硝酸混合液协同去锈。
铝件用硫酸、铬酸混合液进行处理。
要求对周围环境不产生或少产生腐蚀时,而金属骨架锈蚀较轻的骨架,可采用以草酸为主,掺用少量硫酸和加入缓钝剂的水溶液进行处理。
橡胶制品厂实习-橡胶配方设计
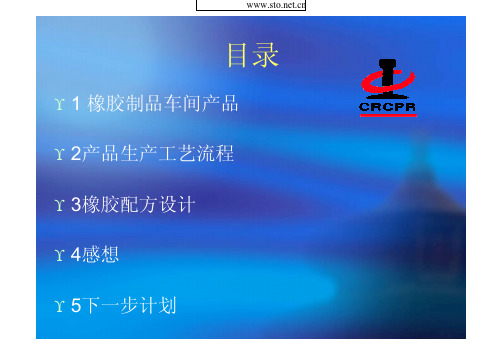
目录¡
¡
¡
¡
¡
1 橡胶制品车间产品¡
¡
¡
¡
¡
¡
¡
¡
¡
2 产品生产工艺流程
¡硫化
¡
3 橡胶配方设计
3.1 橡胶的塑炼天然胶
合成橡胶
3.2 橡胶的混炼¡
天然橡胶
氯丁橡胶
三元乙丙橡胶
3.3 橡胶的硫化体系¡硫磺硫化体系
¡
¡
¡
¡
非硫磺硫化体系¡
¡
¡
3.4补强填充体系炭黑
¡¡
¡¡
¡¡
矿质填料¡碳酸钙
陶土¡
¡碳酸镁
3.5 橡胶老化防护体系
¡
类型产生原因类型产生原因
热老化热+氧气天候老化+臭氧+光+形变
氧气
等氧化老化氧气+热疲劳老化动态变形+氧气+臭氧
+热金属粒子催化老化变价金属离子+氧气介质老化溶剂,化学介质
臭氧老化臭氧辐照老化高能射线
光老化光+氧气
¡¡¡
4 感想¡
对橡胶制品制品的一些思考¡
¡。
橡胶技术网 - 国内外橡胶助剂工业的发展

提高硫黄硫化胶料在无氧条件下的老化性 能 ,即通常所说的抗硫化返原性能 ,一直是提高 轮胎等橡胶制品同步硫化质量和产品使用寿命 的关键问题 [ 11 ] 。特别是为了提高生产效率而采 取的高温硫化工艺已得到越来越广泛的应用 ,在 厚制品 (如轮胎 )高温硫化中提高胶料的抗硫化 返原性能就显得更为重要 。北京橡胶工业研究 设计院开发出了新型高效抗硫化返原剂 Z - 600 系列产品 。该系列产品除具有突出的抗硫化返 原性能外 ,还可提高 NR硫化胶的物理性能 ,降低 胶料的动态生热 [ 12 ] 。山西省化工研究所生产了 多功能抗硫化返原剂 DL - 268 J和后硫化稳定剂 HS - 258。DL - 268 的动态性能良好 ,具有抗硫 化返原性 ,可提高硫化胶的定伸应力 、耐热性能 及帘线 - 橡胶粘合强度 ,用于轮胎缓冲层和胎肩 胶 ,可有效防止“肩空 ”现象 ; HS - 258 是六亚甲 基 - 1, 6 - 二硫代硫酸钠二水合化合物 ,可改善 通用橡胶胶料的抗硫化返原性和动态性能 。
促进剂 D、M、DM、TMTD
防老 剂 甲 、RD、丁 、BLE、 FK - 40
防老剂 4010NA、4020
胶料焦烧的原因与解决办法
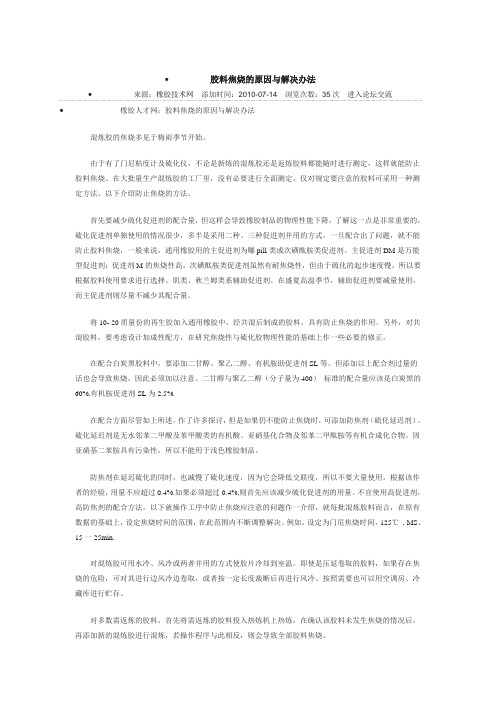
∙胶料焦烧的原因与解决办法∙来源:橡胶技术网添加时间:2010-07-14浏览次数:35次进入论坛交流∙橡胶人才网:胶料焦烧的原因与解决办法混炼胶的焦烧多见于梅雨季节开始。
由于有了门尼粘度计及硫化仪,不论是新炼的混炼胶还是返炼胶料都能随时进行测定,这样就能防止胶料焦烧。
在大批量生产混炼胶的工厂里,没有必要进行全面测定,仅对规定要注意的胶料可采用一种测定方法。
以下介绍防止焦烧的方法。
首先要减少硫化促进剂的配合量,但这样会导致橡胶制品的物理性能下降,了解这一点是非常重要的,硫化促进剂单独使用的情况很少,多半是采用二种、三种促进剂并用的方式。
一旦配合出了问题,就不能防止胶料焦烧,一般来说,通用橡胶用的主促进剂为曝pill类或次磺酞胺类促进剂。
主促进剂DM是万能型促进剂;促进剂M的焦烧性高,次磺酞胺类促进剂虽然有耐焦烧性,但由于硫化的起步速度慢,所以要根据胶料使用要求进行选择。
肌类、秋兰姆类系辅助促进剂。
在盛夏高温季节,辅助促进剂要减量使用,而主促进剂则尽量不减少其配合量。
将10- 20质量份的再生胶加入通用橡胶中,经共混后制成的胶料,具有防止焦烧的作用。
另外,对共混胶料,要考虑设计加成性配方,在研究焦烧性与硫化胶物理性能的基础上作一些必要的修正。
在配合白炭黑胶料中,要添加二甘醇、聚乙二醇、有机胺助促进剂SL等。
但添加以上配合剂过量的话也会导致焦烧,因此必须加以注意。
二甘醇与聚乙二醇(分子量为400)标准的配合量应该是白炭黑的60%,有机胺促进剂SL为2.5%.在配合方面尽管如上所述,作了许多探讨,但是如果仍不能防止焦烧时,可添加防焦剂(硫化延迟剂)。
硫化延迟剂是无水邻苯二甲酸及苯甲酸类的有机酸、亚硝基化合物及邻苯二甲酞胺等有机合成化合物。
因亚硝基二苯胺具有污染性,所以不能用于浅色橡胶制品。
防焦剂在延迟硫化的同时,也减慢了硫化速度,因为它会降低交联度,所以不要大量使用。
根据该作者的经验,用量不应超过0.4%.如果必须超过0.4%,则首先应该减少硫化促进剂的用量。
橡胶技术网_-_混炼胶常见问题总结

混煉膠常見問題總結、橡胶加工問題以及解决方法1 硫黄分散不均,有麻点(凝集物)现象这是一个既老又新的问题,我们的前辈理应解决了的问题现在又旧事重提。
将入库的硫黄放置在水泥板上,从防潮的角度看不是好办法,一定要将它放在席子或垫板上,在计量前将其过筛是预防产生结块的有效方法,这时不必用太细的筛子,用40目或20目的即可,只要能将粉末状硫黄中的结块打碎就可以了。
另外,在一次硫黄添加量较少的情况下,在开炼机上面边过筛边添加为好,在这种场合,即使筛目粗一些也是可以的。
混炼胶中的常见问题及其原因分析、解决办法混炼胶的主要质量问题及其原因A.分散不良的原因(a)混炼过程中的原因[1]混炼时间不够;[2]排胶温度太低或太高;[3]同时增加酸性配合剂和碱性配合剂(如将硬脂酸和防焦剂ESEN与氧化锌和氧化镁一起加入);[4]塑炼不充分;[5]配合剂增加的顺序不恰当;[6]混炼周期中填充剂加得太迟;[7]同时加入小粒径炭黑和树脂或粘性油;[8]金属氧化物分散时间不够;[9]在们料己经开始撕裂或碎裂后加入液态增塑剂;[10]胶料批量太大或太小。
(b)工艺操作上的原因[1]没有遵循所制订的混炼程序;[2]油性材料和干性材料的聚集体粘在上顶栓和进料斗边上;[3]转子速度不恰当[4]胶料从压片机上卸下时太快;[5]没有正确使用压片机上的翻胶装置。
(c)设备上的原因[1]密炼机温度控制失效;[2]上顶栓压力不够;[3]混炼室中焊层部位磨损过度;[4]压片机辊温控制失效;[5]压片机上的高架翻胶装置失灵;(d)原材料方面的原因[1]橡胶过期存放和有部分凝胶;[2]三元乙丙橡胶或丁基橡胶太冷;[3]冷冻天然橡胶;[4]天然橡胶预塑炼不充分;[5]填充剂中水分过量(结块);[6]在低于倾倒点温度下加入粘性配合剂;[7]配合剂使用不当;(e)配方设计方面的原因[1]使用的弹性体门尼粘度差异太大;[2]增塑剂与橡胶选配不适当;[3]硬粒配合剂太多;[4]小粒径填料过量;[5]使用熔点过高的树脂;[6]液态增塑剂不够;[7]填充剂和增塑剂过量;b焦烧的原因(a)配合方面的原因[1]硫化剂、促进剂用量太多;[2]硫化体系作用太快;[3]配合剂称量不正确;[4]小粒径填料过量;[5]液态增塑剂不够。
橡胶技术网 - 三井化学三元乙丙
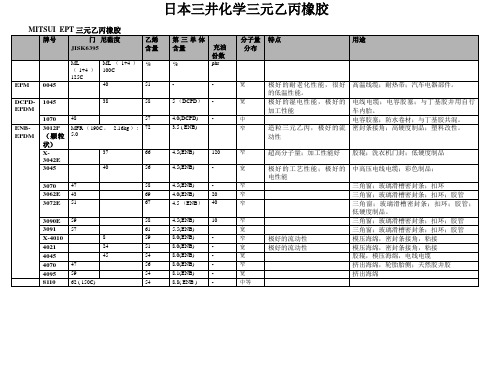
8120E
ML(1+4)150C: 65
56
10.5
20
中
极好的压变,极好的形状保持性
挤出海绵条
14030
27
51
8.0
-
窄
极好的低温曲挠性
三角窗,刹车皮碗
Eptalloy
ENB-EPDM
PX-047
(PE20phr)
40
53
8.0
-
宽
极好的流动性
高发泡海绵模压
PX-049PE
8110
62 (150C)
54
8.8( ENB )
-
中等
日本三井化学三元乙丙橡胶
MITSUI EPT三元乙丙橡胶
牌号
门尼黏度
JISK6395
乙烯
含量
第三单体含量
充油份数
分子量分布
特点
用途
ENB-EPDM
ML(1+4)125C
ML(1+4)100C
%
%
phr
8075E
52
54
8.5
20
中
好的压变,好的形状保持性。
(PE20phr)
ML(1+4)150C: 36
62
4.3
10
窄
极好的挤出性能
高填充,高硬度玻璃导槽,
PX-051
(PP20phr)
71
58
10.0
20
中
好的形状保持记忆性能
高发泡海绵门条,
PX-053
(PP20phr)
55
53
8.0
-
宽
形状保持记忆
橡胶技术网---TPE完全手册

TPE 介绍热塑性弹性体(Thermoplastic Elastomer-TPE)亦称热塑性橡胶(Thermoplastic Rubber-TPR)是一种兼具有橡胶和热塑性塑料特性,在常温下显示橡胶的高弹性,高温下又能塑化成型的高分子材料,热塑性弹性体具有多种可能的结构,最根本的一条是需要有至少两个互相分散的聚合物相,在正常使用温度下,一相为流体(使温度高于它的Tg─玻璃化温度),另一相为固体(使温度低于它的Tg或等于Tg),并且两相之间存在相互作用。
即在常温下显示橡胶弹性,高温下又能塑化成型的高分子材料,具有类似于橡胶的力学性能及使用性能、又能按热塑性塑料进行加工和回收,它在塑料和橡胶之间架起了一座桥梁。
因此,热塑性弹性体可象塑料那样容易加工。
就加工而言,它是一种塑料;就性质而言,它又是一种橡胶。
热可塑性弹性体有许多优于热固性橡胶的特点。
目前国内对热塑性苯乙烯--丁二烯嵌段共聚物则称之为SBS(styrene-butadiene-styren block copolymer),热塑性异戊二烯-苯乙烯嵌段共聚物称为SIS(styrene-isoprene block copolymer),饱和型SBS则称之为SEBS,即Styrene-ethylene-butylene-styrene block copolymer的缩写,就是苯乙烯-乙烯-丁烯-苯乙烯嵌段共聚物。
其它各类热塑性弹性体均以生产厂家的商品名称称之。
我国也采用SBS的代号,表示热塑性苯乙烯-丁二烯-苯乙烯嵌段共聚物,习惯称为热塑性丁苯橡胶。
TPE 简介热塑性弹性体(TPE)可概括为通用TPE和工程TPE两个类型,目前已发展出10大种类30多个品种。
目前,TPE以苯乙烯类(TPS)和乙烯类为中心,在世界各地已获得迅速发展。
双烯类TPE和氯乙烯类TPE也成为通用TPE的重要品种。
氨酯类TPU、酯类TPEE、胺类TPAE、有机氟类TPF等则转向以工程应用为主。
橡胶技术网 - 不同性质N550炭黑对胶料性能的影响
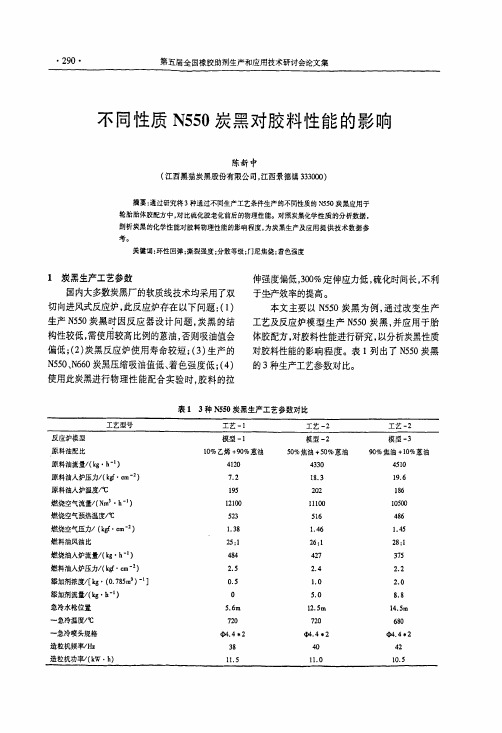
构性较低,需使用较高比例的蒽油,否则吸油值会 偏低;(2)炭黑反应炉使用寿命较短;(3)生产的
N550、N660炭黑压缩吸油值低、着色强度低;(4)
的3种生产工艺参数对比。
使用此炭黑进行物理性能配合实验时,胶料的拉
表1 3种N550炭黑生产工艺参数对比
陈新中・不同性质N550炭黑对胶料性能的影响
l炭黑生产工艺参数
伸强度偏低,300%定伸应力低,硫化时间长,不利 于生产效率的提高。
本文主要以N550炭黑为例,通过改变生产
国内大多数炭黑厂的软质线技术均采用了双
切向进风式反应炉,此反应炉存在以下问题:(1) 生产N550炭黑时因反应器设计问题,炭黑的结
工艺及反应炉模型生产N550炭黑,并应用于胎 体胶配方,对胶料性能进行研究,以分析炭黑性质
分析项目 工艺型号 反应炉模型 12/(g・kg“) DBP/(10’5m3・kg一1)
CI)BP/(10一5nl’・kg‘1)80一90 CT)dl/(103 m2・kg一1) NSA/(103m2・kg‘1) STSA/(103m2-l【g一1)
Tint/% PH 34—46 35—45 34—44
‘291・
造粒水流量/(1‘g・h一1) 干燥炉尾气流量/(Nm3・h。1) 干燥(kg・h.1)
3400 7500 3200 170—230 2630 63.141 1.75
3100 7200 2800 170一230 2832 67.957 1.68
2800 6800 3500 170一230 2979 71.488 1.64
炭黑产量/(d“。)
总油单耗/(吨炭黑/吨油)
由表1可以看出,采用工艺一1及反应炉模 型一1生产N550炭黑对原料油要求较高,需使用 90%蒽油+10%乙烯,添加剂用量为零,产量偏
橡胶技术网 - 美国罗门哈斯:橡胶与金属热硫化粘合剂
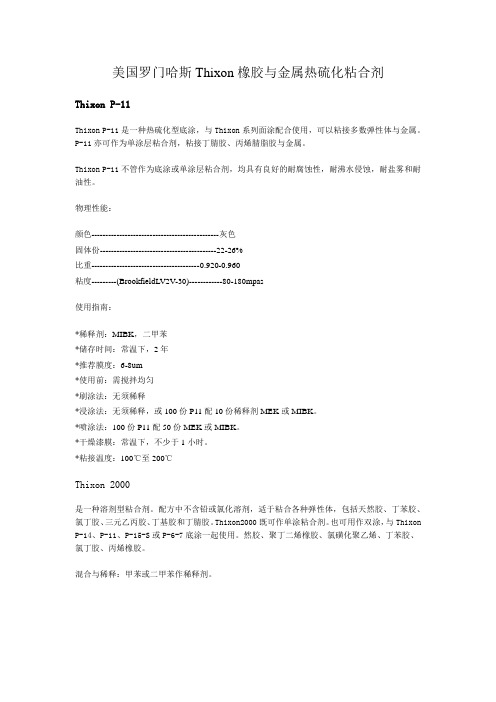
美国罗门哈斯Thixon橡胶与金属热硫化粘合剂Thixon P-11Thixon P-11是一种热硫化型底涂,与Thixon系列面涂配合使用,可以粘接多数弹性体与金属。
P-11亦可作为单涂层粘合剂,粘接丁腈胶、丙烯腈脂胶与金属。
Thixon P-11不管作为底涂或单涂层粘合剂,均具有良好的耐腐蚀性,耐沸水侵蚀,耐盐雾和耐油性。
物理性能:颜色----------------------------------------------灰色固体份------------------------------------------22-26%比重---------------------------------------0.920-0.960粘度---------(BrookfieldLV2V-30)------------80-180mpas使用指南:*稀释剂:MIBK,二甲苯*储存时间:常温下,2年*推荐膜度:6-8um*使用前:需搅拌均匀*刷涂法:无须稀释*浸涂法:无须稀释,或100份P11配10份稀释剂MEK或MIBK。
*喷涂法:100份P11配50份MEK或MIBK。
*干燥漆膜:常温下,不少于1小时。
*粘接温度:100℃至200℃Thixon 2000是一种溶剂型粘合剂。
配方中不含铅或氯化溶剂,适于粘合各种弹性体,包括天然胶、丁苯胶、氯丁胶、三元乙丙胶、丁基胶和丁腈胶。
Thixon2000既可作单涂粘合剂。
也可用作双涂,与Thixon P-14、P-11、P-15-S或P-6-7底涂一起使用。
然胶、聚丁二烯橡胶、氯磺化聚乙烯、丁苯胶、氯丁胶、丙烯橡胶。
混合与稀释:甲苯或二甲苯作稀释剂。
物理性能:颜色-----------------------------------------------黑色粘度-------------(Brookfield 4#转子,100RPM)----1150CPS固体份----------------------------------------------26%比重-----------------------------------------------0.99贮存时间--------------------------------------------1年闪点------------------------------------------------4℃硫化温度------------------------------------100℃至190℃应用方式:推荐漆膜厚度18-25cm.*刷涂:对于刷涂,Thixon 2000无需稀释。
橡胶吐霜防止

现我公司生产的一款EPDM胶产品在放置几天后会出现吐霜,经过是技术员分析为是使用了促进剂BZ的原因,原来使用的是EG-4,但是技术员反映EG-4也会导致EPDM胶产品吐霜,请问是这样吗?BG会导致制品吐霜吗?配方:(因为我看不到质量份的,所以只能贴我们实际生产时1份胶的了,呵呵)EPDM9650=11034.45g;轻质碳酸钙=3309.25g;白艳华CC=3862.6g,宝马碳黑N550=4415.95g;硬脂酸1801=110.34g;OT-10不溶硫磺=165.51g;太阳活性氧化锌=551.72g;BZ=275.86g;KP6030石蜡油=1106.7g硫化条件:硫化温度:175-185度硫化时间:120秒锁模压力:180-200 操作时间:250秒排气次数:3次另外:现在将BZ换回了EG-4还是出现发白。
EPDM是非极性胶,且很多助剂包括促进剂在里面溶剂度都很小,所以喷霜趋势很明显。
1.用量过多;2.分散不良,局部浓度偏高;橡胶技术咨询网为广大从事橡胶行业的朋友提供橡胶技术、橡胶价格信息、橡胶培训学习、橡胶资料交流学习交易的平台。
我们努力打造一个橡胶人最喜爱的橡胶技术信息交流平台。
3.硫化不够,残余未反应的含量高,且由于制品未硫化完全分子量低,残余助剂在里面迁移性大;混炼不均造成的橡胶技术网/bbs/thread-20291-1-1.htmlEPDM是比较饱和的橡胶,喷霜是很常见的,那你可以买复合促进剂EPDM防吐霜综合促进剂-乙丙橡胶EPDMEG-3 EPDM(不喷霜) /company/show/pdetail--1532430--12722 249.htmlEPDM用复合促进剂EG-3用法及用量EG-3 组份:含NA-22用法:EG-3 3~5 S 1~2成份:高效率促进剂之混合物。
外观:淡黄色粉末。
比重:1.4 (20℃)。
污染性:无。
储存性:原封室温至少一年。
包装:20 公斤箱装。
- 1、下载文档前请自行甄别文档内容的完整性,平台不提供额外的编辑、内容补充、找答案等附加服务。
- 2、"仅部分预览"的文档,不可在线预览部分如存在完整性等问题,可反馈申请退款(可完整预览的文档不适用该条件!)。
- 3、如文档侵犯您的权益,请联系客服反馈,我们会尽快为您处理(人工客服工作时间:9:00-18:30)。
胶配方的设计与运用1. 设计配方应在多个方面综合考滤,1.确保指定的物性。
所谓物性大体是在如下几个方面拉伸强度、撕裂强度、定伸应力、硬度、磨耗、疲劳与疲劳破坏、回弹力、扯断伸长率等。
2.胶料加工过程中,性能优良,确保产品高产、省料。
3.成本低价格便宜。
4.所用的原材料很易采购到。
5.生产力高,加工方便,制造过程中能耗少。
6.符合环保及卫生安全要求。
一,.对各种橡胶物性要有充分地了解。
天然胶物性;A. 天然橡胶加热后慢慢软化,到130—140度则完全软化至熔融状态,温度降低至零度时渐变硬,到-70度变成脆性物质。
天然胶的回弹率在0-100度内可达50-85%升至130度时仍保持正常的使用性能。
伸长率最高可达1000%。
天然橡胶是一种结晶性橡胶,自补强性大,具有非常好的机械性能。
纯胶的拉伸强度达17—25MPA,补强硫化胶达25—35MPA,曲绕达到20万次以上,这是因为天然胶,滞后损失小,生热低的结果。
天橡胶具有较好的汽密性。
天然橡胶的老化性能差,不加老防剂的橡胶,在强烈的阳光下曝晒4—7天后即出现龟裂现象。
与一定浓度的臭氧在几秒钟内即发生裂口。
天然胶耐碱性好,但不耐强酸。
耐极性溶剂,故不耐非极性熔剂,耐油性差。
天然胶的配合,普通硫化体系硫黄用量2.0-2.4 促进剂用量1.2-0.5。
半有效硫化体系硫黄1.0-1.7促进剂2.5-1.2,有效硫化体系硫黄0.4-0.8,促进剂5.0-2.0。
普通硫黄体系多硫交联健多,而单硫健少。
多硫健能低,稳定性差,耐热、耐老化性差。
但综合物理机械性能好。
普通硫黄硫化体系,硫黄加多时易喷硫,可用不溶性硫黄替代,不容性硫黄可改善硫化胶料半成品的物理机械性能,解决高温下出现的橡胶返原因题。
可以改善拉伸、定伸应力、及弹性,胎面胶使用还可以改善磨耗。
但有一个缺点,硫速快易焦烧。
有效硫化体系不发生硫化返原现象,一般用于制造要求低蠕变率、高弹性、生热低的优良制品。
硫黄加量一般为0.6—0.7份,氧化锌为3.5-5份,载硫体一般采用TMTD及N,N-二硫化二二吗啡啉硫黄给于体。
有效硫化体系的老化性能也大大地得到了改善。
半有效硫化体系,有着硫黄硫化体系的机械物理性能,有效硫化体系的低蠕变、弹性、生热低等物性。
硫化返原现象在两者之间。
可使用秋兰姆类,但有易喷霜、焦烧等缺点。
常用硫黄给予体DTDM二硫代二吗啡啉,在硫化中DTDM可完全替代硫黄时,形成有效硫化体系。
它的优点是焦烧时间长、不喷霜不污染,硫化胶的物理机械性能良好。
在全天然胶配方中,胶料的耐磨性、动态性能、耐老化性、抗返原性。
和曲绕性能都明显提高。
DTDM在天然胶中的用量是0.5份相当于1份硫黄。
在70/30天然/顺丁中相当于0.6-0.8份硫黄。
50/50时相当于0.5份硫黄。
DTDM的用量不宜超过1份。
天然橡胶可以用有机过氧化物硫化。
最常用的是过氧化二异丙苯,DCP具有良好的热稳定性,耐高温老化性、蠕变小、压缩永久变形小、动态性能好,抗返原性好。
缺点是硫速慢、易焦烧、撕裂强度低与抗臭氧剂不相容硫化模具易积垢。
天然胶的最佳硫化温度是143度,高于150度出现反原现象。
B. 丁苯橡胶分乳聚丁苯、溶聚丁苯、羧基丁苯。
苯乙烯与丁二烯的含量决定了聚合物的性能。
含量在23.5%的共聚物综合性能最佳平衡,含量50—80%共聚物称高苯乙烯丁苯胶。
乳聚丁苯主要有以下物点,1.硫化曲线平坦,胶料不易焦烧、2.耐磨性、耐热性、耐油性和耐老化性比天然胶好、高温耐磨性好。
3.加工分子量降到一定程度后不再降低,因而不易过练。
硫化硬度变化小。
4.提高分子量可达到高填充,充油丁苯加工性好。
5很容易与其它不饱和通用橡胶并用。
与天然、丁苯并用可以克服丁苯的缺点。
硫黄是丁苯胶的主要硫化剂,用量比天然胶少一般是1.0—2.5份,硫化速度比丁苯胶慢,可以增加促进剂或提高温度来加快硫速。
硫黄的用量直接影响硫化胶的物理机械性能。
随着硫黄用量的增加,硫化时间缩短,交联密度增高。
硬度、定伸应力、拉伸强度回弹率者都会增大,但伸长率、永久变形、热老化、屈绕性下降。
丁苯胶的最佳硫化温度是150度它不象天然胶不会出现反原现象。
在150度下硫化可获得优质的产品。
160-175度硫化可获得佷好的弹性各和抗变形性能。
溶聚丁苯具有浅色、较好的压出物尺寸稳定性、较快的硫化速度、较好的硫化平坦性,以用耐曲绕、耐低温和较高的回弹率。
但拉伸强度稍低。
高苯乙烯丁苯橡胶对橡胶具有一定的补强作用。
可与天然、丁苯、顺丁、异戊丁睛及氯丁橡胶等二烯烃类橡胶共混。
可用硫黄进行共硫化。
具有以下优点1.提高橡胶硬度2.耐老化性能3.聚磨性好4.电绝缘性能好5.易着色6.易混练加工7.具有热塑性,流动性强适于制造复杂的橡胶制品。
8.高温下具有撕裂性好,易脱模,表面光滑。
缺点低温性差、永久变形大、对温度依赖性大。
丁苯胶随着苯乙烯含量的增加,硫化胶的定伸应力、拉伸强度撕裂强度、耐磨性有所提高,而永久变形和抗曲绕龟裂性能降低。
C. 顺丁橡胶,分为溶聚丁二烯橡胶、乳聚丁二烯橡胶、丁纳橡胶。
最常用的还是溶聚丁二烯橡胶,可分为高顺式、低顺式、反顺式-1.4聚丁二烯橡胶。
顺丁橡胶的主要物性是1.高弹性是当前所有橡胶中弹性最高的一种橡胶。
并在很宽的范围内显示出高弹性,在-40度时还能保持一点的弹性。
与天然、丁苯并用时可改善它们的低温性能。
2.分子会迅速回复原状。
因此滞后损失小,生热小。
3.低温性能好,主要表在玻璃化温度低为—105度左右,而天然胶为-73 丁苯为-60所以掺用顺丁胶的胎面在高寒地区仍可保持使用性能。
4.耐磨性能优异仅次于丁睛胶。
5.耐曲绕性能优异,动态裂口性能良好,6.填充性好,与丁苯。
天然胶相比顺丁胶可填充更多的操作油及补强填料。
有较强的碳黑润湿能力。
可使碳黑较好地分散有利于降低成本。
7.与天然、丁苯、氯丁都能互溶。
与丁睛并用不超过25%仍有较高的耐油性能。
8.胶料的门尼度低对胶料的口型膨胀及压出速度无影响。
9.模内的流动性好。
10.吸水性低,可用于电线等耐水制品。
但顺丁胶也有众多缺点1.拉伸、撕裂强度低。
2.抗湿滑性差。
3.用于胎面时中后期出现花纹崩掉现象、4.粘着性能差5.加工性能差温度高时易脱辊。
6.较易冷硫。
7.在无补强剂的情况下拉伸强度很低基本无实用价实。
D.异戊橡胶(IR)称人造天然胶,它具有天然胶相似的的化学组成,整体结构和物理机械性能。
但和天然胶存在着一定的差异。
与天然胶相比有以下优点1.质量匀一,纯度高2.塑练时间短,混练加工简便。
3.颜色浅4.膨胀收缩小,这与异戊橡胶的分子量及凝胶的含量有一定的关系。
5.胶料流动性好,在注压或传递模压成型过徎中异戊橡胶的流动性匀好于天然橡胶。
但也有缺点1.纯胶胶料的拉伸强度低。
这主要是异戊橡胶的分子量小,生胶的强度低有关。
2.与等量碳黑的天然胶相比,拉伸强度、定伸应力、撕裂强度都较低,硬度也低于天然胶。
异戊橡胶的硫黄用量通常比天然胶少10-15%一般不超过2.5份。
用量过多,拉伸强度迅速下降。
天然胶含有脂肪酸、蛋白质等物质,硫化中起活化作用,所以促进剂用量相应要增加10-20%这样可以获得优良性能的硫化胶。
促进剂选用一般用次磺酰胺类为主促进剂,秋兰姆类为副促进剂。
与天然胶相比,混练胶拉伸强度低、弹性小,自粘性大、粘着性差,挺性小,流动性也差。
为了改进异戊橡胶的加工性能、提高其硫化胶的物理机械性能。
对其进行一定的改性,一.是混练阶段添加改性剂,二.是在聚合阶段引入改性官能团。
E. 乙丙橡胶,分为二元一丙、三元一丙、改性乙丙、热塑性乙丙橡胶乙丙橡胶是一种无定形非结晶橡胶其分子主链上乙烯与丙烯单体单元呈无规排列,失去了聚乙烯或聚乙烯的规整性。
是具有一定弹性的橡胶。
.乙丙橡胶具有优良的耐老化性能,1.它的耐臭氧不但大大优于通用橡胶,而且也优于一般认为耐老化性能很好的丁基橡胶。
其中DCPD—EPDM的耐臭氧性能最好。
2.耐候性能好,可在阳光下晒三年不发生龟裂其中EPM的耐候性最佳。
3.耐热性能好,可在120度环境中长期使用。
最高使用温度可达150度。
二.具有耐化学药品性。
如醇、酸、强碱、氧化剂、洗涤剂、动植物油、酮和酯类等均有较大的耐候性。
但对脂肪族、芳香族溶济,如汽油甲苯等稳定性较差。
三,电绝缘性好,电性能接近于丁基、氯磺化聚乙烯、聚乙烯。
特别适用于电气绝缘制品、制水中作业的电线。
四。
冲击弹性和低温性能。
弹性仅次于天然、顺丁胶。
最低极限低温使用温度达-50度。
五,具有低密度及高填充性能。
它的比重在0.87左右。
可以加入大量的填充油和填充剂。
最多高达200份,降低了成本。
六,乙丙橡胶具有较好的耐蒸汽性能,甚至优于其耐热性能。
用过氧化物硫化的乙丙橡胶耐过热水性能优于硫黄硫化的硫化胶。
但是乙丙橡胶也有众多的缺点,1.硫化速度最慢,不能和二烯烃类橡胶共硫化。
因而限制了它的用途。
2.自粘性互粘性很差,因而对加工工艺带来了很大的困难。
处理不当会造成脱层及海绵状。
3.耐然性、汽密性差。
4.耐油性及耐多数烃类溶剂性差。
在乙丙橡胶中,三元乙丙橡胶的用量最为广泛。
因为三元乙丙橡胶有第三单体,第三单体含量越高越易与二烯烃类橡胶共硫化。
1,在硫黄硫化体系中,由于硫黄在乙丙橡胶中的溶解度极低最易喷霜,一般用量控制在1—2份随着硫黄的增加硫化焦烧缩短,硫化速度加快。
拉伸、定伸、硬度增高,扯断伸长率下降。
耐热性能下降。
为了防止喷霜促进应选用三种、及三种以上并用。
各促进剂用量严格控制在溶解度以下。
增加氧化锌、硬脂酸的用量来提高活化程度,增加交联密度及抗反原性.。
2,用硫黄给予体、半有效硫化体系,可以改善耐热性及高温下的压缩变形。
延长焦烧但还是易喷霜,应选用多种促进剂并用,减少秋兰姆类的用量,如典形的配合M1.5 TMTD 0.8 TeDDC0.8 DTDM0.8硫黄。
这就是常说的防止EPDM喷霜的三八促进剂搭配。
但是没有绝对的,这是一个优良的典例。
F.氯丁橡胶,是一种通用特种橡胶,除了有一般的橡胶良好的物性外还具有耐候、耐然、耐油、耐化学腐蚀性,在各种橡胶中占有特殊的地位。
有如下特性,1.氯丁橡胶的强伸性能与天然橡胶相似。
其生胶有很高的拉伸强度及扯断长率,是自补强性橡胶。
纯胶配合的硫化胶可达27.5MPA,扯断伸长率可达800%以上。
2.优良的耐老化性能。
即,耐候、耐臭氧、及耐热性能。
其性能在通用橡胶中仅次于三元乙丙橡胶和丁基橡胶。
优于天然、丁苯、顺丁、丁睛。
能在90—110度下使用4—5个月。
3.优异的耐然性是通用橡胶中最好的橡胶。
在高温下分解出氯化氢汽体。
4.且具有一定的耐化学腐蚀性。
及耐油、耐溶剂性。
在通用橡胶中仅次于丁睛胶。
5.电性能,它的绝缘性能一般、只适用于600伏以下使用。
由于它具有耐候、老化、难燃的特点常被用于低压电缆。