橡胶技术网 - 硫化合模力
橡胶技术网 - 硫化产品常见问题及解决方法

5
脱模开裂
1、过硫
2、脱模时模温过高,橡胶分子仍处于剧烈运动中,遇冷空气时局部先冷却,与后冷却的部分形成内应力,极易造成脱模裂伤
6、按规定清洗模具
2、胶料或模具被油脂或其他物质污染,在被污染的地方造成分层
3、脱模剂喷洒太多,使部分侵入胶料中,造成分层、开裂
4、混炼不均或喷霜
5、胶料塑性太差
1、适当增加薄通次数
2、如果油污发生在制品表面,该处就有开裂的可能,因此,胶料要妥善保管,模具在使用前要清理干净
3、处粘模部分外,其他地方可不涂或少涂
4、胶料在使用前要经过充分热炼,可以部分消除混炼不均和喷霜现象,热炼好的胶料最好立即使用,不能停放太久,否则,喷霜现象还可能发生
7、对合线处局部疏松,胶料之间结合强度小
8、缓压太迟
1、增加或检查压力波动的原因
2、使硫化压力降到合适的水平,防止过大或过小。如果降压后飞边增厚,可酌情减少加料量或加大流胶槽,有条件时,可使模具在压力下冷却,然后启模,这样因冷却收缩可以部分或全部抵消上述体积增大现象,减少或杜绝对合线开裂
3、这常常是造成制品抽边的主要原因,制品外部硫化后,由于胶料传热慢,内部还处于未硫化状态,如果这是降压启模,内部硫化反应中的挥发会迅速外溢,同时由于温度下降,胶料严重收缩,这两方面的因素使得对合处抽边,应当调整硫化条件,采用低温长时间硫化法或分阶段升温硫化法
1、压力不足或压力波动,使硫化过程中胶料内部压力大于硫化压力
2、硫化压力过大,胶料被严重压缩,起模时,压力急剧下降,硫化胶体积增大,制品其他部分因受模具限制无法膨胀,而模具对合线处则可自由膨胀,因膨胀不均造成的内应力就导致开裂
橡胶硫化三要素(时间、温度、压力)

橡胶硫化三要素(时间、温度、压力)橡胶件硫化的三大工艺参数是:温度、时间和压力。
其中硫化温度是对制品性能影响最大的参数,硫化温度对橡胶制品的影响的研究也比比皆是。
但对硫化压力比较少进行试验。
橡胶硫化三要素之时间橡胶制品硫化时间:在一定的温度、模压下,为了使胶料从塑性变成弹性,且达到交联密度最大化,物理机械性能最佳化所用的时间叫橡胶制品硫化时间。
通常不含操作过程的辅助时间。
硫化时间是和硫化温度密切相关的,在硫化过程中,硫化胶的各项物理、力学性能达到或接近最佳点时,此种硫化程度称为正硫化或最宜硫化。
在一定温度下达到正硫化所需的硫化时间称为正硫化时间,一定的硫化温度对应有一定的正硫化时间。
当胶料配方和硫化温度一定时,硫化时间决定硫化程度,不同大小和壁厚的橡胶制品通过控制硫化时间来控制硫化程度,通常制品的尺寸越大或越厚,所需硫化的时间越长。
硫化时间的设定方法:1. 1.正硫化时间的测试,胶料正硫化时间的测试方法有:1.1物理-化学法(包括游离硫测定法和溶胀法);1.2 物理-力学性能测定法(包括定伸应力法、拉伸强度法、定伸强度法、抗张积法、压缩永久变形法、综合取值法等);1.3专用仪器法(包括门尼粘度法、硫化仪法)等。
目前最常用的是硫化仪法。
通过硫化仪测试,可以得到胶料的正硫化时间。
2.制品硫化时间的确定2.1若制品厚度为6mm或小于6mm,并且胶料的成形工艺条件可以认为是均匀受热状态,那么,制品的硫化时间与硫化曲线中所测得的正硫化时间相同(温度一致的情况下,即加硫温度使用硫化仪测试的温度);2.2若制品壁厚大于6mm,每增加1mm的厚度,则测试的正硫化时间增加1min,这是一个经验数据。
例如,一橡胶制品,其厚度为22mm,试片测试的正硫化时间为6min(温度设定150℃),那么,在150℃硫化时,该制品的硫化时间为6+(22-6)×1=22min。
这时间不包括操作过程的辅助时间。
二段加硫时间设定:1.定义为了达到合理的制造工艺和合理成本,把橡胶硫化分为一段、二段两个过程来完成的工艺方法,其第二段的工艺就是所谓的二段加硫。
橡胶配方设计与硫化胶性能
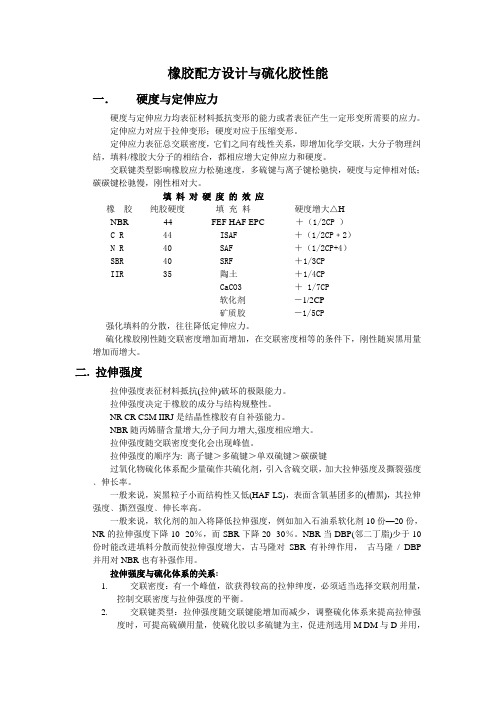
橡胶配方设计与硫化胶性能一.硬度与定伸应力硬度与定伸应力均表征材料抵抗变形的能力或者表征产生一定形变所需要的应力。
定伸应力对应于拉伸变形;硬度对应于压缩变形。
定伸应力表征总交联密度,它们之间有线性关系,即增加化学交联,大分子物理纠结,填料/橡胶大分子的相结合,都相应增大定伸应力和硬度。
交联键类型影响橡胶应力松驰速度,多硫键与离子键松驰快,硬度与定伸相对低;碳碳键松驰慢,刚性相对大。
填料对硬度的效应橡胶纯胶硬度填充料硬度增大△HNBR 44 FEF HAF EPC +(1/2CP )C R 44 ISAF +(1/2CP﹢2)N R 40 SAF +(1/2CP+4)SBR 40 SRF +1/3CPIIR 35 陶土+1/4CPCaCO3 + 1/7CP软化剂-1/2CP矿质胶-1/5CP强化填料的分散,往往降低定伸应力。
硫化橡胶刚性随交联密度增加而增加,在交联密度相等的条件下,刚性随炭黑用量增加而增大。
二. 拉伸强度拉伸强度表征材料抵抗(拉伸)破坏的极限能力。
拉伸强度决定于橡胶的成分与结构规整性。
NR CR CSM IIRJ是结晶性橡胶有自补强能力。
NBR随丙烯腈含量增大,分子间力增大,强度相应增大。
拉伸强度随交联密度变化会出现峰值。
拉伸强度的顺序为: 离子键>多硫键>单双硫键>碳碳键过氧化物硫化体系配少量硫作共硫化剂,引入含硫交联,加大拉伸强度及撕裂强度﹑伸长率。
一般来说,炭黑粒子小而结构性又低(HAF-LS),表面含氧基团多的(槽黑),其拉伸强度﹑撕烈强度﹑伸长率高。
一般来说,软化剂的加入将降低拉伸强度,例如加入石油系软化剂10份—20份,NR的拉伸强度下降10--20%,而SBR下降20--30%。
NBR当DBP(邻二丁脂)少于10份时能改进填料分散而使拉伸强度增大,古马隆对SBR有补绅作用,古马隆/ DBP 并用对NBR也有补强作用。
拉伸强度与硫化体系的关系:1.交联密度:有一个峰值,欲获得较高的拉伸绅度,必须适当选择交联剂用量,控制交联密度与拉伸强度的平衡。
橡胶技术网 新编橡胶配合剂手册

新编橡胶配合剂手册王作龄编译《新编橡胶配合剂手册》系编译自日本于2001年出版的《ゴムワラスチツク配合药品便览》一书。
全书共分25章,系统地介绍了橡胶和塑料用各种配合剂的种类、形状、作用以及生产厂家和商品名称,在此对橡胶配合剂部分编译。
第1章橡胶硫化剂和交联剂添加了硫黄的混炼胶加热后可制得塑性变形减小的,弹性和拉伸强度等诸性能均优异的制品。
该操作称为硫化,而硫化用的物质称为硫化剂(交联剂)。
交联剂一般在弹性体分子间形成交联键。
在交联反应中交联剂部分或全部引入分子中形成交联键。
1829年古特异(Goodyear)发现硫黄引起生胶的硬化现象(硫化),1902年韦伯(Weber)提出了硫化是橡胶和硫黄的化学反应,从此硫黄被广泛用于橡胶的交联。
尔后,开发了过氧化物交联、对醌二肟交联、异氰酸酯交联、酚醛树脂交联等,即开发了硫黄以外的各种交联剂。
橡胶工业中将由硫黄以外的物质引起的交联反应现象一般也称为硫化(Vulcanization)。
硫化剂的主力是硫黄,除此之外还有有机含硫化合物、有机过氧化物、对醌二肟化合物、金属氧化物、有机多价胺化合物、改性酚醛树脂等。
硫化剂多数是根据热能的作用剂的,在配合过程中较稳定,而在硫化工序中与橡胶迅速反应形成三维网状结构。
此外,硫化(交联)剂以粒状或制成母炼胶出售,谋求防止污染环境、提高操作性和分散性等。
1.1 硫黄(Sulfur of Sulphur)淡黄至黄色粉末或块状。
无味、无臭。
比重2.60左右。
熔点115℃。
沸点444℃。
有无定形和结晶形之分,两者的熔点稍有差别。
此外,有溶于二硫化碳和不溶于二硫化碳之分。
不溶性硫黄在120℃下变成可溶性。
硫黄中含有作为杂质的少量的水分和酸,有的还含有其它混合物。
硫黄是最普通的硫化剂,对于天然橡胶软质橡胶制品配合可添加0.3~4份。
用量多时易产生喷霜现象,而且耐老化性能降低,物理性能变差。
硫化时必须与促进剂和促进助剂并用。
此外,对硬质橡胶配合可添加30~60份。
橡胶的硫化与成型技术(十五)

:新书连 载 :
-・・・ t ・‘・・・ ,
橡 胶 的硫 化 与成 型 技 术 ( 十五 )
王作龄 编译
摘 要 : 该 书 系编 译 自 由 日 本 橡 胶 协 会 模 具 分 会 编 写 、 日本 工 业 调 查 会 于 2 0 0 4年 l 1月 出 版 的
《 厶・ 工 灭 7 一 用金 型技 术》 书 。 全 书共 分 l : 具 工 业 动 向 、 胶 与 弹 性 体 、 胶 与 弹 性 体 一 0章 模 橡 橡
8 35 线切 割加 工 .. 这是 一 种 以钢 丝 ( . i 和 0 3 m ) 0 2ml l . m 为 放 电电极 的加 工方 法 。该 法 是在要 求加 工如 图 8 —9那样 的挖 坑形 状 时使 用 , 者 使用 在 预 先 或
用这 种钻 头 , 工成 本 就 会 降 低 , 加 因此 , 好 能 最
种 。在生 产 厂家 的商 标 明确 时 , 了要 做 到 不 为 能 出现 仿 造 品 而必 须 按 指定 文 字 的形 状 、 小 大 和 高度进 行雕 刻 。对于 注重 公 司 自身形 象 的橡 胶企业 , 了其 指定 内容 不被 盗窃 , 为 也备 有公 司 自行 雕刻 的场 所 。
( )精 加工 2
模具 精 加 工 中 的滑 动配 合是
为 了防止胶 边 等而对 合模 面进 行表 面对合 的作
业 。防止胶 边可通 过 对芯 型部 位等施 以压机压
编译者简介: 王作 龄 (98) 男 , 东 青 岛 人 。 级 工 程 师 。 13- , 山 高 长 期 从 事 橡 胶 科 技 情 报研 究 ,3 科 技 文 献 翻 译 及 审 定 工 作 。 1文
力 , 用 铅 丹认 证合 模 面周 边 的 配合 状 态 加 以 及 确 认 。一般 采用 实用硫 化机 合模 力一 半 以下 的
硫化压力的计算
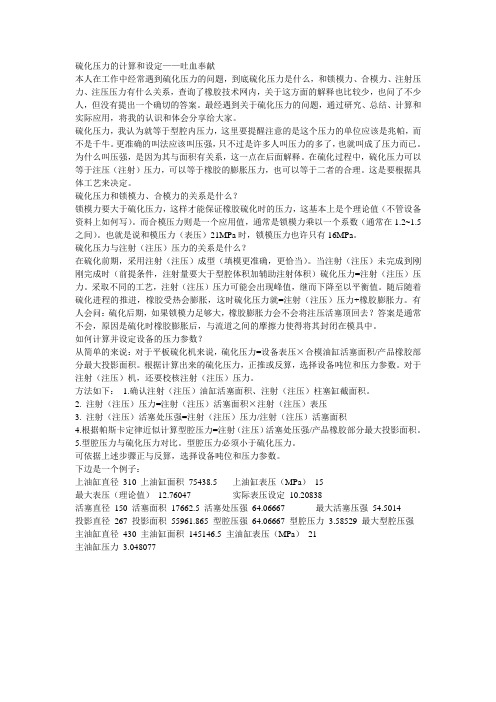
硫化压力的计算和设定——吐血奉献本人在工作中经常遇到硫化压力的问题,到底硫化压力是什么,和锁模力、合模力、注射压力、注压压力有什么关系,查询了橡胶技术网内,关于这方面的解释也比较少,也问了不少人,但没有提出一个确切的答案。
最经遇到关于硫化压力的问题,通过研究、总结、计算和实际应用,将我的认识和体会分享给大家。
硫化压力,我认为就等于型腔内压力,这里要提醒注意的是这个压力的单位应该是兆帕,而不是千牛。
更准确的叫法应该叫压强,只不过是许多人叫压力的多了,也就叫成了压力而已。
为什么叫压强,是因为其与面积有关系,这一点在后面解释。
在硫化过程中,硫化压力可以等于注压(注射)压力,可以等于橡胶的膨胀压力,也可以等于二者的合理。
这是要根据具体工艺来决定。
硫化压力和锁模力、合模力的关系是什么?锁模力要大于硫化压力,这样才能保证橡胶硫化时的压力,这基本上是个理论值(不管设备资料上如何写)。
而合模压力则是一个应用值,通常是锁模力乘以一个系数(通常在1.2~1.5之间)。
也就是说和模压力(表压)21MPa时,锁模压力也许只有16MPa。
硫化压力与注射(注压)压力的关系是什么?在硫化前期,采用注射(注压)成型(填模更准确,更恰当)。
当注射(注压)未完成到刚刚完成时(前提条件,注射量要大于型腔体积加辅助注射体积)硫化压力=注射(注压)压力。
采取不同的工艺,注射(注压)压力可能会出现峰值,继而下降至以平衡值。
随后随着硫化进程的推进,橡胶受热会膨胀,这时硫化压力就=注射(注压)压力+橡胶膨胀力。
有人会问:硫化后期,如果锁模力足够大,橡胶膨胀力会不会将注压活塞顶回去?答案是通常不会,原因是硫化时橡胶膨胀后,与流道之间的摩擦力使得将其封闭在模具中。
如何计算并设定设备的压力参数?从简单的来说:对于平板硫化机来说,硫化压力=设备表压×合模油缸活塞面积/产品橡胶部分最大投影面积。
根据计算出来的硫化压力,正推或反算,选择设备吨位和压力参数。
橡胶技术网 - XXX配方 DFMEA

(设计FME A )FMEA 编号:GS X07-001项目名称:XXX 产品技术部关键日期:2005/12/26编制:XXX2005/12/25(修订):主要参加人:XXX-项目小组橡胶工程师,XXX-项目小组质量工程师表单编号:QR/C2-01-22XR/T-2005-01设计责任部门: FMEA 日期(编制):(设计FME A)FMEA 编号:GS X0 7-001项目名称:XXX产品技术部关键日期:2005/12/26编制:XXX2005/12/25(修订):主要参加人:XXX-项目小组橡胶工程师,XXX-项目小组质量工程师表单编号:QR/C2-01-22XR/T-2005-01设计责任部门:FMEA日期(编制):(设计FME A)FMEA 编号:GS X0 7-001项目名称:XXX产品技术部关键日期:2005/12/26编制:XXX2005/12/25(修订):主要参加人:XXX-项目小组橡胶工程师,XXX-项目小组质量工程师表单编号:QR/C2-01-22XR/T-2005-01设计责任部门:FMEA日期(编制):(设计FME A)FMEA 编号:GS X0 7-001项目名称:XXX产品技术部关键日期:2005/12/26编制:XXX2005/12/25(修订):主要参加人:XXX-项目小组橡胶工程师,XXX-项目小组质量工程师表单编号:QR/C2-01-22XR/T-2005-01设计责任部门:FMEA日期(编制):加工性能(设计FME A)FMEA 编号:GS X0 7-001项目名称:XXX产品技术部关键日期:2005/12/26编制:XXX2005/12/25(修订):主要参加人:XXX-项目小组橡胶工程师,XXX-项目小组质量工程师表单编号:QR/C2-01-22XR/T-2005-01设计责任部门:FMEA日期(编制):。
硫化合模力的计算

桂林硫化机63.5
F=K*Q
K为经验常数1.05-1.15
Q=0.785{D2P+(D S2-D2)*P S}
其中:
D:轮胎外直径mm
P:胶囊工作介质最大工作压力MPa
Ds:蒸气室直径.本硫化机蒸气室直径为1525mm。
Ps:蒸气室工作介质最大工作压力。
MPa
65硫化机
P≥0.785﹝(P内-P外)d2+P外D2﹞(1.25-1.5)
其中:
P——合模力
d——模型结合面平均直径mm
D——蒸气室密封圈平均直径(本机器D=1560mm)
P内——胶囊工作介质压力MPa
P外——硫化外压整齐压力MPa
注意事项:合模力调整应预热后进行,这时合模力即使增加内压力和蒸汽压力的作用,合模力几乎不会增加,冷模调节时应按较小的合模力来调节,因为待模子加热后,合模力约增加0.3倍。
橡胶技术网 - 科学技术 - 合成橡胶
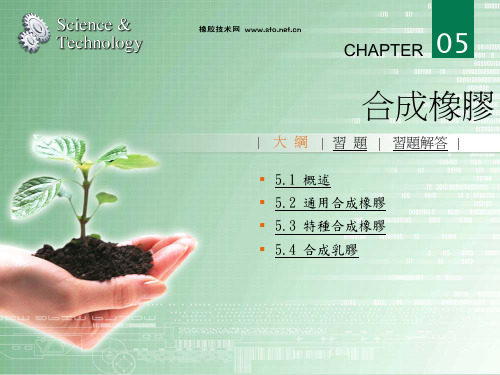
橡胶技术网
混煉膠的加工成型
成型工藝是把構成製品的各部件,通過粘貼、壓合、壓 延、壓出等方法組合成具有一定形狀的整體的過程。 不同類型的橡膠製品,其成型工藝也不同,全膠類製品, 如各種模型製品,成型工藝較簡單,即將壓延或壓出的 膠片或膠條切割成一定形狀,放入模型中經硫化便可得 製品。 而含有紡織物或金屬等骨架材料的製品,如膠管、膠帶、 輪胎、膠鞋等,則必須借助一定的模具,通過粘貼或壓 合方法將各零件組合而成型。粘貼通常是利用膠料的熱 粘性能,或使用溶劑、膠漿、膠乳等粘合劑。
P. 12
橡胶技术网
5.1.5合成橡膠的硫化過程及性能變化 硫化方法
橡膠製品的硫化方法很多,按其使用的硫化條件不同可 分爲冷硫化、室溫硫化和熱硫化三種; 按採用不同的硫化介質可分爲直接硫化(直接蒸汽硫化 和直接熱水硫化)、間接硫化也稱間接蒸汽硫化和混氣 硫化(採用蒸汽和空氣兩種介質)。 按使用的硫化設備可分爲硫化罐硫化、平板硫化機硫化、 個體硫化機硫化和注壓硫化。
橡胶技术网
CHAPTER
05
合成橡膠
大 綱 5.1 概述 5.2 通用合成橡膠 5.3 特種合成橡膠 5.4 合成乳膠 習 題 習題解答
5.1 概述
5.1.1合成橡膠的分類
橡胶技术网
按合成橡膠的性能與用途來分類
通用合成橡膠(簡稱通用橡膠) 特種合成橡膠(簡稱特種橡膠)
P. 20
橡胶技术网
丁苯橡膠的用途很廣,大多數場合下可代替天然橡膠使 用,主要用於汽車輪胎及各種工業橡膠製品。含苯乙烯 較少的丁苯橡膠,可用作耐寒橡膠製品;苯乙烯含量高 者,則製作硬質橡膠製品。
溶液聚合丁苯橡膠
丁二烯與苯乙烯在有機溶劑中用有機鋰化合物作引發劑 進行陰離子共聚反應所得的彈性體,稱爲溶液聚合丁苯 橡膠(SBR),或溶液丁苯。 溶液丁苯橡膠在耐磨、耐寒、彈性、永久變形及動態性 能方面都比乳化法的好,但其成本較貴。
微生物天然橡胶的硫化特性及力学性能

微生物天然橡胶的硫化特性及力学性能橡胶配合剂对橡胶结构与性能的影响第一章前言一、天然橡胶的组份天然橡胶( NR) 是一种重要的工业原料, 来自于三叶橡胶树的树液乳汁中, 这种乳汁就是天然胶乳。
天然橡胶(NR)是从天然植物中获取的以聚顺式1.4异戊二烯为主要成分的天然高分子化合物。
其主要成分为:橡胶烃、水、非胶物质。
其中非胶物质成分占5%一8%,主要是由蛋白质、类脂物、丙酮溶物、水溶物、无机盐等组成。
尽管这些物质的数量不多,但其种类繁多,并对制胶工艺和产品性能有不同程度的影响,赋予天然橡胶具有优越的工艺操作性能和物理机械性能,使天然橡胶在许多领域和行业中都具有广泛的用途。
天然胶乳需经凝固、压薄、压绉脱水、锤磨造粒和干燥工序, 最终才能制成NR。
长期以来, 我国生产中国标准天然橡胶( SCR) 均采用:鲜胶乳→加氨保存→酸凝固的生产工艺。
二、微生物凝固工艺及其机理胶乳的微生物凝固是指通过添加微生物繁殖所需的糖类物质,使割胶后污染的微生物或后来人为接种微生物的活性增强,并在较短时间内大量繁殖,从而加速了胶乳自然凝固的过程。
从胶树流出来的胶乳,放置一段时间后,会发生自然凝固,其根本原因是由于微生物的作用使胶乳中非橡胶物质发生变化。
胶乳中含有大量的糖类、蛋自质、磷酸盐等细菌所需的养料,因而细菌繁殖很快。
其中,糖类被细菌吸收利用,转化为各种酸类,主要是挥发性脂肪酸。
蛋白质也会被细菌分泌的酶分解为氨基酸被吸收利用或发生变性。
因而胶粒的保护层被破坏,pH值不断下降,直至到达或接近等电点的pH值时,胶乳便凝固。
胶乳发生自然凝固的原因通常有3种理论解释:(1)由于细菌在胶乳内不断产生挥发脂肪酸,降低了胶乳的pH值,从而导致胶乳自然凝固;(2)由于胶乳中形成高级脂肪酸并吸附在胶乳中的橡胶粒子上,这些羧酸根同金属离子结合,生成羧酸盐而导致胶乳自然凝固;(3)胶乳中存在分解蛋白酶,即凝固酶和过氧化物酶,作用于胶乳中橡胶粒子的蛋白质层,破坏了橡胶粒子表面的吸附层,使橡胶粒子失去稳定性而互相粘结,导致胶乳自然凝固。
【详细】橡胶的各种硫化体系讲解!(收藏)
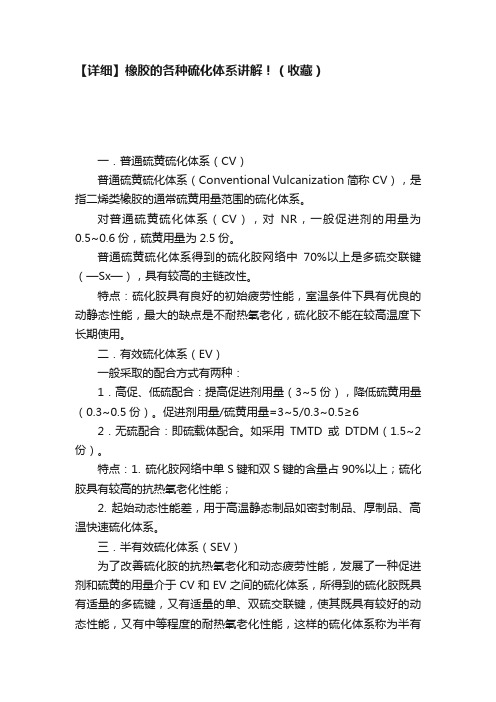
【详细】橡胶的各种硫化体系讲解!(收藏)一.普通硫黄硫化体系(CV)普通硫黄硫化体系(Conventional Vulcanization简称CV),是指二烯类橡胶的通常硫黄用量范围的硫化体系。
对普通硫黄硫化体系(CV),对NR,一般促进剂的用量为0.5~0.6份,硫黄用量为2.5份。
普通硫黄硫化体系得到的硫化胶网络中70%以上是多硫交联键(—Sx—),具有较高的主链改性。
特点:硫化胶具有良好的初始疲劳性能,室温条件下具有优良的动静态性能,最大的缺点是不耐热氧老化,硫化胶不能在较高温度下长期使用。
二.有效硫化体系(EV)一般采取的配合方式有两种:1.高促、低硫配合:提高促进剂用量(3~5份),降低硫黄用量(0.3~0.5份)。
促进剂用量/硫黄用量=3~5/0.3~0.5≥6 2.无硫配合:即硫载体配合。
如采用TMTD或DTDM(1.5~2份)。
特点:1. 硫化胶网络中单S键和双S键的含量占90%以上;硫化胶具有较高的抗热氧老化性能;2. 起始动态性能差,用于高温静态制品如密封制品、厚制品、高温快速硫化体系。
三.半有效硫化体系(SEV)为了改善硫化胶的抗热氧老化和动态疲劳性能,发展了一种促进剂和硫黄的用量介于CV和EV之间的硫化体系,所得到的硫化胶既具有适量的多硫键,又有适量的单、双硫交联键,使其既具有较好的动态性能,又有中等程度的耐热氧老化性能,这样的硫化体系称为半有效硫化体系(SEV)。
用于有一定的使用温度要求的动静态制品。
一般采取的配合方式有两种:1.促进剂用量/硫用量=1.0/1.0=1(或稍大于1);2.硫与硫载体并用,促进剂用量与SEV中一致。
NR的三种硫化体系配合如下表所示:配方成分C V EV高促低硫无硫配合Semi—EV高促低硫硫\硫载体并用SNOB STMT DDMD T 2.50.60.53.0 1.10.6 1.11.11.5 1.51.5 0.60.6四.高温快速硫化体系随着橡胶工业生产的自动化、联动化,高温快速硫化体系被广泛采用,如注射硫化、电缆的硫化等。
橡胶技术网 - 美国罗门哈斯:橡胶和金属热硫化粘合剂
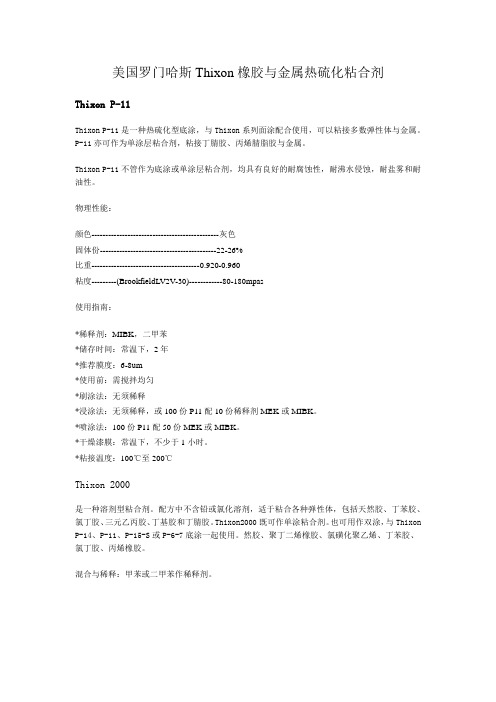
美国罗门哈斯Thixon橡胶与金属热硫化粘合剂Thixon P-11Thixon P-11是一种热硫化型底涂,与Thixon系列面涂配合使用,可以粘接多数弹性体与金属。
P-11亦可作为单涂层粘合剂,粘接丁腈胶、丙烯腈脂胶与金属。
Thixon P-11不管作为底涂或单涂层粘合剂,均具有良好的耐腐蚀性,耐沸水侵蚀,耐盐雾和耐油性。
物理性能:颜色----------------------------------------------灰色固体份------------------------------------------22-26%比重---------------------------------------0.920-0.960粘度---------(BrookfieldLV2V-30)------------80-180mpas使用指南:*稀释剂:MIBK,二甲苯*储存时间:常温下,2年*推荐膜度:6-8um*使用前:需搅拌均匀*刷涂法:无须稀释*浸涂法:无须稀释,或100份P11配10份稀释剂MEK或MIBK。
*喷涂法:100份P11配50份MEK或MIBK。
*干燥漆膜:常温下,不少于1小时。
*粘接温度:100℃至200℃Thixon 2000是一种溶剂型粘合剂。
配方中不含铅或氯化溶剂,适于粘合各种弹性体,包括天然胶、丁苯胶、氯丁胶、三元乙丙胶、丁基胶和丁腈胶。
Thixon2000既可作单涂粘合剂。
也可用作双涂,与Thixon P-14、P-11、P-15-S或P-6-7底涂一起使用。
然胶、聚丁二烯橡胶、氯磺化聚乙烯、丁苯胶、氯丁胶、丙烯橡胶。
混合与稀释:甲苯或二甲苯作稀释剂。
物理性能:颜色-----------------------------------------------黑色粘度-------------(Brookfield 4#转子,100RPM)----1150CPS固体份----------------------------------------------26%比重-----------------------------------------------0.99贮存时间--------------------------------------------1年闪点------------------------------------------------4℃硫化温度------------------------------------100℃至190℃应用方式:推荐漆膜厚度18-25cm.*刷涂:对于刷涂,Thixon 2000无需稀释。
《橡胶的硫化体系》PPT课件

②热硫化(crosslink)阶段
二.硫化的发展
时间 硫化体系 硫化条件
1839年 S 140℃×(9~10hr)
1844年 S+PbO
1906年 S+PbO+苯胺 ~2hr)
1920年 )
S+ZnO+苯胺+硬酯酸
1921年 S+ZnO+D+硬酯酸 in)
1925年 S+ZnO+M+硬酯酸
1930年 S+ZnO+DM+硬酯酸
硫 化
硫化仪的测试过程
硫化仪预热
胶料加入 硫化仪模腔
合模加压施加应变 胶料开始硫化
硫化曲线
传感器将扭矩 转变为电信号
测量扭矩 随时间的变化
硫化历程与硫化曲线
硫化曲线
温度曲线-等温 硫化 扭矩曲线
焦烧 期
热硫化 期
平坦硫化 期
过硫化 期
硫化曲线
硫化曲线中常用的参数
• 最小转矩 (Minimum Torque)ML • 最大转矩 (Maximum Torque) MH • 焦烧时间(T10):胶料从加入到模具中受热开始到转矩
硫化胶
交联反应 网络熟化
2. 橡胶的硫化历程
了解硫化的化学反应过程
实际问题: 如何确定在某一条件下硫化完成的程度?
选定某个反映硫化程度的测试指标
测试
硫化仪
硫化仪
有转子硫化仪
Oscillating Disk Rheometer - ODR
双模硫化机合模力标准
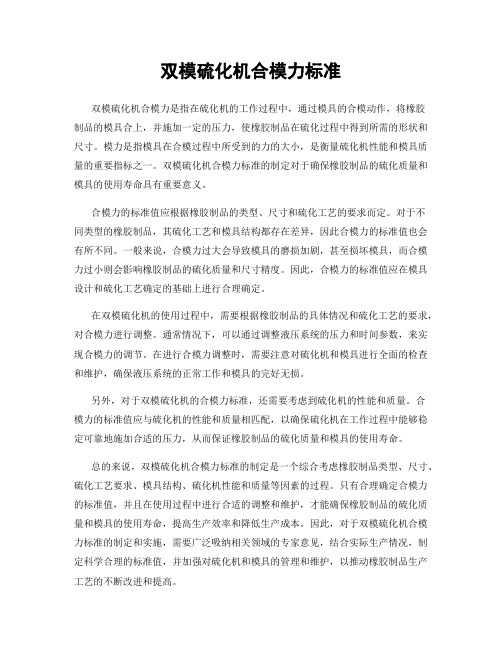
双模硫化机合模力标准双模硫化机合模力是指在硫化机的工作过程中,通过模具的合模动作,将橡胶制品的模具合上,并施加一定的压力,使橡胶制品在硫化过程中得到所需的形状和尺寸。
模力是指模具在合模过程中所受到的力的大小,是衡量硫化机性能和模具质量的重要指标之一。
双模硫化机合模力标准的制定对于确保橡胶制品的硫化质量和模具的使用寿命具有重要意义。
合模力的标准值应根据橡胶制品的类型、尺寸和硫化工艺的要求而定。
对于不同类型的橡胶制品,其硫化工艺和模具结构都存在差异,因此合模力的标准值也会有所不同。
一般来说,合模力过大会导致模具的磨损加剧,甚至损坏模具,而合模力过小则会影响橡胶制品的硫化质量和尺寸精度。
因此,合模力的标准值应在模具设计和硫化工艺确定的基础上进行合理确定。
在双模硫化机的使用过程中,需要根据橡胶制品的具体情况和硫化工艺的要求,对合模力进行调整。
通常情况下,可以通过调整液压系统的压力和时间参数,来实现合模力的调节。
在进行合模力调整时,需要注意对硫化机和模具进行全面的检查和维护,确保液压系统的正常工作和模具的完好无损。
另外,对于双模硫化机的合模力标准,还需要考虑到硫化机的性能和质量。
合模力的标准值应与硫化机的性能和质量相匹配,以确保硫化机在工作过程中能够稳定可靠地施加合适的压力,从而保证橡胶制品的硫化质量和模具的使用寿命。
总的来说,双模硫化机合模力标准的制定是一个综合考虑橡胶制品类型、尺寸、硫化工艺要求、模具结构、硫化机性能和质量等因素的过程。
只有合理确定合模力的标准值,并且在使用过程中进行合适的调整和维护,才能确保橡胶制品的硫化质量和模具的使用寿命,提高生产效率和降低生产成本。
因此,对于双模硫化机合模力标准的制定和实施,需要广泛吸纳相关领域的专家意见,结合实际生产情况,制定科学合理的标准值,并加强对硫化机和模具的管理和维护,以推动橡胶制品生产工艺的不断改进和提高。
橡胶硫化三要素之一压力(原理、计算和设定)
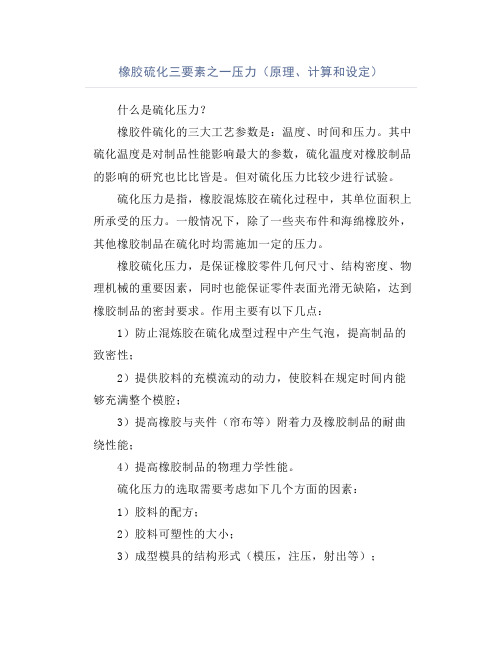
橡胶硫化三要素之一压力(原理、计算和设定)什么是硫化压力?橡胶件硫化的三大工艺参数是:温度、时间和压力。
其中硫化温度是对制品性能影响最大的参数,硫化温度对橡胶制品的影响的研究也比比皆是。
但对硫化压力比较少进行试验。
硫化压力是指,橡胶混炼胶在硫化过程中,其单位面积上所承受的压力。
一般情况下,除了一些夹布件和海绵橡胶外,其他橡胶制品在硫化时均需施加一定的压力。
橡胶硫化压力,是保证橡胶零件几何尺寸、结构密度、物理机械的重要因素,同时也能保证零件表面光滑无缺陷,达到橡胶制品的密封要求。
作用主要有以下几点:1)防止混炼胶在硫化成型过程中产生气泡,提高制品的致密性;2)提供胶料的充模流动的动力,使胶料在规定时间内能够充满整个模腔;3)提高橡胶与夹件(帘布等)附着力及橡胶制品的耐曲绕性能;4)提高橡胶制品的物理力学性能。
硫化压力的选取需要考虑如下几个方面的因素:1)胶料的配方;2)胶料可塑性的大小;3)成型模具的结构形式(模压,注压,射出等);4)硫化设备的类型(平板硫化机,注压硫化机,射出硫化机,真空硫化机等);5)制品的结构特点。
硫化压力选取的一般原则:1)胶料硬度低的(50-ShoreA以下或更低),压力宜选择小,硬度高的选择大;2)薄制品选择小,厚制品选择大;3)制品结构简单选择小,结构复杂选择大;4)力学性能要求高选择大,要求低选择小;5)硫化温度较高时,压力可以小一些,温度较低时,压力宜高点。
对硫化压力,国内外一些橡胶厂家有如下一些经验值供参考:1)模压及移模注压的硫化方式,其模腔内的硫化压力为:10~20Mpa;2)注压硫化方式其模腔内的硫化压力为:0~150Mpa;3)硫化压力增大,产品的静态刚度也随之增大,而收缩率随之逐渐减小;(在国内的减振橡胶行业内,对于调整产品的刚度,普遍采用的依然是增加或者降低产品所使用的胶料硬度,而在国外,已经普遍采用了提高或者降低产品硫化时的胶料硫化压力来调整产品的静态刚度。