炼钢流程及合金辅料(谷风研究)
钢材生产工艺流程

钢材生产工艺流程钢材是一种重要的金属材料,广泛应用于建筑、桥梁、汽车、机械等众多行业。
钢材的生产过程经历了多个步骤和流程,在本文中,我们将详细描述钢材的生产工艺流程,以确保流程清晰且实用。
1. 炼钢炼钢是钢材生产的第一步,其主要目的是将主要原料铁矿石转化为熔融的钢水。
1.1 铁矿石准备铁矿石是炼钢的主要原料,常见的有赤铁矿、磁铁矿、褐铁矿等。
首先,将铁矿石经过破碎、磨矿等工艺处理,使其细化,并去除其中的杂质。
1.2 炼焦炼焦是将冶金焦炭作为还原剂,将炼钢所需的高炉矿石还原为金属铁的过程,也是炼钢过程中重要的一环。
冶金焦炭由高炉煤炭经过热解、干馏等工艺得到。
1.3 确定配比根据所需钢种的成分要求,将铁矿石、冶金焦炭、石灰石等原料按一定比例混合,形成炼钢原料配料。
1.4 高炉炼制在高炉中进行炼钢过程,主要包括以下几个步骤: - 喷吹煤气与空气:通过喷吹煤气和预热空气,使其与炉内原料充分混合并燃烧,提供高炉所需的高温。
- 进料炉料:将预热、干燥后的炼钢原料连续送入高炉顶部,经由料槽、减压室等设备进入高炉,与上升气流一起下降。
- 返炉煤气再利用:炼钢过程中产生的煤气通过除尘、脱硫等处理后,一部分用于高炉本身的煤气喷吹,一部分作为燃料供热能。
- 熔化还原:由喷吹的煤气和炉料中的还原剂CO燃烧反应,使矿石中的铁氧化物还原为金属铁。
- 渗碳反应:喷吹的煤气中的一氧化碳(CO)与熔融金属铁发生气态反应,使铁中的碳含量达到要求。
- 收集钢水:从高炉底部收集炉料中的熔融金属铁,形成炼钢出钢口,流出钢水,也称为铁水。
2. 制钢经过炼钢工艺,我们得到了熔融的钢水,接下来需要对钢水进行精炼、连铸和热处理等过程,最终得到成品钢材。
2.1 精炼钢水中含有一定的杂质,如硫、磷、氧化物等。
为了提高钢的质量,需要对钢水进行精炼。
常用的精炼方法包括转炉法和电炉法: - 转炉法:将钢水转入转炉内,通过与喷吹的氧气反应,使钢中的杂质氧化并排出。
炼钢生产流程详细讲解

钢铁生产工艺主要包括:炼铁、炼钢、轧钢等流程。
(1)炼铁:就是把烧结矿和块矿中的铁还原出来的过程。
焦炭、烧结矿、块矿连同少量的石灰石、一起送入高炉中冶炼成液态生铁(铁水),然后送往炼钢厂作为炼钢的原料。
(2)炼钢:是把原料(铁水和废钢等)里过多的碳及硫、磷等杂质去掉并加入适量的合金成分。
(3)连铸:将钢水经中间罐连续注入用水冷却的结晶器里,凝成坯壳后,从结晶器以稳定的速度拉出,再经喷水冷却,待全部凝固后,切成指定长度的连铸坯。
(4)轧钢:连铸出来的钢锭和连铸坯以热轧方式在不同的轧钢机轧制成各类钢材,形成产品。
炼钢工艺总流程图炼焦生产流程:炼业是将焦煤经混合,破碎后加入炼焦炉经干馏后产生热焦碳及粗焦炉气之制程。
烧结生产流程:烧结作业系将粉铁矿,各类助熔剂及细焦炭经由混拌、造粒后,经由布料系统加入烧结机,由点火炉点燃细焦炭,经由抽气风车抽风完成烧结反应,高热之烧结矿经破碎冷却、筛选后,送往高炉作为冶炼铁水之主要原料。
高炉生产流程:高炉作业是将铁矿石、焦炭及助熔剂由高炉顶部加入炉,再由炉下部鼓风嘴鼓入高温热风,产生还原气体,还原铁矿石,产生熔融铁水与熔渣之炼铁制程。
转炉生产流程:炼钢厂先将熔铣送前处理站作脱硫脱磷处理,经转炉吹炼后,再依订单钢种特性及品质需求,送二次精炼处理站(RH真空脱气处理站、Ladle Injection盛桶吹射处理站、VOD真空吹氧脱碳处理站、STN搅拌站等)进行各种处理,调整钢液成份,最后送大钢胚及扁钢胚连续铸造机,浇铸成红热钢胚半成品,经检验、研磨或烧除表面缺陷,或直接送下游轧制成条钢、线材、钢板、钢卷及钢片等成品。
连铸生产流程:连续铸造作业乃是将钢液转变成钢胚之过程。
上游处理完成之钢液,以盛钢桶运送到转台,经由钢液分配器分成数股,分别注入特定形状之铸模,开始冷却凝固成形,生成外为凝固壳、为钢液之铸胚,接着铸胚被引拔到弧状铸道中,经二次冷却继续凝固到完全凝固。
经矫直后再依订单长度切割成块,方块形即为大钢胚,板状形即为扁钢胚。
炼钢的工艺流程
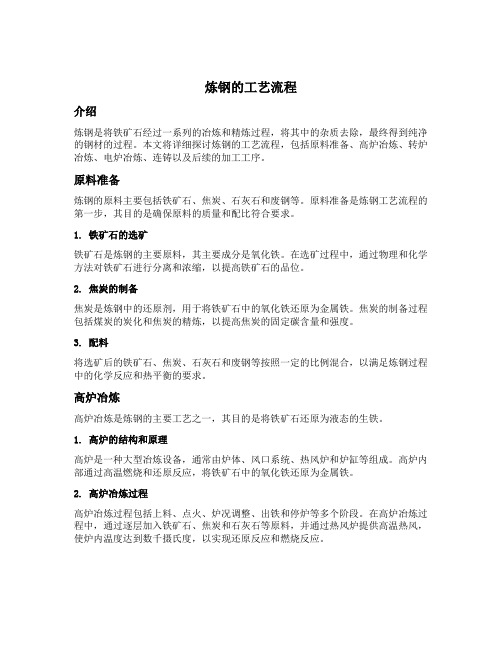
炼钢的工艺流程介绍炼钢是将铁矿石经过一系列的冶炼和精炼过程,将其中的杂质去除,最终得到纯净的钢材的过程。
本文将详细探讨炼钢的工艺流程,包括原料准备、高炉冶炼、转炉冶炼、电炉冶炼、连铸以及后续的加工工序。
原料准备炼钢的原料主要包括铁矿石、焦炭、石灰石和废钢等。
原料准备是炼钢工艺流程的第一步,其目的是确保原料的质量和配比符合要求。
1. 铁矿石的选矿铁矿石是炼钢的主要原料,其主要成分是氧化铁。
在选矿过程中,通过物理和化学方法对铁矿石进行分离和浓缩,以提高铁矿石的品位。
2. 焦炭的制备焦炭是炼钢中的还原剂,用于将铁矿石中的氧化铁还原为金属铁。
焦炭的制备过程包括煤炭的炭化和焦炭的精炼,以提高焦炭的固定碳含量和强度。
3. 配料将选矿后的铁矿石、焦炭、石灰石和废钢等按照一定的比例混合,以满足炼钢过程中的化学反应和热平衡的要求。
高炉冶炼高炉冶炼是炼钢的主要工艺之一,其目的是将铁矿石还原为液态的生铁。
1. 高炉的结构和原理高炉是一种大型冶炼设备,通常由炉体、风口系统、热风炉和炉缸等组成。
高炉内部通过高温燃烧和还原反应,将铁矿石中的氧化铁还原为金属铁。
2. 高炉冶炼过程高炉冶炼过程包括上料、点火、炉况调整、出铁和停炉等多个阶段。
在高炉冶炼过程中,通过逐层加入铁矿石、焦炭和石灰石等原料,并通过热风炉提供高温热风,使炉内温度达到数千摄氏度,以实现还原反应和燃烧反应。
转炉冶炼是炼钢的另一种常用工艺,其主要特点是采用氧气吹炼,将生铁转化为钢水。
1. 转炉的结构和原理转炉是一种承压容器,通常由炉体、氧气吹炼系统和倾炉机构等组成。
转炉内部通过氧气吹炼和搅拌,将生铁中的碳和其他杂质氧化除去,从而得到低碳钢水。
2. 转炉冶炼过程转炉冶炼过程包括预热、装料、吹炼、倾炉和取样等多个阶段。
在转炉冶炼过程中,通过预热转炉、加入生铁和废钢等原料,并通过氧气吹炼和搅拌,使炉内温度升高并实现氧化还原反应,最终得到符合要求的钢水。
电炉冶炼电炉冶炼是一种利用电能将废钢和生铁等原料进行冶炼的工艺,其主要特点是能够灵活调整炉温和合金成分。
炼钢生产流程详解

炼钢生产流程详解炼钢生产是炼铁之后的一个重要工艺过程,其目的是将炼铁中的钢铁元素加以净化和加入适宜的合金元素,制造出各种不同用途的钢材产品。
炼钢生产流程涉及到多个环节和技术,本文将详细阐述炼钢的生产流程。
一、原料准备炼钢的原料主要有生铁、废钢、铁合金、石灰石等。
生铁是炼钢的主要原料之一,它含有较高的铁和碳元素,但同时也含有许多杂质。
废钢是指废旧的钢材制品,其含有一定的碳、铁等元素,但杂质较少。
铁合金是由铁和其他金属元素混合而成的,可以根据不同的用途选择合适的铁合金。
石灰石则用于炼钢炉石灰石反应时的脱硫作用。
二、炼钢炉的预热炼钢需要用到高温,因此需要炉子进行预热,以达到适宜的操作温度。
根据炉子的类型不同,预热温度也有所不同。
电炉的预热温度一般在800-1000℃之间,而转炉的预热温度一般在1200-1300℃之间。
三、熔化原料将原料分别装入炉子中,熔化原料是炼钢流程中的第一步。
熔化生铁时需要将生铁放入电炉或转炉中,在电弧的高温下,生铁被炼化为钢水。
废钢则可以通过回转炉等冶炼设备进行熔化。
铁合金则会根据不同的需要和用途加入炉中。
石灰石则通常在转炉炉缸顶部喷入,与钢中的杂质反应生成气体,协助此后的除渣和脱硫操作。
四、净化钢水钢水中含有铁以外的杂质,如硅、锰、磷、硫等元素。
这些杂质会影响钢材的质量和性能,因此需要对其进行净化。
采用多种技术进行净化操作,比如炼钢炉内加入耐火物质会吸附掉钢水中的杂质等。
五、添加合金炼钢材料需要满足不同的用途和性能要求。
因此,需要根据不同的要求添加适宜的合金元素。
合金的加入可以通过直接加入元素或者加入铁合金的形式实现。
添加铜、铬、钼、锰、镍、钒等元素可以带来钢材的高耐磨性、高强度、耐蚀性等性能。
六、除渣脱硫钢水中还残留有炼钢过程中产生的氧化物和硫化物等溶解在其中,这些溶解物会对钢材质量造成影响,因此需要进行除渣脱硫。
除渣常见的方法包括人工清理、机械清理、氧气喷注清理等;脱硫则可以通过炉体上部加入石灰石进行脱硫操作。
炼钢厂工艺流程

炼钢厂工艺流程炼钢厂工艺流程是指在炼钢过程中,经过一系列步骤将生铁转化为钢铁的过程。
下面将介绍一下炼钢厂工艺流程的主要步骤和其中的关键技术。
首先,炼钢厂工艺流程的第一步是炉料备料。
在这一步中,需要根据生产需要,按照一定比例将生铁、废钢和其他辅助材料混合。
其中,生铁是由高炉炼铁得到的产品,主要含有铁和碳等元素,废钢是指回收利用的旧钢材或副产品。
根据炼钢厂的技术要求,还可以添加合金元素、石灰石等辅助材料。
接下来是炉料熔化和预处理。
这一步通常由高炉完成,将炉料投入高炉进行熔化和还原。
高炉是炼钢的主要设备,其熔化温度可以达到1500摄氏度以上。
在高炉内,炉料中的铁和其他有用元素将被熔化,废气中的不需要的元素则会被排除。
通过控制高炉的温度、压力和喷吹条件,可以使熔化的炉料中的杂质被还原并形成液态铁。
第三步是炼钢。
将高炉产出的液态铁送入转炉或电炉中进行炼钢。
转炉是常用的炼钢设备之一,其内部有一个能够旋转的转鼓,通过喷吹氧气等气体进入转炉,并加入石灰石等辅助料,使液态铁中的碳等杂质被氧气氧化和燃烧,并通过气体的作用将氧化物和杂质排出。
通过不断添加氧气和辅助料,可以调整钢液中的成分和温度,以达到炼钢的要求。
最后一步是连铸。
炼钢过程得到的炼钢钢液会被送入连铸机中,通过连铸机将炼钢钢液填充到连铸结晶器中,经过冷却后形成连铸坯。
连铸是将炼钢钢液快速冷却并成型的过程,通过控制冷却速度和结晶器的形状,可以得到不同尺寸和形状的连铸坯。
连铸坯是生产钢铁产品的基础,后续还需要经过轧制、锻造等工艺加工成形。
总之,炼钢厂工艺流程是一个复杂而严密的过程,涉及到多个步骤和各种工艺设备。
通过合理控制炉料成分、调整炼钢过程的参数和条件,可以得到质量良好的钢铁产品,满足市场的需求。
同时,炼钢过程中还需要注意环保和安全,采取适当的措施处理废气和废渣,保护环境和工人的健康。
炼钢生产流程

3.此外,氧气也作为一种助燃剂,提高炼钢,炼 铁的温度,有助于反应的快速进行。
炼钢生产流程
详细流程及辅助说明
辅助说明:原料初期说明、脱硫 站、取样
详细流程:转炉、连铸机、精炼 炉
原料初期说明
铁水的硫含量:0.04%-0.06% 碳含量:4.3% 钢水的硫含量:0.02%以下 碳含量:0.1% 铁水的磷含量:0.11%-0.13%
硫含量达标—铁水包—转炉
硫含量不达标—脱硫站—取样
脱硫站
由喷枪进入铁水底部吹入氮气, 将镁粉吹出。
其软件已实现了自动化
脱硫后必须扒渣
取样
将凝固后的样品单面磨光,用光 谱仪进行分析,决定成分是否达 标,如硫、碳、锰、磷等。
转炉它是质量控制的重点源自首先加入铁水和废钢(加废钢的作用是为了 降温)
其次是吹氧去碳升温
最后在吹氧过程中加入石灰和清烧白云石
精炼炉
作用:深入脱硫、去除夹杂物、升温、微调 成分
通过吹氩去除夹杂物(已实现自动化)。夹 杂物如三氧化二铝(小颗粒)、二氧化硅 (大颗粒)
微调成分的主要操作需要人工配比。
钢坯质量检验
表面质量:形状、光滑、裂纹、划伤、 气孔
内部质量:中心裂纹、中间裂纹、空 气孔、中间松
补充知识
1.炼铁是还原反应。先是利用氧把矿石中铁及其 他物质氧化为三氧化二铁、硫、磷的氧化物等。 硫的氧化物经过处理后排放,磷的氧化物还要加 入石灰后转化为矿渣后排出。主要反应为利用 C 把铁的氧化物还原 2 Fe2O3+ 3 C=4 Fe+ 3 CO2.
炼钢生产过程及流程图详解 全
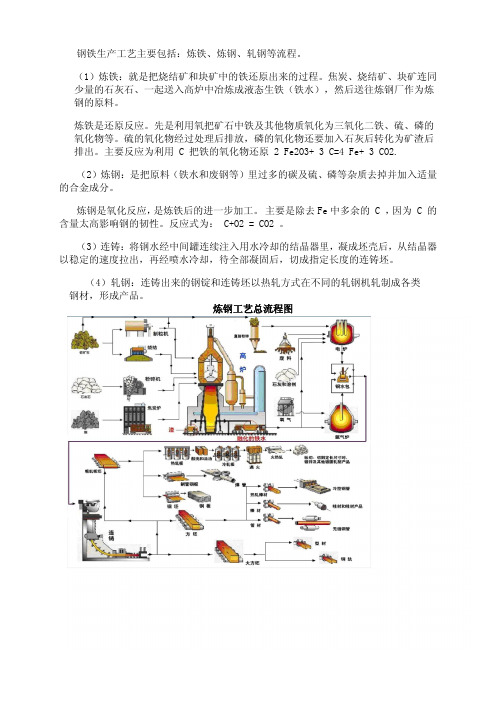
钢铁生产工艺主要包括:炼铁、炼钢、轧钢等流程。
(1)炼铁:就是把烧结矿和块矿中的铁还原出来的过程。
焦炭、烧结矿、块矿连同少量的石灰石、一起送入高炉中冶炼成液态生铁(铁水),然后送往炼钢厂作为炼钢的原料。
炼铁是还原反应。
先是利用氧把矿石中铁及其他物质氧化为三氧化二铁、硫、磷的氧化物等。
硫的氧化物经过处理后排放,磷的氧化物还要加入石灰后转化为矿渣后排出。
主要反应为利用 C 把铁的氧化物还原 2 Fe2O3+ 3 C=4 Fe+ 3 CO2.(2)炼钢:是把原料(铁水和废钢等)里过多的碳及硫、磷等杂质去掉并加入适量的合金成分。
炼钢是氧化反应,是炼铁后的进一步加工。
主要是除去Fe中多余的 C ,因为 C 的含量太高影响钢的韧性。
反应式为: C+O2 = CO2 。
(3)连铸:将钢水经中间罐连续注入用水冷却的结晶器里,凝成坯壳后,从结晶器以稳定的速度拉出,再经喷水冷却,待全部凝固后,切成指定长度的连铸坯。
(4)轧钢:连铸出来的钢锭和连铸坯以热轧方式在不同的轧钢机轧制成各类 钢材,形成产品。
炼钢工艺总流程图炼焦生产流程:炼焦作业是将焦煤经混合,破碎后加入炼焦炉内经干馏后产生热焦碳及粗焦炉气之制程。
烧结生产流程:烧结作业系将粉铁矿,各类助熔剂及细焦炭经由混拌、造粒后,经由布料系统加入烧结机,由点火炉点燃细焦炭,经由抽气风车抽风完成烧结反应,高热之烧结矿经破碎冷却、筛选后,送往高炉作为冶炼铁水之主要原料。
还原气体,还原铁矿石,产生熔融铁水与熔渣之炼铁制程。
转炉生产流程:炼钢厂先将熔铣送前处理站作脱硫脱磷处理,经转炉吹炼后,再依订单钢种特性及品质需求,送二次精炼处理站(RH真空脱气处理站、Ladle Injection盛桶吹射处理站、VOD真空吹氧脱碳处理站、STN搅拌站等)进行各种处理,调整钢液成份,最后送大钢胚及扁钢胚连续铸造机,浇铸成红热钢胚半成品,经检验、研磨或烧除表面缺陷,或直接送下游轧制成条钢、线材、钢板、钢卷及钢片等成品。
钢的冶炼工艺流程

钢的冶炼工艺流程
《钢的冶炼工艺流程》
钢是一种重要的金属材料,广泛用于建筑、机械制造、船舶建造等领域。
它的生产需要经过一系列复杂的冶炼工艺流程。
首先,钢的生产原料主要包括铁矿石、焦炭和石灰石。
这些原料在高炉中被加热,其中焦炭将铁矿石还原成铁,石灰石则用来吸收硫和磷等杂质。
在高炉中产生的熔融铁水被称为生铁,含有较高的碳含量。
接下来,生铁被送入转炉或电炉中进行炼钢。
在转炉中,将生铁与废钢材料一起放入炉内,通入熔化的废钢液体。
通过吹氧和搅拌炉内气流,去除杂质和调整成分,最终得到符合要求的钢水。
在电炉中,生铁和废钢被放入炉内,并通过加热电极产生电弧,使废钢和铁水熔化。
然后通过氧气吹混、搅拌、加入合金等操作,进行精炼和合金化,最终获得所需的钢水。
最后,钢水被浇铸成各种形状的钢锭或钢坯,然后经过轧制、锻造、拉拔等加工工艺,得到符合不同需要的钢材产品。
总的来说,钢的冶炼工艺流程经历了高炉炼铁和转炉或电炉炼钢两个阶段,包括原料处理、熔炼、精炼和成形等多个环节。
这些工艺流程的优化和改进,对于提高钢的质量和生产效率具有重要意义。
钢的炼制过程

钢的炼制过程大致可分为以下几个步骤:
第一步是准备原料,主要是铁水,这是炼钢的核心原料。
然后需要将铁水进行脱磷、脱硫操作,这是因为这能更有效降低有害杂质,有利于下一步的纯净之炼。
第二步是向铁水中加入各种元素,使其成为钢或铁。
具体的加入元素种类和数量取决于所要炼制的钢的类型。
例如,如果要炼制低碳钢,那么就要加入一定量的硅、钙、铝等元素;如果要炼制高碳钢,那么这些元素则不必加入或者需要少加。
第三步是利用氧枪进行喷吹氧化剂,使其与铁水进行氧化反应,进一步净化了钢水,并且使钢水的温度提升。
这一步的关键在于控制好喷吹量,过少过多都会对炼钢结果产生不良影响。
第四步则是将温度合适、成分合格的钢水浇铸到钢锭模具中。
至此,钢的炼制过程基本结束,接下来就是等待钢水完全凝固。
钢的炼制不仅需要技术的支持,还需要严谨的操作流程和严格的质量控制。
每一个环节都至关重要,任何一个环节出现问题都可能导致整个过程的失败。
因此,炼钢行业是一个对细节和经验要求极高的行业。
总的来说,钢的炼制过程是一个复杂而又精密的过程。
它需要熟练的技术、严格的操作流程和质量控制,以及对市场需求的深刻理解。
只有这样,我们才能成功地炼制出高质量的钢产品,满足社会和经济发展的需要。
此外,随着科技的发展,现代炼钢行业也引入了许多新的技术和设备,如计算机控制技术、氧枪等离子喷吹技术等,进一步提高了炼钢的效率和精度。
但无论如何,炼钢的核心原理都没有改变:通过控制化学反应和杂质含量,将原材料转化为符合要求的钢或铁产品。
炼钢生产流程详解.doc

钢铁生产工艺主要包括:炼铁、炼钢、轧钢等流程。
(1)炼铁:就是把烧结矿和块矿中的铁还原出来的过程。
焦炭、烧结矿、块矿连同少量的石灰石、一起送入高炉中冶炼成液态生铁(铁水),然后送往炼钢厂作为炼钢的原料。
(2)炼钢:是把原料(铁水和废钢等)里过多的碳及硫、磷等杂质去掉并加入适量的合金成分。
(3)连铸:将钢水经中间罐连续注入用水冷却的结晶器里,凝成坯壳后,从结晶器以稳定的速度拉出,再经喷水冷却,待全部凝固后,切成指定长度的连铸坯。
(4)轧钢:连铸出来的钢锭和连铸坯以热轧方式在不同的轧钢机轧制成各类钢材,形成产品。
炼钢工艺总流程图炼焦生产流程:炼焦作业是将焦煤经混合,破碎后加入炼焦炉内经干馏后产生热焦碳及粗焦炉气之制程。
烧结生产流程:烧结作业系将粉铁矿,各类助熔剂及细焦炭经由混拌、造粒后,经由布料系统加入烧结机,由点火炉点燃细焦炭,经由抽气风车抽风完成烧结反应,高热之烧结矿经破碎冷却、筛选后,送往高炉作为冶炼铁水之主要原料。
高炉生产流程:高炉作业是将铁矿石、焦炭及助熔剂由高炉顶部加入炉内,再由炉下部鼓风嘴鼓入高温热风,产生还原气体,还原铁矿石,产生熔融铁水与熔渣之炼铁制程。
转炉生产流程:炼钢厂先将熔铣送前处理站作脱硫脱磷处理,经转炉吹炼后,再依订单钢种特性及品质需求,送二次精炼处理站(RH真空脱气处理站、Ladle Injection盛桶吹射处理站、VOD真空吹氧脱碳处理站、STN搅拌站等)进行各种处理,调整钢液成份,最后送大钢胚及扁钢胚连续铸造机,浇铸成红热钢胚半成品,经检验、研磨或烧除表面缺陷,或直接送下游轧制成条钢、线材、钢板、钢卷及钢片等成品。
连铸生产流程:连续铸造作业乃是将钢液转变成钢胚之过程。
上游处理完成之钢液,以盛钢桶运送到转台,经由钢液分配器分成数股,分别注入特定形状之铸模内,开始冷却凝固成形,生成外为凝固壳、内为钢液之铸胚,接着铸胚被引拔到弧状铸道中,经二次冷却继续凝固到完全凝固。
经矫直后再依订单长度切割成块,方块形即为大钢胚,板状形即为扁钢胚。
炼钢厂工艺流程

炼钢厂工艺流程
《炼钢厂工艺流程》
炼钢是一项复杂的工艺,通过各种操作和工序将生铁转化为高质量的钢铁。
炼钢厂工艺流程包括了多个步骤,每一个步骤都非常重要,需要严格控制和操作。
首先,生铁将会被装载到高炉中进行初步冶炼。
在这个阶段,矿石和焦炭会被加入到高炉中,经过高温的燃烧和还原,将生铁的矿石中的杂质转化为炼铁。
随后,炼铁会被送入转炉或电炉中进行精炼,其中杂质将被进一步去除,从而得到高品质的炼钢。
在转炉或电炉中,炼钢师会加入适量的废钢、锰、铬等合金元素,以调整钢铁的化学成分,以满足特定的用途和要求。
随后,炼钢师会通过吹氧和搅拌钢液的方式,控制炉温和杂质的去除,从而得到所需品质的炼钢。
最后,炼钢会被倒入浇注包或连铸机中,进行成形和冷却,得到半成品或成品钢材。
在整个流程中,需要精密的控制和操作,以确保炼钢的质量和性能。
总的来说,《炼钢厂工艺流程》是一个对工艺和操作要求非常严格的工艺,需要炼钢师有着丰富的经验和技术,才能确保生产出高质量的钢材。
炼钢的工艺流程

炼钢的工艺流程
《炼钢的工艺流程》
炼钢是将铁矿石转化为可用于制造工业产品的钢材的过程。
它经历了多个重要的工艺流程,包括炼铁、炼钢和后续的精炼和成型过程。
铁矿石首先需要经过炼铁的过程,这包括将铁矿石和焦炭放入高炉中进行冶炼。
在高炉中,化学反应发生将铁矿石还原成纯铁,同时还生成一些炼铁渣。
然后得到的炼铁需要进行炼钢的过程,这通常是通过转炉、电弧炉或其他炼钢炉来完成的。
在这一步骤中,炼铁被继续冶炼,以去除杂质并调整其成分和温度,最终得到所需的钢材。
在炼钢过程中,还需要进行一些精炼的工艺,例如真空脱气、氩气吹炼和连铸等,以确保所生产的钢材质量符合要求。
最后,成型过程中,钢材还需要经过轧制、锻造、淬火等工艺步骤,最终得到各种规格和形状的钢材产品。
整个炼钢的工艺流程包括了多个关键步骤,需要有高度的自动化和精准的控制,同时也需要对工艺参数和原材料进行全面的分析和调整。
只有如此,才能生产出优质的钢材,满足各种工业生产的需求。
炼钢简单工艺流程
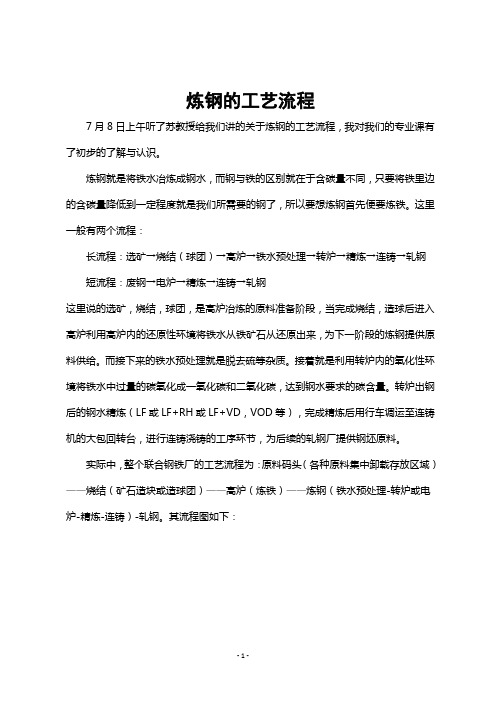
炼钢的工艺流程7月8日上午听了苏教授给我们讲的关于炼钢的工艺流程,我对我们的专业课有了初步的了解与认识。
炼钢就是将铁水冶炼成钢水,而钢与铁的区别就在于含碳量不同,只要将铁里边的含碳量降低到一定程度就是我们所需要的钢了,所以要想炼钢首先便要炼铁。
这里一般有两个流程:长流程:选矿→烧结(球团)→高炉→铁水预处理→转炉→精炼→连铸→轧钢短流程:废钢→电炉→精炼→连铸→轧钢这里说的选矿,烧结,球团,是高炉冶炼的原料准备阶段,当完成烧结,造球后进入高炉利用高炉内的还原性环境将铁水从铁矿石从还原出来,为下一阶段的炼钢提供原料供给。
而接下来的铁水预处理就是脱去硫等杂质。
接着就是利用转炉内的氧化性环境将铁水中过量的碳氧化成一氧化碳和二氧化碳,达到钢水要求的碳含量。
转炉出钢后的钢水精炼(LF或LF+RH或LF+VD,VOD等),完成精炼后用行车调运至连铸机的大包回转台,进行连铸浇铸的工序环节,为后续的轧钢厂提供钢坯原料。
实际中,整个联合钢铁厂的工艺流程为:原料码头(各种原料集中卸载存放区域)——烧结(矿石造块或造球团)——高炉(炼铁)——炼钢(铁水预处理-转炉或电炉-精炼-连铸)-轧钢。
其流程图如下:现在普遍使用的是转炉炼钢法,这种炼钢法使用的氧化剂是氧气。
把空气鼓入熔融的生铁里,使杂质硅、锰等氧化。
在氧化的过程中放出大量的热量(含1%的硅可使生铁的温度升高200摄氏度),可使炉内达到足够高的温度。
因此转炉炼钢不需要另外使用燃料。
转炉炼钢是在转炉里进行。
转炉的外形就像个梨,内壁有耐火砖,炉侧有许多小孔(风口),压缩空气从这些小孔里吹炉内,又叫做侧吹转炉。
开始时,转炉处于水平,向内注入1300摄氏度的液态生铁,并加入一定量的生石灰,然后鼓入空气并转动转炉使它直立起来。
这时液态生铁表面剧烈的反应,使铁、硅、锰氧化(FeO,SiO2 , MnO,) 生成炉渣,利用熔化的钢铁和炉渣的对流作用,使反应遍及整个炉内。
几分钟后,当钢液中只剩下少量的硅与锰时,碳开始氧化,生成一氧化碳(放热)使钢液剧烈沸腾。
炼钢工艺及流程

炼钢工艺及流程炼铁过程实质上是将铁从其自然形态——矿石等含铁化合物中还原出来的过程。
炼铁方法主要有高炉法、直接还原法、熔融还原法等,其原理是矿石在特定的气氛中(还原物质CO、H2、C;适宜温度等)通过物化反应获取还原后的生铁。
生铁除了少部分用于铸造外,绝大部分是作为炼钢原料。
1、高炉炼铁的冶炼原理(应用最多的)1)高炉冶炼用的原料主要由铁矿石、燃料(焦炭)和熔剂(石灰石)三部分组成。
通常,冶炼1吨生铁需要1.5-2.0吨铁矿石,0.4-0.6吨焦炭,0.2-0.4吨熔剂,总计需要2-3吨原料。
为了保证高炉生产的连续性,要求有足够数量的原料供应。
2)工艺流程生铁的冶炼虽原理相同,但由于方法不同、冶炼设备不同,所以工艺流程也不同。
下面分别简单予以介绍。
高炉生产是连续进行的。
一代高炉(从开炉到大修停炉为一代)能连续生产几年到十几年。
生产时,从炉顶(一般炉顶是由料种与料斗组成,现代化高炉是钟阀炉顶和无料钟炉顶)不断地装入铁矿石、焦炭、熔剂,从高炉下部的风口吹进热风(1000~1300摄氏度),喷入油、煤或天然气等燃料。
装入高炉中的铁矿石,主要是铁和氧的化合物。
在高温下,焦炭中和喷吹物中的碳及碳燃烧生成的一氧化碳将铁矿石中的氧夺取出来,得到铁,这个过程叫做还原。
铁矿石通过还原反应炼出生铁,铁水从出铁口放出。
铁矿石中的脉石、焦炭及喷吹物中的灰分与加入炉内的石灰石等熔剂结合生成炉渣,从出铁口和出渣口分别排出。
煤气从炉顶导出,经除尘后,作为工业用煤气。
现代化高炉还可以利用炉顶的高压,用导出的部分煤气发电。
生铁是高炉产品(指高炉冶炼生铁),而高炉的产品不只是生铁,还有锰铁等,属于铁合金产品。
锰铁高炉不参加炼铁高炉各种指标的计算。
高炉炼铁过程中还产生副产品水渣、矿渣棉和高炉煤气等。
高炉炼铁的特点:规模大,不论是世界其它国家还是中国,高炉的容积在不断扩大,如我国宝钢高炉是4063立方米,日产生铁超过吨,炉渣4000多吨,日耗焦4000多吨。
炼钢的过程
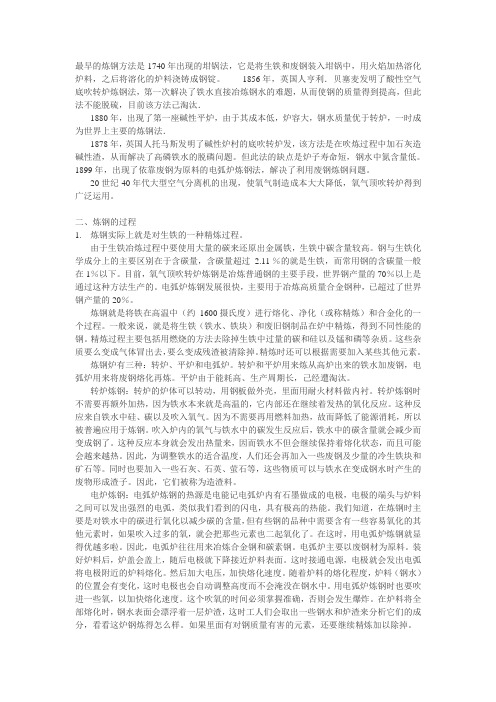
最早的炼钢方法是1740 年出现的坩锅法,它是将生铁和废钢装入坩锅中,用火焰加热溶化炉料,之后将溶化的炉料浇铸成钢锭。
1856 年,英国人亨利.贝塞麦发明了酸性空气底吹转炉炼钢法,第一次解决了铁水直接冶炼钢水的难题,从而使钢的质量得到提高,但此法不能脱硫,目前该方法己淘汰.1880 年,出现了第一座碱性平炉,由于其成本低,炉容大,钢水质量优于转炉,一时成为世界上主要的炼钢法.1878 年,英国人托马斯发明了碱性炉村的底吹转炉发,该方法是在吹炼过程中加石灰造碱性渣,从而解决了高磷铁水的脱磷问题。
但此法的缺点是炉子寿命短,钢水中氮含量低。
1899 年,出现了依靠废钢为原料的电弧炉炼钢法,解决了利用废钢炼钢问题。
20 世纪40 年代大型空气分离机的出现,使氧气制造成本大大降低,氧气顶吹转炉得到广泛运用。
二、炼钢的过程1.炼钢实际上就是对生铁的一种精炼过程。
由于生铁冶炼过程中要使用大量的碳来还原出金属铁,生铁中碳含量较高。
钢与生铁化学成分上的主要区别在于含碳量,含碳量超过 2.11 %的就是生铁,而常用钢的含碳量一般在1%以下。
目前,氧气顶吹转炉炼钢是冶炼普通钢的主要手段,世界钢产量的70%以上是通过这种方法生产的。
电弧炉炼钢发展很快,主要用于冶炼高质量合金钢种,已超过了世界钢产量的20%。
炼钢就是将铁在高温中(约1600 摄氏度)进行熔化、净化(或称精炼)和合金化的一个过程。
一般来说,就是将生铁(铁水、铁块)和废旧钢制品在炉中精炼,得到不同性能的钢。
精炼过程主要包括用燃烧的方法去除掉生铁中过量的碳和硅以及锰和磷等杂质。
这些杂质要么变成气体冒出去,要么变成残渣被清除掉。
精炼时还可以根据需要加入某些其他元素。
炼钢炉有三种:转炉、平炉和电弧炉。
转炉和平炉用来炼从高炉出来的铁水加废钢,电弧炉用来将废钢熔化再炼。
平炉由于能耗高、生产周期长,己经遭淘汰。
转炉炼钢:转炉的炉体可以转动,用钢板做外壳,里面用耐火材料做内衬。
炼钢的工艺流程:

炼钢的工艺流程:一、加料加料 :向电炉或转炉内加入铁水或废钢等原材料的操作,是炼钢操作的第一步。
二、造渣造渣 :调整钢、铁生产中熔渣成分、碱度和粘度及其反应能力的操作。
目的是通过钢铁高炉钢铁高炉渣-- 金属反应炼出具有所要求成分和温度的金属。
例如氧气顶吹转炉造渣和吹氧操作是为了生成有足够流动性和碱度的熔渣,能够向金属液面中传递足够的氧,以便把硫、磷降到计划钢种的上限以下,并使吹氧时喷溅和溢渣的量减至最小。
三、出渣出渣 :电弧炉炼钢时根据不同冶炼条件和目的在冶炼过程中所采取的放渣或扒渣操作。
如用单渣法冶炼时,氧化末期须扒氧化渣 ;用双渣法造还原渣时,原来的氧化渣必须彻底放出,以防回磷等。
四、熔池搅拌熔池搅拌 :向金属熔池供应能量,使金属液和熔渣产生运动,以改善冶金反应的动力学条件。
熔池搅拌可藉助于气体、机械电磁感应等方法来实现。
五、脱磷减少钢液中含磷量的化学反应。
磷是钢中有害杂质之一。
含磷较多的钢,在室温或更低的温度下使用时,容易脆裂,称为 "冷脆 "。
钢中含碳越高,磷引起的脆性越严重。
一般普通钢中规定含磷量不超过0.045% ,优质钢要求含磷更少。
生铁中的磷,主要来自铁矿石中的磷酸盐。
氧化磷和氧化铁的热力学稳定性相近。
在高炉的还原条件下,炉料中的磷几乎全部被还原并溶入铁水。
如选矿不能除去磷的化合物,脱磷就只能在 (高 )炉外或碱性炼钢炉中进行。
铁中脱磷问题的认识和解决,在钢铁生产发展史上具有特殊的重要意义。
钢的大规模工业生产开始于 1856 年贝塞麦发明的酸性转炉炼钢法。
但酸性转炉炼钢不能脱磷 ;而含磷低的铁矿石又很少,严重地阻碍了钢生产的发展。
1879 年托马斯发明了能处理高磷铁水的碱性法炉炼钢法,碱性炉渣的脱磷原理接着被推广到平炉炼钢中去,使大量含磷得以用于生产钢铁,对现代钢铁工业的发展作出了重大的贡献六、电炉底吹电炉底吹 :通过置于炉底的喷嘴将 N2 、Ar 、 CO2 、 CO 、CH4 、O2 等气体根据工艺要求吹入炉内熔池以达到加速熔化,促进冶金反应过程的目的。
- 1、下载文档前请自行甄别文档内容的完整性,平台不提供额外的编辑、内容补充、找答案等附加服务。
- 2、"仅部分预览"的文档,不可在线预览部分如存在完整性等问题,可反馈申请退款(可完整预览的文档不适用该条件!)。
- 3、如文档侵犯您的权益,请联系客服反馈,我们会尽快为您处理(人工客服工作时间:9:00-18:30)。
技术特点:
1.采用“全量”铁水(即100%)预处理;
2、采用Mg复合脱硫剂在铁水包内实现高效脱硫预处理;
3、采用O2脱硅,提高铁水温度;
4、采用转炉实现铁水脱磷和脱硅、脱硫;
炼钢工艺流程 及炼钢用合金辅料知识
技术研究
1
一、简介
矿山 煤矿
烧结厂、球团厂 焦化厂
烧结矿、球团矿 高炉 铁水 焦炭
1.铁水 铁水预处理 转炉炼钢 钢水精炼 连铸 连铸坯
2.废钢+铁水 电弧炉 钢水精炼
连铸
连铸坯
方坯 板坯 圆坯
轧机
棒材、线材、型材 平板、厚板、薄板
无缝钢管
技术研究
2
炼钢简述
1.首先在矿山要对铁矿石和煤炭进行采选,将精炼焦煤 和品位达到要求的铁矿石,通过陆路或水运送到钢铁企业的 原料厂进行配煤或配矿、混匀、再分别在焦化厂和烧结厂炼 焦和烧结,获得符合高炉炼铁质量要求的焦炭和烧结矿。
炼钢任务:①脱碳,②脱磷,③脱硫,④升温,⑤脱氧,⑥合金化,⑦去 除[N]、[H]等气体杂质元素,⑧去除非金属夹杂⑨凝固成型。 其中的脱硫、磷、碳、氧等就需要相应的脱硫剂、脱氧剂等冶金辅料。
技术研究
12
合金化:一方面加入合金(像我们的硅铝铁、硅铝钡等)作为脱
氧剂使用,其中的铝、钡等金属元素与氧发生反应,达到脱氧的目的。 另一方面加入合金可改善钢的某些性能成为合金化。
10
3.炼钢
(1)铁水预处理: 铁水预处理主要是预脱硫。通常高炉铁水含硫在0.03%-0.07%,而钢水的硫
含量一般小于0.025%,有些钢种的硫要求控制在0.005%以下。铁水预处理的任务 就是将铁水进转炉前的硫含量降低到0.005%-0.010%,以减轻炼钢脱硫负担。钢厂 目前主要采用喷吹钝化石灰和钝化镁粉脱硫工艺。
技术研究
9
(5)脱硫:
高炉中的硫主要来自其原燃料,如矿石、烧结矿、球团 矿、焦炭和喷吹燃料等。通常硫以硫化物和硫酸盐形式存在。 硫的热脆和冷脆性对于炼钢的危害是很大的,因此炼铁必须 脱硫。
硫在铁中以FeS的形式存在 FeS+CaO=FeO+CaS(渣) CaO就是石灰石,是一种良好的脱硫剂。
技术研究
2.高炉是炼铁的主要设备,使用的原料有铁矿石(包括 烧结矿、球团矿和块矿)、铁水送炼钢厂炼钢; 高炉煤气主 要用来烧热风炉,同时供炼钢厂和轧钢厂使用;高炉渣经水 淬后送水泥厂生产水泥。
技术研究
3
炼钢简述
3.炼钢,目前主要有两条工艺路线,即转炉炼钢工艺流 程和电弧炉炼钢流程。通常将“高炉——铁水预处理——转 炉——精炼——连铸”称为长流程,而将“废钢——电弧 炉——精炼——连铸”称为短流程。
(3)主要化学反应: Fe2O3+3CO=2Fe+3CO2 Fe3O4+4CO=3Fe+4CO2 2Fe2O3+3C=4Fe+3CO2
技术研究
8
(4)造渣:
炉炼铁过程中,熔剂同矿石的脉石和焦炭的灰分相互作用,将不进入生铁 和煤气的物质溶解、汇集和熔化成液态炉渣的过程。矿石的脉石和焦炭的灰分多 系SiO2、Al2O3等酸性氧化物,它们的熔点都很高,分别为1723℃和2060℃, 不可能在高炉中熔化。由SiO2和化合物3 Al2O3·2 SiO2组成的共晶体,其熔化 温度仍然很高(约1545℃),在高炉中只能形成非常黏稠的物质,难于流动,造成 渣铁不分。这样,高炉冶炼就不能进行。为此需加入助熔物质——熔剂,如石灰 石(CaCO3)、白云石(CaCO3·MgCO3)等。尽管由石灰石、白云石分解生成的碱性 氧化物CaO、MgO自身的熔化温度也很高(CaO2570℃,MgO2800℃),但它们 与SiO2和Al2O3结合生成的低熔点(<1400℃)化合物在高炉内能充分熔化,形成 流动性良好的熔渣,并2.2~ 3.2g/cm)而与铁水分离,使高炉冶炼得以正常进行。
5、“三脱”铁水低氧冶炼技术。
技术研究
11
钢与生铁的区别: 元素 C Si Mn p s
(2)转炉吹炼
生铁货铸铁(%) 2.5-4.5 0.3-4.0 0.4-2.0 0.015-0.5 0.01-0.1
钢(%) 0.002-1.2 0.01-3.0 0.3-2.0 0.01-0.05 0.0005-0.04
4.炼钢厂的最终产品是连铸坯。按照形状,连铸坯分为 方坯、板坯和圆坯。在轧钢厂,方坯分别被棒材、线材和型 材轧机轧制成棒材、线材和型材;板坯被轧制成中厚板和薄 板;圆坯被穿孔、轧制成无缝钢管。
技术研究
4
技术研究
5
技术研究
6
二、详细介绍
1.铁前系统
(1)烧结厂 主要任务:将粉状铁矿石(包括富粉矿、精矿粉等)和钢铁厂二次含铁粉
技术研究
7
2.高炉炼铁
(1)主要任务:是用铁矿石和焦炭冶炼出合格的铁水供转炉炼钢,同时 产生大量高炉煤气供炼铁厂热风炉、烧结厂、炼钢厂、轧钢厂使用。
(2)过程:高炉生产时从炉顶装入铁矿石、焦炭、造渣用熔剂(石灰石), 从位于炉子下部沿炉周的风口吹入经预热的空气。在高温下焦炭(有的高炉也喷 吹煤粉、重油、天然气等辅助燃料)中的碳同鼓入空气中的氧燃烧生成的一氧化 碳和氢气,在炉内上升过程中除去铁矿石中的氧,从而还原得到铁。炼出的铁水 从铁口放出。铁矿石中不还原的杂质和石灰石等熔剂结合生成炉渣,从渣口排出。 产生的煤气从炉顶导出,经除尘后,作为热风炉、加热炉、焦炉、锅炉等的燃料。
尘,通过烧结机的烧结过程,加工成符合高炉要求的人造富块矿——烧结矿。在 烧结混合料中,通过调整加入的熔剂(如消石灰、石灰石、白云石等)和燃料 (焦粉、无烟煤粉)的数量,通过烧结可以控制烧结矿的化学成分(如碱度MgO 等)和冶金性能。通过烧结还能去除烧结原料中80%以上的硫。 (2)焦化厂
焦炭是高炉炼铁不可缺少的燃料和还原剂,生产设备为焦炉。焦炭生产过程 分为洗煤、配煤、炼焦、熄焦及煤气和化工产品回收处理等工序。炼焦的副产品 是高热值的高炉煤气及作为化工原料的焦油、粗苯等。
C:控制钢材强度、硬度的重要元素,每1%C可增加抗拉强度月980MPa。 Si:也是增大强度、硬度的重要元素,每1% Si可增加抗拉强度月 98MPa。 Mn(锰):增加淬透性,提高韧性,降低硫的危害等。 Al:细化钢材组织,控制冷轧钢板退火结构。 V(钒):细化钢材组织,增加强度、韧性。 Cr(铬):增加强度、韧性、耐腐蚀性能。