炼油厂生产工艺简介
燕山石化催化裂化炼油三厂工艺简介

燕山石化催化裂化炼油三厂工艺简介燕山石化催化裂化炼油三厂工艺简介燕山石化催化裂化炼油三厂是位于河北省秦皇岛市临港经济开发区的重要工业设施,是中国石化(集团)公司旗下的一座重要炼油厂。
该工厂始建于1996年,投资建设了世界一流的炼油设备和工艺流程,具有年产1000万吨炼油能力,主要生产汽油、柴油、航空煤油和液化石油气等产品。
催化裂化炼油是一种重要的炼油工艺,通过在高温和高压条件下将重质原油分解成低碳烃烷烃和高碳烷烃的过程,以提高汽油和柴油的产量。
燕山石化催化裂化炼油三厂采用的是流化催化裂化工艺,该工艺具有操作灵活、产品质量好、能耗低等特点。
在催化裂化炼油工艺中,原油首先通过预热器加热至适宜的温度,然后进入主要反应器,加入催化剂进行裂化反应。
在主要反应器中,原油与催化剂在高温(约500℃)和高压(约2-7MPa)的条件下进行接触和反应,重质油分子裂解成轻质油分子。
催化剂起着催化作用,可以降低反应温度和反应压力,并提高裂解产物的选择性。
裂解反应后的产物经过分离器进行初步分离,分离产物包括石脑油、汽油、柴油、煤油和尾气。
其中,石脑油主要用于生产溶剂、涂料和胶粘剂等化工产品,具有重要的经济价值。
汽油、柴油和煤油则是燃料油品,广泛应用于交通运输、工业生产和民用供暖等领域。
尾气中含有大量可燃气体,可以通过处理后转化为燃料气或再生燃气。
为了提高产品质量,燕山石化催化裂化炼油三厂还引入了后处理装置。
后处理装置主要包括脱硫装置、脱氮装置和脱碳装置等,通过这些装置可以有效去除燃料中的硫、氮和杂质,提高产品的清洁度和环保性能。
除了催化裂化炼油工艺,燕山石化催化裂化炼油三厂还配备了其他辅助工艺和设施,如蒸汽供应系统、电力供应系统、废水处理系统和废气处理系统等,这些系统和设施保证了工厂的正常运行和产品的质量安全。
目前,燕山石化催化裂化炼油三厂在国内外市场上具有很高的知名度和竞争力,其产品远销世界各地。
同时,该工厂也积极推动绿色环保炼油技术的研发和应用,在提高产品质量的同时,也注重对环境的保护。
石油炼化七种常用工艺流程

石油炼化七种常用工艺流程石油炼化是将原油中的各种组分分离和转化为更有价值的产品的过程。
石油炼化工艺是指在炼油厂中使用的一系列技术和过程,目的是将原油转变成可用的燃料和化学品。
下面将介绍石油炼化常用的七种工艺流程。
1. 原油蒸馏(Distillation):原油蒸馏是最基本和最重要的炼油工艺之一、原油在高温下在蒸馏塔中进行加热,不同组分的沸点不同,通过升温和冷凝,将原油分离成多个不同沸点范围的馏分,如汽油、柴油和石油沥青等。
2. 裂化(Cracking):裂化是将分子较大的重油转变成分子较小的轻质石油产品的工艺。
裂化工艺有热裂化和催化裂化两种。
热裂化是通过高温将重油分解成低沸点的产品,而催化裂化是在催化剂的作用下,通过低温和高压条件下将重油分解成较小分子的烃化合物。
3. 水洗(Washing):水洗是一种除去原油中的杂质和硫化物的工艺,可以提高石油产品的质量和纯度。
原油经过水和碱溶液的混合后,可将其中的杂质和硫化物转化成可溶性化合物,以达到净化的目的。
4. 精制(Refining):精制是一种用于提纯石油产品的工艺。
通过溶剂萃取、凝固、脱硫、脱气等步骤,去除原油中的杂质和污染物,并提高石油产品的品质。
5. 混合(Blending):混合是将不同种类的石油产品按照一定比例进行混合的工艺。
混合可以根据市场需求来调整产品的特性,使得石油产品符合市场的要求。
6. 气化(Gasification):气化是一种将煤、重油、焦炭等固体燃料转化为气态燃料(如合成气、水煤气)的工艺。
气化可以通过高温和高压条件下,使固体燃料与氧气或水蒸汽反应,生成可燃性气体。
7. 润滑油生产(Lubricant production):润滑油生产是将原油中的润滑性较好的组分提取出来,并经过脱酸、脱硫等工艺处理后,制成润滑油产品。
润滑油产品广泛应用于机械、汽车等领域,起到减少摩擦和磨损的作用。
以上是七种常用的石油炼化工艺流程,它们在炼油厂中发挥着重要的作用,为我们提供了各种石油产品。
棕榈油炼油厂工艺

棕榈油炼油厂工艺
棕榈油是一种常用的食用油,其生产过程需要经过多个步骤进行加工。
以下是棕榈油炼油厂的工艺流程:
1. 清洗和筛选:将新鲜的棕榈果农村码头集中后,进行清洗处理,去
除表皮、污泥、石头等杂质,使其更纯净。
2. 烘干:清洗好的棕榈果经过烘干,去除水分,方便后续的压榨和加工。
3. 压榨:将烘干后的棕榈果压榨出油。
该过程分为初榨和二榨。
初榨
萃取出来的油较浓厚、成份复杂,需要进行二次榨取,以便得到纯度
更高的油。
4. 分离:将压榨得到的混合油通过离心机进行分离。
其中,较轻的清
香油会积聚在上部,而较重的油脂则会沉淀在下部。
5. 氢化:在一定的条件下,将清香油和沉淀油脂进行氢化反应,以使
其转化为更加稠密、富含油脂的食用油。
6. 脱色:经过一系列的过滤、冷却等处理,去除油中的色素和杂质,
得到无色、清澈的棕榈油。
7. 去异味:去除棕榈油中的异味成分,并通过调整其酸、碱度等参数,
使得油品更加符合国家标准。
8. 包装:对处理好的棕榈油进行包装,提高其销售的便利性和稳定性。
通过以上的工艺流程,我们能够得到高质量、纯净的棕榈油,为我们
生活中的烹饪、食用提供了保障。
炼油厂工艺流程
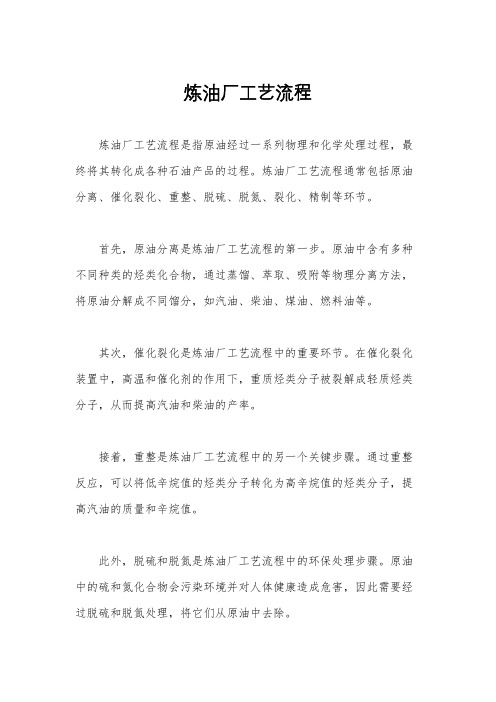
炼油厂工艺流程
炼油厂工艺流程是指原油经过一系列物理和化学处理过程,最终将其转化成各种石油产品的过程。
炼油厂工艺流程通常包括原油分离、催化裂化、重整、脱硫、脱氮、裂化、精制等环节。
首先,原油分离是炼油厂工艺流程的第一步。
原油中含有多种不同种类的烃类化合物,通过蒸馏、萃取、吸附等物理分离方法,将原油分解成不同馏分,如汽油、柴油、煤油、燃料油等。
其次,催化裂化是炼油厂工艺流程中的重要环节。
在催化裂化装置中,高温和催化剂的作用下,重质烃类分子被裂解成轻质烃类分子,从而提高汽油和柴油的产率。
接着,重整是炼油厂工艺流程中的另一个关键步骤。
通过重整反应,可以将低辛烷值的烃类分子转化为高辛烷值的烃类分子,提高汽油的质量和辛烷值。
此外,脱硫和脱氮是炼油厂工艺流程中的环保处理步骤。
原油中的硫和氮化合物会污染环境并对人体健康造成危害,因此需要经过脱硫和脱氮处理,将它们从原油中去除。
裂化是炼油厂工艺流程中用于生产乙烯和丙烯等烯烃产品的重
要工艺。
通过高温和催化剂的作用,将重质烃类分子裂解成轻质烯
烃产品。
最后,精制是炼油厂工艺流程中的最后一步。
通过精制工艺,
可以将各种馏分中的杂质去除,提高产品的纯度和质量,满足不同
产品的要求。
总的来说,炼油厂工艺流程是一个复杂而又精密的系统工程,
其中涉及了多种物理和化学过程。
通过不断的技术创新和工艺优化,炼油厂工艺流程可以实现高效、低能耗、高产率、高质量的生产,
为社会各行业提供了丰富的石油产品。
炼油厂的构成和石油炼制流程工艺简介课件
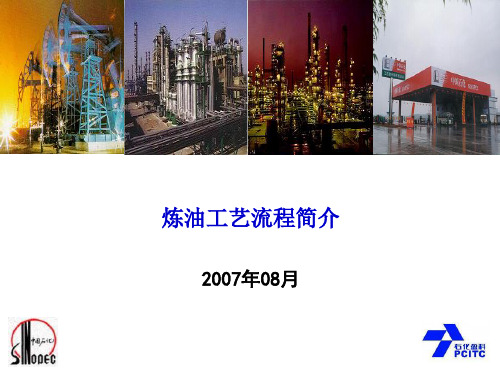
石油产品简介
石油产品根据生产方法和最终用途可分为燃料、溶剂 和化工原料、润滑剂和有关产品、蜡、沥青、石油焦 等几大类。这里简要介绍石油产品中的燃料类。
6
液化石油气简介
石油炼制过程中产生的石油气的统称,在常温下,加压就 容易液化,主要成分为丙烷、丙烯、丁烷、丁烯、少量戊 烷、戊烯和微量硫化物。炼油-化工型炼厂中生产的液化 气不含丙烯、丁烯。
9
煤油简介
煤油旧称灯油,因为煤油一开始主要用于照明。煤油按质 量分为优质品、一级品和合格品三个等级,主要用于点灯 照明、各种喷灯、汽灯、汽化炉和煤油炉等的燃料;也可 用作机械零部件的洗涤剂、橡胶和制药工业溶剂、油墨稀 释剂、有机化工裂解原料;玻璃陶瓷工业、铝板辗轧、金 属表面化学热处理等工艺用油。航空煤油则主要用作喷气 式发动机燃料,目前大型客机均使用航空煤油。航空煤油 分为1 号、2 号、3 号三个等级,只有3 号航空煤油被广 泛使用。
5、You have to believe in yourself. That's the secret of success. ----Charles Chaplin人必须相信自己,这是成功的秘诀。-Thursday, June 17, 2021June 21Thursday, June 17, 20216/17/2021
13
常减压装置工艺流程简图
14
常减压装置工艺简介
首先将原油换热至90~130℃加入精制水和破乳剂,经混合后进入电脱 盐脱水器,在高压交流电场作用下使混悬在原油中的微小液滴逐步扩 大成较大液滴,借助重力合并成水层,将水及溶解在水中的盐、杂质 等脱除。经脱盐脱水后的原油换热至220~250℃,进入初馏塔,塔顶 拔出轻汽油,塔底拔顶原油经换热和常压炉加热到360~370℃进入常 压分馏塔,分出汽油、煤油、轻柴油、重柴油馏分,经电化学精制后 作成品出厂。常压塔底重油经减压炉加热至380~400℃进入减压分馏 塔,在残压为2~8kPa下,分馏出各种减压馏分,作催化或润滑油原料 。减压渣油经换热冷却后作燃料油或经换热后作焦化、催化裂化,氧 化沥青原料。
石油炼制过程和主要工艺简介

石油炼制的主要过程和工艺简介石油、天然气是不同烃化合物的混合物,简单作为燃料是极大的浪费,只有通过加工处理,炼制出不同的产品,才能充分发挥其巨大的经济价值。
石油经过加工,大体可获得以下几大类的产品:汽油类(航空汽油、军用汽油、溶剂汽油);煤油(灯用煤油、动力煤油、航空煤油);柴油(轻柴油、中柴油、重柴油);燃料油;润滑油;润滑油脂以及其他石油产品(凡士林、石油蜡、沥青、石油焦炭等)。
有的油品经过深加工,又获得质量更高或新的产品。
石油加工,主要是指对原油的加工。
世界各国基本上都是通过一次加工、二次加工以生产燃料油品,三次加工主要生产化工产品。
原油在炼厂加工前,还需经过脱盐、脱水的预处理,使之进入蒸馏装置时,其各种盐类的总含盐量低于5mg/L,主要控制其对加工设备、管线的腐蚀和堵塞。
原油一次加工,主要采用常压、减压蒸馏的简单物理方法将原油切割为沸点范围不同、密度大小不同的多种石油馏分。
各种馏分的分离顺序主要取决于分子大小和沸点高低。
在常压蒸馏过程中,汽油的分子小、沸点低(50~200℃),首先馏出,随之是煤油(60~5℃)、柴油(200~0℃)、残余重油。
重油经减压蒸馏又可获得一定数量的润滑油的基础油或半成品(蜡油),最后剩下渣油(重油)。
一次加工获得的轻质油品(汽油、煤油、柴油)还需进一步精制、调配,才可做为合格油品投入市场。
我国一次加工原油,只获得25%~40%的直馏轻质油品和20%左右的蜡油。
原油二次加工,主要用化学方法或化学-物理方法,将原油馏分进一步加工转化,以提高某种产品收率,增加产品品种,提高产品质量。
进行二次加工的工艺很多,要根据油品性质和设计要求进行选择。
主要有催化裂化、催化重整、焦化、减粘、加氢裂化、溶剂脱沥青等。
如对一次加工获得的重质半成品(蜡油)进行催化裂化,又可将蜡油的40%左右转化为高牌号车用汽油,30%左右转化为柴油,20%左右转化为液化气、气态烃和干气。
如以轻汽油(石脑油)为原料,采用催化重整工艺加工,可生产高辛烷值汽油组分(航空汽油)或化工原料芳烃(苯、二甲苯等),还可获得副产品氢气。
炼油行业的加工工艺包括

炼油行业的加工工艺包括
炼油行业的加工工艺主要包括以下几个步骤:
1. 原油采集和储存:原油是炼油的原料,炼油厂需要从油田或海上采集原油,并进行初步的储存和净化处理。
2. 原油预处理:原油中含有杂质、硫化物、水等成分,需要经过预处理操作,例如脱水、脱盐、脱硫等操作,以净化原油。
3. 分馏:原油经过预处理后,通过分馏塔进行分馏,将原油按照不同的沸点和分子量分成不同的馏分,例如汽油、柴油、煤油、残油等。
4. 裂化:裂化是通过加热和催化剂的作用,将高碳链烃分子断裂成低碳链烃分子的过程。
常见的裂化工艺有热裂化和催化裂化。
5. 加氢:加氢是将原油中的不饱和烃分子加入氢气,通过化学反应将其转化为饱和烃的过程。
加氢可以提高制品的品质和性能。
6. 脱硫:在加工过程中,原油中的硫化物会影响制品的品质和环境保护。
脱硫是将硫化物从原油中去除的过程,常见的脱硫工艺有氢气脱硫和吸收脱硫等。
7. 裂化重整:裂化重整是将轻质馏分中的低碳链烃分子与重质馏分中的高碳链
烃分子进行催化反应,以产生高辛烷值的汽油。
8. 焦化:焦化是将残油在高温下分解成焦炭和各种液体和气体产品的过程。
焦化可以产生焦炭、煤沥青、沥青等产品。
以上是炼油行业常见的加工工艺步骤,不同的炼油厂根据原油的性质和需求,可能会有所不同。
燕山石化 催化裂化 炼油三厂 工艺简介

1.概述说明:1.1.装置的地位和作用炼油厂重油催化裂化是在催化剂的作用下将重质油转化为汽油、柴油及液化气等产品的过程,是主要的加工工艺之一。
随着社会的不断发展和进步,能源危机日益成为人们注目的焦点,而催化裂化作为重油深度加工装置,日益显示出其重要作用,我国通过催化裂化工艺生产的汽油约占全国商品汽油的70%,柴油占全国总量的30%,液化气占炼油厂总量的90%以上。
根据中石化总公司’’八五科技进步规则”的精神和炼厂的”九五规划”,为充分利用石油资源,提高二次加工能力,改善产品结构,增加全厂轻质油收率,减少重油产品特拟建此套(200万吨/年)重油催化裂化装置。
本装置是全国最大的重油催化裂化装置之一。
1.2.装置的主要原料、产品和用途1.2.1.本装置所需主要原料为蒸馏装置的常三、常四、减二、减三、减四、减五线、减压渣油以及酮苯蜡膏、糠醛抽余油、和丙烷脱沥青油等。
1.2.2.本装置主要产品为:汽油,柴油,液化气,干气和重油(油浆)。
1.2.2.1.汽油是本装置生产的主要产品之一,其设计牌号为9l号,收率为47.2%。
汽油常用于汽油燃动机,是比较重要的一种动力能源,主要用于轻型汽车,活塞式发动机的飞机,快艇和小型发电机等。
1.2.2.2.柴油也是本装置的主要目标产品,其设计牌号为一10号和0号,收率通常为24.28%,根据季节变化和市场对柴油的使用要求,我们可以通过改变操作条件来生产所需要的目标产品。
柴油的用途相当广泛,主要用于大马力的运输机械,现已广泛用于载重汽车,拖拉机,曳引机,机车,船舶及各种农业,矿山,车用机械作为动力设备,其功率从几十马力到四万马力左右。
1.2.2.3.液化气也是本装置的重要产品,其设计收率为10.736%。
它通常用作民用燃料,但随着科学技术的日新月异,液化气的用途也有了新的变化,比如:由于世界环卫组织宣布氟利昂严重影响生态环境,造成臭氧层破坏,故研究氟利昂的替代产品显得尤其重要,而液化气正是理想的原材料之一。
炼油厂生产工艺简介

炼油厂生产工艺简介炼油厂生产工艺是指石油在炼油厂中经过一系列化学工艺和物理工艺处理,将原油转化为具有市场需求的石油产品的过程。
该过程通常包括原油预处理、石蜡分离、蒸馏、催化裂化、重整、重整和芳构化等工艺。
以下是炼油厂生产工艺的简要介绍:1. 原油预处理:原油进入炼油厂后,会被送入预处理装置,以去除杂质如水、盐、硫化物、砂粒等。
这些杂质会影响后续工艺的效果和设备的寿命。
2. 石蜡分离:原油中含有较高含量的石蜡,通过降温和过滤的方式将石蜡分离出来。
分离得到的石蜡可以用于制造蜡烛、油脂等产品。
3. 蒸馏:原油中的不同组分具有不同的沸点,通过蒸馏塔将原油进行加热和蒸发,然后冷凝成液体,提取出汽油、柴油、煤油等不同馏分。
蒸馏工艺的目的是根据产品需求和市场需求将原油分解成不同的产品。
4. 催化裂化:催化裂化是一种重要的工艺,通过将重质馏分在催化剂作用下进行裂化,将较长链的烃类分子裂解为短链的烃类分子。
这样可以增加汽油产量,提高汽油的辛烷值,提高产品的附加值。
5. 重整:重整工艺是通过在高温和高压下将馏分中的芳烃分子进行重新排列,以提高汽油的辛烷值和提高产品的抗爆性能。
6. 芳构化:芳构化是将低辛烷值的烷烃通过在特定温度和压力下与催化剂接触,使其转变为具有较高辛烷值的芳烃的工艺。
芳构化可以将较低品位的馏分转化为高附加值的芳烃产品,如苯、二甲苯等。
以上是炼油厂生产工艺的主要环节。
炼油厂依靠这些工艺将原油加工成多种石油产品,满足人们对各种能源和化工产品的需求。
同时,炼油厂还需要安全可靠地运行设备和系统,以确保生产工艺的顺利进行。
炼油厂生产工艺是一个复杂而精细的过程,其目标是最大限度地提取和生产市场需求的石油产品。
除了上述所提到的工艺,还有一些其他的工艺步骤,如氢气处理、脱硫、脱氮、脱氧等,这些步骤都对最终产品的质量和性能起着重要作用。
1. 氢气处理:氢气在炼油过程中扮演着重要的角色,它可以用来脱硫、脱氮和脱饱和。
炼油厂的炼油工艺流程介绍
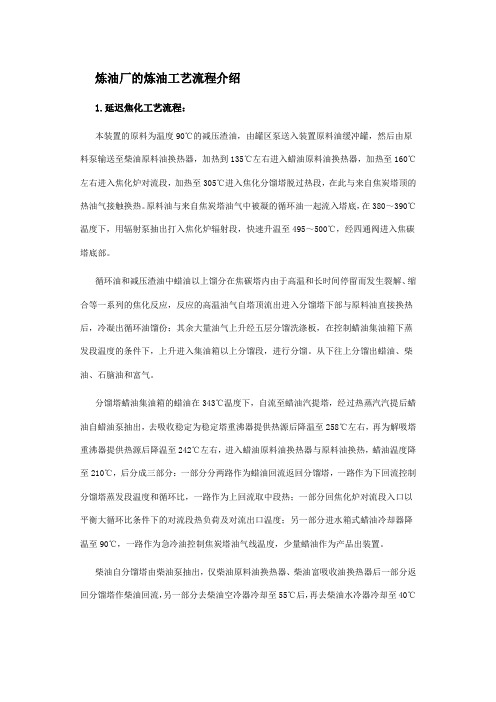
炼油厂的炼油工艺流程介绍1.延迟焦化工艺流程:本装置的原料为温度90℃的减压渣油,由罐区泵送入装置原料油缓冲罐,然后由原料泵输送至柴油原料油换热器,加热到135℃左右进入蜡油原料油换热器,加热至160℃左右进入焦化炉对流段,加热至305℃进入焦化分馏塔脱过热段,在此与来自焦炭塔顶的热油气接触换热。
原料油与来自焦炭塔油气中被凝的循环油一起流入塔底,在380~390℃温度下,用辐射泵抽出打入焦化炉辐射段,快速升温至495~500℃,经四通阀进入焦碳塔底部。
循环油和减压渣油中蜡油以上馏分在焦碳塔内由于高温和长时间停留而发生裂解、缩合等一系列的焦化反应,反应的高温油气自塔顶流出进入分馏塔下部与原料油直接换热后,冷凝出循环油馏份;其余大量油气上升经五层分馏洗涤板,在控制蜡油集油箱下蒸发段温度的条件下,上升进入集油箱以上分馏段,进行分馏。
从下往上分馏出蜡油、柴油、石脑油和富气。
分馏塔蜡油集油箱的蜡油在343℃温度下,自流至蜡油汽提塔,经过热蒸汽汽提后蜡油自蜡油泵抽出,去吸收稳定为稳定塔重沸器提供热源后降温至258℃左右,再为解吸塔重沸器提供热源后降温至242℃左右,进入蜡油原料油换热器与原料油换热,蜡油温度降至210℃,后分成三部分:一部分分两路作为蜡油回流返回分馏塔,一路作为下回流控制分馏塔蒸发段温度和循环比,一路作为上回流取中段热;一部分回焦化炉对流段入口以平衡大循环比条件下的对流段热负荷及对流出口温度;另一部分进水箱式蜡油冷却器降温至90℃,一路作为急冷油控制焦炭塔油气线温度,少量蜡油作为产品出装置。
柴油自分馏塔由柴油泵抽出,仅柴油原料油换热器、柴油富吸收油换热器后一部分返回分馏塔作柴油回流,另一部分去柴油空冷器冷却至55℃后,再去柴油水冷器冷却至40℃后分两路:一路出装置;另一路去吸收稳定单元的再吸收塔作吸收剂。
由吸收稳定单元返回的富吸收油经柴油富吸收油换热器换热后也返回分馏塔。
分馏塔顶油气经分馏塔顶空冷器,分馏塔顶水冷器冷却到40℃,流入分馏塔顶气液分离罐,焦化石脑油由石脑油泵抽出送往吸收稳定单元。
石化炼油厂的工艺流程
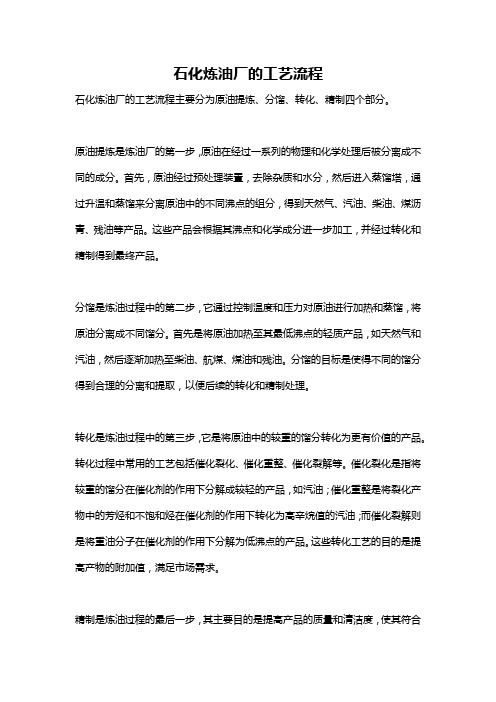
石化炼油厂的工艺流程石化炼油厂的工艺流程主要分为原油提炼、分馏、转化、精制四个部分。
原油提炼是炼油厂的第一步,原油在经过一系列的物理和化学处理后被分离成不同的成分。
首先,原油经过预处理装置,去除杂质和水分,然后进入蒸馏塔,通过升温和蒸馏来分离原油中的不同沸点的组分,得到天然气、汽油、柴油、煤沥青、残油等产品。
这些产品会根据其沸点和化学成分进一步加工,并经过转化和精制得到最终产品。
分馏是炼油过程中的第二步,它通过控制温度和压力对原油进行加热和蒸馏,将原油分离成不同馏分。
首先是将原油加热至其最低沸点的轻质产品,如天然气和汽油,然后逐渐加热至柴油、航煤、煤油和残油。
分馏的目标是使得不同的馏分得到合理的分离和提取,以便后续的转化和精制处理。
转化是炼油过程中的第三步,它是将原油中的较重的馏分转化为更有价值的产品。
转化过程中常用的工艺包括催化裂化、催化重整、催化裂解等。
催化裂化是指将较重的馏分在催化剂的作用下分解成较轻的产品,如汽油;催化重整是将裂化产物中的芳烃和不饱和烃在催化剂的作用下转化为高辛烷值的汽油;而催化裂解则是将重油分子在催化剂的作用下分解为低沸点的产品。
这些转化工艺的目的是提高产物的附加值,满足市场需求。
精制是炼油过程的最后一步,其主要目的是提高产品的质量和清洁度,使其符合市场和环保要求。
精制包括脱酸、脱硫、脱氮、脱氢等工艺。
脱酸是将产品中的酸性物质去掉,脱硫是去除产品中的硫化物,脱氮是去除产品中的氮化物,脱氢是去除产品中的不饱和烃。
这些工艺可以通过物理方法、化学方法或催化剂的作用来实现。
精制之后,产品的质量会得到显著提高,同时也符合环保的要求。
总的来说,石化炼油厂的工艺流程是一个复杂的系统工程,需要通过原油提炼、分馏、转化和精制四个主要步骤来实现对原油的加工和提炼。
每个步骤都需要精心设计和严格控制,以确保产品的质量和生产的安全。
同时,随着技术的不断进步和环保要求的提高,炼油工艺也在不断进行创新和改进,以适应市场的需求和环保的要求。
炼油厂工艺流程

炼油厂工艺流程
炼油厂是将原油转化为燃料和其他石化产品的工厂。
炼油工艺流程主要分为四个步骤:原油处理、提炼、裂解和后处理。
首先,在原油处理步骤中,原油经过脱水和去硫化处理,以去除其中的水和硫化物。
这是为了减少后续生产过程中的腐蚀问题和燃料中的污染物。
接下来,原油通过加热和蒸馏过程分离成不同的馏分。
这一步骤被称为提炼。
在提炼过程中,原油被加热至约400-600°C,从而将其分解为不同的馏分。
较轻的馏分,如天然气和汽油,在较低的温度下沸腾并被蒸馏出来。
而较重的馏分,如柴油和润滑油,在较高的温度下蒸发。
这种分离过程是基于不同组分的沸点差异。
接下来,较重的馏分进入裂解步骤。
裂解是一种将长链烃分子分解成短链烃分子的过程。
这一步骤通过加热和压力作用来进行,以产生更多的轻质烃类产品,如汽油和天然气。
裂解过程可以通过热裂解、催化裂解和加氢裂解等不同的方法来实现。
最后,经过裂解的产品进行后处理。
后处理的目的是去除其中的杂质和不纯物,以满足燃料和石化产品的质量标准。
这一步骤通常包括脱硫、脱氮和脱氧等处理过程,以减少燃料中的污染物。
总体而言,炼油厂工艺流程是一个复杂而精细的过程,需要仔细的控制和调整。
各个步骤的配合和优化对于最终产品的质量和产量都起着至关重要的作用。
另外,为了提高燃料的质量和
减少对环境的污染,炼油厂还需要进行不断的技术创新和工艺改进。
炼油厂的构成和石油炼制流程工艺简介
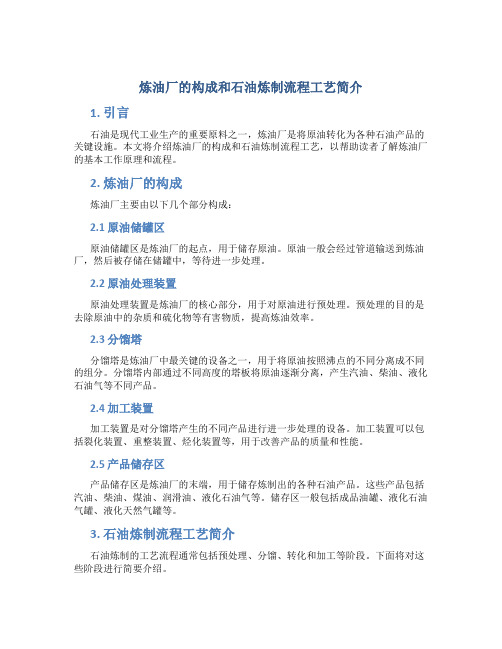
炼油厂的构成和石油炼制流程工艺简介1. 引言石油是现代工业生产的重要原料之一,炼油厂是将原油转化为各种石油产品的关键设施。
本文将介绍炼油厂的构成和石油炼制流程工艺,以帮助读者了解炼油厂的基本工作原理和流程。
2. 炼油厂的构成炼油厂主要由以下几个部分构成:2.1 原油储罐区原油储罐区是炼油厂的起点,用于储存原油。
原油一般会经过管道输送到炼油厂,然后被存储在储罐中,等待进一步处理。
2.2 原油处理装置原油处理装置是炼油厂的核心部分,用于对原油进行预处理。
预处理的目的是去除原油中的杂质和硫化物等有害物质,提高炼油效率。
2.3 分馏塔分馏塔是炼油厂中最关键的设备之一,用于将原油按照沸点的不同分离成不同的组分。
分馏塔内部通过不同高度的塔板将原油逐渐分离,产生汽油、柴油、液化石油气等不同产品。
2.4 加工装置加工装置是对分馏塔产生的不同产品进行进一步处理的设备。
加工装置可以包括裂化装置、重整装置、烃化装置等,用于改善产品的质量和性能。
2.5 产品储存区产品储存区是炼油厂的末端,用于储存炼制出的各种石油产品。
这些产品包括汽油、柴油、煤油、润滑油、液化石油气等。
储存区一般包括成品油罐、液化石油气罐、液化天然气罐等。
3. 石油炼制流程工艺简介石油炼制的工艺流程通常包括预处理、分馏、转化和加工等阶段。
下面将对这些阶段进行简要介绍。
3.1 预处理预处理是指对原油进行初步处理的过程。
预处理可以包括去除杂质、去除硫化物、调整原油性质等操作。
这些操作的目的是提高原油在后续处理过程中的效果和稳定性。
3.2 分馏分馏是将原油按照不同沸点分离成不同组分的过程。
分馏通常通过分馏塔进行,塔内设置不同高度的塔板,使得原油在不同高度处产生沸腾反应,从而分离出汽油、柴油、液化石油气等产品。
3.3 转化转化是指将分馏得到的较重油转化为较轻油的过程。
转化通常包括裂化、重整、烃化等操作。
裂化可以将重油分解成较轻的烃类化合物,重整可以通过催化剂将低质量的将烃类化合物转化为高质量的烃类化合物,烃化则是将烃类化合物转化为其他化合物。
某石化公司炼油厂物料平衡及生产流程简介
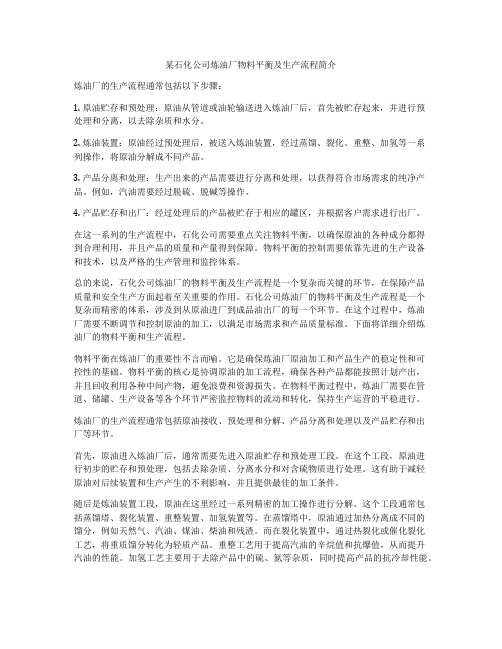
某石化公司炼油厂物料平衡及生产流程简介炼油厂的生产流程通常包括以下步骤:1. 原油贮存和预处理:原油从管道或油轮输送进入炼油厂后,首先被贮存起来,并进行预处理和分离,以去除杂质和水分。
2. 炼油装置:原油经过预处理后,被送入炼油装置,经过蒸馏、裂化、重整、加氢等一系列操作,将原油分解成不同产品。
3. 产品分离和处理:生产出来的产品需要进行分离和处理,以获得符合市场需求的纯净产品。
例如,汽油需要经过脱硫、脱碱等操作。
4. 产品贮存和出厂:经过处理后的产品被贮存于相应的罐区,并根据客户需求进行出厂。
在这一系列的生产流程中,石化公司需要重点关注物料平衡,以确保原油的各种成分都得到合理利用,并且产品的质量和产量得到保障。
物料平衡的控制需要依靠先进的生产设备和技术,以及严格的生产管理和监控体系。
总的来说,石化公司炼油厂的物料平衡及生产流程是一个复杂而关键的环节,在保障产品质量和安全生产方面起着至关重要的作用。
石化公司炼油厂的物料平衡及生产流程是一个复杂而精密的体系,涉及到从原油进厂到成品油出厂的每一个环节。
在这个过程中,炼油厂需要不断调节和控制原油的加工,以满足市场需求和产品质量标准。
下面将详细介绍炼油厂的物料平衡和生产流程。
物料平衡在炼油厂的重要性不言而喻。
它是确保炼油厂原油加工和产品生产的稳定性和可控性的基础。
物料平衡的核心是协调原油的加工流程,确保各种产品都能按照计划产出,并且回收利用各种中间产物,避免浪费和资源损失。
在物料平衡过程中,炼油厂需要在管道、储罐、生产设备等各个环节严密监控物料的流动和转化,保持生产运营的平稳进行。
炼油厂的生产流程通常包括原油接收、预处理和分解、产品分离和处理以及产品贮存和出厂等环节。
首先,原油进入炼油厂后,通常需要先进入原油贮存和预处理工段。
在这个工段,原油进行初步的贮存和预处理,包括去除杂质、分离水分和对含硫物质进行处理。
这有助于减轻原油对后续装置和生产产生的不利影响,并且提供最佳的加工条件。
炼油厂工艺流程

炼油厂工艺流程
《炼油厂工艺流程》
炼油厂是将原油转化为汽油、柴油、煤油等石油产品的重要工业设施。
炼油厂工艺流程是一个复杂的过程,涉及到多个工艺单元和技术,以及各种化学反应和物理分离过程。
首先,原油通过一系列预处理工艺单元进行初步处理,包括脱盐、脱硫、脱水等处理,以去除杂质和硫化物。
然后,原油进入裂化装置进行裂化过程,将大分子烃类分解成小分子烃类,生产出汽油、柴油等产品。
随后,经过蒸馏装置进行蒸馏分馏,将不同沸点的烃类分离出来,得到各种产品。
另外,炼油厂还通过重整、裂化、重整、加氢等工艺单元对产品进行改质升级。
其中,重整是将低辛烷值的馏分转化为高辛烷值的汽油产品;裂化是将重质油产生乙烯、丙烯等烯烃产品;加氢是通过加氢裂化将重质油产品转化为轻油产品。
最后,炼油厂还通过分离、脱硫、脱氮、脱气等工艺单元进行产品的后处理,目的是提高产品质量和符合环保要求。
总体来说,炼油厂的工艺流程包括原油预处理、初步裂化、分馏分离、产品改质升级、产品后处理等多个环节。
各个工艺单元的相互配合,构成了完整的炼油过程,为石油产品的生产提供了技术支持和保障。
炼油厂工艺简介
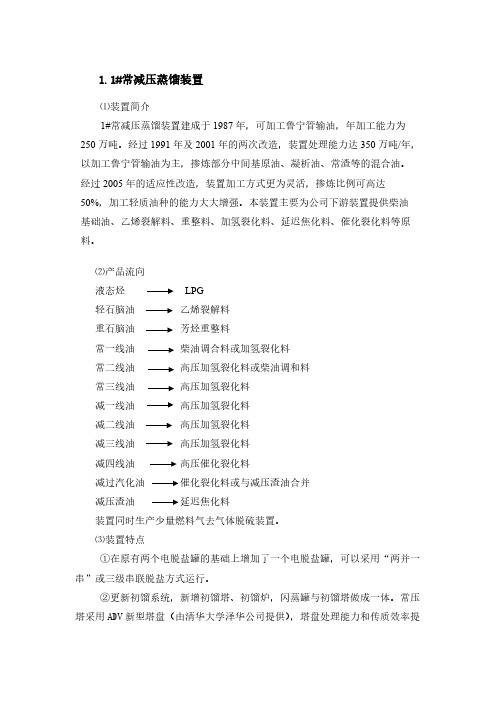
1.1#常减压蒸馏装置⑴装置简介1#常减压蒸馏装置建成于1987年,可加工鲁宁管输油,年加工能力为250万吨。
经过1991年及2001年的两次改造,装置处理能力达350万吨/年,以加工鲁宁管输油为主,掺炼部分中间基原油、凝析油、常渣等的混合油。
经过2005年的适应性改造,装置加工方式更为灵活,掺炼比例可高达50%,加工轻质油种的能力大大增强。
本装置主要为公司下游装置提供柴油基础油、乙烯裂解料、重整料、加氢裂化料、延迟焦化料、催化裂化料等原料。
⑵产品流向液态烃LPG轻石脑油乙烯裂解料重石脑油芳烃重整料常一线油柴油调合料或加氢裂化料常二线油高压加氢裂化料或柴油调和料常三线油高压加氢裂化料减一线油高压加氢裂化料减二线油高压加氢裂化料减三线油高压加氢裂化料减四线油高压催化裂化料减过汽化油减压渣油装置同时生产少量燃料气去气体脱硫装置。
⑶装置特点①在原有两个电脱盐罐的基础上增加了一个电脱盐罐,可以采用“两并一串”或三级串联脱盐方式运行。
②更新初馏系统,新增初馏塔、初馏炉,闪蒸罐与初馏塔做成一体。
常压塔采用ADV新型塔盘(由清华大学泽华公司提供),塔盘处理能力和传质效率提高。
③减压塔填料更换为高效规整填料ZUPAK,采用槽式分布器取代原喷头,进料部位采用流线式快速分布器(天津大学天久公司)。
④加热炉采用LGH-L/Q高效燃烧器(洛阳科恒公司)。
⑤装置增加轻烃回收系统,生产液化气、轻石脑油和重整料。
⑥减压系统采用三级蒸汽抽真空,残压达2.0Kpa以下。
2.2#常减压蒸馏装置⑴装置简介2# 常减压蒸馏装置建成于1995年,该装置主要加工高硫、轻质原油,加工能力为250万吨/年。
2002年装置经过改造,加工能力达450万吨/年,设计加工沙特轻质油、沙特中质混合原油。
800万吨/年炼油改造完成以后,主要以加工沙轻、阿曼等高(含)硫油为主,适当安排部分低硫原油,总硫控制在1.5%左右。
装置主要产品有液化气、乙烯料、重整料、柴油调和基础料、加氢裂化、加氢精制料、催化料、焦化料。
- 1、下载文档前请自行甄别文档内容的完整性,平台不提供额外的编辑、内容补充、找答案等附加服务。
- 2、"仅部分预览"的文档,不可在线预览部分如存在完整性等问题,可反馈申请退款(可完整预览的文档不适用该条件!)。
- 3、如文档侵犯您的权益,请联系客服反馈,我们会尽快为您处理(人工客服工作时间:9:00-18:30)。
常减压装置简介
常减压装置简介 • 原油自原油罐区用泵送入装置,经换热器换 热到 120 ~ 140℃ 。后先后进入三级电脱盐 罐( D -1/1 、 2 、 3 )进行脱水和脱盐。原 油在进入三级电脱盐前,先注水和破乳剂以 增强脱盐效果。原油经过三级脱盐后分三路 进入换热网络进行换热,脱后原油被换热到约 200℃ 后,再混合后进入初馏塔,从初馏塔 分离出大部分石脑油组分。
催化裂化装置简介
• 工艺特点: • ( 1) 产品收率高,汽油质量好。轻油收率高,可达 70%以上。催化裂化所得汽油辛烷值高,并且安定 性好,基本不含二烯烃。。汽油中含低分子烃较多 ,它的 10%与 50%馏出点温度较低,使用性能好 。 、C • ( 2 )可提供大量化工原料。裂化气体中 C 3 4 组分约占 90%, C 中丙烯又占 70%, C 中各种丁 3 4 烯占 55%左右,这些都是优良的石油化工原料,还 能提供大量液化汽供民用。
常减压装置简介
• 在初馏塔中,部分轻质油汽化,从初馏塔顶经初顶 空冷冷却进入初顶回流罐,部分打回流,部分与 常顶石脑油汇合送入吸收稳定塔,初顶不凝气与常 顶不凝气混合送往压缩机。未闪蒸汽化的闪底油由 闪底泵抽出后进入换热网络进行换热,换热到 290 ~ 300℃ 以上,然后再进入常压炉,在常压炉中被加 热到 350 ~ 360℃ 后进入常压塔中进行分馏。
常减压装置简介 • 常底重油由常底泵抽出,经减压炉加热到 36 0 ~ 385℃ 后进入减压塔。减压塔塔顶采用 三级抽真空,减顶油气经冷凝、冷却、油水 分离后污油送出装置,污水进含硫污水处理 系统。减压塔设四个侧线,减一线从减一线 集油箱抽出一部分经换热后和冷却后作减顶 回流,另一路经换热冷却到 60℃ 送出装置。
炼油厂生产工艺简介
典型炼油厂加工方案 • 根据目的产品不同,炼油厂的原油加工方案 大体上可以分为三种基本类型。 • 燃料型:主要产品用做燃料的石油产品。除 了生产部分重质原料油以外,减压馏分油和 减压榨油通过各种轻质化途径转换为各种轻质 原料。
典型炼油厂加工方案
• 燃料— 润滑油型:除生产用做燃料的石油产品之外 ,部分或者大部分减压馏分油和减压渣油还被生产 各种润滑油产品。 • 燃料— 化工型:如了生产燃料产品外,还生产化工 原料以及化工产品,例如某些烯烃、芳烃、聚合物 的单体等。这种加工方案体现了充分利用石油资源 的要求,也是提高炼油厂经济效益的重要途径。 是目前石油加工的发展方向。
常减压装置简介 - 常减压产品
产品名称 液化气 常顶石脑油 常一线 常二线 常三线 减 一线 减 二线 减 三线 减 四线 渣油 用途 制氢原料或乙烯裂解料 乙烯裂解料 乙烯裂解料 轻柴油 重柴油 柴油 加氢裂化料或催化料 催化原料 重油加氢原料 重油加氢原料或沥青 规格 C ≯ 3. 33%或≯ 12 % 5 干点≯ 230℃ 干点≯ 230℃ 干点≯ 360℃ 、闪点≮ 60℃ 350℃ 馏出量≮ 72% 干点≯ 520℃
常减压装置简介 • 常压塔开设三个侧线,常一线从常压塔第 34 层塔盘流入常一线汽提塔,再用泵抽出经过 换热到 40℃ 后送到乙烯装置作为裂解料。 常二线从常压塔第 22 层塔盘抽出,流入常 二线汽提塔,经泵抽出后换热到 60℃ 后,送 到柴油加氢装置。常三线从常压塔第 12 层 塔盘抽出流入常三线汽提塔,用泵抽出经换 热到 60℃ 后送出装置。
常减压装置简介 • 常压塔中,塔顶油气经与常顶空冷冷却、冷 凝到 40℃ 进入常顶回流罐,部分打回流, 部分与初顶来的石脑油混合送往吸收稳定塔。 常顶不凝气与初顶不凝气混合后送至气体压 缩机压缩到 0. 5M Pa ,再送到气体脱硫装置。 稳定塔顶液化气送到脱硫塔进行脱硫,稳定 塔底石脑油作为乙烯装置裂解料。
典型炼油厂加工方案
´ß »¯ÖØ Õû Æû ÓÍ
¼Ó ÇâÁÑ »¯ ¾« ÖÆ ´ß »¯ÁÑ »¯ ʯÄÔ ÓÍ ÖØ ÓÍ ¼Ó Çâ ¼Ó Çâ ¾« ÖÆ ²ñ ÓÍ
³ £¼ Ñ õ ¹Õô Áó
ÑÓ ³Ù½¹»¯
常减压装置简介
• 常减压装置将原油用蒸馏的方法分割成不同沸点 范围的组份,以适应产品或下游工艺装置对原料的 要求。蒸馏分为三种类型:闪蒸、简单蒸馏和精馏 ,由于平衡闪蒸和简单蒸馏都不能有效地分离混合 物,因此工业上常采用精馏的过程来实现。原油精 馏过程的实质是由于气液两相间存在着温度差和浓 度差,在塔盘上进行逆向接触时由于传质和传热使 轻组分逐渐走向塔顶,重组分逐渐走向塔底,从而 在不同的塔盘位置上得到相应的产品的过程。
常减压装置简介
• 减二线由泵从减压塔减二线集油箱抽出,经换热后 分两路,一路返回减压塔三段填料上方作为回流 ,另一路经换热冷却后出装置;减三线从减压塔减 三线集油箱抽出先分两路,一路返回五段填料上 方作为重洗涤油,另一路再分两路,一路经换热后 返回作为四段填料的回流,另一路经换热冷却送出 装置;减四线由泵从四线集油箱抽出,换热后直接 出装置;减底渣油从减压塔底抽出,经换热冷却后 送出装置。
催化裂化装置简介
• 催化裂化是原油二次加工的核心工艺,是炼油厂 经济效益最高的装置。该装置分反应 - 再生、分馏 、吸收稳定脱硫、再生烟气能量回收、余热锅炉 等 5 个部分。它以胜利原油的减压馏分油、 VR常 压渣油、 VR 减压渣油、焦化蜡油等为原料,在 50 0 ~ 510℃ , 0. 33 ~ 0. 34M Pa (绝压)的条件下 ,原料油与分子筛催化剂接触,经过以裂化反应为 主的一系列化学反应,转化成干气、液化汽、汽 油、柴油、油浆等产品。
催化裂化装置简介
• ( 3 )柴油性质差,十六烷值较低,一般只有 3 5 ~ 45 ,需与直馏柴油调合后才能使用。渣油催 化和掺炼重油催化除十六烷值更低外,含硫、氮、 胶质也较多,颜色深,安定性差,易氧化产生沉渣 ,需加氢精制处理。 • ( 4 )产品方案灵活。同一套装置,改变不同的操 作条件,便可得到气体、汽油、柴油的不同产品 分布,以适应市场经济发展的需要。 • ( 5 )原料选择范围比较宽,通常是以减压馏份油 、焦化蜡油等做原料。