冲压模具设计实例讲解
冲压磨具结构设计的案例展示成功案例的启发与学习

冲压磨具结构设计的案例展示成功案例的启发与学习冲压磨具在现代制造业中起着至关重要的作用,它通过在金属材料上施加力量来实现形状改变和加工,广泛应用于汽车零部件、家电产品、通信设备等领域。
而冲压磨具的结构设计直接关系到加工质量、生产效率和成本控制。
本文将通过展示冲压磨具结构设计的成功案例,探讨其启发与学习。
1. 案例一:汽车车门内板冲压磨具设计在汽车制造过程中,车门内板的冲压加工是关键环节之一。
某汽车制造企业为提高生产效率和降低成本,在车门内板冲压磨具的设计过程中进行了不断创新和优化。
通过对冲压磨具的结构进行改进,减少了材料浪费、提高了加工精度,并实现了自动化生产。
启发与学习:此案例表明,在冲压磨具结构设计中,应注重优化设计,以减少材料浪费和提高加工精度。
并且,可以借鉴自动化技术,提高生产效率。
2. 案例二:电子产品金属外壳冲压磨具设计电子产品的金属外壳冲压加工要求高度精密和一致性,因此冲压磨具的设计至关重要。
某电子产品制造商通过对冲压磨具结构的优化,实现了外壳加工的精度要求,提高了产品的质量和可靠性,并且缩短了生产周期。
启发与学习:这个案例给我们的启示是,在冲压磨具结构设计中,应注重满足产品的精度要求,并通过合理的结构设计来提高产品质量和可靠性。
此外,缩短生产周期也是一个重要的目标。
3. 案例三:通信设备金属零部件冲压磨具设计在通信设备制造中,金属零部件的冲压加工是一个关键步骤。
某通信设备制造企业通过对冲压磨具结构的创新,实现了零部件的一次成型加工,避免了二次加工,提高了生产效率和降低了成本。
启发与学习:该案例给我们启示,在冲压磨具结构设计中,应尽量实现一次成型加工,以减少生产环节和成本。
同时,创新性的设计可以带来生产效率的提高。
通过以上案例的展示,我们可以得出以下结论:首先,冲压磨具结构设计对于提高加工质量、生产效率和降低成本至关重要。
其次,优化设计、借鉴自动化技术、满足精度要求、缩短生产周期以及一次成型加工等都是成功案例的共同特点。
冲压模具设计实例讲解

第二节冲压工艺与模具设计实例一、摩托车侧盖前支承冲压工艺设计二、微型汽车水泵叶轮冲压工艺与模具设计一、摩托车侧盖前支承冲压工艺设计图12-1所示为摩托车侧盖前支承零件示意图,材料Q215钢,厚度1.5mm,年生产量5万件,要求编制该冲压工艺方案。
⒈零件及其冲压工艺性分析mm的凸包定位且焊接组合在车架的电气元件支架上,腰圆孔用于摩托车侧盖前支承零件是以2个9.5侧盖的装配,故腰圆孔位置是该零件需要保证的重点。
另外,该零件属隐蔽件,被侧盖完全遮蔽,外观上要求不高,只需平整。
1word版本可编辑.欢迎下载支持.图12-1侧盖前支承零件示意图该零件端部四角为尖角,若采用落料工艺,则工艺性较差,根据该零件的装配使用情况,为了改善落料的工艺性,故将四角修改为圆角,取圆角半径为2mm。
此外零件的“腿”较长,若能有效地利用过弯曲和校正弯曲来控制回弹,则可以得到形状和尺寸比较准确的零件。
2word版本可编辑.欢迎下载支持.腰圆孔边至弯曲半径R中心的距离为2.5mm。
大于材料厚度(1.5mm),从而腰圆孔位于变形区之外,弯曲时不会引起孔变形,故该孔可在弯曲前冲出。
⒉确定工艺方案首先根据零件形状确定冲压工序类型和选择工序顺序。
冲压该零件需要的基本工序有剪切(或落料)、冲腰圆孔、一次弯曲、二次弯曲和冲凸包。
其中弯曲决定了零件的总体形状和尺寸,因此选择合理的弯曲方法十分重要。
(1) 弯曲变形的方法及比较该零件弯曲变形的方法可采用如图12-2所示中的任何一种。
第一种方法(图12-2a)为一次成形,其优点是用一副模具成形,可以提高生产率,减少所需设备和操作人员。
缺点是毛坯的整个面积几乎都参与激烈的变形,零件表面擦伤严重,且擦伤面积大,零件形状与尺寸都不精确,弯曲处变薄严重,这些缺陷将随零件“腿”长的增加和“腿”长的减小而愈加明显。
第二种方法(图12-2b)是先用一副模具弯曲端部两角,然后在另一副模具上弯曲中间两角。
这显然比第一种方法弯曲变形的激烈程度缓和的多,但回弹现象难以控制,且增加了模具、设备和操作人员。
冲压磨具结构设计的实例解析学习成功案例提升自己

冲压磨具结构设计的实例解析学习成功案例提升自己冲压磨具在工业制造领域中扮演着重要角色,其结构设计的合理与否直接影响产品的质量和生产效率。
本文将通过一个成功案例的实例解析,探讨冲压磨具结构设计的关键要点,以提升读者自己在这一领域的专业能力。
一、案例背景分析某汽车制造公司在冲压生产过程中遇到了困扰多时的问题——冲裁加工时模具频繁易损坏,导致生产效率低下、成本高昂。
经过对问题的深入调研和分析,决定对冲压磨具的结构设计进行优化,以提高磨具的使用寿命和生产效率。
二、案例分析与解决方案该汽车制造公司对原有的冲压磨具结构进行了全面评估,并根据实际需求进行改进。
以下是该案例中的几个关键问题及其解决方案。
1. 冲压磨具材料选择原有的冲压磨具使用的材料强度不足,容易出现损坏现象。
为了解决这个问题,公司选择了一种更坚固耐用的合金钢材料,以增强磨具的耐用性和抗压能力。
2. 磨具结构优化通过对现有冲压磨具结构的深入分析,公司发现存在磨具结构复杂、加工独特等问题。
为了降低制造成本和提高生产效率,公司对原有结构进行了简化并优化流程。
他们采用了模块化的设计思路,通过设置可更换的零部件,提高了磨具的可维护性和灵活性。
3. 表面涂层技术应用为了进一步提升冲压磨具的使用寿命,该公司引入了表面涂层技术。
他们选取了合适的材料和涂层工艺,使冲压磨具表面形成了一层坚硬的保护膜,提高了其抗磨损和防腐蚀能力。
4. 冲裁动力系统升级经过对冲裁动力系统的分析,公司发现原有的动力输入方式存在一定的缺陷。
为了解决这个问题,他们采用了一种先进的液压传动系统,提高了冲压磨具的工作效率和精度。
三、成功案例的启示与学习通过这个成功案例的解析,我们可以得到一些关于冲压磨具结构设计的启示,并从中学习以提升自己。
1. 深入分析问题根源在解决冲压磨具结构设计问题时,我们首先要深入分析问题的根源,找出造成问题的原因。
只有找准问题所在,才能采取针对性的解决方案。
2. 结构优化与标准化冲压磨具结构设计的优化与标准化是提高生产效率和产品质量的关键。
冲压模具设计实例讲解.doc
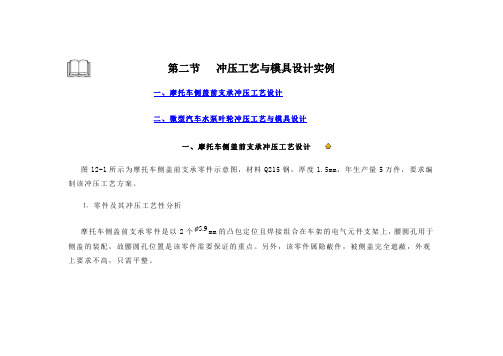
方案六:将方案三全部工序组合,采用带料连续冲压。其优点是工序集中,只用一副模具完成全部工序,其实质是把方案三的各工序分别布置在连续模的各工位上,所以还具有方案三的各项优点,缺点是模具结构复杂,安装、调试和维修困难。制造周期长。
直径 为一般要求的自由尺寸,冲压成形的直径精度的偏差大于表4-1拉深直径的极限偏差。但高度尺寸 精度高于表4-3中的尺寸偏差,需由整形保证。
表12-108Al—ZF的力学性能(GB/T5213—1985T和GB/T710—1991)
/MPa
(%)
不小于
260~300
200
44
0.66
初步分析可以知道叶轮零件的冲压成形需要多道工序。首先,零件中部是有凸缘的圆筒拉深
支点间距 近似取10mm。将上述数据代入 表达式,得:
取 ,得
压料力 =50%×2376=1188
则第二道工序总冲压力
根据第二道工序所需要的冲压力,选用公称压力为400kN的压力机完全能够满足使用要求。
(3)第三道工序—二次弯形(见图12-8)该工序仍需要压料,故冲压力包括自由弯曲力 和压料力 。
自由弯曲力
件,有两个价梯,筒底还要冲 的孔;其次,零件外圈为翻边后形成的7个“竖立”叶片,围绕中心均匀分布。另外,叶片翻边前还要修边、切槽、由于拉深圆角半径比较小(0.5~1),加上对叶片底面有跳动度的要求,因此还需要整形。
对拉深工序,在叶片展开前,按料厚中心线计算有 ≈4.53>1.4,并且叶片展开后凸缘将更宽,所以属于宽凸缘拉深。另外,零件拉深度大(如最小价梯直径的相对高度h/d=20.5/13.5=1.52,远大于一般带凸缘筒形件第一次拉深许可的最大相对拉深高度),所以拉深成形比较困难,要多次拉深。
第九讲冲压模具设计实例分析
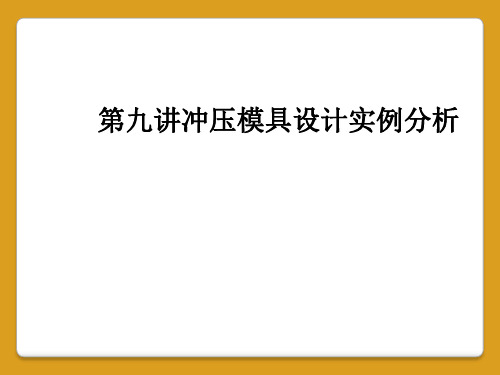
第八章 冲压模具结构及设计
(4)冲压工序压力计算 拟采用正装复合模,固定卸料与刚性推件。 根据冲压工艺总力计算结果并结合工件高度,初选开式双柱可倾压力机J23-25。
(5) 工作部分尺寸计算 落料和拉深的凸、凹模的工作尺寸计算。其中因为该工件口部尺寸要求要与另一件配合,所以在设
计时可将其尺寸作小些。
第八章 冲压模具结构及设计
2、冲压工艺方案的确定 方案一:先落料,后拉深。采用单工序模生产。 方案二:落料-拉深复合冲压。采用复合模生产。 方案三:拉深级进冲压。采用级进模生产。 方案一:模具结构简单,但成本高而生产效率低; 方案二:生产效率较高,尽管模具结构较复杂,但因零件简单对称,模具制造并不困难; 方案三:生产效率高,但模具结构比较复杂,送进操作不方便,加之工件尺寸偏大。 结论:采用方案二为最佳工艺方案。
第八章 冲压模具结构及设计
9、模具的装配 根据级进模装配要点,选凹模作为装配基准件,先装下模,再装上模,并调整间隙、试冲、返修。
第八章 冲压模具结构及设计
二、拉深模设计与制造实例
零件名称:端盖 生产批量:大批量 材料:镀锌铁皮 材料厚度:1mm
第八章 冲压模具结构及设计
1、冲压件工艺性分析 冲压工序:落料、拉深; 材料:为镀锌铁皮,具有良好的拉深性能,适合拉深; 结构:简单对称; 精度:全部为自由公差,工件厚度变化也没有作要求,只是该工件作为另一零件的盖,口部尺寸 φ69可稍作小些。而工件总高度尺寸14mm可在拉深后采用修边达要求 。
5、主要零部件设计 (1)工作零件的结构设计
①落料凸模 直通式,采用线切割加工,2个M8螺钉固定在垫板上,与凸模固定板的配合按H6/m5。
②冲孔凸模 台阶式
③凹模 整体凹模,各冲裁的凹模孔均采用线切割加工。
冲压模具设计和制造实例

冲压模具设计和制造实例冲压模具设计与制造实例例:图1所示冲裁件,材料为A3,厚度为2mm,大批量生产。
试制定工件冲压工艺规程、设计其模具、编制模具零件的加工工艺规程。
零件名称:止动件生产批量:大批材料:A3材料厚度:t=2mm一、冲压工艺与模具设计1.冲压件工艺分析①材料:该冲裁件的材料A3钢是普通碳素钢,具有较好的可冲压性能。
②零件结构:该冲裁件结构简单,并在转角有四处R2圆角,比较适合冲裁。
③尺寸精度:零件图上所有未注公差的尺寸,属自由尺寸,-0.74 0-0.52-0.52-0.52-0.52可按IT14级确定工件尺寸的公差。
孔边距12mm 的公差为-0.11,属11级精度。
查公差表可得各尺寸公差为:零件外形:65 mm 24 mm 30 mm R30 mm R2 mm零件内形:10 mm孔心距:37±0.31mm 结论:适合冲裁。
2.工艺方案及模具结构类型该零件包括落料、冲孔两个工序,可以采用以下三种工艺方案:①先落料,再冲孔,采用单工序模生产。
②落料-冲孔复合冲压,采用复合模生产。
③冲孔-落料连续冲压,采用级进模生产。
方案①模具结构简单,但需要两道工序、两套模具才能完成零件的加工,生产效率较低,难以满足零件大批量生产的需求。
由于零件结构简单,为提高生产效率,主要应采用复合冲裁或级进冲裁方式。
由于孔边距尺寸12 mm 有公差要求,为了更好地保证此尺寸精度,最后确定用复合冲裁方式进行生产。
+0.36 0-0.11工件尺寸可知,凸凹模壁厚大于最小壁厚,为便于操作,所以复合模结构采用倒装复合模及弹性卸料和定位钉定位方式。
3.排样设计查《冲压模具设计与制造》表2.5.2,确定搭边值:两工件间的搭边:a=2.2mm工件边缘搭边:a1=2.5mm步距为:32.2mm条料宽度B=D+2a1=65+2*2.5=70确定后排样图如2所示一个步距内的材料利用率η为:η=A/BS×100%=1550÷(70×32.2)×100%=68.8%查板材标准,宜选900mm×1000mm的钢板,每张钢板可剪裁为14张条料(70mm×1000mm),每张条料可冲378个工件,则η为:η=nA1/LB×100%=378×1550/900×1000×100%=65.1%即每张板材的材料利用率为65.1%4.冲压力与压力中心计算⑴冲压力落料力F总=1.3Ltτ=1.3×215.96×2×450=252.67(KN)其中τ按非退火A3钢板计算。
冲压磨具结构实用案例分享深入了解成功之道

冲压磨具结构实用案例分享深入了解成功之道在工业制造领域,冲压磨具是一种常用的工具,用于加工金属板材或条材。
它们的结构设计和使用方式对于冲压过程的高效性和成品质量有着重要的影响。
本文将通过分享几个冲压磨具的实用案例,深入探讨成功的结构设计和使用方法,以期提供一些有益的参考和启示。
案例一:模具结构的细节设计在冲压磨具的设计中,模具结构的细节决定了其加工精度和稳定性。
一家汽车零部件制造厂对其模具结构进行了优化设计,以提高冲压生产线的效率和产品质量。
首先,他们对冲压模具的支撑结构进行了改进。
通过增加支撑点和设置辅助支撑装置,提高了模具在冲压过程中的稳定性,降低了变形和振动的风险。
其次,他们增加了模具的导向装置,使其在加工过程中的移动更加平稳。
通过合理设置滑动道、导向柱和导向套,成功减少了磨具的摩擦和卡紧现象,提高了冲压的精度和效率。
此外,他们还优化了模具的冲堵结构。
通过减小冲孔套的直径和增加冲头的冲击力,他们成功解决了冲堵现象,提高了模具的使用寿命和生产效率。
案例二:磨具材料的选择和应用另一个成功的案例来自一家金属制造企业,他们通过合理选择和应用磨具材料,实现了高效的冲压加工。
首先,他们使用了高硬度和抗磨损的钢材作为磨具的工作面材料。
这种材料具有优异的耐磨性和耐冲击性,能够有效减少磨具在加工过程中的磨损和损坏,提高了使用寿命和生产效率。
其次,他们采用了表面涂层技术来增加磨具的表面硬度和润滑性。
通过使用钛涂层或氮化处理等方法,他们成功减少了磨具与金属板材之间的摩擦力,提高了冲压的稳定性和精度。
此外,他们还使用了先进的磨具润滑剂,以减少磨具与材料之间的摩擦和热量积聚。
这种润滑剂能够有效降低冲压过程中的摩擦阻力,减少磨具的磨损和形变,提高加工的质量和效率。
结论通过以上案例的分享,我们可以看出冲压磨具的结构设计和使用方法对于提高生产线的效率和产品质量至关重要。
在模具结构的设计中,我们应注重细节并进行优化,例如增加支撑点、优化导向装置和冲堵结构等。
冲压模具实例

冲压模具实例例8.2.1冲裁模设计与制造实例工件名称:手柄工件简图:如图8.2.1所示。
生产批量:中批量材料:Q235-A钢材料厚度:1.2mm1.冲压件工艺性分析此工件只有落料和冲孔两个工序。
材料为Q235-A钢,具有良好的冲压性能,适合冲裁。
工件结构相对简单,有一个φ8mm的孔和5个φ5mm的孔;孔与孔、孔与边缘之间的距离也满足要求,最小壁厚为3.5mm(大端4个φ5mm的孔与φ8mm孔、φ5mm的孔与R16mm外圆之间的壁厚)。
工件的尺寸全部为自由公差,可看作IT14级,尺寸精度较低,普通冲裁完全能满足要求。
2.冲压工艺方案的确定该工件包括落料、冲孔两个基本工序,可有以下三种工艺方案:方案一:先落料,后冲孔。
采用单工序模生产。
方案二:落料-冲孔复合冲压。
采用复合模生产。
方案三:冲孔-落料级进冲压。
采用级进模生产。
方案一模具结构简单,但需两道工序两副模具,成本高而生产效率低,难以满足中批量生产要求。
方案二只需一副模具,工件的精度及生产效率都较高,但工件最小壁厚3.5mm接近凸凹模许用最小壁厚3.2mm,模具强度较差,制造难度大,并且冲压后成品件留在模具上,在清理模具上的物料时会影响冲压速度,操作不方便。
方案三也只需一副模具,生产效率高,操作方便,工件精度也能满足要求。
通过对上述三种方案的分析比较,该件的冲压生产采用方案三为佳。
3.主要设计计算(1)排样方式的确定及其计算图8.2.1手柄工件简图(2)冲压力的计算该模具采用级进模,拟选择弹性卸料、下出件。
冲压力的相关计算见表图8.2.2手柄排样图8.2.1。
根据计算结果,冲压设备拟选J23-25。
(3)压力中心的确定及相关计算计算压力中心时,先画出凹模型口图,如图8.2.3所示。
在图中将某oy坐标系建立在图示的对称中心线上,将冲裁轮廓线按几何图形分解成L1~L6共6组基本线段,用解析法求得该模具的压力中心C点的坐标(13.57,11.64)。
有关计算如表8.2.2所示。
模具设计精品教程-冲压模设计实例分析

冲压模设计实例分析【知识目标】➢熟悉并掌握冲压模设计的一般步骤;➢理解单工序模、复合模和级进模的设计方法。
【技能目标】➢根据冲压件的外形和所用材料,确定冲压工艺类型;➢能进行常见简单冲压模的设计。
【任务描述】如图12-1所示的冲压件,原料采用钢板,该选用哪种冲压工艺呢?怎样进行设计呢?图12-1 冲压件【任务分析】如图12-1所示的冲压件都可以使用冲压模进行生产,要正确选择合适的冲压工艺并设计相应的冲压模来生产这些零件,就要学习本模块的内容。
本模块包括单工序模设计实例详解,复合模设计实例详解和级进模设计实例详解。
【任务引导】(1)冲压模设计步骤一般应包括几步?(2)冲裁、弯曲、拉深等单工序冲压模设计的详细步骤是什么,如何进行设计?(3)复合模设计的详细步骤是什么,如何进行设计?(4)级进模设计的详细步骤是什么,如何进行设计?【知识准备】学习情境1 单工序模设计实例冲压模设计步骤一般应包括:1.分析冲压件的工艺性根据产品的技术图纸,分析冲压件的形状特点、尺寸大小、精度要求以及所选用的材料是否符合冲压工艺的要求。
良好的冲压工艺性应保证材料消耗少、工序数目少、占用设备数量少、模具结构简单而且使用寿命长、产品质量稳定、操作安全简单。
2.确定冲压工艺方案在冲压工艺分析的基础上,以极限变性参数及变形的趋向性分析为依据,提出各种可能的冲压工艺方案,进行综合分析、比较,确定适合于所给定的生产条件的最佳方案。
3.选定模具类型及结构形式,设计模具总装配图及零件图根据确定的冲压工艺和冲压件形状特点、精度要求、生产批量、模具加工条件、操作是否方便与安全等要求,选定冲模类型及结构形式。
此外还需要进行必要的计算,包括模具零件强度计算、压力中心计算、弹性元件选用和核算,再进行装配图设计、模具凸凹模等工作零件设计及标准零件的选取等。
4.冲压设备的选择根据工厂现有设备情况、生产批量、冲压工序性质、冲压件尺寸与精度、冲压加工所需的冲压力、计算变形力以及模具的闭合高度和轮廓尺寸等因素,合理选定冲压设备的类型规格。
冲压模具设计实例讲解

冲压模具设计实例讲解1. 引言冲压模具是用于制作零部件的工具,广泛应用于汽车、电子、家电等行业。
本文将通过一个冲压模具设计实例,为读者介绍冲压模具设计的根本流程和本卷须知。
2. 设计背景我们以一款汽车车门为例,说明冲压模具的设计过程。
车门是汽车的重要部件之一,需要经过冲压加工来获得所需的形状和尺寸。
3. 设计流程3.1 确定产品要求在冲压模具设计之前,首先要明确产品的要求。
包括车门的尺寸、形状、材料以及制造工艺要求等。
3.2 制定模具设计方案根据产品要求,我们可以开始制定模具设计方案。
主要包括冲头、模座、模具顶板等部件的尺寸、形状和结构设计。
3.3 3D建模在制定模具设计方案后,我们可以使用CAD软件进行3D建模。
这样可以更直观地了解模具的结构、尺寸和装配关系。
3.4 模具加工制造根据3D模型,我们可以进一步进行模具零部件的加工制造。
主要包括数控加工、电火花加工、磨削等工艺。
3.5 模具装配和调试将加工好的模具零部件进行装配,并进行模具调试。
确保模具的各个部位协调运转,到达设计要求。
4. 冲压模具设计的本卷须知4.1 材料选择在冲压模具设计中,材料的选择非常重要。
一般情况下,应选用高强度、高韧性、耐磨损的材料,以保证模具的使用寿命和精度。
4.2 精度要求冲压模具对产品的精度要求很高,因此在设计过程中要考虑到产品的尺寸、形状等因素,并进行适宜的修正和优化。
4.3 加工工艺冲压模具的加工工艺对模具的质量和性能起着决定性的作用。
因此,在制造过程中要选择适宜的加工工艺,并确保加工精度和质量。
4.4 模具保养模具使用后需要定期进行保养和维护,以延长模具的使用寿命。
包括清洁、润滑、更换易损件等工作。
5. 总结冲压模具的设计过程需要考虑产品要求、制定设计方案、进行3D建模、加工制造、装配和调试等多个环节。
同时要注意材料选择、精度要求、加工工艺和模具保养等方面的问题。
通过本文的实例讲解,读者可以更深入地了解冲压模具设计的根本流程和本卷须知。
冲压磨具结构设计的十大经典案例

冲压磨具结构设计的十大经典案例案例一:汽车车身冲压件的多工位磨具汽车车身冲压件的磨具设计具有独特的特点和挑战。
为了提高生产效率和质量,设计师通常需要设计多工位磨具。
多工位磨具可以在一次夹紧的情况下完成多个冲压工序,大大提高了冲压生产线的效率。
案例二:飞机翼罩冲压模具飞机翼罩是航空领域中关键的部件之一,其冲压模具设计要求非常高。
翼罩的形状复杂且精度要求高,需要考虑到翼罩的强度、刚度和表面光洁度等因素。
设计师经过精心的磨具结构设计,保证了飞机翼罩的质量和性能。
案例三:家电外壳冲压磨具家电外壳冲压磨具的设计要求外壳的造型美观,同时要满足耐用性和制造成本的要求。
设计师通过合理的冲压工艺和磨具结构设计,实现了家电外壳的高效生产和质量控制。
案例四:电子产品金属外壳冲压模具电子产品金属外壳的冲压模具设计要考虑到外壳的精度、尺寸稳定性和表面处理要求。
设计师通过合理的模具结构设计和冲压工艺,实现了电子产品外壳的高质量和高效生产。
案例五:手机壳冲压模具手机壳的冲压模具设计要考虑到外观要求,如曲面和切割边缘的处理。
设计师通过创新的磨具结构设计和冲压工艺,实现了手机壳的设计复杂性和高质量要求。
案例六:钢铁行业冲压磨具设计钢铁行业的冲压磨具设计要考虑到材料的硬度和可加工性。
设计师通过合理的磨具结构设计和冲压工艺,提高了钢铁行业的生产效率和产品质量。
案例七:航天器零部件冲压模具航天器零部件的冲压模具设计要求非常高,需要考虑到零部件的材料性能、结构复杂度和重量要求等因素。
设计师通过优化的磨具结构设计和精细的制造工艺,实现了航天器零部件的高质量和可靠性。
案例八:新能源汽车零部件冲压模具新能源汽车零部件的冲压模具设计要考虑到其特殊材料和结构要求。
设计师通过创新的磨具结构设计和精细的制造工艺,实现了新能源汽车零部件的高质量和可靠性。
案例九:家具五金件冲压模具家具五金件的冲压模具设计要考虑到五金件的形状复杂度和表面质量要求。
设计师通过合理的磨具结构设计和冲压工艺,实现了家具五金件的高质量和高效生产。
冲压模具设计实例讲解
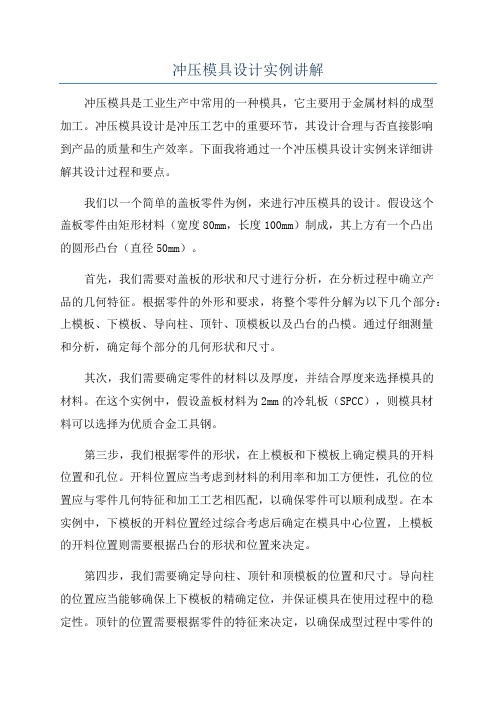
冲压模具设计实例讲解冲压模具是工业生产中常用的一种模具,它主要用于金属材料的成型加工。
冲压模具设计是冲压工艺中的重要环节,其设计合理与否直接影响到产品的质量和生产效率。
下面我将通过一个冲压模具设计实例来详细讲解其设计过程和要点。
我们以一个简单的盖板零件为例,来进行冲压模具的设计。
假设这个盖板零件由矩形材料(宽度80mm,长度100mm)制成,其上方有一个凸出的圆形凸台(直径50mm)。
首先,我们需要对盖板的形状和尺寸进行分析,在分析过程中确立产品的几何特征。
根据零件的外形和要求,将整个零件分解为以下几个部分:上模板、下模板、导向柱、顶针、顶模板以及凸台的凸模。
通过仔细测量和分析,确定每个部分的几何形状和尺寸。
其次,我们需要确定零件的材料以及厚度,并结合厚度来选择模具的材料。
在这个实例中,假设盖板材料为2mm的冷轧板(SPCC),则模具材料可以选择为优质合金工具钢。
第三步,我们根据零件的形状,在上模板和下模板上确定模具的开料位置和孔位。
开料位置应当考虑到材料的利用率和加工方便性,孔位的位置应与零件几何特征和加工工艺相匹配,以确保零件可以顺利成型。
在本实例中,下模板的开料位置经过综合考虑后确定在模具中心位置,上模板的开料位置则需要根据凸台的形状和位置来决定。
第四步,我们需要确定导向柱、顶针和顶模板的位置和尺寸。
导向柱的位置应当能够确保上下模板的精确定位,并保证模具在使用过程中的稳定性。
顶针的位置需要根据零件的特征来决定,以确保成型过程中零件的成型质量。
顶模板则需要根据零件的形状和材料选择合适的凸模形状和尺寸,以确保零件的成型质量。
最后一步,我们需要根据上述设计结果进行模具的绘图制作。
绘图要求精确、准确,需要包含所有的模具建构要素和加工尺寸等信息,以便制造部门进行模具加工和组装。
综上所述,冲压模具设计涉及到多个方面的考虑和决策,需要综合考虑零件的特征、工艺要求、材料特性等多个因素。
通过合理的设计和制作,可以保证模具的质量和使用效果,提高产品的生产效率和质量。
冲压模具设计实例讲解

第二节冲压工艺与模具设计实例一、摩托车侧盖前支承冲压工艺设计二、微型汽车水泵叶轮冲压工艺与模具设计一、摩托车侧盖前支承冲压工艺设计图12-1所示为摩托车侧盖前支承零件示意图,材料Q215钢,厚度1.5mm,年生产量5万件,要求编制该冲压工艺方案。
⒈零件及其冲压工艺性分析摩托车侧盖前支承零件是以2个mm的凸包定位且焊接组合在车架的电气元件支架上,腰圆孔用于侧盖的装配,故腰圆孔位置是该零件需要保证的重点。
另外,该零件属隐蔽件,被侧盖完全遮蔽,外观上要求不高,只需平整。
图12-1侧盖前支承零件示意图该零件端部四角为尖角,若采用落料工艺,则工艺性较差,根据该零件的装配使用情况,为了改善落料的工艺性,故将四角修改为圆角,取圆角半径为2mm。
此外零件的“腿”较长,若能有效地利用过弯曲和校正弯曲来控制回弹,则可以得到形状和尺寸比较准确的零件。
腰圆孔边至弯曲半径R中心的距离为2.5mm。
大于材料厚度(1.5mm),从而腰圆孔位于变形区之外,弯曲时不会引起孔变形,故该孔可在弯曲前冲出。
⒉确定工艺方案首先根据零件形状确定冲压工序类型和选择工序顺序。
冲压该零件需要的基本工序有剪切(或落料)、冲腰圆孔、一次弯曲、二次弯曲和冲凸包。
其中弯曲决定了零件的总体形状和尺寸,因此选择合理的弯曲方法十分重要。
(1) 弯曲变形的方法及比较该零件弯曲变形的方法可采用如图12-2所示中的任何一种。
第一种方法(图12-2a)为一次成形,其优点是用一副模具成形,可以提高生产率,减少所需设备和操作人员。
缺点是毛坯的整个面积几乎都参与激烈的变形,零件表面擦伤严重,且擦伤面积大,零件形状与尺寸都不精确,弯曲处变薄严重,这些缺陷将随零件“腿”长的增加和“腿”长的减小而愈加明显。
第二种方法(图12-2b)是先用一副模具弯曲端部两角,然后在另一副模具上弯曲中间两角。
这显然比第一种方法弯曲变形的激烈程度缓和的多,但回弹现象难以控制,且增加了模具、设备和操作人员。
冲压模具结构设计及实例

冲压模具结构设计及实例冲压模具是指用于冲压工艺的模具,它是冲压工艺中的重要组成部分。
冲压模具的结构设计对于冲压工艺的质量和效率具有重要影响。
本文将从冲压模具的结构设计和实例两个方面进行探讨。
一、冲压模具的结构设计冲压模具的结构设计是冲压工艺的关键环节之一。
一个优秀的冲压模具需要具备以下几个方面的设计要素:1. 合理的结构布局:冲压模具的结构布局应该合理,能够满足冲压工艺的要求,并且方便操作和维护。
通常包括上下模座、导向装置、冲头、顶出装置等部分。
2. 合适的材料选择:冲压模具需要承受较大的冲击和摩擦力,因此材料的选择非常重要。
常用的材料有优质合金钢、工具钢等,具有较高的硬度和耐磨性。
3. 合理的导向装置:导向装置能够确保上下模具的准确对位,以保证冲压工艺的精度。
常见的导向装置有滑块导向、销针导向等。
4. 适当的顶出装置:顶出装置能够将冲制件从模具中顶出,以便进行下一步的操作。
顶出装置的设计需要考虑冲制件的形状和尺寸等因素。
5. 合理的冲头设计:冲头是冲压模具的重要组成部分,其设计需要考虑冲制件的形状和尺寸等因素。
同时,冲头的材料选择和热处理也非常重要。
二、冲压模具结构设计实例以下是一个钣金冲压模具的结构设计实例:该冲压模具用于加工一种带有凹槽的钣金零件。
该零件的厚度为2mm,材料为优质冷轧板。
根据对该零件的要求,设计出了以下的冲压模具结构:1. 上模座:采用整体式上模座,材料为优质合金钢。
上模座上设置有导向装置,确保上下模具的准确对位。
2. 下模座:采用整体式下模座,材料为优质合金钢。
下模座上设置有顶出装置,以便将冲制件顶出。
3. 冲头:冲头采用硬质合金材料制造,并经过热处理,以提高其硬度和耐磨性。
冲头的形状和尺寸与钣金零件的凹槽相匹配。
4. 引导装置:在上模座和下模座上设置有引导装置,确保上下模具的准确对位,以保证冲制件的精度。
通过以上的结构设计,该冲压模具能够满足钣金零件的冲压工艺要求。
冲制过程中,上下模具准确对位,冲头能够将钣金材料冲剪成带有凹槽的零件,并通过顶出装置将零件顶出,以便进行下一步的操作。
冲压模具设计与制造实例教材(PPT 42页)
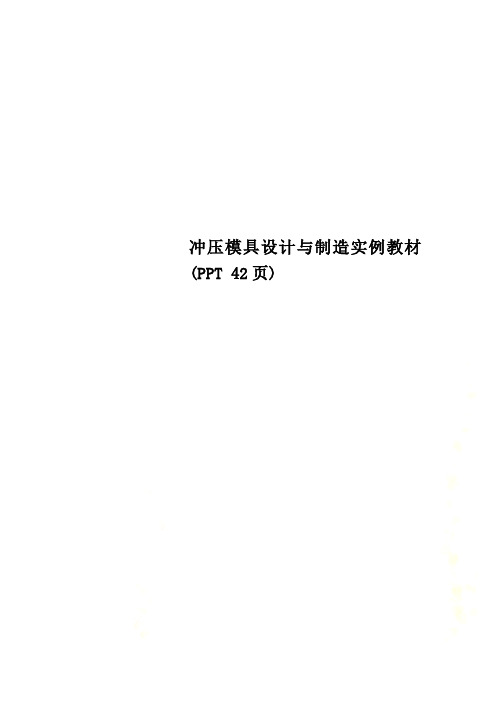
冲压模具设计与制造实例教材(PPT 42页)冲压模具设计与制造实例例:图1所示冲裁件,材料为A3,厚度为2mm,大批量生产。
试制定工件冲压工艺规程、设计其模具、编制模具零件的加工工艺规程。
零件名称:止动件生产批量:大批材料:A3材料厚度:t=2mm一、冲压工艺与模具设计1.冲压件工艺分析①材料:该冲裁件的材料A3钢是普通碳素钢,具有较好的可冲压性能。
②零件结构:该冲裁件结构简单,并在转角有四处R2圆角,比较适合冲裁。
③尺寸精度:零件图上所有未注公差的尺寸,属自由尺寸,-0.74 0-0.52-0.52-0.52-0.52=378×1550/900×1000×100%=65.1%即每张板材的材料利用率为65.1%4.冲压力与压力中心计算⑴冲压力落料力F总=1.3Ltτ=1.3×215.96×2×450=252.67(KN)其中τ按非退火A3钢板计算。
冲孔力F冲=1.3Ltτ=1.3×2π×10×2×450=74.48(KN)其中:d 为冲孔直径,2πd为两个圆周长之和。
卸料力F卸=K卸F卸=0.05×252.67=12.63(KN)推件力F推=nK推F推=6×0.055×37.24=12.30(KN)其中n=6 是因有两个孔。
总冲压力:F总= F落+ F冲+ F卸+ F推=252.67+74.48+12.63+12.30=352.07(KN)⑵压力中心如图3所示:由于工件X方向对称,故压力中心x0=32.5mm=13.0mm其中:L1=24mm y1=12mmL2=60mm y2=0mmL3=24mm y1=12mmL4=60mm y4=24mmL5=60mm y5=27.96mmL6=60mm y6=24mmL7=60mm y7=12mmL8=60mm y8=12mm计算时,忽略边缘4-R2圆角。
冲压磨具结构设计案例分析成功案例的启示与借鉴

冲压磨具结构设计案例分析成功案例的启示与借鉴在冲压加工中,冲压磨具是非常重要的工具之一。
它不仅直接影响产品质量和生产效率,还关系到整个生产线的稳定性和成本控制。
本文通过分析一些成功的冲压磨具设计案例,总结出一些启示和借鉴,以提供给冲压工艺设计师和工装工程师参考。
一、案例一:汽车车身冲压件磨具设计该案例涉及到汽车车身冲压件的磨具设计。
为了实现高质量的冲压加工,并减少生产过程中的杂散变形和损伤,设计师采用了以下几点设计方案:1. 结构刚性优化:通过优化磨具结构,增加钢板厚度和加强磨具内部支撑结构,使磨具的整体刚性增强。
这样可以有效减少因冲击力而导致的磨具的扭曲和变形,保证冲压加工的稳定性。
2. 强化磨具表面处理:磨具的表面经过特殊处理,增加了硬度和耐磨性。
这样可以减少因摩擦而引起的磨损,延长磨具的使用寿命。
3. 优化导向系统:设计师对磨具的导向系统进行了优化,采用了高精度滑块导向和润滑系统。
这样可以确保冲压过程中的导向准确性,减少因导向偏差而导致的磨具损伤。
通过上述的设计方案,该案例中的冲压磨具提供了高质量的冲压加工,并且在长期使用中保持了较好的稳定性和寿命。
二、案例二:家用电器金属壳体冲压件磨具设计该案例涉及到家用电器金属壳体冲压件的磨具设计。
为了提高产品质量和生产效率,设计师采用了以下几点设计方案:1. 精确模具结构设计:通过精确的模具结构设计,确保金属壳体冲压件的尺寸和形状精度。
这可以避免冲压过程中产生的尺寸偏差和变形,保证产品的外观质量。
2. 合理分布冲孔:设计师根据冲压件的形状和结构特点,合理安排冲孔的位置和数量。
这样可以减少冲压过程中的扭力和应力集中,减少磨具的磨损和损伤。
3. 优化润滑系统:针对家用电器金属壳体冲压件的特点,设计师优化了润滑系统。
通过添加适当的润滑剂和优化润滑剂的供应方式,减少摩擦和热量,并提高冲压件的表面光洁度。
通过上述的设计方案,该案例中的冲压磨具实现了高效、稳定的冲压加工,提高了产品质量和生产效率。
《冲压模具课程设计》范例

《冲压模具课程设计》范例《冲压模具课程设计》范例【范例】(1)题目:东风EQ-1090汽车储气简支架(2)原始数据数据如图7—1所示。
大批量生产,材料为Q215,t=3mm。
图7-1零件图(3)工艺分析此工件既有冲孔,又有落料两个工序。
材料为Q235、t=3mm的碳素钢,具有良好的冲压性能,适合冲裁,工件结构中等复杂,有一个直径φ44mm的圆孔,一个60mm×26mm、圆角半径为R6mm的长方形孔和两个直径13mm的椭圆孔。
此工件满足冲裁的加工要求,孔与孔、孔与工件边缘之间的最小壁厚大于8mm。
工件的尺寸落料按ITll级,冲孔按IT10级计算。
尺寸精度一般,普通冲裁完全能满足要求。
(4)冲裁工艺方案的确定①方案种类该工件包括落料、冲孑L两个基本工序,可有以下三种工艺方案。
方案一:先冲孔,后落料。
采用单工序模生产。
方案二:冲孔一落料级进冲压。
采用级进模生产。
方案三:采用落料一冲孔同时进行的复合模生产。
②方案的比较各方案的特点及比较如下。
方案一:模具结构简单,制造方便,但需要两道工序,两副模具,成本相对较高,生产效率低,且更重要的是在第一道工序完成后,进入第二道工序必然会增大误差,使工件精度、质量大打折扣,达不到所需的要求,难以满足生产需要。
故而不选此方案。
方案二:级进模是一种多工位、效率高的加工方法。
但级进模轮廓尺寸较大,制造复杂,成本较高,一般适用于大批量、小型冲压件。
而本工件尺寸轮廓较大,采用此方案,势必会增大模具尺寸,使加工难度提高,因而也排除此方案。
方案三:只需要一套模具,工件的精度及生产效率要求都能满足,模具轮廓尺寸较小、模具的制造成本不高。
故本方案用先冲孔后落料的方法。
③方案的确定综上所述,本套模具采用冲孔一落料复合模。
(5)模具结构形式的确定复合模有两种结构形式,正装式复合模和倒装式复合模。
分析该工件成形后脱模方便性,正装式复合模成形后工件留在下模,需向上推出工件,取件不方便。
- 1、下载文档前请自行甄别文档内容的完整性,平台不提供额外的编辑、内容补充、找答案等附加服务。
- 2、"仅部分预览"的文档,不可在线预览部分如存在完整性等问题,可反馈申请退款(可完整预览的文档不适用该条件!)。
- 3、如文档侵犯您的权益,请联系客服反馈,我们会尽快为您处理(人工客服工作时间:9:00-18:30)。
第三种方法(图12-2c)是先在一副模具上弯曲端部两角并使中间两角预弯45°,然后在另一副模具上弯曲成形,这样由于能够实现过弯曲和校正弯曲来控制回弹,故零件的形状和尺寸精确度高。此外,由于成形过程中材料受凸、凹模圆角的阻力较小,零件的表面质量较好。这种弯曲变形方法对于精度要求高或长“脚”短“脚”弯曲件的成形特别有利。
图12-3毛坯计算图图12-4排样方案
搭边值 和 由表2-12查得,得 =2mm, =1.8mm。????
2)确定板料规格和裁料方式。根据条料的宽度尺寸,选择合适的板料规格,使剩余的边料越小越好。该零件宽度用料为172mm,以选择1.5mm×710mm×1420mm的板料规格为宜。
裁料方式既要考虑所选板料规格、冲制零件的数量,又要考虑裁料操作的方便性,该零件以纵裁下料为宜。对于较为大型的零件,则着重考虑冲制零件的数量,以降低零件的材料费用。
⒉确定工艺方案
首先根据零件形状确定冲压工序类型和选择工序顺序。冲压该零件需要的基本工序有剪切(或落料)、冲腰圆孔、一次弯曲、二次弯曲和冲凸包。其中弯曲决定了零件的总体形状和尺寸,因此选择合理的弯曲方法十分重要。
(1)弯曲变形的方法及比较该零件弯曲变形的方法可采用如图12-2所示中的任何一种。
第一种方法(图12-2a)为一次成形,其优点是用一副模具成形,可以提高生产率,减少所需设备和操作人员。缺点是毛坯的整个面积几乎都参与激烈的变形,零件表面擦伤严重,且擦伤面积大,零件形状与尺寸都不精确,弯曲处变薄严重,这些缺陷将随零件“腿”长的增加和“腿”长的减小而愈加明显。
(3)计算材料消耗工艺定额和材料利用率。根据排样计算,一张钢板可冲制的零件数量为n=4×59=236(件)。
材.7%
零件面积由图12-5计算得出。
图12-5落料、冲孔工序略图
⒋计算各工序冲压力和选择冲压设备
(1)第一道工序—落料冲孔(见图12-6)该工序冲压力包括冲裁力 ,卸料力 和推料力 ,按图12-6所示的结构形式,系采用打杆在滑块快回到最高位置时将工件直接从凹模内打出,故不再考虑顶件力 。
第二节冲压工艺与模具设计实例
一、摩托车侧盖前支承冲压工艺设计
二、微型汽车水泵叶轮冲压工艺与模具设计
一、摩托车侧盖前支承冲压工艺设计
图12-1所示为摩托车侧盖前支承零件示意图,材料Q215钢,厚度1.5mm,年生产量5万件,要求编制该冲压工艺方案。
⒈零件及其冲压工艺性分析
摩托车侧盖前支承零件是以2个 mm的凸包定位且焊接组合在车架的电气元件支架上,腰圆孔用于侧盖的装配,故腰圆孔位置是该零件需要保证的重点。另外,该零件属隐蔽件,被侧盖完全遮蔽,外观上要求不高,只需平整。
考虑到弯曲时材料略有伸长,故取毛坯展开长度L=168mm。
对于精度要求高的弯曲件,还需要通过试弯后进行修正,以获得准确的展开尺寸。
(2)确定排样方案和计算材料利用率
1)确定排样方案,根据零件形状选用合理的排样方案,以提高材料利用率。该零件采用落料与冲孔复合冲压,毛坯形状为矩形,长度方向尺寸较大,为便于送料,采用单排方案(见图12-4)。
(1)毛坯展开尺寸(查工具书)展开尺寸按图12-3分段计算。毛坯展开长度
式中 =12.5mm;
=45.5m;
=30mm;
和 按 计算。
其中圆周半径r分别为2mm和4mm,材料厚度t=1.5mm,中性层位置系数x按 由表3-2查取。当r=2mm时取x=0.43,r=4mm时取x=0.46。
将以上数值代入上式得
图12-2弯曲成形
a)一副模具成形 b)、c)两副模具成形
(2)工序组合方案及比较根据冲压该零件需要的基本工序和弯曲成形的不同方法,可以作出下列各种组合方案。
方案一:落料与冲腰圆孔复合、弯曲四角、冲凸包。其优点是工序比较集中,占用设备和人员少,但回弹难以控制,尺寸和形状不精确,表面擦伤严重。
方案二:落料与冲腰圆孔复合、弯曲端部两角、弯曲中间两角、冲凸包。其优点是模具结构简单,投产快,但回弹难以控制,尺寸和形状不精确,而且工序分散,占用设备和人员多。
方案五:冲腰圆孔、切断及弯曲端部冲腰圆孔、切断连续冲压、弯曲中间两角、冲凸包。这种方案实质上与方案二差不多,只是采用了结构复杂的连续模,故工件回弹难以控制,尺寸和形状不精确。
方案六:将方案三全部工序组合,采用带料连续冲压。其优点是工序集中,只用一副模具完成全部工序,其实质是把方案三的各工序分别布置在连续模的各工位上,所以还具有方案三的各项优点,缺点是模具结构复杂,安装、调试和维修困难。制造周期长。
图12-1侧盖前支承零件示意图
该零件端部四角为尖角,若采用落料工艺,则工艺性较差,根据该零件的装配使用情况,为了改善落料的工艺性,故将四角修改为圆角,取圆角半径为2mm。此外零件的“腿”较长,若能有效地利用过弯曲和校正弯曲来控制回弹,则可以得到形状和尺寸比较准确的零件。
腰圆孔边至弯曲半径R中心的距离为2.5mm。大于材料厚度(1.5mm),从而腰圆孔位于变形区之外,弯曲时不会引起孔变形,故该孔可在弯曲前冲出。
方案三:落料与冲腰圆孔复合、弯曲端部两角并使中间两角预弯45°、弯曲中间两角、冲凸包。其优点是工件回弹容易控制,尺寸和形状精确,表面质量好,对于这种长“腿”短“脚”弯曲件的成形特别有利,缺点是工序分散,占用设备和人员多。
方案四:冲腰圆孔、切断及弯曲四角连续冲压、冲凸包。其优点是工序比较集中,占用设备和人员少,但回弹难以控制,尺寸和形状不精确,表面擦伤严重。
综合上述,该零件虽然对表面外观要求不高,但由于“腿”特别长,需要有效地利用过弯曲和校正来控制回弹,其方案三和方案六都能满足这一要求,但考虑到该零件件生产批量不是太大,故选用方案三,其冲压工序如下:
落料冲孔、一次弯形(弯曲端部两角并使中间两角预弯45°)、二次弯形(弯曲中间两角)、冲凸包。
⒊主要工艺参数计算
冲裁力
式中L—剪切长度;