PCBA新产品试生产控制流程--范文
pcba产品开发流程

pcba产品开发流程PCBA(Printed Circuit Board Assembly)是指将电子元器件焊接到印刷电路板上的工艺过程。
PCBA产品开发流程是指从产品需求到产品交付的整个过程。
本文将详细介绍PCBA产品开发流程。
一、需求分析阶段在PCBA产品开发的初期,需要与客户充分沟通,了解客户的需求。
通过与客户的交流,收集并整理客户的需求,明确产品的功能、性能、规格等要求。
同时,需要对市场进行调研,了解竞争对手的产品情况,为产品定位提供参考。
二、电路设计阶段在需求分析的基础上,进行电路设计。
电路设计包括原理图设计和PCB布局设计两个部分。
原理图设计是将需求转化为电路图,确定电路的连接方式和关系。
PCB布局设计是将原理图转化为PCB板的布局,确定各个元器件的位置和走线方式。
三、元器件采购阶段在电路设计完成后,需要进行元器件的采购。
元器件采购包括选择供应商、询价、样品测试等步骤。
在选择供应商时,需要考虑供应商的信誉度、产品质量、交货周期等因素,确保采购到符合要求的元器件。
四、PCB制造阶段在元器件采购完成后,进行PCB板的制造。
PCB制造包括制作工程图、下单、生产、检测等步骤。
制作工程图时,需要将PCB布局图转化为制作工艺图,确定PCB板的层数、材料、工艺等参数。
下单后,将工程图交给PCB制造商进行生产。
生产完成后,需要进行PCB板的检测,确保其质量符合要求。
五、元器件焊接阶段在PCB板制造完成后,进行元器件的焊接。
元器件焊接包括SMT (表面贴装技术)和DIP(插装技术)两种方式。
SMT是将小型元器件通过自动化设备焊接到PCB板上,而DIP是将大型元器件通过手工焊接到PCB板上。
焊接完成后,需要进行功能测试和质量检验,确保PCBA产品符合设计要求。
六、软件开发阶段在PCBA产品开发中,通常还需要进行软件开发。
软件开发包括嵌入式软件开发和上位机软件开发两个部分。
嵌入式软件开发是指为PCBA产品开发专门的控制程序,实现产品的各项功能。
新产品试产控制程序

5.6.2生产部经理根据生产提出的要求作以下确认。
5.6.2.1生产部经理根据试产阶段的情况对工艺流程合理性进行评估和确认。
5.6.2.2根据试生产阶段的情况评估设备能力能否满足产品精度要求,如无法达到技术要求要求,应提出相应制程能力水平,由业务部与客户沟通解决。
5.8试生产后的改善项目由生产部跟进落实执行。
6.0相关记录
6.1《会议记录》
6.2《生产指令单》
7.0相关文件
7.1《生产控制程序》
7.2《制程检验控制程序》
8.0流程图
新产品打样
NG
5.6.2.3确定需要的夹治具或者模具是否需改进。
5.6.2.4对试生产后相关材料使用结果的确认。
5.6.3品管部根据试生产阶段的检测报告将无法满足技术要求要求的相关异常情况说明,并讨论解决方案。
5.7试生产后会议内容各部门需记录在会议记录上,根据评审的结果由生产部技术小组判定是否同意批量生产,并签署自己的名字;如不同意批量生产,则需重新进行试产,直到试产合格为止。
深圳市XX电子有限公司
新产品试产控制程序
版本/版次:A/0
总 页 数:共 4 页
文件编号 :XX-QP-007
生效日期 :2008-06-06
区分
制定
审核
核准
发行印章
签名
温馨提示:本文件为本公司机密文件,未经许可,不得私自外借或复印!
修订记录
制定/修订日期
修订内容摘要
页次
版本/版次
总页数20XX-06-06来自新制订--A/0
4
1.0目的
为确保新的产品顺利生产,并满足客户要求,防止出现批量性不良,特制定本程序。
PCBA生产作业流程

PCBA生产作业流程2010-03-23 21:02:00| 分类:A TE测试|字号大中小订阅今天是实习的第一天,部门给我安排的Team Leader是俊哥。
开始俊哥带我到部门所在车间参观,让我熟悉车间环境以及产线的生产流程。
之后,他还详细地给我介绍了PCBA生产作业流程。
此次学习的内容大致总结如下一、SMT(Surface Mounted Technology)表面贴装技术1、放置PCB板,PCB板电路图一般由客户自己设计;2、印刷,其作用是将焊膏或贴片胶漏印到PCB的焊盘上,为元器件的焊接做准备。
所用设备为印刷机(锡膏印刷机),位于SMT生产线的最前端;3、贴装,其作用是将表面组装元器件准确安装到PCB的固定位置上。
所用设备为贴片机,位于SMT生产线中印刷机的后面;4、固化,其作用是将贴片胶融化,从而使表面组装元器件与PCB板牢固粘接在一起。
所用设备为固化炉,位于SMT生产线中贴片机的后面;5、回流焊接:其作用是将焊膏融化,使表面组装元器件与PCB板牢固粘接在一起。
所用设备为回流焊炉,位于SMT生产线中贴片机的后面;6、AOI检测,运用视觉处理技术自动检测PCB板上各种不同帖装错误及焊接缺陷。
二、DIP(Dual In-Line Package)双列直插式封装技术(即手插技术)1、插件,即焊接其它贴片机上无法安装的零件;2、过波峰焊,将胶、锡融化,此过程需添加松香助化剂,加快胶、锡融化;3、ICT测试,一种在线式的电路板静态测试设备,主要测试电路板的开短路、电阻、电容、电感、二极管、三极管、电晶体、IC等元件;4、ATE测试,类似于ICT测试,区别在于ATE可以进行上电后的功能测试;5、FCT测试,对测试目标板(UUT:Unit Under Test)加载合适的激励,测量输出端响应是否合乎要求。
位于ICT、ATE测试之后;6、FAE,对检测出现故障的PCB板进行返工,即检修NG板。
配置在生产线中任意位置。
pcba生产工艺流程物料管控

PCBA生产工艺流程物料管控引言PCBA生产工艺流程中的物料管控是确保电路板组装过程中所需的各类物料按照规定的质量标准和数量进行管理和监控的关键步骤。
物料管控的良好实施可以降低产品的生产成本,缩短生产周期,并确保最终产品的质量达到要求。
本文将介绍PCBA生产工艺流程中物料管控的主要内容和流程。
PCBA生产工艺流程PCBA(Printed Circuit Board Assembly)是一种通过将电子元器件和印刷电路板组装在一起完成电路布线和连接的工艺过程。
它涉及到多个步骤,包括物料采购、物料接收、物料存储、物料发料、工艺装配、测试等。
每个步骤都需要进行物料的管控,以确保物料的质量和数量符合要求。
物料管控流程物料采购物料采购是最开始的一步,它需要根据生产计划和需求清单,选择合适的供应商进行物料采购。
在采购过程中,需要关注物料的质量、价格、交货期等因素,并与供应商签订合同以确保供应的稳定性。
同时,还需对供应商的资质和信誉进行评估,以降低采购风险。
物料接收物料接收是将从供应商处购买的物料收到并进行检验的过程。
在接收物料时,需要进行验货和检查,确保物料的外观、规格、数量等与采购合同要求一致。
同时,还需要进行物料的初步质量把控,包括外观检查、尺寸测量、功能测试等。
物料存储物料存储是将接收到的物料进行暂时性的保管和管理。
在存储过程中,需要注意将不同物料按照规定的方式进行分类、标识和储存,以确保物料的可追溯性和整齐有序。
同时,还需要定期检查和清点存放的物料,以确保物料的完好无损和数量一致。
物料发料物料发料是将已经存储好的物料按照生产需求进行发放的过程。
在发料过程中,需要根据生产工艺和工单清单,准确选择所需物料并进行发放。
同时,还需要记录物料的发放数量和时间,并进行合理的物料跟踪和追溯,以便后续的生产过程能够顺利进行。
工艺装配工艺装配是将已经发放好的物料按照规定的工艺流程进行装配的过程。
在装配过程中,需要确保每个步骤的物料使用正确、数量准确,并按照指定的顺序进行装配。
新产品试产工艺流程【范本模板】

新产品试产工艺流程一.工艺准备:1 )2)工艺输出文件:BOM文件:、附件(产品)BOM等。
PCBA托工:(长、宽、厚、拼接方式等)PCB贴片图:提供单板尺寸、置PCBA.二.工艺内部评审:1)工艺文件评审:评审有无缺陷的地方。
需要改善的地方2) 首板样机内部评审:评审电路板及样机是否有设计隐患和不合理设计。
3) 工装夹具评审:评审工装夹具设计和审批周期及内部手续.4) 了解PCBA外协加工情况,确认其对后续的组装及调试是否有影响。
如有需要则在试产准备会上通报,并商定出处理措施。
试产前工艺评审会要以邮件的形式发出会议记录.三、试产准备会确认内容1、明确试产目标:2、确定试产性质试产性质包括:1) 客户要求/新机种2) 更换供应商3)设计变更/工程试做4)常规实验5) 工程实验6)增加模具/工程试做7)其他3、参考图纸、BOM表、工艺文件:工艺部在工艺文件完成后内部召开试产前工艺评审会整合信息在试产准备会上做通报。
4、物料齐套性确认——-计划部通报物料齐套情况。
包括生产备料后的报缺及缺料到货日期等信息。
5、IQC来料检验情况:数据内容包括不良问题的问题点,判定结果,判定人。
(方便后期组装时对接受不良品的验证及影响产品装配情况的判定)。
6、工装、设备调配情况--—生产部根据生产配置表评估满足情况。
7、人员调配情况--—生产部根据生产配置表评估满足情况。
8、项目成员试产工作分工:工艺协同硬件提供调试、测试技术支持。
工艺协同结构提供装配技术支持。
9、试产计划:根据试产准备会时确认的时间做出试产计划,以邮件的形式发给各项目成员。
试产计划内容包括人员培训时间:生产部调配时间(正式试产前)试产开始时间:生产部按排期确定试产时间首件检验时间(QA估算):试产总时间(PE估算):试产总结会时间(PE估算):试产准备会要填写《签到表》,会后发出<〈试产准备会会议纪要>〉,相应的问题对未完成跟踪项确定计划完成时间和实际完成时间,对相应负责人跟踪完成进度.并在试产前一天发出通报,说明延误原因及计划完成时间生产部针对计划完成时间重新确定试产时间。
新产品开发管控流程【模板范本】

新产品开发管控流程由于我司新产品日渐增多,客退、投诉问题也是越来越多,此问题困扰公司各管理人员、及工程师,同时也严重影响了公司的声誉,给公司也造成了较大的负面影响。
诸此,为了有效的改善新开发产品的可靠性、可操作性、可生产性等等问题,工程部于2012年开始进行新开发产品管控流程调控,具体内容以下细述。
1、新电源类灯具产品,分三步走,第一步,为开发期,周期为2~3个月(视产品的难易度),分二个阶段:第一个阶段,为设计初期,周期为1~1。
5个月;第二阶段,为调整、试验期,周期为1~1.5月。
第二步,为失效试验、认证调整期,周期为5个月.第三步,小批量投产期.2、灯具产品,电源部分不定制。
不接受定制订单。
3、电源产品一旦通过认证后,物料品牌不能再修改。
开发期开发期第一阶段接到开发指令后,召集相关技术人员参加产品的开发评审会议,对产品的结构的配合问题、电性问题、光学、热学问题做一个综合性的评估。
评估通过后,相关工程师做相关部分的方案设计、物料选型等工作.方案、物料确认后,需召集采购协助报价、核算成本,评估方案所涉及到的物料采购成本、风险等,一切就绪即开始相关设计工作。
PCB设计回来后需要进行制做、调试、测试、老化等试验。
首先由工程技术员与开发工程师进行制样、调试、测试、老化等,如果没有异常,交接于工艺组人员分别进行不同的试验评审工作。
最后将此产品的改善意见汇总,给开发工程师参考整改。
开发期第二阶段第一阶段圆满完成后,就进行第二阶段,设计工程师据第一阶段的评审建议,修改图纸、资料.新的PCB 物料齐后,及时制样、调试、各项测试后,一切正常就需要进入可靠性试验等工作中去。
一切试验OK 后,需要再次召开产品性能的评审会议,会议通过便进入下一阶段。
失效试验、认证调整期此阶段主要是对产品进行长达5个月的失效试验,并在此阶段需进行产品的认证整改工作。
“失效试验、认证调整期”按照试验3000小时失效期为期限,并分为三个阶段,每个阶段为1000小时。
PCBA NPI新产品导入控制流程--范文

PCBA NPI新产品导入控制流程--范文1 目的1.1 建立NPI新产品在设计阶段至量产阶段,试产过程的标准流程。
1.2 明确新产品导入过程中,各单位的工作职责。
1.3 确保产品在量产过程顺畅,品质得到保证。
2 范围2.1 本程序(新产品导入作业程序,以下简称NPI process)适用于公司所有产品试产的管理控制。
2.2 本程序规范适用于,新产品在设计阶段至量产阶段试产的标准流程。
通过标准流程的建立,能确保量产后品质的保证。
一般NPI需有二个阶段。
2.2.1 MVT 阶段(工程验证阶段:Manufacturing Verification Test Phase)2.2.2 PVT 阶段(小批量验证阶段:Pilot-run Validation Test Phase)2.3 NPI 可以依实际产品开发要求适当调整,并非所有新产品导入都必需执行NPI process的试产流程。
2.4 标准的参考建议:2.4.1 对于全新ODM产品,应需实行NPI process 的作业流程。
2.4.2 对于已有产品而衍生的产品,可调整NPI所需的试产流程并确实执行。
NPI新产品导入3权责3.1 (产品中心)PM3.1.1 负责提供需要试产产品的样机和整套的开发文件。
3.1.2 负责主导试产阶段前所有工作,及试产工作交接。
3.2 (文控中心)DCC负责开发文件的发放,登记,回收和管制工作,保证文件的准确性和有效性。
3.3 (工程)ENG3.3.1 负责可制造性评估,工艺文件制作,确认生产layout,确定试产方案。
3.3.2 主导PFMEA制定,及改善跟进。
3.3.3 负责测试治具制作,生产设备调试。
3.3.4 负责Test程式调试及Test设备架设,测试文件,数据提供。
3.3.5 试产成本统计与分析3.4 (品管)QA3.4.1 试产所需的物料品质状况的检验。
3.4.2 检验试产过程中的产品质量控制状况。
3.4.3 试产产品的验证、出货检验控制和中试认证安排。
PCB电路板产品生产管理制度及流程

PCB电路板产品⽣产管理制度及流程产品⽣产管理⼀、公司⽣产管理制度第⼀章总则第⼀条、为了合理利⽤公司⼈⼒、物⼒及财⼒资源,进⼀步规范公司管理,使公司⽣产持续进步⽅向发展,不断提⾼企业竞争⼒,参考国家相关法律法规,根据公司实际情况制定本制度。
第⼆条、⽣产管理是公司经营管理的重点,是企业经营⽬的实现的重要途径,⽣产管理包括物料管理、⽣产过程管理、质量管理、⽣产安全管理以及⽣产资源管理等。
第三条、本制度是公司⽣产管理的依据,是⽣产管理的最⾼准则。
第四条、本制度适⽤于公司全体⽣产⼈员、⽣产管理员以及与⽣产相关的其他⼈员。
第五条、由总经理负责本制度实施监督。
第六条、本制度总经理签署后,公布施⾏,⾃公布之⽇⽣效,本制度效⼒⼤于公司同类制度。
第七条、本制度修订版公布时,本制度⾃动失效。
第⼆章物料管理第⼀条、物资控制是⽣产管理的先决条件,是⽣产管理的重点,合理的物资控制可以产⽣⾼效率,⾼利⽤率是⽣产前提,物资控制是否合理直接关系到⽣产是否顺畅,物料浪费严重与否和⽣产成本的⾼低。
第⼆条、物料供应部门是物资控制的核⼼部门。
1、物料供应部门下设材料仓库、⼯具仓库、辅助品仓库;2、材料仓库是公司原料的储存机构,负责公司原材料的收发和储存;3、⼯具仓库是公司⽣产⼯具、夹具、模具的储存收发机构。
⼯具、夹具、模具的维护和保养由维护保养机构负责;4、辅助品仓库是公司劳保⽤品、⽂具⽤品的储存机构,负责公司劳保⽤品、⽂具⽤品的收发和储存。
第三条、外协⼯⼚有物品⼊库应先由质检⼈员进⾏检验。
检验合格的物品⽅可⼊库,办理相关⼿续。
检验不合格的物料即超出允许标准的物料,应予以退回。
第四条、仓库员在新进物资⼊库后要及时做好标⽰,同时做好物资的维护保养⼯作。
仓库的物资要与账⽬相符,要不定期对物资进⾏盘点抽查,抽查结果作为仓库员的考核依据。
第五条、车间或其他⼈员领取物资必须出具《领料单》,《领料单》各栏要填写清楚。
领取⽣产材料、⼯具、夹具、模具,车间主任开单后不需要部门经理审核,领取劳保⽤品、办公⽤品等均需部门经理审核签署后⽅可领取。
PCBA新产品试生产控制流程--范文

PCBA新产品试生产控制流程—范文1、试产前的项目进展安排:1.1公司在获得任何有意向合作客户的新项目之后,由PMT和工程部协商指定一个项目负责人来协调负责该项目的整个生产、交付、服务及信息联络沟通等活动。
1.2 针对某个新产品项目,与客户洽谈协商之后,项目负责人应制订1份项目导入计划以明确项目导入时所需实施的各项活动。
1.3 在试产前8天项目必须将客户资料(含BOM.GERBER.坐标文件.PCB.样机.装配图.生产及测试要求等)全部接收与消化。
新产品试产1.4 试产前7天相应PE工程师需召开产前会议简单介绍新产品的SPEC、Schedule及项目达成目标(必要时请客户一起参加),并与负责各制程的工程师就新品导入过程中的重、及难点进行评估和确定解决方案。
对各项试产要求的准备状况予以安排、落实,并视准备状况与PMT决定试产的时间和计划。
会议记录根据<<新产品生产准备会议纪要>>填写,项目工程师或技术员应作为整个试产活动的项目负责人,负责协调、跟踪、掌握整个试产状况。
1.5 项目PE需在试产前3天将工程文件准备(GERBER 、BOM、丝印图、原理图、MS、样品、测试要求及测试配件等全部发放完毕)并组织相关工程师对各工序生产能力进行评估(NPI评审小组)。
1.6 MC确认物料状况并按排备料,PE再次确认文件和治具等情况。
1.7 PC:根据物料情况及PE确认的文件、治、工具情况和出货需求给出具体的生产计划。
2、新产品试产过程的控制:2.1 SMT:根据生产计划进行备料、调试SMT程序、炉温、准备过炉治具、钢网及辅料,并对试产产品做好编号监控。
试产完成后必须在试产Buglist中如实记录各工站的实际生产条件、工艺参数,并对自身制程不良问题点做出分析改善,给出有效的临时改善对策和长期的纠正预防措施!对涉及到与来料品质及客户设计有关的部分及时反馈给QE和PE,以作为试产总结和后续产品品质改善的主要依据;试产结束后将试产总结报告及时反馈给项目PE统一汇总,并跟进反馈的问题点在试产下一阶段和首次量产中有无改善。
PCBA主板生产流程
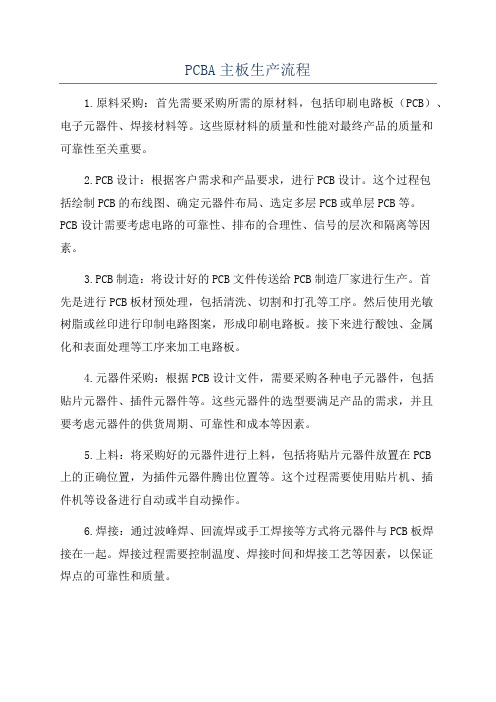
PCBA主板生产流程1.原料采购:首先需要采购所需的原材料,包括印刷电路板(PCB)、电子元器件、焊接材料等。
这些原材料的质量和性能对最终产品的质量和可靠性至关重要。
2.PCB设计:根据客户需求和产品要求,进行PCB设计。
这个过程包括绘制PCB的布线图、确定元器件布局、选定多层PCB或单层PCB等。
PCB设计需要考虑电路的可靠性、排布的合理性、信号的层次和隔离等因素。
3.PCB制造:将设计好的PCB文件传送给PCB制造厂家进行生产。
首先是进行PCB板材预处理,包括清洗、切割和打孔等工序。
然后使用光敏树脂或丝印进行印制电路图案,形成印刷电路板。
接下来进行酸蚀、金属化和表面处理等工序来加工电路板。
4.元器件采购:根据PCB设计文件,需要采购各种电子元器件,包括贴片元器件、插件元器件等。
这些元器件的选型要满足产品的需求,并且要考虑元器件的供货周期、可靠性和成本等因素。
5.上料:将采购好的元器件进行上料,包括将贴片元器件放置在PCB上的正确位置,为插件元器件腾出位置等。
这个过程需要使用贴片机、插件机等设备进行自动或半自动操作。
6.焊接:通过波峰焊、回流焊或手工焊接等方式将元器件与PCB板焊接在一起。
焊接过程需要控制温度、焊接时间和焊接工艺等因素,以保证焊点的可靠性和质量。
7.检测和测试:对已焊接好的PCBA主板进行检测和测试,以确保组装的质量和性能。
这个过程涉及X光检测、AOI(自动光学检测)、ICT(插件测试)等多个环节,以发现潜在的电路问题和焊接质量问题。
8.组装和调试:对已测试合格的PCBA主板进行组装和调试。
这包括安装外壳、键盘、显示屏等组件,并进行软件调试和功能测试等。
同时,也要进行外观检测和性能验证。
9.包装和交付:将已经组装和调试好的PCBA主板进行包装,包括防静电包装、气泡袋包装等,以确保运输过程中的安全和可靠。
最后将产品交付给客户。
总结:PCBA主板生产流程包括原料采购、PCB设计、PCB制造、元器件采购、上料、焊接、检测和测试、组装和调试、包装和交付等多个环节。
小批量试生产控制流程--范文

小批量试生产控制流程一范文1.0目的1.01使设计的新产品、采购新物料得到有效、合理的验证;1.02小批量SMT贴片加工能够有序的进行'并为后续产品量产提供保障;2.0范围适用于本公司新产品、研发工程变更、品质来料改善和实验、新供应商、新材料及验的验PE部试证。
3.0职责3.1生产部3.1.1负责进行小批量SMT贴片加工的人员安排及产品生产;3.1.2小批量SMT贴片试产中对产品问题点的提出;3.1.3试产产品中各项不良数据的统计。
3.2 PE 部3.2.1负责SMT贴片小批量试产前工装治具的提供;3.2.2试产初期《作业指导书》的拟定;3.2.3试产中产品问题点的分析与解决;3.2.4试产过程中各项数据的收集整理。
3.3品质部3.3.1负责小批量SMT贴片试产的跟踪与检验;3.3.2试产中品质标准的判定及确认,总结会议上品质问题的矢闭;3.3.3试产产品可靠性实验的申请及跟进;3.3.4试产产品可靠性实验及数据提供。
3.4 物控部3.4.1负责小批量贴片试产的时间安排;3.4.2试产物料准备;3.4.3《生产指令单》的下达;3.4.4负责组织相矢部门对未定型产品的评估。
3.5采购部3.5.1负责SMT小批量贴片试产物料的采购;3.5.2新材料供应商的引入,承认发起;3.5.3试产所需材料的购买;3.6研发部3.6.1负责试产总结会议的召幵;362提供技术支持,参与小批量试产过程跟进及制程问题的分析与处理;363SMT小批量贴片加工可靠性试验不良的处理;3.6.4小批量试产总结报告中的研发问题处理;3.6.5 SMT小批量贴片加工过程中涉及到设计方面的申请及变更。
3.6.6试产进程中全线跟进。
4.0定义无5.0工作程序5.1接到SMT小批量贴片加工试产的申请(申请部门:研发部品质部采购部\PE部)5.1.1新产品的试产、设计工程变更,由研发部提出申请;5.1.2已批量过的新材料更换的验证,由采购部提出申请;5.1.3品质部来料改善、实验验证,由品质部提出申请及试产跟进:5.1.4 PE部实验验证,由PE部提出申请;5.1.5未定型产品SMT小批量贴片加工试产的验证,由物控部召集研发、工程、品质、市场、采购等部门参与评审其进程状态、物料保证、工艺保证、生产过程控制等,明确责任人及具体的时间要求,形成会议记录并由各部门具体落实,物控部负责过程跟进及确认;5.1.6当小批量试产提出部门填写完《小批量SMT贴片试产申请单》,经市场部回复订单状况、厂长/总经理对《小批量SMT贴片试产申请单》上的内容审核批复通过后,复印交给研发、PE、品质、物控、采购、生产、市场、厂长/总经理等部门。
pcba板控制计划中英文描述

pcba板控制计划中英文描述English:The PCBA board control plan is a detailed document outlining the specific process and procedures for monitoring and managing the production of printed circuit board assemblies (PCBAs). The plan includes a range of factors such as equipment maintenance, environmental controls, and quality control measures to ensure the consistent and reliable production of PCBAs. It details the specific steps for inspecting, testing, and validating the PCBA components, as well as the protocols for addressing any issues or deviations that may arise during the production process. The control plan also outlines the responsibilities of various team members and stakeholders involved in the production and quality control of PCBA boards, as well as the methods for documenting and communicating any changes or updates to the control plan.中文翻译:PCBA板控制计划是一份详细的文件,详细说明了监测和管理印刷电路板组装(PCBA)生产的具体流程和程序。
PCBA品质控制流程图范例
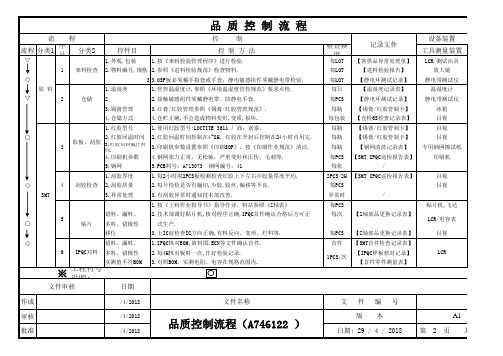
3
取板、刮胶 3.红胶启封截止时 间.
3.印刷机参数设置参照《印刷SOP》,按《印刷作业规范》清洁.
4.印刷机参数 4.钢网张力正常,无松驰,严重变形和压伤,毛刺等.
5.钢网
5.PCB料号:A713073 钢网编号:41
1.刮胶厚度
1.每2小时取2PCS板检测检查红胶上下左右中胶量厚度平均.
◇
4 刮胶检查 2.刮胶质量
▽
2
仓储 2
2.接触敏感组件须戴静电带、防静电手套.
3.锡膏管理
3.红膏/红胶管理参照《锡膏/红胶管理规范》.
4.仓储方式
4.仓贮正确,不会造成物料变形,变质,损坏.
1.红胶型号
1.使用红胶型号:LOCTITE 3611 厂商:诺泰.
○
2.红胶回温时间 2.红胶回温时间控制在4~8H. 红胶在开封后控制在24小时内用完.
每张
/
2PCS/2H 【SMT IPQC巡检报告表】
每PCS
异常时
/
每PCS
每次 【Z轴部品更换记录表】
设备装置 工具测量装置
LCR/测试治具 放大镜
静电带测试仪 温湿度计
静电带测试仪 冰箱 目视 目视 目视
专用钢网擦试纸 印刷机
目视 目视
贴片机,飞达
LCR/电容表
每PCS 首件
1PCS/次
【Z轴部品更换记录表】 【SMT首件检查记录表】 【IPQC样板核对记录】
【首件零件测量表】
目视 LCR
文件编号 版本
日期: 29 / 4 / 2018
A1 第2页 共5页
负责部门
IQC IQC IQC 货仓/IQC 货仓 货仓 货仓 生产 生产 生产 生产/IPQC
PCBA车间工艺流程及管控

PCBA车间工艺流程及管控PCBA(Printed Circuit Board Assembly,印刷电路板装配)车间的工艺流程及管控主要包括以下几个方面:物料准备、质量管控、工艺流程、设备维护和人员管理等。
一、物料准备:1.确定所需的PCB板、元器件和焊接材料,并进行采购;2.对采购的物料进行检查和筛选,确保与工艺要求相符;3.对物料进行登记、分类和存储,确保物料的可追溯性;4.制定物料供应商的评估和选择标准,保证物料的质量和稳定性。
二、质量管控:1.制定相关的质量管理制度和流程,并严格执行;2.对物料进行入厂检验,确保物料的合格率;3.制定可靠的质量检测方法和标准,确保生产过程中的质量;4.对生产过程进行质量监控和记录,及时处理质量问题;5.建立质量回溯和纠正措施,确保不良品不流入下道工序。
三、工艺流程:1.根据产品的特点和要求,制定相应的工艺流程,并进行评审和确认;2.对工艺流程中的每个工序进行详细的操作规范和工艺参数设置;3.对生产过程进行监控,确保每个工序和操作符合工艺要求;4.对关键工序和工艺参数进行实时监控和调整,以保证产品质量;5.建立工艺记录和文件,便于溯源和不断改进。
四、设备维护:1.定期对设备进行检修和保养,确保设备的正常运转;2.制定设备故障和维护预防计划,及时处理设备故障;3.建立设备维修和更换记录,便于分析和改进设备维护工作;4.对设备操作人员进行培训和考核,确保正确使用和保养设备。
五、人员管理:1.建立人员岗位培训计划和体系,确保生产人员具备相应的技能和知识;2.制定生产人员操作规范和工作指导,确保操作的一致性和规范性;3.对生产人员进行实时监控和考核,及时发现问题并进行改进;4.建立相应的奖惩机制,激励员工积极性和责任心。
综上所述,PCBA车间的工艺流程及管控需要从物料准备、质量管控、工艺流程、设备维护和人员管理等方面进行全面掌控,以确保产品的质量和稳定性。
只有将每个环节都严格把控,才能提高PCBA产品的生产效率和质量水平。
新产品试产控制程序

1.0制定新产品生产程序、管理项目,严格控制产品品质,为新产2.0适用于新产品形成过程的试产作业,包括:搪胶、制模、注塑、3.0(1)负责参与新产品的设计及其模具制作、修改及其品质控制、采购(2)负责客户(人)(1)负责客户(人)提供新产品搪(2)(1)(2)质要求、作业指(4)负责新产品试产的技术指导(除制模外)(1)(2)(3)负责新产品试产的各类样●QA(1)(2)(3)4.0作”及“模具制作指引”)●如果客户提供的是新注塑模,则由搪胶部经登记后试产,并将产品●注塑部接到制模部移交的新模具后,根据生产部的“试产通知单”进行●工程部接到注塑和搪胶的试产的产品后进行试装与相关测试,并将其结果以书面报告形式交厂长/经理核准,同时提出改良意见。
●除制模技术文件外,其余新产品涉及的所有文件与资料,包括技术●所有新产品样板的确认程序根据文件:“样板制作及控制”要求进行。
●新产品物(材)料经工程部确认(即对规格、材质、编号等方面确认)后●新产品来料投入试产前须经IQC●新产品在进行试产时,工程部有关人员到现场作技术指导,收集及改进存在问题。
同时各相关部门在试产时,将不良品质情况反映或填写于《新产品试●工程部对试产的半成品进行功能、安全等方面测试,并记录其测试●QA部对试产的最终成品进行全面测试和相关实验,包括:功能、安全、寿命、可靠性等各方面测试与试验,并记录测试数据和提出改●试产的最终成品经QA部作全面测试与实验合格后,再由生产部送客户作最终确认,如果确认合格则可正式投产;如不合格需要修改和改进时,由工程部主导执行。
●新产品试产的数量以100套(只)5.0●《6.0。
pcba电路板生产工艺流程

pcba电路板生产工艺流程PCBA电路板生产工艺流程是指在电路板设计完成后,通过一系列的加工工艺和流程来制造出符合要求的电路板产品。
下面将详细介绍PCBA电路板生产工艺流程。
第一步,电路板设计。
首先根据产品的需求和功能要求,进行电路板的设计。
设计师根据电路功能模块的布局,将各个元器件的引脚连接起来,并合理地布置在电路板上。
第二步,元器件采购。
根据设计好的电路板布局,设计师将设计图纸交给采购部门,采购部门根据设计图纸上的元器件清单,进行元器件的采购。
采购人员需要选择合适的元器件供应商,并确保元器件的品质和性能符合要求。
第三步,钢网制作。
钢网是用于印刷电路板上的焊膏的一种模具,可以精确地控制焊膏的涂布量和位置。
钢网制作一般采用化学腐蚀或激光切割的方式,将钢网制作成与电路板布局一致的形状。
第四步,印刷焊膏。
在电路板上印刷焊膏是为了在后续的贴片焊接过程中,使元器件能够精确地贴合在电路板上。
印刷焊膏一般采用丝网印刷的方式进行,将焊膏均匀地印刷在电路板的焊盘位置上。
第五步,贴片。
在印刷好焊膏的电路板上,将元器件进行贴片焊接。
贴片机通过吸嘴将元器件从料带上吸起,然后精确地放置在电路板上的焊盘位置上。
贴片机的操作需要精确的控制和调试,以确保元器件的贴合度和位置的准确性。
第六步,回流焊接。
在贴片完成后,需要进行回流焊接。
回流焊接是将电路板送入回流焊炉中进行加热,使焊膏熔化并与焊盘和元器件的引脚形成可靠的焊接。
回流焊接温度和时间需要根据焊膏和元器件的要求进行调整和控制。
第七步,清洗。
在回流焊接完成后,需要对电路板进行清洗,去除焊接过程中产生的焊剂残留物和污染物。
清洗过程一般采用化学溶液或超声波清洗的方式,确保电路板表面的干净和良好的导电性能。
第八步,功能测试。
在清洗完成后,对电路板进行功能测试。
功能测试是为了验证电路板的各个功能模块是否正常工作,是否符合设计要求。
功能测试可以通过专用的测试设备或程序来进行。
第九步,包装和出货。
新产品试生产流程办法(参考模板)

新产品试生产流程办法一、目的:1.1、为确保开发的新产品能够提高公司效益,满足市场需求。
1.2、保证新产品能顺利批量生产。
1.3、保证生产产品质量、工艺稳定,效率最高、成本最低等。
二、适用范围:2.1、本试生产流程办法适用于公司总部及各下属公司(基地)三、新产品的定义3.1、采用新技术,新设计研制生产的全新产品或在结构、材质、工艺等比原有产品有明显改进,使产品性能或功能改进,满足客户新的需求。
四、新产品试生产流程图如下:五、职责5.1、各下属公司(基地)申请,提交试生产新产品的报告,并拿出试生产的可行性方案,交公司总部进行会审。
(会审单位:生产部、技术中心、机电部、物资管理中心、财务部、销售总公司)5.2、技术中心5.2.1、负责新产品的整个技术研发过程技术、工艺设计,质量、成本预测等资料的准备,并进行试生产指导工作。
5.2.2、负责落实对新产品试生产过程中的监督和检验,制定新产品检验标准。
5.2.3、对各下属公司(基地)新开发的纸样进行技术指标验收检查,并出具《新产品测试报告》。
5.3、生产部5.3.1、负责对技术中心制定的技术、工艺设计,质量、成本预测,等资料等进行评审、验证、确认,生产过程中各项质量、工艺、效率、成本的全程跟踪落实解决。
5.3.2、负责落实整个试生产过程出现影响质量及效率的问题反馈,如:生产质量、成本、工艺问题、影响生产操作问题,试产完成后编制《试生产报告单》。
5.4、采购部5.4.1、根据试生产数量,下单采购生产所需相关物料。
5.4.2、按照《试生产报告单》及时将所需物资采购到位,并做月度生产计划物料采购需求。
5.5、机电部5.5.1、对满足新产品生产需求技改方案审核,组织生产部、技术中心、机电部确认通过,并报公司生产副总审批。
5.5.2、按照技改方案组织人员实施技改。
5.6、销售总公司5.6.1、对新产品的选择性试用,跟踪使用效果,出具使用效果说明。
5.6.2、对新产品进行市场调查,出具新产品的市场定价。
PCBA新产品试生产控制流程--范文

PCBA新产品试生产控制流程—范文1、试产前的项目进展安排:1.1公司在获得任何有意向合作客户的新项目之后,由PMT和工程部协商指定一个项目负责人来协调负责该项目的整个生产、交付、服务及信息联络沟通等活动。
1.2 针对某个新产品项目,与客户洽谈协商之后,项目负责人应制订1份项目导入计划以明确项目导入时所需实施的各项活动。
1.3 在试产前8天项目必须将客户资料(含BOM.GERBER.坐标文件.PCB.样机.装配图.生产及测试要求等)全部接收与消化。
新产品试产1.4 试产前7天相应PE工程师需召开产前会议简单介绍新产品的SPEC、Schedule及项目达成目标(必要时请客户一起参加),并与负责各制程的工程师就新品导入过程中的重、及难点进行评估和确定解决方案。
对各项试产要求的准备状况予以安排、落实,并视准备状况与PMT决定试产的时间和计划。
会议记录根据<<新产品生产准备会议纪要>>填写,项目工程师或技术员应作为整个试产活动的项目负责人,负责协调、跟踪、掌握整个试产状况。
1.5 项目PE需在试产前3天将工程文件准备(GERBER 、BOM、丝印图、原理图、MS、样品、测试要求及测试配件等全部发放完毕)并组织相关工程师对各工序生产能力进行评估(NPI评审小组)。
1.6 MC确认物料状况并按排备料,PE再次确认文件和治具等情况。
1.7 PC:根据物料情况及PE确认的文件、治、工具情况和出货需求给出具体的生产计划。
2、新产品试产过程的控制:2.1 SMT:根据生产计划进行备料、调试SMT程序、炉温、准备过炉治具、钢网及辅料,并对试产产品做好编号监控。
试产完成后必须在试产Buglist中如实记录各工站的实际生产条件、工艺参数,并对自身制程不良问题点做出分析改善,给出有效的临时改善对策和长期的纠正预防措施!对涉及到与来料品质及客户设计有关的部分及时反馈给QE和PE,以作为试产总结和后续产品品质改善的主要依据;试产结束后将试产总结报告及时反馈给项目PE统一汇总,并跟进反馈的问题点在试产下一阶段和首次量产中有无改善。
- 1、下载文档前请自行甄别文档内容的完整性,平台不提供额外的编辑、内容补充、找答案等附加服务。
- 2、"仅部分预览"的文档,不可在线预览部分如存在完整性等问题,可反馈申请退款(可完整预览的文档不适用该条件!)。
- 3、如文档侵犯您的权益,请联系客服反馈,我们会尽快为您处理(人工客服工作时间:9:00-18:30)。
PCBA新产品试生产控制流程一范文
1试产前的项目进展安排:
1.1公司在获得任何有意向合作客户的新项目之后,由PMT和工程部协商指定一个项目负
责人来协调负责该项目的整个生产、交付、服务及信息联络沟通等活动。
1.2针对某个新产品项目,与客户洽谈协商之后,项目负责人应制订1份项目导入计划以明
确项目导入时所需实施的各项活动。
1.3在试产前8天项目必须将客户资料(含BOM.GERBER.坐标文件.PCB.样机•装配图•生产及测试要求等)全部接收与消化。
新产品试产
1.4试产前7天相应PE工程师需召开产前会议简单介绍新产品的SPEC、Schedule及项目达成目标(必要时请客户一起参加),并与负责各制程的工程师就新品导入过程中的重、及难点进行评估和确定解决方案。
对各项试产要求的准备状况予以安排、落实,并视准备状况与PMT决定试产的时间和计划。
会议记录根据<<新产品生产准备会议纪要>>填写,项目工程师或技术员应作为整个试产活动的项目负责人,负责协调、跟踪、掌握整个试产状况。
1.5项目PE需在试产前3天将工程文件准备(GERBER、BOM、丝印图、原理图、MS、样品、测试要求及测试配件等全部发放完毕)并组织相关工程师对各工序生产能力进行评估(NPI评审小组)。
1.7 PC:根据物料情况及PE确认的文件、治、工具情况和出货需求给出具体的生产计划。
1.6 MC确认物料状况并按排备料,PE再次确认文件和治具等情况。
2、新产品试产过程的控制:
2.1 SMT :根据生产计划进行备料、调试SMT 程序、炉温、准备过炉治具、钢网及辅料,
并对试产产品做好编号监控。
试产完成后必须在试产Buglist 中如实记录各工站的实际生产条件、
工艺参数,并对自身制程不良问题点做出分析改善,给出有效的临时改善对策和长期的纠正预防措施!对涉及到与来料品质及客户设计有关的部分及时反馈给QE和PE,以作
为试产总结和后续产品品质改善的主要依据;试产结束后将试产总结报告及时反馈给项目
PE 统一汇总,并跟进反馈的问题点在试产下一阶段和首次量产中有无改善。
2.2 IE:根据SPEC、BOM及客户要求指导DIP、组装及包装加工工艺;同时要确认相应工装治具的准备状况,
提报 D I P 、组装及包装过程中的不良问题点,并对自身制程不良问题点做出分析改善,给出有效的临时改善对策和长期的纠正预防措施!涉及到与来料品质及客户设计有关的部分及时反馈给QE和PE,以作为新产品试产品质总结和后续产品品质改善的主要依据,试产结束后将试产总结报告及时反馈给项目PE统一汇总,并跟进反馈的问题点在试产下一阶段或首
次量产中有无改善,试产完成 3 个工作日内要输出相应的技术支持文件(如SOP)
2.3 QE :根据品质管控要求进行检验并记录试产状况,如是试产光电产品还必须输出实验室
的相关测试文件。
试产过程的控制
2.4 PE:确认软件版本,准备烧录治具及程序;同时根据板卡的技术特性及客户的测试要求,现场指导测试并
对测试不良板卡进行分析与维修,判定责任归属并及时反馈给相关责任人进行确认。
以作为新产品试产品质总结和后续产品品质改善的主要依据,试产结束后将试产总结报告及时反馈
给项目PE统一汇总,并跟进反馈的问题点在试产下一阶段首次量产中有无改善,试产完成3个工作日内要输出相应的技术支持文件(如SOP)
2.5试产小组:根据工程要求及试产计划提前准备、确认相应物料及治工具状况。
负责新机种非SMT 工序外的试产及工程试组物料的准备管控、机台组装、附件加工、样机生产出及机台管控与统计,反馈试产机台状况。
要求主导部门给出处理意见及时存仓,记录每台机器的状况和数量。
在试产过程中发现不良机台,PP线领班应第一时间知会相关工程师到产线
现场分析,对试产工单的结案工作负责。
3、试产总结报告的输出:
3.1新机种各工序试产结束后,各工序试产负责人必须在24H内将各自的试产问题点及改善
对策汇总在试产Buglist中并提交给该机型的项目负责人。
3.2试产问题点的回复:厂内制程不良部分,由各工序的试产负责人负责回复短期和长期的改善对策。
来料不良部分,由品质部QE回复。
涉及到需要客户配合改善(如设计等)的部
分由项目PE负责回复,且要重点跟进客户的改善落实状况。
负责该机型的项目负责人须评估改善对
策的有效性和可执行性。
3.3试产总结报告由负责新品的项目PE依据各工序反馈的信息在试产结束后48H内汇总完成,试产总结报告中必须要体现所有问题点的短期和长期的改善对策。
任何机型的试产总结
报告必须要经该机型总的项目负责人和工程部主管审核后方可对内对外发出。
新产品试产总结
4、试产总结会的召开及试产结果判定:
1原则上,任何新机型试产结束后负责该机型的项目负责人必须要召开试产总结会(必要时可要求客户来参加)。
如试产过程中无重大设计问题、来料异常及厂内制程问题可经该机型
总的项目负责人、品质部QE及工程部主管同意后可不召开试产总结会,但必须将试产总结
报告和试产结果知会到相关责任部门和责任人。
2在试产总结会上,由机型项目负责人向与会人员重点介绍项目的试产状况及试产问题点的长短期改善对策。
每一个问题点都必须要有行之有效的改善对策、责任人、完成时间,项目PE要重点跟进改善对策的落实状况。
与会人员依据上述信息,判定该机型的试产结果并在纸档的试产总结报告上签署评审意见和姓名。
各方面全部确认试产0K的机型直接转入下一
阶段,判定试产不通过的机型试产总结报告要呈交公司副总经理签字。
由机型项目负责人联
系客户要求再次进行试产,如果客户强行要量产,必须要提供书面的要求出来,经我司高层批准后厂内再安排量产。
5、试产机型的出货:
1原则上,试产机型必须要走完全制程经品质部检验合格后方可出货给客户,如果客户有特
殊要求(如物料空贴、无须测试、产品有BUG让步接收等)或安排,必须要提供书面的请
求给负责该机型的项目PE。
项目PE要以书面形式(联络单或E-Mail )知会到厂内项目责任人和
品质部后方可安排出货。
试产报告的整理收集
6、试产报告的分发:
6.1试产总结会开完后,各部门会签OK的纸档试产总结报告由工程部存档。
电子档要发给
参入试产的各部门和各试产问题点的责任人,以便各部门重点跟进后续的改善状况(如涉及到来料问题的必须反馈给IQC)
7、试产转量产(Ready For Order )的准备:
7.1原则上,A类产品必须要EVT.DVT. PVT全过程走完0K后方可进入Ready For Order 状态。
(如EVT在客户端已完成,工厂可跳过EVT阶段。
B、C类产品必须要PVT验证OK后方可进入Ready For Order状态,D类产品由工程部项目PE主导测试OK后即可进入Ready For Order 状态。
7.2 试产OK 的机型就正式进入待量产( Ready For Order )的状态,在首次量产前项目PE
必须要确认各试产问题点改善对策的落实状况,如发现有未改善的问题点及时反馈给相关的责任人并要求改善。
7.3 试产OK 的机型方可进入各客户量产机型清单,PMT 在安排生产计划时必须要与量产机型清单进行核对,量产机型清单上没有的机型在排计划前必须先与工程部进行确认是否先进行试产,以避免在量产时出现批量性的质量事故。
8、首次量产阶段:
8.1 PMC :确认物料状况,如有异常请及反馈。
8.2 PMT: 依据物料状况和客户的出货需求开出首单生产工单和排程。
8.3 SMT: 根据具体的生产计划进行备料,并确认量产前的准备工作是否到位 (如贴片及AOI 程序、过炉载具、钢网、辅料等)。
8.4 DIP: SMT打板完成后将板卡转到DIP , DIP段按照IE发行的MPI进行加工生产,按照
QE 发行QII 进检验,将加工测试OK 的板卡进行安排入库动作。
8.5 组装MC :确认物料状况开出工单,DE 再次确认组装相应文件及治具准备状况。
8.6组装PC:根据物料及DE确认相应文件治具准备给出具体的系统试产组装排程。
8.7 仓库:根据工单进行备料给到产线物料组,物料组根据工单进行领料确认物料状况是否有缺料,同时将相应物料进行分别标示保管好待上线生产。
8.8 组装线:根据工程要求及计划前准备及确认,相应物料状况、治具准备的状况后安排上
线组装测试包装动作,生产组装时DE、IE、PE、QE 现场跟线确认及处理首次生产出现问
题。
8.9 根据客户的需求开始安排出货,首次量产顺利出货代表新产品导入成功完成。