渣油固定床加氢技术操作
渣油加氢操作规程
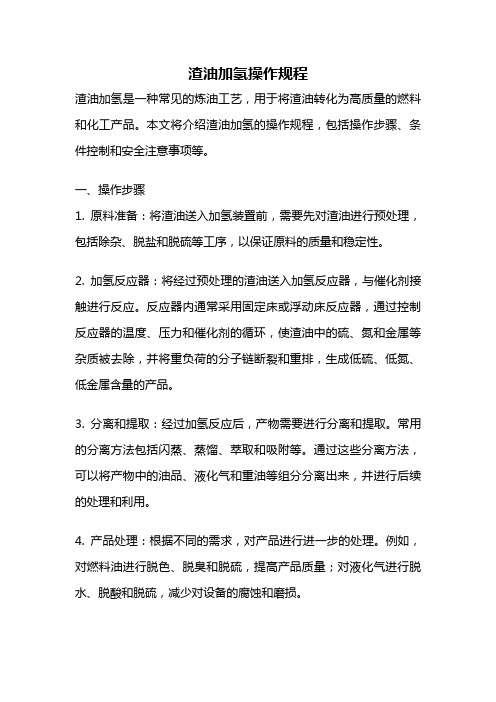
渣油加氢操作规程渣油加氢是一种常见的炼油工艺,用于将渣油转化为高质量的燃料和化工产品。
本文将介绍渣油加氢的操作规程,包括操作步骤、条件控制和安全注意事项等。
一、操作步骤1. 原料准备:将渣油送入加氢装置前,需要先对渣油进行预处理,包括除杂、脱盐和脱硫等工序,以保证原料的质量和稳定性。
2. 加氢反应器:将经过预处理的渣油送入加氢反应器,与催化剂接触进行反应。
反应器内通常采用固定床或浮动床反应器,通过控制反应器的温度、压力和催化剂的循环,使渣油中的硫、氮和金属等杂质被去除,并将重负荷的分子链断裂和重排,生成低硫、低氮、低金属含量的产品。
3. 分离和提取:经过加氢反应后,产物需要进行分离和提取。
常用的分离方法包括闪蒸、蒸馏、萃取和吸附等。
通过这些分离方法,可以将产物中的油品、液化气和重油等组分分离出来,并进行后续的处理和利用。
4. 产品处理:根据不同的需求,对产品进行进一步的处理。
例如,对燃料油进行脱色、脱臭和脱硫,提高产品质量;对液化气进行脱水、脱酸和脱硫,减少对设备的腐蚀和磨损。
二、条件控制1. 温度控制:加氢反应需要在一定的温度范围内进行,通常在300-450摄氏度之间。
温度过低会导致反应速率慢,温度过高则会引起催化剂的失活和热力学反应的副产物生成。
2. 压力控制:加氢反应需要一定的压力条件,通常在10-30兆帕之间。
高压可以促进反应速率和产物质量的提高,但同时也会增加设备成本和操作难度。
3. 催化剂选择:催化剂是加氢反应的核心,对反应效果起着决定性的影响。
选择合适的催化剂可以提高反应效率和产物质量,同时也需要注意催化剂的稳定性和寿命。
4. 氢气供应:加氢反应需要大量的氢气供应,通常通过压缩空气或氢气制备装置供应。
氢气的纯度和供应稳定性对反应效果和设备安全具有重要影响。
三、安全注意事项1. 加氢反应是一种高温、高压的化学过程,需要严格控制操作条件和设备安全性。
操作人员应穿戴好防护装备,严格遵守操作规程,确保人身安全。
渣油加氢工艺标准说明

第一节工艺技术路线及特点一、工艺技术路线300×104t/a渣油加氢脱硫装置采用CLG公司的固定床渣油加氢脱硫工艺技术,该工艺技术满足操作周期8000h、柴油产品硫含量不大于500ppm、加氢常渣产品硫含量不大于0.35w%、残炭不大于5.5w%、Ni+V 不大于15ppm的要求。
二、工艺技术特点1、反应部分设置两个系列,每个系列可以单开单停(单开单停是指装置内二个系列分别进行正常生产和停工更换催化剂)。
由于渣油加氢脱硫装置的设计操作周期与其它主要生产装置不一致,从全厂生产安排的角度,单开单停可以有效解决原料储存、催化裂化装置进料量等问题,并使全厂油品调配更灵活。
2、反应部分采用热高分工艺流程,减少反应流出物冷却负荷;优化换热流程,充分回收热量,降低能耗。
3、反应部分高压换热器采用双壳、双弓型式,强化传热效果,提高传热效率。
4、反应器为单床层设置,易于催化剂装卸,尤其是便于卸催化剂。
5、采用原料油自动反冲洗过滤器系统,滤除大于25μm以上杂质,减缓反应器压降增大速度,延长装置操作周期。
6、原料油换热系统设置注阻垢剂设施,延长操作周期,降低能耗,而且在停工换剂期间可减少换热器和其它设备的检修工作。
7、原料油缓冲罐采用氮气覆盖措施,以防止原料油与空气接触从而减轻高温部位的结焦程度。
8、采用炉前混氢流程,避免进料加热炉炉管结焦。
9、第一台反应器入口温度通过调节加热炉燃料和高压换热器旁路量来控制,其他反应器入口温度通过调节急冷氢量来控制。
10、在热高分气空冷器入口处设注水设施,避免铵盐在低温部位的沉积。
11、循环氢脱硫塔前设高压离心式分离器除去携带的液体烃类,减少循环氢脱硫塔的起泡倾向,有利于循环氢脱硫的正常操作。
12、设置高压膜分离系统,保证反应氢分压。
13、冷低压闪蒸罐的富氢气体去加氢裂化装置脱硫后去PSA回收氢气。
14、新氢压缩机采用二开一备,每台50%负荷,单机负荷较小,方便制造,且装置有备机。
170万吨、年渣油加氢装置操作法
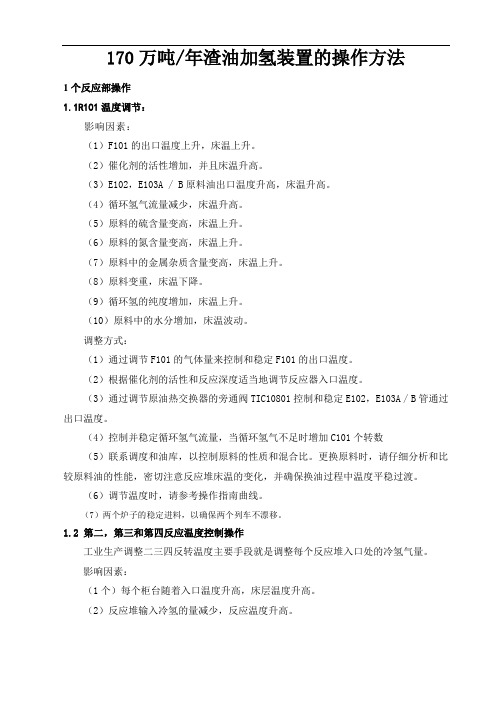
170万吨/年渣油加氢装置的操作方法1个反应部操作1.1R101温度调节:影响因素:(1)F101的出口温度上升,床温上升。
(2)催化剂的活性增加,并且床温升高。
(3)E102,E103A / B原料油出口温度升高,床温升高。
(4)循环氢气流量减少,床温升高。
(5)原料的硫含量变高,床温上升。
(6)原料的氮含量变高,床温上升。
(7)原料中的金属杂质含量变高,床温上升。
(8)原料变重,床温下降。
(9)循环氢的纯度增加,床温上升。
(10)原料中的水分增加,床温波动。
调整方式:(1)通过调节F101的气体量来控制和稳定F101的出口温度。
(2)根据催化剂的活性和反应深度适当地调节反应器入口温度。
(3)通过调节原油热交换器的旁通阀TIC10801控制和稳定E102,E103A / B管通过出口温度。
(4)控制并稳定循环氢气流量,当循环氢气不足时增加C101个转数(5)联系调度和油库,以控制原料的性质和混合比。
更换原料时,请仔细分析和比较原料油的性能,密切注意反应堆床温的变化,并确保换油过程中温度平稳过渡。
(6)调节温度时,请参考操作指南曲线。
(7)两个炉子的稳定进料,以确保两个列车不漂移。
1.2 第二,第三和第四反应温度控制操作工业生产调整二三四反转温度主要手段就是调整每个反应堆入口处的冷氢气量。
影响因素:(1个)每个柜台随着入口温度升高,床层温度升高。
(2)反应堆输入冷氢的量减少,反应温度升高。
(3)反应深度增加并且反应温度升高。
(4)原材料油性质对反应温度的影响与R101相同。
(5)催化剂的活性增加并且床温升高。
(6)循环氢的纯度增加,反应温度升高。
调整方式:(1个)通过监管每个柜台进口冷氢量调整输入口腔温度和床地板温度保持每张床的温度上升≯28℃。
(2)为了防止温度过度波动,温度调节范围应在0.5℃关于。
(3)将转换深度控制在设计范围内。
(4)原材料油当性质改变时,调节反应温度的方法与R101相同。
170万渣油加氢装置培训资料装置操作法
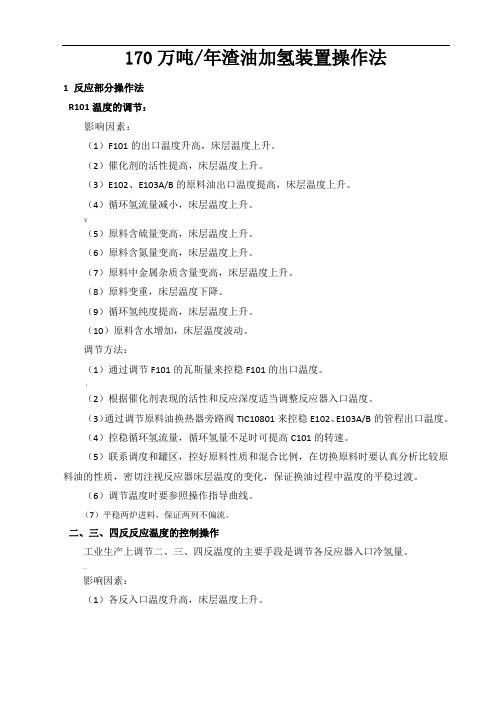
170万吨/年渣油加氢装置操作法1 反应部分操作法R101温度的调节:影响因素:(1)F101的出口温度升高,床层温度上升。
(2)催化剂的活性提高,床层温度上升。
(3)E102、E103A/B的原料油出口温度提高,床层温度上升。
(4)循环氢流量减小,床层温度上升。
¥(5)原料含硫量变高,床层温度上升。
(6)原料含氮量变高,床层温度上升。
(7)原料中金属杂质含量变高,床层温度上升。
(8)原料变重,床层温度下降。
(9)循环氢纯度提高,床层温度上升。
(10)原料含水增加,床层温度波动。
调节方法:(1)通过调节F101的瓦斯量来控稳F101的出口温度。
((2)根据催化剂表现的活性和反应深度适当调整反应器入口温度。
(3)通过调节原料油换热器旁路阀TIC10801来控稳E102、E103A/B的管程出口温度。
(4)控稳循环氢流量,循环氢量不足时可提高C101的转速。
(5)联系调度和罐区,控好原料性质和混合比例,在切换原料时要认真分析比较原料油的性质,密切注视反应器床层温度的变化,保证换油过程中温度的平稳过渡。
(6)调节温度时要参照操作指导曲线。
(7)平稳两炉进料,保证两列不偏流。
二、三、四反反应温度的控制操作工业生产上调节二、三、四反温度的主要手段是调节各反应器入口冷氢量。
…影响因素:(1)各反入口温度升高,床层温度上升。
(2)反应器入口冷氢量减小,反应温度上升。
(3)反应深度增大,反应温度上升。
(4)原料油性质对反应温度的影响与R101相同。
(5)催化剂的活性增加,床层温度上升。
(6)循环氢纯度提高,反应温度上升。
调节方法:(1)通过调节各反的入口冷氢量来调节其入口温度和床层温度,保持各床层温升≯28℃。
(2)为了防止温度波动过大,每次调节温度的范围应在0.5℃左右。
(3)控制转化深度在设计范围内。
(4)原料油性质变化时,反应温度的调节方法与R101相同。
(5)根据催化剂表现的活性和反应深度适当调整反应器入口温度。
固定床加氢工艺_概述说明以及解释

固定床加氢工艺概述说明以及解释1. 引言1.1 概述:固定床加氢工艺是一种在化学工业中广泛应用的重要技术,通过引入氢气来催化加氢反应,将有机物质转化为更有价值或更稳定的产物。
该工艺具有高效、低成本、环保等优势,在石油加工、化工合成、食品加工等领域得到了广泛应用。
1.2 文章结构:本文将分为五个部分进行阐述。
首先是引言部分,对固定床加氢工艺进行概述和说明。
接下来是固定床加氢工艺的概述,包括其基本原理、应用领域以及存在的问题和挑战。
然后是详细的固定床加氢工艺说明,包括相关的工艺步骤、设备与材料要求以及反应条件与控制策略。
紧接着是固定床加氢工艺的解释部分,包括催化剂选择与活性控制、反应机理与动力学分析以及优缺点和发展前景。
最后是结论部分,总结文章主要观点和结果,并对固定床加氢工艺的展望提出建议。
1.3 目的:本文旨在全面了解固定床加氢工艺,介绍其工艺原理、应用领域以及存在的问题和挑战,详细说明该工艺的步骤、设备要求、反应条件与控制策略,并解释相关的催化剂选择与活性控制、反应机理与动力学分析等内容。
同时,本文还将总结固定床加氢工艺的优缺点并展望其未来的发展前景,为相关领域研究人员提供参考和借鉴。
2. 固定床加氢工艺概述:2.1 工艺原理:固定床加氢工艺是一种常用的催化加氢方法,用于将有机化合物或气体通过与催化剂接触进行加氢反应,将其转化为相应的加氢产物。
该工艺基于固体催化剂的活性和选择性,在适当的温度、压力和反应条件下进行。
2.2 应用领域:固定床加氢工艺广泛应用于石油炼制、化学工业和环境保护等领域。
在石油炼制中,固定床加氢工艺可用于重质油的脱硫、裂解轻质烃的饱和、芳香族烃的脱芳等反应。
在化学工业中,该工艺可用于合成各种有机化合物,如醇类、酮类和羧酸类。
此外,固定床加氢还可以用于处理废水中的有机污染物和净化大气中的有害气体。
2.3 存在问题及挑战:尽管固定床加氢工艺具有许多优点,如操作灵活、反应效果稳定等,但也存在着一些问题和挑战。
固定床与流化床、悬浮床渣油加氢处理技术研究

固定床与流化床、悬浮床渣油加氢处理技术研究摘要:随着石油资源的日益减少和原油重质、劣化趋势的加剧,渣油加氢工艺是实现渣油清洁高效转化的关键技术,固定床渣油加氢工艺已成为渣油加工的重要手段。
根据渣油加氢工艺的反应原理,分析了固定床与流化床、悬浮床渣油加氢技术的应用,最后提出了固定床渣油加氢装置高效运行的保障措施。
关键词:炼油;固定床;流化床;悬浮床;渣油加氢工艺技术前言:渣油是原油蒸馏后其中的不理想组分、不理想杂质组成物,渣油的二次加工难度较大,多应用于炼油厂锅炉燃料,也可作为催化裂化装置的原料。
渣油内有较高的硫、氮、残碳和重金属,如果不做处理,燃烧后会产生大量的含硫气体以及温室气体,污染周围环境,威胁生态平衡,也会给下游装置造成较大影响。
渣油加氢技术能脱出渣油中大部分硫、氮、残碳以及重金属,能够大大的降低渣油燃烧后所产生的污染气体,减少废气处理量,增加了重质原油的加工量,减低了企业的加工成本,增加了企业的经济收入。
目前,渣油处理工艺多为固定床渣油加氢处理技术,其他形式的工艺技术也具有相同的效果,但是各有优缺点,本文主要对此进行研讨。
1.固定床渣油加氢工艺反应原理1.1脱硫反应作为脱硫反应沸腾床-固定床组合渣油加氢处理最为重要的化学反应,脱硫反应参与硫化物类型复杂、结构复杂,涉及流程较为复杂。
通常情况下,硫化物脱硫反应可认为是渣油借助硫化物催化作用,促使碳硫反应断裂,属于氢解反应,可释放硫化氢气体、无硫饱和烃,这类化学反应比较强烈,为不可逆反应。
加氢脱硫反应中,催化剂颗粒尺寸、催化剂孔径分布、催化剂颗粒工艺条件为三大主要影响因素。
1.2脱金属反应加氢脱金属反应主要是去除金属杂质,比如:镍、铁,金属杂质会影响残渣二次反应性能。
脱金属与脱硫反应类似,属于沸腾床-固定床组合渣油加氢处理的关键化学反应,属于一个或多个可逆反应。
该反应影响因素为催化剂颗粒尺寸、催化剂孔径分布、反应物分子扩散率。
1.3反硝化反应残渣内的氮元素存在形式为氮杂环化合物,杂环饱和后加氢,能够促进碳氮裂解,并形成气产物。
渣油加氢装置操作任务及操作原则
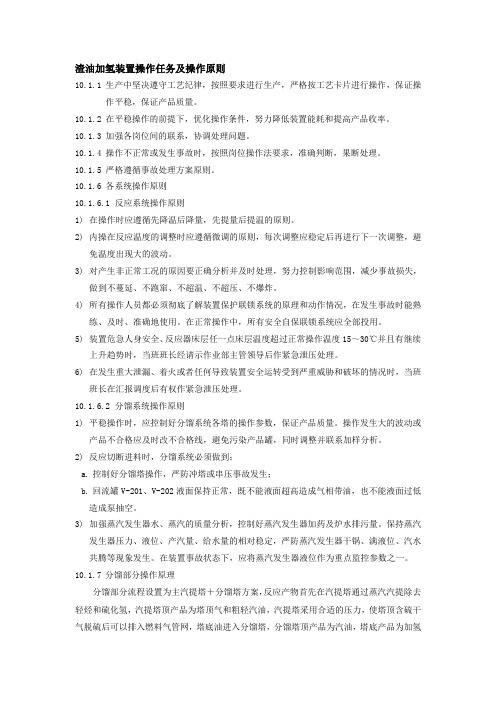
渣油加氢装置操作任务及操作原则10.1.1生产中坚决遵守工艺纪律,按照要求进行生产,严格按工艺卡片进行操作,保证操作平稳,保证产品质量。
10.1.2在平稳操作的前提下,优化操作条件,努力降低装置能耗和提高产品收率。
10.1.3加强各岗位间的联系,协调处理问题。
10.1.4操作不正常或发生事故时,按照岗位操作法要求,准确判断,果断处理。
10.1.5严格遵循事故处理方案原则。
10.1.6各系统操作原则10.1.6.1反应系统操作原则1)在操作时应遵循先降温后降量,先提量后提温的原则。
2)内操在反应温度的调整时应遵循微调的原则,每次调整应稳定后再进行下一次调整,避免温度出现大的波动。
3)对产生非正常工况的原因要正确分析并及时处理,努力控制影响范围,减少事故损失,做到不蔓延、不跑窜、不超温、不超压、不爆炸。
4)所有操作人员都必须彻底了解装置保护联锁系统的原理和动作情况,在发生事故时能熟练、及时、准确地使用。
在正常操作中,所有安全自保联锁系统应全部投用。
5)装置危急人身安全、反应器床层任一点床层温度超过正常操作温度15~30℃并且有继续上升趋势时,当班班长经请示作业部主管领导后作紧急泄压处理。
6)在发生重大泄漏、着火或者任何导致装置安全运转受到严重威胁和破坏的情况时,当班班长在汇报调度后有权作紧急泄压处理。
10.1.6.2分馏系统操作原则1)平稳操作时,应控制好分馏系统各塔的操作参数,保证产品质量。
操作发生大的波动或产品不合格应及时改不合格线,避免污染产品罐,同时调整并联系加样分析。
2)反应切断进料时,分馏系统必须做到:a.控制好分馏塔操作,严防冲塔或串压事故发生;b.回流罐V-201、V-202液面保持正常,既不能液面超高造成气相带油,也不能液面过低造成泵抽空。
3)加强蒸汽发生器水、蒸汽的质量分析,控制好蒸汽发生器加药及炉水排污量。
保持蒸汽发生器压力、液位、产汽量、给水量的相对稳定,严防蒸汽发生器干锅、满液位、汽水共腾等现象发生。
沸腾床渣油加氢装置工艺

沸腾床渣油加氢装置工艺
沸腾床渣油加氢装置是一种炼油厂用于将高硫含量的废旧油转化
成低硫含量燃料的重要设备。
该装置基于热力学原理和化学反应原理,通过加入氢气将硫化物、氮化物、氧化物等有害物质转化为硫化氢、
氨等无害物质,从而制备出高质量的可再生燃料。
沸腾床渣油加氢装置的工艺流程分为四个主要步骤。
首先,高温
的废旧油通过加热器加热至一定温度,然后进入沸腾床反应器。
在沸
腾床反应器中,废旧油和氢气在高温高压的条件下反应,在催化剂的
作用下,有害物质逐渐转化为无害物质。
其次,在与有害物质反应之后,净化处理的油气通过气液分离器
进入催化剂降温器。
在催化剂降温器中,废旧油会逐渐冷却,减少反
应的温度和压力变化。
冷却后的油液再次进入气液分离器,从中分离
出气体和液体,以便进行下一步的工艺处理。
第三,在气液分离器被分离出的气体中,还含有未被反应的氢气。
这些未反应的氢气会进入再循环器中,以便再次参与反应。
最后,在
液体中,剩余的废旧油以及处理后的可再生燃料被分离出来,以供下
游工艺使用。
总的来说,在沸腾床渣油加氢装置工艺流程中,高温高压的反应
促进了油中有害物质的分解和转化,从而制备了高质量的可再生燃料。
同时,该装置还可以实现氢气的再利用,提高了能源的利用率,有利
于实现炼油厂的可持续发展。
渣油加氢工艺流程

第一节工艺技术路线及特点工艺技术路线300X10*“渣油加範脱硫装置采用CLG公司的固定床渣油加氮脱硫匚艺技术.该匸艺技术満足操作删期SOOOh.柴油产骷硫含址不大于500ppm.加氢常渣产品硫含畫不大于0.35硫、残炭不大于5・5w& Ni+V不大于15pp■的要求。
二、工艺技术特点1、反瓯部分设置两个系列.每个系列可以单开单停(单开单停定指装置二个系列分别进行正常生产和停工更换供化剂)O由于渣油加氫脱硫装逆的设计操作用期与其它主耍生产装亀不一致.从全厂生产安排的角度.单开单停可以有效解决原料储存、催化裂化装迸进料址等何题.并便全厂油品调配更灵活.2.反应部分釆用热窩分工艺涼程.减少反咸潦出物冷却负荷:优化换热涼程.充分回收热址.降低能耗,3.反应部分高压换热器采用双壳.双弓型式.强化传热效果.提高传热效率。
4.反应器为单床层设置.易于催化剂装卸.尤其是便于卸催化剂.5.采用原料油自动反冲洗过滤器系统.滤除大于25心以上朵质.减缓反应器压降增大速度.延长装置操作周期;6.原料油换热系统设置注阻垢剂设施.延长操作周期.降低能耗.而且在停1:换剂期间可减少换热器和其它设备的检修匸作•7.原料油缓冲確采用氮气覆盖措施.以防止原料油与空气接触从而减轻高温部位的结焦程度:8.采用炉前混氮流程.避免进料加热炉炉管结焦.9.第一台反应器入口温度通过调节加热炉燃料和高压换热器旁路址来控剑.其他反应器入口温度通过调节急冷氮虽來控制,10.在热商分气空冷器入口处设注水设施.避免钱盐在低鮎部位的沉枳。
11,循环氫脱硫塔前设高压离心式分离器除去携带的液体婭类.域少循坏氮脱硫塔的起泡倾向.有利丁•循环氮脱硫的正常操作。
12.设赳离压膜分离系统.保证反腹氮分压。
13.冷低压闪蒸谜的富氮气体去加氮裂化装魁脱硫后去PSA回收包气,14.新宜压缩机釆用二开一备•每台50%负荷.单机负荷校小.方便制造.且装置有备机,15.分憎部分采用主汽提塔+分懈塔流程.在汽提塔除去轻烧和硫化氮.降低分他塔材质耍求.分懈塔设侧线柴油汽提塔及中段回流加热原料油.降低塔顶冷却负荷.捉高能虽利用率.减小分懈塔塔径。
渣油加氢操作规程

渣油加氢操作规程渣油加氢是一种重要的石油加工技术,可将低质量的渣油转化为高质量的燃料油和化工原料。
本文将介绍渣油加氢操作规程,包括操作步骤、工艺条件和安全措施等内容。
一、渣油加氢操作步骤1. 原料准备:将待加工的渣油送入预处理装置进行脱盐、脱硫等预处理工序,以降低渣油中的杂质含量,确保操作安全和产品质量。
2. 加氢反应器:将预处理后的渣油送入加氢反应器,与催化剂在一定的温度和压力下进行加氢反应。
加氢反应器通常采用固定床反应器或浆床反应器。
3. 反应过程控制:通过调节加氢反应器的温度、压力和催化剂的进料量,控制反应过程中的温度、压力和反应速率,以提高反应效果。
4. 分离和处理:将加氢反应产物送入分离装置,通过分馏、萃取、吸附等工艺将产品中的不同组分分离出来,获得目标产品。
5. 产品处理:对分离出来的目标产品进行进一步处理,如脱色、脱臭等,以提高产品的质量和市场竞争力。
6. 产品储存和装运:将处理好的产品储存于储罐中,通过管道或罐车等方式进行装运,以满足市场需求。
二、渣油加氢工艺条件1. 温度:渣油加氢反应的适宜温度通常在300-450摄氏度之间,具体温度视渣油的性质和产品要求而定。
2. 压力:加氢反应的适宜压力通常在10-30兆帕之间,压力越高,反应速率越快,但也会增加设备的投资和运行成本。
3. 催化剂:选择合适的催化剂对渣油加氢反应至关重要,常用的催化剂有钼、镍等金属及其氧化物或硫化物。
4. 催化剂的进料量:催化剂的进料量需要根据渣油的性质和处理量进行合理的调节,以保证反应效果和催化剂的寿命。
三、渣油加氢操作安全措施1. 设备安全:加氢反应器和分离装置等设备的设计、制造和安装要符合相关标准和规定,确保设备的稳定运行和安全操作。
2. 防火防爆:渣油加氢过程中可能产生易燃易爆的气体和液体,应采取防火防爆措施,如安装爆破片、防火墙等设施。
3. 气体处理:渣油加氢过程中产生的气体需要进行处理,如回收利用或安全排放,以防止对环境和人员造成伤害。
渣油加氢现场操作规程

渣油加氢现场操作规程10.4.1高压换热器操作方法10.4.1.1使用前的检查、准备工作1)检查换热器静电接地是否良好。
2)检查地脚螺栓及各联接法兰螺栓是否松动。
(滑动端应留有间隙)3)检查换热器壳体表面有无变形、碰伤裂纹、锈蚀麻坑等缺陷。
4)检查内、外圈顶丝是否拧紧、顶丝数量是否齐全。
5)气密试验与系统一起进行, 试验时,要检查信号孔有无泄漏现象。
10.4.1.2换热器的投用和停用1)在投用换热器前应首先检查放空阀是否关闭。
2)投用换热器时应先开冷流,后开热流。
停用时应先停热流,后停冷流。
3)在投用过程中,先开出口,后开入口,防止憋压。
4)在投用过程中,热流侧开关阀门要缓慢,防止因升温过快而出现泄漏。
5)用蒸汽吹扫换热器时,吹扫一程时,要将另一程的放空阀或进出口阀打开,防止介质受热膨胀而憋压。
引蒸汽时要缓慢,以防水击。
6)要经常检查换热器的温度、压力是否正常,管壳程是否有内漏,头盖、丝堵、法兰、放空阀等有无渗漏。
10.4.1.3使用中的注意事项1)严禁超温、超压,以免影响使用寿命及损坏设备2)严禁换热器单面受热,以免发生泄漏,一旦发生泄漏,应及时做相应处理。
3)严禁升降温速度过快,流量调节要缓慢。
4)正常使用中注意检查信号孔有无泄漏。
如果有,应将顶丝拧紧,拧紧顶丝时要包含所有顶丝。
5)检查换热器的膨胀量。
6)系统升压时,高压换热器两侧的压差要小于规定值,以免出现内漏现象。
10.4.2低压换热器操作方法10.4.2.1使用前的检查准备工作1)检查换热器静电接地是否良好。
2)检查地脚螺栓及各联接法兰螺栓是否松动。
(滑动端应留有间隙)3)检查出入口阀门是否完好,手轮是否齐全好用。
4)检查换热器壳体表面有无变形、碰伤裂纹、锈蚀麻坑等缺陷。
5)检查温度、压力表等仪表是否好用6)试压合格后,方可使用;10.4.2.2使用时的注意事项1)严禁超温、超压,以免影响使用寿命及损坏设备2)严禁换热器单面受热,以免发生泄漏,一旦发生泄漏,应及时切除。
渣油加氢工艺技术
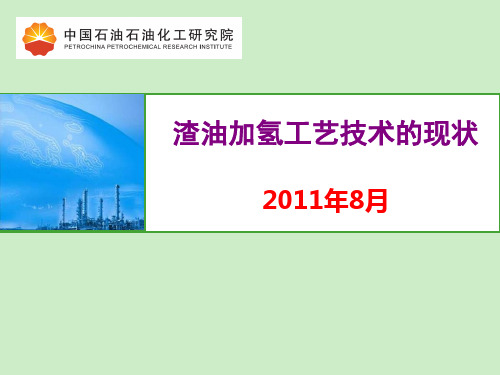
– 部分转化产品的H/C比高于原料,必须有部分产品的
H/C比低于原料
脱碳过程 ,焦化和催化等
– 通过外加H,可提高产品的H/C比
加氢过程
– 实际为H,C和杂原子的重排组合过程
– 脱碳过程与加氢过程各有特点,合理组合使用
前 言-典型炼油厂加工流程
石脑油加氢
重整
煤油加氢
PSA
常
柴油加氢
减
压
装
置
加氢裂化
较成熟 较高
开发中, 基本成熟
中等
200-250 较复杂 基本成熟 较高
前 言--加氢技术发展历程
• 国内加氢技术发展历程和概况
– 重油加氢处理领域技术开发 • 1986年初,探索性研究 • 1995年,脱硫和脱氮两个品种催化剂在齐鲁 VRDS 装置首次工业化 • 1996年,减渣系列四大类12个牌号催化剂在齐鲁 VRDS 全部工业化 • 1999年10月,常渣系列催化剂在大连WEPEC 200 万吨/年ARDS上首次工业化 • 1999年12月,完全采用国内技术和催化剂的茂名 200万吨/年S-RHT 开汽成功
前言--我国炼油业面临的宏观形势
炼油技术发展趋势
1. 发展深加工技术,提高轻质油收率和商品化率; 2. 提高加工各种海外原油的能力; 3. 提高清洁燃料生产能力和水平; 4. 大力推广应用新型节能降耗技术; 5. 生产过程清洁化技术(环保技术)。
前言--石化产业发展之路
面对原油资源短缺,高油价和燃油质量标准 不断升级,污染物排放浓度和总量要求更加严 格的压力,石油化工产业的发展必须坚持科 学发展观,走重油深度加工、环境友好,产品 清洁化道路。提高资源综合利用率,把重质 、劣质原油尽可能多地转化为优质成品油和 化工原料。
170万渣油加氢装置培训资料装置操作法
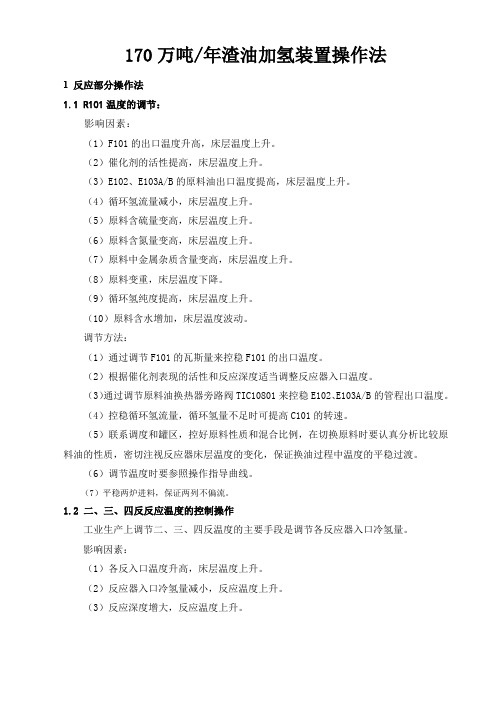
170万吨/年渣油加氢装置操作法1 反应部分操作法1.1 R101温度的调节:影响因素:(1)F101的出口温度升高,床层温度上升。
(2)催化剂的活性提高,床层温度上升。
(3)E102、E103A/B的原料油出口温度提高,床层温度上升。
(4)循环氢流量减小,床层温度上升。
(5)原料含硫量变高,床层温度上升。
(6)原料含氮量变高,床层温度上升。
(7)原料中金属杂质含量变高,床层温度上升。
(8)原料变重,床层温度下降。
(9)循环氢纯度提高,床层温度上升。
(10)原料含水增加,床层温度波动。
调节方法:(1)通过调节F101的瓦斯量来控稳F101的出口温度。
(2)根据催化剂表现的活性和反应深度适当调整反应器入口温度。
(3)通过调节原料油换热器旁路阀TIC10801来控稳E102、E103A/B的管程出口温度。
(4)控稳循环氢流量,循环氢量不足时可提高C101的转速。
(5)联系调度和罐区,控好原料性质和混合比例,在切换原料时要认真分析比较原料油的性质,密切注视反应器床层温度的变化,保证换油过程中温度的平稳过渡。
(6)调节温度时要参照操作指导曲线。
(7)平稳两炉进料,保证两列不偏流。
1.2 二、三、四反反应温度的控制操作工业生产上调节二、三、四反温度的主要手段是调节各反应器入口冷氢量。
影响因素:(1)各反入口温度升高,床层温度上升。
(2)反应器入口冷氢量减小,反应温度上升。
(3)反应深度增大,反应温度上升。
(4)原料油性质对反应温度的影响与R101相同。
(5)催化剂的活性增加,床层温度上升。
(6)循环氢纯度提高,反应温度上升。
调节方法:(1)通过调节各反的入口冷氢量来调节其入口温度和床层温度,保持各床层温升≯28℃。
(2)为了防止温度波动过大,每次调节温度的范围应在0.5℃左右。
(3)控制转化深度在设计范围内。
(4)原料油性质变化时,反应温度的调节方法与R101相同。
(5)根据催化剂表现的活性和反应深度适当调整反应器入口温度。
- 1、下载文档前请自行甄别文档内容的完整性,平台不提供额外的编辑、内容补充、找答案等附加服务。
- 2、"仅部分预览"的文档,不可在线预览部分如存在完整性等问题,可反馈申请退款(可完整预览的文档不适用该条件!)。
- 3、如文档侵犯您的权益,请联系客服反馈,我们会尽快为您处理(人工客服工作时间:9:00-18:30)。
►经过加氢过程,全厂总硫回收率可达到87%:
►进入轻质油品中的硫含量只有2%;
►燃料油,沥青和石油焦带走的硫含量约为10%;
►排入大气的硫含量只有0.8%。
渣渣油加氢系列催化剂及特点
渣油加氢系列催化剂及特点
催化剂种类 保护剂 颗粒大小 大 平均孔径 最大 酸性 最弱 比表面积 最小 孔容 最大 金属含量 最低 脱Fe,Na,Ca 主要作用 HDM 小 次大 次弱 次小 较大 次低
渣油固定床加氢技术的作用
投 资 值 : 亿 元
32 30 28 26 24 22 20 0.3
加氢方案
焦化方案
0.5
焦化:加氢投资比
0.7
0.9
焦化:加氢投资比对两方案总投资值的影响
渣油固定床加氢技术的作用
35 投 30 资 25 利 20 税 15 率%10 5 0 15 20
加氢方案 焦化方案
渣油固定床加氢技术的作用
► 提高原油加工利用率 ► 提供催化裂化装臵原料 ► 提供焦化装臵原料
► 富产优质中间馏分油
► 提高硫磺回收率
渣油固定床加氢技术的作用
► 提高原油加工利用率
加工路线
液体产品(含液化气)收率,% 轻油收率(汽柴油和石脑油),%
加氢路线
87.6 71.70
焦化路线
71.45 61.17
316
371
427
482
反应温度/℃
催化剂级配装填技术
渣油性质、渣油加氢反应和固定床工艺特点决定级配 装填
两种因素变化
床层空隙率(颗粒大小和形状) 内在性质(活性、选择性) 固体沉积分布均匀化 活性与稳定性平衡
效果与原料有关
渣油固定床加氢技术特点
◆ 原料油: 中东含硫原油 ◆ 渣油加氢-RFCC组合加工 ◆ 采用 催化剂组合装填系统(CCS) ◆ 优化反应温度操作模式
±Á Ö ó >370 RDSº ó >370
±Á Ö ó ³ £ Ô ü Í º ¼ Ó Ç â º ó ³ £ Ô ü RFCCÊ ¯ Ä Ô Ó Í (C5-221)Ê Õ Â Ê
50
48
46 ú ² · Æ ú ² 44 Ê Â % 42
40
38
±Á Ö ó >370
RDSº ó >370
45 40 35
% Ê ú Â ¯ ² ¹ » ½
30 25 20 15 10 5 0 ±Á Ö ó ¼ õ Ô ü £ Ô ³ ü ¼ Ó Ç â º ó ¼ õ Ô ü
渣油固定床加氢技术的作用
► 富产优质中间馏分油
►石脑油收率:1-5% ►柴油收率:6-17%
渣油固定床加氢技术的作用
► 提高硫磺回收率 ►国外加工中东原油能力为2100万吨的炼油厂,每年由原油
221-360 ℃ LCO, m%
>360 ℃ /焦炭, m% 催化剂消耗, kg/t
18.9
10.0/10.3 8.09
16.4
7.2/7.0 0.7
催化剂冷却器
需要
否
常压渣油加氢常渣与减压渣油加氢常渣FCC对比
原料油:80%沙轻+20%沙重
馏分 比重(15.6 ℃) S,m% N,m% AR 0.9645 3.5 0.2 RDS AR 0.9198 0.2 0.11 VR 1.0234 4.8 0.36 VRDS AR 0.9440 0.32 0.19
12
10
8
Ê Õ Â ·Ê ú Æ ²
%
6 4 2 0 ±Á Ö ó >370 RDSº ó >370
±Á Ö ó ³ £ Ô ü º Í ¼ Ó Ç â ³ £ Ô ü RFCC´ ß » ¯ ¼ Á Ï û º Ä
6
5
Ä , kg/t û º Á Ï ¯ ¼ ß » ´
4
3
2
1
0 ±Á Ö ó >370 RDSº ó >370
±Á Ö ó ¼ õ Ô ü Ó ë ³ £ Ô ü ¼ Ó Ç â º ó ¼ õ Ô ü ½ ¹ » ¯ 82-177Ê Õ Â Ê
7.8 7.6 7.4
% Ê ú Â ¯ ² ¹ » ½
7.2 7 6.8 6.6 6.4 ±Á Ö ó ¼ õ Ô ü £ Ô ³ ü ¼ Ó Ç â º ó ¼ õ Ô ü
催化剂颗粒形状的影响
►不同形状和直径的催化剂的利用率
催化剂形状 普通圆柱形 普通圆柱形 直径,mm 5 1.5 利用率,% 23 64
空心圆柱形
三叶草行 三叶草行
5
5 1.5
45
35 90
催化剂颗粒度大小的影响
►催化剂的颗粒大小不仅影响催化剂的活性,而且对
反应器催化剂床层的压降也有显著的影响。
►随催化剂颗粒的变小,扩散的限制作用减少,催化
渣油固定床加氢技术的作用
► 提供催化裂化装臵原料 ►
提供优质FCC原料
提高FCC装臵轻油收率 降低FCC汽油烯烃和S含量 降低FCC柴油S含量
►
脱除原料中大部分重金属化合物, 减少 FCC装臵催化剂消耗
直馏常渣与加氢常渣FCC对比
原料油:沙轻 馏分 比重(15.6 ℃) S,m% N,m% CCR,m% Ni+V, μg· g-1
221-360 ℃ LCO, m%
>360 ℃ /焦炭, m% 催化剂消耗, kg/t 催化剂冷却器
14.8
6.8/7.3 0.465 不需要
16.5
8.4/9.2 1.51 需要
±Á Ö ó ³ £ Ô ü º Í ¼ Ó Ç â º ó ³ £ Ô ü RFCCÆ ø Ì å Ê Õ Â Ê
10 9 8 7 ² ú Æ · Ê Õ Â Ê % 6 5 4 3 2 1 0 <C2 C3 ø Ì Æ å Ã û ³ Æ C4
±Á Ö ó ³ £ Ô ü º Í ¼ Ó Ç â º ó ³ £ Ô ü RFCC >360² ú  Ê
12
10
8
Ê Õ Â ·Ê ú Æ ²
%
6 4 2 0 ±Á Ö ó >370 RDSº ó >370
±Á Ö ó ³ £ Ô ü º Í ¼ Ó Ç â º ó ³ £ Ô ü RFCCÉ ú ½ ¹ Á ¿
► 脱氮催化剂的作用和特点
►深度脱除原料中的硫化物 ►深度脱除原料中的氮化物
►深度脱除原料中残存的金属化合物
►加氢转化,降低原料油中残炭值
渣油加氢系列催化剂及特点
► 脱氮催化剂的品种
► 圆柱形
► 四叶草型 ► 蝶形
渣油加氢系列催化剂及特点
◆物化性质对渣油加氢过程的影响
►催化剂颗粒形状的影响 ►催化剂颗粒度大小的影响 ►催化剂孔径的影响 ►催化剂孔容的影响 ►催化剂比表面积的影响
原油价格,美元/桶
25
30
原油价格对投资利税率的影响
渣油固定床加氢技术的作用
加氢与焦化方案投资利税率差 值,%
9.0 7.0 5.0 3.0 1.0 -1.0 -3.0 -5.0 0.7 0.8 0.9
图10
1
1.1 1.2 1.3
(轻/重油)/(轻/重油)基准
轻/重油比价的变化对两方案投资利 税率的影响
轻油+液化气收率,% 液体产品(含液化气)收率差值
轻油(汽柴油和石脑油)收率差 轻油+液化气收率差值
81.87
16.15 10.53 13.48
68.39
渣油固定床加氢技术的作用
26 投 资 利 税24 率% 22 20 18 16 14 0.3
加氢方案
焦化方案
0.5
0.7
0.9
焦化:加氢投资比
焦化 :加氢投资比对两方案投资利税率的影响
剂的活性增加,但催化剂床层的压降也急剧上升, 采用拉西环形催化剂对降低系统的压降比较有利。
►渣油固定床加氢过程,催化剂的颗粒直径不宜过小
,通常选择1-1.6mm。
催化剂孔容,孔径和比表面积的影响
► 催化剂的孔容,孔径和比表面积之间是相互联系和相互影响
的。 ► 在一定的范围内,增加催化剂的孔和孔径,则催化剂的比表 面积将会下降,因此,催化剂孔结构的选择应兼顾催化剂 的孔容,孔径和比表面积。
► 保护催化剂的特点
► 较大的孔容。 ►孔径分布呈双峰型 ►比表面积适中,一般为100m2/g-170m2/g。 ► 表面呈弱碱性或弱酸性。 ► 磨耗低、强度大。
渣油加氢系列催化剂及特点
► 保护催化剂品种
► 球形系列 ► 椭球系列 ► 拉西环系列
► 四叶轮系列
► 蜂窝系列
ห้องสมุดไป่ตู้
渣油加氢系列催化剂及特点
渣油固定床加氢工艺技术操作
胡长禄
2011年8月青岛
渣油固定床加氢技术特点和作用
渣油固定床加氢处理工艺技术特点
H2S 和 NH3 浓度
反应温度 反应物浓度 0 床层位置 1
渣油加氢裂化产品分布随反应温度的变化
538℃+ 182~343℃ 产品收率/wt% (基于进料) C5~182℃ 343~538℃ C1~C4
58.0 24.0
焦炭, m%
±Á Ö ó ¼ õ Ô ü Ó ë ³ £ Ô ü ¼ Ó Ç â º ó ¼ õ Ô ü ½ ¹ » ¯ C5-82Ê Õ Â Ê
3.5 3.4 3.3
% Ê ú Â ¯ ² ¹ » ½
3.2 3.1 3 2.9 2.8 2.7 2.6 ±Á Ö ó ¼ õ Ô ü £ Ô ³ ü ¼ Ó Ç â º ó ¼ õ Ô ü